炼钢系统
MES炼钢系统的设计和应用

MES炼钢系统的设计和应用胡跃武1卢克斌1沈际海1戴玲子2ÉϺ£ 201900 2上海宝信软件股份有限公司以计划调度执行为核心的制造执行系统在很多领域正得到广泛的应用并对该系统的工艺背景目前实践表明各项功能达到设计要求关键词图1 与其它子系统的接口关系Fig.1 Relation of interface with other subsystems图2 MES 炼钢系统的功能划分Fig.2 Function structures of MES steelmaking subsystem3.1预计划管理模块预计划管理模块上承合同管理模块中的合同计划中间还穿插有MES 热轧子系统中热轧预计划模块的部分功能此模块的主要功能有虚拟板坯按照炼钢连铸规程预组炉生成预炼钢炉次PONO3.2初计划管理模块所谓初计划对符合条件的炉次进行收池并按炼钢规程也称浇注顺计划其中一个CAST_LOT 内最多含N 个PONO ͬһ¸öCAST_LOT 内的出钢记号相同等等炼钢初计划模块还考虑设置了以下两个功能L2l 对于已下达给L2但还未排入炼钢终计划的炉次可作转置 l 对于已下达给L2但浇注还未开始的炉次可以作连铸机间的在线移动调整为预计划出钢计划匹配模型提供数据支持成分控制此模块中还嵌入了炼钢品质判定模型操作员可以根据生产中收集的炉次成分信息并对该炉次的钢种作出合格保留或者报废的判定在钢水的处理过程中操作异常也经常导致钢种变更3.4 终计划管理模块炼钢终计划模块的功能主要是根据初计划模块提供的浇注顺计划和品质管理模块提供的作业标准利用出钢计划编制模型生成炼钢各个工序的作业时间表用以指导现场生产接收生产跟踪管理模块提供的工序信息计算得到当前作业炉次和相临炉次的预想作业时间表以及计划匹配判定结果图3 出钢计划编制画面Fig.3 Graph of tapping plan scheduling3.5 生产跟踪管理模块炼钢生产跟踪模块在MES炼钢系统中起到了承上启下通过提供一个可以监视整个炼钢连铸物流生产进程状况的展示界面本模块收集各L2过程计算机上传的生产运转状况事项信息更新炼钢初计划管理模块中在线日计划的状态同时管理作为其动态调整计划的重要依据本模块还记录每炉钢生产过程中所经过的工序如图4显示的是炼钢作业监控画面以指导扒渣站对不锈钢线来说以指导铁合金厂按时提供合格的铬铁水图4 炼钢作业监控画面Fig.4 Graph of steelmaking’s job supervising3.6 生产存货管理模块炼钢生产存货管理模块分为液态管理和固态管理两大部分以制造命令号为键字在数据库表中创建炉次主档和板坯主档并进行各种管理首先与炼钢终计划进行匹配否则向炼钢品质管理模块提供生产质量信息供其作质量处理如在收到板坯切断实绩和精整实绩后并向合同管理模块和上层ERP财务子系统中的成本模块抛帐它是包括炼钢精整轧制在内的生产作业流程的计划管理根据内容划分初计划和终计划三部分组成一体化计划是依据轧制计划种类堆垛规则连铸规程在预计划下达以及调整的过程中支持直接热装轧制作业保持库存量最小化和物流畅通考虑到大系统的复杂性和难度一体化计划主要体现在预计划阶段计划员根据设备产能平衡对炼钢预计划和热轧预计划实行混合编制更符合实际此种编制方式更体现出了工序间合理衔接4.2 运筹优化模型为快速在炼钢终计划管理模块中出钢计划编制模型的机理就是对初计划模块已下达到L2的所有炉次计算出每一炉次在铁水预处理精炼即根据每一炉次在已作业工序的实绩同时判定炼钢炼钢连铸如图4显示的是出钢计划匹配画面火车时刻表不仅可确保生产物流的畅通扩大产能特别是在安排DHCR计划时火车时刻表可实现炼钢从而保证计划的有效实施和生产的正常进行图5 出钢计划匹配画面Fig.5 Graph of tapping plan matching4.3 DHCR计划对于DHCR计划产出板坯按一定顺序装入一座加热炉中的方式炼钢预计划管理模块采用了将一个DHCR计划的预组批分解成两台连铸机的CAST_LOT计划将预组批中的半炉板坯即前75吨先分配给其中一台连铸机从而基本保证实际交替生产出的板坯顺序满足轧制顺的要求该厂产销计算机系统成功上线经过几个月的实践检验各项功能基本达到设计要求不仅大幅降低了人工成本和劳动强度生产的计划精度以及合同完成的控制精度更高快速响应市场提供了有力的技术支撑和保证根据MES炼钢系统在该厂的设计和应用1ÌØµãÍ»³öÒѾ-³ÉΪ¸Ã³§ºÏÀí¸ßЧµÄ±àÅÅÁ¶¸Ö¼Æ»®2ÔÚÆäËüÒ±½ðÆóÒµÖÐÒ²¾ßÓÐÍÆ¹ã¼ÛÖµMES炼钢系统的设计和应用作者:胡跃武, 卢克斌, 沈际海, 戴玲子作者单位:胡跃武,卢克斌,沈际海(宝钢技术中心自动化所,上海,201900), 戴玲子(上海宝信软件股份有限公司)本文链接:/Conference_6090201.aspx。
转炉炼钢信息管理系统

二级系统需采集的现场数据主要分3 P C 类: L 数据、 串 口数据和摄像机视频数据。 从成本、 稳定性及维护量 综合考虑, 所有的数据最终都以工业以太 网方设备都采用MO 。 XA 工业级产品 。 系统数据 采集分为3 种方式:
A sr c : hs a e e b r t n w kn fno ma o b t tT ip p r l oae a a da e ido ifr t nma a e n ss m a a to ma a dme im-z dc n etr t l kn , ih i n g me ty t e d p ts l n l du s e o v r s ema i g whc i e e
用G 一93 系列 及西 门子s —0/ 0 E ¥0 0 7304 系列 。 0 部分未进P C L
随 着钢 铁 冶金 工 艺 及 工 业 自动 化 技术 的 发展 , 新
数据如电子秤 ( 含无线电子秤 )光谱仪 等都 以串 口方 、
式输 出。
型的高级生产管理系统逐步得 到推广, 如企业资源计 划( R 、 E P)制造执行系统( S) 。 ME 等 根据冶金行业 自动 化的分级, 炼钢区域 主要包含3 级系统: 一级基础 自动 化级( 1 、 L )二级过程控制级( 2 、 L )三级生产管理级( 3 。 L ) 由于许多 中小钢 厂因为种种原 因无法实现属于 三级 的ME , S 于是一种功能完善 、 适应转炉炼钢融合过程控 制级和生产管理级具备替代ME 的新型炼钢信息管理 S 系统应运而生。 根据其服务对象 、 具体功能特征及实时
() 1 脱硫站 、 转炉站、 精炼站、 连铸站等P C L 系统及 局部D 系统共同组建成一级工业以太网, L 数据通 CS PC
八钢150T转炉炼钢L2系统分析

服 务 器 第 2个 网 H ( I P 地 址 :1 0 . 1 0 . 2 . 1 0 :子 网 掩 码 : 2 5 5 . 2 5 5 . 2 5 5 . O ) 连接 到 L 2 交换机 ( 位 于二级 中心机房 ) 。机房 L 2 操作 站I P地址为 : 1 O . 1 O . 2 . ( 子网掩码: 2 5 5 . 2 5 5 . 2 5 5 . 0 ) ; 现场 L 2 操作 站 I P 地址为 : 1 0 . 1 O . 2 . ( 子 网掩码 : 2 5 5 . 2 5 5 . 2 5 5 . 0 ) ;检化验 系统的 I P地 址 为: 1 O . 1 O . 2 . 。 服 务 器 第 3个 网 口 ( I P 地 址 :1 0 . 6 2 . 9 0 . ;子 网 掩 码 : 2 5 5 . 2 5 5 . 2 5 5 . 0 : 默认 网关: 1 0 . 6 2 . 9 0 . 2 4 0 ) 连接到 L 3 交换机( 位于二级机 房) 。M E S系统 的 I P 地址为 : 1 O . 6 2 . 2 0 1 . 。 服务器 O P C配置 : 服务 器安装 R S L i n x C 1 a s s i c v 2 . 5 7 . 安装 完毕后 , 需要 对 O P C服务 器进行配置 。O P C服务器的配置实际上就是 在 O P C服务器 中建立标 签( T O P I C ) 。 以便让 O P C客户程 序能 够通过这 些标签 与 P L C进行 通 讯. 存取 P L C中的数据。 服务器配置应用软件 : 服务器应用软件 的功能是数据通讯 、 采集和数据存储 。其 中: H M P S e n r e r - e x e 为数据服务程序 . 负责生产工位 的生产处理 ( 包括 通讯数据处理 、 生产实绩处理等 ) , 需一直运行 , 是常驻进程 。 H M P S a v e D B - e x e 为数据存储 程序 . 负责生产工位 的生产实绩 和其 它相关数据 的数据库保存 . 需一直运行 . 是常驻进程 。 O P C M a n a g e r . e x e 为O P C 管理工具 . 负责 与 P L C的数据通讯 , 通过 数据库与数据服务程序交互 . 需一直运行 。 O p c C o n i f x e 为O P C配置工具 , 负责配置 P L C的通讯 电文 ; 配置 完成后供 O P C管理工 具使用 。 O P C配置工具 只做 电文配置工作 , 配置 完成后 , 不需要一直运行 。 M s g M a n a g e —x e 为S o c k e t 电文通讯程序 .负责与检化验 L 2系统
炼钢厂生产过程数据信息管理系统方案
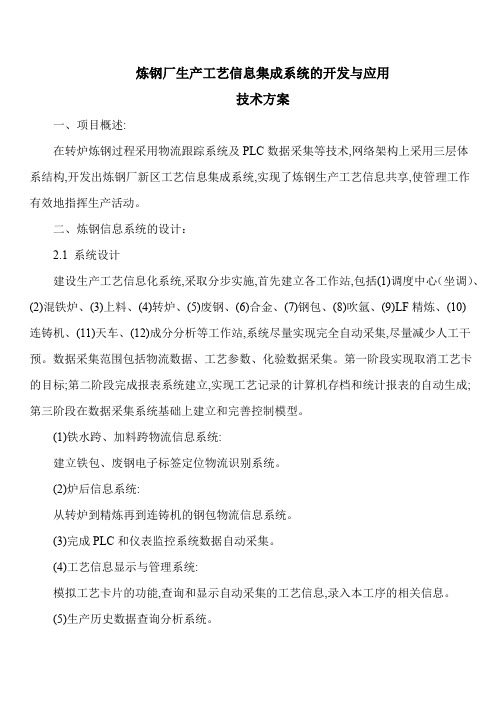
炼钢厂生产工艺信息集成系统的开发与应用技术方案一、项目概述:在转炉炼钢过程采用物流跟踪系统及PLC数据采集等技术,网络架构上采用三层体系结构,开发出炼钢厂新区工艺信息集成系统,实现了炼钢生产工艺信息共享,使管理工作有效地指挥生产活动。
二、炼钢信息系统的设计:2.1 系统设计建设生产工艺信息化系统,采取分步实施,首先建立各工作站,包括(1)调度中心(坐调)、(2)混铁炉、(3)上料、(4)转炉、(5)废钢、(6)合金、(7)钢包、(8)吹氩、(9)LF精炼、(10)连铸机、(11)天车、(12)成分分析等工作站,系统尽量实现完全自动采集,尽量减少人工干预。
数据采集范围包括物流数据、工艺参数、化验数据采集。
第一阶段实现取消工艺卡的目标;第二阶段完成报表系统建立,实现工艺记录的计算机存档和统计报表的自动生成;第三阶段在数据采集系统基础上建立和完善控制模型。
(1)铁水跨、加料跨物流信息系统:建立铁包、废钢电子标签定位物流识别系统。
(2)炉后信息系统:从转炉到精炼再到连铸机的钢包物流信息系统。
(3)完成PLC和仪表监控系统数据自动采集。
(4)工艺信息显示与管理系统:模拟工艺卡片的功能,查询和显示自动采集的工艺信息,录入本工序的相关信息。
(5)生产历史数据查询分析系统。
2.2 功能设计系统分三个层次:(1)数据的采集数据的采集概括为下述3种方式:①自动从PLC和仪表采集;②自动从现有信息系统或数据库中采集;③人工输入。
具体的数据采集时根据生产和工艺流程划分的,主要由以下10个环节采集:调度、混铁炉和铁水包、上料、转炉、转炉合金加入、LF精炼、铁水和钢水成分、吹氩精炼、钢包、铸机、天车、成分分析。
(2)信息的传递。
炼钢生产管理系统简介(数采)
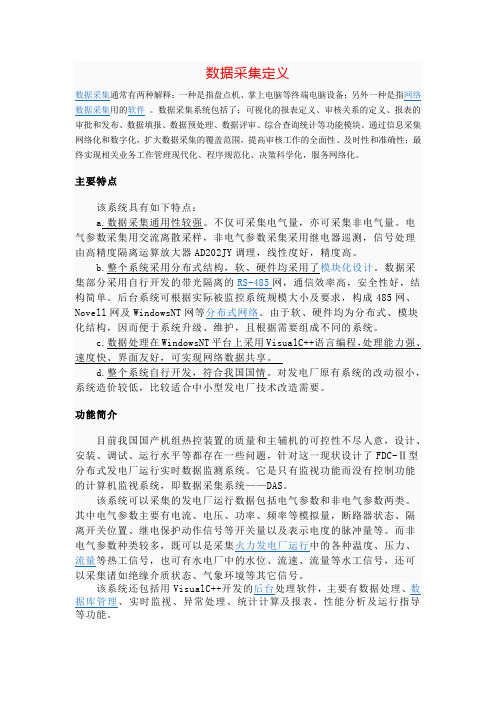
数据采集定义数据采集通常有两种解释:一种是指盘点机、掌上电脑等终端电脑设备;另外一种是指网络数据采集用的软件。
数据采集系统包括了:可视化的报表定义、审核关系的定义、报表的审批和发布、数据填报、数据预处理、数据评审、综合查询统计等功能模块。
通过信息采集网络化和数字化,扩大数据采集的覆盖范围,提高审核工作的全面性、及时性和准确性;最终实现相关业务工作管理现代化、程序规范化、决策科学化,服务网络化。
主要特点该系统具有如下特点:a.数据采集通用性较强。
不仅可采集电气量,亦可采集非电气量。
电气参数采集用交流离散采样,非电气参数采集采用继电器巡测,信号处理由高精度隔离运算放大器AD202JY调理,线性度好,精度高。
b.整个系统采用分布式结构,软、硬件均采用了模块化设计。
数据采集部分采用自行开发的带光隔离的RS-485网,通信效率高,安全性好,结构简单。
后台系统可根据实际被监控系统规模大小及要求,构成485网、Novell网及WindowsNT网等分布式网络。
由于软、硬件均为分布式、模块化结构,因而便于系统升级、维护,且根据需要组成不同的系统。
c.数据处理在WindowsNT平台上采用VisualC++语言编程,处理能力强、速度快、界面友好,可实现网络数据共享。
d.整个系统自行开发,符合我国国情。
对发电厂原有系统的改动很小,系统造价较低,比较适合中小型发电厂技术改造需要。
功能简介目前我国国产机组热控装置的质量和主辅机的可控性不尽人意,设计、安装、调试、运行水平等都存在一些问题,针对这一现状设计了FDC-Ⅱ型分布式发电厂运行实时数据监测系统。
它是只有监视功能而没有控制功能的计算机监视系统,即数据采集系统——DAS。
该系统可以采集的发电厂运行数据包括电气参数和非电气参数两类。
其中电气参数主要有电流、电压、功率、频率等模拟量,断路器状态、隔离开关位置、继电保护动作信号等开关量以及表示电度的脉冲量等。
而非电气参数种类较多,既可以是采集火力发电厂运行中的各种温度、压力、流量等热工信号,也可有水电厂中的水位、流速、流量等水工信号,还可以采集诸如绝缘介质状态、气象环境等其它信号。
炼钢自动化系统的研究与实现
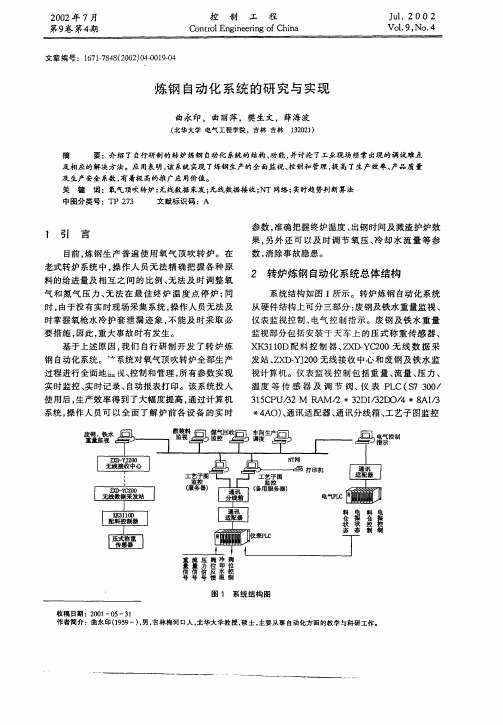
参数, 准确 把握终 炉温度 、 出钢时 间及溅 渣护 炉效
果 , 外 还 可 以及 时 调 节 氧 压 、 却 水 流 量 等 参 另 冷
数, 消除 事故 隐患 。
2 转炉炼钢 自动化 系统总体结构
系 统结构 如 图 1所示 。转 炉炼 钢 自动化 系统
从 硬件 结构上 可分 三部分 : 钢及铁 水重 量监 视 、 废 仪 表监 视控 制 、 电气 控 制 指示 。废 钢及 铁 水 重 量 监视部 分包 括 安装 于天 车 上 的 压式 称 重 传 感 器 、
制
J
l
J
I
l
I
Z匹 C O )卜Y2 0
J
直
臻
, ” 通讯
,
打扣
…一 I
-。 。-●。- J
无线数据采发站
分线箱
_
电气眦
I 料1 l lX1器 I K制 配30 控D
f
适器 通 配 讯
l
.
馨赛
20 0 2年 7月 第9 第 4 卷 期
控 制 工 程
C n r l gn e igo ia o to En ie rn fChn
J 1 u .20 0 2
Vo. No 4 19. .
文章 编 号 :17 .8 82 0 )40 1.4 6 17 4 (0 2 0 .0 90
X 3 1D配 料 控 制 器 、 X - C 0 K 10 Z D Y 2 0无 线 数 据 采 发站 、 X Y 2 0无线接 收 中心 和废 钢 及 铁 水 监 Z D- J 0
气 和氮 气 压力 、 法 在 最 佳 终 炉 温 度 点 停 炉 ; 无 同 时, 由于没 有实 时现 场采集 系统 , 操作 人员 无法 及
炼钢物流系统炉机匹配规则(冶金2008-1、2班资料2011.4.11).

炼钢物流系统炉机匹配规则1.转炉炼钢厂工序产能和品种钢铸机配置炼钢生产组织的核心是生产作业计划与调度。
合理的生产作业计划与调度是保证生产物流通畅、进行资源合理配置与高效利用,提高设备利用率,进而提升生产系统的整体运行效率,降低物耗、能耗及成木,增加企业盈利和企业竞争力的重要途径。
钢产量是衡量炼钢厂生产运营状况的一个重要指标。
对于转炉-LF-连铸机流程,三个工序都有可能成为制约整个流程生产的瓶颈,决定流程的实际生产能力。
瓶颈是企业在实现其目标的过程中现存的或潜伏的制约因素,是生产能力小于或等于生产负荷的资源,而且在不同条件下,同一生产流程的瓶颈可能会发生转移,因此在市场需求允许的情况下,根据钢铁冶金过程工程和炼钢厂系统的运行原则与调控策略等相关理论,充分发挥每个设备的生产能力,首先应该分析限制钢厂年生产能力的因素.在解决了流程瓶颈的基础上,还要解决好各个生产环节的衔接匹配的问题。
具体到BOF—LF—CCM流程,分析三者的实际生产能力,掌握流程的瓶颈并提出改进建议。
炼钢厂生产能力的分析,就是对钢铁制造过程中物质流的三个基本参数(时间、温度和物质量中的物质量进行分析,剖析转炉、LF炉和连铸机生产过程,并进行协调匹配研究,以提升整个流程的产能。
炼钢内部能力匹配这里应考虑炼钢、热轧和冷轧各工序内部的能力匹配关系。
炼钢工序主要包括冶炼、精炼和连铸工段:冶炼和精炼以炉为单位、连铸以浇次为单位分别进行连续生产,连铸的浇次与浇次间隔为30~50m in;为保证连铸的连续生产,这3个工段的时间需满足精炼周期<冶炼周期≤浇注时间,对1炉钢是这样要求,对1个浇次也是这样要求。
精炼在冶炼和连铸之间起到缓冲和协调作用,因此3个工段中要求精炼周期最短,为避免连铸等待钢水则须冶炼周期小于或等于浇注时间。
因此,炼钢工序内部的能力匹配关系为:精炼能力>冶炼能力>连铸能力,其匹配程度与连铸产能扩展能力有关。
连铸产能扩展能力强,则炼钢工序内部之间是一种宽松型能力匹配;连铸扩展能力弱,则炼钢内部之间是一种紧凑型能力匹配,以确保在连铸产能扩展后炼钢内部仍能满足能力匹配关系。
炼钢工艺流程简介

炼钢工艺流程简介炼钢厂目前共有大小转炉11座,其中炼钢一厂8座,分别为40吨转炉4座,80吨转炉1座,100吨转炉3座;炼钢二厂150 吨转炉3座。
炼钢系统的主要工艺流程为:转炉兑铁——冶炼——出钢——钢包吹氩——LF精炼炉——方坯连铸工艺。
•铁水供应转炉炼钢所需铁水用钢包或鱼雷罐由炼铁厂运往炼钢厂。
高炉运来的铁水除一部分兑入混铁炉贮存外,其余铁水经倒包调整和称量作业,保证入炉铁水控制在所需的范围。
需要进行脱硫处理的铁水,由天车运往脱硫站进行脱硫处理,不需处理的铁水,直接兑入转炉。
转炉兑铁铁水是转炉炼钢最主要的金属料,一般占转炉金属料70%以上。
铁水的成分、温度是否适当和稳定,对简化、稳定转炉操作,保证冶炼顺行以及获得良好的技术经济指标都十分重要。
•废钢供应在炼钢厂设有废钢库,外来的废钢由汽车运到废钢库存放。
废钢铁通过磁盘吊车按不同配比和装料顺序装入废钢料槽,由天车加入转炉。
转炉加冷料转炉炼钢时,由于热量富裕,可以加入多达30%的废钢,作为调整吹炼温度的冷却剂。
采用废钢冷却,可以降低铁水量、造渣材料和氧气的消耗,而且比用铁矿石冷却的效果稳定,喷溅少。
•散状原料供应(石灰、铁皮球、镁球等)1、100吨转炉炼钢散状原料上料系统选用皮带上料工艺。
散状原料通过汽车运到地下受料仓,由垂直皮带运送到42m平台,再由水平皮带运输机和布料小车装入相应的料仓。
转炉加料画面2、加料系统布置在转炉的上方,每座转炉有一套炉顶料仓,每套有10个炉顶料仓,分别为调渣剂、脱硫剂、石灰、铁皮球、镁球、萤石、包渣料仓等。
料仓中的散状料分别通过振动给料器→称量斗→汇总斗→下料溜管,加入转炉。
•铁合金供应100吨转炉设有一组铁合金料仓,由10个铁合金料仓组成.,为3座转炉供应合金料。
铁合金是脱氧及合金化材料。
用于钢液脱氧的铁合金叫做脱氧剂;用于调整钢液成分的铁合金叫做合金剂。
炼钢常用的铁合金有:硅铁、锰铁、钒铁、钼铁、硅钙合金等。
•转炉冶炼炼钢是通过氧化反应脱碳、升温、合金化的过程。
钢铁冶炼中的炼钢渣体系和控制方法
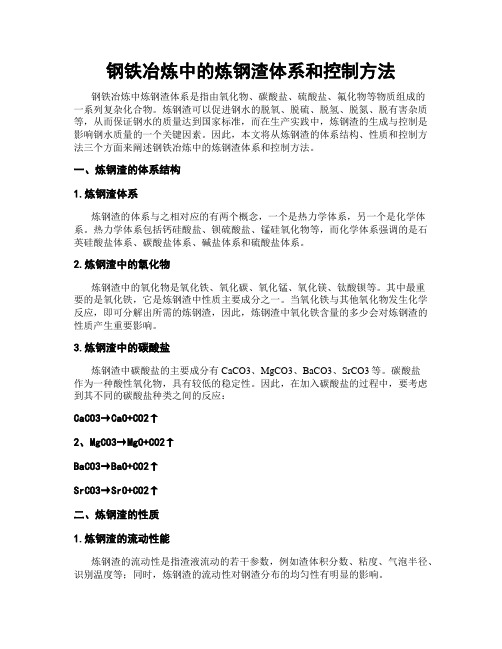
钢铁冶炼中的炼钢渣体系和控制方法钢铁冶炼中炼钢渣体系是指由氧化物、碳酸盐、硫酸盐、氟化物等物质组成的一系列复杂化合物。
炼钢渣可以促进钢水的脱氧、脱硫、脱氢、脱氮、脱有害杂质等,从而保证钢水的质量达到国家标准,而在生产实践中,炼钢渣的生成与控制是影响钢水质量的一个关键因素。
因此,本文将从炼钢渣的体系结构、性质和控制方法三个方面来阐述钢铁冶炼中的炼钢渣体系和控制方法。
一、炼钢渣的体系结构1.炼钢渣体系炼钢渣的体系与之相对应的有两个概念,一个是热力学体系,另一个是化学体系。
热力学体系包括钙硅酸盐、钡硫酸盐、锰硅氧化物等,而化学体系强调的是石英硅酸盐体系、碳酸盐体系、碱盐体系和硫酸盐体系。
2.炼钢渣中的氧化物炼钢渣中的氧化物是氧化铁、氧化碳、氧化锰、氧化镁、钛酸钡等。
其中最重要的是氧化铁,它是炼钢渣中性质主要成分之一。
当氧化铁与其他氧化物发生化学反应,即可分解出所需的炼钢渣,因此,炼钢渣中氧化铁含量的多少会对炼钢渣的性质产生重要影响。
3.炼钢渣中的碳酸盐炼钢渣中碳酸盐的主要成分有CaCO3、MgCO3、BaCO3、SrCO3等。
碳酸盐作为一种酸性氧化物,具有较低的稳定性。
因此,在加入碳酸盐的过程中,要考虑到其不同的碳酸盐种类之间的反应:CaCO3→CaO+CO2↑2、MgCO3→MgO+CO2↑BaCO3→BaO+CO2↑SrCO3→SrO+CO2↑二、炼钢渣的性质1.炼钢渣的流动性能炼钢渣的流动性是指渣液流动的若干参数,例如渣体积分数、粘度、气泡半径、识别温度等;同时,炼钢渣的流动性对钢渣分布的均匀性有明显的影响。
2.炼钢渣的稳定性炼钢渣的稳定性指的是渣液在一定条件下中不被分解、产生新的化学反应,能在限制条件下稳定存在的能力,同时炼钢渣的稳定性还与其流动性和抗渗透性等特点有关。
3.炼钢渣的还原性炼钢渣的还原性体现了其在高温下进行还原反应的倾向。
当加热时,炼钢渣中会产生还原性气体,例如CO和H2等,这些还原性气体在炼钢渣中与氧化铁等发生还原反应,从而影响炼钢渣的稳定性及其对钢水的影响。
炼钢质量管理体系的有效运用分析
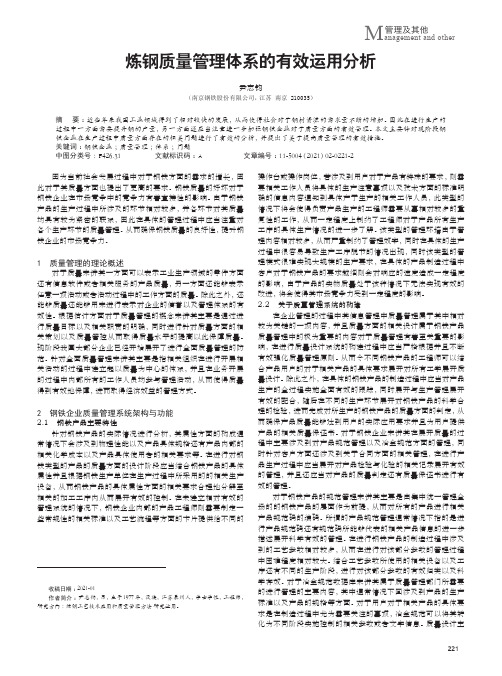
221管理及其他M anagement and other炼钢质量管理体系的有效运用分析尹志钧(南京钢铁股份有限公司,江苏 南京 210035)摘 要:近些年来我国工业领域得到了相对较快的发展,从而使得社会对于钢材资源的需求量不断的增加。
因此在进行生产的过程中一方面需要提升钢的产量,另一方面还应当注重进一步加强钢铁企业对于质量方面的有效管理。
本文主要针对现阶段钢铁企业在生产过程中质量方面存在的相关问题进行了有效的分析,并提出了关于提高质量管理的有效措施。
关键词:钢铁企业;质量管理;体系;问题中图分类号:F426.31 文献标识码:A 文章编号:11-5004(2021)02-0221-2收稿日期:2021-01作者简介:尹志钧,男,生于1977年,汉族,江苏泰州人,学士学位,工程师,研究方向:炼钢工艺技术应用和质量管理方法 研究运用。
因为当前社会发展过程中对于钢铁方面的需求的增长,因此对于其质量方面也提出了更高的要求。
钢铁质量的好坏对于钢铁企业在市场竞争中的竞争力有着直接性的影响。
由于钢铁产品的生产过程中所涉及的环节相对较多,并各环节对其质量均具有较为紧密的联系,因此在具体的管理过程中应当注重对各个生产环节的质量管理。
从而确保钢铁质量的良好性,提升钢铁企业的市场竞争力。
1 质量管理的理论概述对于质量来讲其一方面可以表示工业生产领域的零件方面还有信息软件或者相关服务的产品质量,另一方面还能够表示任意一项活动或者活动过程中的工作方面的质量。
除此之外,还能够质量还能够用来进行表示对企业的信誉以及管理体系的有效性。
根据估计方面对于质量管理的概念来讲其主要是通过进行质量目标以及相关职责的明确,同时进行针对质量方面的相关策划以及质量管控从而取得质量水平的提高以此保障质量。
现阶段我国大部分企业已经开始展开了进行全面质量管理的防范。
针对全面质量管理来讲其主要是指相关组织在进行开展相关活动的过程中建立起以质量为中心的体系,并且在业务开展的过程中内部所有的工作人员均参与管理活动,从而使得质量得到有效地保障,进而取得经济效益的管理方式。
炼钢控制系统实施方案
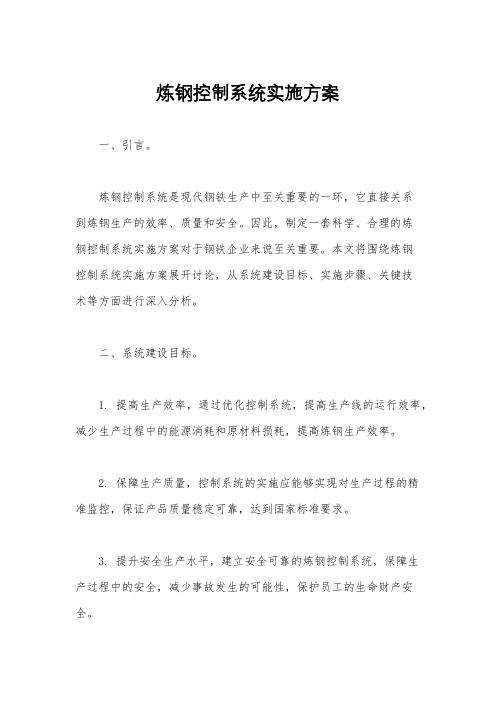
炼钢控制系统实施方案一、引言。
炼钢控制系统是现代钢铁生产中至关重要的一环,它直接关系到炼钢生产的效率、质量和安全。
因此,制定一套科学、合理的炼钢控制系统实施方案对于钢铁企业来说至关重要。
本文将围绕炼钢控制系统实施方案展开讨论,从系统建设目标、实施步骤、关键技术等方面进行深入分析。
二、系统建设目标。
1. 提高生产效率,通过优化控制系统,提高生产线的运行效率,减少生产过程中的能源消耗和原材料损耗,提高炼钢生产效率。
2. 保障生产质量,控制系统的实施应能够实现对生产过程的精准监控,保证产品质量稳定可靠,达到国家标准要求。
3. 提升安全生产水平,建立安全可靠的炼钢控制系统,保障生产过程中的安全,减少事故发生的可能性,保护员工的生命财产安全。
三、实施步骤。
1. 系统规划,明确系统建设的总体目标和具体需求,确定系统的功能模块和关键技术,制定详细的规划方案。
2. 技术选型,根据系统规划确定的功能需求,选择适合的硬件设备和软件系统,确保系统的稳定性和可靠性。
3. 系统集成,进行各功能模块的集成测试,确保系统各部分协调配合,实现系统的整体性能。
4. 系统调试,对系统进行全面调试,验证系统的稳定性和可靠性,保证系统在实际生产中的正常运行。
5. 系统运行,系统建设完成后,对系统进行持续监控和运行,及时发现和解决系统运行中的问题,确保系统的稳定运行。
四、关键技术。
1. 数据采集与处理技术,通过高效的数据采集设备和数据处理算法,实现对生产过程中各种参数的实时监测和分析。
2. 控制算法优化技术,优化炼钢生产过程中的控制算法,提高控制系统的精准度和响应速度,提高生产效率和产品质量。
3. 系统集成与通讯技术,实现控制系统与生产设备的无缝集成,确保各个部分之间的信息交互畅通,提高系统的整体性能和稳定性。
4. 安全监控技术,建立完善的安全监控系统,实现对生产过程中的安全隐患的实时监测和预警,保障生产安全。
五、总结。
炼钢控制系统实施方案的制定对于提高钢铁企业的生产效率、保障产品质量、提升安全生产水平具有重要意义。
炼钢安全指引:风险辨识分级管控
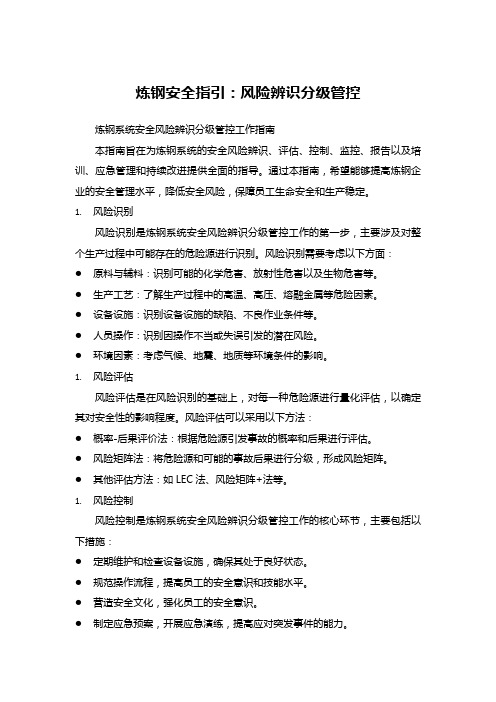
炼钢安全指引:风险辨识分级管控炼钢系统安全风险辨识分级管控工作指南本指南旨在为炼钢系统的安全风险辨识、评估、控制、监控、报告以及培训、应急管理和持续改进提供全面的指导。
通过本指南,希望能够提高炼钢企业的安全管理水平,降低安全风险,保障员工生命安全和生产稳定。
1.风险识别风险识别是炼钢系统安全风险辨识分级管控工作的第一步,主要涉及对整个生产过程中可能存在的危险源进行识别。
风险识别需要考虑以下方面:●原料与辅料:识别可能的化学危害、放射性危害以及生物危害等。
●生产工艺:了解生产过程中的高温、高压、熔融金属等危险因素。
●设备设施:识别设备设施的缺陷、不良作业条件等。
●人员操作:识别因操作不当或失误引发的潜在风险。
●环境因素:考虑气候、地震、地质等环境条件的影响。
1.风险评估风险评估是在风险识别的基础上,对每一种危险源进行量化评估,以确定其对安全性的影响程度。
风险评估可以采用以下方法:●概率-后果评价法:根据危险源引发事故的概率和后果进行评估。
●风险矩阵法:将危险源和可能的事故后果进行分级,形成风险矩阵。
●其他评估方法:如LEC法、风险矩阵+法等。
1.风险控制风险控制是炼钢系统安全风险辨识分级管控工作的核心环节,主要包括以下措施:●定期维护和检查设备设施,确保其处于良好状态。
●规范操作流程,提高员工的安全意识和技能水平。
●营造安全文化,强化员工的安全意识。
●制定应急预案,开展应急演练,提高应对突发事件的能力。
1.风险监控风险监控是在风险控制的基础上,对炼钢系统进行实时监控,以确保及时发现和解决潜在风险。
风险监控可采用以下手段:●安全检查:定期或不定期开展安全检查,发现和整改潜在风险。
●数据分析:利用大数据、人工智能等技术手段,对生产过程进行实时数据分析,发现异常情况。
●在线监测:对关键设备、部位进行在线监测,及时发现设备设施的异常情况。
1.风险报告风险报告是在风险识别、评估和控制过程中形成的相关数据和信息进行汇报和总结的过程。
自动化炼钢的原理及应用

自动化炼钢的原理及应用自动化炼钢是指利用先进的控制系统和自动化设备,实现钢铁生产过程中的自动化操作和控制。
它通过集成各种传感器、执行器和控制器,实现对炼钢过程中的温度、压力、流量等参数的实时监测和调节,从而提高生产效率、降低能耗、提高产品质量。
一、自动化炼钢的原理1. 数据采集与处理:自动化炼钢系统通过传感器实时采集炼钢过程中的各种数据,如温度、压力、流量等,然后将这些数据传输到控制系统中进行处理和分析。
2. 控制策略与算法:控制系统根据炼钢过程的要求和目标,通过预设的控制策略和算法,对炼钢过程中的各种参数进行调节和控制,以实现最佳的生产效果。
3. 执行器控制:控制系统通过执行器控制设备,如阀门、电机等,对炼钢过程中的各种操作进行自动化控制,如调节温度、控制流量等。
4. 监测与反馈:自动化炼钢系统通过监测设备对炼钢过程中的各种参数进行实时监测,并将监测结果反馈给控制系统,以便进行调整和优化。
5. 故障诊断与处理:自动化炼钢系统还能通过故障诊断功能,对炼钢过程中可能出现的故障进行检测和诊断,并及时采取相应的措施进行处理,以确保生产的连续性和稳定性。
二、自动化炼钢的应用1. 生产效率提升:自动化炼钢系统能够实现对炼钢过程中的各个环节进行自动化控制和调节,从而提高生产效率和产能。
通过实时监测和自动调节,可以减少人工干预的时间和成本,提高生产线的运行效率。
2. 能源消耗降低:自动化炼钢系统通过对能源的精确控制和优化利用,可以有效降低能源消耗。
通过实时监测和调节温度、压力等参数,可以减少能源的浪费和损耗,提高能源利用率。
3. 产品质量提升:自动化炼钢系统能够实时监测和调节炼钢过程中的各种参数,从而保证产品的质量稳定性和一致性。
通过精确的控制和调节,可以避免因人为操作不准确而导致的产品质量问题,提高产品的合格率和市场竞争力。
4. 安全性提高:自动化炼钢系统能够实现对炼钢过程中的各种操作和参数进行自动化控制,减少人工操作的风险和安全隐患。
转炉炼钢系统技术与设备的发展分析

转炉炼钢系统技术与设备的发展分析摘要:近年来,在社会经济快速发展的带动下,我国各个行业的发展都取得了显著的成绩,为钢铁行业的发展带来了诸多的机遇,为各项专业技术的发展奠定了坚实的基础。
炼钢技术以及设备的发展为新型工业化发展起到了积极的助动作用,促使我国成为了世界钢铁大国。
但是因为我国钢铁生产中存在吨钢能耗高、劳动生产率低下的问题,这样就对我国钢铁行业的发展带来了诸多的阻碍,鉴于此我们还需要进一步的转炉炼钢技术和先进炼钢设备进行优化和完善。
关键词:转炉炼钢;发展;展望引言钢铁产业在我国社会经济发展中起到了至关重要的作用,其生产技术水平的稳步提升为我国钢铁产业的发展给予了良好的辅助。
这篇文章主要围绕我国转炉炼钢技术的发展展开深入细致的研究分析,希望能够对我国综合国力的未来持续健康发展有所帮助。
1现代转炉炼钢存在的问题1.1废钢资源问题废钢资源问题长期以来都是人们所关注的重点,当下我国大陆的钢材回收周期因为受到多方面因素的影响有所增加,没有形成较为严重的废钢问题,再加上转炉炼钢中会遇到无法避免的消耗等问题,所以导致废钢的转化率相对较低。
相对于很多其他国家,我国废钢产量较少,并且因为我国存在严重的废钢资源利用不足,所以导致我国还没有彻底的解决废钢资源匮乏的问题。
1.2转炉炼钢也会造成不容忽视的环保问题在转炉炼钢的过程中通常都会产生诸多的粉灰污染,并且因为近些年我国环保监控工作没有得到了良好的重视,这样就导致炼钢的成本在逐渐的增加。
尽管我国大陆对于除尘设备在不断地优化,并且也创建了大量的除尘系统的,但是还是无法满足当前人们对于环保工作的需要,这样就对转炉炼钢产业的发展造成了诸多的限制。
1.3炼钢除尘中的环境问题在上世纪八十年代,国内外转炉炼钢技术水平得以不断地提升,在这种形势下装备水平随之逐渐的完善,我国转炉除尘技术随之不断地发展。
在当前新的历史阶段,炼钢除尘工作越发的收到了人们的重视,并且也取得了良好的成绩,怎样彻底的解决炼钢除尘中所涉及到的环境问题,还需要我们进一步的进行研究分析。
长流程炼钢

长流程炼钢长流程工艺:从炼钢原燃料(如烧结矿、球团矿、焦碳等)准备开始,原料入高炉经还原冶炼得到液态铁水,经铁水预处理(如脱硫、脱硅、脱碳)进入顶底复吹氧气转炉,经吹炼去除杂质,将钢水倒入钢包中,经二次精炼(如RH、LF、VD等)使钢水纯洁化,然后钢水经凝固成型(连铸)成为钢坯,再经轧制工序最后成为钢材。
炼钢系统的主要工艺流程为:转炉兑铁——冶炼——出钢——钢包吹氩——LF精炼炉——方坯连铸工艺。
一、转炉兑铁1、铁水供应转炉炼钢所需铁水用钢包或鱼雷罐由炼铁厂运往炼钢厂。
高炉运来的铁水除一部分兑入混铁炉贮存外,其余铁水经倒包调整和称量作业,保证入炉铁水控制在所需的范围。
需要进行脱硫处理的铁水,由天车运往脱硫站进行脱硫处理,不需处理的铁水,直接兑入转炉。
铁水是转炉炼钢最主要的金属料,一般占转炉金属料70%以上。
铁水的成分、温度是否适当和稳定,对简化、稳定转炉操作,保证冶炼顺行以及获得良好的技术经济指标都十分重要。
2、废钢供应在炼钢厂设有废钢库,外来的废钢由汽车运到废钢库存放。
废钢铁通过磁盘吊车按不同配比和装料顺序装入废钢料槽,由天车加入转炉。
转炉炼钢时,由于热量富裕,可以加入多达30%的废钢,作为调整吹炼温度的冷却剂。
采用废钢冷却,可以降低铁水量、造渣材料和氧气的消耗,而且比用铁矿石冷却的效果稳定,喷溅少。
二、转炉冶炼炼钢是通过氧化反应脱碳、升温、合金化的过程。
它的主要任务脱硫、脱磷、脱碳、脱氧,去除有害气体和非金属夹杂物,提高温度和调整成分。
[P]对大多数钢来说是有害元素,它在钢中的含量高会引起:“冷脆”,从高温降到0摄氏度以下,钢的塑性和冲击韧性降低,并使钢的焊接性和冷弯性能变差。
[S]对大多数钢来说是有害元素,它在钢中的含量高会引起:“热脆”会使钢的热加工性能变坏,引起高温龟裂,并在金属焊缝中产生气孔和疏松,从而降低焊接强度。
[O]在吹炼过程中,由于吹入了大量的氧气,当吹炼结束,钢水中有大量氧,在钢的凝固过程中,氧以氧化物形式存在,会降低钢的韧性、塑性等加工性能。
炼钢轧钢及辅助系统生产工艺简介
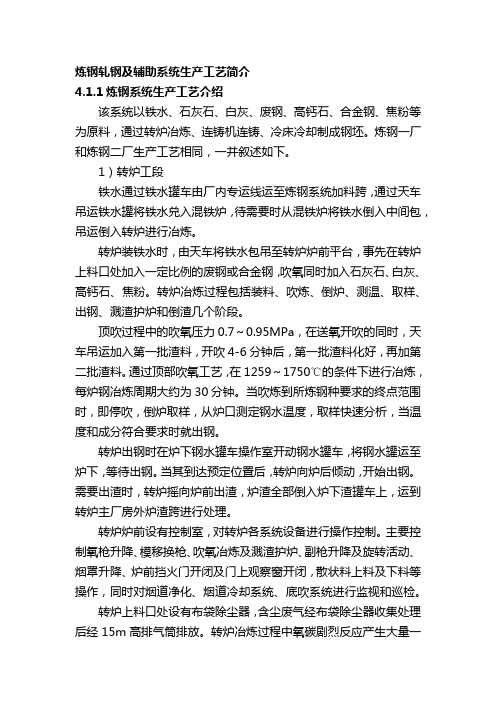
炼钢轧钢及辅助系统生产工艺简介4.1.1炼钢系统生产工艺介绍该系统以铁水、石灰石、白灰、废钢、高钙石、合金钢、焦粉等为原料,通过转炉冶炼、连铸机连铸、冷床冷却制成钢坯。
炼钢一厂和炼钢二厂生产工艺相同,一并叙述如下。
1)转炉工段铁水通过铁水罐车由厂内专运线运至炼钢系统加料跨,通过天车吊运铁水罐将铁水兑入混铁炉,待需要时从混铁炉将铁水倒入中间包,吊运倒入转炉进行冶炼。
转炉装铁水时,由天车将铁水包吊至转炉炉前平台,事先在转炉上料口处加入一定比例的废钢或合金钢,吹氧同时加入石灰石、白灰、高钙石、焦粉。
转炉冶炼过程包括装料、吹炼、倒炉、测温、取样、出钢、溅渣护炉和倒渣几个阶段。
顶吹过程中的吹氧压力0.7~0.95MPa,在送氧开吹的同时,天车吊运加入第一批渣料,开吹4-6分钟后,第一批渣料化好,再加第二批渣料。
通过顶部吹氧工艺,在1259~1750℃的条件下进行冶炼,每炉钢冶炼周期大约为30分钟。
当吹炼到所炼钢种要求的终点范围时,即停吹,倒炉取样,从炉口测定钢水温度,取样快速分析,当温度和成分符合要求时就出钢。
转炉出钢时在炉下钢水罐车操作室开动钢水罐车,将钢水罐运至炉下,等待出钢。
当其到达预定位置后,转炉向炉后倾动,开始出钢。
需要出渣时,转炉摇向炉前出渣,炉渣全部倒入炉下渣罐车上,运到转炉主厂房外炉渣跨进行处理。
转炉炉前设有控制室,对转炉各系统设备进行操作控制。
主要控制氧枪升降、模移换枪、吹氧冶炼及溅渣护炉、副枪升降及旋转活动、烟罩升降、炉前挡火门开闭及门上观察窗开闭,散状料上料及下料等操作,同时对烟道净化、烟道冷却系统、底吹系统进行监视和巡检。
转炉上料口处设有布袋除尘器,含尘废气经布袋除尘器收集处理后经15m高排气筒排放。
转炉冶炼过程中氧碳剧烈反应产生大量一氧化碳含量在60%左右的转炉煤气。
通过冶炼时的降罩,使炉口形成微正压,减少煤气外泄燃烧和空气进入烟道,煤气经降温洗涤除尘后,通过氧气在线分析仪,当氧气含量超过规定的2%时,含尘烟气经通过一次除尘、二次除尘后经旁通阀、三管烟囱、点火器燃烧后经烟囱高空排放。
炼钢系统风险辨识分级管控清单
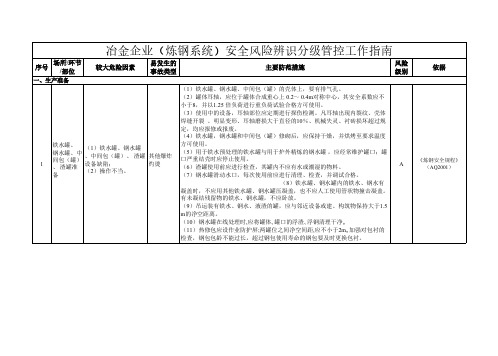
《冶金起重机技术
条件第5部分:铸造
A
起重机》(JBT
铁时吊包高度过高、停
(6)吊运行进途中,吊车必须全程报警提示,防止有人进入吊运区域;下方有
7688.5)
留钢包位置不当;
人时,即使响铃,也要停车等待,等无人后才能动车。吊车与吊车之间保持安全
《起重吊运指挥信
(5)违章操作,吊运
距离,禁止吊车之间顶撞。
(8)扒渣设备的液压系统不得漏油。
《炼钢安全规程》 (AQ2001)
《炼钢安全规程》 (AQ2001)
《炼钢安全规程》 (AQ2001)
3 脱硫 四、炼钢
1 兑铁水
(1)确认脱硫区域各层平台无人。
(2)检查确认铁水罐车地平面无水无潮废物。
(3)搅拌脱硫前要检查确认搅拌器安装完好, 特别是夹紧器,避免搅拌器脱落掉
检查,钢包包龄不能过长,超过钢包使用寿命的钢包要及时更换包衬。
依据
《炼钢安全规程》 (AQ2001)
(1)持吊车指挥合格证的专人将铁水罐指挥吊运至烘烤器罐位,避免撞坏烘烤
器,造成煤气泄漏。
(2)烘烤完毕,烘烤器盖上升到原停放点,避免造成吊车吊物撞坏烘烤器,造
成煤气泄漏。
(1)烧嘴灭火;
(3)检查煤气烘烤器长明火和烧嘴,避免因网管压力过低,造成煤气火熄灭,
(2)管道、阀门泄露
来气后泄漏;发现熄灭立即关阀。
铁水罐、 煤气;
(4)检查烘烤器烘烤介质的各项参数、快速切断阀和熄火检测装置等正常,保
钢水罐、中 (3)烤包区域存放易 中毒和窒息 证长明火不熄,保证正常烘烤进行。
2 间包(罐) 燃易爆物;
灼烫
(5)区域内安装固定式煤气检测报警器。
C
- 1、下载文档前请自行甄别文档内容的完整性,平台不提供额外的编辑、内容补充、找答案等附加服务。
- 2、"仅部分预览"的文档,不可在线预览部分如存在完整性等问题,可反馈申请退款(可完整预览的文档不适用该条件!)。
- 3、如文档侵犯您的权益,请联系客服反馈,我们会尽快为您处理(人工客服工作时间:9:00-18:30)。
三.炼钢系统控制系统:例:1.已知条件:有一座40T 的转炉,铁水包车一辆,需要测钢水温度;铁水温度。
氧气控制系统:氧气流量:0~50m3/h DN50 压力:0~0.6Mpa温度:25℃ 需要流量调节控制。
氮气控制系统:氮气流量:0~50m3/h DN50 压力:0~0.6Mpa温度:25℃ 需要流量调节控制。
冷却水控制系统:冷却水流量:0~50t/h DN50 压力:0~0.6Mpa温度:25℃ 需要流量调节控制2.氧枪控制系统氧枪升降机构采用交流变频电机驱动,由交流变频器控制传动装置。
在传动装置中安装编码器。
根据工艺控制要求输出可频率信号,实现氧枪升降的无级调速控制, 动作曲线如图3.2.1所示。
在转炉生产过程中,氧枪位置的控制是关键, 本系统的氧枪升降有手动和自动两种控制方式。
手动 方式主要用于氧枪在等待点(H 1)以上控制,自动方 式主要用于氧枪在等待点以下的运行控制。
在自动方 式下,氧枪在不吹炼时总处于H 1点,需吹炼时,按 下下枪按钮,氧枪由H 1点快速下降,至开氧点H 2时, 编码器将信号传送到计算机,计算机送出开氧信号,同时转入(自动位置控制)控制,即随着氧枪高度与液面间隙值的减少,不断降 低下降速度,最后准确地停在设定的位置开始吹炼,然后进入枪位曲线控制程序,根据吹氧时间,自动调 氧枪上升曲线(3.1) 整枪位,操作人员也可以根据需要进行手动干预、调整枪位。
当吹炼终止提枪信号发出后,氧枪提升至关氧位置送出关氧信号,至基准点时进行枪位校正(自动动态进行),至等待点氧枪停止,完成一次吹炼。
氧枪的位置是通过安装在氧枪传动装置上的光电脉冲发生器检测后送入计算机的脉冲信号输入卡,经CPU 处理后,将脉冲数转换成氧枪高度显示在主控室CRT 上和操作台LED 数显器上,供操作人员监控。
为了保证吹炼过程连续进行,每座转炉配有两支氧枪,位于炉心位置的称为工作枪,位于备用位置的称为备用枪。
当工作枪在吹炼过程中发生故障,无法吹炼时,可通过按下自动换枪按钮进行自动换枪。
氮气与氧气是互换系统;开氧时停氮,开氮时停氧。
即能计算机自动控制,又能在操作室进行手动操作。
HH 0(最高点) H C (激光点)H 1(等待点) H 2(开氧点) H 3(吹氧点)H B (基准点)APCV(液面)下降上升3.转炉控制系统:见图3.2。
转炉冷却水控制系统见图例3.3。
,.转炉系统氧气、氮气系统检测流程图图3.2转炉系统冷却水系统检测流程图图3.3图中氧气流量调节回路的流量检测系统是带压力温度补偿系统,流量.(流量采用一体化孔板流量计,或涡街流量计)压力(压力采用压力变送器).温度(温度采用铂热电阻)检测点都是防爆系统,需要加检测端安全栅;调节阀采用防爆型调节阀,需要加操作端安全栅。
图中氮气流量调节回路的流量检测系统是带压力温度补偿系统;(流量采用一体化孔板流量计,或涡街流量计)压力(压力采用压力变送器).温度(温度采用铂热电阻)调节阀采用普通型调节阀。
具体型号请参考设备清单:冷却水控制系统:冷却水流量调节系统;流量采用电磁流量计测量流量,调节阀采用普通电子式调节阀。
4.汽化冷却系统:见图3.4。
汽化冷却系统检测流程图图3.4图中液位LT-103是用压力变送器测量液位;一是比液位变送器便宜,二是稳定性好。
图中汽包液位LT-101、LT-102用差压变送器测量液位;选用带自动调节负偏差(零点负偏差移。
测量汽包液位注意安装时加冷凝器。
三阀组。
两台差压变送器最好安装在同一高度上。
图中FT-101蒸汽流量检测采用涡街流量计测量,并带温度压力补偿系统。
涡街流量计安装一般安装在直管段前15后的位置上。
图中FT-102冷却水流量采用电磁流量计测量(内衬采用聚四氟)电压用250V。
(因工厂电源电压不稳定,忽高忽低。
)电磁流量计安装一般安装在直管段5后3的位置上。
250mm 150mmDN50电磁流量计图中FVC-102流量调节采用电子式调节阀进行流量调节。
图中LIC-102是流量调器或者用控制器进行编程。
模拟量是四进两出,是典型的三冲量控制系统。
汽化冷却系统中,汽包液位控制是汽化冷却系统中的关键。
在炼钢系统中汽包水位控制是极其重要的。
它关系到汽包安全运行。
如果水位过高,会影响汽水分离的效果;若水分带入过热器,将引起管壁结水垢,严重的还会使用汽设备发生故障。
而水位过低,则会破坏汽水循环,最严重的情况会使汽包发生爆炸。
同时汽包产生蒸汽流量很大,而汽包的体积相对来说较小,液位的时间常数很小,若给水不及时,数十秒之内就可能达到危险水位,所以汽包水位控制有着特别重要的意义。
汽包给水自动控制的任务,就是控制给水流量,使其适应蒸发量的变化。
蒸汽流量是可以根据需要变化的。
只要调节好给水流量,就能使汽包水位维持在某一合适的水位上。
在大、中型锅炉给水控制系统中,三冲量控制系统应用很广。
除这三个主控制信号,还需要加一些保证安全运行,给水流量能按需要变化的措施,所以控制系统就显得特别复杂。
下面讨论三冲量控制,见图3.5。
和利用计算机系统或仪表控制系统实现的情况。
图3.5给水控制对象结构给水对象如图3.5所示。
给水流量Qw和蒸汽流量Qs是影响水位(L)变化的两个主要扰动。
当给水压力波动时给水流量亦发生相应变化,这将引起水位变化。
简单的给水控制只引进水位信号组成单冲量控制系统。
单冲量控制系统不能克服虚假水位对水位控制的不良影响。
当蒸汽流量大幅度增加时,由于假水位上升,调节器输出信号不但不去开大调节阀增加给水流量,以维持水位,反而去关小调节阀,减少给水量,使水迅速下降。
把蒸汽流量的信号引入控制系统,就基本上克服了虚假水位对控制的不良影响。
因为蒸汽流量增加时,会使水位波动,但由于蒸汽流量增加,直接增加给水量。
因此可以说蒸汽流量信号的变化,超前于水位的变化。
蒸汽流量参与控制是在水位还未出现变化前使调节阀动作,从而达到减少水位波动的目地,由此得名叫前馈控制。
这时水位控制系统成为双冲量控制。
在汽化锅炉中经常采用这种控制策略。
由于给水管道中的给水压力经常要波动,虽然给水流量已经控制,但由于阀前压力波动,也会引起水位波动。
通常情况下采用压力补偿给水位的控制策略。
这样在控制系统中,除水位信号,蒸汽流量信号外,还有给水流量信号。
在给水管道中加流量检测装置,用它测量测量给水流量,这样水位控制系统就成为三冲量的控制系统。
控制方框图见图3.6。
系统功能图见图3.7(用仪表完成三冲量控制)。
计算机组态图见图3.8图3.6中蒸气流量检测采作一体化流量孔板流量计或涡街流量计,并带压力、温度补偿。
图3.6中补水流量检测采用电磁流量计测量,要求电磁流量计内衬采用聚四氟乙烯。
图3.6中汽包液位检测采用EJA智能型差压变送器或罗斯蒙特差压变送器。
要求带负迁移;汽包水位测量范围在-600mmH2O到+600mmH2O。
正常控制在0.0mmH2O之间。
调节阀采用电子式调节阀调节给水流量精度。
(调节阀采用进口或合资例如:无锡精工;吴忠仪表厂;及私企瑞安球精仪表厂)图3.6三冲量水位控制系统方框图在控制系统中一般检测元件及传感器都是都是在反馈回路中,调节阀和控制对象在主回路中。
控制器在主回路中;控制器有几种方式:一是用仪表实现控制器的功能;二是PLC 系统中的控制调节单元;三是DCS系统实现控制;四是计算机系统实现控制调节系统。
图3.7三冲量水位仪表控制调节系统图图3.7是汽包液位三冲量液位仪表控制调节系统:其中压力变送器、涡街流量计、热电阻是安装在现场;液位变送器、电磁流量计、电子式调节阀也安装在现场。
测量蒸汽流量时注意要加压力、温度补偿系统;要求蒸汽流量在控制室仪表盘上显示,并参与调节控制。
图3.7中FIQ-101PI-101TI-101都是二次表;安装在仪表上。
压力变送器、涡街流量计都是两线制:供电24V,接收4~20mA信号;因此,要求二次仪表具备本身供电220V~同时提供给变送器24V直流电压,接收4~20mA信号;流量积算仪即要接收流量信号;还要接收压力信号和热电阻信号。
涡街流量计现场安装要求工艺留出管径的前15D后5D的安装位置。
测量汽包液位的差压变送器也是两线制。
测量供水流量的电磁流量计是四线制:220V~供电,接收4~20mA信号;二次表具备本身供电220V~接收4~20mA信号的流量积算仪。
LIC-102是三冲量调节用的控制器:有4入2出的4~20mA信号功能。
是霍尼韦尔公司的630系列。
同时输入蒸汽流量信号、补水流量信号、汽包液位信号2组;输出调节阀信号。
5.控制要求:1)要求计算机画面显示控制动态状态;报警画面。
随时监视各台泵的工作情况及流量、压力、温度、液位状态。
并进行打印及报表。
监视氧枪高度及下枪情况。
2)机旁控制;控制室控制。
6.设计思想:1)首先要向水道工艺提出资料:要泵的参数;水管的管径、流量、压力、温度。
向工艺专业提出资料:要氧枪行程;电机功率、向电力提出资料:用电量、负荷、电压等级、380V、220V、电流(A)控制室照明向土建提出资料:控制室的面积、开孔地点、尺寸、电缆沟的位置、预埋件。
仪表井位置。
2)先画检测流程图:见图3.2;3.3;3.4将各检测点在系统中标出,并标出管径,流量,压力,温度,液位进机点。
从各专业所提出的资料中可以看出所要的参数。
2)统计输入输出点数,并写入点号表中:见图图3.2输入输出点号表3)画计算机系统配置图:见图3.9 方案一见图3.10 方案二图3.9转炉系统计算机系统配置图(方案一)图3.10转炉系统计算机系统配置图(方案二)方案一,方案二看配置没有太大的变化,实际上并不一样。
方案一设计更趋于合理一些,而且价格便宜,性能较好。
从设计清单中可以看出差4万元左右。
方案一用两家产品。
开关量部分用SIMZ产品;模拟量部分用SIX或泓格产品。
SIX;与泓格产品都是将PC嵌入到控制器中,多省一台PC机。
也是世界发展方向。
方案二用SIMZ产品;但SIMZ产品有点缺陷,热电阻模块爱坏,模拟量输入输出模块又价格太高;通过网络通讯超过50m信号太弱。
注意:在选用PLC系统中,不要过分相信厂家的产品说明书,他说能用户1000个点,但实际上用300~4005)画氧枪系统电气系统原理图:见图3.11图3.11氧枪系统电气控制系统原理图分机旁控制和计算机控制.6)设计选型:压力:选E+H压力变送器425系列智能变送器。
选罗斯蒙特1751系列压力智能变送器。
选EJA系列智能压力变送器。
温度:铂热电阻WZP230系列钢水测温仪KZ300GB系列采用北京科海龙华工业自动化仪器有限公司。
流量:选上海光华·爱而美特电磁流量计IFM4080系列。
液位:池子选用导压式液位变送器;水箱选用压力变送器测液位。