连续退火炉炉内的氮气吹刷2
退火炉的退火过程

7)吊走加热罩,加热结束时,需要用行车把加热罩吊走,8分钟;
8)扣冷却罩,用行车吊一个空闲冷却罩扣于内罩上,8分钟;
9)冷却,开始降温过程,冷却时间随工艺定;
10)后吹扫,用氮气对钢卷进行吹洗,30分钟;
11)吊走冷却罩,用行车把冷却罩吊走,8分钟;
12)出炉,用行车先把内罩吊离,然后把各个钢卷吊走,定。
退火炉罩式炉退火生产的约束条件分为工艺约束、资源约束和能源约束。
1)工艺约束,每个退火计划必须严格按照给定的12个工序进行生产,同时不允许辐射冷却,即在加热罩吊走后,必须立刻扣上冷却罩,若加热结束时没有空闲的冷却罩,则加热罩不能卸走,进行带热罩冷却,直到有空闲的冷却罩为止。
因为各个退火炉退火计划的加热时间和冷却时间不同,装炉顺序对退火车间产量有很大的影响.装炉顺序不合适会导致集中装出炉、集中加热、集中冷却现象,从而造成大量炉台中出现等待资源状况,导致产量下降,交货期延迟所以,优化目标是找到合理的装炉顺序.优化调度的基本思想所示,用离散事件仿真对整个退火车间进行动态模拟,用遗传算法对装炉顺序可行集进行搜索。“其它决策变量”包括各个炉台相应退火作业各阶段中使用的资源号(行车号、加热罩号、冷却罩号)及各操作的起始时间。
2)资源约束,包括加热罩、冷却罩、行车、地爬车约束加热罩和冷却罩资源约束中还存在炉型匹配问题.行车资源和地爬车资源的重入性质使得当炉台数增多时,这两种资源的合理调度对整个车间的作业效率有很大影响。
3)能源约束,包括煤气和氮气能源两种约束.这两种约束一般根据煤气和氮气管道的分布按照炉区来进行限制。
罩式退火炉生产优化调度方法
退火炉的退火过程
河钢邯钢邯宝冷轧厂连续退火炉安全控制优化和改进

圆园19年第8期一、前言河钢邯钢邯宝冷轧厂退火炉采用的是DREVER 公司设计的具有高速气体喷射冷却功能的全辐射加热立式连续退火炉,该退火炉可分为预热段、加热段、缓冷段、快冷段、过时效段、终冷段以及水淬段,炉内充满N 2和H 2,使用热值为1800±100kcal/Nm 3的混合煤气对板带进行辐射加热。
其中,加热段为煤气使用区域,快冷段为主要的冷却段,采取高氢(最高20%氢气)+可移动风箱相结合模式进行冷却,炉子出入口以及快冷段采用N 2注入的方式进行密封。
由于连续退火炉涉及煤气、氢气等易燃、易爆危险气体,因而保证人员以及设备安全成为安全生产的前提条件,是生产任务的重中之重。
为确保连续退火炉长周期安全稳定运行,连退车间针对退火炉存在的安全隐患进行技术攻关,通过优化系统程序控制,在安全方面层层限制,大大地提高了连退炉稳定运行的安全系数。
二、优化前连续退火炉系统存在的问题生产期间退火炉存在以下安全隐患。
1.混合煤气方面:混合煤气的压力和热值出现大幅度波动的时候,会改变烧嘴处的燃烧状况,造成不完全燃烧,残余煤气容易在烟气管道聚集,进而引起爆炸事故。
2.氢气方面:高氢运行期间,引起炉内氢气含量分布不均衡,低温段氢气含量偏高,增加爆炸危险系数。
3.氮气方面:高氢停止期间,氮气吹扫时间不合适,导致炉内氢气含量偏高,停车风险系数增加。
三、混合煤气控制系统优化(一)存在问题邯宝冷轧厂连退车间连续退火炉采用高炉、焦炉混合煤气,从煤气管道进入烧嘴,经烧嘴点火后,在辐射管内充分燃烧,产生的高温烟气经过同流换热器与助燃空气进行换热后,流经烟气管道的余热回收装置,最终经由排烟风机抽取送至烟囱排放至大气。
混合煤气设计压力为12~18kPa ,热值为1800±100kcal/Nm 3。
如果压力过低或者过高,都会导致烧嘴燃烧质量不好,烟气中CO 含量增加,容易在烟气管道里面聚集,一旦达到临界条件,会发生爆炸危险;如果煤气热值过低,也会导致煤气燃烧质量不好,导致烟气管道中CO 聚集,容易产生爆炸;而煤气热值过高,则可能会导致单位体积下煤气发热量过大,燃烧后温度过高,造成辐射管烧损穿孔,进而导致大量烟气进入炉膛中,影响板带质量。
光亮退火炉氢氮混合气体的作用

光亮退火炉氢氮混合气体的作用
光亮退火炉中氢氮混合气体主要有以下作用:
1. 保护作用:为了获得冷轧板的光亮表面,退火应在保护气氛中进行。
氢氮混合气体作为保护气体,可以防止冷轧薄板氧化。
2. 还原作用:氢含量的增加有助于提高气氛的还原性,这也有助于防止冷轧薄板氧化。
3. 清洗作用:氢气可以促进乳化液中烃类的分解和挥发,从而去除冷轧板表面的碳污染,提高冷轧板的表面质量。
4. 改变物理性质和提高耐腐蚀性:氮气可以改变金属的物理性质,并提高其耐腐蚀性能,从而提高金属产品的质量和可靠性。
总之,氢氮混合气体在光亮退火过程中发挥了重要作用,可以提高金属产品的质量和可靠性。
如需更多信息,建议咨询专业退火炉技术人员。
论连续退火炉节能减排降耗的控制措施
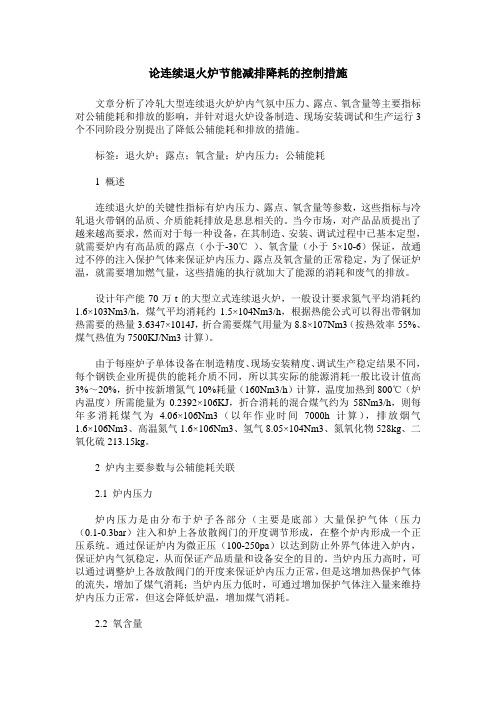
论连续退火炉节能减排降耗的控制措施文章分析了冷轧大型连续退火炉炉内气氛中压力、露点、氧含量等主要指标对公辅能耗和排放的影响,并针对退火炉设备制造、现场安装调试和生产运行3个不同阶段分别提出了降低公辅能耗和排放的措施。
标签:退火炉;露点;氧含量;炉内压力;公辅能耗1 概述连续退火炉的关键性指标有炉内压力、露点、氧含量等参数,这些指标与冷轧退火带钢的品质、介质能耗排放是息息相关的。
当今市场,对产品品质提出了越来越高要求,然而对于每一种设备,在其制造、安装、调试过程中已基本定型,就需要炉内有高品质的露点(小于-30℃)、氧含量(小于5×10-6)保证,故通过不停的注入保护气体来保证炉内压力、露点及氧含量的正常稳定,为了保证炉温,就需要增加燃气量,这些措施的执行就加大了能源的消耗和废气的排放。
设计年产能70万t的大型立式连续退火炉,一般设计要求氮气平均消耗约1.6×103Nm3/h,煤气平均消耗约1.5×104Nm3/h,根据热能公式可以得出带钢加热需要的热量3.6347×1014J,折合需要煤气用量为8.8×107Nm3(按热效率55%、煤气热值为7500KJ/Nm3计算)。
由于每座炉子单体设备在制造精度、现场安装精度、调试生产稳定结果不同,每个钢铁企业所提供的能耗介质不同,所以其实际的能源消耗一般比设计值高3%~20%,折中按新增氮气10%耗量(160Nm3/h)计算,温度加热到800℃(炉内温度)所需能量为0.2392×106KJ,折合消耗的混合煤气约为58Nm3/h,则每年多消耗煤气为 4.06×106Nm3(以年作业时间7000h计算),排放烟气1.6×106Nm3、高温氮气1.6×106Nm3、氢气8.05×104Nm3、氮氧化物528kg、二氧化硫213.15kg。
2 炉内主要参数与公辅能耗关联2.1 炉内压力炉内压力是由分布于炉子各部分(主要是底部)大量保护气体(压力(0.1-0.3bar)注入和炉上各放散阀门的开度调节形成,在整个炉内形成一个正压系统。
连续退火炉的施工要点

浅谈连续退火炉的施工要点摘要:冷轧立式连续退火炉的工艺比较复杂,施工过程中需要特别注意的问题较多。
本文从立式连续退火炉施工过程中的工艺钢结构、炉壳、辐射管及炉辊设备安装和炉体气密性试验等四个方面,浅要分析了连续退火炉施工过程中的要点。
关键词:退火炉;炉体;炉壳;施工要点连续退火机组主要用于轧后带钢的再结晶退火,以消除冷加工硬化,产品主要用于建筑、家电、汽车等行业。
我国第一条连续退火机组是宝钢在1989年从新日铁引入的2030mmcapl线。
连续退火机组工艺线上的退火炉分为立式炉和卧式炉两种。
相比于结构简单的卧式炉,立式炉的结构复杂得多,施工难度更大,其施工要点也就更值得研究总结。
连续退火机组立式炉的设备一般由炉体设备、炉内设备、炉外设备三部分组成。
从整体来说,立式连续退火炉设备安装的施工要点主要体现在炉子工艺钢结构、炉壳、辐射管、炉辊和炉子气密性试验上。
笔者就宝钢1750mmcal为例对这几个方面的施工要点进行分析与探讨。
从工艺上来说,退火一般分为9段:分别为喷气预热段、辐射管加热段、均热段、缓冷段、闪冷段、过时效段1、过时效段2、最终冷却段及水淬塔段。
生产时连续退火炉段工艺速度可达420m/min。
一、炉子工艺钢结构的施工要点因连续退火炉的工艺特点,炉子工艺钢结构及其平台的安装与炉壳安装、风机、热交换器、管道施工等必须穿插进行,一层结构一层设备,整个退火炉的安装期间呈现高空立体交叉作业状态。
工艺钢结构的安装要分别从入口和出口向炉中安装,这样可以把安装过程中的误差在炉中消除,能够更好地保证安装精度。
为了减少高空作业和确保施工安全,一般把炉体两侧的工艺钢结构柱子及梁预拼装成“井”字形框架。
再进行整体吊装作业。
吊装作业主要利用厂房内的桥式起重机进行,由于主厂房内桥式起重机数量有限,退火炉施工又为多点作业,行车使用频繁,需另配置数台汽车吊配合钢结构拼装作业。
作为整个退火炉工艺钢结构安装的基础,钢结构下段立柱及横梁的各项安装精度都应严格按设计要求和规范来进行,然后进行地脚螺栓的一次灌浆,待强度达到后进行立柱的精找和下部横梁的连接,使底层结构形成刚性框架,最后再进行柱、梁的找正找平。
冷轧连续退火炉工艺论文资料
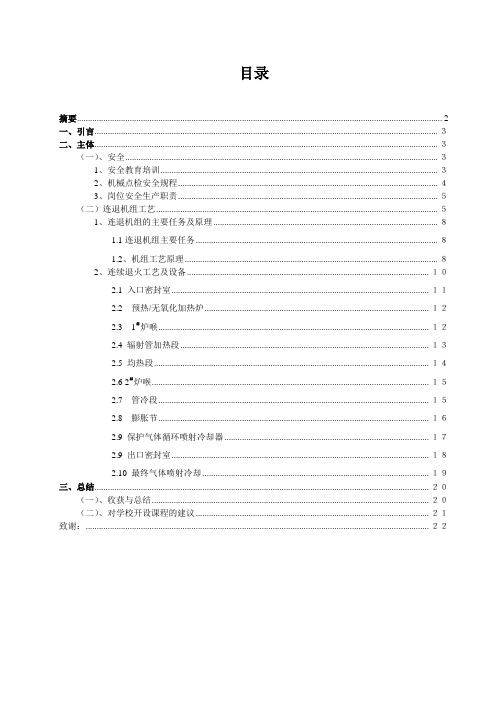
目录摘要 (2)一、引言............................................................................................................................................................ 3二、主体............................................................................................................................................................ 3(一)、安全.............................................................................................................................................. 31、安全教育培训.............................................................................................................................. 32、机械点检安全规程...................................................................................................................... 43、岗位安全生产职责...................................................................................................................... 5(二)连退机组工艺................................................................................................................................ 51、连退机组的主要任务及原理 ...................................................................................................... 81.1连退机组主要任务.............................................................................................................. 81.2、机组工艺原理................................................................................................................... 82、连续退火工艺及设备.............................................................................................................. 102.1 入口密封室..................................................................................................................... 112.2 预热/无氧化加热炉...................................................................................................... 122.3 1#炉喉........................................................................................................................... 122.4 辐射管加热段................................................................................................................. 132.5 均热段............................................................................................................................. 142.6 2#炉喉.............................................................................................................................. 152.7 管冷段........................................................................................................................... 152.8 膨胀节........................................................................................................................... 162.9 保护气体循环喷射冷却器 ............................................................................................. 172.9 出口密封室..................................................................................................................... 182.10 最终气体喷射冷却....................................................................................................... 19三、总结........................................................................................................................................................ 20(一)、收获与总结.............................................................................................................................. 20(二)、对学校开设课程的建议.......................................................................................................... 21致谢:............................................................................................................................................................ 22摘要:硅钢被誉为钢铁行业的“工艺品”,广泛的应用于各种电机和变压器的中心部件,其制造工艺复杂,装备总类多,设备自动化程度较高,生产过程困难,对各项指标的要求较高。
FCL退火炉介质管路
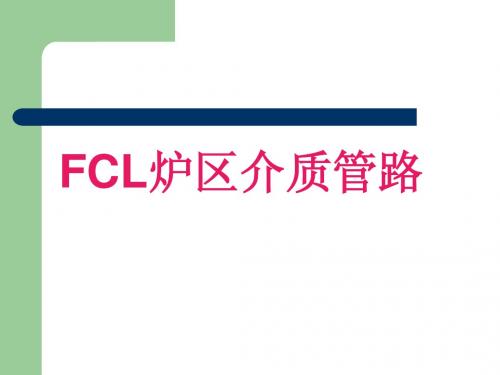
常用氮气 一是通入ESD、Thr.1、SJC、RJC、EXSD中 一是通入ESD、Thr.1、SJC、RJC、EXSD中 ESD 作为正常炉气使用 二是用于高温计吹扫 三是用于SJC RJC的风机 法兰、阀门、 SJC、 的风机、 三是用于SJC、RJC的风机、法兰、阀门、 仪表的密封 四是输送到DF RTF的传动侧 DF、 的传动侧, 四是输送到DF、RTF的传动侧,用于氮气吹 扫
事故氮气
事故氮气主要供RTF、SF、SJC、RJC使 、 、 事故氮气主要供 、 使 用 SJC RJC SF
混合用氮气 与氢气管路共同连接到混合器处, 与氢气管路共同连接到混合器处,按一定 的比例(H2: %),形成氮氢混合 的比例(H2:2%—4%),形成氮氢混合 通入SF中作为正常炉气使用。 SF中作为正常炉气使用 气,通入SF中作为正常炉气使用。
FCL炉区介质管路 炉区介质管路
退火炉区介质种类
1.氮气 氮气 2.氢气 氢气 3.氮氢混合气 氮氢混合气 4.压缩空气 压缩空气 5.冷却水 冷却水 6.天然气 天然气
氮气
氮气TOP点在 点在RJC的DS侧,由一条主管路 氮气 点在 的 侧 引出三条支路 PI 现场
按用途分类:
1.常用氮气管路 常用氮气管路 2.事故氮气管路(紧急氮气) 事故氮气管路(紧急氮气) 事故氮气管路 3.混合用氮气管路 混合用氮气管路
主要用于DF、RTF助燃空气风机的冷却 DF、 助燃空气风机的冷却; 主要用于DF、RTF助燃空气风机的冷却;DF、 DF RTF烟气风机的冷却 DF与RTFTF之间的支承 辊轴承的冷却。 辊轴承的冷却。
RJC的DS侧冷却水TOP点 RJC的DS侧冷却水TOP点 侧冷却水TOP 主要用于SJC、RJC换热器冷却;SJC、 主要用于SJC、RJC换热器冷却;SJC、RJC SJC 换热器冷却 风机的冷却;SJC、RJC法兰的冷却 DF、 法兰的冷却; 风机的冷却;SJC、RJC法兰的冷却;DF、 RTF、SF、SJC的五个高温计的冷却 其中, 的五个高温计的冷却。 RTF、SF、SJC的五个高温计的冷却。其中, 所有高温计的冷却水回水是经过一条单独 的回水管流入到地面上的水箱里。 SJC、 的回水管流入到地面上的水箱里。在SJC、 RJC的顶部每个冷却单元的上边 的顶部每个冷却单元的上边, RJC的顶部每个冷却单元的上边,均设有回 流水溢流水箱。 流水溢流水箱。
连续退火炉炉内露点温度高故障分析与控制
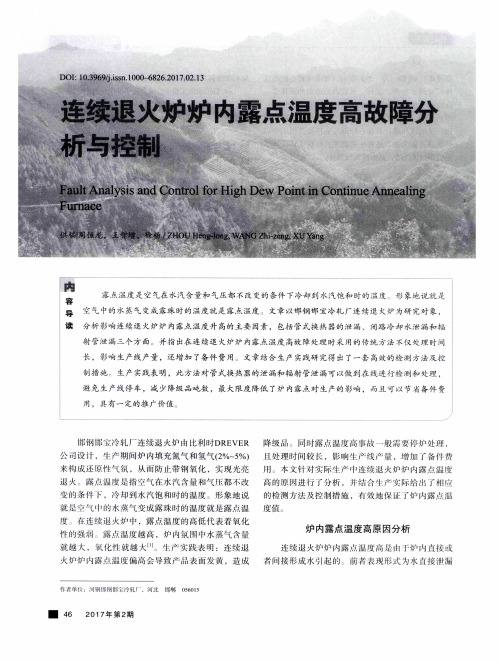
1 " 4 1 路 冷却水 主要 是川 来 对与炉 内直 接接 触 没备
期处 温状 态 l 损 坏 闭路 冷却水 泄漏 主要 足 南
寻找泄漏 点 ,这 样会导致 謦个 敞 处理时 『 H J 偏长 温度高事故 r l 1 .仅 寻找该泄漏点就牦费l 天时间
薹 l _ 、 = _ -
射 管泄 漏三 个方面 并指 出在连 续退 火炉炉内露点温度 高故 障处理 时采 用的传 统方法不仅 处理 时 间
长 ,影响 生产线产量 ,还增加 了备件 费用。文章 结合生产 实践研 究得 出了一套 高效的检测 方法及 控 制措施 生产 实践表 明,此 方法对管 式换 热器的泄漏和辐射 管泄漏 可以做 到在 线进行检测 和处理 ,
到炉1 人 】 ,包括 管式换 热 泄 漏和 闭路冷 却水泄 漏 ;
去,进 l f l j …观局部 岛温 ;= 址 燃 比参数设 小 碳变脆现 象 ,产生裂纹 一2 0 1 5  ̄ 1 i 3 月 ,加热段 l 2 … 现辐射管泄漏 导致炉内露点 温度商、 、
I ; 现渗 现为 气 巾的氧 ( J _ I j 炉『 大 】 的氢 气在高温 环境 合适 ,不 能满 足富氧燃烧 条件 ,导致辐 射管 } 卜 进 行化学反心 牛成 水,上 表现为辐射管_ 『 I I f 漏、
度 在连续 退火炉 中 ,露点 温度 的高低 代表着 氧化 性 的强弱 露点 温度越 高 ,炉 内氛 同巾水蒸 气 含量
就越 大 ,氧化 性 就越大 【 I I :生 产实践 表 明 :连 续退
炉 内露点 温度 高原 因分析
连续 退火 炉炉 内露 点温 度高 是 } { 1 丁' t J ’ , 1 人 】 白 : 接 或
公 司设计 ,牛产期 间炉 内填 充氮气 和 氢气 ( 2 %~ 5 %) 且处理 时 间较长 ,影响生 产线 产量 ,增 加 丁 备件 费
连续退火炉参数

连续退火炉参数
连续退火炉是一种重要的热处理设备,用于对金属材料进行退火
处理,可实现材料的去应力、软化、调质等目的。
为了保证退火质量,连续退火炉在使用时需要根据工作要求不断调整参数,以下是常用的
参数及调整方法:
1. 温度控制:连续退火炉需要设置合适的退火温度才能实现预期
效果。
温度过高会导致材料变形、熔化、氧化等问题,而温度过低则
会影响退火效果。
为了保证温度的准确性,可以使用高精度热电偶对
温度进行实时监测和调整。
2. 保温时间:保温时间决定了材料在炉内停留的时间,从而影响
材料在退火过程中的晶粒长大和组织变化。
保温时间长短应该根据不
同材料的特性和工作要求进行调整,通常可以通过加速或减缓输送速
度来改变保温时间。
3. 气氛控制:连续退火炉内不同气氛的存在对材料的退火效果有
着重要影响。
如在球墨铸铁的退火过程中,需要保持适当含量的氧气
以防止石墨氧化。
而在不锈钢等金属的退火过程中则需保持氮气或氢
气的气氛,以防止材料表面产生氧化皮。
4. 输送速度:连续退火炉通过输送带将材料送入炉内进行退火,
输送速度的快慢直接影响着材料的停留时间和受热时间。
为了保证材
料在炉内的均匀受热,输送速度应该适当调整,特别是对于比较薄的
管材或板材来说,输送速度的调整显得尤为重要。
总体而言,连续退火炉的参数调整需要根据具体材料和工作要求进行合理调整,以保证退火效果和质量。
在实际使用中,可以通过实时监测和反馈来及时调整参数,不断完善和提升退火技术,实现更好的退火效果。
试论连续退火炉冷却技术的发展

试论连续退火炉冷却技术的发展发布时间:2021-01-12T08:04:29.476Z 来源:《中国科技人才》2021年第1期作者:陈鹏远[导读] 本论文着重于研究连续退火炉冷却技术的发展。
中冶南方(武汉)热工有限公司湖北省武汉市 430205摘要:冷轧后连退线和镀锌线上所使用的主要设备是火炉,其所发挥的作用是采用退火技术处理冷轧带钢。
将冷轧加工应力消除,使其力学性能良好。
退火炉要实现其应有的功能,主要在于加热方面和冷却方面。
冷却技术的应用,主要体现为冷却的能力以及冷却的速率,两者缺一不可。
其中,冷却能力对退火炉的产量起到了决定性的作用;冷却速率对产品的性能有一定的影响。
本论文着重于研究连续退火炉冷却技术的发展。
关键词:连续退火炉;冷却技术;发展引言在生产带钢的过程中,带钢机械性能往往会受到冷却速度的影响,所以,最为关键的技术是一次冷却技术,该技术质量如何对产品机械性能具有直接相关性,同时还会影响退火周期以及适应机组的品种[1]。
对于带钢连退机组而言,快速冷却技术是最为重要的。
一、退火工艺的流程应用退火工艺技术的时候,需要严格按照流程操作。
退火炉段按照技术操作流程需要经过预热段、加热段,经过保温之后,就进入到缓冷段和快冷段,然后进入到时效段和终冷段,最后是淬水冷却段。
每个操作环节都不能缺少,否则会影响工艺质量。
所以,对于退火工艺流程要严格执行,并强化监督工作[2]。
二、连续退火炉冷却技术(一)气体喷射冷却技术新日本制铁公司在二十世纪70年代开发了气体喷射冷却技术。
该技术的应用中,用循环喷射保护气体冷却的方式,减慢了冷却速度,大约为每秒钟5摄氏度至30摄氏度之间,延长了过时效时间。
(二)冷水淬冷却技术日本钢管公司开发冷水淬冷却技术,可以有效降低炉内带钢的温度,从原有的700摄氏度至850摄氏度冷却到560摄氏度,经过淬水冷却之后,可以达到65摄氏度,冷却的速度可以达到每秒钟500摄氏度至2000摄氏度之间。
退火工艺流程、参数及产品
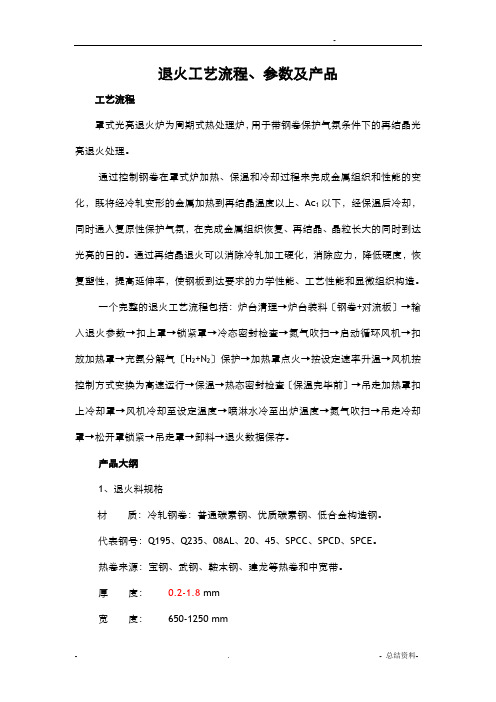
-退火工艺流程、参数及产品工艺流程罩式光亮退火炉为周期式热处理炉,用于带钢卷保护气氛条件下的再结晶光亮退火处理。
通过控制钢卷在罩式炉加热、保温和冷却过程来完成金属组织和性能的变化,既将经冷轧变形的金属加热到再结晶温度以上、Ac1以下,经保温后冷却,同时通入复原性保护气氛,在完成金属组织恢复、再结晶、晶粒长大的同时到达光亮的目的。
通过再结晶退火可以消除冷轧加工硬化,消除应力,降低硬度,恢复塑性,提高延伸率,使钢板到达要求的力学性能、工艺性能和显微组织构造。
一个完整的退火工艺流程包括:炉台清理→炉台装料〔钢卷+对流板〕→输入退火参数→扣上罩→锁紧罩→冷态密封检查→氮气吹扫→启动循环风机→扣放加热罩→充氨分解气〔H2+N2〕保护→加热罩点火→按设定速率升温→风机按控制方式变换为高速运行→保温→热态密封检查〔保温完毕前〕→吊走加热罩扣上冷却罩→风机冷却至设定温度→喷淋水冷至出炉温度→氮气吹扫→吊走冷却罩→松开罩锁紧→吊走罩→卸料→退火数据保存。
产品大纲1、退火料规格材质:冷轧钢卷:普通碳素钢、优质碳素钢、低合金构造钢。
代表钢号:Q195、Q235、08AL、20、45、SPCC、SPCD、SPCE。
热卷来源:宝钢、武钢、鞍本钢、建龙等热卷和中宽带。
厚度:0.2-1.8 mm宽度:650-1250 mm卷径:φ510 mm卷外径:φ900 –φ1900 mmφ900 –φ1650 mm 两种卷重:Max 26t〔1250mm板宽〕屈服强度:max. 910MPa拉伸强度:max. 1280MPa2、成品尺寸:厚度:同来料宽度:同来料卷径:同来料卷外径:同来料卷重:同来料屈服强度:max. 360MPa拉伸强度:max. 700MPa15万吨热处理产品大纲如下:4、罩式退火炉机组主要条件和要求:1〕机组型式:强对流循环罩式退火炉机组2〕炉子数量:炉台数16台3〕热处理形式:冷轧带钢的再结晶〔软化〕退火。
4〕燃料:天然气热值≥8400kcal/ N m3.〔考核消耗按8500kcal/ N m3〕5〕保护气体:氨分解气,75%H2,25%N26〕最大装炉高度:按板宽950mm装四卷、1250mm装三卷考虑。
退火炉管理规定

退火煤气炉管理规定
退火炉停炉期间,煤烟经退炉进行放散,为保证安全及防止环境污染,试运行期间规定如下:
1、退火炉停炉1小时内,一次风机风量不低于20个风,且停炉后立即将通炉底的饱和蒸汽进行放散。
2、退火炉停炉后1小时——2小时内,一次风机风量逐渐控制在10个风以上。
3、退火炉停炉后2小时以后,一次风机风量不小于5个风。
4、退火炉停炉及点炉整个空闲期间,不许停止二次风机。
5、点火前必须将煤气从退火炉内倒出,并将退火炉内残余烟气处理干净,以及煤气合格后,再进行点火。
6、组织相关人员进行现场煤气浓度测试,并将结果上报生产安环部与机动部,经讨论指示后执行。
值班操作工要根据以上要求,按步骤进行操作,不能图方便以及急于交班,将一次见机风量一次降到最低。
机动部
生产安环部
2008年5月13日。
连续退火炉炉内气氛分析与控制

( 1 ) 预热段入 口密封棍密封不严或密封氮气效果不佳 ; ( 2 ) 3 J I 热炉 辐射管烧穿 , 导致加热段氧气含量高 图4 为辐射管烧穿( 裂) 实例 。 ( 3 )
…
…
上接 第6 9 页
2 . 5完善技 术管 理
实施严格的工艺技术管理 , 保障每个采矿小组至少配备一名专 利用系数。 其次 , 尽量让工艺车停靠位置贴近挖掘机装矿岩 附近 , 让 对工艺进行控制 。 以提升挖掘效率 以生产力为 目 挖掘机回转角度小于9 0 度, 这样 可以避 免因挖掘机 回转而支 出不必 业采矿技术人员 , 对挖掘顺序进行合理分配 。 要 的时间 , 为生产 能力赢得 时间。 最后, 不要让挖掘机与工艺车处于 标 , 同一水 平面可以让工 艺车停泊在挖掘机下步台阶 , 减少挖掘机提斗 3结语 时间和 回转时 间 , 这 也是提升挖掘机生产 能力 的有效措施之一 。 本文主要对影响单斗挖掘机生 产能力的因素进行 分析 并结 合 2 . 2避 免 不 必 要 的 挖 掘 机 移 动 编制月度生产计划过程中要将 生产连续. 陛问题考 虑其 中, 解决 因采场分散 而加大运距 的难题 , 减少挖掘机不必要的移动可以从作 业时间上赢得更大 的生 产力 及挖掘效率 。 2 , 3重视 挖 掘 设备 养护 工 作 提 出因素给予提高单斗挖掘机生产能力的对 应策略 , 其中影响露天 矿单斗挖掘机 生产能力的最大 因素莫过于挖 掘机 的工 作时间与时 间利用系数 , 我国矿部之所 以对挖掘机生 产效率严 抓 , 其 目的就在 于宣传及明确有效时 间利用和小 时产能对挖 掘机 生产能力影响的 重要性 。 随着 我 国矿 产 业 的 发展 , 对 单 斗 挖 掘 机 的 利 用 将 会 继 续 下
BAF介绍
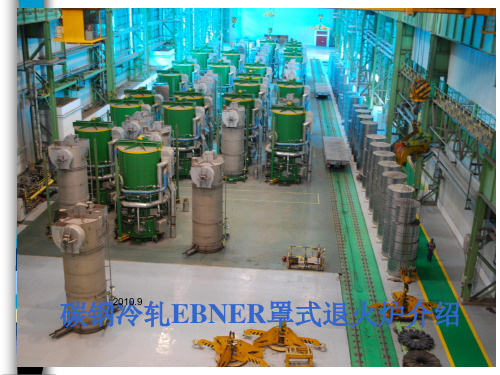
罩式炉设计产能
年产80万吨冷轧带钢 生产钢种CQ、DQ、DDQ、EDDQ、HSS/HSLA 年生产时间8000小时,作业率92.6% 最大装炉净重为100t,装炉高度5400mm 装、出炉总时间设定为1.0h 机时产量100吨/小时,平均日产2191吨
全氢罩式退火炉机组参数
终冷台布置图
1.7.2 终冷台-终冷台对流板
类型 支撑 厚度 面积 内径 直径 1950mm 数量 单重 30 约353 对流顶 30mm 30% 板
中间对 50mm 37.5% 流板 对流底 60mm 39.5% 板
570mm
590mm
1950mm
1950mm
100
30
约514
约 1295
1.8 调压站
1.9 液压站
用于内罩锁紧机构 由两台液压泵、马达、控制阀等必需的 元气配件及管道组成 装有电热元件,用于在低温环境下保持 液压动力系统的工作温度
液 压 站 外 观 图
液压站-技术参数
液压泵电机功率:4kW 能力:约12 L/min 速度:1500rpm 油箱容积:220L 压力:最小:110bar,最大:130bar 过滤器目数:10 µ m 手动泵泵排量:14cm³
2、全氢罩式炉的主要技术特点
保护气氛的强对流 采用纯氢作为保护气体 全封闭炉台,可将内罩下退火
气氛的露点降至-65℃; 带加热罩缓冷的冷却方式,减 少钢卷出现粘接的几率;
保护气氛的强对流
罩式退火炉退火的传 热方式:通过内罩对 带钢卷进行间接加热 。炉料得到热量多少 取决于内罩壁的辐射 传热和气体对流传热 的能力 提高辐射传热的效果 :形成较高的温度差 ,这必将导致钢卷外 圈过热 强对流的目的:把内 罩壁上的热量尽快地 传递给钢卷,就需要 提高对流换热的效率
连续退火炉炉内气氛分析与控制

连续退火炉炉内气氛分析与控制作者:贺有赵赛胡树森马凯来源:《中国科技纵横》2015年第11期【摘要】介绍了连续退火炉炉内气氛的组成及监测,说明了炉内气氛主要组成成分,阐述了氢气含量配比控制和炉内正常生产控制以及有害成份控制,分析了有害成分含量升高的主要常见原因,并提供了具体问题的解决措施,在实际生产中,特别适用于特种钢材的生产操作炉内气氛要求,使得退火炉炉内氛围得到有效控制,保证了带钢退火生产工艺稳定,满足各类带钢退火要求,提高产品质量。
【关键词】退火炉炉内气氛氢气含量控制1 前言邯钢西区冷轧厂连续退火炉由比利时DREVER公司设计的立式退火炉,按照带钢走向和热处理功能分为预热段、加热段、均热段、缓冷段、快冷段、过时效段和终冷段。
炉内氛围为氮气和氢气按照一定比例混合构成的还原性气氛,保证带钢在炉内不被氧化,去除带钢表面残留的氧化物,达到保证带钢表面质量的条件要求下进行退火。
2 炉内气氛含量的测量邯钢西区冷轧厂连续退火炉炉内气氛检测仪按区段布置共有3台CAA(炉内氛围分析柜),每台分析内都包含3种分析仪,分别检测氢气含量、氧气含量和露点。
氢气含量使用ABB AO2040氢气分析仪,采用热导原理进行分析,氧气含量分析使用Delta F 150氧气分析仪,采用电化学原理进行分析,露点分析仪采用Vaisla DMT 142露点分析仪。
CAA01检测预热段2个区、加热段3个区、均热段炉内气氛;CAA02检测缓冷段2个区、快冷段3个区、过时效段2个区炉内气氛;CAA03检测过时效段2个区、终冷5个区炉内气氛。
各段特征气氛含量的测量是利用分析仪巡回扫描的方式进行的,一个周期大约45分钟,通过对炉内各段气体含量的监测,控制炉内还原气氛状况。
3 炉内气氛控制连续退火炉炉内气氛是由氮气和氢气组成的还原性保护气体,为了防止外界空气进入炉内,连续退火炉正常生产时采用微正压操作。
为了保证一定的炉压需要持续注入一定比例的保护气体和还原性气体氢气。
卧式连退炉培训资料(1)

连续退火炉及涂层干燥炉 培 训 资 料第一章 连续退火炉及涂层干燥炉设备 连续退火炉是冷轧硅钢带连续退火机组的中心环节,是硅钢进行热处理的关键设备。
第一节炉子设备概述1.1 连续退火机组炉子的组成硅钢连续退火机组的炉子部分主要包括:连续退火炉部分、涂层干燥炉部分、涂后冷却段部分。
1.1.1 连续退火炉的组成连续退火炉有13个部分组成,见图1-1。
图1-1 连续退火炉及涂层干燥炉的组成其组成主要包括:1)进口密封室、2)预热段(PH)、3)无氧化炉(NOF)、4)1#炉喉、5)加热炉 (RTF) 、6)2#炉喉、7)均热炉(SF)、8)3#炉喉、9)炉体膨胀节、10)4#炉喉、11)循环气体喷射冷却段(RJC)、12)出口密封室、13)FJC1.1.2 涂层干燥炉的组成涂层干燥炉分两个部分:14)干燥炉(DF-DS)、15)烧结炉(DF-BS)1.1.3 涂后冷却段的组成14)空气喷射冷却段(AJC)1.2 各部分的功用1.2.1 进口密封室进口密封室的主要功用是维持恒定的炉压和防止空气渗进炉内。
其结构由一根水冷密封辊和一个密封门、密封用氮气通入装置(喷氮管)及非常用氮气喷嘴所组成。
1.2.2 预热段(PH)预热段主要目的是利用NOF排出烟气的物理热、NOF未燃尽气体和SF流过来的氢气燃烧的化学热,预热带钢至要求温度。
该炉段为弱氧化气氛。
配置10套只供空气不给煤气的补燃烧嘴。
1.2.3 无氧化加热炉(NOF)无氧化加热炉采用经精脱硫的煤气(H2S<0.015g/m3)作为燃料,并用燃烧效率极高的高速煤气烧嘴,进行直接燃烧。
空燃比一般设定为0.85~0.95之间,即采用煤气过剩的燃烧方式燃烧。
因而其能对进入炉内的钢带无氧化地、均匀而快速地加热,这样既缩短了对钢带的加热时间,又缩短了炉子的长度。
炉底辊采用耐热钢制的水冷辊。
1.2.4 1#炉喉1#炉喉是设置于NOF炉和HF炉之间的—个断面相当狭窄的钢带通道,它的设置主要是为防止NOF的燃烧废气渗入到后面的HF及SF内去,以免污染炉内的控制气氛。
氮气吹扫解决方案

鄂尔多斯联合化工有限公司60/104化肥项目氮气(N2)管线吹扫方案(ELGF-006-028)编制:李永伟张腾飞审核:审定:批准:内蒙古鄂尔多斯联合化工有限公司尿素分厂目录一、编制依据二、吹扫目的及技术要求三、吹扫前应具备的条件四、吹扫前的准备工作五、作业程序六、作业后处理七、安全注意事项八、作业记录九、作业结果报告十、作业附件附图:尿素分厂氮气(N2)管线吹扫示意图图氮气(N2)管线吹扫方案一、编制依据1、尿素装置的PID图;2、尿素生产工艺的基本原理;3、尿素动静设备工作的基本原理;4、化工生产的安全技术规范。
二、吹扫目的及技术要求1、目的:1.1.检查N2管网是否畅通。
检查管网配管是否有疏漏;检查管网中的法兰,阀门、仪表等的接口处,填料压盖等是否有泄漏。
1.2.由于管道施工及设备制造过程中残留的杂物,如:焊渣沉积物、在管道及设备内表面的氧化皮、颗粒物、附于其内壁的泥砂杂物、油脂、焊渣和锈蚀物等。
在工艺管道及设备投用前,必须进行彻底地清除,保证管道、设备的清洁,避免引起发生的堵塞管道、设备;损坏机器、阀门和仪表;玷污催化剂及化学溶液、影响产品质量保证化工投料的顺利进行及安全生产。
2、技术要求:2.1. 0.7Mpa(A)、25℃的N2用于吹扫各N2管网线;2.2.吹扫的空气流速≥30m/s。
2.3. 吹扫时,应将管道上安装的所有仪表测量元件(如流量计、孔板等)拆除,防止吹扫时流动的赃物将仪表元件损坏,同时,还应对调节阀采取保护措施;2.4. 吹扫时,必须在换热器、塔器等设备入口侧加盲板,只有待上游吹扫合格后方可进入设备,一般情况下换热器本体不参加空气吹扫;2.5.吹扫时原则上不得使用系统中的调节阀作为吹扫的控制阀,如需控制系统吹扫风量时,应选用临时吹扫阀门,吹扫时,应将安全阀与管道连接处断开,并加盲板或挡板,以免脏杂物吹扫到阀底,使安全阀底部密封面磨损;2.6.系统吹扫时,所有的仪表引压管线均应打开进行吹扫,并应在系统综合气密实验中再次吹扫;2.7.所有的放空火炬管线和导淋管线,应在与其连接的主管后进行吹扫,设备壳体的导淋及液面计、流量计引出管和阀门等都必须吹扫;2.8.在吹扫进行中只有上游系统合格后,吹扫空气才能通过正常流程进入下游系统;2.9. 当管道直径大于500mm和有人孔的设备,吹除前先要用人工清扫,并拆除其有碍吹扫的内件;2.10.所有罐、塔、反应器等容器,在系统吹扫合格后应再进行人工清扫,并复位相应的内件;2.11.检查系统内所有管道管卡安装完毕,配备合理,确保吹除过程中不会发生管道震动现象。