夹杂物成分及形态控制
夹杂物的生成及控制

夹杂物的生成及控制作者:shicm 发表日期:2007-5-28 阅读次数:7631 非金属夹杂物情况及分类按其化学成分组成和结构可以分以下几类(1)氧化物夹杂:单一金属氧化物、硅酸盐、尖晶石和各种钙铝酸盐;(2)硫化物夹杂:MnS、CaS等,在轧制过程中具有良好的变形能力;(3)磷化物夹杂:CaP、BaP等还原脱磷产物,在一般钢种中较少出现;(4)氮化物夹杂:TiN、ZrN等夹杂物,是钢液从大气中吸氮的产物;(5)含不同类型夹杂物的复合夹杂。
按其来源主要分为两类:(1)外来夹杂物,主要来源为炉渣卷入钢液形成的卷渣、钢液或炉渣与炉衬耐火材料接触时的侵蚀产物、铁合金及其它炉料带入的夹杂等等,在浇铸过程未及时上浮而残留在钢中,它偶然出现,外形不规则,尺寸大,危害极大;(2)内生夹杂物,在液态或固态钢中,由于脱氧和凝固时进行的各类物理化学反应而形成的,主要是和钢中氧、硫、氮的反应产物,它的形成有四个阶段,钢液脱氧反应时形成的成为原生(一次)夹杂;出钢和浇铸过程中温度下降平衡移动时形成的成为二次夹杂;钢水凝固过程中生成为再生(三次)夹杂;固态相变时因溶解度变化而生成的成为四次夹杂;由于一次、三次夹杂生成和析出的热力学和动力学条件最有利,因此可以认为内生夹杂大部分是在脱氧和凝固时生成的,因此控制夹杂最主要的就是要加强脱氧和严格防止二次氧化。
(3)一些尺寸较大的多相复合结构的夹杂物,有时是不同类型的内生夹杂复合而成,有时则是内生夹杂物与外来夹杂物互相包裹而形成的。
为了方便生产评级和比较,按照标准评级图显微检验法根据夹杂物形态和大小分布将夹杂物分为A、B、C、D、DS五类,这五大类夹杂物代表最常观察到的夹杂物的类型和形态:—A类(硫化物类):具有高的延展性,有较宽范围形态比(长度/宽度)的单个灰色夹杂物,一般端部呈圆角;—B类(氧化铝类):大多数没有变形,带角的,形态比小(一般<3),黑色或带蓝色的颗粒,沿轧制方向排成一行(至少有3个颗粒);—C类(硅酸盐类):具有高的延展性,有较宽范围形态比(一般>3)的单个呈黑色或深灰色夹杂物,一般端部呈锐角;—D类(球状氧化物类,如钙铝酸盐):不变形,带角或圆形的,形态比小(一般<3),黑色或带蓝色的,无规则分布的颗粒;—DS类(单颗粒球状类):圆形或近似圆形,直径>13μm的单颗粒夹杂物。
304不锈钢中夹杂物的控制

304不锈钢中夹杂物的控制304不锈钢是一种广泛应用的奥氏体不锈钢,具有优良的耐腐蚀性和高温强度。
然而,夹杂物的存在可能会对其组织和性能产生不利影响。
因此,控制304不锈钢中的夹杂物对于保证其质量和性能具有重要意义。
本文将介绍夹杂物控制的重要性、夹杂物的来源和分类,以及夹杂物控制的措施和效果。
夹杂物是指存在于金属内部或表面的非金属杂质。
在304不锈钢中,夹杂物可能会破坏材料的连续性,导致应力集中,降低材料的耐腐蚀性和力学性能。
夹杂物对304不锈钢组织和性能的影响主要表现在以下几个方面:降低材料的耐腐蚀性:夹杂物能够破坏不锈钢表面的氧化膜,加速局部腐蚀,降低材料的耐腐蚀性。
降低材料的力学性能:夹杂物会破坏材料的连续性,导致应力集中,降低材料的强度和韧性。
影响材料的加工性能:夹杂物可能引起材料加工过程中的缺陷,如裂纹、折叠等,影响加工质量和精度。
夹杂物主要分为有意夹杂物和无意夹杂物。
有意夹杂物是人为添加的,如为了改善材料的某些性能而特意加入的合金元素。
无意夹杂物是在冶炼、加工过程中引入的,如炉渣、耐火材料、以及与炉气、熔剂、燃料等反应生成的产物。
为了控制304不锈钢中的夹杂物,可以采取以下措施:增加夹杂物球化处理:通过适当的热处理,使夹杂物呈球形颗粒分布,降低其对材料性能的不利影响。
控制原材料及熔炼过程:选用低杂质含量的原材料,严格控制熔炼工艺,避免过度氧化和污染。
精炼和净化处理:采用精炼技术,如电渣重熔、真空熔炼等,去除熔体中的夹杂物;同时,进行净化处理,如加入稀土元素细化晶粒,提高材料的纯净度。
合理安排工艺流程:在加工过程中合理安排工艺流程,避免过度变形和加热,以减少夹杂物的引入。
采取上述控制措施后,可以显著降低304不锈钢中的夹杂物数量和尺寸,改善材料的组织和性能。
具体效果如下:夹杂物形态:通过控制措施,可以使夹杂物呈球形或不规则形态分布,降低其对材料性能的不利影响。
夹杂物分布:采取控制措施后,夹杂物分布更加均匀,避免了局部浓度过高现象,降低材料脆性。
IF钢中成分及夹杂物的过程控制研究

IF钢中成分及夹杂物的过程控制研究一、本文概述随着现代工业的发展,钢铁材料作为国民经济的重要支柱,其质量和性能的提升对于满足社会生产的需求至关重要。
IF钢(Interstitial Free Steel,无间隙原子钢)作为一种优质的低碳钢,以其高强度、高韧性、良好的焊接性和成形性等特点,在汽车、石油、化工、建筑等领域得到了广泛应用。
然而,IF钢的生产过程中,钢中成分的控制以及夹杂物的控制对于其最终性能的影响至关重要。
因此,本文旨在深入研究IF钢中成分及夹杂物的过程控制,为提高IF钢的质量和性能提供理论支持和实践指导。
本文将首先介绍IF钢的基本特性和应用领域,阐述研究IF钢中成分及夹杂物过程控制的必要性。
接着,将重点分析IF钢生产过程中成分控制的关键因素,包括碳、氮、氧等主要元素的含量控制,以及合金元素的添加和调整。
还将探讨夹杂物对IF钢性能的影响及其形成机制,提出有效的夹杂物控制策略。
在此基础上,本文将总结国内外在IF钢成分及夹杂物过程控制方面的研究成果和进展,以期为我国IF钢生产技术的进步提供借鉴和参考。
通过本文的研究,期望能够为IF钢的生产过程优化提供理论依据,为提升我国钢铁工业的整体竞争力做出贡献。
二、IF钢的成分控制IF钢(Interstitial-Free Steel)作为一种高级别的深冲用钢,其成分控制对于最终产品的质量和性能具有至关重要的影响。
成分控制不仅关乎钢的强度、韧性、耐腐蚀性,还直接影响到其深冲加工性能和表面质量。
因此,对IF钢的成分进行精确控制是提升产品质量、满足市场需求的关键。
在IF钢的生产过程中,碳(C)、氮(N)和硫(S)等元素是需要特别关注的。
碳元素是影响IF钢性能的主要因素之一,通过降低钢中的碳含量,可以有效提高钢的深冲性能和焊接性能。
氮元素同样对钢的强度、韧性和焊接性有显著影响,因此需要通过精确控制冶炼和精炼过程来降低钢中的氮含量。
硫元素虽然在一定程度上可以提高钢的切削加工性能,但过高的硫含量会导致钢的韧性降低,因此也需要对其进行严格控制。
宝钢金属夹杂标准

宝钢金属夹杂标准
宝钢金属夹杂标准主要涉及以下几个方面:
1. 夹杂物分类:根据夹杂物的性质和形态,宝钢金属将其分为以下几类:A类(金属氧化物)、B类(非金属氧化物)、C类(金属硫化物)、D类(非金属硫化物)和E类(其他夹杂物)。
2. 夹杂物等级:宝钢金属夹杂物等级分为五个级别,分别为:I级(清洁度最高)、II级(清洁度较高)、III级(清洁度一般)、IV级(清洁度较低)和V级(清洁度最低)。
3. 夹杂物检测方法:宝钢金属采用以下几种方法检测夹杂物:光学显微镜观察、扫描电子显微镜(SEM)观察、X射线衍射(XRD)分析、能谱分析(EDS)等。
4. 夹杂物控制要求:宝钢金属在生产过程中,对各类夹杂物含量有一定的控制要求。
例如,对于氧化物夹杂,要求其总量不超过某一限值;对于硫化物夹杂,要求其形态和分布满足一定要求等。
5. 夹杂物去除和减少措施:为了提高金属产品的纯净度,宝钢金属采取了一系列去除和减少夹杂物的措施,如:选用高品质原料、优化冶炼工艺、严格控制浇注温度和冷却速度、采用净化剂净化金属液等。
这些标准旨在确保宝钢金属产品的质量和性能,满足国内外市场的需求。
同时,宝钢金属也不断研究和探索新的夹杂物控制技术,以进一步提高产品竞争力。
钢帘线用盘条夹杂物成分控制技术对比

p o u e y A,B se l a t r n J p n a d C, E se lfco n d me t r r h l g b ev d a d c mp s in rd c d b t e f co y i a a n D, t e a tr i o si wee mop oo y o s r e n o o i o y c t a ay e y S M.T e c nr lo n l so s i i o o te o d h s t o meh d T e v h 2 3i te t e nlzd b E h o t fi cu i n n w r r d frse l r a w t o s. o rmo e t eA1 O n se l, o e c h
钢 厂 生 产 的钢 帘 线 用 盘 条 的夹 杂 物 进 行 形 貌 观 察 和 成 分 分 析 。 钢 帘 线 用 盘 条 夹 杂 物 成 分 控 制 主 要 有 2种 方 式 。
去除钢 中的 A 使 夹杂物中 S 于含量较 高的范围 ; I , 0 i 处 ቤተ መጻሕፍቲ ባይዱ 采取措施使钢 帘线用 盘条的夹杂物中 A , 1O 质量分数控
CHANG i u Gu— a,G U Da y n h O —o g,GAO n Ha g,GENG i h a g , J— u n s
XUE J n, ANG n — i u W Big x ,CAO - a Ya d n
( n ags e C ,t. A sa 10 1 C ia A g n el o Ld , nh n14 0 , h ) t n
制 在 2 % 左 右 , C O)w( i: 在 0 2~10的低 熔 点 、 变 形 区 。 0 W( a / SO ) . . 易 关 键 词 钢 帘 线 ; 条 ; 杂 物 ; 谱 分 析 盘 夹 能
IF钢中成分及夹杂物的过程控制研究共3篇
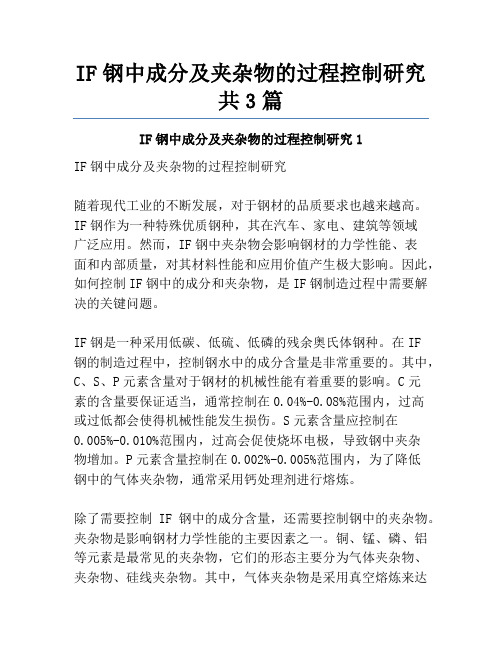
IF钢中成分及夹杂物的过程控制研究共3篇IF钢中成分及夹杂物的过程控制研究1IF钢中成分及夹杂物的过程控制研究随着现代工业的不断发展,对于钢材的品质要求也越来越高。
IF钢作为一种特殊优质钢种,其在汽车、家电、建筑等领域广泛应用。
然而,IF钢中夹杂物会影响钢材的力学性能、表面和内部质量,对其材料性能和应用价值产生极大影响。
因此,如何控制IF钢中的成分和夹杂物,是IF钢制造过程中需要解决的关键问题。
IF钢是一种采用低碳、低硫、低磷的残余奥氏体钢种。
在IF钢的制造过程中,控制钢水中的成分含量是非常重要的。
其中,C、S、P元素含量对于钢材的机械性能有着重要的影响。
C元素的含量要保证适当,通常控制在0.04%-0.08%范围内,过高或过低都会使得机械性能发生损伤。
S元素含量应控制在0.005%-0.010%范围内,过高会促使烧坏电极,导致钢中夹杂物增加。
P元素含量控制在0.002%-0.005%范围内,为了降低钢中的气体夹杂物,通常采用钙处理剂进行熔炼。
除了需要控制IF钢中的成分含量,还需要控制钢中的夹杂物。
夹杂物是影响钢材力学性能的主要因素之一。
铜、锰、磷、铝等元素是最常见的夹杂物,它们的形态主要分为气体夹杂物、夹杂物、硅线夹杂物。
其中,气体夹杂物是采用真空熔炼来达到控制的。
夹杂物控制主要采用铝剂、钝化剂来控制,将夹杂物和夹杂物粒子分散固溶。
夹杂物控制涉及到工艺流程中的温度、时间、气氛等多个因素。
其中,温度是控制夹杂物形成和发展的最主要因素。
在熔炼过程中,温度不稳定会导致夹杂物粗化、合并,影响到产品的质量。
时间是影响夹杂物生成的另一个因素。
时间越长,夹杂物的净化越好,但同时也会增加钢材的消耗和制造成本,因此需要在时间与效果之间做出平衡。
气氛对于夹杂物的控制也是至关重要的。
在IF钢制造过程中,要求钢水在加工过程中不氧化,因此需要高纯氧化铝和氮气配制的高保护因素。
总而言之,IF钢中成分及夹杂物的过程控制是IF钢提高品质的关键。
满足钢中DS类等夹杂物及其他严格要求的生产实践

满足钢中DS类等夹杂物及其他严格要求的生产实践摘要经过前期研究钢中Ds类夹杂物的形成机理,配合电镜能谱分析,对比试验前后Ds类夹杂物种类及演变。
通过生产工艺优化试验,包括精炼渣系优化,硅钙线使用量等试验,形成可靠生产控制工艺。
满足客户严格要求,每炉检验四个样,铝脱氧非金属夹杂物B类粗系≤1.0级、DS类≤0.5级,淬透性A、B面差≤4HRC, Ti/N要求控制4~8等。
关键词 Ds类夹杂物非金属夹杂物钙处理铝脱氧高铝渣系镁铝尖晶石随着科技的快速发展,对原材料的质量要求日益提高,下游客户对钢中夹杂物含量的要求也越来越苛刻。
其中大型球状夹杂物(Ds类)会显著降低产品的疲劳寿命,然而在实际生产中处理不当就会产生Ds类夹杂物,且只要产生级别基本都>0.5级。
基于铝脱氧的钢种,在单炉次取样频次提高的基础上,B类夹杂物粗系≤1.0级也比较严格。
同时还要保障生产节奏及成分控制的稳定,以满足淬透性、Ti/N等要求。
为满足客户以上要求,结合装备、工艺,研究理论基础,通过前期的相关试验,制定相关攻关方案。
1.Ds类夹杂物形成机理及形貌研究表明Ds类夹杂物主要分为几种:一种为形核部位为镁铝尖晶石,外层钙铝酸盐的二层复合物;一种为心部含有钙铝酸盐,其外围附有CaS的二层复合物;再有就是三层复合物。
镁铝尖晶石(熔点2135℃)首先形成夹杂物的核心,钙铝酸盐(熔点1455-1875℃)包裹镁铝尖晶石,最外层为CaS。
镁铝尖晶石是构成Ds类夹杂物的主因之一,不含镁铝尖晶石的纯钙铝酸盐的Ds夹杂物仅占20%。
在显微镜下寻找大级别Ds类夹杂,再用SEM观察形态,并利用能谱分析定性鉴定以及电镜扫描,发现我公司轴承钢Ds类夹杂物分为几种:一是形核部位为镁铝尖晶石,外层钙铝酸盐的二层复合物(见图1+图2);二是Ca-Mg-Al-O复合态夹杂物(见图3);三是外包有硫化物的复合型夹杂物(见图4)。
其中第三类最多,并经常伴有Ba元素。
图1 镁铝尖晶石核心图2 外围钙铝酸盐图3 Ca-Mg-Al-O复合态夹杂物图4 外包有硫化物的复合型夹杂物2.控制Ds类夹杂物的工艺理论、优化及试验2.1转炉终点控制转炉终点C控制在0.10%以上,以降低钢中总氧量,从而避免出钢过程经铝强脱氧后,形成大量细小的Al2O3质点,为Ds类夹杂形成起到形核作用。
夹杂物控制攻关方案

夹杂物控制方案夹杂物控制是高品质钢生产的关键环节,也是控制生产成本的重要环节。
非金属夹杂物降低了钢的塑形、韧性和疲劳寿命,使钢的冷热加工性能乃至某些物理性能变坏。
中厚板生产,采用铝脱氧工艺,容易出现B类夹杂超标,连铸过程往往在铸坯1/4处夹杂物富集,存在大量的大颗粒氧化物脆性夹杂,造成板材B类夹杂物超标。
除此之外,A类硫化物夹杂主要是在钢水凝固过程,随着温度的降低,1415℃时开始大量析出,1000℃左右全部析出,针对凝固过程控制冷却强度等控制A类夹杂物。
接下来要开展的工作方案如下:一、B类夹杂物控制改善1)转炉终点氧含量。
夹杂物的多少与钢水中氧含量有直接的关系,控制终点氧含量,通过副枪测定[%C]和[%O],保证波动在C-O平衡曲线附近。
通过炼几炉235B钢种,统计一下转炉终点[%O].[%C]=0.16 T=1600℃ Pco=100KPa,得出理论[%O]=160ppm。
2)脱氧剂的选择。
ASM复合脱氧剂的脱氧能力大于单一Al脱氧剂,不同脱氧剂形成脱氧产物不同,脱氧剂的消耗量也不同。
选择不同的脱氧剂,加入量如何确定?3)严禁转炉出钢下渣,通过检测包渣(FeO+MgO)。
4)出钢脱氧后吹氩去除脱氧产物。
不同脱氧剂形成的脱氧产物不同,大部分为低熔点液态大颗粒产物,氩气流量的控制加速夹杂物的上浮去除。
5)精炼工艺。
根据进站[%O],目标[%O]决定喂多少铝线,在此基础上进行Ca处理,喂多少Ca线必须通过理论计算,生成C12A7。
根据钙处理后变性产物,决定精炼渣系成分的选择,包括碱度、MI指数、w[%FeO+MgO]、w[Al2O3]。
出站前,软吹气量控制,是根据流量计还是根据渣眼裸露直径?6)防止二次氧化。
全程保护浇注,长水口及浸入式水口氩封。
二、A类夹杂物控制改善硫化物夹杂主要是在钢的凝固过程析出,控制工艺从两方面下手:1、LF深脱硫,使得钢中[%S]降低;2、改善冷却条件,调整冷却速率,二冷配水如何使得MnS选分析出。
金属材料学思考题答案1

金属材料学思考题答案11.简述什么是材料科学研究材料组分、结构、性能相互关系和变化规律的科学,是一门基础应用学科。
2.什么是工程材料?工程材料分为哪些类别?凡与工程相关的材料均可称为工程材料。
按性能可分为结构材料和功能材料;按化学方法分为金属材料,陶瓷材料,高分子材料和复合材料。
3.什么是新材料?开发新材料的重要意义是什么?新材料:相对于传统的材料而言。
经过新工艺新技术制造的整合原有材料的功能的材料。
意义:对高科技和新技术的发展具有非常关键的作用;是发展高科技的物质基础;是国家在科技领域处于领先地位的标志之一。
4.钢的分类方法很多通常有哪些分类?按冶金方法分:平炉、转炉、电炉(镇静钢、半镇静钢,沸腾钢)。
按化学成分分:碳钢(普通碳钢,优质碳钢),合金钢(合金元素,合金含量);按质量分:普通质量钢,优质质量钢,高级优质钢。
按金相分:退火态(P+F,珠光体钢,P+Fe3C),正火态(珠光体钢,贝氏体钢,奥氏体钢);冷却时有无相变(铁素体,马氏体,奥氏体,双相钢);按用途分:工程结构钢,机器零件用钢,工程模具用钢,特殊用钢(不锈钢,耐热钢、磁钢)。
5.通常钢中的P,S控制钢的质量,按质量等级碳素钢,合金钢的钢材质量可分为哪些等级,P,S含量是如何控制的可分为:普通质量钢,优质钢,高级优质钢三个等级。
碳素钢合金钢S%P%S%P%普通质量钢0.0450.0450.0450.045优质钢0.0350.0350.0350.035高级优质钢0.0300.0300.0250.0256.合金元素在钢中的分布或存在的形式有哪几种?可分为五种情况:1)形成非金属夹杂物(如氧化物、氮化物和硫化物等),2)溶入固熔体,3)形成碳化物,4)自由存在,5)金属间化合物。
7.按化学成分如何区分低中高碳钢和低中高合金钢?碳钢:(含碳量)低碳钢≤0.25%,中碳钢0.3-0.6%,高碳钢≥0.6%;合金钢:(合金元素)低合金钢<5%,中合金钢5-10%,高合金钢>10%8.利用晶界偏聚理论解释钢的第二类回火脆性以及硼钢的淬透性问题钢的溶质原子在晶界的浓度大大超过在基体中的平均浓度的现象,称为晶界偏聚。
夹杂物成分及形态控制
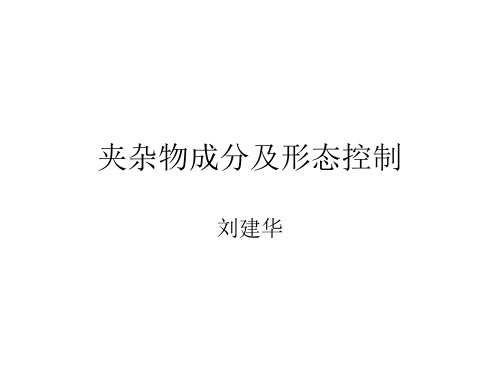
钢帘线夹杂物控制实验室研究
• 当炉渣碱度为0.71~1.36,Al2O3含量低于8 %时,可以将夹杂物的成分控制在塑性区 或其周边的区域。
夹杂物中的Al2O3含量随着钢液中酸溶铝含量的 增加而增加,当夹杂物中Al2O3含量为8%~25 %,钢液[Al]s含量应控制在0.0006%以下。
夹杂物成分及形态控制
刘建华
1. 概述
• 夹杂物成分和形态控制技术是现代洁 净钢冶炼的主要内容之一,不同用途的 钢材对非金属夹杂物的形态、数量、 组成有不同的要求.
• 根据钢种的要求及夹杂物的性质提出 夹杂物成分和形态控制要求。
• 根据钢-夹杂物反应热力学,利用MnO-Al2O3SiO2和CaO-Al2O3-SiO2等三元系图内钢液成分 等值线来预测夹杂物组成及钢液中氧、硅、锰、 铝、钙等成分的控制,并制定顶渣成分控制.
• 部分钢种还需结合S-Me反应热力学提出 钢中硫含量控制策略
• 问题:1)夹杂物是多元的;2)夹杂物有 时熔点较高,是固态的,反应未达到平衡; 3)炼钢、精炼工艺对夹杂物组成影响较大; 4)热力学相图局部区域组元活度测量有较 大误差
2. 脱氧剂对夹杂物成分的影响
• 脱氧剂对内生夹杂物的成分存在巨大影响。 • 根据钢种和产品质量,脱氧分为三种模式:
USS/KOBE钢厂精炼过程中夹杂物成分变化在相图中的体现
2)Kakogawa Works钢厂采用BOF-LF- CC工艺生产钢帘线
Kakogawa Works钢厂夹杂物成分变化在精炼过程中的变化
• Mn/Si低时形成SiO2夹杂会导致水口堵塞;Mn/Si 高时生成典型的液态MnO•SiO2,夹杂物容易上 浮。因此因调整钢成分,保持Mn/Si>2.5,
铸件中的夹杂物来源及其危害

铸件中的夹杂物来源及其危害铸件中的夹杂物主要影响铸件的疲劳强度、加工性能、组织性能,还是铸件裂纹产生的原因之一。
但是,在铸件中不可避免存在一定数量的微观夹杂物,一般数量在10的7次方和10的7次方范围内,也就是在70000000--700000000之间。
任何事物都是有利有弊,夹杂物也是如此,数量过多,影响铸件质量,造成铸件缺陷。
控制在一定范围内,有利于铸件凝固结晶、生核,我们铸造工作人员要做的就是把它们的数量控制在我们需要的范围,造富我们的生产即可。
在铸造中,夹杂物来源主要为内生和外生源头内生夹杂物来源于:1.脱气、脱硫物,特别是一些密度大的脱氧产物未及时排除。
2.随合金温度的降低,硫、氧、氮等元素的溶解度相应下降,达到过饱和,这些过饱和析出的组元以低熔点共晶或化合物的形式残留于铸件。
内生夹杂物的类型和组成取决于合金的熔炼工艺与合金成分。
外生夹杂物来源于:1.合金液与金属料表面的粘砂、锈蚀、熔渣,以及与炉衬、包衬等相互作用而生成的非金属夹杂物。
2.合金液被大气氧化生成的氧化物。
外来夹杂物多为成分复杂的氧化物,其尺寸较大,形状多呈多角形,分布无规律。
上面是金属夹杂物在铸件中的来源,下面我们再聊一聊夹杂物对铸件的影响。
非金属夹杂物对铸件质量的影响:一是影响冲击吸收量和疲劳极限等力学性能。
文章开篇我们就说了,各种铸件中不可避免的存在一定量的夹杂物。
这些夹杂物中氧化夹杂物对钢类铸件冲击吸收能量的影响很大。
夹杂物会使材料的疲劳强度极限降低。
夹杂物越粗大,材料的疲劳极限就越低。
夹杂物往往还是零件断裂的裂纹源。
尖角形夹杂物引起应力集中,加快零件的破坏。
二是影响铸造性能。
合金中含有固态夹杂物时,其流动性降低。
分布在晶界上的低熔点夹杂物是铸件产生裂纹的原因之一。
低熔点夹杂物还会促进铸件产生微观缩孔和缩松。
三、夹杂物对铸件有益的影响在某些情况下非金属甲酰胺物对铸佣质量有良好的影响。
例如,钢中的氧化物、硫化物和铸铁中的磷共晶能提高材料的硬度,增加耐磨性。
钢中夹杂物控制原理

钢中夹杂物控制原理钢中氧的存在形式T[O]=[O]溶+[O]夹(1)转炉吹炼终点:[O]夹=>0,T[O]→[O]溶=200~1000ppm[O]溶决定于:l 钢中[C],转炉吹炼终点钢中[C]与a[O] 关系如图l 渣中(FeO);l 钢水温度。
1 顶底复吹转炉炉龄C–Fe的选择性氧化平衡点根据式[C] + [O] = {CO} (1) lg (Pco/ac* [%O])= 1149/T–2.002以及反应[Fe] + [O] = (FeO)(2) lg aFeo/[%O] = 6317/T – 2.739得到反应(FeO)+ [C] = [Fe] + {CO} (3) lg (Pco/ac* aFeo)= –5170/T+4.736 结论钢液中C-Fe的选择性氧化平衡点为[C]=0.035%,也就是说终点[C] < 0.035%时,钢水的过氧化比较严重。
图1-1的统计数据也说明了这点。
同时由式(1)可以求出此时熔池中的平衡氧含量为740ppm。
理论分析1)终点[C]-[O]关系1) 当终点[C]<0.04%时钢水的终点氧含量较高2) 当终点[C]在0.02~0.04%范围时,有些炉次钢水氧波动在平衡曲线附近(区域Ⅰ)有些炉次钢水氧含量则远离平衡曲线(区域Ⅱ),说明在该区域钢水过氧化严重。
2)温度对氧含量的影响在终点[C] = 0.025~0.04%时,终点氧含量虽然较分散,但总的趋势是随着终点温度的升高,终点氧基本呈上升趋势。
1620℃~1680℃之间,氧含量总体水平较低,平均为702ppm ,该范围的炉次共占总炉次的30%左右;出钢温度大于1680℃时,终点钢水氧含量有明显的升高趋势,平均为972ppm ,占总炉次的70%左右。
3)终渣氧化性对终点氧的影响20040060080010001200140016001800160016201640166016801700172017401760终点温度(℃)终点氧含量(p p m )终点[0]0200400600800100012001400160018001214161820222426炉渣中(FeO+MnO)的含量(%)终点氧含量(p p m )终点[0]1416182022242600.020.040.060.080.10.12终点碳含量(%)渣中(F e O +M n O )含量 %MnO+FeO渣中(FeO+MnO )增加,终点[O]有增加趋势;终点[C]<0.04%,渣中(FeO+MnO )增加且波动较大,说明此时吹氧脱碳是比较困难的,而铁则被大量氧化。
高炉铁合金对钢铁液相中夹杂物形成的影响

高炉铁合金对钢铁液相中夹杂物形成的影响引言:夹杂物是冶金工程中不可避免的问题,它们对钢铁的性能和品质产生着重要影响。
其中,高炉铁合金作为一种重要的添加剂,在钢铁冶炼过程中发挥着重要作用。
本文旨在探讨高炉铁合金对钢铁液相中夹杂物形成的影响,并探讨一些减少夹杂物生成的方法。
一、高炉铁合金的种类及添加时机高炉铁合金是一种通过高炉还原过程中产生的铁合金,包括硅铁、锰硅铁、镁铁等。
它们在钢铁冶炼过程中根据需要添加,以调整钢液的成分和性能。
添加高炉铁合金的时机主要有三个:在高炉炉石入炉时进行原料料位调整,亦即在炉石装入路径上添加;在给高炉供冷却水的空冷壁管或加热面上边缘部分添加高炉铁合金;炉渣场或装渣方式中键在装渣船上边缘部分添加高炉铁合金。
二、高炉铁合金对夹杂物形成的影响1. 脱氧作用高炉铁合金中含有丰富的硅、锰等元素,这些元素在钢铁冶炼中起到一定的脱氧作用。
通过与氧反应生成相应的氧化物,可以有效地减少钢液中的溶解氧含量,并防止夹杂物的形成。
而溶解氧是夹杂物生成的主要原因之一。
因此,添加高炉铁合金有助于降低钢铁液相中的夹杂物含量。
2. 夹杂物形核作用高炉铁合金中的硅、锰等元素可以形成一些夹杂物形核,使其他夹杂物向其结晶,形成更稳定的结构。
这些形核可以分散夹杂物,减少其对钢铁性能的影响。
因此,高炉铁合金的添加可以促进夹杂物的分散,并改善钢铁的整体性能。
3. 夹杂物的形态调控高炉铁合金中的一些添加元素(如锰、硅等)可以影响钢铁中夹杂物的形态和组成。
通过调控添加量和添加时机,可以使夹杂物在钢铁冶炼过程中以比较稳定的形式存在,有利于对夹杂物进行后续处理和控制。
这种形态调控可以减少夹杂物在钢铁中的聚集和生长,从而提高钢铁的品质。
三、减少夹杂物生成的方法1. 优化高炉工艺参数通过合理调整高炉冶炼工艺参数,如温度、炉渣成分、气氛控制等,可以有效减少夹杂物的生成。
例如,适当提高冷却速度和冷却时间,有助于夹杂物的凝固和分散。
钢中夹杂物的产生与去除途径
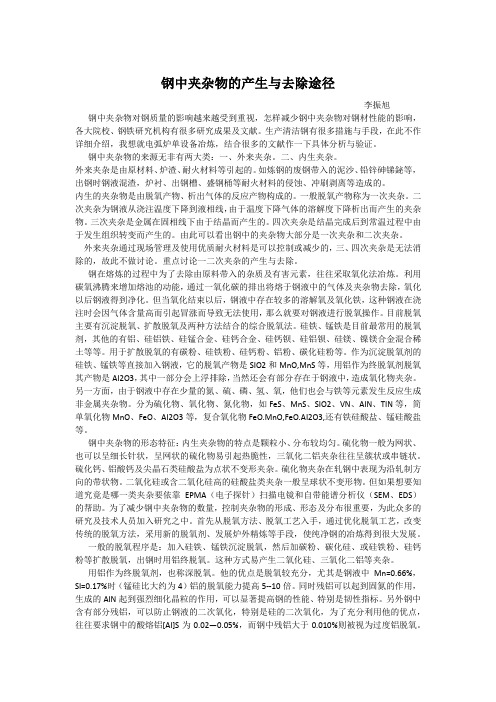
钢中夹杂物的产生与去除途径李振旭钢中夹杂物对钢质量的影响越来越受到重视,怎样减少钢中夹杂物对钢材性能的影响,各大院校、钢铁研究机构有很多研究成果及文献。
生产清洁钢有很多措施与手段,在此不作详细介绍,我想就电弧炉单设备冶炼,结合很多的文献作一下具体分析与验证。
钢中夹杂物的来源无非有两大类:一、外来夹杂。
二、内生夹杂。
外来夹杂是由原材料、炉渣、耐火材料等引起的。
如炼钢的废钢带入的泥沙、铅锌砷锑鉍等,出钢时钢液混渣,炉衬、出钢槽、盛钢桶等耐火材料的侵蚀、冲刷剥离等造成的。
内生的夹杂物是由脱氧产物、析出气体的反应产物构成的。
一般脱氧产物称为一次夹杂。
二次夹杂为钢液从浇注温度下降到液相线,由于温度下降气体的溶解度下降析出而产生的夹杂物。
三次夹杂是金属在固相线下由于结晶而产生的。
四次夹杂是结晶完成后到常温过程中由于发生组织转变而产生的。
由此可以看出钢中的夹杂物大部分是一次夹杂和二次夹杂。
外来夹杂通过现场管理及使用优质耐火材料是可以控制或减少的,三、四次夹杂是无法消除的,故此不做讨论。
重点讨论一二次夹杂的产生与去除。
钢在熔炼的过程中为了去除由原料带入的杂质及有害元素,往往采取氧化法冶炼。
利用碳氧沸腾来增加熔池的动能,通过一氧化碳的排出将熔于钢液中的气体及夹杂物去除,氧化以后钢液得到净化。
但当氧化结束以后,钢液中存在较多的溶解氧及氧化铁,这种钢液在浇注时会因气体含量高而引起冒涨而导致无法使用,那么就要对钢液进行脱氧操作。
目前脱氧主要有沉淀脱氧、扩散脱氧及两种方法结合的综合脱氧法。
硅铁、锰铁是目前最常用的脱氧剂,其他的有铝、硅铝铁、硅锰合金、硅钙合金、硅钙钡、硅铝钡、硅镁、镍镁合金混合稀土等等。
用于扩散脱氧的有碳粉、硅铁粉、硅钙粉、铝粉、碳化硅粉等。
作为沉淀脱氧剂的硅铁、锰铁等直接加入钢液,它的脱氧产物是SIO2和MnO,MnS等,用铝作为终脱氧剂脱氧其产物是AI2O3,其中一部分会上浮排除,当然还会有部分存在于钢液中,造成氧化物夹杂。
钢中氧化物夹杂的来源及控制

钢中氧化物夹杂的来源及控制江苏科技大学冶金与材料学院摘要简述了钢中氧化物夹杂的种类、来源和控制方法,加铝脱氧工艺析出的一次脱氧产物的去除方法是解决问题的主要方法。
对于对氧含量要求高的钢种,加入变性剂使氧化物夹杂改性是必要手段。
关键词氧化物夹杂深脱氧吹氩变性剂随着科学技术的进步,各行各业对钢材性能和质量的要求越来越高。
纯净钢的市场需求不断增加,关于纯净钢生产技术的研究也越来越深入[1]。
其研究主要包括两方面内容:一是提高钢的纯净度,二是严格控制钢中非金属夹杂物的数量和形态。
而非金属夹杂物中,氧化物夹杂是最主要的部分,其分类如图1所示[2]。
简单氧化物有FeO, Fe2O3 , MnO, SiO2 , Al2O3 , MgO和Cu2 O 等。
在铸钢中, 当用硅铁或铝进行脱氧时, SiO2和Al2 O3夹杂比较常见。
A l2O3在钢中常常以球形聚集呈颗粒状成串分布。
复杂氧化物, 包括尖晶石类夹杂物和各种钙的铝酸盐等,以及钙的铝酸盐。
硅酸盐夹杂也属于复杂氧化物夹杂,有2FeO · SiO2 ( 铁硅酸盐) 、2MnO · SiO2 ( 锰硅酸盐) 和CaO · SiO2 ( 钙硅酸盐) 等。
这类夹杂物在钢的凝固过程中, 由于冷却速度较快, 某些液态的硅酸盐来不及结晶, 其全部或部分以玻璃态的形式保存于钢中[2]。
明确氧化物夹杂的来源并探讨其控制方法对于二次精炼以及纯净钢冶炼来说十分重要。
图1 氧化物夹杂的分类1 氧化物夹杂的危害钢中O与Ai、Si、Cr、Mn、Fe等元素反应,可形成Al2O3 、SiO2、Cr2O3、MnO、Fe2O3、FeO氧化物和FeO·Cr2O3等复杂氧化物夹杂。
钢中氧化物和硅酸盐的存在,破坏了钢基体的连续性并导致了应力集中,从而降低了钢的塑性、韧性和抗疲劳性能。
一方面增强钢的力学性能的方向性使横向性能恶化;另一方面使钢的切削加工性能下降, 而且很难抛光。
钢中夹杂物控制原理
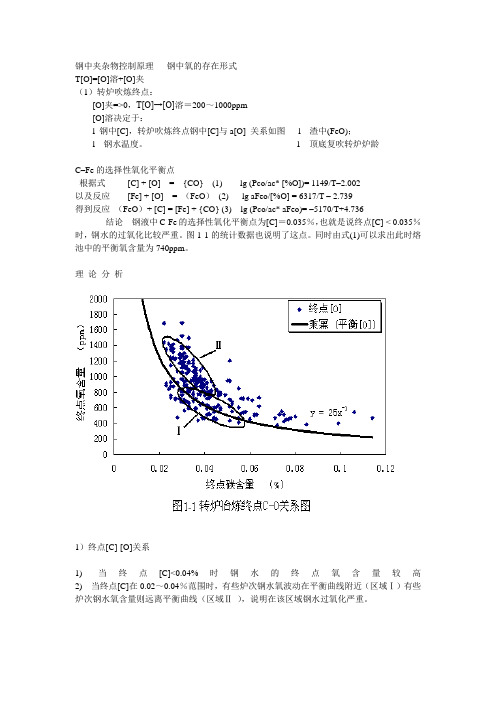
钢中夹杂物控制原理钢中氧的存在形式T[O]=[O]溶+[O]夹(1)转炉吹炼终点:[O]夹=>0,T[O]→[O]溶=200~1000ppm[O]溶决定于:l 钢中[C],转炉吹炼终点钢中[C]与a[O] 关系如图l 渣中(FeO);l 钢水温度。
1 顶底复吹转炉炉龄C–Fe的选择性氧化平衡点根据式[C] + [O] = {CO} (1) lg (Pco/ac* [%O])= 1149/T–2.002以及反应[Fe] + [O] = (FeO)(2) lg aFeo/[%O] = 6317/T – 2.739得到反应(FeO)+ [C] = [Fe] + {CO} (3) lg (Pco/ac* aFeo)= –5170/T+4.736 结论钢液中C-Fe的选择性氧化平衡点为[C]=0.035%,也就是说终点[C] < 0.035%时,钢水的过氧化比较严重。
图1-1的统计数据也说明了这点。
同时由式(1)可以求出此时熔池中的平衡氧含量为740ppm。
理论分析1)终点[C]-[O]关系1) 当终点[C]<0.04%时钢水的终点氧含量较高2) 当终点[C]在0.02~0.04%范围时,有些炉次钢水氧波动在平衡曲线附近(区域Ⅰ)有些炉次钢水氧含量则远离平衡曲线(区域Ⅱ),说明在该区域钢水过氧化严重。
2)温度对氧含量的影响在终点[C] = 0.025~0.04%时,终点氧含量虽然较分散,但总的趋势是随着终点温度的升高,终点氧基本呈上升趋势。
1620℃~1680℃之间,氧含量总体水平较低,平均为702ppm ,该范围的炉次共占总炉次的30%左右;出钢温度大于1680℃时,终点钢水氧含量有明显的升高趋势,平均为972ppm ,占总炉次的70%左右。
3)终渣氧化性对终点氧的影响20040060080010001200140016001800160016201640166016801700172017401760终点温度(℃)终点氧含量(p p m )终点[0]0200400600800100012001400160018001214161820222426炉渣中(FeO+MnO)的含量(%)终点氧含量(p p m )终点[0]1416182022242600.020.040.060.080.10.12终点碳含量(%)渣中(F e O +M n O )含量 %MnO+FeO渣中(FeO+MnO )增加,终点[O]有增加趋势;终点[C]<0.04%,渣中(FeO+MnO )增加且波动较大,说明此时吹氧脱碳是比较困难的,而铁则被大量氧化。
关于焊接过程中夹杂物的形成及防止措施分析

关于焊接过程中夹杂物的形成及防止措施分析摘要:夹杂物的存在对焊接质量会有很大影响,故文章在分析其形成机理的基础上,重点介绍了初生夹杂物、二次氧化夹杂物以及焊缝中夹杂物的防止措施,以供参考。
关键词:焊接夹杂物形成措施引言夹杂物是指金属内部或表面存在的和基本金属成分不同的物质,它主要来源于原材料本身的杂质及金属在熔炼、浇注和凝固过程中与非金属元素或化合物发生反应而形成的产物。
其来源途径大概有以下几种:①原材料本身含有的夹杂物,如金属炉料表面的粘砂、氧化锈蚀、随同炉料一起进入熔炉的泥砂、焦炭中的灰分等,熔化后变为溶渣;②金属熔炼时,脱氧、脱硫、孕育和变质等处理过程,产生大量的mno、sio2、al2o3 等夹杂物;③金属与炉衬、浇包的耐火材料及溶渣接触时,会发生相互作用,产生大量的mno、al2o3 等夹杂物;④在精炼后转包及浇注过程中,金属表面与空气接触形成的表面氧化膜,被卷入金属后形成氧化夹杂物;⑤在铸造和焊接过程中,金属与非金属元素发生化学反应而产生的各种夹杂物,如fes、mns 等硫化物。
夹杂物的存在对金属焊接具有很多危害,通常包括以下几个方面的内容:①夹杂物的存在破坏了金属本体的连续性,使金属的强度和塑性下降;②尖角形夹杂物易引起应力集中,显著降低金属的冲击韧性和疲劳强度;③易熔夹杂物(如钢铁中的 fes)分布于晶界,不仅降低强度且能引起热裂;④夹杂物也能促进气孔的形成,它既能吸附气体,又是气核形成的良好衬底。
因此,必须对其形成机理进行分析,采取有效的防止措施。
2、夹杂物的分类2.1 按夹杂物化学成分,可分为:氧化物---- feo、mno、sio2、al2o3;硫化物----fes、mns、cu2s;硅酸盐---- feo.sio2、fe2sio4、mn2sio4、feo.al2o3.sio2。
2.2 按夹杂物形成时间,可分为初生夹杂物、次生夹杂物和二次氧化夹杂物。
初生夹杂物:是在金属熔炼及炉前处理过程中产生的;次生夹杂物:是在金属凝固过程中产生的;二次氧化夹杂物:而在浇注过程中因氧化而产生的夹杂物称为二次氧化夹杂物。
- 1、下载文档前请自行甄别文档内容的完整性,平台不提供额外的编辑、内容补充、找答案等附加服务。
- 2、"仅部分预览"的文档,不可在线预览部分如存在完整性等问题,可反馈申请退款(可完整预览的文档不适用该条件!)。
- 3、如文档侵犯您的权益,请联系客服反馈,我们会尽快为您处理(人工客服工作时间:9:00-18:30)。
2. SiO2-Al2O3-CaO-MnO 系夹杂 物成分的热力学优化
2.3 SiO2-Al2O3-CaO-MnO 系夹杂物优化 2.3.1 Al2O3 含量对SiO2-Al2O3-CaO-MnO 系夹杂物熔点的 影响 Al2O3 的来源:炼钢过程的加入物,钢液被耐火材料 颗粒玷污。 钢液中溶解铝和溶解氧反应达到平衡时其平衡常数很 低,即便是钢水用无铝合金脱氧,或溶解的铝量很低,夹 杂物中也常常会含有一定量的Al2O3。 可以通过控制加入合金中铝含量和控制渣中Al2O3 含 量来控制钢液中酸溶铝含量的大小。
精炼渣组成对高碳帘线钢钢液平衡铝含量的影响
精炼渣组成对高碳帘线钢钢液钙活度的影响
2)高碳帘线钢在合金化时析出的平衡夹杂 物组成主要决定于钢液中的[Al]s 的含量
当[Al]s<3×10-6 时,平衡夹杂物组成落在锰 铝榴石(M3AS3)范围内。
������ 3)1823K 时当钙和铝同时参与脱氧时, 当[Al]s >22.3×10-6 时钢中只析出Al2O3, 当[Al]s<22.3×10-6, a[Ca]< 1×10−9时钢中 可析出CaO· Al2O3· 2SiO2。
CaO 含量不同时,低于1400℃区域占总相图的百分比
2. SiO2-Al2O3-CaO-MnO 系夹杂 物成分的热力学优化
2.3.3 CaO/Al2O3 对SiO2-Al2O3-CaO-MnO 系夹杂物熔点的影响 随着CaO/Al2O3 比的增加,低熔点区域 是先增加后减少。 CaO/Al2O3 为0.94 时,低熔点区域面 积所占百分比最大,占50%左右。 控制 SiO2-Al2O3-CaO-MnO 系中 CaO/Al2O3 比为1 左右有利于降低夹杂物 的熔点。
CaO-SiO2-MnO 相图
不同Al2O3 含量对应的低熔点区域对比
2. SiO2-Al2O3-CaO-MnO 系夹杂 物成分的热力学优化
CaO-SiO2-Al2O3-MnO 四元系夹杂物比 不含Al2O3 的CaO-SiO2-MnO 三元系夹杂 物的低熔点区域大。 Al2O3 含量在从0 变化到20%的过程中, 低熔点区域迅速增加,在20%变化到30% 过程中,低熔点区域有所减少,但变化不 大。
1.5 夹杂物成分控制策略
• 生产中控制夹杂物的组成主要可以归纳为两种方 式:脱氧工艺和炉渣组成。
• 部分钢种还需结合S-Me反应热力学提出 钢中硫含量控制策略
1.5 夹杂物成分控制策略
• 问题: 1)夹杂物是多元的; 2)夹杂物有时熔点较高,是固态的, 反应未达到平衡; 3)炼钢、精炼工艺对夹杂物组成影响 较大; 4)热力学相图局部区域组元活度测量 有较大误差
CaO 含量在从0变化到40%的过程中, 低熔点区域是先增加后减少,当CaO 含量 在25%~30%时,低熔点区域最大,控制 SiO2-Al2O3-CaO-MnO 系中CaO 含量在 25%~30%有利于降低夹杂物熔点。 在整个变化过程中,CaO/SiO2 比也相 应的越来越大。
2. SiO2-Al2O3-CaO-MnO 系夹杂 物成分的热力学优化
夹杂物塑性控制研究进展
1. 概述
• 夹杂物成分和形态控制技术是现代洁净钢冶炼的 主要内容之一
不同用途的钢材对非金属夹杂物的形态、数量、组成 有不同的要求。
• 钢中夹杂物在冶炼过程中不可能得到完全去除
但可以通过各种方法来降低其危害,如减小夹杂物尺 寸、改变夹杂物成分。
• 根据钢种的要求及夹杂物的性质提出夹杂物成分 和形态控制要求。
SiO2-Al2O3-CaO 系相图 图中阴影部分为熔点低于1400℃的区域, 低熔点区域的大致范围为:SiO2 36%~70%; Al2O3 10%~25%;CaO10%~50%。
Al2O3 含量、CaO/SiO2 和Al2O3-CaO-SiO2 系夹杂物熔点的关系 CaO/SiO2 比为2 时夹杂物熔点较高,Al2O3 可控区域较小,当 Al2O3/(SiO2+CaO)为30%时,夹杂物的熔点最低,为1540℃左右, 夹杂物的熔点仍然很高,此时夹杂物的塑性很差。 CaO/SiO2 比为0.8、1 时,夹杂物熔点较低,Al2O3 可控区域 较大。 控制夹杂物CaO/SiO2 比在0.8~1 范围将有利于降低夹杂物熔点。
2. SiO2-Al2O3-CaO-MnO 系夹杂 物成分的热力学优化
2.1 SiO2-Al2O3-MnO 系夹杂物优化 帘线钢为硅锰镇静钢,因此初始夹杂物 多含有SiO2 和MnO。 Al2O3 主要来源于脱氧剂、合金、炉渣 以及耐火材料中的铝与钢液中的氧反应, 因此形成SiO2-Al2O3-MnO 夹杂物。
2. SiO2-Al2O3-CaO-MnO 系夹杂 物成分的热力学优化
帘线钢中夹杂物在整个冶炼过程中有很明显的 变化。 在实际生产过程中,钢中的夹杂物除了少量的 MnS 外,绝大部分是SiO2-MnO-Al2O3 和SiO2CaO-Al2O3 系。 前一种系主要在钢水脱氧初期发现,后者主要 在冶炼中期和末期以及铸坯中发现。 生产中比上述要复杂,常以CaO-SiO2Al2O3-MnO、CaO-SiO2-Al2O3-MgO 类四元及 四元以上夹杂物存在。
1.3 夹杂物分类
• 根据变形性能夹杂物分类:
形; 1) Al2O3 和Ca-aluminates :在炼钢温度以下的温度内都不变
2) 尖晶石(AO-B2O3):在室温下不变形,在更高的温度 1200℃以上)下可以变形; 3) 二氧化硅:在室温下不变形,在更高的温度下变形,它是由 二氧化硅的组成决定的; 4) FeO, MnO, (Fe, Mn)O:在室温下为塑性,但从400℃开始 随着温度的升高逐渐失去塑性; 5) MnS::直到1000℃MnS 都是塑性的,当高于1000℃后塑 性下降; 6) 纯硅石:直到1300℃都不变形。
1823K 时钙铝含量对高碳帘线钢脱氧产物组成的影响
4)控制熔渣的组成,由钢-渣反应控制钢液 中钙、铝的含量,从而控制夹杂物的组成。
1823K 时熔渣组成对高碳帘线钢钢液残铝和钙含量的控制
5)喂Si-Ca 线对控制夹杂物的成分不利 钙还原渣和包衬中的Al2O3 使得钢液中的酸 溶铝含量增加。 从控制高碳合金钢中夹杂物成分的角度考虑, 建议不采用喂Si-Ca丝。
CaO-Al2O3-SiO2 三元系夹杂物
钙斜长石(CaO· Al2O3· 2SiO2)及其与 假硅灰石(CaO· SiO2)相邻的周边低熔点区域具 有良好的变形能力。
1.2 MnO-Al2O3-SiO2 和CaO-Al2O3-SiO2 三 元系塑性区
一般氧化物夹杂的目标成分范围应该是 那些具有低熔点的非结晶相组成。
1.1 夹杂物变形能力与熔点关系
• 夹杂物变形能力和其熔点有很大关系
在轧制温度下随着夹杂物熔点降低,变形 性能越来越好。
当夹杂物的熔点低于1500℃时,其变形能力 就比同温度下的钢的变形能力好了。
夹杂物熔点和变性率之间的关系
夹杂物熔点和硬度之间的关系
1.2 MnO-Al2O3-SiO2 和CaO-Al2O3-SiO2 三 元系塑性区
G. Bernard 等根据外推法测定的夹杂物相与钢基体在 900℃~1100℃时相对粘性的大小,将三元系划分为四个 区域: 区域①为不变形的均相夹杂物; 区域④为两相区,其中有一相不能变形。 区域②具有很强的结晶能力,因而也不能变形; 区域③为可变形的夹杂物区域。
900~1100℃MnO-Al2O3-SiO2系氧化物夹杂的变形性
900~1100℃ CaO-Al2O3-SiO2 系氧化物夹杂的变形性
1.2 MnO-Al2O3-SiO2 和CaO-Al2O3-SiO2 三 元系塑性区
MnO-Al2O3-SiO2 三元系夹杂物
具有良好变形能力的夹杂物组成分布在 锰铝榴石(3MnO· Al2O3· 3SiO2)及其周围的低 熔点区 在该区域内Al2O3/(Al2O3+SiO2+MnO) 变化在15%~30%。
1.5 夹杂物成分控制策略
通过一系列化学反应方程式以及不同温度下 CaO-SiO2-Al2O3、MnO-SiO2-Al2O3 系等活度 曲线计算: 钢液合金ቤተ መጻሕፍቲ ባይዱ、冷却时析出夹杂物的控制; 精炼渣控制钢液成分; VD 和喂丝等工艺过程中钢液成分的控制。
1.5 夹杂物成分控制策略
2[Si] + [O] = SiO2(S) ΔG0 = −581900 + 221.8T J / mol 2[Al]+3[O]=Al2O3(S) ΔG0 = −1202000 + 386.3T J / mol
2. SiO2-Al2O3-CaO-MnO 系夹杂 物成分的热力学优化
CaO/Al2O3 比不同时,低于1400℃区域占总相图的百分比
2. SiO2-Al2O3-CaO-MnO 系夹杂 物成分的热力学优化
2.3.4 CaO/SiO2 比对SiO2-Al2O3-CaO-MnO 系夹杂物熔点的影响
2. SiO2-Al2O3-CaO-MnO 系夹杂 物成分的热力学优化
酸溶铝随着钙活度的增加而增加
1.5 夹杂物成分控制策略
6)合金脱氧时要控制好合金中的铝含量 合金中的铝是导致钢液增铝的一个重要 原因。
1.5 夹杂物成分控制策略
7)夹杂物组成与炉渣化学成分关系密切
当钢渣间达到热力学平衡时,夹杂物的成分与钢渣的 成分相同。 在冶金生产过程中,绝对的钢液与夹杂物之间的平衡 是少见的,但可达到局部的钢与夹杂物、渣与钢、炉衬与 钢渣、炉衬与钢液的准平衡状态。 夹杂物的成分在很大程度上受顶渣和炉衬的影响。通 过控制顶渣成分、炉衬材料和一定的脱氧条件,夹杂物成 分的准确控制是可以实现的。
2. SiO2-Al2O3-CaO-MnO 系夹杂 物成分的热力学优化
Al2O3 含量不同时,低于1400℃区域占总面积的百分比