级进模工艺和结构设计注意事项共23页
多工位级进模的设计(基础知识)(doc 23页)

的加工工艺规程,以获得最佳的技术经济效益。
显然,采用多工位级进模进行冲压成形与采用普通冲模进行冲压成形在冲压成形工艺、模具结构设计及模具加工等方面存在许多不同,本章将重点介绍它们在冲压工艺与模具设计上的不同之处。
2. 多工位级进模的排样设计排样设计是多工位级进模设计的关键之一。
排样图的优化与否,不仅关系到材料的利用率,工件的精度,模具制造的难易程度和使用寿命等,而且关系到模具各工位的协调与稳定。
冲压件在带料上的排样必须保证完成各冲压工序,准确送进,实现级进冲压;同时还应便于模具的加工、装配和维修。
冲压件的形状是千变万化的,要设计出合理的排样图,必须从大量的参考资料中学习研究,并积累实践经验,才能顺利地完成设计任务。
排样设计是在零件冲压工艺分析的基础之上进行的。
确定排样图时,首先要根据冲压件图纸计算出展开尺寸,然后进行各种方式的排样。
在确定排样方式时,还必须对工件的冲压方向、变形次数、变形工艺类型、相应的变形程度及模具结构的可能性、模具加工工艺性、企业实际加工能力等进行综合分析判断。
同时全面考虑工件精度和能否顺利进行级进冲压生产后,从几种排样方式中选择一种最佳方案。
完整的排样图应给出工位的布置、载体结构形式和相关尺寸等。
当带料排样图设计完成后,模具的工位数及各工位的内容;被冲制工件各工序的安排及先后顺序,工件的排列方式;模具的送料步距、条料的宽度和材料的利用率;导料方式,弹顶器的设置和导正销的安排;模具的基本结构等就基本确定。
所以排样设计是多工位级进模设计的重要内容,是模具结构设计的依据之一,是决定多工位级进模设计优劣的主要因素之一。
2.1 排样设计的原则多工位级进模的排样,除了遵守普通冲模的排样原则外,还应考虑如下几点:(1)先制作冲压件展开毛坯样板(3~5个),在图面上反复试排,待初步方案确定后,在排样图的开始端安排冲孔、切口、切废料等分离工位,再向另一端依次安排成形工位,最后安排工件和载体分离。
第七章 级进模解读

二、浮料装置
级进模中存在拉深,弯曲等工序,条 料的下面就必然不平整,送进就会有障 碍。对此有两条措施:一是在凹模上开 槽,二是每次冲压后都用弹顶器将条料 抬高,使条料在浮顶器上松劲,从而避 免障碍。
对于第一种措施,只能在最后几个工步采用,重要措施是采用弹 顶器。 弹顶器结构如上图(这是标准弹顶器)。 在级进模中也大量使用带导向槽的弹顶器,它既有弹顶作用,也 有取代导料板导向的作用。 使用导向槽弹顶器,可减少送进阻力。选择这种弹顶器应在模具 进料端或进、出料两端加局部导料板配合使用。
第一节 级进模设计基础
一、概述
级进模,又称:多工位级进模、连续模、跳步模,它是在一副模 具内,按所加工的工件为若干等距离的工位,在每个工位上设置 一个或几个基本冲压工序,来完成冲压工件某部分的加工。 被 加工材料,事先加工成一定宽度的条料,采用某种送进方法,每 次送进一个步距。经逐个工位冲制后,便得到一个完整的冲压工 件。在一副级进模中,可以连续完成冲裁、弯曲、拉深、成形等 工序。 一般来说,无论冲压零件形状怎样复杂,冲压工序怎样 多,均可用一副级进模冲制完成。
排样图设计的好坏,对模具设计的影响很大,因 此要反复思考,设计多个方案,加以比较。
设计排样图时要考虑的问题:
(1)工序安排 各工序的顺序关系除一些常规考虑外,级 进模的工序安排还要注意以下内容:
1)冲裁工序尽量避免一次完成复杂形状的冲裁,复杂工件的外形可通 过多次局部冲裁,最后完成工件的外形要求。对于冲孔落料件,应先冲 孔,在逐步完成外形的冲裁。
搭接如右图a所示,若第一次冲出A、 B两区,第二次冲出C区,图示的搭接 区是冲裁C区凸模的扩大部分,搭接 量应大于0.5倍材料厚,如果不受位 置的限制可以增大至1~2.5倍材料厚 度。
级进模设计说明书
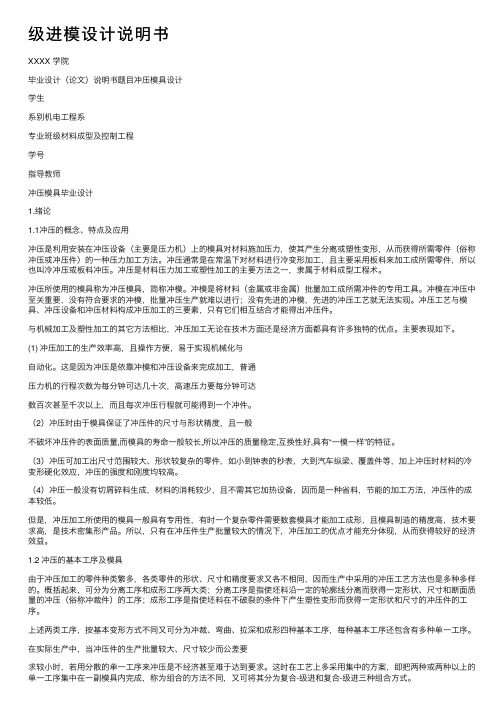
级进模设计说明书XXXX 学院毕业设计(论⽂)说明书题⽬冲压模具设计学⽣系别机电⼯程系专业班级材料成型及控制⼯程学号指导教师冲压模具毕业设计1.绪论1.1冲压的概念、特点及应⽤冲压是利⽤安装在冲压设备(主要是压⼒机)上的模具对材料施加压⼒,使其产⽣分离或塑性变形,从⽽获得所需零件(俗称冲压或冲压件)的⼀种压⼒加⼯⽅法。
冲压通常是在常温下对材料进⾏冷变形加⼯,且主要采⽤板料来加⼯成所需零件,所以也叫冷冲压或板料冲压。
冲压是材料压⼒加⼯或塑性加⼯的主要⽅法之⼀,⾪属于材料成型⼯程术。
冲压所使⽤的模具称为冲压模具,简称冲模。
冲模是将材料(⾦属或⾮⾦属)批量加⼯成所需冲件的专⽤⼯具。
冲模在冲压中⾄关重要,没有符合要求的冲模,批量冲压⽣产就难以进⾏;没有先进的冲模,先进的冲压⼯艺就⽆法实现。
冲压⼯艺与模具、冲压设备和冲压材料构成冲压加⼯的三要素,只有它们相互结合才能得出冲压件。
与机械加⼯及塑性加⼯的其它⽅法相⽐,冲压加⼯⽆论在技术⽅⾯还是经济⽅⾯都具有许多独特的优点。
主要表现如下。
(1) 冲压加⼯的⽣产效率⾼,且操作⽅便,易于实现机械化与⾃动化。
这是因为冲压是依靠冲模和冲压设备来完成加⼯,普通压⼒机的⾏程次数为每分钟可达⼏⼗次,⾼速压⼒要每分钟可达数百次甚⾄千次以上,⽽且每次冲压⾏程就可能得到⼀个冲件。
(2)冲压时由于模具保证了冲压件的尺⼨与形状精度,且⼀般不破坏冲压件的表⾯质量,⽽模具的寿命⼀般较长,所以冲压的质量稳定,互换性好,具有“⼀模⼀样”的特征。
(3)冲压可加⼯出尺⼨范围较⼤、形状较复杂的零件,如⼩到钟表的秒表,⼤到汽车纵梁、覆盖件等,加上冲压时材料的冷变形硬化效应,冲压的强度和刚度均较⾼。
(4)冲压⼀般没有切屑碎料⽣成,材料的消耗较少,且不需其它加热设备,因⽽是⼀种省料,节能的加⼯⽅法,冲压件的成本较低。
但是,冲压加⼯所使⽤的模具⼀般具有专⽤性,有时⼀个复杂零件需要数套模具才能加⼯成形,且模具制造的精度⾼,技术要求⾼,是技术密集形产品。
多工位级进模的装配工艺及装配要点

第一章多工位级进模的装配工艺及装配要点(总10页)--本页仅作为文档封面,使用时请直接删除即可----内页可以根据需求调整合适字体及大小--教学项目四多工位级进模的装配、调试1.项目目标提高多工位级进模的装配和调试综合能力。
2.项目内容能进行多工位级进模的装配能熟练操作冲压设备能进行多工位级进模的调试工作3.项目要求能识读多工位级进模的装配图及相关工艺文件,能制订多工位级进模的装配工艺,并能按装配工艺进行正确装配作业能熟练操作冲压设备,正确安装模具,并调整冲压行程能进行多工位级进模的调试,并能分析常见质量问题第一章多工位级进模的装配工艺及装配要点第一节多工位级进模具结构要点一、级进模具有以下优点1)级进模是多工序冲模,在一副模具内,可以包括冲裁、弯曲、成形和拉深等多种多道工序,具有比复合模更高的劳动生产率,也能生产相当复杂的冲压件;2)级进模操作安全,因为人手不必进入危险区域;3)级进模设计时,工序可以分散。
不必集中在一个工位,不存在复合模中的“最小壁厚”问题。
因而模具强度相对较高,寿命较长。
4)级进模易于自动化,即容易实现自动送料,自动出件,自动叠片;5)级进模可以采用高速压力机生产,因为工件和废料可以直接往下漏;6)使用级进模可以减少压力机,减少半成品的运输。
车间面积和仓库面积可大大减小。
级进模的缺点是结构复杂,制造精度高,周期长,成本高。
因为级进模是将工件的内、外形逐次冲出的,每次冲压都有定位误差,较难稳定保持工件内、外形相对位置的一次性。
但精度高的零件,并非全部轮廓的所有内、外形相对位置要求都高,可以在冲内形的同一工位上,把相对位置要求高的这部分轮廓同时冲出,从而保证零件的精度要求。
二、冲压工序顺序安排的原则1)对于纯冲裁级进模,原则上先冲孔,随后再冲切外形余料,最后再从条料上冲下完整的工件。
应保持条料载体的足够强度,能在冲压时准确无误送进。
2)对于冲裁弯曲级进模,应先冲切掉孔和弯曲部分的外形余料,再进行弯曲,最后再冲靠近弯边的孔和侧面有孔位精度要求的侧壁孔。
级进模的维护要领及常见故障的排除

级进模的维护要领及常见故障的排除This manuscript was revised by the office on December 10, 2020.级进模的维护要领及常见故障的排除奕达电脑制品有限公司郭平喜1模具的维护要领级进模的维护,须做到细心、耐心、按部就班,切忌盲目从事。
因故障拆模时,需附有料带,以便问题的查询。
打开模具,对照料带,检查模具状况,确认故障原因,找出问题所在,再进行模具清理,清洗掉料屑等,方可进行拆模。
拆模时,受力要均匀。
针对卸料弹簧在上模(固定)板与卸料板之间的模具结构形式,其卸料板的拆卸,应保证平衡弹出。
卸料板的倾斜有可能导致模内凸模断裂。
1.1凸凹模的维护凸、凹模拆卸时,应留意模具原有的状况,以利後续装模时方便复原。
更换凸模时,应看通过卸料板是否顺畅。
针对维修後凸模总长度变短,需加垫片达到需要的长度时,应检查凸模有效长度是否足够。
使用新凸模或凹模镶块时,要注意清角部位的处理。
内凹清角因研磨中砂轮的磨损,会有较小R产生,相对在外凸处,亦需人为修出R,以使配合间隙合理。
对成形的细小突出部位更需注意。
更换已断凸模,应查其原因,同时对凹模进行检查是否已引起崩刃,是不是需研磨刃口。
组装凹模,应水准置入,再用较平的铁块置於模芯上用铜棒将其轻轻敲到位,切不可斜置而靠强力敲入(必要时,可在模芯底部角倒出R以便容易导入),组装时如受力不均,在凹模下加设垫片应平整,一般不超过两片(且尽可能使用钢垫),否则容易引发凹模的断裂或成形尺寸不稳定(特别是弯曲成形)。
凸模及模芯等组装完毕,应对照料带作必要检查,各部位是否装错或装反,检查凹模芯有无倒装现象发生,确认无误後方可组装卸料板或合模。
注意做卸料板螺丝的锁紧确认,以便获得足够的锁紧力。
锁紧时应从内到外,平衡用力交叉锁紧,不可一次锁紧某一个螺丝再一次锁紧另一个螺丝,否则会造成凸模断裂或降低模具精度。
1.2卸料板的维护卸料板的拆卸,可用两把起子平衡撬起,再用双手平衡使力将其取出。
级进模工艺和结构设计注意事项

600T级进模上台面能承受的重量不超过7吨
旧
新
改进措施:不影响模具强度及产品质量的情况下, 尽量减轻上模座及压料器的重量
级进模工艺和结构设计注意事项
四、级进模结构设计注意事项
1、上模重量超过上台面能承受的重量
B515-N617K65-66-BA工装厂开始设计上模的重量为7.8吨,而我司
600T级进模上台面能承受的重量不超过7吨
3-2、噪音处理-由于级进模生产节拍快,切边冲头较多,导致噪音较大 案例2:对于切边线在250mm左右,刀口做成波浪剪,减小冲裁力 的同时减小噪音的分贝
级进模工艺和结构设计注意事项
四、级进模结构设计注意事项
3-3、噪音处理3-由于级进模生产节拍快,切边冲头较多,导致噪音较大 案例3:当冲切刀块过多时,刀块需要做成高低差,以达到减小噪音的分贝
求废料排出是否顺畅
送料的稳定性
噪音的处理
零件成型性工艺是否可 行材料利用率
冲头结构的设计 产品滑出是否顺畅
5、对于异性冲头,我司目前一般采取做挂台结构实现防掉(因为当 螺纹与冲头连接松动后冲头掉在模具上,易出现安全事故)
更改后
级进模工艺和结构设计注意事项
四、级进模结构设计注意事项
6、产品划出不顺
CD391-F020C47冲压完成后,零件会卡在下模翻边凸模与切边刀块之间(如右图), 导致无法靠料带将产品推出
级进模工艺和结构设计注意事项
一、级进模的定义
2、级进冲压设备的构成
送料机:按照一定的 步距完成送料
模具与机床:完成各工序 冲压
级进模工艺和结构设计注意事项
二、级进模排样设计基本原则
1、展开制件
通常使用AutoForm/Dynaform/Formingsuite®进行产品展开
级进模设计要点及问题解决

级进模设计中的要点及生产中的故障排除[摘要]通过介绍级进模排样、镶块、模板和其它零件的设计过程,指出了级进模设计中应注意的事项,并介绍了模具生产中一些常见故障和解决办法。
[关键词]:级进模;排样;镶块;间隙1 引言对冲压生产而言,单工位模具结构单一,生产效率低,而且钣金零件不能过于复杂,否则就需要多副单工位模具才能实现。
如果采用级进模进行冲压生产,就司拟改变这些缺点。
级进模的特点是生产效率高,生产周期短,占用的操作人员少,非常适合大批量生产。
2 级进模设计要点2.1 产品的展开计算与排样读懂产品图后,先要进行展开计算,产品的展开尺寸一般是通过经验公式得来的,也有的是通过软件计算得来的。
无论用哪种方法,应该保证计算结果是在允许的范围内。
因为一旦展开尺寸计算错了,最后的产品—定是不合格的,再改正会很麻烦。
所以应该对展开计算的结果进行验算,以保证展开尺寸准确无误。
设计排样图的过程,就是确定模具结构的过程,如呆排样图确定了,那么模具的基本结构也就确定下来了。
所以,在进行排样设计时,要从全局进行详尽的考虑,不能受限于局部结构,而且还要多注意细节。
例如:在分配每一步工位时,不但要考虑哪一工位冲裁,哪一工位折弯,哪一工位成形,还要考虑各个镶块应如何排布,排布的空间够不够,各个镶块之间有没有相互影响。
对于冲裁的工位,应主要考虑冲裁力如何分布均匀合理,冲裁模强度是否能够保证,复杂的冲裁应适当分察。
对于折弯和成形等工位,则应考虑是否能一次成形,如果没有把握,应增加一步顶成形或空步,以方便模具调整。
对于平面度要求高或成形中易形成翘曲的产品,应增加校平工位来保证平面度。
在排布工位顺序时,应注意前后上位不能有影响,否则应调整工忙顺序。
例如:在进行z字形弯曲时,如果z字形弯曲而上有冲孔且冲孔位置有较严格的公差要求,那么就应该先进行z字形弯曲,然后再冲扎,这样就保证了冲孔的位置。
级进模的最后上位是根重要的工位.因为它涉及到产品如何从模具中取出。
第四讲级进模结构设计要点

第八章 冲压模具结构及设计
(4)拉深弯曲级进模,先拉深,再冲切周边余料,然后弯曲。 (5)压印级进模,先冲切周边余料,再压印,最后精确 冲切余料,若压印部位有孔,则压印后再冲孔。(便于金 属流动和减少压印力) (6)压印、弯曲级进模,先压印,再冲切余料,最后弯曲。
第八章 冲压模具结构及设计
本讲小结 1、多工位级进模的特点 2、多工位级进模的排样设计 3、多工位级进模工位数的确定 4、级进模冲压工序顺序的确定 下讲预习 1、模具压力中心的计算 2、模具闭合高度和压力机封闭高度的校核
重要性:
条料的定位精度直接影响到工件的加工精度,特别是对工位数比较多的排样,应特别注意条 料的定位精度。
排样时:
一般应在第一工位冲导正工艺孔,在第二工位设置导正销导正,以该导正销矫正自动送料的步 距误差。
条料的定位精度是确定凹模、固定板和卸料板等零件型孔位置精度的依据。
标注与步距有关的孔位尺寸: 以第一工位为尺寸基准向后标注,以对称偏差标注型孔位置公差,以保证孔位制造精度。
谢谢观赏!
2020/11/5
24
第八章 冲压模具结构及设计 多工位级进模的排样,除了遵守普通冲模的排样原则外,还应考虑如下几点:
1.利于成形,后工序不能影响前已成形工序。 2.连接形式选择
连接体: 多工位冲压时条料上连接工序件,并使工序件在模具上稳定送进的部分材料。
载体基本形式:
双边连接体、单边连接体、中间连接体
第八章 冲压模具结构及设计
第八章 冲压模具结构及设计 边料载体
第八章 冲压模具结构及设计
a)等宽双边载体 双边载体
第八章 冲压模具结构及设计
b) 不等宽双边载体 双边载体
第八章 冲压模具结构及设计 单边载体
本科毕业设计论文设计(多工位级进模设计)
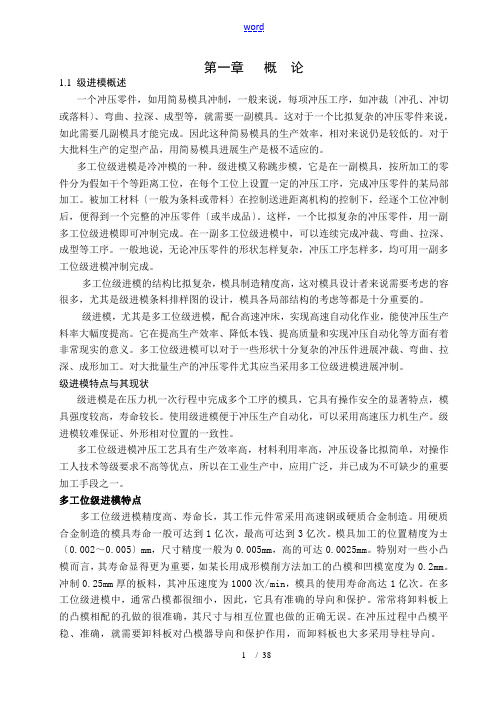
第一章概论1.1 级进模概述一个冲压零件,如用简易模具冲制,一般来说,每项冲压工序,如冲裁〔冲孔、冲切或落料〕、弯曲、拉深、成型等,就需要一副模具。
这对于一个比拟复杂的冲压零件来说,如此需要几副模具才能完成。
因此这种简易模具的生产效率,相对来说仍是较低的。
对于大批料生产的定型产品,用简易模具进展生产是极不适应的。
多工位级进模是冷冲模的一种。
级进模又称跳步模,它是在一副模具,按所加工的零件分为假如干个等距离工位,在每个工位上设置一定的冲压工序,完成冲压零件的某局部加工。
被加工材料〔一般为条料或带料〕在控制送进距离机构的控制下,经逐个工位冲制后,便得到一个完整的冲压零件〔或半成品〕。
这样,一个比拟复杂的冲压零件,用一副多工位级进模即可冲制完成。
在一副多工位级进模中,可以连续完成冲裁、弯曲、拉深、成型等工序。
一般地说,无论冲压零件的形状怎样复杂,冲压工序怎样多,均可用一副多工位级进模冲制完成。
多工位级进模的结构比拟复杂,模具制造精度高,这对模具设计者来说需要考虑的容很多,尤其是级进模条料排样图的设计,模具各局部结构的考虑等都是十分重要的。
级进模,尤其是多工位级进模,配合高速冲床,实现高速自动化作业,能使冲压生产料率大幅度提高。
它在提高生产效率、降低本钱、提高质量和实现冲压自动化等方面有着非常现实的意义。
多工位级进模可以对于一些形状十分复杂的冲压件进展冲裁、弯曲、拉深、成形加工。
对大批量生产的冲压零件尤其应当采用多工位级进模进展冲制。
级进模特点与其现状级进模是在压力机一次行程中完成多个工序的模具,它具有操作安全的显著特点,模具强度较高,寿命较长。
使用级进模便于冲压生产自动化,可以采用高速压力机生产。
级进模较难保证、外形相对位置的一致性。
多工位级进模冲压工艺具有生产效率高,材料利用率高,冲压设备比拟简单,对操作工人技术等级要求不高等优点,所以在工业生产中,应用广泛,并已成为不可缺少的重要加工手段之一。
多工位级进模特点多工位级进模精度高、寿命长,其工作元件常采用高速钢或硬质合金制造。
级进模的设计(内部资料)
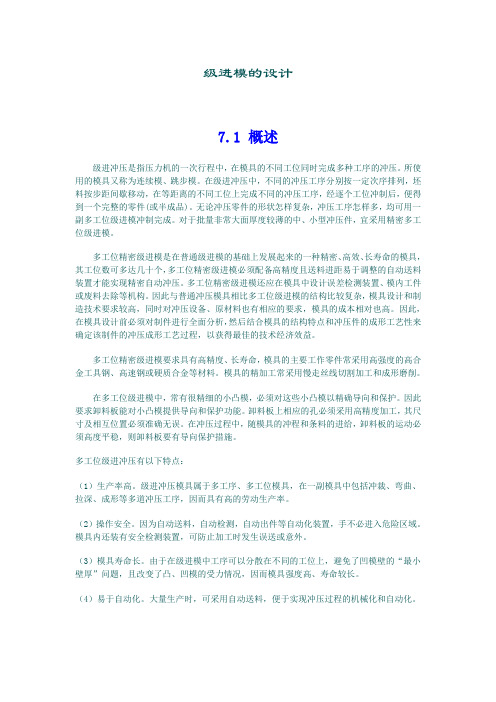
级进模的设计7.1 概述级进冲压是指压力机的一次行程中,在模具的不同工位同时完成多种工序的冲压。
所使用的模具又称为连续模、跳步模。
在级进冲压中,不同的冲压工序分别按一定次序排列,坯料按步距间歇移动,在等距离的不同工位上完成不同的冲压工序,经逐个工位冲制后,便得到一个完整的零件(或半成品)。
无论冲压零件的形状怎样复杂,冲压工序怎样多,均可用一副多工位级进模冲制完成。
对于批量非常大面厚度较薄的中、小型冲压件,宜采用精密多工位级进模。
多工位精密级进模是在普通级进模的基础上发展起来的一种精密、高效、长寿命的模具,其工位数可多达几十个,多工位精密级进模必须配备高精度且送料进距易于调整的自动送料装置才能实现精密自动冲压。
多工位精密级进模还应在模具中设计误差检测装置、模内工件或废料去除等机构。
因此与普通冲压模具相比多工位级进模的结构比较复杂,模具设计和制造技术要求较高,同时对冲压设备、原材料也有相应的要求,模具的成本相对也高。
因此,在模具设计前必须对制件进行全面分析,然后结合模具的结构特点和冲压件的成形工艺性来确定该制件的冲压成形工艺过程,以获得最佳的技术经济效益。
多工位精密级进模要求具有高精度、长寿命,模具的主要工作零件常采用高强度的高合金工具钢、高速钢或硬质合金等材料。
模具的精加工常采用慢走丝线切割加工和成形磨削。
在多工位级进模中,常有很精细的小凸模,必须对这些小凸模以精确导向和保护。
因此要求卸料板能对小凸模提供导向和保护功能。
卸料板上相应的孔必须采用高精度加工,其尺寸及相互位置必须准确无误。
在冲压过程中,随模具的冲程和条料的进给,卸料板的运动必须高度平稳,则卸料板要有导向保护措施。
多工位级进冲压有以下特点:(1)生产率高。
级进冲压模具属于多工序、多工位模具,在一副模具中包括冲裁、弯曲、拉深、成形等多道冲压工序,因而具有高的劳动生产率。
(2)操作安全。
因为自动送料,自动检测,自动出件等自动化装置,手不必进入危险区域。
级进模设计要点及模具使用故障排除方法
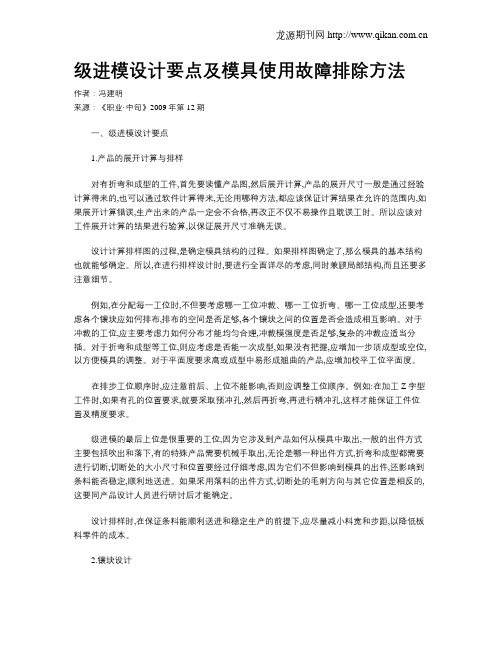
级进模设计要点及模具使用故障排除方法作者:冯建明来源:《职业·中旬》2009年第12期一、级进模设计要点1.产品的展开计算与排样对有折弯和成型的工件,首先要读懂产品图,然后展开计算,产品的展开尺寸一般是通过经验计算得来的,也可以通过软件计算得来,无论用哪种方法,都应该保证计算结果在允许的范围内,如果展开计算错误,生产出来的产品一定会不合格,再改正不仅不易操作且耽误工时。
所以应该对工件展开计算的结果进行验算,以保证展开尺寸准确无误。
设计计算排样图的过程,是确定模具结构的过程。
如果排样图确定了,那么模具的基本结构也就能够确定。
所以,在进行排样设计时,要进行全面详尽的考虑,同时兼顾局部结构,而且还要多注意细节。
例如,在分配每一工位时,不但要考虑哪一工位冲裁、哪一工位折弯、哪一工位成型,还要考虑各个镶块应如何排布,排布的空间是否足够,各个镶块之间的位置是否会造成相互影响。
对于冲裁的工位,应主要考虑力如何分布才能均匀合理,冲裁模强度是否足够,复杂的冲裁应适当分插。
对于折弯和成型等工位,则应考虑是否能一次成型,如果没有把握,应增加一步顶成型或空位,以方便模具的调整。
对于平面度要求高或成型中易形成翘曲的产品,应增加校平工位平面度。
在排步工位顺序时,应注意前后、上位不能影响,否则应调整工位顺序。
例如:在加工Z字型工件时,如果有孔的位置要求,就要采取预冲孔,然后再折弯,再进行精冲孔,这样才能保证工件位置及精度要求。
级进模的最后上位是很重要的工位,因为它涉及到产品如何从模具中取出,一般的出件方式主要包括吹出和落下,有的特殊产品需要机械手取出,无论是哪一种出件方式,折弯和成型都需要进行切断,切断处的大小尺寸和位置要经过仔细考虑,因为它们不但影响到模具的出件,还影响到条料能否稳定,顺利地送进。
如果采用落料的出件方式,切断处的毛刺方向与其它位置是相反的,这要同产品设计人员进行研讨后才能确定。
设计排样时,在保证条料能顺利送进和稳定生产的前提下,应尽量减小料宽和步距,以降低板料零件的成本。
级进模设计

级进模设计讲座第一章概论一. 冲压加工的重要性及优点。
1. 重要性:冲压工艺应用范围十分广泛,在国民经济的各个部门中,几乎都有冲压加工产品。
如汽车,飞机,拖拉机,电器,电机,仪表,铁道,邮电,化工以及轻工日用产品中均占有相当大的比重。
2. 优点:1 )生产率高。
2)精度高,质量稳定。
3 )材料利用率高。
4)操作简便,特别适宜于大批量生产和自动化。
二. 冲压加工的概念。
1. 概念:即利用压力机及其外部设备,通过模具对板材施加压力,从而获得一定形状和尺寸零件的加工方法。
冲压加工的三要素:冲床,模具,材料。
冲压是生产中应用广泛的一类加工方法,主要用于金属薄板料零件的加工。
在产品零件的整个生产系统中,冲压只是一个子系统,所涉及的也仅是产品制造过程的一部分。
随着市场对产品成本和周期等要求的提高,从系统的整体优化中确定相关的各要素已成为技术和管理发展的重要方向。
影响冲压加工的因素:冲安自安润生质价运废噪后压动产量格料音序工全化装滑管管管输处对工艺丨I I 理理理丨理策艺压模材辅工力助机具料装具三. 冲压工序的分类。
冲压工艺按其变形性质可以分为材料的分离与成形两大类,每一类中又包括许多不同的工序。
冲压的基本工序:1. 冲裁:包括落料和冲孔两个工序。
1 )落料:模具沿封闭线冲切板料,冲下的部分为工件,其余部分为废料,设计时尺寸以模仁为准,间隙取在冲子上;2 )冲孔:模具沿封闭线冲切板料,冲下的部分是废料,设计时尺寸以冲子为准,间隙取在模仁上。
2. 剪切:用模具切断板材,切段线不封闭.3. 切口:在坯料上将板材部分切开,切口部分发生弯曲•4. 切边:将拉深或成形后的半成品边缘部分的多余材料切掉。
5. 剖切:将半成品切开成两个或几个工件,常用于成双冲压。
10. 变薄拉深:用减小直径与壁厚,增加工件高度的方法来改变空心件的尺寸,得到要求的底厚,壁薄的工件。
11. 孔的翻边:将板料或工件上有孔的边缘翻成竖立边缘。
II12.外缘翻边:将工件的外缘翻起圆弧或曲线状的竖立边缘。
级进模结构设计
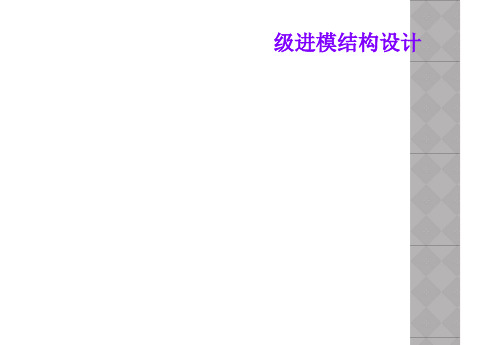
•
⑥定位针装在弹压板上,定位针露出弹压板下平面的有效长度为lmm左右。
(2)整体弹压板多工位级进模应用场合
•
①A型整体弹压板模具适应所有原料厚度,B型整体弹压板模具适应原材料厚度大于0.15mm;
原材料硬度超过100HV的情形。
•
②适应大批量生产。
•
③适应各类产品生产。
•
④产品精度高,毛刺小于0.03mm。
• ②模板内镶嵌零件与安装孔采用过渡或小过盈配合,过盈配合的双边负间隙为0.005mm。
• ③弯曲起伏尽量采取向下弯曲方式。
• ④下模板内的抬料弹顶装置要用装在上模板上的打杆打下,注意:
•
弹顶杆长度≥定位针有效长度≥冲裁凸模及成形凸模的长度;它们之间的长度级推荐采用上下模板各工位有合模要求的型孔及定位销孔同线切割。
,定位针直径略大,防止条料刚度不足、粘料而引起条料变形。 • ④为简化模具的设计与制造,允许部分成形凸模零件直接装于弹压板内。 • ⑤上模板型孔与凸模采用大间隙配合,双边间隙0.05~0.10mm。 • ⑥推荐采用弹压板与下模板中各工位有合模要求的型孔及导向导柱之导套孔同线切割。
4.5.4 分段弹压板多工位级进模
• 分段式独立弹压板级进模具结构适应更高冲压速度、提高模具的通用性、提高更换及维护模具的效 率、提高模具的可靠性及寿命、提高模具制造及产品制造精度,可以有效地降低高精度模具制造的 工艺难度。
(1)分段式弹压板级进模具结构特点
•
①使用高级精度标准模架,
•
②各个独立单元体相当于一副小型整体弹压板模具。
•
③各个独立单元体内主模板之间有四个高精度滚珠导向导柱。
•
④弹压板弹性元件直接压在四个导柱上,通过导柱传递弹力给弹压板
级进模模具设计标准
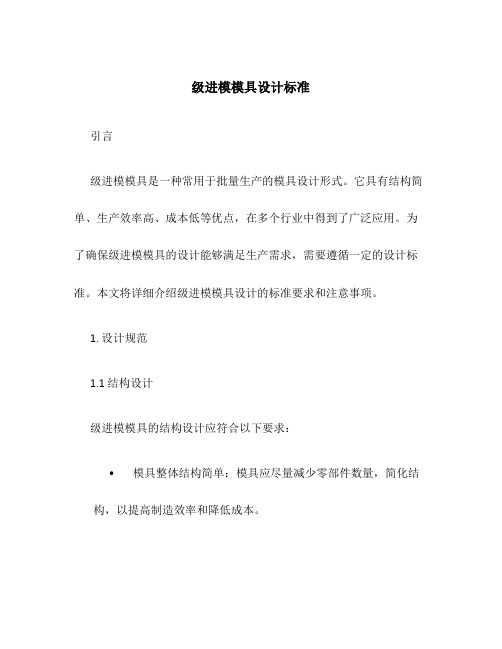
级进模模具设计标准引言级进模模具是一种常用于批量生产的模具设计形式。
它具有结构简单、生产效率高、成本低等优点,在多个行业中得到了广泛应用。
为了确保级进模模具的设计能够满足生产需求,需要遵循一定的设计标准。
本文将详细介绍级进模模具设计的标准要求和注意事项。
1. 设计规范1.1 结构设计级进模模具的结构设计应符合以下要求:•模具整体结构简单:模具应尽量减少零部件数量,简化结构,以提高制造效率和降低成本。
•模腔划分合理:根据产品的形状和尺寸要求,合理划分模腔,使之满足产品的加工需求。
•模腔间距适当:模腔之间应保持适当的间距,以便于模具的制造和使用。
•导向方式合理:模具的导向方式应选择合适的形式,以确保模腔的定位准确性和稳定性。
1.2 材料选择级进模模具的材料选择应满足以下要求:•耐磨性:模具材料应具有较高的耐磨性,以保证模具的使用寿命。
•硬度:模具材料应具有足够的硬度,以防止在使用过程中产生变形或磨损。
•导热性:模具材料应具有良好的导热性能,以便于热量的传导和分散。
•韧性:模具材料应具有一定的韧性,以防止在使用过程中出现断裂等问题。
1.3 管理要求级进模模具的设计还需要满足一定的管理要求:•标准化设计:级进模模具的设计应尽量遵循标准化设计,以便于制造流程的统一和生产效率的提高。
•文档管理:对级进模模具的设计文件应进行有效的管理,确保设计变更的及时更新和追踪。
•维护保养:对模具的维护保养工作应进行规范化管理,定期检查和维护模具,延长模具的使用寿命。
2. 设计流程级进模模具的设计流程可以分为以下几个步骤:2.1 产品分析在设计级进模模具之前,需要进行产品的详细分析。
分析产品的形状、尺寸、材料等特点,确定模具的基本要求和设计方案。
2.2 模腔划分根据产品的特点和生产需求,设计师需要合理划分模腔。
在划分过程中,需要考虑产品的形状、尺寸、生产效率等因素,确保模腔的布局合理。
2.3 结构设计在模腔划分完成后,设计师需要进行模具的结构设计。