带电流截至负反馈的直流调速系统
运动控制_第3章____转速、电流双闭环直流调速系统

U
*
im
,转速外环呈开环状态,
转速的变化对系统不再产生影响。在这种情况下,电流负反
馈环起恒流调节作用,转速线性上升,从而获得极好的下垂
特性,如图 3-5中的AB段虚线所示。
第二十一页,编辑于星期三:九点 二十二分。
第 3章 转速、电流双闭环直流调速系统
此时,电流
I
d
U* im ?
?
I dm
,Idm 为最大电流,是由设
差调节。
第二十页,编辑于星期三:九点 二十二分。
第 3章 转速、电流双闭环直流调速系统
1) 转速调节器饱和
在电动机刚开始起动时,突加阶跃给定信号 U*n,由于
机械惯性,转速 n很小,转速负反馈信号 Un很小,则转速偏
差电压 ΔUn=U*n-Un>0很大,转速调节器 ASR 很快达到饱和
状态, ASR的输出维持在限幅值
图 3-5 双闭环直流调速系统的静特性
第二十三页,编辑于星期三:九点 二十二分。
第3章 转速、电流双闭环直流调速系统
2) 转速调节器不饱和
当转速n达到给定值且略有超调时 (即n>n0),ΔUn=
U*n-Un<0,则转速调节器 ASR的输入信号极性发生改变,
ASR 退出饱和状态,转速负反馈环节开始起转速调节作用,
用以调节起动电流并使之保持最大值,使得转速线性变化, 迅速上升到给定值; 在电动机稳定运行时,转速调节器退 出饱和状态,开始起主要调节作用,使转速随着转速给定信 号的变化而变化,电流环跟随转速环调节电动机的电枢电流 以平衡负载电流。
第六页,编辑于星期三:九点 二十二分。
第 3章 转速、电流双闭环直流调速系统
器ACR和转速调节器 ASR的输入电压偏差一定为零,因此,
直流电动机有哪几种调速方法各有哪些特点答:直流电动机有三种

直流电动机有哪几种调速方法?各有哪些特点?答:直流电动机有三种调速方法:1)调节电枢供电电压U ;2)减弱励磁磁通Φ;3)改变电枢回路电阻R 。
特点:对于要求在一定范围内无极平滑调速的系统来说,以调节电枢供电电压的方式为最好。
改变电阻只能有级调速;减弱磁通虽然能够平滑调速,但调速范围不大,往往只是配合调压方案,在基速(额定转速)以上作小范围的弱磁升速。
晶闸管—电动机系统当电流断续时机械特性的显著特点是什么?答:电流断续时的电压、电流波形图(Ⅰ10P 、Ⅱ 12P )(三相零式为例)。
断续时,0d u 波形本身与反电势E 有关,因而就与转速n 有关,而不是像电流连续时那样只由控制角α决定的常值。
机械特性呈严重的非线性,有两个显著的特点:第一个特点是当电流略有增加时,电动机的转速会下降很多,即机械特性变软。
当晶闸管导通时,整流电压波形与相电压完全一致,是电源正弦电压的一部分。
当电流断续后,晶闸管都不导通,负载端的电压波形就是反电势波形。
电流波形是一串脉冲波,其间距为︒120,脉冲电流的底部很窄。
由于整流电流平均值d I 与电流波形包围的面积成正比,如果电流波形的底部很窄,为了产生一定的d I ,各相电流峰值必须加大,因为RE u i d d -=,而整流输出的瞬时电压d u 的大小由交流电源决定,不能改变。
也就是说应使E 下降很多即转速下降很多,才能产生一定的d I ,这就是电流断续时机械特性变软的原因。
第二个特点是理想空载转速0n 升高。
因为理想空载时0=d I ,所以2m a x 02U u E d ==,所以0n 升高。
简述直流PWM 变换器电路的基本结构。
答:直流 PWM 变换器基本结构如图所示,包括 IGBT 和续流二极管。
三相交流电经过整流滤波后送往直流 PWM 变换器,通过改变直流 PWM 变换器中 IGBT 的控制脉冲占空比来调节直流 PWM 变换器输出电压大小,二极管起续流作用。
Ug0Ton T t 直流PWM 变换器基本结构直流PWM 变换器输出电压的特征是什么?答:频率一定、宽度可调的脉动直流电压。
带电流截至负反馈的直流调速系统
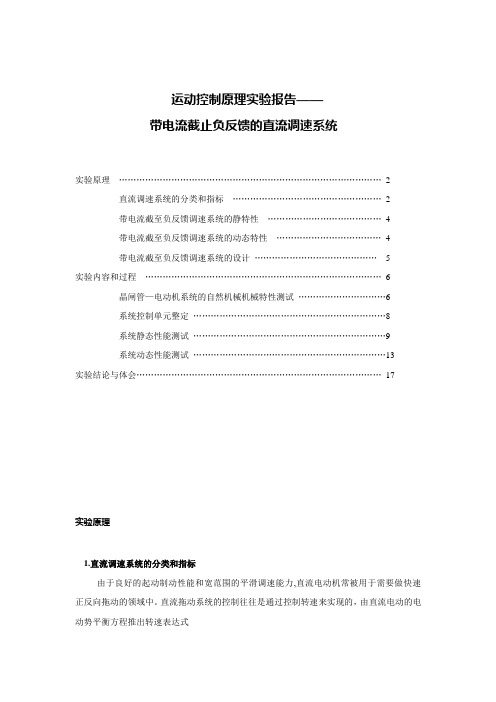
运动控制原理实验报告——带电流截止负反馈的直流调速系统实验原理 (2)直流调速系统的分类和指标 (2)带电流截至负反馈调速系统的静特性 (4)带电流截至负反馈调速系统的动态特性 (4)带电流截至负反馈调速系统的设计 (5)实验内容和过程 (6)晶闸管—电动机系统的自然机械机械特性测试 (6)系统控制单元整定 (8)系统静态性能测试 (9)系统动态性能测试 (13)实验结论与体会 (17)实验原理1.直流调速系统的分类和指标由于良好的起动制动性能和宽范围的平滑调速能力,直流电动机常被用于需要做快速正反向拖动的领域中。
直流拖动系统的控制往往是通过控制转速来实现的,由直流电动的电动势平衡方程推出转速表达式φe adl d C R I U n -=U 为电枢电压 ,dl I 为一定负载对应的电流,a R 为电枢回路总电压 φ电枢励磁磁通 e C 电机的电动势参数可知直流电机有三种可用的调速方法,分别是调压(U )调速,弱磁(φ)调速和改变串入电阻(aR )调速。
然而通过改变串入电阻阻值来调速不能实现无级调速,弱磁调速的调速范围又太小,所以直流调速系统常采用调压调速的方式。
对于一个建立好的直流调速系统,可以从调速范围(D ),干扰造成的转速波动大小(静差率s )和调速系统的起动和制动时间这三个方面来衡量,这些参数有如下关系,min max n n D =N Nn n n s ∆+∆=min其中Nn ∆为直流电机的转速降落,是在电机负载从理想空载增加到额定值对应的转速降落,可以作为衡量直流电机机械特性硬度的参量.调速范围和静差率两个概念也有密切的联系,同样的转速降落Nn ∆下,调速范围越大,转速越低对应的静差率也会大一些,两者满足)1(D n n D s N N+∆=而真正衡量不同系统机械特性时我们用的是转速最低时的静差率,这是的静差率最难满足系统的性能指标。
本次实验使用的是晶闸管整流器—电动机调速系统的组合(M V -),同样广泛使用的还有PWM —电动机的组合。
带电流截止负反馈转速单闭环直流调速系统建模与仿真
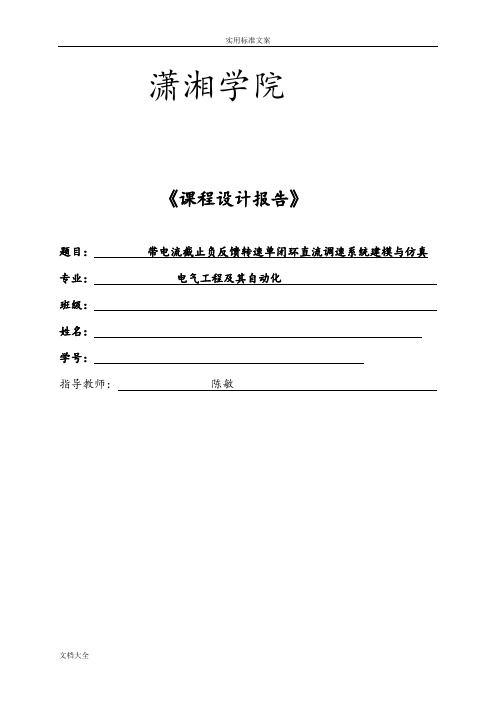
潇湘学院《课程设计报告》题目:带电流截止负反馈转速单闭环直流调速系统建模与仿真专业:电气工程及其自动化班级:姓名:学号:指导教师:陈敏初始条件:1.技术数据输出功率为:7.5Kw 电枢额定电压220V电枢额定电流 36A 额定励磁电流2A额定励磁电压110V 功率因数0.85电枢电阻0.2欧姆电枢回路电感100mH电机机电时间常数2S电枢允许过载系数1.5额定转速 1430rpm2.技术指标稳态指标:无静差(静差率s≤2%, 调速范围 D≥10 )动态指标:系统稳定要求完成的主要任务:1.技术要求:(1) 该调速系统能进行平滑的速度调节,负载电机不可逆运行,具有较宽的调速范围(D ≥10),系统在工作范围内能稳定工作(2) 根据指标要求进行动态校正,选择调节器的参数,并确定电流截止负反馈环节的相关参数,(3) 系统在5%负载以上变化的运行范围内电流连续2.设计内容:(1) 根据题目的技术要求,分析论证并确定主电路的结构型式和闭环调速系统的组成,画出系统组成的原理框图(2) 根据带电流截止负反馈转速单闭环直流调速系统原理图, 分析转速调节器和电流截止负反馈的作用,(3) 通过对调节器参数设计, 得到转速和电流的仿真波形,并由仿真波形通过MATLAB 来进行调节器的参数调节。
(4) 绘制带电流截止负反馈转速单闭环直流调速系统的电气原理总图(要求计算机绘图)(5) 整理设计数据资料,课程设计总结,撰写设计计算说明书目录摘要 (3)1.闭环调速控制系统构成 (5)1.1 主电路 (5)1.2 原理框图 (5)2带电流截止负反馈的转速负反馈的分析 (6)2.1电流截止负反馈的提出 (6)2.2 电流截止负反馈环节 (7)2.3 带电流截止负反馈调速系统结构框图和静特性 (8)3 参数设计 (10)3.1整体分析 (10)3.2稳定性参数计算和判断 (10)3.3 转速调节器校正 (11)3.3.1 PI调节器结构 (11)3.3.2 调节器的选择 (12)3.4 电流截止负反馈参数设计 (16)4. 电流MATLAB仿真 (17)4.1 将设计的参数进行仿真 (17)4.2 调节器参数调整 (18)5.电气总图 (19)6.结束语 (20)参考文献 (20)摘要为了提高直流调速系统的动态、静态性能,通常采用闭环控制系统(主要包括单闭环、双闭环)。
带电流截止负反馈的转速单闭环可逆调速系统设计心得

带电流截止负反馈的转速单闭环可逆调速系统设计心得在设计带有电流截止负反馈的转速单闭环可逆调速系统时,我获得了一些有价值的心得。
这种系统通常用于电机控制,通过闭环反馈来实现对电机转速的精确控制。
首先,设计一个合适的电流截止负反馈环路非常重要。
电流截止是一种常用的控制策略,通过将电流与设定值进行比较,然后根据比较结果调整控制信号来实现对转速的控制。
在设计负反馈环路时,需要注意选择合适的比例和积分增益来实现稳定的控制。
其次,选择合适的转速控制策略也是至关重要的。
常见的转速控制策略包括PID 控制、模糊控制和神经网络控制等。
根据实际需求和系统特点,选择最适合的控制策略能够提高系统的控制性能和稳定性。
此外,设计合适的传感器和测量电路也是设计可逆调速系统的重要一环。
转速传感器的准确性对于精确控制转速至关重要。
在选择传感器时,需要考虑其测量范围、精度和响应速度等因素。
最后,合理设计控制回路,并对系统进行充分的仿真和实验。
通过仿真和实验可以验证设计的合理性和系统的性能。
在仿真和实验中,可以对系统进行各种工况的测试,以确保系统在各种条件下都能稳定工作。
总结起来,设计带有电流截止负反馈的转速单闭环可逆调速系统需要考虑多个因素,包括负反馈环路设计、转速控制策略选择、传感器选择和系统仿真与实验。
通过综合考虑这些因素,可以设计出高性能和稳定的转速控制系统。
带电流截止负反馈单闭环直流调速系统

前言电动机作为一种有利工具,在日常生活中得到了广泛的应用。
而直流电动机具有很好的启动,制动性能,所以在一些可控电力拖动场所大部分都采用直流电动机。
而在直流电动机中,带电压截止负反馈直流调速系统应用也最为广泛,其广泛应用于轧钢机、冶金、印刷、金属切割机床等很多领域的自动控制。
他通常采用三相全桥整流电路对电机进行供电,从而控制电动机的转速,传统的控制系统采用模拟元件,比如:晶闸管、各种线性运算电路的等。
虽在一定程度上满足了生产要求,但是元件容易老化和在使用中易受外界干扰影响,并且线路复杂,通用性差,控制效果受到器件性能、温度等因素的影响,从而致使系统的运行特征也随着变化,所以系统的可靠性及准确性得不到保证,甚至出现事故。
直流调速系统是由功率晶闸管、移相控制电路、转速电路、双闭环调速系统电路、积分电路、电流反馈电路、以及缺相和过流保护电路。
通常指人为的或自动的改变电动机的转速,以满足工作机械的要求。
机械特性上通过改变电动机的参数或外加电压等方法来改变电动机的机械特性,从而改变电动机的机械特性和工作特性的机械特性的交点,使电动机的稳定运转速度发生变化由于本人和能力有限,错误或不当之处再所难免,期望批评和指正第1章主电路选型和闭环系统的组成1.1 V—M系统简介晶闸管—电动机调速系统(简称V—M系统),其简单原理图如图1。
图中VT是晶闸管的可控整流器,它可以是单相、三相或更多相数,半波、全波、半控、全控等类型。
优点:通过调节触发装置GT的控制电压来移动触发脉冲的相位,即可改变整流电压从而实现平滑调速。
缺点:1.由于晶闸管的单向导电性,它不允许电流反向,给系统的可逆运行造成困难。
2.元件对过电压、过电流以及过高的du/dt和di/dt都十分敏感,其中任一指标超过允许值都可能在很短时间内损坏元件。
因此必须有可靠的保护装置和符合要求的散热条件,而且在选择元件时还应有足够的余量。
图1.1 V—M系统1.2主电路的确定虽然三相半波可控整流电路使用的晶闸管个数只是三相全控桥整流电路的一半,但它的性能不及三相全控桥整流电路。
带电流截止负反馈的转速单闭环直流调速系统

实验八带电流截止负反馈的转速单闭环直流调速系统一、实验目的(1)了解单闭环直流调速系统的原理、组成及各主要单元部件的原理。
(2)掌握晶闸管直流调速系统的一般调试方法及电流截止负反馈的整定。
(3)通过实验,加深理解负反馈原理及转速负反馈电流截止负反馈的在调速系统中的作用。
二、实验所需挂件及附件三、实验线路及原理为了提高直流调速系统的动静态性能指标,通常采用闭环控制系统(包括单闭环系统和多闭环系统)。
对调速指标要求不高的场合,采用单闭环系统,而对调速指标较高的则采用多闭环系统。
按反馈的方式不同可分为转速反馈,电流反馈,电压反馈等。
在单闭环系统中,转速单闭环使用较多。
在本装置中,转速单闭环实验是将反映转速变化的电压信号作为反馈信号,经“速度变换”后接到“速度调节器”的输入端,与“给定”的电压相比较经放大后,得到移相控制电压U Ct,用作控制整流桥的“触发电路”,触发脉冲经功放后加到晶闸管的门极和阴极之间,以改变“三相全控整流”的输出电压,这就构成了速度负反馈闭环系统。
电机的转速随给定电压变化,电机最高转速由速度调节器的输出限幅所决定,速度调节器采用P(比例)调节对阶跃输入有稳态误差,要想消除上述误差,则需将调节器换成PI(比例积分)调节。
这时当“给定”恒定时,闭环系统对速度变化起到了抑制作用,当电机负载或电源电压波动时,电机的转速能稳定在一定的范围内变化。
在电流单闭环中,将反映电流变化的电流互感器输出电压信号作为反馈信号加到“电流调节器”的输入端,与“给定”的电压相比较,经放大后,得到移相控制电压U Ct,控制整流桥的“触发电路”,改变“三相全控整流”的电压输出,从而构成了电流负反馈闭环系统。
电机的最高转速也由电流调节器的输出限幅所决定。
同样,电流调节器若采用P(比例)调节,对阶跃输入有稳态误差,要消除该误差将调节器换成PI(比例积分)调节。
当“给定”恒定时,闭环系统对电枢电流变化起到了抑制作用,当电机负载或电源电压波动时,电机的电枢电流能稳定在一定的范围内变化。
带电流截至负反馈的转速单闭环直流调速系统概要

带电流截至负反馈的转速单闭环直流调速系统概要概述直流调速系统是现代工业中常见的一种控制系统,其主要作用是通过控制电机的转速来调节其输出的功率。
转速单闭环直流调速系统是其中一种常见的控制系统,它采用了带电流截至负反馈的技术,可以有效地提高系统的稳定性和响应速度。
系统结构转速单闭环直流调速系统主要由三部分组成:电机控制电路、转速测量电路和控制器。
其中电机控制电路用于控制电机的转速,转速测量电路用于测量电机的转速,控制器用于计算误差并发送控制信号到电机控制电路。
具体来说,电机控制电路包括电源、电机以及功率调节器等组件。
电源提供电流给电机,功率调节器则可以控制电流的大小和方向,从而实现对电机转速的控制。
转速测量电路主要用于测量电机的转速,它通常包括一些传感器和信号处理电路。
传感器可以检测电机转子的位置,信号处理电路则将传感器输出的信号转换为脉冲信号,供控制器使用。
控制器是这个系统的核心部件,它负责计算误差并发送控制信号到电机控制电路。
具体来说,控制器可以将目标转速和实际转速之间的差值作为误差,通过算法计算出电机电流的大小和方向,从而实现对电机转速的控制。
技术应用转速单闭环直流调速系统广泛应用于各种需要精确控制电机转速的场合,比如机床、风扇、电动机车、水泵等等。
用转速单闭环直流调速系统可以实现对电机的精确的控制,提高设备的工作效率和稳定性。
此外,带电流截至负反馈的技术也可以应用于其他类型的控制系统中,比如温度控制系统、光照控制系统等等。
它的优点是可以提高系统的稳定性和响应速度,从而提高设备的性能和可靠性。
转速单闭环直流调速系统是一种常见的控制系统,它采用了带电流截至负反馈的技术,可以实现对电机转速的精确控制。
该系统结构简单,应用广泛,可用于机床、风扇、电动机车、水泵等设备的控制。
此外,该技术也可以应用于其他类型的控制系统中,提高设备的性能和可靠性。
带电流截止负反馈的转速单闭环直流调速系统设计与仿真运动控制实验报告

带电流截止负反馈的转速单闭环直流调速系统设计与仿真 一、设计要求系统稳定并无静差 二、给定参数17,220,3000/min N N N P kw U V n r ===,I N =87.3A ,电枢回路电阻0.087a R =Ω,电感0.0032a L H =,励磁回路电阻181.5Ω,电动机的转动惯量20.76.J Kg m =三、闭环直流调速系统稳态参数的计算 1)额定负载时的稳态速降应为:m i n/12.6min /)02.01(1002.03000)1(r r s D s n n N cl =-⨯⨯≤-=∆2)闭环系统应有的开环放大系数:计算电动机的电动势系数: r V r V n R I U C N a N N e min/071.0min/3000087.03.87220⋅=⋅⨯-=-=闭环系统额定速降为:min /97.106min /071.0087.03.87r r C R I n e N op =⨯==∆闭环系统的开环放大系数为:5.16112.697.1061=-≥-∆∆=clop n n K003.0/max max n ==n U α3)计算运算放大器的放大系数和参数 运算放大器放大系数K p 为:5.16/e p ≥=s K KC K α电枢回路的总电感为0.0032H电磁时间常数为037.0/l ==R L T 27/1l ==τK4)电流截止负反馈 四加电网扰动(第8s电压220→240)负载扰动给定值扰动五、将PI调节器参数改变1.电网扰动(第8s电压220→240)2.负载扰动3.给定值扰动转速、电流双闭环直流调速系统设计与仿真一、设计要求系统稳定并无静差 二、给定参数17,220,3000/min N N N P kw U V n r ===,I N =87.3A ,电枢回路电阻0.087a R =Ω,电感0.0032a L H =,励磁回路电阻181.5Ω,电动机的转动惯量20.76.J Kg m =三、电流调节器ACR 参数计算允许电流过载倍数λ=2;设调节器输入输出电压im nm **U U ==10V ,电力电子开关频率为f=l kHz .首先计算电流反馈系数β和转速反馈系数α:06.0 I n im *==ββλU N U n nm *α= α=0.003s T 001.0s = ,电流环小时间常数为s T T T oi 002.0s i =+=∑电流调节器超前时间常数为s T K l i 015.0/1i ===τ 而对电流环开环增益局l K =250/5.0=∑i T ,于是ACR 的比例系数为:94.4/i l i ==s K R K K βτ 四、转速调节器ASR 参数计算 选中频段宽度h=5。
单闭环直流调速系统

第十七单元 晶闸管直流调速系统第二节单闭环直流调速系统一.转速负反馈宜流调速系统转速负反馈直流调速系统的原理如图17-40所示。
转速负反馈直流调速系统由转速给左、转速调节器ASR 、触发器CF 、晶闸管变流器U 、 测速发电机TG 等组成。
直流测速发电机输出电压与电动机转速成正比。
经分圧器分圧取出与转速n 成正 比的转速反馈电压Ufn 0转速给定电压Ugn 与Ufn 比较,其偏差电压A U=Ugn-Ufn 送转速调节器ASR 输入 端。
ASR 输出电圧作为触发器移相控制电压Uc,从而控制晶闸管变流器输出电压Udo 本闭环调速系统只有一个转速反馈环,故称为单闭环调速系统.1. 转速负反馈调速系统工作原理及其静特性设系统在负载T L 时,电动机以给定转速nl 稳定运行,此时电枢电流为Idl,对应 转速反馈电圧为Ufnl,晶闸管变流器输出电压为Udi 。
当电动机负载T L 增加时,电枢电流Id 也增加,电枢回路压降增加,电动机转速下 降,则Ufn 也相应下降, 而转速给定电压Ugn 不变,A U=Ugn-Ufn 加。
转速调节器ASR 输出电压Uc 增加,使控制角a 减小,晶闸管整流装置输出电压Ud 增加,于是电动机转速便相应自动回升,其调节过程可简述为:T L t — Id t — ld (R 》+Rd ) t I -*Ufn I U t — Uc t -* a | —Ud t -*n t 。
图17-41所示为闭坏系统静特性和开环机械特性的关系。
n亠 =H o + A//图17—41闭环系统静特性和开环机械特性的关系.图中①②③④曲线是不同Ud之下的开环机械特性。
假设当负载电流为Idl时,电动机运行在曲线①机械特性的A点上。
当负载电流增加为Id2时,在开环系统中由于Ugn不变,晶闸管变流器输出电压Ud 也不会变,但由丁•电枢电流Id增加,电枢回路压降增加,电动机转速将由A点沿着曲线①机械特性下降至&点,转速只能相应下降。
直流调速控制系统的分析及仿真
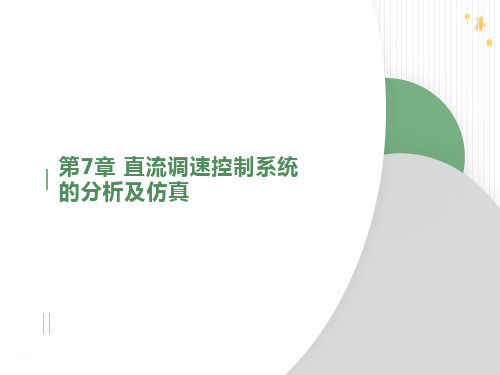
当电流负反馈环节起主导作用时的自动调节过程如图7-1-8所示。
7.1.4系统的性能分析
代入图7-1-5中,由图可见,它是一个二阶系统,已知 二阶系统总是稳定的。但若考虑到晶闸管有延迟,晶 闸管整流装置的传递函数便为
相反。
5.电流截止负反馈环节
当 时,(亦即 ),则二极管VD截止,电流截止负反馈不起作用。当 时,(亦即 ),则二极管VD导通, [此处略去二极管的死区电压],电流截止负反馈环节起作用,它将使整流输出电压 下降,使整流电流下降到允许最大电流。 的数值称为截止电流,以 表示。调节电位器RP3即可整定 ,亦即整定 的数值。一般取 〔 为额定电流〕。 由于电流截止负反馈环节在正常工作状况下不起作用,所以系统框图上可以省去。
在图7-1-1中,主电路中串联了一个阻值很小的取样电阻
(零点几欧)。电阻
上的电压
与
成正比。比 较阈值电压
是由一个辅助电源经电位器RP3提供的。电 流反馈信号(
图7-1-7调速系统的“挖土机”机械特性
当电流负反馈环节起主导作用时的自动调节过程如图7-1-8所示。 机械特性很陡下垂还意味着,堵转时(或起动时)电流不是很大。 这是因为在堵转时,虽然转速n=0,反电动势E=0,但由于电流 截止负反馈的作用,使
大大下降,从而
不致过大。此时 电流称为堵转电流
⑥ 晶闸管整流电路的调节特性为输出的 平均电压
与触发电路的控制电压
之间的关系,即
图7-1-4为晶闸管整流装置的调节特性。
由图可见,它既有死区,又会饱和。 (当全导通以后,
再增加, 也不会再 上升了),且低压段还有弯曲段。面对 这非线性特性,常用的办法是讲它“看 作”一条直线,即处理成
为
带电流截止负反馈环节的单闭环直流调速系统设计

带电流截止负反馈环节的单闭环直流调速系统设计1设计目的(1)了解带电流截止负反馈的转速单闭环直流调速系统的工作原理,熟悉组成环节及每个环节的作用。
(2)应用所学的交、直流调速系统的基本知识与工程设计方法,结合生产实际,确定系统的性能指标与实现方案,进行运动控制系统的初步设计。
(3)应用计算机仿真技术,通过在MATLAB软件上建立运动控制系统的数学模型,对控制系统进行性能仿真研究,掌握系统参数对系统性能的影响。
2设计参数采用晶闸管三相桥式全控整流电路供电,基本数据如下:直流电动机UN=220V, IN=65A,nN =1000r/min,电枢电阻Ra=0.15Ω,电枢电感La=0.0002H,励磁电压Uf=220V,励磁电流If=1.5A,电枢绕组和励磁绕组互感Laf=0.82H,供电电源电压U2=130V;晶闸管装置Ts=0.00167s,放大系数Ks=40;电枢回路总电阻R=0.5Ω;电枢回路总电感L=15mH;电动机轴上的总飞轮惯量GD2=12.5N·m2;转速调节器最大给定值*nmU=10V;3 设计任务(1)分析电流截止负反馈环节的工作原理,画出系统稳态结构图;(2)在MATLAB中建立带电流截止负反馈环节的单闭环直流调速系统;(3调节控制器参数,确定最佳调节参数。
将Simulink仿真模型,以及启动过程中的电流、转速波形图附在设计说明书中。
比较带电流截止负反馈环节和不带电流截止负反馈环节启动过程的差异。
4设计要求1.稳态指标:转速无静差;2.动态指标:启动电流的最大值150 A。
空载启动到额定转速的转速超调量σn≤15%。
4 设计基本内容4.1问题的提出在转速反馈控制直流调速系统中存在一个问题,在启动、制动过程和堵转状态时,电枢电流会过大。
为了解决反馈闭环调速系统的起动和堵转时电流过大的问题,系统中必须有自动限制电枢电流的环节。
引入电流负反馈,可以使它不超过允许值。
但这种作用只应在起动和堵转时存在,在正常的稳速运行时又得取消,让电流随着负载的增减而变化。
转速电流反馈控制的直流调速系统课件

IdL
0
t1
转速电流反馈控制的直流调速系统
t2 t3 t4 课件t
在A快于St上负=R0和升载时A,转,C在矩R系,两 Id统上转个突升速P加I到调为阶I节d零l跃之器。给前的定,作信电用号动下U机,n*转,Id矩在很小
当性作Id用≥ I,dL 后转,速电不机会开很始快起增动长,,由AS于R输机入电偏惯 差电压仍较大, ASR很快进入饱和状态, 而U*AimC。R一般不饱和。直到Id = Idm , Ui =
转速电流反馈控制的直流调速系统 课件
图3-8 典型的阶跃响应过程和跟随性能指标
超调量σ
Cm ax C 100%
C
上升时间
峰值转时速间电流反馈控课制件的直调流调节速系时统间
2.抗扰性能指标
当调速系统在稳定运行中,突加一个使输 出量降低(或上升)的扰动量F之后,输出 量由降低(或上升)到恢复到稳态值的过 渡过程就是一个抗扰过程。
个阶段, 转速调节器在此三个阶段中经历了不饱和、饱和
以及退饱和三种情况。
转速电流反馈控制的直流调速系统 课件
转速电流反馈控制的直流调速系统 课件
图3-6 双闭环 直流调速系统 起动过程的转 速和电流波形
第Ⅰ阶段:电流上升阶段(0~t1)
n
Ⅰ n*
Ⅱ
Ⅲ
电流从0到达最
。
大允许值 I dm
0
t
Id Idm
3.1.2 稳态结构图与参数计算
图3-2 转速、电流反馈控制直流调速系统原理图 ASR——转速调节器 ACR——电流调节器 T转G速—电流—反馈测控课速制件的发直流电调速机系统
1. 稳态结构图和静特性
转速调节器ASR的输出限幅电压决定了电流给定 的最大值,电流调节器ACR的输出限幅电压限制 了电力电子变换器的最大输出电压,
(完整word版)带电流截止负反馈转速单闭环直流调速系统设计..

目录摘要 (2)1主电路的设计 (2)1.1变压器参数的设计与计算 (2)1.2平波电抗器参数的设计与计算 (3)1.3晶闸管元件参数的计算 (4)1.4保护电路的设计 (4)2反馈调速及控制系统 (5)2.1闭环调速控制系统 (5)2.2带电流截止负反馈闭环控制系统 (5)2.3调节器设定 (9)2.4控制及驱动电路设计 (10)3参数计算 (11)3.1基本参数计算 (11)3.2电流截止负反馈环节参数计算与设计 (13)3.3调节器的参数设计与计算 (14)3.4调节器串联校正设计 (17)4总电气图 (18)5心得体会 (20)参考资料 (20)带电流截止负反馈转速单闭环直流调速系统设计摘要直流电动机具有良好的起、制动性能,宜于在大范围内平滑调速,并且直流调速系统在理论和实践上都比较成熟,是研究其它调速系统的基础。
在直流电动机中,带电流截止负反馈直流调速系统应用也最为广泛,其广泛应用于轧钢机、冶金、印刷、金属切割机床等很多领域的自动控制。
本次课设就带电流截止负反馈转速单闭环直流调速系统进行参数的设计。
1主电路的设计1.1变压器参数的设计与计算变压器副边电压采用如下公式进行计算: ⎪⎪⎭⎫ ⎝⎛-+=N sh Td I I CU A nU U U 2min max cos αβVU C I I U A n V U V U Nsh T d 110)105.05.09848.0(9.034.2122205.0105.0109.034.221,220222min max =⨯⨯-⨯⨯+==========则取已知αβ因此变压器的变比近似为:45.311038021===U U K 一次侧和二次侧电流I 1和I 2的计算 I 1=1.05×287×0.861/3.45=75A I 2=0.861×287=247A 变压器容量的计算S 1=m 1U 1I 1=3×380×75=85.5kVA S 2=m 2U 2I 2=3×110×247=81.5kVAS=0.5×(S 1+S 2)=0.5×(85.5+81.5)=83.5kVA因此整流变压器的参数为:变比K=3.45,容量S=83.5kVA1.2平波电抗器参数的设计与计算U d =2.34U 2cos αU d =U N =220V, 取α=0° U 2=V U d 0171.9434.22200cos 34.2==I dmin =(5%-10%)I N ,这里取10% 则 L=0.693mH I U d 2308.375.171.00171.94693.0min 2=⨯⨯=⨯0067.0150010*===N nm n U α1.3晶闸管元件参数的计算晶闸管的额定电压通常选取断态重复峰值电压U DRM和反向重复峰值电压U RRM中较小的标值作为该器件的额定电压。
直流电动机转速负反馈调速系统工作原理分析
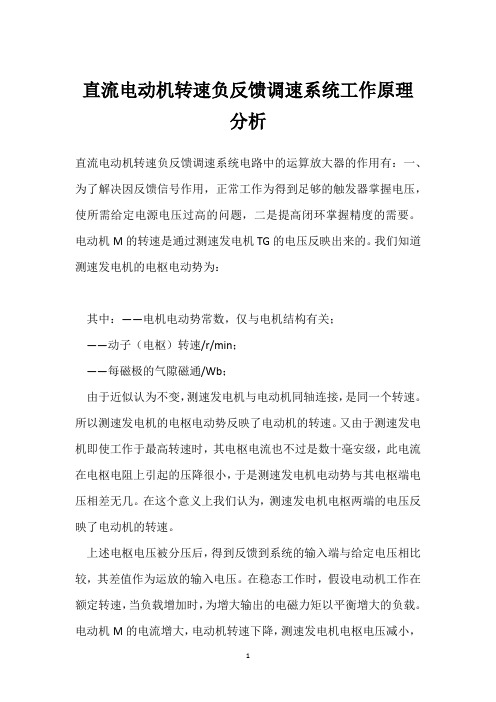
直流电动机转速负反馈调速系统工作原理
分析
直流电动机转速负反馈调速系统电路中的运算放大器的作用有:一、为了解决因反馈信号作用,正常工作为得到足够的触发器掌握电压,使所需给定电源电压过高的问题,二是提高闭环掌握精度的需要。
电动机M的转速是通过测速发电机TG的电压反映出来的。
我们知道测速发电机的电枢电动势为:
其中:——电机电动势常数,仅与电机结构有关;
——动子(电枢)转速/r/min;
——每磁极的气隙磁通/Wb;
由于近似认为不变,测速发电机与电动机同轴连接,是同一个转速。
所以测速发电机的电枢电动势反映了电动机的转速。
又由于测速发电机即使工作于最高转速时,其电枢电流也不过是数十毫安级,此电流在电枢电阻上引起的压降很小,于是测速发电机电动势与其电枢端电压相差无几。
在这个意义上我们认为,测速发电机电枢两端的电压反映了电动机的转速。
上述电枢电压被分压后,得到反馈到系统的输入端与给定电压相比较,其差值作为运放的输入电压。
在稳态工作时,假设电动机工作在额定转速,当负载增加时,为增大输出的电磁力矩以平衡增大的负载。
电动机M的电流增大,电动机转速下降,测速发电机电枢电压减小,
按分压关系成比例减小,由于速度给定电压没有转变,所以增大,它使晶闸管整流电压增加,电动机转速回升到接近原来的额定转速值。
其过程可示意为:
同理当负载下降时,转速上升,其调整过程可示意为:
可见,当转速下降,调整的结果使回升到接近原来的值;当转速上升时,调整的结果使下降到接近原来的值。
这就形成了速度负反馈闭环系统,被控量也参与了掌握作用,掌握形成闭环。
转速电流双闭环直流调速系统的组成及其静特性ppt课件.ppt

稳态时 :两个调节器均不饱和(输入偏差为零,偏差的积分使调节器
有恒定的电压输出,输出没有达到饱和值)
n
U
* n
n0
U n * U n n n 0 ,
ASR饱和时 : U*i = U*im,
Id
Ui*m
Idm
反馈系数:
U
* nm
n max
U
* im
I dm
U i * U iI dL
• 双环系统PI调节器的特点:
ASR饱和(AB段):当负载电流达到Idm时,对应于转速调节 器的饱和输出Uim*,这时,电流调节器起主要调节作用, 系统表现为电流无静差,得到过电流的自动保护。
比较:电流截止负反馈。
cf:带电流截至,转速负反馈无静差直流调速系统的静 特性,Idcr和IdbL均小于Idm
5、双环系统稳态参数计算
• P调节器的输出量总是正比于其输入量,而PI调节器未饱 和时,其输出量的稳态值是输入的积分,最终使PI调节器 输入为零,才停止积分。
• PI调节器的输出量在动态过程中决定于输入量的积分,到 达稳态时,输入为零,输出的稳态值与输入无关,而是由 它后面环节的需要决定的。稳态时:
ASR的输出: Ui* Id
篮球比赛 是根据 运动队 在规定 的比赛 时间里 得分多 少来决 定胜负 的,因 此,篮 球比赛 的计时 计分系 统是一 种得分 类型的 系统
解: (1)电流反馈系数 β=0.25V/A,
转速反馈系数 α=0.01V.min/r。 (2)当电动机在最高转速发生堵转时,看稳态结构图。
转速为0,ASR饱和,Ui*= Uim*=10V。 E为0,Ud0-IdR=0,此时Id=Idm=40A,R=1Ω 所以Ud=40V。Ks=40,Uc=1V Ui= Idmβ=10V。
实验四 转速、电流反馈控制直流调速系统的仿真

实验四转速、电流反馈控制直流调速系统的仿真一、实验目的熟练使用MATLAB下的SIMULINK软件进行系统仿真。
学会用MATLAB下的SIMULINK软件建立转速、电流反馈控制的直流调速系统的仿真模型和进行仿真实验的方法。
二、实验器材PC机一台,MATLAB软件三、实验参数采用转速、电流反馈控制的直流调速系统,按照要求分别进行仿真实验,输出直流电动机的电枢电流I d和转速n的响应数据,绘制出它们的响应曲线,并对实验数据进行分析,给出相应的结论。
转速、电流反馈控制的直流调速系统中各环节的参数如下:直流电动机:额定电压U N = 220 V,额定电流I dN =136 A,额定转速n N = 1460r/min,电动机电势系数C e= 0.132 V·min/r,允许过载倍数λ=1.5。
晶闸管整流装置的放大系数K s = 40。
电枢回路总电阻R =0.5Ω,电枢回路电磁时间常数T l = 0.03s,电力拖动系统机电时间常数T m = 0.18 s,整流装置滞后时间常数T s=0.0017s,电流滤波时间常数T oi=0.002s。
电流反馈系数β=0.05V/A(≈10V/1.5I N)。
四、实验内容1、电流环的仿真。
参考教材P90中相关内容建立采用比例积分控制的带限幅的电流环仿真模型,设置好各环节的参数。
图1电流环的仿真模型2、按照表1中的数据分别改变电流环中比例积分控制器的比例系数K p 和积分系数K i ,观察电流环输出电枢电流I d 的响应曲线,记录电枢电流I d 的超调量、响应时间、稳态值等参数,是否存在静差?分析原因。
表1 比例积分系数t/sI d /A不同比例系数Kp 和积分系数Ki 时的电枢电流曲线表1不同比例系数K p 和积分系数K i 的电枢电流数据对比分析:由表1可知,不同的比例系数K p 和积分系数K i 会影响系统的电枢电流且系统存在静差,原因是电流调节系统受到电动机反电动势的扰动,电动机反电动势是一个线性渐增的扰动量,所以系统做不到无静差。
- 1、下载文档前请自行甄别文档内容的完整性,平台不提供额外的编辑、内容补充、找答案等附加服务。
- 2、"仅部分预览"的文档,不可在线预览部分如存在完整性等问题,可反馈申请退款(可完整预览的文档不适用该条件!)。
- 3、如文档侵犯您的权益,请联系客服反馈,我们会尽快为您处理(人工客服工作时间:9:00-18:30)。
运动控制原理实验报告——带电流截止负反馈的直流调速系统实验原理 (2)直流调速系统的分类和指标 (2)带电流截至负反馈调速系统的静特性 (4)带电流截至负反馈调速系统的动态特性 (4)带电流截至负反馈调速系统的设计 (5)实验内容和过程 (6)晶闸管—电动机系统的自然机械机械特性测试 (6)系统控制单元整定 (8)系统静态性能测试 (9)系统动态性能测试 (13)实验结论与体会 (17)实验原理1.直流调速系统的分类和指标由于良好的起动制动性能和宽范围的平滑调速能力,直流电动机常被用于需要做快速正反向拖动的领域中。
直流拖动系统的控制往往是通过控制转速来实现的,由直流电动的电动势平衡方程推出转速表达式φe adl d C R I U n -=U 为电枢电压 ,dl I 为一定负载对应的电流,a R 为电枢回路总电压 φ电枢励磁磁通 e C 电机的电动势参数可知直流电机有三种可用的调速方法,分别是调压(U )调速,弱磁(φ)调速和改变串入电阻(aR )调速。
然而通过改变串入电阻阻值来调速不能实现无级调速,弱磁调速的调速范围又太小,所以直流调速系统常采用调压调速的方式。
对于一个建立好的直流调速系统,可以从调速范围(D ),干扰造成的转速波动大小(静差率s )和调速系统的起动和制动时间这三个方面来衡量,这些参数有如下关系,min max n n D =N Nn n n s ∆+∆=min其中Nn ∆为直流电机的转速降落,是在电机负载从理想空载增加到额定值对应的转速降落,可以作为衡量直流电机机械特性硬度的参量。
调速范围和静差率两个概念也有密切的联系,同样的转速降落Nn ∆下,调速范围越大,转速越低对应的静差率也会大一些,两者满足)1(D n n D s N N+∆=而真正衡量不同系统机械特性时我们用的是转速最低时的静差率,这是的静差率最难满足系统的性能指标。
本次实验使用的是晶闸管整流器-电动机调速系统的组合(M V -),同样广泛使用的还有PWM -电动机的组合。
常用的M V -系统有开环直流调速系统,带转速反馈的闭环直流调速系统(根据转速调节器ASR 的不同又分为比例和P 比例积分PI 调节),致力于解决过电流问题的带电流截止负反馈的直流调速系统(同样分为有差和无差)和能快速启动制动的双闭环直流调速系统。
从开环系统到带转速反馈的调速系统,同样电机的转速降落大大减小,静差率减小,调速范围扩大,调节精度和系统抗干扰的能力增强,比例积分调节还消除了系统的静态误差;从单闭环转速反馈系统到双闭环转速电流,直流电机可以实现最大恒流起动和制动。
V-M 触发的电机调速系统在转速负反馈控制的调速系统中突加给定电压,由于电机的惯性,转速不可能立即上升,反馈电压尚未建立时,转速调节器ASR 的输入偏差电压很大,电枢电流会很快升到其最大值,此时电枢电流极易过流,在制动和堵转时,电枢电流也容易过流。
为了限制电流,系统需要有自动限制电枢电流的环节,也就是电流截至环节 通过三相电流互感器取出电动机电枢回路的电流d I , 当d I 大于临界截至电流dcr I ,稳压管两端电压comU 大于sdcr R I 时,稳压管ST V 被击穿,电流负反馈加入,阻止电流的进一步上升。
利用稳压管产生比较电压带电流截至负反馈的有静差调速系统的稳态结构图如下,电流较小时,i U =0,调速系统只由转速负反馈调节,当coms d U R I ≥时,电流反馈电压coms d i U R I U -=电流反馈环节输入输出特性2.带电流截至负反馈调速系统的静特性带电流截至负反馈的闭环系统稳定结构图 带电流截至负反馈的闭环直流调速系统静特性分为2段dcrd I I ≤ 时,sR 上的电压小于稳压管的击穿电压comU ,电流反馈环没有接入,系统只受反馈转速环ASR 控制,此时)1()1(*K C RI K C U K K n e de ns p +-+=dcrd I I > 时,稳压管被击穿,随即电流负反馈环节接入系统,进一步减小输入放大器的偏差电压,抑制了转速的进一步上升,效果上如同串入了一个阻值为ss p R K K 的大电阻并提高电枢电压,结果使系统的机械特性变软,堵转电流减小)1()()1()(*K C I R K K R K C U U K K n e ds s p e com n s p ++-++=直流调速系统的机械特性如图在电流较大时加入电流负反馈相当于在主回路中串入了一个值为ss p R K K 的大电阻,使系统的特性迅速下降,堵转电流大大减小。
此时的堵转电流为scom n ss p com n s p db R U U R K K R U U K K I +≈++=**)( (RR K K s s p >>)实验中用到的直流调速系统属于有静差的调速系统。
3.带电流截至负反馈调速系统的设计设备:直流他励电动机的参数(额定电压,电流,转速)vU nom 220=A I num 1.1=rpmn nom 1450=电枢回路电阻 Ω=22a R 平波电感电阻 Ω=12L R 整流电源电阻 Ω=12n R 晶闸管整流增益 135=s K 调节器电阻Ω=k R o 22 稳压管稳压电压VU w 9.6=性能指标和要求: 最大给定电压v U nm 7||*=截至电流A I I nom dcr 2.11.1≈=最大堵转电流nomdbl I I 4.1=调速范围 3=D 静差率 %10<s根据性能指标计算P 调节的电阻1R 和电流截至反馈回路的电阻2R . (1)计算额定速降rpms D sn n nom cl 704.53)1(≤-⨯⨯=∆(2)计算系统开环增益07.61==-∆⨯⨯=es p cl e nom C K K n C RI K α(3)确定调节器比例系数5.1)1(*=++=ns nom e nom p U K RI K C n K(4)在最大堵转点时利用运放的特性计算电阻210*R U U R U R U wim ct n -== Ω=k R 331 Ω=k R 2.62(5)计算电流反馈系数75.5==dcrwI U β(6)计算转速反馈系数165.0==n U dnα实验内容和过程1.晶闸管—电动机系统的自然机械机械特性测试(1)连接晶闸管的直流电源—电动机系统主电路及负载(L=700MH,R=450Ω,I=1A ),负载电机励磁回路(R=900Ω,I=)(2)空载启动调节到空载转速0n (rmp 1600~1500),加上负载将电机调整到额定工作点(aN I ,N n ),在额定负载电流范围内测量出一条自然机械特性(5组数据)(3)计算出电机的自然机械特性为ded d I C RI U n 159.4-1629.90=-=(4)利用端电压基本相等的N1~N4 和额定点绘制电机的一条自然机械曲线实验中负载电流较小的时候转速偏大,这是主要由于此时的电枢电压比理论值(220V )偏大,电机的机械特性曲线已经上移。
随着电枢电流增大,转速增加,实验中得到的曲线与实验曲线越来越接近。
2.系统控制单元整定(1)调试出满足系统要求的电流反馈强度β为了防止系统过流,电流负反馈环节发挥作用需有稳压管被击穿,dW I U β<此时的负载电流AI I nom dcr 1.11.1== ,dI 取稍大于dcrI 的 ,因此nomW I U 2.1=β稳压管击穿电压w U 为,所以β 单位为 A V ,取,同时由于电流截至环节产生电压的不是电阻而是稳压管,β得物理意义不能理解为电阻。
通过调节电阻3p R 可以调节β,先将给定电压降低到额定的三分之一,再加负载使电枢电流达到dcrI ,调节3p R 的阻值使电机转速刚好出现明显下降,这时的β值就对应了实验所需的截至电压。
(2)确定截至稳压管的极性,连接电流反馈支路确定稳压管的极性可以通过测稳压管正反接时的电阻,选择ΩM 级电阻,接入电流反馈端和主回路。
(3)按实现计算出的21R R ,连接调节器和反馈回路 由堵转点时的运放特性得出210*R U U R U R U wim ct n -== Ω=k R 331 Ω=k R 2.62(4)调试出合适的速度反馈强度α加入转速负反馈,将给定电压*n U 设置到额定给定7V ,再调节测速电阻和转速反馈电阻FR 和0R ,使电机的转速达到额定转速。
3.系统静态性能测试(1)给定电压*n U 为最大值时是转速调到最大,在N I 1.1范围内测量出一条静特性(给出5组数据)给定电压最大时系统理论上静特性方程应该为 d I n 4.1591626.9-=图中可以看到实验得到的电机静特性和计算出的特性曲线吻合度较高,误差不超过20rpm,此时电机运行在额定工作点,误差的主要来源是电压,转速等测量器的量化误差,电机偶然受到的扰动等。
加入转速环后,随着负载电流的增加,电机的转速降落明显减小,这主要是由于转速环调节了电机工作电压的缘故,转速下降时,偏差使电机端电压提升,抵消了大部分负载电流上升带来的速降,电机前的环节如晶闸管整流,偏差放大器的放大系数越大,这种抵消速降的能力就越强。
上图中转速负反馈系统的静特性明显比电机自然机械特性要平,但仍有下降,这在比例调节的负反馈系统中是不可避免的。
随着电枢电流的增大,实验曲线的斜率也有增大,这种现象在下一个静态特性测试实验(将给定电压降到最大给定值的1/3)后也有出现,这可能是端电压的影响,也有可能是电流反馈电压的影响,端电压的变化速度幅度太大可能是比例调节的单闭环系统所无法跟踪的,而电流反馈回路的漏电流在稳压管两段电压明显增大后也会对主回路早成影响,还有可能是电机本身的带负载后机械特性的变化。
由于截至电流较大,测试静特性时没有选取截至电流和之后的点,如果一起绘出来,会看到一条在截至电流后明显下降的曲线,此时稳压管被击穿,电流反馈电压接入主回路,起到过流保护的作用。
(2)给定电压3*nU为最大值时是转速调到最大,在NI0.6范围内测量出一条静特性(给出5组数据)改变给定电压后的dI n 4.1593.543-=将给定电压减小到最大给定的1/3时,此时得到了调速范围内的最低转速,此时电机出现了转速不稳定的现象,电机的运行声音不连续,电枢端电压明显波动,转速也在波动。
在1/3给定电压处实验得到的静特性曲线和理论的静特性曲线有较大的差距(rpm rpm 100~50),一方面是由于电机在较低转速时运行不稳定,另一方面有由两条曲线存在系统误差可以看出,在单闭环外存在扰动,或许是电压给定的偏差造成。
4.系统动态性能测试额定负载时,系统突加最大给定(n = 1450)启动电机,用示波器测量并记录Id 、n 的动态响应波形。