烧结烟气分段式综合处理工艺
烧结烟气处理工艺流程
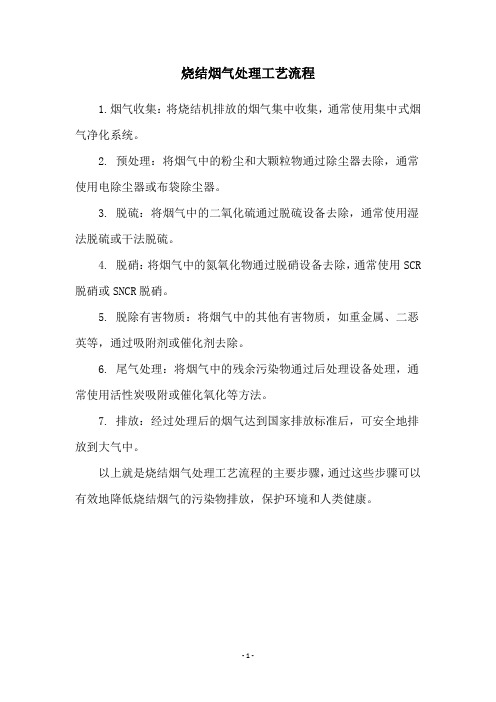
烧结烟气处理工艺流程
1.烟气收集:将烧结机排放的烟气集中收集,通常使用集中式烟气净化系统。
2. 预处理:将烟气中的粉尘和大颗粒物通过除尘器去除,通常使用电除尘器或布袋除尘器。
3. 脱硫:将烟气中的二氧化硫通过脱硫设备去除,通常使用湿法脱硫或干法脱硫。
4. 脱硝:将烟气中的氮氧化物通过脱硝设备去除,通常使用SCR 脱硝或SNCR脱硝。
5. 脱除有害物质:将烟气中的其他有害物质,如重金属、二恶英等,通过吸附剂或催化剂去除。
6. 尾气处理:将烟气中的残余污染物通过后处理设备处理,通常使用活性炭吸附或催化氧化等方法。
7. 排放:经过处理后的烟气达到国家排放标准后,可安全地排放到大气中。
以上就是烧结烟气处理工艺流程的主要步骤,通过这些步骤可以有效地降低烧结烟气的污染物排放,保护环境和人类健康。
- 1 -。
太钢烧结机烟气脱硫脱硝工艺演示幻灯片
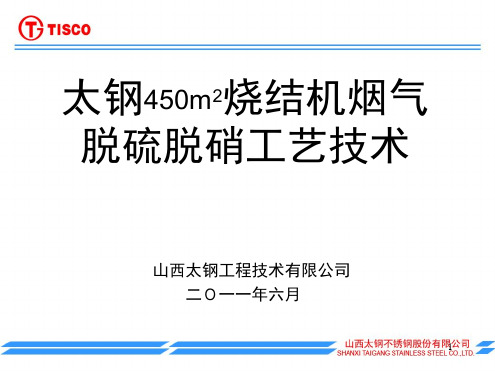
15
⑤、热风系统:
?吸附塔 ?发生器压力控制阀
?N2
?热气入口挡板
?热气循环风机
?助燃空气风机
?COG
?COG 增压风机
?N2
?热气发生器
?A ?COG 废气隔离
阀
?SRG 旁通 阀
7
1、烟气系统
?W G
?主风机 ?M
?M
?增压风机旁通挡 板
?M
?M ?隔离挡板
?吸附塔
?空气入口 挡板
?BUF
?M
?M
?增压风机入口挡板
?吸附塔入口挡 板
?M ?吸附塔出口挡板
①、系统正常运作时,烧结烟气通过机头电除尘器净化后,烟气含 尘浓度为98 mg/Nm3,烟气经过现有主风机及新增设的增压风机 进入脱硫脱硝设备,经过净化以后,再通过烧结主烟囱排入大 气。
?M
?二段灰尘收
集器 ?一段灰尘收
集器
?活性碳 筛子
?M ?M
?A
?解析塔
?SRG隔离 阀
?A ?A
?SRG
?冷却空气风 机
? 主要提供解析活性炭的热风。在此系统中,通过煤气 发生器将空气加热至450℃,在通过循环风机送至加 热段。
16
⑥、冷风系统:
? 在此部分,将经过解析后的活性炭,在冷却段中冷却 到150℃以下。
?通风
⑦、除尘系统: ?解析塔
?活性碳一号运输机 下部刮板式运输机
9
? 脱硫反应:
在脱硫反应中,是物理吸附和化学吸附的结合的复合反应;
a. 物理吸附 SO2→SO2(SO2吸附在活性炭微细孔中)
玻璃窑炉烟气综合治理的工艺选择与方案设计
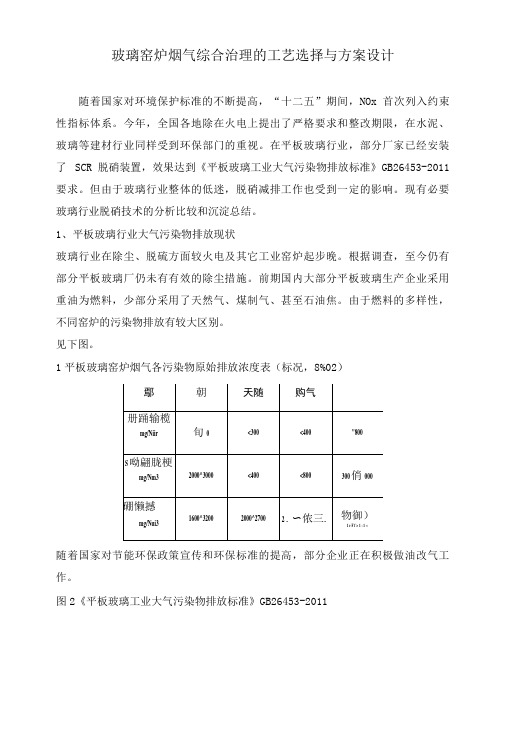
玻璃窑炉烟气综合治理的工艺选择与方案设计随着国家对环境保护标准的不断提高,“十二五”期间,NOx首次列入约束性指标体系。
今年,全国各地除在火电上提出了严格要求和整改期限,在水泥、玻璃等建材行业同样受到环保部门的重视。
在平板玻璃行业,部分厂家已经安装了SCR脱硝装置,效果达到《平板玻璃工业大气污染物排放标准》GB26453-2011 要求。
但由于玻璃行业整体的低迷,脱硝减排工作也受到一定的影响。
现有必要玻璃行业脱硝技术的分析比较和沉淀总结。
1、平板玻璃行业大气污染物排放现状玻璃行业在除尘、脱硫方面较火电及其它工业窑炉起步晚。
根据调查,至今仍有部分平板玻璃厂仍未有有效的除尘措施。
前期国内大部分平板玻璃生产企业采用重油为燃料,少部分采用了天然气、煤制气、甚至石油焦。
由于燃料的多样性,不同窑炉的污染物排放有较大区别。
见下图。
1平板玻璃窑炉烟气各污染物原始排放浓度表(标况,8%02)随着国家对节能环保政策宣传和环保标准的提高,部分企业正在积极做油改气工作。
图2《平板玻璃工业大气污染物排放标准》GB26453-2011新建企业大气污染物排放限值注:•4 1.2 口2014年1月1日起,现有企业执行衣2规定的大气污展物排放瞅值.4 1 4 n 2011年10月1 H起.新建企业执行表2规定的大气污染物持放限值•2、成熟技术选择2. 1除尘技术成熟的玻璃窑炉粉尘治理可选择电除尘、袋式除尘、湿法除尘等技术。
除尘技术的选择,将根据工程项目的适用工艺来确定。
如选择湿法脱硫时,湿法除尘将具有更好的协同适应性。
各种除尘技术性能表如下2. 2脱硫技术脱硫方案中,可选择成熟的湿法脱硫(双碱法、石灰石石膏法)、半干法、高温干法。
湿法中成功应用的方案有双碱法、石灰石石膏法、MgO法、氨法,根据调研情况,双碱法和石灰石石膏法在运行成本和操作维护上具有优势。
另脱硫技术的简化应用,可满足玻璃窑炉烟气的调质要求。
2.3脱硝技术脱硝主流技术有选择性催化还原反应(SCR)、选择性非催化还原反应(SNCR)及湿法脱硝。
烟气净化系统工艺说明书11
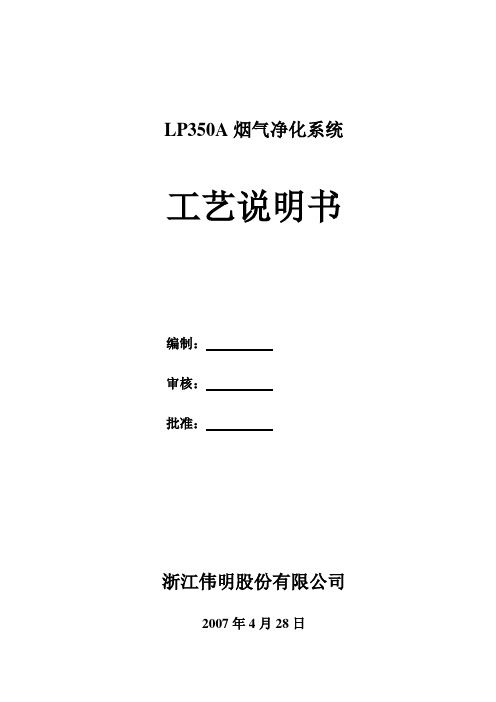
LP350A烟气净化系统工艺说明书编制:审核:批准:浙江伟明股份有限公司2007年4月28日LP350A烟气净化系统工艺说明书1 概述1.1产品特点YQJH×××系列垃圾焚烧烟气净化系统针对中国城市生活垃圾焚烧尾气的特点而设计。
烟气净化系统的设计符合《生活垃圾焚烧处理工程技术规范》(CJJ90-2002)的规定。
YQJH×××系列垃圾焚烧烟气净化系统具有工艺先进、设备设计合理、制作精良、耐腐蚀性能好、对垃圾焚烧烟气成分适应性强、负荷调节能力大、使用操作方便和自动化程度高等特点。
在合理的炉排和锅炉结构设计条件和自动控制系统的控制下,YQJH×××系列垃圾焚烧烟气净化系统可以保证烟气排放达到《生活垃圾焚烧污染控制标准》(GB18485-2001)的要求。
1.2主要用途及适用范围YQJH×××系列垃圾焚烧烟气净化系统用于生活垃圾焚烧发电厂焚烧尾气的净化。
适用范围如下:锅炉排烟温度范围:200~250℃;锅炉排烟含尘量:≤30g/Nm3;烟气处理量:≤110000Nm3。
1.3规格型号的组成及其代表意义规格型号的组成及其代表意义表示如下:设备改进号,A,B,C,……对应焚烧炉生活垃圾额定日处理垃圾量(t/d)烟气净化系统1.4使用环境条件1.4.1海拔高度:不超过3000m;1.4.2周围环境温度:-15℃~+40℃;1.4.3周围空气相对湿度:≤95%(+25℃);1.4.4防雨防晒:室内布置;1.4.5厂区地震基本烈度:≤7度。
1.5工作条件1.5.1电源AC380V,50Hz;AC220V,50Hz;1.5.2压缩空气压缩空气压力:0.7Mpa。
2 结构特征与工作原理2.1总体结构及其工作原理;YQJH×××系列垃圾焚烧烟气净化系统一般由石灰制浆系统、喷雾干燥吸收塔(SDA,Spray Dry Absorber)、旋转喷雾系统、活性炭喷射装置、布袋除尘器和飞灰输送系统等组成。
烧结烟气scr工艺
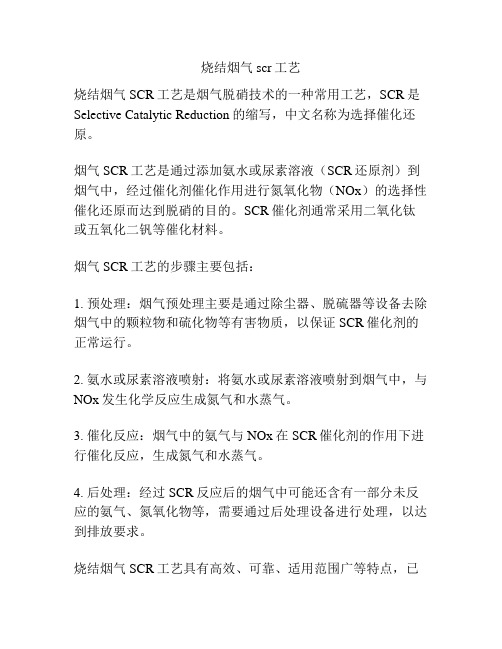
烧结烟气scr工艺
烧结烟气SCR工艺是烟气脱硝技术的一种常用工艺,SCR是Selective Catalytic Reduction的缩写,中文名称为选择催化还原。
烟气SCR工艺是通过添加氨水或尿素溶液(SCR还原剂)到烟气中,经过催化剂催化作用进行氮氧化物(NOx)的选择性催化还原而达到脱硝的目的。
SCR催化剂通常采用二氧化钛或五氧化二钒等催化材料。
烟气SCR工艺的步骤主要包括:
1. 预处理:烟气预处理主要是通过除尘器、脱硫器等设备去除烟气中的颗粒物和硫化物等有害物质,以保证SCR催化剂的正常运行。
2. 氨水或尿素溶液喷射:将氨水或尿素溶液喷射到烟气中,与NOx发生化学反应生成氮气和水蒸气。
3. 催化反应:烟气中的氨气与NOx在SCR催化剂的作用下进行催化反应,生成氮气和水蒸气。
4. 后处理:经过SCR反应后的烟气中可能还含有一部分未反应的氨气、氮氧化物等,需要通过后处理设备进行处理,以达到排放要求。
烧结烟气SCR工艺具有高效、可靠、适用范围广等特点,已
广泛用于钢铁、水泥、发电、玻璃等行业的烟气脱硝处理中,可以有效降低烟气中的氮氧化物排放,减少对环境的污染。
我国烧结烟气脱硫现状及脱硝技术研究

我国烧结烟气脱硫现状及脱硝技术研究随着全世界经济的快速发展,环境问题已经成为了我们人类所面临的最严峻的问题之一。
而其中大气环境又是人类赖以生存的最基本的要素之一,如今人们还是主要利用煤、石油和天然气等能源作为燃料,它们的燃烧会产生大量的二氧化硫、氮氧化合物和烟尘颗粒物等,而其中SO2和NOx又是主要的大气污染物,对大气环境造成了严重的污染。
大气污染造成的自然灾害也在我们的身边频繁發生,酸雨泛滥、气候异常、光化学烟雾等严重影响了我们的生活、健康,可以预见,如果随着大气环境的不断恶化,最终会导致地球生态环境和平衡遭到严重破坏,人类以及动植物的生存将会面临严重威胁。
标签:烟气烧结;脱硫技术;脱硝技术一、烟气脱硫脱硝技术现状目前,人们为了减少二氧化硫排放到大气中去,主要采用的控制方法是燃烧一些低硫燃料、对燃料进行前期脱硫、燃料燃烧过程脱硫以及末端尾气处理。
燃烧前脱硫主要是利用一些特定的方法对煤等燃料进行净化,以去除原来燃料中的硫分、灰分等杂质。
燃烧过程中脱硫主要是指当煤等燃料在炉内燃烧时,同时向炉内恰当的位置喷入脱硫剂(常用的有石灰石、熟石灰、生石灰等),脱硫剂在炉内较高温度下受热分解成CaO和MgO等,然后与燃烧过程中产生的SO2和SO3发生反应,生成硫酸盐和亚硫酸盐,最后以灰渣的形式排出,从而达到脱硫的目的。
而目前世界上应用比较成熟的技术主要是燃烧后脱硫,即烟气脱硫技术。
其中,又以一些湿法、干法以及其他典型的方法应用最为广泛。
二、烟气脱硫技术(一)湿法烟气脱硫技术(1)石灰石/石灰法石灰石/石灰法烟气脱硫是采用石灰石或者石灰浆液脱除烟气中二氧化硫的方法。
石灰石/石灰法开发比较早,工艺成熟,吸收剂价格便宜而且容易得到,应用比较广泛。
其主要工艺参数为:浆液pH在5.6-7.5之间,浆液固体含量:1.0%-15%,液气比:大于5.3L/m3钙硫比为1.05-1.1之间,碳酸钙粒度90%通过325目,纯度大于90%脱硫率大于90%。
烧结烟气循环工艺

烧结烟气循环工艺1. 引言烧结烟气循环工艺是一种高效利用烧结烟气中热能和废气中有害物质的技术。
通过对烧结烟气进行净化和循环利用,可以减少环境污染和能源消耗,提高工业生产的可持续发展能力。
本文将详细介绍烧结烟气循环工艺的原理、主要设备和应用案例。
2. 原理烧结烟气循环工艺的基本原理是将烧结烟气经过处理后,分离出其中的有害物质,同时回收其中的热能,再经过处理后重新进入烧结系统。
其主要步骤包括:烟气净化、烟气冷却、烟气再加热和烟气再循环。
2.1 烟气净化烟气净化是烧结烟气循环工艺的第一步。
通过使用除尘器、脱硫装置和脱硝装置等设备,可以将烟气中的颗粒物、二氧化硫和氮氧化物等有害物质去除,使烟气达到排放标准。
其中,除尘器可用于捕集颗粒物,脱硫装置可用于去除二氧化硫,脱硝装置可用于降低氮氧化物的浓度。
2.2 烟气冷却烟气冷却是为了降低烟气温度,以便后续步骤的操作和设备的正常运行。
通常采用烟气换热器进行烟气冷却,将烟气中的热能传递给饱和蒸汽或其他工艺介质。
这样既可以回收烟气中的热能,又可以使烟气温度降低到适宜处理的范围。
2.3 烟气再加热烧结过程中的煤气可以被燃烧后再加热烧结烟气,从而提高烧结烟气的温度。
这可以提高烧结过程的效率和产量,减少固定碳的负荷。
烟气再加热可以通过燃烧煤气或其他可燃介质来实现。
2.4 烟气再循环烟气再循环是烧结烟气循环工艺的核心部分。
通过将经过净化和处理的烟气再回收利用,可以达到节能减排的目的。
具体操作可分为两个阶段:回收再循环和再利用。
回收再循环阶段将烟气从烧结系统中抽出,经过处理后再重新进入烧结系统。
再利用阶段将回收的烟气中的热能和有用组分用于其他工艺过程中,如预热燃料、热风炉供热等。
3. 主要设备烧结烟气循环工艺涉及的主要设备包括除尘器、脱硫装置、脱硝装置、换热器、再加热炉等。
3.1 除尘器除尘器主要用于去除烟气中的颗粒物。
按照除尘原理的不同,常见的除尘器有电除尘器、湿式除尘器和布袋除尘器等。
工艺方法——烧结烟气及污染物减量技术

工艺方法——烧结烟气及污染物减量技术工艺简介一、降低烧结系统漏风技术烧结机漏风量的大小与风箱系统的内外压差△P及移动台车与风箱间结合面的间隙δ有关。
△P决定于风箱内负压的大小,风箱内负压的大小又决定于烧结混合料的阻力大小。
δ与间隙位置、密封结构、加工制造、运行工况等息息相关。
可见,通过加强原料准备、强化混匀制粒等措施改善烧结料层透气性,开发先进的密封技术以减小设备动静结合面漏风间隙是降低烧结系统漏风量的关键。
1、降低烧结料层阻力技术(1)生石灰双级双螺旋搅拌消化技术常规的生石灰消化系统存在消化能力差、时间短、除尘难度大等问题,限制了该技术的应用。
双级双螺旋搅拌生石灰消化技术及装备,将整个消化过程分为两级(一级预消化、二级充分消化),延长了消化时间,完善了消化过程,提高了消化率。
它在单螺旋的基础上,增加一个螺旋转子,形成双轴搅拌形式,具有搅拌、粉碎结块和自清理等多重作用与功效,大幅提高了搅拌频率和消化反应速度。
针对生石灰消化过程产生的粉尘强黏结性、亲水性、高分散性及水硬性等几大特点,开发出复合湿式除尘技术。
双级双螺旋搅拌生石灰消化器及配套复合湿式除尘器已于2016年底在新余钢铁6号烧结机投入运行,与烧结机同步作业,消化率达87.5%,混合料制粒效果改善,年增产烧结矿8万吨,粉尘排放浓度低至9.87mg/m3,配料室环境明显改善,消化系统除尘废水实现“零”排放。
(2)强化混匀制粒技术强力混匀装备根据结构不同,可分为卧式和立式强力混合机。
卧式强力混合机在工作过程中,筒体固定,主轴旋转带动犁头运动,使物料产生对流运动、混合充分。
立式强力混合机在工作过程中,转动的混合桶体和高速旋转的搅拌桨配合,使混合料进行剧烈的对流、剪切、扩散运动,混匀更为充分。
中冶长天成功开发出具有自主知识产权的卧式和立式强力混合机,其中,立式强力混合机与进口爱立许的相比,一次性投资成本可降低40%,运行成本可降低20%,且耐磨件使用寿命更长。
钢铁冶炼中烧结烟气污染物的特征及处理方法

钢铁冶炼中烧结烟气污染物的特征及处理方法在钢铁冶炼工序中,烧结过程所排放的烟气是体量最大、污染物种类较为集中且浓度较高的一种工业废气。
烧结烟气中包含的主要大气污染物有SO2、NO、Hg等重金属以及二噁英等有机污染物,据统计,每生产1t烧结大约产生4000-6000ml的烟气,其携带粉尘量较大,一般含尘量为0.5-15g/m3,且含有SO x、NOx等酸性气态污染物。
因此烧结烟气的治理与净化是冶金行业大气污染物节能减排的重点。
一、烧结烟气的特征1、烧结烟气量大且分布不均匀由于漏风率高(40%-50%)和固体料循环率高,有相当一部分空气没有通过烧结料层,使烧结烟气量大大增加。
每产生一吨烧结矿大约产生4000-6000m3烟气。
由于烧结料透气性的差异及辅料不均等原因,造成烧结烟气系统的阻力变化较大,最终导致烟气量变化大,变化幅度可高达40%以上。
2、二氧化硫浓度变化大SO2排放浓度的波动范围较宽,受矿石和燃料中S含量和烧结工况决定,随着原燃料供需矛盾的不断变化和钢铁企业追求成本的最低化。
钢铁企业所使用原燃料的产地、品种变化很大,由此造成其质量、成分(包括含硫率)等的差异波动很大,使得烧结生产最终产生的二氧化硫的浓度变化范围较大。
3、烧结烟气成分复杂由于使用铁矿石为原料,因此烧结烟气的成分相对比较复杂,除二氧化硫外,含有多种腐蚀性气体和重金属污染物。
包括HCI、HF、NOx等腐蚀性气体,以及铅、汞、铬、锌等有毒重金属物。
4、烟气温度变化范围大、含氧量与含湿量高随着生产工艺的变化,烧结烟气的温度变化范围一般在120-180℃,但有些钢厂从节约能源消耗、降低运行成本考虑,采用低温烧结技术后,使烧结烟气的温度大幅下降,可低至80℃左右。
烟气含湿量大,为了提高烧结混合料的透气性,混合料在烧结前必须加适量的水制成小球,所以烧结烟气的含湿量较大,按体积比计算,水分含量一般在10%左右。
含氧量一般为15%-18%。
烧结机头烟气氧含量为15%-18%。
三种脱硫方案综合比较
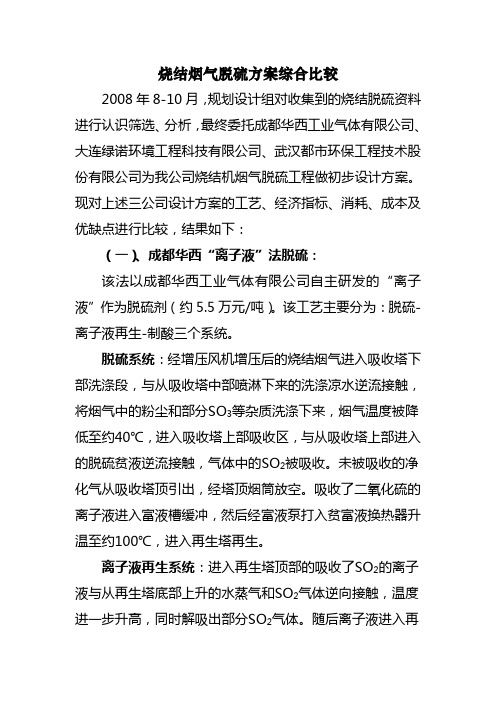
烧结烟气脱硫方案综合比较2008年8-10月,规划设计组对收集到的烧结脱硫资料进行认识筛选、分析,最终委托成都华西工业气体有限公司、大连绿诺环境工程科技有限公司、武汉都市环保工程技术股份有限公司为我公司烧结机烟气脱硫工程做初步设计方案。
现对上述三公司设计方案的工艺、经济指标、消耗、成本及优缺点进行比较,结果如下:(一)、成都华西“离子液”法脱硫:该法以成都华西工业气体有限公司自主研发的“离子液”作为脱硫剂(约5.5万元/吨)。
该工艺主要分为:脱硫-离子液再生-制酸三个系统。
脱硫系统:经增压风机增压后的烧结烟气进入吸收塔下部洗涤段,与从吸收塔中部喷淋下来的洗涤凉水逆流接触,将烟气中的粉尘和部分SO3等杂质洗涤下来,烟气温度被降低至约40℃,进入吸收塔上部吸收区,与从吸收塔上部进入的脱硫贫液逆流接触,气体中的SO2被吸收。
未被吸收的净化气从吸收塔顶引出,经塔顶烟筒放空。
吸收了二氧化硫的离子液进入富液槽缓冲,然后经富液泵打入贫富液换热器升温至约100℃,进入再生塔再生。
离子液再生系统:进入再生塔顶部的吸收了SO2的离子液与从再生塔底部上升的水蒸气和SO2气体逆向接触,温度进一步升高,同时解吸出部分SO2气体。
随后离子液进入再沸器进一步升温到约110℃,SO2气体全部解吸出来。
从再沸器出来的气液混合物在再生塔底部分离,液体从底部出口流出,进入贫富液换热器;SO2气体和水蒸气向上流动,从顶部出口出来后进入再生气冷却器降温到约40℃,然后进入再生气分离器进行气液分离,分离出的高纯度SO2气体作为制酸原料进入制酸系统;液体经冷凝水泵增压后回流至再生塔顶部。
制酸系统:空气和SO2气体一并进入干燥塔,经金属丝网除沫器除雾、除沫后由SO2鼓风机送至转化工段。
经一次转化后的气体进入吸收塔,用98%H2SO4吸收其中的SO3,经塔顶的金属丝网除沫器除沫、除雾后,去主系统。
干燥、吸收工段有93%、98%硫酸的串酸管线,产品酸由98% H2SO4酸冷却器冷却后产出。
烧结机烟气脱硫除尘工艺设计说明书
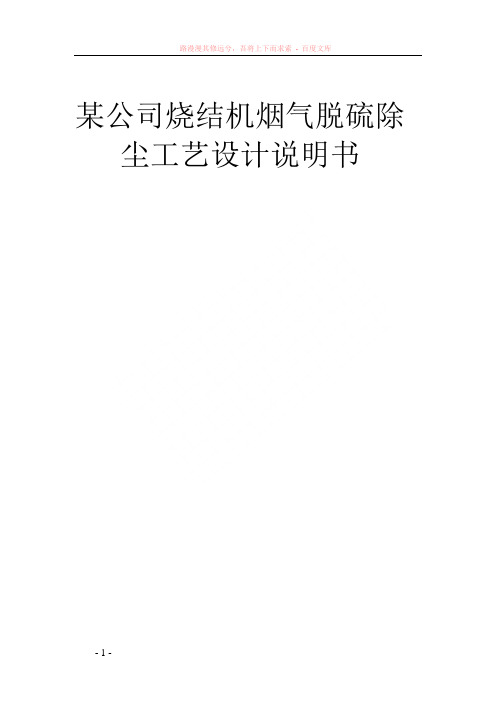
某公司烧结机烟气脱硫除尘工艺设计说明书目录一.设计背景1.设计对象-------------------------------12.设计原始数据---------------------------13.设计施工地点---------------------------2 二.设计步骤⒈原始数据的计算----------------------------------2⒉净化系统设计方案的分析确定----------------------3⒊除尘器和脱硫净化塔的比较和选择------------------4⒋管网布置及计算----------------------------------8⒌风机及电机的选择设计---------------------------13 三.小结1.处理效果-----------------------------------162.工程造价-----------------------------------163.综合评价-----------------------------------16 四.参考文献-------------------------------------16 五.附图------------------------------------------17一.设计背景介绍:1.设计对象内容:某公司烧结机烟气脱硫除尘工程设计方案。
2.设计原始数据资料:①锅炉型号:SZL4-13型,共4台(2.8MW×4)②设计耗煤量:600kg/h(台)③排烟温度:160℃④烟气密度(标准状态下):1.34kg/m3⑤空气过剩系数:α=1.4⑥排烟中飞灰占煤中不可燃成分的比例:16%⑦烟气在锅炉出口前阻力:800Pa⑧当地大气压力:97.86kPa⑨冬季室外空气温度:-1℃⑩空气含水(标准状态下)按0.01293kg/m3⑪烟气其他性质按空气计算⑫煤的工业分析值:⑬C Y=68% H Y=4% S Y=1% O Y=5%⑭N Y=1% W Y=6% A Y=15% V Y=13%⑮按锅炉大气污染物排放标准(GB13271-2001)中一类区II时段标准执行。
烧结烟气综合治理技术
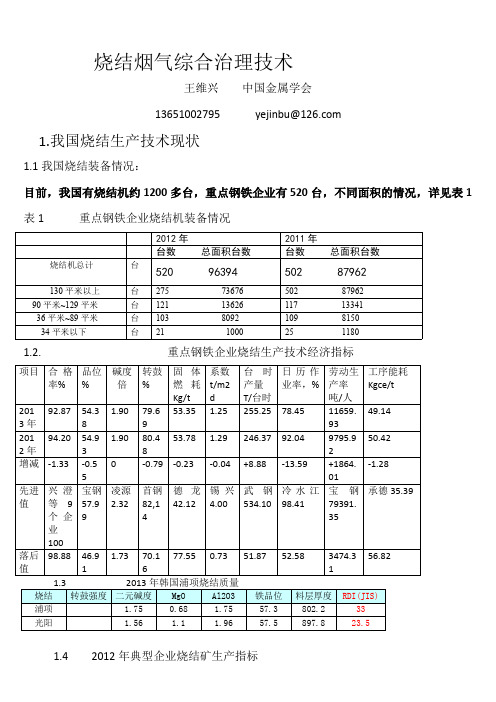
3) 脱硫装置类型情况: 据统计,全国有 372 套(454 台烧结机),面积 74930m2,其中循环流化床 32 套、
因此,钢铁企业要在不到两年的时间内全面实施提标改造,时间紧、任务重、资金 压力大。特别是在钢铁行业大面积亏损的情况下,环保提标改造任务十分艰巨。
6.烧结烟气综合治理技术 国家提出要对烧结烟气要进行综合治理,即要进行脱硫、脱硝、脱二噁英、除尘
联合进行;不能再单一进行脱硫了。
选择性烧结烟气处理技术:烧结点火器后约三分之一风箱的烟气中含硫不高,且 温度高。这部分废气可不必脱硫,返回烧结,作热风烧结,即节能(可降低固体燃耗 2kg/t),减少烟气处理量,又有降低脱硫运行费的好效果,还可减少废气排放量。 6.1.烧结烟气脱硫技术 1) 烧结烟气脱硫技术分类:干法、半干法和湿法。
56.99
2.00
1.23 740 50.7 0.58 46.8 69.7 77.7 55.8 2.00
柳钢 110 128
1.62 650 42.1 0.58 42.6 50.1 77.0 52.7
2.06
2.钢铁企业面临着严峻的环保形势
国家已将环境保护定为我国发展的基本国策。国家陆续公布了《中华人民共和国环保
湿法主要有:石灰-石膏法、硫铵法、氧化镁法、双碱法、离子液法等。 干法主要有:LJS 循环流化床法、ENS 法、密相干塔法、GSCA 双循环流化床法、
MEROS 烟道喷射法、活性炭吸附法、NID 烟道循环法等。 半干法主要有:循环流化床(CFB),SDA 旋转喷雾法,密相干塔法等。
脱硫效率高。易造成低温腐 蚀以及烟囱雨,PM2.5 的主 要产生源,很难实现多污染 物的协同控制。
太钢炼铁厂烧结烟气脱硫脱硝技术

5、入口氮氧化物
吸附塔入口 NOX ppm 200.0 150.0 100.0 50.0 0.0 0 500 1000 1500 2000 2500 3000 3500 4000
入口氮氧化物浓度平均102mg/Nm3。
21
6、出口氮氧化物
吸附塔出口 NOX ppm 80.0 60.0 40.0 20.0 0.0 0 500 1000 1500 2000 2500 3000 3500 4000
脱硝效率平均:39.9%,
24
9、保证性能与实测值如下表所示
各性能指标为投运4个月后(2011年1月)经市环保局检测的结果。所有项 目均超过保证性能。 另外,生产的硫酸达到了工业硫酸一等品质,在太钢轧钢系统进行了有效 利用。
保证项目
SO2(脱硫)
保证值 mg/m3N-dry
% mg/m3N-dry %
三烧 硫酸产量(T)
2)、硫酸产量
从2010年9月到2012年6月产酸13001吨,平均每月590吨。
27
3)、液氨用量
300 250 200 150 100 50 0 三烧 液氨用量(T)
20 10 年 20 11 10 月 年 20 12月 11 年 20 1月 11 年 20 2月 11 年 20 3月 11 年 20 4月 11 年 20 5月 11 年 20 6月 11 年 20 7月 11 年 20 8月 11 20 年9 11 月 年 20 10 11 月 年 20 11 11 月 年 20 12月 12 年 20 1月 12 年 20 2月 12 年 20 3月 12 年 20 4月 12 年 20 5月 12 年 6月
太钢炼铁厂烧结烟气脱硫脱硝
技术及应用
烧结烟气循环设计工艺流程

烧结烟气循环设计工艺流程1一般规定1.1 烧结烟气循环技术的实施,总体原则是在烧结矿产量、质量指标以及烧结矿硫含量不受明显影响的前提下,提高烧结清洁生产的水平。
烧结烟气循环进入料面的气体,相比常规烧结的空气,其氧含量降低,温度提高,二氧化碳、一氧化碳、水蒸气含量增加。
氧含量降低会对烧结指标产生不利影响,但温度、一氧化碳含量的提高,以及含有适量的二氧化碳、水蒸气,可以削弱因氧含量下降而引起的负面影响。
合理的气流介质条件是确保烧结指标不受影响的关键。
氧气的影响:烧结气流介质中的氧气含量降低至一定程度时,因影响到燃料的充分燃烧,烧结矿的质量会急剧变差,此氧含量为烧结指标明显受到影响的临界点。
因此烧结气流介质中的氧气含量不宜低于此临界值。
相关研究表明,赤铁矿为主、磁铁矿为主、褐铁矿为主的烧结过程需氧量不同,磁铁矿氧化需要额外消耗氧量,褐铁矿因燃料用量高而氧消耗量大,采用烟气循环时,其氧含量的临界值更高,三种原料体系的氧含量临界值分别为15%、17%、18%。
因此,氧含量18%为普遍适用的临界值。
一般而言,烧结烟气中氧气含量约为12%~16%,为了保证循环至台车面的气流介质中的氧气含量大于临界值,通常在烧结烟气中配加富氧气体,富氧气体可为空气、冷却废气或纯氧。
二氧化硫的影响:烧结气流介质中含有少量的二氧化硫对烧结矿的产品质量指标影响不大,而当烧结气流介质中二氧化硫的含量大于700mg/Nm3时,硫在成品烧结矿中会发生明显的富集。
因此规定烧结气流介质中二氧化硫含量最好不超过700mg/Nm3。
水蒸气的影响:烧结气流介质中水蒸气在高温下会与燃料发生水煤气反应而起促燃作用,可以一定程度减轻氧含量下降对燃料燃烧的不利影响,因此少量的水蒸气对烧结过程有促进作用。
但水蒸气含量过高,会增加烧结过程料层的过湿,对各项烧结指标不利,所以水蒸气含量有临界值。
赤铁矿为主、磁铁矿为主、褐铁矿为主的原料,各自的水蒸气含量临界值不同。
烧结全过程节能减排生产实践

烧结全过程节能减排生产实践DOI:10.3969/j.issn.l006-110X.2021.02.005烧结全过程节能减排生产实践聂荣恩,张文政,陈艳(天津市新天钢联合特钢有限公司,天津361500)[摘要]烧结矿生产过程中,能源消耗高、污染物排放量大是钢铁企业面临的比较严峻的问题。
为了降低烧结生产污染物排放压力,提高能源利用率,天钢联合特钢通过优化烧结原、燃料的成分和配比,改进烧结的工艺控制,实施厚料层烧结以及烧结烟气脱硫、脱硝净化等技术措施,实现了烧结生产污染物排放达到超低排放标准,能源利用率显著提升,获得了较好的经济效益和社会效益。
[关键词]烧结生产;污染物排放;脱硫脱硝;经济效益Production practice of energy savingand emission reduction in the whole sintering processHE Rong-en*ZHANG Wen-zheng and CHEN Yan(Tianjin New Tianvanv uuited spepm steel Co.Ltd.,TIANJIN3。
700)Abstract DuOna sintered o re proOuction,high eperay consumption and larpe pollutant emission are seoons proOlems feed bs ion nd steel er—oOses.In orUcs to reduce sintered proOuction pollutant emission pressure nV improve eperay utilization rate,bs oo-mizba the constituevts and popoO—nba of sinterina f e dstoch nV fiei,improvina the process control of sinterina,implemevtinc thich mPeOb layes sinterina,nV sb—Ong fuc yas duuIfuOzP—n,derit—ppt—n puObcaPon nd othes technicai measures, the discharpe of poOu—nts fom sinterina poOuction has reached the ultra-low emission stanVarU in Combined with Spuib Steel Co.,the utiPzation rate of eperay has improved sinnifpn—丫,nd gooO economic nV sociai beveUts have beer oO—ived.Key words sintered proOuchon,pollutant emission,desulfiOzatiov devit—PcaVon,cconomic eUicierca0引言钢铁工业是国民经济支柱产业,属于高能耗、高物耗和高污染行业,也是大气污染的主要来源之一。
烧结烟气脱硫脱硝处理技术的比较分析
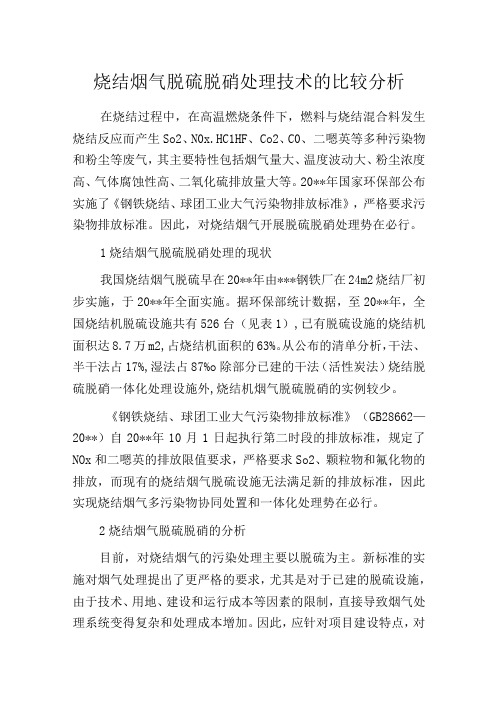
烧结烟气脱硫脱硝处理技术的比较分析在烧结过程中,在高温燃烧条件下,燃料与烧结混合料发生烧结反应而产生So2、N0x.HC1HF、Co2、C0、二嗯英等多种污染物和粉尘等废气,其主要特性包括烟气量大、温度波动大、粉尘浓度高、气体腐蚀性高、二氧化硫排放量大等。
20**年国家环保部公布实施了《钢铁烧结、球团工业大气污染物排放标准》,严格要求污染物排放标准。
因此,对烧结烟气开展脱硫脱硝处理势在必行。
1烧结烟气脱硫脱硝处理的现状我国烧结烟气脱硫早在20**年由***钢铁厂在24m2烧结厂初步实施,于20**年全面实施。
据环保部统计数据,至20**年,全国烧结机脱硫设施共有526台(见表1),已有脱硫设施的烧结机面积达8.7万m2,占烧结机面积的63%。
从公布的清单分析,干法、半干法占17%,湿法占87%o除部分已建的干法(活性炭法)烧结脱硫脱硝一体化处理设施外,烧结机烟气脱硫脱硝的实例较少。
《钢铁烧结、球团工业大气污染物排放标准》(GB28662—20**)自20**年10月1日起执行第二时段的排放标准,规定了NOx和二嗯英的排放限值要求,严格要求So2、颗粒物和氟化物的排放,而现有的烧结烟气脱硫设施无法满足新的排放标准,因此实现烧结烟气多污染物协同处置和一体化处理势在必行。
2烧结烟气脱硫脱硝的分析目前,对烧结烟气的污染处理主要以脱硫为主。
新标准的实施对烟气处理提出了更严格的要求,尤其是对于已建的脱硫设施,由于技术、用地、建设和运行成本等因素的限制,直接导致烟气处理系统变得复杂和处理成本增加。
因此,应针对项目建设特点,对新建烧结机、已建成的脱硫设施区别对待,综合考虑一种一体化的处理技术。
由于现有的烧结烟气脱硫工艺主要集中于传统的干法、半干法、湿法,因此分别选取干法、半干法、湿法脱硫脱硝一体化等技术开展分析比照。
2.1活性炭烟气净化技术20世纪50年代德国开始研发活性炭吸附工艺,20世纪60年代日本也开始研发。
长江钢铁烧结余热发电实践

长江钢铁烧结余热发电实践周劲军;史德明;包自力;顾厚淳【摘要】为了能使环冷机余热得到有效利用,采用BOT模式承建了烧结余热发电项目.通过采用分段热风循环、烧结余热发电智能控制系统(BP-CICS)等创新技术,年净供电量达到7700万kWh以上、吨矿发电量达到17kWh以上、系统供电率达到77%以上.【期刊名称】《冶金动力》【年(卷),期】2018(000)012【总页数】4页(P40-43)【关键词】烧结环冷机;余热;发电系统;实践【作者】周劲军;史德明;包自力;顾厚淳【作者单位】马钢(集团)控股有限公司,安徽马鞍山 243000;马钢(集团)控股有限公司,安徽马鞍山 243000;马钢(集团)控股有限公司,安徽马鞍山 243000;马钢(集团)控股有限公司,安徽马鞍山 243000【正文语种】中文【中图分类】TM6171 项目概况在钢铁生产过程中,烧结工序能耗约占总能耗的10%~12%,其中冷却机排放的废气显热约占20%~28%[1]。
马钢集团安徽长江钢铁股份有限公司建有3条192m2烧结环冷生产线,烧结机配套3台235 m2环冷机。
为了能使环冷机余热资源得到有效利用,由马钢集团安徽欣创节能环保科技股份有限公司采用BOT模式承建了长江钢铁烧结余热发电项目:新建3台22 t/h(7 t/h)双通道双压式烧结余热锅炉;1套15 MW补凝式汽轮发电机组,余热锅炉产生中压蒸汽作为汽轮机的主蒸汽、低压蒸汽作为汽轮机补汽,推动汽轮机发电机组产生电能。
该项目于2014年12月开工,2015年10月投产,经过一系列攻关调试,年净供电量达到7700万kWh以上,吨矿发电量达到17 kWh以上,系统供电率达到77%以上,超过设计参数。
长江钢铁烧结余热发电实践是马钢在总结中国第一套烧结余热发电系统经验基础上的又一次实践创新。
该项目成功实施,为国内余热利用项目的高效利用提供了宝贵经验,对推动行业节能工作有着重要的意义。
烧结工艺废气处理工艺情况调查

烧结工艺废气处理工艺情况调查摘要:本文在对烧结烟气特点的分析基础之上, 对我国烧结烟气脱硫的进展情况进行了简单介绍。
并就目前在国内外烧结脱硫行业的几种典型的脱硫方式进行了介绍, 最后给出在选择脱硫方案时所需要注意的几个问题。
关键词:烧结,烟气脱硫脱硝,烟气处理工艺1、引言近年来, 我国钢铁行业飞速发展, 我国粗钥产量已连续多年居世界首位。
但由于钢铁生产消耗大里的燃料和矿石,产生大量的大气污染物, 对环境的影响不断加重:钢铁行业的SO2等大气污染物的排放量已仅次于电力行业,排第二位;尤其烧结工艺,产生的SO2、CO2等污染排放量占钢铁行业年排放量的40%—60%,而烧结工艺过程中产生的SO2年排放量约占钢铁企业年排放量的40%~60%。
因此,控制烧结生产过程中SO2的排放,是控制钢铁企业SO2污染的重点,更是控制大气SO2污染的重点。
对烧结烟气污染物排放治理已迫在眉睫,并且对生态环境的保护具有重要的意义。
对于烟气的脱硫脱硝,在燃煤电厂行业出现较早。
现在大多的烧结烟气脱硫技术都是在燃煤电厂烟气脱硫技术上发展而来的。
要想在烧结烟气脱硫上取得成功,就必须研究烧结烟气与电厂烟气相比的独特之处,并针对其特殊性对燃煤脱硫技术加以改进,使之更有效的应用于烧结烟气脱硫。
2、烧结烟气的特点烧结烟气是烧结混合料点火后, 随着台车的运行, 在高温烧结成型过程中所产生的含尘废气. 其突出特点是:(1)由于烧结机漏风率高, 相当一部分空气没有通过烧结料层,使烧结烟气量大大增加, 约合4000—6000m3/t烧结矿。
(2)烧结烟气温度较高, 波动大, 随工艺操作的不同有变化, 一般在120-180℃。
(3)烧结烟气含尘量大, 约在10g/Nm3。
(4) SO2浓度含量低,浓度含量波动大,根据原材料差异。
(5)含湿量大,水分含量高达10%左右。
(6)含有腐蚀性气体及重金属污染物,烟气中含有HcL、SO、NO、HF、Hg等。
(7)含有二垩英(Dioxin)。
生活垃圾焚烧发电厂烟气处理工艺
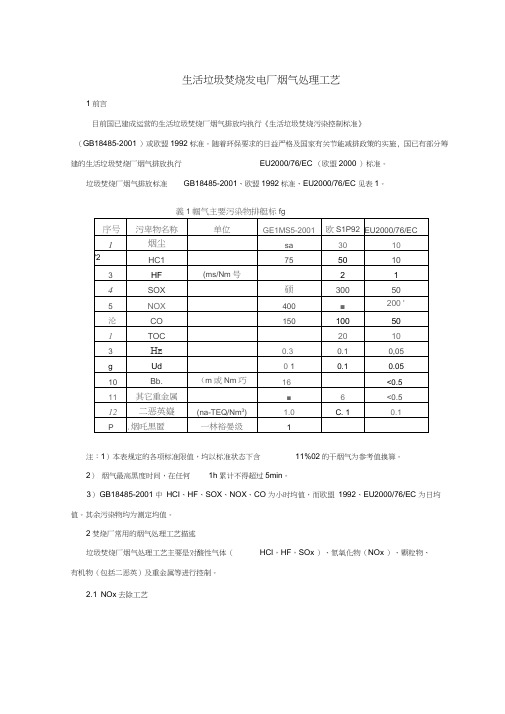
生活垃圾焚烧发电厂烟气处理工艺1前言目前国已建成运营的生活垃圾焚烧厂烟气排放均执行《生活垃圾焚烧污染控制标准》(GB18485-2001 )或欧盟1992标准。
随着环保要求的日益严格及国家有关节能减排政策的实施, 国已有部分筹建的生活垃圾焚烧厂烟气排放执行EU2000/76/EC (欧盟2000 )标准。
垃圾焚烧厂烟气排放标准GB18485-2001、欧盟1992标准、EU2000/76/EC 见表1。
注:1)本表规定的各项标准限值,均以标准状态下含11%02的干烟气为参考值换算。
2)烟气最高黑度时间,在任何1h累计不得超过5min。
3)GB18485-2001 中HCI、HF、SOX、NOX、CO 为小时均值,而欧盟1992、EU2000/76/EC 为日均值。
其余污染物均为测定均值。
2焚烧厂常用的烟气处理工艺描述垃圾焚烧厂烟气处理工艺主要是对酸性气体(HCI,HF,SOx )、氮氧化物(NOx )、颗粒物、有机物(包括二恶英)及重金属等进行控制。
2.1 NOx去除工艺目前国已运行的生活垃圾焚烧厂均未设置专门的脱氮装置,烟气中的 在300~400mg/Nm3 ,能够达到 GB18485-2001 中 400mg/Nm3 的排放限值,但达不到 EU2000/76/EC 中 200mg/Nm3 的排放限值,必须设置专门的脱氮设施。
NOx 去除工艺主要有选择性非催化还原法( SNCR )和选择性催化还原法( SCR )。
SCR 法是在催化剂作用下 NOx 被还原成N2 ,为达到SCR 法还原反应所需的 200 C 的温度,烟 气在进入催化脱氮器前需加热。
SCR 法可将 NOx 排放浓度控制在 50mg/Nm3 以下。
SNCR 是以 NH4OH (氨水)或 (NH2)2CO (尿素)作为还原剂,将其喷入焚烧炉。
NOx 在高温 下被还原为 N2和H2O 。
SNCR 法可将NOx 排放浓度控制在 200mg/Nm3 以下。
- 1、下载文档前请自行甄别文档内容的完整性,平台不提供额外的编辑、内容补充、找答案等附加服务。
- 2、"仅部分预览"的文档,不可在线预览部分如存在完整性等问题,可反馈申请退款(可完整预览的文档不适用该条件!)。
- 3、如文档侵犯您的权益,请联系客服反馈,我们会尽快为您处理(人工客服工作时间:9:00-18:30)。
烧结烟气分段式综合处理工艺烧结是钢铁冶炼过程中SO2和NO x最大的产生源,约有51%~62%的SO2及48%的NO x来自烧结工序,因此烧结厂成为钢铁企业环境治理的重中之重。
目前烧结烟气中污染物的脱除基本采取单一末端处理工艺。
这种处理工艺存在烟气处理量大、污染物浓度偏低、受生产过程波动影响较大等弊端。
随着国家对烟气中污染物限制排放种类的增多及排放量的要求越发严格,单一污染物的末端处理工艺设备配置越来越复杂,占地越来越大,势必造成建设投资及生产运行成本不断攀升。
根据研究成果显示,在不同的烧结区段,随着烧结气氛中O2和CO x浓度的变化,烟气中SO2和NO x 的浓度随着料温不断升高也产生相应变化。
据此类研究结论,并结合有关烧结机尾烟气热风烧结的实践,本文以210m2烧结机为例,设计一种选择性的烧结烟气分段式综合处理工艺。
该工艺是将热风烧结生产工艺与烟气脱硫脱硝分段治理工艺有机结合的烧结烟气环保减排综合处理工艺。
一、烧结烟气中SO2、NO x、CO x浓度在烧结过程中分布特点1、烧结过程中SO2的形成及分布特点烧结烟气中的SO2主要是由含铁原料中的FeS2,FeS和燃料中的有机硫,FeS2或FeS氧化生成,还有部分来自硫酸盐的高温分解。
SO2的产生存在于烧结生产的整个过程。
在烧结生产过程中,烟气温度快速升高之前(即过湿带完全消失之前),烟气中SO2浓度一直处于较低且较稳定状态;当烟气温度开始快速升高(即干燥带接近烧结料底层时),料层原先吸附的SO2快速释放导致SO2浓度迅速升高;当燃烧带接近烧结料底层和达到烧结终点之前,SO2浓度达到最大值。
由此可以看出,烧结生产过程中的SO2浓度与烟气温度存在对应关系,但SO2浓度最大值出现的时间点比烟气温度最高点的时间要提前一些。
2、烧结过程中NO x形成及铁酸钙的催化作用烧结烟气中NO x主要由烧结生产过程中气体、固体燃料的燃烧产生。
烟气中生成的NO x主要以NO 为主,只有很少量NO2。
高碱度烧结矿生产过程中其主要矿物相是铁酸钙。
据有关研究发现,在CO还原NO的反应中,铁酸钙起显著催化作用,它先被CO还原再被NO氧化,因此该反应属于自催化;同时铁酸钙催化NO还原还服从多相催化的吸附活化物理论,在铁酸钙催化剂活性部位发生NO分子吸附、离解、表面活性物种的重组和产物脱附的反应。
在这2种反应机理共同作用下,该还原反应的活化能由246.68kJ/mol降到138.80kJ/mol,且加快了反应速度。
铁酸钙有3种不同种类,其催化能效排序依次为CaO•Fe2O3>CaO•2Fe2O3>2CaO•Fe2O3。
因此,在烧结过程中希望尽可能的产生铁酸钙系粘结相,在烧结矿表层形成铁酸钙,以便达到铁酸钙自催化NO x还原的效果,这样不仅能减少烟气中NO x的排放,同时可降低NO排放浓度近44%,还可改善烧结产质量指标。
3、烧结过程中CO x形成及分布特点烧结烟气中的CO x主要由气体及固体燃料的燃烧产生,由于固体燃料在混合料中分散分布,其燃烧规律介于单体焦粒燃烧与焦粒层燃烧之间,属非均相反应。
在点火阶段,烟气中的CO x浓度快速上升,其中φ(CO)从0升到约7%,φ(CO2)从0升到14%左右;而烟气中的φ(O2)从20.9%降到2%左右。
点火后烧结过程中φ(CO)快速降到2%左右后基本不变,φ(CO2)则一直在14%左右波动;O2浓度波动方向均与CO2浓度的波动方向相反,这种现象一直持续到烧结终点前2~3min。
当烧结烟气温度达到最高点时,O2浓度恢复至空气中O2浓度水平,而CO浓度降至很低,CO2浓度则下降到几乎为0,因此烧结烟气中的CO x以CO2为主,只含有少量CO和O2。
二、烟气热风烧结烧结机尾高温烟气目前主要用于烟气循环烧结或烟气余热回收产蒸汽。
而在烟气循环烧结方面,主要有热风烧结、点火保温及用于点火助燃风预热等技术手段。
烧结生产采用热风烧结、点火保温工艺后,可降低燃料消耗,促进产物中铁酸钙的形成,防止烧结台车中的烧结矿在出点火器后表层温度骤降造成强度变差,增加烧结返矿率。
因此热风烧结能有效提高烧结矿强度,改善烧结矿质量,降低燃料消耗。
据有关热风烧结生产的统计数据,采用热风烧结工艺,烧结产量可提高2%,转鼓指数提高1.5%,成品率提高2%,降低燃耗12%~15%固体燃耗降低2%~4%。
而经过SCR脱硝处理的烟气温度完全能够满足热风烧结。
三、选择性烧结烟气分段式综合处理工艺依据上述有关烧结烟气中SO2、NO x、CO x浓度在烧结过程中分布的研究结论,结合有关烧结机尾烟气热风烧结的实践及烟气SCR法脱硝工艺中烟气温度的要求,设计了一种选择性的烧结烟气分段式综合处理工艺。
该工艺按烧结烟气中的各污染物分布特点将烧结过程分为4个部分,有选择性的将烧结烟气以不同手段进行分段处理:将SO2、NO x浓度低的烟气除尘后直接排放;将SO2浓度高的烟气经烟气循环烧结将SO2富集后,再集中进行脱硫处理,达标后外排;将NO x浓度高的烟气进行SCR脱硝处理达标后,利用该段烟气的高温余热及烟气中O2浓度较高进行热风烧结,从而实现将烧结烟气脱硫、脱硝分段治理工艺与热风烧结生产工艺有机结合的烧结烟气环保减排综合处理手段。
1、工艺方案以210m2烧结机为例,该烧结机共22个2m风箱,从机头开始设置3个风箱,中部设置17个3m 风箱,尾部设置2个2m风箱,台车宽3.5m,有效烧结长度61m。
某烧结厂210m2烧结机各风箱检测风温见表1。
依据上述研究结论,将烧结机风箱沿台车运行方向分为4个区域,设计一种选择性的分段式烧结烟气综合处理工艺,如图1所示。
区域①(烧结烟气点火区域):由1号~3号风箱组成,本区域内烧结烟气SO2,CO浓度较高,NO x 浓度很低;区域②(烧结烟气直排区域):由4号~11号风箱组成,本区域内烧结烟气中SO2浓度较低。
将区域④烟气引至本区域进行热风烧结既能利用热烟气的物理热减少燃料消耗,同时又能利用混合料层对SO2的强烈吸附作用及烧结料层中铁酸钙对NO x的自催化还原作用,进一步降低直排烟气中SO2,NO x浓度;区域③(烧结烟气脱硫区域):由12号~19号风箱组成,本区域内烧结烟气中SO2浓度很高,同时由于将区域①烟气(烟气中SO2、CO浓度较高)引至本区域进行烟气循环烧结,一方面将区域烟气中SO2和本区域烟气中SO2汇集,实现SO2富集后进行烟气脱硫;另一方面区域①烟气中CO浓度较高,可以利用烧结料层中铁酸钙对NO x的自催化还原作用,进一步降低脱硫烟气中NO x的浓度;区域④(烧结烟气脱硝区域):由20号~22号风箱组成,本区域内烧结烟气温度在320℃以上,烟气中NO x、O2含量浓度很高,CO x浓度SO2很低,烟气温度高,烟气中O2含量接近空气中O2含量水平,因此本区域内烧结烟气完全可以进行烟气SCR法脱硝,脱硝后的热烟气进行烟气热风烧结。
2、工艺配置1)烧结机。
有效抽风面积213.5m2,栏板高度700mm,台车宽度3.5m。
2)环冷机。
有效冷却面积为228m2,栏板高度1500mm,台车宽度3.2m。
3)烧结烟气1段(区域①)。
烟气参数:风量2100m3/min(工况),风温100~120℃,风压-10~-12kPa;主要工艺设备:1号多管除尘器、1号循环风机、机头烟气循环管道及相应管道阀门。
4)烧结烟气2段(区域②)。
烟气参数:风量8400m3/min(工况),风温90~110℃,风压-16.5kPa;主要工艺设备:烧结电除尘器(有效除尘面积150m2)、烧结主抽风机(功率3200kW)、直排烟气管道及相应管道阀门。
5)烧结烟气3段(区域③)。
烟气参数:风量8400m3/min(工况),风温120~180℃,风压-16.5kPa;主要工艺设备:脱硫电除尘器(有效除尘面积150m2)、脱硫风机(参数视具体脱硫方式而定)、烟气脱硫设施、脱硫烟气管道及相应管道阀门。
6)烧结烟气4段(区域④)。
烟气参数:风量2500m3/min(工况),风温320~400℃,风压-8~-10kPa;主要工艺设备:2号多管除尘器、2号循环风机、烟气脱硝设施(SCR)、脱硝烟气管道、机尾热风烧结烟气管道及相应管道阀门。
四、新工艺与常规烟气系统工艺配置对比新工艺的工艺配置与常规工艺配置中烧结机及点火器等烧结主体设备配置完全相同,主要区别在于烧结烟气系统的工艺配置。
常规烟气系统工艺配置如下:1、烧结主抽风系统(2个烟道分为2个系统配置)。
主要烟气参数(单个):风量11000m3/min(工况),风温80~120℃,风压-17kPa;主要工艺设备:1号机头除尘器(有效除尘面积200m2)、1号烧结主抽风机(功率4200kW)、2号机头除尘器(有效除尘面积200m2)、2号烧结主抽风机(功率4200kW)、大烟道及相应管道阀门。
2、烧结烟气脱硫系统。
主要烟气参数:风量22000m3/min(工况),风温80~120℃,风压视具体脱硫方式而定;主要工艺设备:除尘器、脱硫增压风机、脱硫烟气管道及烟气挡板阀门等相应烟气阀门。
相对于常规工艺的烟气参数和主要工艺设备配置,新工艺有以下改进:1、将烧结机头及机尾部分烟气进行烟气循环烧结,相对常规烧结烟气全排工艺,新工艺整体外排烟气量减少23.6%,相应的电除尘器及烧结主抽风机配置减小,烧结主抽风机功率减少23.8%;2、将烧结机头烟气循环至烧结中部脱硫段,烟气中硫富集后将脱硫段烟气引出脱硫,相对常规烧结烟气全脱工艺,新工艺脱硫烟气处理量减少61.8%,脱硫烟气中φ(SO2)提高50%左右,同时减少NO x的排放浓度,相应的脱硫除尘器、脱硫风机配置减小,烧结烟气脱硫、脱硝设施的设备投资和生产成本分别减少40%左右。
3、依据烧结烟气中NO x浓度分布特点,有针对性的进行SCR脱硝,在满足即将执行的新环保排放要求的前提下,减少脱硝设施配置及设备占地,实现降低投资建设及运行成本。
五、结论1)设计的选择性烧结烟气分段式综合处理工艺是将热风烧结生产工艺与烟气脱硫脱硝分段治理工艺进行有机结合的烧结烟气环保减排综合处理工艺。
2)与传统工艺相比,新工艺预计可使烧结烟气脱硫、脱硝时处理烟气量减少40%~60%,烟气中SO2、NO x体积分数提高50%左右,同时减少烟气脱硫、脱硝设施的设备投资和生产成本40%左右。