第1章 金刚石钻头基本知识
金刚石钻头

(5). 钻头铰刀: 为了大量生产之需要,其前端为钻头,后端为铰 刀,钻头直径与铰刀直径只差铰孔之裕留量,也有钻头于螺攻 丝混合使用,故又称为混合钻头. (6).深孔钻头:最早用于枪管及石包管之钻孔加工,又称为枪 管钻头。深孔钻头为一直槽型,在一圆管中切除四分之一强的 部份以产生刃口排屑 (7). 锥度钻头: 当加工模具进料口时,可使用锥度钻头. (8). 圆柱孔钻头: 我们称其为沉头铣刀,此种钻头前端有一直 径较小之部分称为道杆. (9).圆锥孔钻头: 为钻削圆锥孔之用,其前端角度有90°,60° 等各种,我们使用的倒角刀就是圆锥孔钻头的一种.
金刚石钻头的物理性质
1. 硬度 硬度是金刚石最重要的性能之一。金刚石的硬度极高, 莫氏硬度为 10级, 研磨硬度是刚玉的150倍,是石英的1 000倍。 2. 强度 金刚石具有极大的抗静压强度。天然金刚石的抗压强度大约8 600MPa,约为刚玉的3.5倍 , 硬质合金的1.5倍,钢的9倍。用于钻探的人 造金刚石一般要求强度达 500MPa以上。 3. 耐磨性 金刚石具有极高的耐磨性,是刚玉的90倍,硬质合金的40~200 倍 , 钢的2000 ~5000倍。用于钻探的人造金刚石聚晶体 一般要求与中 硬碳化硅砂轮的磨耗比在1∶30000以上。 4. 热稳定性 金刚石是热的良导体,它散热比硬质合金刃具快。金刚石容 易受到热损伤,虽然温度尚低于其燃烧温度,但金刚石的强度、耐磨性 已受到严重影响。所以钻进中必须充分冷却,防止发生金刚石微烧或烧 钻事故。
第二节 金刚石钻头的组成
金刚石钻头是以锋利、耐磨和能够自锐的天然金 刚石或人造金刚石为切削齿,在钻低钻压下即可获 得较高的钻速和钻头进尺,是石油钻井中广泛使用 的一种高效钻头。 1 按金刚石来源可分为天然金刚石钻头和人造金刚 石钻头 2 按功用可分为取心钻头和全面钻进钻头; 3 按镶嵌方式可分为表镶和孕镶两类; 4 按钻井方式则可分为转盘钻井和涡轮钻井用两 类。
金刚石钻头的原理和结构

金刚石钻头的原理和结构金刚石钻头是一种广泛用于岩石钻探、矿物开采以及石油、天然气勘探等领域的工具。
它具有较高的硬度、很强的抗磨性能和较强的耐腐蚀能力,能够在高温、高压和复杂环境下工作。
金刚石钻头是以人工合成的金刚石作为切削工具的一种机械钻头。
金刚石钻头的主要原理是利用钻具在岩石中切削和击碎岩石产生孔眼。
金刚石钻头的结构由刀具和钻具两个主要部分组成。
首先,我们来看一看金刚石钻头的刀具部分。
金刚石钻头的刀具部分通常由金刚石刀具和钢制材料组成。
金刚石刀具通常由人工合成的金刚石微粉和金属粉末混合而成,经过高温高压处理形成固态金刚石。
金刚石是一种非常硬的材料,其硬度仅次于金属元素钨,能够有效地切削硬岩。
在钻具部分,金刚石钻头通常采用钢制的钻杆和连接器。
钻杆通常由镍铬合金钢制成,能够承受极高的压力和扭矩。
而连接器则用于连接钻杆和刀具部分,确保刀具可以旋转。
金刚石钻头的结构非常复杂,通常由多个组件组成。
其中,较为重要的组件包括钻杆、导向装置、喷嘴和刀具。
钻杆是连接刀具和钻机的零件,用于传递旋转力和推进力。
导向装置主要用来控制钻头在钻削过程中的方向。
喷嘴常常与金刚石刀具相连接,用来喷射冷却液,降低切削区域的温度。
刀具是金刚石钻头最重要的部分,通常由多个金刚石片组成。
这些金刚石片贴合在刀具上,形成切削边缘,用于切削和击碎岩石。
金刚石钻头的工作原理可以分为两个主要过程:切削和击碎。
在切削过程中,金刚石钻头通过刀具上的金刚石片切削岩石。
金刚石的硬度能够有效地切削硬岩。
在切削过程中,金刚石钻头需要施加足够的推进力和旋转力,使刀具旋转并向前推进。
同时,喷嘴喷射的冷却液可以冷却刀具和减少切削过程中的摩擦和热量。
而在击碎过程中,金刚石钻头利用撞击力将岩石击碎。
当金刚石钻头切削岩石时,金刚石片的表面可能会形成尖锐的碎屑。
当这些碎屑与钻孔壁摩擦时,会产生巨大的撞击力,将岩石击碎。
总而言之,金刚石钻头通过切削和击碎的方式向岩石中钻孔。
金刚石钻头+标准

金刚石钻头+标准摘要:I.引言- 简要介绍金刚石钻头的概念和应用领域II.金刚石钻头的种类与特点- 按形状分类:圆钻头、方钻头、六边形钻头等- 按金刚石的镶嵌方式分类:整体金刚石钻头、复合金刚石钻头等- 各类金刚石钻头的适用范围和优缺点III.金刚石钻头的选择标准- 钻头材质:金刚石的含量、质量、类型等- 钻头形状和尺寸:与被加工材料和钻孔要求相适应- 钻头的加工精度:影响钻孔的精度和效率IV.金刚石钻头的使用与维护- 使用方法:合理选择钻头,正确安装和调试,控制切削参数等- 维护保养:清洁、检查、更换磨损部件等V.结论- 总结金刚石钻头在现代工业中的重要性及其发展趋势正文:金刚石钻头是一种以金刚石为切削刃的钻头,广泛应用于各类工业材料的高效加工。
金刚石钻头的种类繁多,不同的形状、结构和镶嵌方式适应不同的加工需求。
正确选择和使用金刚石钻头,对于提高加工效率、保证加工质量具有重要意义。
金刚石钻头主要有圆钻头、方钻头、六边形钻头等。
其中,圆钻头应用最为广泛,适用于大多数材料的高速钻孔。
方钻头和六边形钻头则适用于难加工材料和特殊场景。
此外,根据金刚石的镶嵌方式,金刚石钻头可分为整体金刚石钻头和复合金刚石钻头。
整体金刚石钻头结构简单、镶嵌牢靠,但更换成本较高;复合金刚石钻头则兼具高切削性能和较低的制造成本。
在选择金刚石钻头时,应综合考虑钻头材质、形状和尺寸、加工精度等因素。
钻头材质直接影响金刚石的含量、质量、类型等,从而影响钻孔效果。
钻头形状和尺寸要与被加工材料和钻孔要求相适应,以保证切削稳定、钻孔精度高。
钻头的加工精度也至关重要,直接关系到钻孔的精度和效率。
在使用金刚石钻头过程中,合理选择钻头、正确安装和调试、控制切削参数是提高加工效率的关键。
此外,还需定期对钻头进行维护保养,如清洁、检查、更换磨损部件等,以延长钻头使用寿命。
总之,金刚石钻头在现代工业中具有重要地位,其发展趋势将更加注重高效、环保和智能化。
金刚石钻进介绍课件
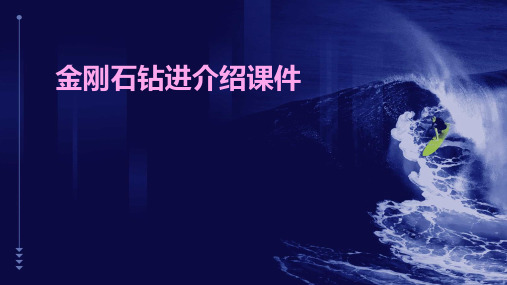
04
金刚石钻进
在钻进前,应对所有设备进行全 面检查,确保设备完好无损,特 别是金刚石钻头,应检查其磨损
情况,确保钻进效率。
场地准备
清理钻进场地,确保场地平整,无 杂物,防止在钻进过程中发生意外 。
安全措施
准备好安全设备,如安全帽,防护 镜,防火器等,确保工作人员的人 身安全。
废弃物对环境的压力。
在金刚石钻进结束后,对破 坏的生态环境进行恢复和治 理,促进生态环境的修复和
改善。
06
金刚石钻进的发展前景与应用拓展
金刚石钻进技术的发展趋势
01
自动化和智能化
随着科技的进步,金刚石钻进技术将越来越趋向于自动化和智能化。通
过引入现代传感技术、计算机技术和人工智能技术,实现钻进过程的实
钻头磨损检测与更换标准
磨损检测
钻头磨损检测主要通过观察钻头表面的金刚石颗粒磨损情况、测量钻头直径变 化等方法进行。定期检测能及时发现钻头磨损,避免影响钻进效果。
更换标准
当钻头磨损到一定程度时,需进行更换。更换标准主要根据钻头直径磨损量、 钻进速度变化等因素确定。按照更换标准及时更换钻头,能确保钻进效率和安 全。
卡钻处理:如遇卡钻情况,首先尝试通过调整钻 压和转速来解决问题,如无效,则需要停止钻进 ,人工清理卡钻。
设备故障处理:如设备在钻进过程中出现故障, 应立即停止钻进,检查并修复设备,确保设备能 正常运行后再进行钻进。
钻头磨损处理:在钻进过程中,如发现钻头磨损 严重,应立即停止钻进,更换新的钻头。
以上即为金刚石钻进工艺与操作的相关内容,通 过严格的操作规程和及时的故障排除处理,能确 保金刚石钻进的顺利进行,提高钻进效率,同时 也保障了工作人员的人身安全。
地质钻探用金刚石取芯钻头简介
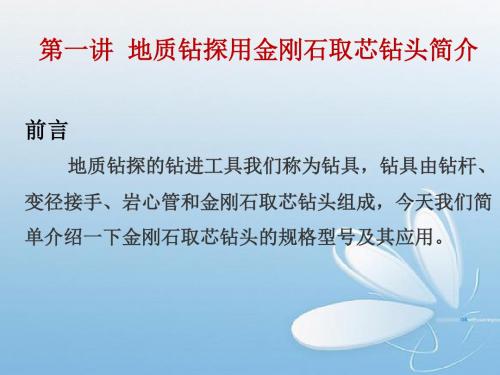
三、取芯钻头规格
在我国地质钻探作业中,常用的国标口径的金刚石取芯钻头 口径为: 75mm、91mm、110mm、130mm、150mm、170mm。
文章来源:
四、市场价格
对于金刚石取芯钻头的价格,随着制作工艺的改善,钻头的 成本有所下降,售价也是在逐步的下调,以金钻110钻头为 例,03年的售价高达430元,现今最新价格在360元左右。而 且工艺的改进使得现在钻头的质量较以前有大幅度的提升, 钻探效率明显增强,成本逐步在下降。
第一讲 地质钻探用金刚石取芯钻头简介
前言
地质钻探的钻进工具我们称为钻具,钻具由钻杆、 变径接手、岩心管和金刚石取芯钻头组成,今天我们简 单介绍一下金刚石取芯钻头的规格型号及其应用。
主要内容:
一、取芯钻头分类 二、取芯钻头选择原则 三、取芯钻头规格 四、市场价格
一、取芯钻头分类
在地质钻探中,取芯钻头分为 1,金刚石钻头 2,金刚石复合片钻头 3,金刚石绳索钻头
文章来源:
2,钻进比较坚硬的岩石地层时,我们推荐使用电镀金 刚石取芯钻头,这类钻头由于制作工艺的原因,进尺 效率异常突出,破岩能力极强,在岩层中钻进的效率 远超复合片钻头。
3,我们需要钻进300米以上孔深时,这时候,金刚石绳 索取芯钻头就非常适合了,因为孔深的增加,对于岩心的 提取是非常重要的,绳索钻具的不需要提钻的特点极大的 缩短了上下钻具的时间,是深孔钻的成本极大降低。
文章来源:
二、取芯钻头选择原则
根据不同的钻探任务,我们必须选择合适的钻头,目的就 是提高钻探的钻进效率和缩小钻探的综合成本。 1,钻进比较松软的泥岩类岩层时,我们推荐使用金刚石 复合片钻头,因为这类钻头的耐磨性能突出,水口大,对 于泥土层有比较好的进尺效率和工作时间。
金刚石钻头参考资料

由于热压烧结一般没有保护气氛,胎体 在烧结过程中容易氧化,影响胎体的致密化 及烧结强度。因此,在胎体材料中通常要加 入某些活泼金属元素,使其在烧结过程中起 到脱氧作用,例如锰和钛等。这样,在烧结 过程中,残存于胎体孔隙之中未及排除的氧 就会优先与这些活泼金属反应,生成氧化物, 从而促进其他粉末的烧结。大家知道,铜及 其合金容易浸润各种金属及其合金或化合物, 同样也容易浸润在烧结过程中所形成的活泼 金属的氧化物,活泼金属的氧化物对于胎体 的整体性能不仅无害,而且这些细小的氧化 物颗粒还可在胎体中起到弥散强化的作用。 其化学反应式为:
事实上胎体中的其他粉末由于已经存放了某些时间以及环境的影响其表面一点也不被氧化和在表面上一点吸附气体也没有是不可能的所添加的活泼金属除了有一部分与空隙中的氧发生反应外还有一部分将与粉末表面的这些氧化物或所吸附的气体发生反应其反应这些置换反应均为放热反应对于表面活化了的粘结金属以及中间相的烧结无疑是具有重要作用的
第三节 孕镶钻头
第三节 孕镶钻头
孕镶钻头是将金刚石与胎体粉末拌 合在一起所制成的钻头(图6-6),胎体将 金刚石全部包镶在里面,在钻头工作时, 金刚石随胎体的磨损以接力的形式不断 出露、工作、脱落、再出露。这种钻头 是为弥补大颗粒天然金刚石稀缺和昂贵 的不足而出现的。实践证明,孕镶金刚 石钻头具有优异的钻进性能和耐用性能。
.mm
• 石墨的线膨胀系数: 石 5.4 106 / C
• 钢体的线膨胀系数: 钢 15106 / C
中频炉
前已述及,对于孕镶钻头,其金刚石将随着
工作层胎体的磨损而逐渐出露,形成切削刃,胎 体工作面表层上切削刃的数量和出刃高度与金刚 石的浓度、粒度、品级以及胎体的耐磨性、对金 刚石的粘结性能密切相关。由于孕镶于胎体中的 金刚石是随机而又相对均匀地分布着,每粒金刚 石都经过初磨→初露→出刃工作→碎裂或脱落的 全过程。整个钻头胎体中的金刚石是以接力的形 式而进行工作的,如图6-7所示。与表镶钻头相比, 孕镶钻头对胎体性能有更复杂的要求。
金刚石钻头

现场使用
金刚石钻头在软-中硬地层中钻进时,有速度快、进尺多、寿命长、工作平稳、井下事故少、井身质量好等优 点。金刚石钻头不但使用时间长,还可以重复利用,返厂修复的金刚石钻头使用起来和出厂的金刚石钻头使用效 果差不多,能大量的节约钻井成本。
谢谢观看
优势
1力平衡设计使钻头具有良好的导向性,适应配合井下马达应用于定向钻井,具有较小的径向震动; 2不同结构的专利PDC复合片在钻头不同位置的合理布置使钻头具有较强的攻击性和抗研磨性; 3强攻击性设计使钻头可获得高的机械钻速; 4动态流场模拟技术应用于水力设计,使井底流场最优化,有利于提高排屑速度和防泥包。
使用
一.金刚石钻头钻前准备 1、检查上一只金刚石钻头是否存在有钻头体损坏,掉齿等,确定井底清洁,无落物。 2、小心搬运金刚石钻头,将金刚石钻头放置在橡胶垫或木板上。禁止把金刚石钻头直接放置在铁板上。 3、检查金刚石钻头切削齿是否有损伤,金刚石钻头内是否有异物,喷嘴孔内是否有O型密封圈,根据需要安 装喷嘴。 二.金刚石钻头上扣 1、清理金刚石钻头公扣或母扣并涂抹丝扣油。 2、将卸扣器卡在金刚石钻头上,放下钻柱使之与公扣或母扣接触上扣。 3、把金刚石钻头和卸扣器一起放入转盘补心,然后按照推荐上扣扭矩值旋紧丝扣。 三.下钻 1、下放金刚石钻头要慢,通过转盘,防喷器,套管悬挂器尤其要缓慢,以保护好切削齿。2、注意上次起钻 时出现的遇阻井段,下钻过程中遇到缩径和狗腿时应使钻头缓慢通过。
金刚石钻头基本知识

第一章金刚石钻头基本知识第一节概述金刚石钻头的发展历史金刚石钻头是不同于牙轮钻头的另一类钻井破岩工具,其使用可以追溯到19世纪60年代。
最初人们以天然金刚石为切削元件制作打炮眼和挖掘隧道的工具,后来出现了用于石油钻井的钢体鱼尾式天然金刚石全面钻进钻头和取心钻头。
早期的金刚石钻头是将天然金刚石冷镶在低碳钢上的。
由于天然金刚石来源有限,价格昂贵,加之本身尺寸、性能方面的原因以及当时落后的制造工艺,大大限制了金刚石钻头在石油钻井工业中的应用。
随着粉末冶金技术的发展,出现了采用烧结碳化钨作为钻头体的胎体式金刚石钻头。
这种技术的出现使金刚石钻头的制造水平大大提高。
胎体式金刚石钻头具有耐冲蚀、耐磨损的特点,具有良好的使用性能,其制造工艺也不复杂,因此一经出现就迅速推广开来。
人造聚晶金刚石的研制成功,对金刚石钻头技术的发展起了巨大的推动作用。
人造聚晶金刚石复合片钻头(PDC钻头)的出现一度被称为20世纪80年代钻井工业技术的一大突破,这种新技术对石油钻井业的发展产生了巨大的影响。
现场使用证明,软到中等硬度地层钻井用PDC钻头具有机械钻速高、进尺多、寿命长、工作平稳、井下事故少、井身质量好等优点,并能与井下动力钻具配合用于高速钻井。
合理使用金刚石钻头可以大大缩短建井周期,降低钻井成本,提高钻井经济效益。
金刚石钻头的发展前景经过近二十多年的发展,金刚石钻头已经成为继牙轮钻头之后的又一重要破岩工具。
时至今日,PDC钻头在石油钻头市场所占的份额越来越大,几乎每年以30%的速度侵吞牙轮钻头市场。
随着新的设计理论、设计方法和材料等技术的发展,PDC钻头的适用范围也在不断扩展,以前被认为不适用于PDC钻头的地层现在也广泛使用,比如我国中原油田的文留区块的沙二至沙三地层由于地质情况复杂、夹层多,可钻性差,以前一直被认为是PDC钻头的禁区,在这里钻的井除了取心之外用的都是牙轮钻头。
可是从2000年开始,PDC钻头在这个区块的使用量逐渐增多,效果也很好,而2001年底我公司的一只8 1/2 BK542-4型PDC钻头更在该区块的文-133井创下了1600米(东营组)入井,打到3390米(沙三上)完井,纯钻时间小时,进尺1790米,平均机械钻速米的好指标。
4电镀金刚石钻头(1)
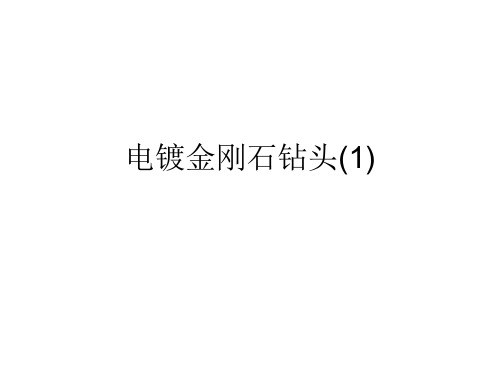
第一章 电镀钻头原理
第一节 基本定律 一、两类导体 在盛有溶液的镀槽中装置 阳极(如镍板)和阴极(如钻头), 接通直流电源后,可以看到线 路中电流表的指针移动。这表 明整个线路中有电流通过。 在电镀中,电流从直流电 钻头 镍板 源经外导线(如铜线)引入镍阳极, 经过溶液再进入阴极(如钻头钢 图1-1 镀镍槽示意图 体),然后经外导线又回到直流 电源,如图1-1。
二、法拉第定律
电镀槽通电时,电极与溶液界面间有化学反应发生。当通过电镀槽 的电流达到稳态时,由外电路流向阴极的电子全部参加电极反应。对镀 镍的阴极过程来说,自直流电源流过来的自由电子越多,则镀上的镍层 越厚。为了了解在施镀时间内镀层的厚度或质量,有必要寻求电流强度 寻求电流强度 与电极上所形成产物的量的关系。 与电极上所形成产物的量的关系。 根据生产实践及实验结果,总结出了描述电极上通过的电量与电极 反应产物质量之间的关系。 (1)法拉第定律 电流通过电镀槽时,在电极上析出物质的量与溶液中 通过的电量关系,可用下式表示:
(3)温度 镀镍的温度通常是不高的,在一定电压条件 镀镍的温度通常是不高的, 下提高槽温就会观察到电流增大的现象。 下提高槽温就会观察到电流增大的现象。其原因 之一就是升高温度可以使离子运动速度增大, 之一就是升高温度可以使离子运动速度增大,因 而提高溶液的导电能力。 而提高溶液的导电能力 各种溶液的电导率,都可以直接测出来。通 常在溶液中加入一定量的导电盐类(如镀镍溶液 中的NaCI),以提高镀液的电导率。这对于节约 电能和改善镀液的分散能力均起着重大的作用。 但导电盐类也不可加得过多,一方面它有可能反 而会使镀液的电导率下降,另一方面镀液浓度过 高,粘度也相应增大,不但有可能使电极反应的 进行遇到阻力,而且会使镀件出槽时夹带出来镀 液的量增加,造成额外的损失,甚至当槽温变化 时还可能出现某些物质结晶析出的现象。
金刚石工具基础知识

3.金刚石工具
金刚石工具是金刚石颗粒与金属、树脂等 结合剂混合按一定工艺而成的一种特殊的复合 材料。由于建材工业的发展,对金刚石工具的 使用也越来越广泛,这也使对工具的生产从经 济和性能上都有很高的要求。而提高金刚石工 具性能的关键是制品的耐磨,同时保持锋利性。
3.1金刚石工具的结构: • 金刚石+金属粉末=刀头(主要技术) • 刀头+基体(刚体)=金刚石锯片(钻头、 磨盘)
3.2金刚石工具的分类 • 按用途划分 钻头类 锯片类 磨削类 即“钻、切、 磨”工具。 • 按制作工艺划分 烧结类 焊接类 电镀制品等 • 按结合剂划分 金属结合剂 树脂结合剂 陶瓷结合剂 等
3.3金刚石工具的浓度概念
定义金刚石在胎体中体积比为25%时浓度为100%。 浓度是金刚石工具的重要特性之一,对工具的效率、 寿命和加工效果有很大的影响。一般金刚石浓度高,则 单位工作层面积上的金刚石颗粒数就多,每个磨粒的受 力就小,切入工件的深度小,金刚石不易破碎和脱落, 反而容易被磨平和抛光,宏观表现为效率低、寿命长; 金刚石浓度低,每个磨粒有更大的切入压力,切入深, 金刚石易破碎和脱落,工具表现为效率高、寿命低。 通常,锯切工具的金刚石浓度多选在10%~45%;钻 探工具、烧结金属结合剂金刚石磨具多选50%~125%浓度; 树脂金刚石磨具的浓度多选50%~100%;陶瓷金刚石磨具 多选75%~150%浓度;电镀其生成方式分为天然金刚石和人
工合成金刚石,用于金刚石工具制作的一般是
人工合成金刚石。也称作工业金刚石。
其密度为3.52g/cm3, 其质量单位一般情况
用“克拉”表示,1克拉=0.2克。 人造金刚石的粒度(颗粒大小)一般用 “目”表示 。人造金刚石常见粒度为25/30、 30/40、40/45、45/50、50/60、60/70… …
金刚石钻头

(1)钻头基体
PDC钻头可分为钢体PDC钻头和碳化钨胎体PDC钻头。 钢体式PDC钻头的表面不耐冲蚀,规径易于磨小,而胎体式钻头的碳化钨合金耐 冲蚀、耐磨损,允许使用较高的钻头压力降、较高钻井液含砂量,易于进行优化水 力设计,具有较大的设计灵活性,鱼尾形钻头寿命较长。 鱼尾形 PDC钻头基体有四种基本冠部外形: 浅锥形 短抛物线形 抛物线形
翼片很长,增加了复合片出刃高度,增加了钻头冠部与地层之间的间隙, 使岩屑易于排向环形空间不致于粘附于钻头体,有利于射流的清洗。
鱼尾形
特点: 特点:能减少泥包和与泥包相关的钻井问题。 适用范围: 适用范围:转盘钻井的直井和定向钻井,钻进粘性极高的泥页岩层。
有一个带锥度的冠部,冠顶相当圆顿。可以使钻头外侧布置更多数量的 切削齿。
PDC钻头设计中用负前角、侧偏角和切削齿出露高度来 规定切削齿的排列方向。 负前角又称后倾角,它是指复合片层面与岩石工作面垂线 负前角又称后倾角 之间的夹角。 采用适当的负前角,可以大大改善切削齿的抗冲击性。一 般负前角取值范围为0 ° ~25 ° 。 软地层:取0或较小负前角值; 硬地层,负前角应较大,以保证有效切削,并防止冲击载 荷引起切削齿的损坏。 侧偏角是指切削齿面与钻头径向平面之间的夹角,有侧偏角的钻头比无侧偏 侧偏角 角的钻头钻进性能好,钻速快,并可以改善钻头的清洗和岩屑的及时排除;减少 岩屑粘附切削齿的机会。实验表明,侧偏角为-15°时粘附机会最小。 切削齿的出露高度与所钻岩性有关,可分为全出露和部分出露两种。 切削齿的出露高度 全部出露:适于钻软地层; 部分出露:使于钻硬地层,可以提高切削齿刚度,有利于延长PDC钻头的寿命。
第五节
金刚石钻头及其破岩原理
金刚石钻头是以锋利、耐磨和能够自锐的天然金刚石或人造金刚石为切削齿, 在钻低钻压下即可获得较高的钻速和钻头进尺,是石油钻井中广泛使用的一种高 效钻头。
金刚石钻头分类及使用

金刚石钻头分类及使用金刚石钻头是一种非常有用的工具,可以用于各种不同类型的材料的加工和处理,包括硬质材料。
由于金刚石十分坚硬,并且能够耐受高温和压力,因此它是一种非常强大和有用的钻头。
在这篇文章中,我们将探讨金刚石钻头的分类和使用。
1. 金刚石钻头的分类金刚石钻头有很多不同的类型,每种类型都适用于不同材料和任务。
以下是一些常见的金刚石钻头类型:(1) 金刚石中空钻头这种钻头的中心部分是空心的,可以用于钻孔和泥浆循环。
它适用于钻探石油、天然气和纯净水等领域。
(2) 钎头式金刚石钻头这种钻头看起来像一把锤子,其结构是由零件组成的。
钻头的外层是钻石,内部支撑杆和水的循环系统。
这种钻头适用于地下勘探和巨型土建项目。
(3) 金刚石螺丝钻头这种钻头是由许多钻石和钻头组成的,并且有一个螺旋形的切割方式。
它可以钻遍许多不同种类的岩石,包括花岗岩和大理石。
(4) 手持式金刚石钻头这种钻头通常是用手持钻机或钻头座等电动工具进行使用。
它可以用于一些个人DIY工作,例如在家里进行墙上插钩等。
2. 金刚石钻头的使用接下来,我们将为您介绍金刚石钻头的使用方法。
首先,你需要了解材料的类型和密度。
钻头的不同类型适用于不同的材料,具有不同的使用范围。
在使用金刚石钻头时,需要特别注意钻头是否适用于你要钻的材料。
其次,钻头的切割速度应该通过调整钻机的速度来控制。
太低的速度会使钻头失去作用,太高的速度则会导致加工过程中出现不必要的摩擦和磨损。
再次,钻头应该在有冷却水的情况下使用。
金刚石钻头适合进行湿式切割,因此需要足够的冷却水进行冷却。
如果没有足够的水来冷却金刚石切削表面,钻头表面的金刚石可能会因过热而脱落。
最后,在使用过程中需要注意安全问题。
钻机应该放在一个平稳的表面上,操作时注意穿工作手套和护目镜等防护装备,以免被分离的金刚石颗粒损伤眼睛和手部。
总之,金刚石钻头是一种很实用的工具,可以用于将不同类型的材料加工和处理。
在使用时,需要认真了解钻头的类型和使用方法,严格按照要求使用。
第一节 钻头

牙轮布置方案
(1)非自洗无滑动布置: 各牙轮牙齿齿圈不嵌合,单锥、不超顶,不移轴,用
于硬地层; (2)自洗不移轴布置:
各牙轮牙齿齿圈相互嵌合,副锥、超顶,不移轴,用 于中硬地层; (3)自洗移轴布置:
(3)金刚石钻头类型(按金刚石材料分) 1)天然金刚石钻头 2)聚晶金刚石复合片钻头(PDC) 3)热稳定聚晶金刚石钻头(TSP)。
刮刀钻头(drag bit)
牙轮钻头(cone bit)
金刚石钻头(diamond drill bit)
PDC钻头
PDC双心钻头
TSP钻头
(二)三类钻头的使用率
刮刀钻头主要以切削作用破碎地层。 破碎塑性岩石过程:
在钻压W 作用下,刀翼容易吃入地层;刃 前岩石在扭转力T 的作用 下不断产生塑性流动。
这和车刀切削软金属的过程类似。
(三)刮刀钻头的应用
刮刀钻头制造工艺简单,成本低; 刮刀钻头适用于软地层,钻速快,每米钻进成本低; 刮刀钻头容易磨损成锥形,造成缩径和井斜; 刮刀钻头产生剧烈的扭转振动,破坏钻具和设备; 刮刀钻头目前逐渐被PDC钻头取代。
密封圈
滚密 柱封
圈 止推
台阶
滑动摩 擦衬套 滑动摩 擦副
③根据轴承副的结构(大轴承)分类: 滚动轴承和滑动轴承两大类。
滚动轴承的结构形式: a.“滚柱—滚珠—滚柱—止推” b.“滚柱—滚珠—滚珠—止推”
滑动轴承的结构: a.“滑动—滚动—滑动—止推” b.“滑动—滑动—滑动—止推”
4.储油润滑密封系统
牙轮钻头使用约占总进尺的80%左右,其 次是金刚石材料钻头,刮刀钻头很少用。
钻头知识2010.8
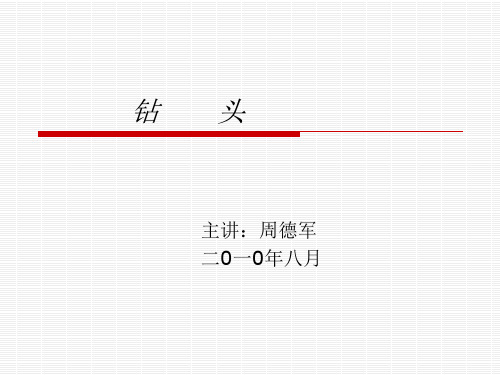
钻头简述
钻头单位进尺成本:
式中 C=[Cb-Cr(T+Tt)]/H C-单位进尺成本,元/米 Cb-钻头成本,元 Cr-钻机作业费,元/小时 T -钻头纯钻进时间,小时 Tt-起下钻时间,小时 H-钻头总进尺,米
第二章 钻头的分类
钻头
牙轮(取心) 金刚石(取心)
刮刀(取心)
钻头的分类
一、牙轮钻头的分类: 1、按工作牙轮数量分为: 单牙轮,两牙轮,三牙轮,四牙轮钻头等。 2、按切削材质可分为: 铣齿(钢齿)和镶齿牙轮钻头。 3、按用途可分为: 钻进用牙轮钻头、取芯用牙轮钻头和其它 用牙轮钻头。
第六章
取芯钻头
一、取芯钻头的结构取芯钻头的结构 2010.8.doc
第七章
钻头事故预防及处理
一、钻头事故预防 1、按照井下实际情况并结合邻井实钻正确 选择钻头类型; 2、严格按照钻头的机械性能,确定合理的 钻压、转速值; 3、及时掌握机械钻速、扭矩和泵压等钻井 参数的变化。
第七章
第四章
金刚石钻头
(4)下钻要慢,安全通过转盘、防喷器、井眼中 不规则的台阶。“狗腿”、缩径段,保护好切削齿。 下到最后一个单根时,应开泵并旋转循环,消除岩 屑及沉砂。 (5)钻头接触井底后,应以低转速 (50~60r/min)和低钻压(10~20kN)钻进 0.5m左右,完成新井底造型。 (6)做好钻速试验,即固定钻压,改变转速,或 固定转速,改变钻压,使钻压和转速合理匹配,以 获得最高机械钻速钻进。
钻头的分类
三、刮刀钻头的分类: 1、按刮刀片(刀翼)分类: 二、三、四等刮刀钻头。 2、按切削材料分类: 硬质合金和聚晶金刚石刮刀钻头。 3、按用途分类: 全面钻进用、取芯用和其它用刮刀钻头。
天然金刚石钻头的工作原理

天然金刚石钻头的工作原理天然金刚石钻头是一种用于钻探地下岩石和矿石的工具,其工作原理是利用金刚石的硬度和耐磨性。
下面将详细介绍天然金刚石钻头的工作原理。
首先,让我们了解一下金刚石的特性。
金刚石是一种天然的碳晶体,由于其晶格结构的完整性和化学键的稳定性,金刚石具有非常高的硬度和耐磨性。
金刚石的硬度是其他任何物质所无法比拟的,它在莫氏硬度量表中的评定为10级。
另外,金刚石的热导率也非常高,可以将热量迅速传导出去,从而减少钻头受热损伤的概率。
天然金刚石钻头的工作原理主要包括以下几个方面:1. 钻头结构:天然金刚石钻头通常由金刚石刀具和钻杆组成。
金刚石刀具上嵌有许多金刚石颗粒,接触到岩石表面时,金刚石颗粒会快速旋转和摩擦,从而破碎和磨损岩石。
2. 钻杆传递动力:钻杆是将动力从钻机传递到钻头的工具。
通常,钻机通过转子的旋转运动产生动力,并通过钻杆将动力传递到钻头。
因此,钻杆需要具有足够的强度和刚度,以抵抗旋转时的扭转力和钻孔时的抵抗力。
3. 钻头运动:当钻机启动时,钻头开始旋转并向下推进。
金刚石刀具上的金刚石颗粒会与岩石表面发生摩擦和冲击,从而破碎岩石。
破碎的岩石粉末通过钻头中的冷却液冲刷出来,以防止堵塞和降低钻头的温度。
4. 冷却系统:钻探过程中,由于金刚石刀具的摩擦会产生大量的热量,如果不及时降温,金刚石颗粒可能会因过热而失去硬度和断裂。
因此,天然金刚石钻头通常配备有冷却系统,通过喷射冷却液冷却金刚石刀具和岩石表面,防止过热。
5. 排渣系统:在钻探过程中,岩石的破碎物会形成岩屑,如果不及时排除,可能会阻碍钻探的进行。
因此,天然金刚石钻头通常具有排渣系统,通过冷却液的流动和钻孔中产生的旋转力,将岩屑冲刷出孔口。
总的来说,天然金刚石钻头是通过让金刚石颗粒与岩石表面摩擦和冲击,从而破碎和磨损岩石,并通过钻杆传递动力、冷却系统降温和排渣系统排除岩屑来完成钻探作业。
其工作原理基于金刚石的硬度、耐磨性和热导率这些特性,以及钻杆的结构设计和冷却排渣系统的功能。
钻进工具 - 金刚石钻头

钻头水力结构 切削齿的大小和
特点
切削齿的密度
1-9,R、X、 O
1-9,0
R-放射式流道
X-分流式流道
O-其他形式流 道
切削齿的大小和 切削齿的密度
0为孕镶式钻头
三、金刚石钻头和刮刀钻头
7、金刚石钻头的使用
井底要求清洁 避免划眼 钻井参数和选择 钻压:均匀施钻压 转速;尽可能高些 排量:满足携岩要求
三、金刚石钻头和刮刀钻头
5、金刚石钻头的特点
(1)一体性,适应于高钻速和定向井钻井 (2)使用正确时,耐磨寿命长,适用于深井和研磨性地层 (3)高温情况下,不会出现轴承密封失效 (4)适用于小井眼钻井 (5)设计制造灵活 (6)PDC钻头是切削钻头,有着自锐特点 (7)受热稳定性限制 (8)抗冲击载荷性能差 (9)价格昂贵
由表面水槽分散冷却 PDC钻头,钻井液从水眼流出,经分流元件分散到钻
头各处,水眼位置和数量由钻头结构而定。 (4)保径部分,有拉槽式、平镶式和组合式
三、金刚石钻头和刮刀钻头
1、金刚石钻头的总体结构
(5)金刚石钻头的切削刃 天然金刚石(最硬、抗压强度最大,抗磨损能力最高)。 弱点:脆性大,热稳定性差 0.5粒/克拉-15粒/克拉 卡邦(Carnon)、伯尔兹(Boarz)、巴拉斯(Ballas)、刚果金刚石 PDC(钴粘合、与碳化钨结合) 特点:抗磨性和强度,要高于天然金刚石,但是抗冲击的能力差 TSP(滤钴粘合)巴拉斯钻头 特点:耐磨性高于PDC钻头,抗冲击能力强
屑 槽
槽、排屑槽)、保径刃和切削刃等部分 钢体
组成。
三、金刚石钻头和刮刀钻头
1、金刚石钻头的总体结构
(1)钻头体,钢制材料,连接钻柱
冠部
胎体
金刚石钻进

金刚石钻进第一节合理选择金刚石钻头金刚石钻头是目前最锐利的钻岩工具,从理论上讲它应该可以顺利地钻进各类地层,但在实践中往往出现一些反常现象:如在某些地层中,钻头金刚石耗量很大而钻头进尺很少;在另一些地层中,钻头的钻速很低,甚至出现钻头"打滑"不进尺的情况;有时某种钻头在一个矿区钻效很高,而在另一个矿区却效果很差。
这些现象归结起来说明一个问题,金刚石钻进中所选用的钻头必须和所钻的岩性相适应,这是提高金刚石钻进技术经济指标的关键环节之一。
尤其是孕镶金刚石钻头的结构参数较为复杂,选择时应根据所钻岩层性质综合考虑到金刚石品级、胎体性能(保证钻头自锐)、唇面形状、内外径补强和水路设计等因素。
金刚石钻进规程参数:评定金刚石钻进规程的主要依据是钻速、钻头总进尺和单位进尺的金刚石耗量三个指标。
图5-7 钻压对钻速和金刚石耗量的影响1. 钻压钻压与钻速和金刚石耗量的关系曲线如图5-7所示,可分为三个区:Ⅰ区为表面研磨破碎,钻速极低;Ⅱ区为疲劳破碎,依靠多次重复使裂纹扩展才能破碎岩石;Ⅲ区为体积破碎区,钻速随钻压增长很快,但单位进尺的金刚石耗量也增长很快。
图中显示,过大的钻压将使金刚石耗量急剧增大,并导致钻速有所下降,因此建议取钻压值在图中的最优区内。
1.1 表镶金刚石钻头的钻压PP=Gp (dN) (5-19)式中: G--钻头上的金刚石粒数;p--单粒金刚石上允许的压力,dN/粒。
细粒金刚石:p≈1.0~1.5dN/粒;中粒金刚石:p≈1.5~2.0dN/粒;粗粒金刚石:p≈2.0~3.0dN/粒;特优质级金刚石:p≈5.0dN/粒;1.2 孕镶金刚石钻头的钻压WW=Fq (dN) (5-20)式中: F--钻头实际工作唇面面积,cm2;q--单位底唇面面积上允许的压力,dN/cm2。
中硬岩石:q≈40~50 dN/cm2;坚硬岩石或金刚石质量高者:q≈60~70 dN/cm2。
表5--3列出了不同类型金刚石钻头推荐采用的钻压值,可供选择时参考。
第1章 金刚石钻头基本知识汇总

第一章金刚石钻头基本知识第一节概述1.1金刚石钻头的发展历史金刚石钻头是不同于牙轮钻头的另一类钻井破岩工具,其使用可以追溯到19世纪60年代。
最初人们以天然金刚石为切削元件制作打炮眼和挖掘隧道的工具,后来出现了用于石油钻井的钢体鱼尾式天然金刚石全面钻进钻头和取心钻头。
早期的金刚石钻头是将天然金刚石冷镶在低碳钢上的。
由于天然金刚石来源有限,价格昂贵,加之本身尺寸、性能方面的原因以及当时落后的制造工艺,大大限制了金刚石钻头在石油钻井工业中的应用。
随着粉末冶金技术的发展,出现了采用烧结碳化钨作为钻头体的胎体式金刚石钻头。
这种技术的出现使金刚石钻头的制造水平大大提高。
胎体式金刚石钻头具有耐冲蚀、耐磨损的特点,具有良好的使用性能,其制造工艺也不复杂,因此一经出现就迅速推广开来。
人造聚晶金刚石的研制成功,对金刚石钻头技术的发展起了巨大的推动作用。
人造聚晶金刚石复合片钻头(PDC钻头)的出现一度被称为20世纪80年代钻井工业技术的一大突破,这种新技术对石油钻井业的发展产生了巨大的影响。
现场使用证明,软到中等硬度地层钻井用PDC钻头具有机械钻速高、进尺多、寿命长、工作平稳、井下事故少、井身质量好等优点,并能与井下动力钻具配合用于高速钻井。
合理使用金刚石钻头可以大大缩短建井周期,降低钻井成本,提高钻井经济效益。
1.2金刚石钻头的发展前景经过近二十多年的发展,金刚石钻头已经成为继牙轮钻头之后的又一重要破岩工具。
时至今日,PDC钻头在石油钻头市场所占的份额越来越大,几乎每年以30%的速度侵吞牙轮钻头市场。
随着新的设计理论、设计方法和材料等技术的发展,PDC钻头的适用范围也在不断扩展,以前被认为不适用于PDC钻头的地层现在也广泛使用,比如我国中原油田的文留区块的沙二至沙三地层由于地质情况复杂、夹层多,可钻性差,以前一直被认为是PDC钻头的禁区,在这里钻的井除了取心之外用的都是牙轮钻头。
可是从2000年开始,PDC钻头在这个区块的使用量逐渐增多,效果也很好,而2001年底我公司的一只8 1/2 BK542-4型PDC钻头更在该区块的文-133井创下了1600米(东营组)入井,打到3390米(沙三上)完井,纯钻时间227.31小时,进尺1790米,平均机械钻速7.9米的好指标。
你必须掌握的钻头知识(基础、易懂、珍藏版)

你必须掌握的钻头知识(基础、易懂、珍藏版)钻头分类按类型可分为刮⼑钻头、⽛轮钻头、⾦刚⽯钻头和PDC钻头等四种;按功⽤分为全⾯钻进钻头、取⼼钻头和特殊⼯艺⽤钻头(⽐如扩眼钻头、定向造斜钻头等)。
刮⼑钻头刮⼑钻头是旋转钻井使⽤最早的⼀种钻头,从⼗九世纪开始采⽤旋转钻井⽅法的时候就开始使⽤这种钻头,⽽且直到现在某些油⽥仍在使⽤。
这种钻头主要⽤在软地层和粘软地层,具有很⾼的机械钻速和钻头进尺。
刮⼑钻头最⼤的优点是结构简单,制造⽅便,成本低,各油⽥可⾃⾏设计和制造。
1)刮⼑钻头的结构刮⼑钻头由钻头体、刮⼑⽚、分⽔帽和喷嘴四部分组成。
钻头体是刮⼑钻头焊接刮⼑⽚和分⽔帽的本体,采⽤中碳钢材料加⼯⽽成。
下端焊接刮⼑⽚和分⽔帽,上端车有丝扣和钻柱连接。
刮⼑⽚⼜称⼑翼,是刮⼑钻头主要⼯作部件。
2)刮⼑钻头⼯作原理刮⼑钻头以切削⽅式破碎岩⽯。
刮⼑钻头在软的塑性地层⼯作时,其切削过程类似于⼑具切削软⾦属。
⼑⽚在钻压的作⽤下吃⼊地层,与此同时⼑刃前⾯的岩⽯在扭转⼒的作⽤下不断产⽣塑性流动,井底岩⽯被层层剥起。
刮⼑钻头钻进脆性较⼤的地层时,破碎岩⽯的过程则分为碰撞、压碎及⼩剪切和⼤剪切三个阶段:碰撞:刃前岩⽯破碎后,岩⽯对⼑⽚的扭转阻⼒减⼩,⼑⽚向前推进,碰撞刃前岩⽯;压碎及⼩剪切:⼑⽚在扭转⼒作⽤下压碎前⽅的岩⽯,使其产⽣⼩剪切破碎;扭转⼒增⼤:⼑⽚继续挤压前⽅岩⽯,当扭转⼒增⼤到极限值时,岩⽯沿剪切⾯产⽣⼤剪切破碎,然后扭转⼒突然减⼩。
碰撞、压碎及⼩剪切、⼤剪切这三个过程反复进⾏,形成刮⼑钻头破碎塑脆性岩⽯的全过程。
3)刮⼑钻头的正确使⽤刮⼑钻头适⽤于软地层和粘软地层。
钻进时需要适当控制钻压与转速,注意防斜、防蹩、防⽌⼑翼断裂。
由于刮⼑钻头在软地层中的机钻速较快,岩屑量较⼤,宜采⽤⼤排量钻进,充分清洗井底和冷却钻头。
刮⼑钻头钻进时,⼑翼外侧线速度较⾼,磨损速度较快,钻头容易磨损成锥形,此时要特别注意防斜和防⽌井径缩⼩。
- 1、下载文档前请自行甄别文档内容的完整性,平台不提供额外的编辑、内容补充、找答案等附加服务。
- 2、"仅部分预览"的文档,不可在线预览部分如存在完整性等问题,可反馈申请退款(可完整预览的文档不适用该条件!)。
- 3、如文档侵犯您的权益,请联系客服反馈,我们会尽快为您处理(人工客服工作时间:9:00-18:30)。
第一章金刚石钻头基本知识第一节概述1.1金刚石钻头的发展历史金刚石钻头是不同于牙轮钻头的另一类钻井破岩工具,其使用可以追溯到19世纪60年代。
最初人们以天然金刚石为切削元件制作打炮眼和挖掘隧道的工具,后来出现了用于石油钻井的钢体鱼尾式天然金刚石全面钻进钻头和取心钻头。
早期的金刚石钻头是将天然金刚石冷镶在低碳钢上的。
由于天然金刚石来源有限,价格昂贵,加之本身尺寸、性能方面的原因以及当时落后的制造工艺,大大限制了金刚石钻头在石油钻井工业中的应用。
随着粉末冶金技术的发展,出现了采用烧结碳化钨作为钻头体的胎体式金刚石钻头。
这种技术的出现使金刚石钻头的制造水平大大提高。
胎体式金刚石钻头具有耐冲蚀、耐磨损的特点,具有良好的使用性能,其制造工艺也不复杂,因此一经出现就迅速推广开来。
人造聚晶金刚石的研制成功,对金刚石钻头技术的发展起了巨大的推动作用。
人造聚晶金刚石复合片钻头(PDC钻头)的出现一度被称为20世纪80年代钻井工业技术的一大突破,这种新技术对石油钻井业的发展产生了巨大的影响。
现场使用证明,软到中等硬度地层钻井用PDC钻头具有机械钻速高、进尺多、寿命长、工作平稳、井下事故少、井身质量好等优点,并能与井下动力钻具配合用于高速钻井。
合理使用金刚石钻头可以大大缩短建井周期,降低钻井成本,提高钻井经济效益。
1.2金刚石钻头的发展前景经过近二十多年的发展,金刚石钻头已经成为继牙轮钻头之后的又一重要破岩工具。
时至今日,PDC钻头在石油钻头市场所占的份额越来越大,几乎每年以30%的速度侵吞牙轮钻头市场。
随着新的设计理论、设计方法和材料等技术的发展,PDC钻头的适用范围也在不断扩展,以前被认为不适用于PDC钻头的地层现在也广泛使用,比如我国中原油田的文留区块的沙二至沙三地层由于地质情况复杂、夹层多,可钻性差,以前一直被认为是PDC钻头的禁区,在这里钻的井除了取心之外用的都是牙轮钻头。
可是从2000年开始,PDC钻头在这个区块的使用量逐渐增多,效果也很好,而2001年底我公司的一只8 1/2 BK542-4型PDC钻头更在该区块的文-133井创下了1600米(东营组)入井,打到3390米(沙三上)完井,纯钻时间227.31小时,进尺1790米,平均机械钻速7.9米的好指标。
现在,在该区块只要条件允许,几乎用的都是PDC钻头。
第二节金刚石钻头的结构简介2.1金刚石钻头的破碎机理金刚石钻头的破岩方式主要有四种,即:剪切、预破碎(开槽效应)、犁削及磨削。
2.1.1 剪切岩石破碎力学的研究表明,岩石的抗剪强度比其抗压强度要低得多,两者的比值在0.09~0.15左右。
显然,采用剪切方式破碎岩石比用压碎方式破碎岩石要容易而且有效得多。
PDC钻头的复合片正是利用了岩石的这一力学特性,采用高效的剪切方式来破碎岩石,从而达到快速钻井的目的。
当PDC钻头工作时,复合片在钻压和扭矩的作用下克服地层应力切入地层并向前滑动,岩石在切削齿的作用下沿其剪切方向破碎并产生塑性流动,切削所产生的岩屑呈大块片状。
这一切削过程与刀具切削金属材料非常相似。
2.1.2 预破碎(开槽效应)预破碎(开槽效应)是采用特殊的“尖/圆”齿交替布置切削结构所具有的岩石破碎方式,主要用在以纯剪切方式不容易钻进的地层,如具有一定塑性的地层。
预破碎过程是通过开槽切削来完成的,具有这种切削结构的钻头在钻进过程中,尖形齿因与地层接触面积小受力集中而先行切入地层,岩石在接触应力的作用下产生破碎裂纹,随着钻头的不断旋转,尖形齿在岩石中切出一条条较小的环状“卸荷槽”,使地层应力预先释放,而紧随其后的圆形切削齿则以剪切方式切削其强度已大大减弱的大块岩石,达到快速钻进的目的。
这样大大提高了切削效率,降低了切削齿的磨损速度。
2.1.3犁削天然金刚石钻头和TSP钻头在钻进塑性地层时,常常以犁削方式来破碎岩石。
岩石在钻头钻进过程中,由于受到切削齿的作用,在其内部发生破碎并向表面传递。
堆积在切削齿前面的破碎岩屑由于切削齿的移动被推向两边,最后由泥浆带出井底,这一切削过程相似于犁地过程。
2.1.4磨削天然金刚石钻头和TSP钻头在钻进极硬的粗晶粒地层时,切削齿克服岩石的高抗压强度实现岩石的局部破碎。
即其切削结构常常以磨削方式破碎岩石。
由于硬地层岩石的高强度,使破碎的岩屑比较小,呈细粒状,因而钻头的机械钻速相应较低。
2.2金刚石钻头结构介绍金刚石钻头属一体式钻头,整个钻头没有活动零部件,结构比较简单。
主要由上体、钢图1心、胎体、切削齿、喷嘴及密封件组成。
见图1钻头上体是经过热处理的钢制件,其上端车有API标准连接螺纹,用以和其它井下钻具相连。
上体下端与钻头体上的钢心通过焊接而构成一个整体。
上体上部两个对称槽为钻头卸扣槽,用于和卸扣板相配合来装卸钻头。
钢心是位于钻头中心的空心钢体,是钻头体的骨架,它的一端与碳化钨胎体烧结在一起,另一端则与上体焊接相连。
胎体是碳化钨粉末经过烧结而形成的具有不同轮廓形状的钻头基体。
胎体粘附在钢心上,构成坚韧的、抗冲击、耐磨损的钻头体(冠部)。
切削齿可以采用天然金刚石、TSP齿及PDC齿。
天然金刚石和TSP齿通过烧结直接固结到钻头胎体上,PDC钻头的切削齿则通过低温钎焊固定到钻头胎体上。
钻头所采用的喷嘴为可换式硬质合金整体喷嘴,主要有标准喷嘴和内六方孔小喷嘴两种。
标准喷嘴的水孔出口截面为圆形,内六方小喷嘴水孔截面则为六边形,这种结构的水孔,既可作为泥浆流道,又可用于喷嘴安装。
喷嘴中心水孔有各种不同的尺寸以满足不同的钻井需要。
喷嘴与喷嘴座之间采用“O”形橡胶密封圈密封,以保证其使用安全可靠。
从设计和使用的角度,钻头又可分为上体和钻头体两大部分。
钻头体包括钻头冠部轮廓、切削结构、水力结构、保径结构等。
钻头轮廓指胎体表面形状,不同的钻头轮廓形状适应于不同的地层钻井。
切削结构即由不同类型的金刚石齿以一定的布齿密度和布齿方式布置在钻头表面用以切削地层的工作部分。
钻头水力结构是用以控制和分配钻井液,为钻头提供充分的冷却、清洗及排屑的部分。
它包括水孔、主流道、副流道、排屑槽和集屑槽等。
天然金刚石钻头和TSP钻头的水孔结构一般为鸦爪式中心水孔,PDC钻头的水孔则一般采用可换式喷嘴。
钻头保径结构为钻头提供良好的扶正和保径作用,以保证钻头的正常钻进和较长的工作寿命。
2.3金刚石钻头分类关于金刚石钻头的分类,按用途分,可分为全面钻进钻头和取心钻头;按钻头体材料及制造方式分,可分为钢体钻头和胎体钻头;按切削齿材料分,可分为PDC钻头、TSP钻头、天然金刚石钻头。
胎体金刚石钻头具有固齿牢靠、钻头体抗冲蚀能力强、耐磨性好、钻头寿命长、钻头结构设计灵活、产品制造周期短、非标尺寸钻头制造容易等优点,在金刚石钻头市场上占绝大多数,为目前各生产厂家广泛应用。
天然金刚石(ND)钻头以优质天然金刚石作为切削刃,以表镶方式将其直接烧结在抗冲蚀、耐磨性好的碳化钨胎体上。
切削结构选用不同粒度金刚石,采用不同的布齿密度和布齿方式,以满足在中至坚硬地层钻井的需要。
TSP钻头切削元件采用了各种不同形状并具有自锐作用的热稳定聚晶金刚石(TSP)齿。
与天然金刚石相比,这种TSP持具有良好的耐热性,可耐1200摄氏度的高温,抗破碎性及耐磨性俱佳。
TSP钻头与天然金刚石钻头一样,其切削齿直接烧结在碳化钨胎体上。
TSP钻头更适合于在带有研磨性的中等至硬地层快速钻井。
PDC钻头采用聚晶金刚石复合片(PDC片)作为切削刃,以钎焊方式将其固定到碳化钨胎体上的预留齿穴中。
钻头所采用的PDC切削齿具有高强度、高耐磨性和抗冲击能力,且切削刃口和刃面都具有良好的自锐性,在钻进过程中切削刃能始终保持锋利。
钻头在软到中等硬度地层中以剪切方式破碎岩石,采用较小钻压即可获得较高的机械钻速,是一种高效钻井钻头。
第三节金刚石钻头的设计与制造3.1金刚石钻头的设计理论在常规的PDC钻头切削结构设计中,遵循的基本原理有如下几条:①、每个切削齿的切削体积相等,即等体积原则;②、每个切削齿的磨损速度相等,即等磨损原则;③、每个切削齿的切削功率相等,即等功率原则;④、每个切削齿的切削面积相等,即等面积原则。
最常用的设计理论有:力平衡理论和抗回旋理论。
3.1.1、力平衡PDC钻头1)钻头的受力分析PDC钻头在正常钻进时,同时受到钻压和旋转设备施加的扭矩的作用。
在这两个力的作用下,每个切削齿都受到一个法向力Fn和一个切向力(周向力)Fc的作用。
其中法向力Fn 由钻压产生,它是使切削齿穿透岩石所需的力;切向力Fc是在法向力将切削齿压入岩石后沿切口向前推进切削齿所需的力,即将岩屑从岩石上剥离下来所需的力。
法向力Fn能分解成一个垂直分力Fv和一个径向分力Fr。
切向力Fc能分解为一个径向分力和一个绕着钻头中心的力矩。
作用在钻头上且位于垂直钻头旋转轴线的平面内的法向力和切向力能分解为一个作用于钻头中心上的力和一个力矩,它们均位于法向平面内。
该力矩是旋转钻头所需的力矩,而该力则是侧向不平衡力。
这个侧向不平衡力指向与钻头面相关的一个方向,在钻头旋转时,它趋向于把钻头推向井壁。
由于侧向不平衡力的大小、方向都不受控制,所以很难保证钻头的力学性能良好。
由于力学性能差,将会直接导致钻头的运动学性能变差。
由于其所受侧向不平衡力较大,当钻头在井底钻进时,钻头被推向井壁。
这时,钻头上的保径齿以及部分外排齿在侧向不平衡力的推动下会吃入井壁,与井壁的岩层产生“啮合效应”。
此时钻头不再平滑钻进,而开始产生侧向振动,PDC钻头上的切削齿会横向向后移动,并且比正常旋转的钻头上的切削齿运动快得多,伴随这种运动的冲击载荷会引起PDC切削齿的破碎,而这种破碎反过来会导致加速磨损,并且切削齿破碎后产生的碎片会对其它完好的PDC切削齿产生冲击碰撞,从而导致大面积的切削齿损坏。
对于力平衡钻头来说,由于侧向不平衡力被控制在一个极小的范围之内,它对PDC钻头的影响就比普通PDC钻头要小得多。
在经过调整之后,钻头上的各个力的大小及方向都发生了很大的变化。
侧向不平衡力Fimb由原来的9.2%降至了1.4%(这一百分比是侧向不平衡力与钻压的比值)。
径向力Fr与切向力Fc大小基本相等。
整个钻头的受力情况处于一个良好的状态。
3.1.2抗回旋PDC钻头通过对钻头的切削齿进行受力分析,运用调整齿位的办法,使得钻头的侧向合力指向较大面积的低摩阻保径垫,在钻头工作时该保径垫始终与井壁接触,最终使钻头的回旋程度降到最低,保证钻头工作平稳,延长钻头的使用寿命。
需要指出的是,力平衡技术、抗回旋技术只是PDC钻头设计制造技术的一个方面,要设计出性能优良的PDC钻头,光靠这一点是远远不够的。
在发展这项技术的同时,还需要合理的水力分布、先进的PDC切削齿、优选钻头轮廓等许多方面技术的运用。
3.2金刚石钻头冠部轮廓设计与选择依据研究及现场试验表明,钻头冠部形状对其使用性能具有较大影响。