热轧带钢孔洞缺陷的形成原因与控制措施
热轧型钢常见外观缺陷与控制方法.docx
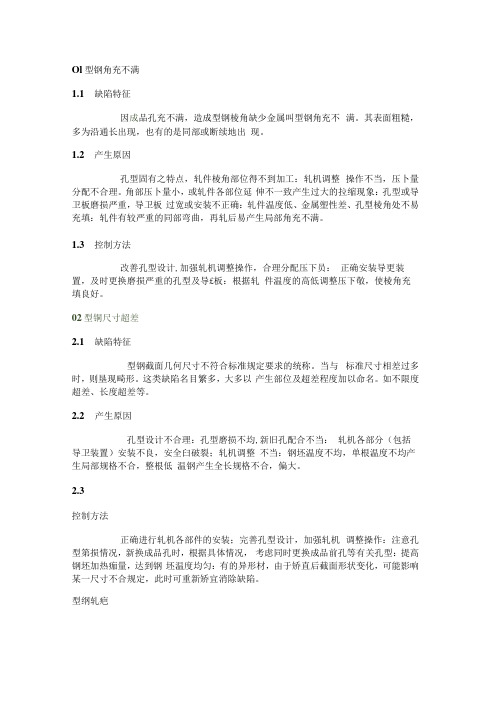
Ol型钢角充不满1.1缺陷特征因成品孔充不满,造成型钢棱角缺少金属叫型钢角充不满。
其表面粗糙,多为沿通长出现,也有的是同部或断续地出现。
1.2产生原因孔型固有之特点,轧件棱角部位得不到加工:轧机调整操作不当,压卜量分配不合理。
角部压卜量小,或轧件各部位延伸不一致产生过大的拉缩现象:孔型或导卫板磨损严重,导卫板过宽或安装不正确:轧件温度低、金属塑性差、孔型棱角处不易充填:轧件有较严重的同部弯曲,再轧后易产生局部角充不满。
1.3控制方法改善孔型设计,加强轧机调整操作,合理分配压下员:正确安装导更装置,及时更换磨损严重的孔型及导£板:根据轧件温度的高低调整压下敬,使棱角充填良好。
02型铜尺寸超差2.1缺陷特征型钢截面几何尺寸不符合标准规定要求的统称。
当与标准尺寸相差过多时,则垦现畸形。
这类缺陷名目繁多,大多以产生部位及超差程度加以命名。
如不限度超差、长度超差等。
2.2产生原因孔型设计不合理:孔型磨损不均,新旧孔配合不当:轧机各部分(包括导卫装置)安装不良,安全臼破裂;轧机调整不当:钢坯温度不均,单根温度不均产生局部规格不合,整根低温钢产生全长规格不合,偏大。
2.3控制方法正确进行轧机各部件的安装;完善孔型设计,加强轧机调整操作:注意孔型第损情况,新换成品孔时,根据具体情况,考虑同时更换成品前孔等有关孔型:提高钢坯加热痂量,达到钢坯温度均匀:有的异形材,由于矫直后截面形状变化,可能影响某一尺寸不合规定,此时可重新矫宜消除缺陷。
型纲轧疤3.1缺陷特征由于轧制中造成的粘接在型钢表面的金属块状物。
其外形类似结疤,与结疤不同的主要是,轧疤的形状及其在型钢表面上的分布有一定规律性。
缺陷下面常无非金屈氧化物夹杂。
3.2产生原因粗轧机孔型磨损严重,在型钢的固定面上产生断续分布的活轧疤:金属外物(或轧件本身被导T!装置刮下的金属)压入轧件表面形成轧疤:由于在成品孔前某道轧件表面产生周期性凸块或凹坑,再也后形成周期性轧疤,具体原因有:孔槽刻痕不良:轧槽有砂眼或掉肉:轧槽被“黑头”轧件撞伤或粘有结疤等凸起物:轧件在孔型内打滑,造成金属堆积在变形区表面上,再轧后形成轧疤:轧件局部被困盘、短道、翻钢机等机械设备卡(刮)伤或刮弯,再轧后也会形成轧疤。
热轧质量缺陷及产生原因
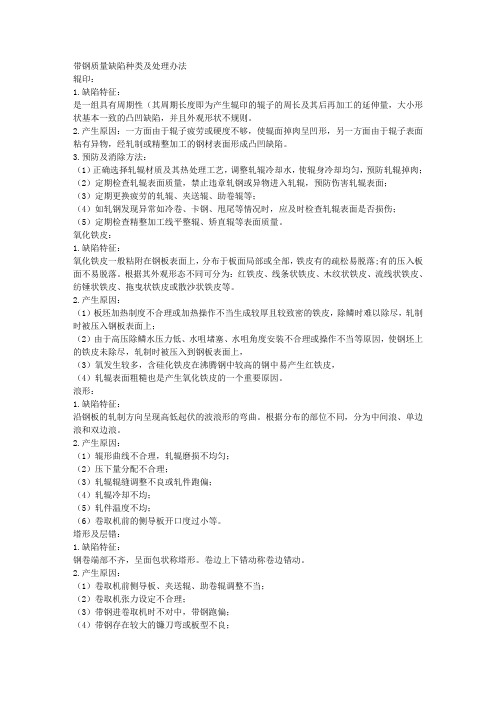
带钢质量缺陷种类及处理办法辊印:1.缺陷特征:是一组具有周期性(其周期长度即为产生辊印的辊子的周长及其后再加工的延伸量,大小形状基本一致的凸凹缺陷,并且外观形状不规则。
2.产生原因:一方面由于辊子疲劳或硬度不够,使辊面掉肉呈凹形,另一方面由于辊子表面粘有异物,经轧制或精整加工的钢材表面形成凸凹缺陷。
3.预防及消除方法:(1)正确选择轧辊材质及其热处理工艺,调整轧辊冷却水,使辊身冷却均匀,预防轧辊掉肉;(2)定期检查轧辊表面质量,禁止违章轧钢或异物进入轧辊,预防伤害轧辊表面;(3)定期更换疲劳的轧辊、夹送辊、助卷辊等;(4)如轧钢发现异常如冷卷、卡钢、甩尾等情况时,应及时检查轧辊表面是否损伤;(5)定期检查精整加工线平整辊、矫直辊等表面质量。
氧化铁皮:1.缺陷特征:氧化铁皮一般粘附在钢板表面上,分布于板面局部或全部,铁皮有的疏松易脱落;有的压入板面不易脱落。
根据其外观形态不同可分为:红铁皮、线条状铁皮、木纹状铁皮、流线状铁皮、纺锤状铁皮、拖曳状铁皮或散沙状铁皮等。
2.产生原因:(1)板坯加热制度不合理或加热操作不当生成较厚且较致密的铁皮,除鳞时难以除尽,轧制时被压入钢板表面上;(2)由于高压除鳞水压力低、水咀堵塞、水咀角度安装不合理或操作不当等原因,使钢坯上的铁皮未除尽,轧制时被压入到钢板表面上,(3)氧发生较多,含硅化铁皮在沸腾钢中较高的钢中易产生红铁皮,(4)轧辊表面粗糙也是产生氧化铁皮的一个重要原因。
浪形:1.缺陷特征:沿钢板的轧制方向呈现高低起伏的波浪形的弯曲。
根据分布的部位不同,分为中间浪、单边浪和双边浪。
2.产生原因:(1)辊形曲线不合理,轧辊磨损不均匀;(2)压下量分配不合理;(3)轧辊辊缝调整不良或轧件跑偏;(4)轧辊冷却不均;(5)轧件温度不均;(6)卷取机前的侧导板开口度过小等。
塔形及层错:1.缺陷特征:钢卷端部不齐,呈面包状称塔形。
卷边上下错动称卷边错动。
2.产生原因:(1)卷取机前侧导板、夹送辊、助卷辊调整不当;(2)卷取机张力设定不合理;(3)带钢进卷取机时不对中,带钢跑偏;(4)带钢存在较大的镰刀弯或板型不良;(5)卷取机卸卷时将钢卷头部拽出。
热轧带钢表面质量缺陷原因分析

热轧带钢表面质量缺陷原因分析热轧带钢的表面质量缺陷是指在热轧工艺过程中,带钢表面出现的各种缺陷。
这些缺陷对带钢的外观和性能都有不良影响,严重时还会导致带钢失效。
以下是热轧带钢表面质量缺陷原因的分析。
1. 轧制工艺不合理:热轧带钢的表面质量缺陷与轧制工艺有着密切关系。
如果轧制工艺控制不当,例如轧制温度过高、辊缝调整不当等,就会导致带钢表面产生热裂纹、鱼鳞鳞片状缺陷等。
2. 材料质量问题:带钢是由钢坯经过多道次轧制形成的,如果钢坯的质量不佳,例如存在夹杂物、气孔等缺陷,就会在轧制过程中扩展并形成表面缺陷。
3. 辊缝问题:辊缝是带钢在轧制过程中受到的挤压力的集中作用点,如果辊缝调整不当,例如过大或过小,都会对带钢表面产生压痕、划痕等缺陷。
4. 轧制润滑问题:轧制过程中需要使用润滑剂来减小摩擦力,如果润滑不均匀或润滑剂存在污染物,就会导致带钢表面出现涂敷不均匀、氧化皮不易剥离等缺陷。
5. 切割质量问题:在热轧带钢生产中,需要对带钢进行切割,如果切割工艺不当,例如切割速度过快、切割刀具磨损等,就会导致切口不整齐、毛刺等缺陷。
6. 后续工艺操作问题:热轧带钢在后续的加工和处理过程中,如果操作不当,例如维护不及时、设备老化等,就会导致带钢表面产生擦伤、磕碰等缺陷。
针对以上分析,可以采取以下措施来改善热轧带钢的表面质量:1. 优化轧制工艺:合理控制轧制温度、辊缝调整,减小轧制力度等,以提高带钢的表面质量。
2. 加强材料质量控制:采用优质钢坯,并对钢坯进行充分检验和清洁处理,以减少杂质的含量和夹杂物的存在。
3. 确保辊缝质量:定期对辊缝进行调整和检查,确保辊缝的尺寸和形状符合要求,减少对带钢表面的压力集中。
4. 加强润滑管理:优化润滑剂的选择和使用方法,确保润滑剂均匀涂敷在轧制表面,并定期清洗润滑系统,减少污染物的残留。
5. 优化切割工艺:控制切割速度,保证切割刀具的锋利度,加强切割设备的维护和监测,以保证切口的质量。
轧制缺陷及质量控制

轧制缺陷及质量控制一、引言轧制是金属加工中的一种重要工艺,用于将金属坯料通过轧机进行塑性变形,以获得所需的形状和尺寸。
然而,在轧制过程中,由于各种因素的影响,会产生一些缺陷,如裂纹、夹杂物、表面缺陷等,这些缺陷会严重影响产品的质量和性能。
因此,对轧制缺陷进行有效的控制和管理,是确保产品质量的关键。
二、轧制缺陷的分类1. 表面缺陷:包括轧痕、轧花、氧化皮、划伤等。
2. 内部缺陷:包括夹杂物、裂纹、孔洞等。
3. 尺寸偏差:包括厚度偏差、宽度偏差等。
三、轧制缺陷的原因分析1. 材料因素:原材料的质量和成份会直接影响轧制过程中的缺陷产生。
如含有夹杂物、氧化皮等。
2. 工艺参数:轧制过程中的轧制力、轧制速度、轧制温度等参数的控制不当,会导致缺陷的产生。
3. 设备状况:轧机的磨损、不平衡等问题会影响轧制质量。
4. 操作人员:操作人员的技术水平和经验也会对轧制质量产生影响。
四、轧制缺陷的质量控制方法1. 前期控制:在轧制前对原材料进行严格的检查和筛选,确保材料的质量符合要求。
2. 工艺参数控制:根据产品的要求和轧制材料的特性,合理设置轧制力、轧制速度、轧制温度等参数,以减少缺陷的产生。
3. 设备维护:定期对轧机进行检修和维护,确保设备的正常运行,减少设备因素对轧制质量的影响。
4. 操作人员培训:加强对操作人员的培训和技术指导,提高其对轧制过程中缺陷产生原因的认识和处理能力。
5. 检测方法:采用先进的无损检测技术,如超声波检测、磁粉检测等,对轧制产品进行全面的检测,及时发现和排除缺陷。
6. 质量管理体系:建立完善的质量管理体系,包括质量控制计划、质量检验记录、质量问题分析等,确保轧制产品的质量稳定可控。
五、案例分析某钢铁厂在轧制过程中,时常浮现轧制缺陷问题,导致产品质量不稳定,客户投诉频繁。
经过对生产过程的分析和改进,采取了以下措施:1. 强化原材料的筛选工作,严格控制夹杂物和氧化皮的含量。
2. 优化工艺参数,合理调整轧制力、轧制速度和轧制温度,降低缺陷的产生率。
热轧工序典型质量缺陷产生原因与预防措施

预防措施
加强原材料质量检查,去除夹杂物;加强生 产过程控制,及时清除金属氧化物和其他夹 杂物。
03
热轧工序质量缺陷预防措施
提高原料质量
01
总结词:优化源头
02
详细描述:选用质量稳定的原料 ,控制原料的化学成分、物理性 能等指标,确保原料质量稳定, 为热轧工序打下良好的基础。
优化热轧工艺参数
要点一
热轧钢板内部存在气泡缺陷,影响产品质量和使用性能。
产生原因:熔炼和连铸过程控制不当、坯料加热时间过长或加热温度 过高、轧制速度过快。
预防措施:加强熔炼和连铸过程控制、合理控制坯料加热时间和温度 、降低轧制速度。
案例五:某钢厂热轧带钢表面翘曲预防措施
热轧带钢表面翘曲
产生原因:轧制温度和 冷却速度控制不当、坯 料厚度和成分不均。
案例三
01
热轧圆钢表面划痕
02
热轧圆钢表面存在划痕等缺陷, 影响产品外观和使用性能。
产生原因:轧辊表面损伤、坯料 表面质量差、冷却不均匀。
03
预防措施:检查和修复轧辊表面 损伤、加强坯料检查和加热控制
、调整冷却制度。
04
案例四:某钢厂热轧钢板内部气泡控制措施
01 02 03 04
热轧钢板内部气泡
01
02
03
04
热轧带钢表面存在翘曲 缺陷,影响产品平整度 和使用性能。
预防措施:合理控制轧 制温度和冷却速度、加 强坯料检查和控制。
THANK YOU
质量缺陷分类
根据缺陷的性质和产生原因,可 将热轧工序的质量缺陷分为材质 缺陷、工艺缺陷、设备缺陷和外 观缺陷等。
质量缺陷对产品的影响
影响使用性能
如强度、韧性等力学性能下降, 导致产品在使用过程中出现早期
带钢轧制时产生的主要缺陷与分析

带钢轧制时产生的主要缺陷与分析带钢轧制时产生的主要缺陷与分析在热带轧机上轧制带钢所形成的缺陷最主要有下列几种:(1)结疤。
在板坯清理时对裂口及裂纹没有全部清除干净,结果在轧制时形成结疤;板坯加热时过热,特别是铬不锈钢,轧制时在带钢上形成结疤。
带钢坯表面大量集结的非金属夹杂物,也是产生结疤的原因。
(2)裂边。
板坯侧面缺陷未全面清除干净,这是带钢裂边的原因。
(3)过热。
板坯在过高温度下长时间停留会引起过热。
过热板坯轧制时会产生大裂口和剥落;邻近过热的部分出现细裂纹,细裂纹在进一步轧制时会变成结疤。
为防止板坯过热必须严格遵守规定的加热制度,尤其是高温下的均热时间。
加热铁素体类钢时,温度超过850℃后必须快速加热。
(4)机械损伤。
轧入碎屑、压痕、划痕是热轧不锈带钢表面最有特征的缺陷。
轧人碎屑和压痕缺陷是由于坯料上的结疤块、裂边在导卫上摩擦时有碎片落到带钢表面上以及其他东西被轧辊或矫直机辊子压人而形成的。
划痕大部分是在带钢运动时,下表面与不光滑的导卫、辊面不平的辊子及被动辊相接触时形成的。
上表面划痕通常是在未卷紧运送时卷层间摩擦造成的。
在卷取中,带钢与卷取机成形辊和喂料辊之间发生摩擦时,带钢表面上会产生很多短条状划伤。
(5)带钢厚薄不均。
带钢长度上的厚度不均匀与沿板坯长度加热的均匀性及带钢在机架间张力值有关。
带钢的前端和后端一般比中部厚一些,这是因为在连续式精轧机组中带钢端部没有张力的缘故。
带钢后端一般比前端厚,这是温度不同所致热轧带钢开裂的改进热轧带钢生产的工艺流程:铁液一铁液预处理一顶底复吹转炉一脱氧合金化一吹氩一板坯连铸一铸坯检验一加热一粗轧高压水除鳞一立辊轧一可逆式粗轧一中轧一热卷箱一精轧高压水除鳞一精轧一层流冷却一卷取一入库。
热轧带钢在生产检验及用户使用过程中常出现的开裂现象,并对开裂带钢进行了化学成分及低倍和金相检验分析。
结果表明,化学成分符合要求,铸坯存在皮下气泡、带钢存在非金属夹杂及游离渗碳体是带钢出现开裂主要原因,针对以上情况给你针对性改进建议,具体如下。
热轧工序典型质量缺陷产生原因与预防措施
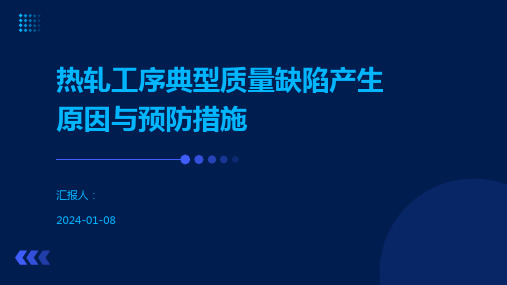
工艺参数设置不合理、工艺流程不完善等工艺因素是导致热轧工序质量缺陷的 重要原因。
详细描述
加热温度、轧制速度、道次压下量等工艺参数的设置对热轧产品的质量有显著 影响。工艺流程中的不合理之处,如冷却速度控制不当、轧制道次不足等,也 可能导致产品出现各种缺陷。
设备因素
总结词
设备故障、维护不当等设备因素是热轧工序中常见的质量缺 陷原因。
热轧工序典型质量缺陷产生 原因与预防措施
汇报人: 2024-01-08
目录
• 热轧工序简介 • 典型质量缺陷类型 • 产生原因分析 • 预防措施 • 案例分析 • 结论与展望
01
热轧工序简介
热轧工序的定义和重要性
定义
热轧工序是将金属材料在高温下 进行轧制的过程,目的是改变材 料的形状并获得所需的机械性能 。
钢材内部碳化物分布不均,导致钢材 性能不均一。
03
产生原因分析
原料因素
总结词
原料质量不均、成分偏析等原料因素 是导致热轧工序质量缺陷的主要原因 之一。
详细描述
原料的化学成分、微观组织结构、夹 杂物含量等因素可能影响热轧过程中 的流动性和变形行为,从而导致产品 出现裂纹、孔洞、夹杂等缺陷。
工艺因素
板形不良产生的原因可能是轧辊磨损严重、轧 制工艺参数设置不合理,或者是来料温度和厚 度波动过大。
厚度超差产生的原因可能是轧辊间隙调整不当 、轧制过程中张力控制不准确,或者是轧制润 滑条件不佳,导致金属流动不均匀。
预防措施实施效果评估
对于表面裂纹,通过优化轧制温 度和润滑条件,加强轧辊检查和 维护,可以显著减少裂纹的产生
2
针对这些质量缺陷,需要采取有效的预防措施, 如控制工艺参数、优化设备参数和加强质量检测 等。
热轧带钢表面质量缺陷原因分析
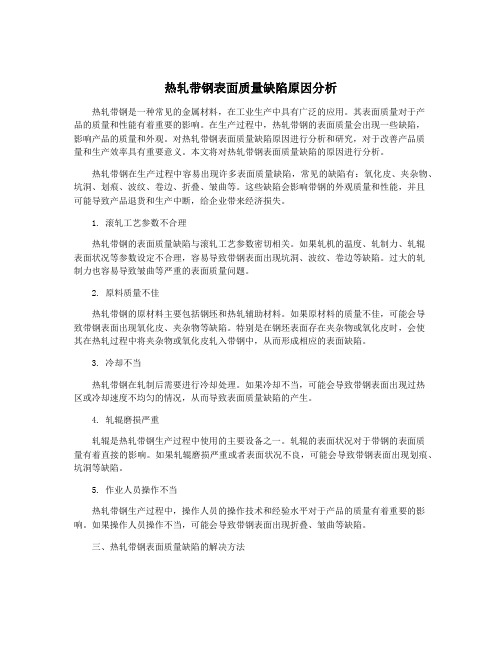
热轧带钢表面质量缺陷原因分析热轧带钢是一种常见的金属材料,在工业生产中具有广泛的应用。
其表面质量对于产品的质量和性能有着重要的影响。
在生产过程中,热轧带钢的表面质量会出现一些缺陷,影响产品的质量和外观。
对热轧带钢表面质量缺陷原因进行分析和研究,对于改善产品质量和生产效率具有重要意义。
本文将对热轧带钢表面质量缺陷的原因进行分析。
热轧带钢在生产过程中容易出现许多表面质量缺陷,常见的缺陷有:氧化皮、夹杂物、坑洞、划痕、波纹、卷边、折叠、皱曲等。
这些缺陷会影响带钢的外观质量和性能,并且可能导致产品退货和生产中断,给企业带来经济损失。
1. 滚轧工艺参数不合理热轧带钢的表面质量缺陷与滚轧工艺参数密切相关。
如果轧机的温度、轧制力、轧辊表面状况等参数设定不合理,容易导致带钢表面出现坑洞、波纹、卷边等缺陷。
过大的轧制力也容易导致皱曲等严重的表面质量问题。
2. 原料质量不佳热轧带钢的原材料主要包括钢坯和热轧辅助材料。
如果原材料的质量不佳,可能会导致带钢表面出现氧化皮、夹杂物等缺陷。
特别是在钢坯表面存在夹杂物或氧化皮时,会使其在热轧过程中将夹杂物或氧化皮轧入带钢中,从而形成相应的表面缺陷。
3. 冷却不当热轧带钢在轧制后需要进行冷却处理。
如果冷却不当,可能会导致带钢表面出现过热区或冷却速度不均匀的情况,从而导致表面质量缺陷的产生。
4. 轧辊磨损严重轧辊是热轧带钢生产过程中使用的主要设备之一。
轧辊的表面状况对于带钢的表面质量有着直接的影响。
如果轧辊磨损严重或者表面状况不良,可能会导致带钢表面出现划痕、坑洞等缺陷。
5. 作业人员操作不当热轧带钢生产过程中,操作人员的操作技术和经验水平对于产品的质量有着重要的影响。
如果操作人员操作不当,可能会导致带钢表面出现折叠、皱曲等缺陷。
三、热轧带钢表面质量缺陷的解决方法为了避免因滚轧工艺参数不合理而导致的表面质量缺陷,需要对滚轧工艺参数进行合理的调整和优化。
通过科学合理的轧制力、温度、冷却速度等参数的设定,可以有效地改善热轧带钢的表面质量。
热轧质量缺陷及产生原因
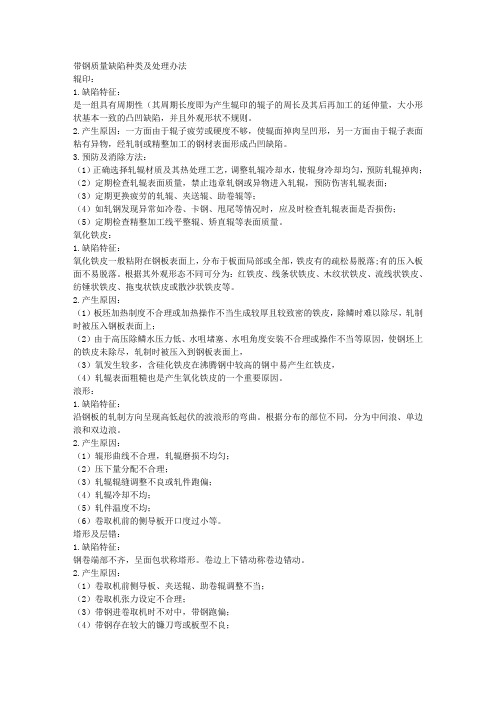
带钢质量缺陷种类及处理办法辊印:1.缺陷特征:是一组具有周期性(其周期长度即为产生辊印的辊子的周长及其后再加工的延伸量,大小形状基本一致的凸凹缺陷,并且外观形状不规则。
2.产生原因:一方面由于辊子疲劳或硬度不够,使辊面掉肉呈凹形,另一方面由于辊子表面粘有异物,经轧制或精整加工的钢材表面形成凸凹缺陷。
3.预防及消除方法:(1)正确选择轧辊材质及其热处理工艺,调整轧辊冷却水,使辊身冷却均匀,预防轧辊掉肉;(2)定期检查轧辊表面质量,禁止违章轧钢或异物进入轧辊,预防伤害轧辊表面;(3)定期更换疲劳的轧辊、夹送辊、助卷辊等;(4)如轧钢发现异常如冷卷、卡钢、甩尾等情况时,应及时检查轧辊表面是否损伤;(5)定期检查精整加工线平整辊、矫直辊等表面质量。
氧化铁皮:1.缺陷特征:氧化铁皮一般粘附在钢板表面上,分布于板面局部或全部,铁皮有的疏松易脱落;有的压入板面不易脱落。
根据其外观形态不同可分为:红铁皮、线条状铁皮、木纹状铁皮、流线状铁皮、纺锤状铁皮、拖曳状铁皮或散沙状铁皮等。
2.产生原因:(1)板坯加热制度不合理或加热操作不当生成较厚且较致密的铁皮,除鳞时难以除尽,轧制时被压入钢板表面上;(2)由于高压除鳞水压力低、水咀堵塞、水咀角度安装不合理或操作不当等原因,使钢坯上的铁皮未除尽,轧制时被压入到钢板表面上,(3)氧发生较多,含硅化铁皮在沸腾钢中较高的钢中易产生红铁皮,(4)轧辊表面粗糙也是产生氧化铁皮的一个重要原因。
浪形:1.缺陷特征:沿钢板的轧制方向呈现高低起伏的波浪形的弯曲。
根据分布的部位不同,分为中间浪、单边浪和双边浪。
2.产生原因:(1)辊形曲线不合理,轧辊磨损不均匀;(2)压下量分配不合理;(3)轧辊辊缝调整不良或轧件跑偏;(4)轧辊冷却不均;(5)轧件温度不均;(6)卷取机前的侧导板开口度过小等。
塔形及层错:1.缺陷特征:钢卷端部不齐,呈面包状称塔形。
卷边上下错动称卷边错动。
2.产生原因:(1)卷取机前侧导板、夹送辊、助卷辊调整不当;(2)卷取机张力设定不合理;(3)带钢进卷取机时不对中,带钢跑偏;(4)带钢存在较大的镰刀弯或板型不良;(5)卷取机卸卷时将钢卷头部拽出。
热轧带钢缺陷识别与质量控制
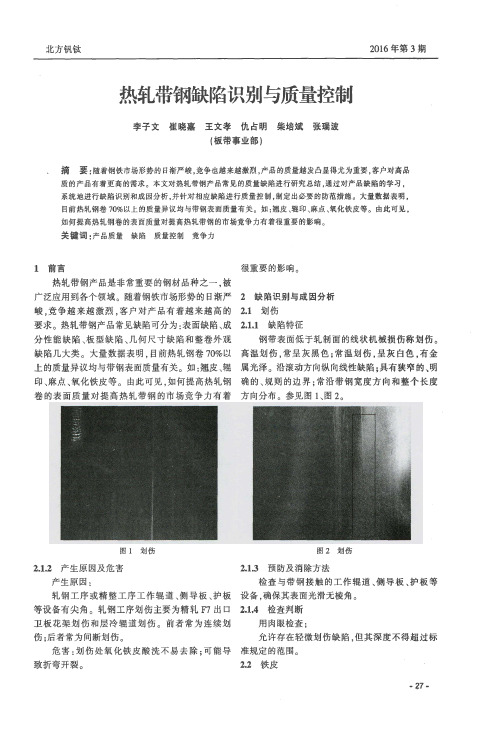
一
,
缺陷 调 边 表 面状况
王
.
良
好 w除鳞水 系
.
-
统 故障 原 h 轧 制 过程 中 未能
冲 刷 轧件 表 S
f
,
,
常投 入 高
丨
k
水进 行
致 使表 面 大 范 围 金 属 氧 化 物碾 X
。
①除 鳞 水 嘴 堵 塞 导 致 流 量 减 小
② 除 鱗水 嘴 角 度 偏 移 导致
。
F7
出 口
2
.
1
.
4
检 查判 断
用 肉 眼检查
;
卫 板 花 架划 伤 和 层 冷 辊 道 划 伤
前 者 常为 连 续 划
伤 后 者 常为 间 断划 伤
; :
。
允许 存 在 轻 微 划 伤 缺 陷 但 其 深 度 不 得 超 过 标
, ;
危 害 划 伤 处 氧 化 铁皮 酸 洗 不 易 去 除 可 能 导
,
,
一
,
对 于 氧 化膜 来 讲
过 厚 与 过 薄 都是 不 利 的 我
,
缺 陷 周 边 表 面 状 况 良 好 分 布 位 置 没 有 规律
,
;
们 需 要 的 是 细 腻稳 定 的 结 构
。
■■ ■1
■■ ■
图
6
轧 辊氧 化过程
-
28
-
北 方钒 钛
目
。
大量 数 据 表 明
。
,
前热 轧 钢 卷
70
% 以 上 的 质 量 异 议 均 与 带 钢表 面 质 量 有 关
。
如 翘皮 辊印 麻点
轧制缺陷及质量控制

轧制缺陷及质量控制一、引言轧制是金属加工中的一种常见工艺,用于将金属坯料通过连续压制和拉伸的方式减小其截面积,从而获得所需的形状和尺寸。
然而,在轧制过程中,由于各种因素的影响,可能会浮现一些缺陷,如表面裂纹、内部气孔、夹杂物等,这些缺陷会对产品的质量和性能产生不利影响。
因此,对轧制缺陷进行有效的控制和管理是至关重要的。
二、轧制缺陷分类1. 表面缺陷:包括轧制印记、划伤、氧化皮、烧伤等。
这些缺陷通常是由于轧制辊或者其他设备的不良状况导致的,可以通过定期检查和维护设备来减少这些缺陷的发生。
2. 内部缺陷:包括气孔、夹杂物、晶界偏差等。
这些缺陷通常是由于原材料的质量问题或者轧制过程中的温度、压力等参数控制不当导致的。
通过优化原材料选择和精确控制轧制工艺参数,可以最大程度地减少内部缺陷的发生。
三、轧制缺陷的检测方法1. 目视检测:通过肉眼观察产品表面,检查是否存在明显的缺陷。
这种方法简单直观,但对于一些弱小的缺陷可能无法有效检测。
2. 超声波检测:利用超声波的传播特性,检测产品内部的缺陷。
通过超声波的反射和散射情况,可以确定缺陷的位置和大小。
这种方法对于检测内部缺陷非常有效,但需要专业的设备和技术人员进行操作。
3. X射线检测:利用X射线的穿透性,检测产品内部的缺陷。
通过检测X射线透射的强度和散射情况,可以确定缺陷的位置和性质。
这种方法对于检测较小的内部缺陷非常有效,但需要专业的设备和防护措施。
四、轧制缺陷的质量控制1. 原材料控制:选择高质量的原材料,确保其化学成份和物理性能符合要求。
通过与供应商建立稳定的合作关系,进行原材料的定期检验和评估,以确保产品质量的稳定性。
2. 工艺参数控制:根据产品要求和原材料特性,合理确定轧制过程中的温度、压力、速度等参数。
通过实时监测和调整这些参数,确保产品在轧制过程中获得良好的塑性变形和细化晶粒,减少缺陷的发生。
3. 设备维护管理:定期检查和维护轧制设备,确保其正常运行和性能稳定。
轧制缺陷及质量控制

轧制缺陷及质量控制一、引言轧制是金属加工过程中的一种重要工艺,用于将金属坯料通过压力和磨擦力的作用,使其产生塑性变形,从而得到所需形状和尺寸的金属产品。
然而,在轧制过程中,由于各种因素的影响,可能会浮现一些缺陷,如裂纹、气孔、夹杂物等,这些缺陷会极大地影响产品的质量和性能。
因此,对轧制缺陷进行有效的控制和管理至关重要。
二、轧制缺陷的分类根据轧制缺陷的性质和形态,可以将其分为以下几类:1. 表面缺陷:包括轧痕、划伤、氧化皮等,主要是由于轧辊和金属表面之间的磨擦和压力引起的。
2. 内部缺陷:包括夹杂物、气孔、裂纹等,主要是由于金属内部的不均匀组织或者外来杂质引起的。
3. 尺寸偏差:包括厚度不均匀、宽度不一致等,主要是由于轧制过程中的工艺参数不当或者设备故障引起的。
三、轧制缺陷的原因分析1. 材料因素:材料的成份和结构对轧制缺陷有重要影响。
例如,含有夹杂物或者杂质的金属坯料容易在轧制过程中产生裂纹温和孔。
2. 工艺因素:轧制工艺参数的选择和控制对缺陷的形成和控制至关重要。
例如,轧制温度、轧制速度、轧制力等参数的不合理调整都可能导致缺陷的产生。
3. 设备因素:轧机的性能和状态对缺陷的形成和控制也有重要影响。
例如,轧辊的磨损、轧辊的几何形状、轧机的润滑和冷却系统等都会影响产品的质量。
四、轧制缺陷的质量控制措施为了有效控制轧制缺陷,提高产品的质量和性能,可以采取以下措施:1. 优化材料选择:选择质量好、含杂质少的金属坯料,减少夹杂物和杂质对产品质量的影响。
2. 严格控制工艺参数:根据不同的金属材料和产品要求,合理选择轧制温度、轧制速度、轧制力等参数,确保轧制过程中的温度和力的均匀分布。
3. 定期维护设备:定期对轧机进行维护和检修,保证轧辊的几何形状和表面光洁度,确保润滑和冷却系统的正常运行。
4. 引入先进的检测技术:利用先进的无损检测技术,如超声波检测、磁粉检测等,对轧制产品进行全面、准确的检测,及时发现和处理缺陷。
带钢轧制时产生的主要缺陷与分析

带钢轧制时产生的主要缺陷与分析在热带轧机上轧制带钢所形成的缺陷最主要有下列几种:(1)结疤。
在板坯清理时对裂口及裂纹没有全部清除干净,结果在轧制时形成结疤;板坯加热时过热,特别是铬不锈钢,轧制时在带钢上形成结疤。
带钢坯表面大量集结的非金属夹杂物,也是产生结疤的原因。
(2)裂边。
板坯侧面缺陷未全面清除干净,这是带钢裂边的原因。
(3)过热。
板坯在过高温度下长时间停留会引起过热。
过热板坯轧制时会产生大裂口和剥落;邻近过热的部分出现细裂纹,细裂纹在进一步轧制时会变成结疤。
为防止板坯过热必须严格遵守规定的加热制度,尤其是高温下的均热时间。
加热铁素体类钢时,温度超过850℃后必须快速加热。
(4)机械损伤。
轧入碎屑、压痕、划痕是热轧不锈带钢表面最有特征的缺陷。
轧人碎屑和压痕缺陷是由于坯料上的结疤块、裂边在导卫上摩擦时有碎片落到带钢表面上以及其他东西被轧辊或矫直机辊子压人而形成的。
划痕大部分是在带钢运动时,下表面与不光滑的导卫、辊面不平的辊子及被动辊相接触时形成的。
上表面划痕通常是在未卷紧运送时卷层间摩擦造成的。
在卷取中,带钢与卷取机成形辊和喂料辊之间发生摩擦时,带钢表面上会产生很多短条状划伤。
(5)带钢厚薄不均。
带钢长度上的厚度不均匀与沿板坯长度加热的均匀性及带钢在机架间张力值有关。
带钢的前端和后端一般比中部厚一些,这是因为在连续式精轧机组中带钢端部没有张力的缘故。
带钢后端一般比前端厚,这是温度不同所致热轧带钢开裂的改进热轧带钢生产的工艺流程:铁液一铁液预处理一顶底复吹转炉一脱氧合金化一吹氩一板坯连铸一铸坯检验一加热一粗轧高压水除鳞一立辊轧一可逆式粗轧一中轧一热卷箱一精轧高压水除鳞一精轧一层流冷却一卷取一入库。
热轧带钢在生产检验及用户使用过程中常出现的开裂现象,并对开裂带钢进行了化学成分及低倍和金相检验分析。
结果表明,化学成分符合要求,铸坯存在皮下气泡、带钢存在非金属夹杂及游离渗碳体是带钢出现开裂主要原因,针对以上情况给你针对性改进建议,具体如下。
热轧带钢表面质量缺陷原因分析

热轧带钢表面质量缺陷原因分析【摘要】热轧带钢表面质量缺陷是影响产品质量和生产效率的重要因素,本文从影响因素、分类特点、检测方法、处理方法以及综合分析等方面进行了深入研究。
研究发现,温度、轧制力度、冷却方式等因素对质量缺陷有着显著影响。
通过对各类缺陷进行分类并分析其特点,可以更好地找到解决方法。
检测方法的进步为及时发现和处理缺陷提供了保障,而处理方法的不断完善则能有效减少质量问题。
综合分析不同因素交织的情况,提出了一些启示和未来展望,为提高热轧带钢表面质量做出了重要贡献。
【关键词】热轧带钢、表面质量、缺陷、原因分析、影响因素、分类、特点、检测方法、处理方法、综合分析、启示、未来展望。
1. 引言1.1 热轧带钢表面质量缺陷原因分析热轧带钢表面质量缺陷是制约热轧带钢质量的重要因素之一,对热轧带钢的机械性能、外观质量和使用寿命都会造成不同程度的影响。
深入分析热轧带钢表面质量缺陷的原因,对于提高热轧带钢质量和市场竞争力具有十分重要的意义。
热轧带钢表面质量缺陷主要来源于多种因素的综合作用,包括原材料、热轧工艺、设备磨损、操作技术等方面。
原材料的质量直接影响着热轧带钢的表面质量,原料中的杂质、氧化皮等都会对表面质量造成影响;热轧工艺参数如温度、压下量、冷却方式等也是决定表面质量的关键因素;设备的磨损会导致不均匀的压下力和不稳定的轧制质量,进而影响表面质量;操作技术不到位或不规范也会引起表面质量缺陷。
通过深入分析热轧带钢表面质量缺陷的原因,可以找到相应的解决方法,提高热轧带钢的表面质量,增强市场竞争力。
2. 正文2.1 热轧带钢表面质量缺陷的影响因素分析热轧带钢表面质量缺陷的形成是受多种因素的综合影响的。
原材料的质量是影响热轧带钢表面质量的关键因素之一。
原材料的成分、结构和含杂质等都会直接影响到热轧带钢的表面质量。
热轧工艺参数的选择和控制也是决定热轧带钢表面质量的重要因素。
热轧工艺中的温度、压力、速度等参数的选择不当会导致热轧带钢表面出现缺陷。
轧制缺陷及质量控制
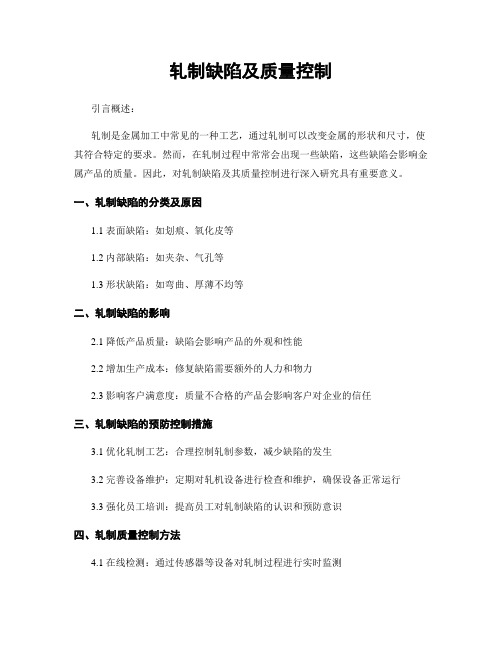
轧制缺陷及质量控制
引言概述:
轧制是金属加工中常见的一种工艺,通过轧制可以改变金属的形状和尺寸,使其符合特定的要求。
然而,在轧制过程中常常会出现一些缺陷,这些缺陷会影响金属产品的质量。
因此,对轧制缺陷及其质量控制进行深入研究具有重要意义。
一、轧制缺陷的分类及原因
1.1 表面缺陷:如划痕、氧化皮等
1.2 内部缺陷:如夹杂、气孔等
1.3 形状缺陷:如弯曲、厚薄不均等
二、轧制缺陷的影响
2.1 降低产品质量:缺陷会影响产品的外观和性能
2.2 增加生产成本:修复缺陷需要额外的人力和物力
2.3 影响客户满意度:质量不合格的产品会影响客户对企业的信任
三、轧制缺陷的预防控制措施
3.1 优化轧制工艺:合理控制轧制参数,减少缺陷的发生
3.2 完善设备维护:定期对轧机设备进行检查和维护,确保设备正常运行
3.3 强化员工培训:提高员工对轧制缺陷的认识和预防意识
四、轧制质量控制方法
4.1 在线检测:通过传感器等设备对轧制过程进行实时监测
4.2 人工检验:对轧制后的产品进行目视检查和尺寸测量
4.3 抽样检测:定期抽取产品进行全面检验,确保产品质量符合标准
五、轧制缺陷处理方法
5.1 修磨:对表面缺陷进行修磨处理,恢复产品表面光洁度
5.2 热处理:对内部缺陷进行热处理,消除缺陷并提高产品性能
5.3 重新轧制:对形状缺陷的产品进行重新轧制,确保产品尺寸和形状符合要求
总结:
轧制缺陷及质量控制是金属加工中一个重要的环节,只有通过科学的方法对轧制缺陷进行预防和控制,才能生产出高质量的金属产品,提高企业的竞争力和市场占有率。
希望本文的内容能够对相关行业的从业人员有所帮助。
热轧工序典型质量缺陷产生原因与预防措施

形状缺陷
• 轧制力或轧制速度控制不当。 预防措施
• 定期检查并更换轧辊,确保轧辊表面质量。
形状缺陷
01
• 优化热轧温度,避免温度过高 导致材料变形抗力降低。
02
• 精确控制轧制力和轧制速度, 确保在合适的参数下进行生产 。
内部组织缺陷
原因:内部组织缺陷包括晶粒粗 大、组织不均匀等,主要原因有
• 热轧温度过高或过低,导致晶 粒长大或组织不均匀。
出现开裂、断裂等缺陷。
提高设备精度与维护水平
轧机精度保障
定期检查轧机的各项精度指标,如轧辊圆度、轧辊间隙等 ,确保设备在良好状态下运行,避免因设备问题导致的质 量缺陷。
润滑与冷却系统维护
加强润滑与冷却系统的维护,保持系统稳定、高效地运行 ,确保热轧过程中轧辊与原料之间的良好润滑和冷却,防 止因摩擦过热引起的表面质量缺陷。
表面裂纹
• 严格控制热轧温度和轧后冷 却速度,避免温度剧烈变化 。
• 优化热轧设备和 加强原料检查,剔除表面有 缺陷或污染的原料。
形状缺陷
原因:形状缺陷通常表现为板材的波浪形、边浪、中浪等,主要原因有 • 轧辊磨损或不均匀磨损。
• 热轧温度高,材料变形抗力低。
原材料检测
对热轧所用原材料进行化 验检测,分析原材料成分 、组织结构等因素对质量 缺陷的影响。
持续质量改进体系建设
建立质量信息数据库
引入质量分析工具
整合热轧工序的质量检测数据、缺陷分析 数据等,建立统一的质量信息数据库。
应用六西格玛、田口方法等质量分析工具 ,对热轧过程中的质量问题进行深入挖掘 ,提出改进措施。
命。
02
典型质量缺陷及其产生原因
表面裂纹
原因:表面裂纹是热 轧过程中最常见的缺 陷之一,主要原因包 括
SPHD热轧带钢孔洞形成原因及改进

S t e e l Gr o u p,Ha n d a n ,He b e i ,0 5 6 0 1 5 )
Abs t r a c t :I t i s a n a l y z e d t h e ma c r o a nd mi c r o c h a r a c t e r i s t i c s of h o l e de f e c t i n SPHD h ot— r o l l i ng s t r i p s t e e l ,
重 时还可 引起 酸轧 机组 或者 连退 机组 断带 等生 产 事
故 。本文 对邯 宝冷 轧厂 冷硬板 生 产过 程 中出现 的两
例典 型轧 制孔 洞 进 行 了 系统 分 析 , 对 酸轧 机 组 及 热
轧带 钢原 料 的生产 提 出 了一 些ห้องสมุดไป่ตู้ 进建 议 。
2 孔 洞 缺 陷 分 析
关键词 : 热轧带钢 ; 孑 L 洞; 原因; 措 施 中图分类号 : T G 3 3 5 . 5 文献标识码 : B 文章 编 号 : 1 0 0 6— 5 0 0 8 ( 2 0 1 3 ) 0 8— 0 0 5 3— 0 2
REA S ON OF HOLE 0N S PHD
t he ba s e p l a t e c a n no t be c on t i n uo u s l y de f or me d;a n ot h e r r e a s o n i s t ha t i f r a w p l a t e i s n o r ma l ,t he n r o l l e r c o n— t a c t i n g wi t h s t r i p s t e e l i n p i c k l i n g a nd r o l l i ng l i ne wo ul d c u t s ma l l h ol e s i n r a w pl a t e a n d t h e s e s ma l l ho l e s wou l d f o r m l a r ge r h o l e s wh e n s t 6p s t e e l i s r o l l e d i n mi l 1 . So me me a s u r es p r op os e d.
- 1、下载文档前请自行甄别文档内容的完整性,平台不提供额外的编辑、内容补充、找答案等附加服务。
- 2、"仅部分预览"的文档,不可在线预览部分如存在完整性等问题,可反馈申请退款(可完整预览的文档不适用该条件!)。
- 3、如文档侵犯您的权益,请联系客服反馈,我们会尽快为您处理(人工客服工作时间:9:00-18:30)。
热轧带钢孔洞缺陷的形成原因与控制措
施
摘要:随着国内粗钢产能日益过剩,各大钢铁企业都在关注高品质、高附加值产品,这使得连铸坯洁净度受到高度重视。
连铸坯中的大型夹杂物会引起后序热轧、冷轧过程引起孔洞、起皮、线形缺陷等带钢表面缺陷,进而降低成品收得率,增加钢铁企业的生产成本。
本文针对孔洞缺陷进行分析,并提出了优化改进的措施。
关键词:热轧带钢;孔洞;缺陷
引言
由于热轧带钢优异的性能,在建筑结构、机械加工、航空航天等领域具有广阔的应用前景。
热轧带钢过程中或经历长期使用后,受自身材料特性、加工工艺和环境条件等因素影响可能会导致热轧带钢产生孔洞等缺陷,孔洞缺陷的出现会降低钢结构强度、刚度、稳定性以及耐腐蚀等性能,对整个钢结构使用性能和寿命产生严重影响,造成巨大安全隐患。
因此研究热轧带钢孔洞缺陷的形成原因与控制措施,对促进热轧带钢的发展具有重要意义。
1热轧带钢孔洞缺陷的形成原因
某厂生产的热轧带钢在灭火器、空调压缩机罐体、钢桶、焊丝及轮毂的应用上,频繁出现孔洞类质量缺陷,带来较大的损失。
根据夹杂孔洞的成分特征,可能来源于内壁结瘤物的脱落、钢包精炼渣、中包覆盖剂、结晶器保护渣的卷入以及钢水的二次氧化等。
根据钢水夹杂物成分分布特征,对可能卷入钢包精炼渣、中包渣、结晶器保护渣的成分分布特征做对比分析。
钢包精炼渣的主要成分是CaO和Al2O3,以及少量的SiO2、MgO,其中碱度控制在24~28,CaO/Al2O3为1.65~1.93。
可见,其主要成
分分布与成品钢卷缺陷处检测到的主要成分明显不同。
中间包下层覆盖剂主要成分是CaO、Al2O3和少量MgO、SiO2,碱度达到10,上层酸性覆盖剂基本为SiO2,其次是Al2O3,此外还有少量的MgO和CaO,基本呈酸性。
两者均含有少量的Na2O,可见Na并不是结晶器保护渣的特征元素,成品中的含Na的夹杂物也有可能是中包渣卷入导致的。
整体来看,成品孔洞处缺陷成分与中包覆盖剂成分差异较大。
结晶器保护渣的主要成分是CaO和SiO2,另外还有相当含量的MgO和Al2O3,Na2O 的含量也将近10%。
此成分组成也与孔洞处夹杂物成分差异较大。
出现夹杂类孔洞炉次连铸过程Als损失平均为30ppm,控制在60ppm以内的过程能力指数Cpk为1.06,孔洞处夹杂物成分未发现纯的Al2O3,保护浇注基本正常。
因此,连铸二次氧化不是导致成品钢卷出现大型夹杂的主要原因。
由以上分析可知,成品钢卷上的孔洞类缺陷处夹杂物成分分布特征与钢包精炼渣、中包覆盖剂、结晶器保护渣相比存在显著差异,排除其直接卷入可能。
连铸过程Als 损失均小于50ppm,处于正常范围内,孔洞夹杂也没有发现单纯的Al2O3夹杂,可排除连铸过程直接二次氧化导致的可能。
从与内壁附着物成分的对比来看,二者基本组成非常相似。
因此,可以看出,成品带钢上孔洞处的夹杂主要来源于内壁附着物在浇注过程中的脱落钢水在浇注过程中,非金属夹杂逐渐在内壁的吸附、长大、脱落,如在结晶器中未上浮而被凝固坯壳捕获则铸坯中形成大型夹杂物,进而在成品钢卷中出现孔洞缺陷。
2热轧带钢孔洞缺陷控制措施
在这些孔洞夹杂的检测中,除了钙铝酸盐,还发现了引流砂成分Cr,保护渣成分F、Na,以及较高含量的MgO,这说明结瘤物部分混合了保护渣、钢包渣、中包渣等杂质。
因此,要控制好低碳钢成品钢卷的夹杂类缺陷,首先要控制好钢包Al脱氧产物的变性和去除,防止其在内壁的富集,还要控制好中间包、结晶器的卷渣。
孔洞处检测出的夹杂物中的Cr2O3应来源于引流砂,高含量的MgO应来源于中间包耐火材料的侵蚀,二者均应在中间内上浮去除,但钢卷中存在此类物质表明存在引流砂、中包耐火材料的卷入。
连铸中间包物理模拟的流场特征显示中间包内存在短路流现象。
钢水从钢包长水口浇注到冲击区后,沿中包底部直接流向
浸入式水口,这种流动将导致钢水中卷入的中间包耐火材料、引流砂等上浮时间不足而直接进入结晶器。
比向减小方向移动;另一方面钢水吸氧,钢水增加,就可使反应向着生成液相区边界移动,生成大量高熔点的xCaO·yAl2O3夹杂物。
因此,连铸工序需进一步做好二次氧化的控制。
检测结果表明结晶器保护渣直接卷入导致大型夹杂的可能性不大,但检测出的部分含有Na、Zr的氧化物成分表明,仍有少量保护渣被卷入结晶器中。
目前连铸过程存在两个主要频率的波动,一种是鼓肚导致的,频率为0.4~0.5Hz,结合拉速计算波长为200mm左右,为扇形段的辊间距,需要强化扇形段的二次冷却;另一种是钢水流动导致的,频率为1.2~1.6Hz,波长约为70mm,与结晶器内钢水自由流动相关,可通过优化塞棒动作控制程序、塞棒抗鼓肚模型进行控制。
连铸过程保护浇注、优化覆盖剂的成分性能减少二次氧化,采取满包操作、优化中间包的流场,降低结晶器内的钢水流动强度、降低结晶器的液面波动等措施,
综合判定业务是系统对尺表观、成分、性能及过程分类检验项目进行再次集成,并辅助强制性尺寸最大值及最小值、尺寸公称差异项目的检验,对带钢所有生产过程状态进行直观监控,并集合所有检验分流程结果对带钢做出综合判定结果,赋予带钢实时质量状态,指定后续流向。
综合判定界面在信息化系统中的集成主要由带钢信息列表、检验特征值、家族质量日志、综合判定结果等组成。
带钢信息列表包含了生产时间、带钢号、板坯号、产出工序、生产步骤类型、评审状态、上工序判定钢种、计划出口钢种及标准、公称厚度及宽度、性能取样个数、进线卷标志、表面质量等级、表面判定结果、成分判定状态、性能判定状态、过程判定状态、备注信息、返工信息、订单主要信息等列项目,可对各分过程判定状态、对订单特殊要求信息进行获取。
检验特征值是对尺表观、成分、性能、过程工艺监控状态的整体集成,进一步加强检验的直观性及可靠性。
家族质量日志包含了带钢从铸坯产出到带钢发货过程中上下工序全流程的判定内容,可实现工序间重要信息的传递,进一步加强综合质量的判定。
如何保证实际质量与新订单要求匹配恰当进而实现效益的最大化,已成为企业质量管理工作中的重点。
开发余材换单及改降判产品重新挂单后的再次质量检查模块,把一次判定流程与再换单流程进行重新整合,对再换单质量检
验再次形成全流程的管控,保证出厂质量,有效减少不合格产品的流出及提高实际质量与订单质量要求的匹配程度。
结束语
炼钢厂生产技术人员对于生产用原料,除了要控制夹杂物的形态和大小外,还应该研究夹杂物的分布,避免夹杂物的集中和聚集。
为改善日钢热轧带钢大尺寸夹杂导致的孔洞缺陷,通过提高Ca处理深度以减少钙铝酸盐夹杂在内壁的聚集,优化中间包流场以促进夹杂物的碰撞、长大及上浮去除,优化中间包覆盖剂的成分及操作以减少二次氧化。
针对不同原因导致结晶器液面波动,制定相应的控制措施以防止保护渣的卷入。
参考文献:
[1]杨光.热轧中牌号硅钢边部线状缺陷机理与实验研究[D].燕山大学,2021.
[2]王鹏建.热轧带钢异物压入缺陷分析及改进措施[J].金属世
界,2021(01):54-57.
[3]何永全.热轧带钢免酸洗还原热镀锌工艺研究与应用[D].东北大学,2015.
[4]黄其义.热轧带钢异物压入缺陷分析及改进措施[J].金属材料与冶金工程,2015,43(02):22-24.
[5]孙明军,夏小明,穆海玲.热轧软质镀锡原板的开发及质量改进[J].上海金属,2014,36(06):54-57+61.。