FQC检验记录表
FQC工作职责与与流程

1.目的:规范生产制造出的成品之品质管理作业,保障生产的成品品质。
2.适用范围:公司生产出的成品品质管控3.定义:成品检测(FQC):是在产品完成所有制程工序后,产品入库前,对于产品的品质状况,包括:外观检验(颜色、光泽、粗糙度、毛边、是否有刮伤)、尺寸的量测、性能测试(电气特性、操作控制),进行一次全面的检验与测试,目的在确保入库的成品为合格成品。
4.内容:4.1FQC工作职责:4.1.1对生产送检批次的成品进行抽检。
4.1.2针对抽样成品进行外观检测,并记录。
4.1.3针对抽样成品进行电性检测,并记录。
4.1.4针对不良情况,根据判定标准,决定其是否允收。
4.1.5针对不良品返工,再次送检产品,再次进行抽检测试,如再次不合格返工,第三次抽检将执行加严抽检方式抽检。
4.1.6统计每次检测的记录,并详细统计成为电子档保存,以方便后续追踪。
4.1.7对送检检测与生产未送检的产品,严格区分,并对抽检测试不良进行标试。
4.1.8完成公司和上级交代的其它工作,并对上级负责。
4.2IQC工作流程:生产送检按AQL抽样抽样外观检验5.参考文件: 无6.表单/记录:6.1成品送检单6.2 FQC检验日报表7.附件:无学习交流文档OKOKNG允收入库整批返工电性按AQL抽样抽样电性检验OK —NG允收入库1 t 1按加严抽样允收入库抽样电性检验NG整批返工外观整批返工按AQL抽样OK NG整批返工整批返工。
CCC认证记录表格-审核查检表7
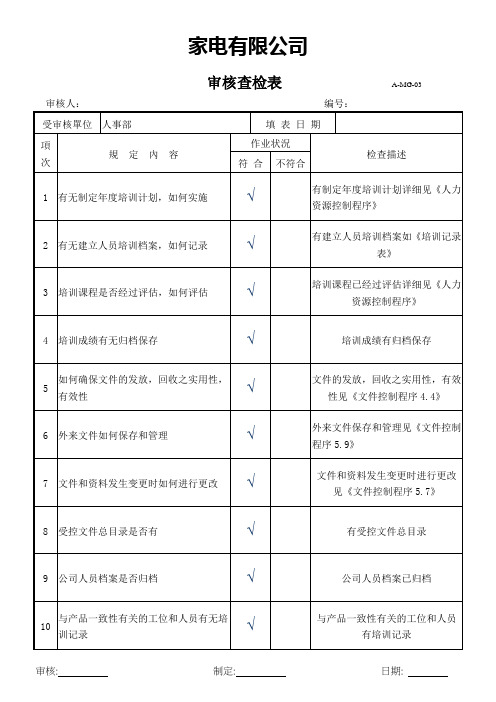
家电有限公司
审核查检表A-MG-03审核人:编号:
受审核單位人事部填表日期
項次規定內容
作业状況
检查描述
符合不符合
1 有无制定年度培训计划,如何实施√有制定年度培训计划详细见《人力资源控制程序》
2 有无建立人员培训档案,如何记录√有建立人员培训档案如《培训记录
表》
3 培训课程是否经过评估,如何评估√培训课程已经过评估详细见《人力
资源控制程序》
4 培训成绩有无归档保存√培训成绩有归档保存
5 如何确保文件的发放,回收之实用性,
有效性
√文件的发放,回收之实用性,有效
性见《文件控制程序4.4》
6 外来文件如何保存和管理√外来文件保存和管理见《文件控制程序5.9》
7 文件和资料发生变更时如何进行更改√文件和资料发生变更时进行更改见《文件控制程序5.7》
8 受控文件总目录是否有√有受控文件总目录
9 公司人员档案是否归档√公司人员档案已归档
10 与产品一致性有关的工位和人员有无培
训记录
√与产品一致性有关的工位和人员
有培训记录
审核: 制定: 日期:。
IQC、IPQC、FQC、OQC、QAQE质量检验有关的概念
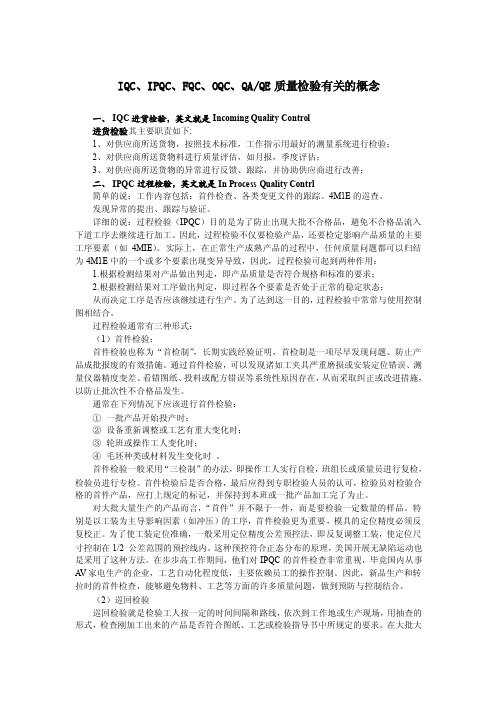
IQC、IPQC、FQC、OQC、QA/QE质量检验有关的概念一、IQC进货检验,英文就是Incoming Quality Control进货检验其主要职责如下:1、对供应商所送货物,按照技术标准,工作指示用最好的测量系统进行检验;2、对供应商所送货物料进行质量评估,如月报,季度评估;3、对供应商所送货物的异常进行反馈、跟踪,并协助供应商进行改善;二、IPQC过程检验,英文就是In Process Quality Contrl简单的说:工作内容包括:首件检查、各类变更文件的跟踪。
4M1E的巡查。
发现异常的提出、跟踪与验证。
详细的说:过程检验(IPQC)目的是为了防止出现大批不合格品,避免不合格品流入下道工序去继续进行加工。
因此,过程检验不仅要检验产品,还要检定影响产品质量的主要工序要素(如4MIE)。
实际上,在正常生产成熟产品的过程中,任何质量问题都可以归结为4M1E中的一个或多个要素出现变异导致,因此,过程检验可起到两种作用:1.根据检测结果对产品做出判走,即产品质量是否符合规格和标准的要求;2.根据检测结果对工序做出判定,即过程各个要素是否处于正常的稳定状态;从而决定工序是否应该继续进行生产。
为了达到这一目的,过程检验中常常与使用控制图相结合。
过程检验通常有三种形式:(1)首件检验:首件检验也称为“首检制”,长期实践经验证明,首检制是一项尽早发现问题、防止产品成批报废的有效措施。
通过首件检验,可以发现诸如工夹具严重磨损或安装定位错误、测量仪器精度变差、看错图纸、投料或配方错误等系统性原因存在,从而采取纠正或改进措施,以防止批次性不合格品发生。
通常在下列情况下应该进行首件检验:①一批产品开始投产时;②设备重新调整或工艺有重大变化时;③轮班或操作工人变化时;④毛坯种类或材料发生变化时。
首件检验一般采用“三检制”的办法,即操作工人实行自检,班组长或质量员进行复检,检验员进行专检。
首件检验后是否合格,最后应得到专职检验人员的认可,检验员对检验合格的首件产品,应打上规定的标记,并保持到本班或一批产品加工完了为止。
IPQC FQC不良记录表

序號型號料號日期稽核人問題點描述1140w2-A0015-A110-11馬娟娟IPQC在巡检时发现标示为7号灯LE上的保护膜未去掉2140w2-A0015-A110-11馬娟娟IPQC在巡检时发现标示为15号灯负极线露在外面3140w2-A0015-A110-11馬娟娟IPQC在巡检时发现反光罩上有明显黑手印,正在烧机中的灯竟然灭了。
4140w2-A0015-A110-12馬娟娟IPQC巡检时发现标示为10号灯黑色绝缘线外露5140w2-A0015-A110-12馬娟娟IPQC巡检时发现标示为5号及7号烤弯玻璃外部有硅胶外溢6140w2-A0015-A110-12馬娟娟IPQC巡检时发现3号反光罩变形,里面有异物7120W7-A0012-A111-9陈爱丽OQC在成品入库时发现OP在拉叉车时,由于没做好适当处理,造成产品摔落到地。
8140W7-A0012-A111-12马娟娟IPQC在制程巡检中发现上下盖已组装好的产品有1PCS上盖缺料9140W7-A0012-A111-12马娟娟IPQC在制程巡检中发现已组装好的产品在放入烧机架上有电源线接错位置现像,没有按SOP作业10140W7-A0012-A111-12马娟娟IPQC在制程巡检中发在安装灯杆固定片上的华司有少装的多装现像,没有按SOP作业11#######马娟娟IPQC在制程巡检中发现产线在自制线材时没有在线头加上黑色绝缘套,导致Y型端子头裸露在外。
12#######马娟娟IPQC在制程巡验中发现产线在组装上盖时把没有套有绝缘套的线材安装到产品上,未按SOP作业。
13#######马娟娟IPQC在制程巡检中发现产线在连接Power与线材时有线头接错位置的现象。
14#######马娟娟IPQC在制程巡检中发现已组装好的产品在放入烧机架上再次把电源线接错位置,没有按SOP作业IPQC巡檢異常追蹤:460cm/600cm线材加工上盖组装(半成品)上盖组装(半成品)上盖组装(半成品)15加工线材#######王彩红IPQC在制程巡验时发现产线在加工460CM /600CM 线材时没有挂SOP进行作业。
SAP FQC&OQC
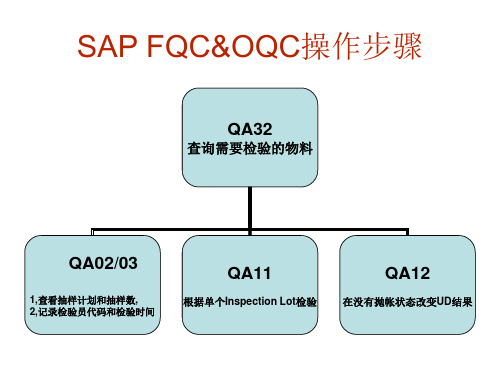
2,在此输入密码
3,点击此处
3.进入SAP界面
进入此界面
4.根据操作指示(输入相关T-Code查询)
1,在此处输入:QA32 2,点击此处(回车)
5.进入T-Code界面后输入需要查询的相关信息
5,点击闹钟
1,输入查询日期从什么时候到什么时候
2,输入XX工厂代码(XX:3380 ; FT:336计 划名(前面一定 要有”/”) 2,在此输入名 3,点击此 图标
3,点此保存
2,点此按钮
1,点击此图标
2,点击此图标 2,点击此图 标 1,选择设置
三.QA32里导出数据
1,点击此图 标
2,点击此图标
1,选择此处 1,选择 Table 2,点击此图标
2,点击此图标
1.数据导出
查看进入的T-Code
7.进入检验界面进行检验
2,点击此处 1,点击此处
8.进入检验界面记录/查看检验信息
3,点击保存
1,点击此处
1,点击此 处
2,查看此处抽验数 是多少? 2,输入检验信息.如:日期; 时间;QC代号
1,点击此处
2,查看此处AQL是多少?
9.进入QA32做UD操作
1,点击此处选 择相应的料号 2,做UD点击此处
SAP FQC&OQC操作步骤
QA32
查询需要检验的物料
QA02/03
1,查看抽样计划和抽样数, 2,记录检验员代码和检验时间
QA11
根据单个Inspection Lot检验
QA12
在没有抛帐状态改变UD结果
1.双击SAP图表进入
双击图标
2,点击此处
1,选择此处
2.进入登入界面(输入用户信息)
称重记录表
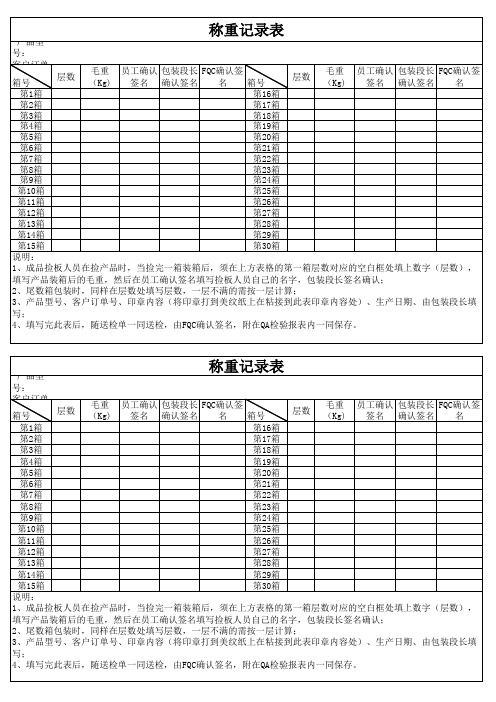
称重记录表
产品型号: 客户订单号: 印章内容: 生产日期: 员工确认 包装段长 FQC确认签 员工确认 包装段长 FQC确认签 层数 毛重(Kg) 层数 毛重(Kg) 箱号 签名 确认签名 名 箱号 签名 确认签名 名 第1箱 第16箱 第2箱 第17箱 第3箱 第18箱 第4箱 第19箱 第5箱 第20箱 第6箱 第21箱 第7箱 第22箱 第8箱 第23箱 第9箱 第24箱 第10箱 第25箱 第11箱 第26箱 第12箱 第27箱 第13箱 第28箱 第14箱 第29箱 第15箱 第30箱 说明: 1、成品捡板人员在捡产品时,当捡完一箱装箱后,须在上方表格的第一箱层数对应的空白框处填上数字(层数), 填写产品装箱后的毛重,然后在员工确认签名填写捡板人员自己的名字,包装段长签名确认; 2、尾数箱包装时,同样在层数处填写层数,一层不满的需按一层计算; 3、产品型号、客户订单号、印章内容(将印章打到美纹纸上在粘接到此表印章内容处)、生产日期、由包装段长填 写; 4、填写完此表后,随送检单一同送检,由FQC确认签名,附在QA检验报表内一同保存。
称重记录表
产品型号: 客户订单号: 印章内容: 生产日期: 员工确认 包装段长 FQC确认签 员工确认 包装段长 FQC确认签 层数 毛重(Kg) 层数 毛重(Kg) 箱号 签名 确认签名 名 箱号 签名 确认签名 名 第1箱 第16箱 第2箱 第17箱 第3箱 第18箱 第4箱 第19箱 第5箱 第20箱 第6箱 第21箱 第7箱 第22箱 第8箱 第23箱 第9箱 第24箱 第10箱 第25箱 第11箱 第26箱 第12箱 第27箱 第13箱 第28箱 第14箱 第29箱 第15箱 第30箱 说明: 1、成品捡板人员在捡产品时,当捡完一箱装箱后,须在上方表格的第一箱层数对应的空白框处填上数字(层数), 填写产品装箱后的毛重,然后在员工确认签名填写捡板人员自己的名字,包装段长签名确认; 2、尾数箱包装时,同样在层数处填写层数,一层不满的需按一层计算; 3、产品型号、客户订单号、印章内容(将印章打到美纹纸上在粘接到此表印章内容处)、生产日期、由包装段长填 写; 4、填写完此表后,随送检单一同送检,由FQC确认签名,附在QA检验报表内一同保存。
品质部各岗位绩效考核标准(QC主管、IQC、IPQC、FQC、OQC)

10
每月
公司工作范围内
连续4个月工作完成积极,态度良好
5
连续2个月工作完成积极,态度良好
2
当月工作完成积极,工作态度良好
0
工作完成不积极,多次催促才做好
-2
工作故意拖拉,工作太度差
-5
不能完成工作,工作态度极差
-10
6
纪律
QC是否能模范遵守各种规章管理制度
行政人事部汇总及各部门反应信息
连续3个月无C级以上客诉
30
每月
内部客户、外部客户
默认奖金基数500元(其中实验员从当月工资中抽取250元,公司提供250元)。绩效指数默认为一百分,奖励或扣罚分数依具体指标执行。(注:对于严重违纪者,一次性扣5-10分.
连续2个月无C级以上客诉
10
当月无C级以上客诉
0
1-2起C级客诉
-5
2-4起C级客诉或1起B级客诉
连续3月100分
5
每月
IQC检验办
公区
100分
2
95(含)-100分
0
90(含)-95分
-2
90分以下
-5
品质部IPQC绩效考核标准
序号
考核对象
考核指标
指标说明
数据来源
指标定义/计算公式
具体指标
奖惩分值
考核周期
范围
绩效基数
1
注塑PQC
客户投诉(单位:次)
出现A、B、C级质量事故以及其它相关方面的投诉
-10
5-6起C级客诉2起B级客诉
-20
超出上述的客诉
-30
2
制程生产不良率
所有车间的不良率
ISO9001不合格品控制程序(含流程图)
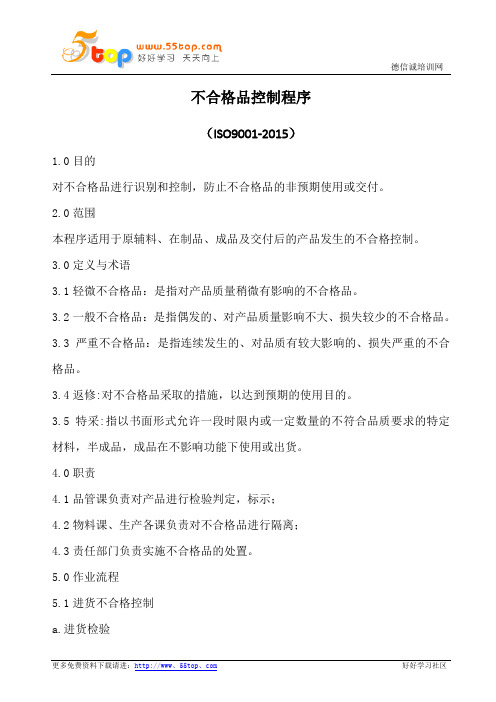
不合格品控制程序(ISO9001-2015)1.0目的对不合格品进行识别和控制,防止不合格品的非预期使用或交付。
2.0范围本程序适用于原辅料、在制品、成品及交付后的产品发生的不合格控制。
3.0定义与术语3.1轻微不合格品:是指对产品质量稍微有影响的不合格品。
3.2一般不合格品:是指偶发的、对产品质量影响不大、损失较少的不合格品。
3.3严重不合格品:是指连续发生的、对品质有较大影响的、损失严重的不合格品。
3.4返修:对不合格品采取的措施,以达到预期的使用目的。
3.5特采:指以书面形式允许一段时限内或一定数量的不符合品质要求的特定材料,半成品,成品在不影响功能下使用或出货。
4.0职责4.1品管课负责对产品进行检验判定,标示;4.2物料课、生产各课负责对不合格品进行隔离;4.3责任部门负责实施不合格品的处置。
5.0作业流程5.1进货不合格控制a.进货检验检验人员依据原物料检验标准、工程图纸、顾客要求等进行检验,判定为不合格品时开《品质异常处理单》并填写相关异常信息并附上不合格样品一并交给品管课长审核和管理部经理批准后扫描发邮件给采购课、生管课、物料课。
b.标示隔离进料不合格品由品管课检验人员进行标示,物料课人员将产品移至不合格品区域进行隔离。
c.不合格品处理1.退货:由物料课开具《退货单》,经品管、仓管确认后,经物料课长审核后通知采购课在7日内退货,若超出期限由我司自行处理。
当同一供应商因产品连续有2批因同样质量被拒收时,品管课开出《纠正和预防措施单》交采购课处理。
2.挑选使用:由采购课通知供应商,确定挑选方式:(1)由供应商进行挑选,挑选后的原物料须由品管课重新检验合格后方可入库使用;(2)由我公司安排物料课全检组人员进行挑选,挑选后的原物料须由品管课重新检验合格后方可入库使用;3.特采接收:在生产急需或紧急出货的情况下不影响安全,功能或结构的不合格品由采购课填写《品质异常处理单》交相关单位会审后由管理部经理核准后方可特采,同时品管员于该批产品上加贴“进料特采标签”;4.报废:制程中发现无法使用的来料不良品(含特采物料),由采购课与供应商沟通处理方式,物料课接收到可报废处理邮件或已扣款的财务部确认签署后开立《报废单》经资材部经理审核、副总核准后进行报废;5.不合格品的处理期限要求:采购课接单后需在24H内签回。
FQC_中英文出货检验指南
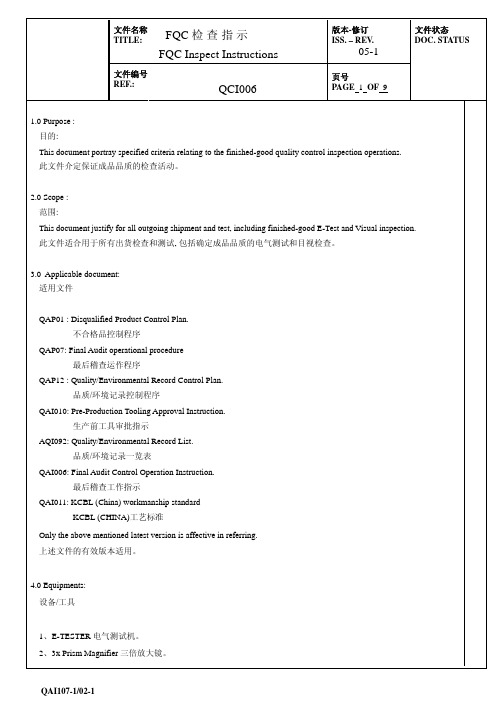
6.2 E-Test 电气测试:
6.2.1 Rinsed boards must conduct E-Test for open and short on circuitry. 洗板后的板要进行电气测试,以便发现线路的开路与短路。
6.2.2 All P/R testing condition must follow MEI027 instruction. Unless otherwise specified. 所有 P/R 的测试条件必须符合 MEI027 规定,除非有工程更改或其它新要求。
文件名称 TITLE:
FQC 检 查 指 示
FQC Inspect Instructions
文件编号 REF.:
QCI006
版本-修订 ISS. – REV.
05-1
页号 PAGE 1 OF 9
文件状态 DOC. STATUS
1.0 Purpose : 目的:
This document portray specified criteria relating to the finished-good quality control inspection operations. 此文件介定保证成品品质的检查活动。
品质部FQC技能考试题及答案
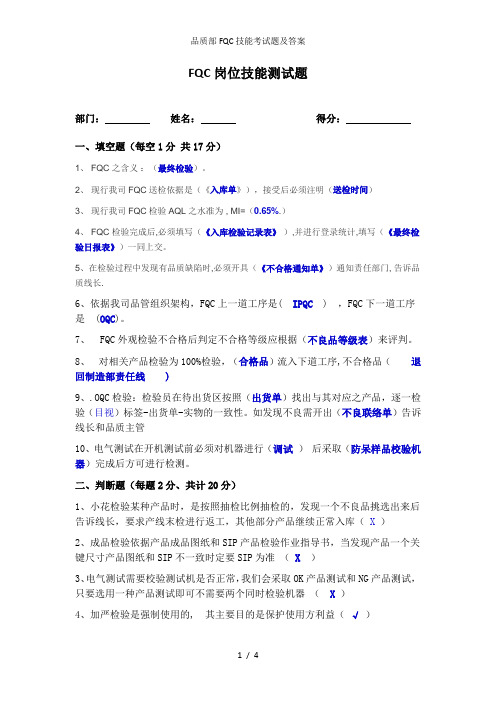
FQC岗位技能测试题部门:姓名:得分:一、填空题(每空1分共17分)1、 FQC之含义:(最终检验)。
2、现行我司FQC送检依据是(《入库单》),接受后必须注明(送检时间)3、现行我司FQC检验AQL之水准为 , MI=(0.65%.)4、 FQC检验完成后,必须填写(《入库检验记录表》),并进行登录统计,填写(《最终检验日报表》)一同上交。
5、在检验过程中发现有品质缺陷时,必须开具(《不合格通知单》)通知责任部门, 告诉品质线长.6、依据我司品管组织架构,FQC上一道工序是( IPQC) ,FQC下一道工序是(OQC)。
7、FQC外观检验不合格后判定不合格等级应根据(不良品等级表)来评判。
8、对相关产品检验为100%检验,(合格品)流入下道工序,不合格品(退回制造部责任线)9、.OQC检验:检验员在待出货区按照(出货单)找出与其对应之产品,逐一检验(目视)标签-出货单-实物的一致性。
如发现不良需开出(不良联络单)告诉线长和品质主管10、电气测试在开机测试前必须对机器进行(调试)后采取(防呆样品校验机器)完成后方可进行检测。
二、判断题(每题2分、共计20分)1、小花检验某种产品时,是按照抽检比例抽检的,发现一个不良品挑选出来后告诉线长,要求产线末检进行返工,其他部分产品继续正常入库(X)2、成品检验依据产品成品图纸和SIP产品检验作业指导书,当发现产品一个关键尺寸产品图纸和SIP不一致时定要SIP为准( X)3、电气测试需要校验测试机是否正常,我们会采取OK产品测试和NG产品测试,只要选用一种产品测试即可不需要两个同时检验机器(X)4、加严检验是强制使用的, 其主要目的是保护使用方利益(√)5、5S是指-清扫--、-清洁--、整理--、-整顿--、-修养(X )6、质量检验不包括查验原始质量凭证。
(X)7、质量检验的主要功能包括:产品检验(X)8、在上班前,必须检查/核对检测仪器和检测治具是否合格(√)9、检验前,FQC应了解产品的功能与要求,掌握检验重点首先掌握图纸中的公差和技术要(X )10、凡经检验或返修合格产品,按色差分类作好标识并加盖合格印章后放入已检存放区( X)三、不定项选择题(每题3分、共33分)多选、少选、漏选均不得分1、端子压接以下那一项(C)决定端子压接后的效果A、端子导体铆压高度B、端子绝缘铆压高度C、端子的压缩比例是关键D、绝缘铆压宽度2、若超过规定的特性值要求,将造成产品部分功能丧失的质量特性为(B)A.关键质量特性B.重要质量特性C.次要质量特性D.一般质量特性3、从适合顾客需要的角度对产品质量下定义被称为(D)A.符合性质量 B.广义性质量 C.满意的质量 D.适用性质量5、下列论述中错误的是(B)。
供应商年度审核查检表
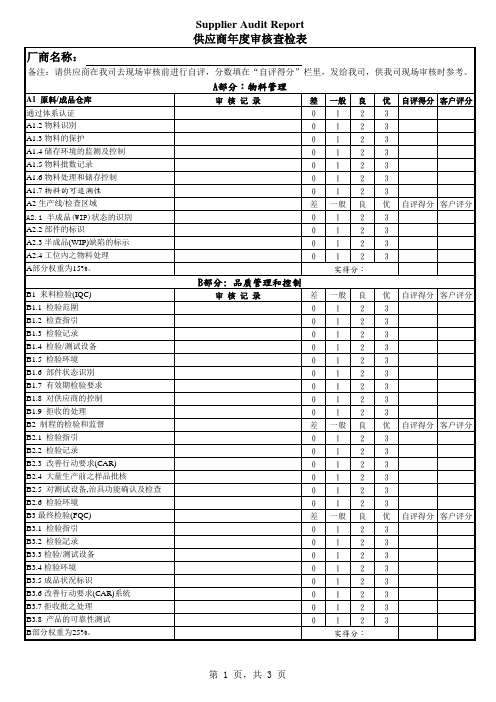
一般 良 12 12 12 12 12 12 实得分:
优 自评得分 客户评分 3 3 3 3 3 3 3 3 3 3 3 3
优 自评得分 客户评分 3 3
优 自评得分 客户评分 3 3 3 3 3 3
优 自评得分 客户评分 3 3 3 3 3
优 自评得分 客户评分 3 3 3 3 3 3
G1 员工有无环境保护的意识 G2 垃圾的有效分类 G3 废水的有效处理 G4 废气的有效处理 G5 废渣的有效处理 G6 ROHS要求的实现 G部分权重为5%
Supplier Audit Report 供应商年度审核查检表
C部分: 生产管理和控制
审核记录
差
0
0
0
0
0
0
0
0
0
0
0
0
D部分: 设计接收,检讨及发出
0123
B2.4 大量生产前之样品批核
0123
B2.5 对测试设备,治具功能确认及检查
0123
B2.6 检验环境
0123
B3 最终检验(FQC)
差 一般 良 优 自评得分 客户评分
B3.1 检验指引
0123
B3.2 检验記录
0123
B3.3 检验/测试设备
0123
B3.4 检验环境 B3.5 成品状況标识 B3.6 改善行动要求(CAR)系統 B3.7 拒收批之处理
0123 0123 0123 0123
B3.8 产品的可靠性测试
0123
B部分权重为25%。
实得分:
第 1 页,共 3 页
C1 工作岗位作业指引文件(指导书) C2 作业指导书之修改 C3 机器/治具的预防保养维修 C4 工作岗位要保留批核样品 C5 作业员,QC/IPQC设备操作 C6 生产流程效率 C7 制程/生产线上的缺陷部品处理 C8 物料标识 C9 车间整洁状況 C10 作业员对物料处理的态度(意识) C11 维修工序的有效性 C12 生产人员和品管人员的区別 C部分权重为30%.
品质部表格大全

品质部表格大全
目录
1送检单
2原材料不合格处理单
3进货检验报告
4品质异常处理单
5首件确认单(金工-装配)
6首件确认单(封装)
7巡检记录表
8成品送检单
9成品常规检验记录表
10出货检验报告
11样品检验记录单
12不合格品处置单
13不合格品统计表
14让步接收降级使用申报单
15不合格品审理人员资格确认表
16不合格(品)对策表
17不合格(品)因果分析表
18纠正与预防措施及实施验证报告
19品质部工作目标
20IQC合格率统计表
21产品老化抽检合格率统计表
22FQC检验一次合格率统计表
23质量整改 (FQC工位分析整改)
24维修工位不良统计表
25质量整改 (维修工位分析整改)
26包装工序输出电压检测合格率
27OQC抽检合格率统计表
28现场质量问题点
29客户投诉统计表
30质量整改
31在用计量器具管理总台帐
32在用计量器具领用登记表
33年度计量器具周期检定计划表
34计量器具降级、限用、报废申请单35检定、校准报告
36监视和测量设备验收单
37校验通知单
38测量设备校验申请单
39强制校验召回通知单
40设备标签。
一次性使用医用口罩IQC、IPQC、FQC及OQC检验规范

一次性使用医用口罩IQC、IPQC、FQC及OQC检验规范IQC进料检验规范1.目的和范围1.1目的规范一次性使用医用口罩的原材料进货检验操作,确保原材料符合规定要求,保证产品质量。
1.2范围适用于本公司一次性使用医用口罩产品的原材料进货检验。
2.工作程序2.1原材料进厂后应放原材料仓库待检区,由仓库填写请检单,送交质量部,质量部收到请检单后派员到现场进行检验或取样。
2.2质量部收集产品质量证明书。
3检验项目、要求、方法及抽样方案3.1熔喷布3.1.1外观质量3.1.2理化性能3.1.3徼生物3.2鼻夹3.3口罩带3.4包装袋IPQC过程检验1.目的规范一次性使用医用口罩产品生产过程中的检验项目、检验方法与检具、抽样方案及判定准则的要求,确保产品在生产过程中的质量要求。
2.范围适用于本公司一次性使用医用口罩生产过程检验。
3.检验项目、要求、检验方法、检验规则见下表FQC及OQC成品检验1.目的规范一次性使用医用口罩产品岀厂前检验项目、检验内容与要求、检验方法、抽样方案判定准则及检验记录的要求,桷保出厂成品符合注册标准要求。
2.范围适用于本公司一次性使用医用口罩成品出厂前检验。
3.检验依据3.1一次性使用医用口罩技术要求4.检测项目、质量要求、检验方法检测包括出厂检验和型式检验。
出厂检验项目项目:4.1外观、4.2结构与尺寸、4.3鼻夹、4.4口罩带、4.7微生物指标。
其中4.7为委托第三方检测项目,每批原材料送检一次。
型式检验应为产品标准的全性能检验。
4.1外观4.1.1口罩外观应整洁、形状完好,表面不得有破损、污渍。
4.1.2口罩的超声波复合应均匀、平直、牢固、无明显皱折。
4.1.3口罩超声波复合处粘合应牢固。
检验方法:随机抽取3个样品进行试验。
目视检查,结果应符合要求。
4.2结构与尺寸口罩佩戴好后,应能罩住佩戴者的口、鼻至下颌。
应符合表1的规定尺寸,最大偏差应不超过士5%表1口罩规格型号和基本尺寸单位:mm检验方法:随机抽取3个样品进行试验。
生产车间过程首检巡检记录表

N/A
1次/2H 目测
目测
一个流确认 装配现场是否按一个流作业,有无产品堆积现象
目测
不合格标识 不良品是否放置在不良品箱(盒)内,不良现象是否标识清楚
目测
NO 标准要求
换线管理 在换线前产线上物料是否清理干净,无物料遗留(含不良品)产线
新品状态确认
量(试)产品有无(临时)生产许可证;临时生产许可证上涉及的 问题点责任部门有无按时间节点完成
外观检查
PVC皮管上的批号正确,印字清晰(记录批次号) 面罩安装方向是否正确,无左右反装,上下反装现象
灯体内无杂物(橡胶碎屑、镀膜磨损物、灯壳飞边等)
检验频率
首检
巡检
检查
首检记录
巡检检查结果与判定
方式 检验结果及相关数据 判定 1.巡检 2.巡检 3.巡检 4.巡检
1件
3pcs/1次 /2H
塞尺
1件
用专用工装封闭灯头部位将灯浸入水中对灯内加压05mpa观看密封部位是否漏水外观整体性是否符合客户标准比对样品胶槽一周有无影响外观的溢胶必要时封样5成品检验外观检查pvc皮管上的批号正确印字清楚记录批次号面罩安装方向是否正确无左右反装上下反装现象灯体内无杂物橡胶碎屑镀膜磨损物灯壳飞边等1件3pcs1次2h1件气密验证1pcs调机气密机胶时气压源目测目测目测目测目测成品外观fqc089a0序号67检验频率项目检验类别主要检验要求及方法首检1件
涂胶重量 气密验证 成品外观
涂胶重量符合标准要求(记录在热熔胶喷涂重量管理表)
封闭式灯具:取标准样件(一只漏气,一只OK)检查气密机工作是否 正常 带漏水孔的灯具:用专用工装封闭灯头部位,将灯浸入水中,对灯 内加压0.5MPa,观察密封部位是否漏水
品质部各岗位绩效考核标准(QC主管、IQC、IPQC、FQC、OQC)

10
每月
管控范围内所产生的所有记录
4个月100%
5
2个月100%
2
100%
0
99.9%(含)-100%
-2
99.7%(含)-99.9%
-5
99.7%以下
-10
4
工作态度
QC是否能积极主动的配合完成上级分配的工作
品质经理工作完成状况汇总及各部门反应的工作配合情况
对指标说明中出现的情形进行次数累加注:1、对工作有责任心,敢于承担自己的责任2、工作积极,能积极主动的完成上级分配的任3、做人做事原则性强,能坚定自己的力场,敢于同违法违纪行为做不懈的斗争4、工作协调性强,能很好的协调好上级及同事间的关系和工作5、工作配合态度良好,能积极主动的配合各部门工作的完成
-10
600-1500PPM
-20
1500PPM以上
-25
3
制程返工率
注塑车间的返工率
注塑车间日报、月报汇总、品质部汇总(日报、周报、月报)信息
公式=注塑车间返工总数量/注塑车间生产总数量(注:注塑月返工数量=注塑生产过程中的数量+包装车间统计的因注塑过程所导致的返工数量;
0%
15
每月
所管控
车间
0.01-0.09
3个月无事故
5
每月
公司正常办公范围内
2个月无事故
2
1个月无事故
0
1起事故
-2
2起以上
-5
7
6S红旗发放和得分情况
6S现场稽核过程中发放的红旗面数和得分分数
6S推委会
对指标说明中出现的情形进行次数累加和稽查得分统计(注:发放红旗后,改善不力——两天内未改善,或同一区域被重复发放红旗,扣发分值按1.5倍扣分)
入库检验作业指导书
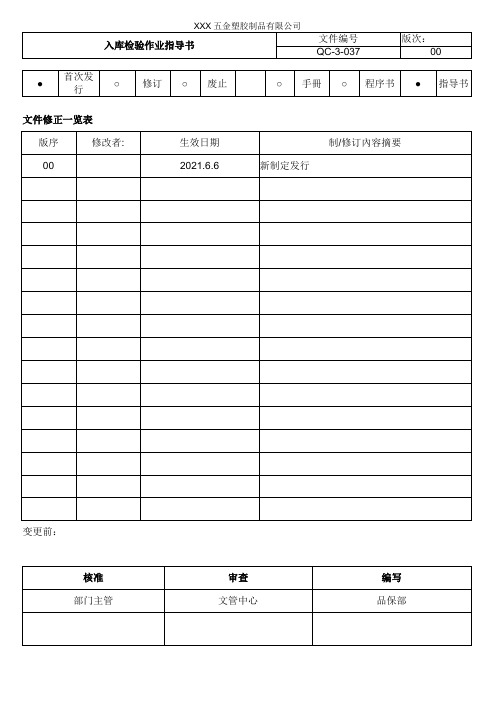
文件修正一览表变更前:1. 目的规范FQC入库检验作业行为。
2. 范围适用我司所有的入库检验作业。
3. 参考记录3.1 《生产派工单》3.2 《产品标签制作作业指导书》3.3 《品质异常反馈单》3.4 《留样标识卡》3.5 《组装PQC入库检验记录表》4.维护单位品保部5. 权责生产部:负责入库检验需求的提出品保部:负责待入库产品的检验及结果反馈6. 作业程序与说明6.1 检验时机:生产部将已生产完成的产品包装好后置于待检区,通知FQC进行入库前最终检验。
6.2 入库检验项目:6.3.1 依《生产派工单》核对实物与标签是否相符。
6.3.2 对重点尺寸进行5PCS检查,.此重点尺寸定义为1.带针脚类产品为外露脚长加总长,2.无针脚类产品为总长加总P距。
3.记录其中一个最大值,一个最小值。
6.3.3 依包装规范检验产线包装方式是否正确。
6.3.4 依包装明细检验包装数量是否正确。
6.3.5 依《产品标签制作作业指导书》检验内/外盒及尾数盒标签是否正确。
6.3.6 依AQL抽样计划对每批成品进行外观抽检。
6.3.7 每批产品的FQC至少检验尾数盒加一个整数盒的包装方式、包装数量和标签。
6.4 检验标识:如全部检验合格,FQC需在所有内盒标签上加盖PASS章。
并通知生产单位可以进行入库作业。
6.5 检验异常处理:6.5.2 FQC检验时如发现不良,整批产品全数退产线重工处理。
并开立《品质异常反馈单》,要求产线改善。
6.6 留样:6.5.1 成型FQC需要求成型技术员在生产完成后停机前将最后一模送FQC进行末件确认,如末件检验无误,成型FQC将整模穴样品作为末件留样,并填写完整《留样标识卡》留样保存。
6.5.2 组装FQC在对产品抽检无误后,需留取1PCS作为末件留样,并填写完整《留样标识卡》留样保存。
6.7 FQC将以上检验结果记录在《组装PQC入库检验记录表》上,并归档留存。
FQC检验作业规范
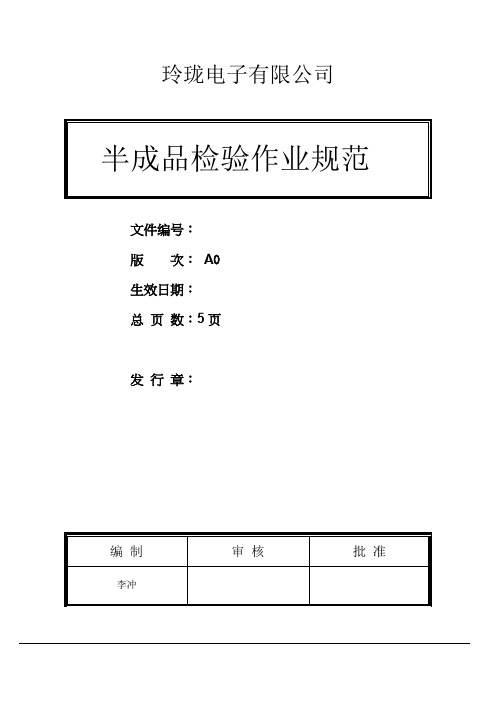
玲珑电子有限公司文件编号:版次:A0生效日期:总页数:5页发行章:履历表Document History1 目的标准化本公司内部生产作业规范,使涂布人员、品质人员有所依循,保证产品品质的稳定性。
2 范围适用于所有批量生产半成品的品质检验。
3 名词定义3.1 涂布INK 首件:同一生产参数,同一品名生产单位生产出来的第一卷产品。
3.2 涂布INK末件:同一生产参数,同一品名生产单位生产出来的最后一卷产品。
3.3 涂布INK批抽检:同一生产参数,同一品名从中依照频率进行抽检3.4 熟化批抽检件:同一生产参数,同一品名从中依照频率进行抽检。
4 权责4.1 制造部:负责半成品的取样以及自检。
送测时需在产品上标示清楚完整,然后填写《制程检验记录及登记表》一起放置无尘室入口处,通知品质部门检验。
取样时间要求自涂布收卷起2分钟内交接至品质部。
品质部:对取样产品检验,并将检验判定结果回复给制造部门。
5 程序5.1 油墨层INK首件、末件及批抽检检验项目:5.2 INK、熟化批抽检确认项目:5.3首/末件检验时机:5.3.1 首件检验时机:5.3.1.1生产单位生产出来的第一个产品产品时;5.3.1.2作业人员交接班时5.3.1.3量产品更换规格时;5.3.1.4主设备停机达4H以上或维修后重新开机需时5.3.1.5作业方法变更时5.3.1.6设备治工具变更时(模具维修)5.3.1.7生产条件变更时(机台调查)5.3.1.8新机种导入时5.3.1.9生产环境发生变更时5.3.2末件检验时机:5.3.2.1生产单位生产的最后一个产品时;5.3.3取样量:首末件每卷0.5m5.3.4允收标准:0收1退。
5.4首件不合格不可批量生产,末件不合格需追溯批量品的前三批5.5 量产抽检时机:5.5.1 首件各项检验合格达到批量抽检时5.6抽样(巡检)频率:依抽样计划作业规范5.7 取样量:每卷0.5m5.8外观:依抽样计划作业规范中的量产抽样(巡检)检验计划,判定标准依照INK外观检验标准。
食品企业IQC FQC IPQC
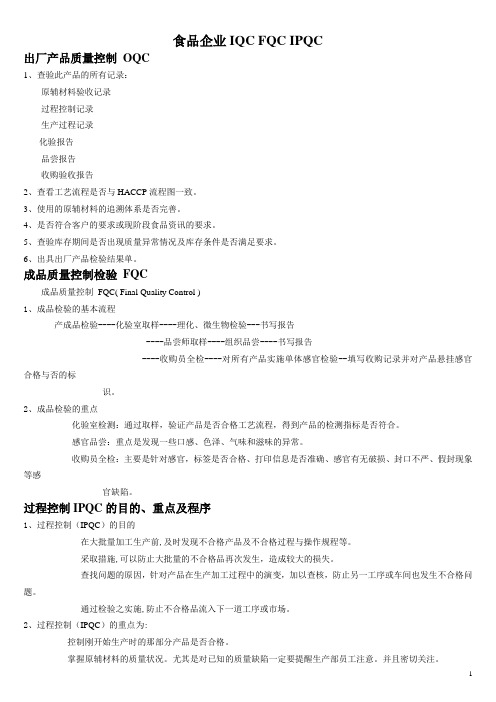
食品企业IQC FQC IPQC出厂产品质量控制OQC1、查验此产品的所有记录:原辅材料验收记录过程控制记录生产过程记录化验报告品尝报告收购验收报告2、查看工艺流程是否与HACCP流程图一致。
3、使用的原辅材料的追溯体系是否完善。
4、是否符合客户的要求或现阶段食品资讯的要求。
5、查验库存期间是否出现质量异常情况及库存条件是否满足要求。
6、出具出厂产品检验结果单。
成品质量控制检验FQC成品质量控制FQC( Final Quality Control )1、成品检验的基本流程产成品检验----化验室取样----理化、微生物检验---书写报告----品尝师取样----组织品尝----书写报告----收购员全检----对所有产品实施单体感官检验--填写收购记录并对产品悬挂感官合格与否的标识。
2、成品检验的重点化验室检测:通过取样,验证产品是否合格工艺流程,得到产品的检测指标是否符合。
感官品尝:重点是发现一些口感、色泽、气味和滋味的异常。
收购员全检:主要是针对感官,标签是否合格、打印信息是否准确、感官有无破损、封口不严、假封现象等感官缺陷。
过程控制IPQC的目的、重点及程序1、过程控制(IPQC)的目的在大批量加工生产前,及时发现不合格产品及不合格过程与操作规程等。
采取措施,可以防止大批量的不合格品再次发生,造成较大的损失。
查找问题的原因,针对产品在生产加工过程中的演变,加以查核,防止另一工序或车间也发生不合格问题。
通过检验之实施,防止不合格品流入下一道工序或市场。
2、过程控制(IPQC)的重点为:控制刚开始生产时的那部分产品是否合格。
掌握原辅材料的质量状况。
尤其是对已知的质量缺陷一定要提醒生产部员工注意。
并且密切关注。
以前不合格现象和原因的分析产品一定要密切关注。
新产品的投入生产。
新操作员、设备等作业条件变动关键工序、关键控制点CCP、质量关键控制点QCP的控制不稳定的工具、机器(含模具、夹具).发生变化的环境。
FQC检验规范

FQC检验规范流程1. 最终检验程序(FQC)1.1 目的:对产品出厂前检验/试验,确保产品质量满足客户要求。
1.2范围:产品检验和试验。
1.3责任:除已指定之外,品质主管负责以下程序中的所有运作。
1.4最终检验流程图:(见下页)1.5最终检验员(FQC)须具备资格条件:1.5.1 高中、中专或以上文化程度;1.5.2 熟悉产品装配工艺及客户品质要求;1.5.3 受过3C及有关成品检验培训并考核合格。
1.6 FQC职责和权限:1.6.1 按《FQC检验规范流程》对成品进行检验;1.6.2 记录和保存检验数据;1.6.3 对检验过程中发生批量性品质问题,按《不合格品评审程序》处理;1.6.4 对质量记录做统计分析,用以指导生产,稳定和提高产品质量;1.6.5 受理客户投诉,调查不合格原因,跟踪纠正和预防措施,及时答复客户改善情况。
1.7 FQC运作程序:1.7.1 FQC检验员按《作业指导书》对产品进行检验;1.7.2 FQC员每2小时对生产线上的材料、工位操作及治具确认一次,并填写《2小时生产部品确认表》,由品质主管审核;1.7.3 FQC按客户品质要求对产品进行抽样检验:对符合要求的产品,填写《FQC报告》并在现品票上贴上“合格”标签,标明机种、检验日期及检验员签名;1.7.4 FQC抽样不良缺陷超过客户要求AQL标准,即产品质量不符合客户要求时,填写《FQC报告》并在每栈板的现品票上贴上“不合格”标签,标明机种、不良原因、不良数量、检验日期及检验员签名,同时填写《重流通知单》,写明不良原因及数量,经品质主管审核后,并经公司领导确认后,发给生产;1.7.5 制造接到《重流通知单》后,安排时间重流,PQC重点对不良项目进行全检,检验结果记录在《重流通知单》上;1.7.6 FQC对重流过的成品重新进行抽检,合格后进仓;如重流二次均不符客户要求,则应组织有关人员进行评审,执行《不合格批评审程序》;1.7.7 FQC巡拉发现生产线员工违反《作业指导书》操作或引起品质异常时,必须通知生产部,要求制生产主管即时纠正员工操作,同时发出《纠正行动通知单》给制造,限其在8小时内将问题的原因及改善措施书面回复FQC,FQC不定期跟踪问题改善情况并将跟进结果记录于《品质问题跟踪表》中;1.7.8 在仓库存货交货前,仓库成品管理员应核查成品储存期,如超期,应书面通知FQC,FQC检验员将采取以下行动。