铜玻璃复合材料的制备和性能分析
高热导率低热膨胀系数CuZrW2O8复合材料的制备与性能
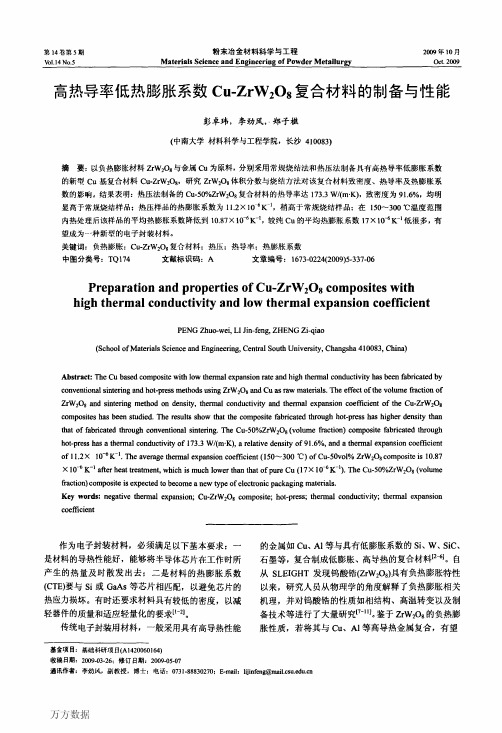
万方数据万方数据万方数据340粉末冶金材料科学弓1:程2009年lO月力增加到400MPa时相转变基本结束。
当压力除去后,这种y正交相仍能保持,属亚稳相。
y相加热到120℃时会逆转变为立方结构的a相。
常规烧结法是在常温下压制成形,然后进行烧结。
在压制过程中发生伉一y相变,而后在烧结过程中随着温度升高,),相逆转变为a相,使得整个样品中的。
c.ZrW208的含量居多;而热压法的加热和加压是同时进行的,相转变进行比较频繁,随着热压温度和压力增加,发生仅一y相变,由于烧结样品体积膨胀而导致y—a相转变受到抑制,从而使得复合材料体系内y-ZrW208的含量较多,所以热压法制备的样品热膨胀系数高于常规烧结样品。
如果对热压样品进行后续热处理,使y相转变为a相,其热膨胀系数应该会降低。
有研究证实,500℃/2h或400℃/24h的热处理制度可以使Cu.ZrW208复合材料中大部分的y相转变为仅相,同时不发生Cu与ZrW20R之间的化学反应【131。
将热压法制备的不同ZrW208体积分数的Cu-ZrW208复合材料在400℃下保温24h后随炉冷却,在150~300℃温度范围内测试其热膨胀系数,结果表明:Cu.50%ZrW208的平均热膨胀系数(温度范围150~300℃)约为10.87×10‘6K~,低于该材料在热处理前的平均热膨胀系数11.2×10拍K一,而Cu一60%ZrW208的平均热膨胀系数(温度范围150~300℃)降低至7.77×10书K-1,这与文献[13]报道的结论近似。
Cu.50%ZrW208复合材料的热导率和热膨胀系数与现有的W-Cu、Mo.Cu复合材料的热导率140-210W/(m・K)和热膨胀系数5.6×10-6~9.1×10-6K。
1相近,有望成为新型的低膨胀、高导热的电子封装材料。
ZrW208和Cu之间存在着巨大的热膨胀系数差,室温时达到29×10-6K,因此当复合材料从烧结温度冷却到室温时产生非常大的残余应力,即热错配应力。
高速列车IGBT用石墨烯-铜复合材料的制备与理论模拟研究
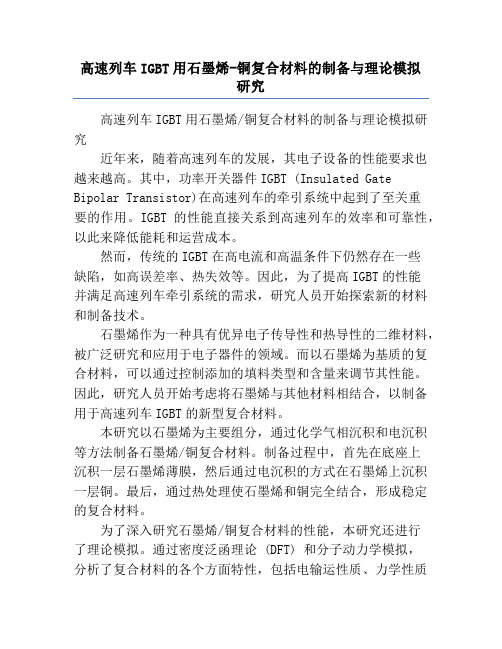
高速列车IGBT用石墨烯-铜复合材料的制备与理论模拟研究高速列车IGBT用石墨烯/铜复合材料的制备与理论模拟研究近年来,随着高速列车的发展,其电子设备的性能要求也越来越高。
其中,功率开关器件IGBT (Insulated Gate Bipolar Transistor)在高速列车的牵引系统中起到了至关重要的作用。
IGBT的性能直接关系到高速列车的效率和可靠性,以此来降低能耗和运营成本。
然而,传统的IGBT在高电流和高温条件下仍然存在一些缺陷,如高误差率、热失效等。
因此,为了提高IGBT的性能并满足高速列车牵引系统的需求,研究人员开始探索新的材料和制备技术。
石墨烯作为一种具有优异电子传导性和热导性的二维材料,被广泛研究和应用于电子器件的领域。
而以石墨烯为基质的复合材料,可以通过控制添加的填料类型和含量来调节其性能。
因此,研究人员开始考虑将石墨烯与其他材料相结合,以制备用于高速列车IGBT的新型复合材料。
本研究以石墨烯为主要组分,通过化学气相沉积和电沉积等方法制备石墨烯/铜复合材料。
制备过程中,首先在底座上沉积一层石墨烯薄膜,然后通过电沉积的方式在石墨烯上沉积一层铜。
最后,通过热处理使石墨烯和铜完全结合,形成稳定的复合材料。
为了深入研究石墨烯/铜复合材料的性能,本研究还进行了理论模拟。
通过密度泛函理论 (DFT) 和分子动力学模拟,分析了复合材料的各个方面特性,包括电输运性质、力学性质和热传导性质等。
模拟结果表明,石墨烯和铜的复合能够显著提高材料的电导率和热导率,同时保持较好的力学性能。
实验结果表明,制备的石墨烯/铜复合材料具有良好的导电性和热导性。
在高电流和高温条件下,复合材料表现出了比传统材料更好的性能,包括更低的误差率和更好的稳定性。
此外,石墨烯的添加还能提高材料的耐热性,延长了材料的使用寿命。
综上所述,本研究成功制备了石墨烯/铜复合材料,并通过理论模拟研究了复合材料的性能。
结果表明,石墨烯/铜复合材料在高速列车IGBT中具有巨大的潜力,其优异的电导性和热导性能可以提高IGBT的效率和可靠性。
复合材料的制备和性能分析
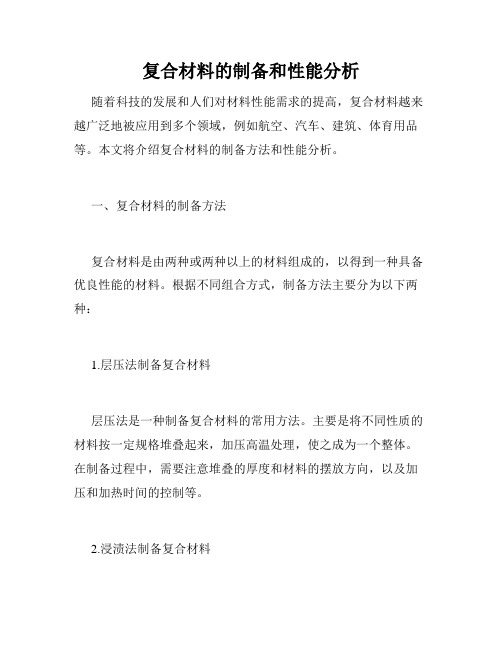
复合材料的制备和性能分析随着科技的发展和人们对材料性能需求的提高,复合材料越来越广泛地被应用到多个领域,例如航空、汽车、建筑、体育用品等。
本文将介绍复合材料的制备方法和性能分析。
一、复合材料的制备方法复合材料是由两种或两种以上的材料组成的,以得到一种具备优良性能的材料。
根据不同组合方式,制备方法主要分为以下两种:1.层压法制备复合材料层压法是一种制备复合材料的常用方法。
主要是将不同性质的材料按一定规格堆叠起来,加压高温处理,使之成为一个整体。
在制备过程中,需要注意堆叠的厚度和材料的摆放方向,以及加压和加热时间的控制等。
2.浸渍法制备复合材料浸渍法主要是将纤维材料浸泡在树脂中,再加压高温处理,以得到一个外观光滑、具有优良物理力学性能的复合材料。
在制备过程中,需要注意纤维的选材和密度、树脂的性质选择以及浸渍时间、加压温度等制造工艺。
二、复合材料性能分析复合材料的性能主要取决于其组成材料的性质和制作工艺。
下面将从强度、刚度、耐热性、耐腐蚀性等方面进行分析:1.强度复合材料的强度主要来自于其纤维材料的拉伸强度,而不是树脂材料。
纤维材料中通常采用的有碳纤维、玻璃纤维、Kevlar纤维等。
在制备过程中,需要注意纤维的数量、排列方式和使用规格。
2.刚度复合材料的刚度是指其抵御外界变形作用的能力。
通常来说,复合材料的刚度比较高。
在制备过程中,需要注意纤维材料的排列方式和密度,同时也需要对树脂材料进行一定的调整。
3.耐热性复合材料的耐热性取决于其纤维材料的耐热性以及树脂材料的热稳定性。
在制备过程中,需要注意纤维材料的选用,同时也需要选用具有较高热稳定性的树脂材料。
4.耐腐蚀性复合材料的耐腐蚀性通常比较好,但也受到其组成材料的影响。
树脂材料通常比较容易受到腐蚀,而纤维材料的耐腐蚀性较好。
三、总结复合材料具有优异的综合性能,但也存在制作工艺复杂、成本高等问题。
在复合材料的制备过程中,需要对组成材料的选择以及制备工艺等进行适当控制,以得到具有良好性能的复合材料。
金刚石_铜复合材料的制备及其性能研究

太原理工大学硕士研究生学位论文金刚石/铜复合材料的制备及其性能研究摘要随着电子元器件电路集成规模日益提高,电路工作产生的热量也相应升高,对与集成电路芯片膨胀系数相匹配的封装材料的热导率提出了更高的要求。
本论文以制备高热导率封装材料为目的,以金刚石颗粒、Cu粉、CuTi合金粉末和W靶材作为原材料,分别利用放电等离子体烧结工艺、无压渗透工艺以及金刚石表面镀W后放电等离子体烧结制备Cu/金刚石复合材料,利用X射线衍射分析仪(XRD)研究材料成分、采用扫描电子显微镜(SEM)观察复合材料的组织特征,并且采用激光闪射热导率测试仪测试了复合材料的热导率,着重研究了材料成分对Cu/金刚石复合材料热导率的影响。
本文首先采用无压渗透法制备Cu-Ti/金刚石复合材料。
首先将酚醛树脂和金刚石颗粒混合压制并置于真空烧结炉内800℃碳化处理得到孔隙度为50%的金刚石压坯。
然后将Cu粉和一定质量分数的Ti粉进行均匀混合后对碳化后的金刚石预制体进行包埋熔渗,冷却后得到Cu-Ti/金刚石复合材料。
实验结果表明,当Ti含量低于10wt%时,Cu合金液不能自发渗入多孔金刚石预制体中。
当Ti含量大于10wt%时,Cu-Ti/金刚石复合材料中存在界面层。
随着Ti含量的增加,Cu-Ti/金刚石复合材料致密度从83.2%逐渐增大至89.4%,金刚石颗粒与Cu基体之间的界面层厚度从0.8µm逐渐增大至4µm。
随着基体中Ti含量的增加,复合材料的热导率先增大后减小。
当Ti的质量太原理工大学硕士研究生学位论文分数为15%时,Cu/金刚石复合材料的热导率达到最大值为298W/ (m·K)。
采用扩散不匹配模型对复合材料的理论卡皮查热阻进行理论估算,将所得结果带入Hasselman-Johnson模型对不同Ti含量下制备的Cu-Ti/金刚石复合材料的理论热导率进行计算可知,当Ti含量为15wt%时,复合材料的实际热导率可以达到理论热导率的82%。
复合材料的微观结构与性能分析
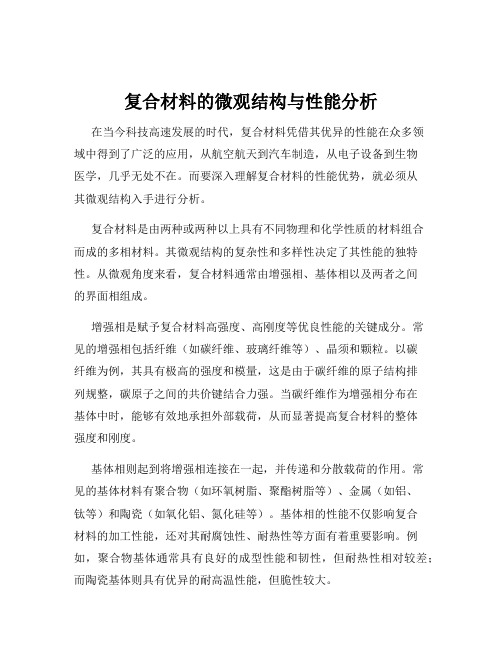
复合材料的微观结构与性能分析在当今科技高速发展的时代,复合材料凭借其优异的性能在众多领域中得到了广泛的应用,从航空航天到汽车制造,从电子设备到生物医学,几乎无处不在。
而要深入理解复合材料的性能优势,就必须从其微观结构入手进行分析。
复合材料是由两种或两种以上具有不同物理和化学性质的材料组合而成的多相材料。
其微观结构的复杂性和多样性决定了其性能的独特性。
从微观角度来看,复合材料通常由增强相、基体相以及两者之间的界面相组成。
增强相是赋予复合材料高强度、高刚度等优良性能的关键成分。
常见的增强相包括纤维(如碳纤维、玻璃纤维等)、晶须和颗粒。
以碳纤维为例,其具有极高的强度和模量,这是由于碳纤维的原子结构排列规整,碳原子之间的共价键结合力强。
当碳纤维作为增强相分布在基体中时,能够有效地承担外部载荷,从而显著提高复合材料的整体强度和刚度。
基体相则起到将增强相连接在一起,并传递和分散载荷的作用。
常见的基体材料有聚合物(如环氧树脂、聚酯树脂等)、金属(如铝、钛等)和陶瓷(如氧化铝、氮化硅等)。
基体相的性能不仅影响复合材料的加工性能,还对其耐腐蚀性、耐热性等方面有着重要影响。
例如,聚合物基体通常具有良好的成型性能和韧性,但耐热性相对较差;而陶瓷基体则具有优异的耐高温性能,但脆性较大。
界面相是增强相与基体相之间的过渡区域,其性能对复合材料的整体性能起着至关重要的作用。
一个良好的界面能够有效地传递载荷,防止在界面处产生应力集中,从而提高复合材料的强度和韧性。
界面的结合强度、化学相容性和物理相容性等因素都会影响界面性能。
如果界面结合过弱,在受到载荷时容易发生脱粘,导致复合材料过早失效;而界面结合过强,则可能限制了复合材料的韧性。
复合材料的微观结构特征对其力学性能有着显著的影响。
例如,增强相的含量、分布和取向会直接影响复合材料的强度和刚度。
当增强相含量增加时,复合材料的强度和刚度通常会相应提高,但同时也可能会导致其韧性下降。
铜基复合材料的电学性能分析

铜基复合材料的电学性能分析王晶;常燕【摘要】为改进铜基复合材料的电学性能,分别研究了TiC含量和SnO2含量对铜基复合材料电学性能的影响,同时测试了不同退火温度下复合材料的电导率.结果表明,复合材料的电导率随着TiC和SnO2含量的增加而呈现减小趋势,且SnO2含量对电导率的影响更大.烧结后复合材料的电导率在15~35 MS/m,经过退火处理后,材料的电导率比未退火处理前有一定程度的提高,同时退火温度对于晶粒长大及品格畸变也会造成影响,进而影响复合材料的电导率.【期刊名称】《矿冶》【年(卷),期】2019(028)002【总页数】4页(P61-64)【关键词】铜基;复合材料;电学性能【作者】王晶;常燕【作者单位】商洛学院城乡规划与建筑工程学院,陕西商洛726000;商洛学院城乡规划与建筑工程学院,陕西商洛726000【正文语种】中文【中图分类】TB333铜基复合材料不仅具备了良好的电学和热学等特性,而且还表现出较高的机械强度和耐磨损等优良性能[1-2]。
从铜基复合材料的应用方面考虑,材料电学性能和力学性能的好坏直接影响了其使用寿命的长短[3-4]。
对电学特性而言,一般主要对电导率进行考察,电导率同时也是决定抗熔焊性能的一个重要指标,电导率越大,抗熔焊能力越强。
为了使第二相的加入对复合材料的导电性的影响不至太大,第二相应选择导电性能良好的材料。
同时,第二相的加入应该可以有效改善复合材料的力学性能。
TiC因具有硬度高、化学稳定性好、优异的耐磨性和良好的导电性能,作为一种极具潜力的碳化物增强体受到广泛关注[5-7]。
早在20世纪90年代,我国科学家高桥辉男等[8]开始采用机械合金法,以电解铜粉、高纯钛粉和石墨粉为原料制备得到了Cu-Ti-C混合合金粉,并通过热压成型的方法制得TiC弥散强化铜基复合材料。
为了可以同时满足铜基复合材料作为电触头材料应用时的灭弧性,本文在前人研究基础之上在铜基体中加入的第二个重要增强相为氧化物SnO2。
《挤压铸造制备铜-铝双金属构件关键技术及组织性能研究》范文

《挤压铸造制备铜-铝双金属构件关键技术及组织性能研究》篇一挤压铸造制备铜-铝双金属构件关键技术及组织性能研究一、引言随着现代工业的快速发展,对具有优良性能和特定结构的多金属复合材料的需求日益增长。
铜/铝双金属构件作为一种典型的复合材料,因其兼具铜的高导电性和铝的低密度、高导热性等优点,在电子、汽车、航空航天等领域具有广泛的应用前景。
挤压铸造作为一种重要的制备工艺,能够有效地将不同金属结合在一起,成为制备铜/铝双金属构件的主要方法之一。
本文将针对挤压铸造制备铜/铝双金属构件的关键技术进行深入的研究,并对其组织性能进行探讨。
二、挤压铸造制备铜/铝双金属构件关键技术(一)工艺原理挤压铸造是一种通过模具对金属液施加压力,使其在高压下填充并固化成型的工艺。
在制备铜/铝双金属构件时,通过将熔融的铜和铝液分别填充到模具中,再通过施加压力使两种金属紧密结合。
(二)关键技术点1. 合金设计:根据实际需求,设计合理的合金成分比例,以获得最佳的物理性能和机械性能。
2. 模具设计:模具的设计对于产品的成型和质量具有决定性影响。
需要考虑到金属的流动性、热传导性以及冷却速度等因素。
3. 工艺参数:包括温度、压力、时间等参数的合理设置,对于保证产品的质量至关重要。
(三)技术实现在实际操作中,需要严格控制合金的熔炼过程,确保熔融金属的纯净度和温度;同时,模具的预热和填充速度也需要精确控制,以保证金属液的填充质量和成型效果。
此外,还需要对产品进行后处理,如热处理、表面处理等,以提高产品的性能和稳定性。
三、组织性能研究(一)组织结构铜/铝双金属构件的组织结构对其性能具有重要影响。
通过合理的合金设计和工艺参数设置,可以获得均匀、致密的微观组织结构。
在铜和铝的界面处,通过合理的工艺控制,可以实现良好的冶金结合,提高产品的力学性能和耐腐蚀性。
(二)性能分析1. 力学性能:通过对产品的硬度、抗拉强度、延伸率等力学性能进行测试和分析,评估产品的性能表现。
《医用可降解锌铜基复合材料的制备及其性能研究》范文

《医用可降解锌铜基复合材料的制备及其性能研究》篇一一、引言随着现代医疗技术的不断发展,医用材料在医疗领域的应用越来越广泛。
其中,可降解医用材料因其良好的生物相容性和可降解性,成为了研究的热点。
本文旨在研究医用可降解锌铜基复合材料的制备工艺及其性能,以期为医用材料的研究和应用提供新的思路和方法。
二、材料与方法1. 材料准备本实验所需材料主要包括锌、铜及其他添加剂。
所有材料均经过严格筛选和预处理,以确保其纯度和质量。
2. 制备方法(1)采用熔炼法制备锌铜基合金;(2)通过机械合金化法将其他添加剂与锌铜基合金混合,制备出锌铜基复合材料;(3)对制备出的复合材料进行热处理,以提高其性能。
3. 性能测试(1)采用X射线衍射(XRD)和扫描电子显微镜(SEM)对材料的微观结构和形貌进行分析;(2)通过力学性能测试,测定材料的抗拉强度、抗压强度等力学性能;(3)进行体外降解实验,观察材料的降解过程和降解速率;(4)通过细胞毒性实验,评估材料的生物相容性。
三、结果与讨论1. 微观结构与形貌分析通过XRD和SEM分析,我们发现制备出的锌铜基复合材料具有均匀的微观结构和良好的形貌。
材料中各组分分布均匀,无明显的相分离现象。
2. 力学性能分析力学性能测试结果表明,制备出的锌铜基复合材料具有较高的抗拉强度和抗压强度。
这主要归因于材料中各组分的良好协同作用以及热处理过程中形成的强化相。
3. 体外降解性能分析体外降解实验结果显示,锌铜基复合材料具有良好的可降解性。
在生理环境下,材料能够逐渐降解,并释放出对人体无害的锌、铜等元素。
降解速率适中,符合医用材料的要求。
4. 生物相容性分析细胞毒性实验表明,锌铜基复合材料具有良好的生物相容性。
材料对细胞无明显的毒性作用,且能够促进细胞的生长和繁殖。
这为材料在医用领域的应用提供了良好的基础。
四、结论本文成功制备了医用可降解锌铜基复合材料,并对其性能进行了系统研究。
结果表明,该材料具有优良的力学性能、可降解性和生物相容性。
金属基复合材料的制备与性能分析

金属基复合材料的制备与性能分析金属基复合材料是一种具有优异性质的新型材料,将金属基体和其他材料复合,形成了一种具有新特性的复合材料。
金属基复合材料具有高强度、高耐腐蚀、高导热、高导电等优秀性能。
在航空、航天、汽车、船舶、电子等领域得到了广泛的应用。
本文将重点探讨金属基复合材料的制备工艺以及性能分析。
一、金属基复合材料的制备金属基复合材料的制备方法多种多样,主要分为以下几种:1. 热压法热压法是将金属基体和其他材料按照一定比例混合,通过高温高压的条件下进行制备的方法。
该方法制备的复合材料具有高密度、高强度、高硬度、高耐腐蚀性等优点,适用于制备高硬度、高强度、高温下使用的零部件。
2. 熔浸法熔浸法是将其他材料熔在金属表面,使两种材料通过化学反应牢固地结合在一起的方法。
这种制备方法可以制备高密度、高强度、高耐腐蚀性的复合材料,适用于制备涉及到化学反应的部件。
3. 搅拌摩擦焊接法搅拌摩擦焊接法是利用旋转工具将两种金属板材固定在一起,通过旋转摩擦和挤压的过程,产生高热和高压,将两种材料连接在一起的方法。
该方法可以制备具有优异耐磨性的复合材料,适用于制备耐磨部件。
以上三种制备方法,都需要在金属基体上涂覆一层其他材料才能形成复合材料。
除此之外,还有一种直接混合法,即将两种或多种金属材料和其他材料混合,制成复合材料。
这种方法分为干法和湿法制备,适用于制备一些低强度、低温下使用的零部件。
二、金属基复合材料的性能分析金属基复合材料具有许多优异的性能,下面我们将逐一进行分析:1. 高强度金属基复合材料的强度要高于金属基体,这是由于复合材料中添加了其他材料,它们的耐拉强度、屈服强度均高于纯金属。
同时,两种相互牵拉的材料之间的结合能力也会提升材料的整体强度。
2. 高耐腐蚀性金属基复合材料的耐腐蚀性也要优于金属基体,这是由于添加的其他材料本身就具有良好的耐腐蚀性能。
同时,复合材料中添加的其他材料还可以吸收腐蚀性物质,保护金属基体,延长材料的使用寿命。
《石墨烯增强铜基复合材料的制备及其性能研究》范文
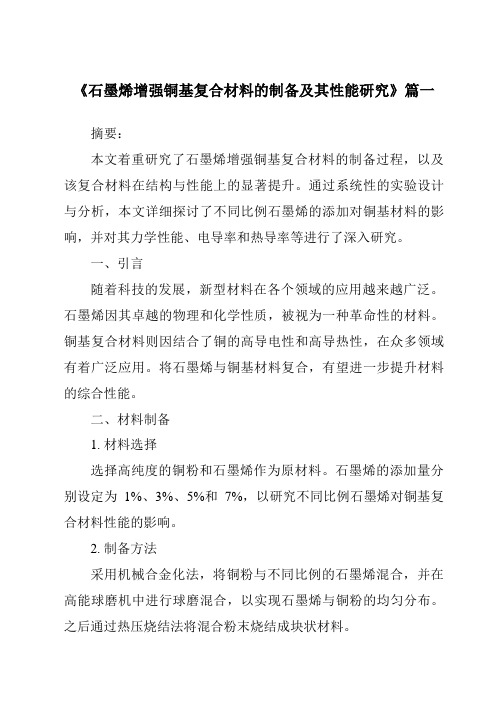
《石墨烯增强铜基复合材料的制备及其性能研究》篇一摘要:本文着重研究了石墨烯增强铜基复合材料的制备过程,以及该复合材料在结构与性能上的显著提升。
通过系统性的实验设计与分析,本文详细探讨了不同比例石墨烯的添加对铜基材料的影响,并对其力学性能、电导率和热导率等进行了深入研究。
一、引言随着科技的发展,新型材料在各个领域的应用越来越广泛。
石墨烯因其卓越的物理和化学性质,被视为一种革命性的材料。
铜基复合材料则因结合了铜的高导电性和高导热性,在众多领域有着广泛应用。
将石墨烯与铜基材料复合,有望进一步提升材料的综合性能。
二、材料制备1. 材料选择选择高纯度的铜粉和石墨烯作为原材料。
石墨烯的添加量分别设定为1%、3%、5%和7%,以研究不同比例石墨烯对铜基复合材料性能的影响。
2. 制备方法采用机械合金化法,将铜粉与不同比例的石墨烯混合,并在高能球磨机中进行球磨混合,以实现石墨烯与铜粉的均匀分布。
之后通过热压烧结法将混合粉末烧结成块状材料。
三、性能研究1. 力学性能通过硬度测试和拉伸试验,研究了不同比例石墨烯对铜基复合材料力学性能的影响。
实验结果表明,随着石墨烯含量的增加,材料的硬度逐渐提高,拉伸强度也有所增强。
当石墨烯含量达到5%时,复合材料的综合力学性能达到最优。
2. 电导率与热导率利用电导率测试仪和热导率测试仪,分别对复合材料的电导率和热导率进行了测试。
结果显示,适量石墨烯的添加能够显著提高铜基复合材料的电导率和热导率。
当石墨烯含量为3%时,复合材料的电导率和热导率达到最佳状态。
四、结果与讨论实验结果表明,适量石墨烯的添加可以显著提高铜基复合材料的力学性能、电导率和热导率。
这是因为石墨烯具有优异的力学性能、电学性能和热学性能,能够有效地增强铜基材料的综合性能。
然而,当石墨烯含量过高时,可能会在材料内部形成团聚现象,反而降低材料的综合性能。
因此,选择合适的石墨烯含量对于制备高性能的铜基复合材料至关重要。
五、结论本文通过实验研究了石墨烯增强铜基复合材料的制备过程及其性能。
复合材料的抗腐蚀性能分析

复合材料的抗腐蚀性能分析在现代工业和科技的快速发展中,材料的性能要求越来越高。
其中,抗腐蚀性能是许多应用场景中至关重要的一个方面。
复合材料由于其独特的结构和组成,在抗腐蚀领域展现出了巨大的潜力。
复合材料通常由两种或两种以上不同性质的材料组成,通过特定的工艺结合在一起,从而综合了各组分材料的优点。
这种特性使得复合材料在面对腐蚀环境时,能够表现出比单一材料更出色的性能。
首先,我们来了解一下腐蚀的基本原理。
腐蚀是材料与周围环境发生化学反应或电化学反应,导致材料的性能下降甚至失效的过程。
常见的腐蚀类型包括化学腐蚀、电化学腐蚀和微生物腐蚀等。
化学腐蚀是材料直接与化学物质发生反应,如金属在酸中的溶解。
电化学腐蚀则是由于材料表面形成了原电池,导致电子的转移和材料的损耗。
微生物腐蚀则是由微生物的代谢活动引起的材料破坏。
复合材料在抗腐蚀方面具有多种优势。
其一,复合材料可以通过选择合适的组分来避免或减少与腐蚀介质的反应。
例如,在纤维增强复合材料中,纤维材料如碳纤维、玻璃纤维等通常具有良好的化学稳定性,不易与大多数腐蚀介质发生反应。
而基体材料如树脂可以经过特殊的处理或选择具有耐腐蚀性的树脂,从而提高整体的抗腐蚀性能。
其二,复合材料的微观结构也有助于提高抗腐蚀性能。
复合材料中的纤维分布和界面结构可以有效地阻止腐蚀介质的渗透和扩散。
纤维与基体之间的良好结合能够减少缝隙和缺陷的存在,降低腐蚀介质侵入的可能性。
以碳纤维增强复合材料(CFRP)为例,碳纤维具有极高的强度和优异的化学稳定性,而常用的环氧树脂基体经过适当的改性处理后,能够抵抗多种化学物质的侵蚀。
在航空航天领域,CFRP 被广泛应用于飞机结构部件,不仅减轻了重量,还能够在恶劣的环境中保持良好的性能,减少腐蚀带来的安全隐患。
玻璃纤维增强复合材料(GFRP)也是常见的一种复合材料。
玻璃纤维成本相对较低,但其耐腐蚀性也相当不错。
在化工管道、船舶制造等领域,GFRP 被用于替代传统的金属材料,有效地延长了设备的使用寿命,降低了维护成本。
复合材料的耐久性分析与评估

复合材料的耐久性分析与评估在现代工程领域,复合材料因其优异的性能而被广泛应用。
然而,要确保复合材料在长期使用中的可靠性和安全性,对其耐久性的深入分析与评估至关重要。
复合材料是由两种或两种以上具有不同物理和化学性质的材料组合而成,通过协同作用实现比单一材料更出色的性能。
常见的复合材料包括纤维增强复合材料(如碳纤维增强复合材料、玻璃纤维增强复合材料)和层合复合材料等。
耐久性,简单来说,是指材料在特定环境条件下抵抗性能退化和保持其功能完整性的能力。
对于复合材料,耐久性受到多种因素的影响。
首先,复合材料的组成成分对其耐久性有着直接的影响。
增强纤维的类型、性能和含量,以及基体材料的特性都会改变复合材料的耐久性表现。
例如,碳纤维具有高强度和高模量,但在某些化学环境中可能不如玻璃纤维稳定。
基体材料的耐腐蚀性、耐热性和抗疲劳性能等也是关键因素。
其次,制造工艺也在很大程度上决定了复合材料的耐久性。
在制备过程中,纤维与基体的结合质量、孔隙率的大小以及残余应力的分布等都会影响复合材料的长期性能。
如果制造过程中存在缺陷,如纤维分布不均匀、孔隙过多或界面结合不良,这些都会成为潜在的薄弱点,加速材料的性能退化。
环境因素是影响复合材料耐久性的另一个重要方面。
温度、湿度、化学介质以及机械载荷等环境条件的变化,都可能导致复合材料的性能下降。
高温可能会使基体软化或导致纤维与基体的界面结合弱化;湿度会引起材料的吸湿膨胀,从而影响其力学性能;化学介质可能会腐蚀基体或与纤维发生化学反应;而长期的机械载荷则会导致材料的疲劳损伤。
在对复合材料耐久性进行分析时,需要采用一系列的实验方法和技术。
力学性能测试是常用的手段之一,包括拉伸、压缩、弯曲和剪切试验等,以评估材料在不同载荷条件下的强度和变形特性。
此外,还可以通过疲劳试验来研究材料在循环载荷下的耐久性。
微观结构分析也是必不可少的,如扫描电子显微镜(SEM)、X 射线衍射(XRD)和能谱分析(EDS)等技术,可以帮助观察材料内部的纤维分布、界面状态以及可能存在的缺陷和损伤。
复合材料实验报告

复合材料实验报告
实验目的:
本实验旨在探究复合材料的制备方法以及其力学性能,通过实验数据的收集和分析,进一步了解复合材料的特点和应用。
实验装置与材料:
1. 复合材料制备设备:包括玻璃纤维、碳纤维、树脂等原料的混合搅拌设备。
2. 复合材料力学性能测试设备:如拉伸试验机、弯曲试验机等。
3. 实验所需其他辅助工具:包括称量器、计时器等。
实验步骤:
1. 准备工作:准备所需原材料,包括特定比例的玻璃纤维、碳纤维和树脂,并进行充分混合搅拌。
2. 复合材料制备:将混合好的复合材料浇铸到模具中,待固化后取出制备成型。
3. 力学性能测试:对制备好的复合材料进行拉伸试验和弯曲试验,记录数据并进行分析。
4. 结果展示:展示实验数据,包括复合材料的拉伸强度、弹性模量等力学性能参数。
实验结果与分析:
根据实验数据分析得出如下结果:复合材料具有较高的拉伸强度和弯曲强度,比传统材料具有更好的机械性能。
在实际应用中,复合材料被广泛应用于航空航天、汽车制造等领域,因其轻质高强的特点,能够大幅减少产品自重,提高产品的性能。
结论:
通过本次实验,我们对复合材料的制备方法和力学性能有了更深入的了解。
复合材料以其独特的优势在工业生产中得到广泛应用,未来将继续深入研究复合材料的制备工艺和性能,为实际生产提供更多有益的参考和指导。
钙长石_玻璃复合材料的制备和性能研究

万方数据
赣 船
雹 惫
图4 复合材料的介电性能随钙长石含量的变化
了
至
赣
越
雠
骥
甏
妪
釜
档
麓
图5复合材料的热膨胀系数和抗折强度 随钙长石含量的变化
钙长石本身具有较低的介电损耗以及样品基本都 达到致密化[10‘,这一点可以从图1看出。
图5所示为复合材料的热膨胀系数和抗折强 度随钙长石含量变化的关系图。由图5可知,复 合材料的热膨胀系数随钙长石含量的增加而增 加。这是由于钙长石的热膨胀系数比硼玻璃的 大,根据加和法则,钙长石含量越蔚,它对复合材
233.
[5]董伟霞.顾幸勇.包启富.zno对钙长石/莫来石复合材料性
能的影响[J].电子元件与材料.2009,28(3):57—59.
[6]张兆生.卢振亚.陈志武.电子封装用陶瓷基片材料的研究
进展[J].材料导报.2008,22(11):16—20. [7] sen M。Juan Y。Ferreira Jose M F.The densification and
《2024年钴酸铜及其复合电极材料的制备与电化学性能》范文

《钴酸铜及其复合电极材料的制备与电化学性能》篇一一、引言随着现代科技的快速发展,人们对新型能源材料的需求日益增长。
钴酸铜作为一种具有高能量密度的电极材料,在锂离子电池、超级电容器等新能源领域具有广泛的应用前景。
本文旨在研究钴酸铜及其复合电极材料的制备方法,并对其电化学性能进行探讨,以期为实际应用提供理论基础。
二、钴酸铜及其复合电极材料的制备(一)钴酸铜的制备钴酸铜的制备主要通过化学共沉淀法进行。
具体步骤为:在一定的温度和pH值条件下,将钴盐和铜盐溶液混合,加入适量的沉淀剂,使钴和铜离子同时沉淀为钴酸铜。
经过滤、洗涤、干燥后得到钴酸铜粉末。
(二)钴酸铜复合电极材料的制备为提高钴酸铜的电化学性能,可将其与其他材料复合制备复合电极材料。
如将钴酸铜与导电碳材料(如碳纳米管、石墨烯等)混合,制备出具有高导电性的复合电极材料。
此外,还可以将钴酸铜与其他金属氧化物(如氧化锰、氧化铁等)进行复合,以提高其电化学性能。
三、电化学性能研究(一)材料结构与形貌分析通过X射线衍射(XRD)、扫描电子显微镜(SEM)等手段对制备的钴酸铜及其复合电极材料进行结构与形貌分析。
结果表明,所制备的钴酸铜具有较高的纯度和良好的结晶性,而复合电极材料则具有较高的比表面积和良好的导电性。
(二)电化学性能测试采用循环伏安法(CV)、恒流充放电测试、电化学阻抗谱(EIS)等方法对钴酸铜及其复合电极材料的电化学性能进行测试。
结果表明,钴酸铜具有较高的比容量和良好的循环稳定性。
而复合电极材料则具有更高的比容量和更好的倍率性能。
此外,我们还发现复合电极材料的循环稳定性也得到了显著提高。
四、结果与讨论(一)制备条件对材料性能的影响实验发现,制备条件对钴酸铜及其复合电极材料的性能具有重要影响。
如反应温度、pH值、沉淀剂种类及用量等都会影响材料的结构和性能。
因此,在制备过程中需要严格控制这些条件,以获得具有优异性能的材料。
(二)复合材料协同效应分析通过对比实验数据,我们发现复合电极材料中的各组分之间存在协同效应。
玻璃陶瓷复合材料的制备及其性能研究
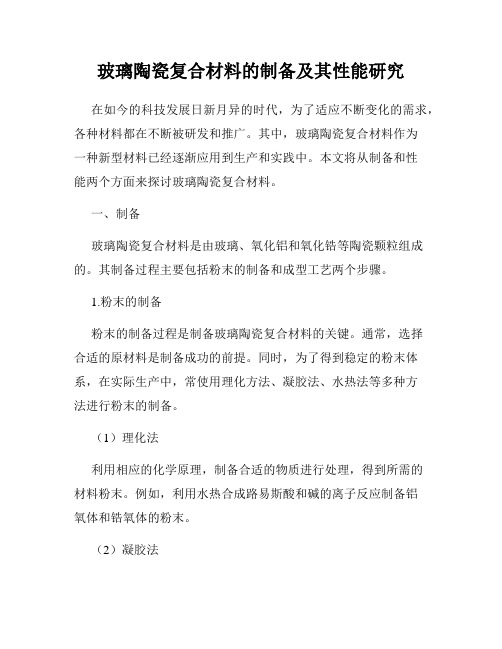
玻璃陶瓷复合材料的制备及其性能研究在如今的科技发展日新月异的时代,为了适应不断变化的需求,各种材料都在不断被研发和推广。
其中,玻璃陶瓷复合材料作为一种新型材料已经逐渐应用到生产和实践中。
本文将从制备和性能两个方面来探讨玻璃陶瓷复合材料。
一、制备玻璃陶瓷复合材料是由玻璃、氧化铝和氧化锆等陶瓷颗粒组成的。
其制备过程主要包括粉末的制备和成型工艺两个步骤。
1.粉末的制备粉末的制备过程是制备玻璃陶瓷复合材料的关键。
通常,选择合适的原材料是制备成功的前提。
同时,为了得到稳定的粉末体系,在实际生产中,常使用理化方法、凝胶法、水热法等多种方法进行粉末的制备。
(1)理化法利用相应的化学原理,制备合适的物质进行处理,得到所需的材料粉末。
例如,利用水热合成路易斯酸和碱的离子反应制备铝氧体和锆氧体的粉末。
(2)凝胶法在凝胶法中,将氧化铝和氧化锆悬浊液加入可以生成凝胶的化学物质(如硝酸铝、氯化锆、硝酸铅等)中制备所需的粉末。
(3)水热法在水热法中,将氧化铝和氧化锆的混合物加入含有相应化学物质的水溶液中。
在设定好的温度和时间条件下,得到所需要的粉末。
2.成型工艺从制备材料的角度分析,研究制备材料的成型方法的优化是非常必要且重要的。
常用的成型方法包括:压制、注射成型、挤压成型、模压和3D打印等。
(1)压制制备过程中,将所需的粉末压缩成固体,之后再通过烧结和高温处理得到所需的终产品。
(2)注射成型在注射成型中,将粉末混合物加入注射机中,通过注射器将混合物注入一个模具中,依靠模具的形状来进行成型。
(3)挤压成型在挤压成型中,将粉末混合物通过挤压机挤压成形,依靠挤压机的压力来进行成型。
(4)模压在模压中,将粉末混合物压入一个模具中进行成型,通过模具的形状来进行成型。
(5)3D打印使用3D打印技术可以制造出复杂的玻璃陶瓷复合材料件。
只要在计算机上进行设计,并且设置好对应的参数,就可以通过机器进行制造。
二、性能1.物理性能玻璃陶瓷复合材料的物理性能主要包括机械性能、热膨胀系数、热导率、热稳定性等方面。
材料制备综合实验报告

一、实验目的本次实验旨在通过综合实验,掌握材料制备的基本方法,熟悉不同材料的制备工艺,提高对材料性能的测试与分析能力。
同时,培养实验操作技能和科学思维,为后续材料科学研究奠定基础。
二、实验内容及步骤1. 实验材料(1)金属:纯铁、纯铜、纯铝等;(2)非金属:碳纤维、石墨、陶瓷等;(3)复合材料:碳纤维增强复合材料、玻璃纤维增强复合材料等。
2. 实验步骤(1)金属材料的制备① 纯铁、纯铜、纯铝的熔炼:采用电阻炉熔炼,熔化后铸造成型;② 金属材料的轧制:将熔炼好的金属坯料进行轧制,制备不同厚度的金属板;③ 金属材料的切割:根据实验要求,对金属板进行切割,制备实验样品。
(2)非金属材料的制备① 碳纤维、石墨的制备:采用聚丙烯腈(PAN)原丝进行碳化处理,制备碳纤维;采用天然石墨进行石墨化处理,制备石墨;② 陶瓷材料的制备:采用高温烧结法制备陶瓷材料;③ 复合材料的制备:将碳纤维或石墨纤维与树脂基体进行复合,制备碳纤维增强复合材料或玻璃纤维增强复合材料。
(3)材料性能测试① 金属材料的力学性能测试:采用万能试验机进行拉伸、压缩、弯曲等力学性能测试;② 非金属材料的力学性能测试:采用万能试验机进行拉伸、压缩、弯曲等力学性能测试;③ 复合材料的力学性能测试:采用万能试验机进行拉伸、压缩、弯曲等力学性能测试;④ 材料的微观结构分析:采用扫描电镜(SEM)观察材料的表面形貌,采用透射电镜(TEM)观察材料的内部结构。
三、实验结果与分析1. 金属材料的制备实验中,通过电阻炉熔炼、轧制、切割等工艺,成功制备了纯铁、纯铜、纯铝等金属材料。
测试结果表明,这些金属材料的力学性能符合要求。
2. 非金属材料的制备实验中,通过碳化、石墨化、高温烧结等工艺,成功制备了碳纤维、石墨、陶瓷等非金属材料。
测试结果表明,这些非金属材料的力学性能符合要求。
3. 复合材料的制备实验中,通过碳纤维或石墨纤维与树脂基体的复合,成功制备了碳纤维增强复合材料或玻璃纤维增强复合材料。
《2024年Ti2AlN-La2O3-Cu复合材料的制备及性能研究》范文

《Ti2AlN-La2O3-Cu复合材料的制备及性能研究》篇一Ti2AlN-La2O3-Cu复合材料的制备及性能研究一、引言随着现代科技的发展,复合材料因其独特的物理和化学性能在众多领域得到了广泛应用。
Ti2AlN-La2O3/Cu复合材料是一种新型的高性能金属陶瓷复合材料,该材料在航空、能源和汽车等关键领域中具有重要的应用前景。
本文着重研究该复合材料的制备方法及性能分析,旨在为其应用和发展提供一定的理论基础。
二、制备方法Ti2AlN-La2O3/Cu复合材料的制备过程主要包含以下步骤:首先将原始的原材料如钛、铝、镧和铜等进行预处理,然后通过高温熔炼、热压成型等工艺制备出复合材料。
具体步骤如下:1. 原材料预处理:将钛、铝、镧和铜等原材料进行清洗、破碎和研磨,确保其粒度符合后续工艺要求。
2. 熔炼:将预处理后的原材料放入高温熔炼炉中,在高温条件下进行熔炼,使各元素充分融合。
3. 制备:将熔炼后的金属溶液通过精密的工艺和设备,加入特定比例的La2O3进行搅拌和凝固,随后通过热压成型法制备出Ti2AlN-La2O3/Cu复合材料。
三、性能研究对于Ti2AlN-La2O3/Cu复合材料的性能研究,本文主要从以下几个方面进行:1. 硬度与强度:通过维氏硬度计和拉伸试验机对复合材料的硬度和强度进行测试,分析其力学性能。
2. 耐腐蚀性:通过电化学腐蚀测试和盐雾试验等方法,评估复合材料在各种环境中的耐腐蚀性能。
3. 热稳定性:通过高温热处理和热循环测试等方法,研究复合材料在不同温度条件下的热稳定性。
4. 微观结构分析:利用X射线衍射仪、扫描电子显微镜等设备对复合材料的微观结构进行分析,了解其相组成和晶粒形态。
四、结果与讨论经过一系列的制备和性能测试,我们得到了以下结果:1. 硬度与强度:Ti2AlN-La2O3/Cu复合材料具有较高的硬度和强度,表明其具有良好的力学性能。
2. 耐腐蚀性:该复合材料在各种环境中的耐腐蚀性能优异,具有较好的抗腐蚀能力。
- 1、下载文档前请自行甄别文档内容的完整性,平台不提供额外的编辑、内容补充、找答案等附加服务。
- 2、"仅部分预览"的文档,不可在线预览部分如存在完整性等问题,可反馈申请退款(可完整预览的文档不适用该条件!)。
- 3、如文档侵犯您的权益,请联系客服反馈,我们会尽快为您处理(人工客服工作时间:9:00-18:30)。
铜/玻璃复合材料的制备和性能分析材料094班:王波指导教师:郭宏伟陕西科技大学材料科学与工程学院陕西西安710021摘要:本文采用铝硼硅酸盐玻璃粉与铜粉,经过不同铜玻璃配比用高温烧结的方法得到铜/玻璃复合材料。
通过抗折强度测试,得出不同烧结温度、不同配比与强度的关系。
再通过XRD、SEM、热膨胀等方法对复合材料进行探究。
结果表明:铜/玻璃复合材料中主要是由玻璃相、铜相、亚铜相组成,玻璃完全包裹铜相和亚铜相,烧结致密,没有气泡,复合材料的强度高。
关键词:玻璃粉,导电性,复合材料Preparation and P erformance of C opper-glassABSTRACT:In this paper,aluminum borosilicate glass powder and copper powder,copper glass ratio through different methods used to obtain high-temperature sintering of copper-glass composite materials.By flexural strength tests,the different sintering temperatures and in different proportions and intensity relationships.Through XRD,SEM,and other methods of thermal expansion composites were explored.The results showed that:Copper-glass composite material is mainly made of glass phase and copper phase, cuprous phase composition,the glass completely wrapped cuprous copper phase and phase sintering,no bubbles,high strength composite material.KEY WORDS:Glass frit,conductive,composite materials近几年块状金属玻璃(BMG)引起了人们的广泛关注,其主要原因是金属玻璃作为高强度结构材料表现出的应用潜力[1]。
然而铜/玻璃复合材料的研究在国内外的研究还不是很多,都停留在以前理论的基础之上。
此次在结合前人的基础上,选用铜粉与铝硼硅酸盐玻璃粉在高温下烧结,得到一种新的复合材料,分析工艺条件对复合材料性能的影响,并通过XRD、SEM、硬力分析、热膨胀分析来研究铜玻璃复合材料的性能。
1实验第一步:玻璃粉的制备1)首先,按质量分数将50%的SiO2,13%的Al2O3,20%的CaO,5%的MgO,10%的B2O3,2%的Na2O,0.5%的Sb2O3混合均匀后,形成配合料;2)然后,将配合料的加入已经升温至1400℃的刚玉坩埚中通过10min升温至1550℃,并保温20min;再将剩余配合料再加入刚玉坩埚中,并通过10min升温至1550~1600℃,保温60min后,将熔制好的玻璃液倒入水中水淬;3)最后,将水淬后的玻璃渣捞出,烘干球磨后过400目标准筛,既得玻璃/金属复合材料用玻璃粉末;第二步:玻璃/金属复合材料的制备1)首先,玻璃粉末与铜粉末按照一定配比混合均匀形成混合料;2)然后,再向混合料中加入混合料质量分数1~3%蒸馏水,并混合均匀;3)然后,将加水的混料放入密闭的容器中,室温下放置8h备用;4)然后,将混合料装入模具中,于40~70KPa的压力下成型;5)然后,将成型的试样放入80℃烘箱中,保温2小时;6)然后,将马弗炉温度升高到800℃,将试样放放入炉中3-5min,取出试样密闭冷却至常温,得到复合材料。
2结果与讨论2.1烧结时间、温度、配料比与强度的关系在烧结时间为4min,成型压力为70kPa,复合材料的硬力强度随温度配料比的变化如下图。
强度单位(MPa)图2-1不同配料比在不同温度下的强度关系B-表示铜与玻璃配比1:1,C-表示铜与玻璃配比3:4,D-表示铜与玻璃配比3:5,E-表示铜与玻璃配比1:2图2-1是不同烧结温度,不同铜玻璃配比,在烧结时间为4min,成型压力为70KPa,条件下的强度折线图。
由此图2-1可以看出在烧结温度和成型压力控制不变的情况下,温度在800-870℃之间,配料比一定的情况下,随着温度的升高,复合材料的硬力强度随着增大;温度在870-900℃之间,配料比在0.6-1之间,复合材料的强度随温度的升高而降低,所以870℃是温度的一个转折点。
由图可以看出配料比为1:1时,其复合材料的强度是最大的,随着配料比的降低,强度随着降低。
温度在800-840℃之间时,复合材料的强度的变化不是很大,所以这个温度不是复合材料的生成温度[2]。
2.2在烧结温度为900℃,成型压力为70kPa,复合材料的硬力强度随温度配料比的变化如下图。
强度单位(MPa)图2-2是不同烧结温度、不同烧结时间,在铜玻璃配料比1:1,成型压力为70KPa下的强度折线图。
由此图2-2可以看出在烧结时间为4min时,复合材料的强度是最大的。
在温度为800-870℃之间时,随着温度的升高,复合材料的强度随之增大。
在温度870-900℃之间时,随着温度的升高,材料强度随之降低。
在870℃左右是烧结温度的一个转折点。
在烧结时间为3min时,温度为800℃时,材料强度是最低的。
温度在840℃时,随着烧结时间的增大,材料的变化强度不是很大,造成这种的原因是烧结温度过低,铜和玻璃没有完全反应。
温度在870℃时,随着时间的增加材料强度先增大再减小,中间有最大值。
在烧结时间为4min时,强度减小是因为烧结时间过长造成的。
B-烧结时间为3min,C-烧结时间3.5min,D-烧结时间4min,E-烧结时间4.5min图2-2不同烧结时间下的不同温度的强度关系2.3试样XRD 分析下图是在870℃烧结温度下,烧结时间为4min,成型压力为70KPa,铜玻璃配料比为3:5的复合材料的XRD 图图2-3870℃下复合材料的XRD 图2-4870℃时复合材料的热膨胀曲线图2-3是在870℃烧结温度下,烧结时间为4min,成型压力为70kPa,铜玻璃配料比为3:5的复合材料的XRD 图。
作图可以得出Cu、Cu 2O 的X 衍射峰与该复合材料的峰值重合如上图所示。
由图2-3可以看出该复合材料中有Cu 相、Cu 2O 相组成。
Cu 相、Cu 2O 相是该复合材料的主要晶相。
产生这种现象的主要原因是,复合材料主要是铜和玻璃粉复合,玻璃粉在847℃时融化包裹玻璃,这个温度比800℃时铜的衍射强度更大,所以有大量铜相;而此烧结是在氧化气氛中进行,开始烧结时,复合材料的表面与氧接触,生成氧化铜,随着表面的氧化,氧与符合材料的接触减少,所以生成氧化亚铜。
2.4热膨胀分析图2-4是在870℃烧结温度下,烧结时间为4min,成型压力为70kPa,铜玻璃配料比为3:5的复合材料的热膨胀图图2-4是铜-玻璃粉复合后在870℃下烧结后,室温至750℃下的线膨胀曲线。
由图2-4可以看出,铜与玻璃粉的重量比为3:5时,烧结后试样室温500℃的线膨胀系数为81.7×10-7/K,并且随温度的升高,在转变温度576℃以上试样的膨胀系数表现出了常规玻璃的伸长变化规律[3]。
2.5扫描电镜分析图2-5这是在烧结温度为870℃,烧结时间为4min,铜-玻璃配料比3:5,成型压力为70KPa,条件下生成的复合材料的扫描电镜图。
由图2-5a 可以看出该复合材料的表面很光滑,像洋葱皮的形状。
(a)(b)图2-5870℃下复合材料的SEM看不到裂痕,表面光滑。
通过放大图2-5b 可以看出铜-玻璃复合材料比较致密,表面没有产生气泡。
这是因为在在这个温度下玻璃能够很好的融化,把铜能够完全包裹,在烧结时间内可以排出内部的气体,所以复合材料的强度很大。
2.6导电分析通过用万能表测试其铜玻璃配比1:1、3:4、3:5、1:2,四种配比下不同条件的所有试样的导电情况。
通过万能表测得在配料比1:1、3:4、3:5情况下均导电,只有在铜玻璃配比1:2情况下不导电,虽然断面也有较好的金属光泽。
所以在铜玻璃配比从0.6-1的范围内,剩余条件都在最佳条件时,都具有导电性。
3结论(1)用高温烧结的方法制备了铜/玻璃复合材料,玻璃是铝硼硅酸盐玻璃,配方如下:SiO 250%,Al 2O 313%,CaO20%,MgO5%,B 2O 310%,Na 2O2%,Sb 2O 30.5%。
制得的玻璃球磨成400目的粉末。
铜粉选择200目.(2)通过正交实验得出了影响制备工艺的因素主次,得出温度是最重要的影响因素,下来依次是同玻璃配料比、烧结时间、成型压力。
并得出了它们的最优值,最佳温度:870℃、铜玻璃配比1:1、烧结时间4min、成型压力70KPa。
(3)通过实验得出随着烧结温度的升高,复合材料的强度先升高后降低;随着烧结时间的增长复合材料的强度是先升高后降低,有一个最佳烧结时间点;而随着铜玻璃备料比的增大,复合材料的强度随之增大;成型压力对复合材料的强度影响不是很大。
(4)通过SEM 可以看出复合材料的内部比较致密,玻璃在870℃烧结时间3min 后把铜的包裹的比较好,没有出现气泡和裂纹,所以复合材料的强度比较大。
根据万用表可以测出复合材料导电,这是因为里面含有铜,并且分布较均匀。
参考文献[1]F E 卢博斯基;柯成;唐与湛;罗阳,何开元,非晶态金属合金,1989[2]Ma H;Zheng Q;Xu J Doubling the critical size for bulk metallic glass formation in the Mg-Cu-Y ternary system 2005(09)[3]赵彦钊,殷海荣,玻璃工艺学[M].北京:化学工业出版社2006.7。