PCB失效分析技术与案例
PCB上发生的离子迁移失效案例
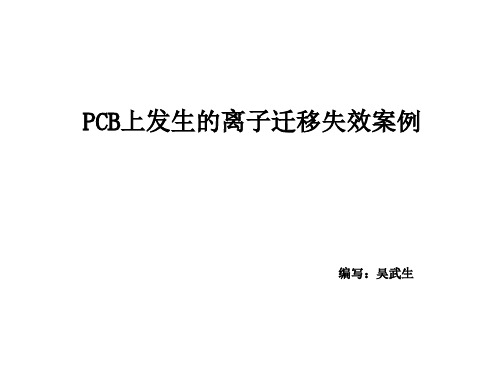
四、不良品SEM&EDS分析总结
从SEM&EDS分析结果看,两个放静电焊盘之间有枝蔓状的残留物残留,并且残留物主 要元素为碳,氧,溴,氯,硫,银等;根据元素分析结果,我司判断此不良现象为表面银离 子迁移造成的结果,放静电焊盘之间的残留物为助焊剂残留物,是造成银离子迁移的前提条 件。后面,会进一步解释下此结论的原因。
三、不良品SEM&EDS分析---测试区域
测试区域
SEM图:测试区域基本覆盖整条残留物
三、不良品SEM&EDS分析---测试区域1
测试区域1
测试结果:枝蔓状残留物的主要元素有 碳,氧,溴,氯,硫,银等
三、不良品SEM&EDS分析---测试区域2
测试区域2
测试结果:枝蔓状残留物的主要元素有 碳,氧,溴,氯,硫,银等; 其中第2点分析位置处于焊盘区域,主要元素有碳,氧,铜,银,属于正常元素分布。
放静电焊盘失效区域二不良品分析前面省略锁定失效位置的分析在对放静电焊盘位置进行eds分析确定残留物前我司先将背面铜箔剥掉使用显微镜再次确认放静电焊盘之间是否有残留物图片如下
PCB上发生的离子迁移失效案例
编写:吴武生
一、背景
客户抱怨某汽车产品有11台按键无作用通过现场分析,确认按键失效,对地测量有阻值,断 电切割线路后微短现象消失,初步怀疑放静电焊盘位置有助焊剂残留。Leabharlann 失效区域放静电焊盘
PCB的CAF测试失效分析案例
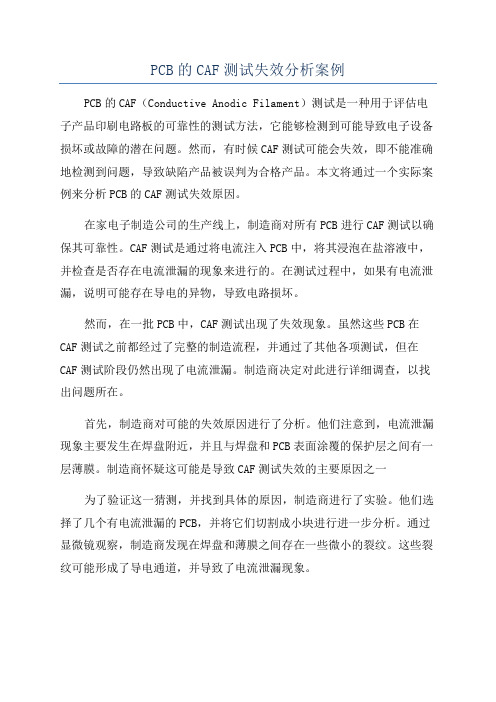
PCB的CAF测试失效分析案例PCB的CAF(Conductive Anodic Filament)测试是一种用于评估电子产品印刷电路板的可靠性的测试方法,它能够检测到可能导致电子设备损坏或故障的潜在问题。
然而,有时候CAF测试可能会失效,即不能准确地检测到问题,导致缺陷产品被误判为合格产品。
本文将通过一个实际案例来分析PCB的CAF测试失效原因。
在家电子制造公司的生产线上,制造商对所有PCB进行CAF测试以确保其可靠性。
CAF测试是通过将电流注入PCB中,将其浸泡在盐溶液中,并检查是否存在电流泄漏的现象来进行的。
在测试过程中,如果有电流泄漏,说明可能存在导电的异物,导致电路损坏。
然而,在一批PCB中,CAF测试出现了失效现象。
虽然这些PCB在CAF测试之前都经过了完整的制造流程,并通过了其他各项测试,但在CAF测试阶段仍然出现了电流泄漏。
制造商决定对此进行详细调查,以找出问题所在。
首先,制造商对可能的失效原因进行了分析。
他们注意到,电流泄漏现象主要发生在焊盘附近,并且与焊盘和PCB表面涂覆的保护层之间有一层薄膜。
制造商怀疑这可能是导致CAF测试失效的主要原因之一为了验证这一猜测,并找到具体的原因,制造商进行了实验。
他们选择了几个有电流泄漏的PCB,并将它们切割成小块进行进一步分析。
通过显微镜观察,制造商发现在焊盘和薄膜之间存在一些微小的裂纹。
这些裂纹可能形成了导电通道,并导致了电流泄漏现象。
为了进一步验证,制造商还进行了材料分析。
通过对薄膜的成分进行分析,制造商发现薄膜中掺有一种对电导率较敏感的材料。
这些材料可能在制造过程中被不慎混入,导致了薄膜在CAF测试中失效。
综合以上分析结果,制造商得出结论,PCB的CAF测试失效是由于焊盘附近的薄膜存在裂纹,并含有导电材料引起的。
制造商进一步调整了制造过程,增强了焊盘附近薄膜的耐压性,并加强了对材料的筛选和控制,以确保不会再次出现类似问题。
通过这个案例,我们可以看到CAF测试失效的原因可能是多方面的,可能与制造过程中的材料问题、设计问题或操作问题有关。
失效分析典型案例分享--镍腐蚀
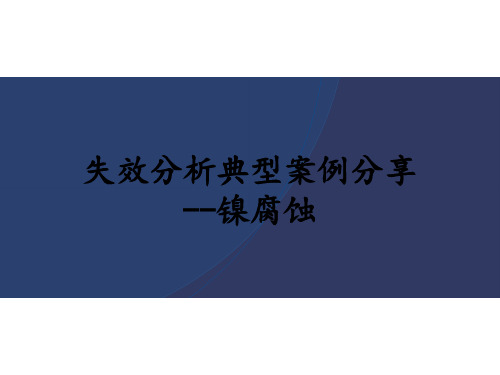
沉锡
沉银
无铅喷锡
(Immersion Tin) (Immersion silver) (Lead free HASL)
OSP
在电路板裸铜表面 在电路板裸铜表 在电路板裸铜表 在电路板裸铜表面 沉积形成一层平整 面经化学置换反 面经化学置换反 经热风整平形成一 而致密的有机覆盖 应形成一层洁白 应形成一层洁白 层较光亮而致密的 层,厚度约0.2而致密的锡镀层, 而致密的银镀层, 无铅覆盖锡合金层, 0.6um,既可保护 厚度约0.7-1.2um。 厚度约0.15-0.4um。 厚度约1-40um。 铜面,又可保证焊
表面易被污染而 影响焊接性能
表面易被污染,银 面容易变色,从而 影响焊接性能和外 观
表面处理温度高, 可能会影响板材和 阻焊油墨的性能
表面在保存环境差 的情况下易出现 OSP膜变色,焊接 不良等
电镍金后还经 过多道后工序, 表面处理后若 受到污染易产 生焊接不良
成本很高
完成沉锡表面处 理后如再受到高 温烘板或停放时 间较长,则可导 致沉锡层的减少
u
Pu
Pu
Pu
P uP
Pu P
uP
Pu P
u
u
Ni
Ni P
Ni
Ni
Ni
P
Ni
Ni
Ni P
Ni Ni
Ni P
Ni
Ni
Ni
P
Ni
富磷层
Ni
Ni P
Ni
Ni
Ni P
Ni
Ni
Ni
PCB失效分析介绍
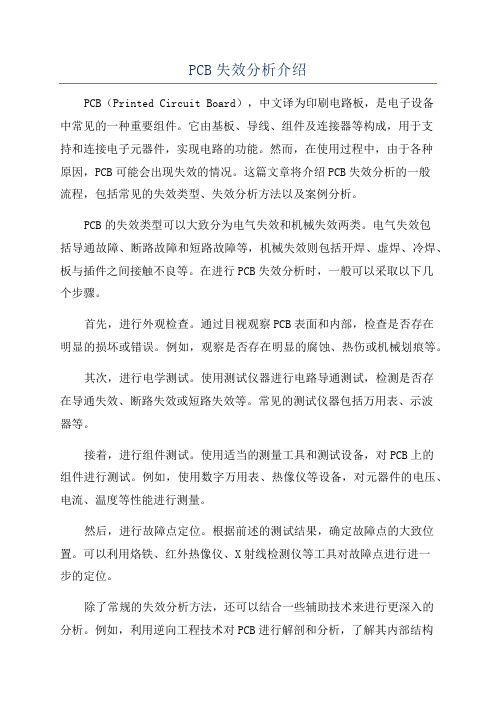
PCB失效分析介绍PCB(Printed Circuit Board),中文译为印刷电路板,是电子设备中常见的一种重要组件。
它由基板、导线、组件及连接器等构成,用于支持和连接电子元器件,实现电路的功能。
然而,在使用过程中,由于各种原因,PCB可能会出现失效的情况。
这篇文章将介绍PCB失效分析的一般流程,包括常见的失效类型、失效分析方法以及案例分析。
PCB的失效类型可以大致分为电气失效和机械失效两类。
电气失效包括导通故障、断路故障和短路故障等,机械失效则包括开焊、虚焊、冷焊、板与插件之间接触不良等。
在进行PCB失效分析时,一般可以采取以下几个步骤。
首先,进行外观检查。
通过目视观察PCB表面和内部,检查是否存在明显的损坏或错误。
例如,观察是否存在明显的腐蚀、热伤或机械划痕等。
其次,进行电学测试。
使用测试仪器进行电路导通测试,检测是否存在导通失效、断路失效或短路失效等。
常见的测试仪器包括万用表、示波器等。
接着,进行组件测试。
使用适当的测量工具和测试设备,对PCB上的组件进行测试。
例如,使用数字万用表、热像仪等设备,对元器件的电压、电流、温度等性能进行测量。
然后,进行故障点定位。
根据前述的测试结果,确定故障点的大致位置。
可以利用烙铁、红外热像仪、X射线检测仪等工具对故障点进行进一步的定位。
除了常规的失效分析方法,还可以结合一些辅助技术来进行更深入的分析。
例如,利用逆向工程技术对PCB进行解剖和分析,了解其内部结构和材料组成。
同时,还可以利用红外热像仪、X射线检测仪等高级测试设备,对PCB进行非破坏性测试,以获取更全面的信息。
下面以一个实际案例进行PCB失效分析。
电子设备中的一个PCB上的一些电路失效,导致整个设备无法正常运行。
通过外观检查发现,该PCB表面没有明显的损坏,但观察到一些插件的焊点存在异常。
接着,进行电学测试。
使用示波器进行导通测试,发现在该焊点附近存在断路失效。
然后,进行组件测试,发现焊点附近的元器件没有明显的故障。
第五章 PCB质量保证及失效案例分析
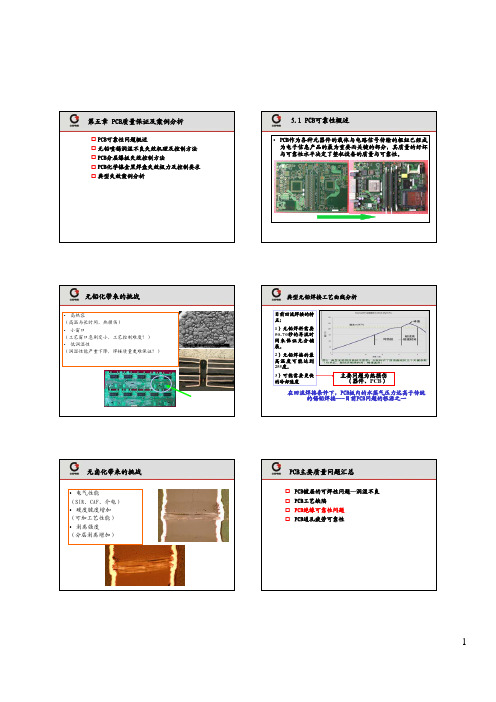
5.3.2 PCB化学镍金(ENIG)失效机理及控制
黑焊盘的由来
ENIG最为PCB和BGA封装基板焊盘表面处理,主要用来防止Cu焊盘 的氧化,并得到可焊接的表面。黑盘是和ENIG处理的相关失效。 在元件组装过程中,焊料对焊盘不润湿,不润湿的焊盘会显著变 黑---黑盘的最初来源。 牙签试验 机械性能测试
PCB润湿不良的分类及原因
润湿不良的原因
不润湿: 焊盘严重氧化(通常表面处理工艺有关系) 焊盘受到有机物等污染 焊盘表面存在杂志膜(如不可焊的白油)等物质
反润湿: 焊盘氧化: 焊盘表面处理异常(HASL和ENIG)
注:反润湿和不润湿的最大区别在于直接接触面的可焊性存在差异。
PCB焊盘润湿不良照片
润湿不良分析方法
案例2 PCB短路开路
1 样品描述:所送5种型号的PCB有开路和短路现象。
分析结论
1)PCB电镀工艺不良是过孔开路的主要原因。 2)PCB基材(包含外层粘接材料和内层芯板粘接材 料)PTE偏大,会进一步加剧过孔开路。
2 外观检查
相邻导线 由于铜箔 相连造成 短路
2
2 外观检查
炭膜相连导致短路 3 分析结论
结论: 镍层扩散至金镀层浅表面而氧化以及镍层存在较严重的裂 缝降低了PCB焊盘的可焊性,从而导致焊盘上锡不良。
案例8 PCB焊盘氧化腐蚀导致器件脱落案例
样品外观照片及脱落后焊盘照片
1)金部分未溶解 2)存在锡元素
SEM&EDS分析
未脱落的焊点金相分析 1)存在润湿不良 2)镍层存在腐蚀
SEM&EDS分析
PCB失效分析技术及解决方案
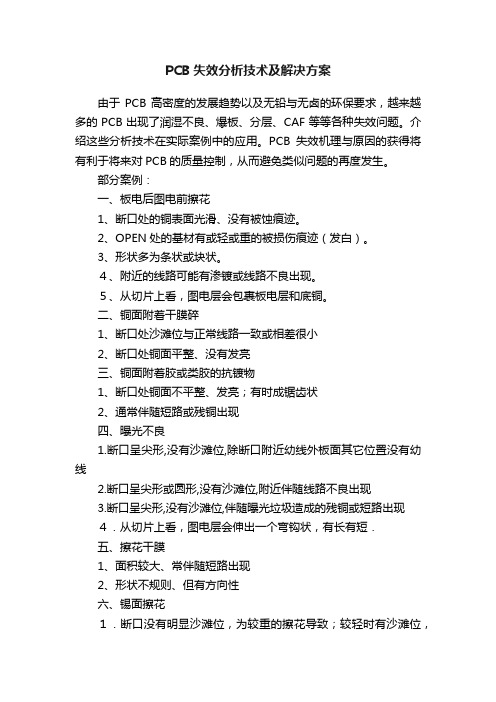
PCB失效分析技术及解决方案由于PCB高密度的发展趋势以及无铅与无卤的环保要求,越来越多的PCB出现了润湿不良、爆板、分层、CAF等等各种失效问题。
介绍这些分析技术在实际案例中的应用。
PCB失效机理与原因的获得将有利于将来对PCB的质量控制,从而避免类似问题的再度发生。
部分案例:一、板电后图电前擦花1、断口处的铜表面光滑、没有被蚀痕迹。
2、OPEN处的基材有或轻或重的被损伤痕迹(发白)。
3、形状多为条状或块状。
4、附近的线路可能有渗镀或线路不良出现。
5、从切片上看,图电层会包裹板电层和底铜。
二、铜面附着干膜碎1、断口处沙滩位与正常线路一致或相差很小2、断口处铜面平整、没有发亮三、铜面附着胶或类胶的抗镀物1、断口处铜面不平整、发亮;有时成锯齿状2、通常伴随短路或残铜出现四、曝光不良1.断口呈尖形,没有沙滩位,除断口附近幼线外板面其它位置没有幼线2.断口呈尖形或圆形,没有沙滩位,附近伴随线路不良出现3.断口呈尖形,没有沙滩位,伴随曝光垃圾造成的残铜或短路出现4.从切片上看,图电层会伸出一个弯钩状,有长有短.五、擦花干膜1、面积较大、常伴随短路出现2、形状不规则、但有方向性六、锡面擦花1.断口没有明显沙滩位,为较重的擦花导致;较轻时有沙滩位,或没有蚀穿.2.从切片上看,被蚀处较为圆滑,有平缓的坡度,沙滩位较大。
七、溶锡或电锡不良八、显影不净1、较少发生、一般面积较大2、断口及附近线路边缘发亮,九、图电后擦花切片图1、图电后的擦花,一般擦花处的基材和铜面都较为粗糙,基材上会有铜粒,擦花的线路处会有明显被擦花的痕迹,线路边会有顺着擦花方向的突出。
2、从切片上看,擦花处的线路会被压向基材方向,有明显的弯曲。
(公众号:电子汇)十、甩膜干膜余胶导致的线路不良1、干膜余胶造成的线路不良,基材位不会有残铜。
2、线路不良处底部一般都非常平整,会露出铜的颜色,与周围线路的颜色不一样。
3、从切片上看,线路不良处板电层和底铜完整,但镀不上二铜,周围的图电层有一个包裹的动作。
PCB通孔焊接不良失效分析

PCB 通孔焊接不良失效分析美信检测 失效分析实验室摘要:本文通过外观检查,可焊性测试,焊点表面分析,焊点剖面分析,剥金检查等分析手段,分析导致化镍浸金通孔润湿不良的原因为镍层质量较差,存在严重的镍腐蚀。
关键词:通孔焊接不良 润湿不良 PCB 焊接不良 PCBA 焊接不良 化镍浸金 ENIG 镍层腐蚀1. 案例背景PCB 组装过程正发生通孔焊盘润湿不良,润湿不良位置主要集中在焊盘较窄部位。
2. 分析方法简述对NG 样品进行外观检查,问题焊点颜色异常区域润湿不良,润湿不良区域显示黑色。
图1.NG 样品焊点外观照片(10X/20X ) 图2. PCB 光板可焊性测试照片(10X) 利用SEM/EDS 对NG 样品问题焊点润湿不良区域表面进行分析,发现Au 层已经完全溶入焊料中,焊盘表面未形成足够的金属间化合物,镍层晶间腐蚀清晰可见,氧元素的存在说明镍层表面可能受到了氧的侵蚀。
失效区域图3. NG 样品问题焊点SEM/EDS 测试和谱图对NG 样品问题焊点剖面进行分析,异常区域存在明显的不润湿,焊料在焊盘上的润湿角大于等于90°,这明显不符合可接受要求。
不润湿区域的焊盘表面未生成明显的金属间化合物层,无法形成有效的连接,导致这种现象的根本原因在于焊盘镍层腐蚀、氧化严重。
此外,问题焊点的镍镀层质量较差,存在缝隙或裂纹,正常焊点则不存在明显的腐蚀裂纹,这已经在剖面观察中得到证实。
图4.NG 样品问题焊点切片后SEM 图片 图5. PCB 空板窄焊盘SEM/EDS 测试对PCB 空板焊盘进行剥金检查,检查结果表明镍层表面普遍存在明显的腐蚀,窄焊盘的腐蚀程度明显要比宽焊盘严重。
需要进一步指出的是,镍层腐蚀不会导致焊盘完全不润湿,因为化镍金工艺过程中镍层的腐蚀、氧化几乎不可避免,只有当镍层表面腐蚀、氧化达到一定程度时才会出现拒焊或出现部分不润湿现象。
3.讨论及结论1) 外观观察表明问题焊点黑色区域润湿不良;谱图22)可焊性测试结果表明个别焊盘存在润湿不良现象;3)通过切片和焊点表面分析可知,润湿不良区域焊盘表面的金层已经溶解,但镍层表面未形成明显的金属间化合物;镍层质量较差,存在严重的镍腐蚀。
PCB失效原因与案例分析
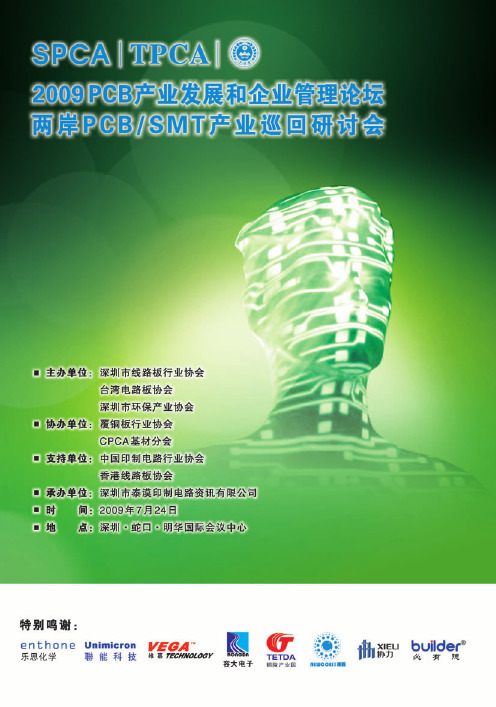
84
深圳市线路板行业协会--台湾电路板协会
2009年7月24日
2009PCB产业论坛
2.7 能谱分析
主要用途
•焊盘表面或截面成分分析 •可焊性不良的焊盘表面污 染物的元素分析
FPC-pad镍镀层开裂分析
SEM
Ni 层
EDS
Reliability Makes Classic
信息产业部电子信息产品污染防治标准工作组 ‘限量与检测方法’项目组牵头负责人
国家有害物质检测方法标准委员会(TC297/SC-3) 副主任委员
中国电子学会SMT专家咨询委员会委员 国家焊接标委会委员(TC55/SC2)
Reliability Makes Classic
PCB作为各种元器件的载体与电路信号传输的枢纽已经成 为电子信息产品的最为重要而关键的部分,其质量的好坏 与可靠性水平决定了整机设备的质量与可靠性。
Reliability Makes Classic
1.1 无铅化带来的挑战
高热容 (高温与长时间,热损伤) 小窗口 (工艺窗口急剧变小,工艺控制难度?) 低润湿性 (润湿性能严重下降,焊接质量更难保证?)
Reliability Makes Classic
外观检测分析的案例
Reliability Makes Classic
78
深圳市线路板行业协会--台湾电路板协会
2009年7月24日
联能科技(深圳)有限公司(板厂)
南京协力多层电路板有限公司(飞针测试)
确信电子—乐思化学(化学药水)
安徽省铜陵经济技术开发区 PCB 产业园(产业园)
日 期:2009 年 7 月 24 日(星期五)
PCB失效分析技术与典型案例

视系统来检查。X 光透视系统就是利用不同材料厚度或是不同材料密度对 X 光的吸湿或透过率的不 同原理来成像。该技术更多地用来检查 PCBA 焊点内部的缺陷、通孔内部缺陷和高密度封装的 BGA 或 CSP 器件的缺陷焊点的定位。目前的工业 X 光透视设备的分辨率可以达到一个微米以下,并正由 二维向三维成像的设备转变,甚至已经有五维(5D)的设备用于封装的检查,但是这种 5D 的 X 光 透视系统非常贵重,很少在工业界有实际的应用。
前言 PCB 作为各种元器件的载体与电路信号传输的枢纽已经成为电子信息产品的最为重要而关键
的部分,其质量的好坏与可靠性水平决定了整机设备的质量与可靠性。随着电子信息产品的小型化 以及无铅无卤化的环保要求,PCB 也向高密度高 Tg 以及环保的方向发展。但是由于成本以及技术 的原因,PCB 在生产和应用过程中出现了大量的失效问题,并因此引发了许多的质量纠纷。为了弄 清楚失效的原因以便找到解决问题的办法和分清责任,必须对所发生的失效案例进行失效分析。本 文将讨论和介绍一部分常用的失效分析技术,同时介绍一些典型的案例。
综合上述分析可知,PP 层粘接材料的局部固化不足,增大了 PCB 在高温强热中所受的的应力, 外层铜箔与 PP 层树脂结合力不足, 降低了铜箔与树脂之间的结合强度, 而这些均与板的层压工及艺 粘接材料的性能相关。 PCB 板吸潮又严重降低了 PCB 的耐热性能,使得 PCB 在过回流焊中水份急剧 汽化导致出现爆板分层失效现象。 结论
1.1 外观检查 外观检查,就是目测或利用一些简单仪器,如立体显微镜、金相显微镜甚至放大镜等工具检查
PCB 的外观,寻找失效的部位和相关的物证,主要的作用就是失效定位和初步判断 PCB 的失效模式 。 外观检查主要检查 PCB 的污染、腐蚀、爆板的位置、电路布线以及失效的规律性,如是批次的或是 个别,是不是总是集中在某个区域等等。另外,有许多 PCB 的失效是在组装成 PCBA 后才发现,是 不是组装工艺过程以及过程所用材料的影响导致的失效也需要仔细检查失效区域的特征。
PCB失效分析技术总结及实用案例分享
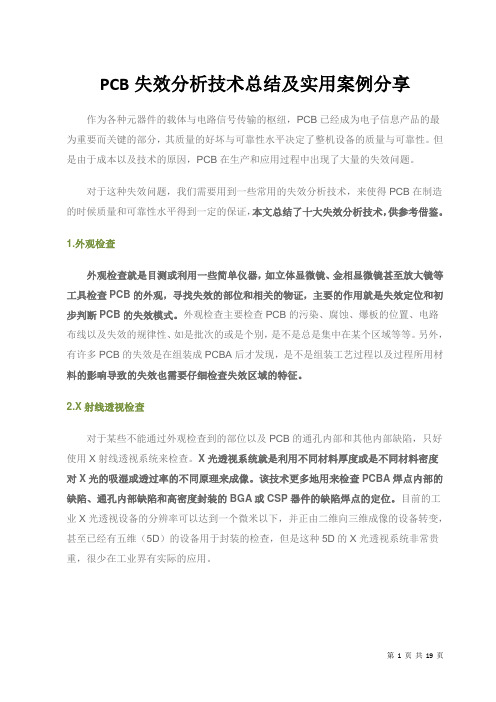
PCB失效分析技术总结及实用案例分享作为各种元器件的载体与电路信号传输的枢纽,PCB已经成为电子信息产品的最为重要而关键的部分,其质量的好坏与可靠性水平决定了整机设备的质量与可靠性。
但是由于成本以及技术的原因,PCB在生产和应用过程中出现了大量的失效问题。
对于这种失效问题,我们需要用到一些常用的失效分析技术,来使得PCB在制造的时候质量和可靠性水平得到一定的保证,本文总结了十大失效分析技术,供参考借鉴。
1.外观检查外观检查就是目测或利用一些简单仪器,如立体显微镜、金相显微镜甚至放大镜等工具检查PCB的外观,寻找失效的部位和相关的物证,主要的作用就是失效定位和初步判断PCB的失效模式。
外观检查主要检查PCB的污染、腐蚀、爆板的位置、电路布线以及失效的规律性、如是批次的或是个别,是不是总是集中在某个区域等等。
另外,有许多PCB的失效是在组装成PCBA后才发现,是不是组装工艺过程以及过程所用材料的影响导致的失效也需要仔细检查失效区域的特征。
2.X射线透视检查对于某些不能通过外观检查到的部位以及PCB的通孔内部和其他内部缺陷,只好使用X射线透视系统来检查。
X光透视系统就是利用不同材料厚度或是不同材料密度对X光的吸湿或透过率的不同原理来成像。
该技术更多地用来检查PCBA焊点内部的缺陷、通孔内部缺陷和高密度封装的BGA或CSP器件的缺陷焊点的定位。
目前的工业X光透视设备的分辨率可以达到一个微米以下,并正由二维向三维成像的设备转变,甚至已经有五维(5D)的设备用于封装的检查,但是这种5D的X光透视系统非常贵重,很少在工业界有实际的应用。
3.切片分析切片分析就是通过取样、镶嵌、切片、抛磨、腐蚀、观察等一系列手段和步骤获得PCB横截面结构的过程。
通过切片分析可以得到反映PCB(通孔、镀层等)质量的微观结构的丰富信息,为下一步的质量改进提供很好的依据。
但是该方法是破坏性的,一旦进行了切片,样品就必然遭到破坏;同时该方法制样要求高,制样耗时也较长,需要训练有素的技术人员来完成。
无铅PCB坑裂失效案例
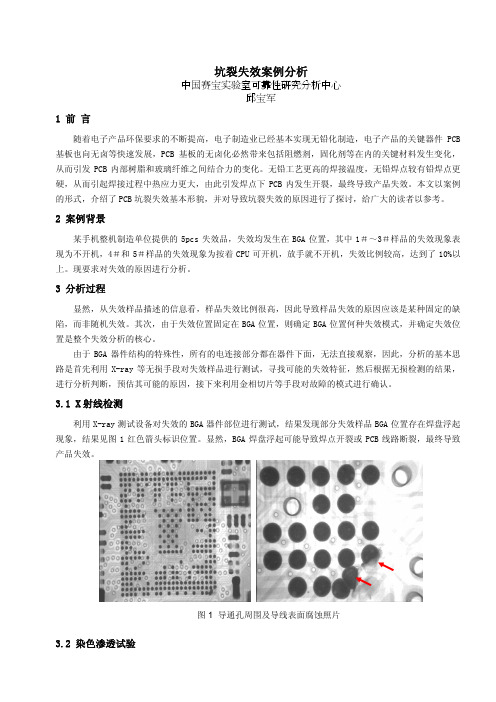
坑裂失效案例分析中国赛宝实验室可靠性研究分析中心邱宝军1 前 言随着电子产品环保要求的不断提高,电子制造业已经基本实现无铅化制造,电子产品的关键器件PCB 基板也向无卤等快速发展,PCB基板的无卤化必然带来包括阻燃剂,固化剂等在内的关键材料发生变化,从而引发PCB内部树脂和玻璃纤维之间结合力的变化。
无铅工艺更高的焊接温度,无铅焊点较有铅焊点更硬,从而引起焊接过程中热应力更大,由此引发焊点下PCB内发生开裂,最终导致产品失效。
本文以案例的形式,介绍了PCB坑裂失效基本形貌,并对导致坑裂失效的原因进行了探讨,给广大的读者以参考。
2 案例背景某手机整机制造单位提供的5pcs失效品,失效均发生在BGA位置,其中1#~3#样品的失效现象表现为不开机,4#和5#样品的失效现象为按着CPU可开机,放手就不开机,失效比例较高,达到了10%以上。
现要求对失效的原因进行分析。
3 分析过程显然,从失效样品描述的信息看,样品失效比例很高,因此导致样品失效的原因应该是某种固定的缺陷,而非随机失效。
其次,由于失效位置固定在BGA位置,则确定BGA位置何种失效模式,并确定失效位置是整个失效分析的核心。
由于BGA器件结构的特殊性,所有的电连接部分都在器件下面,无法直接观察,因此,分析的基本思路是首先利用X-ray等无损手段对失效样品进行测试,寻找可能的失效特征,然后根据无损检测的结果,进行分析判断,预估其可能的原因,接下来利用金相切片等手段对故障的模式进行确认。
3.1 X射线检测利用X-ray测试设备对失效的BGA器件部位进行测试,结果发现部分失效样品BGA位置存在焊盘浮起现象,结果见图1红色箭头标识位置。
显然,BGA焊盘浮起可能导致焊点开裂或PCB线路断裂,最终导致产品失效。
图1 导通孔周围及导线表面腐蚀照片3.2 染色渗透试验对1#失效品的BGA焊点进行染色渗透试验。
试验后分离器件与PCB,观察发现:大量的焊点存在明显的染色渗透现象。
PCB上发生的离子迁移失效案例
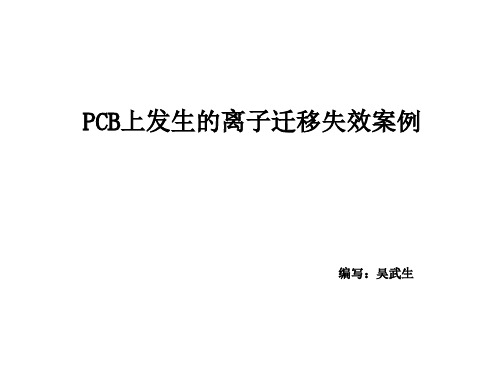
未剥铜前显微镜检查
剥铜后显微镜检查
图中发亮的区域是两个焊盘间的基材区,在 显微镜下明显可以观察到残留物,下一步针 对该物质做SEM&EDS分析;
三、不良品SEM&EDS分析---测试区域
测试区域
SEM图:测试区域基本覆盖整条残留物
三、不良品SEM&EDS分析---测试区域1
测试区域1
测试结果:枝蔓状残留物的主要元素有 碳,氧,溴,氯,硫,银等源自PCB上发生的离子迁移失效案例
编写:吴武生
一、背景
客户抱怨某汽车产品有11台按键无作用通过现场分析,确认按键失效,对地测量有阻值,断 电切割线路后微短现象消失,初步怀疑放静电焊盘位置有助焊剂残留。
失效区域
放静电焊盘
二、不良品分析
前面省略锁定失效位置的分析,在对放静电焊盘位置进行EDS分析确定残留物前,我司先将背 面铜箔剥掉,使用显微镜再次确认放静电焊盘之间是否有残留物,图片如下:
三、不良品SEM&EDS分析---测试区域2
测试区域2
测试结果:枝蔓状残留物的主要元素有 碳,氧,溴,氯,硫,银等; 其中第2点分析位置处于焊盘区域,主要元素有碳,氧,铜,银,属于正常元素分布。
四、不良品SEM&EDS分析总结
从SEM&EDS分析结果看,两个放静电焊盘之间有枝蔓状的残留物残留,并且残留物主 要元素为碳,氧,溴,氯,硫,银等;根据元素分析结果,我司判断此不良现象为表面银离 子迁移造成的结果,放静电焊盘之间的残留物为助焊剂残留物,是造成银离子迁移的前提条 件。后面,会进一步解释下此结论的原因。
银迁移:银迁移(Silver Migration)现象是指在存在直流电压梯度的潮湿环境中,水分子渗入含 银导体表面电解形成氢离子和氢氧根离子:H20→H++OH银在电场及氢氧根离子的作用下,离解产生银离子; 在电场的作用下,银离子从高电位向低电位迁移,并形成絮状或枝蔓状扩展,在高低电位相 连的边界上形成黑色氧化银。
PCB失效原因与案例分析

PCB失效原因与案例分析PCB(Printed Circuit Board)是一种用于支持和连接电子组件的基板。
它是电子产品中最重要的组成部分之一,但由于各种原因,PCB也会出现失效的情况。
下面将从物理损坏、化学腐蚀以及设计和制造不良等角度分析PCB失效的原因,并列举一些相关的案例。
1.物理损坏物理损坏是导致PCB失效的主要原因之一、这种损坏可能由外部因素引起,例如机械压力、震动、温度变化等。
而且,也可能在制造和组装过程中造成,例如不正确的操作、错误的钳工行为等。
物理损坏可能导致PCB上电子元件的松动、脱落,以及电路轨迹断裂等失效现象。
案例1:一家制造商在PCB组装过程中不小心使用过于硬朗的工具,损坏了PCB上的电子元件。
这导致一些元件无法正常工作,最终导致整个电路板失效。
案例2:在运输过程中,由于未能妥善保护,PCB遭受了剧烈的撞击,导致电路轨迹断裂。
这使得PCB无法正常传递电流,导致整个电路板失效。
2.化学腐蚀化学腐蚀是导致PCB失效的另一个常见原因。
PCB会暴露在各种化学物质中,例如湿度、气体、液体等。
如果这些化学物质对PCB材料具有腐蚀性,它们会导致元件的氧化、腐蚀,甚至电路轨迹的腐蚀,从而导致电路板失效。
案例3:在一个潮湿的环境中,PCB上的金属电路轨迹开始发生氧化和腐蚀,导致电流无法正常传递,最终使整个电路板失效。
案例4:在一个工业环境中,PCB暴露在有害气体中,如硫化氢。
这导致PCB上的电子元件遭受腐蚀,损坏了电路的功能,从而导致PCB失效。
3.设计和制造不良设计和制造过程中的不良也是导致PCB失效的重要原因之一、设计不良可能导致电路板无法正常工作,例如布线错误、不正确的元件布局等。
制造不良可能导致电路板存在材料缺陷、焊接不良、导线间隙不正确、层间短路等问题,进而导致电路板失效。
案例5:在PCB设计中,布线人员错误地连接了两个电路轨迹,导致电流传输错误。
这导致PCB无法正常工作,最终导致整个电路板失效。
PCB短路失效分析
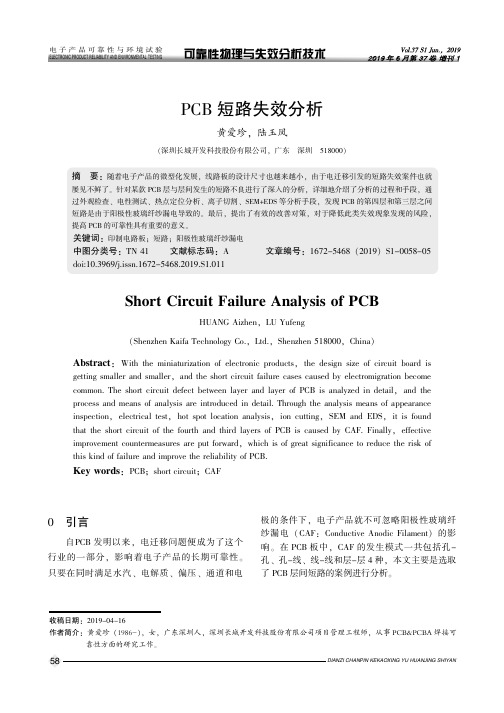
PCB 短路失效分析黄爱珍,陆玉凤(深圳长城开发科技股份有限公司,广东深圳518000)摘要:随着电子产品的微型化发展,线路板的设计尺寸也越来越小,由于电迁移引发的短路失效案件也就屡见不鲜了。
针对某款PCB 层与层间发生的短路不良进行了深入的分析,详细地介绍了分析的过程和手段,通过外观检查、电性测试、热点定位分析、离子切割、SEM+EDS 等分析手段,发现PCB 的第四层和第三层之间短路是由于阳极性玻璃纤纱漏电导致的。
最后,提出了有效的改善对策,对于降低此类失效现象发现的风险,提高PCB 的可靠性具有重要的意义。
关键词:印制电路板;短路;阳极性玻璃纤纱漏电中图分类号:TN 41文献标志码:A 文章编号:1672-5468(2019)S1-0058-05doi:10.3969/j.issn.1672-5468.2019.S1.011Short Circuit Failure Analysis of PCBHUANG Aizhen ,LU Yufeng(Shenzhen Kaifa Technology Co.,Ltd.,Shenzhen 518000,China )Abstract :With the miniaturization of electronic products ,the design size of circuit board isgetting smaller and smaller ,and the short circuit failure cases caused by electromigration become common.The short circuit defect between layer and layer of PCB is analyzed in detail ,and the process and means of analysis are introduced in detail.Through the analysis means of appearance inspection ,electrical test ,hot spot location analysis ,ion cutting ,SEM and EDS ,it is found that the short circuit of the fourth and third layers of PCB is caused by CAF.Finally ,effective improvement countermeasures are put forward ,which is of great significance to reduce the risk of this kind of failure and improve the reliability of PCB.Key words :PCB ;short circuit ;CAF收稿日期:2019-04-16作者简介:黄爱珍(1986-),女,广东深圳人,深圳长城开发科技股份有限公司项目管理工程师,从事PCB&PCBA 焊接可靠性方面的研究工作。
PCB(A)失效分析介绍
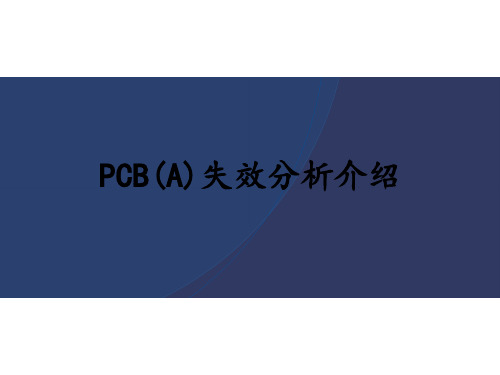
三、失效案例(2)
样品编号 区域1 区域4
线膨胀系数(ppm/℃)
≥Tg
265.6
≤Tg
52.43
≥Tg
254.7
≤Tg
62.17
50~260℃膨胀百分比(%) 4.167
3.887
测试样品 区域1 区域4
测试结果(℃) 317.09(5%质量损失,N2) 318.28(5%质量损失,N2)
备注:区域1为通孔相对密集区,区域4为通孔相对稀疏区。 其中铜孔密集区基板的热膨胀系数较铜孔稀疏区偏高,即前者比后者热膨胀量略大,这主 要是由于铜本身吸热、传导速度快,使得基板孔铜密集区接受热量相对较高导致。
•根据测试的需求,我们也可以用到前面提到的 更精密的仪器!
PCB(A)典型缺陷
三、失效案例(1)
NG样品爆板分层位置较集中,位于孔附近或样品边缘。爆板位置剥离 后表面平整,仅有少量树脂在爆板时被分离。
爆板分层主要发生在芯板和PP之间,断面平整,少量树脂附着于PP上, 部分位置存在芯板开裂现象。
三、失效案例(1)
失效分析流程
失效发生 失效样品保存
外观检查、电性能测 试
无损分析
内部分析
样品制备 定位失效点
物理分析 确定失效机理
纠正措施
搜集失效及环境信息 失效分析方案设计
应力试验分析
故障模拟分析
结果验证
二.仪器简介
外观检查 无损分析
体式显微镜、金相显微镜 X射线透视仪、CT、扫描声学显微镜(C-SAM)
性能分析
PCB(A)失效分析介绍
目录
一.失效分析定义 二.仪器简介 三.典型案例
一.失效分析定义
失效分析是一种事后分析手段,在开发、测试、小批 量试产,量产阶段及用户使用期间器件产生的失效问 题,通过使用各种测试分析技术和分析程序确认产品 的失效现象,分辨其失效模式或机理,确定其最 终的失效原因,提出在物料、设计、工艺等方面的改 进建议,来消除失效并防止失效的再次发生,提高产 品可靠性,它来自可靠性工程的一个重要组成部分。
PCB失效分析技术与案例

PCB失效分析技术与案例PCB(Printed Circuit Board,印刷电路板)作为电子产品的核心组成部分,承载着各种电子元件和连接线路,是电子产品正常运行的基础。
然而,由于各种原因,PCB可能会出现失效现象,例如电气失效、机械失效、热失效等。
本文将介绍几种常见的PCB失效分析技术以及相应的案例。
一、电气失效分析技术1.测试仪器:使用示波器、万用表、频谱分析仪等仪器对PCB进行电气特性分析,检测电气性能是否正常。
2.红外测试:使用红外线热像仪对PCB进行红外检测,查找异常发热点,判断是否存在热失效等问题。
3.焦耳热分析:通过加热PCB,利用焦耳热效应来检测是否有电气连接不良,或是电敏感元器件的温度分布不均等问题。
案例:电子产品的PCB在使用过程中发现频繁死机。
经过电气失效分析发现,其中一个芯片温度异常升高,通过焦耳热分析发现该芯片与PCB之间的焊点存在接触不良,导致芯片发热过高而死机。
二、机械失效分析技术1.目视检查:通过目视检查PCB表面是否存在物理损伤,如裂纹、变形等。
2.显微镜观察:使用显微镜对PCB进行观察,检查PCB连接是否完好,是否存在疲劳裂纹等。
3.声发射检测:利用声发射检测仪器对PCB进行检测,通过检测不同频率的声波来判断是否存在机械失效。
案例:电子产品的PCB在物理冲击后无法正常工作。
经过机械失效分析发现,PCB上的一个元件发生了松动,导致接触不良。
通过目视检查和显微镜观察,最终发现该元件的焊点出现了裂纹,进一步造成了PCB的机械失效。
三、热失效分析技术1.热测量:使用热敏电阻或红外线热像仪对PCB进行温度测量,查找温度异常区域,判断热失效的可能性。
2.热分析:利用有限元软件对PCB进行热仿真分析,通过数值模拟来预测PCB在工作过程中的温度分布和热应力。
案例:电子产品的PCB过热导致无法正常工作。
经过热失效分析发现,PCB散热不良,导致温度过高。
通过热测量发现,PCB上的散热片连接不良,无法正确散热。
- 1、下载文档前请自行甄别文档内容的完整性,平台不提供额外的编辑、内容补充、找答案等附加服务。
- 2、"仅部分预览"的文档,不可在线预览部分如存在完整性等问题,可反馈申请退款(可完整预览的文档不适用该条件!)。
- 3、如文档侵犯您的权益,请联系客服反馈,我们会尽快为您处理(人工客服工作时间:9:00-18:30)。
PCB失效分析技术与典型案例2009-11-18 15:10:05 资料来源:PCBcity 作者: 罗道军、汪洋、聂昕摘要| 由于PCB高密度的发展趋势以及无铅与无卤的环保要求,越来越多的PCB出现了润湿不良、爆板、分层、CAF等等各种失效问题。
本文首先介绍针对PCB在使用过程中的这些失效的分析技术,包括扫描电镜与能谱、光电子能谱、切片、热分析以及傅立叶红外光谱分析等。
然后结合PCB的典型失效分析案例,介绍这些分析技术在实际案例中的应用。
PCB失效机理与原因的获得将有利于将来对PCB的质量控制,从而避免类似问题的再度发生。
关键词| 印制电路板,失效分析,分析技术一、前言PCB作为各种元器件的载体与电路信号传输的枢纽已经成为电子信息产品的最为重要而关键的部分,其质量的好坏与可靠性水平决定了整机设备的质量与可靠性。
随着电子信息产品的小型化以及无铅无卤化的环保要求,PCB也向高密度高Tg以及环保的方向发展。
但是由于成本以及技术的原因,PCB在生产和应用过程中出现了大量的失效问题,并因此引发了许多的质量纠纷。
为了弄清楚失效的原因以便找到解决问题的办法和分清责任,必须对所发生的失效案例进行失效分析。
本文将讨论和介绍一部分常用的失效分析技术,同时介绍一些典型的案例。
二、失效分析技术介于PCB的结构特点与失效的主要模式,本文将重点介绍九项用于PCB失效分析的技术,包括:外观检查、X射线透视检查、金相切片分析、热分析、光电子能谱分析、显微红外分析、扫描电镜分析以及X射线能谱分析等。
其中金相切片分析是属于破坏性的分析技术,一旦使用了这两种技术,样品就破坏了,且无法恢复;另外由于制样的要求,可能扫描电镜分析和X射线能谱分析有时也需要部分破坏样品。
此外,在分析的过程中可能还会由于失效定位和失效原因的验证的需要,可能需要使用如热应力、电性能、可焊性测试与尺寸测量等方面的试验技术,这里就不专门介绍了。
2.1 外观检查外观检查就是目测或利用一些简单仪器,如立体显微镜、金相显微镜甚至放大镜等工具检查PCB的外观,寻找失效的部位和相关的物证,主要的作用就是失效定位和初步判断PCB的失效模式。
外观检查主要检查PCB的污染、腐蚀、爆板的位置、电路布线以及失效的规律性、如是批次的或是个别,是不是总是集中在某个区域等等。
另外,有许多PCB的失效是在组装成PCBA后才发现,是不是组装工艺过程以及过程所用材料的影响导致的失效也需要仔细检查失效区域的特征。
2.2 X射线透视检查对于某些不能通过外观检查到的部位以及PCB的通孔内部和其他内部缺陷,只好使用X射线透视系统来检查。
X光透视系统就是利用不同材料厚度或是不同材料密度对X光的吸湿或透过率的不同原理来成像。
该技术更多地用来检查PCBA焊点内部的缺陷、通孔内部缺陷和高密度封装的BGA或CSP器件的缺陷焊点的定位。
目前的工业X光透视设备的分辨率可以达到一个微米以下,并正由二维向三维成像的设备转变,甚至已经有五维(5D)的设备用于封装的检查,但是这种5D的X光透视系统非常贵重,很少在工业界有实际的应用。
2.3 切片分析切片分析就是通过取样、镶嵌、切片、抛磨、腐蚀、观察等一系列手段和步骤获得PCB横截面结构的过程。
通过切片分析可以得到反映PCB(通孔、镀层等)质量的微观结构的丰富信息,为下一步的质量改进提供很好的依据。
但是该方法是破坏性的,一旦进行了切片,样品就必然遭到破坏;同时该方法制样要求高,制样耗时也较长,需要训练有素的技术人员来完成。
要求详细的切片作业过程,可以参考IPC的标准IPC-TM-650 2.1.1和IPC-MS-810规定的流程进行。
2.4 扫描声学显微镜目前用于电子封装或组装分析的主要是C模式的超声扫描声学显微镜,它是利用高频超声波在材料不连续界面上反射产生的振幅及位相与极性变化来成像,其扫描方式是沿着Z轴扫描X-Y平面的信息。
因此,扫描声学显微镜可以用来检测元器件、材料以及PCB与PCBA内部的各种缺陷,包括裂纹、分层、夹杂物以及空洞等。
如果扫描声学的频率宽度足够的话,还可以直接检测到焊点的内部缺陷。
典型的扫描声学的图像是以红色的警示色表示缺陷的存在,由于大量塑料封装的元器件使用在SMT工艺中,由有铅转换成无铅工艺的过程中,大量的潮湿回流敏感问题产生,即吸湿的塑封器件会在更高的无铅工艺温度下回流时出现内部或基板分层开裂现象,在无铅工艺的高温下普通的PCB也会常常出现爆板现象。
此时,扫描声学显微镜就凸现其在多层高密度PCB无损探伤方面的特别优势。
而一般的明显的爆板则只需通过目测外观就能检测出来。
2.5 显微红外分析显微红外分析就是将红外光谱与显微镜结合在一起的分析方法,它利用不同材料(主要是有机物)对红外光谱不同吸收的原理,分析材料的化合物成分,再结合显微镜可使可见光与红外光同光路,只要在可见的视场下,就可以寻找要分析微量的有机污染物。
如果没有显微镜的结合,通常红外光谱只能分析样品量较多的样品。
而电子工艺中很多情况是微量污染就可以导致PCB焊盘或引线脚的可焊性不良,可以想象,没有显微镜配套的红外光谱是很难解决工艺问题的。
显微红外分析的主要用途就是分析被焊面或焊点表面的有机污染物,分析腐蚀或可焊性不良的原因。
2.6 扫描电子显微镜分析扫描电子显微镜(SEM)是进行失效分析的一种最有用的大型电子显微成像系统,其工作原理是利用阴极发射的电子束经阳极加速,由磁透镜聚焦后形成一束直径为几十至几千埃(A)的电子束流,在扫描线圈的偏转作用下,电子束以一定时间和空间顺序在试样表面作逐点式扫描运动,这束高能电子束轰击到样品表面上会激发出多种信息,经过收集放大就能从显示屏上得到各种相应的图形。
激发的二次电子产生于样品表面5~10nm范围内,因而,二次电子能够较好的反映样品表面的形貌,所以最常用作形貌观察;而激发的背散射电子则产生于样品表面100~1000nm范围内,随着物质原子序数的不同而发射不同特征的背散射电子,因此背散射电子图象具有形貌特征和原子序数判别的能力,也因此,背散射电子像可反映化学元素成分的分布。
现时的扫描电子显微镜的功能已经很强大,任何精细结构或表面特征均可放大到几十万倍进行观察与分析。
在PCB或焊点的失效分析方面,SEM主要用来作失效机理的分析,具体说来就是用来观察焊盘表面的形貌结构、焊点金相组织、测量金属间化物、可焊性镀层分析以及做锡须分析测量等。
与光学显微镜不同,扫描电镜所成的是电子像,因此只有黑白两色,并且扫描电镜的试样要求导电,对非导体和部分半导体需要喷金或碳处理,否则电荷聚集在样品表面就影响样品的观察。
此外,扫描电镜图像景深远远大于光学显微镜,是针对金相结构、显微断口以及锡须等不平整样品的重要分析方法。
2.7 X射线能谱分析上面所说的扫描电镜一般都配有X射线能谱仪。
当高能的电子束撞击样品表面时,表面物质的原子中的内层电子被轰击逸出,外层电子向低能级跃迁时就会激发出特征X射线,不同元素的原子能级差不同而发出的特征X射线就不同,因此,可以将样品发出的特征X射线作为化学成分分析。
同时按照检测X射线的信号为特征波长或特征能量又将相应的仪器分别叫波谱分散谱仪(简称波谱仪,WDS)和能量分散谱仪(简称能谱仪,EDS),波谱仪的分辨率比能谱仪高,能谱仪的分析速度比波谱仪快。
由于能谱仪的速度快且成本低,所以一般的扫描电镜配置的都是能谱仪。
随着电子束的扫描方式不同,能谱仪可以进行表面的点分析、线分析和面分析,可得到元素不同分布的信息。
点分析得到一点的所有元素;线分析每次对指定的一条线做一种元素分析,多次扫描得到所有元素的线分布;面分析对一个指定面内的所有元素分析,测得元素含量是测量面范围的平均值。
在PCB的分析上,能谱仪主要用于焊盘表面的成分分析,可焊性不良的焊盘与引线脚表面污染物的元素分析。
能谱仪的定量分析的准确度有限,低于0.1%的含量一般不易检出。
能谱与SEM结合使用可以同时获得表面形貌与成分的信息(如图1),这是它们应用广泛的原因所在。
2.8 光电子能谱(XPS)样品受X射线照射时,表面原子的内壳层电子会脱离原子核的束缚而逸出固体表面形成电子,测量其动能Ex,可得到原子的内壳层电子的结合能Eb,Eb 因不同元素和不同电子壳层而异,它是原子的“指纹”标识参数,形成的谱线即为光电子能谱(XPS)。
XPS可以用来进行样品表面浅表面(几个纳米级)元素的定性和定量分析。
此外,还可根据结合能的化学位移获得有关元素化学价态的信息。
能给出表面层原子价态与周围元素键合等信息;入射束为X射线光子束,因此可进行绝缘样品分析,不损伤被分析样品快速多元素分析;还可以在氩离子剥离的情况下对多层进行纵向的元素分布分析(可参见后面的案例),且灵敏度远比能谱(EDS)高。
XPS在PCB的分析方面主要用于焊盘镀层质量的分析、污染物分析和氧化程度的分析,以确定可焊性不良的深层次原因。
2.9 热分析2.9.1差示扫描量热仪(DSC)差示扫描量热法(Differential Scanning Calorim- etry)是在程序控温下,测量输入到物质与参比物质之间的功率差与温度(或时间)关系的一种方法。
DSC在试样和参比物容器下装有两组补偿加热丝,当试样在加热过程中由于热效应与参比物之间出现温差ΔT时,可通过差热放大电路和差动热量补偿放大器,使流入补偿电热丝的电流发生变化,而使两边热量平衡,温差ΔT消失,并记录试样和参比物下两只电热补偿的热功率之差随温度(或时间)的变化关系,根据这种变化关系,可研究分析材料的物理化学及热力学性能。
DSC的应用广泛,但在PCB的分析方面主要用于测量PCB上所用的各种高分子材料的固化程度(例如图2)、玻璃态转化温度,这两个参数决定着PCB在后续工艺过程中的可靠性。
2.9.2 热机械分析仪(TMA)热机械分析技术(Thermal Mechanical Analysis)用于程序控温下,测量固体、液体和凝胶在热或机械力作用下的形变性能,常用的负荷方式有压缩、针入、拉伸、弯曲等。
测试探头由固定在其上面的悬臂梁和螺旋弹簧支撑,通过马达对试样施加载荷,当试样发生形变时,差动变压器检测到此变化,并连同温度、应力和应变等数据进行处理后可得到物质在可忽略负荷下形变与温度(或时间)的关系。
根据形变与温度(或时间)的关系,可研究分析材料的物理化学及热力学性能。
TMA 的应用广泛,在PCB的分析方面主要用于PCB最关键的两个参数:测量其线性膨胀系数和玻璃态转化温度。
膨胀系数过大的基材的PCB在焊接组装后常常会导致金属化孔的断裂失效。
2.9.3 热重分析仪(TGA)热重法(Thermogravimetry Analysis)是在程序控温下,测量物质的质量随温度(或时间)的变化关系的一种方法。