提高伺服系统定位精度的方法
伺服电机编码器调零对位方法

伺服电机编码器调零对位方法伺服电机编码器调零对位是一项重要的操作,它确保了伺服系统运行的准确性和稳定性。
在对伺服电机编码器进行调零对位时,首先需要明确编码器的作用和原理。
编码器是用来测量旋转角度和位置的装置,通过编码器可以准确地监测电机的位置,实现精准控制。
一、调零对位的原理伺服电机编码器的调零对位是通过将电机控制系统中的位置反馈信号归零来实现的。
在电机停止运动的时候,通过调整编码器信号,使得当前位置被定义为零点位置,从而实现对位。
这样可以确保电机在后续的运动过程中,能够准确地控制位置和角度。
二、调零对位的步骤1.停止电机运动:在进行编码器调零对位之前,必须先停止电机的运动,确保安全性和操作的准确性。
2.进入编码器调零模式:根据具体的伺服系统和编码器类型,进入编码器调零的设置界面或模式。
3.调整位置:根据系统的要求,调整编码器信号,使当前位置被定义为零点位置。
4.确认对位:确认调零后的位置是否准确,可以通过系统的显示界面或其他功能进行验证。
5.保存设置:对于一些系统来说,调零对位是一次性的操作,需要保存设置以确保后续操作的准确性。
三、注意事项1.在进行编码器调零对位时,需要谨慎操作,以避免对系统造成不必要的损坏。
2.在调零对位的过程中,要确保环境安全,避免因误操作导致事故发生。
3.对于初次进行编码器调零对位的操作者,建议在有经验的人员的指导下进行操作。
4.在进行编码器调零对位之前,需要确保系统处于正常工作状态,避免出现意外情况。
四、总结伺服电机编码器调零对位是伺服系统中重要的操作之一,它确保了电机位置控制的准确性和稳定性。
通过本文介绍的调零对位原理、步骤和注意事项,希望可以帮助操作者正确地进行编码器调零对位操作,保证系统的正常运行和工作效率。
数控机床工作台的定位精度检测与调整方法

数控机床工作台的定位精度检测与调整方法随着科技的进步和工业的发展,数控机床在制造业中扮演着重要的角色。
而数控机床的定位精度对于加工产品的质量起着至关重要的作用。
本文将介绍数控机床工作台的定位精度检测与调整方法,旨在帮助读者更好地理解和应用相关技术。
首先,我们需要了解数控机床工作台的定位精度定义。
定位精度是指数控机床工作台在特定工作条件下,其运动轴与工作轴的相对位置的准确性。
定位精度关系着加工零件的尺寸和形状精度,直接影响着产品的质量。
数控机床工作台的定位精度检测需要借助于专业的测量设备和工具。
其中常用的测量设备包括激光干涉仪、高精度角度测量仪、坐标测量机等。
通过这些设备,可以对数控机床工作台的各个轴进行精确的测量。
在进行定位精度检测之前,需要进行工作台的预热,确保温度稳定。
同时,注意检测设备的放置位置,以避免外界因素对测量结果的干扰。
接下来,根据具体的检测要求和机床结构,采用合适的测量方法和测量点,对数控机床工作台的各个轴进行测量。
针对机床工作台不同的轴,可采取不同的检测方法。
例如,对于直线轴,可使用激光干涉仪进行测量;对于旋转轴,可以使用高精度角度测量仪进行测量。
通过这些测量设备,可以精确测量出数控机床工作台在坐标轴上的定位精度。
定位精度检测完成后,如发现定位精度不符合要求,需要进行调整。
调整的目的是通过调整机床的各个部分,使得机床的定位精度达到规定的标准。
调整方法具体根据机床的结构和不同轴的特点而定,下面将介绍一些常见的调整方法。
首先,针对直线轴的调整,可以通过调整导轨和滑块的间隙来实现。
通过适当调整导轨和滑块的间隙,可以有效消除摆动和间隙,提高直线轴的定位精度。
其次,对于旋转轴的调整,可以通过调整机床的传动部分来实现。
例如,在滚珠螺杆传动的机床中,可以通过调整滚珠螺杆的预紧力和轴承的安装间隙来改善旋转轴的定位精度。
此外,还可以通过调整伺服系统的参数来实现定位精度的调整。
伺服系统是数控机床的核心部分,负责控制机床的运动。
数控车床位置精度如何提高

数控车床位置精度如何提高在伺服系统设计过程中应注意惯量匹配及力矩匹配,加添机械刚性和降低系统的惯性,削减机械传动部位的响应时间。
负载惯量JL由拖板及上面安装的刀架,滚珠丝杠,联轴器等直线和旋转运动件的惯量折合到伺服电机轴上的惯量构成,JL随切削负载更改而变化。
JM为伺服电机转子惯量。
要依据伺服电机的特性,掌控JM与JL的比值。
在滚珠丝杠装配过程中应注意以下几点:丝杠两端轴承座固定后,确保丝杠上母线及侧母线分别与数控车床导轨主平面和次平面平行;确保丝杠螺母座轴线与丝杠轴线重合(修磨调整垫片);确保丝杠螺母座安装端面与丝杠轴线垂直。
丝杠是修长杆件,平行度偏差导致丝杠挠曲,直接影响定位精度。
丝杠螺母与丝杠螺母座安装端面不垂直会导致螺母受力不均,丝杠摩擦发热严重,引起丝杠热变形,将影响重复定位精度。
为保证丝杠有良好的刚性和动态特性,丝杠装配时必需做预拉伸,以补偿因温升所产生的热变形。
同时要掌控丝杠两端的锁紧螺母的锁紧力矩和滚珠丝杠与伺服电机的联接刚度,否则会对机床的传动精度有影响。
应提高数控车床导轨的防护罩的性能和质量,钢制防护罩壳自身较重,其中心1层或几层护板是跟随拖板一起移动的,防护罩壳需要轻松,平稳的运行,不能有干涉现象,否则也会影响机床的定位精度。
数控车床的床身底座,主轴箱,十字拖板等大结构件,在生产过程因铸造,热处理,机械加工产生的内应力残留在零件中,带有内应力的零件总是处于一种不稳定的状态。
为除去内应力引起零件的结构变形和几何精度变化,应选用合适的时效方法来除去内应力,如自然时效,热处理时效或者振动时效;其次,合理布置加工工艺,包括粗,精加工的次序和加工余量的调配,时效的次数和时间,在精加工之前尽可能除去零件内部的残余应力。
在数控车床装配过程中,刀架与上拖板,主轴箱和底座的固定结合面,滚珠丝杠的螺母座和轴承座与其固定结合面肯定要进行刮研并作着色检验,确保部件结合面的接触刚度,这也是提高机床精度保持性的措施之一、数控车床切削过程发热量大,为掌控并减小机床的热变形,要进行冷却处理,并且要能够自动适时地排屑;对于发热大的部位,应加大其散热面积,改善散热或实行隔热处理。
伺服电机如何实现高精度定位和高动态响应

伺服电机如何实现高精度定位和高动态响应在现代工业自动化领域,伺服电机凭借其出色的性能,成为实现高精度定位和高动态响应的关键设备。
要理解伺服电机如何达成这两个重要目标,我们需要深入探讨其工作原理、关键技术以及相关的控制系统。
首先,让我们来了解一下伺服电机的基本工作原理。
伺服电机本质上是一种能够精确控制旋转角度和速度的电机。
它通常由电机本体、编码器、驱动器和控制器等部分组成。
电机本体负责产生旋转动力,而编码器则实时反馈电机的位置和速度信息。
驱动器根据控制器给出的指令和编码器反馈的信息,精确调整电机的电流和电压,从而实现对电机的精确控制。
那么,伺服电机是如何实现高精度定位的呢?这主要依赖于其精密的反馈机制。
编码器是实现高精度定位的核心部件之一。
常见的编码器有光电编码器和磁性编码器等。
这些编码器能够以极高的分辨率检测电机的旋转位置,并将这些信息反馈给控制器。
控制器通过对比目标位置和实际位置,计算出误差,并通过调整驱动器的输出,使电机逐渐趋近目标位置,直至误差在允许范围内。
除了编码器,电机的机械结构和制造工艺也对高精度定位起着重要作用。
高精度的滚珠丝杠、直线导轨等传动部件能够减少运动中的间隙和摩擦,从而提高定位精度。
同时,电机的制造工艺也需要保证电机的定子和转子之间的气隙均匀,以确保电机的输出扭矩稳定且均匀。
在实现高动态响应方面,伺服电机的快速响应能力至关重要。
这主要取决于电机的电气特性和驱动器的性能。
电机的电气时间常数越小,其响应速度就越快。
此外,驱动器的电流环带宽越高,其对电流的控制就越迅速,从而能够使电机更快地响应负载的变化。
为了进一步提高动态响应性能,先进的控制算法也被广泛应用。
例如,前馈控制可以根据预期的负载变化提前调整电机的输出,从而减少响应时间。
而模型预测控制则可以通过预测系统未来的状态,优化控制策略,提高系统的动态性能。
另外,伺服系统的参数整定也是实现高精度定位和高动态响应的关键环节。
合理调整控制器的增益参数,如比例增益、积分增益和微分增益等,可以在稳定性和响应速度之间取得平衡。
消除振荡和提高位置精度的方法

4)加入观测器功能 如果加入转矩指令滤波器不起作用, 可能是震荡频率在数百赫兹以上,这是可加入观测器功能。 此功能实际上是对速度指令中的高频成分进行分离,并加 以拟制。设定参数如下: 参数P2003#2(OBEN),此位参数设为1,观测 器功能有效; 参数P2047,设定观测器检测系数POA1,设定值按 标准设定(初始化设定); 参数P2050,设定观测器检测系数POK1,设定值按 标准设定(初始化设定); 参数P2051,定观测器检测系数POK2,设定值按标 准设定(初始化设定); 以上是最基本的拟制方法,可在不同的机床上试验 应用,但因为机床的结构和配置差别较大,震荡产生的原 因也不尽相同,所以不可以一概而论。
对于半闭环可能产生的高频震荡,则有以下几种对策; 1)使用250us加速反馈功能 此功能是对速度环反馈的一种补偿 功能,由于机床的传动环节导致弹性变形,或是负载的惯量折合到 电机轴上后与电动机的转子惯量相比较大时,就会产生50-150赫 兹的震荡。使用此功能补偿加速时的反馈,使响应加快,消除震荡。 该参数为P2066,一般设定在-10~-20之间,如在加减速时有震 荡,可适当减少此参数值。需要注意,此值太大,可能引起不正常 震荡。 2)适当降低负载惯量比(见低频震荡时的措施) 3)加入转矩指令滤波器功能 该功能是一低通滤波环节,对于100 赫兹以上的转矩指令有拟制作用,因此可以消除高频震荡。参数为 P2067,这是一个与截止频率有关的量值,范围为1166(200赫 兹)~2327(90赫兹)。例如当确定100赫兹为振荡截止频率时, 其相应的设定值为2185。
加入静摩擦补偿功能 当机床由停止状态转为激活运动时,由于静摩擦,机械运动必然滞 后。设置参数包括:参数P2005#7,设定为1,静摩擦补偿功能有 效。参数P2072(静摩擦补偿量),通常设置为100,当克服静摩 擦运行启动后,此补偿要取消。故还需设置如下参数:1)参数 P2009#7,设置为1,可以取消静摩擦补偿功能;2)参数P2073 (静摩擦补偿取消时间),设定值为8 ms的倍数;3)参数P2097 (静摩擦补偿停止参数),通常设置为55。 加入前馈功能 前馈功能是对伺服系统运算滞后的一种补偿功能。设置参数包括: 参数P2005#1设置为1,使前馈功能有效;参数P2068(前馈系 数),典型设置值为70;参数P2067(速度前馈系数),典型设 置值为50。设置好以上参数,断电并重新上电,如有超调,可以适 当降低前馈系数;如无超调,可逆向调整之。
伺服系统中如何实现高精度定位
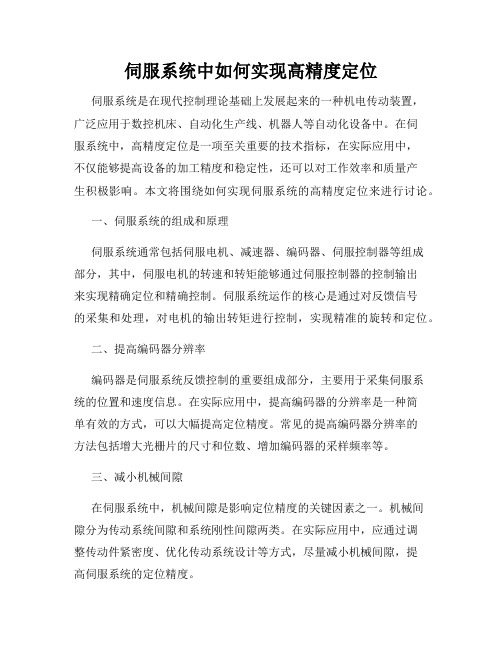
伺服系统中如何实现高精度定位伺服系统是在现代控制理论基础上发展起来的一种机电传动装置,广泛应用于数控机床、自动化生产线、机器人等自动化设备中。
在伺服系统中,高精度定位是一项至关重要的技术指标,在实际应用中,不仅能够提高设备的加工精度和稳定性,还可以对工作效率和质量产生积极影响。
本文将围绕如何实现伺服系统的高精度定位来进行讨论。
一、伺服系统的组成和原理伺服系统通常包括伺服电机、减速器、编码器、伺服控制器等组成部分,其中,伺服电机的转速和转矩能够通过伺服控制器的控制输出来实现精确定位和精确控制。
伺服系统运作的核心是通过对反馈信号的采集和处理,对电机的输出转矩进行控制,实现精准的旋转和定位。
二、提高编码器分辨率编码器是伺服系统反馈控制的重要组成部分,主要用于采集伺服系统的位置和速度信息。
在实际应用中,提高编码器的分辨率是一种简单有效的方式,可以大幅提高定位精度。
常见的提高编码器分辨率的方法包括增大光栅片的尺寸和位数、增加编码器的采样频率等。
三、减小机械间隙在伺服系统中,机械间隙是影响定位精度的关键因素之一。
机械间隙分为传动系统间隙和系统刚性间隙两类。
在实际应用中,应通过调整传动件紧密度、优化传动系统设计等方式,尽量减小机械间隙,提高伺服系统的定位精度。
四、提高伺服控制器的响应速度伺服控制器的响应速度直接影响伺服系统的跟踪精度。
在实际应用中,可以通过增加控制器的带宽,提高信号采样频率等方式,提高控制器的响应速度和稳定性。
五、改进PID控制算法伺服系统的控制算法是影响定位精度的关键因素之一。
传统的基于PID控制算法的控制方法存在响应速度慢、超调量大等问题。
在实际应用中,可以通过改进PID控制算法。
如采用自整定PID控制算法、先进的模糊控制算法等,可以实现更为准确和稳定的控制。
六、结语在伺服系统中,高精度定位是实现精准控制和定位的重要技术指标。
通过改进编码器精度、减小机械间隙、提高控制器响应速度、改进控制算法等措施,可以不断提高伺服系统的定位精度和稳定性,在实际应用中发挥更好的作用。
伺服系统定位误差形成原因与克服办法

伺服系统定位误差形成原因与克服办法1.机械结构方面的原因机械结构方面的原因是导致伺服系统定位误差的一个主要因素。
机械件的加工精度、刚性以及装配质量都会对定位误差产生影响。
例如,机床滚珠丝杠的传动精度不高、松动现象严重,会导致定位误差增大。
为了克服这一问题,可以采取以下方法:-提高机械制造工艺,增加机械加工的精度和装配的精度,以减小机械结构方面的误差;-选择高精度的机械件,例如精密滚珠丝杠、高精度的导轨等,可以提高定位的精度;-采用刚性好的机械结构,减小机械变形,从而减小定位误差。
2.传感器方面的原因传感器方面的原因也是导致伺服系统定位误差的一个重要因素。
传感器的精度、分辨率以及非线性特性都会影响定位的准确性。
为了克服这一问题,可以采取以下方法:-选择高精度、高分辨率的传感器,例如光电编码器、磁性编码器等,以提高测量的精度;-对传感器进行校准和补偿,消除传感器的非线性特性,实现更准确的测量;-采用多传感器测量的方法,提高定位系统的容错能力和鲁棒性。
3.控制系统方面的原因控制系统方面的原因也会导致伺服系统定位误差的增大。
控制系统的采样周期、控制算法以及采样信号的噪声都会对定位系统的性能产生影响。
为了克服这一问题,可以采取以下方法:-缩短控制系统的采样周期,提高对系统状态的采样频率,以实时调整控制量,减小定位误差;-采用更高级的控制算法,例如模糊控制、自适应控制等,提高系统的鲁棒性和适应性;-提高采样信号的质量,例如增加滤波器、降低噪声等,提高采样信号的可靠性,减小错误干扰。
4.环境因素的原因环境因素也会对伺服系统的定位误差产生影响。
例如,温度变化会导致机械结构的膨胀和传感器的漂移,进而影响定位的准确性。
为了克服这一问题,可以采取以下方法:-在机械结构设计中考虑温度膨胀的影响,采用温度补偿措施,减小温度变化对定位系统的影响;-选用温度稳定性好的材料,降低机械结构的热膨胀系数,减小温度变化对定位精度的影响;-对传感器进行温度补偿,校正传感器的漂移,提高测量的准确性。
如何提高数控机床各轴的定位精度和重复定位精度

如何提高数控机床各轴的定位精度和重复定位精度如何提高数控机床各轴的定位精度和重复定位精度对机床工作状态进行监控和对机床精度进行经常的测试是非常必要的,以便及时发现和解决问题,提高零件加工精度,那么如何提高机床各轴的定位精度和重复定位精度呢?同一台机床,由于采用的标准不同,所得到的位置精度也不相同, 因此在选择数控机床的精度指标时,也要注意它所采用的标准。
数控机床的位置标准通常指各数控轴的反向偏差和定位精度。
对于这二者的测定和补偿是提高加工精度的必要途径。
反向偏差在数控机床上,由于各坐标轴进给传动链上驱动部件(如伺服电动机、伺服液压马达和步进电动机等)的反向死区、各机械运动传动副的反向间隙等误差的存在,造成各坐标轴在由正向运动转为反向运动时形成反向偏差,通常也称反向间隙或失动量。
对于采用半闭环伺服系统的数控机床,反向偏差的存在就会影响到机床的定位精度和重复定位精度,从而影响产品的加工精度。
在G01切削运动时,反向偏差会影响插补运动的精度,若偏差过大就会造成“圆不够圆,方不够方”的情形;而在G00快速定位运动中,反向偏差影响机床的定位精度,使得钻孔、镇孔等孔加工时各孔间的位置精度降低。
同时,随着设备投入运行时间的增长,反向偏差还会随因磨损造成运动副间隙的逐渐增大而增加,因此需要定期对机床各坐标轴的反向偏差进行测定和补偿。
【反向偏差的测定】反向偏差的测定方法:在所测量坐标轴的行程内,预先向正向或反向移动一个距离并以此停止位置为基准,再在同一方向给予一定移动指令值,使之移动一段距离,然后再往相反方向移动相同的距离,测量停止位置与基准位置之差。
在靠近行程的中点及两端的三个位置分别进行多次测定(一般为七次),求出各个位置上的平均值, 以所得平均值中的最大值为反向偏差测量值。
在测量时一定要先移动一段距离,否则不能得到正确的反向偏差值。
测量直线运动轴的反向偏差时,测量工具通常采有千分表或百分表,若条件允许,可使用双频激光干涉仪进行测量。
如何采用PLC控制伺服电机的精确定位

如何采用PLC控制伺服电机的精确定位1 PLC定义PLC主要是指数字运算操作电子系统的可编程逻辑控制器,用于控制机械的生产过程。
PLC的特点是性能稳定可靠,一般由大公司如三菱,LG、台达、西门子等生产制造,质量可靠,使用寿命长,其次PLC的扩展性好,一般可通过简单方法实现多种专业的功能,如AD/DA功能,波形输出功能,PID模糊控制功能等。
PLC可采用代码编程或者梯形图编程,逻辑清楚,编程简单,适合于初学者学习和使用,因此用途广泛。
目前PLC已经在世界各地的重要控制系统中发挥了重要的作用。
大到航天航海,小到普通家用电器,都有它的身影,特别是制造工厂,更是得到了大量的使用。
2 伺服电机定义伺服电机主要靠脉冲来定位,基本上可以这样理解,伺服电机接收到1个脉冲,就会旋转1个脉冲对应的角度,从而实现位移,因为,伺服电机本身具备发出脉冲的功能,所以伺服电机每旋转一个角度,都会发出对应数量的脉冲,这样,和伺服电机接受的脉冲形成了呼应,或者叫闭环,如此一来,系统就会知道发了多少脉冲给伺服电机,同时又收了多少脉冲回来,这样,就能够很精确的控制电机的转动,从而实现精确的定位,可以达到0.001mm。
伺服电机在要求精密控制的工业自动化设备中得到了广泛的应用,他的闭环控制功能,是步进电机无法比拟的。
在一些场合,由于步进电机没有反馈,因此当步进电机卡死或打滑会出现丢步的情况,从而大大影响设备使用精度,因此步进电机一般用于纯粹的转动过程,或者用于对精度要求不高的使用场合。
3 如何采用PLC控制伺服电机运转文中采用了LG品牌PLC,伺服电机采用英迈克的伺服电机及驱动器。
3.1 PLC控制伺服电机原理图PLC控制伺服电机原理如图1所示。
①PLC引脚说明。
PLC引脚P00为电机运行启动信号;PLC引脚P40属于LG PLC的专用高速脉冲通道,用于控制伺服电机驱动器。
P41属于LG PLC专用方向脉冲通道;P属于高速脉冲通道的专用高电平端,当高速脉冲通道为低电平时,电流从P流向高速脉冲通道,从而伺服电机收到高速脉冲,并执行相关控制,如转动和换向。
伺服控制定位精度计算

伺服控制定位精度计算建筑物防直击雷的防雷装置包括一、伺服系统定位误差形成原因与克服办法通常情况下,伺服系统控制过程为:升速、恒速、减速和低速趋近定位点,整个过程都是位置闭环控制。
减速和低速趋近定位点这两个过程,对伺服系统的定位精度有很重要的影响。
减速控制具体实现方法很多,常用的有指数规律加减速算法、直线规律加减速算法。
指数规律加减速算法有较强的跟踪能力,但当速度较大时平稳性较差,一般适用在跟踪响应要求较高的切削加工中。
直线规律加减速算法平稳性较好,适用在速度变化范围较大的快速定位方式中。
选择减速规律时,不仅要考虑平稳性,更重要的是考虑到停止时的定位精度。
从理论上讲,只要减速点选得正确,指数规律和线性规律的减速都可以精确定位,但难点是减速点的确定。
通常减速点的确定方法有:(1)如果在起动和停止时采用相同的加减速规律,则可以根据升速过程的有关参数和对称性来确定减速点。
(2)根据进给速度、减速时间和减速的加速度等有关参数来计算减速点,在当今高速CPU十分普及的条件下,这对于CNC的伺服系统来说很容易实现,且比方法(1)灵活。
伺服控制时,由软件在每个采样周期判断:若剩余总进给量大于减速点所对应的剩余进给量,则该瞬时进给速度不变(等于给定值),否则,按一定规律减速。
理论上讲,剩余总进给量正好等于减速点所对应的剩余进给量时减速,并按预期的减速规律减速运行到定位点停止。
但实际上,伺服系统正常运转时每个采样周期反馈的脉冲数是几个、十几个、几十个甚至更多,因而实际减速点并不与理论减速点重合。
如图1所示,其最大误差等于减速前一个采样周期的脉冲数。
若实际减速点提前,则按预期规律减速的速度降到很低时还未到达定位点,可能需要很长时间才能到达定位点。
若实际减速点滞后于理论减速点,则到达定位点时速度还较高,影响定位精度和平稳性。
为此,我们提出了分段线性减速方法。
图1减速点误差示意图在低速趋近定位点的过程中,设速度为V0(mm/s),伺服系统的脉冲当量为delta;(mu;m),采样周期为tau;(ms),则每个采样周期应反馈的脉冲数为:N0=V0tau;/delta;。
一种永磁同步电机伺服系统高精度定位的方法[发明专利]
![一种永磁同步电机伺服系统高精度定位的方法[发明专利]](https://img.taocdn.com/s3/m/d2a54aa4767f5acfa0c7cd9b.png)
专利名称:一种永磁同步电机伺服系统高精度定位的方法专利类型:发明专利
发明人:黄强,李丹凤,蒋志宏,李辉
申请号:CN201110261248.X
申请日:20110906
公开号:CN102946222A
公开日:
20130227
专利内容由知识产权出版社提供
摘要:本发明公开了一种永磁同步电机伺服系统高精度定位的方法,使用位置环、速度环和电流环三闭环系统控制电流运转,其中所述位置环的控制器采用速度分段控制法,即根据不同的关节位置误差给出不同的位置环输出值,即速度给定值;当关节实际位置与期望位置越近,即位置误差越小时,速度给定值越小,使电机转动的越慢,直到位置误差达到定位精度要求;此时,本发明公开了软锁紧和硬锁紧两种锁紧方式,分别为速度为零锁紧法和使用制动器锁紧。
本发明为了实现以上技术方案,实现电机的高精度定位,使用光电编码器运用M/T法进行转速高精度测量,即在对反映转速ω的光电编码器输出脉冲个数m计数的同时,对反映测速时间的时基脉冲个数m也进行计数,并提出了DSP的具体实现过程。
申请人:北京理工大学
地址:100081 北京市海淀区中关村南大街5号北京理工大学机电学院智能机器人研究所
国籍:CN
更多信息请下载全文后查看。
数控机床伺服参数调整方法

数控机床伺服参数调整方法1. 引言1.1 引言数、岗次等。
数控机床是一种自动化加工设备,其控制系统由伺服系统负责实现精确的位置控制和运动控制。
伺服系统中的参数设置对机床的性能和加工质量有着直接的影响。
正确调整数控机床伺服参数是保证机床正常工作和提高加工精度的重要步骤。
在实际生产中,有时会出现数控机床运行不稳定或加工质量不理想的情况,这时就需要进行伺服参数的调整。
本文将介绍数控机床伺服参数的调整方法,包括调整方法一、调整方法二、调整方法三和调整方法四。
通过本文的学习,读者将能够全面了解数控机床伺服参数的调整原理和方法,从而更好地应对各种生产实际需求,提高加工效率和质量。
2. 正文2.1 数控机床伺服参数调整方法数控机床伺服参数调整方法主要包括四种不同的调整方法,每种方法都有其独特的特点和适用场景。
下面将分别介绍这四种调整方法。
调整方法一:手动调整手动调整是最基础也是最直观的调整方法,操作人员可以通过手动旋钮或按钮来改变伺服参数,实现对机床的控制。
这种方法适用于简单的调整需求,操作简单直观,但需要操作人员对机床进行实时监控,无法实现自动化控制。
调整方法二:自动调整自动调整是通过数控系统自动优化伺服参数,根据预设的算法和规则对参数进行调整。
这种方法可以提高生产效率,减少人工干预,适用于需要大量重复调整的场景。
但需要提前设定好优化算法,以及对数控系统有一定的了解和操作技能。
调整方法三:智能调整智能调整是结合人工智能技术对伺服参数进行智能化调整,通过学习和优化算法,使得机床能够自动适应不同工件的加工要求。
这种方法能够实现个性化定制,提高加工精度和效率,但需要大量的数据支持和复杂的算法设计。
调整方法四:在线优化在线优化是在实际加工过程中根据机床工作状态和负载情况实时调整伺服参数,以达到最佳加工效果。
这种方法可以最大限度地提高加工质量和效率,但需要对机床和加工过程有深入的理解,以及高级的控制算法和技术支持。
综上所述,数控机床伺服参数调整方法有多种选择,操作人员可以根据实际需求和技术水平选择合适的调整方法,以实现最佳的加工效果和效率。
安川伺服的参数设定技巧与注意事项

安川伺服的参数设定技巧与注意事项在这篇文章中,我们将探讨安川伺服的参数设定技巧与注意事项。
安川伺服是一种常用的控制系统,广泛应用于工业自动化领域。
正确地设置安川伺服的参数对于提高系统性能和运行稳定性至关重要。
下面我们将介绍几个需要注意的技巧和事项。
一、选择适当的伺服参数1. 转矩参数(Torque Parameters):根据实际应用需求设置伺服的转矩参数。
这些参数包括目标扭矩、增益和补偿等。
需要根据工作负载的特点和性能要求来进行调整,以确保系统的动态响应和稳定性。
2. 速度参数(Velocity Parameters):根据系统的轴速度要求设置伺服的速度参数,包括目标速度、加减速时间和限制值等。
合适的速度参数能够提高伺服系统的响应速度和运动平滑度。
3. 位置参数(Position Parameters):位置参数对于伺服系统的定位控制至关重要。
需要根据工作环境的要求,设置合适的位置参数,包括目标位置、位置偏移和位置补偿等。
正确的位置参数设置可以提高系统的定位精度和重复性。
二、注意事项1. 系统稳定性:在参数设定过程中,需要注意系统的稳定性。
过高的增益值和不合理的参数设置可能导致系统的振荡和不稳定。
因此,应该根据实际情况逐步调整参数,以确保系统的稳定性。
2. 运动平滑度:在高速运动和快速变化的过程中,伺服系统的运动平滑度尤为重要。
合理的速度和加减速时间参数可以改善系统的运动平滑性,减少冲击和振动。
3. 动态响应:伺服系统的动态响应直接影响其控制性能。
适当调整伺服的响应速度和增益参数,可以提高系统的动态响应和控制精度。
4. 负载特性:在参数设定过程中,需要考虑工作负载的特点和变化。
不同的负载特性可能需要不同的参数设置,特别是在负载变化较大的情况下。
因此,应该根据实际负载情况进行参数调整。
5. 保护设置:在设置伺服参数时,要注意合理设置保护参数,以防止过流、过热和过载等问题。
这些保护参数可以保护伺服系统免受意外故障的影响,延长系统的寿命。
分析伺服定位不准的可能原因

分析伺服定位不准的可能原因伺服定位不准确是一个常见的问题,在许多应用领域中都会遇到。
对于机器人、自动化设备、数控机床等需要精确定位的系统来说,定位的准确性尤为重要。
在本文中,我将分析伺服定位不准的可能原因,并探讨如何解决这些问题。
1. 机械问题机械问题是导致伺服定位不准确的主要原因之一。
机械部件的磨损、松动或不平衡可能会导致伺服系统的运动不稳定。
导轨的磨损会导致运动时的摩擦增加,从而降低定位精度。
紧固件的松动也可能影响机械系统的稳定性和准确性。
解决方法:定期检查和维护机械部件。
如有必要,更换磨损的部件,紧固松动的紧固件,并校准机械系统以确保其准确性和稳定性。
2. 传感器问题传感器是伺服系统中关键的组成部分,用于监测位置、速度和加速度等参数。
如果传感器出现故障或校准不准确,那么伺服定位的准确性将受到影响。
解决方法:检查传感器的运行状态和校准。
确保传感器的连接稳定可靠,校准参数正确设置。
如有必要,更换故障的传感器并重新校准系统。
3. 控制系统问题控制系统是伺服定位的核心,它负责接收指令并控制伺服系统的运动。
如果控制系统存在问题,如信号干扰、控制算法不准确等,那么伺服定位将不准确。
解决方法:检查控制系统的连接和设置。
确保信号传输无干扰,控制算法准确。
如果需要,可以对控制系统进行升级或更换以提高定位准确性。
4. 燥刺激和环境条件环境条件也可能对伺服定位的准确性产生影响。
机械振动、温度变化、湿度等因素都可能干扰伺服系统的运动,导致定位不准确。
解决方法:减少环境条件对伺服系统的干扰。
通过采取隔离措施来降低震动对系统的影响,控制好温度和湿度等因素。
伺服定位不准确可能是由于机械问题、传感器问题、控制系统问题以及燥刺激和环境条件等多个因素引起的。
要解决这些问题,我们需要定期检查和维护机械部件,确保传感器的正常运行和准确校准,检查和升级控制系统,并降低环境条件对系统的干扰。
只有综合考虑和解决这些问题,才能提高伺服定位的准确性和稳定性。
伺服定位不准的原因

伺服定位不准的原因伺服定位不准是指在伺服系统中,所设定的目标位置与实际位置存在偏差。
这种偏差可能会导致机器运行不稳定,影响加工质量甚至出现事故。
下面将从以下几个方面分析伺服定位不准的原因。
一、机械结构问题1.机械结构刚度不足:机床刚度不足会导致在加工过程中发生振动,进而影响伺服系统的精度。
2.传动链路松动:传动链路松动会导致传递到伺服系统的指令信号与实际运动存在误差,从而影响定位精度。
3.负载过大:当负载过大时,由于惯性力的作用,伺服系统难以控制电机的速度和位置,从而影响定位精度。
二、电气问题1.电源电压波动:当电源电压波动较大时,会直接影响到驱动器输出的电压和电流大小,从而导致驱动器输出功率不稳定,进而影响伺服系统的精度。
2.编码器损坏:编码器是反馈信号的重要来源之一,在编码器损坏的情况下,伺服系统无法准确获取实际位置信息,从而影响定位精度。
3.控制卡故障:控制卡是伺服系统的核心部件之一,当控制卡发生故障时,会导致指令信号无法正常输出,从而影响定位精度。
三、环境问题1.温度过高或过低:温度是影响伺服系统的重要因素之一。
当环境温度过高或过低时,会导致电子元器件的参数发生变化,从而影响伺服系统的工作稳定性和精度。
2.湿度过大或过小:湿度是影响电子元器件寿命和可靠性的重要因素之一。
当湿度过大或过小时,会导致电子元器件氧化、腐蚀等问题,从而影响伺服系统的工作稳定性和精度。
以上就是伺服定位不准的原因分析。
在实际应用中,我们需要根据不同情况采取相应措施来解决问题。
例如,在机械结构方面可以加强机床刚度、调整传动链路等;在电气方面可以保证电源稳定、及时更换损坏的编码器等;在环境方面可以控制温湿度等。
只有全面分析问题,找到根本原因,才能有效解决伺服定位不准的问题,保证机器的稳定运行和加工质量。
提升数控机床定位精度的常用方法
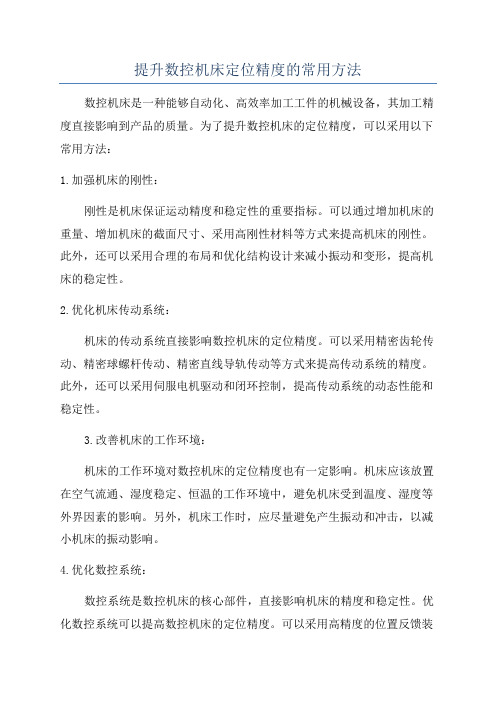
提升数控机床定位精度的常用方法数控机床是一种能够自动化、高效率加工工件的机械设备,其加工精度直接影响到产品的质量。
为了提升数控机床的定位精度,可以采用以下常用方法:1.加强机床的刚性:刚性是机床保证运动精度和稳定性的重要指标。
可以通过增加机床的重量、增加机床的截面尺寸、采用高刚性材料等方式来提高机床的刚性。
此外,还可以采用合理的布局和优化结构设计来减小振动和变形,提高机床的稳定性。
2.优化机床传动系统:机床的传动系统直接影响数控机床的定位精度。
可以采用精密齿轮传动、精密球螺杆传动、精密直线导轨传动等方式来提高传动系统的精度。
此外,还可以采用伺服电机驱动和闭环控制,提高传动系统的动态性能和稳定性。
3.改善机床的工作环境:机床的工作环境对数控机床的定位精度也有一定影响。
机床应该放置在空气流通、湿度稳定、恒温的工作环境中,避免机床受到温度、湿度等外界因素的影响。
另外,机床工作时,应尽量避免产生振动和冲击,以减小机床的振动影响。
4.优化数控系统:数控系统是数控机床的核心部件,直接影响机床的精度和稳定性。
优化数控系统可以提高数控机床的定位精度。
可以采用高精度的位置反馈装置,如光栅尺、编码器等,提供更精确的位置反馈信号。
另外,可以采用高性能的数控控制器,提供更稳定、更精确的控制信号。
5.加强机床的维护和保养:机床的定位精度会受到磨损、松动等因素的影响,因此定期的维护和保养是必不可少的。
可以定期进行机床的清洁、润滑和紧固,检查机床各部位的磨损情况,及时更换损坏的零部件。
此外,还可以定期校准机床的精度,确保机床的定位精度符合要求。
6.合理选择切削参数:切削参数的选择对机床的定位精度也有一定影响。
合理选择切削速度、进给量和切削深度,可以减小切削力和热变形,提高机床的加工精度。
7.采用补偿技术:补偿技术是提高机床定位精度的一种重要方法。
根据机床运动过程中产生的误差特点,可以通过运动轨迹的补偿来改善机床的定位精度。
补偿技术主要包括误差补偿、刀具半径补偿、刀具长度补偿、热变形补偿等。
数控机床伺服参数调整方法

数控机床伺服参数调整方法数控机床在现代工业生产中占据着非常重要的位置,而数控机床的伺服系统则是数控机床的核心部件之一。
伺服系统的参数调整对于数控机床的性能和精度有着非常重要的影响。
掌握伺服系统参数调整的方法对于提高数控机床的加工精度和效率具有非常重要的意义。
伺服系统是一种能够控制机械装置的位置、速度和加速度的系统。
而数控机床的伺服系统又是指能够控制机床轴的位置、速度和加速度的系统。
通过对伺服系统的参数进行调整,可以使数控机床在加工过程中实现更高的精度和效率。
1. 确定调整参数首先需要确定要调整的伺服系统参数,一般涉及的参数包括比例增益、积分时间、微分时间、速度环参数、位置环参数等。
每个参数调整的目的和影响都不同,因此需要根据具体情况来选择调整的参数。
2. 调整比例增益比例增益是伺服系统的一个重要参数,它决定了伺服系统的响应速度和稳定性。
调整比例增益可以改变伺服系统的灵敏度,使机床在加工过程中更加稳定和精确。
调整比例增益的方法一般是先将比例增益设为一个合适的初始值,然后进行试加工,通过观察加工结果和机床的运动情况来逐步调整比例增益的大小,直到达到最佳的加工效果。
3. 调整积分时间和微分时间积分时间和微分时间是影响伺服系统稳定性和抗干扰能力的重要参数。
通过调整积分时间和微分时间可以使伺服系统对扰动和干扰的抵抗能力更强,从而提高加工精度和稳定性。
位置环是伺服系统中最基本的控制环节,通过调整位置环参数可以改变伺服系统的定位精度和稳定性。
调整位置环参数可以使机床在定位和转角控制方面更加精确和稳定。
在进行伺服参数调整的过程中,需要重点考虑机床的加工类型、材料的特性、工件的形状和加工要求等因素,以及连续的试加工过程中不断调整参数,逐步找到最佳的调整方案。
同时还需要注意遵守相关的安全规范和操作规程,确保在调整伺服参数的过程中不影响机床的正常运行和操作人员的安全。
伺服系统参数调整是数控机床加工精度和效率提高的关键。
伺服电机增益调整的原理及方法
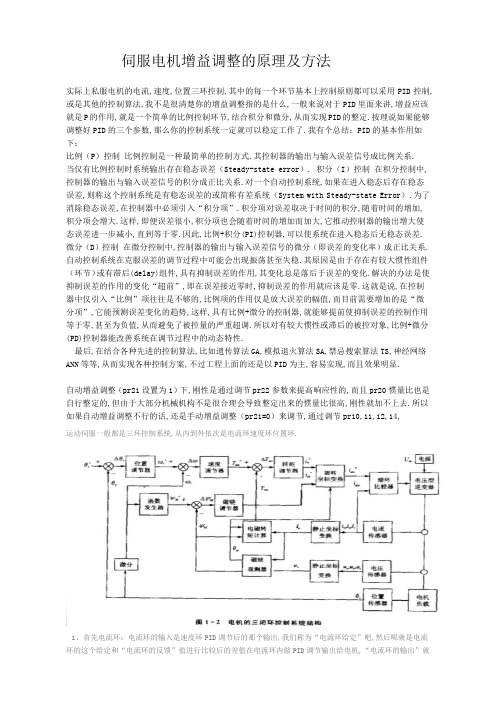
伺服电机增益调整的原理及方法实际上私服电机的电流,速度,位置三环控制,其中的每一个环节基本上控制原则都可以采用PID控制,或是其他的控制算法,我不是很清楚你的增益调整指的是什么,一般来说对于PID里面来讲,增益应该就是P的作用,就是一个简单的比例控制环节,结合积分和微分,从而实现PID的整定.按理说如果能够调整好PID的三个参数,那么你的控制系统一定就可以稳定工作了.我有个总结:PID的基本作用如下:比例(P)控制比例控制是一种最简单的控制方式.其控制器的输出与输入误差信号成比例关系.当仅有比例控制时系统输出存在稳态误差(Steady-state error). 积分(I)控制在积分控制中,控制器的输出与输入误差信号的积分成正比关系.对一个自动控制系统,如果在进入稳态后存在稳态误差,则称这个控制系统是有稳态误差的或简称有差系统(System with Steady-state Error).为了消除稳态误差,在控制器中必须引入“积分项”.积分项对误差取决于时间的积分,随着时间的增加,积分项会增大.这样,即便误差很小,积分项也会随着时间的增加而加大,它推动控制器的输出增大使态误差进一步减小,直到等于零.因此,比例+积分(PI)控制器,可以使系统在进入稳态后无稳态误差. 微分(D)控制在微分控制中,控制器的输出与输入误差信号的微分(即误差的变化率)成正比关系. 自动控制系统在克服误差的调节过程中可能会出现振荡甚至失稳.其原因是由于存在有较大惯性组件(环节)或有滞后(delay)组件,具有抑制误差的作用,其变化总是落后于误差的变化.解决的办法是使抑制误差的作用的变化“超前”,即在误差接近零时,抑制误差的作用就应该是零.这就是说,在控制器中仅引入“比例”项往往是不够的,比例项的作用仅是放大误差的幅值,而目前需要增加的是“微分项”,它能预测误差变化的趋势,这样,具有比例+微分的控制器,就能够提前使抑制误差的控制作用等于零,甚至为负值,从而避免了被控量的严重超调.所以对有较大惯性或滞后的被控对象,比例+微分(PD)控制器能改善系统在调节过程中的动态特性.最后,在结合各种先进的控制算法,比如遗传算法GA,模拟退火算法SA,禁忌搜索算法TS,神经网络ANN等等,从而实现各种控制方案,不过工程上面的还是以PID为主,容易实现,而且效果明显.自动增益调整(pr21设置为1)下,刚性是通过调节pr22参数来提高响应性的,而且pr20惯量比也是自行整定的,但由于大部分机械机构不是很合理会导致整定出来的惯量比很高,刚性就加不上去.所以如果自动增益调整不行的话,还是手动增益调整(pr21=0)来调节,通过调节pr10,11,12,14,运动伺服一般都是三环控制系统,从内到外依次是电流环速度环位置环.1、首先电流环:电流环的输入是速度环PID调节后的那个输出,我们称为“电流环给定”吧,然后呢就是电流环的这个给定和“电流环的反馈”值进行比较后的差值在电流环内做PID调节输出给电机,“电流环的输出”就是电机的每相的相电流,“电流环的反馈”不是编码器的反馈而是在驱动器内部安装在每相的霍尔元件(磁场感应变为电流电压信号)反馈给电流环的.2、速度环:速度环的输入就是位置环PID调节后的输出以及位置设定的前馈值,我们称为“速度设定”,这个“速度设定”和“速度环反馈”值进行比较后的差值在速度环做PID调节(主要是比例增益和积分处理)后输出就是上面讲到的“电流环的给定”.速度环的反馈来自于编码器的反馈后的值经过“速度运算器”得到的.3、位置环:位置环的输入就是外部的脉冲(通常情况下,直接写数据到驱动器地址的伺服例外),外部的脉冲经过平滑滤波处理和电子齿轮计算后作为“位置环的设定”,设定和来自编码器反馈的脉冲信号经过偏差计数器的计算后的数值在经过位置环的PID调节(比例增益调节,无积分微分环节)后输出和位置给定的前馈信号的合值就构成了上面讲的速度环的给定.位置环的反馈也来自于编码器.编码器安装于伺服电机尾部,它和电流环没有任何联系,他采样来自于电机的转动而不是电机电流,和电流环的输入、输出、反馈没有任何联系.而电流环是在驱动器内部形成的,即使没有电机,只要在每相上安装模拟负载(例如电灯泡)电流环就能形成反馈工作.谈谈PID各自对差值调节对系统的影响:1、单独的P(比例)就是将差值进行成比例的运算,它的显着特点就是有差调节,有差的意义就是调节过程结束后,被调量不可能与设定值准确相等,它们之间一定有残差,残差具体值您可以通过比例关系计算出...增加比例将会有效减小残差并增加系统响应,但容易导致系统激烈震荡甚至不稳定...2、单独的I(积分)就是使调节器的输出信号的变化速度与差值信号成正比,大家不难理解,如果差值大,则积分环节的变化速度大,这个环节的正比常数的比例倒数我们在伺服系统里通常叫它为积分时间常数,积分时间常数越小意味着系统的变化速度越快,所以同样如果增大积分速度(也就是减小积分时间常数)将会降低控制系统的稳定程度,直到最后出现发散的震荡过程,...这个环节最大的好处就是被调量最后是没有残差的...3、PI(比例积分)就是综合P和I的优点,利用P调节快速抵消干扰的影响,同时利用I调节消除残差...4、单独的D(微分)就是根据差值的方向和大小进行调节的,调节器的输出与差值对于时间的导数成正比,微分环节只能起到辅助的调节作用,它可以与其他调节结合成PD和PID调节...它的好处是可以根据被调节量(差值)的变化速度来进行调节,而不要等到出现了很大的偏差后才开始动作,其实就是赋予了调节器以某种程度上的预见性,可以增加系统对微小变化的响应特性...伺服的电流环的PID常数一般都是在驱动器内部设定好的,操作使用者不需要更改...速度环主要进行PI(比例和积分),比例就是增益,所以我们要对速度增益和速度积分时间常数进行合适的调节才能达到理想效果...位置环主要进行P(比例)调节...对此我们只要设定位置环的比例增益就好了...位置环、速度环的参数调节没有什么固定的数值,要根据外部负载的机械传动连接方式、负载的运动方式、负载惯量、对速度、加速度要求以及电机本身的转子惯量和输出惯量等等很多条件来决定,调节的简单方法是在根据外部负载的情况进行大体经验的范围内将增益参数从小往大调,积分时间常数从大往小调,以不出现震动超调的稳态值为最佳值进行设定...当进行位置模式需要调节位置环时,最好先调节速度环(此时位置环的比例增益设定在经验值的最小值),调节速度环稳定后,在调节位置环增益,适量逐步增加,位置环的响应最好比速度环慢一点,不然也容易出现速度震荡.一般伺服都有三种控制方式:速度控制方式,转矩控制方式,位置控制方式 .1、转矩控制:转矩控制方式是通过外部模拟量的输入或直接的地址的赋值来设定电机轴对外的输出转矩的大小,具体表现为例如10V对应5Nm的话,当外部模拟量设定为5V时电机轴输出为:如果电机轴负载低于时电机正转,外部负载等于时电机不转,大于时电机反转(通常在有重力负载情况下产生).可以通过即时的改变模拟量的设定来改变设定的力矩大小,也可通过通讯方式改变对应的地址的数值来实现.应用主要在对材质的受力有严格要求的缠绕和放卷的装置中,例如饶线装置或拉光纤设备,转矩的设定要根据缠绕的半径的变化随时更改以确保材质的受力不会随着缠绕半径的变化而改变.2、位置控制:位置控制模式一般是通过外部输入的脉冲的频率来确定转动速度的大小,通过脉冲的个数来确定转动的角度,也有些伺服可以通过通讯方式直接对速度和位移进行赋值.由于位置模式可以对速度和位置都有很严格的控制,所以一般应用于定位装置.3、速度模式:通过模拟量的输入或脉冲的频率都可以进行转动速度的控制,在有上位控制装置的外环PID 控制时速度模式也可以进行定位,但必须把电机的位置信号或直接负载的位置信号给上位反馈以做运算用.位置模式也支持直接负载外环检测位置信号,此时的电机轴端的编码器只检测电机转速,位置信号就由直接的最终负载端的检测装置来提供了,这样的优点在于可以减少中间传动过程中的误差,增加整个系统的定位精度.4、谈谈3环,伺服电机一般为三个环控制,所谓三环就是3个闭环负反馈PID调节系统.最内的PID环就是电流环,此环完全在伺服驱动器内部进行,通过霍尔装置检测驱动器给电机的各相的输出电流,负反馈给电流的设定进行PID调节,从而达到输出电流尽量接近等于设定电流,电流环就是控制电机转矩的,所以在转矩模式下驱动器的运算最小,动态响应最快.第2环是速度环,通过检测的电机编码器的信号来进行负反馈PID调节,它的环内PID输出直接就是电流环的设定,所以速度环控制时就包含了速度环和电流环,换句话说任何模式都必须使用电流环,电流环是控制的根本,在速度和位置控制的同时系统实际也在进行电流(转矩)的控制以达到对速度和位置的相应控制.第3环是位置环,它是最外环,可以在驱动器和电机编码器间构建也可以在外部控制器和电机编码器或最终负载间构建,要根据实际情况来定.由于位置控制环内部输出就是速度环的设定,位置控制模式下系统进行了所有3个环的运算,此时的系统运算量最大,动态响应速度也最慢.。
如何提高伺服系统的定位精度
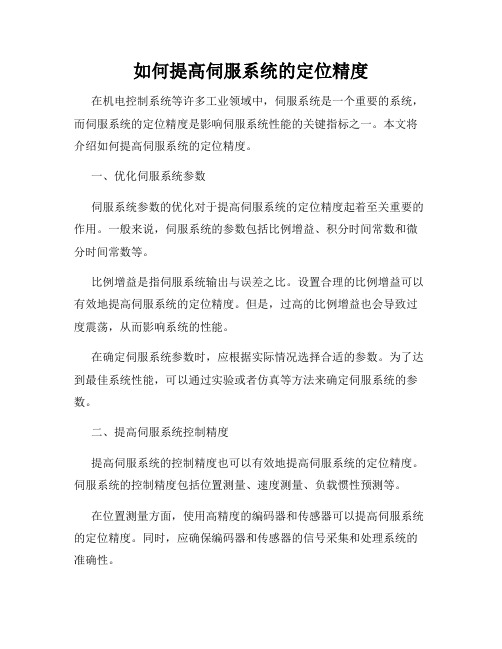
如何提高伺服系统的定位精度在机电控制系统等许多工业领域中,伺服系统是一个重要的系统,而伺服系统的定位精度是影响伺服系统性能的关键指标之一。
本文将介绍如何提高伺服系统的定位精度。
一、优化伺服系统参数伺服系统参数的优化对于提高伺服系统的定位精度起着至关重要的作用。
一般来说,伺服系统的参数包括比例增益、积分时间常数和微分时间常数等。
比例增益是指伺服系统输出与误差之比。
设置合理的比例增益可以有效地提高伺服系统的定位精度。
但是,过高的比例增益也会导致过度震荡,从而影响系统的性能。
在确定伺服系统参数时,应根据实际情况选择合适的参数。
为了达到最佳系统性能,可以通过实验或者仿真等方法来确定伺服系统的参数。
二、提高伺服系统控制精度提高伺服系统的控制精度也可以有效地提高伺服系统的定位精度。
伺服系统的控制精度包括位置测量、速度测量、负载惯性预测等。
在位置测量方面,使用高精度的编码器和传感器可以提高伺服系统的定位精度。
同时,应确保编码器和传感器的信号采集和处理系统的准确性。
在速度测量方面,采用良好的速度测量技术可以提高伺服系统的定位精度。
例如,可以使用德罗布滑动模式观测法等方法来提高速度测量的精度。
在负载惯性方面,通过精确地测量负载的惯性和预测负载惯性来提高伺服系统的定位精度。
三、使用高精度位置环在传统伺服系统中,位置环是控制系统的核心。
使用高精度位置环可以有效地提高伺服系统的定位精度。
高精度位置环具有较高的带宽和稳定性,可以减少系统的噪声干扰,从而提高系统的精度。
四、使用高精度伺服电机和减速器伺服电机和减速器也是影响伺服系统定位精度的关键因素之一。
使用高精度的伺服电机和减速器可以提高伺服系统的定位精度。
例如,使用高精度的同步电机和精密减速器等装置,可以提高伺服系统的定位精度。
五、结论伺服系统的定位精度是影响其性能的关键指标之一。
通过优化伺服系统参数,提高伺服系统的控制精度,使用高精度位置环和伺服电机等方法,可以有效地提高伺服系统的定位精度,从而满足实际工程需求。
定位精度

定位精度:它是指数控机床各移动轴在确定的终点所能达到的实际位置精度,其误差称为定位误差。
定位误差包括伺服系统、检测系统、进给系统等的误差,还包括移动部件导轨的几何误差等。
它将直接影响零件加工的精度。
影响系统的工作精度有:系统中电机的质量、机械传动部分的结构和质量、控制电路的性能。
解决上述因素的方法有:改善步进电机的性能、减小步距角、采用精密传动副、减小传动链中传动间隙等方法。
另外,从控制方法上讲主要有:传动间隙补偿、螺距误差补偿、细分线路。
1. 传动间隙补偿数控机床上加工零件时的进给运动,是依靠驱动装置带动齿轮、丝杠传动.进而推动机床工作台产生位移来实现的。
作为传动元件的齿轮、丝杠尽管制造装配精度很高,但总免不了存在着间隙,当运动方向改变时,最初的若干个指令脉冲只能起到消除间隙的作用,工作台不动,从而产生传动误差。
传动间隙补偿的基本方法为:判别进给方向变化后,首先不向步进电机输送反向位移脉冲,而是将间隙值换算为脉冲数,驱动步进电机转动,越过传动间隙,待间隙补偿结束后再按指令脉冲进行动作。
间隙补偿脉冲的数目由实测决定,并作为参数存储在RAM 中。
2. 螺距误差补偿传动链中的滚珠丝杠螺距累积误差直接影响工作台的位移精度,为数控设备提供了自动螺距误差补偿功能来解决这个问题。
设备进给精度调整时,设置若干个补偿点(通常可达128—256个),在每个补偿点处,把工作台的位置误差测量下来确定补偿值,作为控制参数输入给数控设备。
设备运行时,工作台每经过一个补偿点,CNC控制机就向规定的方向加入一个设定的补偿量,补偿掉螺距误差,使工作台到达正确的位置。
3. 细分线路细分线路是把步进电机的一步再分得细一些。
如十细分线路,将原来输入一个进给脉冲步进电机走一步变为输入十个脉冲才走一步。
即采用十细分线路后,在进给速度不变的情况下,可使脉冲当量缩小到原来的十分之一。
- 1、下载文档前请自行甄别文档内容的完整性,平台不提供额外的编辑、内容补充、找答案等附加服务。
- 2、"仅部分预览"的文档,不可在线预览部分如存在完整性等问题,可反馈申请退款(可完整预览的文档不适用该条件!)。
- 3、如文档侵犯您的权益,请联系客服反馈,我们会尽快为您处理(人工客服工作时间:9:00-18:30)。
分析了伺服系统定位误差形成的原因,提出了伺服系统采用分段线性减速并以开环方式精确定位的方法,给出了相应的程序流程图,对提高数控机床伺服系统的定位精度具有实用参考价值。
数控机床的定位精度直接影响到机床的加工精度。
传统上以步进电动机作驱动机构的机床,由于步进电动机的固有特性,使得机床的重复定位精度可以达到一个脉冲当量。
但是,步进电动机的脉冲当量不可能很小,因而定位精度不高。
伺服系统的脉冲当量可以比步进电动机系统小得多,但是,伺服系统的定位精度很难达到一个脉冲当量。
由于CPU性能已有极大提高,故采用软件可以有效地提高定位精度。
我们分析了常规控制算法导致伺服系统定位精度误差较大的原因,提出了分段线性减速并以开环方式精确定位的方法,实践中取得了很好的效果。
一、伺服系统定位误差形成原因与克服办法
通常情况下,伺服系统控制过程为:升速、恒速、减速和低速趋近定位点,整个过程都是位置闭环控制。
减速和低速趋近定位点这两个过程,对伺服系统的定位精度有很重要的影响。
减速控制具体实现方法很多,常用的有指数规律加减速算法、直线规律加减速算法。
指数规律加减速算法有较强的跟踪能力,但当速度较大时平稳性较差,一般适用在跟踪响应要求较高的切削加工中。
直线规律加减速算法平稳性较好,适用在速度变化范围较大的快速定位方式中。
选择减速规律时,不仅要考虑平稳性,更重要的是考虑到停止时的定位精度。
从理论上讲,只要减速点选得正确,指数规律和线性规律的减速都可以精确定位,但难点是减速点的确定。
通常减速点的确定方法有:
(1)如果在起动和停止时采用相同的加减速规律,则可以根据升速过程的有关参数和对称性来确定减速点。
(2)根据进给速度、减速时间和减速的加速度等有关参数来计算减速点,在当今高速CPU 十分普及的条件下,这对于CNC的伺服系统来说很容易实现,且比方法(1)灵活。
伺服控制时,由软件在每个采样周期判断:若剩余总进给量大于减速点所对应的剩余进给量,则该瞬时进给速度不变(等于给定值),否则,按一定规律减速。
理论上讲,剩余总进给量正好等于减速点所对应的剩余进给量时减速,并按预期的减速规律减速运行到定位点停止。
但实际上,伺服系统正常运转时每个采样周期反馈的脉冲数是几个、十几个、几十个甚至更多,因而实际减速点并不与理论减速点重合。
如图1所示,其最大误差等于减速前一个采样周期的脉冲数。
若实际减速点提前,则按预期规律减速的速度降到很低时还未到达定位点,可能需要很长时间才能到达定位点。
若实际减速点滞后于理论减速点,则到达定位点时速度还较高,影响定位精度和平稳性。
为此,我们提出了分段线性减速方法。
在低速趋近定位点的过程中,设速度为V0(mm/s),伺服系统的脉冲当量为δ(μm),采样周期为τ(ms),则每个采样周期应反馈的脉冲数为:N0=V0τ/δ。
由于实际反馈的脉冲数是个整数,可能有一个脉冲的误差,即此时速度检测误差最大值为l/N0=δ/(V0τ)。
采样周期越小、速度越低,则速度检测误差越大。
为了满足定位精度是一个脉冲的要求,应使V0很小,使得N0≤1,此时速度检测误差达到100%甚至更高。
如果此时仍然实行位置闭
环控制,必然造成极大的速度波动,严重影响伺服机构的精确定位。
所以,我们认为此时应采取位置开环控制,以避免速度波动。
二、分段线性减速精度定位
1、方法与步骤
分段线性减速的特点是减速点不需要精确确定。
首先讨论最不利情况,即由伺服系统的最高速度开始减速过程,具体的减速步骤是:
(1)初始速度VG经AB段以加速度a2降速到V2,在BC段以V2匀速运行T2个采样周期,用BC这个时间段来补偿减速点A的误差。
A点最大误差是VG对应的一个采样周期的脉冲数NG=VGτ/δ,速度为V2时一个采样周期的脉冲数为N2=V2τ/δ,则只要保证T2≥NG/N2=VG/V2,就可以使BC时间段补偿减速点A点的误差。
(2)速度V2经CD段以加速度a1降速到V1,在DE段以V1匀速运行T1个采样周期,用DE这个时间段来补偿减速点C的误差。
类似地,应保证T1≥V2/V1。
由于速度V1较低,假设取V1=5mm/s,脉冲当量δ=1μm,采样周期τ=1ms,则单位采样周期应反馈的脉冲数为N1=5,速度检测误差最大可达20%。
所以,从这段过程开始就可以采用开环控制,以避免由于速度检测误差而引起速度波动。
值得注意的是,开环控制算法应包括伺服机构的死区补偿和零漂补偿模块。
(3)速度V1经EF段以加速度a0降速到V0,在FG段以V0匀速运行T0个采样周期,直到到达定位点,这个过程采用位置开环控制。
通常情况下开始减速时伺服系统的速度(假设为VG1)小于最高速度,这时相当于减速起始点A向下移动到A1点,如图2虚线所示。
如果初始速度小于V2,如图2中的VG2所示,相当于减速起始点移到了CD段,少了一段减速过程。
程序框图如图3所示,图中R为总剩余进给量(脉冲数),RA、RB、RC、RD、RE、RF分别对应图2减速曲线A、B、C、D、E、F点所对应的剩余进给量(脉冲数),可以由V、a、T、τ等参数算出。
例如:
2、几组参数的确定原则
(1)V0、V1和V2在常规的减速过程中,减速点的位置误差全靠最后低速趋近阶段来补偿,这样,V0就很不好选取。
如果V0选得过小,应保证T0≥(VG/V0),则需要很长时间才能到达定位点;如果V0选得较大,直接影响定位精度。
分段线性减速方法与常规的减速方法相比,增加了BC、DE两个时间段,减速点的位置误差可以在较高速度得到绝大部分的补偿。
因此,V0可以选得很小。
通常可取伺服系统的最低速度,这样可以提高伺服系统的定位精度。
V1、V2可分别取伺服系统最高速度的1%和10%。
(2)a0、a1和a2加速度越大,减速过程越短,但引起的冲击和误差也越大。
因此,在高速阶段加速度可取大些,以保证减速过程的快速性;低速阶段应取较小的加速度,以保证定位精度。
通常a0的值在数值上可取为与V0相等。
(3)T0、T1和T2由前面分析可知,为了补偿减速点的位置误差,应取T0=KV1/V0,T1=KV2/V1,T2=KVG/V2,式中K为可靠性系数,用来补偿算法的计算误差及其它一些不确定因素的影响,常取K=1.1~1.3。
该方法与伺服系统本身特性无关,可作为任何伺服系统在任意速度下减速控制方法。
在
我们为上海机床厂研制的YKA7232蜗杆砂轮磨齿机数控系统中,采用了分段线性减速开环趋近定位点的控制方法。
实测各轴定位精度和重复定位精度都控制在一个脉冲当量内,性能稳定,获得了很好的效果。
交流伺服系统根据其处理信号的方式不同,可以分为模拟式伺服、数字模拟混合式伺服和全数字式伺服;如果按照使用的伺服电动机的种类不同,又可分为两种:一种是用永磁同步伺服电动机构成的伺服系统,包括方波永磁同步电动机(无刷直流机)伺服系统和正弦波永磁同步电动机伺服系统;另一种是用鼠笼型异步电动机构成的伺服系统。
二者的不同之处在于永磁同步电动机伺服系统中需要采用磁极位置传感器而感应电动机伺服系统中含有滑差频率计算部分。
若采用微处理器软件实现伺服控制,可以使永磁同步伺服电动机和鼠笼型异步伺服电动机使用同一套伺服放大器。