液压系统的设计
完整的液压系统设计毕业设计

完整的液压系统设计毕业设计1. 引言液压系统在工程领域中具有广泛的应用,特别是在机械制造、航空航天、汽车制造等领域中。
本文档旨在设计一个完整的液压系统作为毕业设计,并提供系统设计的详细说明。
2. 设计目标本设计的目标是创建一个可靠、高效的液压系统,满足以下需求:•传递大量的力和动力;•控制和调节工作负载;•提供良好的工作稳定性;•实现节能和环保。
3. 系统设计3.1 系统结构我们的液压系统将包含以下主要组件:1.液压泵:负责将液体加压并输送到液压马达或液压缸;2.液压马达或液压缸:负责将液压能转化为机械能,实现力的传递及工作载荷控制;3.液体储存装置:用于储存液体并平衡系统压力;4.液压阀门:用于控制液体流动和压力,实现系统工作的调节和控制;5.传感器和仪表:用于监测和测量液压系统的压力、流量、温度等参数。
3.2 液体选择在设计液压系统时,我们需要选择合适的液体作为工作介质。
一般情况下,液压系统常采用液体油作为工作介质,因为它具有良好的润滑性、稳定性和耐高温性能。
对于不同的应用场景,需要考虑液体的黏度、温度范围、氧化稳定性以及环境友好程度等因素。
3.3 液压元件选型为了实现液压系统的设计目标,我们需要对液压元件进行合理的选型。
液压泵、液压马达或液压缸、液压阀门等元件都有不同的类型和规格可供选择。
在选型过程中,需要考虑力的传递要求、流量和压力范围、工作稳定性以及适应特定工况的能力等因素。
3.4 系统控制在液压系统设计中,系统的控制是十分重要的。
通过合理的控制方法和策略,可以实现对液体流动、压力和工作负载的准确控制。
常用的液压系统控制方法有手动控制、自动控制和比例控制等。
根据具体需求,选择适合的控制方式可以提高系统的稳定性和性能。
4. 系统优化为了提高液压系统的工作效率和节能性,我们可以进行进一步的优化。
以下是一些常见的系统优化方法:•使用高效节能的液压泵和液压马达;•优化液体流动路径,减小能量损失;•采用高效的液压阀门和控制系统,减小能量损耗;•合理设计系统布局和管路,减小摩擦损失;•控制液压系统的工作温度,在适当的范围内减小能量损失。
液压系统设计计算
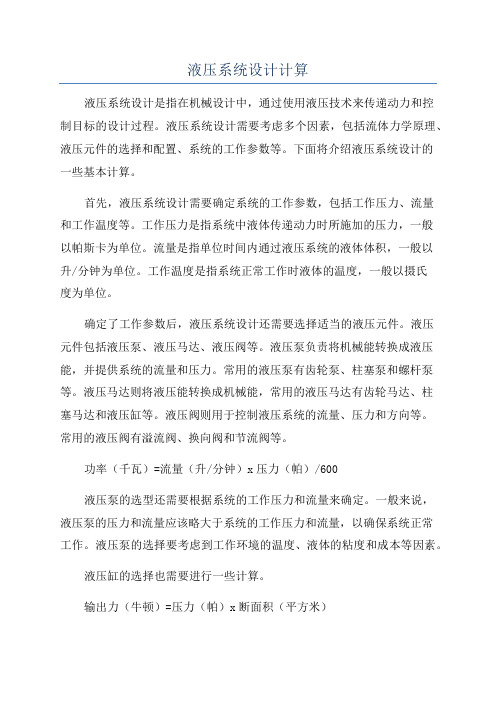
液压系统设计计算液压系统设计是指在机械设计中,通过使用液压技术来传递动力和控制目标的设计过程。
液压系统设计需要考虑多个因素,包括流体力学原理、液压元件的选择和配置、系统的工作参数等。
下面将介绍液压系统设计的一些基本计算。
首先,液压系统设计需要确定系统的工作参数,包括工作压力、流量和工作温度等。
工作压力是指系统中液体传递动力时所施加的压力,一般以帕斯卡为单位。
流量是指单位时间内通过液压系统的液体体积,一般以升/分钟为单位。
工作温度是指系统正常工作时液体的温度,一般以摄氏度为单位。
确定了工作参数后,液压系统设计还需要选择适当的液压元件。
液压元件包括液压泵、液压马达、液压阀等。
液压泵负责将机械能转换成液压能,并提供系统的流量和压力。
常用的液压泵有齿轮泵、柱塞泵和螺杆泵等。
液压马达则将液压能转换成机械能,常用的液压马达有齿轮马达、柱塞马达和液压缸等。
液压阀则用于控制液压系统的流量、压力和方向等。
常用的液压阀有溢流阀、换向阀和节流阀等。
功率(千瓦)=流量(升/分钟)x压力(帕)/600液压泵的选型还需要根据系统的工作压力和流量来确定。
一般来说,液压泵的压力和流量应该略大于系统的工作压力和流量,以确保系统正常工作。
液压泵的选择要考虑到工作环境的温度、液体的粘度和成本等因素。
液压缸的选择也需要进行一些计算。
输出力(牛顿)=压力(帕)x断面积(平方米)液压缸的选择要根据所需的输出力和工作压力来确定。
液压缸的密封性能和机械结构等因素也需要考虑。
另外,液压系统设计中还需要考虑管道的设计和安装。
管道的设计要根据系统的工作温度、压力和流量来确定。
管道的材料和尺寸选择要满足系统的需要,并保持良好的连接和密封性能。
综上所述,液压系统设计涉及到多个方面的计算和选择。
通过合理的设计和计算,可以确保液压系统的性能和可靠性。
因此,在液压系统的设计过程中,需要充分考虑各个因素,并进行适当的计算和分析。
液压系统的设计计算举例
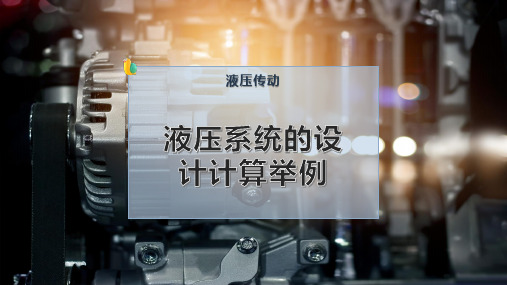
作缸的小腔,即从泵的出口到缸小腔之间的压力损失 Δp = 5.5×105 MPa ,于是小泵出
口压力 pp1 = 21.56×105 MPa (小泵的总效率 η 1 = 0.5 ),大泵出口压力 pp2 =
23.06×105 MPa (大泵的总效率 η 2 = 0.5 )。故电机功率为
P pp1q1 pp2q2 21.56 105 0.167 103 W 23.06 105 0.267 103 W 1 951.5 W
= 0.5 ,大泵出口压力 pp2 = 15.18×105 MPa (大泵的总效率 η 2 = 0.5 )。故电机功率
为
P1
pp1q1 1
pp 2 q2 2
13.68 105 0.167 103 0.5
W 15.18 105 0.267 103 0.5
W
1 267.5 W
(2)工进
小泵的出口压力 pp1 = p1 +Δp1 = 32.19×105 MPa ,大泵卸载,卸载压力取 pp2 =
液压传动
液压系统的设计计算举例
1.1 分析工况及主机工作要求,拟定液压系统方案 1.2 参数设计 1.3 选择元件 1.4 液压系统性能验算
液压系统的设计计算举例
1.1 液分析工况及主机工作要求,拟定液压系统方案
(一) 确定执行元件类型
(二) 确定执行元件的负载、速度变化范围
Fw 18 000 N
1
2
0.5
0.5
综合比较,快退时所需功率最大。据此查产品样本选用Y112M—6型异步电机,
电机功率2.2 kW,额定转速为940 r/min。
(三) 选择液压阀
根据液压阀在系统中的最高工作压力与通过该阀的最大流量,可选出这些元件的 型号及规格。选定的元件列于表中。
液压驱动系统设计与控制

液压驱动系统设计与控制引言液压驱动系统是一种广泛应用于各个领域的动力传动装置,它可实现高扭矩、高功率输出以及精确的位置控制。
本文将探讨液压驱动系统设计与控制的原理和方法,讨论其在工程实践中的应用和挑战。
一、液压驱动系统设计1. 动力源选择液压系统的动力源通常为液压泵,其类型包括齿轮泵、叶片泵和柱塞泵等。
根据应用场景和性能要求,设计人员需综合考虑工作压力、流量要求以及能源消耗等因素选择合适的液压泵。
同时还需要注意泵的噪音、振动和寿命等方面的要求。
2. 液压元件选择液压驱动系统的核心是液压元件,如液压缸、液压阀和液压马达等。
设计人员需要根据系统工作需求选择合适的液压元件,并考虑到其额定工作压力、流量和驱动力等参数。
同时还需要充分考虑元件的可靠性、使用寿命和维修保养等因素。
3. 管路设计管路设计是液压系统设计中重要的一环,它直接关系到流体传递的可靠性和效率。
在设计管路时,需要注意管道的截面尺寸、长度、弯曲和连接方式等,以保证系统的正常运行和流体的稳定流动。
此外,还需注意避免管路中的漏油、渗漏和压力损失等问题。
二、液压驱动系统控制1. 控制方式选择液压驱动系统的控制方式通常分为手动控制和自动控制。
手动控制适用于简单的操作任务,如手动控制阀门或压力开关。
而自动控制则通过传感器和控制器等设备实现对液压系统的精确控制,包括位置、速度和压力等参数。
2. 控制策略液压驱动系统的控制策略包括开环控制和闭环控制。
开环控制基于预设条件进行操作,适用于一些简单的工作。
闭环控制通过传感器反馈信号不断调整输出信号,实现对系统参数的精确控制。
选择合适的控制策略可以提高系统的控制精度和性能。
3. 控制器设计液压驱动系统的控制器通常由传感器、执行器、计算机等装置组成。
控制器的设计需要考虑到控制算法的选择、信号采集和处理等方面。
合理选择控制器的参数和配置,优化控制器的动态响应特性,可以提高液压驱动系统的控制性能。
三、液压驱动系统应用与挑战1. 工程应用液压驱动系统广泛应用于各个领域,如工业生产线、建筑机械、航空航天等。
液压系统的设计

液压系统的设计液压系统设计是液压主机设计的重要组成部分,也是对前面各章内容的概括总结和综合应用。
本章主要阐述液压系统设计的一般步骤,设计内容和设计计算方法,并通过实例来说明液压系统的设计过程。
9.1 液压系统的设计步骤液压系统设计与主机的设计是紧密联系的,两者往往同时进行,互相协调。
设计液压系统时应首先明确主机对液压系统在动作、性能、工作环境等方面的要求,如执行元件的运动方式、行程、调速范围、负载条件、运行平稳性和精度、工作循环及周期、工作环境、安装空间大小、结构简单、工作安全可靠、效率高、使命寿命长、经济性好、使用维修方便等设计原则。
液压系统设计步骤大体上可按图9-1所示的内容和流程进行。
这里除了最后一项(8)外,均属性能设计范围。
这些步骤是相互关联,相互影响的,必须经反复修改才能完成。
设计步骤及方法介绍如下。
9.1.1 明确系统的设计要求设计液压系统时,首先要对液压主机的工况进行分析,明确主机对液压系统的要求,具体包括:1)主机的用途、主体布局、对液压装置的位置和空间尺寸的限制。
2)主机的工作循环,液压系统应完成的动作、动作顺序或互锁要求,以及自动化程度的要求。
3)液压执行元件的负载和运动速速的大小及其变化范围,运动平稳性、定位精度及转化精度等的要求。
4)液压系统的工作环境和工作条件。
5)工作效率、安全性、可靠性及经济性等要求。
9.1.2 分析系统工况,确定主要参数1.工况分析工况分析,就是分析主机在工作过程中各执行元件的运动速度和负载的变化规律。
它是拟定液压系统方案,选择或设计液压元件的依据。
工况分析包括动力参数分析和运动参数分析两个部分,即:1)动力参数分析就是通过计算液压执行元件的载荷大小和方向,并分析各执行元件在工作过程中可能产生的冲击、振动及过载等。
对于动作较复杂的机械设备,根据工艺要求,将各执行元件在各阶段所需克服的负载用图9-2a所示的负载-位移(F-L)曲线表示,称为负载图。
液压系统设计
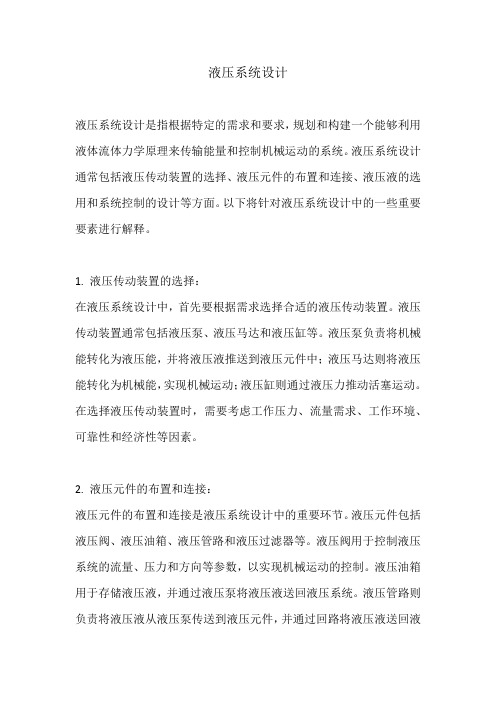
液压系统设计液压系统设计是指根据特定的需求和要求,规划和构建一个能够利用液体流体力学原理来传输能量和控制机械运动的系统。
液压系统设计通常包括液压传动装置的选择、液压元件的布置和连接、液压液的选用和系统控制的设计等方面。
以下将针对液压系统设计中的一些重要要素进行解释。
1. 液压传动装置的选择:在液压系统设计中,首先要根据需求选择合适的液压传动装置。
液压传动装置通常包括液压泵、液压马达和液压缸等。
液压泵负责将机械能转化为液压能,并将液压液推送到液压元件中;液压马达则将液压能转化为机械能,实现机械运动;液压缸则通过液压力推动活塞运动。
在选择液压传动装置时,需要考虑工作压力、流量需求、工作环境、可靠性和经济性等因素。
2. 液压元件的布置和连接:液压元件的布置和连接是液压系统设计中的重要环节。
液压元件包括液压阀、液压油箱、液压管路和液压过滤器等。
液压阀用于控制液压系统的流量、压力和方向等参数,以实现机械运动的控制。
液压油箱用于存储液压液,并通过液压泵将液压液送回液压系统。
液压管路则负责将液压液从液压泵传送到液压元件,并通过回路将液压液送回液压油箱。
液压过滤器则用于过滤液压液中的杂质和污染物,保持液压系统的正常运行。
3. 液压液的选用:在液压系统设计中,选择合适的液压液对系统的性能和可靠性至关重要。
液压液应具备良好的润滑性能、热稳定性、抗氧化性和抗腐蚀性,以确保液压元件的正常运行,并延长系统的使用寿命。
常见的液压液包括矿物油、合成液压油和生物液压油等。
选择液压液时,需要考虑工作温度、压力要求、环境因素和液压元件的材质等因素。
4. 系统控制的设计:液压系统的控制是液压系统设计中的另一个重要方面。
系统控制可以通过手动控制、自动控制和比例控制等方式实现。
手动控制包括使用手柄、脚踏板或开关等来控制液压系统的运行;自动控制可以通过传感器和控制器等设备来实现液压系统的自动化操作;比例控制则是根据输入信号的大小来控制液压系统的输出参数,以实现精确的控制。
液压系统设计毕业设计
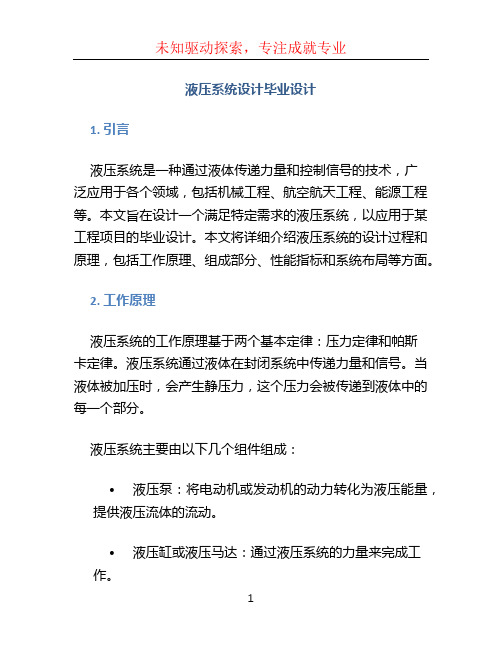
液压系统设计毕业设计1. 引言液压系统是一种通过液体传递力量和控制信号的技术,广泛应用于各个领域,包括机械工程、航空航天工程、能源工程等。
本文旨在设计一个满足特定需求的液压系统,以应用于某工程项目的毕业设计。
本文将详细介绍液压系统的设计过程和原理,包括工作原理、组成部分、性能指标和系统布局等方面。
2. 工作原理液压系统的工作原理基于两个基本定律:压力定律和帕斯卡定律。
液压系统通过液体在封闭系统中传递力量和信号。
当液体被加压时,会产生静压力,这个压力会被传递到液体中的每一个部分。
液压系统主要由以下几个组件组成:•液压泵:将电动机或发动机的动力转化为液压能量,提供液压流体的流动。
•液压缸或液压马达:通过液压系统的力量来完成工作。
•油箱:存储液压油,保持液压系统的温度和压力稳定。
•阀门:控制液体的流动,包括方向阀、流量控制阀和压力控制阀等。
•导管和连接件:连接液压系统的各个部件,传递液体。
3. 性能指标设计液压系统时,需要考虑以下性能指标:•动力输出:液压系统需要能够提供足够的动力来执行所需的工作任务。
•响应时间:液压系统的响应时间应该尽可能短,以确保工作的准确性和效率。
•系统效率:液压系统的效率应高,以减少能量损失和热量产生。
•系统可靠性:液压系统需要具备一定的可靠性,以确保长时间运行的稳定性。
•安全性:液压系统在设计上需要满足工作环境的安全要求,以防止意外事故的发生。
4. 系统布局设计在设计液压系统的布局时,需要考虑以下因素:•功能需求:根据所需的工作任务确定液压系统的功能需求,包括液压泵的选型、液压缸的布置等。
•空间约束:根据工作场地的限制,确定液压系统的尺寸和布局。
•连接方式:选择合适的连接方式和连接件,确保液压系统的连接可靠性。
•管道布置:设计合理的管道布置,避免过长或过短的管道对系统性能产生影响。
•安全设备:根据安全要求,选择合适的安全设备,如压力开关、液压阀等。
5. 结论通过本文的液压系统设计,我们能够满足特定需求的液压系统的毕业设计要求。
液压系统设计规范要求
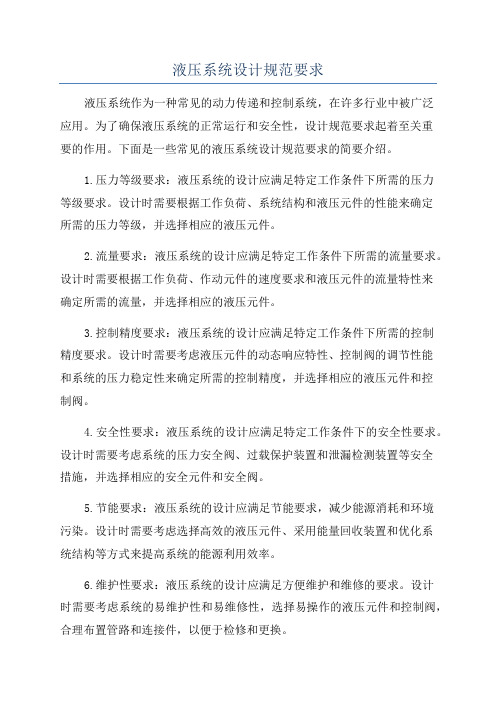
液压系统设计规范要求液压系统作为一种常见的动力传递和控制系统,在许多行业中被广泛应用。
为了确保液压系统的正常运行和安全性,设计规范要求起着至关重要的作用。
下面是一些常见的液压系统设计规范要求的简要介绍。
1.压力等级要求:液压系统的设计应满足特定工作条件下所需的压力等级要求。
设计时需要根据工作负荷、系统结构和液压元件的性能来确定所需的压力等级,并选择相应的液压元件。
2.流量要求:液压系统的设计应满足特定工作条件下所需的流量要求。
设计时需要根据工作负荷、作动元件的速度要求和液压元件的流量特性来确定所需的流量,并选择相应的液压元件。
3.控制精度要求:液压系统的设计应满足特定工作条件下所需的控制精度要求。
设计时需要考虑液压元件的动态响应特性、控制阀的调节性能和系统的压力稳定性来确定所需的控制精度,并选择相应的液压元件和控制阀。
4.安全性要求:液压系统的设计应满足特定工作条件下的安全性要求。
设计时需要考虑系统的压力安全阀、过载保护装置和泄漏检测装置等安全措施,并选择相应的安全元件和安全阀。
5.节能要求:液压系统的设计应满足节能要求,减少能源消耗和环境污染。
设计时需要考虑选择高效的液压元件、采用能量回收装置和优化系统结构等方式来提高系统的能源利用效率。
6.维护性要求:液压系统的设计应满足方便维护和维修的要求。
设计时需要考虑系统的易维护性和易维修性,选择易操作的液压元件和控制阀,合理布置管路和连接件,以便于检修和更换。
7.可靠性要求:液压系统的设计应满足可靠性要求,确保系统能够长时间、稳定地运行。
设计时需要考虑液压元件的寿命和可靠性,选择可靠性较高的液压元件和材料,并采取相应的措施来提高系统的可靠性。
8.环境适应性要求:液压系统的设计应满足特定工作环境的要求,如高温、低温、潮湿、腐蚀等。
设计时需要选择适应工作环境的液压元件和密封件,选用符合环保要求的液压油和材料。
总之,液压系统设计规范要求涉及压力等级、流量要求、控制精度、安全性、节能性、维护性、可靠性和环境适应性等方面。
机床液压系统的设计

2 液压传动的工作原理和组成液压传动是用液体作为工作介质来传递能量和进行控制的传动方式。
液压系统运用液压泵将原动机的机械能转换为液体的压力能, 通过液体压力能的变化来传递能量, 通过各种控制阀和管路的传递, 借助于液压执行元件(缸或马达)把液体压力能转换为机械能, 从而驱动工作机构, 实现直线往复运动和回转运动。
驱动机床工作台的液压系统是由油箱、过滤器、液压泵、溢流阀、开停阀、节流阀、换向阀、液压缸以及连接这些元件的油管、接头等组成。
2.1 工作原理1)电动机驱动液压泵经滤油器从油箱中吸油, 油液被加压后,从泵的输出口输入管路。
油液经开停阀、节流阀、换向阀进入液压缸, 推动活塞而使工作台左右移动。
液压缸里的油液经换向阀和回油管排回油箱。
2)工作台的移动速度是通过节流阀来调节的。
当节流阀开大时, 进入液压缸的油量增多, 工作台的移动速度增大;当节流阀关小时, 进入液压缸的油量减少, 工作台的移动速度减少。
由此可见, 速度是由油量决定的。
2.2 液压系统的基本组成1)能源装置——液压泵。
它将动力部分(电动机或其它远动机)所输出的机械能转换成液压能, 给系统提供压力油液。
2)执行装置——液压机(液压缸、液压马达)。
通过它将液压能转换成机械能, 推动负载做功。
3)控制装置——液压阀。
通过它们的控制和调节, 使液流的压力、流速和方向得以改变, 从而改变执行元件的力(或力矩)、速度和方向, 根据控制功能的不同, 液压阀可分为村力控制阀、流量控制阀和方向控制阀。
压力控制阀又分为益流阀(安全阀)、减压阀、顺序阀、压力继电器等;流量控制阀涉及节流阀、调整阀、分流集流阀等;方向控制阀涉及单向阀、液控单向阀、梭阀、换向阀等。
根据控制方式不同, 液压阀可分为开关式控制阀、定值控制阀和比例控制阀。
4)辅助装置——油箱、管路、蓄能器、滤油器、管接头、压力表开关等.通过这些元件把系统联接起来, 以实现各种工作循环。
5)工作介质——液压油。
(完整word版)液压系统回路设计

1、液压系统回路设计1.1、 主干回路设计对于任何液压传动系统来说, 调速回路都是它的核心部分。
这种回路可以通过事先的调整或在工作过程中通过自动调整来改变元件的运行速度, 但它的主要功能却是在传递动力(功率)。
根据伯努力方程: 2d v p q C x ρ∆= (1-1)式中 q ——主滑阀流量d C ——阀流量系数v x ——阀芯流通面积p ∆——阀进出口压差ρ——流体密度其中 和 为常数, 只有 和 为变量。
液压缸活塞杆的速度:q v A= (1-2) 式中A 为活塞杆无杆腔或有杆腔的有效面积一般情况下, 两调平液压缸是完全一样的, 即可确定 和 所以要保证两缸同步, 只需使 , 由式(1-2)可知, 只要主滑阀流量一定, 则活塞杆的速度就能稳定。
又由式(1-1)分析可知, 如果 为一定值, 则主滑阀流量 与阀芯流通面积成正比即: ,所以要保证两缸同步, 则只需满足以下条件:, 且此处主滑阀选择三位四通的电液比例方向流量控制阀,如图1-1所示。
图1-1 三位四通的电液比例方向流量控制阀它是一种按输入的电信号连续地、按比例地对油液的流量或方向进行远距离控制的阀。
比例阀一般都具有压力补偿性能, 所以它输出的流量可以不受负载变化的影响。
与手动调节的普通液压阀相比, 它能提高系统的控制水平。
它和电液伺服阀的区别见表1-1。
表1-1 比例阀和电液伺服阀的比较项目 比例阀 伺服阀低, 所以它被广泛应用于要求对液压参数进行连续远距离控制或程序控制, 但对控制精度和动态特性要求不太高的液压系统中。
又因为在整个举身或收回过程中, 单缸负载变化范围变化比较大(0~50T), 而且举身和收回时是匀速运动, 所以调平缸的功率为, 为变功率调平, 为达到节能效果, 选择变量泵。
综上所可得, 主干调速回路选用容积节流调速回路。
容积节流调速回路没有溢流损失, 效率高, 速度稳定性也比单纯容积调速回路好。
为保证值一定, 可采用负荷传感液压控制, 其控制原理图如图1-2所示。
液压系统的设计计算步骤和内容

• 最大负载值是初步确定执行元件工作压力和结构尺寸的依据。 • 液压马达的负载力矩分析与液压缸的负载分析相同,只需将上述负载
设计计算
步骤和内容
4~5
>5~7
18
系统工作压力的确定
表9-3 按主机类型选择系统工作压力
设备 类型
磨床
机床
组合机床 牛头刨床
插床 齿轮加工
机床
车床 铣床 镗床
珩磨 拉床 机 龙门 床 刨床
农业机械 汽车工业 小型工程 机械及辅 助机械
工程机械 重型机械 锻压设备 液压支架
船用 系统
压力 /MPa
摆动缸
单叶片缸转角小于300°,双叶片缸转角小于150°
往复摆动运动
齿轮、叶片马达 轴向柱塞马达 径向柱塞马达
结构简单、体积小、惯性小 运动平稳、转大、转速范围宽 结构复杂、转大、转速低
设计计算
步骤和内容
高速小转矩回转运动 大转矩回转运动 低速大转矩回转运动
7
负载分析
• 负载分析就是通过计算确定各液压执行元件的负载大小和方向,并分 析各执行元件运动过程中的振动、冲击及过载能力等情况。
设计计算
步骤和内容
2
1.1 液压系统的设计依据和工况分析
液压系统的设计依据
• 设计要求是进行工程设计的主要依据。设计前必须把主机对液压系统 的设计要求和与设计相关的情况了解清楚,一般要明确下列主要问题:
液压系统的设计毕业设计

液压系统的设计毕业设计液压系统的设计毕业设计引言液压系统是一种利用液体传递能量的技术,广泛应用于各个领域,如工业、农业、航空航天等。
在液压系统的设计中,需要考虑多个因素,包括系统的结构、元件的选择、流体的性质等。
本文将探讨液压系统的设计过程,并介绍一些常见的设计原则和方法。
一、液压系统的基本原理液压系统的基本原理是利用液体在封闭的管路中传递力和能量。
液压系统由液压泵、执行元件、控制阀等组成。
液压泵通过机械能转化为液压能,将液体压入管路中。
控制阀通过控制液体的流动方向和流量来实现对执行元件的控制。
执行元件将液体的能量转化为机械能,完成所需的工作。
二、液压系统的设计步骤1. 确定系统的需求:在进行液压系统的设计之前,需要明确系统的工作要求和目标。
例如,需要确定系统的工作压力、流量需求、工作环境等。
2. 选择液压元件:根据系统的需求,选择合适的液压元件,包括液压泵、执行元件、控制阀等。
在选择液压元件时,需要考虑元件的性能参数、可靠性、成本等因素。
3. 设计管路布局:根据系统的工作需求和元件的选择,设计合理的管路布局。
管路布局应考虑液体的流动路径、压力损失、泄漏等因素,以确保系统的稳定性和效率。
4. 进行系统分析:通过数学模型和仿真软件对系统进行分析,评估系统的性能和可靠性。
分析过程中需要考虑液体的性质、流动特性、压力变化等因素。
5. 进行系统优化:根据系统分析的结果,对系统进行优化。
优化的目标可以包括提高系统的效率、减少能量损失、降低成本等。
6. 进行系统测试:设计完成后,进行系统的实际测试。
测试过程中需要检查系统的各个部件是否正常工作,是否满足设计要求。
三、液压系统设计的原则和方法1. 简化系统结构:在液压系统的设计中,应尽量简化系统的结构,减少元件的数量和复杂性。
简化系统结构可以提高系统的可靠性和维护性。
2. 选择合适的元件:在选择液压元件时,应考虑元件的性能参数、可靠性、成本等因素。
选择合适的元件可以提高系统的性能和效率。
液压系统的优化设计
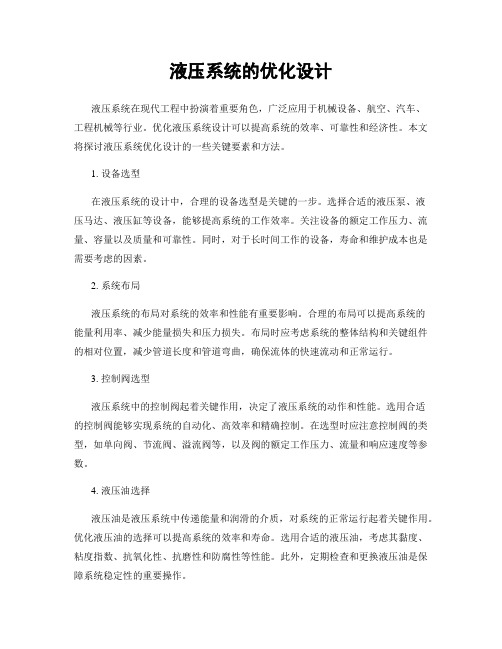
液压系统的优化设计液压系统在现代工程中扮演着重要角色,广泛应用于机械设备、航空、汽车、工程机械等行业。
优化液压系统设计可以提高系统的效率、可靠性和经济性。
本文将探讨液压系统优化设计的一些关键要素和方法。
1. 设备选型在液压系统的设计中,合理的设备选型是关键的一步。
选择合适的液压泵、液压马达、液压缸等设备,能够提高系统的工作效率。
关注设备的额定工作压力、流量、容量以及质量和可靠性。
同时,对于长时间工作的设备,寿命和维护成本也是需要考虑的因素。
2. 系统布局液压系统的布局对系统的效率和性能有重要影响。
合理的布局可以提高系统的能量利用率、减少能量损失和压力损失。
布局时应考虑系统的整体结构和关键组件的相对位置,减少管道长度和管道弯曲,确保流体的快速流动和正常运行。
3. 控制阀选型液压系统中的控制阀起着关键作用,决定了液压系统的动作和性能。
选用合适的控制阀能够实现系统的自动化、高效率和精确控制。
在选型时应注意控制阀的类型,如单向阀、节流阀、溢流阀等,以及阀的额定工作压力、流量和响应速度等参数。
4. 液压油选择液压油是液压系统中传递能量和润滑的介质,对系统的正常运行起着关键作用。
优化液压油的选择可以提高系统的效率和寿命。
选用合适的液压油,考虑其黏度、粘度指数、抗氧化性、抗磨性和防腐性等性能。
此外,定期检查和更换液压油是保障系统稳定性的重要操作。
5. 噪音与振动控制液压系统在工作过程中常常伴随着噪音和振动。
优化设计可以减少系统的噪音和振动,提高设备的工作环境和可靠性。
通过合理的管道布局、隔振措施和吸声材料的使用,可以降低噪音和振动对周围环境和操作人员的影响。
6. 故障诊断与维护液压系统的故障诊断与维护是优化设计的重要环节。
采用先进的故障诊断技术和设备,及时发现和排除系统中的故障,可以减少停机时间和损失。
定期维护和保养液压系统,对系统的各个组件进行检查、清洁和润滑,延长系统的使用寿命。
7. 系统集成与自动化随着科技的发展,液压系统的集成与自动化正在成为趋势。
液压系统设计说明书
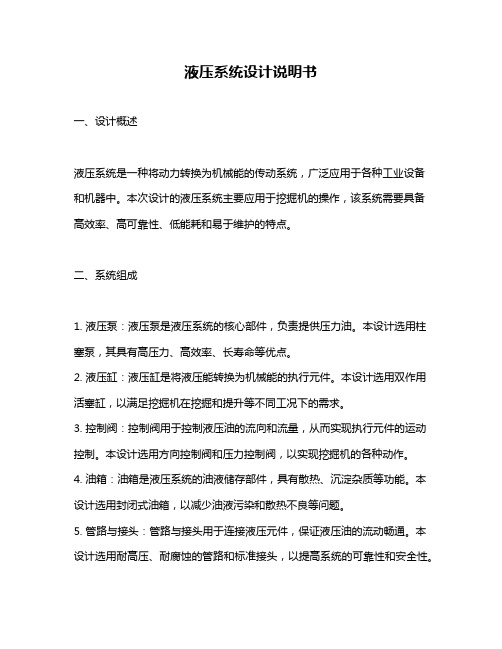
液压系统设计说明书一、设计概述液压系统是一种将动力转换为机械能的传动系统,广泛应用于各种工业设备和机器中。
本次设计的液压系统主要应用于挖掘机的操作,该系统需要具备高效率、高可靠性、低能耗和易于维护的特点。
二、系统组成1. 液压泵:液压泵是液压系统的核心部件,负责提供压力油。
本设计选用柱塞泵,其具有高压力、高效率、长寿命等优点。
2. 液压缸:液压缸是将液压能转换为机械能的执行元件。
本设计选用双作用活塞缸,以满足挖掘机在挖掘和提升等不同工况下的需求。
3. 控制阀:控制阀用于控制液压油的流向和流量,从而实现执行元件的运动控制。
本设计选用方向控制阀和压力控制阀,以实现挖掘机的各种动作。
4. 油箱:油箱是液压系统的油液储存部件,具有散热、沉淀杂质等功能。
本设计选用封闭式油箱,以减少油液污染和散热不良等问题。
5. 管路与接头:管路与接头用于连接液压元件,保证液压油的流动畅通。
本设计选用耐高压、耐腐蚀的管路和标准接头,以提高系统的可靠性和安全性。
三、系统特点1. 高效率:本设计采用高效率的柱塞泵,可有效降低能量损失,提高系统效率。
2. 高可靠性:选用高质量的液压元件和管路,采用标准化的连接方式,提高了系统的可靠性和稳定性。
3. 低能耗:通过优化液压元件的参数和系统布局,降低能耗,符合绿色环保要求。
4. 易于维护:采用模块化设计,便于拆卸和维修;同时,选用易于购买的标准件,降低了维护成本。
四、系统控制本设计的液压系统采用手动控制和自动控制相结合的方式。
手动控制主要用于初次的设备调试和应急情况下的操作;自动控制则根据预设的程序,自动完成挖掘机的各种动作。
在自动控制中,还引入了传感器和电液比例阀等智能控制元件,以提高控制的精度和响应速度。
五、系统安全为确保系统的安全运行,采取了以下措施:1. 设置溢流阀和减压阀等安全保护装置,防止过载和压力过高对系统造成损坏;2. 在油箱中设置液位计和温度计,实时监测油液的液位和温度,防止油液不足或温度过高对系统造成影响;3. 在管路中设置过滤器,防止杂质进入系统对元件造成损坏;4. 设置报警装置,当系统出现异常情况时,及时发出报警信号并切断电源,确保设备和人员的安全。
液压系统的优化设计与工程应用

液压系统的优化设计与工程应用随着现代机械制造业的持续发展和技术的不断进步,液压系统在机械制造、工程建设等领域得到了广泛应用。
液压系统的作用在于将液体能量转换成机械能,实现某一特定运动或作用。
液压系统的优化设计和工程应用,可以提高机械性能、减少机械故障、降低生产成本等,具有重要的意义和价值。
一、液压系统的基本原理和构成液压系统是由液压源、液压执行器、液压控制元件、液压传动装置和液压工作介质五部分组成。
液压源是关键的能源,它通常由泵、发动机或电动机、气压机等提供动力。
液压执行器是实现工作的元件,可分为液压缸和液压马达两类。
液压控制元件是对液压系统进行液压功率控制或流量/压力控制的元件,例如:伺服阀、节流阀、溢流阀、比例阀、多路换向阀等。
液压传动装置则负责将能量传递给执行器。
液压工作介质则是液压系统中传递动力的介质,如机油、水等。
在液压系统的运行过程中,液体在各个元件之间流动,通过一定的流道和元件来实现机械能的转化和传递。
液压系统的优化设计和工程应用,则在于提高系统的效率、稳定性和可靠性,实现最优化的液压功率控制和流量/压力控制。
二、液压系统的优化设计液压系统的优化设计,主要包括液压功率控制和流量/压力控制。
对于液压功率控制,产品应通过最小化泵源流量、最小化回油压力、降低油管管路损失等方面来提高系统效率。
对于流量/压力控制,优化设计应通过使用中点消耗控制、最小间隙节流和最小回程节流等控制方法,来消除液压波动和闪烁,并提高系统的稳定性和可靠性。
液压波动和闪烁是液压系统常见的问题,它们的存在会导致机械设备的噪音和振动加剧,降低机械性能和工作效率。
中点消耗控制是一种常见的消除液压波动和闪烁的方法,它通过增加油路的缓冲容量,使得压力波动和流量波动能够被吸收和缓冲。
最小间隙节流和最小回程节流这两种节流方法,也可以有效地减少液压波动和闪烁,同时还能提高系统的传动效率和工作性能。
三、液压系统的工程应用液压系统的工程应用广泛,涉及船舶、航空、机械制造、建筑工程等多个领域。
第九章液压系统的设计与计算

按各执行元件在工作中的速度v以及位移s或经历的时间t 绘制v-s或v-t速度循环图。
三、确定液压系统的主要参数
液压系统的主要参数——工作压力和流量是选择液压元 件的主要依据,而系统的工作压力和流量分别取决于液压执 行元件工作压力、回路上压力损失和液压执行元件所需流量 、回路泄漏,所以确定液压系统的主要参数实质上是确定液 压执行元件的主要参数。 1. 初选液压系统的主要参数 执行元件工作压力是确定其结构参数的重要依据。工作 压力选得低一些,对液压系统工作平稳性、可靠性和降低噪 声等都有利,但对液压系统和元件的体积、重量就相应增大 ;工作压力选得过高,虽然液压元件结构紧凑,但对液压元 件材质、制造精度和密封要求都相应提高,制造成本也相应 提高。执行元件的工作压力一般可根据负载进行选择。
二、液压系统的工况分析和系统的确定
对执行元件负载分析与运动分析,也称为液压系统的工 况分析。工况分析就是分析每个液压执行元件在各自工作过 程中负载与速度的变化规律,一般执行元件在一个工作循环 内负载、速度随时间或位移而变化的曲线——用负载循环图 和速度循环图表示。 1. 负载分析 液压缸与液压马达运动方式不同,但他们的负载都是由 工作负载、惯性负载、摩擦负载、背压负载等组成的。 (1) 工作负载 FW 包括切削力、夹紧力、挤压力、重力等, 其方向与液压缸运动方向相反时为正,相同时为负;
2. 确定执行元件的主要结构参数 (1)确定液压缸主要结构参数 根据负载分析得到的最
大负载Fmax和初选的液压缸工作压力p,再设定液压缸回
油腔背压pb以及杆径比d/D,即可由第四章中液压缸的力 平衡公式来求出缸的内径D、活塞杆直径d和缸的有效工作
面积A,其中D、d值应圆整为标准值 。
(2)确定液压马达排量VM 排量VM 由马达的最大负载扭矩Tmax、
液压系统设计方法

液压系统设计方法液压系统是一种通过液体传递能量的系统,广泛应用于各种工业和机械设备中。
液压系统设计的目标是实现高效、可靠的能量传递和控制,同时满足系统的性能要求。
下面是液压系统设计的一般方法和步骤。
第一步:明确系统的工作要求在液压系统设计之前,首先需要明确系统的工作要求,包括工作条件、所需输出力或动力、速度和精度要求等。
这些要求将直接影响到系统的设计和选型。
第二步:选择液压元件在液压系统中,液压元件起到能量传递和控制的作用。
选择适合系统要求的液压元件是液压系统设计的核心步骤之一、常见的液压元件包括液压泵、阀门、缸体、马达等。
在选择液压元件时,需要考虑其技术参数、工作压力范围、流量要求、密封性能和可靠性等。
第三步:设计液压系统布局液压系统布局是指液压元件在系统中的位置和连接方式。
液压系统布局的设计直接影响液压系统的性能和工作效率。
在设计液压系统布局时,需要考虑以下几个因素:1.系统的可维修性和易操作性,便于维护和检修。
2.尽量减少管路的长度和对流动的阻力,提高系统的工作效率。
3.避免液压元件之间的相互干扰和干涉,确保系统的正常工作。
第四步:计算和选择液压元件参数在设计液压系统时,需要计算和选择液压元件的参数。
例如,液压泵的流量和压力选择要根据系统的工作需求来确定,阀门的开口面积需要根据所需流量来计算,缸体的尺寸和活塞面积需要根据所需输出力来选择等。
第五步:进行系统的动态和静态模拟在液压系统设计的过程中,进行系统的动态和静态模拟可以帮助工程师预测系统的性能和响应。
动态模拟可以用于分析系统的运动特性和响应时间,判断系统是否满足要求;静态模拟可以用于分析系统的压力分布和流动性能,优化设计。
第六步:进行系统的试验验证总结:。
液压系统的设计与优化
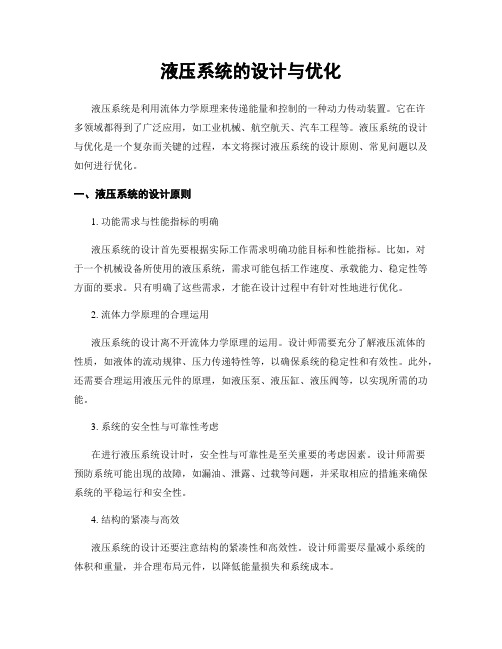
液压系统的设计与优化液压系统是利用流体力学原理来传递能量和控制的一种动力传动装置。
它在许多领域都得到了广泛应用,如工业机械、航空航天、汽车工程等。
液压系统的设计与优化是一个复杂而关键的过程,本文将探讨液压系统的设计原则、常见问题以及如何进行优化。
一、液压系统的设计原则1. 功能需求与性能指标的明确液压系统的设计首先要根据实际工作需求明确功能目标和性能指标。
比如,对于一个机械设备所使用的液压系统,需求可能包括工作速度、承载能力、稳定性等方面的要求。
只有明确了这些需求,才能在设计过程中有针对性地进行优化。
2. 流体力学原理的合理运用液压系统的设计离不开流体力学原理的运用。
设计师需要充分了解液压流体的性质,如液体的流动规律、压力传递特性等,以确保系统的稳定性和有效性。
此外,还需要合理运用液压元件的原理,如液压泵、液压缸、液压阀等,以实现所需的功能。
3. 系统的安全性与可靠性考虑在进行液压系统设计时,安全性与可靠性是至关重要的考虑因素。
设计师需要预防系统可能出现的故障,如漏油、泄露、过载等问题,并采取相应的措施来确保系统的平稳运行和安全性。
4. 结构的紧凑与高效液压系统的设计还要注意结构的紧凑性和高效性。
设计师需要尽量减小系统的体积和重量,并合理布局元件,以降低能量损失和系统成本。
二、液压系统的常见问题与解决方案1. 压力波动与振荡压力波动和振荡是液压系统中常见的问题。
造成这一问题的原因可能有系统的不稳定性、液压元件材料的问题、油液质量的影响等。
解决这一问题的方法包括更换优质的液压元件、调整系统的参数、增加缓冲装置等。
2. 漏油与泄露漏油与泄露是液压系统中常见的问题,可能导致系统能量损失、无法正常工作甚至系统故障。
解决这一问题需要检查液压元件的密封性能、使用优质的密封件,并定期进行检修和维护。
3. 能量损失与效率低下液压系统中存在能量损失和效率低下的问题,主要表现为泄露损失、摩擦损失和流量控制不当等。
为了提高系统的效率,设计师可以采用高效的元件、优化管路布局、减小流量损失等。
- 1、下载文档前请自行甄别文档内容的完整性,平台不提供额外的编辑、内容补充、找答案等附加服务。
- 2、"仅部分预览"的文档,不可在线预览部分如存在完整性等问题,可反馈申请退款(可完整预览的文档不适用该条件!)。
- 3、如文档侵犯您的权益,请联系客服反馈,我们会尽快为您处理(人工客服工作时间:9:00-18:30)。
液压系统的设计计算液压系统设计计算是液压液压传动课程设计的主要内容包括明确设计要求进行工况分析、确定液压系统主要参数、拟定液压系统原理图、计算和选择液压件以及验算液压系统性能等。
现以一台卧式单面多轴钻孔组合机床动力滑台液压系统为例,介绍液压系统的设计计算方法。
1 设计要求工况分析设计要求要求设计的动力滑台实现的工作循环是:快进→工进→快退→停止。
主要性能参数与性能要求如下:切削阻力42000L F N =;运动部件所受重力7200G N =;快进、快退速度m s 13ν=ν=0.1/,工进速度m s -32ν=0.85⨯10/;快进行程1260mm L =,工进行程2130mm L =;往复运动的加速时间t 0.2s ∆=;动力滑台采用平导轨,静摩擦系数0.2s μ=,动摩擦系数0.1d μ=。
液压系统执行元件选为液压缸。
负载与运动分析(1)工作负载 工作负载即为切削阻力42000L F N =。
(2)摩擦负载 摩擦负载即为导轨的摩擦阻力: 静摩擦阻力 0.272001440fs s F G N =μ=⨯= 动摩擦阻力 0.17200720fd d F G N =μ=⨯= (3)惯性负载 72000.1360100.2i G F N N g t ∆ν==⨯=∆ (4)运动之间快进 311126010 2.60.1L t s s -⨯===ν工进 3223213010152.940.8510L t s s --⨯===ν⨯ 快退 ()3333260130103.90.1L t s s -+⨯===ν设液压缸的机械效率0.9cm η=,得出液压缸在各工作阶段的负载和推力,如表1所列。
表1 液压缸各阶段的负载和推力根据液压缸在上述各阶段内的负载和运动时间,即可绘制出负载循环图F t -和速度循环图t ν-,如图1所示。
2 确定液压系统主要参数初选液压缸工作压力所设计的动力滑台在工进时负载最大,在其它工况负载都不太高,参考表2和表3,初选液压缸工作压力1 4.5p MPa =。
计算液压缸主要尺寸鉴于动力滑台快进和快退速度相等,这里的液压缸可选用单活塞杆式差动液压缸(),快进时液压缸差动连接。
工进时为防止孔钻通时负载突然消失发生前冲现象,液压缸的回油腔应有背压,参考表4选此背压为2 1.0p MPa =。
表4 执行元件背压力注:1ν—无杆腔进油时活塞运动速度;2ν—有杆腔进油时活塞运动速度。
由式1122cmFp A p Aη-=得242162142720119101.00.9 4.51022cmFA m mppη-===⨯⎛⎫⎛⎫⨯-⨯- ⎪⎪⎝⎭⎝⎭则活塞直径0.123123D m mm====参考表5及表6,得0.7187d D mm≈=,圆整后取标准数值得125D mm=,90d mm=。
由此求得液压缸两腔的实际有效面积为2224210.1251231044DA m mππ-⨯===⨯()()222224220.1250.0959.11044A D d m mππ-=-=⨯-=⨯根据计算出的液压缸的尺寸,可估计出液压缸在工作循环中各个阶段的压力、流量和功率,如表7所列,由此绘制的液压缸工况如图2所示。
注:1.p ∆为液压缸差动连接时,回油口到进油口之间的压力损失,取p=0.5MPa ∆。
2.快退时,液压缸有杆腔进油,压力为1p ,无杆腔回油,压力为2p 。
3 拟定液压系统原理图选择基本回路(1)选择调速回路 由图2可知,这台机床液压系统功率较小,滑台运动速度低,工作负载为阻力负载且工作中变化小,故可选用进口节流调速回路。
为防止孔钻通时负载突然消失引起运动部件前冲,在回油路上加背压阀。
由于系统选用节流调速方式,系统必须为开式循环系统。
(2)选择油源形式 从工况图可以清楚看出,在工作循环内,液压缸要求油源提供快进、快退行程的低压大流量和工进行程的高压小流量的油液。
最大流量与最小流量之比()2max min q /0.64/1.051061q -=⨯≈;其相应的时间之比()t 2.6 3.9/152.940.043=+=132(+t )/t 。
这表明在一个工作循环中的大部分时间都处于高压小流量工作。
从提高系统效率、节省能量角度来看,选用单定量泵油源显然是不合理的,为此可选用限压式变量泵或双联叶片泵作为油源。
考虑到前者流量突变时液压冲击较大,工作平稳性差,且后者可双泵同时向液压缸供油实现快速运动,最后确定选用双联叶片泵方案,如图2a 所示。
(3)选择快速运动和幻换向回路 本系统已选定液压缸差动连接和双泵供油两种快速运动回路实现快速运动。
考虑到从工进转快退时回油路流量较大,故选用换向时间可调的电液换向阀式换向回路,以减小液压冲击。
由于要实现液压缸差动连接,所以选用三位五通电液换向阀,如图2b 所示。
(4)选择速度换接回路 由于本系统滑台由快进转为工进时,速度变化大(()312/0.1/0.8510118υυ-=⨯≈),为减少速度换接时的液压冲击,选用行程阀控制的换接回路,如图2c 所示。
(5)选择调压和卸荷回路 在双泵供油的油源形式确定后,调压和卸荷回路问题都已经基本解决。
即滑台工进时,高压小流量泵的出口压力由油源中的溢流阀调定,无需另设调压回路。
在滑台工进和停止时,低压大流量泵通过液控顺序阀卸荷,高压小流量泵在滑台停止时虽未卸荷,但功率损失较小,故可不需再设卸荷回路。
图2 选择的基本回路组成液压系统将上面选出的液压基本回路组合在一起,并经修改和完善,就可得到完整的液压系统工作原理图,如图3所示。
在图3中,为了解决滑台工进时进、回油路串通使系统压力无法建立的问题,增设了单向阀6。
为了避免机床停止工作时回路中的油液流回油箱,导致空气进入系统,影响滑台运动的平稳性,图中添置了一个单向阀13。
考虑到这台机床用于钻孔(通孔与不通孔)加工,对位置定位精度要求较高,图中增设了一个压力继电器14。
当滑台碰上死挡块后,系统压力升高,它发出快退信号,操纵电液换向阀换向。
图3 整理后的液压系统原理图4 计算和选择液压件确定液压泵的规格和电动机功率 (1)计算液压泵的最大工作压力小流量泵在快进和工进时都向液压缸供油,由表7可知,液压缸在工进时工作压力最大,最大压力为1 3.95p MPa =,如在调速阀进口节流调速回路中,选取进油路上的总压力损失1.0p MPa ∑∆=,考虑到压力继电器的可靠动作要求压差0.5e p MPa ∆=,则小流量泵的最高工作压力估算为11(3.95 1.00.5) 5.45p e p p p p MPa MPa ≥+∑∆+∆=++=大流量泵只在快进和快退时向液压缸供油,由表7可见,快退时液压缸的工作压力为1 1.24p MPa =,比快进时大。
考虑到快退时进油不通过调速阀,故其进油路压力损失比前者小,现取进油路上的总压力损失0.3p MPa ∑∆=,则大流量泵的最高工作压力估算为21(1.240.3) 1.54p p p p MPa MPa ≥+∑∆=+=(2)计算液压泵的流量由表7可知,油源向液压缸输入的最大流量为330.6410/m s -⨯,若取回路泄漏系数 1.1K =,则两个泵的总流量为33331 1.10.6410/0.70410/42.24/min p q Kq m s m s L --≥=⨯⨯=⨯=考虑到溢流阀的最小稳定流量为3/min L ,工进时的流量为531.0510/0.63/min m s L -⨯=,则小流量泵的流量最少应为3.63/min L 。
(3)确定液压泵的规格和电动机功率根据以上压力和流量数值查阅产品样本,并考虑液压泵存在容积损失,最后确定选取YB-6/40型双联叶片泵。
其小流量泵和大流量泵的排量分别为6/mL r 和40/mL r ,当液压泵的转速960/min p n r =时,其理论流量分别为5.76/min L 和38.4/min L ,若取液压泵容积效率0.9v η=,则液压泵的实际输出流量为 ()()1269600.9/1000409600.9/1000/min 5.1834.56/min 39.74/minp p p q q q L L L =+=⨯⨯+⨯⨯=+= 由于液压缸在快退时输入功率最大,若取液压泵总效率0.8P η=,这时液压泵的驱动电动机功率为6331.541042.2410 1.36600.810p ppp q P KW KW η-⨯⨯⨯≥==⨯⨯ 根据此数值查阅产品样本,选用规格相近的型电动机,其额定功率为KW ,额定转速为960/min r 。
确定其它元件及辅件(1)确定阀类元件及辅件根据系统的最高工作压力和通过各阀类元件及辅件的实际流量,查阅产品样本,选出的阀类元件和辅件规格如表8所列。
其中,溢流阀9按小流量泵的额定流量选取,调速阀4选用型,其最小稳定流量为/min L ,小于本系统工进时的流量/min L 。
*注:此为电动机额定转速为时的流量。
(2)确定油管在选定了液压泵后,液压缸在实际快进、工进和快退运动阶段的运动速度、时间以及进入和流出液压缸的流量,与原定数值不同,重新计算的结果如表9所列。
由表9可以看出,液压缸在各阶段的实际运动速度符合设计要求。
根据表9数值,按表10推荐的管道内允许速度取/m s υ=,由式d =杆腔和有杆腔相连的油管内径分别为d mm ===d mm ===为了统一规格,按产品样本选取所有管子均为内径、外径的号冷拔钢管。
(3)确定油箱油箱的容量按式pn V q α=估算,其中α为经验系数,低压系统,α=;中压系统,α=;高压系统,α=。
现取α=,得pn V q L L α===5 验算液压系统性能验算系统压力损失由于系统管路布置尚未确定,所以只能估算系统压力损失。
估算时,首先确定管道内液体的流动状态,然后计算各种工况下总的压力损失。
现取进、回油管道长为l m =,油液的运动粘度取2/v m s =,油液的密度取3/kg m ρ=。
判断流动的状态在快进、工进和快退三种工况下,进、回油管路中所通过的流量以快退回油流量2/min q L =为最大,此时,油液流动的雷诺数4e d q R v dvυπ====也为最大。
因为最大的雷诺数小于临界雷诺数(2000),故可推出:各种工况下的进、回油路中的油液的流动状态全为层流。
计算系统压力损失将层流流动状态沿程阻力系数75754e dv R qπλ== 和油液在管道内流速 24q dυπ=同时代入沿程压力损失计算公式212l p d υλρ∆=,并将已知数据代入后,得 144752vlp q q q d ρπ⨯∆===可见,沿程压力损失的大小与流量成正比,这是由层流流动所决定的。
在管道结构 尚未确定的情况下,管道的局部压力损失p ζ∆常按下式经验计算10.1p p ζ∆=∆各工况下的阀类元件的局部压力损失可根据下式计算2v n n q p p q ⎛⎫∆=∆ ⎪⎝⎭其中的n p ∆由产品样本查出,n q 和q 数值由表8和表9 列出。