结晶器漏钢预报系统 文献综述
结晶器漏钢预报专家系统(优选.)

·现场经验·结晶器漏钢预报专家系统刘玉玲①(济钢第三炼钢厂 山东济南250101)摘要 着重介绍了济钢第三炼钢厂结晶器专家系统的软硬件组成和数据通信的实现。
关键词 结晶器漏钢 专家预报系统 模型 通信Foreca st Expert Syste m of M old BreakoutL iu Yuling(J inan Ir on and Steel Co.,L td.)ABSTRACT The hard ware and s oft w are of mold breakout expert syste m and how t o realize communicati on bet w een the m are intr ouduced detailedly.KE YWO R D S Mold breakout Forecast expert syste m Model Communicati on1 前言济钢第三炼钢厂结晶器漏钢预报专家系统是从奥钢联(VA I)连铸自动化中引进的一项关键技术,它是在生产过程中对连铸机结晶器内部进行观察和预防漏钢的工具,通过实时观察结晶器状况以监测不稳定和临界的浇铸情况,及时进行漏钢预报避免铸机漏钢,还可以通过结晶器的历史数据来分析浇铸问题。
因此它在连铸生产中有着至关重要的作用。
2 专家系统功能简介第三炼钢厂引进的结晶器漏钢预报专家系统,除了热电偶检测漏钢的预报系统之外,还包括了结晶器热力学检测系统和结晶器振动摩擦力检测系统,它实现连铸机生产过程结晶器内部的可视化和漏钢保护。
因此它是一个融合了金属热力学、计算机技术、图形可视化技术、数学模型优化技术等多项技术的综合系统。
3 结晶器专家系统组成结晶器专家是一个独立的系统,其硬件和软件是模块式构建的。
其所需的信号是直接测量的,或是从其他系统(例如P LC系统)收集来的。
1)专家系统硬件构成铸机结晶器专家系统作为一种新型智能设备,组成包括仪表、计算机等多个设备,其硬件组成示意图如图1所示。
降低结晶器漏钢预报系统的误报率

降低结晶器漏钢预报系统的误报率作者:罗霄来源:《科学与财富》2017年第18期摘要:结合马钢四钢轧实际生产情况,基于SMS-DEMAG的漏钢预报系统(BPS)的基本原理,分析了影响该厂BPS误报的原因主要是温度梯度报警值、结晶器保护渣、结晶器铜板厚度、结晶器热电偶漏水等。
通过优化温度梯度报警门槛值,优化保护渣性能,采用铜板厚度补偿功能,优化热电偶密封垫圈性能等措施后,BPS误报率月平均值由0.80%下降到0.11%。
关键词:漏钢预报;报警值;保护渣;铜板厚度;热电偶密封目前钢铁行业已步入微利时代,钢铁生产环节降本增效已成为钢铁企业提高经济效益的主要措施之一。
结晶器漏钢预防系统(BPS)是为了预防连铸生产过程出现粘接漏钢事故的重要措施,但是系统误报警不仅严重影响连铸生产顺行,还会造成连铸非稳态浇铸,增加连铸坯夹杂物含量,降低铸坯等级,造成额外的经济损失,因此降低BPS系统误报具有非常重要的意义。
1生产现状2013年马钢第四钢轧总厂1、2#机BPS系统的平均报警率为0.80%,但其中误报次数占报警总次数的比例平均高达96.25%,系统误报已经严重制约了提高铸坯质量、降低生产成本这一目标的实现。
因此,马钢第四钢轧总厂基于SMS-DEMAG的BPS的基本原理[1],找出影响其误报的主要原因,制定工艺改善措施,降低其误报率。
2影响BPS误报的因素分析2.1BPS的基本原理添加BPS报警的基本原理系统每250ms对热电偶进行一次取值计算,热电偶每次所测温度值与前一次所测温度值的差值若超过系统设定的温度梯度报警值,则引起BPS系统报警。
2.2温度梯度的报警值温度梯度是BPS系统中一个重要的参数,温度梯度报警值设置过大,则会导致不能对有效的起到漏钢预报作用,反之则会增加大量误报警次数,所以合理的温度梯度报警值对BPS 的误报影响明显[2~3]。
2.3结晶器保护渣结晶器保护渣是铸坯向结晶器传热的重要介质,对结晶器均匀传热,形成均匀生长的坯壳有着至关重要的作用[3]。
漏钢预报管理

漏钢预报管理漏钢预报管理是钢铁行业中一项重要的生产管理技术,它可以帮助企业准确预测和控制漏钢现象,提高生产效率和产品质量。
本文将从漏钢的定义、原因、预测方法和管理措施等方面进行探讨。
我们来了解一下什么是漏钢。
漏钢是指在连铸过程中,由于各种原因导致钢水在连铸机结晶器到达浇口之前流失的现象。
漏钢不仅会造成资源浪费,还会影响产品质量,甚至导致事故发生。
因此,预测和管理漏钢现象对于钢铁企业来说至关重要。
那么,导致漏钢现象的原因有哪些呢?首先,连铸机设备的故障是导致漏钢的主要原因之一。
设备的不合理设计、磨损和老化等问题都可能导致钢水漏出。
其次,操作人员的不当操作也是导致漏钢的一个重要原因。
操作不规范、操作技术不熟练等都会增加漏钢的风险。
此外,钢水的温度、浇注速度、结晶器的结构等因素也会对漏钢产生影响。
针对漏钢现象,我们可以采取一些预测方法来提前预警和预防。
首先,通过连铸机设备的监测和检测系统,可以实时监测设备的运行状态,并及时发现设备故障。
其次,可以通过对操作人员进行培训和考核,提高其操作技术和意识,减少人为因素对漏钢的影响。
此外,还可以通过温度、浇注速度等参数的实时监控,及时调整操作参数,降低漏钢风险。
除了预测方法,科学的漏钢预报管理也是非常重要的。
首先,需要建立完善的数据采集和分析系统,对连铸过程中的各种参数进行收集和分析,找出与漏钢相关的规律和因素。
其次,需要建立漏钢预报模型,通过对历史数据的分析和建模,预测钢水漏出的可能性和程度。
最后,根据预测结果,制定相应的管理措施,减少漏钢风险。
在漏钢预报管理中,还需要注意一些关键问题。
首先,需要确保数据的准确性和及时性,只有准确的数据才能进行有效的预测和管理。
其次,需要加强对设备和操作人员的监督和管理,确保设备正常运行和操作规范。
此外,还需要进行定期的漏钢风险评估,及时发现和解决潜在的风险隐患。
漏钢预报管理是钢铁行业中一项重要的生产管理技术,它可以帮助企业准确预测和控制漏钢现象,提高生产效率和产品质量。
结晶器漏钢预报专家系统
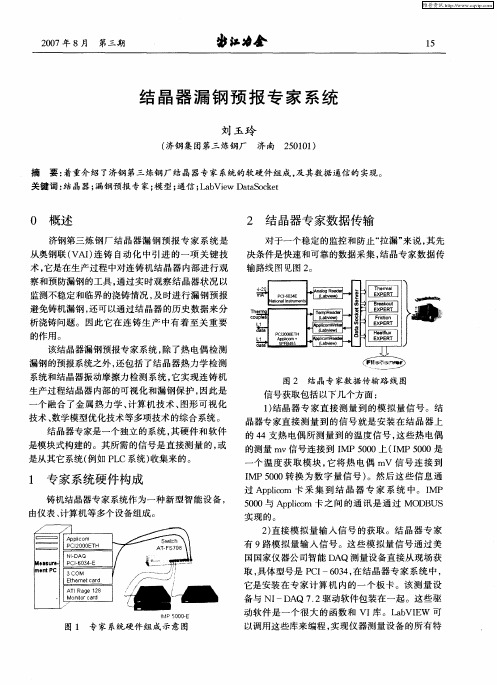
技术 、 学模 型优化技 术 等多项 技术 的综 合系统 。 数 结 晶器专 家是一 个独 立 的系 统 , 硬 件 和 软件 其
是模块式构建 的。其所需的信号是直接测量 的, 或
是从 其它 系统 ( 如 P C系统 ) 例 L 收集来 的 。
的 4 支热 电偶所测量到 的温度信号 , 4 这些热电偶 的测 量 rV信 号连 接 到 I 0 0上 (M 0 0是 f l MP5 0 I 50 P
察和预 防漏钢 的工 具 , 过 实时 观察 结 晶器 状 况 以 通
2 结晶器专 家数据传输
对 于一个 稳定 的监 控 和防 止 “ 漏 ” 说 , 拉 来 其先 决 条件 是快 速和可 靠 的数据 采 集 , 晶专 家数 据传 结
输 路线 图 见图 2 。
监测不 稳定 和临界 的浇铸 情 况 , 时进 行漏 钢 预 报 及 避 免铸 机漏钢 , 可 以通 过结 晶器 的历史 数 据来 分 还 析浇铸 问题 。 因此 它 在 连铸 生 产 中有 着 至 关 重 要 的作 用 。 该 结 晶器漏 钢预 报专 家 系统 , 了热 电偶 检 测 除 漏钢 的预报 系统 之外 , 包 括 了结 晶器 热力 学 检 测 还 系统 和结 晶器振 动摩擦 力检 测 系统 , 实现 连 铸 机 它 生产过 程结 晶器 内部 的可视 化 和漏 钢保 护 , 此 是 因
一
图 2 结 晶专 家数据 传 输路 线 图
信号 获取 包括 以下几 个方 面 : 1结 晶器 专 家 直 接 测 量 到 的模 拟量 信 号 。结 ) 晶器专 家直 接 测 量 到 的 信 号就 是 安 装 在 结 晶 器 上
个 融 合 了金属 热 力 学 、 算 机 技术 、 计 图形 可视 化
钢预报检测系统
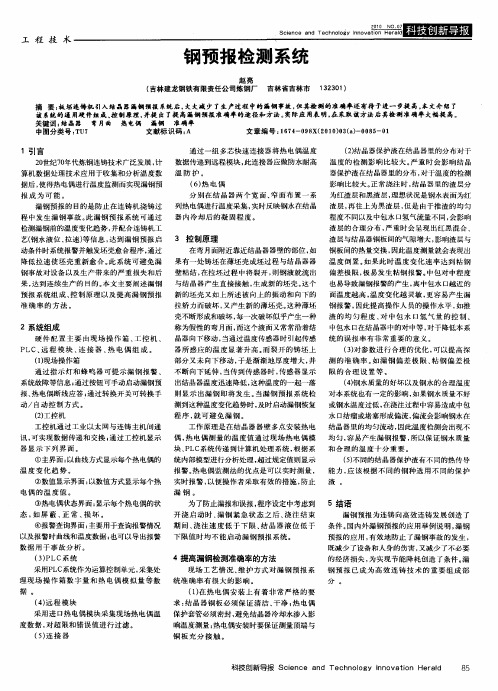
称 为假性的 弯月面 , 而这个 液面又常 常沿着结 中包水 口在结 晶器中的对 中等 , 对于 降低 本系 晶器向下移动 , 当通过温度 传感器时 引起 传感 统 的误 报 率有 非 常重要 的 意义 。 器所 感应 的 温度 显 著升 高 。 裂开 的铸 坯 上 而
部 分又 未 向下 移动 , 于是 渐渐地 厚度 增大 , 并 不 断 向下延伸 , 当传 到传 感器时 , 感器 显示 传
中圈分 类号 :U T7
ห้องสมุดไป่ตู้
文 献标 识码 : A
文 章编 号 :6 4 0 8 (0O0() 0 8— 1 17 — 9 X 2 1)3a一 0 5 0
() 2 结晶器保 护渣在结 晶 器里 的分布 对于 器保 护渣在结 晶器里的分 布 , 对于温度 的检测 影 响比较 大 。 正常浇 注时 , 晶器里 的渣 层分 结
1引 言
通 过一 组 多芯快 速连接 器将 热 电偶温 度
此连接 器应做防水 耐高 温 度 的检 测影 响 比较 大 。 重 时会 影 响结 晶 2 世纪7 年 代炼钢连铸技 术广泛发展 , 0 0 计 数据 传递到远程 模块 , 严
算机数 据处 理技术应 用 于收集 和分 析温 度数 温 防 护 。 据后 , 使得热 电偶进行温度监 测而实现 漏钢预 报成为可能 。
程 中发生 漏钢 事 故 。 漏钢 预报 系 统可 通过 此 ( 热 电 偶 6)
分 别 在 结 晶器 两个 宽 面 、 面 布置 一 系 为红渣 层和黑渣 层 , 窄 理想状况是 钢水表面为红
器 内冷 却 后的 凝 固程 度 。
实时 反映钢水在结 晶 渣 层 , 再往 上为 黑渣 层 , 但是 由于 推渣 的均 匀 漏钢预 报 的 目的 是防止 在连 铸机 浇铸过 列热 电偶进行温 度采集 , 程度不 同以及 中包水 I氢气流量 不同 , Z l 会影响 渣层 的合理 分布 , 重时会 呈现 出红黑 混合 、 严 渣层与结 晶器铜板 间的气隙增大 , 响渣层与 影 温度 倒 置 。 如果 此 时温 度 变化 速率 达 到粘 钢
漏钢预报的原理

同时被拉断的部位因拉坯而向下运动 (5) 当被拉断的部位拉出结晶器下口时就发生
漏钢 由于结晶器是按某一频率 某一规律上 下振
动 发生粘结的坯壳始终向下运动 而发生粘结处 的坯壳不断地被撕裂和重新愈合 所以粘结漏钢部 位的坯壳薄厚不均 振痕紊乱有明显的 V 型缺 口 如图 2 所示 随着不断被撕开及愈合的 V 型缺口下移 坯壳在热电偶上方发生撕裂 撕裂部 位靠近热电偶时热电偶测出温度升高 当撕裂部位 通过热电偶所在位置时温度达到峰值 然后随着撕 裂部位离开热电偶 温度逐渐降低
(3) 由于结晶器振动 新形成的薄坯壳再次被 拉断 然后再次形成薄坯壳
(4) 随着每次振动 重复 2 和 3 的过程
图 3 粘结漏钢预报过程
C-080-10 1
图 4 粘结漏钢前热电偶温度变化(1)和漏钢的极限时间及极限温度变化率 2
在结晶器上水平安装一定数量的热电偶 图 3 口后保证不漏钢 其余 A B C 三点若仅有一点
所示的条件 ;另外到相邻最近的热电偶发生温度变
化的时间 图 4(1)中的 t2 也是一个重要因素 在粘结漏钢预报系统中发生粘结漏钢必须满
坯拉出结晶器后才能不漏钢 则l0 与 H 的关系应
满足
足的三个基本条件是
h = (3l0 − l) ⋅ tga + s
1 θ&≥ θ&cr t1 tcr 表示温度变化率
产 增加维修量和维修成本 而且使机械设备受到 损害 常见的漏钢形式有 因使用不适当的保护渣 或结晶器液面波动大产生的粘结漏钢 结晶器冷却 不均匀 使得凝固坯壳薄厚不均 在薄处易产生裂 纹或者在振痕波谷处产生裂纹拉出结晶器后产生横 裂或纵裂漏钢 中包内的异物或未熔化的保护渣嵌 在凝固坯壳表面 拉出结晶器后由于钢水静压力的 作用在夹杂物位置处漏钢 统称卷渣漏钢 铸造开 始后不久 钢水从引锭头与铸坯的连接处流出来产 生的漏钢 尾坯输出时拉速过快 产生的尾坯甩钢 其它原因产生的漏钢 2 粘结漏钢产生的原因及坯壳特征
提高结晶器漏钢预报专家系统准确率的措施

作者简介:王玉民(1971-),男(汉族),山东长清人,济南钢铁股份有限公司第三炼钢厂连铸车间,工程师。
提高结晶器漏钢预报专家系统准确率的措施王玉民,赵登报,曹运涛,董光军,温维新(济南钢铁股份有限公司第三炼钢厂,山东济南250101)摘 要:通过对影响结晶器专家系统漏钢预报准确率的原因进行分析,实施了相应的改进措施,取得了良好的效果。
关键词:结晶器专家;准确率;措施;效果中图分类号:TF 777 文献标识码:B 文章编号:100221043(2006)022*******Measure for improvement in breakout predictive precisionof mold expert systemWAN G Yu 2min ,ZHAO Deng 2bao ,CAO Yun 2tao ,DON G Guang 2jun ,WEN Wei 2xin(No.3Steel 2making Plant of Jinan Iron &Steel Corporation ,Jinan 250101,China )Abstract :Factors affecting t he precision of t he expert system in prediction of t he mold breakout are analyzed and appropriate counter 2measures adopted and very satisfactory result s achieved as well.K ey w ords :mold expert system ;p recision ;measure ;result 在目前高效连铸生产中,采用结晶器漏钢预报专家系统是减少粘结漏钢的最有效方式之一。
济南钢铁股份有限公司第三炼钢厂(以下简称济钢三炼钢)一号连铸机采用奥钢联(VA I )开发的结晶器粘结漏钢预报专家系统,自2003年3月1日投产以来,已成功预防了多起结晶器粘结漏钢事故,取得了巨大的经济效益;但是在使用过程中专家系统存在误报、漏报的现象,影响生产的高效稳定。
关于对板坯漏钢及结晶器铜板有关情况的调研反馈
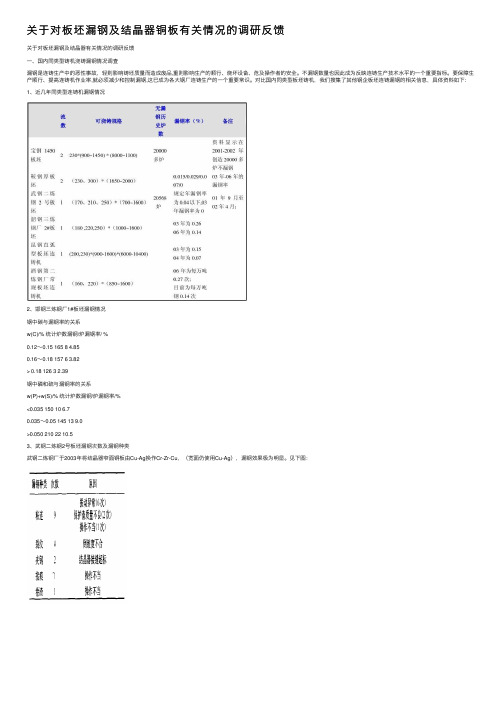
关于对板坯漏钢及结晶器铜板有关情况的调研反馈关于对板坯漏钢及结晶器有关情况的调研反馈⼀、国内同类型铸机浇铸漏钢情况调查漏钢是连铸⽣产中的恶性事故,轻则影响铸坯质量⽽造成废品,重则影响⽣产的顺⾏、烧坏设备、危及操作者的安全。
不漏钢数量也因此成为反映连铸⽣产技术⽔平的⼀个重要指标。
要保障⽣产顺⾏、提⾼连铸机作业率,就必须减少和控制漏钢,这已成为各⼤钢⼚连铸⽣产的⼀个重要常识。
对⽐国内同类型板坯铸机,我们搜集了其他钢企板坯连铸漏钢的相关信息,具体资料如下:1、近⼏年同类型连铸机漏钢情况2、邯钢三炼钢⼚1#板坯漏钢情况钢中碳与漏钢率的关系w(C)/% 统计炉数漏钢/炉漏钢率/ %0.12~0.15 165 8 4.850.16~0.18 157 6 3.82> 0.18 126 3 2.39钢中磷和硫与漏钢率的关系w(P)+w(S)/% 统计炉数漏钢/炉漏钢率/%<0.035 150 10 6.70.035~0.05 145 13 9.0>0.050 210 22 10.53、武钢⼆炼钢2号板坯漏钢次数及漏钢种类武钢⼆炼钢⼚于2003年将结晶器窄⾯铜板由Cu-Ag换作Cr-Zr-Cu,(宽⾯仍使⽤Cu-Ag),漏钢效果极为明显。
见下图:4、攀钢⼀号板坯连铸机5、国内钢企个⼈浇铸不漏钢先进指标1、2007年10⽉,武钢⼆炼钢连铸机长陈建钢连续5年浇钢7500炉50万吨⽆漏钢事故,硅钢浇铸质量合格率99.96%,再次刷新个⼈历史记录。
因此成为武钢的“防漏”专家,被称为“浇钢王”。
2、武钢三炼钢⼚3号连铸机机长马江⽣总结出⼀套预防漏钢的先进操作法。
⾃1998年8⽉以来,浇铸1.1万多炉,300万吨钢⽔不漏钢,创下了个⼈浇铸钢⽔不漏钢的国内最好⽔平。
3、攀钢新钢钒炼钢⼚板坯浇钢⼄班Ⅱ流刘关洪所带领的班组连浇不漏钢炉数达到15004炉,在攀钢率先突破1.5万炉不漏⼤关,这也是国产⼤坯连铸机⾸次达到这⼀⾼度。
一种新的综合型漏钢预报专家系统的研究

3 1 系统原理 . 漏钢事故可分为开浇漏钢、 惫挂漏钢、 裂纹漏钥
( 包括角裂、 纵裂、 横裂)夹渣漏钢、 、 起步漏钢、 剪切 漏钢和粘结性漏钢等 控制漏锅的根本途径是控制 结晶器与坯壳之间的相互作用. 而铸坯质t〔 表面质
量和内在质t) 也与结晶器与坯壳之间的作用行为
洲 一 一
在振动器支架上安装应变仪;) 3 将加速计安装在结
各种专家系统, 将会更精确地监控诸如结晶器铜板 温度、 结晶器器壁和铸坯坯壳之间的摩擦力、 结晶器 的放热量、 结晶器锥度、 结晶器内钢水液面的变化等
工艺参数.
近年来, 国外一些钢厂将拉坯阻力检测法与热 电偶漪量法结合起来使用, 以保证能 10 0%地预报
面质量和连铸机的生产率, 如果超过临界摩擦力, 还
可能发生铸坯粘连和撕裂导致漏钥事故的发生. 结
晶器和板坯之间的摩擦力取决于结晶器保护渣特 性、 钢种、 结晶器振动方式和振动参数等 可见, 要在 摩擦力和拉漏之间建立关系困难很多 目前已经采 用或建议采用定量确定结晶器摩擦力的几种侧量和
分析方法包括`:) '1在结晶 1 器支架上安装测力仪; 2 )
基于工业计算机控制的连铸结晶器漏钢预报系统
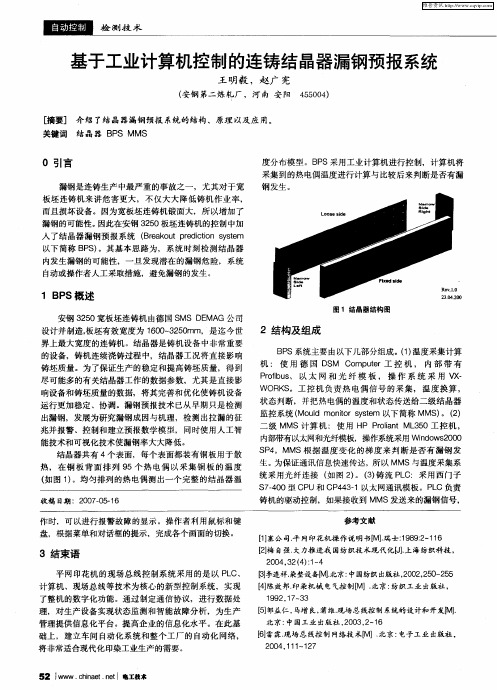
计算机、现场总线等技术为核心 的新型控制系统,实现 了整机的数字化功能。通过制定通信协议,进行数据处 理,对生产设备实现状态监测和智能故障分析,为生产 管理提供信息化平台。提高企业的信息化水平 。在此基
【】 5 邹益仁 , 马增 良, 蒲维. 现场总线控 制 系统的设计和开发M .
算机进行编程,并且通过集成的 WI H 人机界面查看 N M1
每一 个 热 电偶 的 温度 和状态 。系统 网络 如 图 2 。
图 3 各阶段温度梯度
图 2 系统 网络 图
20 1 1 2 0 4. 1 ~1 7
维普资讯
检 测技 术
P C 会 自动 降 低驱 动 拉 速 以保 证 漏 钢 部 位 重 新 接 成 坯 L
I
壳。() 4 工程师站 :工程师站采用德国 Ta s c工控机, rnt e
内部安 装 以太 网卡, 操作 系统 是 Wi o 2 0 。工 程 师 n ws0 0 d 站 利用 S S D M G 公 司的 L g a 软 件 对温 度采 集 计 M EA oi d c
维普资讯
检 测 技 术
基于工业计算机控制的连铸结晶器漏钢预报系统
王 明毅 ,赵 广 宪
( 钢 第二 炼 轧 厂 , 河 南 安 阳 安 450) 5 0 4
[ 摘要] 介绍 了结 晶器漏钢预报 系统 的结构 、原理 以及应 用。
关键 词 结 晶 器 B S MMS P
运 行 更加 稳定 、协调 。漏钢 预 报 技术 已从早 期 只是 检 测
2结构及组成
B S系统主要 由以下几部分组成。() P 1 温度采集计算 机 :使 用 德 国 D M o p tr 控 机 , 内部 带 有 S C m u 工 e Poi s 以 太 网 和 光 纤模 板 , 操 作 系 统 采 用 V ・ rf u 、 b X WO K 。工控机 负责热电偶信号 的采集 ,温度换算 , RS 状态判断,并把热电偶的温度和状态传送给二级结晶器
基于结晶器与坯壳间摩擦力的漏钢预报研究

~
,
C。
一
。
一
,
.
,
一
,
,
,
,
。
,
图4
粘结 漏 钢坯 壳
图5
摩擦 应 力变 小
一
维普资讯
生 长 造成 局 部 坯 壳过 薄 坯 壳 出 结 晶 器 粘结 漏 钢 因 使 用 不 适 当 的 保 护 渣 或结 晶 器 液 面 1 后 如 果 坯 壳 的 厚 度 不 足 以抵 抗 钢 水 的 静 压力 就 会发 生 漏 钢 事故 波动大造成 保护 渣流 动性 差 致使初 生 坯 异 物 卷 入 后 在 坯 壳表 面 或 皮 下 形 成 大 壳在结 晶 器 内形 成局 部 粘 结 点 在拉 坯 状 块 夹 杂 由于 异 物 导热 系 数 和 凝 固 系 数 与钢 态下粘结点处坯 壳被拉断粘结在结 晶器铜 水 不 同 所 以 异 物与坯 壳 之 间存在 裂纹 而 且 板 上 若拉 断 坯 壳 到 了 结 晶 器 下 口 气 隙 区 随 坯 壳 向下 运 动 裂 纹 在 逐 渐扩 大 异 物 卷 仍 无 法焊 合 将 发 生 粘结 漏 钢 铸 坯 发 生 粘 在坯 壳 处导 致热 流分 布不 均 坯 壳薄厚 不 均 结 时 首 先 在坯 壳表 面 有 粘 结 点 结 晶 器 上 下 便形 成 条波 在该处 产 生 较 大 的 热应 力 在钢水 静 压 力作 每振 动 次 在撕 裂线 用下 坯 壳外鼓 所 以 结 晶 器 摩擦 力逐 渐 增 大 纹 线 即断 裂线 该 线 相 对 水平 线 几 乎 接 近 45 30 且漏 随 异 物拉 出结 晶 器 摩擦 力减 小 并恢 复正 常 最大 剪切 应 力 方 向成 角 如 图 8 所示 坯 表 面 呈 现 典 型 的 V 型 缺 口 且 振痕 钢板 4 所示 综 上 所述 坯 壳 在结 晶 器 内 发生 粘 结 紊乱 如 图 裂 纹 及 异 物 卷 入 后 结 晶 器 摩擦 力均 有 不 坯 壳 与结 晶 器 铜 板 间 发 生 粘 结 后 当 坯 壳 粘 结 在结 晶 器 铜 板 上 并 随 结 晶 器 起 同 特 征 的 显 著变化 由此 根 据 结 晶 器 摩擦 力的 特 征 变化 可 建 立 基 于 结 晶 器 摩擦 力 的 同 步 上 下 振动 在结 晶 器 液 面 高 度 不 变 漏 钢 预 报 系统 拉 速恒 定 情 况 下 坯 壳 与 铜 板 发 生 粘 结 比 不 发 生 粘 结时 坯 壳 与铜板 间相 对滑 动 面 积 4 粘结 纵 裂 及 及 异 物卷 入 漏 钢 变 小 结 晶 器 摩 擦应 力 显 著 减 小 如 图 5 所
漏钢预报系统的组成和工作原理

漏钢是连铸生产中的重大事故,给钢厂造成很大的经济损失。
为避免漏钢的发生,通过在结晶器内安装热电偶矩阵,分析温度的变化,在发生漏钢之前就能预知漏钢征兆,并及时提醒操作人员或自动地降低拉速在连铸生产过程中,钢坯坯壳由于某种原因,超过其机械强度而破裂,如果该坯壳破裂处未能凝固,则破裂处会以低于拉坯速度向下和横向扩展,当坯壳破裂处到达结晶器底部时,就发生拉漏。
由于坯壳破裂时,钢水直接与结晶器壁接触,因而该处会有温升,这样,如果安装了漏钢预报系统,便可以通过分析分布在结晶器壁上的热电偶采集到的温度变化,得知坯壳破裂处及其扩展,从而检测出漏钢趋势并进行报警及采取相应的处理。
RAMON漏钢预报系统是镭目公司十几年来在连铸自动化测控领域不断开发、实践、应用过程中的技术成果,它包含了镭目公司最新的模糊控制和神经网络技术,能够更准确地对漏钢进行预报。
组成漏钢预报系统主要由两部分组成:检测系统与控制系统。
检测系统包括热电偶矩阵、热电偶模块、总线通信网络、PLC等,主要负责采集实时数据(温度、拉速、液位等);控制系统包括数据分析处理单元、操作箱、PLC等,主要负责对数据进行分析,输出分析结果,并通过控制拉速达到消除漏钢隐患的目的。
漏钢预报系统的特点主要表现在数据分析处理的算法与优化的方法上,因各研究方向不同而存在差异。
目前国内外普通采用的是基于逻辑分析的漏钢预报模型,这种模型在很大程度上依赖于现场具体的设备和工艺条件,预报数学模型中各种参数的最佳值是根据系统投入运行前对现场测试后确定的。
因此,这种最佳值无法适应实际生产中的变化因素,如改变钢种后,其参数值必须重新进行测试后才能达到最佳效果。
结果是减少了漏报率而导致了高误报率的出现,而降低误报率又会引起漏报的增加。
镭目公司的RAMON漏钢预报系统采用了最新的神经网络模型进行漏钢分析。
神经网络分析系统具有自学习、自调整能力,即通过一定的学习规则学习新的报警样本,并具有记忆功能,故整个系统可以根据自身学习获得的知识对漏钢征兆做出准确的判断,能更好地适应现场不同的生产条件及工艺参数。
漏钢预报讲稿

钢铁研究总院
连铸技术国家工程研究中心
首钢京唐联合有限责任公司
2012年9月8日
NERC CCT
个人简介
• 席常锁,高级工程师(教授级) • 工作单位:钢铁研究总院连铸中心 • 连铸技术国家工程研究中心 • 1962年7月生人,1984年7月,东北工学院冶金 物理化学专业毕业。 • 毕业后至今一直在钢铁研究总院从事钢铁冶金 及相关技术的科研开发工作,特别是在连铸及 相关领域,包括板坯连铸漏钢预报系统开发, 铸坯质量、结晶器保护渣,连铸过程关键工艺 参数的检测技术及分析等领域。
2.3、描述铸坯粘结发生的数学模型
对上页公式的说明
此不等式的右边数值越小,或者不等式左边的数值越大,则凝壳越不容 易被撕裂。由此式可以推断各种因素对粘结的影响。 由上式可知,振动频率f与振幅h的乘积越大,则上式右边数值越大。通 常连铸机生产过程中,固定振幅而调整振动频率。因此,在通常情况下, f越大,则上式右边数值越大。这表明结晶器振动频率较高时,结晶器内 凝壳容易撕裂。 K越小,则上式左边数值越小。这表明凝固系数较小时,凝壳撕裂的敏 感性增加。 V越大,则上式右边数值越大。这表明拉坯速度高时,凝壳撕裂的敏感 性增加。 μ越大,则上式右边数值越大。这表明保护渣粘度高时,凝壳撕裂的敏 感性增加。 σ值反映的是钢种性能的影响。上式表明,高温强度低的钢种凝壳撕裂 的敏感性较大。 NERC
据文献报道和相关资料调研显示,国外早在20世纪80年代就针 对连铸过程粘结漏钢预报模型开始了实质性研究,并实现了工业
化应用。目前国外应用比较典型漏钢预报技术包括有:美国
Inspat Inland公司的Pilot结晶器在线监控系统、日本Kawasaki (川崎)钢铁公司的单排热电偶监测系统、美国LTV钢铁公司的
- 1、下载文档前请自行甄别文档内容的完整性,平台不提供额外的编辑、内容补充、找答案等附加服务。
- 2、"仅部分预览"的文档,不可在线预览部分如存在完整性等问题,可反馈申请退款(可完整预览的文档不适用该条件!)。
- 3、如文档侵犯您的权益,请联系客服反馈,我们会尽快为您处理(人工客服工作时间:9:00-18:30)。
内蒙古科技大学信息工程学院测控专业毕业实习报告——文献综述题目:结晶器漏钢预报热电偶温度数据采集系统设计学生姓名:张超学号:0867112337专业:测控技术与仪器班级:测控2008-3指导教师:李文涛(教授)一、前言1.1 连铸技术连续铸造技术,简称连铸,是一种使钢水不断地通过水冷结晶器,凝成硬壳后从结晶器下方出口连续拉出,经喷水冷却,全部凝固后切成坯料的一种铸造工艺如图1.1所示。
连铸具有工艺简短、金属收得率高、能源消耗低、铸坯质量好、品种多‘2捌、生产过程机械化、自动化程度高等优点,其应用彻底改变了铸造车间的生产流程和物流控制,为生产的连续化、自动化和信息化技术的应用,以及大幅度改善环境和提高产品质量提供了条件[1]。
图1.1 连铸全过程1.2 漏钢在连铸生产过程中,如果结晶器中形成的固化坯壳由于某种原因发生破裂,而破裂口又不能在该段铸坯被拉出结晶器之前重新固化弥合,就会发生结晶器及铸坯中尚未凝固的钢水突然泄漏的事故,这种事故称为漏钢(breakout)。
漏钢是连铸生产最严重的事故之一,漏钢带来的直接经济损失及对生产组织的有序性都有巨大的影响。
因此,减少漏钢的发生频率成为连铸技术人员关注的重点之一。
冶金工作者通过借鉴以往大量漏钢的经验,并结合数学模型形成了基于各种原理的结晶器漏钢预报系统,通过不断地改进完善,目前漏钢预报系统已广泛应用于连铸生产中[2-3]。
结晶器漏钢预报系统构成如图1.2 所示。
该系统主要包括:温度数据采集系统、基础控制程序和计算机分析处理应用软件。
图1.2 结晶器漏钢预报系统结构示意图温度数据采集系统通过采用安装在结晶器铜板上的K 型热电偶进行铜板温度的测量与传输,热电偶的布置为结晶器铜板内外弧宽边各若干列;基础控制程序根据铸机浇注的断面尺寸进行热电偶选择,并将实时的温度测量数据显示在界面上;计算机分析处理应用软件把采集到的实时数据通过模型进行对比逻辑判断分析,当达到报警设定值时,将会反馈信号进行报警。
在连铸生产过程中,漏钢不仅会影响连铸生产,增加维修量和维修成本,而且使机械设备受到损害。
常见的漏钢形式有:1.3 裂纹漏钢开浇漏钢是指引锭头刚拉出结晶器下口即漏钢,主要原因是:塞引锭头时加入冷料过多或过少、杂质过多或有油污、引锭头与结晶器壁间的缝隙没有塞严、出苗时间短、开浇时钢流过大将冷料冲散等; 设备原因有结晶器与扇形段对弧不准等情况都极易产生开浇漏钢[4]。
裂纹坯的表面纵裂纹在结晶器内产生, 由于热流分布不均匀, 造成坯壳生长厚度不均漏钢形成的机理铸, 在坯壳薄的地方产生应力集中; 静压力随坯壳往下移动呈直线增加, 静压力使得坯壳往外鼓, 表面裂纹进一步扩展,从而导致纵裂漏钢。
裂纹漏钢坯壳特征纵裂坯壳特征是铸机在拉钢过程中沿板坯纵向产生近似直线裂纹, 由该裂纹产生的漏钢如图3, 在板坯表面产生圆饼状叠层, 其中部凹陷。
通过纵裂漏钢产生部位分析, 裂纹多产生在宽面中心线左右各1/ 4 区域内距弯月面100 ~ 150mm, 裂纹宽度5mm< < 10mm。
板坯角部纵裂漏钢是由于钢水的硫含量偏高, 加上过小的结晶器倒锥度, 板坯窄面发生鼓肚, 撕裂薄弱的坯壳, 造成漏钢。
角裂坯壳特征: 板坯角部纵裂位于四个角部, 棱角向下10 ~ 30mm 以内, 此部位是坯壳最薄的地方, 沿纵向呈条状突棱。
图3 板坯表面纵裂坯壳1.4悬挂漏钢结晶器内初生坯壳局部和结晶器铜板内腔或角缝挂住,或由于冒钢造成坯壳与结晶器上沿挂住而引起的漏钢。
通常是由于结晶器角缝过大, 结晶器铜板内腔表面变形等原因导致悬挂漏钢[5]。
1.5 粘接漏钢在钢水浇铸过程中,结晶器弯月面的钢水处于异常活跃的状态,如果浇铸过程中流入结晶器与坯壳之间的液态渣被阻断,并且结晶器铜板与初生坯壳摩擦力大于初生坯壳的强度时,初生坯壳被拉断,与铜板产生粘结。
这时被粘着的铸坯和向下拉的铸坯的界面凝固壳破裂,在破裂处流入钢液,重新形成新的很薄的坯壳。
在振动和滑动时该坯壳又被拉断,钢液补充后又形成另外一个新的薄的坯壳。
这一过程反复进行,直到新坯壳达到结晶器出口后就会漏钢[5]。
2 粘结漏钢产生的原因及坯壳特征发生粘结漏钢的原因是由于使用不适当的保护渣或结晶器液面控制不好,造成液面波动使凝固坯壳与结晶器铜板粘结[6]。
粘结漏钢发生过程如图1.5所示,图1.5 粘接漏钢过程图中:(1)粘在结晶器铜板上的坯壳(A)与向下拉的坯壳(B)被撕开一条裂缝。
(2)紧接着钢水流入坯壳(A)和(B)之间的裂缝并形成新的坯壳(C),这时坯壳外表面形成皱纹状痕(D)。
(3)由于结晶器振动,新形成的薄坯壳再次被拉断,然后再次形成薄坯壳。
(4)随着每次振动,重复(2)和(3)的过程,同时被拉断的部位因拉坯而向下运动。
(5)当被拉断的部位拉出结晶器下口时就发生漏钢[7-8]。
图1 粘结漏钢发生过程由于结晶器是按某一频率,某一规律上、下振动,发生粘结的坯壳始终向下运动,而发生粘结处的坯壳不断地被撕裂和重新愈合,所以粘结漏钢部位的坯壳薄厚不均,振痕紊乱有明显的“V”形缺口,(如图2所示)随着不断被撕开及愈合的“V”形缺口下移,坯壳在热电偶上方发生撕裂,撕裂部位靠近热电偶时热电偶测出温度升高,当撕裂部位通过热电偶所在位置时温度达到峰值,然后随着撕裂部位离开热电偶、温度逐渐降低。
发生粘接的板坯表面二、结晶器漏钢预报系统进行实质性研究,并经历了从结晶器冷却水进、出口温差和结晶器铜板热流量(热流密度)分析到结晶器铜板与坯壳之间的摩擦力和结晶器铜板温度监测的发展过程[9-10]。
漏钢预报系统的开发是一个庞大的系统工程,从各种形式漏钢的机理研究到连铸设备的自动化控制,是一项典型的交叉学科研究和应用,本文对不同理论的预报方法进行简要阐述。
2.1基于结晶器铜板热传输的漏钢预报逻辑判断模型逻辑判断模型, 就是结合连铸设备工艺的实际情况, 定时采样处理每一组热电偶数据, 把其中的温度上升值、升温速率、上下热电偶温差等数据与设定的阈值进行对比。
通过对比, 分析单个热电偶温度变化的时间序列和组偶温度关联的空间序列, 结合钢种、拉速、铸坯宽度、经验值等因素, 判断坯壳断裂的发生部位、裂口的发展方向和坯壳的生长情况。
逻辑判断模型的本质是识别出可能引起漏钢的温度模式, 属于动态波形模式识别问题, 如图3所示。
上排热电偶随着时间的变化(即在几个采样周期内), 出现温度上升的情况, 此温度梯度为判断参数之一, 该曲线的极值超过设定值(说明粘钢)或低于某个值。
几个采样周期后, 下面的热电偶温度上升, 该曲线的极值也超过设定值(说明粘钢)或低于某个值, 此温度梯度为判断参数之二;再过一段时间, 随着上面热电偶的温度下降, 下面热电偶的温度上升, 出现负温差情况, 此温差为判断参数之三。
这样通过监控温度变化就可发出漏钢预报报警(图2.1( e) )。
因此, 上述特征的漏钢预报逻辑判断模型主要包括: 最大最小值模型; 温度上升速度模型; 温度下降速度模型; 温度上升幅度模型; 温度下降幅度模型; 粘结点空间传递速度模型; 单偶漏钢温度模式识别; 组偶漏钢温度模式识别; 采样滤波模型等等。
图2.1 连铸粘结漏钢预报动态波形模式识别2.2热电偶网络化的漏钢预报逻辑判断模型S iemens和Dan ie li的薄板坯连铸连轧均采用热电偶网络化的漏钢预报逻辑判断模型, 如唐山钢铁集团有限责任公司CSP 连铸采用D anieli技术, 具有粘结预报和漏钢预报两种功能。
其自动控制系统扫描结晶器上的温度传感器网络(m 排n列共m *n 个K 型热电偶, 布满结晶器的宽面和窄面), 采样周期2ms。
它选择宽面上数第2行的热电偶为标准热电偶行, 称为弯月面行( Men iscus),以该行的每个热电偶温度值( TC _m eniscus)为标准值, 与对应列的其它热电偶温度值( TC _check)比较, 来判断温度是否接近粘结点, 可自动避免粘结和漏钢的发生。
原理如图4。
模型主要参数包括: St ick ing Check V alue, 热电偶实际检测温度值与同列M eniscus行热电偶平均温度的差值, 为绝对正值; Stick ingD ev ia tion Lim i,t 可设定的粘结判断阈值, 超过此值就认定产生了粘结; Check In terva,l 保证正确的弯月面温度曲线倾斜度条件的循环检测时间差值; S ticking Warning CountL im i,t 粘结警告所需的符合粘结条件的最少热电偶数量; Stick ing A larm Count L im i,t 粘结报警所需的符合粘结条件的最少热电偶数量; Breakout Deviation L im i,t 可设定的漏钢判断阈值, 热电偶的温度超过这个值时就会被标定为符合漏钢条件点(H ot Spot)。
图2.2 温度传感器网漏钢预报原理图以上参数值由技术人员根据不同钢水等级、浇铸条件设定。
2.3 基于结晶器热流分析的预报方法当坯壳发生漏钢或是在结晶器内部形成表面缺陷的时候,坯壳的表面会形成热点,即坯壳温度较高、并且相对较薄的区域,留在结晶器内的钢液较正常浇铸时多,因此漏钢发生时,结晶器铜板的热流小于正常浇铸时的热流,如图1.2所示。
而结晶器是通过冷却水带走热量的,因此可以通过监测结晶器每个面冷却水的进、出口温差来直接监测是否有漏钢的发生[12]。
但Shipman认为应该对结晶器铜板的热流进行监测,与连铸机生产该钢种的历史数据做比较,以不发生漏钢的最小坯壳厚度为基准,其所需的总的传热量为临界值,当所测热流量低于临界值便可判定漏钢,图1.3为拉速与最小传热量之间的关系。
早在20世纪50年代就有关于该方法的理论报道,但直到1970年应用热交换法来分析检测漏钢才成为现实。
该预报方法在中板坯和小方坯连铸中有其一定的优越性,但是该预报方法的准确性相对较低,现在连铸现场主要将其作为辅助判据。
2.4 摩擦力测量法在结晶器弯月面区域,钢水进入结晶器后在强制冷却作用下凝固收缩,随着结晶器的振动,熔化了的液态保护渣进入到坯壳冷却收缩形成的气隙中,这样就形成了结晶器铜板热面与保护渣、保护渣与铸坯坯壳两个接触面,当铸坯在拉矫棍作用下运动时,这两个接触面间就形成了摩擦力,统称为结晶器铜板与铸坯坯壳之间的摩擦力[13]。
摩擦力的大小受到保护渣性能、钢种、钢水纯洁度、拉速、结晶器倒锥度、结晶器振动等因素的影响。
研究人员普遍认为结晶器与坯壳之间的摩擦力对铸件质量起到决定性的影响,由于润滑不足而产生的较大摩擦力,会造成铸坯与结晶器间有较强的的附着力从而使他们产生粘结性焊合。
通过现场实践观察,粘结产生时,摩擦力的突然增大,变得极不稳定,是粘结产生的重要征兆,以此判断漏钢情况,因此通过监测摩擦力来预报粘结在原理上基于人工智能与热成像的结晶器漏钢预报系统是可行的。