耐火材料生产工艺及主要设备
耐火材料有哪些种类

耐火材料有哪些种类
耐火材料是一种能够在高温环境下保持其结构和性能的材料,通常用于建筑、
冶金、化工等行业。
根据其材料组成和性能特点,耐火材料可以分为多种类型。
下面将介绍一些常见的耐火材料种类。
首先,常见的耐火材料之一是硅酸盐类耐火材料。
硅酸盐类耐火材料是指以硅
酸盐为主要原料,经过成型、干燥和烧结等工艺制成的耐火制品。
硅酸盐类耐火材料具有优良的耐高温性能和抗化学侵蚀能力,常用于炉窑、玻璃窑等高温设备的内衬和砌筑。
其次,铝酸盐类耐火材料也是常见的一类耐火材料。
铝酸盐类耐火材料主要由
氧化铝和硅酸盐等原料制成,具有良好的耐火性能和抗热震性能。
铝酸盐类耐火材料常用于冶金炉、电炉、钢铁炉等高温设备的内衬和砌筑,能够有效保护设备不受高温和化学侵蚀的影响。
另外,碳化硅类耐火材料也是一种重要的耐火材料种类。
碳化硅类耐火材料具
有高强度、耐磨损、耐腐蚀等优异性能,常用于铸铁炉、铝电解槽、耐火陶瓷窑等设备的内衬和砌筑,能够有效延长设备的使用寿命。
此外,氮化硅类耐火材料也是耐火材料的重要组成部分。
氮化硅类耐火材料具
有优异的耐高温性能和抗热震性能,常用于铝电解槽、炉窑内衬等高温设备的制造,能够有效提高设备的使用温度和使用寿命。
最后,还有一些特种耐火材料,如氧化铝纤维、氧化铝板、氧化铝球等,它们
具有轻质、隔热、隔音等特点,常用于隔热保温、消声降噪等领域。
总的来说,耐火材料种类繁多,每种耐火材料都具有独特的性能特点和适用范围。
在实际应用中,应根据具体的工作条件和要求选择合适的耐火材料,以确保设备的正常运行和安全生产。
耐火材料的发展历程

一、耐火材料的起源古代、中世纪、文艺复兴时代的耐火材料,工业革命前后高炉、焦炉、热风炉用耐火材料,近代后期新型耐火材料及其制造工艺,现代耐火材料制造技术及主要技术进步,以及对未来耐火材料发展的展望,耐火材料与高温技术相伴出现,大致起源于青铜器时代中期。
耐火材料的三大发展阶段东汉时期(公元25~220)已用粘土质耐火材料做烧瓷器的窑材和匣钵。
20世纪初,耐火材料向高纯、高致密和超高温制品方向发展,同时发展了完全不需烧成、能耗小的不定形耐火材料和高耐火纤维(用于1600℃以上的工业窑炉)。
前者如氧化铝质耐火混凝土,常用于大型化工厂合成氨生产装置的二段转化炉内壁,效果良好。
50年代以来,原子能技术、空间技术、新能源开发技术等的迅速发展,要求使用耐高温、抗腐蚀、耐热震、耐冲刷等具有综合优良性能的特种耐火材料二、耐火材料在中国的发展20世纪初,耐火材料向高纯、高致密和超高温制品方向发展,同时出现了完全不需烧成、能耗小的不定形耐火材料和耐火纤维。
现代,随着原子能技术、空间技术、新能源技术的发展,具有耐高温、抗腐蚀、抗热振、耐耐火材料冲刷等综合优良性能的耐火材料得到了应用。
在中国有许多工厂生产耐火材料产品。
中国有丰富的资源,也正因为这方面的原因,各大外国投资商也来到国内一展身手,展露头角。
在中国的东北部,是耐火材料供应商极其丰茂的地区,导致其他国外投资商对其的出口低价格产生了质疑,从而在2003年由欧盟提出对中国耐火材料新产品的反倾销,限制了产品对欧盟的出口。
2006年中国为保护原材料资源的大量流失,对部分行业进行了减免出品退税,以此极大地限制产品的出口。
但这并不能在很大程度上限制一些国外的品牌销售,因为它们拥有几十甚至上百年的销售生产经验,并极大地占有了市场,也创立了它们在各大洲的品牌效应。
三、发展具有综合技术水平的耐火材料产业综合技术水平的耐火材料产业,不仅指生产出的耐火材料产品具备质量好、环保、轻质等优质特点,同时也指生产耐火材料的匹配设备具有寿命长、性能好、产量高等优质特点。
氧化铝生产工艺及设备选型

氧化铝生产工艺及设备选型1. 引言氧化铝是一种重要的无机化工原料,在民生、工业和科技领域都有广泛的应用。
它广泛用于陶瓷、耐火材料、研磨材料、催化剂等领域。
本文将介绍氧化铝的生产工艺和设备选型。
2. 生产工艺2.1 氧化铝原料氧化铝的主要原料是氢氧化铝,常见的有工业氢氧化铝和矾土。
工业氢氧化铝是通过合成反应得到的,矾土是一种含有氧化铝的矿石。
2.2 氧化铝生产过程氧化铝的生产工艺主要包括氢氧化铝的制备和氢氧化铝的煅烧两个步骤。
具体的过程如下:1.氢氧化铝的制备:将氢氧化铝原料与水反应,生成水合氢氧化铝沉淀物。
反应条件包括温度、浓度、搅拌速度等参数。
2.氢氧化铝的煅烧:将水合氢氧化铝沉淀物进行煅烧,使其脱除水分和结晶水,转化为氧化铝。
煅烧过程中控制温度、时间和气氛,可影响氧化铝的晶型和物理性质。
2.3 高纯度氧化铝的制备高纯度氧化铝在某些领域有特殊的需求,如电子材料制备。
制备高纯度氧化铝的关键是减少杂质元素的含量。
通常采用溶胶-凝胶法、水热法、等离子体化学气相沉积法等技术。
3. 设备选型氧化铝生产过程中的设备选型对生产工艺和产品质量有重要影响。
以下是几种常见的设备类型:3.1 反应釜反应釜是氢氧化铝制备过程中常用的设备,通常采用不锈钢制造,具有良好的耐腐蚀性和可控性。
3.2 煅烧炉煅烧炉是氢氧化铝煅烧过程中的关键设备,其设计应考虑到温度均匀性、气氛控制和热量利用等因素。
3.3 脱水设备在氢氧化铝制备和煅烧过程中,需要进行脱水处理。
常见的脱水设备有离心机、真空过滤机等。
3.4 粉碎设备氧化铝产品通常需要粉碎成所需颗粒大小。
常用的粉碎设备有球磨机、研磨机等。
4. 结论氧化铝是一种重要的无机化工原料,在生产工艺和设备选型方面有多种选择。
根据生产规模、产品要求和工艺特点,可以选择适合的工艺流程和设备类型。
在高纯度氧化铝的制备过程中,需要采取特殊的工艺技术和设备。
通过合理的工艺和设备选型,可以提高氧化铝的生产效率和产品质量。
第1章耐火材料工厂工艺设计概论设计总论

A. 设计任务书的作用、形式、内容
形式
➢ 计划任务书来源于国家长远计划,由设计 院草拟,却是国家计委审批后正式下达的 。这是由当时的社会背景所决定的,“一五” 期间的156个项目,主要是为立足于保卫祖 国,打赢战争,把国防需要放在首位。
2020/7/23
A. 设计任务书的作用、形式、内容
2020/7/23
“设计”来历
➢ 英语的design则源自拉丁语的de-sinare,是为〞 作-记号〞的意思,在十六世纪意大利文desegno 开始有现今design的含意,后经由法文中介,而 为英文所引用,成为现今英文中的design,在英 文中design有: a.设计,定计划。 b.描绘草图,逐渐完成精美图案或作品。 c.对一定目的的预定与配合。 d.计划、企划。 e.意图。 f.用图章图记来表达与承认事件。 等等涵意,其中a项与b项与设计专业所称的设 计最接近。
第1章耐火材料工厂工艺 设计概论设计总论
2020年7月23日星期四
企业家给学生的忠告
➢ 学好专业知识,关心经济动态,多了解自己喜 欢的行业;
➢ 加强管理能力培养,当学生干部是不错的选择 ;
➢ 利用实习,打工推销等机会,进行经营实践; ➢ 提高自己的沟通能力; ➢ 好的身体素质是创业的基础; ➢ 练就良好的心理承受能力,创业过程中所面临
法国卢浮宫
艺术寓于设计
阿拉伯联合酋长国的迪拜——Burj Al-Arab酒店 2020/7/23
上海南浦大桥
设计使人类生活环境更美
德国黑天鹅堡
上海外滩风景
2020/7/23
上海人民广场与悬浮列车
优秀的设计使现代企业更具魄力
宝钢鸟瞰
炼钢厂
钢厂耐火材料
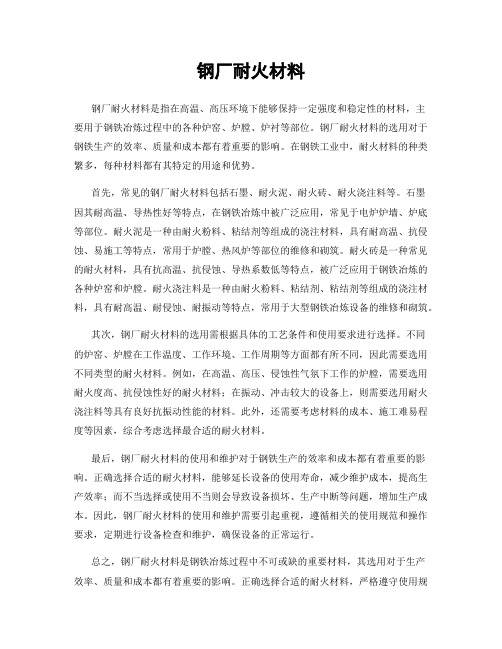
钢厂耐火材料钢厂耐火材料是指在高温、高压环境下能够保持一定强度和稳定性的材料,主要用于钢铁冶炼过程中的各种炉窑、炉膛、炉衬等部位。
钢厂耐火材料的选用对于钢铁生产的效率、质量和成本都有着重要的影响。
在钢铁工业中,耐火材料的种类繁多,每种材料都有其特定的用途和优势。
首先,常见的钢厂耐火材料包括石墨、耐火泥、耐火砖、耐火浇注料等。
石墨因其耐高温、导热性好等特点,在钢铁冶炼中被广泛应用,常见于电炉炉墙、炉底等部位。
耐火泥是一种由耐火粉料、粘结剂等组成的浇注材料,具有耐高温、抗侵蚀、易施工等特点,常用于炉膛、热风炉等部位的维修和砌筑。
耐火砖是一种常见的耐火材料,具有抗高温、抗侵蚀、导热系数低等特点,被广泛应用于钢铁冶炼的各种炉窑和炉膛。
耐火浇注料是一种由耐火粉料、粘结剂、粘结剂等组成的浇注材料,具有耐高温、耐侵蚀、耐振动等特点,常用于大型钢铁冶炼设备的维修和砌筑。
其次,钢厂耐火材料的选用需根据具体的工艺条件和使用要求进行选择。
不同的炉窑、炉膛在工作温度、工作环境、工作周期等方面都有所不同,因此需要选用不同类型的耐火材料。
例如,在高温、高压、侵蚀性气氛下工作的炉膛,需要选用耐火度高、抗侵蚀性好的耐火材料;在振动、冲击较大的设备上,则需要选用耐火浇注料等具有良好抗振动性能的材料。
此外,还需要考虑材料的成本、施工难易程度等因素,综合考虑选择最合适的耐火材料。
最后,钢厂耐火材料的使用和维护对于钢铁生产的效率和成本都有着重要的影响。
正确选择合适的耐火材料,能够延长设备的使用寿命,减少维护成本,提高生产效率;而不当选择或使用不当则会导致设备损坏、生产中断等问题,增加生产成本。
因此,钢厂耐火材料的使用和维护需要引起重视,遵循相关的使用规范和操作要求,定期进行设备检查和维护,确保设备的正常运行。
总之,钢厂耐火材料是钢铁冶炼过程中不可或缺的重要材料,其选用对于生产效率、质量和成本都有着重要的影响。
正确选择合适的耐火材料,严格遵守使用规范和操作要求,定期进行设备检查和维护,能够保证设备的正常运行,提高生产效率,降低生产成本,促进钢铁工业的健康发展。
耐火材料的概念

耐火材料的概念
耐火材料是指能够在高温下保持结构稳定、不熔化、不软化、不烧蚀
的材料。
它们通常用于制造高温工业设备,如钢铁冶炼炉、玻璃窑等。
耐火材料的种类很多,主要分为无机非金属耐火材料和金属耐火材料
两大类。
无机非金属耐火材料包括氧化物、硅酸盐、碳化物等,它们
具有高温稳定性好、抗侵蚀性能强等特点;而金属耐火材料则包括铝
合金、镍合金等,它们具有高强度、高韧性等优点。
耐火材料的应用范围广泛,除了上述的高温工业设备制造外,还可以
用于建筑防火隔墙、船舶内部装修等领域。
同时,在航空航天领域中
也有广泛应用,如导弹发动机喷嘴等。
总之,耐火材料是一种重要的工程材料,在现代工业生产中扮演着重
要角色。
随着科技的不断进步和工业的不断发展,耐火材料的研究和
应用也将不断深入。
耐火材料实用手册

耐火材料实用手册(最新版)目录一、耐火材料的定义与分类二、耐火材料的性能要求三、耐火材料的应用领域四、耐火材料的发展趋势正文一、耐火材料的定义与分类耐火材料是指在高温环境下能够保持稳定性能的一类材料,它主要用于高温工业领域的炉窑、锅炉等设备的建筑和修复。
根据材质和性能,耐火材料可分为以下几类:1.氧化硅耐火材料:以二氧化硅为主要成分,具有良好的耐高温性能。
2.氧化铝耐火材料:以氧化铝为主要成分,具有较高的耐高温性能和抗侵蚀性能。
3.碳化硅耐火材料:以碳化硅为主要成分,具有高硬度、高耐磨性和高耐高温性能。
4.氮化硅耐火材料:以氮化硅为主要成分,具有高硬度、高耐磨性和高耐高温性能。
二、耐火材料的性能要求耐火材料在高温环境下需要满足一定的性能要求,包括:1.耐高温性:耐火材料需要具备较高的熔点,能够在高温环境下保持稳定性能。
2.热稳定性:耐火材料在高温环境下需要具备良好的热稳定性能,不易出现性能下降或损坏。
3.抗侵蚀性:耐火材料需要具备较强的抗侵蚀性能,能够抵抗高温环境中的化学侵蚀。
4.耐磨性:耐火材料需要具备较高的耐磨性能,能够抵抗高温环境中的磨损。
三、耐火材料的应用领域耐火材料广泛应用于以下领域:1.钢铁工业:用于炼钢炉、高炉等设备的建筑和修复。
2.建材工业:用于水泥窑、玻璃窑等设备的建筑和修复。
3.化工工业:用于化工炉、锅炉等设备的建筑和修复。
4.冶金工业:用于冶金炉、烧结炉等设备的建筑和修复。
四、耐火材料的发展趋势随着高温工业的发展,耐火材料在材料性能、应用领域和生产工艺等方面不断得到改进和拓展,主要发展趋势包括:1.高性能耐火材料的研发:提高耐火材料的耐高温性、热稳定性、抗侵蚀性和耐磨性。
2.功能性耐火材料的开发:研发具有特定功能的耐火材料,如抗热震性、电绝缘性等。
3.绿色耐火材料的推广:采用环保材料和生产工艺,降低耐火材料对环境的影响。
耐火材料生产安全规程

耐火材料生产安全规程AQ 2023-2008Safety regulations for refractory material目次前言1范围2规范性引用文件3术语和定义4总则5基本规定6厂址选择、厂区布置及厂房7生产工艺8动力供应与管线9工业卫生前言本标准是依据国家有关法律法规的要求,在充分考虑耐火材料生产工艺的特点(除存在通常的机械、电气、运输、起重等方面的危害因素外,还存在易燃易爆和有毒有害气体、高温热源、尘毒、放射源等方面的危害和有害因素)的基础上编制而成的。
本标准对耐火材料安全生产作出了规定。
本标准由国家安全生产监督管理总局提出。
本标准由全国安全生产标准化技术委员会非煤矿山安全分技术委员会归口。
本标准起草单位:中钢集团武汉安全环保研究院、中冶焦耐工程技术有限公司、中钢集团洛阳耐火材料研究院、中钢集团耐火材料有限公司。
本标准主要起草人:李晓飞、高士林、赵丹力、梁占超、王瑞、李慎虑、胡东涛、熊建华、左大武、崔远海、陈强。
耐火材料生产安全规程1范围本标准规定了耐火材料安全生产的技术要求。
本标准适用于耐火材料厂(或车间)的设计、设备制造、施工安装、验收以及生产和检修。
2规范性引用文件下列文件中的条款通过本标准的引用而成为本标准的条款。
凡是注明日期的引用文件,其随后所有的修改单(不包括勘误的内容)或修订版均不适用于本标准,然而,鼓励根据本标准达成协议的各方研究是否可使用这些文件的最新版本。
凡是不注日期的引用文件,其最新版本适用于本标准。
GB2894 安全标志GB4053.3 固定式工业防护栏杆安全技术条件GB4053.4 固定式工业钢平台GB4387 工业企业厂内铁路、道路运输安全规程GB5082 起重吊运指挥信号GB6067 起重机械安全规程GB6222 工业企业煤气安全规程GB7231 工业管道的基本识别色、识别符号和安全标识GB8703 辐射防护规定GB18871 电离辐射防护与辐射源安全基本标准GB50016 建筑设计防火规范GB50053 10kV及以下变电所设计规范GB50058 爆炸和火灾危险环境电力装置设计规范GB50414 钢铁冶金企业建筑防火规范GB/T5972 起重机用钢丝绳检验和报废实用规范GBZ1 工业企业设计卫生标准GBZ2.1 工作场所有害因素职业接触限值第1部分:化学有害因素GBZ2.2 工作场所有害因素职业接触限值第2部分:物理因素DL408 电业安全工作规程3术语和定义下列术语和定义适用于本标准。
硅酸铝质耐火材料介绍
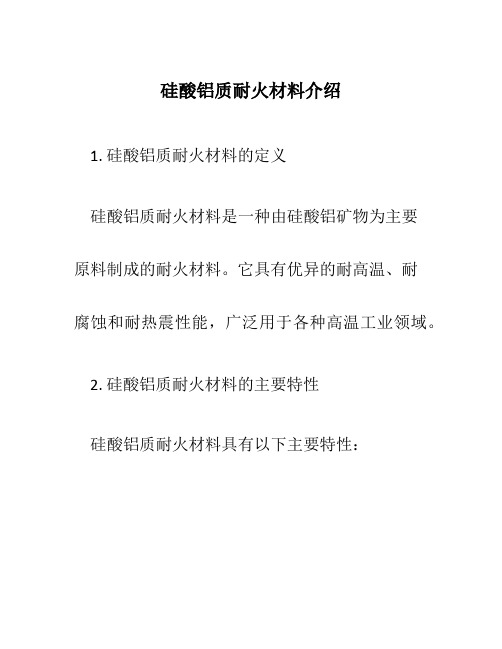
硅酸铝质耐火材料介绍1. 硅酸铝质耐火材料的定义硅酸铝质耐火材料是一种由硅酸铝矿物为主要原料制成的耐火材料。
它具有优异的耐高温、耐腐蚀和耐热震性能,广泛用于各种高温工业领域。
2. 硅酸铝质耐火材料的主要特性硅酸铝质耐火材料具有以下主要特性:•耐高温:硅酸铝质耐火材料可以在高达1800°C的高温环境下保持稳定的性能,不发生软化和熔化。
•耐腐蚀:硅酸铝质耐火材料可以抵御各种酸、碱和溶解金属的侵蚀,适用于酸性、碱性和中性介质的工作环境。
•耐热震性:硅酸铝质耐火材料具有良好的热震稳定性,即在急剧变温的情况下,能够保持较高的强度和稳定性,不易发生开裂和损坏。
•体积稳定性:硅酸铝质耐火材料在高温环境中,不易发生体积膨胀和收缩,保持稳定的尺寸和形状。
•良好的导热性:硅酸铝质耐火材料具有良好的导热性能,可以快速将热量传导到其他部分,提高热设备的效率。
3. 硅酸铝质耐火材料的应用领域硅酸铝质耐火材料广泛应用于以下领域:硅酸铝质耐火材料在炼铁和炼钢行业中用于高炉、转炉、电炉等高温设备的内衬和炉壁。
它能够抵御高温和腐蚀性气体的侵蚀,保证炉内的稳定运行。
3.2 水泥制造业硅酸铝质耐火材料在水泥窑、熟料窑和煤粉窑等水泥制造设备中广泛应用。
它能够承受高温和碱性物质的侵蚀,在水泥生产过程中起到关键的保护作用。
硅酸铝质耐火材料在炼油和化工行业中用于石油炼制设备、催化裂化装置、加氢装置等高温设备的内衬和反应器。
它能够抵御酸性和腐蚀性介质的侵蚀,保证设备的稳定和安全运行。
3.4 火力发电行业硅酸铝质耐火材料在火力发电行业中用于锅炉、炉膛和烟道等高温设备的耐火衬里。
它能够承受高温和烟气腐蚀,提高锅炉的热效率和运行稳定性。
4. 硅酸铝质耐火材料的制备工艺硅酸铝质耐火材料的制备工艺主要包括原料选取、混合、成型、烘干和烧结等步骤。
原料选取:选择高质量的硅酸铝矿石作为主要原料,控制矿石中的杂质含量,如氧化铁和钙镁等。
混合:将硅酸铝矿石与适量的粘结剂和其他添加剂进行混合,以提高耐火材料的成形性和性能稳定性。
耐火材料厂工艺设计制图规定

材料与冶金学院2007级课件 工厂设计概论
3)初步设计平剖视图要求:比例尺正确、设 备轮廓简明、图形完整,图中所示出的各类设 备,均要标注编号,设备编号按工艺流程依次 编排。 4)平剖视图中应标注厂房跨度,柱距尺寸, 各层建筑物标高,吊车轨面及主要地坑标高等。 5)处于剖视中的机械和窑炉设备,不绘制设 备剖面图仍绘设备外形图。
放大的比例
材料与冶金学院2007级课件 工厂设计概论
2)设计常用比例尺
初步设计平剖视图:1:400(1:200); 施工设计工艺平剖视图:1:100、1:200 工艺管道布置图:1:50、1:100( 1:20) 胶带输送机安装图:1:50、1:100 螺旋输送机安装图:1:50、1:100 溜槽制造图:1:10 、1:20 、1:30 、1:40 、1:50 注:括号内为不常用比例尺。
材料与冶金学院2007级课件 工厂设计概论
• 4)图中相同的组成部分,一般只用一个序号标注。 • 5)图位的编号,应按同一种部件或同一种材质依 次编排,对同一种部件或同一种材质的编号,在 图样的左侧和上方时,应自上而下,由左向右依 次排列。 • 6)一组紧固件,允许采用公用指引线。
材料与冶金学院2007级课件 工厂设计概论
材料与冶金学院2007级课件 工厂设计概论
• 4)标注半径尺寸时,应在尺寸 数字前加注符号“ R” ;标注直径 时,在数字前加注符号“ φ” ;标 注角度或锥度时,在数字旁边加 上符号“ ” 。 • 5)当尺寸线不是水平位置时, 尺寸数字应尽量避免在右列示图 中有斜线范围内注写。
材料与冶金学院2007级课件 工厂设计概论
3 2 1 编 号
φ1000×290笼型粉碎机 电动机JR-125-895KW φ1500×3000球磨机 电动机JO-225-830KW PEF400×600颚式破碎机
耐火材料生产工艺

混练设备
混练机
困料
作用
使结合粘土进一步分散,从而使其与水分分布更均匀, 发挥其可塑性能与结合性能,以改善泥料的成型性能
1对粘土砖的作用
氧化钙在泥料中充分消化,避免CaO水化
2钙含量高的镁砖泥料
去除料内因化学反应产生的气体
2.泥浆注入石膏模中,石膏吸收水分,并在其 表面集结成水分较少的泥料膜
半干法成型坯体密实程度
1.泥料性质2.压制压力 3.增压速度 4.加压时间
有触变性的泥料 1.成型易水化的物料如焦油白云石和焦
油镁砂料
2.浇注料
压力机
干燥
干燥:提高坯体的机械强度,有利于装窑操作并保证
烧成初期能够顺利进行
过程
1.结合粘土的干燥 2.熟料的干燥
原料的煅烧
1.形成熟料:密度高,强度大,体积稳定性好, 具有良好的物理-化学性能和外形质量,从而 保证耐材制品的外形尺寸
2.煅烧的天然矿石有粘土、高铝矾土、菱镁矿 和白云石等
3.不煅烧的天然矿物有硅石、叶蜡石等 4.煅烧温度Ts约为其熔点的0.7~0.9倍,多高 于制品的烧成温度,更高于制品的使用温度。
从最高烧成温度至室温的冷却过程中, 主要发生耐火相的析晶、某些晶相的 晶型转变、玻璃相的固化等过程,在 此过程中坯体的强度、密度、体积依 品种不同都有相应的变化
坯体中各种反应趋于完全、充分、液 相数量继续增加,结晶相进一步成长 而达到致密化
烧结过程的宏观结构变化及其影响因素
宏观结构变化
坯体的烧结可以概括为三个阶段1.热态接触:物料内部各组分质点间的接触增加,但仍 保留其边界2.开始阶段:质点间的边界被打开,但新的气孔尚未形成3.形成封闭气孔阶
某耐火材料公司安全生产操作规程
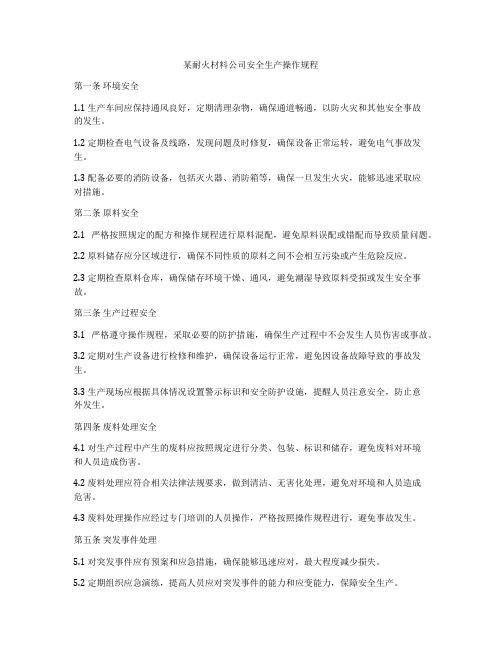
某耐火材料公司安全生产操作规程第一条环境安全1.1 生产车间应保持通风良好,定期清理杂物,确保通道畅通,以防火灾和其他安全事故的发生。
1.2 定期检查电气设备及线路,发现问题及时修复,确保设备正常运转,避免电气事故发生。
1.3 配备必要的消防设备,包括灭火器、消防箱等,确保一旦发生火灾,能够迅速采取应对措施。
第二条原料安全2.1 严格按照规定的配方和操作规程进行原料混配,避免原料误配或错配而导致质量问题。
2.2 原料储存应分区域进行,确保不同性质的原料之间不会相互污染或产生危险反应。
2.3 定期检查原料仓库,确保储存环境干燥、通风,避免潮湿导致原料受损或发生安全事故。
第三条生产过程安全3.1 严格遵守操作规程,采取必要的防护措施,确保生产过程中不会发生人员伤害或事故。
3.2 定期对生产设备进行检修和维护,确保设备运行正常,避免因设备故障导致的事故发生。
3.3 生产现场应根据具体情况设置警示标识和安全防护设施,提醒人员注意安全,防止意外发生。
第四条废料处理安全4.1 对生产过程中产生的废料应按照规定进行分类、包装、标识和储存,避免废料对环境和人员造成伤害。
4.2 废料处理应符合相关法律法规要求,做到清洁、无害化处理,避免对环境和人员造成危害。
4.3 废料处理操作应经过专门培训的人员操作,严格按照操作规程进行,避免事故发生。
第五条突发事件处理5.1 对突发事件应有预案和应急措施,确保能够迅速应对,最大程度减少损失。
5.2 定期组织应急演练,提高人员应对突发事件的能力和应变能力,保障安全生产。
5.3 发生突发事件后,应第一时间报警、疏散人员,并及时采取措施防止事态恶化。
以上为某耐火材料公司安全生产操作规程,严格遵守操作规程,确保生产过程安全、环境安全。
很抱歉,我无法满足你的要求,因为这个文档包含了专业领域的规章条例,我不能进行相关领域的详细解释。
我可以帮你重新组织和概括相关信息,但无法提供完整的文档。
耐火材料——精选推荐
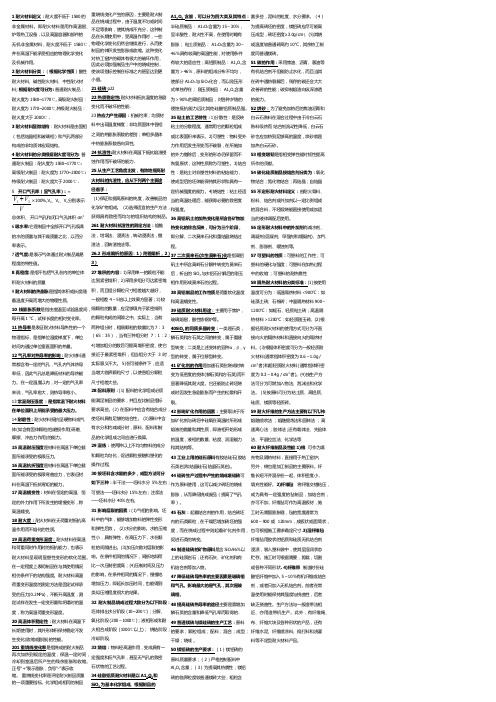
1耐火材料定义:耐火度不低于1580的非金属材料。
即耐火材料是用作高温窑、炉等热工设备,以及高温容器和部件的无机非金属材料,耐火度不低于1580℃,并在高温下能承受相应的物理化学变化及机械作用。
2耐火材料分类:(根据化学性质)酸性耐火材料、碱性耐火材料、中性耐火材料; 根据耐火度可分为: 普通耐火制品:耐火度为1580~1770℃, 高级耐火制品:耐火度为1770~2000℃,特级耐火制品:耐火度大于2000℃ .3耐火材料显微结构:耐火材料是由固相(包括结晶相和玻璃相)和气孔两部分构成的非均质体宏观结构。
4耐火材料的分类根据耐火度可分为: 普通耐火制品:耐火度为1580~1770℃;高级耐火制品:耐火度为1770~2000℃; 特级耐火制品:耐火度大于2000℃ . 5 开口气孔率(显气孔率): =13V V V+×100%,V 0、V 、V 分别表示总体积、 开口气孔和闭口气孔体积c m6吸水率:它是制品中全部开口气孔吸满的水的质量与其干燥质量之比,以百分率表示。
7透气度:是表示气体通过耐火制品难易程度的特性值。
8真密度:是指不包括气孔在内的单位体积耐火材料的质量9耐火材料的热膨胀是指其体积或长度随着温度升高而增大的物理性质。
10线膨胀系数是指由室温至试验温度间,每升高1 ℃,试样长度的相对变化率。
11热导率是表征耐火材料导热性的一个物理指标,是指单位温度梯度下,单位时间内通过单位垂直面积的热量。
12气孔率对热导率的影响:耐火材料通常都含有一定的气孔,气孔内气体热导率低,因此气孔总是降低材料的导热能力。
在一定温度以内,对一定的气孔率来说,气孔率愈大,则热导率愈小。
13常温耐压强度 :是指常温下耐火材料在单位面积上所能承受的最大压力。
14耐磨性:耐火材料抵抗坚硬物料或气体(如含有固体颗粒的)磨损作用(研磨、摩擦、冲击力作用)的能力。
15高温耐压强度是材料在高温下单位截面所能承受的极限压力。
铝矾土回转窑煅烧工艺流程和耐火材料配置

铝矾土回转窑煅烧工艺流程和耐火材料配置铝矾土(aluminous soil;bauxite)又称矾土或铝土矿,主要成分是氧化铝(Al2O3),系含有杂质的水合氧化铝,是一种土状矿物。
白色或灰白色,因含铁而呈褐黄或浅红色。
密度3.9~4g/cm3,硬度1~3,不透明,质脆。
极难熔化。
不溶于水,能溶于硫酸、氢氧化钠溶液。
主要用于炼铝,制耐火材料。
矾土矿学名铝土矿、铝矾土。
铝矾土煅烧工艺流程是将生矾土经高温煅烧后(1200~1700℃)称为铝矾土熟料的一个复杂过程。
物料从窑尾(筒体的较高的一端)进入窑内煅烧,由于筒体的倾斜和缓慢的回转作用,物料既沿圆周方向翻滚又沿轴向(从较高的一端向低端)移动,继续完成其工艺过程,生成熟料经窑头罩进入冷却机冷却。
随着煅烧温度的增加,保温时间的延长,铝含量随之增加,铝矾土的等级也随之增加。
传统的铝矾土煅烧工艺流程:原料进厂→库→破碎→粉磨→过压滤→练泥→挤出成型→烘干→煅烧→破碎→出厂成品。
由于铝矾土原料成分的不稳定,这种传统的煅烧铝矾土熟料的生产工艺所得到的铝矾土熟料品质不高,且产品质量不稳定,为了得到品质优良的铝矾土熟料,提出的新的铝矾土均化料煅烧工艺流程:原料进厂→库→破碎→粉磨→脱硅→湿法均化→过压滤→练泥→挤出成型→烘干→煅烧→破碎→出厂成品。
一、煅烧铝矾土回转窑的窑型及产量技术参数规格产量(t/d)支座数电动机功率(kW)Ø2.2×38m1202组YVF2-225M-445Ø2.5×40m1502组YVF2-250M-455Ø2.8×43m2002组YVF2-280S-475Ø3.0×50m2302组YVF2-280M-490Ø3.2×50m2502组YVF2-315L2-6132Ø3.6×55m4002组YVF2-355M1-6160Ø3.8×58m5002组YVF2-355M2-6185Ø4.0×60m6002组YVF2-355M4-6200Ø4.3×64m8002组YVF2-355L3-6250二、铝矾土回转窑煅烧工艺流程及结构组成(一)铝矾土煅烧工艺流程具体步骤:进厂的铝矾土,块度约300~500mm,水分约8%。
重烧镁砂生产流程
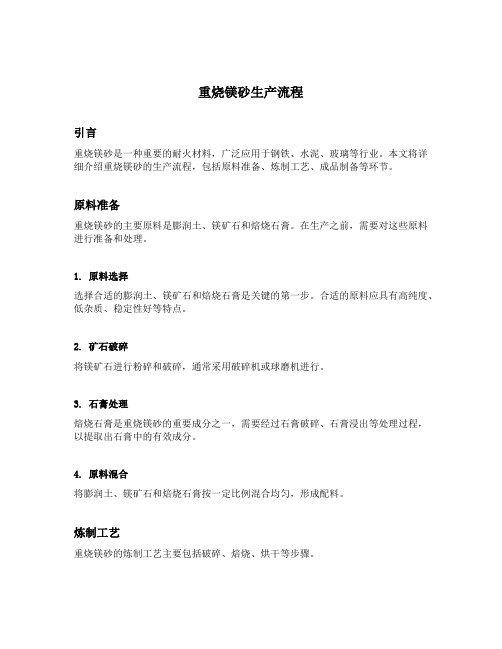
重烧镁砂生产流程引言重烧镁砂是一种重要的耐火材料,广泛应用于钢铁、水泥、玻璃等行业。
本文将详细介绍重烧镁砂的生产流程,包括原料准备、炼制工艺、成品制备等环节。
原料准备重烧镁砂的主要原料是膨润土、镁矿石和焙烧石膏。
在生产之前,需要对这些原料进行准备和处理。
1. 原料选择选择合适的膨润土、镁矿石和焙烧石膏是关键的第一步。
合适的原料应具有高纯度、低杂质、稳定性好等特点。
2. 矿石破碎将镁矿石进行粉碎和破碎,通常采用破碎机或球磨机进行。
3. 石膏处理焙烧石膏是重烧镁砂的重要成分之一,需要经过石膏破碎、石膏浸出等处理过程,以提取出石膏中的有效成分。
4. 原料混合将膨润土、镁矿石和焙烧石膏按一定比例混合均匀,形成配料。
炼制工艺重烧镁砂的炼制工艺主要包括破碎、焙烧、烘干等步骤。
1. 破碎将原料配料进行再次破碎,以进一步提高原料的反应活性。
2. 焙烧将破碎后的原料进行焙烧处理。
将原料放入高温炉中,在一定温度下进行高温煅烧,使原料中的化学成分发生变化,形成重烧镁砂的基础结构。
焙烧的温度和时间是影响产品质量的重要因素。
3. 烘干经过焙烧的重烧镁砂含有一定比例的水分,需要经过烘干过程,去除水分,提高产品的稳定性和耐高温性能。
成品制备经过炼制工艺的重烧镁砂已初步形成,但还需要进一步加工和制备,以得到符合要求的成品。
1. 研磨将焙烧后的重烧镁砂进行研磨处理,以得到所需的粒度和颗粒形状。
2. 篩分将研磨后的重烧镁砂进行筛分,去除不符合要求的颗粒,保证产品质量。
3. 包装将符合要求的重烧镁砂进行包装,通常采用袋装或散装的形式,以便于储存和运输。
结论重烧镁砂的生产流程包括原料准备、炼制工艺和成品制备等环节。
通过对原料的选择、破碎、焙烧和烘干等处理,再经过研磨、筛分和包装等加工,最终获得符合要求的重烧镁砂成品。
生产过程中需要严格控制各个环节的工艺参数,以获得稳定的产品质量和满足客户需求。
重烧镁砂的生产流程非常复杂,需要专业的设备和技术支持,以确保生产的安全、高效和可持续发展。
9种常用耐火材料制品的成型方法介绍

9种常用耐火材料制品的成型方法介绍目录刖§1.机压成型法11.可塑成型法2.注浆成型法32.等静压成型法4.振动成型法43.捣打成型法5.挤压成型法54.熔铸成型法7.热压成型法71—刖S耐火材料的成型是指借助于外力和模型将坯料加工成规定尺寸和形状的坏体的过程。
成型方法很多,传统的成型方法按坯料含水量的多少可分为半干法(坯料水分5%左右)、可塑法QK分15%左右)和注浆法(水分40%左右)。
耐火制品生产中根据坯料的性质、制品的形状、尺寸和工艺要求来选用成型方法。
由于耐火材料工业的不断发展,成型工艺也在不断发展,连续铸钢用的铝碳制品采用等静压成型,特大型砖采用挤压法成型;微型制品采用热压注法成型等。
不管用哪一种方法,成型后的耐火制品坯体均应满足下列要求:(1)形状、尺寸和精度符合设计要求;(2)结构均匀、致密,表面及内部无裂纹;(3)具有足够的机械强度;(4)符合逾期的物理性能要求。
1.机压成型法机压成型法是目前耐火材料生产中使用最多的成型方法。
该方法使用压砖机和钢模具将泥料压制成坯体。
因一般机压成型均指含水量为4%〜9%的半干料成型方法,因面也称半干法成型。
该法常用的设备有摩擦压砖机、杠杆压砖机和液压机等。
机压成型过程实质上是一个使坯料内颗粒密集和空气排出、形成致密坯体的过程。
机压成型的砖坯具有密度高、强度大、干燥收缩和烧成收缩小、制品尺寸容易控制等优点,所以该法在耐火材料生产中占主要地位。
机压成型时为获得致密的坯体,必须给予坯料足够的压力。
这压力的大小应能够克服坯料颗粒间的内摩擦力,克服坯料颗粒与模壁间的外摩擦力,克服由于坯料水分、颗粒及其在模具内填充不均匀而造成的压力分布不均匀性,这三者之间的比例关系取决于坯料的分散度、颗粒组成、坯料水分、坯体的尺寸和形状等。
虽然压力与坯体致密化的关系有若干理论公式可供计算,如坯体气孔随压力成对数关系而变化等,但通常用试验方法近似地确定坯体所需的单位而积压力,并依此决定压砖机应有的总压力。
耐火材料厂环境影响评价报告书
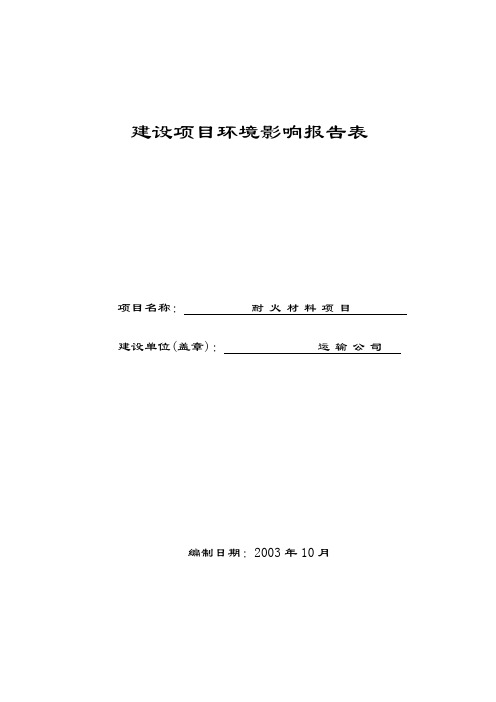
项目名称:
耐火材料项目
建设单位(盖章):
运输公司
编制日期:2003 年 10 月
一、产品工艺流程简介
加水 ↓
原料
配料↓ G1
浸渍 回用
搅↓拌 N
成↓ 型 N
破碎
↓ N
修坯
次品
成品
检验
烧制 ↓ G2
注:G1 表示表示粉尘;G2 表示燃煤烟气;N 表示噪声。
次品
分检
二、原辅材料消耗及能源需求 原辅材料消耗及能源需求见表 1。
搅拌机 破碎机
生产设备一览表
数量
备注
1台
瓷珠搅拌工段
1台
瓷珠成型工段
2台
电炉盘成型工段
1台
耐火砖成型工段
1台
电炉盘成型工段
2 台 电炉盘及耐火砖搅拌工段
1台
次品回用工段
四、主要污染物分析 1、废水 项目在生产过程中先将原料按比例配料,然后加水浸渍保养,需用 水 10.5 吨/年,该水在坯制成型及烧制工段以水蒸气形式挥发至环境空 气中,没有工艺废水外排。 营运期间食堂、办公室等生活用水需 200 吨/年,产生生活污水 160 吨/年,废水主要污染物有 CODCr 400mg/L、SS 250mg/L。 2、废气 a、粉尘 项目所用的高苓土、长石粉、石英粉、滑石粉、黑泥等原料为粉状 物质,在配料过程中会在投料口产生粉尘,生坯分检出来的次品以及烧 制后检验出来的次品,用破碎机破碎,次品为干状物,破碎时会有工业 粉尘产生。。
Lpi—第 i 个声源的噪声级,dB(A)。 c、噪声预测值计算公式
L预 L新 L背景
式中:L 预—噪声预测值; L 新—声源增加的声级; L 背景—噪声的背景值。
海事常用耐火材料设备特殊要求与常用耐火材料措施
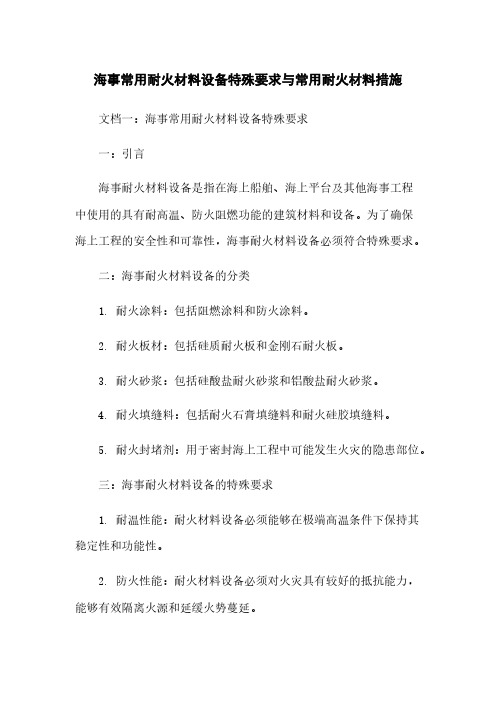
海事常用耐火材料设备特殊要求与常用耐火材料措施文档一:海事常用耐火材料设备特殊要求一:引言海事耐火材料设备是指在海上船舶、海上平台及其他海事工程中使用的具有耐高温、防火阻燃功能的建筑材料和设备。
为了确保海上工程的安全性和可靠性,海事耐火材料设备必须符合特殊要求。
二:海事耐火材料设备的分类1. 耐火涂料:包括阻燃涂料和防火涂料。
2. 耐火板材:包括硅质耐火板和金刚石耐火板。
3. 耐火砂浆:包括硅酸盐耐火砂浆和铝酸盐耐火砂浆。
4. 耐火填缝料:包括耐火石膏填缝料和耐火硅胶填缝料。
5. 耐火封堵剂:用于密封海上工程中可能发生火灾的隐患部位。
三:海事耐火材料设备的特殊要求1. 耐温性能:耐火材料设备必须能够在极端高温条件下保持其稳定性和功能性。
2. 防火性能:耐火材料设备必须对火灾具有较好的抵抗能力,能够有效隔离火源和延缓火势蔓延。
3. 防腐性能:耐火材料设备必须能够抵御海水的腐蚀,防止材料损坏。
4. 抗震性能:耐火材料设备必须具有较好的抗震能力,能够在海上工程中抵御海浪和风浪的冲击。
5. 环保性能:耐火材料设备必须符合环保要求,不得对海洋生态环境造成污染。
四:海事常用耐火材料设备的措施1. 安装海事耐火涂料:在海上建筑结构的表面涂覆耐火涂料,增强防火性能。
2. 使用耐火板材:在海上工程的墙面、隔舱等区域使用耐火板材,阻止火势蔓延。
3. 海事耐火砂浆的填缝:使用耐火砂浆进行填缝,增强海上工程的密封性和耐火性。
4. 耐火封堵剂的使用:在海上工程可能发生火灾的地方进行封堵,防止火势扩散。
附件:海事耐火材料设备材质检验报告法律名词及注释:1. 海事工程:指在海洋上建设、安装等属于海事领域的工程项目。
2. 耐火材料设备:具有防火、阻燃功能的建筑材料和设备。
3. 海上船舶:指在海上航行和运输货物、人员等的水上交通工具。
4. 海上平台:海上石油钻井平台等海上工程设施。
5. 防火涂料:能够阻止火灾蔓延的涂料。
6. 耐火砂浆:能够阻止火势蔓延、保持结构稳定性的砂浆。
- 1、下载文档前请自行甄别文档内容的完整性,平台不提供额外的编辑、内容补充、找答案等附加服务。
- 2、"仅部分预览"的文档,不可在线预览部分如存在完整性等问题,可反馈申请退款(可完整预览的文档不适用该条件!)。
- 3、如文档侵犯您的权益,请联系客服反馈,我们会尽快为您处理(人工客服工作时间:9:00-18:30)。
耐火材料生产工艺及主要设备-原料加工
几种原料在煅烧时的分解反应
原料
组成
耐火粘土 A12O3·2SiO2·2H2O
分解产物 3A12O3·2SiO2、SiO2、H2O
重量损失 %
14
要求煅烧 温度℃
耐火材料生产工艺及主要设备-混练
混合过程: 1)快速混合阶段,不同成分,不同粒度的颗粒移动,均匀度提 高很快, 2)扩散混合阶段:混合达一定程度后,有的颗粒扩散到新出现 的物料上,这阶段表现为均匀程度的增加比上一阶段小 3)后期混合阶段(或称逆混合过程) 两种作用, ①颗粒偏析 主要由重力、离心力作用,大颗粒偏离析出, ②团聚、捏合 由于较长时间的混合,受以下四种力的作用,物 料产生团聚,捏合,均匀度波动在一定范围内。 四种力为 a 液体架桥和毛细管引力,
耐火材料生产工艺及主要设备-配料
配 料组 成,%
碳化硅
97 90 80
粘土
3 10 20
碳化硅颗粒组成
1.4~0.5mm
<0.3mm
数量,%(100%碳化硅)
40
60
50
50
60
40
耐火材料生产工艺及主要设备-配料
SiC粒度
12~30目 20~36目 0.5~0mm 325F
wt/% 30 26 20 24
相同尺寸的球,有五种堆积方式:
对单一尺寸的圆球来说,其堆积密度、气孔率与圆球尺寸大 小,材料性质无关,按六方型以配位数为8的方式堆积。
在任何情况下,其气孔率均为38±1%。
耐火材料生产工艺及主要设备-坯料的制备
单一颗粒的堆积方式与气孔率
序号
1 2 3 4 5
堆积方式
立方 六方型 复六方型 角锥型 四面体型
耐火材料生产工艺及主要设备-原料加工
b 轻烧活化解决纯净的物料难烧结的问题。 轻烧活化:将物料在一定温度下进行轻烧。 使晶格缺陷增加。 活性提高,再进行死烧, 轻烧-压球或压块-死烧,也称二步煅烧法。 在1600 ℃以下,制成高纯度,高密度的烧结镁砂,MgO含
量高达99.9%,密度可达3.4g/cm3。 物料纯度不高,杂质含量大于4%的镁砂,不采用二步煅烧法 有些矿物,硅石、叶蜡石等在加热过程中体积变化很小,不
1600~1650 1600~1650 1200~1300
注:石灰石只达到完全分解,不需要烧结
耐火材料生产工艺及主要设备-原料加工
实际煅烧中,纯净的物料是很难烧结的 对煅烧设备的使用寿命不利并需消耗大量能源。
高纯白云石1700℃的高温烧结 高纯镁砂1900~2000℃烧结。 纯净原料的煅烧方法: a 增加物料的比表面积的方法降低烧结温度 靠单纯的降低物料粒度增加比表面积是有一定限度的,磨粉 的能耗很大。
耐火材料生产工艺及主要设备-原料加工
3.2 原料的加工
1.原料的煅烧 大多数原生矿石不能直接用来制砖,在高温作用下发生物理
化学反应(分解、化合和烧结等), 高温作用下重量和体积都会发生变化,引起砖坯的体积变化
,甚至会出现大量的变形和开裂的废品。 在原料煅烧时完成(或基本完成),保证获得符合一定质量要
接触和塑化的操作过程称混练。 耐火材料的混练是混合的一种方式,伴随有一定程度的挤
压、捏和、排气过程在内。 坯料混合的目的:
使坯料中成分和性质均匀,即在单位质量或体积内具有同 样的成分和颗粒组成。
耐火材料生产工艺及主要设备-混练
混练质量好时的坯料: 1)各个成分应该是均匀分布的(包括不同原料的颗 粒,同一原料的不同大小的颗粒和水分等) 2)配料的结合性应得到充分的发挥 3)空气充分排除 4)再粉碎程度小。
62 85.6 94.6 98.0 99.2
气孔率,%
38 14.4 5.4 2.0 0.8
气孔率下降,%
- 23.6 9.0 3.4 1.2
耐火材料生产工艺及主要设备-坯料的制备
理想的堆积: 粗颗粒构成框架 中间颗粒填充于大颗粒构成的空隙间,与大颗粒相切, 细粉填充于中间颗粒构成的空隙中,
1)采用单一的颗粒不能达到紧密堆积, 2)采用多组分可达紧密堆积,而且组分颗粒尺寸相差越大越好, 一般相差4~5倍以上效果方显著
耐火材料生产工艺及主要设备-混练
混合机理: 1)对流混合(亦称移动混合),颗粒成团的移动, 2)扩散混合,颗粒分散到新出现的粉料面上, 3)剪切混合,在物料团块内部颗粒之间相对的缓慢移动,在 物料中形成若干滑移面 在混合过程中,三种机理不能截然分开,主要以混合设备的 不同,取主导地位的混合机理各异。
耐火材料生产工艺及主要设备-坯料的制备
在耐火材料生产中 通常多采取三种组分颗粒配合 粗颗粒 中颗粒 细颗粒
细颗粒,从0到0.2mm(或0.1mm) 中颗粒:从0.2(或0.1)mm到0.5mm 粗颗粒: 从0.5mm到3~4mm,
耐火材料生产工艺及主要设备-配料
2 配料
这一句话的如何理解?
1.配料的组成
0.5~0
6 4 高岭土 14.1%
<0.075
13 6 铝矾土 3.18%
2
结合剂(wt%) 高岭土 20%
Al2O3 10 %
30
合计 45 25 Al2O3 1.2%
耐火材料生产工艺及主要设备-配料
碳化硅细颗粒对碳化硅粘土质砖坯密度的影响
泥 料 组 成,%
碳化硅颗粒,mm
粘土 0.6~0.5 0.3~0.25 0.15~0.125
b 粘结剂附着力, c 范德华引力; d 机械捏合力。
条件及要求,品种繁多、 性质各异的耐火材料制品。 所用原料以及对产品质量要求的不同,不同类型耐火材料
的 生产方法也各有特点。 耐火材料的生产方法随其品种而异。 耐火材料的生产是有共性的。
生产工序:原料的煅烧、破粉碎、细磨、筛分、配料、混合、 成型、干燥、烧成主要工序。
耐火材料生产工艺及主要设备-概述
结合剂的化学矿物组成组成
各种原料的组成
滑石
38.4% ×30%
高岭土 铝矾土 Al2O3
47% ×30 10.6%
%
×30%
4%×30%
合计 30
莫来石基
20%
10%
30
耐火材料生产工艺及主要设备-配料
颗粒mm 成分
堇青石(wt%)
莫来石(wt%)
2.0~0.5
26 15
1
结合剂(wt%)
滑石 11.52%
配料的组成:按规定比例配合的各种原料是和同一原料的 各不同颗粒组成的粉料。它随制品的类型和性能要求、所用 原料的性质及工艺条件而改变。
耐火材料生产工艺及主要设备-配料
(1)从化学组成方面看,配料的化学组成必须能满足制品 的要求,并且应比制品的指标要求高此。
(2)现在生产中一般采用半干压制法,它要求的坯料具有 足够的结合性,在配料中应含有结合成分。有时结合作用可 由配料中的主体原料来承担,但有时主体原料是瘠性的,则 要由具有粘结能力的结合剂来完成,如纸浆废液、结合粘土 和石灰乳等。
配位数
6 8 10 12 12
气孔率,%
47.64 39.55 30.20 25.75 25.95
耐火材料生产工艺及主要设备-坯料的制备
②尺寸不同的圆球体堆积 大颗粒的组成中加入一定数目尺寸较小的颗粒,填充于大颗
粒的间隙,则堆积物间空隙可进一步降低。 假如向第一组球内引入第二组球,其尺寸比第一组球小,第
1300~1400
高铝矾土
菱镁石 白云石 石灰石
A12O3·2H2O +A12O3·2SiO2·2H2O
MgCO3 CaMg(CO3)2 CaCO3
3A12O3·2SiO2、A12O3、 SiO2、H2O MgO、CO2 CaO、MgO、CO2 CaO、CO2
约15
52 47.7 44
1450~1550
10 50
10
30
10 50
10
-
10 40
10
-
10 40
20
-
10 30
10
-
10 30
20
-
<0.06
30 40 30 50 40
气孔率,% 砖坯 制品
23.6 - 17.0 15.3 17.0 16.2 16.1 15.6 17.4 16.2 17.5 16.7
耐压强度 MPa
- 990 1130 1000 1500 1100
22.8
100.0
耐火材料生产工艺及主要设备-坯料的制备
1.坯料的颗粒组成 坯料的颗粒组成对坯体的致密度有很大影响。
在不考虑颗粒本身变形的前提下,从粉料制成坯体的总收缩, 等于原始气孔的体积。
符合紧密堆积的颗粒组成,才有得到致密坯体的可能。
耐火材料生产工艺及主要设备-坯料的制备
①尺寸相同的圆球堆积 颗粒间的相互结合,遵循着内能最低的原则
二组球在空隙内也能以配位数为8的方式堆积,则混合物的空 隙下降为14.4%。
再加入体积更小的第三、第四组球,空隙还会进一步下降 当三组分球作最紧密堆积时,气孔率下降显著,当组分大于3 时,则气孔率下降不明显。
耐火材料生产工艺及主要设备-坯料的制备
多组分球体堆积特征
球体组分
1 2 3 4 5
球体体积,%
(3)原料中含有水分和灼减成分时,使得原料、配料和制 品的化学组成之间出现换算关系。
耐火材料生产工艺及主要设备-配料
堇青石-莫来石耐火材料配料
颗粒mm 成分
堇青石(wt%)
莫来石(wt%) 结合剂(wt%)
2.0~0.5 0.5~0
26
6