管道深度预制方案
管道预制施工方案

中国南京YPC/BASF一体化石油化工基地基础化学联合装置60万吨/年乙烯装置管道预制施工方案中国石化集团第四建设公司扬巴乙烯工程项目经理部目录1 编制说明 (1)2 编制依据 (1)3 工程特点 (1)4 预制范围 (1)5 质量目标 (2)6 预制厂资源装备 (2)7 管道工厂化预制施工工艺设计 (4)8 管道预制工厂化施工方案 (9)9 管道预制技术管理 (17)10 管道预制质量管理 (18)11 管道预制施工管理 (18)12 材料管理 (21)13 HSE管理 (23)13 预制厂平面布置图 (25)1编制说明本施工方案适用于扬巴乙烯装置管道预制的施工.针对扬巴乙烯装置管道安装、焊接工程量大等特点,为充分发挥我公司现有的长芦预制厂(月平均加工能力15万寸D)的作用,采取深度预制的工厂化施工技术,并运用我公司开发的管道施工管理软件,科学、有效地搞好管道施工管理,解决工期、场地和施工的矛盾,减少现场焊接工作量,提高工程施工质量,加快现场施工进度,充分发挥设备、人员等使用效率,使管道的总体预制深度达到65%以上,特制定本方案。
2编制依据2.1施工及验收规范S&W规格书PS-C113—R.1ASME B31。
3 2001《石油化工工程建设交工技术文件规定》SH3503—2001《石油化工施工安全技术规程》SH3505—19993工程特点1)乙烯装置管道安装工程量大,平均口径大,相对焊接工作量大;2)管道材质种类多;3)SS超高压管道壁厚较大,施工工序多,周期长,必须加强预制深度,尽量减少现场焊接作业工作量;4)管道支架种类多,型式多样,必须集中统一制作;管支架符合设计及SW规格书要求。
4预制范围1)1—1/2″及以上直径的工艺管道及公用工程管道,包括阀组、框架及设备配管、管廊膨胀弯等,主要型式有:直管—弯头—法兰、法兰-直管—弯头—直管、弯头—直管—三通—直管、弯头—直管—异径管—法兰等;2)管道支架,包括管托、承重及导向组合支架(带位号)、垫板、管式支架等;3)直径小于1—1/2″、但焊口相对集中的管段,如伴热分配管、伴热煨弯、燃烧器配管、阀组、小型设备及炉子附属成批小管线等。
不锈钢管道预制施工方案.docx

.一、 Purpose 目的This statement is compiled to ensure the construction quality of Bayer project pipe fabrication and meet the progress requirement.This statement is used to guide the fabrication of all Stainless Steelpipe afforded by CNF in Bayer MDI 。
为了保证项目管道预制工程的施工质量和满足工程进度要求,特编制本方案。
本方案用以指导拜耳异氰醋酸聚醚项目 MDI联合装置内 CNF承担的所有不锈钢材质管道的预制施工。
二、 Applicable Scope适用范围This statement is applicable for all Stainless Steel pipe fabricationwork afforded by CNF in Bayer MNB(V210) / WNILINE(V310).本方案适用于拜耳项目MNB(V210)/WNILINE(V310)装置内 CNF承担的所有不锈钢管道预制工程的施工。
三、 Reference编制依据Technical specification and standard of this method statement:本方案编制依据的施工技术规范和标准为:(1) GB50235-97《construction and acceptance of industrial metal pipe project ≥ GB50235-97 《工业金属管道工程施工及验收规范》(2) GB50236-98《welding project construction and acceptancespecification of site equipment and industrial pipe》GB50236-98 《现场设备工业管道焊接工程施工及验收规范》(3) Bayer relevant technical document standard拜耳的相关技术资料(WN标准)(4)管道相关图纸四、 Overview 工程概况1Work scope 工作范围The scope of this project includes all Stainless Steel pipe fabrication of MNB/ANILINE包括 MNB 、ANILINE 两个装置中的所有不锈钢管道的预制。
管道深基坑专项方案

一、工程概况本工程为管道深基坑施工项目,基坑开挖深度为15米,周长200米,面积3000平方米。
基坑位于城市中心区域,周边环境复杂,需确保施工安全、质量、进度及环保要求。
二、编制依据1. 《建筑地基基础工程施工质量验收规范》(GB 50202-2002)2. 《混凝土工程施工质量验收规范》(GB 50204-2002)3. 《建筑基坑支护技术规程》(JGJ 120-99)4. 《钢筋焊接及验收规程》(JGJ 18-2003)5. 《建筑安装工程质量检验评定统一标准》(GB50300-2001)6. 《建筑工程施工测量规范》(DBJ01-21-95)7. 《建筑机械使用安全技术规程》(JGJ33-2001)8. 《施工现场临时用电技术规范》(JGJ46-2005)9. 《混凝土质量控制标准》(GB50164-92)10. 《施工现场临时用电安全技术规范》(JGJ46-2005)11. 《建筑边坡工程技术规范》(GB50330-2002)12. 《岩土锚杆(索)技术规程》(CECS-22:2005)13. 《锚杆喷射混凝土支护技术规范》(GB50086—2001)三、施工准备1. 组织管理:成立项目领导小组,明确各部门职责,确保施工顺利进行。
2. 人员配置:根据施工需求,合理配置施工人员,包括技术人员、施工人员、安全管理人员等。
3. 材料设备:提前采购所需材料,确保材料质量符合规范要求。
同时,准备好施工设备,如挖掘机、吊车、混凝土搅拌车等。
4. 施工现场布置:按照施工组织设计,合理布置施工现场,确保施工区域、材料堆放区、办公区、生活区等区域划分明确。
四、施工工艺技术1. 基坑支护:采用排桩支护结构,桩径为800mm,桩间距为1.5米,桩长根据地质条件确定。
2. 土方开挖:采用分层开挖方式,每层厚度不超过1.5米,确保土方开挖安全。
3. 混凝土浇筑:采用商品混凝土,按照设计要求进行浇筑,确保混凝土强度和质量。
管道预埋施工方案
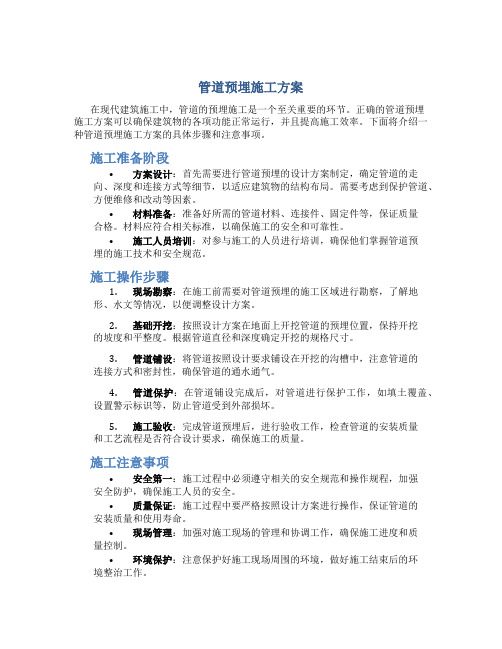
管道预埋施工方案在现代建筑施工中,管道的预埋施工是一个至关重要的环节。
正确的管道预埋施工方案可以确保建筑物的各项功能正常运行,并且提高施工效率。
下面将介绍一种管道预埋施工方案的具体步骤和注意事项。
施工准备阶段•方案设计:首先需要进行管道预埋的设计方案制定,确定管道的走向、深度和连接方式等细节,以适应建筑物的结构布局。
需要考虑到保护管道、方便维修和改动等因素。
•材料准备:准备好所需的管道材料、连接件、固定件等,保证质量合格。
材料应符合相关标准,以确保施工的安全和可靠性。
•施工人员培训:对参与施工的人员进行培训,确保他们掌握管道预埋的施工技术和安全规范。
施工操作步骤1.现场勘察:在施工前需要对管道预埋的施工区域进行勘察,了解地形、水文等情况,以便调整设计方案。
2.基础开挖:按照设计方案在地面上开挖管道的预埋位置,保持开挖的坡度和平整度。
根据管道直径和深度确定开挖的规格尺寸。
3.管道铺设:将管道按照设计要求铺设在开挖的沟槽中,注意管道的连接方式和密封性,确保管道的通水通气。
4.管道保护:在管道铺设完成后,对管道进行保护工作,如填土覆盖、设置警示标识等,防止管道受到外部损坏。
5.施工验收:完成管道预埋后,进行验收工作,检查管道的安装质量和工艺流程是否符合设计要求,确保施工的质量。
施工注意事项•安全第一:施工过程中必须遵守相关的安全规范和操作规程,加强安全防护,确保施工人员的安全。
•质量保证:施工过程中要严格按照设计方案进行操作,保证管道的安装质量和使用寿命。
•现场管理:加强对施工现场的管理和协调工作,确保施工进度和质量控制。
•环境保护:注意保护好施工现场周围的环境,做好施工结束后的环境整治工作。
综上所述,管道预埋施工是一个需要细心、认真和规范操作的工程环节。
只有严格遵守施工方案,加强现场管理和质量控制,才能确保管道预埋施工的顺利完成,并为建筑物的正常使用提供有力保障。
管道预埋施工方案

管道预埋施工方案1. 引言管道预埋施工是一种常见的管道安装方式,通过提前将管道埋入地下,有效地保护了管道的安全和稳定性。
本文档将介绍管道预埋施工的步骤和注意事项,以便工程人员正确、高效地进行施工。
2. 施工步骤2.1 方案设计在进行管道预埋施工前,需要制定详细的方案设计。
方案设计包括以下内容:•管道材料选择:根据实际情况和需求,选择适当的管道材料,如PVC、HDPE等。
•管道布置方案:根据场地情况和管道用途,确定管道的布置方案,包括管道的走向、坡度等。
•施工工艺和流程:制定详细的施工工艺和流程,包括开挖、敷设管道、连接管道等。
2.2 场地准备在施工前,需要对施工场地进行准备工作。
具体步骤如下:1.清理场地:清除场地上的杂物和障碍物,确保施工区域的平坦和整洁。
2.定位标识:根据方案设计的要求,在场地上进行标识,确定管道的走向和位置。
3.地质勘测:进行地质勘测,了解地下情况,避免施工中出现地质灾害。
2.3 开挖在场地准备完成后,进行开挖工作。
具体步骤如下:1.根据方案设计要求,使用挖掘机进行开挖,确保开挖的深度和宽度符合设计要求。
2.开挖过程中,需要注意低洼地带的排水,避免因地下水造成施工困难。
3.开挖完毕后,对开挖的土壤进行分类和处理,避免对环境造成污染。
2.4 敷设管道开挖完成后,开始进行管道的敷设工作。
具体步骤如下:1.清理开挖区域:清理开挖区域的杂物,确保敷设的地面平整。
2.基础处理:根据管道类型和设计要求,对敷设区域的基础进行处理,如加铺砂浆等。
3.敷设管道:按照方案设计的要求,将管道放置在敷设区域,并进行必要的连接和固定。
2.5 管道连接和测试在敷设管道完成后,进行管道的连接和测试。
具体步骤如下:1.连接管道:根据方案设计要求,对管道进行连接,包括弯头、三通等。
2.测试管道:对管道进行测试,包括压力测试和泄漏测试,确保管道的安全性和完整性。
3.修复和调整:如果测试中出现问题,需要进行修复和调整,确保管道达到设计要求。
管道预埋工程施工方案

管道预埋工程施工方案一、工程概况管道预埋工程是指在地面、桥梁、隧道、河道、马路等交通要道挖掘、敷设管线,为城市供水、供气、供暖、电力等基础设施提供保障的一项重要工程。
其施工需要综合考虑地下管线的走向、材质、埋设深度、施工方法等因素,确保管线敷设质量和工程安全。
本文以某城市供水管道预埋工程为例,对其施工方案进行详细阐述,以期为类似工程提供借鉴和参考。
二、工程内容本次供水管道预埋工程涉及路面、人行道等多个区域,共计预埋供水管道1000米,其中包括主水管、支线管及相关附属设施。
具体工程内容如下:1. 地面勘察:对工程区域进行全面勘察,确定地下管线走向、深度、地质条件等情况。
2. 管线设计:根据勘察结果和城市规划要求,设计管线敷设方案和材料选型。
3. 施工准备:准备施工所需的设备、材料、人员等资源。
4. 施工过程:挖掘、敷设管道、连接管线、地下设施回填等工作。
5. 工程验收:对已完成的管道预埋工程进行验收,确保工程合格、安全。
三、施工准备1. 设备准备:挖掘机、钻孔机、管线敷设机、起重机等大型设备,以及安全帽、安全绳等个人防护用品。
2. 材料准备:防腐保护材料、管道材料、接头、密封胶等管线施工所需的各种材料。
3. 人员准备:具备相应证书和工作经验的挖掘机操作员、管道工、安全员等人员。
4. 动力准备:接通施工区域的电力、水源等基础设施,确保施工进行顺利。
四、施工过程1. 地面勘察在施工前,首先对预埋管道的敷设区域进行全面勘察,准确了解地下管线的走向、深度、地质条件等情况,制定合理的施工方案。
2. 管线设计根据勘察结果和城市规划要求,设计管线敷设方案和材料选型。
合理布局管线走向,保障供水管道的正常运行。
3. 施工准备确定了施工方案后,开始准备施工所需的设备、材料、人员等资源。
4. 施工过程(1)挖掘:根据设计要求,在地下挖掘管道敷设的沟槽,保持沟槽的纵横坡和平整度。
(2)敷设管道:将预制好的管道逐段敷设于挖掘好的沟槽中,确保管道的平整和牢固。
直埋式预制保温管施工

2.直埋式预制保温管施工方案直埋式预制保温管是一种用于在埋地管道中提供热传导保温的设备。
它具有安装方便、热损失小、耐久性好等特点,被广泛应用于给水、给气、给热等管道的保温工程中。
2.1施工准备预制保温管及配件:根据工程需要,采购符合相关标准要求的预制保温管和配件。
根据图纸,确定管道的走向、施工断面等。
清理施工区域,确保施工区域无障碍物。
安排好施工人员,分工合作。
2.2施工步骤(1)管槽开挖1)放线:首先进行放线,确定管道走向和建筑物位置,对管槽预期暂时的占地范围进行划定,包括管槽底坡脚线和开挖线,对控制高程进行预设和检查。
管道测量放线,分为纵向放线和横向放线。
纵向放线确定管道沟中心线的平面位置和设置高程控制点。
横向放线任务是确定管槽横断面的空间位置,找出挖填起点,并钉置边桩。
2)人工开挖管槽:采用台阶式分层开挖,开挖程序是先挖台阶后削坡,初挖断面应略小于设计断面,经校核无误后再行修整。
控制沟底高程的简单办法是“三棍法”,即用三根长度相等的棍,将其中两根放在两个中心桩处沟底的设计高程上,然后在两桩间的中心线上移动第三根棍;用眼瞄棍顶,如棍顶超过视线,说明沟底挖深不足;棍顶低于视线,说明沟底挖得太多;棍顶正落在视线上,说明沟底挖得恰好。
3)机械开挖一般用反铲挖掘机,顺管槽方向边推边挖,先挖中间部位土方,而后向两边扩挖,最后进行修整。
管道开挖断面采用梯形断面,要求沟线顺直,沟底平整。
挖土尽量堆放在沟槽的同一侧,以利于管道安装施工。
沟底修整及底部保护层由人工完成,开挖沟槽同时安装管道,如有局部超挖,应以同类土回填。
4)管沟的挖掘,须依照管线设计线路正直平整施工,不得任意偏斜曲折,而管线如必须弯曲时,其弯曲角度应按照管子每一承口允许弯折的角度进行。
5)管沟挖掘,应视土壤性质,作适当的斜坡,以防止崩塌及发生危险,如在规定的深度,发现砾石层或坚硬物体时,须加挖深度10㎝,以便于配管前的填砂,再行放置管材。
6)土质较松软的外,应作挡土设施,以防崩塌,管底并须夯实。
管道深基坑开挖专项施工方案
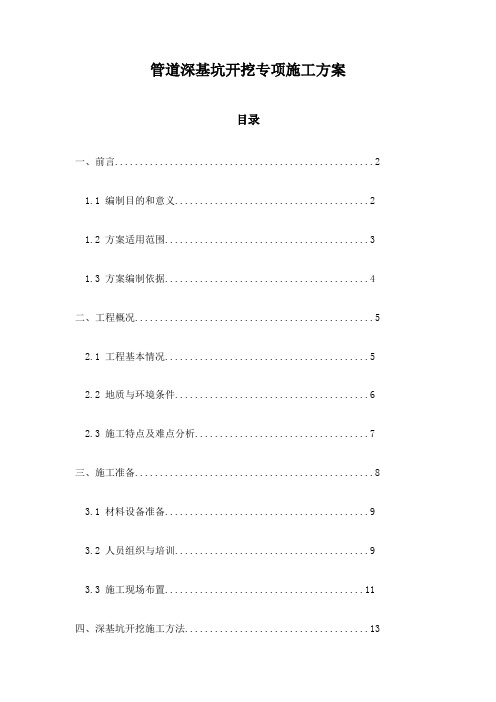
管道深基坑开挖专项施工方案目录一、前言 (2)1.1 编制目的和意义 (2)1.2 方案适用范围 (3)1.3 方案编制依据 (4)二、工程概况 (5)2.1 工程基本情况 (5)2.2 地质与环境条件 (6)2.3 施工特点及难点分析 (7)三、施工准备 (8)3.1 材料设备准备 (9)3.2 人员组织与培训 (9)3.3 施工现场布置 (11)四、深基坑开挖施工方法 (13)4.1 开挖顺序与流程 (13)4.2 边坡支护方案 (14)4.3 开挖机械选择与使用 (16)4.4 挖掘过程中的监控与安全措施 (17)五、土方开挖与管理 (18)5.1 土方开挖顺序与方法 (20)5.2 土方运输方案 (21)5.3 施工现场土方管理 (22)六、质量与安全保证措施 (23)6.1 质量保证措施 (23)6.2 安全生产责任制 (24)6.3 安全防护设施及措施 (25)6.4 应急预案与救援措施 (26)七、环境保护与文明施工 (28)7.1 环境保护措施 (29)7.2 文明施工管理要求 (30)7.3 清洁与废弃物处理方案 (30)一、前言本工程为XXXXXX(工程名称)项目管道深基坑开挖专项施工方案,工程位于XXXXXX(工程地点),概况为在一层XXXXXX(基坑深度)的深度开挖建造XXXX(基坑用途)的深基坑。
该方案从项目背景、基坑设计特点、安全要求及施工原则等方面详细阐述施工的制定依据和目标,并围绕“安全第质量第效率第一”结合项目实际情况,制定了符合规范、科学合理的施工工艺和组织措施,旨在确保深基坑顺利开挖,为后续工程建设打下坚实基础。
1.1 编制目的和意义本管道深基坑开挖专项施工方案的编制旨在确保管道深基坑开挖施工过程中的安全性、施工效率和施工质量达到国家相关标准的规定,同时能够满足城市的建设和环境保护要求。
保障施工安全:深基坑施工复杂、风险高,通过对施工过程进行详细规划和安全措施的制定,能有效预防坍塌、触电等可能发生的安全事故。
管道布局预埋施工方案

管道布局预埋施工方案1. 方案背景该方案旨在为管道布局的预埋施工提供指导和解决方案,确保施工过程安全、高效、符合规范要求。
2. 施工前准备在施工前,需要进行以下准备工作:- 确定管道布局的设计图纸,包括管道的走向、连接点等。
- 清理施工区域,确保没有障碍物和妨碍施工的物品。
- 准备好所需的施工设备和工具,包括挖掘机、水平仪等。
3. 施工步骤根据管道布局设计图纸和实际情况,按照以下步骤进行施工:1. 使用挖掘机挖掘出管道的预埋沟槽,注意保持沟槽的平整和斜度。
2. 在沟槽底部垫设合适的填充物,如砂石等,以提供均匀的支撑和抗压能力。
3. 将管道逐段放入沟槽内,确保每段管道的连接部位处于沟槽的上方,以便日后连接。
4. 使用水平仪和测量工具确保管道的水平度和垂直度,必要时进行调整。
5. 逐段连接管道,使用合适的连接件和密封材料,确保连接牢固且密封可靠。
6. 检查每段管道的连接处及周围是否存在缺陷或损坏,如有需要及时修复或更换。
7. 完成管道布局的预埋施工后,进行必要的压力测试和检测,确保管道系统的安全性和耐久性。
4. 安全措施在进行管道布局的预埋施工时,需要注意以下安全措施:- 施工人员必须佩戴符合要求的安全防护用具,如安全帽、安全鞋等。
- 确保周边区域有足够的警示标识和隔离措施,以避免他人误入施工区域。
- 管道布局的预埋沟槽周边必须搭设足够的支护结构,防止沟槽塌方。
- 注意施工现场的通风和排水,避免积水和有害气体的堆积。
以上就是管道布局预埋施工方案的基本内容,希望能对您的工作有所帮助。
如有任何问题,请随时与我们联系。
管道管沟深开挖技术方案

管道管沟深开挖技术方案一、项目背景及目标深开挖技术在城市地下管道、地铁、隧道等工程中广泛应用,其安全、高效、环保的特点日益受到重视。
本项目旨在针对管道管沟深开挖工程,制定一套完整的技术方案,确保工程顺利进行,降低安全风险,提高施工效率。
二、工程概况1.工程地点:我国某城市地下管道工程2.工程规模:管道管沟长度约5公里,深度最大15米3.工程地质条件:以黏土、粉土、砂土为主,局部存在软土、硬土等特殊地质4.工程目标:确保工程安全、高效、环保完成三、技术方案1.施工方法(1)明挖法:适用于管沟较浅的工程,采用挖掘机、装载机等设备进行土方开挖,然后进行管道安装、回填等后续施工。
(2)暗挖法:适用于管沟较深的工程,采用盾构、顶管等设备进行施工。
暗挖法具有对周边环境影响小、施工速度快等特点。
2.深开挖施工技术(1)土方开挖:根据工程地质条件,采用分层开挖、分段施工的方法。
先进行表层土方开挖,然后逐层下挖,直至设计深度。
(2)支撑体系:根据开挖深度和地质条件,采用钢管、木支撑、钢板桩等材料进行支撑。
支撑体系应具备足够的强度、刚度和稳定性,确保施工安全。
(3)降水排水:采用排水井、排水管道、降水泵等设备,对施工区域进行降水排水,降低地下水位,防止土体流失和涌水现象。
(4)监测系统:安装监测设备,实时监测施工区域的地表沉降、地下水位、土体位移等参数,确保施工安全。
3.施工安全措施(1)安全培训:对施工人员进行安全培训,提高安全意识,确保施工过程中遵守安全操作规程。
(2)安全防护:施工现场设置安全警示标志,配备防护栏杆、安全网等防护设施。
(3)应急预案:制定应急预案,应对突发情况,确保施工安全。
四、施工进度安排1.工程准备阶段:完成施工图纸、施工方案、施工组织设计等文件的编制,办理相关手续,进行施工现场布置。
2.施工阶段:按照施工方案进行土方开挖、支撑体系施工、降水排水等工程,确保工程进度和质量。
3.竣工验收阶段:完成工程验收、资料整理、工程结算等工作。
管井管道施工方案

管井管道施工方案一、引言管井管道施工是水利工程中的重要环节,对于确保水利设施的正常运转和安全运行具有至关重要的作用。
本文将详细阐述管井管道施工的方案,包括施工准备、管道安装、质量检测与验收等环节,旨在为相关工程提供参考和指导。
二、施工准备1、现场勘查:在施工前,应对管井管道施工区域进行详细的现场勘查,了解现场的地形、地貌、水文等条件,以便为后续的施工提供准确的基础资料。
2、图纸设计:根据工程需求和现场实际情况,进行管井管道施工图纸设计,确定管道的材质、规格、埋深等参数,为施工提供详细的图纸指导。
3、材料采购:根据图纸要求,采购符合规格和质量要求的管材、阀门、附件等材料,确保施工过程中材料供应充足。
4、设备准备:根据施工需要,准备相应的施工设备,如挖掘机、起重机、焊机等,确保设备的性能良好,为施工提供有力的设备保障。
5、安全措施:制定并实施安全施工方案,配备相应的安全设备和器材,如安全帽、安全带、消防器材等,确保施工过程的安全。
三、管道安装1、沟槽开挖:按照图纸要求,对管道安装区域进行沟槽开挖,沟槽的深度和宽度应符合图纸要求,以确保管道安装的顺利进行。
2、管道铺设:将管材按照设计要求铺设在沟槽内,确保管道的平直度和稳定性。
在管道连接处应采用专门的连接件进行连接,确保连接牢固、密封良好。
3、阀门安装:根据设计要求,安装相应的阀门和附件,阀门的位置和高度应符合设计要求,以确保管道的正常运行和维修保养。
4、回填与夯实:在管道安装完毕后,对沟槽进行回填并夯实,确保回填土的密实度符合要求,防止后期出现沉降等问题。
5、防腐处理:对管道进行内外防腐处理,以延长管道的使用寿命。
常用的防腐方法包括涂层防腐、电化学防腐等。
四、质量检测与验收1、质量检测:在管道安装过程中和安装结束后,应进行相应的质量检测,包括管道的平直度、连接处密封性、阀门启闭灵活性等方面。
对于发现的问题应及时进行整改和修复。
2、水压试验:在管道安装完毕后,应进行水压试验,以检验管道的抗压能力和密封性能。
管道深度预制方案
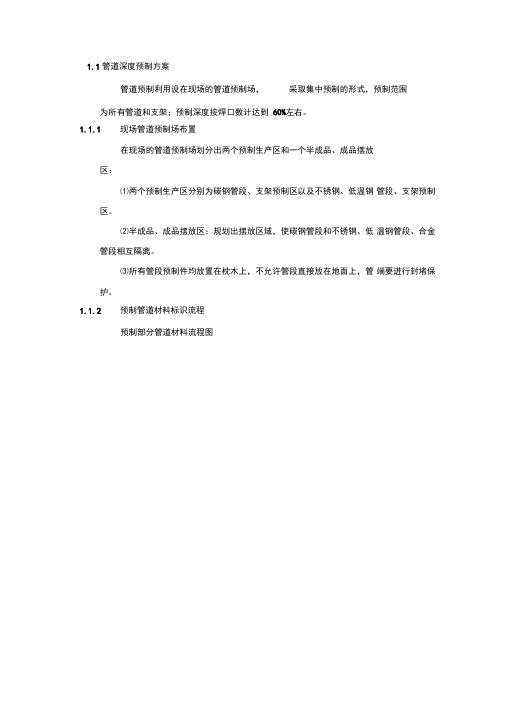
1.1管道深度预制方案管道预制利用设在现场的管道预制场,采取集中预制的形式,预制范围为所有管道和支架;预制深度按焊口数计达到60%左右。
1.1.1现场管道预制场布置在现场的管道预制场划分出两个预制生产区和一个半成品、成品摆放区:⑴两个预制生产区分别为碳钢管段、支架预制区以及不锈钢、低温钢管段、支架预制区。
⑵半成品、成品摆放区:规划出摆放区域,使碳钢管段和不锈钢、低温钢管段、合金管段相互隔离。
⑶所有管段预制件均放置在枕木上,不允许管段直接放在地面上,管端要进行封堵保护。
1.1.2预制管道材料标识流程预制部分管道材料流程图备注:每一批喷砂和刷漆的材料只能有一种1.1.3 预制生产施工程序⑴ 碳钢管道:审图一下料、坡口加工一打磨坡口一清扫管内-组对一焊接f (热处理)f编号f探伤f吹扫管内f封口f出厂。
注:设计需进行消除应力处理的管段,需进行焊后热处理。
⑵ 低温钢管道:审图f下料、坡口加工(包括切割、车制坡口)f打磨坡口f清扫管内f组对f焊前预热f焊接f编号f探伤f吹扫管内f封口f出厂。
⑶ 不锈钢管道:审图f下料、坡口加工(包括切割、车制坡口)f打磨坡口f清扫管内f组对f焊接f编号f探伤f焊道酸洗钝化f吹扫管内f 封口f出厂。
⑷ 合金管道:审图f下料、坡口加工(包括切割、车制坡口)f打磨、清洗坡口f清扫管内f组对f焊接f编号f探伤f吹扫管内f封口f出厂。
⑸预制过程中,关键工序保证合格后才能进行下一道工序。
1.1.4 预制方法及要求⑴ 根据预制计划,按照确认的管道单线图进行管段的预制:①原材料检验合格,并标识明确。
对于低温钢、不锈钢、合金管材采用不同的色环进行标识和区分。
②管道原则上采用机械切割及加工坡口,对于某些难以进行机加工的部位,可使用火焰、等离子切割方式,同时必须人工打磨清除氧化层和可能的淬硬层,必要时使用渗透的方法进行检验。
③不锈钢、低温钢管若使用砂轮切割或修磨时,必须使用专用砂轮片,严禁与碳钢管共用。
电力管道工程施工方案
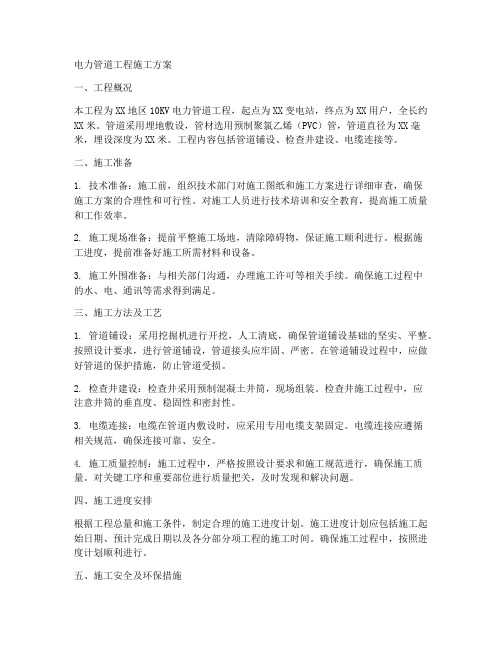
电力管道工程施工方案一、工程概况本工程为XX地区10KV电力管道工程,起点为XX变电站,终点为XX用户,全长约XX米。
管道采用埋地敷设,管材选用预制聚氯乙烯(PVC)管,管道直径为XX毫米,埋设深度为XX米。
工程内容包括管道铺设、检查井建设、电缆连接等。
二、施工准备1. 技术准备:施工前,组织技术部门对施工图纸和施工方案进行详细审查,确保施工方案的合理性和可行性。
对施工人员进行技术培训和安全教育,提高施工质量和工作效率。
2. 施工现场准备:提前平整施工场地,清除障碍物,保证施工顺利进行。
根据施工进度,提前准备好施工所需材料和设备。
3. 施工外围准备:与相关部门沟通,办理施工许可等相关手续。
确保施工过程中的水、电、通讯等需求得到满足。
三、施工方法及工艺1. 管道铺设:采用挖掘机进行开挖,人工清底,确保管道铺设基础的坚实、平整。
按照设计要求,进行管道铺设,管道接头应牢固、严密。
在管道铺设过程中,应做好管道的保护措施,防止管道受损。
2. 检查井建设:检查井采用预制混凝土井筒,现场组装。
检查井施工过程中,应注意井筒的垂直度、稳固性和密封性。
3. 电缆连接:电缆在管道内敷设时,应采用专用电缆支架固定。
电缆连接应遵循相关规范,确保连接可靠、安全。
4. 施工质量控制:施工过程中,严格按照设计要求和施工规范进行,确保施工质量。
对关键工序和重要部位进行质量把关,及时发现和解决问题。
四、施工进度安排根据工程总量和施工条件,制定合理的施工进度计划。
施工进度计划应包括施工起始日期、预计完成日期以及各分部分项工程的施工时间。
确保施工过程中,按照进度计划顺利进行。
五、施工安全及环保措施1. 施工安全:加强施工现场安全管理,设置安全警示标志,制定安全事故应急预案。
对施工人员进行安全帽、安全带等劳动防护用品的配备,确保施工安全。
2. 环保措施:施工过程中,严格控制噪音、粉尘、废水等污染物的排放,遵守相关环保法规。
对施工废弃物进行分类处理,减少对环境的影响。
管道预制计划表(终级版)

目录一、概述 (3)二、编制依据及编制说明 (3)三、设置原则 (4)四、设置的具体准则 (4)(一)标示清楚 (4)1、围栏及进、出口门栏杆 (4)2、公司标识 (5)3、安全生产标志牌 (5)4、施工区域标识 (5)5、业主要求 (5)(二)区域设置及分类 (6)1、防腐区域 (6)2、预制区 (8)(三)先进的新技术 (8)1、新技术原则 (8)2、管道自动焊施工技术 (9)(四)节约用地及运输 (12)1、平面布置图 (12)2、预制厂规模 (14)五、材料控制基本准则 (14)六、管道预制的工艺流程 (15)七、管道预制过程控制 (17)(一)、管道预制施工生产流程 (17)(二)、管道标识 (17)(三)、管道组对标识 (18)(一)、焊接标识 (18)(二)、焊缝质检标识 (19)(三)、管段标识 (19)(四)、探伤标识 (19)(五)、热处理标识 (20)(六)管段验收标识 (20)(七)、管段区域标识 (20)八、焊接控制 (20)九、管段验收 (24)十、管道预制后期控制 (26)(一)、制造技术文件编制 (26)(二)、管段储存交接 (26)(三)、管段包装 (26)(四)、管段搬运 (27)(五)、管段储存 (27)(六)、管段交付 (27)(七)、管段运输 (27)十一、人员配备及其职责和组织机构 (29)(一)、强调人员的合理配备 (29)(二)、管道预制厂人员配备 (29)(三)、预制厂施工组织机构及职责 (29)十二、区域能力及目标控制点 (33)(一)、主要区域 (33)(二)、区域设置 (33)1、预制区厂房内设置 (33)2、厂房外设置 (33)(三)、厂房生产能力 (33)1、防腐喷砂区喷砂能力 (33)2、预制区生产能力 (33)十三、管道人力计划 (34)十四、管道机具计划 (35)十五、管道预制计划表 (36)一、概述本项目为马来西亚Rapid项目,根据工作经验,暂估管道工作量共计120万Din,(其中包含碳钢类管道82.8万、不锈钢20.2万、特殊钢15.2万、大口径管道1.8万)、暂估工程工期1年(12个月)。
埋地管道施工方案
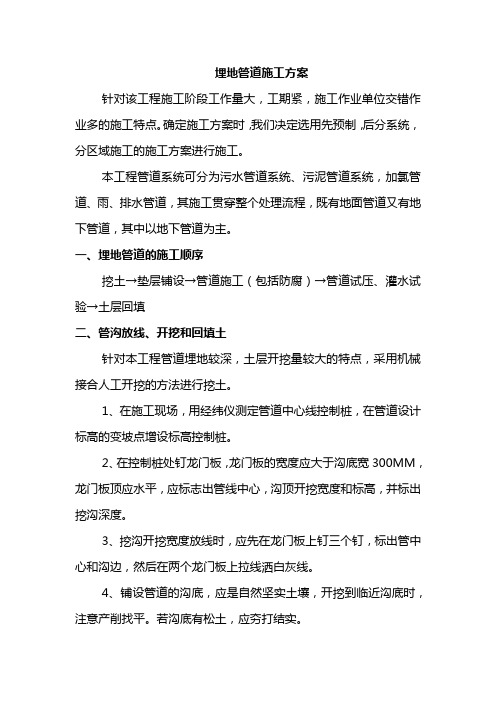
埋地管道施工方案针对该工程施工阶段工作量大,工期紧,施工作业单位交错作业多的施工特点。
确定施工方案时,我们决定选用先预制,后分系统,分区域施工的施工方案进行施工。
本工程管道系统可分为污水管道系统、污泥管道系统,加氯管道、雨、排水管道,其施工贯穿整个处理流程,既有地面管道又有地下管道,其中以地下管道为主。
一、埋地管道的施工顺序挖土→垫层铺设→管道施工(包括防腐)→管道试压、灌水试验→土层回填二、管沟放线、开挖和回填土针对本工程管道埋地较深,土层开挖量较大的特点,采用机械接合人工开挖的方法进行挖土。
1、在施工现场,用经纬仪测定管道中心线控制桩,在管道设计标高的变坡点增设标高控制桩。
2、在控制桩处钉龙门板,龙门板的宽度应大于沟底宽300MM,龙门板顶应水平,应标志出管线中心,沟顶开挖宽度和标高,并标出挖沟深度。
3、挖沟开挖宽度放线时,应先在龙门板上钉三个钉,标出管中心和沟边,然后在两个龙门板上拉线洒白灰线。
4、铺设管道的沟底,应是自然坚实土壤,开挖到临近沟底时,注意产削找平。
若沟底有松土,应夯打结实。
5、当挖土深度超过地下水位时,必须下井点,用泵抽水。
6、回填土时,管沟内积水应排尽,回填的松土应掌握适宜湿度,在回填土时,机械不得在管沟上行走,应分层填、夯,逐层夯实,管子下面及两侧的回填土密度,应大于90%,管顶以上500MM内,回填土密度应大于80%。
回填土应高出地面200MM,并呈拱形。
三、埋地管道安装采用地面预制与槽底施工相接合的施工方法进行施工。
1、地面预制一般为20-30米一段(小口径管道可更长些)。
预制管段通过吊装的方法下到沟槽底(大口径管道通过汽车吊,小口径管道通过人工吊装的方法),槽底管道衔接处的作业面通过扩大开挖面的方法予以保证。
2、碳钢管道防腐在管道进场时及时除锈工作,明露管道先刷两道防锈漆,埋地管道做好两油三布的防腐。
做好防腐的管道堆放时,地面应垫好隔水材料,同时做好管道表面的防护工作,避免管道被泥水二次污染。
2024年管道预制、安装技术及质量要求(三篇)
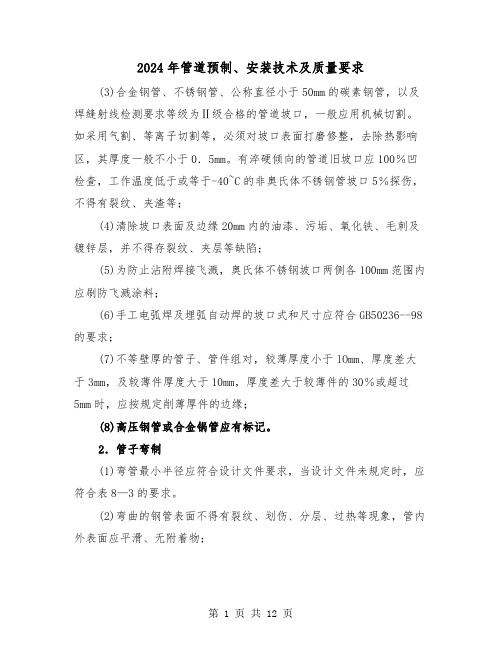
2024年管道预制、安装技术及质量要求(3)合金钢管、不锈钢管、公称直径小于50mm的碳素钢管,以及焊缝射线检测要求等级为Ⅱ级合格的管道坡口,一般应用机械切割。
如采用气割、等离子切割等,必须对坡口表面打磨修整,去除热影响区,其厚度一般不小于0.5mm。
有淬硬倾向的管道旧坡口应100%凹检查,工作温度低于或等于-40~C的非奥氏体不锈钢管坡口5%探伤,不得有裂纹、夹渣等;(4)清除坡口表面及边缘20mm内的油漆、污垢、氧化铁、毛刺及镀锌层,并不得存裂纹、夹层等缺陷;(5)为防止沾附焊接飞溅,奥氏体不锈钢坡口两侧各100mm范围内应刷防飞溅涂料;(6)手工电弧焊及埋弧自动焊的坡口式和尺寸应符合GB50236--98的要求;(7)不等壁厚的管子、管件组对,较薄厚度小于lOmm、厚度差大于3mm,及较薄件厚度大于10mm,厚度差大于较薄件的30%或超过5mm时,应按规定削薄厚件的边缘;(8)高压钢管或合金锅管应有标记。
2.管子弯制(1)弯管最小半径应符合设计文件要求,当设计文件未规定时,应符合表8—3的要求。
(2)弯曲的钢管表面不得有裂纹、划伤、分层、过热等现象,管内外表面应平滑、无附着物;(3)弯管制作后,弯管处的最小壁厚不得小于管子公称壁厚的90%,且不得小于设计文件规定的最小壁厚。
弯管处的最大外径与最小外径之差,应符合下列规定:①GCl级管道应小于弯制前管子外径的5%;②GC2、GC3级管道应小于弯制前管子外径的8%。
(4)弯曲角度偏差,高压管不得超过1.5mm/m,最大不得超过5mm;中低压管弯曲角度偏差对冷弯管不超过3mm/m,最大不得超过10mm;对热弯管不得超过5mm,最大不得超过15mm;(5)褶皱弯管波纹分布均匀、平整、不歪斜;(6)碳素钢管、合金钢管在冷弯后,应按规定进行热处理。
有应力腐蚀倾向的弯管(如介质为苛性碱、湿硫化氢环境等),不论壁厚大小,均应做消除应力热处理。
(7)对有晶间腐蚀要求的奥氏体不锈钢管,热处理后应从同批管子中取两件试样做晶间腐蚀倾向试验。
《建筑业10项新技术》7管道工厂化预制技术

◆对设计蓝图进行分析,结合工程现状进行实测,进行图纸深化,完成加工 图、管段分类编号、装配图,满足不同阶段〔预制、仓储、运输配送、现场装配) 的需求。
②预制加工
加工图经确认后,交付给预制加工厂,由其按图尺寸进行预制加工。 根据现场施工进度计划,按时保质完成相应管段成品或半成品的预制加工工 作;预制加工过程中,质量检验人员依据国家规范、设计要求、施工深化图以及 预制加工图,对加工后的成品和半成品及时进行质量检验,防止不合格品流入施
工现场;
③预制加工厂(场)建设 有条件的尽可能建设固定预制加工厂。 特点:功能齐全,流动性小,实现配送。 预制加工场地有条件的可能选择在施工现场附近,加工基地一 般根据工程规模、类别、预制加工量而定。特点:流动性大,无需 配送,功能实现可变组合。
●组件的标识的要求、方法 京沪高速铁路上海虹桥站封闭付费区和西南模块喷淋管道组件 的标识从绘制预制加工图开始,加工图详细标明图纸号、管线编号、 管段编号、管道材质、预制尺寸、加工数量、材料列表、质量要求 以及支架图、支架编号、支架数量、防腐要求等。 预制管道组对完成后进行管段编号标识,编号按预制加工图的 编号要求标识。 经过编号的管段按管线号要求在半成品堆放区域分别堆放整齐。
(7)应用实例_京沪高铁虹桥站-消防喷淋管道预制
①工程概况 高铁虹桥站用地面积为22.42万m2,站房总建筑面积为239717m2, 无站台立柱雨棚建筑面积为68842m2,南北辅助办公楼建筑面积为 17814m2,客站设高速和城际,普速两个车场,总规模按16台30线 设计。其中高速场10台19线,城际、普速6台11线。
管道预制加工安全操作规程

管道预制加工安全操作规程管道预制加工是一项涉及钢管切割、切削、焊接等工序的重要工艺。
为了确保加工过程的安全,保障人员的生命财产安全,制定并遵守相应的操作规程非常重要。
以下是管道预制加工的安全操作规程:一、工作前准备1.1 在操作前,应检查工作场所是否整洁,通风良好,并移除可能存在的杂物和障碍物。
1.2 配备所需的个人防护装备,包括安全帽、护目镜、防护手套、耳塞等。
1.3 检查和确保加工设备的正常运行状态,如切割机、钳工台和焊接机等。
1.4 检查已配备的工具,包括切割刀、焊接电极、夹具等,确保其完好无损。
1.5 检查使用的钢管是否符合要求,如规格、材质、质量等。
二、切削操作2.1 在切割前,应先调整切割机的切割深度和速度,确保其适合被切割的钢管。
2.2 切割机切割时需保持稳定,确保切割平稳无颤动,避免发生事故。
2.3 切割时需采取防护措施,如戴眼镜、手套避免切割屑溅入眼睛或手部。
2.4 切割完成后,应关闭切割机并等待其冷却后方可进行后续操作。
三、切割焊接3.1 在切割焊接前,应根据其长度和直径,准备相应的焊接设备和焊接材料。
3.2 切割口的处理需确保切割平整、无毛刺,以提高焊接质量和连接强度。
3.3 在焊接前,需先通过焊接试板进行焊接测试,确保焊接质量和稳定性。
3.4 焊接操作需要循序渐进,先从焊缝的两端开始,逐渐向中间焊接,避免焊接区域集中产生热量和应力。
3.5 在焊接过程中,应保持良好的焊接姿势,避免手部和身体接触热源和焊接面。
四、操作注意事项4.1 操作过程中需严格遵守安全操作规程,不得将手部或其他身体部位靠近切削和焊接区域。
4.2 管道预制加工过程中,严禁随意修改和调整设备的参数和设置,以免引发事故。
4.3 加工过程中需及时清理切割屑和焊渣,保持工作区域整洁,防止跌倒和滑倒事故的发生。
4.4 平时应保持工作区域的通风良好,防止气体积聚和引发火灾或爆炸事故。
4.5 操作人员必须熟练掌握相关技能和知识,在操作过程中保持专注并随时准备应对突发状况。
- 1、下载文档前请自行甄别文档内容的完整性,平台不提供额外的编辑、内容补充、找答案等附加服务。
- 2、"仅部分预览"的文档,不可在线预览部分如存在完整性等问题,可反馈申请退款(可完整预览的文档不适用该条件!)。
- 3、如文档侵犯您的权益,请联系客服反馈,我们会尽快为您处理(人工客服工作时间:9:00-18:30)。
1.1 管道深度预制方案
管道预制利用设在现场的管道预制场,采取集中预制的形式,预制范围为所有管道和支架;预制深度按焊口数计达到60%左右。
1.1.1现场管道预制场布置
在现场的管道预制场划分出两个预制生产区和一个半成品、成品摆放区:
⑴两个预制生产区分别为碳钢管段、支架预制区以及不锈钢、低温钢
管段、支架预制区。
⑵半成品、成品摆放区:规划出摆放区域,使碳钢管段和不锈钢、低
温钢管段、合金管段相互隔离。
⑶所有管段预制件均放置在枕木上,不允许管段直接放在地面上,管
端要进行封堵保护。
1.1.2预制管道材料标识流程
预制部分管道材料流程图
备注:每一批喷砂和刷漆的材料只能有一种。
1.1.3预制生产施工程序
⑴碳钢管道:审图→下料、坡口加工→打磨坡口→清扫管内→组对→
焊接→(热处理)→编号→探伤→吹扫管内→封口→出厂。
注:设计需进行消除应力处理的管段,需进行焊后热处理。
⑵低温钢管道:审图→下料、坡口加工(包括切割、车制坡口)→打磨
坡口→清扫管内→组对→焊前预热→焊接→编号→探伤→吹扫管内→封口→出厂。
⑶不锈钢管道:审图→下料、坡口加工(包括切割、车制坡口)→打磨
坡口→清扫管内→组对→焊接→编号→探伤→焊道酸洗钝化→吹扫管内→封口→出厂。
⑷合金管道:审图→下料、坡口加工(包括切割、车制坡口)→打磨、
清洗坡口→清扫管内→组对→焊接→编号→探伤→吹扫管内→封口→出厂。
⑸预制过程中,关键工序保证合格后才能进行下一道工序。
1.1.4预制方法及要求
⑴根据预制计划,按照确认的管道单线图进行管段的预制:
①原材料检验合格,并标识明确。
对于低温钢、不锈钢、合金管材采
用不同的色环进行标识和区分。
②管道原则上采用机械切割及加工坡口,对于某些难以进行机加工的
部位,可使用火焰、等离子切割方式,同时必须人工打磨清除氧化层和可能的淬硬层,必要时使用渗透的方法进行检验。
③不锈钢、低温钢管若使用砂轮切割或修磨时,必须使用专用砂轮片,
严禁与碳钢管共用。
④管子切口质量须符合下列规定:
a 管子切口表面要平整,无裂纹、重皮、毛刺、凹凸、缩口、熔渣、氧
化物、铁屑等。
b 斜口端面倾斜偏差△不大于管子外径的1%,且不得超过3mm。
如
下图所示。
⑤对于不等厚的管子加工、组对,按照设计和施工规范要求进行。
⑥在专用平台或胎具上组对时,对口使用同母材的卡具固定。
⑦自由管段和封闭管段的加工尺寸允许偏差应符合下表的规定:
自由管段和封闭管段加工尺寸允许偏差(mm)
⑧在管段的组对、运输、吊装过程中,应避免可能会造成的机械损伤。
⑨对预制完的管段,对其内部使用空压机进行吹扫。
清洁后,进行管段封闭。
⑩所有预制管段必须进行编号和标识工作,其中不锈钢、低温钢和合金管道严禁使用钢印做标记。
⑵管道组对:
①管道组对按单线图进行,各管段交接处需妥善衔接,尺寸准确,否则要留调节余量。
②管子组对时在距焊口中心200mm处测量平直度,当管子直径<
100mm时,允许偏差为1mm;当管子公称直径≥100mm,允许偏差为2mm,但全长允许偏差不得超过10mm。
确保法兰面的平行度及垂直度,满足设计
和规范要求。
③合金管道的坡口及焊丝需用丙酮清理:先用丙酮除去两侧坡口(不小于50mm)表面油污。
坡口清除油污后,坡口及其附近的表面用不锈钢丝刷清理至露出金属光泽;焊丝油污清除油污后,用5%~10%的NaOH溶液,在温度为70℃下浸泡30~60s,然后水洗,再用15%左右的HNO3在常温下浸泡2min,然后用温水洗净,使其干燥。
④管段组对时,对中并点焊牢固,防止焊接过程中产生变形或位移。
⑤管道组对需方便运输和安装,组合件应有足够的刚度与强度,否则设临时加固措施,必要时标出吊装索具捆绑点的位置。
⑶管道焊接:见焊接技术方案。
⑷奥氏体不锈钢焊道需进行酸洗和钝化处理。
焊道酸洗和钝化采用刷洗法。
①酸洗操作:用刷子醮取酸洗液对焊道区域进行刷洗,反复几次,至刷洗区域呈白亮色为止,然后用清水冲洗干净。
②钝化操作:焊道酸洗后进行钝化操作,用钝化液再酸洗区域涂刷一边,然后用冷水冲洗,再用抹布仔细擦洗,最后用清水冲洗干净并擦干。
⑸管段标识:
①明确预制过程中个工序标识责任人:
下料结束后标识责任人—下料组长
焊接后标识责任人—焊工
焊道外观检测合格后标识责任人—质检员
NDT检验后标识责任人—检验人员
热处理后标识责任人—热处理施工员
热处理完检验合格后标识责任人—检验人员
②各道工序必须标识明确,并附文字记录。
需做热处理的焊道标识应与焊道距离保持在100mm以上。
⑹焊口管理:
①在自检合格的基础上,实行日报日检制,及时填写管道焊接工作记录和无损检测日委托单,并在管道单线图上标识。
②无损检测、返修、热处理、增加或减少焊口的情况,也必须在管道单线图上标识,实现焊口管理的可追溯性。
注:
管工、焊工、无损检测人员用白色标识,质检员用蓝色标识,热处理用红色标识。
各道工序必须标识明确,格框制作模板。
⑺明确各工序的施工记录(见下表),严格预制工厂化的过程控制:
各工序施工记录明细表。