焊缝缺陷金相样
常见的焊接缺陷及缺陷图片.docx
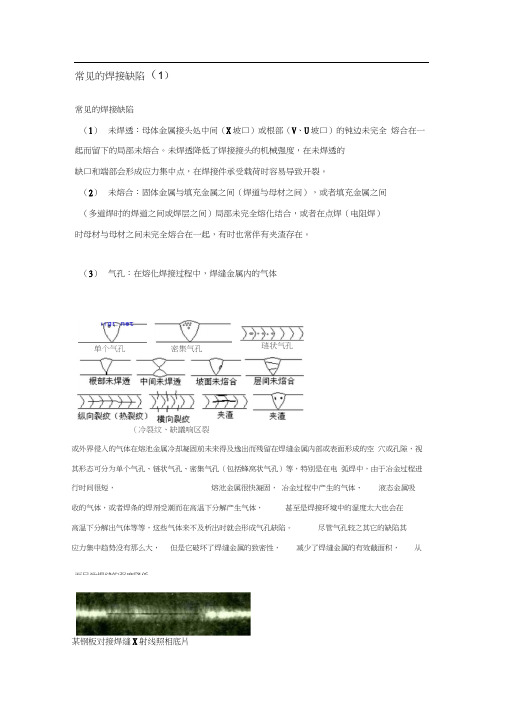
常见的焊接缺陷(1)常见的焊接缺陷(1) 未焊透:母体金属接头处中间(X 坡口)或根部(V 、U 坡口)的钝边未完全 熔合在一起而留下的局部未熔合。
未焊透降低了焊接接头的机械强度,在未焊透的缺口和端部会形成应力集中点,在焊接件承受载荷时容易导致开裂。
(2) 未熔合:固体金属与填充金属之间(焊道与母材之间),或者填充金属之间(多道焊时的焊道之间或焊层之间)局部未完全熔化结合,或者在点焊(电阻焊)时母材与母材之间未完全熔合在一起,有时也常伴有夹渣存在。
(3) 气孔:在熔化焊接过程中,焊缝金属内的气体或外界侵入的气体在熔池金属冷却凝固前未来得及逸岀而残留在焊缝金属内部或表面形成的空 穴或孔隙,视其形态可分为单个气孔、链状气孔、密集气孔(包括蜂窝状气孔)等,特别是在电 弧焊中,由于冶金过程进行时间很短, 熔池金属很快凝固, 冶金过程中产生的气体、 液态金属吸收的气体,或者焊条的焊剂受潮而在高温下分解产生气体, 甚至是焊接环境中的湿度太大也会在高温下分解出气体等等,这些气体来不及析出时就会形成气孔缺陷。
尽管气孔较之其它的缺陷其应力集中趋势没有那么大, 但是它破坏了焊缝金属的致密性, 减少了焊缝金属的有效截面积,从某钢板对接焊缝X 射线照相底片单个气孔 密集气孔 琏状气孔(冷裂纹、缺議响区裂纹)而导致焊缝的强度降低。
V型坡口,手工电弧焊,未焊透某钢板对接焊缝X射线照相底片V型坡口,手工电弧焊,密集气孔(4)夹渣与夹杂物:熔化焊接时的冶金反应产物,例如非金属杂质(氧化物、硫化物等)以及熔渣,由于焊接时未能逸出,或者多道焊接时清渣不干净,以至残留在焊缝金属内,称为夹渣或夹杂物。
视其形态可分为点状和条状,其外形通常是不规则的,其位置可能在焊缝与母材交界处,也可能存在于焊缝内。
另外,在采用钨极氩弧焊打底+手工电弧焊或者钨极氩弧焊时,钨极崩落的碎屑留在焊缝内则成为高密度夹杂物(俗称夹钨)。
W18Cr4V(高速工具钢)-45钢棒对接电阻焊缝中的夹渣断口照片钢板对接焊缝X射线照相底片V型坡口,手工电弧焊,局部夹渣钢板对接焊缝X射线照相底片V型坡口,手工电弧焊,两侧线状夹渣钢板对接焊缝X射线照相底片V型坡口,钨极氩弧焊打底+手工电弧焊,夹钨(5)裂纹:焊缝裂纹是焊接过程中或焊接完成后在焊接区域中出现的金属局部破裂的表现。
焊缝、铸件缺陷及伪缺陷在X射线底片上影像特征的分析

焊缝、铸件缺陷及伪缺陷在X 射线底片上影像特征的分析樊星明一 .单个气孔 (分散气孔 )1.特征和分布状态单个气孔缺陷在焊接内部多呈单一状态均匀分布,在焊缝上部,气孔体积不大 ,呈球状或椭圆形,外表光滑。
2.X 射线检测单个气孔与 X 射线底片上能清晰地显示出气孔的球状,椭圆状轮廓,由于经常采用射线方向与焊缝纵向垂直的透照方法,我们在底片上看到的都是气孔的正投影图象,所以,在 X 射线底片上都不能反映单个气孔缺陷在焊缝横向所处位置,即不能说明单个气孔是在焊缝的上部、中部或下部。
3.形成原因A焊接前未将焊缝坡口处金属上的铁锈、油污和油漆等清理干净。
B电焊条潮湿,水分在电弧高温作用下分解成氢气和氧气等气体,溶解于液态金属中,此时假设焊缝中液态金属凝固过快,熔解气休不能及时自焊缝中逸出。
C由于电弧加热母材温度不够高,焊接速度又过快等不合理工艺因素影响。
二 .链式气孔缺陷1.特征与分布状态链式乞孔在焊缝中呈一直线分布,气孔边沿相互衔接,状如链条,链的中心与焊缝轴线平行。
在埋弧焊中带出现在母材与焊缝之间。
在单面对接焊缝中常出现在焊接底部,链式乞孔缺陷很容易和未焊透缺陷混淆。
为了与未焊透缺陷区别,链状乞孔又称细线气孔。
在焊缝边沿的纵剖面上可以看到链状气孔,在母材与焊缝分界面上呈链环状影像。
在焊缝横剖面上链状气孔是呈单个分布,并有一定距离。
链状气孔之所以有以上所述的分布状态是由于母材与焊缝边界处冷却速度大,液态金属在此处受母材激冷,首先在此处凝固。
而氢气泡在固相外表上形成时消耗的功又小,因此氢气在熔池中析出即在此处元集形成气泡,来不及逸出。
2.X 射线检测链式气孔缺陷在X 射线底片上能清晰地显示出来,有的链环状分布,连续长度有30mm 以上有的那么呈断链状。
一段一段分布在焊缝与母材边沿部位底片上呈暗色图像,在链的边沿可清楚扯到气孔圆形轮廓。
3.形成原因主要是由氢引起的,氢来源于潮湿的助熔剂和没有充分枯燥的焊条涂料中的水分。
焊接缺陷,探伤图解(收藏)

焊接缺陷,探伤图解(收藏)一起学习,共同进步!先看18张很清晰的焊接缺陷图谱,身边搞焊接的朋友和搞探伤的朋友们应该人手一份。
万分感谢将这篇文章分享给我的同仁另外总结了一些常见焊接缺陷产生的原因、危害及防止措施!文章结尾蓝色字体内容更精彩!先看这几张图片,射线探伤底片结合横切面示意图,便于理解学习,拿出来分享给朋友们!1、weld01(High Low、高低)2、welld02(IncompleteRootFusion、根部未熔合)3、welld03(InsuffucientReinforcement、增强高)4、welld04(Excess RootPenetration、根部焊瘤)5、welld05(ExternalUndercut、外部咬肉)6、welld06(InternalUndercut、内部咬肉)7、welld07(RootConcavity、根部凹陷)8、welld08(BurnThrough、烧穿)9、welld09(Isolated SlagInclusion、单个的夹渣)10、welld10(WagonTrack Slag Line、线状夹渣)11、welld11(InterrunFusion、内部未熔合)12、welld12(Lack ofSidewallFusion、内侧未熔合)13、welld13(Porosity、气孔)14、welld14(Cluster Porosity、链状气孔)15、welld15(HollowBead、夹珠)16、welld16(Transverse Crack、横向裂纹)17、welld17(CenterlineCrack、中心线裂纹)18、welld18(RootCrack、根部裂纹)常见焊接缺陷产生原因、危害及防止措施一、焊接缺陷的分类焊接缺陷可分为外部缺陷和内部缺陷两种1.外部缺陷1)外观形状和尺寸不符合要求;2)表面裂纹;3)表面气孔;4)咬边;5)凹陷;6)满溢;7)焊瘤;8)弧坑;9)电弧擦伤;10)明冷缩孔;11)烧穿;12)过烧。
金相熔深试验检验指导书080919

4.检验方法:按简图指定位置切取金相样品,经180#、320#砂纸研磨,在抛光机上抛光,用2—10%硝酸酒精溶液浸蚀和用吹风机吹干后进行测试。
5.判定标准:(1)焊接缺陷依据DIN EN5817标准评定。
(2)焊缝熔深f≥0.2mm为合格。
(3)焊缝厚度SN≥a(理论焊缝厚度)或SN≥0.7tmin为合格。
№:01
浙江相检验指导书
第一版
第1/1页
零件名称:左/右管框骨架总成
零件图号:165 881 105D/106B
车型:
序号
检验内容
检验频次
容量
检验设备
简图
1
弧焊
(MAG)
1.检验依据:VW01106/TLD811 011V1
2.检验项目:焊接缺陷、熔深、焊缝厚度.
1次/批
3件/次
体视显微镜
SZ—61
更改依据
标记及数目
更改人签名及日期
编制及日期
审核及日期
批准及日期
常见的焊接缺陷及缺陷图片
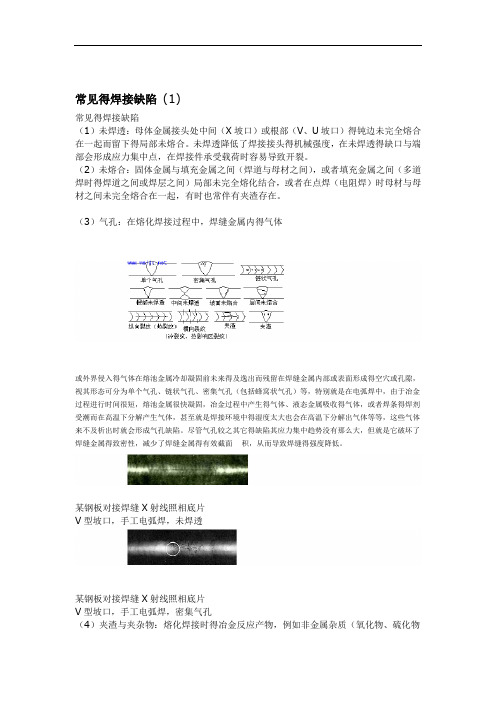
常见得焊接缺陷(1)常见得焊接缺陷(1)未焊透:母体金属接头处中间(X坡口)或根部(V、U坡口)得钝边未完全熔合在一起而留下得局部未熔合。
未焊透降低了焊接接头得机械强度,在未焊透得缺口与端部会形成应力集中点,在焊接件承受载荷时容易导致开裂。
(2)未熔合:固体金属与填充金属之间(焊道与母材之间),或者填充金属之间(多道焊时得焊道之间或焊层之间)局部未完全熔化结合,或者在点焊(电阻焊)时母材与母材之间未完全熔合在一起,有时也常伴有夹渣存在。
(3)气孔:在熔化焊接过程中,焊缝金属内得气体或外界侵入得气体在熔池金属冷却凝固前未来得及逸出而残留在焊缝金属内部或表面形成得空穴或孔隙,视其形态可分为单个气孔、链状气孔、密集气孔(包括蜂窝状气孔)等,特别就是在电弧焊中,由于冶金过程进行时间很短,熔池金属很快凝固,冶金过程中产生得气体、液态金属吸收得气体,或者焊条得焊剂受潮而在高温下分解产生气体,甚至就是焊接环境中得湿度太大也会在高温下分解出气体等等,这些气体来不及析出时就会形成气孔缺陷。
尽管气孔较之其它得缺陷其应力集中趋势没有那么大,但就是它破坏了焊缝金属得致密性,减少了焊缝金属得有效截面积,从而导致焊缝得强度降低。
某钢板对接焊缝X射线照相底片V型坡口,手工电弧焊,未焊透某钢板对接焊缝X射线照相底片V型坡口,手工电弧焊,密集气孔(4)夹渣与夹杂物:熔化焊接时得冶金反应产物,例如非金属杂质(氧化物、硫化物等)以及熔渣,由于焊接时未能逸出,或者多道焊接时清渣不干净,以至残留在焊缝金属内,称为夹渣或夹杂物。
视其形态可分为点状与条状,其外形通常就是不规则得,其位置可能在焊缝与母材交界处,也可能存在于焊缝内。
另外,在采用钨极氩弧焊打底+手工电弧焊或者钨极氩弧焊时,钨极崩落得碎屑留在焊缝内则成为高密度夹杂物(俗称夹钨)。
W18Cr4V(高速工具钢)-45钢棒对接电阻焊缝中得夹渣断口照片钢板对接焊缝X射线照相底片型坡口,手工电弧焊,局部夹渣V.钢板对接焊缝X射线照相底片型坡口,手工电弧焊,两侧线状夹渣V钢板对接焊缝X射线照相底片手工电弧焊,夹钨型坡口,钨极氩弧焊打底+V(5)裂纹:焊缝裂纹就是焊接过程中或焊接完成后在焊接区域中出现得金属局部破裂得表现。
焊缝接头组织的金相观察与分析

焊缝接头组织的金相观察分析一、实验目的1、认识焊缝区和热影响区各区段的组织特征。
2、了解焊缝金相检验方法和焊接接头的形成过程3、掌握焊接组织对性能的影响二、实验原理焊接是工业生产中用来连接金属材料的重要加工方法。
根据工艺特点不同,焊接方法又分为许多种,其中熔化焊应用得最广泛。
熔化焊的实质就是利用能量高度集中的热源,将被焊金属和填充材料快速熔化,热后冷却结晶而形成牢固接头。
由于熔化焊过程的这一特点,不仅焊缝区的金属组织与母材组织不一样,而且靠近焊缝区的母材组织也要发生变化。
这部分靠近焊缝且组织发生了变化的金属称为热影响区。
热影响区内,和焊缝距离不一样的金属由于在焊接过程中所达到的最高温度和冷却速度不一样,相当于经受了不同规范的热处理,因而最终组织也不一样。
根据组织和性能区别,焊接接头分为焊接区和焊接影响区。
焊缝区,是熔池泠凝后为铸态组织,在冷却过程中,液态金属自熔合区向焊缝的中心方向结晶形成的柱状晶组织,焊缝金属的性能一般不低于母材性能,但易产生裂纹。
以低碳钢为例,根据热影响区内各区段在焊接过程中所达到的最高温度范围,依次分为熔合区(固相线一液相线),过热区(1100℃——固相线);完全正火区(AC3——1100℃);不完全旺火区(AC1~AC3)。
对易淬火钢而言,还会出现淬火组织。
热影响区如图所示如图所示(1)熔合区即融合线附近焊缝金属到基体金属的过渡部分,温度处在固相线附近与液相线之间,金属处于局部熔化状肪,晶粒十分粗大,化学成分和组织极不均匀,冷却后的组织为过热组织,呈典型的魏氏组织。
这段区域很窄(0.1-1mm),金相观察实际上很难明显的区分出来,但该区对于焊接接头的强度、塑性都有很大影响,往往熔合线附近是裂纹和脆断的发源地。
(2)过热区(粗晶粒区)加热温度范围Tks-Tm(Tks为开始晶粒急剧长大温度,Tm 为熔点),当加热至1100℃以上至熔点,奥氏体晶粒急剧长大,尤其在1300℃以上,奥氏体晶粒急剧粗化,焊后空冷条件下呈粗大的魏氏组织,塑性、韧性降低,使接头处易出现裂纹。
焊接缺陷中英文对照
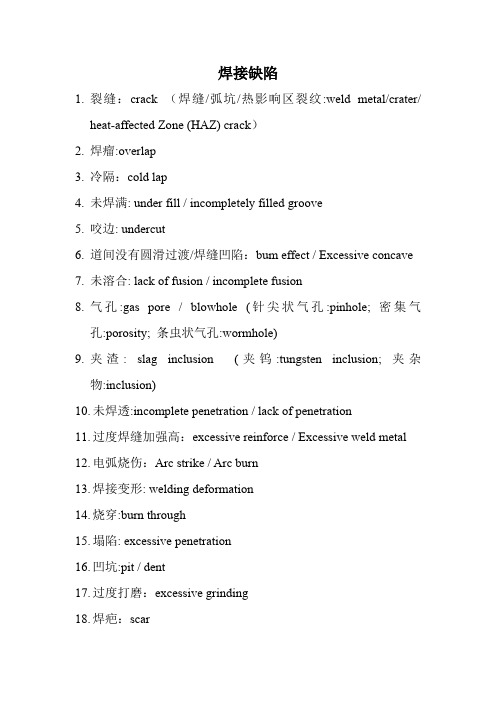
焊接缺陷1.裂缝:crack (焊缝/弧坑/热影响区裂纹:weld metal/crater/heat-affected Zone (HAZ) crack)2.焊瘤:overlap3.冷隔:cold lap4.未焊满: under fill / incompletely filled groove5.咬边: undercut6.道间没有圆滑过渡/焊缝凹陷:bum effect / Excessive concave7.未溶合: lack of fusion / incomplete fusion8.气孔:gas pore / blowhole (针尖状气孔:pinhole; 密集气孔:porosity; 条虫状气孔:wormhole)9.夹渣: slag inclusion (夹钨:tungsten inclusion; 夹杂物:inclusion)10.未焊透:incomplete penetration / lack of penetration11.过度焊缝加强高:excessive reinforce / Excessive weld metal12.电弧烧伤:Arc strike / Arc burn13.焊接变形: welding deformation14.烧穿:burn through15.塌陷: excessive penetration16.凹坑:pit / dent17.过度打磨:excessive grinding18.焊疤:scar19.飞溅:spatter20.焊缝成行不好:poor profile21.焊角不足:lack of weld leg附录attachment焊接工艺方法1.熔焊:fusion welding 压焊:pressure welding 钎焊:brazing welding2.焊缝倾角:weld slope, inclination of weld axis.3.焊缝转角:weld rotation, angle of rotation4.平焊:flat position of welding, downhand welding 横焊:Horizontal position welding.5.立焊:vertical position welding 仰焊:overhead position welding.6.向下立焊:vertical down welding, downward welding in the vertical position.7.向上立焊:vertical up welding, upward welding in the vertical position.8.倾斜焊;inclined position welding9.上坡焊: upward welding in the inclined position10.下坡焊: downward welding in the inclined position11.对接焊:butt welding 角焊:fillet welding 搭接焊:lap welding12.船形焊: fillet welding in the downhand / flat position13.坡口焊:groove welding14.I 形坡口对接焊:square groove welding15.Y形坡口对接焊:flare groove welding16.纵缝焊接:welding of longitudinal seam. 横缝焊接:welding of transverse seam.17.环缝焊接:girth welding, circumferential welding18.螺旋缝焊接:welding of spiral seam, welding of helical seam.19.环缝对接焊:Butt welding of circumferential seam.20.单面焊:welding by one side 双面焊:welding by both sides21.单道焊:single-pass welding, single-run welding 多道焊: multi-pass welding..22.单层焊:single layer welding 多层焊:multi-layer welding23.分段多层焊:block sequence, block welding24.连续焊:continuous welding 打底焊:backing welding 封底焊:back sealing weld25.自动焊:automatic welding 半自动焊:semi-automatic welding26.手工焊:manual welding, hand welding27.车间焊接:shop welding 工地焊接:site welding, field welding28.堆焊:surfacing welding, building up welding, overlaying welding.29.衬垫焊:welding with backing.30.焊剂垫焊:welding with flux backing31.电弧点焊:arc spot welding.32.套环:ferrule 试板test piece 随机检查random check33.单面/双面串联点焊:direct/indirect serial spots welding.34.机械性能试验mechanical properties test35.简历curriculum vitae36.分类category37.风险评估risk assessment38.第三方notified body39.基准modules坡口, 焊缝1.焊接工艺参数:welding parameter2.坡口: groove 钝边:root face3.坡口面角度: angle of bevel, bevel angle.4.坡口角度: Included angle, groove angle.5.坡口高度:groove depth6.开坡口:beveling of the edge, chamfering.7.single-V/U groove (with root face)8.焊缝区:weld metal zone 热影响区:heat-affected Zone (HAZ)9.工艺/使用/热/焊接性:fabrication/service/thermal weldability.10.碳弧气刨:carbon arc air gouging. 火焰气刨:flame gouging11.等离子切割:plasma arc cutting(PAC) 激光切割: laser cutting (LC)12.喷沙: sand blast 清渣:slag removal 清根: back chipping13.碳/铬/镍当量:carbon/chromium/nickel equivalent.电弧焊1.手工电弧焊:manual metal arc welding2.直流电弧焊:direct current arc welding3.交流电弧焊:alternating current arc welding4.三相电弧焊:three phases current arc welding5.熔化极电弧焊: arc welding with consumable electrode6.金属极电弧焊:metal arc welding 电弧堆焊:arc surfacing7.碳弧焊:carbon arc welding 自动堆焊:automatic surfacing8.埋弧焊:submerged-arc welding (SAW)9.自动埋弧焊:automatic submerged-arc welding (SAW)10.半自动埋弧焊:semi-automatic submerged-arc welding (SAW)11.气体保护焊:gas shielded arc welding12.惰性气体保护焊:inert-gas arc welding13.氩弧焊:argon arc welding14.钨极惰性气体保护焊:tungsten inert-gas arc welding15.活性气体保护焊:metal active gas arc welding16.Co2气体保护焊:carbon-dioxide arc welding.17.电渣焊:electro-slag welding (ESW) 电阻焊:resistance welding (RW)18.点焊:spot welding 摩擦焊:friction welding (FW) 爆炸焊: explosive welding (EW)19.热切割: thermal cutting (TC) 气割: gas cutting20.塑性/脆性:plastic/brittle21.焊缝\环焊缝\打磨:welding seam\circumference seam\grind22.发证:certification issue焊接检验1.试件/试样: test piece/specimen2.直射/斜射/水浸超声探伤:straight/angle beam/immersed ultrasonic inspection3.射线探伤:radiographic inspection 超声探伤:ultrasonic inspection4.磁粉探伤:magnetic particle examination 渗透探伤: penetration inspection5.荧光检验:fluorescent penetration inspection6.着色检验:dye penetration inspection7.电磁法探伤:electromagnetic test8.密封性检验:leak test 气密性检验: airtight test10. 破坏检验:destructive test9.耐压检验:pressure test 水压试验:hydraulic test 气压试验:pneumatic test10.声发射:acoustic emersion11.淬火:quenching 回火:tempering退火:annealing 熔炼:smelting12.强制检验:mandatory inspection13.拉伸试验\弯曲试验\冲击试验:tension test\bend test\impact test14.金相检查:metallographic exam15.面弯\背弯\侧弯\断口\弯曲条件:face bend\root bend\side bend\break\condition of bend16.合格级别\评定级别\底片编号acceptable grade\interpretation level\radiograph no17.铱同位素:iridium isotope∙welding inspection clearance groove, assembly space whether it meets the requirements, positioning it firmly welding, weld around is not oil, rust;清理焊口:焊前检查坡口、组装间隙是否符合要求,定位焊是否牢固,焊缝周围不得有油污、锈物;∙开孔前要按照图纸给定的方位、标高,结合排版图进行放样、测量、号孔、划线。
焊缝的外观质量检验

(1) 直接目视检测 也称为近距离目视检测,这种检 测用于眼睛能充分接近被检物体,直接观察和分辨缺陷 形态的场合。
(2)远距离目视检测 用于眼睛不能接近被检物体, 必须借助望远镜、内孔管道镜等进行观察的场合。
2、目视检测的项目 (1)焊后清理质量 所有焊缝及其边缘,应无焊渣、 飞溅及阻碍外观检查附着物。
四、焊缝检测中常见焊接缺陷 (一)焊接缺陷及其分类
在焊接接头上产生的金属不连续、组织不致密或连接 不良的现象,统称为焊接缺陷。
一般来说,焊接接头的质量取决于焊接缺陷的性质、 大小、数量和危害程度。
焊接缺陷一般可分为以下三类: 1、尺寸上的缺陷 包括焊缝尺寸不符合要求及焊缝形状不佳。 2、结构上的缺陷 包括气孔、夹渣、未熔合、未焊透、咬边、裂纹等。
1、质量保证职能
万吨远洋轮
电气
质量保证的职能通过对焊接原材料、工序、半成品和 成品的检测,做到不合格原材料不投入生产,不合格半 成品不留转到下一道工序,不合格的成品不出厂。
2、 缺陷防御的职能 检测获得的信息和数据是质量控制的依据,通过检测 能及早发现质量问题,并找出原因并及时纠正、预防或 减少不合格焊缝的生产。
含氢量较高
、拘束度高)
及工件表面有水分、油污及
2、焊缝布置在应力集 铁锈
冷
中区
4、焊后未进行保温处理
裂 淬火 1、钢中的C或合 3、坡口形式不合适( 1、对冷却裂倾向较大的材
纹 裂纹 金元素含量增高, 如V形坡口的拘束应力 料,其预热温度未作相应的
使淬硬倾向增大 较大)
提高
2、对于多组元合
2、焊后未立即进行高温回
3)焊缝咬边 在工件上沿焊缝边缘所形成的凹陷 叫咬边,如图下所示。它不仅减少了接头工 作截面,而且在咬边处造成严重的应力集中。
焊接件的金相检验
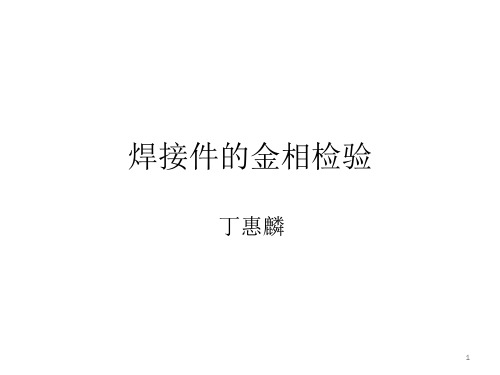
3
焊接件的金相检验—宏观检验
二、宏观检验
5
焊接件的金相检验—焊接区显微组织特征
三、焊接区显微组织特征 焊接区有焊缝、热影响区(包括熔合区)和母材三部分组成。 1.焊缝组织 焊缝从加热熔化后由高温冷到室温,中间经过两次组织转变: 第一次从液体转变为固体时的结晶过程,称为一次结晶; 第二次是当焊缝金属温度降低至相变时所发生的组织转变,称二次结晶。 焊缝的组织和性能除与化学成分有关外,还取决于这两次结晶情况。 1)焊缝一次结晶组织 (1)一次结晶的特点: ①一般焊接溶池较小,又被周围冷金属和环境介质所包围,所以溶池冷速快
焊接件的金相检验
丁惠麟
1
焊接件的金相检验—概述
一、概述
焊接过程是在高温热源的作用下,基体金属发生局部熔化,并与熔融的填充金 属混合而形成熔池。当热源离开后焊接熔池温度迅速下降,并凝固结晶形成焊缝。 焊接一般经历以下几个过程:
加热—熔化—冶金反应—结晶—固态相变—形成接头 焊接热过程贯穿焊接的始终,它是影响焊接质量的主要因素之一。焊接应力、 应变以及冶金、结晶、相变都与之相关。 在化学冶金过程中,熔化金属、熔渣、气相之间将发生一系列的冶金反应,如 金属氧化、还原、脱P、S、焊缝金属与氢作用等等,都会直接影响焊缝金属的成分、 组织和性能。 焊接时金属结晶和相变是在快速连续冷却条件下进行的,可能产生偏析、夹杂、 气孔、裂纹、淬硬和脆化等缺陷。所以,这一过程也是影响焊接质量的重要环节。 焊缝两侧的基体金属也受到焊接热的作用,受热后温升不同,发生组织变化也 不同,也将不同程度地影响其性能。 归纳起来,焊接过程的特点如下: 1.加热温度高 熔池液态金属温度可达1770~1870℃,比炼钢温度不高,焊缝 区的熔合线附近都在1350℃以上。 2.加热速度快 熔化→凝固及热影响区相变仅几秒至几分钟。 3.高温停留时间短。 4.局部加热、温差大 造成组织转变的差异和组织的不均匀。
焊接件金相检验报告

样
品
描述
12
见照片1-1
试样数量 Sample Quantity
材质 Material 产品名称 Sample name
XXXXX零件焊接试验件16Mo3标准/要求Standard or Requirement
无宏观焊接缺陷(包括无气孔、未溶合、咬边等)检测项目 Test Item
产品数量 Production Quantity 产品外观 Production Appearance
宏观检验 附加微观(100X)组织照片试样1 / 编号:9#-1试样2 / 编号:9#-2未发现有宏观焊接缺陷未发现有宏观焊接缺陷
腐蚀介质 Cauterization liquid
4%硝酸酒精溶液1-4 热影响区过渡区组织 100X 1-3 基体微观组织 100X 1-1 产品外观 1X 检测结果
Inspection result 1-2 宏观检验 30X
1-5 热影响区组织 100X 1-6 焊缝组织 100X
检测/日期: 祖晓彬 2010/3/9 批准/日期:苏相国 2010/3/9
2-2 宏观检验 30X 2-1 产品外观 1X
2-3 基体微观组织 100X
2-4 热影响区过渡区组织 100X 2-5 热影响区组织
2-6 焊缝组织。
常见焊接缺陷及其产生原因

类。
中国核工业第二三建设公司
熔焊缺陷除了以上六类之外,还有金相组织不符合要求(如晶粒粗大、 金相组织的成分不合格等)及焊接接头的理化性能不符合要求的性能缺 陷(包括化学成分、力学性能及不锈钢焊缝的耐腐蚀性能等)。这类缺 陷大多是由于违反焊接工艺或错用焊接材料所引起的,不在此讨论。
中国核工业第二三建设公司
图三
中国核工业第二三建设公司
六、未熔合和未焊透 在焊缝金属和母材之间或焊道金属与焊道金属之间未完全熔化结合
的部分称为未熔合(如图四)。常出现在坡口的侧壁、多层焊的层间及 焊缝的根部。这种缺陷有时间隙很大,与熔渣难以区别。有时虽然结合 紧密但未焊合,往往从未熔合区末端产生微裂纹。
温失塑裂纹是低于固相线温度下,在焊缝金属凝固后的冷却过程中形成 的一种热裂纹。
焊接接头冷却到Ms线温度以下时形成的裂纹称为冷裂纹。其特点是 表面光亮,无氧化特征。冷裂纹主要发生在焊接热影响区,对某些合金 成分多的高强度钢来说,也可能发生在焊缝金属中。常见的冷裂纹可分 为氢致裂纹、淬火裂纹和层状撕裂。氢致裂纹具有延迟特征,即焊后经 过数小时、数日或更长时间才出现的冷裂纹称为氢致裂纹,或称延迟裂 纹;淬火裂纹是在焊接含碳量高、淬硬倾向大的钢材时出现的冷裂纹; 层状撕裂是母材本身固有的缺陷,因焊接使其暴露出来,一般发生在角 焊缝的厚板结构中中国。核工业第二三建设公司
中国核工业第二三建设公司
图7 焊瘤
3、烧穿和下塌 焊接过程中,熔化金属自坡口背面流出,形成穿孔的缺陷叫烧穿。
烧穿容易发生在第一道焊道及薄板对接焊缝或管子对接焊缝中。在烧穿 的周围常有气孔、夹渣、焊瘤及未焊透等缺陷。
穿过单层焊缝根部,或在多层焊接接头中穿过前道熔敷金属塌落的 过量焊缝金属称为下塌。
EN_ISO_5817_焊缝外观检测缺陷分级

不允许
不允许Biblioteka >3d≤0,3s, 最大3mm d≤0,3a, 最大3mm
d≤0,2s,最大2mm d≤0,2a,最大2mm
不允许
编 号
根据 ISO 6520-1 编号
缺欠 名称
解释
t mm
不同评定组别所允许的缺欠的极限值
D
h≤0,2 t
C
B
0,5至3
不允许
不允许
1.4
2025
开口弧坑 >3 h≤0,2 t, 最大2 mm h ≤0,1 t, 最大1mm 不允许
不允许
1.8
5013
根部咬边 >3
短缺欠: h ≤ 0,2 t, 最大 2 mm
短缺欠: h ≤ 0,1 t, 最大 1 mm
短缺欠: h ≤ 0,05 t, 最大0,5mm
要圆滑过渡
1.9
502
余高过大 (对接焊缝)
≥0,5
h ≤1 mm + 0,25 b, 但最大 10mm
h≤ 1mm + 0,15b, 但最大 7mm
2.评定组别 B C D
高 中 低
3.定义
短缺欠:
在100mm焊缝长度内,一个或多个
缺欠的总长不大于25mm,或当焊缝不足 100mm时,缺欠总长不大于焊缝长度的 25%,此时的缺欠称为短缺欠。
4.评定
缺欠分组: -表面缺欠 -内部缺欠 -焊缝的几何形状缺欠 -多重缺欠
编 号
根据 ISO 6520-1 编号
短缺欠: h ≤ 0,2 t
C
短缺欠: h ≤0,1t
B
不允许
要圆滑过渡 不能是成簇缺欠
0,5 至 3
1.7
5011 5012
锅筒焊缝纵向裂纹产生原因及检验修复措施

设备管理与维修2021翼4(上)图2纵缝Z1裂纹缺陷图1锅筒焊缝布置图3纵焊缝金相图4母材金相锅筒焊缝纵向裂纹产生原因及检验修复措施徐火力,陈其锦(厦门市特种设备检验检测院,福建厦门361004)摘要:分析某台电站锅炉锅筒焊缝产生纵向裂纹的原因,提出针对性的修复工艺建议和质量检验要求,确保维修质量,进而提出了锅筒制造工艺和定期检验的建议和措施。
关键词:锅筒;焊缝;纵向裂纹;原因;措施中图分类号:TM621;TG441.7文献标识码:BDOI :10.16621/ki.issn1001-0599.2021.04.300引言厦门某热电公司一台高压电站锅炉,锅炉型号NG-220/9.8-M24,额定蒸汽压力9.8MPa ,额定蒸发量220t/h ,额定蒸汽温度540益,给水温度215益,于2005年3月制造。
锅筒是该锅炉最重要的受压部件,该锅筒有3个筒节,内径1600mm ,长度8400mm ,厚度为100mm ,材料为P355GH (19Mn6),工作压力10.98MPa 。
该锅炉于2007年3月投入使用至今。
1锅炉定期检验发现裂纹情况2020年4月对锅炉进行内部检验,期间对锅筒纵环焊缝进行磁粉无损检测,发现该锅筒纵焊缝Z1内表面下边沿存在一处开口裂纹,总长2200mm ,贯穿该筒节焊缝全长,如图1、图2所示;再从锅筒外表面采用超声波对该焊缝进一步无损检测,结果显示缺陷上端点距锅筒外表面最小值处约86.5mm (锅筒壁厚100mm ),即该裂纹最大深度约13.5mm 。
发现纵焊缝Z2内表面上边沿存在一处开口裂纹,长310mm ,深度约2mm 。
纵焊缝Z3内表面下边沿存在一处开口裂纹,长330mm ,深度约2mm 。
2产生原因分析2.1进一步检测缺陷部位为了找出产生缺陷的原因,查阅了该锅炉的制造、安装等技术资料和运行、维修记录,并对锅筒焊缝、热影响区和母材进行外观检查、硬度和金相检测。
(1)查阅了锅炉制造、安装等技术资料。
焊接件的金相检验1

焊接件的金相检验—焊接区显微组织特征
焊缝冷速快,成分来不及扩散,分布不均匀,形成偏析,非金属夹杂来不及浮 出而残留在焊缝内,因此对焊缝性能影响大。 焊缝偏析分为显微偏析、宏观偏析和层状偏析。 ①显微偏析 低碳钢焊缝中C或杂质晶界上含量比钢平均含量高—晶界偏析。 ②宏观偏析 熔池中杂质浓度高,使最后凝固部分严重偏析,易产生纵向裂纹。 ③焊缝横断面上出现分层组织、成分不均匀,称为层状偏析。 (4)一次晶组织的性能 粗大柱状晶不仅降低焊缝强度,而且使塑性、韧性下降。 树枝晶比胞状晶产生裂纹倾向大。 粗大树枝晶比细小的树枝晶产生热裂纹倾向大。 2)焊缝金属的二次结晶(固态相变) 一次结晶后的奥氏体组织进一步转变成何种组织,取决于焊缝化学成分、冷却 条件及焊后热处理等因素。 (1)二次结晶组织 低碳钢:大部分为铁素体+少量珠光体,铁素体沿原奥氏体晶界析出。 冷速快,珠光体增加,还可能出现贝氏体。 冷速慢,铁素体呈粗大的魏氏组织。 低合金钢: ①合金元素含量少(如16Mn、20G钢),焊缝组织与低碳钢相似(铁素体+少量 珠光体),冷速快,出现粒状贝氏体,甚至出现马氏体。 ②合金元素较多的低合金高强度钢,焊后组织为贝氏体或下贝氏体,甚至出现
13
焊接件的金相检验—焊接区显微组织特征
(2)不完全淬火区( Ac1~Ac3之间区域) 铁素体不发生变化,只有不同程度长大。 珠光体、贝氏体转变为奥氏体,随后快速冷却得到马氏体。 最后形成马氏体+铁素体共存组织。 碳和合金元素含量低,冷速缓慢,也可能出现珠光体组织。 (3)回火区 焊前为调质态,除上述两个区域外,还可能发生不同程度的回火区。 所以,热影响区组织不仅与基体成分和焊接热循环特征有关,还和焊前热处理 状态有关。 3)焊接接头组织形貌特征 (1)铁素体 在焊缝金属和热影响区中常见的是先共析铁素体,包括自由铁素 体和魏氏组织铁素体两种。 ①自由铁素体 是由奥氏体晶界上析出的铁素体,常见有块状和网状两种形貌。 块状铁素体是在高温下而过冷度较小的冷却过程中形成的。 网状铁素体是在较低温度和过冷度较大的冷却过程中形成的。 自由铁素体析出数量与奥氏体晶粒大小有关,晶粒越大,铁素体越少。 ②魏氏组织铁素体 低碳钢焊缝金属和热影响区极易形成魏氏组织铁素体。 其形貌为除晶界铁素体外,还有大量的从晶界伸向晶粒内部形似锯齿状或梳状 的铁素体,或在晶内以针状独立分布的铁素体,往往针粗大且交叉分布。
常见金相组织缺陷与失效介绍
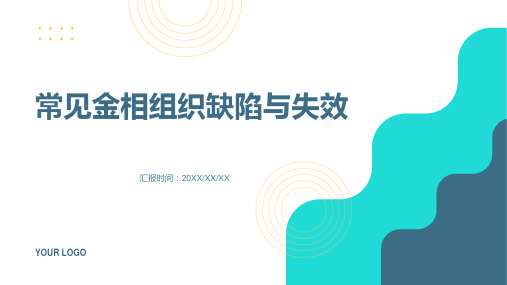
缺陷与失效分析
缺陷类型:气孔、夹杂、裂纹、磨损等 失效原因:设计不合理、材料选择不当、加工工艺问题等 失效后果:影响产品性能、缩短使用寿命、造成安全隐患等 预防措施:优化设计、选用合适材料、改进加工工艺等
解决方案
优化材料选择:选择合适的材料,避免缺 陷产生
改进工艺:优化生产工艺,减少缺陷产生
加强检测:提高检测频率和质量,及时发 现缺陷
材料缺陷:如夹杂物、气孔、裂纹等 加工工艺不当:如热处理不当、锻造不当等 设计不合理:如结构不合理、应力集中等 使用环境恶劣:如高温、高压、腐蚀等 维护保养不当:如润滑不足、磨损严重等
失效机理
疲劳失效:循环载荷作用下,材料疲劳 损伤累积导致断裂
断裂失效:材料内部缺陷或应力集中导 致断裂
腐蚀失效:环境因素导致材料表面腐蚀, 降低机械性能
气压:气 压变化可 能导致材 料变形或 破裂
辐射:辐 射可能导 致材料老 化或失效
化学物质: 接触有害 化学物质 可能导致 材料腐蚀 或变质
生物因素: 生物侵蚀 可能导致 材料损坏 或失效
金相组织缺陷检测方法
宏观检测
肉眼观察:直接观察样品表面,发 现明显缺陷
低倍显微镜观察:使用低倍显微镜 观察样品表面,发现更细微的缺陷
变形预防:合理设计、正确选材、控制热处理工艺等
金相组织缺陷原因
原材料问题
原材料质量不 合格:如杂质、 气孔、裂纹等
原材料加工工 艺不当:如热 处理、锻造、 焊接等工艺不
当
原材料选择不 当:如选材不 当、材料搭配
不当等
原材料储存不 当:如储存环 境不当、储存
时间过长等
工艺问题
材料选择不当:材料 性能与使用环境不匹 配
焊接区断口金相分析(图片转文字)

第一章绪论 (1)§1—1断口金相学的发展及任务……………1 一、断口金相学的由来爰发展……………1 二、断口金相学的任务……………………1 三、断口金相学在焊接中的应用…………1 §1—2断口金相的一般技术…………………2 一、断口的保存与清洗………………………2 二、断口的宏观分析技术……………………2 三、断口的微观分析技术……………………3 §2—1§2—2二、v §2-3§3一l §3-2一、氢致延迟裂纹断口特征及其形成机制………………………………………68 二、淬火裂纹断口特征及其形成机制………87 三、层状撕裂断口特征及其形成机制………93 §3-3焊接再热裂纹断口特征厦形成机制……………………………………………100 一、裂纹性质,宏观特征爰形成条件…100 二、裂纹形成机制爰断口微观形貌……102 第四章焊接区脆化及脆性断裂断口形貌分析……………………………108 §4—1焊缝金属的低温脆性及其断口 §1-1断口金相学的发展及任务一、断口金相学的由来及发展金属断口分析是一门研究金属断裂表面的科学。
由于断裂过程往往是瞬间完成的,所以靠实验方法直接掌握整个断裂过程的物理现象或断裂机理比较困难,然而,在断裂造成的断口表面上却往往留下某些反映断裂的物理过程的痕迹或信息。
正如考古学家靠分析化石,法医靠解剖尸体来取得结论那样,断口金相工作者靠对断口表面保留的痕迹的分析目录来获得断裂起因或断裂机制方面的可靠情报。
从中世纪开始,人们已经会运用肉眼或放大镜对金属断口进行宏观分析,16世纪,人们已懂得用断口的宏观形貌来评定金属材料的质量。
如将开缺口的铜锭横向打断,观察断口以检查铜锭的质量。
19世纪,人们已经把断口的宏观形貌进行分类;研究了断口形貌由纤维状转变为结晶状的影响因素;认识了典型的标准形状拉伸断口的形成与分区等(2)作为事故分析的重要手段。