第三讲_机械加工精度和表面质量
机械加工精度与表面质量分析

机械加工精度与表面质量分析机械加工是制造业中常见的一种工艺,它对于零件的精度和表面质量要求非常高。
机械加工精度和表面质量的好坏直接影响到零件的使用效果和寿命。
本文将从机械加工精度和表面质量的定义、影响因素、提高方法等方面进行阐述。
1. 机械加工精度的定义机械加工精度指的是加工零件的尺寸和形状与设计要求之间的偏差程度。
一般来说,机械加工精度分为三个方面:形位精度、尺寸精度和粗糙度。
形位精度是指零件各个面、轴线和孔中心轴线之间的位置关系,包括平行度、垂直度、圆度、同心度等。
尺寸精度是指零件在加工过程中的实际尺寸与设计尺寸之间的偏差,包括直线度、平面度、圆度等。
粗糙度是指加工表面的光洁度,也就是表面的起伏程度,常用Ra值来表示。
粗糙度越小,表面越光滑。
2. 影响机械加工精度的因素机械加工精度受到多种因素的影响,包括机床的精度、刀具的强度和刚度、切削工况、刀具磨损和材料性质等。
其中,机床的精度是机械加工精度的基础,如刚性、传动精度等。
刀具的强度和刚度决定了切削力和振动情况,对加工精度影响较大。
切削工况包括切削速度、进给量和切削深度,不同工况会引起不同的加工精度。
此外,刀具磨损和材料性质也会影响加工精度。
3. 机械加工表面质量的定义机械加工表面质量是指零件在机械加工过程中获得的表面光洁度和形貌特征。
表面质量的好坏通常通过表面粗糙度和表面形貌来衡量。
表面粗糙度是指在单位表面积内,表面起伏的最小值与最大值之差。
通常使用Ra值来表示,Ra值越小,表面质量越好。
表面形貌是指加工表面的纹理和形态特征,如划痕、疤痕等。
表面质量的好坏直接影响到零件的摩擦、磨损、密封性能等。
4. 影响机械加工表面质量的因素机械加工表面质量的好坏与多种因素有关。
首先,刀具的磨损和切削参数会直接影响表面粗糙度。
刀具磨损会增加切削力和振动,导致表面粗糙度增加。
其次,材料的硬度和韧性对表面质量有重要影响。
硬度高的材料加工困难,容易产生划痕和裂纹。
机械加工精度与加工表面质量

机械加工精度与加工表面质量机械加工精度和加工表面质量是衡量机械加工工艺质量的两个重要指标。
机械加工精度是指加工件在尺寸、形状、位置和几何特征等方面的精确度,而加工表面质量则是指加工件表面的光洁度、粗糙度以及表面缺陷等特征。
这两个指标在现代制造业中具有重要的意义,直接关系到产品的质量和性能。
1. 机械加工精度机械加工精度通常表示加工件与其设计尺寸之间的误差。
机械加工精度的高低直接影响着加工件的装配性能和使用寿命。
常见的机械加工精度包括以下几个方面:1.1 尺寸精度尺寸精度是指加工件的几何尺寸与其设计尺寸之间的偏差。
尺寸精度可以通过测量加工件的长度、直径、角度等几何参数来评估。
通常,尺寸精度可以分为直线度、平行度、圆度、圆柱度、角度度等几个方面。
1.2 形状精度形状精度是指加工件的形状与设计形状之间的误差。
形状精度通常包括圆度、平面度、圆锥度、曲率半径等方面。
1.3 位置精度位置精度是指加工件上各个特征点的位置与设计位置之间的误差。
位置精度可以通过测量加工件上的特征点坐标来评估。
常见的位置精度指标有平行度、垂直度、位置误差等。
2. 加工表面质量加工表面质量是指加工件表面的光洁度、粗糙度以及表面缺陷等特征。
加工表面质量直接影响着摩擦、磨损、润滑等性能,同时也会影响产品的外观质量。
常见的加工表面质量指标包括以下几个方面:2.1 光洁度光洁度是指加工件表面的光亮程度。
光洁度往往是使用表面粗糙度指标来评估的,一般可通过光学显微镜、表面形貌仪等设备进行测量。
2.2 粗糙度粗糙度是指加工件表面的不规则程度。
表面粗糙度通常用Ra值表示,Ra值越小代表表面越光滑。
可以通过表面粗糙度仪进行测量,也可以使用触摸法、光学法等方法。
2.3 表面缺陷表面缺陷是指加工件表面的瑕疵、裂纹、划痕等缺陷。
表面缺陷会降低产品的整体质量和可靠性,因此正常加工过程中要尽量避免表面缺陷的产生。
3. 如何提高机械加工精度和加工表面质量为了提高机械加工精度和加工表面质量,可以从以下几个方面入手:3.1 选择合适的机床和刀具机床和刀具是机械加工的基础设备,选择合适的机床和刀具对于提高加工精度和表面质量非常重要。
机械加工中的表面质量与精度控制技术

机械加工中的表面质量与精度控制技术质量和精度的控制是机械加工中的重要环节,主要从当前机械加工精度的概念和内容出发,分析机械加工过程中产生误差的原因,力图探索在机械加工的过程中如何才能提高加工的质量,并且加强对加工过程的精度控制,从而提高整体加工水平。
标签:机械加工;表面质量;精度控制中图分类号:TB 文献标识码:A 文章编号:16723198(2012)180174011 机械加工精度概述机械加工精度是指工件在机械加工后的实际几何参数与零件图纸所规定的理想值之间的符合程度,如果它们之间存在不相符的程度则就称为加工误差。
机械的加工精度包括了三方面因素:首先是尺度因素,尺度因素限制加工表面和基准间尺寸的误差;其次是几何形状精度,主要是指限制加工表面的宏观性状的误差,从而达到提高机械加工表面质量的目的;最后是相互位置的精度,主要是指限制加工表面和其基准间的相互位置误差。
机械加工误差的大小反映了机械加工的精度高低。
2 影响机械加工质量和精度的因素及对策2.1 机床的几何误差在机械加工的过程中对工件的成形操作加工一般都是在机床上完成的,因此,机械加工品的机床几何误差直接会影响最终的加工质量和精度。
直接影响机械加工质量和精度的因素主要是主轴回转误差以及传动链误差。
从主轴回转误差来看,轴承本身的是指主轴在各个瞬间的实际回转轴线相对于其平均回转轴线的误差。
从传动链误差来看,主要是指传动链的始末两端传动元件之间相互运动产生的误差。
2.2 定位误差定位误差包括了两方面内容,分别是基准不重合誤差和定位副制造不准确误差。
在机床上对工件进行加工的过程中,需要将几何要素作为定位标准,当选择的定位基准和设计基准之间存在误差时就会产生基准不重合的误差。
另外夹具上的定位元件不可能完全准确,其实际尺寸都在允许范围内变动,当超过允许范围时就会造成较大的定位误差。
2.3 刀具的几何误差刀具在使用的过程中难免会产生磨损,从而在机械加工的过程中造成工件的尺寸以及形状的误差,最终影响了加工的质量和精度。
加工精度和表面质量的要求

加工精度和表面质量的要求一、加工精度要求。
1. 尺寸精度。
这就好比给零件做衣服,尺寸得合身。
比如说要做个轴,图纸上要求直径是10毫米,那你加工出来的轴直径可不能偏差太大。
如果偏差个0.1毫米,可能这个轴就塞不进它该去的孔里了,就像大脚穿小鞋或者小脚穿大鞋一样别扭。
一般来说,根据零件的用途,尺寸精度会有不同的等级要求,有的可能允许偏差在±0.01毫米以内,这就要求加工的时候得非常精细,就像雕刻大师刻小佛像,一丁点儿差错都不行。
2. 形状精度。
形状精度就是要让零件的形状长得像它设计的那样。
拿一个圆柱来说,它得是真正的圆柱,不能是歪歪扭扭的。
如果形状精度不达标,就像盖房子,本来要盖个四四方方的房子,结果盖成了梯形的,那可就麻烦了。
比如说加工一个平面,这个平面得平得像镜子一样,如果有凸起或者凹陷,那在装配或者使用的时候就会出问题。
像一些高精度的机床导轨,形状精度要求特别高,要是导轨不平,那机床加工出来的其他零件也都跟着遭殃了。
3. 位置精度。
这就像是给零件里的各个小部件排座位。
比如一个箱体上有几个孔,这些孔之间的距离、角度都得按规定来。
如果是发动机的缸体,缸孔之间的位置精度不达标,发动机的性能就会大打折扣。
就好像一个乐队,每个乐手的位置站错了,演奏出来的音乐肯定就乱套了。
像孔与孔之间的平行度、垂直度这些位置关系,都得严格控制在一定的误差范围内,不然整个零件或者设备就可能没法正常工作了。
二、表面质量要求。
1. 表面粗糙度。
2. 表面纹理。
表面纹理也很重要呢。
有时候我们希望零件表面有一定的纹理方向,就像木材的纹理一样。
比如说在车削加工的时候,车刀走刀的方向会在零件表面留下纹理。
如果纹理方向不对,可能会影响零件的受力情况。
比如一个受轴向力的轴,表面纹理最好是沿着轴向的,如果是杂乱无章的或者垂直于轴向的,这个轴在受力的时候就容易出问题,就像顺着木材纹理砍木头和横着纹理砍木头,难度和效果完全不一样。
3. 表面层物理机械性能。
浅谈机械加工中的表面质量和精度控制

科技经济市场
浅 谈机 械 加 工 中的表 面质 量和 精 度 控 制
任 晓 园
( 杭 州友佳 精 密机械 有 限公 司哈 尔滨 办事处 , 黑龙 江 哈 尔滨 1 5 0 0 4 0 ) ‘
摘 要 : 现 代 机 械 制 造 工 业 的 多功 能 需求 , 对机械加X - 质量的要求也不断提升。 表 面 质 量 和 精 度 是 机 械 加 工 中的 重 要 内 容 , 是 提 升 工 件 使 用性能的重要影响因素, 是 保 障机 械 加 工 质 量 的前 提 和 基 础 。 深 入探 究机 械 加 工 中的 表 面 质 量 和 精 度 控 制 措 施 , 是 推进 机 械 加 工科 学发展的有效手段。 关键 词 : 机械 加 工 : 表面质量: 精度 控 制
( 1 ) 加 工 的原 材 料 原 材 料 是 机 械 加 工 的 前 提 和 基 础 。在 进行 机 械 加 工 时 , 原
虑 副偏 角 、 刀尖圆弧半径等各方面因素 , 选 择 合 适 的修 光 刃 、 精 车刀等。 合 适 刀 具 的使 用 能够 使 机 械 加 工 工 件 表 面 质 量 得 到 提
3 影 响 机 械 加 工 精 度 的 因 素 分 析
机械加工中的加工精度控制和表面质量

机械加工中的加工精度控制和表面质量机械加工中的加工精度控制和表面质量是制造业中非常重要的关键问题。
在工业生产中,加工精度和表面质量直接影响着产品的性能和质量,因此在机械加工过程中如何控制加工精度和提高表面质量成为工程师和操作人员必须要解决的难题。
一、加工精度控制1. 数控机床的应用随着科技的发展,数控机床在机械加工领域中的应用越来越广泛。
数控机床可以通过程序控制加工过程,精确控制每一个阶段的加工参数,从而达到精确控制加工精度的目的。
与传统机床相比,数控机床具有更高的加工精度和稳定性。
2. 加工工艺的优化在机械加工过程中,加工工艺的优化对于提高加工精度至关重要。
合理选择切削速度、进给量、刀具类型等加工参数,可以减少刀具磨损和热变形,从而提高加工精度。
此外,采用先进的刀具和夹具,以及适当的切削液,也可以有效提高加工精度。
3. 检测与反馈控制在机械加工过程中,及时检测加工件的精度并进行反馈控制是非常重要的。
通过使用精密检测仪器和传感器,可以实时监测加工精度,并根据检测结果调整加工参数,以达到精确控制加工精度的目的。
同时,及时对设备进行维护和保养,保证设备的稳定性和精度。
二、表面质量提升1. 切削工艺的改进切削工艺是影响加工件表面质量的关键因素之一。
通过改进切削工艺,可以减少加工件表面的毛刺、划痕等缺陷,并提高表面光洁度。
采用合适的刀具,调整切削速度和进给量,以及增加切削液的使用量,都可以有效改善加工件的表面质量。
2. 表面处理技术的应用在机械加工过程中,常常会采用表面处理技术来提升加工件的表面质量。
例如,机械抛光、喷砂、电镀等技术可以使加工件表面更加光滑、均匀,从而提高表面质量。
此外,采用表面喷涂技术可以增加加工件的耐磨性和抗腐蚀性能。
3. 加工设备的改进加工设备的改进也可以提高机械加工中的表面质量。
例如,采用高精度的加工设备,如五轴加工中心和超精密磨床,可以有效减小加工误差,提高加工件的表面精度和平整度。
1.1.4加工精度和加工表面质量

加工精度和加工表面质量
一
1、零件的加工质糙度
物理机械参数:强度、硬度、磁性 其它参数:防腐性、平衡性、密封性
可以概括为两方面的含义: 1)宏观几何参数(加工精度) 2)微观几何参数与物理机械性能参数(加工表面质量)
2、加工精度概念的产生: 由于加工时不可能得到准确的参数值,并且从使用要 求方面讲也不需要绝对准确,于是就产生的加工精度的概念。
重载 轻载
思考:
新车为什么要磨合?
2、对疲劳强度的影响:
交变载荷下,零件表面不平的缺陷,最容易产生应力集中, 并可发展为疲劳裂纹,从而导致零件的疲劳破坏。
1)表面粗糙度的影响:表面粗糙度值大,将降低疲劳强度。
2)表面残余应力的影响:表面的残余压应力将抵消部分交变载荷引起的 拉应力,提高了零件的疲劳强度。
冷作硬化的程度与下列因素有关:
1)产生塑性变形的力:力越大,塑性变形越大,硬化程度越 大。 2)变形速度:速度越大,塑性变形越不充分,硬化程度越小。 3)被加工材料:材料硬度越小、塑性越大,硬化程度越大。 4)刀具:刃口圆角和后面磨损增大时,硬化程度增大。 5)切削用量:切削速度越大,硬化程度越小;进给量较大或 较小,会使硬化程度增大。
3、加工精度与加工误差是相关联的,加工精度在数 值上通过加工误差反映出来。
加工精度的概念
1、加工精度:实际加工的点、线、面与理想的几何参 数相符合的程度。 理想的几何参数: 1)尺寸:尺寸的公差带中心 2)形状:绝对准确的圆柱面、平面、锥面等。 3)位置:绝对平行、垂直、同轴 加工精度包括:尺寸精度、形状精度、相互位置精度
3)表面冷作硬化的影响:适当的冷硬能减小交变载荷引起的交变幅值, 阻止疲劳裂纹扩展,提高疲劳强度。
加工精度及表面质量

3)获得尺寸精度的方法 ) ① 定径刀具法: 主要用于孔加工,如铰孔、拉孔等。此 法容易保证加工质量,生产率较高。 ② 试切法: 通过试切—→测量尺寸—→调整刀具的吃刀 量—→走刀切削—→再试切,如此反复直至达到所需 尺寸。此法主要用于单件小批生产。 ③ 调整法: 通过预先调整好机床、夹具、工件和刀具的 相对位置获得所需尺寸。此法生产率高,主要用于大 批大量生产。
2)变形强化的利弊 ) ① 对后续工序的某些加工(如刮削)带来不便; ② 可提高零件表面耐磨性和疲劳强度。
“加工精度及表面质量”部分结束! 请转入:
“生产率 加工精度及表面质量 一、加工精度
1.尺寸精度 . 1)尺寸精度的概念 ) 零件的直径、长度、表面间距离等尺寸的实际数 值与理想数值的接近程度。 2)尺寸公差等级 ) 尺寸精度是用尺寸公差来控制的。国标GB80079至GB1084- 79将确定尺寸精度的标准公差等级分为 20级。分别为IT01,IT0,IT1,…IT18,其中IT01的 公差值最小,尺寸精度最高。
2.形状精度 . 1)形状精度的概念 ) 加工后零件上的线、面的实际形状,与理想形状的符 合程度。 2)形状公差的种类 ) 形状精度用形状公差控制。GB1182- 80至 GB1184- 80规定了六项形状公差,即直线度、平面度、 圆度、圆柱度、线轮廓度和面轮廓度。前4种较为常用。
常用形状公差的名称、符号、 常用形状公差的名称、符号、标注及其说明
常用位置公差的名称、符号、 常用位置公差的名称、符号、标注及其说明
项 目 图 例 说 明 平行度公差为 0.02mm, 实际平面必须位于距离为 0.02mm 且平行于 基准平面 A 的两平行平面之间 平行度
垂直度公差为 0.02mm, 实际端面必须位于距离为 0.02mm 且垂直于 基准轴线 A 的两平行平面之间 垂直度
机械加工精度及表面质量

理论讲授课专业能力:了解与机械零件的加工质量的相关因素;理解加工精度及表面质量的基本概念;掌握机械加工精度及表面质量的影响因素和改善措施。
社会能力:观察能力、分析能力、语言表达能力、逻辑思维能力。
方法能力:注重培养学生学会正确的分析方法,运用学过的理论知识去解决数控实际加工中所遇到的工艺问题。
加工精度及表面质量的基本概念;表面质量对零件使用性能的影响;机械加工精度及表面质量的影响因素和改善的措施。
加工精度及表面质量的基本概念;机械加工精度及表面质量的影响因素和改善措施。
多媒体课件、车间实操视频、多媒体课室、示教简图。
讲授、提问启发、举例分析、比较法、示范法讲练结合、情境教学。
90分钟。
课 题 教学课时 教学教具 教学方法教学难点教学重点 教学目标题 型机械加工精度及表面质量教学流程设计:开 讲教师 学生讲授完毕传授新知、情境教导提出目标、创设情境、引导启发 多谋体课件、视频、简图演示 拟定目标、讨论、思考 回答问题、练习吸收知识、掌握技能师生交流、教与学互动反馈课堂拓展、归纳、总结布置课后任务趣味导学教学内容教学说明[新课引入](讲授时间:5分钟)随着现代机器制造工业的飞速发展,对机器的要求日益提高,一些重要的零件必须在高速、高温、高压和重载条件下工作,表面层的缺陷,不仅直接影响零件的工作性能,而且使零件加速磨损、腐蚀和失效,使用寿命缩短,因而必须重视加工质量的问题。
如飞机,特别是战斗机,其加工质量要求非常严格,要求其在升空之前必须经过严格的检查。
在飞行过程中,只要存在一丝裂纹,都会出现事故。
因为飞机在飞行过程中,空气的对流严重、摩擦剧烈,加剧裂纹扩大,最终引起事故。
所以零件的加工质量问题不容忽视。
那么这两节课我们就来学习有关数控加工中,机械加工精度和表面质量所涉及到的知识。
[新课]一、基本概念加工精度加工质量表面质量1、加工精度(讲授时间:15分钟)(1)含义(符合程度)加工精度零件加工后的几何参数理想零件几何参数(尺寸、几何形状和相互位置)(偏离程度)加工误差大:精度低加工误差小:精度高引导提问:加工误差对加工精度有何影响?学生思考得出结论:加工误差大,加工精度低;加工误差小,加工精度高。
机械加工中的加工精度与表面质量控制

模拟式检测方法:通过模拟被测表面的形貌,如使用计算机模拟、物理模拟等方法, 来获取表面粗糙度信息。
加工过程的质量监控技术
加工精度的检测方法:使用精密 测量仪器,如千分尺、百分表等
表面质量的检测方法:使用表面 粗糙度仪、光学显微镜等
机械加工中的加工精 度与表面质量控制
汇报人:XX
目录
01 添加目录标题 02 机械加工精度与表面质量的概念 03 机械加工精度控制 04 机械加工表面质量控制 05 机械加工精度与表面质量的检测与评价 06 提高机械加工精度与表面质量的措施
添加章节标题
机械加工精度与表面质量的 概念
加工精度与表面质量的定义
和耐腐蚀性
激光处理:利用 激光照射,改变 表面微观结构, 提高硬度和耐磨
性
机械加工精度与表面质量的 检测与评价
加工精度的检测方法
直接测量法:使用测量仪器 直接测量工件的尺寸、形状 和位置误差
间接测量法:通过测量工件 与其他标准件的相对位置关 系来间接测量加工精度
光学测量法:利用光学仪器 测量工件的尺寸和形状误差
发展趋势与未来展望
加工精度不断提高,表面质量控制 技术不断发展
绿色制造、节能环保成为机械加工 发展的重要方向
添加标题
添加标题
添加标题
添加标题
智能化、自动化技术在机械加工中 的应用越来越广泛
复合加工、纳米加工等新兴技术逐 渐兴起,为机械加工带来新的机遇 和挑战
感谢您的观看
汇报人:XX
加工过程的质量监控技术:采用 实时监控系统,如SPC、FMEA 等
质量控制措施:制定严格的工艺 规程,加强员工培训,定期进行 质量检查等
机械加工精度与表面质量优化

机械加工精度与表面质量优化机械加工是一种常见的制造工艺,广泛应用于各个行业,如汽车制造、航空航天、电子设备等。
在这些领域中,机械零件的精度和表面质量是关键因素,直接影响产品的性能和可靠性。
因此,如何优化机械加工精度和表面质量,成为了制造业的重要课题。
在机械加工中,精度指的是加工尺寸与设计要求尺寸之间的差异。
精度越高,加工的零件尺寸越接近设计要求,从而保证产品的功能正常。
而表面质量则是指零件表面的光洁度和光泽度,直接影响到零件的外观和阻尼特性。
因此,精度和表面质量的优化是为了提高产品质量和降低成本的关键所在。
首先,要提高机械加工的精度和表面质量,必须选用合适的加工设备和工艺。
加工设备的性能和精度是决定加工质量的关键因素之一。
例如,在数控机床加工中,要选择高精度的主轴和伺服系统,以保证刀具的定位精度和运动稳定性。
同时,还需要合理选择切削工具,如切削刃角、刀片坚硬度等,以确保切削力的合理分布和刀具寿命的延长。
此外,在加工过程中,还应注意机床的刚度和振动情况,以减小加工误差和表面粗糙度。
其次,要提高机械加工的精度和表面质量,还需要优化加工工艺。
加工工艺包括刀具的选择、切削参数的确定和冷却液的使用等。
刀具的选择应根据加工材料的硬度和加工质量要求来确定。
切削参数的确定要根据加工材料的性质和机床的性能来调整,如进给速度、切削深度和切削速度等。
冷却液的使用对于控制加工温度、减小切削力和排除切屑等方面起到重要作用。
因此,要根据具体情况来优化加工工艺,以提高加工精度和表面质量。
另外,要保证机械加工的精度和表面质量,还需要考虑材料的选用和预处理。
材料的性质直接影响到加工的结果。
例如,金属材料的硬度和塑性会影响到刀具的磨损和切削力的分布,而非金属材料的热膨胀系数和热导率会影响到加工温度的控制。
因此,在进行机械加工前,应根据加工要求来选择合适的材料,并进行必要的预处理,如热处理、表面处理等,以提高加工精度和表面质量。
最后,要提高机械加工的精度和表面质量,还需要进行严格的质量控制和检测。
表面质量与加工精度
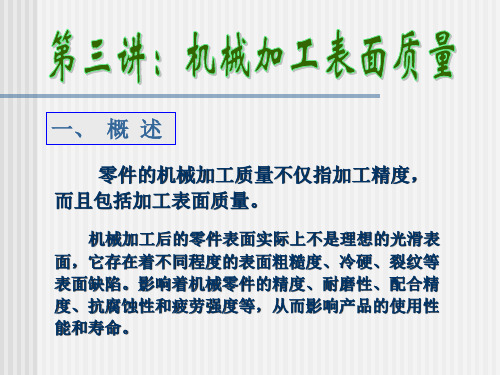
残余压应力能部分抵消工作载荷施加的拉应力,延缓疲劳
裂纹的扩展,从而提高零件的疲劳强度。
3.表面质量对零件工作精度的影响
(1)表面粗糙度对零件配合精度的影响
表面粗糙度较大,则降低了配合精度。
(2)表面残余应力对零件工作精度的影响 表面层有较大的残余应力,就会影响它们精 度的稳定性。
4.表面质量对零件耐腐蚀性能的影响
开槽砂轮
a) 槽均匀分布 b)槽均匀分布
内冷却装置
1-锥形盖 2-通道孔 3-砂轮中心孔 4-有径向小孔的薄壁套
形成压应力的方法
既然压应力可提高疲劳强度,怎样才能使工件表面产生压应力呢? 常用的方法有滚压、喷丸、高频淬火、滲碳、渗氮、氰化等。
滚压:图6-9所示为外圆滚压工具,图a为刚性滚压工具,用于刚性较好的 工件;图b为弹性滚压工具,用于刚性较差的工件。滚压深度一般0.03~ 0.1mm,滚压次数不超过3次。 滚轮可用W18Cr4V、硬质合金等材 料制成。硬度要求HRC60-64以上,也可用滚珠轴承代替。
↑→ Ra↓
砂轮修正
影响磨削加工表面 粗糙度的因素
砂轮硬度
磨削用量
工件材料性质
四、 影响表面层物理力学性能的 主要因素及其控制
影响表面层物理力学性能的主要因素
影响显微硬度因素 塑变引起的冷硬 金相组织变化引起 的硬度变化
表面物理力学性能
影响残余应力因素
冷塑性变形 热塑性变形 金相组织变化
影响金相组织变化 因素
2、 磨削中影响粗糙度的物理因素
磨削速度高,且磨粒大多数是负前角,切削刃又不锐利,磨粒 在磨削过程中对被加工表面挤压,没有切削。加工表面出现沟槽与 隆起,磨削高温加剧了塑性变形。
(1)磨削用量
精度及表面质量
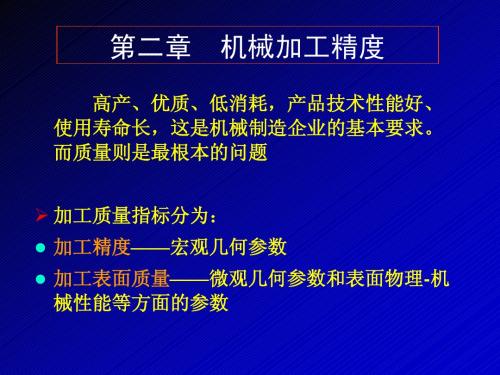
刀具的制造误差
刀具的制造误差对加工精度的影响,根据刀具的种类不同 而不同。定尺寸刀具以刀具尺寸误差为主;成形刀具以刀 具形状误差为主
刀具的磨损:分为三个阶段:初始磨损、正常磨损、
急剧磨损
减少刀具制造误差对加工精度的影响的措施:
提高制造精度 合理选择刀具材料 合理选择切削用量 合理选择刀具几何参数
几种产生内应力的工艺过程
毛坯制造中产生的内应力 铸造、锻造、焊接和热处理过程中,因热胀冷缩不匀以 及金相组织转变 冷校直带来的内应力
切削加工的附加应力 切除金属后,破坏了原有的内应力平衡 高温、高压下,局部表面层因不均匀的塑性变形而产 生内应力
时效中产生的二次应力
时效过程冷却阶段产生的二次残余应力
1.误差的性质
误差分为两类:
系统性误差
当连续加工一批零件时,误差的大小和方向或是保持不 变,或是按一定规律变化。前者称为常值系统性误差, 后者称为变值系统性误差
常值系统性误差有:原理误差,刀具、夹具、量具、机 床的制造误差,调整误差,系统受力变形 变值系统性误差有:工艺系统热变形,刀具、夹具、量 具、机床磨损
到工件尺寸达到规定要求为止
调整法:先调整好刀具和工件在机床上的相对位置,
并在一批零件的加工过程中保持这个位置不变,以保证 工件被加工尺寸
定尺寸刀具法:通过刀具的相应尺寸保证加工表面的
尺寸精度
自动控制法:将测量、进给装置和控制系统组成一个
自动加工系统,通过自动测量和数字控制装置,在达到 尺寸精度后自动停止加工
包括机床本身各部件的制造误差、安装误差和使用过程 中磨损
主轴回转运动误差及其影响因素
- 1、下载文档前请自行甄别文档内容的完整性,平台不提供额外的编辑、内容补充、找答案等附加服务。
- 2、"仅部分预览"的文档,不可在线预览部分如存在完整性等问题,可反馈申请退款(可完整预览的文档不适用该条件!)。
- 3、如文档侵犯您的权益,请联系客服反馈,我们会尽快为您处理(人工客服工作时间:9:00-18:30)。
Z1
1
2
Z2
z1 i12 z2
2 i121
图 车螺纹的传动误差示意图
S-工件导程;T-丝杠导程;Z1~Z8-各齿轮齿数
若齿轮Z1有转角误差δ1,造成Z2的转角误差为: δ12=i12δ1 传到丝杠上的转角误差为δ1n,即: Z1
Z2
δ1
δ2
δ1n=i1nδ1
图4-11 车床导轨扭曲对工件形状精度影响
2、机床主轴回转误差
(1)机床主轴回转误差的概念
主轴的实际回转轴线对其理想回转轴线(一般用平均 回转轴线来代替)产生的偏移量。
主轴回转误差的基本形式
• 轴向窜动 • 纯径向跳动 • 纯角度摆动
实际上主轴回转误差是上述三种形式误差的合成。由于主轴实际 回转轴线在空间的位置是在不断变化的,由上述三种运动所产生的 位移(即误差)是一个瞬时值。
项目三 机械加工精度和表面质量
第一节 机械加工精度概 述
产品的质量与零件的加工质量、产品的装配质 量密切相关,而零件的加工质量是保证产品质量的 基础。它包括零件的加工精度和表面质量两方面。
零件的加工精度包括尺寸精度、形状精度和相
互位置精度。
一、加工精度与加工误差
1.加工精度
加工精度是指零件加工后的实际几何参数(尺寸、 形状及各表面相互位置等参数)与理想几何参数的符合程 度。符合程度越高,加工精度就越高。反之,越低。
采用近似的成形运动和刀具刃形,不但可以简化机床或刀具的结 构,而且能提高生产效率和加工的经济效益。
二、机床几何误差
机床几何误差的来源
机床制造 磨损 安装
①主轴回转误差 ②导轨误差 ③传动链误差
机床几何误差的组成
机床的几何误差组成
机床主轴回转误差 •轴向窜动 •径向跳动 •角度摆动
机床几何误差
理想几何参数
表面——绝对平面、圆柱面等; 位置——绝对平行、垂直、同
尺寸——位于公差带中心。
轴等;
2.加工误差 加工误差是指零件加工后的实际几何参数对 理想几何参数的偏离程度,所以,加工误差的大 小反映了加工精度的高低。
实际加工时不可能也没有必要把零件做得与理想零 件完全一致,而总会有一定的偏差,即加工误差。只要 这些误差在规定的范围内,即能满足机器使用性能的要 求。
4)消除传动链中齿轮副的间隙。
5)采用误差校正机构
图 丝杠加工误差校正装置
1-工件 2-螺母 3-母丝杠 4-杠杆 5-校正尺 6-触头 7-校正曲线
三、工艺系统其它几何误差
一般刀具 定尺寸刀具 1、刀具 误差 成形刀具 展成法刀具
如普通车刀、单刃 镗刀和面铣刀等)的制 造误差对加工精度没有 直接影响,但磨损后对 工件尺寸或形状精度有 一定影响 定尺寸刀具(如钻 头、铰刀、圆孔拉刀等) 的尺寸误差直接影响被 加工工件的尺寸精度。 刀具的安装和使用不当, 也会影响加工精度。
3)夹具在使用过程中工作表面的磨损。(图例)
工件的安装误差包括定位误差和夹紧误差。
图例 钻孔夹具误差对加工精度的影响
(1)量具、量仪和测量方法本身的误差
(2)环境条件的影响(温度、振动等)
3、测量误差
(3)测量人员主观因素的影响(视力、测量 力大小等) (4)正确选择和使用量具,以保证测量精度
试切法调整 定程机构调整 4、 调整误差 样板、样件调整 夹具安装调整
(扭曲)
现以卧式车床为例,说明导轨误差是怎样影响工件 的加工精度的。
(1)导轨在水平面内直线度误差的影响 当导轨在水平面内的直线度误差为△y时,引起工件在 半径方向的误差为(图4-9): △R=△y
由此可见:床身导轨在水平面内如果有直线度误差,使工件 在纵向截面和横向截面内分别产生形状误差和尺寸误差。
•工艺系统的几何误差 •工艺系统受力变形引起的误差 •工艺系统热变形引起的误差 •工件的残余应力引起的误差 •进给系统位移误差等
原始误差是产生加工误差的根源,它包括:
机床几何误差 工艺系统静误差 刀具几何误差 夹具几何误差 工艺系统几何误差 原理误差 调整误差 测量误差
•主轴回转误差 •导轨误差 •传动链误差 •一般刀具 •定尺寸刀具 •成形刀具 •展成法刀具 • 试切法 •调整法
②轴向窜动对车、镗削加工精度的影响
主轴的轴向窜动对内、外圆的加工精度没有 影响,但加工端面时,会使加工的端面与内外圆 轴线产生垂直度误差。 主轴每转一周,要沿轴向窜动一次,使得切 出的端面产生平面度误差(图4-6)。当加工螺纹 时,会产生螺距误差。
图4-6 主轴轴向窜动对端面加工精度的影响
③角度摆动对车、镗削加工精度的影响
•测量误差 •进给机构位移误差(爬 行现象) •加工余量的影响(余量 很小时,刀刃打滑)
大批量生产时常采用 行程挡块、靠模、凸轮 作为定程机构,其制造 精度和调整精度产生调 整误差
影响工件在机床上 占有正确的加工位置
统计分析法
是对具体加工条件下得到的几何 参数进行实际测量,然后运用数理统 计学方法对这些测试数据进行分析处 理,找出工件加工误差的规律和性质, 进而控制加工质量。
• 加工精度
•尺寸精度 •形状精度 •位置精度
• 加工误差 • 工艺系统
•与理想零件的偏离 •加工精度的另一描述
•机床 •刀具 •夹具 •工件 •分析计算法 •统计分析法
图 龙门刨床导轨垂直面 内直线度误差
1-刨刀 2-工件 3-工作台 4-床身导轨
(3)前后导轨平行度误差的影响
床身前后导轨有平行度误差(扭曲) 时,会使车床溜板在沿床身移动时发生 偏斜,从而使刀尖相对工件产生偏移, 使工件产生形状误差(鼓形、鞍形、锥 度)。
从图4-11可知,车床前后导轨扭曲的最终结果 反映在工件上,于是产生了加工误差△y。从几何 关系中可得出: △y≈H△/B 一般车床H≈2B/3,外圆磨床H≈B,因此该项 原始误差△对加工精度的影响很大。
讨论
若镗杆进给,即镗杆既旋转又移动(图示), 导轨误差对加工精度有无影响? 答:不会产生孔的形状误差,但会产生孔的 位置误差。
讨论
刨平面时,导轨误差对加工精度有何影响? 答:产生加工表面的直线度误差、平面度 误差。 若刨削刚性很差的薄板时,会产生何种加 工误差? 答:无形状误差,但有尺寸误线度 •垂直面内直线度 •前后导轨的平行度
机床传动链误差
•内联传动链始末两 端传动元件间相对 运动误差
1、机床导轨误差
机床导轨是机床中确定某些主要部件相对位置的 基准,也是某些主要部件的运动基准。
机床导轨误差的基本形式
•水平面内的直线度 •垂直面内的直线度 •前后导轨的平行度
定位误差
工艺系统力变形
•外力作用点变化 •外力方向变化 •外力大小变化 •机床热变形 •工件热变形 •刀具热变形
工艺系统动误差
工艺系统热变形 工艺系统内应力变形
四、研究机械加工精度的方法
分析计算法
是在掌握各种原始误差对加工精 度影响规律的基础上,分析工件加工 中所出现的误差可能是哪一种或哪几 种主要原始误差所引起的,并找出原 始误差与加工误差之间的影响关系, 通过估算来确定工件加工误差的大小, 再通过试验测试来加以验证。
传动链末端元件产生的转角误差。它的大小 对车、磨、铣螺纹,滚、插、磨(展成法磨齿) 齿轮等加工会影响分度精度,造成加工表面的形 状误差,如螺距精度、齿距精度等。
例如,车螺纹时,要求主轴与传动丝杠的转速比恒定 (图示),即
z1 z3 z5 z7 S T i1i2i3i4T iT z2 z4 z6 z8
δ2n=i2nδ2
………………
δn δnn=innδn
n
Zn
在任一时刻,各齿轮的转角误差反映到丝杠的总误差为:
Σ 1n 2 n nn j i jn
j 1
(3)减少传动链误差的措施
1)尽量缩短传动链。
2)提高传动件的制造和安装精度,尤其是末端 零件的精度。 3)尽可能采用降速运动,且传动比最小的一级 传动件应在最后。
图4-7 主轴纯角度摆动对镗孔精度的影响
(3)提高主轴回转精度的措施
1)提高主轴的轴承精度。
2)减少机床主轴回转误差对加工精度的影响。 3)对滚动轴承进行预紧,以消除间隙。 4)提高主轴箱体支承孔、主轴轴颈和与轴承 相配合的零件有关表面的加工精度。
讨论
镗床上镗孔时,工作台进给(图示),即 工件直线进给运动,镗杆旋转运动。导轨 在水平面、垂直面内的直线度误差对加工 精度有何影响? 答:孔径没有误差,有圆柱度误差。轴线 不直。因为误差敏感方向不断变化。
思考题
端铣时,若主轴回转轴线与工件进给方向 不垂直,会产生何种加工误差?误差大小?
3、机床传动链误差
在车螺纹、插齿、滚齿等加工时,刀具与工件之 间有严格的传动比要求。要满足这一要求,机床内联 系传动链的误差必须控制在允许的范围内。 (1)机床传动链误差定义
(2)机床传动链误差描述
指传动链始末两端 执行元件间相对运动的误 差。
• 原始误差
• 研究加工精度方法
•工艺系统的误差 •产生加工误差的根源 •包括工艺系统静误差、动误差
第二节 影响加工精度的因素
一、原理误差
原理误差是指由于采用了近似的加工方法、近似的成 形运动或近似的刀具轮廓而产生的误差。
例如滚齿用的齿轮滚刀,就有两种误差,一是为了制造方便,采 用阿基米德蜗杆代替渐开线基本蜗杆而产生的刀刃齿廓近似造形误差; 二是由于滚刀切削刃数有限,切削是不连续的,因而滚切出的齿轮齿 形不是光滑的渐开线,而是折线。 成形车刀、成形铣刀也采用了近似的刀具轮廓。
△ R ≈△Z2/d =0.000001mm
此值完全可以忽略不计。由于△Z2数值很小,因此该误差对 工件的尺寸精度和形状精度影响甚小。