120×120连铸方坯定尺火焰切割机
一种方坯火切机去除铸坯切割瘤的可行性方案
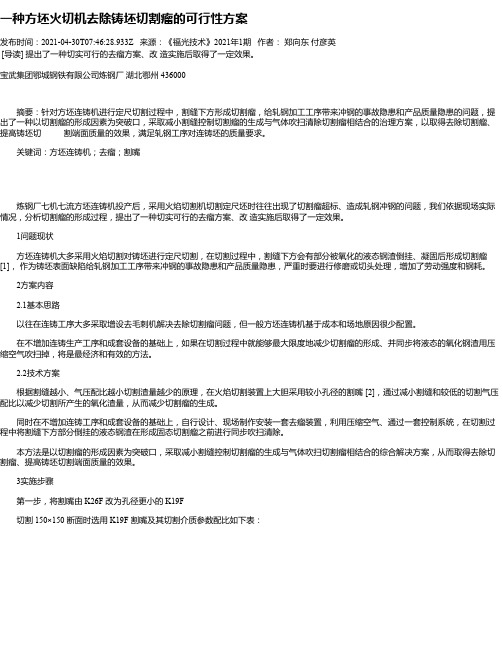
一种方坯火切机去除铸坯切割瘤的可行性方案发布时间:2021-04-30T07:46:28.933Z 来源:《福光技术》2021年1期作者:郑向东付彦英[导读] 提出了一种切实可行的去瘤方案、改造实施后取得了一定效果。
宝武集团鄂城钢铁有限公司炼钢厂湖北鄂州 436000摘要:针对方坯连铸机进行定尺切割过程中,割缝下方形成切割瘤,给轧钢加工工序带来冲钢的事故隐患和产品质量隐患的问题,提出了一种以切割瘤的形成因素为突破口,采取减小割缝控制切割瘤的生成与气体吹扫清除切割瘤相结合的治理方案,以取得去除切割瘤、提高铸坯切割端面质量的效果,满足轧钢工序对连铸坯的质量要求。
关键词:方坯连铸机;去瘤;割嘴炼钢厂七机七流方坯连铸机投产后,采用火焰切割机切割定尺坯时往往出现了切割瘤超标、造成轧钢冲钢的问题,我们依据现场实际情况,分析切割瘤的形成过程,提出了一种切实可行的去瘤方案、改造实施后取得了一定效果。
1问题现状方坯连铸机大多采用火焰切割对铸坯进行定尺切割,在切割过程中,割缝下方会有部分被氧化的液态钢渣倒挂、凝固后形成切割瘤[1],作为铸坯表面缺陷给轧钢加工工序带来冲钢的事故隐患和产品质量隐患,严重时要进行修磨或切头处理,增加了劳动强度和钢耗。
2方案内容2.1基本思路以往在连铸工序大多采取增设去毛刺机解决去除切割瘤问题,但一般方坯连铸机基于成本和场地原因很少配置。
在不增加连铸生产工序和成套设备的基础上,如果在切割过程中就能够最大限度地减少切割瘤的形成、并同步将液态的氧化钢渣用压缩空气吹扫掉,将是最经济和有效的方法。
2.2技术方案根据割缝越小、气压配比越小切割渣量越少的原理,在火焰切割装置上大胆采用较小孔径的割嘴 [2],通过减小割缝和较低的切割气压配比以减少切割所产生的氧化渣量,从而减少切割瘤的生成。
同时在不增加连铸工序和成套设备的基础上,自行设计、现场制作安装一套去瘤装置,利用压缩空气、通过一套控制系统,在切割过程中将割缝下方部分倒挂的液态钢渣在形成固态切割瘤之前进行同步吹扫清除。
鞍钢一炼钢大方坯连铸机

Abstract T h is article in troduces the m ain info rm ation concern ing the bloom caster built up recen tly at N o11 Steelm ak ing P lan t, A n shan Iron & Steel (Group ) Com pany, and the discussion of the techn ical characteristics of the caster, in term s of the quality requirem en t of the h igh2carbon steel bloom 1
90t 3座 36m in 95t
100t 36m in 5℃ m in
100t 36m in 215ppm
3 连铸设备的工艺流程和主要性能 参数
转炉冶炼的连铸钢水由钢水渡线车运输到连 铸车间的钢水接收跨后, 吊运到100t L F VD 装 置上进行二次精炼, 经吹A r、提温、合金化和真 空脱气处理后, 再由160t 天车吊放到大包回转台 上进行浇注。浇注的4流大方坯经切割和称量后, 由推钢机移送至热送辊道并热送到连轧车间进行 装炉轧制。对有缺陷的铸坯, 在连轧车间由横移台 车运送至铸坯精整跨进行下线精整。连铸机的工 艺流程和设备的主要性能参数分别见图1和表3。
·6 · 重 型 机 械 2000 N o16
事故回转系统。 (2) 中间罐系统及保护浇注 采用了大容量
T 形中间罐, 并设有拦渣墙和溢流堰, 使夹杂物能 够充分地上浮分离。中间罐正常容量32t, 工作液 位高度800mm , 能保证多炉连浇更换钢包时连铸 机保持正常的浇注速度。中间罐内的钢水液位采 用称重系统与大包滑动水口联锁控制, 保证中间 罐钢水液面的稳定。中间罐钢水向结晶器的注入 采用滑动水口控制。
连铸坯切割
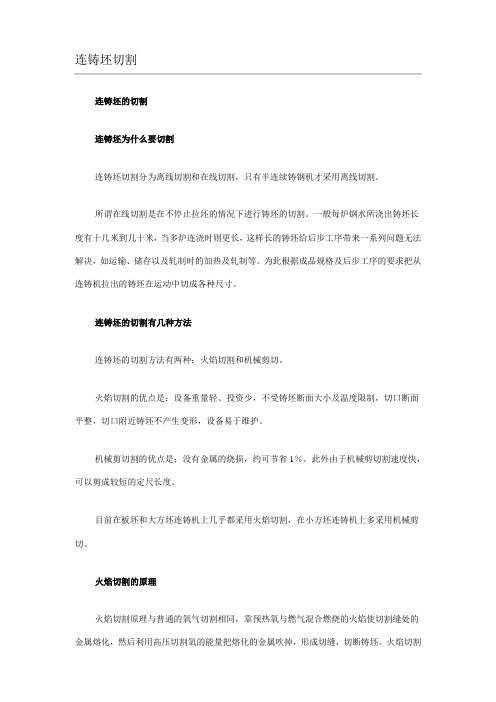
连铸坯切割连铸坯的切割连铸坯为什么要切割连铸坯切割分为离线切割和在线切割,只有半连续铸钢机才采用离线切割。
所谓在线切割是在不停止拉坯的情况下进行铸坯的切割。
一般每炉钢水所浇出铸坯长度有十几米到几十米,当多炉连浇时则更长,这样长的铸坯给后步工序带来一系列问题无法解决,如运输、储存以及轧制时的加热及轧制等。
为此根据成品规格及后步工序的要求把从连铸机拉出的铸坯在运动中切成各种尺寸。
连铸坯的切割有几种方法连铸坯的切割方法有两种:火焰切割和机械剪切。
火焰切割的优点是:设备重量轻、投资少,不受铸坯断面大小及温度限制,切口断面平整,切口附近铸坯不产生变形,设备易于维护。
机械剪切割的优点是:没有金属的烧损,约可节省1%。
此外由于机械剪切割速度快,可以剪成较短的定尺长度。
目前在板坯和大方坯连铸机上几乎都采用火焰切割,在小方坯连铸机上多采用机械剪切。
火焰切割的原理火焰切割原理与普通的氧气切割相同,靠预热氧与燃气混合燃烧的火焰使切割缝处的金属熔化,然后利用高压切割氧的能量把熔化的金属吹掉,形成切缝,切断铸坯。
火焰切割可使用多种燃气,如乙炔、天然气、丙烷、精制的焦炉煤气等。
当用火焰切割不锈钢铸坯时,因在高温条件下易于产生粘稠的铬氧化物,熔点较高,能阻断切割的进行,且熔渣不易排除,使切割中断,所以须要辅加铁粉或其它助熔剂。
火焰切割设备的特点火焰切割设备应具有如下特点:(1)切割设备应具有防热、防尘措施,能在强烈热辐射和尘埃等恶劣工况下长期正常运转,可实现自动定尺自动切割功能。
(2)切割枪效能高,切割速度快,切口质量好,切缝小,工作稳定可靠,抗回火能力强,切割噪音低,介质耗量少,切嘴寿命长。
(3)介质供送及控制系统布置合理,安全可靠,可实现远距离控制。
火焰切割装置由切割车、同步装置、切割小车及传动、切割枪、铸坯端面检测装置、能源介质供应系统及电控系统所组成。
切割枪的形式切割枪是火焰切割装置的重要部件,而割嘴又是它的核心器件,它直接影响到切割速度、切割质量、切缝宽度、介质耗量以及切割稳定等重要指标。
一套R10m十机十流方圆坯连铸机技术平台(可编辑)

1 以高起点高效率为原则确保将项目建设成为具有先进水平科技
含量高经济效益好资源消耗少人力资源优势得到充分发挥的现代化
2 合理选择生产工艺和技术对各生产环节的生产工艺附件进行严
格科学的论证采用先进可靠的技术现代化高效化的设备配置紧凑合
理的总图布置实现企业的最低成本和最佳的经济效益
连铸机工艺技术在连铸生产中起着至关重要的作用本章就临沂
手动夹持装置
液压控制单元
技术参数
表 3-8 技术参数
数量 10×2 套快换结构四支缸
形式 带 有推 进液 压缸 的
快速更换装置
推进液压缸行程 300mm 液压介质供应 单
独液压站 塞棒自动执行机构
功能和结构
塞棒自动执行机构安装在中间罐体上用于在浇注过程中控制中
间罐至结晶器的钢水流量流量由结晶器液面控制系统控制
技术参数
表 3-3 技术参数
数量 2 套
形式 半自动
长水口压紧方式 液压
旋转方式 减速器
摆动方式 手动 前后移动 手动
水口密封气体 氩气 参数以最终设计为准
中间罐
功能与结构
中间罐采用钢板焊接结构内部砌耐火砖
罐体上设有吊耳方便中间罐的吊动和检修更换中间罐上设有挡
块方便中间罐盖在中间罐上的定位同时中间罐上设有加工好的安装
辅助设备包括液压管线阀块控制阀台等
技术参数
表 3-12 技术参数
型式 高低轨式 承载能力 ~80t 行走机构 行 走 驱 动 装
置 变频电机减速器驱动
行走驱动电机功率 75KW×2
行走速度 2~20mmin 变频可调 升降机构 升 降 驱 动 型 式
液压缸 一组 4 个
升降行程 ~400mm
方坯连铸机切割系统电气自动控制改造

投产至 20 年 l , 04 0月 该系统难 以实现稳定 自动切 割 。原系统是采用每流 3 个信号传感器进行控制 的 接 触式 自动切 割 , 系统原 理在 理论 上简单 可行 , 由 但 于切割环境温度过高 , 使得在该系统 中起 主要作用
p o r m f u o c r o u , t h i f ie o i o in l i l t n d t r d c d b n o e ,t f cl ov d p be f ih r g a o t - ot l t Wi t ea d o l tp st n sg a mu ai aa p o u e y e c d r I e e t s le r lmso g a r c h b i s o y o h
据模 拟产生切 割机 的位 置定 尺信 号来取代 原来 的传感器信号 , 而有 效地解决 了因高温区 电缆 及信号 传感器 寿命 从
短, 故障率高而影响生产的问题。
关
键
词 : 方 坯连 铸机 ; 火焰 切割机 ;L 增量 型编码 器 ; P C; 高数计 数模 块
文献 标识码 : B
维普资讯
・
3 ・ 0
江
西
冶
金
20 0 7年 2月
横杆 上有 3个 位置 A, C B, 。
3 2 主要 设备技 术 .
中图分 类号 : T 3 5 1 F4 .
Pli ay i fCu trElc r nc Auo c n r lS s m an An lsso te e to i t -o to y t e
Tr n f r a i n Bi e n n o s M a h n a so m t on o l t Co t u u l i c ie
一种火焰切割机模块化设计分析与研究

( C C S n u til un c O.L D, h n qn 0 01 , hn ) MC I DI d sra F r a eC , T C o g ig4 0 3 C ia I
机 械 设 计 与 制 造
24 5 文章 编 号 :0 1 39 (0 10 — 2 4 0 10 —9 7 2 1 )4 0 5 - 2
一
第 4期
2 l 年 4月 01
Ma hi r De i n c ne y sg
&
Ma u a t r n f cu e
种 火焰切 割机模 块化 设计 分析 与研 究
面以摆动机构、 同步装置作分析如下。
图 1靠模块摆动机构图 1 . 切割机架 2固定轴 3 管 4油缸 5 . 导 _ _ 模块( )6托架 7 三 . . 托辊 . 拉板 9 . 调整螺栓 l. 0 模块( )1 模块( )1. 二 1 . 一 2 偏转滑动轴承 l. 3 重锤 从切割机摆动机构 结构 , 如图 l 所示。我们可 以看出 : 切割 8 1. 4主枪 1. 5副枪 l. 6手轮 1. 7 切割枪 1. 8接触臂
枪离坯釉轴心线的夹角( ) 1 可通过 副枪上的手轮进行调整。 3 该机 构的主、 副枪通过两组 导向辊 ( 1 托在固定轴 ( ) , 2) 2 上 副枪 (5 1)
通过偏转滑动轴承(2 导在主枪(4 上 , t) 1 ) 并可绕主枪 (4 转动 ; 1)
副枪 (5 上 有一 副辊 (2靠 重 锤 的作 用 压 在 模 块 ( ) 1) 。 1) 2) 一 ( 1上 主枪 上 有 一 主 切 线辊 轮 (3 可 在模 块 ( ) 5 上 滚 动实 现 主枪 2) 三 ()
R10m八机八流小方坯连铸机技术规格书

R10m八机八流小方坯连铸机技术规格书1.1在线机械设备1.1.1 大包回转台数量:1套结构形式:直臂双叉回转台,带称重装置。
主要参数:单臂承重:240t回转半径:4800mm回转速度: 1.0rpm(变频可调)0.5rpm(气动事故驱动)回转范围:360°电机功率:37kW结构及特点描述:1)转台安全销气缸驱动。
2)转台工作回转采用减速机变频电机(电机功率:37kw),专用位置开关控制器控制角度和变速点,事故回转采用气动马达驱动。
3)钢包加盖机构安装在回转台上,每个回转臂各独立一套加盖机构,含钢包包盖,带高温岩棉。
其回转、升降采用电液推杆驱动。
电缆管线采用专用的电气滑环上回转台。
4)大包开浇液压缸分别挂于二转臂下。
5)配备大包称重装置。
6)事故钢包由乙方设计,甲方自供。
1.1.2 钢包长水口机械手数量:1套作用:采用钢流保护浇注时,借助于机械手将长水口安装在钢包滑动水口的下方。
定位:安装在浇铸平台上。
结构及特点描述:1)水平回转:手动。
2)密封形式:氩气。
1.1.3中间罐车数量:2台作用:用于承载中间罐,在浇铸过程中能快速更换中间罐,保证连续浇铸的顺利进行,此外在出现事故时能使中间罐迅速离开结晶器。
定位:安装在浇铸平台上。
结构形式:带升降的高低腿(一条轨道在浇铸平台上,另一条为高架轨道)中间罐车。
其中一台工作;另一台准备及烘烤。
主要参数:承载量:100t升降行程:400mm横移行程:120mm(±60 mm)升降速度: 1.2m/min行走速度:2~20m/min(变频传动)行走驱动功率:7.5×2kW(初步设计确定)结构及特点描述:1)升降型式为同步油马达结构,欧洲品牌的精密同步油马达输出油液进入布置于中包四角的油缸,保证四缸升降平稳,同步精度为:1%。
2)中间罐横移采用液压缸驱动。
3)变频传动,使走行平稳,对中准确。
4)用拖链将电缆及液压管线引上车体。
5)与中间罐之间的操作防护挡板为摆动形式(气缸驱动,手动操作。
连续铸钢基本概念

连续铸钢基本概念(1)发表日期:2007-5-19 阅读次数:7051.什么是钢水的浇注作业?钢的生产过程主要分为炼钢和浇注两大环节。
浇注作业就是将成分合格的钢水铸成适合于轧钢和锻压加工所需要的一定形状的固体。
把钢水凝固铸成固体有两种工艺方法:一种是钢锭模浇注法,一种是连续铸钢法。
后者可以将炼钢炉炼好的钢水直接浇注成板坯、扁坯、方坯和圆坯等钢坯,再将钢坯供给各种轧钢机,生产各种规格的钢材。
浇注作业是衔接炼钢和轧钢之间的一项特殊作业。
它的特殊性表现为把钢水转变为固体的凝固过程。
当钢水一旦凝固成固体后,在以后的轧钢过程中就不能对质量有本质上的改进了。
因此,浇注作业对产品质量和成本有重大影响,必须予以特别重视。
要精心操作,不出废品,保证质量。
否则将“前功尽弃”。
2.什么叫连续铸钢?连续铸钢与普通模铸不同,它不是将高温钢水浇注到一个个的钢锭模内,而是将高温钢水连续不断地浇到一个或几个用强制水冷带有“活底”(叫引锭头)的铜模内(叫结晶器),钢水很快与“活底”凝结在一起,待钢水凝固成一定厚度的坯壳后,就从铜模的下端拉出“活底”,这样已凝固成一定厚度的铸坯就会连续地从水冷结晶器内被拉出来,在二次冷却区继续喷水冷却。
带有液芯的铸坯,一边走一边凝固,直到完全凝固。
待铸坯完全凝固后,用氧气切割机或剪切机把铸坯切成一定尺寸的钢坯。
这种把高温钢水直接浇注成钢坯的新工艺,就叫连续铸钢。
它的出现从根本上改变了一个世纪以来占统治地位的钢锭一初轧工艺。
3.连续铸钢有哪些优越性?—简化了生产钢坯的工艺流程,节省大量投资。
省去了模铸工艺中脱模、整模,以及均热和初轧开坯等中间工序。
基建投资和操作费用可节省40%,占地面积减少50%,设备费用减少70%,耐火材料消耗减少15%。
—提高了金属收得率和成材率。
连铸从根本上消除了模铸中注管和汤道的残钢损失,提高了钢水的收得率。
同时省去了钢锭的保温帽,不需要切除钢坯的头部,成材率可提高10~15%。
方坯连铸机工艺技术操作规程

一、连铸机主要参数:二、连铸机工艺流程图转炉出钢→钢包回转台→中间罐→结晶器→二次冷却→拉矫机→火焰切割机→输送辊道→翻钢机、移坯机→出坯三、中间包的准备与烘烤1、定径水口技术要求:定径水口技术参数控制表2、中间包的检查:必须认真检查中间包水口座砖,发现座砖有问题,应及时更换。
绝热板包应认真检查中间包绝热板和绝热板之间的泥料,发现问题,及时处理;然后方可安装定径水口。
干式料中包应认真检查中包快换机构工作是否正常,是否存在滑块打不到位,滑块打不正等情况。
3、中间包的烘烤:3.1、绝热板包的烘烤:3.1.1、使用绝热板中间包,中包烘烤前必须清扫干净。
正常生产准备条件下,中间包在线烘烤时间为1-2小时,按以下步骤烘烤:小火烘烤不小于20分钟,中火烘烤不小于20分钟,大火烘烤不小于20分钟,大火烘烤时据煤气压力可考虑开风机。
3.1.2、非正常生产准备条件下,中间包在线烘烤时间不得低于40分钟,中火烘烤20分钟,大火烘烤20分钟。
3.1.3、定径水口安装后,应比内衬提前1小时以上进行烘烤,烘烤时间最长不得超过3小时。
3.2方坯干式料包的烘烤:3.2.1、使用干式料中间包,中包烘烤前必须清扫干净,包盖损坏要及时更换。
正常生产准备条件下,中间包烘烤时间2.5-3.5小时,按以下步骤烘烤:小火烘烤不小于50分钟,中火烘烤不小于50分钟,大火烘烤不小于50分钟,确保烘烤温度大于900℃,中包为红热状态。
3.2.2、非正常生产准备条件下,中间包在线烘烤时间不得低于2小时,中火烘烤60分钟,大火烘烤60分钟。
四、基本工艺参数控制:1、连铸钢水准备:1.1、常炼钢种:Q195-Q235、HRB400E等,其成分应符合相应的国家标准规定,并保证有良好的流动性,要求Mn/S必须大于15,Mn/Si不小于2.5。
1.2、钢水必须脱氧良好,钢中酸溶铝≤0.006%。
1.3、钢水必须进行吹N2处理,吹N2时间普碳钢不低于2分钟、低合金钢不低于3分钟,品种钢执行品种钢操作要点,氮气压力和流量以能达到钢包液渣面翻动而不裸露钢水为准。
方坯连铸机工艺技术操作规程
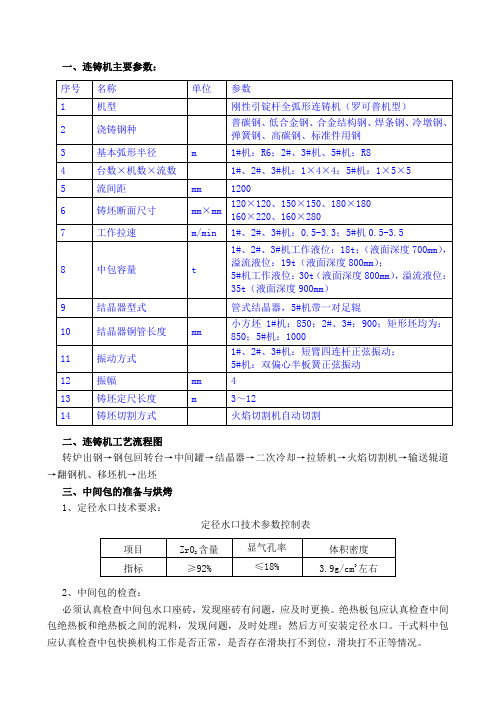
一、连铸机主要参数:二、连铸机工艺流程图转炉出钢→钢包回转台→中间罐→结晶器→二次冷却→拉矫机→火焰切割机→输送辊道→翻钢机、移坯机→出坯三、中间包的准备与烘烤1、定径水口技术要求:定径水口技术参数控制表2、中间包的检查:必须认真检查中间包水口座砖,发现座砖有问题,应及时更换。
绝热板包应认真检查中间包绝热板和绝热板之间的泥料,发现问题,及时处理;然后方可安装定径水口。
干式料中包应认真检查中包快换机构工作是否正常,是否存在滑块打不到位,滑块打不正等情况。
3、中间包的烘烤:3.1、绝热板包的烘烤:3.1.1、使用绝热板中间包,中包烘烤前必须清扫干净。
正常生产准备条件下,中间包在线烘烤时间为1-2小时,按以下步骤烘烤:小火烘烤不小于20分钟,中火烘烤不小于20分钟,大火烘烤不小于20分钟,大火烘烤时据煤气压力可考虑开风机。
3.1.2、非正常生产准备条件下,中间包在线烘烤时间不得低于40分钟,中火烘烤20分钟,大火烘烤20分钟。
3.1.3、定径水口安装后,应比内衬提前1小时以上进行烘烤,烘烤时间最长不得超过3小时。
3.2方坯干式料包的烘烤:3.2.1、使用干式料中间包,中包烘烤前必须清扫干净,包盖损坏要及时更换。
正常生产准备条件下,中间包烘烤时间2.5-3.5小时,按以下步骤烘烤:小火烘烤不小于50分钟,中火烘烤不小于50分钟,大火烘烤不小于50分钟,确保烘烤温度大于900℃,中包为红热状态。
3.2.2、非正常生产准备条件下,中间包在线烘烤时间不得低于2小时,中火烘烤60分钟,大火烘烤60分钟。
四、基本工艺参数控制:1、连铸钢水准备:1.1、常炼钢种:Q195-Q235、HRB400E等,其成分应符合相应的国家标准规定,并保证有良好的流动性,要求Mn/S必须大于15,Mn/Si不小于2.5。
1.2、钢水必须脱氧良好,钢中酸溶铝≤0.006%。
1.3、钢水必须进行吹N2处理,吹N2时间普碳钢不低于2分钟、低合金钢不低于3分钟,品种钢执行品种钢操作要点,氮气压力和流量以能达到钢包液渣面翻动而不裸露钢水为准。
连铸机钢坯火焰切割系统节能技术改造
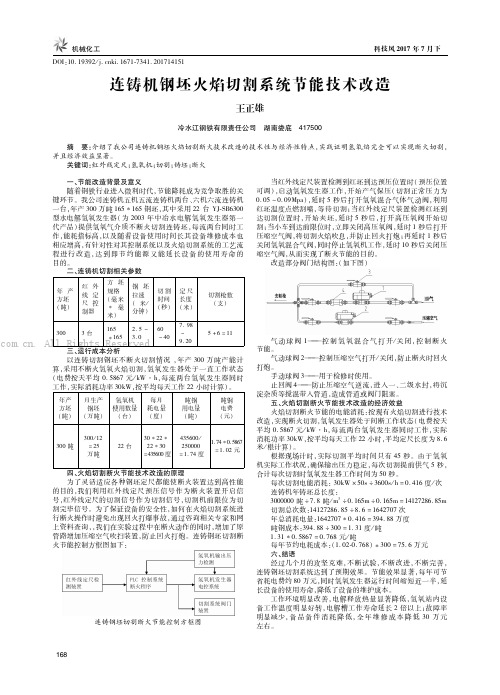
一节能改造背景及意义 随着钢铁行业进入微利时代"节能降耗成为竞争取胜的关 键环节% 我公司连铸机五机五流连铸机两台$六机六流连铸机 一台"年产 (%% 万吨 $05"$05 钢坯"其中采用 )) 台 kG2I<0(%% 型水电解氢氧发生器+ 为 )%%( 年中冶水电解氢氧发生器第一 代产品# 提供氢氧气介质不断火切 割 连 铸 坯"每 流 两 台 同 时 工 作"能耗指标高"以及随着设备使用时间长其设备维修成本也 相应增高"有针对性对其控制系统以及火焰切割系统的工艺流 程进行改造" 达到即节约能源又能延长设备的使用寿 命 的 目的% 二连铸机切割相关参数
改造部分阀门结构图!+ 如下图#
气动 球 阀 $...控 制 氢 氧 混 合 气 打 开 *关 闭" 控 制 断 火 节能%
气动球阀 )...控制压缩空气打开 *关闭"防止断火时回火 打炮%
手动球阀 (...用于检修时使用% 止回阀 3...防止压缩空气逆流"进入一$二级水封"将沉 淀杂质等搅混带入管道"造成管道或阀门阻塞% 五火焰切割断火节能技术改造的经济效益 火焰切割断火节能的电能消耗!按现有火焰切割进行技术 改造"实现断火切割"氢氧发生器处于间断工作状态+ 电费按天 平均 %&5901 元 *.J,X"每流两台氢氧发生器同时工作"实际 消耗功率 (%.J"按平均每天工作 )) 小时"平均定尺长度为 9&0 米 *根计算# % 根据现场计时"实际切割平均时间只有 35 秒% 由于氢氧 机实际工作状况"确保输出压力稳定"每次切割提前供气 5 秒" 合计每次切割时氢氧发生器工作时间为 5% 秒% 每次切割电能消耗! (%.J 85%7t(0%%7*X B%&3$0 度 *次 连铸机年铸坯总长度! (%%%%%% 吨 t1&9 吨 *:( t%&$05:t%&$05:B$3$)1)90&95: 切割总次数!$3$)1)90&95 t9&0 B$03)1%1 次 年总消耗电量!$03)1%1"%&3$0 B('3&99 万度 吨钢成本!('3&99 t(%% B$&($ 度 *吨 $&($"%&5901 B%&109 元 *吨 每年节约电耗成本!+$&%)2%&109# "(%% B15&0 万元 六结语 经过几个月的攻坚克难"不断试验"不断改进"不断完善" 连铸钢坯切割系统达到了预期效果% 节能效果显著"每年可节 省耗电费约 9% 万元"同时氢氧发生器运行时间缩短近一半"延 长设备的使用寿命"降低了设备的维护成本% 工作环境明显改善"电解释放热量显著降低"氢氧站内设 备工作温度明显好转"电解槽工作寿命延长 ) 倍以上&故障率 明显减少" 备 品 备 件 消 耗 降 低" 全 年 维 修 成 本 降 低 (% 万 元 左右%
连铸设备主要技术参数
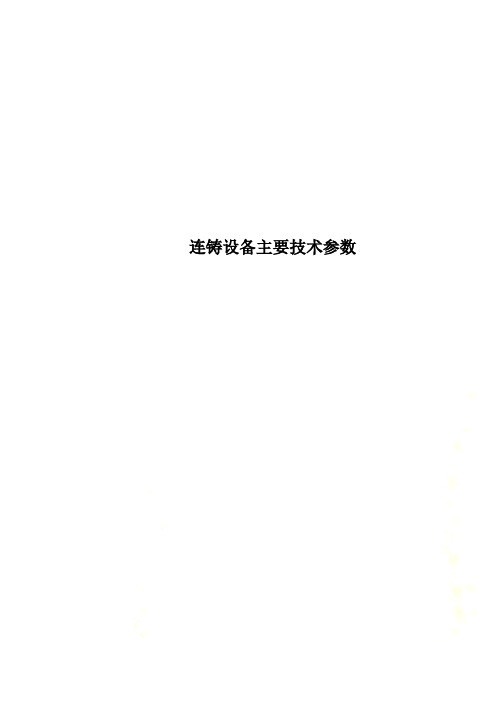
连铸设备主要技术参数2010连铸设备及岗位职能love2010-1-51.设备主要技术参数1.1.设备主要技术参数:连铸机型式弧形小方坯连铸机弧形半径 R=6000mm流数三机三流流间距 1200mm铸坯断面 120×120mm 150×150mm Φ110-Φ160mm铸坯定尺长度 3.7-12米钢水罐支撑方式钢包回转台中间罐车台数 2台中间罐型式、容量电动缸自动控制塞棒开闭式,容量12t结晶器结构形式铜管水套组合式铸坯导向装置上段为活动段下段为固定段拉矫机拉速范围 0.6-6.0m/min铸坯切断方式火焰切割机出坯方式轨道,双层翻转冷床,翻缸机,移缸机和推钢机轨道速度 32m/min移钢能力 3.2t钢结构平台上层平台面标高 +6.700m(轨道面标高+0.60m)上层平台面长宽 23800×13100mm下层平台面标高 +4.05mm连铸机长度(基准线至固定挡板面) 39680mm1.2 主要设备技术性能1.2.1钢包回转台承载能力 2×80t(钢水重40t,钢包重40t)回转半径 3500mm旋转速度正常1r/min,启、制动0.1r/min旋转角度±180°;故障时±360°旋转用电机 YZR160MB-6 AC 8.5KW 930r/min 单轴伸 IM1001 380V H级绝缘 IP54事故旋转速度 0.5rpm事故旋转角度 180°事故旋转油马达斜轴式轴向柱塞马达A2F63W2P1 P=10-13MPa471r/min N=5.2-6.8KW放钢包时冲击系数 2干油润滑系统:1.2.1.1齿轮润滑系统多点干油泵 ZB-2型 N=18KW工作压力 31.5MPa贮油容积 30L给油量 3.2立方厘米/minDC24V喷射嘴 GPZ-135型(JB/ZQ4538-86)空气压力 0.45-0.6MPa喷射直径 135mm喷嘴与润滑表面距离 200mm气动三联件 398.263二位二通电磁阀 DF-10 DC24V润滑介质连铸机专用脂空气工作压力 0.45-0.6MPa1.2.1.2 轴承圈润滑系统电动干油泵 DRB4-M120Z换向阀 24EJF-M(JB/ZQ4584-86)压差开关 YCK-M5 (JB/ZQ4585-86)双线分配器 4SSP2-M1.5(JB/ZQ4583-86)2SSP2-M1.5(JB/ZQ4583-86)润滑介质连铸机专用脂1.2.2中间罐车结构型式框型结构的车架,单侧链轮驱动载重量 15.5t轨距 1700mm轮架 3800mm最大轮压 80KN减速器 BWD2.2-3-29摆线针轮行星减速器车轮直径Φ350mm走行速度 9.52m/min走行方向微调手动操作中间罐横向微调行程±30mm车体运行距离±8000mm供电方式电缆卷筒操作方式固定操作箱1.2.3中间罐烘烤站结构型式烧嘴可垂直旋转升降80°烧嘴型式鼓风助燃的天然气火焰燃烧嘴烘烤温度 -25~1100℃烘烤时间 45~60min烧嘴数量 2个/台天然气压 0.2MPa空气压力 0.4MPa风机型号(2#机配置) GY8-12-1 NO.6 右旋1.2.4 结晶器结构型式弧形铜管水套组合式外弧半径 6000mm断面尺寸 120×120mm 150×150mm Φ110-Φ160mm铜管长度方坯750mm,圆坯 800mm冷却水量 95立方米/小时水压 0.6MPa-0.8Mpa足辊水方坯角喷 120(4×4) 150(8×4);圆坯Φ110-Φ160mm(6×3),Φ160-Φ180(8×3)喷嘴型号 3/8〞PZ2265QZ11.2.5结晶器振动装置结构型式四连杆短臂振动弧形半径 R6000mm振动方式正弦曲线振幅±3~±6mm(实际±5)频率 0~300Hz(可调)1.2.6二冷装置活动段结构型式弧形导架体气缸摆动驱动用气缸 S型尾部悬挂式气缸Φ160×750mm气缸工作压力 0.4-0.6MPa1.2.7.二冷装置固定1段结构型式带导向夹辊托辊固定式水冷弧形导向架夹辊Φ160×180mm夹辊最大辊面间距 200mm1.2.8二冷装置固定Ⅱ段同固定Ⅰ段1.2.9拉矫机1.2.9.1拉矫机2#连铸机铸坯断面mm 120×120mm 150×150mm Φ110-Φ160mm 拉坯速度m/min 0.3-5m/min开口度mm 85-237拉矫辊直径×宽Φ350×250mm 个数 5驱动辊两个上辊驱动减速器型号F1212.1(上海新中专利)总速比430.25液压缸型号UY-TF/MI(JB/ZQ4181-97)规格Φ140/Φ100-320,Φ140/Φ100-520 工作压力0-10MPa1.2.9.2辅助拉矫机2#连铸机铸坯断面mm 120×120mm 150×150mm Φ110-Φ160mm拉坯速度m/min 0.3-5m/min开口度mm 85-237拉矫辊直径×宽Φ350×250mm 个数 5驱动辊上辊单辊驱动减速器型号F1212.1(上海新中专利)总速比430.25液压缸型号UY-TF/MI( JB/ZQ4181-97)规格Φ140/Φ100-320工作压力0-10MPa1.2.10 蒸汽排出装置2#连铸机配风机 Y4-73N010D-4 左风量 44004立方米/min1.2.11 引锭杆承放装置结构型式气缸驱动,四连杆摆动摆动距离(升高×距离) 80×260mm托架个数/流 8每流驱动气缸数 2气缸型号 2#连铸机:SΦ200×250mm空气压力 0.4-0.6MPa1.2.12 引锭杆结构型式箱型对扣式半板簧引锭杆总长 111000mm节距 400mm插入结晶器长度 150mm引锭杆断面 145×143mm(150坯)115×113mm(120坯)Φ105(Φ110坯)Φ115(Φ120坯)Φ125(Φ130坯)Φ135(Φ140坯)Φ145(Φ150坯)Φ155(Φ160坯)1.2.13轨道1.2.13.1主要参数2#机结构型式辊子双轴承支座,分组集中链条传动(辊径×辊身长)输出辊道Φ165×180 冷床区Φ220×200辊道运行速度32m/min冷床区32.17m/min减速机行星摆线针轮减速器BWD18-23-2.2 i=23冷床区辊道:XWD4-29-2.2i=29链条16A-1(GB1243.1-83)1.2.13.2辊道分组(每流)输出辊道分组编号辊道名称每组辊子数辊子编号辊距mm备注Ⅰ切前辊道 4 1~4 820 水冷Ⅱ切后辊道 6 8~12 900Ⅲ输出辊道(一)6 13~18 900Ⅳ输出辊道(二)4 19~22 900Ⅴ输出辊道(三)5 23~27 9002#机冷床区辊道Ⅰ 3 28~30 900 30~31辊距1200 Ⅱ 4 31~34120Ⅲ 3 35~371201.2.14 双层翻转冷床(2#机)铸坯定尺 2600mm-12000mm铸坯截面 20×120mm 150×150mm Φ110-Φ160mm铸坯翻转角度 90°液压缸(2个) Y-HGI-E100×380LEI-HL10T2系统最大压力 14MPa1.2.15横向移钢机横移铸坯重量 3200Kg横移速度 23m/min横移行程 6200mm减速器 ZS82.5-1-Ⅲ型 i=51.22制动器 YWZ300/25型配YT1-25 ZC/4电力液压推动器额定推力 250N额定行程 40mm制动瓦退距 0.7mm制动力矩 320Nm1.2.16 推钢机和冷床冷床尺寸长12005mm 宽 11350mm存放铸坯最大重量 42t推钢机行程 1000mm液压缸(2个) SDG-160/110-e型行程650mm系统最大压力 14MPa1.2.17 中间包倾翻装置(2#机)倾翻速度 1.785rpm倾翻方向逆时针方向倾翻角度±180°行星减速器 NGW123-11 i=56输入1000r/min时允许输入功率7.5kw制动器 YT1-25电动液压推动器1.2.18 拉矫机干油润滑站(2#连铸机)干油润滑泵(江苏启东润滑设备有限公司)型号 HA-Ⅲ1X公称压力 40MPa额定给油量 430ml/min电机功率 1.5kw贮油筒容积 60升电动加油泵(江苏启东润滑设备有限公司)型号 DJB-V70/860公称压力 3.15MPa额定给油量 70L/H电机功率 0.37kw贮油筒容积 200升润滑介质连铸机专用脂1.2.19 二冷活动段,气动阀门站分水滤气器 QSL-25 1MPa空气减压阀 QTY-25 1MPa压力表 Y-60ZT 0-1.6MPa油雾器 QIU-25 1MPa电控电器滑阀 K25D2-15-L1 直流24v消音器 XS-L15-L11.2.20二冷固定段气动阀门站压力 0.2~0.6MPa流量 0.13~0.15立方米/min减压阀 QTY-25 G1〞 1Mpa节流阀 L41H-25电控电气滑阀 k25D2-15-L1 DC24及以下项目1.2.20.1快速调压阀1/2〞 AR4000-04 烟台未来气动组件设备有限公司技术参数:进口压力 0.7~1.0MPa压力调节范围 0.05~0.6MPa输入压力波动 0.2MPa时输入压力波动<0.02MPa压力变换时间 2~5秒1.2.20.2旋塞阀X13W-10 G1/2〞1.2.20.3压力表Y-100ZT 0~1.6MPa1.2.21火焰切割机型号:FGR3 方圆坯火焰切割车上海新中切割钢种:普碳钢、优质钢、低合金钢切割铸坯断面尺寸: 100×100 120×120 180×180 220×220 240×240 Φ100-Φ200mm铸坯最大拉速: 3.5m/min切割速度:300-450mm/min能源介质:乙炔、天然气、液化石油气、丙烷、丙烯、焦炉煤气等。
方坯连铸机热调试手册

小方坯连铸机热调试手册一. 主要操作参数:1.1 机型:弧形渐进矫直型连铸机1.2 铸坯主半径: R90001.3 流数: 6流1.4 流间距: 1200mm1.5 转炉:容量: 60T 平均出钢量 70 吨,最大80吨平均冶炼时间: 32min/炉1.6连铸机浇铸断面: 150×150; 171Kg/m1.7 定尺:2.8~9m1.8 浇注方式:保护浇铸/定经水口1.9连铸机拉坯速度150×150mm 2.4~2.9m/min2.0 浇铸主要钢种及代表钢号:低合金钢、碳结钢、合结钢(预留冷墩钢、钢丝绳钢)2.1 计算作业率: 80%2.2 连铸机产量:(按150×150计算)6流浇铸能力:Q=0.171t/m×2.5m/min×6流=2.565t/min工作时间: 7008H/Y(全年365天,80%作业率计)辅助时间: 587H/Y(连浇10炉,准备时间32分钟,35分钟/炉计)纯工作时间: 6421H/Y钢水收得率;96%6流年产量: ~95万吨YS=6421H/Y×2.565t/min×60min×96%=948655t二. 热调试参数2.1 转炉钢水条件:买方提供浇铸的钢水,应满足以下条件:2.1.1 钢水温度:T中=T L+30 ±10℃T大包= T中+70 ±10℃第一炉允许提高10℃T L :液相线温度T中:中间包温度T大包:连铸平台大包温度(视大包散温及等待时间作适当调整) 2.1.2 有害元素限制:P≤0.045% S ≤ 0.045%Cu≤ 0.350% Sn ≤ 0.065%As≤ 0.065%2.1.3 含AI量:采用定径水口浇铸时:C AL≤ 0.2% 0.007%>0.2% 0.004%如生产细粒钢时,可将铝丝喂入中间包至结晶器之间的钢流中, AL含量可提高至0.025%.2.1.4 锰硫比:不小于12比12.1.5 含氧量及含氮量:中间包中含氧量 120P.P.M.含氮量 80P.P.M2.2 中间罐2.2.1 中间罐水口孔径定经水口孔径对以下断面的铸坯, 推荐的定经水口孔径如下:水口直径选定后,通过改变中间罐钢水面高度,可在小范围内调速,但最低液面不能低于200mm,否则可能造成卷渣及漏钢。
连铸的切割辊道等附属设备

连铸的切割辊道等附属设备切割机A)作用将被连续拉出的铸坯按定尺要求切断的连铸设备。
即根据成品规格及后步工序的要求,在连铸坯完全凝固后,进行在线定尺或倍尺切割。
B)类型连铸机的切割设备有火焰切割机和机械剪切(剪切机)两大类。
⑴火焰切割机①工作原理火焰切割机使用预热氧和燃气混合燃烧的火焰使切割缝处的金属熔化,并利用高压切割氧的能量把熔化的金属吹掉,形成切缝,切断铸坯。
燃料有高压精制焦炉煤气、天然气、丙烷和乙炔等。
②特点火焰切割机设备简单,质量轻,投资省,设备也易于维护;不受铸坯断面尺寸和温度的限制(冷坯也可切割),切口平整不变形;但切缝金属损失较多(切割时有一定量的金属损耗)③应用目前绝大多数连铸机采用火焰切割。
小断面连铸坯只用一支切割枪切割,大断面连铸坯需用双枪从铸坯两侧同时进行切割。
火焰切割机广泛用于板坯、方坯、圆坯和异型坯的定尺切割和头、尾切割等。
同步机构是使切割车与铸坯在无相对运动的条件下完成切割的机构。
常用的有夹钳式、背负式和坐骑式等几种方式。
夹钳式靠气缸使两侧夹臂的夹头夹住铸坯。
背负式靠自重或气缸的推力使夹紧臂直接压在铸坯上达到与铸坯同步的目的,适用于宽板坯和宽度变化大的板坯连铸机上。
坐骑式为切割枪小车直接骑在板坯上,这种方式已很少采用了割枪小车是用于支承切割枪并使之运动的装置。
割枪运动方式有直线式和摆动式两种,安装在切割车上。
割枪小车的速度可灵活调速,有起切、正常切割、高速返回和高速接近等不同的速度。
切割枪对铸坯进行切割。
它由枪体和割嘴组成。
割嘴的种类主要有内混式、外混式和内预混式。
以内预混式为最好,加热效率高,焰心长,有利于优质快速切割。
还有一种带喷粉的割嘴,用于高合金钢和不锈钢铸坯的切割。
气水分配系统包括氧气、燃气、压缩空气和冷却水的各种阀门、管线以及测量仪表等。
切割设备的电控系统一般采用PLC控制。
⑵机械剪切(剪切机)A)分类①按驱动方式有电动和液压(机械剪和液压剪)两种;②按其与铸坯同步运动方式分摆动式和平移式;③按剪切运动方式分上切式和下切式。
连铸坯火焰切割原理

连铸坯火焰切割原理连铸坯火焰切割机是利用燃气和氧气将铸坯快速燃烧,达到切断铸坯的目的的。
燃气在燃烧的时候,需要一定的氧气,这些氧气主要是起到助燃作用,同时氧气供给量的多少还直接影响火焰的性质。
燃气燃烧就是其中的可燃成份碳,氢,硫以及其他碳氢化合物与氧气化合生成CO2,H2O,SO2等的反应。
按照这些完全燃烧的反应方程式计算出来所需氧气量称为理论氧气量。
在实际燃气中,为了保证燃气的完全燃烧,供给的氧气量应该比理论氧气量多一些,多出的这部分氧气称为过剩氧气。
实际氧气供给量与理论氧气需要量之比,称为氧气过剩系数,用式子表示为:a=实际氧气供给量/理论氧气需要量。
根据a值的大小可以判断火焰的性质a>1,氧化焰;是指燃气中全部可燃成分在氧气充足的情况下达到完全燃烧,燃气产物中没有游离C及CO ,H2,CH4等可燃成份的一种无烟火焰;氧化焰的温度可达3100℃~3400℃,此时的火焰呈清彻的蓝色,没有黑烟。
a=1,中性焰;是指燃气中全部可燃成分与氧气化合量几乎相等,处于平衡状态,,最后使燃气达到完全燃烧的一种无烟火焰;但控制中性焰非常困难,实际生产实践中是难以做到,通常用弱碳化焰代替它,此时的火焰基本呈蓝色,没有黑烟;“中性焰”的温度可达1500℃~3000℃。
a<1,碳化焰;碳化焰是指在燃烧过程中,氧气供应不足,燃烧不充分,在燃烧产物中有一氧化碳等还原性气体,没有或者极少游离氧的存在的火焰;火焰呈黄色,温度低,有黑烟,此时的燃烧为不完全的燃烧,会造成燃气的浪费。
连铸坯需要中性焰进行预热,在切割时只需要氧化焰,被喷的地方剧烈氧化成为熔渣并被吹走,断面平整,切割速度快而且不会像水力切割那样产生激冷导致裂纹,只是对钢坯的合金成分有一定要求,钨钼铬等不能太多,下面是原理与应用条件:燃气是产生火焰的必需品,它可以决定火焰的最高温度,同时也决定了氧气的消耗量。
所以,氧气切割简称气割,也称氧——火焰切割。
氧气切割原理和过程:钢材的氧气切割是利用气体火焰(称预热火焰)将钢材表层加热到燃点,并形成活化状态,然后送进高纯度、高流速的切割氧,使钢中的铁在氧氛围中燃烧生成氧化铁熔渣同时放出大量的热,借助这些燃烧热和熔渣不断加热钢材的下层和切口前缘使之也达到燃点,直至工件的底部。
方坯连铸技术操作规程
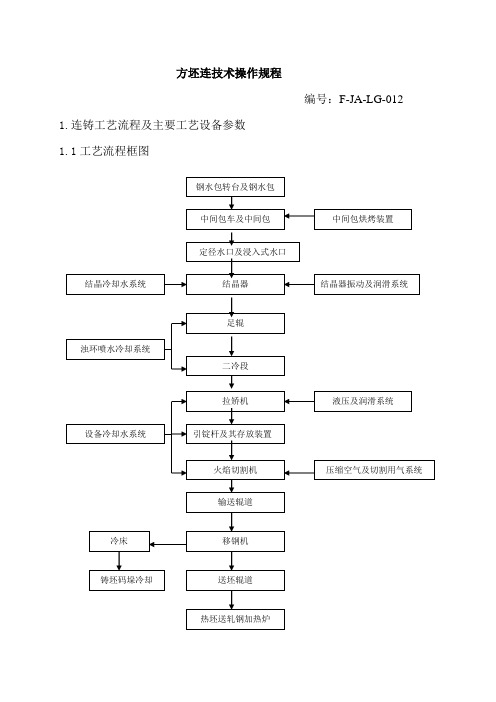
方坯连技术操作规程编号:F-JA-LG-012 1.连铸工艺流程及主要工艺设备参数1.1工艺流程框图1.2连铸机主要工艺参数1.2.1连铸机机型:四机四流弧型连铸机铸机半径:R=6m铸机流数:四机四流注流间距:1200mm冶金长度:Ly=9.4m,浇注断面: 165×280 165×330定尺长度:3.5~6.0m1.2.2大包台型式:轨道式承载重量120吨驱动形式:两边电机传动1.2.3中间包车及中间包中间包车型式:高低腿式最大承载重量:50t走行速度:0-20m/min横向微调:±40mm中间包容量:15吨工作液面深度:>500mm水口间距:1200mm快换水口:上水口直径20mm 下水口直径19-16mm 浸入式水口:560*75mm 内径26mm.1.2.4结晶器型式:全弧型、外弧半径R=6m铜管长度:900mm 锥度:0.5~0.8%足辊:2层、165×280、165*330水缝宽度:4mm1.2.5结晶器振动装置型式:半板簧短连杆,正弦式振动振频:35-333次/min振幅:±3,±4mm1.2.6拉矫机型式:采用五辊式单点矫直,上下拉坯辊开口度大小及上拉矫辊上下移动和脱坯辊动作均由液压系统来实现。
电机通过长轴和减速机传动远离热源,机架及辊子内部通水冷却。
1.2.7 引锭杆及存放装置引锭杆由引锭头、杆身、连接件组成。
形式:刚性引锭杆,外弧直径为6m。
送引锭杆速度:1.2m/min1.2.8火焰切割机型式:无动力式,夹紧机构及切割装置返回驱动均为气动。
切割速度:~300mm/min,随拉坯速度同步调节。
切割断面: 165×280mm 165×330 mm切割行程:1300mm.能源介质:液化炳烷管道压力>0.04MPa氧气管压力:1.0~1.2Mpa压缩空气压力:0.4~0.6Mpa1.2.9移钢机单电机驱动,双长轴输出,两侧运行轨道与齿条并行。
连铸设备主要技术参数

2010连铸设备及岗位职能love2010-1-51.设备主要技术参数1.1.设备主要技术参数:连铸机型式弧形小方坯连铸机弧形半径 R=6000mm流数三机三流流间距 1200mm铸坯断面 120×120mm 150×150mm Φ110-Φ160mm铸坯定尺长度 3.7-12米钢水罐支撑方式钢包回转台中间罐车台数 2台中间罐型式、容量电动缸自动控制塞棒开闭式,容量12t结晶器结构形式铜管水套组合式铸坯导向装置上段为活动段下段为固定段拉矫机拉速范围 0.6-6.0m/min铸坯切断方式火焰切割机出坯方式轨道,双层翻转冷床,翻缸机,移缸机和推钢机轨道速度 32m/min移钢能力 3.2t钢结构平台上层平台面标高 +6.700m(轨道面标高+0.60m)上层平台面长宽 23800×13100mm下层平台面标高 +4.05mm连铸机长度(基准线至固定挡板面) 39680mm1.2 主要设备技术性能1.2.1钢包回转台承载能力 2×80t(钢水重40t,钢包重40t)回转半径 3500mm旋转速度正常1r/min,启、制动0.1r/min旋转角度±180°;故障时±360°旋转用电机 YZR160MB-6 AC 8.5KW 930r/min 单轴伸 IM1001 380V H级绝缘 IP54事故旋转速度 0.5rpm事故旋转角度 180°事故旋转油马达斜轴式轴向柱塞马达A2F63W2P1 P=10-13MPa471r/min N=5.2-6.8KW放钢包时冲击系数 2干油润滑系统:1.2.1.1齿轮润滑系统多点干油泵 ZB-2型 N=18KW工作压力 31.5MPa贮油容积 30L给油量 3.2立方厘米/minDC24V喷射嘴 GPZ-135型(JB/ZQ4538-86)空气压力 0.45-0.6MPa喷射直径 135mm喷嘴与润滑表面距离 200mm气动三联件 398.263二位二通电磁阀 DF-10 DC24V润滑介质连铸机专用脂空气工作压力 0.45-0.6MPa1.2.1.2 轴承圈润滑系统电动干油泵 DRB4-M120Z换向阀 24EJF-M(JB/ZQ4584-86)压差开关 YCK-M5 (JB/ZQ4585-86)双线分配器 4SSP2-M1.5(JB/ZQ4583-86)2SSP2-M1.5(JB/ZQ4583-86)润滑介质连铸机专用脂1.2.2中间罐车结构型式框型结构的车架,单侧链轮驱动载重量 15.5t轨距 1700mm轮架 3800mm最大轮压 80KN减速器 BWD2.2-3-29摆线针轮行星减速器车轮直径Φ350mm走行速度 9.52m/min走行方向微调手动操作中间罐横向微调行程±30mm车体运行距离±8000mm供电方式电缆卷筒操作方式固定操作箱1.2.3中间罐烘烤站结构型式烧嘴可垂直旋转升降80°烧嘴型式鼓风助燃的天然气火焰燃烧嘴烘烤温度 -25~1100℃烘烤时间 45~60min烧嘴数量 2个/台天然气压 0.2MPa空气压力 0.4MPa风机型号(2#机配置) GY8-12-1 NO.6 右旋1.2.4 结晶器结构型式弧形铜管水套组合式外弧半径 6000mm断面尺寸 120×120mm 150×150mm Φ110-Φ160mm铜管长度方坯750mm,圆坯 800mm冷却水量 95立方米/小时水压 0.6MPa-0.8Mpa足辊水方坯角喷 120(4×4) 150(8×4);圆坯Φ110-Φ160mm(6×3),Φ160-Φ180(8×3)喷嘴型号 3/8〞PZ2265QZ11.2.5结晶器振动装置结构型式四连杆短臂振动弧形半径 R6000mm振动方式正弦曲线振幅±3~±6mm(实际±5)频率 0~300Hz(可调)1.2.6二冷装置活动段结构型式弧形导架体气缸摆动驱动用气缸 S型尾部悬挂式气缸Φ160×750mm气缸工作压力 0.4-0.6MPa1.2.7.二冷装置固定1段结构型式带导向夹辊托辊固定式水冷弧形导向架夹辊Φ160×180mm夹辊最大辊面间距 200mm1.2.8二冷装置固定Ⅱ段同固定Ⅰ段1.2.9拉矫机1.2.9.1拉矫机2#连铸机铸坯断面mm120×120mm 150×150mm Φ110-Φ160mm 拉坯速度m/min0.3-5m/min开口度mm85-237拉矫辊直径×宽Φ350×250mm 个数5驱动辊两个上辊驱动减速器型号F1212.1(上海新中专利)总速比430.25液压缸型号UY-TF/MI(JB/ZQ4181-97)规格Φ140/Φ100-320,Φ140/Φ100-520工作压力0-10MPa1.2.9.2辅助拉矫机2#连铸机铸坯断面mm120×120mm 150×150mm Φ110-Φ160mm拉坯速度m/min0.3-5m/min开口度mm85-237拉矫辊直径×宽Φ350×250mm 个数5驱动辊上辊单辊驱动减速器型号F1212.1(上海新中专利)总速比430.25液压缸型号UY-TF/MI( JB/ZQ4181-97)规格Φ140/Φ100-320工作压力0-10MPa1.2.10 蒸汽排出装置2#连铸机配风机 Y4-73N010D-4 左风量 44004立方米/min1.2.11 引锭杆承放装置结构型式气缸驱动,四连杆摆动摆动距离(升高×距离) 80×260mm托架个数/流 8每流驱动气缸数 2气缸型号 2#连铸机:SΦ200×250mm空气压力 0.4-0.6MPa1.2.12 引锭杆结构型式箱型对扣式半板簧引锭杆总长 111000mm节距 400mm插入结晶器长度 150mm引锭杆断面 145×143mm(150坯)115×113mm(120坯)Φ105(Φ110坯)Φ115(Φ120坯)Φ125(Φ130坯)Φ135(Φ140坯)Φ145(Φ150坯)Φ155(Φ160坯)1.2.13轨道1.2.13.1主要参数2#机结构型式辊子双轴承支座,分组集中链条传动(辊径×辊身长)输出辊道Φ165×180 冷床区Φ220×200辊道运行速度32m/min冷床区32.17m/min减速机行星摆线针轮减速器BWD18-23-2.2 i=23冷床区辊道:XWD4-29-2.2i=29链条16A-1(GB1243.1-83)1.2.13.2辊道分组(每流)输出辊道分组编号辊道名称每组辊子数辊子编号辊距mm备注Ⅰ切前辊道41~4820水冷Ⅱ切后辊道68~12900Ⅲ输出辊道(一)613~18900Ⅳ输出辊道(二)419~22900Ⅴ输出辊道(三)523~279002#机冷床区辊道Ⅰ328~3090030~31辊距1200Ⅱ431~341200Ⅲ335~3712001.2.14 双层翻转冷床(2#机)铸坯定尺 2600mm-12000mm铸坯截面 20×120mm 150×150mm Φ110-Φ160mm铸坯翻转角度 90°液压缸(2个) Y-HGI-E100×380LEI-HL10T2系统最大压力 14MPa1.2.15横向移钢机横移铸坯重量 3200Kg横移速度 23m/min横移行程 6200mm减速器 ZS82.5-1-Ⅲ型 i=51.22制动器 YWZ300/25型配YT1-25 ZC/4电力液压推动器额定推力 250N额定行程 40mm制动瓦退距 0.7mm制动力矩 320Nm1.2.16 推钢机和冷床冷床尺寸长12005mm 宽 11350mm存放铸坯最大重量 42t推钢机行程 1000mm液压缸(2个) SDG-160/110-e型行程650mm系统最大压力 14MPa1.2.17 中间包倾翻装置(2#机)倾翻速度 1.785rpm倾翻方向逆时针方向倾翻角度±180°行星减速器 NGW123-11 i=56输入1000r/min时允许输入功率7.5kw制动器 YT1-25电动液压推动器1.2.18 拉矫机干油润滑站(2#连铸机)干油润滑泵(江苏启东润滑设备有限公司)型号 HA-Ⅲ1X公称压力 40MPa额定给油量 430ml/min电机功率 1.5kw贮油筒容积 60升电动加油泵(江苏启东润滑设备有限公司)型号 DJB-V70/860公称压力 3.15MPa额定给油量 70L/H电机功率 0.37kw贮油筒容积 200升润滑介质连铸机专用脂1.2.19 二冷活动段,气动阀门站分水滤气器 QSL-25 1MPa空气减压阀 QTY-25 1MPa压力表 Y-60ZT 0-1.6MPa油雾器 QIU-25 1MPa电控电器滑阀 K25D2-15-L1 直流24v消音器 XS-L15-L11.2.20二冷固定段气动阀门站压力 0.2~0.6MPa流量 0.13~0.15立方米/min减压阀 QTY-25 G1〞 1Mpa节流阀 L41H-25电控电气滑阀 k25D2-15-L1 DC24及以下项目1.2.20.1快速调压阀1/2〞 AR4000-04 烟台未来气动组件设备有限公司技术参数:进口压力 0.7~1.0MPa压力调节范围 0.05~0.6MPa输入压力波动 0.2MPa时输入压力波动<0.02MPa压力变换时间 2~5秒1.2.20.2旋塞阀X13W-10 G1/2〞1.2.20.3压力表Y-100ZT 0~1.6MPa1.2.21火焰切割机型号:FGR3 方圆坯火焰切割车上海新中切割钢种:普碳钢、优质钢、低合金钢切割铸坯断面尺寸: 100×100 120×120 180×180 220×220 240×240 Φ100-Φ200mm铸坯最大拉速: 3.5m/min切割速度:300-450mm/min能源介质:乙炔、天然气、液化石油气、丙烷、丙烯、焦炉煤气等。
提高连铸机切割系统铸坯收得率的实践

降低冷却速度 。这样 ,可进一步降低轧制工序
成本
参 考文 献
1 王 克杰 . 低碳 钢 盘条氧 化铁 皮 形成机 理及 其控 制研 究. 天津 冶金 ,2 0 1 2 , ( 5 ) :1 ~2
( 2 )不 断试验摸 索合适 的割嘴 ,割嘴尺 寸
由3 . 3 m m到 2 . 7 m m和 2 . 5 mm,最 后 稳 定 在 :
1 . 7 m m ( 方坯连铸机) 、1 . 9 m m ( 板 坯连铸机) 。 制 作 割 缝 检 测 工 具 ,拉 钢 切 割 过 程 测 量 割 缝 , 根 据 不 同钢 种 断 面 及 时 调 整 切 割 的燃 气 、预 热 氧 、切 割 氧 的参 数 ,在 确 保 割 缝 最 小 的 同时 又 能 割 断铸 坯 。对板 坯定 尺 超过 6 . 5 m 的使 用单 枪 切 割保 证 割 口平 直 ,双 枪 切 割 要 求 保 证 枪 的 直
创造 了条件 。
( 上接第 3 3页)和优 化轧制冷却工艺 ,使 W ( Mn ) 降低 0 . 1 %,坯料 吨钢成本 铁 皮越 薄 、结构 越 致 密 , 拉 拔 后 吨钢 氧 化 铁 皮 损 耗 越 低 。柳 钢 光 圆钢 筋 氧化 铁皮 外 层 F e , 0 层 较厚 。为进 一 步 降低 柳 钢
2 改 进
( 1 )将 4 5 t 、1 2 0 t 系统连铸切割机 的燃气 由煤气改为丙烷 ,使用丙烷后 ,切割机 的故 障
大 大 减 少 ,检 修 基 本 上 不 用 吹 扫 管 道 ,割 枪 割
3 结 语
改 进后 ,割缝 从 使 用 煤 气 时 1 0 m m 降 到 了
平均 3 . 5 m m,并保持稳定 。板坯连铸机收得率
- 1、下载文档前请自行甄别文档内容的完整性,平台不提供额外的编辑、内容补充、找答案等附加服务。
- 2、"仅部分预览"的文档,不可在线预览部分如存在完整性等问题,可反馈申请退款(可完整预览的文档不适用该条件!)。
- 3、如文档侵犯您的权益,请联系客服反馈,我们会尽快为您处理(人工客服工作时间:9:00-18:30)。
学生毕业设计(论文)原创性声明本人以信誉声明:所呈交的毕业设计(论文)是在导师的指导下进行的设计(研究)工作及取得的成果,设计(论文)中引用他(她)人的文献、数据、图件、资料均已明确标注出,论文中的结论和结果为本人独立完成,不包含他人成果及为获得重庆科技学院或其它教育机构的学位或证书而使用其材料。
与我一同工作的同志对本设计(研究)所做的任何贡献均已在论文中作了明确的说明并表示了谢意。
毕业设计(论文)作者(签字):年月日摘要火焰切割机是利用各种燃气的燃烧和氧气来切割钢坯,火焰切割机的主要特点是:投资少,切割设备的外形较小,切缝比较平整,并不受铸坯温度和断面大小的限制,特别是大断面的铸坯其优越性明显,但切割时间长,切缝宽,切口处的金属损耗严重,污染严重。
切割机构是火焰切割装置的关键部分。
它主要由切割枪和关键部分组成。
同步机构是指切割小车与连铸坯同步运行的机构。
切割小车与铸坯无相对运动的的条件下切割钢坯。
返回机构是指采用普通小车运行机构。
定尺机构是由气缸推动测量辊,使之顶在铸坯的下面,靠摩擦力使之转动。
利用脉冲器发出脉冲信号。
关键词:火焰切割机切割机构同步机构返回机构定尺机构ABSTRACTFlame cutting machine is using various gas combustion and oxygen to cut billet, the main characteristics of flame cutting machine is: less investment, cutting equipment appearance is lesser, cut compares level, not by the seam billet temperature and section size restrictions, especially large cross-section of the slab of its advantages, but obviously cutting time long, and the wide, incision seam in loss of metal serious, serious pollution.Cutting mechanism is a key part of the flame cutting device. It mainly consists of cutting gun and key parts. Synchronous institutions refer cutting the trolley and continuous casting slab synchronization operation institution. Cutting the trolley and slab no relative motion conditions cutting billet.Return to institutions refer USES ordinary car operation organization. Scale agency is measured by cylinder roller, to push in the next top slab ?目录摘要 (Ⅰ)ABSTRACT (Ⅱ)1绪论 (1)1.1 连铸钢的概念 (1)1.2连铸比的概念 (1)1.3国内外连铸技术的发展 (1)1.4 今后我国连铸发展要求 (2)1.5 连铸机的组成 (2)1.6 弧形连铸机的生产流程 (3)1.7切割设备的技术要求 (3)1.8切割设备的类型及特点 (4)2.同步机构方案论证 (5)3.火焰切割机机构设计及计算 (6)3.1火焰切割主要参数的确定 (6)3.2火焰切割机的机构 (8)3.2.1切割机构 (8)3.2.2电机的选择 (9)3.2.3螺旋传动的设计 (9)3.2.4同步机构 (11)3.2.5返回机构 (14)3.2.6 自动定尺装置 (17)4火焰切割机的安装与维修 (19)4.1设备的安装 (19)4.1.1设备就位和找正调平 (19)4.1.2设备安装准备 (19)4.1.3零、部件的清洗与装配 (19)4.1.4机械设备试运转阶段 (20)4.1.5竣工验收 (20)4.2日常检查与维护 (20)4.3火焰切割机的常见故障 (20)4.4火焰切割机检修 (21)设计心得 (23)参考文献 (24)1 绪论1.1 连续铸钢的概念连续铸钢是一项把钢水直接浇铸成形的节能新工艺,它具有节省工序、缩短流程,提高金属收得率,降低能量消耗,生产过程机械化和自动化程度高,钢种扩大,产品质量高等许多传统模铸技术不可比拟的优点。
自从20世纪50年代连续铸钢技术进入工业性应用阶段后,不同类型、不同规格的连铸机及其成套设备应运而生。
20世纪70年代以后,连铸技术发展迅猛,特别是板、方坯连铸机的发展对加速连铸技术替代传统的模铸技术起到了决定性作用。
1.2 连铸比的概念连铸坯的吨数与总铸坯(锭)的吨数之比叫做连铸比,它是衡量一个国家或一个钢铁工厂生产发展水平的重要标志之一,也是连铸设备、工艺、管理以及和连铸有关的各生产环节发展水平的综合体现。
1.3 国内外连铸技术的发展1.3.1 国外连铸技术的发展概况20世纪50年代,连铸开始用于钢铁工业生产。
连铸坯产量仅有110万t左右,连铸比约为0.34%20世纪60年代,弧型连铸机问世,连铸进入了稳步发展时期。
年产铸坯能力达4000万t以上,连铸比达5.6%。
20世纪70年代,世界范围的两次能源危机促进了连铸技术大发展,连铸进入了迅猛发展时期。
铸坯产量已逾2亿t,连铸比上升为25。
8%。
20世纪80年代,连铸进入完全成熟的全盛时期。
世界连铸比由1981年的33。
8%上升到1990年的64。
1%。
连铸技术的进步主要表现在对铸坯质量设计和质量控制方面达到了一个新水平。
20世纪90年代以来,近终形连铸受到了实际各过的普遍关注,近终形薄板坯连铸与连扎相结合,形成紧凑式短流程,其发展速度之快,非人们所料及。
1.3.2 我国连铸发展概况近几年,我国连铸发展很快。
除海南、西藏和宁夏,都有了连铸。
2000年,连铸坯产量达到11450万吨,突破一亿吨,位居各国之首。
连铸比88.08%,超过了世界连铸比的平均数87.2%。
从1996~2000年的五年,连铸坯的产量增加7017万吨,平均年增1403万吨,连铸比比1995(46.48%)增长41.6个百分点 ,平均年增8.32个百分点.这个增速在世界上也是罕见的.2000年,全连铸单位达到130个占有连铸单位的总数165个的78.8%(没有连铸的单位仅12个);高效和较高效连铸机占连铸机总数339台的约50%.在品种质量方面,可以说除个别品种外都能生产并满足质量要求。
进入新世纪,连铸生产发展更快.2001年连铸坯产量达13820万吨,连铸比达92.8%,比2000年猛增2370万吨,增长21%,连铸比增长4.72个百分点。
2002年预计将产连铸坯16500万吨连铸比将达94%左右,全连铸单位将达157个,占当前有连铸的单位总数175的89.7%.2002年预计将新增连铸机60台200流,产能3500万吨以上.到2002年在线连铸机将达444台,产能共19450万吨.预计到2005年连铸机产能将达23500万吨,产量将达21000万吨,连铸比将达97%.现在新建的钢长起步都是全连铸,新建的连铸机基本上都是高效的,而且达产很快。
1.4 今后我国连铸发展要求1.提高品质.国内市场所需的品种应能自己生产并保证质量,充分满足市场要求,并有利于扩大出口。
2.提高效率.还有近半数的连铸机需要进行高效化改造,已改造的效率需进一步提高,新建连铸机必须高效化且一步到位,提高近终型连铸的比率,进一步提高效率。
3.提高连铸比.尤其是提高特钢连铸比, 进一步发展全连铸.目前,影响我国连铸比的主要是几个大的钢铁企业和一批老的特钢企业,包钢和攀钢可望于2003或2004年实现全连铸,宝钢可望于2006年实现全连铸,太钢也正在努力。
4.流程最佳化.炉外精炼、铸坯热装、连轧成材,连铸是中间环节和中心环节,力求匹配、衔接最佳化,使之充分发挥炼钢及轧钢的能力,缩短工艺流程,降低各项消耗,提高劳动生产率,增加经济效益。
1.5 连铸机的组成连铸机主要由钢包运载装置、中间包、中间包运载装置、结晶器、结晶器振动装置、二次冷却装置、拉坯矫直机、引锭装置、切割装置和铸坯运出装置等部分组成。
图1.1 弧形连铸机1-钢包转台; 2-中间罐; 3-结晶器; 4-二次冷却及导向装置; 5-结晶器振动装置6-拉矫机; 7-引锭存放装置; 8-切割装置; 9-铸坯运出装置1.6 弧形连铸机的生产流程连续浇注时,钢水罐中的钢液经过中间罐注入水冷铜板结晶器内,结晶器的底部由引锭头承托,使引锭头与结晶器壁密封后便可开始浇注。
注入结晶器的钢水受到水冷铜模的强烈冷却,迅速成为具有一定厚度坯壳的铸坯。
当钢液浇至规定高度时,开动拉矫机,拉锟夹住引锭杆以一定速度把铸坯连续拉出结晶器。
为了防止铸坯坯壳被拉断,并减少结晶器内的拉坯阻力,在浇注过程中,结晶器始终要进行往复振动。
铸坯拉出结晶器以后,进入二次喷水冷却区,直到完全凝固。
当铸坯拉出拉矫机后,脱去引锭装置,铸坯经过矫直,再经过割机切成定尺长度,由输送锟道运走,这一整个过程是连续进行的。
铸坯切割装置处于整个连铸装置的末端,也是整个连铸流程的结尾部分,负责把连铸坯按照轧钢机的要求切割成定尺或倍尺长度。
铸坯是在连续运行中完成切割,因此切割装置必须与铸坯同步运动。
1.7切割设备的技术要求1.把被矫直的铸坯,按要求切割成一定长度。
2.铸坯切口应与铸坯长度方向垂直,切面平整,切头不应有大于原铸坯断面的变形。
3.切割能力应适应铸坯温度的变化。
1.8切割设备的类型及特点1.8.1 种类小方坯连铸机采用的切割设备种类较多,有电动机械剪,液压剪,火焰切割机等。
1.8.2火焰切割机原理火焰切割机是利用燃气和氧气将铸坯快速燃烧,达到切断铸坯的目的,其优点是在线设备轻,一次性投资省,适应铸坯的温度宽;缺点是切割渣不易处理,金属损耗大,但当铸坯定尺较长时,金属损耗则较少,因而目前有些中、小企业又趋向建火焰切割机。
1.8.3 火焰切割机的种类火焰切割机用于小方坯铸机的机型目前有三种:其一自动化程度较高,投资也较大的为全自动化的火焰切割机,切割枪的摆动,切割小车的随动及返回,以及自动计数定尺,都由微机控制。
电动或气压做动力源。
另两种近来较流行的经济型的火焰切割机:一种称无动力型火焰切割机,另一种称夹坯型火焰切割机。