薄膜高密度互连技术及其应用
薄膜技术的发展和应用

薄膜技术的发展和应用随着科技的不断进步,薄膜技术也得到了广泛应用和发展。
本文将就薄膜技术的发展和应用进行介绍。
一、薄膜技术的定义和分类薄膜技术是指将材料以极薄的层数覆盖在基材表面上的技术。
薄膜技术因其独特的性质,在电子、医疗、能源、光电和材料领域都有广泛的应用。
薄膜技术按照制备工艺可分为物理气相沉积法、化学气相沉积法、溅射法、离子束沉积法和溶液法等。
其中,物理气相沉积法和化学气相沉积法是基于气相反应制备薄膜,而溅射法和离子束沉积法则是基于固态反应制备薄膜。
二、薄膜技术的应用1、电子领域薄膜技术在电子领域有着广泛的应用,如显示器件中的膜电极和透光薄膜,硅上集成电路中的金属线薄膜和凸点薄膜,以及太阳能电池中的透明导电膜等。
通过不同种类的薄膜组合,可以制造出光电显示器件、光二极管、半导体器件等。
2、医疗领域薄膜技术在医疗领域也有广泛的应用,如人造器官表面的生物相容性薄膜、药物释放薄膜、医用传感器薄膜、隔离膜和过滤膜等。
这些薄膜可以帮助医学界实现更好的医学检测和治疗。
3、能源领域薄膜技术在能源领域也发挥了重要的作用,如太阳能电池和燃料电池中的薄膜。
通过合适的制备工艺可以制造出透明导电膜、锂离子电池隔膜、固体氧化物燃料电池氧离子传输膜等薄膜材料。
4、光电领域光电领域是薄膜技术应用较早的领域之一,尤其是光学涂层和抗反射膜方面的应用。
薄膜技术不仅可以增强光学元件的透过率和强度,还可以制造仿生光学器件等。
5、材料领域薄膜技术还可以制造出纳米微观结构,实现材料性质的精细控制,如金属膜的纳米微结构、高分子复合薄膜、磁性薄膜等,这些材料在生产制造、传感器等领域有广泛的应用。
三、薄膜技术未来的发展趋势随着技术的不断更新,薄膜技术也在不断地发展和创新。
未来薄膜技术的发展趋势将主要集中在以下几个方面:1、多层薄膜技术的发展多层薄膜技术是目前的一个研究热点,它可以实现对于薄膜性质的控制和变化。
通过不同比例的堆叠和改变各种材料的结构和性质,可以制备出更加精细的薄膜材料。
薄膜高密度互连技术及其应用

第 6巷. 第4期
V l NO 4 o 6
电
子
与
封
装
EL CT E RONI CS & P ACKAGI NG
总 第3 期 6 20 年4月 06
综 述
薄膜 高密度互连技术及其应用
云 振 新
( 围营 9 0厂 ,四川 成都 6 0 5 7 1 0 1)
个 表 面上 ,同时覆 盖通孑 的壁 上 。之后 ,用 光刻工 L
就 是一 种 薄 膜 高 密度 互 连 基 片 。这 种 草 片足 制 造
术还能制造高质量 的集成无源元件 ,包括电阻器 、电
1 引言
现代 电子装置对小型化 、轻量化 、高性能化 、多
功能化 、低功耗化和低成本化的要 求不断提高且 日益
容器 、电感器 和各种传输线 。薄膜多层高密度互连结 构不仅尺寸小 、互连密度高 ,而且具有优 异的高频性
能 。薄膜高密度互连技术是一种应用广泛 的小型化集
摘 要 :高 密度互连 ( I HD )基 片在微 电子 集成技 术 中用来缩小尺 寸、减轻 重量和提 高电气性 能。
薄膜技术是获得高密度互连的最佳技术。 文章介绍了薄膜高密度互连技术的概念、 特点、 设计与工艺考
虑 ,并指 出其主要领域 的应 用情 况。
关键词 :高密度互连 ;薄膜技术 ;淀积薄膜型 多芯片组件
和方法进 行制造 一种广泛使 的T 艺足在硅或 氧化
乍 网片 ( 吕 也可 用其 他基 片 )上形 成多层 结构 先 将 聚酰 亚胺涂 覆在网片上 ,逐步升高 温度到 4 5 寸 2 ℃H 同
化 。接 着 ,用 光 刻作 为掩膜 或使 川 光刻 …罔案 的金
对先进封装技术的认识

对先进封装技术的认识先进封装技术是指在集成电路封装过程中利用先进的材料、工艺和设备,以达到提高功能密度、减小尺寸、提高性能和可靠性等目的的新型封装技术。
随着集成电路技术的不断发展和普及,先进封装技术的重要性和应用价值日益凸显。
本文将探讨先进封装技术的发展趋势、特点和应用前景,旨在为读者提供对该领域的全面了解。
一、先进封装技术的发展趋势随着电子产品市场对性能、尺寸和功耗的不断要求提高,先进封装技术已成为集成电路行业发展的重要趋势。
在这种背景下,先进封装技术的发展呈现出以下几个趋势:1.三维封装技术的发展为了提高集成电路的功能密度和性能,传统的二维封装技术已经不能满足市场需求。
三维封装技术通过在垂直方向上堆叠多个芯片,可以在同一封装体积内实现更高的功能密度和性能。
因此,三维封装技术成为了先进封装技术的一个重要发展方向。
2.高密度互连技术的应用高密度互连技术是实现多芯片封装的关键。
通过采用先进的互连工艺和材料,可以在封装体积内实现更多的信号传输通路,从而提高封装的性能和可靠性。
因此,高密度互连技术的应用将成为先进封装技术的一个重要方向。
3.先进材料的应用先进封装技术需要利用具有优异性能的材料来实现。
例如,低介电常数材料可用于减小封装的信号传输损耗,高热导率材料可用于提高封装的散热能力,高可靠性材料可用于提高封装的可靠性。
因此,先进材料的应用将是先进封装技术的一个重要发展方向。
二、先进封装技术的特点先进封装技术相对于传统封装技术具有许多优点,其主要特点包括以下几点:1.功能密度高先进封装技术利用三维封装和高密度互连技术,可以在同一封装体积内实现更多的功能,从而提高芯片的功能密度。
2.尺寸小先进封装技术采用先进的材料和工艺,可以实现更小封装尺寸,从而可以满足电子产品对小型化的需求。
3.性能优越先进封装技术可以通过优化设计和材料的应用,实现更高的传输速率、更低的功耗和更优越的散热能力,从而提高封装的性能。
4.可靠性好先进封装技术的材料和工艺通常经过严格的测试和认证,具有较高的可靠性,能够满足电子产品对可靠性的要求。
高密度互连(HDI)印制电路板技术现状及发展前景
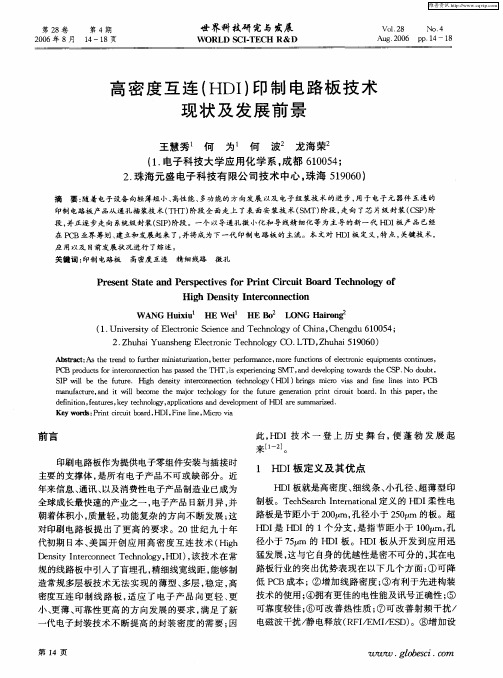
关键词 : 印制 电路板
高密度 互连
精 细线路
微孔
Pr s n t t n r p c i e o i tCic i a d Te h o o y o e e tS a ea d Pe s e tv s f r Pr n r u tBo r c n l g f
2 Z u a Yu segE et nc c n l yC L D, h h i 1 0 0 . h h i a h n l r i Teh o g O. T Z u a 5 9 6 ) n co o
A  ̄ r c : h rn o f rh r mi it r a in, e tr p ro ma c , r u c in f ee to i q ime t o t u s l t a t As t e te d t u t e n a u i t z o b te e f r n e mo e f n t s o lcr n c e u p n s c n i e , o n P B r d c o t ro n t n h s p s e h _ i e p r cn MT , n e e pn o r s t eCs No d u t C p o u t f ri e c n e i a a s d t eT} r, x e i i g S s n c o r s n e a d d v l i g t wa d h P. o b , o
印制 电路 板产品从通孔插装技 术 ( r ) T卜r 阶段 全 面走上 了表 面安 装技 术 ( MT) S 阶段 , 走向 了芯 片级封 装 ( S 阶 C P)
段, 并正逐 步走向 系统级封装 (i ) sp 阶段 。一 个以导通孔微 小化和导 线精 细化等 为主导 的新一代 HD 板产 品 已经 I 在 P B业界 筹划 、 C 建立和发展 起来 了, 并将成 为下一代 印制 电路 板 的主流 。本文对 H 板 定 义 , 点 , DI 特 关键技 术 ,
hdi工艺技术
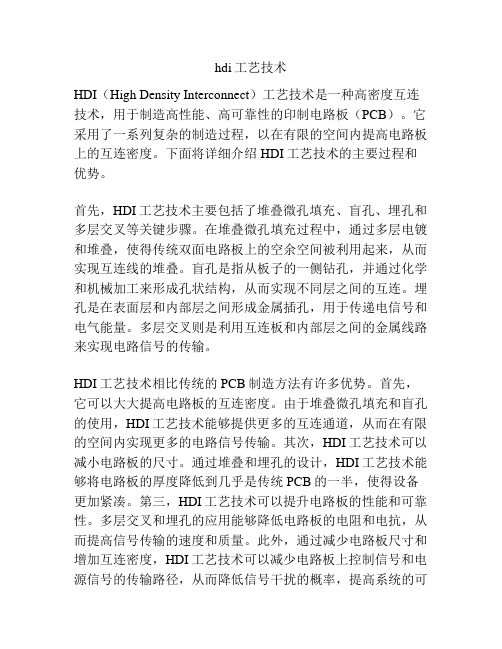
hdi工艺技术HDI(High Density Interconnect)工艺技术是一种高密度互连技术,用于制造高性能、高可靠性的印制电路板(PCB)。
它采用了一系列复杂的制造过程,以在有限的空间内提高电路板上的互连密度。
下面将详细介绍HDI工艺技术的主要过程和优势。
首先,HDI工艺技术主要包括了堆叠微孔填充、盲孔、埋孔和多层交叉等关键步骤。
在堆叠微孔填充过程中,通过多层电镀和堆叠,使得传统双面电路板上的空余空间被利用起来,从而实现互连线的堆叠。
盲孔是指从板子的一侧钻孔,并通过化学和机械加工来形成孔状结构,从而实现不同层之间的互连。
埋孔是在表面层和内部层之间形成金属插孔,用于传递电信号和电气能量。
多层交叉则是利用互连板和内部层之间的金属线路来实现电路信号的传输。
HDI工艺技术相比传统的PCB制造方法有许多优势。
首先,它可以大大提高电路板的互连密度。
由于堆叠微孔填充和盲孔的使用,HDI工艺技术能够提供更多的互连通道,从而在有限的空间内实现更多的电路信号传输。
其次,HDI工艺技术可以减小电路板的尺寸。
通过堆叠和埋孔的设计,HDI工艺技术能够将电路板的厚度降低到几乎是传统PCB的一半,使得设备更加紧凑。
第三,HDI工艺技术可以提升电路板的性能和可靠性。
多层交叉和埋孔的应用能够降低电路板的电阻和电抗,从而提高信号传输的速度和质量。
此外,通过减少电路板尺寸和增加互连密度,HDI工艺技术可以减少电路板上控制信号和电源信号的传输路径,从而降低信号干扰的概率,提高系统的可靠性。
总的来说,HDI工艺技术是一种先进的PCB制造技术,能够实现更高的互连密度、更小尺寸的电路板以及更高性能和可靠性的电路设计。
随着电子产品的发展和需求的不断增加,HDI 工艺技术也将得到广泛的应用。
在未来,我们可以预见,HDI 工艺技术将继续发展,为电子设备带来更多的创新和突破。
薄膜技术及应用

20世纪末至今
随着新材料和制备技术的 不断发展,新型薄膜材料 不断涌现,薄膜技术应用 领域不断扩大。
02
薄膜制备技术
物理气相沉积(PVD)
真空蒸发沉积
利用加热蒸发材料,使其 原子或分子从固态表面升 华进入气态,然后在基底 表面凝结形成薄膜。
导体薄膜
功能薄膜
用于制造集成电路、微电子器件和薄 膜晶体管等,具有高导电性能和稳定 性。
如光电转换薄膜、磁性薄膜、传感器 用敏感薄膜等,在电子器件中具有特 定功能。
绝缘薄膜
用作电子器件的介质层和绝缘材料, 具有低介电常数和损耗、高击穿场强 等特点。
光学领域
反射和滤光薄膜
用于控制光的反射、透射、干涉和偏振等特性, 在光学仪器、摄影、照明等领域有广泛应用。
多功能化薄膜
通过材料复合和结构设计,制备具有多功能特性的薄膜,如光学、热学、电学、磁学等多重性能的集 成。
THANKS FOR WATCHING
感谢您的观看
薄膜的分类
01
按材料分类
金属薄膜、制备方法分类
功能薄膜(如导电薄膜、光学薄 膜、磁性薄膜等)、结构薄膜等。
物理气相沉积、化学气相沉积、 溶胶-凝胶法等。
薄膜技术的发展历程
01
02
03
19世纪末
真空蒸发镀膜技术出现, 主要用于制造光学仪器和 装饰品。
20世纪中期
薄膜技术及应用
目录
• 薄膜技术简介 • 薄膜制备技术 • 薄膜的应用领域 • 薄膜的未来发展与挑战
01
薄膜技术简介
薄膜的定义与特性
定义
薄膜是一种厚度在微米到纳米级别的 材料,覆盖在基底上,具有特定的物 理、化学和机械性能。
高密度互连积层板研发制造方案(二)

高密度互连积层板研发制造方案一、实施背景随着科技的飞速发展,电子设备正朝着更轻、更薄、更高效的方向发展。
高密度互连积层板(HDI)作为PCB(Printed Circuit Board,印刷电路板)的一种,因其高集成度、高可靠性、低重量等优点,已成为航空航天、医疗设备、智能手机、汽车电子等领域的关键组件。
当前,HDI市场主要由日本、韩国和中国台湾等少数企业主导,国内企业在高端市场上的竞争力较弱。
因此,开展高密度互连积层板的研发制造,对于提升国内企业在该领域的竞争力,具有重要意义。
二、工作原理HDI是一种多层板,其制造过程主要包括以下几个步骤:1.基材制备:采用高导热、低膨胀系数、高耐腐蚀性的材料作为基材。
2.线路制作:在基材上采用激光切割或化学腐蚀等方式制作线路。
3.绝缘层制作:在制作好的线路层之间添加绝缘材料。
4.孔金属化:通过电镀或化学镀的方式在需要的孔内形成金属化层。
5.焊接:通过焊接将各层线路连接起来。
其中,孔金属化是HDI制造的关键技术之一。
由于孔径小、孔深,且需满足不同导电层之间的连接,因此对孔金属化的制备工艺和技术要求极高。
三、实施计划步骤1.技术研究:开展HDI制造关键技术的研发,包括孔金属化技术、多层板制作技术等。
2.设备选型与采购:根据技术研发需要,采购相应的制造设备和检测设备。
3.工艺流程设计:根据HDI的制造特点,设计合理的工艺流程。
4.中试生产:在实验室条件下进行小批量生产,验证工艺流程的可行性。
5.批量生产:根据中试结果,调整工艺参数,进行批量生产。
6.产品检测与认证:对生产的产品进行性能检测和认证。
7.市场推广:将产品推向市场,与需求方建立合作关系。
四、适用范围HDI适用于以下领域:1.航空航天:HDI的高可靠性、低重量特性使其成为航空航天领域的首选组件。
2.医疗设备:HDI的精密线路制作能力使其成为医疗设备的重要组件。
3.智能手机:HDI的高集成度使其成为智能手机主板的首选材料。
薄膜技术的理论和应用

薄膜技术的理论和应用薄膜技术是一种高新技术,它通过将材料分子层层堆积析出而形成一种薄而均匀的材料。
薄膜技术的应用非常广泛,包括光电、电子、化工、食品、医疗等领域。
本文将从薄膜技术的理论和应用两个方面来详细探讨。
一、薄膜技术的理论1. 薄膜生长模型薄膜生长模型是研究薄膜形成规律的数学模型。
它可以描述薄膜生长的物理过程,并预测薄膜的形态和结构。
在薄膜生长模型中,主要包括表面扩散、沉积、缺陷漂浮、晶化、成核等几个重要步骤。
这些步骤影响着薄膜的形态和质量。
薄膜生长模型的出现,为薄膜技术的发展提供了重要的理论基础。
2. 薄膜吸附理论在薄膜形成过程中,吸附理论是非常重要的。
它可以描述薄膜形成的过程中物质分子与基底表面的物理化学现象。
普通的吸附理论往往是以吸附能为研究对象,但是对于薄膜来说,由于它的尺寸极小,故应采用尺寸效应吸附理论。
这个理论为薄膜技术的精确控制提供了良好的理论依据。
3. 薄膜在化学反应中的应用化学反应中使用薄膜技术,常常采用气相沉积、热蒸发等方法。
在化学反应中,薄膜的化学反应起到重要的作用,可以产生一些特殊的物理化学性质。
因此,薄膜技术在催化、传感等领域发挥着重要的作用。
4. 纳米薄膜技术纳米薄膜技术是薄膜技术的一个分支,它将薄膜做到了纳米尺度。
纳米薄膜具有极高的比表面积和表面反应性,因此在传感、催化、光电等领域有着广泛的应用前景。
同时,纳米薄膜技术的研究也给薄膜技术开发提供了重要的思路。
二、薄膜技术的应用1. 光电领域薄膜技术在光电领域有着广泛的应用。
例如,太阳能电池、液晶显示器等都是依靠薄膜技术制成的。
此外,薄膜技术在光学薄膜、光学滤波、全息成像等领域也都有着广泛的应用。
2. 电子领域薄膜技术在电子领域的应用也非常广泛。
例如,利用薄膜技术可以制备高温超导材料,用于高功率电子器件;还可以制备高品质的晶体管。
此外,在电阻器、金属线、电容器等器件中也广泛使用了薄膜技术的成果。
3. 化学领域在化学领域,薄膜技术应用非常广泛。
基板ABF材料成分
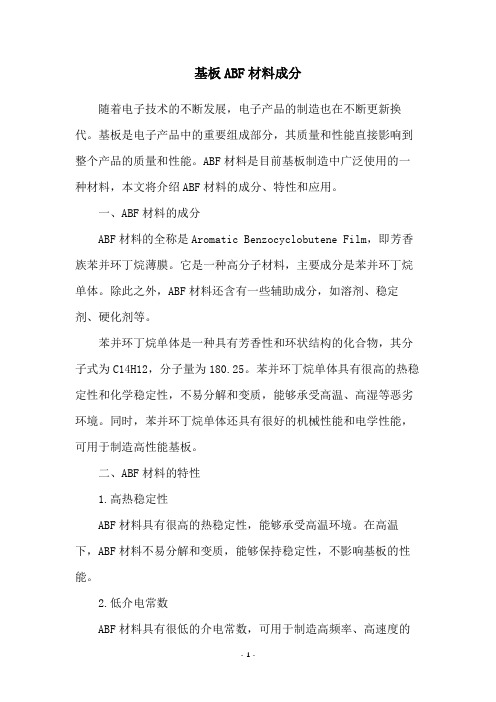
基板ABF材料成分随着电子技术的不断发展,电子产品的制造也在不断更新换代。
基板是电子产品中的重要组成部分,其质量和性能直接影响到整个产品的质量和性能。
ABF材料是目前基板制造中广泛使用的一种材料,本文将介绍ABF材料的成分、特性和应用。
一、ABF材料的成分ABF材料的全称是Aromatic Benzocyclobutene Film,即芳香族苯并环丁烷薄膜。
它是一种高分子材料,主要成分是苯并环丁烷单体。
除此之外,ABF材料还含有一些辅助成分,如溶剂、稳定剂、硬化剂等。
苯并环丁烷单体是一种具有芳香性和环状结构的化合物,其分子式为C14H12,分子量为180.25。
苯并环丁烷单体具有很高的热稳定性和化学稳定性,不易分解和变质,能够承受高温、高湿等恶劣环境。
同时,苯并环丁烷单体还具有很好的机械性能和电学性能,可用于制造高性能基板。
二、ABF材料的特性1.高热稳定性ABF材料具有很高的热稳定性,能够承受高温环境。
在高温下,ABF材料不易分解和变质,能够保持稳定性,不影响基板的性能。
2.低介电常数ABF材料具有很低的介电常数,可用于制造高频率、高速度的电子产品。
其介电常数在2.8左右,比常见的FR-4材料低很多。
3.高机械性能ABF材料具有很好的机械性能,不易破裂和变形。
其弯曲强度和模量都比FR-4材料高。
4.良好的电学性能ABF材料具有很好的电学性能,可用于制造高性能电子产品。
其表面电阻率和体积电阻率都比FR-4材料低,且具有很好的耐电压性能。
5.易加工性ABF材料易于加工和成型,可用于制造各种形状和尺寸的基板。
其加工性能比FR-4材料好,可实现更高精度的加工。
三、ABF材料的应用ABF材料广泛应用于基板制造领域,主要用于制造高性能、高速度、高频率的电子产品。
以下是ABF材料的几个主要应用领域: 1.高速度和高频率应用ABF材料具有很低的介电常数和损耗,能够实现高速度和高频率的信号传输。
因此,它被广泛应用于制造高速度、高频率的电子产品,如服务器、路由器、高速传输接口等。
HDI板高密度互连板简介演示

金属化孔制作
金属化孔是HDI板实现导电的关键,其制作质量直接影响 HDI板的电气性能。
金属化孔的制作方法有电镀、化学镀、蒸发等,这些方法 可以根据需要进行选择,以达到最佳的金属化效果。
表面处理
表面处理是HDI板制造的最后一步,它决定了HDI板的外观和性能。
表面处理方法有多种,如氧化、镀膜、喷涂等,这些方法可以增强HDI板的耐腐 蚀性、绝缘性和美观度。
技术创新与突破
新型材料
01
采用新型的高导电材料和低损耗绝缘材料,提高HDI板的性能和
可靠性。
微型化工艺
02
通过更精细的加工技术和微型化工艺,减小HDI板的尺寸和重量
,满足便携式和穿戴式设备的需求。
集成化技术
03
将多个功能模块集成在一块HDI板上,实现多功能一体化,提高
设备的紧凑性和集成度。
市场前景展望
优化信号传输
高密度互连技术能够优化电路布局,减少信号传输路径和延迟,提 高信号传输速度和稳定性。
降低能耗
通过减小线路长度和降低线路电阻,高密度互连技术有助于降低能 耗,减少热量产生。
微孔加工技术
01
02
03
实现精细加工
微孔加工技术能够在HDI 板上加工出微米级甚至纳 米级的孔径,实现精细电 路结构和互连。
特点
HDI板具有高密度、高可靠性、低成 本、轻薄等特点,广泛应用于通信、 计算机、医疗、航空航天等高科技领 域。
HDI板的应用领域
通信
HDI板在通信领域中广泛应用 于基站、路由器、交换机等通
信设备的制造。
计算机
HDI板用于制造笔记本电脑、 平板电脑、服务器等计算机硬 件。
医疗
HDI板在医疗领域中用于制造 医疗设备和仪器的控制电路板 。
hdi生产工艺
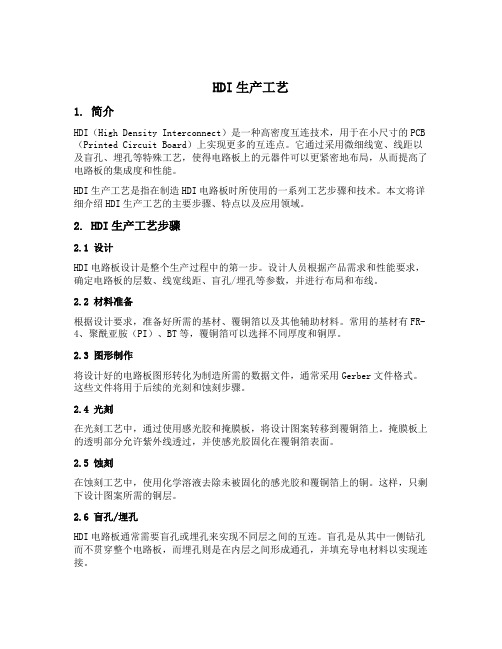
HDI生产工艺1. 简介HDI(High Density Interconnect)是一种高密度互连技术,用于在小尺寸的PCB (Printed Circuit Board)上实现更多的互连点。
它通过采用微细线宽、线距以及盲孔、埋孔等特殊工艺,使得电路板上的元器件可以更紧密地布局,从而提高了电路板的集成度和性能。
HDI生产工艺是指在制造HDI电路板时所使用的一系列工艺步骤和技术。
本文将详细介绍HDI生产工艺的主要步骤、特点以及应用领域。
2. HDI生产工艺步骤2.1 设计HDI电路板设计是整个生产过程中的第一步。
设计人员根据产品需求和性能要求,确定电路板的层数、线宽线距、盲孔/埋孔等参数,并进行布局和布线。
2.2 材料准备根据设计要求,准备好所需的基材、覆铜箔以及其他辅助材料。
常用的基材有FR-4、聚酰亚胺(PI)、BT等,覆铜箔可以选择不同厚度和铜厚。
2.3 图形制作将设计好的电路板图形转化为制造所需的数据文件,通常采用Gerber文件格式。
这些文件将用于后续的光刻和蚀刻步骤。
2.4 光刻在光刻工艺中,通过使用感光胶和掩膜板,将设计图案转移到覆铜箔上。
掩膜板上的透明部分允许紫外线透过,并使感光胶固化在覆铜箔表面。
2.5 蚀刻在蚀刻工艺中,使用化学溶液去除未被固化的感光胶和覆铜箔上的铜。
这样,只剩下设计图案所需的铜层。
2.6 盲孔/埋孔HDI电路板通常需要盲孔或埋孔来实现不同层之间的互连。
盲孔是从其中一侧钻孔而不贯穿整个电路板,而埋孔则是在内层之间形成通孔,并填充导电材料以实现连接。
2.7 堆叠与压合通过堆叠多个经过处理的内外层,使得整个HDI电路板具有更高的集成度和互连能力。
堆叠后的电路板需要经过压合工艺,以确保各层之间的粘合度。
2.8 表面处理为了提高电路板的焊接性能和耐腐蚀性,常常需要对表面进行处理。
常见的表面处理方法有镀金、喷锡、喷镍等。
2.9 最终检测与包装在完成上述工艺步骤后,对HDI电路板进行最终检测,确保其符合设计要求和性能指标。
薄膜材料制备原理、技术及应用
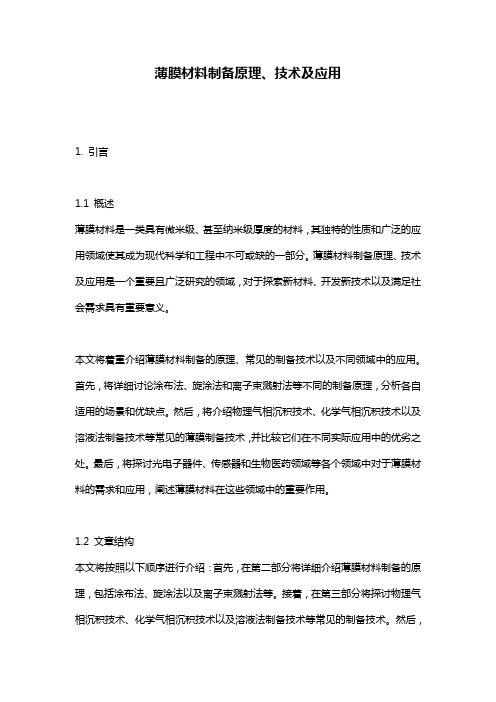
薄膜材料制备原理、技术及应用1. 引言1.1 概述薄膜材料是一类具有微米级、甚至纳米级厚度的材料,其独特的性质和广泛的应用领域使其成为现代科学和工程中不可或缺的一部分。
薄膜材料制备原理、技术及应用是一个重要且广泛研究的领域,对于探索新材料、开发新技术以及满足社会需求具有重要意义。
本文将着重介绍薄膜材料制备的原理、常见的制备技术以及不同领域中的应用。
首先,将详细讨论涂布法、旋涂法和离子束溅射法等不同的制备原理,分析各自适用的场景和优缺点。
然后,将介绍物理气相沉积技术、化学气相沉积技术以及溶液法制备技术等常见的薄膜制备技术,并比较它们在不同实际应用中的优劣之处。
最后,将探讨光电子器件、传感器和生物医药领域等各个领域中对于薄膜材料的需求和应用,阐述薄膜材料在这些领域中的重要作用。
1.2 文章结构本文将按照以下顺序进行介绍:首先,在第二部分将详细介绍薄膜材料制备的原理,包括涂布法、旋涂法以及离子束溅射法等。
接着,在第三部分将探讨物理气相沉积技术、化学气相沉积技术以及溶液法制备技术等常见的制备技术。
然后,在第四部分将介绍薄膜材料在光电子器件、传感器和生物医药领域中的应用,包括各个领域需求和现有应用案例。
最后,在结论部分对整篇文章进行总结,并提出未来研究方向和展望。
1.3 目的本文旨在全面系统地介绍薄膜材料制备原理、技术及应用,为读者了解该领域提供一个基本知识框架。
通过本文的阐述,读者可以充分了解不同的制备原理和方法,并了解到不同领域中对于特定功能或性质的薄膜材料的需求与应用。
同时,本文还将重点突出薄膜材料在光电子器件、传感器和生物医药领域中的重要作用,以期为相关研究提供参考和启发。
以上为“1. 引言”部分内容的详细清晰撰写,请根据需要进行修改补充完善。
2. 薄膜材料制备原理:2.1 涂布法制备薄膜:涂布法是一种常见的制备薄膜的方法,它适用于各种材料的制备。
首先,将所需材料以溶解或悬浮态形式制成液体,然后利用刷子、喷雾或浸渍等方式将液体均匀地涂敷在基板上。
hdi合成工艺
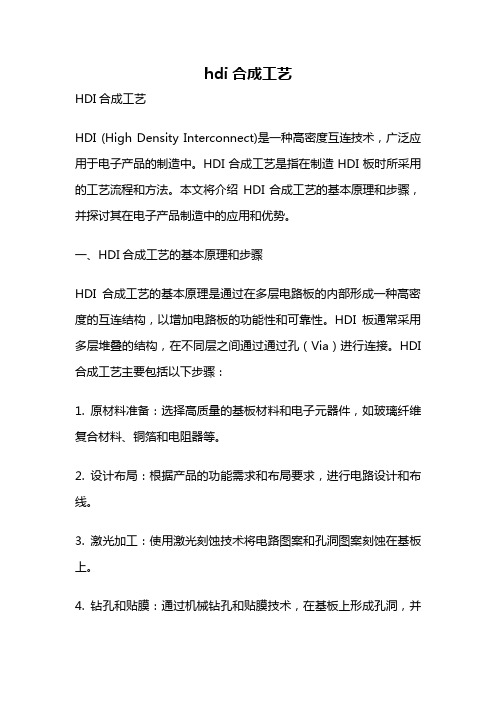
hdi合成工艺HDI合成工艺HDI (High Density Interconnect)是一种高密度互连技术,广泛应用于电子产品的制造中。
HDI合成工艺是指在制造HDI板时所采用的工艺流程和方法。
本文将介绍HDI合成工艺的基本原理和步骤,并探讨其在电子产品制造中的应用和优势。
一、HDI合成工艺的基本原理和步骤HDI合成工艺的基本原理是通过在多层电路板的内部形成一种高密度的互连结构,以增加电路板的功能性和可靠性。
HDI板通常采用多层堆叠的结构,在不同层之间通过通过孔(Via)进行连接。
HDI 合成工艺主要包括以下步骤:1. 原材料准备:选择高质量的基板材料和电子元器件,如玻璃纤维复合材料、铜箔和电阻器等。
2. 设计布局:根据产品的功能需求和布局要求,进行电路设计和布线。
3. 激光加工:使用激光刻蚀技术将电路图案和孔洞图案刻蚀在基板上。
4. 钻孔和贴膜:通过机械钻孔和贴膜技术,在基板上形成孔洞,并在孔洞内部镀上一层导电膜。
5. 堆叠层压:将多个经过处理的基板层叠在一起,并使用压力和热量将其压合。
6. 内部连接:在堆叠的基板层之间形成互连通道,通过导电膜和孔洞进行电路连接。
7. 外层制造:在堆叠结构的外部形成表面电路图案,并进行金属化处理。
8. 最终加工:进行最终的修整和测试,确保HDI板的功能和可靠性。
二、HDI合成工艺在电子产品制造中的应用和优势HDI合成工艺在电子产品制造中具有广泛的应用和重要的优势。
1. 提高了电路板的功能性:HDI合成工艺可以大大增加电路板的功能性和集成度。
通过在多层电路板内部形成高密度的互连结构,可以实现更复杂的电路设计和布线,满足各种功能需求。
2. 提高了电路板的可靠性:HDI合成工艺可以提高电路板的可靠性和稳定性。
通过采用高质量的材料和精密的制造工艺,可以减少电路板的故障率和失效率,提高产品的寿命和性能。
3. 减小了电路板的尺寸和重量:HDI合成工艺可以显著减小电路板的尺寸和重量。
hdi生产工艺

hdi生产工艺HDI生产工艺简介•HDI(High Density Interconnect)即高密度互连技术,是一种新型的电路板制造工艺。
•HDI生产工艺在实现高密度互连的同时,提升了电路板的性能和可靠性。
工艺流程1.设计阶段–使用CAD软件进行电路板设计。
–确定板层结构和层次划分。
2.材料准备–选择高质量的基板材料,如FR-4、高Tg材料等。
–准备合适尺寸的耐热胶片、中间层和薄钼箔。
3.印制内层板–在基板上涂覆铜箔。
–利用光刻技术制作互连图形。
–酸蚀去除多余铜箔。
4.人工堆叠–根据设计要求,将印制好的内层板和其他材料按照设计顺序堆叠在一起。
5.压合–将堆叠好的板材进行高温高压的压合,使其紧密结合。
6.钻孔–利用激光钻孔机对板材进行钻孔,形成互连通孔。
7.化学镀铜–通过电化学反应,在互连通孔内形成导电铜层。
8.镭射光刻–利用镭射光刻机器绘制外层图形。
9.酸蚀与艾纳普电镀–酸蚀去除未被光刻保护的铜箔。
–进行电镀,增加铜箔导电性。
10.表面处理–在电路板的表面形成焊接和防腐蚀层。
–可选择镍/金、锡/铅等材料进行处理。
11.最终测试–对生产好的HDI电路板进行全面的功能和可靠性测试。
特点与应用•特点:–高密度互连:通过减小通孔间距和孔径,实现更高密度的互连。
–降低电磁干扰:采用层与层之间引线及盲通孔结构,减少信号互相干扰的可能性。
–小型化和轻量化:可在有限空间内实现更多功能,适用于小尺寸的电子设备。
–提升性能和可靠性:稳定的制造工艺和高品质材料,提高电路板的性能和可靠性。
•应用:–移动通信设备:如智能手机、平板电脑等。
–汽车电子系统:如车载导航、车载娱乐系统等。
–医疗器械:如医疗监测设备、移植仪器等。
HDI生产工艺的发展为电子产品的革新提供了关键支持,带来了更高的性能、更小的体积和更好的可靠性,将继续在电子制造行业发挥重要作用。
未来发展趋势随着科技的不断进步和需求的增长,HDI生产工艺也在不断发展和创新。
高密度互连_HDI_印制电路板技术现状及发展前景
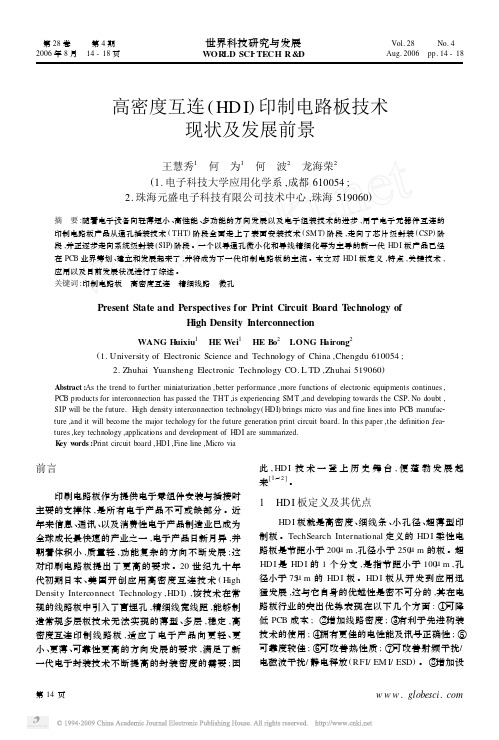
高密度互连(HD I)印制电路板技术现状及发展前景王慧秀1 何 为1 何 波2 龙海荣2(1.电子科技大学应用化学系,成都610054;2.珠海元盛电子科技有限公司技术中心,珠海519060)摘 要:随着电子设备向轻薄短小、高性能、多功能的方向发展以及电子组装技术的进步,用于电子元器件互连的印制电路板产品从通孔插装技术(THT)阶段全面走上了表面安装技术(SM T)阶段,走向了芯片级封装(CSP)阶段,并正逐步走向系统级封装(SIP)阶段。
一个以导通孔微小化和导线精细化等为主导的新一代HDI板产品已经在PCB业界筹划、建立和发展起来了,并将成为下一代印制电路板的主流。
本文对HDI板定义,特点,关键技术,应用以及目前发展状况进行了综述。
关键词:印制电路板 高密度互连 精细线路 微孔Present State and Perspectives for Print Circuit Board T echnology ofHigh Density InterconnectionWANG H uixiu1 HE Wei1 HE Bo2 LONG H airong2 (1.University of Electronic Science and Technology of China,Chengdu610054;2.Zhuhai Yuansheng Electronic Technology CO.L TD,Zhuhai519060)Abstract:As the trend to further miniaturization,better performance,more functions of electronic equipments continues, PCB products for interconnection has passed the THT,is experiencing SM T,and developing towards the CSP.No doubt, SIP will be the future.High density interconnection technology(HDI)brings micro vias and fine lines into PCB manufac2 ture,and it will become the major techology for the future generation print circuit board.In this paper,the definition,fea2 tures,key technology,applications and development of HDI are summarized.K ey w ords:Print circuit board,HDI,Fine line,Micro via前言 印刷电路板作为提供电子零组件安装与插接时主要的支撑体,是所有电子产品不可或缺部分。
高密度2.5D TSV转接板关键技术研究
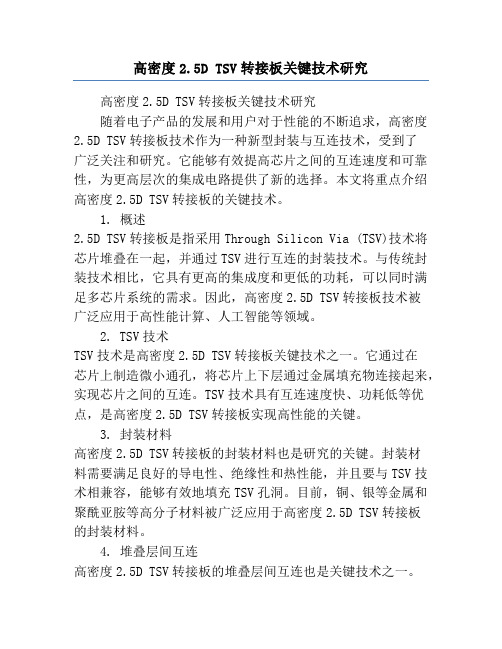
高密度2.5D TSV转接板关键技术研究高密度2.5D TSV转接板关键技术研究随着电子产品的发展和用户对于性能的不断追求,高密度2.5D TSV转接板技术作为一种新型封装与互连技术,受到了广泛关注和研究。
它能够有效提高芯片之间的互连速度和可靠性,为更高层次的集成电路提供了新的选择。
本文将重点介绍高密度2.5D TSV转接板的关键技术。
1. 概述2.5D TSV转接板是指采用Through Silicon Via (TSV)技术将芯片堆叠在一起,并通过TSV进行互连的封装技术。
与传统封装技术相比,它具有更高的集成度和更低的功耗,可以同时满足多芯片系统的需求。
因此,高密度2.5D TSV转接板技术被广泛应用于高性能计算、人工智能等领域。
2. TSV技术TSV技术是高密度2.5D TSV转接板关键技术之一。
它通过在芯片上制造微小通孔,将芯片上下层通过金属填充物连接起来,实现芯片之间的互连。
TSV技术具有互连速度快、功耗低等优点,是高密度2.5D TSV转接板实现高性能的关键。
3. 封装材料高密度2.5D TSV转接板的封装材料也是研究的关键。
封装材料需要满足良好的导电性、绝缘性和热性能,并且要与TSV技术相兼容,能够有效地填充TSV孔洞。
目前,铜、银等金属和聚酰亚胺等高分子材料被广泛应用于高密度2.5D TSV转接板的封装材料。
4. 堆叠层间互连高密度2.5D TSV转接板的堆叠层间互连也是关键技术之一。
堆叠层间互连需要通过TSV和封装材料实现芯片之间的电气连接。
为了实现高密度的互连,需要设计合适的TSV布局和通孔间距,并制定堆叠层间连接的工艺过程。
5. 热管理由于高密度2.5D TSV转接板的堆叠结构,芯片之间反复传递大量的能量,其热管理成为另一个重要的关键技术。
合理的散热设计和热导材料的选择能够有效地降低芯片的工作温度,提高系统的可靠性。
6. 测试与可靠性高密度2.5D TSV转接板的测试与可靠性评估也是关键技术研究的重点。
hdi的工艺技术
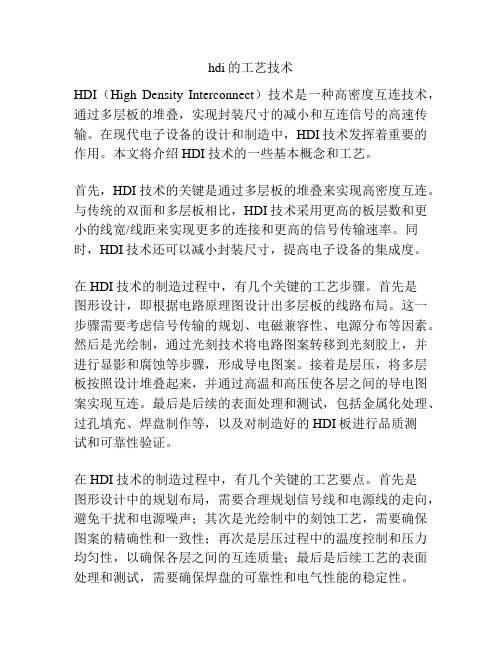
hdi的工艺技术HDI(High Density Interconnect)技术是一种高密度互连技术,通过多层板的堆叠,实现封装尺寸的减小和互连信号的高速传输。
在现代电子设备的设计和制造中,HDI技术发挥着重要的作用。
本文将介绍HDI技术的一些基本概念和工艺。
首先,HDI技术的关键是通过多层板的堆叠来实现高密度互连。
与传统的双面和多层板相比,HDI技术采用更高的板层数和更小的线宽/线距来实现更多的连接和更高的信号传输速率。
同时,HDI技术还可以减小封装尺寸,提高电子设备的集成度。
在HDI技术的制造过程中,有几个关键的工艺步骤。
首先是图形设计,即根据电路原理图设计出多层板的线路布局。
这一步骤需要考虑信号传输的规划、电磁兼容性、电源分布等因素。
然后是光绘制,通过光刻技术将电路图案转移到光刻胶上,并进行显影和腐蚀等步骤,形成导电图案。
接着是层压,将多层板按照设计堆叠起来,并通过高温和高压使各层之间的导电图案实现互连。
最后是后续的表面处理和测试,包括金属化处理、过孔填充、焊盘制作等,以及对制造好的HDI板进行品质测试和可靠性验证。
在HDI技术的制造过程中,有几个关键的工艺要点。
首先是图形设计中的规划布局,需要合理规划信号线和电源线的走向,避免干扰和电源噪声;其次是光绘制中的刻蚀工艺,需要确保图案的精确性和一致性;再次是层压过程中的温度控制和压力均匀性,以确保各层之间的互连质量;最后是后续工艺的表面处理和测试,需要确保焊盘的可靠性和电气性能的稳定性。
HDI技术的应用非常广泛,例如在智能手机、平板电脑和笔记本电脑等电子产品中。
HDI技术可以实现更小的封装尺寸,提高设备的集成度和可靠性。
同时,HDI技术还可以实现更高的信号传输速率,满足高速数据传输和通信需求。
在未来,随着电子设备的不断进步和智能化的发展,HDI技术将继续发挥着重要的作用。
综上所述,HDI技术是一种高密度互连技术,通过多层板的堆叠来实现高密度互连和信号传输。
hdi流程工艺技术

hdi流程工艺技术HDI(High Density Interconnect)是一种高密度互连技术,用于制造多层印制电路板(PCB)。
HDI流程工艺技术是为了满足现代电子产品对更小、更轻、更高性能的要求而发展起来的。
HDI流程工艺技术一般分为以下几个步骤:首先是基板制备。
基板通常由玻璃纤维与环氧树脂复合材料构成,制备基板的过程包括材料选择、切割、清洗、钻孔等工序。
在HDI技术中,通常需要进行微孔钻孔和盲孔钻孔,以满足高密度布线的要求。
然后是图形化处理。
通过光刻技术,将电路设计转移到基板上。
这个过程涉及到照相、曝光、显影等步骤,最终形成图案化的电路线路。
接下来是电镀和制作多层。
在电镀工艺过程中,将电路板浸入电解液中,利用电流使其表面镀上一层金属,以提高导电性。
制作多层是为了增加电路板的布线密度,通过将多个薄板层叠在一起并使用层间电镀技术,以实现电路的互连。
然后是图形化处理第二次。
在HDI流程工艺技术中,通常需要进行多次图形化处理,以满足高密度布线的要求。
这包括用光刻技术制作更细小的线路,并且需要更高的精度和分辨率。
最后是外层处理。
外层处理是为了保护电路线路,提供更好的焊接性能和电阻特性。
这包括覆盖清漆、锡镀等工艺,以提高电路板的可靠性和耐久性。
HDI流程工艺技术的优点在于它可以实现更高的布线密度、更低的信号损耗和更好的电热性能。
这使得HDI技术在现代电子产品中得到了广泛应用,如智能手机、平板电脑、笔记本电脑等。
然而,HDI流程工艺技术也存在一些挑战。
首先是生产成本较高,特别是在多层制作和精度要求较高的情况下。
其次,HDI 技术需要更为复杂的制造设备和技术,对制造商的要求较高。
总的来说,HDI流程工艺技术是一种提高电路板布线密度和性能的重要技术。
随着电子产品对更小、更轻、更高性能的需求不断增加,HDI技术将继续得到广泛应用和进一步发展。
《电子与封装》2006年 第6卷1~12期目次索引

周亚丽 ,周
辰
倒装芯片热电极键合_ T艺研究 不锈钢压力传感器管座 电子封装中的铝碳化硅及其应用 测试系统分析方法研究 集成电路封装中的引线键合技术
贴片机视觉 对中系统
程 明生 ,陈该青 ,蒋健乾
严志 良
龙
乐
周 亚 丽 。黄 芝 花
黄玉财 ,程 秀兰 ,蔡俊荣
鲜 飞
七 (1 ) 6
谢 广超
Xi g h n u n s e gLi
P c a i ga d P ro ma c f 8 n B o dAr aS mi o d co a e s a k gn n e r n eo 0 m r a e e c n u t r sr f 9 L
(6 )
Xu -e h n , o gYa e ,i g e a e rn Z a gT n rT eJn —n Lu n l
二 (1O )
二 (1 6 )
二 (2 O )
高体积分数电子封装用铝基复合材料陛能研究
封 装树脂 与 P G 层 的关 系 K 分
修子扬 ,张强 ,武 高辉 ,等
铌 酸锂声 表面波 S MD的全 陶瓷封 装
曾 理 , 陈 文 嫒 ,谢 诗 文 ,等
维普资讯
第 6卷 , 1 第 2期
V 1 6 No 1 o . 2
. .
电 子
与
封
装
EL CTRONI E CS & P CKAGI A I NG
总 第4 4期 20 0 6年 l 2月
《 电子 与封装 》2 6年 0 0
第 6 1 1 期 目次索弓 卷 ~2
(1 6 )
电能计量专用集成电路测试方法研究
HDI制作流程
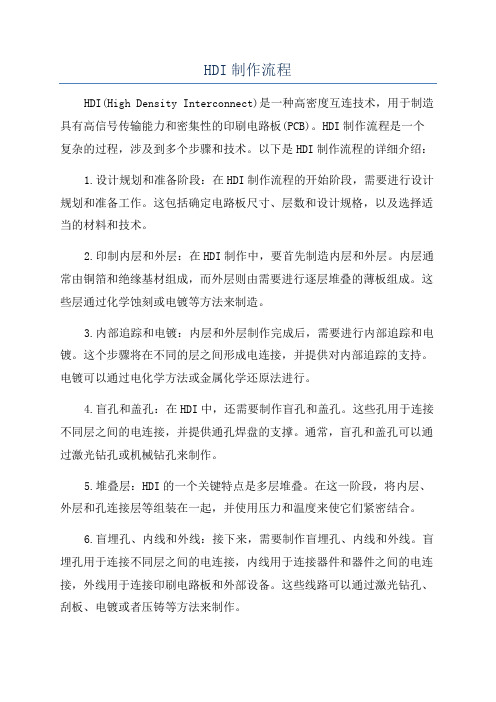
HDI制作流程HDI(High Density Interconnect)是一种高密度互连技术,用于制造具有高信号传输能力和密集性的印刷电路板(PCB)。
HDI制作流程是一个复杂的过程,涉及到多个步骤和技术。
以下是HDI制作流程的详细介绍:1.设计规划和准备阶段:在HDI制作流程的开始阶段,需要进行设计规划和准备工作。
这包括确定电路板尺寸、层数和设计规格,以及选择适当的材料和技术。
2.印制内层和外层:在HDI制作中,要首先制造内层和外层。
内层通常由铜箔和绝缘基材组成,而外层则由需要进行逐层堆叠的薄板组成。
这些层通过化学蚀刻或电镀等方法来制造。
3.内部追踪和电镀:内层和外层制作完成后,需要进行内部追踪和电镀。
这个步骤将在不同的层之间形成电连接,并提供对内部追踪的支持。
电镀可以通过电化学方法或金属化学还原法进行。
4.盲孔和盖孔:在HDI中,还需要制作盲孔和盖孔。
这些孔用于连接不同层之间的电连接,并提供通孔焊盘的支撑。
通常,盲孔和盖孔可以通过激光钻孔或机械钻孔来制作。
5.堆叠层:HDI的一个关键特点是多层堆叠。
在这一阶段,将内层、外层和孔连接层等组装在一起,并使用压力和温度来使它们紧密结合。
6.盲埋孔、内线和外线:接下来,需要制作盲埋孔、内线和外线。
盲埋孔用于连接不同层之间的电连接,内线用于连接器件和器件之间的电连接,外线用于连接印刷电路板和外部设备。
这些线路可以通过激光钻孔、刮板、电镀或者压铸等方法来制作。
7.表面处理和喷锡:在HDI制作完成后,需要对印刷电路板进行表面处理和喷锡。
表面处理可以增强印刷电路板的抗腐蚀性,并提供更好的焊接性能。
喷锡则是为了方便后续的表面组装。
8.质量检查和测试:最后,需要进行质量检查和测试。
这包括使用X射线检查内部连接和结构,以及使用测试设备检查电路的功能和性能。
总结:HDI制作流程是一个复杂、精细和技术密集的过程。
它需要设计规划、印制内层和外层、内部追踪和电镀、盲孔和盖孔、堆叠层、盲埋孔、内线和外线、表面处理和喷锡,以及质量检查和测试等多个步骤。
- 1、下载文档前请自行甄别文档内容的完整性,平台不提供额外的编辑、内容补充、找答案等附加服务。
- 2、"仅部分预览"的文档,不可在线预览部分如存在完整性等问题,可反馈申请退款(可完整预览的文档不适用该条件!)。
- 3、如文档侵犯您的权益,请联系客服反馈,我们会尽快为您处理(人工客服工作时间:9:00-18:30)。
薄膜高密度互连技术及其应用云振新(国营970厂,四川成都610051)1 引言现代电子装置对小型化、轻量化、高性能化、多功能化、低功耗化和低成本化的要求不断提高且日益迫切。
手机等便携式电子装置是体现这些要求的典型例子。
现代电子装置的需求推动微电子集成技术迅速发展,系统芯片(SoC)、系统级封装(SIP)、多芯片组件(MCM)、高密度互连(HDI)等多种新技术不断涌现。
高密度互连结构可以采用不同的技术来实现。
每一种技术都有其优点和缺点。
但就高互连密度和最佳电气性能而言,一般认为多层薄膜技术是最佳选择。
使用这一技术可使线宽和线距很容易达到20μm、甚至10μm的极小尺寸,而且仅需两层细线布线层就能实现密度非常高的互连结构。
此外,薄膜高密度互连技术还能制造高质量的集成无源元件,包括电阻器、电容器、电感器和各种传输线。
薄膜多层高密度互连结构不仅尺寸小、互连密度高,而且具有优异的高频性能。
薄膜高密度互连技术是一种应用广泛的小型化集成技术,更是实现RF电路和微波电路低成本集成的一种优先解决方案。
2 概述[1]、[2]高密度互连(HDI)基片被定义为比一般PCB具有更高单位面积连线密度的基片。
同普通PCB相比,HDI基片的线宽和线距更加精细(<75 μ m)、通孔小(<150μm)、定位焊盘(Capture Pad)也小(<400μm)、连接焊盘(Connection Pad)密度较大(>20个焊盘·cm-2)。
HDI基片在微电子集成技术中用来缩小尺寸、减轻重量和提高电气性能。
HDI基片在日本称作"积层板"(build-up board),在美国又被称作"序列积层"(SBU,Seauential build-up)板或"微孔"(Microuia)板。
虽然有多种技术都可用来制造HDI基片,按照上述定义,从尺寸缩小角度来看,薄膜技术显然是获得高互连密度的最佳技术。
MCM-D(淀积薄膜型多芯片组件)基片就是一种薄膜高密度互连基片。
这种基片是制造MCM-D最重要的基础,直接决定着MCM-D的尺寸、封装密度和性能。
众所周知,MCM-D是一种十分重要的高密度小型化封装技术。
这从一个侧面充分反映了薄膜高密度互连技术在微电子集成方面的重要意义。
薄膜高密度互连技术是在薄膜制备、光刻等IC工艺技术基础上发展起来的。
其主要特点是相继地沉积用做导体的金属薄膜和作介质隔离层的绝缘膜.薄膜高密度互连基片采用半导体加工的薄膜工艺、设备和方法进行制造,一种广泛使川的工艺是在硅或氧化铝圆片(也可用其他基片)上形成多层结构。
先将聚酰亚胺涂覆在圆片上,逐步升高温度到425℃时固化。
接着,用光刻作为掩膜或使用光刻出图案的金属或旋转涂覆玻璃(SOG)作为掩膜,等离子刻蚀通孔。
然后,将金属(一般为铝或铜)溅射在整个表面上,同时覆盖通孔的壁上。
之后,用光刻工艺刻蚀成所需的导体图案。
通过重复上面的工艺,旋转涂覆另一层聚酰亚胺,固化、刻蚀通孔和进行金属化,直到产生所要求层数的信号层、接地层和电源层为止。
除聚酰亚胺之外,还可采用其他介质作绝缘膜。
图1是一种MCM-D用薄膜多层高密度互连基片的剖面示意图。
3 设计与工艺考虑薄膜高密度互连基片在设计过程中要涉及许多技术参数和材料。
通过对信号线、尺寸、噪声和响应条件进行恰当的选择与设置,可以实现不同的设计要求。
用途不同,设计方案也就不一样。
适合某些应用场合的基片材料、金属化结构和互连技术对其他应用场合就不完全适用。
无论是需要电阻器网络、集成电阻器-电容器网络、多层元件、定制薄膜网络、还是需要特定形状的基片,都必须对不同的方案进行充分的比较、评价然后择优确定。
这对设计工作无疑是十分重要的。
制定薄膜高密度互连基片的设计方案。
通常包含下面几个主要的步骤:①选择基片材料。
②确定导体金属材料。
③根据功率和单元尺寸要求来确定电阻器是设置在基片正面还是底面。
④如果从正面至底面的各层间需要电气连接,则必须考虑是用固体填充通孔还是用金属化通孔来实现这种连接。
⑤根据电容器、空气交叉、耦合器等其他元件的设置情况,设计另外一个布线层连接这些元件,用以完成高密度互连。
3.1 基片基片既是电气互连图案和制造膜电阻器的基底又是装配器件的机械支撑和器件散热的媒质。
它必须满足一系列电气、物理、化学、热学、机械等多方面的性能要求。
基片选择是电路设计中最重要的工作之一。
基片材料多种多样,每种材料都有其独特的性能。
基片选择时考虑的主要因素是终端应用要求。
必须充分了解各种基片材料的特点和性能。
只有这样才能选出最适合终端应用的基片材料。
薄膜高密度互连采用氧化铝陶瓷、氧化铍陶瓷、氮化铝陶瓷、硅、石英等多种材料作基片、氧化铝陶瓷基片广泛用于一般薄膜集成电路和微波中功率集成电路,要求基片的氧化铝含量大于99.6%(重量百分数)和表面光洁度0.025~0.15μm CLA(中心线平均值)。
在质量和等级方面,薄膜用氧化铝基片比厚膜用氧化铝基片要求高得多。
石英基片具有表面光洁、损耗因数低、热膨胀系数很小(仅为0.55×10-6/℃,是氧化铝基片的l/10左右)等特点,可制作很高密度的互连图形,特别适合微波、毫米波、小功率、低并联电容场合使用。
但石英基片的价格较高。
硅、氧化铍、氮化铝等三种基片的导热性能好,它们的热导率比氧化铝基片和石英基片高得多。
硅基片可在中功率、大功率直流场合使用,而且是高密度多层细线布线的最佳基片。
氧化铍是一种集高绝缘电阻和高热导率于一身的基片材料。
其热导率接近金属铝并具有极好的塑料才有的绝缘电阻。
而且,它的热导率值与材料纯度密切相关。
高纯度氧化铍陶瓷的热导率比典型的环氧塑料高l200倍,比大多数玻璃高200倍,优于氧化铝陶瓷6~10倍。
常用氧化铍材料的热导率在25℃时一般为300W(m·k)-1,在l00℃时通常为240W(m·k)-1。
它的主要问题是成本高和制造中的毒性。
氧化铍适合在大功率混合电路和大功率微波电路中做互连基片。
氮化铝的性能与用途同氧化铍类似,具有高热导率(170 W(m·k)-1~200W(m·k)-1)和优良的电气、机械性能,但是不像氧化铍那样有毒性。
氮化铝的另外一个优点是热膨胀系数(4.4×10-6/℃)低,可与硅的热膨胀系数(3×10-6/℃)形成良好的匹配。
由于氮化铝性能上的这些优点,使其作为高功率混合电路、大功率微波电路和高密度多芯片组件的互连基片而受到重视。
3.2 导体基片材料选定之后,电路设计的重要工作是确定导体材料和导体图案。
电流密度和导体阻抗对电路性能有很重要的影响,设计上要认真考虑。
作为互连线的导体带既要能承受要求的电流又要具有很低的电阻(对信号线尤其重要),以保证电路性能的实现。
铝和金是最常用的导体金属材料。
金的导电性能优良,可传导很大的电流。
美国《混合微电路总技术规范》(MIL-H一38534)指出,在导体宽度同为500μm时,金的电流容量比铝大五倍。
金常常用作键合引线材料。
当键合引线长度大于1mm时,金的电流容量虽有较大降低,但仍然相当高。
但是,金线的直径是有限制的,通常在50μm以下,这就限制了可使用的电流容量的范围。
而铝线的直径就没有这种使用上的限制,因此通过增大铝线的直径可得到很高的电流容量。
在导体设计中必须考虑通孔的设置。
通孔用于穿过介质进行金属化层之间的电气连接,是高密度互连基片的重要组成部份之一。
通孔技术是薄膜多层高密度互连技术的关键技术之一。
通孔有多种形状,如叠加式、阶梯式、螺旋式、交错式、埋入式、偏移式、一端封闭式等。
导体图案结构不同,互连通孔的形状也不一样。
除了形状之外,通孔的尺寸及其纵横比、通孔壁的剖面形状等因素,也是通孔设计必须考虑的问题。
3.3 电阻器选择电阻器时,有如下几个重要问题需要考虑:(1)在实际的厚度范围内,具有可控制的、能重复的面电阻率(Ω/口);(2)低的电阻温度系数(TCP);(3)紧密的阻值跟踪;(4)长期的稳定性(在加电或热老化时有低的漂移)。
制造电阻器的常用材料有镍铬、氧化钽和铬硅氧化物金属陶瓷。
镍铬具有很低的电阻温度系数,而面电阻率比氮化钽高,是薄膜高密度互连技术中最常用的一种电阻器材料。
但镍铬电阻器的性能比氮化钽电阻器更易受环境条件变化的影响而不很稳定。
表1对镍铬电阻器和氮化钽电阻器的特性作了比较。
[1]铬硅氧化物金属陶瓷是一氧化硅和铬(SiO-Cr)的复合物。
它具有很高的面电阻率,能在最小的基片面积上制造出高阻值电阻器。
通过改变一氧化硅对铬的配比,可在较宽的范围内调整面电阻率的大小。
这为电阻器提供了设计灵活性。
最实用的面电阻率的范围是1 000 Ω/口~3 000 Ω/口。
这种电阻器的电阻温度系数一般是负的,当氧化物含量增加时,它将变得更负。
对于组份为70%Cr、30%SiO的陶瓷金属电阻,其电阻温度系数为一60×10-6/℃~-40×10-6/℃。
标准电阻器的电阻值为5Ω~2MΩ,绝对公差为5%~0.1%,比公差为1%~0.0l%。
而且,其比公差的大小与电阻值有关。
微波电阻器的电阻值范同较窄,为10 Ω~1 000Ω;其绝对公差和比公差均为0.5%;电阻温度系数小于200×10-6/℃。
无论是设计方法还是可用电阻值的范同,微波电阻器同一般的直流电阻器截然不同,它所考虑的问题更为复杂。
微波电阻器设计源于微波带状线技术。
微波电阻图形通常是一个不带任何切口的简单矩形。
切口会引起反射并将对电压驻波比特性产生不良影响。
当对电阻器的公差要求较严时,通常都在制造上采用调阻的方法来提高生产的合格率。
为了把调阻方法的不利影响减到最小,可以利用中心线来确定边界进行调阻,以保持频率响应特性不变。
当前的检验要求允许去除电阻器的一半。
采用高温稳定工艺可以制造出性能十分稳定的电阻器,其时间稳定性和温度稳定性都很好。
表2列出了主要的基片特性及其参数水平[3]。
3.4 切口、特殊成形和互连层在薄膜高密度互连技术的应用中,有许多场合需要将基片装入器件内的特定空腔中;而另一些场合则要求在基片上开出切口,用来放置与其表面齐平的芯片元件。
要满足这些应用要求,必须对基片进行加工。
CO2切割技术可以在基片上加工出各种形状,从圆片形到复杂的U形结构都可以实现。
U形结构具有多个孔位。
另外,CO2切割技术也可以用来对电镀通孔作钻孔加工、制作填充通孔以及在基片正反两面刻制图形。
加工的参数要求包括:定位公差为75μm,基片边沿与电路之间的距离不得小于50μm,最小内角半径为125μm,基片去除量为25%。
一般来说,应用装置对薄膜高密度互连基片提出的尺寸要求决定了互连层的层数。