18CrNiMo7-6钢齿轮磨削烧伤裂纹分析
CrNiMo钢高速轴裂纹断轴分析及防止措施
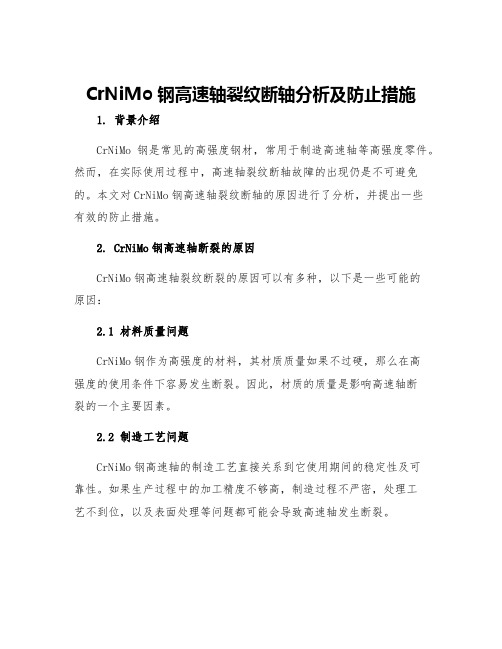
CrNiMo钢高速轴裂纹断轴分析及防止措施1. 背景介绍CrNiMo钢是常见的高强度钢材,常用于制造高速轴等高强度零件。
然而,在实际使用过程中,高速轴裂纹断轴故障的出现仍是不可避免的。
本文对CrNiMo钢高速轴裂纹断轴的原因进行了分析,并提出一些有效的防止措施。
2. CrNiMo钢高速轴断裂的原因CrNiMo钢高速轴裂纹断裂的原因可以有多种,以下是一些可能的原因:2.1 材料质量问题CrNiMo钢作为高强度的材料,其材质质量如果不过硬,那么在高强度的使用条件下容易发生断裂。
因此,材质的质量是影响高速轴断裂的一个主要因素。
2.2 制造工艺问题CrNiMo钢高速轴的制造工艺直接关系到它使用期间的稳定性及可靠性。
如果生产过程中的加工精度不够高,制造过程不严密,处理工艺不到位,以及表面处理等问题都可能会导致高速轴发生断裂。
2.3 设计问题高速轴的设计对于其使用情况也有很大的影响。
如果设计不合理,就会导致高速轴各部分之间的应力不均衡,从而加剧材料的疲劳,并且加速高速轴的磨损和腐蚀,从而导致高速轴断裂。
3. 防止CrNiMo钢高速轴断裂的措施为了防止CrNiMo钢高速轴发生断裂,我们可以采取以下措施:3.1 加强材料质量控制材料质量是关键,对于高速轴而言也是不可或缺的条件。
只有采用质量上乘的材料,才能保障高速轴的耐磨性、耐腐蚀性、强度和硬度的稳定性。
因此,加强材料的质量控制,是防止高速轴断裂的一个必要的环节。
3.2 加强工艺控制加强工艺控制是防止高速轴断裂的另一个重要措施。
在工艺上,要提高工人的专业技能,规范操作,增强工人对于制造过程的掌控能力,同时要加强现有设备的维护和管理工作,防止设备出现故障。
这样能够避免制造过程中发生的功能缺陷,提高产品质量,降低产品瑕疵率。
3.3 加强产品设计制造高速轴,必须要有一个合理的设计。
换言之,制造高速轴之前,首先要进行充分的研发,对高速轴的设计进行科学性的评估。
在设计过程中,需要尽力降低高速轴内部的应力,均衡高速轴各部分的应力及定量的予以计算,实现高速轴各部分负荷的分配、使高速轴质量适宜于其使用。
《18CrNiMo7-6渗碳钢磁场深冷处理工艺及磨损监测技术的研究》范文
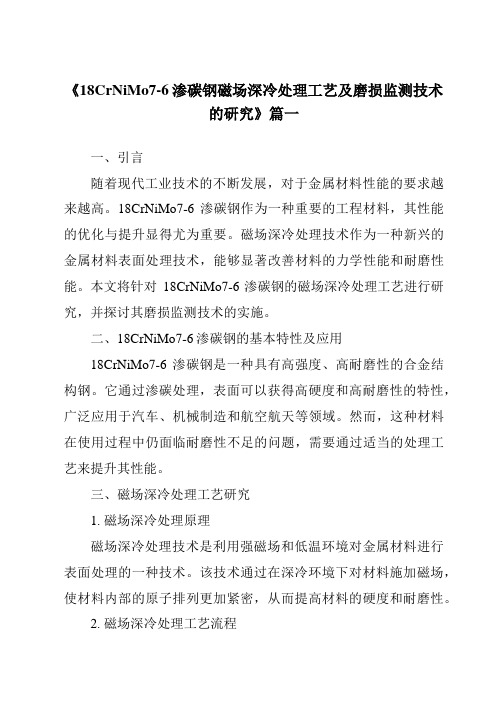
《18CrNiMo7-6渗碳钢磁场深冷处理工艺及磨损监测技术的研究》篇一一、引言随着现代工业技术的不断发展,对于金属材料性能的要求越来越高。
18CrNiMo7-6渗碳钢作为一种重要的工程材料,其性能的优化与提升显得尤为重要。
磁场深冷处理技术作为一种新兴的金属材料表面处理技术,能够显著改善材料的力学性能和耐磨性能。
本文将针对18CrNiMo7-6渗碳钢的磁场深冷处理工艺进行研究,并探讨其磨损监测技术的实施。
二、18CrNiMo7-6渗碳钢的基本特性及应用18CrNiMo7-6渗碳钢是一种具有高强度、高耐磨性的合金结构钢。
它通过渗碳处理,表面可以获得高硬度和高耐磨性的特性,广泛应用于汽车、机械制造和航空航天等领域。
然而,这种材料在使用过程中仍面临耐磨性不足的问题,需要通过适当的处理工艺来提升其性能。
三、磁场深冷处理工艺研究1. 磁场深冷处理原理磁场深冷处理技术是利用强磁场和低温环境对金属材料进行表面处理的一种技术。
该技术通过在深冷环境下对材料施加磁场,使材料内部的原子排列更加紧密,从而提高材料的硬度和耐磨性。
2. 磁场深冷处理工艺流程(1)材料准备:对18CrNiMo7-6渗碳钢进行预处理,包括清洗、打磨等步骤,以保证表面质量。
(2)磁场处理:将预处理后的材料放入磁场深冷设备中,设置适当的磁场强度和深冷温度,进行磁场深冷处理。
(3)热处理:处理完成后,进行适当的热处理,以稳定材料的组织结构。
(4)性能检测:对处理后的材料进行性能检测,包括硬度、耐磨性等指标的测试。
四、磨损监测技术研究磨损监测技术是评估材料耐磨性能的重要手段。
针对18CrNiMo7-6渗碳钢的磁场深冷处理过程,可以采用以下磨损监测技术:1. 显微镜观察法:通过扫描电子显微镜等设备观察材料的磨损表面形态,分析磨损机制。
2. 摩擦系数测试法:通过摩擦试验机测试材料在不同条件下的摩擦系数,评估材料的耐磨性能。
3. 硬度测试法:通过硬度计测试材料的硬度,以评估材料的抗磨损能力。
18crnimo7-6钢的热处理工艺研究

18crnimo7-6钢的热处理工艺研究18CrNiMo7-6钢是一种低碳合金钢,广泛应用于高强度零部件的制造,如轴承、齿轮等。
其性能的优劣直接关系到零部件的使用寿命和安全性。
因此,对18CrNiMo7-6钢的热处理工艺进行深入研究和优化具有重要的意义。
本文将探讨18CrNiMo7-6钢的热处理工艺、性能调控以及可能的优化方向。
一、18CrNiMo7-6钢的基本性质化学成分:18CrNiMo7-6钢主要成分包括铁、碳、铬、镍、硅、锰、钼等。
适度的合金元素含量使其具有较高的强度和韧性。
机械性能:18CrNiMo7-6钢在经过适当热处理后,可以获得高的硬度、强度和韧性,适用于要求高耐磨性和高强度的零部件。
二、18CrNiMo7-6钢的热处理工艺退火处理:18CrNiMo7-6钢的退火处理可通过加热至适当温度,然后进行缓慢冷却。
这有助于消除焊接或加工过程中的残余应力,提高材料的韧性。
正火处理:正火处理可以在850-880摄氏度的温度下进行,然后进行适当速度的冷却。
正火处理可以提高18CrNiMo7-6钢的硬度,但保持一定的韧性。
淬火处理:淬火是提高18CrNiMo7-6钢硬度和强度的有效方式。
通过迅速冷却,可以形成马氏体组织,提高钢的硬度,但也可能导致脆性的增加。
回火处理:淬火后的18CrNiMo7-6钢通常需要进行回火处理,以调整其硬度和韧性的平衡。
回火温度和时间的选择关系到最终的性能。
三、性能调控与优化方向回火工艺优化:通过调整回火工艺的温度和时间,可以实现硬度和韧性的平衡。
适当的回火可以降低淬火带来的脆性。
表面处理:对于一些特殊应用,如耐磨零部件,可考虑表面处理,如渗碳、氮化等,以提高18CrNiMo7-6钢的表面硬度和耐磨性。
热处理工艺监测:引入先进的监测技术,如热处理过程中的温度、冷却速率等实时监测,有助于提高工艺的可控性和一致性。
成分调整:通过微量元素的添加或调整,如微合金化处理,可以对18CrNiMo7-6钢的相变行为进行调控,进而优化性能。
渗碳齿轮齿面磨削裂纹的研究
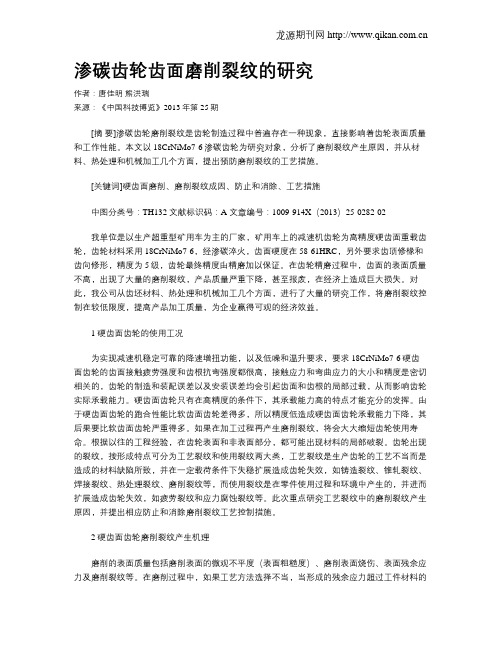
渗碳齿轮齿面磨削裂纹的研究作者:唐佳明熊洪瑞来源:《中国科技博览》2013年第25期[摘要]渗碳齿轮磨削裂纹是齿轮制造过程中普遍存在一种现象,直接影响着齿轮表面质量和工作性能。
本文以18CrNiMo7-6渗碳齿轮为研究对象,分析了磨削裂纹产生原因,并从材料、热处理和机械加工几个方面,提出预防磨削裂纹的工艺措施。
[关键词]硬齿面磨削、磨削裂纹成因、防止和消除、工艺措施中图分类号:TH132 文献标识码:A 文章编号:1009-914X(2013)25-0282-02我单位是以生产超重型矿用车为主的厂家,矿用车上的减速机齿轮为高精度硬齿面重载齿轮,齿轮材料采用18CrNiMo7-6,经渗碳淬火,齿面硬度在58-61HRC,另外要求齿顶修椽和齿向修形,精度为5级,齿轮最终精度由精磨加以保证。
在齿轮精磨过程中,齿面的表面质量不高,出现了大量的磨削裂纹,产品质量严重下降,甚至报废,在经济上造成巨大损失。
对此,我公司从齿坯材料、热处理和机械加工几个方面,进行了大量的研究工作,将磨削裂纹控制在较低限度,提高产品加工质量,为企业赢得可观的经济效益。
1 硬齿面齿轮的使用工况为实现减速机稳定可靠的降速增扭功能,以及低噪和温升要求,要求18CrNiMo7-6硬齿面齿轮的齿面接触疲劳强度和齿根抗弯强度都很高,接触应力和弯曲应力的大小和精度是密切相关的,齿轮的制造和装配误差以及安装误差均会引起齿面和齿根的局部过载,从而影响齿轮实际承载能力。
硬齿面齿轮只有在高精度的条件下,其承载能力高的特点才能充分的发挥。
由于硬齿面齿轮的跑合性能比软齿面齿轮差得多,所以精度低造成硬齿面齿轮承载能力下降,其后果要比软齿面齿轮严重得多。
如果在加工过程再产生磨削裂纹,将会大大缩短齿轮使用寿命。
根据以往的工程经验,在齿轮表面和非表面部分,都可能出现材料的局部破裂。
齿轮出现的裂纹,按形成特点可分为工艺裂纹和使用裂纹两大类,工艺裂纹是生产齿轮的工艺不当而是造成的材料缺陷所致,并在一定载荷条件下失稳扩展造成齿轮失效,如铸造裂纹、锥轧裂纹、焊接裂纹、热处理裂纹、磨削裂纹等,而使用裂纹是在零件使用过程和环境中产生的,并进而扩展造成齿轮失效,如疲劳裂纹和应力腐蚀裂纹等。
地铁齿轮箱齿轮轴齿面点蚀失效探究

a.齿面有麻点的中间齿轮轴b.齿面麻点形态图1 中间齿轮轴与齿面麻点分布形态图2 齿表面磨削后的粗糙度形态和麻点所处部位1.2 硬度测定1/2齿高距齿表面0.1mm处硬度为677HV0.2(相当于59.0HRC),心部硬度为41.5~42.0HRC(齿根圆与轮齿中心线相交处)。
1.3 磨削烧伤检查将齿面清洗和轻微打磨后进行磨削烧伤检查,结果齿面有条状的轻微烧伤(一般是允许存在的)。
在体视显微镜下可看到,剥落麻坑正处于轻微磨削烧伤的条带内(见3)。
麻坑大小不一,但均较浅,麻坑局部有相连外,一般均独立存在(见图4、5)。
1.4 化学成分分析结果如表1所示,符合相关技术要求。
2020年9月(下)/ 总第269期表1 化学成分表元素(%)失效件与标准C Si Mn P S Cr Ni Mo 中间齿轮轴0.190.230.730.0100.004 1.69 1.410.2818CrNiMo7-6钢0.15~0.210.17~0.350.50~0.90≤0.020≤0.0151.50~1.801.40~1.700.25~0.351.5 齿面渗碳淬火硬化层深度测定从有麻坑剥落的齿部取样检查,结果有剥落麻坑的齿面渗碳淬火硬化层深度为CHD550HV0.2=1.15mm,无剥落麻坑的齿面渗碳淬火硬化层深度为CHD550HV0.2= 1.17mm。
从齿部取样磨制抛光后,按GB/T 10561-2005标准检查和A法评定,结果A类夹杂物为0.5级、B类和D类夹杂物均为1级、DS类夹杂物为1.5级。
1.6 显微组织检查(1)直接在齿面轻微抛光浅浸蚀后观察,齿面有呈条带状分布的不规则剥落坑,有的剥落坑的尾端和其周围出现微裂纹形态,如图6所示。
(2)垂直于齿面和剥落坑剖开磨制抛光浸蚀后观察,在剥落坑的周围未见有明显的组织变化,剥落坑深度也较浅,仅为0.01~0.015mm(齿表面在做磨削烧伤检查时经细砂纸轻微打磨,实际剥落坑要比测量的略深一些),如图7~10所示。
齿轮磨齿烧伤的分析与防止

齿轮磨齿烧伤的分析与防止磨齿的烧伤1磨齿烧伤的原因磨削过程中不可避免的会产生大量的磨削热,一部分被冷却液带走,另一部分被传导入加工齿轮的浅表面层内,并快速使齿轮的表层温度升高。
在磨削热大量产生时会在齿面浅层形成回火层,在磨削特别异常时,甚至可达到相变乃至熔化温度,经冷却液激冷形成二次淬火层,因此便形成了磨齿烧伤。
当产生并作用在被磨齿齿面表层内的磨削拉应力超过材料的脆断强度时还会形成磨削裂纹。
2磨齿烧伤的判定磨齿时主要工艺参数对烧伤形成的影响可用4种方法作定性或定量的评价。
•侵蚀检验法按GB/T17879-1999齿轮磨削后表面回火的侵蚀检验,用3% ~ 5% 的硝酸溶液侵蚀后,根据回火区域颜色的变化从轻到重分为A、B、C、D、E 共5个级别,根据回火表面积的最大百分比分为1、2、3 共3个级别。
分别从回火颜色和回火面积的最大百分数对磨齿烧伤的程度进行判定。
•金相法是用金相图分析和测量显微硬度方法确定组织变化层深度,也是在实际生产中常用的方法。
•解析试验法即用系数K= Q/ F来评价。
其中,Q为砂轮在单位时间内磨下的金属数量( 体积金属的单位磨除量),F为砂轮同齿面的接触面积。
用此种方法要完成一定量的金相分析,根据这些资料,建立起系数K与组织变化层深度的关系,从而确定磨齿烧伤的层深。
•解析法根据热波渗透方程式中:h'---- 损伤层深度α----温度传导系数λ----传热系数c----单位热容量Υ----被加工材料的密度Τ----散热时间Tmax ----磨削区内最高接触温度Tper----许用温度( 在深度 h'处不引起马氏体分解)这种评价方法是在某些假设的情况下,对磨齿热过程许多参数分析的基础上进行的,必须完成较大的计算量。
第一种方法主要从表面反应对磨齿烧伤判定,是最简单最便捷的检验方法,也是在生产实践中常用的方法之一。
第二种方法是通过对磨齿烧伤层的金相分析对磨齿烧伤的硬度影响、组织变化等影响因素进行深层次分析。
18CrNiMo7-6风电输出齿轮轴失效分析

细 系 粗 系 细 系 粗 系 细 系 粗 系 细 系 粗 系
O. 5 O. 5 O. 5 O O . 5 O 0- 5 O
应力及残留奥氏体检测 ( 见表3 、表4 ),断裂齿部
齿 面 最大 残 留压应 力 - 1 0 9 5 MP a ,齿根 在 1 0 0 m处
0 2
≤ 1 . 5 ~ 1 . 4~ 0 _ 2 5 ~ 0 . 0 1 2 1 . 8 1 . 7 0 - 3 5
齿 有效 截 面 减 少 ,最 后轮 齿 断 裂 。但 对 于 渗碳 淬 火 最 佳 淬硬 层 深 度 的确 定 ,至 今 也 没 有一 个 权 威 的理 论 和 方法 被 大 家 所完 全接 受 。这 些理 论 和 方 法 一直 都 有 争 议 ,0 . 8 l mm深 度 可 能 仅 是 齿 轮 轴 断齿 的非 直 接 性 因素 ,但 其 为 断 裂 事 故 提 供 了潜 在 失 效 基
1 7 . 4 1 0 m左右 ,无 可 见碳 化物 ,残 留奥 氏体 测 点 2
1 . 9 2 _ 3
表3 X 射 线衍射法残 留应力结果 ( MP a )
2 5 0 3 0 H 0
2 . 渗碳淬 火组织检测
截取 断裂齿部 ,经 磨制后 ,在金相
显 微 镜 下 进 行 微 观 组 织 观 察 ,齿 根 脱碳 层1 6 m,内 氧 化I GO 为1 0 m,脱 碳 层 及I GO符 合 技 术 要 求 ,不 存 在 齿 根 表 面 因 脱 碳 而 产 生 拉 应 力 引起 疲 劳 断 裂 的 可 能 。断 口区域 齿 面 显 微 组织 见 图4 ,心 部
表4 X 射 线衍射法残 留奥 氏体结果 ( 体积分数 )
部 位 齿 面 齿 根 表 面
某钢厂风电齿轮钢18CrNiMo7-6产品研发

122管理及其他M anagement and other某钢厂风电齿轮钢18CrNiMo7-6产品研发叶明在,徐瑞军,赵 鹏(湖南华菱湘潭钢铁有限公司,湖南湘潭 411101)摘 要:18CrNiMo7-6钢中Cr、Ni 元素含量高,容易产生氢质裂纹(白点缺陷)和应力裂纹。
工艺设计合理的化学成分,合适的精炼脱氧、脱气工艺和连铸工艺。
冶炼工序降低钢水中[H]含量,提高铸坯缓冷温度;轧钢工序预热段缓慢加热、均热段充分高温扩散,提高圆钢入坑缓冷温度,通过上述措施充分释放钢中[H]含量,消除白点缺陷和应力裂纹。
使最终圆钢产品成分均匀,圆周碳偏析小,非金属夹杂物和全氧含量低,力学性能优良,末端淬透性稳定,且完全满足用户使用需求。
关键词:18CrNiMo7-6;工艺设计;缓冷;高温扩散中图分类号:TF76 文献标识码:A 文章编号:11-5004(2020)21-0122-3收稿日期:2020-11作者简介:叶明在,男,生于1985年,工程师,本科,研究方向:炼钢品种开发与质量管理。
欧盟标准《EN10084:2008-渗碳齿轮钢技术条件》中的18CrNiMo7-6直条圆钢,主要用于生产风电减速机齿轮,不仅要求钢种化学成分稳定、钢水纯净度高,同时要求圆钢末端淬透性波动小,力学性能优良,金相组织均匀。
某钢厂在成功开发20CrMnTiH 齿轮钢的基础上,进行了更高档次风电渗碳齿轮钢18CrNiMo7-6的研发。
1 工艺流程高炉铁水→转炉冶炼→LF 精炼→真空脱气→连铸(150mm 方/280mm 方/350*430mm 方)→铸坯缓冷+热轧+圆钢缓冷+修磨→检验入库。
2 化学成分设计18CrNiMo7-6末端淬透性带宽按EN10084:2008欧标中18CrNiMo7-6H 交货,按18CrNiMo7-6HH 窄带目标设计,带宽只有7个(J9:40~47、J15:38~46),该钢厂没有开发过含碳量在0.20%左右CrNiMo 系列合金钢,无历史数据可以借鉴,成分设计技术难度较大。
成形砂轮修整对18CrNiMo7-6_钢磨削表面完整性的影响

成形砂轮修整对18CrNiMo7-6钢磨削表面完整性的影响*郜 伟1, 李梦琪1, 殷会鹏2, 张银霞1, 刘治华1(1. 郑州大学 机械与动力工程学院, 郑州 450001)(2. 郑州大学 河南省资源与材料工业技术研究院, 郑州 450001)摘要 为了探究修整切深a d 、轴向进给速度f d 和修整速比q d 等修整工艺参数对18CrNiMo7-6齿轮钢磨削表面完整性的影响,分别采用树脂结合剂金刚石碟轮、青铜结合剂金刚石碟轮和单颗粒金刚石笔3种修整工具对陶瓷结合剂铬刚玉砂轮进行成形修整工艺正交试验,并用修整后的铬刚玉砂轮对18CrNiMo7-6齿轮钢进行横磨试验。
结果表明:随着各修整工艺参数的增大,齿轮钢磨削加工表面粗糙度R a 增大,磨削表面更容易产生残余压应力;通过归一化无量纲方法综合评价3种修整工具的磨削表面完整性,表明采用青铜结合剂金刚石碟轮修整时的磨削表面完整性优于其余2种修整工具的,且当a d =4 μm ,f d =100 mm/min ,q d =0.3时齿轮钢,磨削表面的完整性较优。
关键词 成形砂轮修整;金刚石碟轮;表面完整性;18CrNiMo7-6齿轮钢;正交试验中图分类号 TG74;TG580.1 + 3 文献标志码 A 文章编号 1006-852X(2023)05-0632-08DOI 码 10.13394/ki.jgszz.2022.0170收稿日期 2022-10-11 修回日期 2022-11-09数控成形磨削加工具有数字化、高柔性化、高精度加工、高效率等特点,是提高工件形面精度和表面质量的合理、有效的加工方式[1]。
成形砂轮修整是成形磨削的关键技术之一,与一般砂轮的修整不同,其不仅要保证修去砂轮工作表面已磨损的部分,以恢复砂轮的磨削性能,还需要保证砂轮外圆被修整成与复杂工件轮廓相吻合的形状,从而实现复杂轮廓的磨削。
因此,研究成形砂轮修整是精密、超精密加工技术的重中之重[2]。
渗碳齿轮钢18CrNiMo7-6低倍夹杂缺陷的分析研究
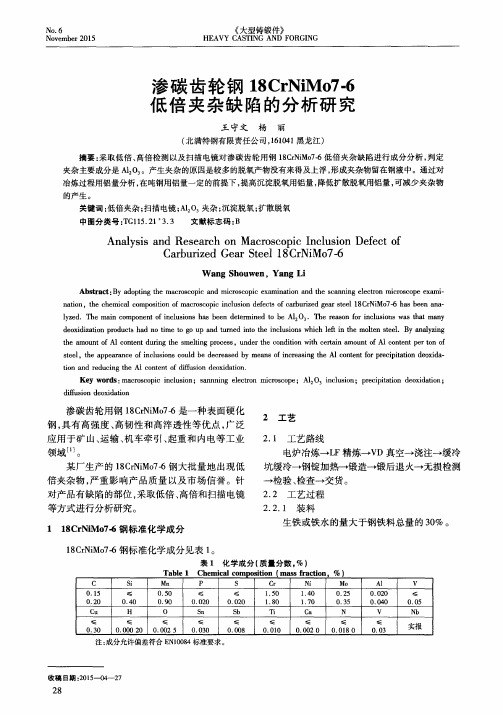
摘要 : 采取低倍 、 高倍检 测以及扫描 电镜对渗碳齿轮用 钢 1 8 C r N i Mo 7 - 6低倍 夹杂缺 陷进行 成分分析 , 判定 夹杂主要成分是 A 1 : O , 。产生夹杂 的原 因是较多的脱氧产物没有来得及上浮 , 形成夹杂物 留在钢液中。通过对 冶炼 过程用铝量分析 , 在吨钢用铝量 一定 的前 提下 , 提高沉淀脱氧用铝量 , 降低扩散脱氧用铝量 , 可减 少夹杂物
d e o x i d i z a t i o n p r o d u c t s h a d n o t i me t o g o u p a n d t u r n e d i n t o t h e i n c l u s i o n s w h i c h l e f t i n t h e mo l t e n s t e e 1 .B y a n ly a z i n g t h e a mo u n t o f A 1 c o n t e n t d u i r n g t h e s me h i n g p r o c e s s ,u n d e r t h e c o n d i t i o n wi t h c e r t a i n m o u n t o f A1 c o n t e n t p e r t o n o f
No . 6 No v e mb e r 2 0 1 5
《 大型铸锻 件》
HEA VY CA S TI N G AND F O RGI NG
渗碳齿轮钢 1 8 C r N i Mo 7 ・ 6 低 倍 夹 杂 缺 陷 的 分 析 研 究
王 守文 杨 丽
( 北满特钢有限责任公 司, 1 6 1 0 4 1黑龙 江)
C a r b u r i z e d Ge a r S t e e l 1 8 C r N i M0 7 _ 《 5
18CrNiMo7–6钢高速外圆磨削残余应力和硬度的试验分析

2021年2月第1期第41卷总第241期金刚石与磨料磨具工程D i a m o n d&A b r a s i v e sE n g i n e e r i n gF e b.2021N o.1 V o l.41 S e r i a l24118C r N i M o7-6钢高速外圆磨削残余应力和硬度的试验分析*张银霞,原少帅,王子乐,杨鑫,郜伟(郑州大学机械与动力工程学院/抗疲劳制造技术河南省工程实验室,郑州450001)摘要针对18C r N i M o7-6渗碳钢工件,以砂轮线速度v s㊁工件转速n w㊁砂轮径向进给速度v f r和砂轮C B N 磨料粒度为变量设计单因素试验,分别采用X射线残余应力分析仪和显微硬度计对工件的表面残余应力和硬度进行检测㊂结果表明:高速外圆磨削可为18C r N i M o7-6渗碳钢工件的表面引入残余压应力,X方向的压应力小于Y方向的压应力,同时高速外圆磨削可以提高工件表面的硬度;随着v s的增大,残余压应力先增大后趋于平稳,硬度先减小后增大且在v s为75m/s时最小;随着n w的增大,工件表面残余压应力和硬度的变化不具单调性;v f r对工件表面残余压应力和硬度的影响较大,线性拟合后残余压应力和硬度整体上均呈减小趋势;不同C B N磨料粒度砂轮磨削在工件表面产生残余压应力和硬度的大小依次为M10/20最大, 120/140次之,230/270最小;18C r N i M o7-6钢表面存在拉应力时硬度较低,表面存在压应力时硬度较高㊂关键词高速外圆磨削;砂轮线速度;砂轮C B N磨料粒度;残余应力;硬度中图分类号 T G58文献标识码A 文章编号1006-852X(2021)01-0065-06D O I码10.13394/j.c n k i.j g s z z.2021.1.0011E x p e r i m e n t a l a n a l y s i s o f r e s i d u a l s t r e s s a n d h a r d n e s s o f18C r N i M o7-6s t e e li n h i g h s p e e d c y l i n d r i c a l g r i n d i n gZ H A N G Y i n x i a Y U A N S h a o s h u a i W A N G Z i l e Y A N G X i n G A O W e i S c h o o l o f M e c h a n i c a l E n g i n e e r i n g H e n a n K e y E n g i n e e r i n g L a b o r a t o r y o f A n t i-f a t i g u eM a n u f a c t u r i n g T e c h n o l o g y Z h e n g z h o u U n i v e r s i t y Z h e n g z h o u450001C h i n aA b s t r a c t F o r18C r N i M o7-6c a r b u r i z e d s t e e l w o r k p i e c e a s i n g l e f a c t o r t e s t w a s d e s i g n e d s t u d y i n g t h e w h e e l s p e e d t h e w o r k p i e c e s p e e d t h e f e e d r a t e a n d t h e a b r a s i v e s i z e X-r a y r e s i d u a l s t r e s s a n a l y z e r a n d m i c r o h a r d n e s s t e s t e r a r e u s e d t o d e t e c t t h e r e s i d u a l s t r e s s a n d h a r d n e s s T h e r e s u l t s s h o w t h a t h i g h-s p e e d c y l i n d r i c a l g r i n d i n g c a n i n t r o d u c e r e s i d u a l c o m p r e s s i v e s t r e s s t o t h e s u r f a c e o f t h e w o r k p i e c e a n d t h a t t h e c o m p r e s s i v e s t r e s s i n t h e X d i r e c t i o n i s l e s s t h a n t h a t i n t h e Y d i r e c t i o n M e a n w h i l e h i g h-s p e e d c y l i n d r i c a l g r i n d i n g c a n i m p r o v e t h e s u r f a c e h a r d n e s s o f t h e w o r k p i e c e W i t h t h e i n c r e a s e o f w h e e l s p e e d t h e c o m p r e s s i v e s t r e s s i n c r e a s e s f i r s t a n d t h e n t e n d s t o b e s t a b l e w h i l e t h e h a r d n e s s d e c r e a s e s f i r s t a n d t h e n i n c r e a s e s a n d t h e m i n i m u m v a l u e i s o b t a i n e d w h e n t h e s p e e d i s75m s W i t h t h e i n c r e a s e o f w o r k p i e c e s p e e d t h e c h a n g e o f r e s i d u a l c o m p r e s s i v e s t r e s s a n d h a r d n e s s i s n o t m o n o t o n i c T h e f e e d r a t e h a s a g r e a t i n f l u e n c e o n t h e c o m p r e s s i v e s t r e s s a n d h a r d n e s s o f t h e w o r k p i e c e s u r f a c e w h i c h a r e r e d u c e d i n g e n e r a l a f t e r l i n e a r f i t t i n g G r i n d i n g w h e e l s w i t h d i f f e r e n t CB N a b r a s i v e g r a i n s i z e s p r o d u c e d i f f e r e n t c o m p r e s s i v e s t r e s s a n d h a r d n e s s o n t h e s u r f a c e o f t h e w o r k p i e c e n a m e l y M1020p r o d u c e s t h e l a r g e s t f o l l o w e d b y120140a n d t h e n230270 t h e s m a l l e s t O n t h e s u r f a c e o f t h e w o r k p i e c e t h e h a r d n e s s i s l o w w h e n t h e r e i s t e n s i l e s t r e s s a n d t h e h a r d n e s s i s h i g h w h e n t h e r e i s c o m p r e s s i v e s t r e s sK e y w o r d s h i g h s p e e d c y l i n d r i c a l g r i n d i n g l i n e a r s p e e d o f g r i n d i n g w h e e l C B N a b r a s i v e s i z e o f g r i n d i n g w h e e l r e s i d u a l s t r e s s h a r d n e s s*基金项目:国家自然科学基金重点项目(U1804254);国家留学基金委项目(201907045070);河南省自然科学基金(162300410244)㊂Copyright©博看网 . All Rights Reserved.金刚石与磨料磨具工程总第241期高速/超高速磨削具有高的材料磨除率,能够实现低能耗加工和难磨除材料的高效率低损伤磨削[1]㊂超高速磨削可以提高生产效率,提高零件质量[2]㊂高速/超高速磨削加工能够保证产品零件的高精度和高表面质量,已经成为现代磨削的重要发展趋势[3]㊂表面完整性不仅包含表面形貌特征,也包含表面物理化学变化特征[4]㊂磨削表面完整性包括:表面粗糙度㊁波度㊁硬度㊁残余应力㊁组织相变等,各因素之间有一定的关系[5]㊂残余应力和硬度作为表面完整性的2个重要指标,得到了国内外学者的广泛关注㊂王栋等[6]进行了高速平面磨削试验,揭示了磨削参数对18C r N i M o7-6钢表面硬度的变化规律㊂张银霞等[7]探究了研磨工艺对18C r N i M o7-6钢残余应力的影响㊂Z H O U等[8]通过正交试验,研究了工艺参数对G C r15合金钢表面完整性的影响㊂N I等[9]进行了高速外圆磨削试验,砂轮线速度最高为80m/s,探究了磨削参数对S i C材料残余应力的影响㊂黄惠茹等[10]采用剥层法,探索了45钢的工件硬度和残余应力,指出残余应力和硬度存在一定的幂函数关系㊂孙渊等[11]分析了残余应力对工件硬度的影响,指出残余应力不同对硬度的影响不同㊂18C r N i M o7-6为欧洲标准的一种优质表面渗碳钢,该钢表面硬度高㊁耐磨性好,由于其优越的力学性能,该材料被用于锻造大型部件(如直升机轴)等诸多领域[12–13]㊂目前,关于18C r N i M o7-6钢高速外圆磨削的研究较少,本试验通过单因素试验探究了砂轮线速度㊁工件转速㊁砂轮径向进给速度及砂轮C B N磨料粒度对18C r N i M o7-6钢表面残余应力和硬度的影响,砂轮线速度最高达到120 m/s,建立残余应力和硬度的定性关系㊂1试验样件与方法1.1试验样件试验样件为18C r N i M o7-6合金钢,该样件经920ħ渗碳㊁830ħ淬火并回火,热处理后的化学成分含量见表1所示,热处理的样件在普通磨床磨削加工后尺寸为ϕ35mmˑ80mm㊂1.2试验设备及方案磨削试验首先在MK1320型普通外圆磨床上进行,以去除工件表面渗碳处理形成的黑色氧化皮,然后通过C N C8325型超高速凸轮轴复合磨床进行高速外圆磨削试验㊂高速外圆磨削所用的砂轮由郑州磨料磨具磨削研究所有限公司生产提供,为陶瓷结合剂C B N 砂轮(V-C B N),砂轮相关参数见表2所示;修整轮选用烧结金刚石滚轮(规格参数代号为S-14A1-125ˑ12ˑ28ˑ2.2ˑ8)㊂表118C r N i M o7-6材料化学成分含量T a b.118C r N i M o7-6m a t e r i a l c h e m i c a l c o m p o s i t i o n c o n t e n t 元素名称质量分数w/%C0.15~0.21S i0.15~0.40M n0.60~0.90S<0.012P<0.020C r1.50~1.80N i1.40~1.70M o0.25~0.35F e<96.00表2砂轮相关参数T a b.2G r i n d i n g w h e e l r e l a t e d p a r a m e t e r s参数名称规格或数值砂轮类型V-C B N形状尺寸代号14A1500ˑ30ˑ127ˑ5ˑ20 C B N粒度120/140,230/270,M10/20 C B N浓度175%砂轮最高转速ɤ125m/s残余应力检测设备为加拿大P r o t o公司的大功率X射线衍射残余应力分析仪,硬度检测设备为H V-1000型显微硬度计,设备如图1所示㊂(a)X射线衍射残余应力分析仪X-r a y d i f f r a c t i o n r e s i d u a l s t r e s s a n a l y z e r(b)H V-1000型显微硬度计H V-1000m i c r o h a r d n e s s t e s t e r图1残余应力分析仪和显微硬度计F i g.1R e s i d u a l s t r e s s a n a l y z e r a n d m i c r o h a r d n e s s t e s t e r高速外圆磨削圆柱工件的结构如图2所示,残余应力检测[14]包括X方向和Y方向,即圆柱工件的周向和轴向;硬度检测[15]沿圆柱工件的周向㊂残余应力分析仪选用的靶材为C r-Kα,衍射晶面{211},光斑直径为1 m m;硬度检测类型为洛氏硬度H R C,加载力为1N,保66Copyright©博看网 . All Rights Reserved.第1期张银霞,等:18C r N i M o7-6钢高速外圆磨削残余应力和硬度的试验分析载时间15s㊂高速外圆磨削试验方案见表3所示㊂图2工件结构及X㊁Y方向示意F i g.2W o r k p i e c e s t r u c t u r e a n d X,Y d i r e c t i o n s表3高速外圆磨削试验方案T a b.3T e s t s c h e m e f o r h i g h s p e e d c y l i n d r i c a l g r i n d i n g参数名称规格或数值砂轮线速度v s/(m/s)60,75,90,105,120工件转速n w/(r/m i n)30,45,60,75,90砂轮径向进给速度v w/(mm/m i n)0.2,0.3,0.4,0.5,0.6砂轮C B N磨料粒度120/140,230/270,M10/20磨削深度a p/mm0.5磨削液水基21-2型磨削方式单程切入式逆磨2试验结果与讨论2.1砂轮线速度对残余应力和硬度的影响砂轮线速度对残余应力的影响如图3所示㊂由图3可知:随着砂轮线速度v s的增大,工件表面X㊁Y方向的残余压应力绝对值均先增大后趋于平稳,且X方向残余压应力绝对值小于Y方向的(图3中,负值表示残余压应力,正值表示残余拉应力)㊂这是因为随着v s的增大,单位时间内参与磨削的磨粒数目增加,磨粒与工件的摩擦㊁挤压作用增大,磨削温度升高,但高速磨削使工件表面热能传导到下一层之前就被磨屑带走,所以热应力的影响较小,此时机械应力影响较大,残余压应力增大㊂砂轮线速度对硬度的影响如图4所示㊂由图4可知:随着v s的增大,工件表面硬度先减小后增大,硬度值在v s为75m/s时最小㊂这是因为,工件硬度的高低是磨削产生的加工硬化和温度对材料的软化综合作用的结果㊂根据图4曲线,当v s处于60~75m/s时,磨削温度升高,工件表面材料软化,硬度值有所降低㊂当v s处于90~120m/s时,高速磨削突破了临界速度,磨削温度降低,材料软化程度下降,同时v s的增大使工件表面加工硬化效果更加突出,故硬度增大㊂图3砂轮线速度对残余应力的影响F i g.3E f f e c t o f w h e e l s p e e d o n r e s i d u a l s t r e ss图4砂轮线速度对硬度的影响F i g.4E f f e c t o f w h e e l s p e e d o n h a r d n e s s2.2工件转速对残余应力和硬度的影响工件转速对残余应力的影响如图5所示㊂由图5可知:随着工件转速n w的增大,X㊁Y方向的表面残余压应力绝对值均先增大后出现波动㊂这是因为n w的增大导致v s与n w的磨削速比q减小,磨屑形状加大,磨削加剧,磨削温度升高,残余压应力绝对值在机械应力和热应力的综合影响下逐渐增大;随着n w的持续增大,材料去除率及磨屑脱落速度增大,磨屑带走了大量热能,此时热应力的影响减小,残余压应力出现波动㊂图5工件转速对残余应力的影响F i g.5E f f e c t o f w o r k p i e c e s p e e d o n r e s i d u a l s t r e s s76Copyright©博看网 . All Rights Reserved.金刚石与磨料磨具工程总第241期工件转速对硬度的影响如图6所示㊂由图6可知:随着工件转速n w 的增大,工件表面硬度先略微增大,随后减小又增大㊂这是因为当工件转速n w 处于30~75r /m i n 时,工件与砂轮的磨削加剧,致使磨削温度升高,材料发生软化,故硬度整体上呈减小趋势,随着n w 的持续增大,磨屑脱落速度加快使一部分热能散出,磨削温度下降,材料软化程度下降,故硬度略有提高㊂图6 工件转速对硬度的影响F i g .6E f f e c t o f w o r k p i e c e s pe e d o n h a r d n e s s 2.3 砂轮径向进给速度对残余应力和硬度的影响砂轮径向进给速度对残余应力的影响如图7所示㊂由图7可知:随着砂轮径向进给速度v f r 的增大,X ㊁Y 方向的表面残余压应力绝对值整体上均有减小的趋势;当v f r 为0.6mm /m i n 时,X 方向的残余压应力最小值为-98.89M P a ;当v f r 为0.5mm /m i n 时,Y 方向的残余压应力最小值为-198.18M P a㊂这是因为v f r 增大,使得砂轮的径向磨损增大,磨削温度升高,磨削热造成的热塑性变形加大,此时热应力的影响较大,残余压应力整体上逐渐减小㊂图7 砂轮径向进给速度对残余应力的影响F i g.7E f f e c t o f w h e e l f e e d r a t e o n r e s i d u a l s t r e s s 砂轮径向进给速度对硬度的影响如图8所示㊂由图8可知:随着砂轮径向进给速度v f r 的增大,工件表面的硬度整体上呈减小趋势,硬度值在拟合线附近上下波动,v f r 为0.6mm /m i n 时,硬度取得最小值为52.30H R C ㊂这是因为v f r 增大使相同时间内参加磨削的磨粒数增加,磨削温度升高,温度对材料软化的影响程度增大,硬度整体上逐渐减小㊂图8 砂轮径向进给速度对硬度的影响F i g.8E f f e c t o f w h e e l f e e d r a t e o n h a r d n e s s 2.4 砂轮C B N 磨料粒度对残余应力和硬度的影响砂轮C B N 磨料粒度对残余应力的影响如图9所示㊂由图9可知:不同C B N 磨料粒度砂轮高速磨削后工件表面残余应力绝对值的大小依次为M 10/20的最大,120/140的次之,230/270的最小,X ㊁Y 方向趋势一致,且均为残余压应力㊂究其原因,M 10/20磨粒尺寸较小,拥有较强自锐性以满足新磨粒的出露,同时,较小的磨粒与工件磨削引起的塑性变形小,产生的磨削热较少,磨削热引起的拉应力被抑制,故工件表面的残余压应力较大;120/140的砂轮磨粒较大,磨削过程中单颗磨粒的切削力较大,产生的磨削温度较高,磨削热造成的热塑性变形较大,残余压应力在热应力的影响下较小;230/270的磨粒尺寸介于前两者之间,但砂轮内部气孔尺寸较120/140砂轮的小,砂轮自锐性又不如M 10/20,因此散热较差,磨削产生的温度最高,热应力的影响最大,工件表面残余压应力绝对值最小㊂砂轮粒度对硬度的影响如图10所示㊂由图10可知:不同粒度砂轮高速磨削后工件表面硬度的大小依次为M 10/20的最大,120/140的次之,230/270的最小㊂由以上分析,230/270的砂轮磨削时产生的磨削温度最大,材料受温度软化的程度最高,故硬度最小;120/140的砂轮磨粒尺寸大,但其较大的气孔尺寸使一部分磨削热有效散出,材料软化程度较低,其磨削后工件表面硬度较大;M 10/20砂轮自锐性较强,磨粒尺寸最小,引起的塑性变形及磨削温度较前两者最小,材料软化程度最低,故其磨削后工件表面硬度最大㊂86Copyright©博看网 . All Rights Reserved.第1期张银霞,等:18C r N i M o 7-6钢高速外圆磨削残余应力和硬度的试验分析图9 砂轮C B N 磨料粒度对残余应力的影响F i g .9E f f e c t o f C B N a b r a s i v e s i z e o f g r i n d i n gw h e e l o n r e s i d u a l s t r e ss图10 砂轮C B N 磨料粒度对硬度的影响F i g .10E f f e c t o f C B N a b r a s i v e s i z e o f g r i n d i n gw h e e l o n h a r d n e s s2.5 残余应力和硬度的相关性热处理后的工件通过普通外圆磨床加工,得到ϕ35m mˑ80m m 的原始工件,选择5组原始工件,分别测得其表面残余应力和硬度值,如图11所示㊂从图11可以看出:5组原始工件表面X ㊁Y 方向的残余应力均为残余拉应力,工件表面的硬度值区间为45.8~53.1H R C ㊂图11 原始工件表面残余应力与硬度曲线F i g .11R e s i d u a l s t r e s s a n d h a r d n e s s c u r v e o f o r i g i n a l w o r k pi e c e 高速外圆磨削不同工艺参数对工件表面周向残余应力和硬度的影响如图12所示(实线对应残余应力,虚线对应硬度),横轴分别对应表3中单因素变量的各个水平㊂从图12可以看出:高速外圆磨削可为工件表面引入残余压应力,工件表面的硬度区间为52.30~58.75H R C ,残余压应力大的位置对应的硬度也较大,反之亦同㊂通过对比图11㊁图12可以看出:对于18C r N i M o 7-6渗碳钢,其高速外圆磨削前后工件表面的残余应力和硬度有如下关系:工件表面存在拉应力时硬度值较低,工件表面存在压应力时硬度值较高㊂图12 工艺参数对残余应力和硬度的影响F i g.12E f f e c t o f p a r a m e t e r s o n r e s i d u a l s t r e s s a n d h a r d n e s s 3 结论(1)对于18C r N i M o 7-6渗碳钢,高速外圆磨削可为工件表面引入残余压应力,X 方向的残余压应力绝对值小于Y 方向的值;同时,高速外圆磨削可以提高工件表面的硬度㊂(2)随着砂轮线速度v s 的增大,工件表面残余压应力绝对值先增大后趋于平稳,工件表面硬度先减小后逐渐增大;工件转速n w 对工件表面残余压应力和硬度的影响不具单调性;工件表面残余压应力绝对值和硬度随着砂轮径向进给速度v f r 的增大整体上均呈减小趋势;不同磨料粒度砂轮磨削在工件表面产生残余压应力绝对值和硬度的大小依次为M 10/20的最大,120/140的次之,230/270的最小㊂(3)18C r N i M o 7-6渗碳钢高速外圆磨削时的残余应力和硬度有如下关系:表面存在拉应力时硬度值较低,表面存在压应力时硬度值较高㊂高速外圆磨削工艺使工件表面的应力由拉应力变为压应力,表面硬度值提高了11%~14%,这对于提高零件的疲劳强度,延长疲劳寿命有着较为重要的意义㊂96Copyright©博看网 . All Rights Reserved.金刚石与磨料磨具工程总第241期参考文献:1盛晓敏谢桂芝尚振涛高速超高速磨削工艺M北京科学出版社2015S H E N G X i a o m i n X I E G u i z h i S HA N G Z h e n t a o H i g h s p e e d u l-t r a h i g h s p e e d g r i n d i n g p r o c e s s M B e i j i n g S c i e n c e P r e s s20152 Y A N G L F U Y C X U J H e t a l U l t r a-h i g h-s p e e d g r i n d i n gT h e o r e t i c a l b a s i s a n d d e v e l o p m e n t o f a g r i n d i n g m a c h i n e t o o l JK e y E n g i n e e r i n g M a t e r i a l s2013589-590293-2983李伯民赵波李清磨料㊁磨具与磨削技术M北京化学工业出版社2016L I B o m i n Z HA O B o L I Q i n g A b r a s i v e a b r a s i v e t o o l s a n dg r i n d i n g t e c h n o l o g y M B e i j i n g C h e m i c a l I n d u s t r yP r e s s20164何柏林邓海鹏表面完整性研究现状及发展趋势J表面技术2015449140–146152H E B o l i n D E N G H a i p e n g R e s e a r c h s t a t u s a n d d e v e l o p m e n tt r e n d o f s u r f a c e i n t e g r i t y J S u r f a c e T e c h n o l o g y2015449140-1461525李伯民赵波现代磨削技术M北京机械工业出版社2003L I B o m i n Z H A O B o M o d e r n g r i n d i n g t e c h n o l o g y M B e i-j i n g M a c h i n e r y I n d u s t r y P r e s s20036王栋刘昱范陈鑫18C r N i M o7-6高速磨削条件下表面质量的试验研究J郑州大学学报工学版201738378–8186WA N G D o n g L I U Y u f a n C H E N X i n E x p e r i m e n t a l r e s e a r c h o n s u r f a c e q u a l i t y o f18C r N i M o7-6u n d e r h i g h s p e e d g r i n d i n g JJ o u r n a l o f Z h e n g z h o u U n i v e r s i t y E n g i n e e r i n g E d i t i o n201738 378-81867张银霞王文广郜伟等研磨工艺对18C r N i M o7-6钢表面粗糙度和残余应力的影响J表面技术2020491343–348Z H A N G Y i n x i a W A N G W e n g u a n g G A O W e i e t a l E f f e c t o fg r i n d i n g p r o c e s s o n s u r f a c e r o u g h n e s s a n d r e s i d u a l s t r e s s o f18C r N i M o7-6s t e e l J S u r f a c e T e c h n o l o g y2020491343-348 8 Z H O U C Q I A N J X I N G Y e t a l O p t i m i z a t i o n o f t h e g r i n d i n gp r o c e s s t o i m p r o v e t h e s u r f a c e i n t e g r i t y o f b e a r i n g r a c e w a y s JT h e I n t e r n a t i o n a l J o u r n a l o f A d v a n c e d M a n u f a c t u r i n g T e c h n o l o-g y2017919-124243-42529 N I J M L I B Z P A N G J Z H i g h-s p e e d c y l i n d r i c a l g r i n d i n g o fS i C t h e p r o c e s s c h a r a c t e r i s t i c s a n d s u r f a c e i n t e g r i t y J C e r a m i cE n g i n e e r i n g a n d S c i e n c e P r o c e e d i n g s201314170-7610黄惠茹李晓阳张琳琳等淬火低碳钢硬度㊁残余应力和微观组织间的关系J科学技术与工程20171734191–196HU A N G H u i r u L I X i a o y a n g Z H A N G L i n l i n e t a l T h e r e l a-t i o n s h i p b e t w e e n h a r d n e s s r e s i d u a l s t r e s s a n d m i c r o s t r u c t u r e o f q u e n c h e d m i l d s t e e l J S c i e n c e T e c h n o l o g y a n d E n g i n e e r i n g20171734191-19611孙渊张栋午丽娟等材料残余应力对硬度测试影响程度的分析J华东理工大学学报自然科学版2012385652–656S U N Y u a n Z H A N G D o n g WU L i j u a n e t a l A n a l y s i s o f t h ei n f l u e n c e d e g r e e o f m a t e r i a l r e s i d u a l s t r e s s o n h a r d n e s s t e s t JJ o u r n a l o f E a s t C h i n a U n i v e r s i t y o f S c i e n c e a n d T e c h n o l o g y N a t-u r a l S c i e n c e E d i t i o n2012385652-65612 S P R I N G E R P P R A H L U C h a r a c t e r i s a t i o n o f m e c h a n i c a l b e-h a v i o r o f18C r N i M o7-6s t e e l w i t h a n d w i t h o u t N b u n d e r w a r mf o rg i n g c o n d i t i o n s th r o u g h p r o c e s si n g m a p s a n a l y s i s J J o u r n a lo f M a t e r i a l s P r o c e s s i n g T e c h n o l o g y2016237216-23413张银霞陈欢郜伟等18C r N i M o7-6钢渗碳淬火过程的数值研究J热加工工艺20174618238–241Z H A N G Y i n x i a C H E N H u a n G A O W e i e t a l N u m e r i c a l s t u d y o n c a r b u r i z i n g a n d q u e n c h i n g p r o c e s s o f18C r N i M o7-6s t e e lJ H o t P r o c e s s i n g T e c h n o l o g y20174618238-24114王海斗朱丽娜邢志国表面残余应力检测技术M北京机械工业出版社2013W A N G H a i d o u Z H U L i n a X I N G Z h i g u o S u r f a c e r e s i d u a l s t r e s sd e t e c t i o n t e c h n o l o g y M B e i j i n g M a c h i n e r y I n d u s t r y P r e s s2013 15任敬心华定安磨削原理M北京电子工业出版社2011 R E N J i n g x i n H U A D i n g a n G r i n d i n g p r i n c i p l e M B e i j i n g E l e c-t r o n i c I n d u s t r y P r e s s2011作者简介张银霞,女,1974年生,博士㊁副教授㊂主要研究方向:抗疲劳制造技术和精密超精密加工技术㊂E-m a i l:z h a n g y i n x i a@z z u.e d u.c n通信作者:原少帅,男,1995年生,硕士研究生㊂主要研究方向:抗疲劳制造技术和精密超精密加工技术㊂E-m a i l:1146970305@q q.c o m㊂(修回日期:2020–06–10)(编辑:王洁)07Copyright©博看网 . All Rights Reserved.。
18CrNiMo7-6

1 8 C r N i Mo 7 — 6齿 轮轴 失 效分 析
丁 贤模
( 西 门子机械 传动 ( 天津) 有 限公 司 , 天津 3 0 0 4 0 0 )
a n a l y s i s , me c h a n i c l a p r o p e r t y t e s t , f r a c t u r e a n a l y s i s a n d me t a l l o g r a p h i c i n s p e c t i o n . T e s t r e s u l t s s h o w e d t h a t t h e i mp o r t a n t r e a s o n f o r f a t i g u e f r a c t u r e wa s s ma l l s fe a t y ma r g i n f o r t h e i r s k r e s i s t a n t w o r k i n g l o a d
An a l y s i s o n F a i l u r e o f 1 8 Cr Ni Mo 7 - 6 Ge a r S h a f t
DI NG Xi a n -mo
( S i e m e n s Me c h a n i c a l D i r v e S y s t e m s[ T i a n j i n ] C o . , Dd . , T i a n j i n 3 0 0 4 0 0 , C h i n a )
《18CrNiMo7-6渗碳钢磁场深冷处理工艺及磨损监测技术的研究》
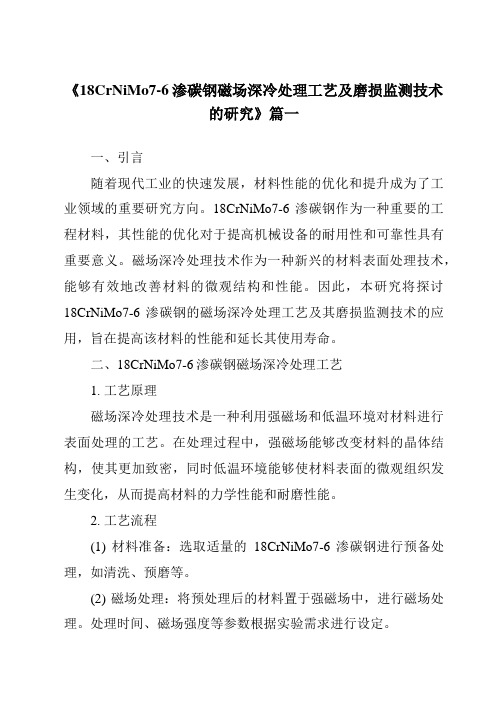
《18CrNiMo7-6渗碳钢磁场深冷处理工艺及磨损监测技术的研究》篇一一、引言随着现代工业的快速发展,材料性能的优化和提升成为了工业领域的重要研究方向。
18CrNiMo7-6渗碳钢作为一种重要的工程材料,其性能的优化对于提高机械设备的耐用性和可靠性具有重要意义。
磁场深冷处理技术作为一种新兴的材料表面处理技术,能够有效地改善材料的微观结构和性能。
因此,本研究将探讨18CrNiMo7-6渗碳钢的磁场深冷处理工艺及其磨损监测技术的应用,旨在提高该材料的性能和延长其使用寿命。
二、18CrNiMo7-6渗碳钢磁场深冷处理工艺1. 工艺原理磁场深冷处理技术是一种利用强磁场和低温环境对材料进行表面处理的工艺。
在处理过程中,强磁场能够改变材料的晶体结构,使其更加致密,同时低温环境能够使材料表面的微观组织发生变化,从而提高材料的力学性能和耐磨性能。
2. 工艺流程(1) 材料准备:选取适量的18CrNiMo7-6渗碳钢进行预备处理,如清洗、预磨等。
(2) 磁场处理:将预处理后的材料置于强磁场中,进行磁场处理。
处理时间、磁场强度等参数根据实验需求进行设定。
(3) 深冷处理:将经过磁场处理的材料置于低温环境中进行深冷处理。
深冷温度、处理时间等参数同样需要根据实验需求进行设定。
(4) 后续处理:深冷处理后,对材料进行适当的后续处理,如回火、清洗等。
三、磨损监测技术的应用磨损监测技术是评估材料性能的重要手段。
在18CrNiMo7-6渗碳钢的磁场深冷处理过程中,通过引入磨损监测技术,可以实时监测材料的磨损情况,从而评估处理效果。
常用的磨损监测技术包括摩擦系数测量、磨损量测量、表面形貌观察等。
四、实验结果与分析1. 磁场深冷处理对18CrNiMo7-6渗碳钢性能的影响通过对比实验前后的材料性能,可以发现磁场深冷处理能够显著提高18CrNiMo7-6渗碳钢的硬度、耐磨性和抗疲劳性能。
其中,硬度提高的主要原因是强磁场和深冷处理使材料表面微观组织更加致密;耐磨性和抗疲劳性能的提高则归因于材料晶体结构的改善和表面粗糙度的降低。
高速精密磨削18crnimo7-6表面三维粗糙度试验研究

粤遭泽贼则葬糟贼:In order to study the effect of high -speed precision grinding on the surface quality of 18CrNiMo7 -6 steel,the single-factor test was carried out on the wheel granularity,wheel velocity,grinding depth and workpiece velocity .The twodimensional and three-dimensional surface roughness were compared,and the influence and its degree of grinding parameters on surface roughness were analyzed. The test draws the following conclusions. Three -dimensional roughness reflects surface information more precisely than two -dimensional roughness. The increases of the wheel velocity and the wheel granularity result in the decrease of arithmetic -mean deviation Sa,root -mean -square deviation Sq,kurtosis Sku and the increase of skewness Ssk .That is,the surface quality improved. W hlie,the increases of grinding depth and workpiece velocity will cause the parameters to have the opposite trend. W heel granularity has the greatest influence on the three -dimensional roughness parameters,while the workpiece velocity has almost no effect on three -dimensional roughness. The conclusions provide a reference for the parameters selection of high-speed precision grinding. Key Words:High-Speed Precision Grinding;Three-Dimensional Roughness;Kurtosis;Skewness
18crnimo7-6钢输出齿轮轴裂纹分析

^1裂纹横向形貌 裂纹横向形貌见图Ia。宏观组织除肯主裂纹外.还柯一条小裂纹。
2.1裂纹断121形貌描述 裂纹断13形貌见图Ib。飙裂纹断面的形貌来看:从外到里。裂纹花样有四种。
孺瓣¨mⅢ圳㈣∽Ⅻ㈣㈣目∞掘嗍㈣Ⅲ㈣…. I、裂纹断面比较平.占裂纹整体的8 3%,是第一次裂纹的主裂纹,而且裂纹表面有氧化皮.说明该裂纹
ladKun,ZHANGKai,LINGHu’qtill,ZHUYu-hua,L1Dc-jtm (DHIDCWGroupCo.Ltd.DalianHuarui Special TransmissionEquipmentCo,LtdDalanll6620)
l引言 我公司生产的输出齿轮轴.齿部础38m1×130mm,轴总长505 5 ram。使用的材料是18CrNiMo%6钢.加
渗剂,从而降低冷却速度,使表面硬度低;距裂纹处的硬度高,是由于裂纹处有渗碳屡,经过渗碳淬火后,从 而提高了裂纹两侧的硬度。
I)裂纹样:第一部分裂纹断面比较平的裂纹处经腐蚀有溶碳层,择检测有效硬化层2 20mm。由裂纹表 面及里依次细针马氏体+残余莞氏体+少量碳化物—板条马氏体。由十裂纹两侧青海碳层,说明裂纹在渗碳自i就 已经存在。第二部分裂纹断面呈典型的河流花样,该裂纹表面处的组织是扳器与氏体。说明该处的裂纹是在港 碟淬火后形成的。
2】裂纹断口处的高倍试片,磨制横向试样后在金相显微镜r观察,裂纹处有鞍重非金属夹杂物.见图2a。 ’F行于断13磨制纵向试样.在外圆附近有大最夹杂物,呈条状分布,见罔2b。
增刊
付M.荨18CrNiMoT-6铡输出齿轮轴圜附近夹镕}物lOOx
3)齿样:由表及里依次细钳马氏体+残余奥氏体+少量碳化物一板条马氏体。齿样的洛碳层215ramt碳化
18CrNiMo7-6合金钢的弯曲微动疲劳特性
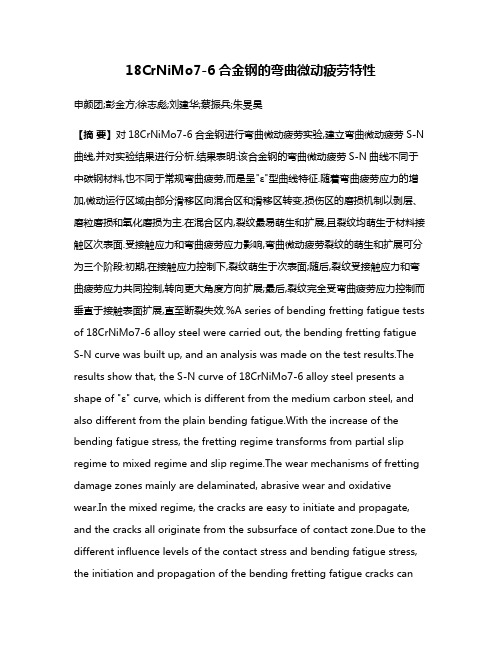
18CrNiMo7-6合金钢的弯曲微动疲劳特性申颜团;彭金方;徐志彪;刘建华;蔡振兵;朱旻昊【摘要】对18CrNiMo7-6合金钢进行弯曲微动疲劳实验,建立弯曲微动疲劳S-N 曲线,并对实验结果进行分析.结果表明:该合金钢的弯曲微动疲劳S-N曲线不同于中碳钢材料,也不同于常规弯曲疲劳,而是呈"ε"型曲线特征.随着弯曲疲劳应力的增加,微动运行区域由部分滑移区向混合区和滑移区转变,损伤区的磨损机制以剥层、磨粒磨损和氧化磨损为主.在混合区内,裂纹最易萌生和扩展,且裂纹均萌生于材料接触区次表面.受接触应力和弯曲疲劳应力影响,弯曲微动疲劳裂纹的萌生和扩展可分为三个阶段:初期,在接触应力控制下,裂纹萌生于次表面;随后,裂纹受接触应力和弯曲疲劳应力共同控制,转向更大角度方向扩展;最后,裂纹完全受弯曲疲劳应力控制而垂直于接触表面扩展,直至断裂失效.%A series of bending fretting fatigue tests of 18CrNiMo7-6 alloy steel were carried out, the bending fretting fatigue S-N curve was built up, and an analysis was made on the test results.The results show that, the S-N curve of 18CrNiMo7-6 alloy steel presents a shape of "ε" curve, which is different from the medium carbon steel, and also different from the plain bending fatigue.With the increase of the bending fatigue stress, the fretting regime transforms from partial slip regime to mixed regime and slip regime.The wear mechanisms of fretting damage zones mainly are delaminated, abrasive wear and oxidative wear.In the mixed regime, the cracks are easy to initiate and propagate, and the cracks all originate from the subsurface of contact zone.Due to the different influence levels of the contact stress and bending fatigue stress, the initiation and propagation of the bending fretting fatigue cracks canbe divided into three stages.Firstly, the cracks initiate from subsurface under the control of contact stress;then propagate to a larger angle direction under the joint control of contact stress and bending fatigue stress;lastly the cracks propagate vertically to contact surface until fracture failure under the control of bending fatigue stress.【期刊名称】《材料工程》【年(卷),期】2017(045)007【总页数】8页(P103-110)【关键词】弯曲微动疲劳;微动损伤;疲劳寿命;裂纹扩展【作者】申颜团;彭金方;徐志彪;刘建华;蔡振兵;朱旻昊【作者单位】西南交通大学牵引动力国家重点实验室,成都 610031;西南交通大学牵引动力国家重点实验室,成都 610031;西南交通大学材料先进技术教育部重点实验室,成都 610031;西南交通大学牵引动力国家重点实验室,成都 610031;西南交通大学材料先进技术教育部重点实验室,成都 610031;西南交通大学牵引动力国家重点实验室,成都 610031;西南交通大学材料先进技术教育部重点实验室,成都610031【正文语种】中文【中图分类】TH117.1微动疲劳是指构件接触表面由于承受外界交变疲劳载荷引起变形而产生位移幅值极小的相对运动(通常在微米量级),促使疲劳裂纹提前萌生和扩展,最终导致构件过早失效破坏的现象[1,2]。
外圆磨削18CrNiMo7-6力模型及表面完整性研究

外圆磨削18CrNiMo7-6力模型及表面完整性研究王栋;陈磊;张志鹏【期刊名称】《中国机械工程》【年(卷),期】2024(35)3【摘要】为了准确和有效地控制磨削参数对磨削力及表面完整性的影响,通过解析法,以磨粒与材料间的塑性变形、压痕理论以及剪切应变效应为理论依据,建立了三阶段的磨削力理论模型。
选定棕刚玉砂轮进行磨削试验,探究了磨削参数对磨削力的影响以及磨削参数和磨削力对表面完整性的影响,通过外圆横向磨削正交试验获得了外圆磨削最优工艺参数。
结果表明,外圆磨削力模型法向磨削力和切向磨削力的预测平均误差分别为5.56%和7.08%;砂轮径向进给速度f_(r)对磨削力的影响最大,磨削宽度b次之,工件转速n_(w)和砂轮粒度的影响较小;f_(r)和b对残余应力的影响较大,砂轮粒度对表面粗糙度的影响最大;随着磨削力的增大,表面粗糙度值一直增大,残余应力先减小后增大,沿深度方向残余应力最大值先增大后减小,在试验所取参数条件下,影响残余应力的深度分布范围基本在20~40μm;最优工艺参数组合如下:f_(r)=0.15 mm/min,n_(w)=120 r/min,b=10 mm,砂轮粒度80。
【总页数】13页(P381-393)【作者】王栋;陈磊;张志鹏【作者单位】郑州大学机械与动力工程学院【正文语种】中文【中图分类】TH16;TG58【相关文献】1.外圆磨削18CrNiMo7-6表面完整性研究2.外圆磨削18CrNiMo7-6表面完整性研究3.18CrNiMo7-6外圆磨削力对残余应力的影响4.高速磨削对18CrNiMo7-6表面完整性的影响研究5.外圆纵向磨削工艺对18CrNiMo7-6钢表面完整性的影响因版权原因,仅展示原文概要,查看原文内容请购买。
18CrNiMo7-6合金钢J-C损伤模型失效参数研究

18CrNiMo7-6合金钢J-C损伤模型失效参数研究吴少洋;张建伟;卢凤强;李元鑫;秦瑾鸿【期刊名称】《郑州大学学报:工学版》【年(卷),期】2023(44)1【摘要】针对高速冲击、机械成型加工等数值模拟中广泛应用的Johnson-Cook(J-C)损伤模型失效参数求取问题,对18CrNiMo7-6合金钢材料开展了3个系列的力学实验。
通过缺口试样准静态拉伸实验和有限元模拟,确定了既考虑空间分布效应,又考虑应变累积效应的应力三轴度的计算方法。
结果表明:失效应变随应力三轴度的增大而减小;通过10^(-3)、10、10^(3)s^(-1)应变率下的拉伸实验与霍普金森拉杆(SHTB)冲击实验,发现随着应变率的增大,材料屈服强度有所增加,表明了材料有明显的应变率强化效应,并且失效应变随着应变率的增大而增大;在25、200、300、400℃的拉伸实验中发现随着温度的升高,材料屈服强度逐渐降低,但材料的抗拉强度在300℃时要高于200℃下的结果,并且随着温度的升高失效应变逐渐减小。
根据上述实验结果拟合得到了J-C损伤模型失效参数,从拟合优度可以看出拟合所得参数的可靠性。
最后通过Taylor冲击实验与有限元模拟进行验证,结果表明,当冲击速度为430 m/s时,实验与仿真得到的冲击试样均发生了破坏,并且有限元模拟得到的试样破坏形态与实验结果最大误差为6.3%,结果吻合良好,验证了所选用的J-C 损伤模型的合理性以及实验所得参数的有效性。
【总页数】7页(P70-76)【作者】吴少洋;张建伟;卢凤强;李元鑫;秦瑾鸿【作者单位】郑州大学机械与动力工程学院;郑州大学力学与安全工程学院【正文语种】中文【中图分类】O346.5【相关文献】1.信息科学与系统科学信息科学与系统科学基础学科——两参数指数分布产品全样本场合下步进应力加速寿命试验损伤失效率模型下的统计分析2.基于应力三轴度修正的Q345钢J-C失效模型参数研究3.45钢的J-C损伤失效参量研究4.单参数指数分布产品截尾样本场合简单步进应力加速寿命试验损伤失效率模型下的统计分析5.基于多晶体模型的18CrNiMo7-6合金钢本构参数确定因版权原因,仅展示原文概要,查看原文内容请购买。
- 1、下载文档前请自行甄别文档内容的完整性,平台不提供额外的编辑、内容补充、找答案等附加服务。
- 2、"仅部分预览"的文档,不可在线预览部分如存在完整性等问题,可反馈申请退款(可完整预览的文档不适用该条件!)。
- 3、如文档侵犯您的权益,请联系客服反馈,我们会尽快为您处理(人工客服工作时间:9:00-18:30)。
18CrNiMo7-6钢齿轮磨削烧伤裂纹分析孔德群;孔新建【摘要】主要使用金相学的方法研究了18CrNiMo7-6风电齿轮渗碳淬火后磨削烧伤/裂纹。
结合光谱分析与硬度检测,探索了“渗碳-淬火-回火”热处理与磨削烧伤对金相组织的影响,讨论了残余应力对磨削裂纹形核与长大的影响。
引起磨削烧伤及裂纹的原因是磨齿工序中冷却液喷射角度不良。
将磨削烧伤及裂纹的可能性最小化,过程质量控制应从以下方面实现:原材料检验、热处理工艺及显微组织,磨削工具及工艺参数。
【期刊名称】《金属加工:热加工》【年(卷),期】2016(000)019【总页数】5页(P20-24)【关键词】齿轮;渗碳;淬火;磨削;烧伤;裂纹【作者】孔德群;孔新建【作者单位】采埃孚传动系统(北京)有限公司;长城汽车股份有限公司【正文语种】中文某型号风电齿轮模数7.85,材质18CrNiMo7-6,在渗碳淬火后磨齿工序发生烧伤与裂纹现象。
磨齿采用成形磨工艺,机床为国外某品牌P1200G型磨床,磨具为国外某品牌TG型砂轮,切削液为不含氯和重金属的国外某品牌G600HC型高性能纯油性切削液。
烧伤发生在齿轮的一部分齿面;裂纹发生在一部分烧伤严重的齿面,自烧伤的底部产生,其形态特征为,垂直于磨削前进方向,向齿顶扩展。
调整切削液喷嘴角度后,继续磨削加工,加工量不超过0.05mm,未产生新的烧伤/裂纹,原有的烧伤面积减少,烧伤深度与裂纹深度均有减小。
该齿轮已申请报废处理,检测其烧伤/开裂的齿,通过理化检验,讨论分析产生失效的原因。
使用线切割机在裂纹齿与正常齿上分别切取小试块,使用SPECTROTEST型直读光谱仪检测其化学成分;使用INNOVATEST Nemesis 9000 型万能硬度计和Zwick/Roell ZHμ型显微硬度计,检测试样的表面/心部硬度与渗层深度;试样经镶嵌、磨抛处理、3%硝酸酒精腐蚀后,使用Zeiss Axio Imager A 2m型显微镜观测金相组织,用金相法评定残留奥氏体含量。
图1显示了磨削烧伤与裂纹的情况。
图2 展示了裂纹齿的切样试块的形态特征,裂纹逐渐向齿顶方向扩展;目视看不出烧伤或裂纹的迹象,如图2a所示;但是经硝酸酒精溶液腐蚀后,齿面既有裂纹,又有烧伤,如图2b所示,黑色即为烧伤带。
1. 化学成分齿轮材料为渗碳钢18CrNiMo7-6 (DIN 10084),其合金成分满足技术要求,结果见表1。
2. 非金属夹杂物在裂纹源区附近分别沿横向和纵向切取金相试样,磨抛后观察,仅可见数量很少的微小夹杂。
根据GB/T 10561—2005《钢中非金属夹杂物含量的测定标准评级图显微检验法》,夹杂物评级结果见表2,可见符合技术要求。
3. 硬度检测试样的表面硬度、心部硬度(转换为抗拉强度)与渗碳硬化层深度(CHD550HV1),检测结果见表3。
心部硬度与CHD均满足技术要求,而表面硬度则有所不同。
正常齿的齿面硬度符合要求;而裂纹齿的齿面硬度因烧伤而降低,低于硬度下限值。
图3给出裂纹齿与正常齿的齿面硬度曲线。
正常齿的表面硬度最高722HV1,自表面向内部逐渐降低。
心部硬度(抗拉强度)与渗层深度均符合技术要求,齿轮经历了正常的热处理工艺过程。
裂纹齿与正常齿的表层硬度差别很大。
裂纹齿受磨削烧伤的影响,显著降低齿面硬度至524HV1,影响深度为0.70~0.90mm。
4. 金相检验表4给出了金相组织检验结果。
由于磨削量较大,热处理后的表面氧化层(0.01~0.02mm)已完全去除,均未检测到。
渗碳层均无碳化物,心部组织均为低碳板条马氏体,无块状铁素体。
正常齿的渗碳层为弥散分布的细小针状马氏体,残留奥氏体含量为6%,符合技术要求(见图4)。
裂纹齿的渗碳层残留奥氏体因磨削烧伤的温度升高而发生组织转变,几乎无残留奥氏体。
(1)烧伤特征磨削热产生的温度,从表至里逐渐降低,因此磨削烧伤使齿面也由表至里有规律地发生组织转变,导致硬度产生变化。
图5给出了典型烧伤区域的组织,磨削热的影响深度约0.75mm,这与硬度-深度曲线的结果(见图3)吻合。
齿面由表至里的金相组织转变为二次淬火马氏体、回火索氏体、二次回火马氏体、原一次回火马氏体。
结合以上的硬度分析,可以推测出磨削烧伤产生瞬时的温度场梯度。
注意到图5最外面有1个白亮层,该层组织为强烈的磨削热与切削液共同作用而得到的二次淬火马氏体。
图6与图7佐证了这一点,二次淬火层深度约0.90 mm,其硬度应该显著增加,测试值为781~804HV1。
另外还应注意到,最外面有约1个晶粒深度的晶粒过烧现象,表明磨削热相当剧烈,使齿面温度剧升,甚至超过1000℃。
二次淬火层下侧即为回火烧伤区,硬度显著下降。
随着回火温度降低,逐渐由黑色转变为棕褐色/棕黄色,磨削热产生的温度使其依次发生回火索氏体(见图8)转变、回火马氏体转变,硬度下降的趋势也逐渐减弱。
(2)裂纹特征首先考察二次磨削后裂纹区的显微特征。
图9由5张金相图片拼接而成,裂纹产生于磨削烧伤区(黑褐色区域)。
早在1979年Torrance教授[1]研究证实,未烧伤工件表面从未发生磨削裂纹,磨削裂纹总是与工件的烧伤有关,裂纹总是由其附近的烧伤诱发而产生的。
从图9可以看出,裂纹沿磨削烧伤影响区呈弧形向前扩展,沿裂纹扩展方向,裂纹宽度逐渐变窄。
本研究中,裂纹最大深度约为1.45mm,长度8.50~10.50mm。
裂纹长大方向的一侧为大面积烧伤带,另一侧为正常区域。
正常区域为渗碳淬火后的一次回火马氏体,未受到磨削的热影响。
图10显示了裂纹源附近的特征,裂纹最大宽度约0.18mm,裂纹开口翘起高度为0.08mm,说明裂纹源位置在开裂之前承受了巨大的拉应力,产生较大的宏观塑性变形。
图11给出了裂纹扩展前沿的形貌,可以看出明显的沿晶断裂的特征。
Torrance教授[1]曾报道,裂纹形核于二次淬火区域的内侧,大体上沿垂直于表面的方向穿过回火烧伤区域,在回火区域之下主裂纹会分叉,通过与原奥氏体晶粒晶界的对比,确认裂纹呈现沿晶断裂形貌,与淬火裂纹是一样的。
本文所观察的磨削裂纹,基本与之一致。
然而,因原一次回火马氏体区域的强度较高,主裂纹在穿过回火烧伤区之后发生明显的转折,裂纹的扩展方向大体与齿面平行,这一点Torrance教授没有提及。
随着裂纹扩展的进行,残余应力也逐渐释放,裂纹长大的驱动力降低,裂纹的宽度变小;裂纹停止长大前,长大方向又转向更容易发生开裂的回火烧伤区(见图9)。
1. 烧伤原因磨削加工对工件表面产生的缺陷分为3类:二次淬火烧伤、回火烧伤和裂纹[2]。
当表面温度超过钢的回火温度而不超过Ar1线(约730℃)时,磨削表面将发生回火,即回火烧伤;烧伤的局部因而变软,在应力作用下发生塑性变形。
当温度超过Ar1线后,就会形成奥氏体,随后立即因快速冷却发生淬火,形成脆硬马氏体组织,即二次淬火烧伤;二次淬火烧伤,总是在其内侧伴随着回火烧伤;马氏体组织呈膨胀状态,表层处于压应力作用。
烧伤的直接原因是,砂轮片与齿面在一定压力下产生大量的热量,切削液未能及时有效地带走,致使齿面温度剧烈骤升,结果使齿面发生高温回火;温度过高则会导致奥氏体化,甚至奥氏体晶粒过烧,在切削液作用下发生二次淬火。
一般齿面磨削烧伤的原因,与磨削加工的工艺参数有关,与原材料、热处理基本无关。
影响齿面烧伤的因素主要有:砂轮片的粒度、硬度、转速,修行间隔,进给量,磨削前进速度,磨削压力,切削液的能力、流量、速度、角度等。
对于本次磨削烧伤,结合实际现场调查,由于切削液喷嘴位置不良,切削液未能有效地将磨削热量带走,引起齿面温度急剧升高,引起渗碳层组织转变,造成烧伤现象。
2. 裂纹原因引起磨削裂纹的因素有内因(原材料质量/热处理工艺)和外因(磨削工艺)两方面。
关于原材料缺陷,主要是较大的非金属夹杂物,严重的带状组织或冶金成分偏析。
关于热处理,渗碳淬火齿轮表面磨削裂纹可能因素有晶粒粗大或马氏体针粗大,网状碳化物,过多的残留奥氏体含量(20%以上)。
关于机加工磨齿工艺,如上述的引起烧伤的因素,都可能造成热应力过大而引起齿面开裂。
结合以上检测分析结果,从3个方面讨论该齿轮的裂纹原因。
(1)原材料分析影响磨削裂纹的原材料因素主要是冶金质量,包括化学成分、低倍缺陷(如偏析、疏松)和高倍缺陷(如非金属夹杂、带状组织)。
经光谱分析与非金属夹杂物检验,原材料符合技术要求,不具备有利于烧伤或裂纹的因素。
(2)热处理分析检测结果显示,渗碳淬火后齿面硬度与金相组织达到技术要求,齿面硬度60.7~61.8HRC,表面碳含量(质量分数)为0.72%,表层组织为细小的针状马氏体,无碳化物,残留奥氏体6%,远低于要求的20%。
Tkhagapsoev等[3]研究表明,组织的非均匀性是产生残余内应力的根本原因,而残余内应力在裂纹形成中占主导地位。
当表面碳化物尺寸达到6~10μm时,容易产生磨削裂纹,若碳化物发生聚集,裂纹趋势急剧增加。
渗碳层的表面碳含量降至0.60%~0.75%时,几乎无碳化物,渗碳层与心部的马氏体转变温度差异显著缩小,残余应力也相应减小。
在此条件下,齿轮表面形成磨削裂纹的可能性降低,即热处理后齿面不具备利于磨削裂纹的因素。
(3)磨削分析 1976年Hahn提出了关于磨削应力的热塑性理论[4],在回火烧伤区,最大拉应力产生于工件表面的烧伤区域的中心位置;然而当二次淬火发生时,淬火区域受相变的影响而呈压应力状态,与其紧邻的回火烧伤区则呈最大拉应力状态,裂纹最容易在这里形成。
裂纹沿原奥氏体晶界扩展,是与工件在热处理时产生的内应力有关的。
Stickels[5]发现在奥氏体化过程中,碳化物更倾向于在奥氏体晶界溶解,而非奥氏体晶粒内部。
当工件淬火时,马氏体将首先在奥氏体的贫碳区(晶粒内部)形成,随着淬火进行,马氏体片朝着晶界方向迅速长大,不同位向的马氏体片可能在晶界发生撞击,引发强烈的局部应变,也就可能造成沿晶的淬火显微裂纹。
即便未形成淬火裂纹,原奥氏体晶界仍是强度的薄弱区,成为磨削裂纹扩展的快速通道。
Wojcik等[6]发现,二次淬火区的深度可达到0.213mm,磨削裂纹可深入0.14~0.68mm,磨削裂纹的产生与砂轮的磨料、线速度、切削用量、切削液等息息相关。
对于本次磨削裂纹,由于切削液喷嘴位置不良,造成烧伤现象。
原残留奥氏体发生转变,随温度升高而转变为回火马氏体,300℃基本转变完成。
温度继续升高,发生二次淬火,由外至内,从原来的一次回火马氏体转变成二次淬火马氏体、高温回火索氏体、二次回火马氏体;淬火马氏体、一次回火马氏体、二次回火马氏体、回火索氏体的比体积依次较小,相变必然引起比体积的变化;而比体积的变化则引起组织应力,再加上急热急冷造成的热应力,在烧伤影响区附近形成强烈的拉应力,二次淬火烧伤与高温回火烧伤的过渡区所受的拉应力水平最高。