原材料实木颗粒板生产工艺流程
实木颗粒板的制作工艺流程

实木颗粒板的制作工艺流程英文回答:To make solid wood particle board, several steps are involved in the manufacturing process. Here is a detailed description of the process:1. Timber selection: The first step is to select the appropriate timber for making solid wood particle board. Different types of wood can be used, such as pine, oak, or birch. The timber should be of good quality and free from defects like knots or cracks.2. Log preparation: Once the timber is selected, it needs to be cut into logs of the desired length. The logs are then debarked to remove the outer layer of bark.3. Chipping: The debarked logs are then fed into a chipper machine, which cuts them into small wood chips. These chips can vary in size, depending on the desiredthickness of the final particle board.4. Drying: The wood chips are then dried to reducetheir moisture content. This is usually done in a kiln or through air-drying methods. The moisture content needs to be carefully controlled to ensure the stability and quality of the final product.5. Blending: After drying, the wood chips are blended together to create a homogeneous mixture. This is done by combining chips of different sizes and species to achieve the desired characteristics of the particle board.6. Resin application: A resin binder is then applied to the wood chips to bind them together. The resin can be a synthetic adhesive like urea-formaldehyde or a natural adhesive like soy-based resin. The resin is evenly distributed over the wood chips to ensure proper bonding.7. Mat formation: The resin-coated wood chips are then spread out on a conveyor belt or in a forming machine. Pressure is applied to compress the chips and form a mat.The thickness of the mat can be adjusted to achieve the desired density and strength of the particle board.8. Hot pressing: The mat is then transferred to a hot press machine, where heat and pressure are applied. This process activates the resin and bonds the wood chips together to form a solid panel. The temperature and pressure need to be carefully controlled to ensure proper curing of the resin and prevent any defects in the final product.9. Trimming and sanding: After the hot pressing, the solid wood particle board is trimmed to the desired size and shape. It is then sanded to achieve a smooth and even surface. This step helps to improve the appearance and quality of the final product.10. Finishing: The particle board can be finished with various coatings or laminates to enhance its durability and aesthetics. This can include applying a layer of paint, veneer, or laminate to the surface.11. Quality control: Throughout the manufacturing process, quality control checks are conducted to ensure that the particle board meets the required standards. This includes checking for defects, such as delamination, warping, or uneven thickness.中文回答:制作实木颗粒板的工艺流程包括以下几个步骤:1. 选材,首先需要选择适合制作实木颗粒板的木材。
原材料实木颗粒板生产工艺流程图

实木颗粒板生产工艺实木颗粒板生产工艺流程原料---刨花制备---干燥---分选---拌胶---铺装---预压---热压---后处理---检验---入库一、实木颗粒板生产木质原料(1)原材料种类小径级原木:原材料基地提供的小径级原木原料造材剩余物胶合板木芯剩余物:采伐剩余物(间伐剩余物,枝桠材)加工剩余物(板皮,端头,碎单板,锯屑)竹材和农作物秸秆(杆类,壳类,渣类)(2) 原材料的选择1。
资源丰富M=KM’M--- 一年生产所需原料; M’--- 产量;K--- 生产1立方米人造板所需原料 K=1.52。
原料本身密度低,强度高密度低,可增大板材的压缩率,板材能获得较高强度。
密度低,提高单位重量原料的刨花表面积(比表面积),可使板材获得较高的胶合强度。
目前,生产中多采用针阔叶材混合原料。
3。
树皮含量经量少树皮对板材的影响:树皮颜色深,板面质量差(有斑点);树皮中有角质物质,影响板材强度;通常要求生产总树皮含量小于10%,且仅作芯层材料。
4。
含水率要适合一搬要求含水率在40%-60%内。
含水率过低,板材脆性大,原材料制备过程中产生的木屑多,影响板材质量。
含水率过高,干燥时所要的能耗大。
5 。
PH值要适合木材HP值影响固化剂的用量和胶黏剂的固化速度。
固化剂呈酸性,原料若呈碱性,则固化剂用量就多,反之则少。
6。
抽提物含量尽量少抽提物多为油脂类物质(石蜡,油脂,树胶等)影响胶黏剂对板材的润湿性,不利于胶合。
但能起到防水作用。
二、实木颗粒板刨花制备1. 刨花形态刨花的几何形态(长,宽,厚对其表面积)对刨花板的质量有较大影响,其中其中影响最大的厚度。
一般刨花越薄,板的强度越高,但过薄的刨花容易碎裂,很难保证刨花板的表面质量和强度要求。
在测试刨花板的抗拉强度和抗弯强度时,总希望刨花在板内断裂而不是被拔出。
这样的刨花板才能够发挥刨花最大的木质纤维强度,这样理想的刨花几何形状,即刨花的长,宽和厚度是制造刨花板重要的工艺参数,也是工艺和设备追求的方向。
板材的工艺流程是什么

板材的工艺流程是什么在建筑、家具、制作等各个领域中,板材被广泛应用。
无论是常见的胶合板、颗粒板,还是复合板、硬质板材等,都需要经过一系列的工艺流程才能生产出最终的产品。
本文将介绍板材的常见工艺流程。
板材的预处理在制作板材之前,原料需要进行预处理。
预处理的目的是清除原料中的杂质,提高板材的质量和耐用性。
1. 木材的预处理木材是制作板材最常用的原材料之一。
在木材预处理中,通常包括以下几个步骤:a. 原料采购原材料采购是木材预处理的第一步。
在采购木材时,需要选择优质的木材,并检查木材的湿度和杂质情况。
b. 去皮和修整去皮是指将原木表面的树皮去除,以免树皮影响后续工艺流程。
修整是将原木两端的不平整部分切割去除,使原木的两端平整。
c. 切割和锯齿处理原木需要根据所需板材的规格进行切割,常见的切割方法包括横切和纵切。
锯齿处理是在切割过程中,使用锯齿将木材切成所需厚度的板材。
2. 其他原料的预处理除了木材之外,制作板材的原料还包括胶水、颗粒等。
这些原料通常需要进行除尘、筛选等预处理过程,以保证原料的纯净度。
板材的制作工艺经过预处理的原料将进入板材制作工艺流程。
板材的制作工艺多样,下面将介绍常见的几种制作工艺。
1. 胶合板的制作工艺胶合板是使用胶水将多层木材热压在一起制成的板材。
其制作工艺包括以下几个步骤:a. 原料贴合将经过预处理的木材按照一定规格和厚度贴合在一起,形成多层结构。
b. 胶合处理将胶水均匀涂在木材层之间,以保证木材之间的粘合度。
c. 热压处理将胶合前的木材放入胶合机中,并施加一定的温度和压力,使胶水充分固化,确保板材的强度和稳定性。
2. 颗粒板的制作工艺颗粒板是将木屑、秸秆等颗粒状原料添加胶水后,进行热压制成的板材。
其制作工艺包括以下几个步骤:a. 原料混合将经过预处理的颗粒原料与胶水进行混合,以保证颗粒均匀分布。
b. 颗粒板成型将混合好的原料放入颗粒板成型机中,通过热压使颗粒固化成板状。
c. 硬化处理颗粒板经过热压后,需要进行硬化处理,以增加板材的硬度和耐久性。
木质颗粒工艺
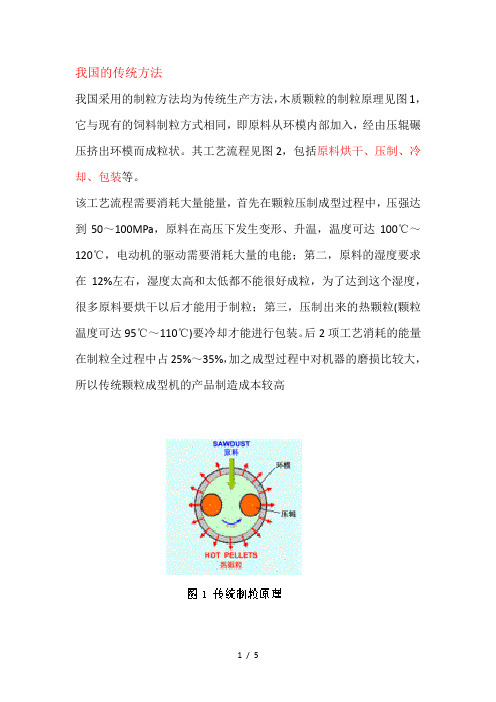
我国的传统方法我国采用的制粒方法均为传统生产方法,木质颗粒的制粒原理见图1,它与现有的饲料制粒方式相同,即原料从环模内部加入,经由压辊碾压挤出环模而成粒状。
其工艺流程见图2,包括原料烘干、压制、冷却、包装等。
该工艺流程需要消耗大量能量,首先在颗粒压制成型过程中,压强达到50~100MPa,原料在高压下发生变形、升温,温度可达100℃~120℃,电动机的驱动需要消耗大量的电能;第二,原料的湿度要求在12%左右,湿度太高和太低都不能很好成粒,为了达到这个湿度,很多原料要烘干以后才能用于制粒;第三,压制出来的热颗粒(颗粒温度可达95℃~110℃)要冷却才能进行包装。
后2项工艺消耗的能量在制粒全过程中占25%~35%,加之成型过程中对机器的磨损比较大,所以传统颗粒成型机的产品制造成本较高图二传统工艺流程图引进ETS系统ETS(EcoTre System)是意大利研制开发的新型木质颗粒制粒生产系统,原理见图3。
它对原料的湿度适应性强,湿度为10%~35%时就可以成粒,所以大部分原料不需要干燥即可直接用于制粒;成粒以后的升温只有10℃~15℃,压制出来的颗粒温度一般只有55℃~60℃,无须冷却即可直接进行包装,通常可以去掉干燥和冷却2道工序,如图4所示。
这种制粒方法能耗很低(比传统的工艺方法减少60%~70%的能量消耗),而且机器磨损也大大减小,总成本降低很多。
对于不同的原料,ETS系统在整个生产制粒过程的单位能量消耗为25~60kWh/t、生产成本为68~128美元/t,而传统工艺的单位能耗为80~180kWh/t,可见,ETS生产效率显著提高。
图三图四美国威猛公司技术原理:煤是秸秆、树枝、杂草等生物质堆积层埋在地下,经过长期的地质作用和一系列的物理化学反应形成的。
利用现代生物化学技术,可以模拟天然煤的形成过程,将农作物秸秆等切碎或粉碎后,加入专业制剂,进行煤化反应,在高温高压下可以具备天然煤一样的品质。
实木家具生产工艺流程

实木家具生产工艺流程实木家具生产工艺流程是指将原材料木材经过一系列的加工工序,最终制作成成品家具的过程。
下面是一般实木家具生产工艺流程的简要介绍。
第一步:原材料采购和准备首先需要根据产品设计要求选择合适的木材进行采购。
常见的实木家具所用的木材有橡木、松木、榉木等。
在选择木材时需要考虑到材质的稳定性、硬度和美观度等方面的因素。
采购好的木材进行裁切,按照设计要求切割成相应的尺寸。
第二步:木材干燥处理木材需要经过干燥处理以提高稳定性和防止变形。
木材通常通过常温干燥或者采用烘干机进行干燥处理。
常温干燥需要一定的时间,而烘干机则可以缩短干燥时间。
第三步:木材修整和打磨经过干燥处理后的木材进行修整,将木材上的毛刺、凹凸处修整平整。
然后进行打磨,使整个表面光滑。
第四步:组装和结构加固将各个木材组成家具的框架。
通过使用榫卯和螺丝等连接件将各个部件固定在一起。
在必要的位置加固结构,以增加家具的稳定性和耐用性。
第五步:上色和喷漆家具制作完成后,进行上色和喷漆。
上色是用颜色剂对木材进行上色处理,以增加家具的美观度。
然后进行喷漆,喷上保护漆,使家具表面更加光滑,增加耐用性。
第六步:组装配件和细节加工将家具的功能性配件和装饰性配件进行组装。
根据设计要求和客户需求加入相应的配件,如抽屉滑轨、玻璃门铰链等。
对家具的细节进行加工,如雕刻、镶嵌等,以增加家具的艺术价值和装饰效果。
第七步:质检和包装在产品出厂前,需要进行质量检验。
检查家具的结构稳定性、装配工艺和外观质量,确保产品符合标准要求。
检验合格后,对产品进行包装,保护家具的表面不受损坏和污染。
以上是一般实木家具生产工艺流程的简要介绍。
实木家具生产过程有很多细节需要注意,如设计、加工、组装、装配等环节,每个环节都需要专业知识和技术来保证产品的质量和效果。
实木家具作为高档家具的代表,制作工艺要求高,需要注重每一个环节的操作,以生产出高品质的实木家具。
颗粒板的生产流程

颗粒板的生产流程Particleboard is a type of engineered wood product that is commonly used in furniture manufacturing and construction. 颗粒板是一种常用于家具制造和建筑行业的人造木材产品。
It is made by compressing wood particles or fibers together with resin under high pressure and heat. 它是通过在高温高压下将木屑或纤维与树脂压缩在一起制成的。
The production process of particleboard involves several key steps that are critical to the quality and performance of the final product. 颗粒板的生产流程涉及几个关键步骤,这些步骤对最终产品的质量和性能至关重要。
The first step in the production process is the selection of raw materials. 生产过程中的第一步是选择原材料。
Wood particles or fibers used to make particleboard are typically sourced from sawmill residues, such as wood chips and sawdust. 用于制造颗粒板的木屑或纤维通常来自锯木厂的剩余物,如木屑和锯末。
The quality and composition of these raw materials can greatly impact the strength and durability of the final product. 这些原材料的质量和成分可以极大地影响最终产品的强度和耐用性。
实木家具生产流程规范
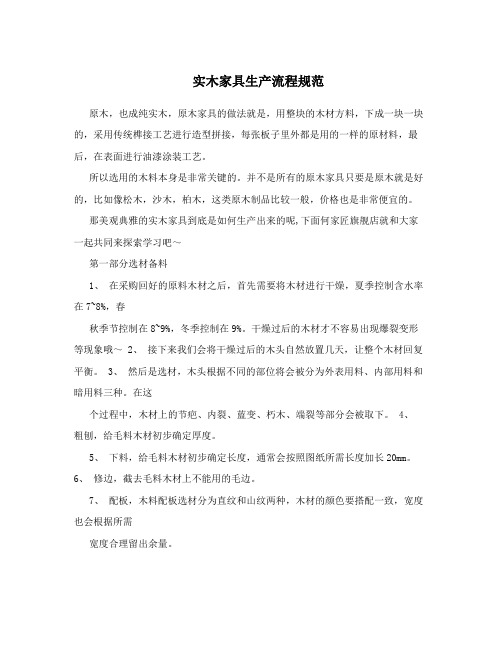
实木家具生产流程规范原木,也成纯实木,原木家具的做法就是,用整块的木材方料,下成一块一块的,采用传统榫接工艺进行造型拼接,每张板子里外都是用的一样的原材料,最后,在表面进行油漆涂装工艺。
所以选用的木料本身是非常关键的。
并不是所有的原木家具只要是原木就是好的,比如像松木,沙木,柏木,这类原木制品比较一般,价格也是非常便宜的。
那美观典雅的实木家具到底是如何生产出来的呢,下面何家匠旗舰店就和大家一起共同来探索学习吧~第一部分选材备料1、在采购回好的原料木材之后,首先需要将木材进行干燥,夏季控制含水率在7~8%,春秋季节控制在8~9%,冬季控制在9%。
干燥过后的木材才不容易出现爆裂变形等现象哦~ 2、接下来我们会将干燥过后的木头自然放置几天,让整个木材回复平衡。
3、然后是选材,木头根据不同的部位将会被分为外表用料、内部用料和暗用料三种。
在这个过程中,木材上的节疤、内裂、蓝变、朽木、端裂等部分会被取下。
4、粗刨,给毛料木材初步确定厚度。
5、下料,给毛料木材初步确定长度,通常会按照图纸所需长度加长20mm。
6、修边,截去毛料木材上不能用的毛边。
7、配板,木料配板选材分为直纹和山纹两种,木材的颜色要搭配一致,宽度也会根据所需宽度合理留出余量。
8、布胶,在木材之间均匀涂上胶水,胶水一般按照固化剂(10—15克)、拼胶板(100克)的比例来调制,每次技术员们大概会调胶500克左右。
9、下一步就是拼板啦~使用拼板机对木材进行拼装,过程中要注意高低差、长短差、色差和节疤。
拼板时间根据厚度的不同,夏天为2—3小时,冬天为3—4小时。
使压时间为40分钟至1个小时,放置时间为2—3个小时。
10、将拼板完成之后的木材放置2小时左右,让胶水凝固。
11、砂刨,刨去木材之间多余的胶水,使木材板面无多余胶水。
12、锯切定宽,用单片锯子给木材定下宽度。
13、然后把木材四面刨成型,根据需要的形状刨出来。
14、养生,将木材自然放置24小时左右。
实木生产工艺操作流程
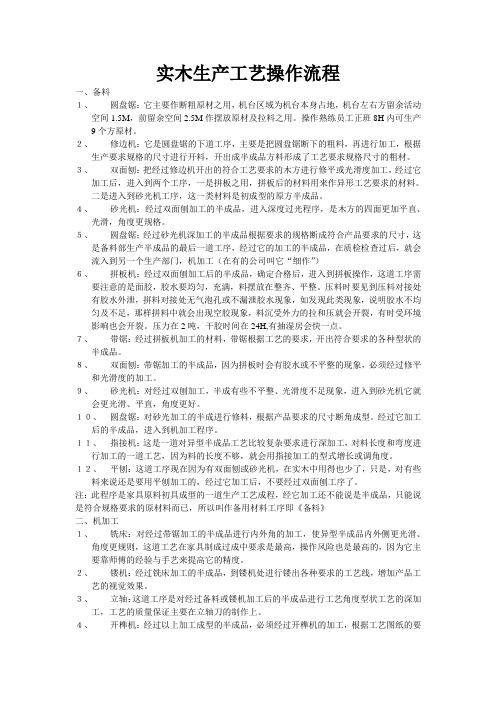
实木生产工艺操作流程一、备料1、圆盘锯:它主要作断粗原材之用,机台区域为机台本身占地,机台左右方留余活动空间1.5M,前留余空间2.5M作摆放原材及拉料之用。
操作熟练员工正班8H内可生产9个方原材。
2、修边机:它是圆盘锯的下道工序,主要是把圆盘锯断下的粗料,再进行加工,根据生产要求规格的尺寸进行开料,开出成半成品方料形成了工艺要求规格尺寸的粗材。
3、双面刨:把经过修边机开出的符合工艺要求的木方进行修平或光滑度加工,经过它加工后,进入到两个工序,一是拼板之用,拼板后的材料用来作异形工艺要求的材料。
二是进入到砂光机工序,这一类材料是初成型的原方半成品。
4、砂光机:经过双面刨加工的半成品,进入深度过光程序,是木方的四面更加平直、光滑,角度更规格。
5、圆盘锯:经过砂光机深加工的半成品根据要求的规格断成符合产品要求的尺寸,这是备料部生产半成品的最后一道工序,经过它的加工的半成品,在质检检查过后,就会流入到另一个生产部门,机加工(在有的公司叫它“细作”)6、拼板机:经过双面刨加工后的半成品,确定合格后,进入到拼板操作,这道工序需要注意的是面胶,胶水要均匀,充满,料摆放在整齐、平整。
压料时要见到压料对接处有胶水外泄,拼料对接处无气泡孔或不漏泄胶水现象,如发现此类现象,说明胶水不均匀及不足,那样拼料中就会出现空胶现象,料沉受外力的拉和压就会开裂,有时受环境影响也会开裂。
压力在2吨,干胶时间在24H,有抽湿房会快一点。
7、带锯:经过拼板机加工的材料,带锯根据工艺的要求,开出符合要求的各种型状的半成品。
8、双面刨:带锯加工的半成品,因为拼板时会有胶水或不平整的现象,必须经过修平和光滑度的加工。
9、砂光机:对经过双刨加工,半成有些不平整、光滑度不足现象,进入到砂光机它就会更光滑、平直,角度更好。
10、圆盘锯:对砂光加工的半成进行修料,根据产品要求的尺寸断角成型。
经过它加工后的半成品,进入到机加工程序。
11、指接机:这是一道对异型半成品工艺比较复杂要求进行深加工,对料长度和弯度进行加工的一道工艺,因为料的长度不够,就会用指接加工的型式增长或调角度。
板材生产工艺流程

板材生产工艺流程板材是一种常见的建材,广泛应用于家居装修、建筑工程以及家具制造等领域。
下面将介绍一下板材的生产工艺流程。
首先,板材的生产工艺可以分为四个主要的步骤:原材料准备、切割加工、胶合处理和涂装加工。
第一步是原材料准备。
板材的原材料通常是木材,包括松木、榉木、橡木等等。
这些木材需要经过蒸煮、干燥等处理,以去除其中的水分和杂质,并增加木材的稳定性和耐腐蚀性。
第二步是切割加工。
在原材料准备完毕后,木材需要被切割成板材的形状和大小。
这一步通常使用的设备是多刀电锯或者切割机,可以快速准确地将木材切割成所需的尺寸。
第三步是胶合处理。
切割好的木材板材需要经过胶合处理,以增加其强度和稳定性。
这一步通常使用的是胶合剂,例如脲醛胶、酚醛胶等。
胶合剂将木材板材粘合在一起,形成一块坚固的板材。
胶合处理一般有两种方式,一种是单层胶合,即将同方向的木材板材按照一定顺序粘合在一起;另一种是多层胶合,即将不同方向的木材板材交错粘合在一起,增加板材的强度和稳定性。
最后一步是涂装加工。
胶合处理好的板材需要进行涂装处理,以增加其耐磨性和美观度。
涂装通常采用的是涂料,根据不同的用途和需求,可以选择不同的涂料,如乳胶漆、油漆等。
涂装需要进行喷涂、刷涂等工艺,并经过烘干处理,以使涂料完全固化。
综上所述,板材的生产工艺流程包括原材料准备、切割加工、胶合处理和涂装加工。
通过这些工艺步骤,原始的木材可以得到精细加工,形成耐用美观的板材产品。
随着科学技术和生产工艺的不断进步,板材的制造工艺也在不断改进和完善,以满足人们对板材的不同需求和应用场景。
原材料实木颗粒板生产实用工艺流程

实木颗粒板生产工艺实木颗粒板生产工艺流程原料---刨花制备---干燥---分选---拌胶---铺装---预压---热压---后处理---检验---入库一、实木颗粒板生产木质原料(1)原材料种类小径级原木:原材料基地提供的小径级原木原料造材剩余物胶合板木芯剩余物:采伐剩余物(间伐剩余物,枝桠材)加工剩余物(板皮,端头,碎单板,锯屑)竹材和农作物秸秆(杆类,壳类,渣类)(2) 原材料的选择1。
资源丰富M=KM’M--- 一年生产所需原料; M’--- 产量;K--- 生产1立方米人造板所需原料 K=1.52。
原料本身密度低,强度高密度低,可增大板材的压缩率,板材能获得较高强度。
密度低,提高单位重量原料的刨花表面积(比表面积),可使板材获得较高的胶合强度。
目前,生产中多采用针阔叶材混合原料。
3。
树皮含量经量少树皮对板材的影响:树皮颜色深,板面质量差(有斑点);树皮中有角质物质,影响板材强度;通常要求生产总树皮含量小于10%,且仅作芯层材料。
4。
含水率要适合一搬要求含水率在40%-60%内。
含水率过低,板材脆性大,原材料制备过程中产生的木屑多,影响板材质量。
含水率过高,干燥时所要的能耗大。
5 。
PH值要适合木材HP值影响固化剂的用量和胶黏剂的固化速度。
固化剂呈酸性,原料若呈碱性,则固化剂用量就多,反之则少。
6。
抽提物含量尽量少抽提物多为油脂类物质(石蜡,油脂,树胶等)影响胶黏剂对板材的润湿性,不利于胶合。
但能起到防水作用。
二、实木颗粒板刨花制备1. 刨花形态刨花的几何形态(长,宽,厚对其表面积)对刨花板的质量有较大影响,其中其中影响最大的厚度。
一般刨花越薄,板的强度越高,但过薄的刨花容易碎裂,很难保证刨花板的表面质量和强度要求。
在测试刨花板的抗拉强度和抗弯强度时,总希望刨花在板内断裂而不是被拔出。
这样的刨花板才能够发挥刨花最大的木质纤维强度,这样理想的刨花几何形状,即刨花的长,宽和厚度是制造刨花板重要的工艺参数,也是工艺和设备追求的方向。
板材生产工艺流程
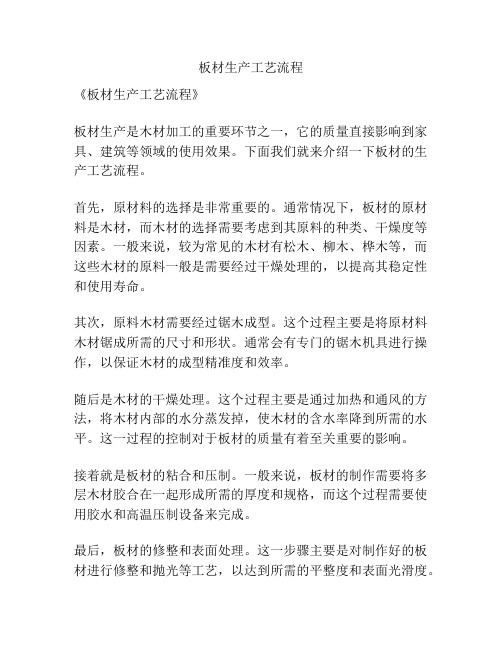
板材生产工艺流程
《板材生产工艺流程》
板材生产是木材加工的重要环节之一,它的质量直接影响到家具、建筑等领域的使用效果。
下面我们就来介绍一下板材的生产工艺流程。
首先,原材料的选择是非常重要的。
通常情况下,板材的原材料是木材,而木材的选择需要考虑到其原料的种类、干燥度等因素。
一般来说,较为常见的木材有松木、柳木、桦木等,而这些木材的原料一般是需要经过干燥处理的,以提高其稳定性和使用寿命。
其次,原料木材需要经过锯木成型。
这个过程主要是将原材料木材锯成所需的尺寸和形状。
通常会有专门的锯木机具进行操作,以保证木材的成型精准度和效率。
随后是木材的干燥处理。
这个过程主要是通过加热和通风的方法,将木材内部的水分蒸发掉,使木材的含水率降到所需的水平。
这一过程的控制对于板材的质量有着至关重要的影响。
接着就是板材的粘合和压制。
一般来说,板材的制作需要将多层木材胶合在一起形成所需的厚度和规格,而这个过程需要使用胶水和高温压制设备来完成。
最后,板材的修整和表面处理。
这一步骤主要是对制作好的板材进行修整和抛光等工艺,以达到所需的平整度和表面光滑度。
以上所述即是板材的生产工艺流程的基本步骤。
通过合理的工艺流程和精细的操作,可以生产出高质量的板材产品,从而满足各个领域对板材产品的需求。
木柴生物质颗粒生产工艺流程详解
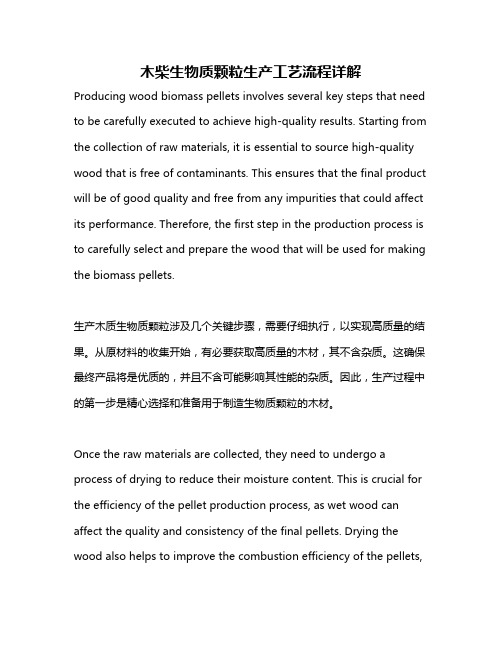
木柴生物质颗粒生产工艺流程详解Producing wood biomass pellets involves several key steps that need to be carefully executed to achieve high-quality results. Starting from the collection of raw materials, it is essential to source high-quality wood that is free of contaminants. This ensures that the final product will be of good quality and free from any impurities that could affect its performance. Therefore, the first step in the production process is to carefully select and prepare the wood that will be used for making the biomass pellets.生产木质生物质颗粒涉及几个关键步骤,需要仔细执行,以实现高质量的结果。
从原材料的收集开始,有必要获取高质量的木材,其不含杂质。
这确保最终产品将是优质的,并且不含可能影响其性能的杂质。
因此,生产过程中的第一步是精心选择和准备用于制造生物质颗粒的木材。
Once the raw materials are collected, they need to undergo a process of drying to reduce their moisture content. This is crucial for the efficiency of the pellet production process, as wet wood can affect the quality and consistency of the final pellets. Drying the wood also helps to improve the combustion efficiency of the pellets,making them a more efficient and environmentally friendly fuel source. Proper drying techniques and equipment are essential to ensure that the wood is dried effectively without compromising its quality.一旦收集到原材料,它们需要经历干燥过程,以减少其含水量。
实木家具生产工艺流程
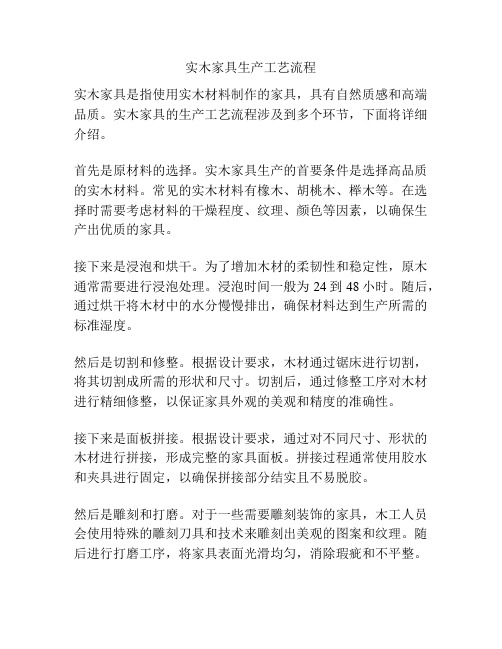
实木家具生产工艺流程实木家具是指使用实木材料制作的家具,具有自然质感和高端品质。
实木家具的生产工艺流程涉及到多个环节,下面将详细介绍。
首先是原材料的选择。
实木家具生产的首要条件是选择高品质的实木材料。
常见的实木材料有橡木、胡桃木、榉木等。
在选择时需要考虑材料的干燥程度、纹理、颜色等因素,以确保生产出优质的家具。
接下来是浸泡和烘干。
为了增加木材的柔韧性和稳定性,原木通常需要进行浸泡处理。
浸泡时间一般为24到48小时。
随后,通过烘干将木材中的水分慢慢排出,确保材料达到生产所需的标准湿度。
然后是切割和修整。
根据设计要求,木材通过锯床进行切割,将其切割成所需的形状和尺寸。
切割后,通过修整工序对木材进行精细修整,以保证家具外观的美观和精度的准确性。
接下来是面板拼接。
根据设计要求,通过对不同尺寸、形状的木材进行拼接,形成完整的家具面板。
拼接过程通常使用胶水和夹具进行固定,以确保拼接部分结实且不易脱胶。
然后是雕刻和打磨。
对于一些需要雕刻装饰的家具,木工人员会使用特殊的雕刻刀具和技术来雕刻出美观的图案和纹理。
随后进行打磨工序,将家具表面光滑均匀,消除瑕疵和不平整。
接下来是上色和涂漆。
通过上色和涂漆,可以使家具呈现出各种不同的颜色和质感。
上色可以使木材的纹理更加突显,涂漆则可以增加木材的防水性和耐久性。
最后是组装和包装。
将各个部分的家具进行组装,可以使用螺丝、胶水等固定物料。
组装完成后,对家具进行最后的质量检查,确保家具没有明显的瑕疵和质量问题。
随后,对家具进行包装,以保护家具不受运输过程中的碰撞和损坏。
通过以上的工艺流程,实木家具从原材料到最终成品的生产过程完成。
这些工艺流程确保了实木家具的品质和寿命,使其成为高端家具市场的热门选择。
实木家具以其自然质感和独特韵味,成为许多人喜爱的家居装饰品。
原材料实木颗粒板生产工艺流程
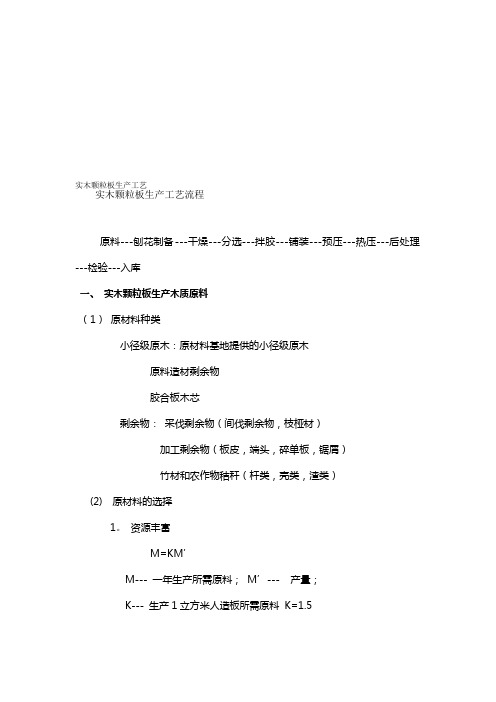
实木颗粒板生产工艺实木颗粒板生产工艺流程原料---刨花制备---干燥---分选---拌胶---铺装---预压---热压---后处理---检验---入库一、实木颗粒板生产木质原料(1)原材料种类小径级原木:原材料基地提供的小径级原木原料造材剩余物胶合板木芯剩余物:采伐剩余物(间伐剩余物,枝桠材)加工剩余物(板皮,端头,碎单板,锯屑)竹材和农作物秸秆(杆类,壳类,渣类)(2)原材料的选择1。
资源丰富M=KM’M---一年生产所需原料;M’---产量;K---生产1立方米人造板所需原料K=1.52。
原料本身密度低,强度高密度低,可增大板材的压缩率,板材能获得较高强度。
密度低,提高单位重量原料的刨花表面积(比表面积),可使板材获得较高的胶合强度。
目前,生产中多采用针阔叶材混合原料。
3。
树皮含量经量少树皮对板材的影响:树皮颜色深,板面质量差(有斑点);树皮中有角质物质,影响板材强度;通常要求生产总树皮含量小于10%,且仅作芯层材料。
4。
含水率要适合一搬要求含水率在40%-60%内。
含水率过低,板材脆性大,原材料制备过程中产生的木屑多,影响板材质量。
含水率过高,干燥时所要的能耗大。
5。
PH值要适合木材HP值影响固化剂的用量和胶黏剂的固化速度。
固化剂呈酸性,原料若呈碱性,则固化剂用量就多,反之则少。
6。
抽提物含量尽量少抽提物多为油脂类物质(石蜡,油脂,树胶等)影响胶黏剂对板材的润湿性,不利于胶合。
但能起到防水作用。
二、实木颗粒板刨花制备1.刨花形态刨花的几何形态(长,宽,厚对其表面积)对刨花板的质量有较大影响,其中其中影响最大的厚度。
一般刨花越薄,板的强度越高,但过薄的刨花容易碎裂,很难保证刨花板的表面质量和强度要求。
在测试刨花板的抗拉强度和抗弯强度时,总希望刨花在板内断裂而不是被拔出。
这样的刨花板才能够发挥刨花最大的木质纤维强度,这样理想的刨花几何形状,即刨花的长,宽和厚度是制造刨花板重要的工艺参数,也是工艺和设备追求的方向。
- 1、下载文档前请自行甄别文档内容的完整性,平台不提供额外的编辑、内容补充、找答案等附加服务。
- 2、"仅部分预览"的文档,不可在线预览部分如存在完整性等问题,可反馈申请退款(可完整预览的文档不适用该条件!)。
- 3、如文档侵犯您的权益,请联系客服反馈,我们会尽快为您处理(人工客服工作时间:9:00-18:30)。
实木颗粒板生产工艺
实木颗粒板生产工艺流程
原料——-刨花制备-——干燥—--分选-—-拌胶—--铺装——-预压—--热压-——后处理—--检验--—入库
一、实木颗粒板生产木质原料
(1)原材料种类
小径级原木:原材料基地提供得小径级原木
原料造材剩余物
胶合板木芯
剩余物: 采伐剩余物(间伐剩余物,枝桠材)
加工剩余物(板皮,端头,碎单板,锯屑)
竹材与农作物秸秆(杆类,壳类,渣类)(2)原材料得选择
1. 资源丰富
M=KM'
M-—- 一年生产所需原料; M’-——产量;
K——-生产1立方米人造板所需原料K=1、5
2。
原料本身密度低,强度高
密度低,可增大板材得压缩率,板材能获得较高强度。
密度低,提高单位重量原料得刨花表面积(比表面积),可使板材获得较高得胶合强度.目前,生产中多采用针阔叶材混合原料.
3。
树皮含量经量少
树皮对板材得影响:树皮颜色深,板面质量差(有斑点);树皮中有角质物质,影响板材强度;通常要求生产总树皮含量小于10%,且仅作芯层材料。
4。
含水率要适合
一搬要求含水率在40%—60%内。
含水率过低,板材脆性大,原材料制备过程中产生得木屑多,影响板材质量。
含水率过高,干燥时所要得能耗大。
5。
PH值要适合
木材HP值影响固化剂得用量与胶黏剂得固化速度.固化剂呈酸性,原料若呈碱性,则固化剂用量就多,反之则少.
6。
抽提物含量尽量少
抽提物多为油脂类物质(石蜡,油脂,树胶等)影响胶黏剂对板材得润湿性,不利于胶合。
但能起到防水作用.
二、实木颗粒板刨花制备
1、刨花形态
刨花得几何形态(长,宽,厚对其表面积)对刨花板得质量有较大影响,其中其中影响最大得厚度.一般刨花越薄,板得强度越高,但过薄得刨花容易碎裂,很难保证刨花板得表面质量与强度要求.在测试刨花板得抗拉强度与抗弯强度时,总希望刨花在板内断裂而不就是被拔出。
这样得刨花板才能够发挥刨花最大得木质纤维强度,这样理想得刨花几何形状,即刨花得长,宽与厚度就是制造刨花板重要得工艺参数,也就是工艺与设备追求得方向。
(1)刨花形状系数
长细比
片状刨花S=L/t
杆状刨花S=L/d
L刨花长度 d 刨花直径t刨花厚度
通常S大于100-120
长宽比
J=L/W W 刨花宽度
定向刨花J大于10
宽厚比
K=W/t
(2)刨花尺寸对板材性能得影响
刨花长度对板材强度得影响:最适宜长度取决于刨花本身得强度与刨花之间得接触面积,刨花过长会造成分布与施胶不均。
刨花宽度对板材强度得影响:宽度对表面积与施胶量得影响比长度大,但比厚度小.
刨花厚度对板材强度得影响:一般刨花越薄板得强度越高,但就是过薄得刨花容易碎裂,很难保证刨花板得表面质量与强度要求.
(3)刨花形状系数得确定
形状系数包括长宽比,长细比,宽细比。
长宽比可根据板得种类与性质而定。
形状系数小,加压就是边部容易溃散,裁边尺寸要大,否则板得边部强度很低
形状系数过大,给胶量与成型带来一定困难.刨花之间得间隙大,不
容易制得高强度刨花板.
目前各种普通刨花板得刨花尺寸统计:
初碎型机床(1)削片机(盘式削片机与辊式削片机)
(2)刨片机(盘式刨片机与鼓式刨片机)
再碎型机床(鼓式刨片机与锤式再碎机)
研磨型机床
三、实木颗粒板刨花干燥
1 刨花含水率
刨花含水率对产品质量有很大影响。
MC过高,不但热压时能耗增加,延长热压时间,降低热压机得效率,而且影响胶合剂得胶合能力,降低强度,刨花板容易分层鼓泡。
刨花MC过低,刨花塑性减小,加压困难,不易压实,提高了刨花得孔隙率;刨花吸收胶液过多,刨花表面胶量减小,也会使刨花板强度下降。
对刨花含水率得要求,因使用胶种不同而有差别。
使用不同胶种,刨花含
水率分别控制在下列范围:
酚醛树脂胶小于12%
单层板6%
三层板中板3—6%
三层板表板5-9%
2刨花干燥设备
削制刨花含水率一般在35%-60%之间,与施胶前所要求得含水率相差很远,所以要进行干燥。
A 接触加热回转式辊筒干燥机
B 转子式干燥机
C 单通道干燥机
D三套筒干燥机
E 喷气式干燥机
四、实木颗粒板刨花分选
(1)刨花分选得目得
分离合格与不合格得刨花,去除尺寸过大得刨花,木片与碎屑;
分离粗细刨花,以实施表芯层刨花分开施胶,满足工艺要求。
(2)分选方法
A机械分选
工作原理:将刨花置于水平或垂直运动得筛网内振动或摆动,根据刨花得重力与惯性,使平面尺寸(长与宽)小于筛网孔得刨花通过筛选,大得则留下.
B 气流分选
工作原理:将刨花置于气流中,通过气流得运动,借助刨花得质量与表面积得比例,将刨花分成不同等级(根据刨花厚度分选)。
在原材树种,刨花长度与宽度确定得情况下,刨花得运动状态主要取决于厚度。
C 机械气流分选
通过气流分选选出表层刨花,较粗得刨花落入圆筒筛进行机械分选,选择合格得刨花与过大刨花(我国少用).
五、实木颗粒板刨花拌胶
1 对胶黏剂得要求
对UF胶得型能要求:固含量:60-65%,粘度:200—400cp,(25℃)PH 值:7—8,与石蜡乳胶得相溶性好;具有一定初粘性,足以使成型板坯在运输过程中边部不会塌散。
既要在热压时快速固化,也要防止胶得早期固化.
无污染至少就是低污染,如低游离甲醛,低游离酚含量。
与阻燃剂,防水剂与防腐剂等有较好得相溶性。
有较宽得使用范围与稳定性,以适应各种混杂树种得生产工艺。
2 拌胶方法
(1)拌胶方法
摩擦法:适用于细小刨花得施胶
涂布法:适用于高粘度得胶液
喷雾法:胶黏剂在空气压力(或液压)作用下,通过喷嘴形成雾状,喷到悬浮状态得刨花上。
(2) 拌胶方法比较
采用喷雾施胶法,50-100%刨花表面被胶粘液覆盖得比列就是刨花总量得90% 而摩擦法小于60%。
施胶方法对刨花表面覆盖率得影响 (表)
采用喷雾施胶法,制成得刨花板力学性能优于摩擦法。
一般建议喷雾工艺参数:空气压力
0、2-0、35Mp a,胶液粘度150-600cp,可获得50um 得胶滴。
施胶方法对胶合强度得影响
3 施胶量
刨花施胶量: 固体树脂胶剂得质量与绝干刨花质量得百分比(%)。
施胶量对板材性能性能得影响:施胶量大板材性能高,但成本高。
施胶量得确定:
不同胶种:UF胶8-12%PF胶5-8%
不同树种:以阔叶树为原材料得施胶比以针叶树得高10%左右。
不同刨花形状与尺寸:刨花得施胶与表面积之间存在一种类似线性得关系.薄刨花,细胞花用胶量大.
刨花表面质量:表面粗糙得刨花施胶量大。
现在刨花板密度在600—700KG/M3 得刨花施胶量一般为:
单层:8—12%
三层:芯层5-6%表层9-12%
渐变结构:8-12%
六、实木颗粒板刨花得成型
1 工艺要求
(1)铺装均匀稳定:表面上得密度与厚度偏差尽可能小,控制方法:用同位数密度计测量板坯各点处得密度与测量刨花得下落量.
(2)板坯结构对称:以板厚中心为对称平面,两侧得树种,刨花形态,含水率,施胶量等对称
(3) 板坯结构合理, 一般芯层站1/2—3/4,表层站1/8-1/4。
随着板得厚度增加,表层含量减小。
(4)板坯应具有足够得初强度,以避免板坯在运输与进入压机前气流造成破坏
2、成型方法
按铺装线成型原理分为:机械成型,气流成型,机械气流成型以及定向成型。
3 、刨花成型设备
机械浦装机
气流铺装机
七、实木颗粒板刨花板坯预压
预压方式:周期式平压,连续式预压
预压工艺:压缩量度1/2-1/3,压力1、5-1、6Mpa,预压时间10-30s,回弹率15-25%
预压机
连续式预压机就是板坯在连续式预压机中,板坯在被压缩状态下移动,板坯就是直接在铺装带上铺装与预压。
辊式预压
履带式预压
八、热压
热压就是制造刨花板得重要工序,正确选择热压规程,热压方法与设
备才能生产出理想得板子
1 刨花板得热压工艺条件
(1) 刨花板得含水率按生产工艺分别为:
周期式:单层板9-14%
三层板得中层9-12%
三层板得外层12—16%
连续式压机,履带式压机9-11%
挤压法压机10-15%
(2)不同比重得刨花板热压就是得单位压力如下:
比重0、4以下得:0、2-0、7Mpa
0、4-0、85得0、7-2、5
0、85以上2、5-7
(3) 热压温度
脲醛胶刨花板:110-140℃
酚醛胶: 140—155℃
(4)热压时间
树脂胶:0、7-1、0 min/nmm 板厚
蛋白胶:1、4-2、0
2热压设备
周期式(多层热压机,单层热压机)
连续式(辊式连续热压机,钢带平板连续热压机)
九、实木颗粒板后期处理
1 热处理
为提高刨花板得耐水性,(喷石蜡,热空气循环处理)
2 等湿处理
平衡含水率。
(存放5-8天使板子平均含水率在8—10%)3裁边,砂光。