半导体制造技术简介
半导体芯片制造技术
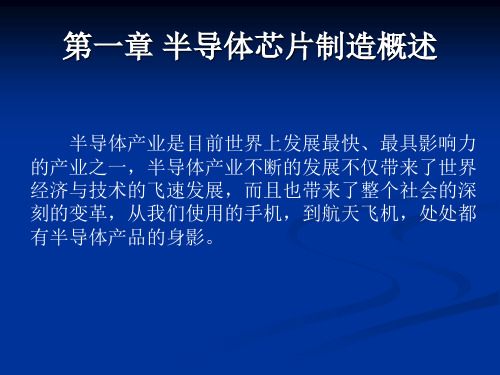
⑸固定的熔点
图1-8 晶体非晶体的加热曲线
2. 晶体的缺陷 晶体缺陷按缺陷的几何尺寸可分为点缺陷,如空 位、间隙原子;线缺陷,如位错;及面缺陷,如晶粒 间界和堆垛层错等。
第三节 半导体生产污染控制
一、污染物种类
1.颗粒污染物 颗粒包括空气中所含的颗粒、人员产生的颗粒、 设备和工艺操作过程中使用的化学品产生的颗粒等。 在任何晶片上,都存在大量的颗粒。有些位于器件不 太敏感的区域,不会造成器件缺陷,而有些则属于致 命性的。根据经验得出的法则是:颗粒的大小要小于 器件上最小的特征图形尺寸的1/10,否则,就会形成 缺陷。
单晶体
多晶体
非晶体
图1-3 特性, 称之为晶体的自限性。
⑶各向异性 晶体的物理性质随着晶面的方向不同而不同, 称为晶体的各向异性。
图1-7 云母片和玻璃片的石蜡熔化实验
⑷对称性 晶体在某几个特定的方向上所表现出的物理、 化学性质完全相同。在晶体中,如果沿某些特定的 方向原子排列的密度相同,则沿这些方向的性能相 同。
浓度/(粒/ 升) 小于等于1 小于等于10
最高 最低 最高 最低
噪声(A声 级)/db
100
1000 10000
大于等 于0.5
小于等于 100
小于等于 1000
27
18
60
40
小于等于70
小于等于 10000
五、洁净室的维护 超净间的定期维护是非常必要的。清洁人员 必须要穿着与生产人员一样的洁净服,超净 间的清洁器具,包括拖把,也要仔细选择。 一般家庭使用的清洁器具太脏,无法在超净 间使用。而且使用真空吸尘器也要特别注意。 真空吸尘器中的排风系统中,装有HEPA过 滤器,现在已经可以在超净间中使用。许多 超净间采用内置式真空系统来减少清洁时产 生的脏东西。
半导体制造工艺技术概述

铝淀积
42
蒸铝的台阶覆盖
43
难熔阻挡金属(RBM)溅射
44
塞状钨通孔系统
45
硅化
46
现代金属化系统
47
铜金属化
• 铝的缺点
– 电阻比铜大,在亚微米工艺下表现明显 – 电迁徙问题
• 铜的优点
– 导电性能好 – 提高抗电迁徙特性
48
双大马士革工艺
49
功率铜
50
组装
晶圆结构
52
安装与键合
• 氧化工艺
– 干法:在纯净干燥的氧气中加热,速度缓慢,质量很高,用于器件 – 湿法:在氧气混合水蒸气中加热,速度加快,质量降低,用于场氧化层 – 淀积:在非硅材料上形成二氧化硅,通过气态硅化合物和气态氧化剂反
应值得,用于两层导体之间的绝缘层或保护层
17
氧化炉简图
18
氧化物去除
19
氧化物刻蚀
• 湿法刻蚀
– 使用稀释的氢氟酸溶液
• 干法刻蚀
– 反应离子刻蚀 (RIE) – 等离子刻蚀 – 化学气相刻蚀
20
反应离子刻蚀
21
对晶圆表面形貌的影响
22
氧化分凝机制
23
杂质增强氧化效应
24
硅的局部氧化 (LOCOS)
25
Kooi效应
26
扩散和离子注入
扩散工艺
28
磷扩散工艺
29
横向扩散
30
改变扩散速率的机制
中国芯技术系列
半导体制造工艺技术概述
技术创新,变革未来
提纲
• 硅制造 • 光刻技术 • 氧化物生长和去除 • 扩散和离子注入 • 硅淀积和刻蚀 • 金属化 • 组装
半导体制造技术导论离子注入工艺

• 阈值电压控制:通过离子注入工艺调节PMOS和NMOS
区
的阈值电压
• NMOS器件:N型半导体作为沟道,P型半导体作为源漏
• 掺杂区形成:通过离子注入工艺形成PMOS和NMOS的
区
源漏区
离子注入工艺在光电二极管中的应用
光电二极管的结构特点
• P-N结:由P型半导体和N型半导体组成的结
• 光敏区:位于P-N结附近的区域,对光敏感
• 掺杂浓度均匀性:如何实现更均匀的掺杂,提高器件性能
• 注入损伤:离子注入过程中如何减少对半导体材料的损伤
• 工艺集成:如何将离子注入工艺与其他工艺集成,提高生产效率
解决方案
• 优化离子注入设备和工艺:提高掺杂浓度的均匀性和降低注入损伤
• 采用新型离子注入技术:如扫描离子注入、等离子体浸入离子注入等,提高工艺效
• 多离子注入技术的发展:实现多种元素的共注入,提高器件的性能和可靠性
离子注入工艺的发展方向
• 精确控制掺杂:实现更精确的浓度控制和更均匀的掺杂
• 降低能耗优化离子注入设备和工艺,降低能耗
• 环保减排:减少离子注入过程中的污染排放,提高环保水平
离子注入工艺面临的挑战及解决方案
离子注入工艺面临的挑战
果
• 加强工艺集成:与光刻、刻蚀等工艺进行集成,提高生产效率
离子注入工艺在未来半导体制造中的应用前景
离子注入工艺在集成电路制造中的应用
• 提高晶体管、二极管等器件的性能,提高集成电路的整体性能
• 实现新型器件的制作,如鳍式场效应晶体管(FinFET)等
离子注入工艺在光电二极管制造中的应用
• 提高光电二极管的光电转换效率,提高光电传感器的性能
• 大电流器件:需要承受大电流的器件
半导体制造工艺技术

半导体制造工艺技术近年来,随着智能化和信息化的加速推进,半导体技术逐渐成为各行各业发展的重要支撑。
而半导体制造工艺技术作为半导体领域中的重要组成部分,也逐渐发挥着越来越重要的作用。
半导体制造工艺技术是指将半导体材料加工成各种晶体管、电子元件等的一系列加工过程。
具体的技术过程需要先将半导体原片进行各种加工和处理,然后在其表面涂上不同的光刻胶,在光刻机中通过利用激光光源或者电子束来进行微细的图案设计和成像。
随后,将图案部分进行刻蚀或注入等处理,形成半导体器件的各个部分。
最终,通过不同的清洗和检测等工艺,制成成品。
随着技术的不断发展,半导体制造工艺技术也不断提高。
其中,掩膜技术、微影技术、氧化和扩散技术等都得到了广泛应用。
而像微流水线加工、纳米加工等也逐渐成为了前沿技术。
在这些技术的支持和推动下,半导体制造工艺技术已经在过去几十年中实现了飞跃式的进步。
然而,同时也存在着一些技术问题,如色散、残留应力等。
这些问题对于器件的性能和稳定性有很大影响。
因此,如何解决这些问题也成为了今后半导体制造工艺技术发展的一大关键。
除了以上技术问题外,环保和成本方面的问题也在制约着半导体制造工艺技术的发展。
制造过程中产生的化学废水、化学废气等对环境的影响不可忽视。
解决这些环保问题将成为今后半导体制造工艺技术发展中的另一个难点。
同时,随着技术的不断进步,半导体制造工艺技术成本也在不断下降。
这将进一步推动半导体工业的稳健发展。
但是,这也意味着制造厂商需要降低成本、提高效率,这对制造工艺技术的研究和创新提出了更高的要求。
总的来说,半导体制造工艺技术是半导体领域中不可或缺的一个重要组成部分。
随着技术和市场的不断变化,今后其发展将会面临更多挑战。
但是,通过不断的技术创新和优化,相信半导体制造工艺技术能够顺利实现新的突破和发展。
半导体行业的智能制造了解半导体行业的智能制造技术和趋势

半导体行业的智能制造了解半导体行业的智能制造技术和趋势半导体行业的智能制造:了解半导体行业的智能制造技术和趋势随着科技的不断发展,智能制造已经成为各个行业的发展趋势,其中半导体行业也不例外。
半导体作为信息时代的基石,其制造技术的先进程度对整个行业的发展起到至关重要的作用。
本文将介绍半导体行业的智能制造技术和当前的趋势。
一、智能制造在半导体行业的应用智能制造技术在半导体行业的应用领域涵盖生产、研发以及供应链等方面,主要体现在以下几个方面:1. 生产领域在半导体生产的整个过程中,智能制造技术可以提高生产效率、降低成本和提升产品质量。
通过引入自动化设备和机器人技术,半导体厂商可以实现生产流程的智能化管理,减少人力资源的浪费,提高生产线的运行效率。
2. 研发领域智能制造在半导体研发中的应用主要体现在缩短研发周期、提高研发效率和优化设计流程等方面。
通过引入虚拟仿真技术和数据分析算法,半导体研发团队可以更加快速地验证和优化设计方案,降低研发成本,提高产品的设计质量。
3. 供应链管理半导体行业的供应链十分庞大复杂,包括原材料采购、生产计划、库存管理等环节。
智能制造技术可以通过数据分析和预测算法,提高供应链的可视化程度和反应速度,降低库存压力,提高供应链的灵活性和准确性。
二、半导体行业智能制造的趋势1. 自动化升级半导体行业智能制造的趋势之一是自动化升级。
随着机器人技术和自动化设备的不断发展,越来越多的传统工序可以由机器代替人工操作,从而提高生产效率和降低成本。
例如,自动化的芯片组装设备可以实现高速、高精度的芯片组装,大幅提高生产效率。
2. 数据分析与人工智能数据分析和人工智能技术在半导体行业的应用也是当前的趋势之一。
通过收集和分析海量的生产数据和设备数据,可以实现对生产过程的实时监控和预测故障的能力。
同时,人工智能技术可以应用于半导体设备的优化和智能控制,提高生产效率和设备可靠性。
3. 智能供应链管理供应链管理是半导体行业智能制造的重要环节,当前的趋势是通过智能化的供应链管理系统,实现对供应链各个环节的实时监控和管理。
半导体制程技术简介

• 然后再进行烘烤,使没有被洗掉的光阻变得比较坚硬 而不至于在下一步蚀刻的时候被破坏掉。
2.4 酸蚀刻
• Acid Etch
– 将没有被光阻覆盖的薄膜腐蚀掉,是酸蚀刻的 主要任务。
– 蚀刻完毕之后,再将光阻洗去。
• 酸蚀刻要使用到多种酸剂,例如:腐蚀 SiO2需要用氢氟酸(剧毒无比的东东);去除 光阻需要用到硫酸。
• 铜制程沉积
– Copper Deposition
• 化学气相沉积
– Chemical Vapor Deposition
• Metal Deposition
– 一般来说,采用Physical Vapor Deposition (PVD;物理气相沉积)的方法制作金属薄膜。
– 这里面的金属薄膜包括:Aluminum(铝), Gold (金) and Tungsten(钨)。
2.5 清洗甩干
• Spin Rinse Dry
– 晶园本质上是一种类似于玻璃的东西,很脆、 易碎。任何碰撞都将导致晶园碎裂,所以在半 导体厂使用真空吸盘来抓取晶园。
– 但是即便如此,在防止了晶园碎裂导致的细小 颗粒之后。仍然必须对晶园做经常性的清洗, 以防止细小颗粒残留在晶园的表面上。
• 几乎在每一步的操 作后,都需要对晶 园进行清洗。
– 采用铜导线的困难:
• 当铜和硅接触的时候,会在硅中发生非常快速的扩 散。
• 这种扩散还将改变制作在硅上面半导体三极管的电 学特性,导致三极管失效。
– IBM最终克服了这些困难(Damascene):
• 采用先做绝缘层,再做铜导线层的方法解决扩散问 题。
• 在制作铜导线层的时候,IBM采用一种铜的多晶体, 进一步限制铜在硅中的扩散。
半导体制造技术

半导体制造技术
半导体制造技术是指以半导体材料为基础,利用先进的设备、工艺和测试技术,在晶圆上制作各种尺寸、形状和功能的集成电路(IC)元件。
半导体制造技术包括晶圆生产、片上集成、封装、测试等一系列步骤。
晶圆生产技术是半导体制造的核心步骤,其目的是在晶圆表面形成一层导电层,用于在其表面制作微纳米尺寸的元件及连接线路。
常用的晶圆生产技术有光刻、电镀、气相沉积、激光刻蚀、无损整形、金属化学气相沉积等。
片上集成技术是将器件与线路集成在一个晶片上,实现信号传输及功能实现。
目前,在片上集成中使用的技术主要有光刻、激光刻蚀和激光加工等。
封装技术是指将晶片封装到一个容器中,以便将其与外部电路和环境完全隔离,并保护其内部结构。
一般来说,封装技术可以分为焊接、固化、涂覆、压合和滴胶等。
测试技术是检查半导体元件及集成电路性能的手段,如功耗测试、性能测试、动态测试、稳态测试等。
半导体制造工艺流程简介
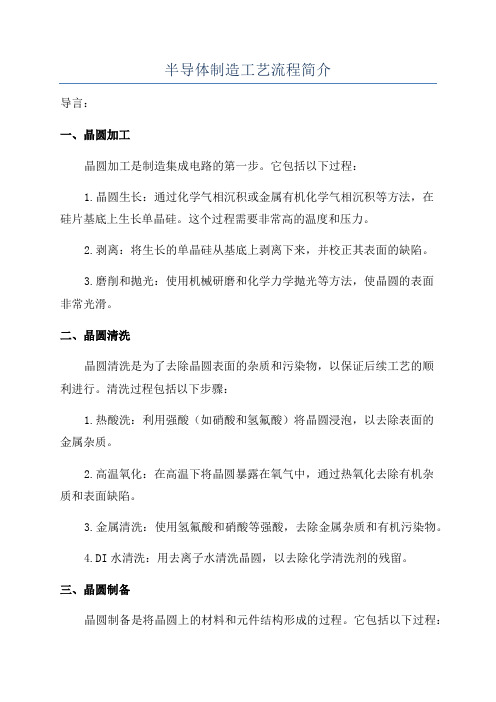
半导体制造工艺流程简介导言:一、晶圆加工晶圆加工是制造集成电路的第一步。
它包括以下过程:1.晶圆生长:通过化学气相沉积或金属有机化学气相沉积等方法,在硅片基底上生长单晶硅。
这个过程需要非常高的温度和压力。
2.剥离:将生长的单晶硅从基底上剥离下来,并校正其表面的缺陷。
3.磨削和抛光:使用机械研磨和化学力学抛光等方法,使晶圆的表面非常光滑。
二、晶圆清洗晶圆清洗是为了去除晶圆表面的杂质和污染物,以保证后续工艺的顺利进行。
清洗过程包括以下步骤:1.热酸洗:利用强酸(如硝酸和氢氟酸)将晶圆浸泡,以去除表面的金属杂质。
2.高温氧化:在高温下将晶圆暴露在氧气中,通过热氧化去除有机杂质和表面缺陷。
3.金属清洗:使用氢氟酸和硝酸等强酸,去除金属杂质和有机污染物。
4.DI水清洗:用去离子水清洗晶圆,以去除化学清洗剂的残留。
三、晶圆制备晶圆制备是将晶圆上的材料和元件结构形成的过程。
它包括以下过程:1.掩膜制作:将光敏材料涂覆在晶圆表面,通过光刻技术进行曝光和显影,形成图案化的光刻胶掩膜。
2.沉积:通过物理气相沉积或化学气相沉积等方法,在晶圆上沉积材料层,如金属、氧化物、硅等。
3.腐蚀:采用湿法或干法腐蚀等技术,去除晶圆上不需要的材料,形成所需的结构。
4.清洗:再次进行一系列清洗步骤,以去除腐蚀产物和掩膜残留物,保证材料层的质量。
四、材料获取材料获取是指在晶圆上制造晶体管、电阻器、电容器等器件结构的过程。
它包括以下步骤:1.掺杂:通过离子注入或扩散等方法,在晶圆上引入有选择性的杂质,以改变材料的导电性或断电性能。
2.退火:通过高温热处理,消除杂质引入过程中的晶格缺陷,并使掺杂的材料达到稳定状态。
3.金属-绝缘体-金属(MIM)沉积:在晶圆上沉积金属、绝缘体和金属三层结构,用于制造电容器。
4.金属-绝缘体(MIS)沉积:在晶圆上沉积金属和绝缘体两层结构,用于制造晶体管的栅极。
五、封装和测试封装是将晶圆上制造的芯片放在封装底座上,并封装成可插入其他设备的集成电路。
半导体制造技术ppt

半导体制造的环保与安全
05
采用低能耗的设备、优化生产工艺和强化能源管理,以降低能源消耗。
节能设计
利用废水回收系统,回收利用生产过程中产生的废水,减少用水量。
废水回收
采用低排放的设备、实施废气处理技术,以减少废气排放。
废气减排
半导体制造过程中的环保措施
严格执行国家和地方的安全法规
安全培训
安全检查
半导体制造过程的安全规范
将废弃物按照不同的类别进行收集和处理,以便于回收利用。
废弃物处理和回收利用
分类收集和处理
利用回收技术将废弃物进行处理,以回收利用资源。
回收利用
按照国家和地方的规定,将无法回收利用的废弃物进行合法处理,以减少对环境的污染。
废弃物的合法处理
未来半导体制造技术的前景展望
06
新材料
随着人工智能技术的发展,越来越多的半导体制造设备具备了智能化控制和自主学习的能力。
半导体制造设备的最新发展
更高效的生产线
为了提高生产效率和降低成本,各半导体制造厂家正在致力于改进生产线,提高设备的联动性和生产能力。
更先进的材料和工艺
随着科学技术的发展,越来越多的先进材料和工艺被应用于半导体制造中,如石墨烯、碳纳米管等材料以及更为精细的制程工艺。
薄膜沉积
在晶圆表面沉积所需材料,如半导体、绝缘体或导体等。
封装测试
将芯片封装并测试其性能,以确保其满足要求。
半导体制造的基本步骤
原材料准备
晶圆制备
薄膜沉积
刻蚀工艺
离子注入
封装测试
各步骤中的主要技术
制造工艺的优化
通过对制造工艺参数进行调整和完善,提高产品的质量和产量。
制造工艺的改进
半导体芯片制造技术
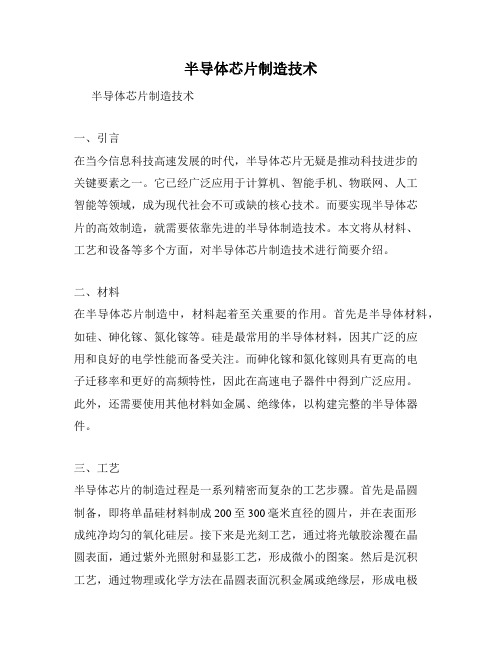
半导体芯片制造技术半导体芯片制造技术一、引言在当今信息科技高速发展的时代,半导体芯片无疑是推动科技进步的关键要素之一。
它已经广泛应用于计算机、智能手机、物联网、人工智能等领域,成为现代社会不可或缺的核心技术。
而要实现半导体芯片的高效制造,就需要依靠先进的半导体制造技术。
本文将从材料、工艺和设备等多个方面,对半导体芯片制造技术进行简要介绍。
二、材料在半导体芯片制造中,材料起着至关重要的作用。
首先是半导体材料,如硅、砷化镓、氮化镓等。
硅是最常用的半导体材料,因其广泛的应用和良好的电学性能而备受关注。
而砷化镓和氮化镓则具有更高的电子迁移率和更好的高频特性,因此在高速电子器件中得到广泛应用。
此外,还需要使用其他材料如金属、绝缘体,以构建完整的半导体器件。
三、工艺半导体芯片的制造过程是一系列精密而复杂的工艺步骤。
首先是晶圆制备,即将单晶硅材料制成200至300毫米直径的圆片,并在表面形成纯净均匀的氧化硅层。
接下来是光刻工艺,通过将光敏胶涂覆在晶圆表面,通过紫外光照射和显影工艺,形成微小的图案。
然后是沉积工艺,通过物理或化学方法在晶圆表面沉积金属或绝缘层,形成电极和绝缘层结构。
接着是离子注入工艺,通过注入掺杂物,改变半导体材料的导电性质。
最后是退火和封装工艺,通过高温和真空等条件,使半导体器件的性能得到进一步提升,并进行包装,以保护器件并便于使用。
四、设备为了实现半导体芯片的高效制造,需要依靠先进的制造设备。
例如,光刻机是半导体芯片制造中至关重要的设备,用于将图案图案转移到晶圆表面。
离子注入设备则用于将掺杂物注入到半导体材料中,改变其导电性能。
薄膜沉积设备用于沉积金属或绝缘膜层,形成半导体器件的结构。
还有退火设备、切片机、封装机等。
这些设备都需要高度精确的控制和先进的工艺技术,以确保半导体芯片的品质和性能。
五、前沿技术目前,半导体芯片制造技术正朝着更小、更高集成度和更高性能的方向发展。
随着摩尔定律的推进,传统的2D平面尺寸已经达到极限,因此研究人员正在探索新的制备技术,如三维堆叠集成技术、纳米级材料和器件结构设计等。
半导体制程简介
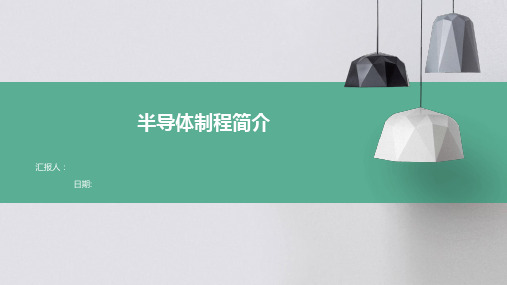
阐述图形化工艺的基本原理和方法,包括光刻、刻蚀、镀膜等步骤,以及这些步骤对半导体性能 的影响。
掺杂与退火
讲解掺杂剂的种类和作用,以及掺杂工艺的基本步骤和退火工艺对半导体性能的影响。
制程环境与设备
制程环境
介绍半导体制造所需的环境条件 ,如洁净度、温度、湿度等,以 及这些环境因素对半导体性能的 影响。
03
常见的半导体材料有硅、锗、砷化03
半导体材料具有高纯度、低缺陷等 特性。
硅是最常用的半导体材料,具有资 源丰富、制备工艺成熟等优势。
锗是一种具有高迁移率的半导体材 料,适用于高速电子器件。
半导体产业概述
01
半导体产业包括半导体制造、半导体设备、半 导体材料等领域。
案例三:纳米半导体器件制程
总结词
纳米半导体器件制程是一种制造纳米级尺寸 的半导体器件的制程,具有高频率、低功耗 、小尺寸等特点。
详细描述
纳米半导体器件制程采用先进的纳米制造技 术,如纳米压印、电子束光刻等,将半导体 材料加工成纳米级别的器件。该制程在微电 子、光电子、生物医学等领域具有广泛的应 用前景。
5G和物联网的驱动
5G和物联网技术的发展将推动半导体产业持续增长,对低功耗、 高性能半导体的需求不断增加。
中国市场的崛起
中国半导体市场已成为全球最大的市场之一,政府支持力度大,产 业发展迅速,国际合作与竞争日益激烈。
国际合作与竞争
国际合作
随着半导体产业的发展,国际合作成 为提高技术水平和竞争力的重要手段 ,各国纷纷建立合作机制,加强技术 交流和联合研发。
详细描述
半导体技术可以用于开发太阳能、风能等新能源发电设备中的半导体器件,提高能源利用效率;同时 也可以用于环保领域的半导体传感器、气体检测器等设备的开发,实现环境污染的监测与治理。
半导体器件的加工和制备技术

半导体器件的加工和制备技术半导体器件是现代电子技术的核心组成部分,也是现代工业和信息化建设的基石之一。
人们熟悉的电脑、手机、平板等都离不开半导体器件的帮助。
本文将介绍半导体器件的加工和制备技术,以帮助读者更加深入地了解这一领域。
一、半导体半导体是介于导体和绝缘体之间的一类物质,其导电性介于导体和绝缘体之间。
半导体的导电性是通过控制其材料内部的杂质浓度和形成PN结等方式实现的。
因此,半导体器件的性能和特点都与其材料本身和制造工艺密切相关。
二、半导体加工技术1. 半导体晶片的制作半导体晶片制作的第一步是在硅晶圆上进行掩膜光刻。
在掩膜中预设芯片的结构图案,然后使用掩膜光刻机将这些结构刻在硅晶圆上。
随后,使用化学腐蚀或等离子体刻蚀机将掩膜刻蚀掉,即可得到芯片的初始形态。
接下来是掺杂,即在硅晶圆表面和内部注入少量惰性原子或掺杂原子,来改变晶圆的电学性质。
个别掺杂的原子数可以达到一个亿分之一。
掺杂后的芯片要进行多次清洗和高温烘干才能进行下一步操作。
2. 半导体器件的制作半导体晶片通过漏洞(Via)连接到导线,形成晶片内部电路。
漏洞的制作依靠与光刻机类似的掩膜光刻。
制作出的漏洞上覆盖有金属覆盖层,连接到先前预留的金属线上,形成电路。
金属导线的制作是通过先将金属层涂在整个晶圆表面上,然后利用光刻机进行掩膜光刻和腐蚀来制作的。
三、半导体制备技术1. 溅射沉积溅射沉积是一种化学气相沉积法,它将固体半导体材料置于靶面,利用高速惰性气体原子轰击靶面并溅射出材料,形成晶体沉积在衬底上。
该技术制备的薄膜薄、质量好、成本低。
2. 分子束外延分子束外延是一种常见的薄膜制备方法,在超高真空下通过半导体材料块分子束与衬底反应生成薄膜。
该技术制备出的薄膜有良好的结晶性和均匀性,晶粒大小也比较小。
3. 金属有机化学气相沉积金属有机化学气相沉积是一种以金属有机气体为原料的化学气相沉积法。
它利用金属有机气体在高温下分解,并与衬底表面材料反应来制备薄膜。
半导体制造技术导论

半导体制造技术导论
半导体制造技术是指利用诸如金属化学气相沉积技术、外延物理气相沉积技术、光刻技术、电抗沉积技术等复杂的生产工艺结构,以原材料(硅)作为基础,精细地编织出特定的晶体材料加工和芯片制造工艺的过程。
主要应用在半导体元件的制造和芯片封装等。
目前,半导体制造工艺结构分为三大部分:前处理、主处理和后处理。
前处理包括硅晶体生长、内层抗拉开口处理、外层处理、元件芯片封装、检测测试和组装。
主处理主要包括金属物理气相沉积、光刻、掩模、波峰焊、液相沉积和电抗沉积等。
后处理主要包括芯片封装、测试检测和组装工艺。
半导体制造技术是电子集成电路和电子元件的核心技术之一,它的成功主要取决于精细的工艺结构操作、严格的工艺控制,以及完整的质量控制体系,这些都是半导体制造技术取得成功的关键因素。
半导体工艺制造技术的原理与

半导体工艺制造技术的原理与应用半导体工艺制造技术的原理与应用半导体工艺制造技术是指将半导体材料加工成各种器件的技术过程。
随着科技的快速发展,半导体工艺制造技术在电子产业中发挥着重要的作用。
本文将介绍半导体工艺制造技术的原理和应用。
一、半导体工艺制造技术的原理半导体工艺制造技术的原理主要涉及到半导体材料的特性和制造工艺的基本原理。
1. 半导体材料的特性半导体材料具有介于导体和绝缘体之间的电导率。
这是由于半导体材料的能带结构决定的。
在半导体材料中,价带是最高的完全占据能级,而导带是最低的未占据能级。
两者之间的能量间隙称为禁带宽度。
半导体材料的导电性取决于禁带宽度的大小。
2. 制造工艺的基本原理半导体器件的制造过程主要包括沉积、光刻、蚀刻、扩散和离子注入等步骤。
(1)沉积:沉积是将材料沉积在基片上形成薄膜的过程。
常用的沉积方法有化学气相沉积(CVD)和物理气相沉积(PVD)等。
(2)光刻:光刻是通过光刻胶和光刻机将图案转移到基片上的过程。
光刻胶会在紫外线曝光后发生化学反应,形成图案。
(3)蚀刻:蚀刻是通过化学反应将不需要的材料从基片上去除的过程。
常用的蚀刻方法有湿蚀刻和干蚀刻等。
(4)扩散:扩散是将杂质掺入半导体材料中,改变材料的电性质的过程。
常用的扩散方法有固相扩散和液相扩散等。
(5)离子注入:离子注入是将离子注入到半导体材料中,形成特定的杂质区域的过程。
离子注入可以改变材料的电性能。
二、半导体工艺制造技术的应用半导体工艺制造技术在电子产业中有着广泛的应用,主要体现在以下几个方面:1. 集成电路制造集成电路是半导体工艺制造技术的重要应用领域之一。
通过将不同的电子器件集成在一个芯片上,实现了电子元件的微型化和高集成度。
集成电路制造技术的不断发展,使得计算机、手机、平板电脑等电子产品的性能和功能不断提升。
2. 太阳能电池制造太阳能电池是利用半导体材料的光电转换效应将太阳能转化为电能的装置。
半导体工艺制造技术在太阳能电池的制造过程中起到了至关重要的作用。
半导体制造工艺技术

半导体制造工艺技术半导体制造工艺技术是指用于生产半导体器件的工艺步骤和方法。
半导体器件是现代电子设备中最基本的组成部分,包括晶体管、集成电路等。
半导体制造工艺技术是将半导体材料加工成器件的关键环节,对于器件的性能和质量有着重要影响。
首先,半导体制造工艺技术的第一步是选择合适的半导体材料。
常用的半导体材料有硅、砷化镓等。
这些材料具有较好的导电性和半导性,能够在一定条件下控制电流的传导。
接下来,半导体制造工艺技术的第二步是进行材料清洁和去除氧化层。
在制造过程中,材料表面可能会附着一些杂质和氧化层,会影响器件的性能。
因此,将材料进行清洁和去除氧化层是非常重要的步骤。
第三步是进行材料的掺杂和扩散。
掺杂是向材料中加入一定浓度的所需的杂质元素,以改变材料的导电性。
扩散是使掺杂材料均匀分布在整个材料中,以获得稳定的性能。
第四步是进行光刻和蚀刻。
光刻是在材料表面涂覆光刻胶,通过光刻机械刻蚀模板上的图案,以形成器件的结构。
蚀刻是使用化学物质去除材料表面的不需要的部分。
第五步是进行金属沉积和金属化。
金属沉积是将金属材料沉积在材料表面,以与器件的其他部分连接。
金属化是利用蚀刻制造导线和联系器件。
第六步是进行热处理和包封。
热处理是使用高温处理器件,以提高其电学性能和结构稳定性。
包封是将器件用封装材料密封,以保护器件并提供连接接口。
最后,进行测试和质检。
测试是检验制造的器件是否符合要求。
质检是对制造过程中的每个步骤进行检查,以确保器件的质量和可靠性。
总的来说,半导体制造工艺技术是一项复杂而精密的工艺,需要严格控制每个步骤和参数,以确保制造出高性能、高质量的半导体器件。
随着科技的进步,半导体制造工艺技术也在不断创新和发展,为电子产业的发展提供了强有力的支持。
半导体制造工艺技术是一门关乎现代电子产业发展的重要技术,其应用范围广泛,涵盖了从传统的晶体管制造到先进的集成电路制造等多个领域。
随着电子产品的普及和需求的不断增长,半导体制造工艺技术也在不断发展和改进,以满足市场的需求。
半导体制造技术pdf

半导体制造技术pdf
半导体制造技术是制造电子器件或元件所需要的技术,几乎每一个电子器件或元件都需要这种技术。
半导体制造技术可以将纯净的原材料,如锗、硅、锡、铜等,经过复杂的制造过程而进行形成和凝结,形成适合的半导体晶体。
这种技术的重要性不言而喻,可以实现把集成电路上的小尺寸和薄型电子部件进行封装,以形成完整的集成电路。
根据不同的半导体制造技术,制造出来的半导体晶体具有不同的性能特点,如封装密度、功耗、电气特性等都可以由不同的制造技术而有所改变。
另外,由于每一种半导体制造技术自身都有其特定的材料要求,任何在制造过程中含锡、铜等金属元素的技术都需要特殊的条件,以便在不产生尘埃的环境中进行金属元素的过滤和偶合,以便最后形成完整的晶体,这也是一项复杂的技术。
总之,半导体制造技术是电子器件的基础,无论通用的集成电路还是特定的芯片以及其他晶体,都需要依据半导体制造技术进行制造,而它的正确使用及材料的挑选,对电子器件制造性能有着至关重要的影响。
polymide 半导体工艺制程简介
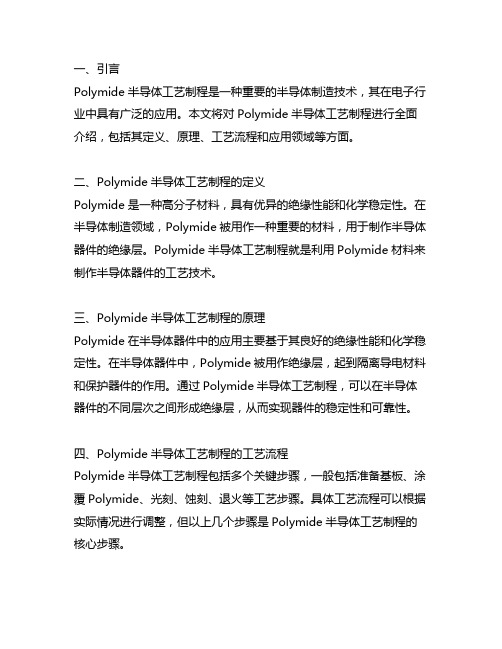
一、引言Polymide半导体工艺制程是一种重要的半导体制造技术,其在电子行业中具有广泛的应用。
本文将对Polymide半导体工艺制程进行全面介绍,包括其定义、原理、工艺流程和应用领域等方面。
二、Polymide半导体工艺制程的定义Polymide是一种高分子材料,具有优异的绝缘性能和化学稳定性。
在半导体制造领域,Polymide被用作一种重要的材料,用于制作半导体器件的绝缘层。
Polymide半导体工艺制程就是利用Polymide材料来制作半导体器件的工艺技术。
三、Polymide半导体工艺制程的原理Polymide在半导体器件中的应用主要基于其良好的绝缘性能和化学稳定性。
在半导体器件中,Polymide被用作绝缘层,起到隔离导电材料和保护器件的作用。
通过Polymide半导体工艺制程,可以在半导体器件的不同层次之间形成绝缘层,从而实现器件的稳定性和可靠性。
四、Polymide半导体工艺制程的工艺流程Polymide半导体工艺制程包括多个关键步骤,一般包括准备基板、涂覆Polymide、光刻、蚀刻、退火等工艺步骤。
具体工艺流程可以根据实际情况进行调整,但以上几个步骤是Polymide半导体工艺制程的核心步骤。
1. 准备基板:首先需要选择适合的半导体基板,通常是硅片或玻璃基板。
2. 涂覆Polymide:利用涂覆机将Polymide溶液均匀涂覆在基板表面,并经过烘烤使其形成均匀的绝缘层。
3. 光刻:利用光刻技术,在Polymide层上形成所需的图案。
4. 蚀刻:利用化学蚀刻或物理蚀刻技术,将Polymide层非光刻区域去除。
5. 退火:对蚀刻后的Polymide层进行退火处理,提高其物理性能和化学稳定性。
五、Polymide半导体工艺制程的应用领域Polymide半导体工艺制程在电子行业中具有广泛的应用,主要包括集成电路、传感器、显示器件等领域。
在集成电路制造中,Polymide被用作多层金属线路的绝缘层;在传感器制造中,Polymide被用作传感器的封装层;在显示器件制造中,Polymide被用作柔性显示器的基底材料。
半导体制造技术.pdf

半导体制造技术.pdf
《半导体制造技术》在半导体领域,技术的变化遵循着摩尔定律的快速节奏,是以月而不是以年为单位计的。
《半导体制造技术》详细追述了半导体发展的历史并吸收了当今最新技术资料,学术界和工业界都称赞这是一本目前在市场上能得到的最全面、最先进的教材。
全书共分20章,章节根据应用于半导体制造的主要技术分类来安排,内容包括:与半导体制作相关的基础技术信息;总体流程图的工艺模型概况,用流程图将硅片制造的主要领域连接起来;具本讲解每一个主要工艺;集成电路装配和封装的后部工艺概况。
此外,各章为读者提供了关于质量测量和故障排除的问题,这些都是会在硅片制造中遇到的实际问题。
半导体结构的制造方法
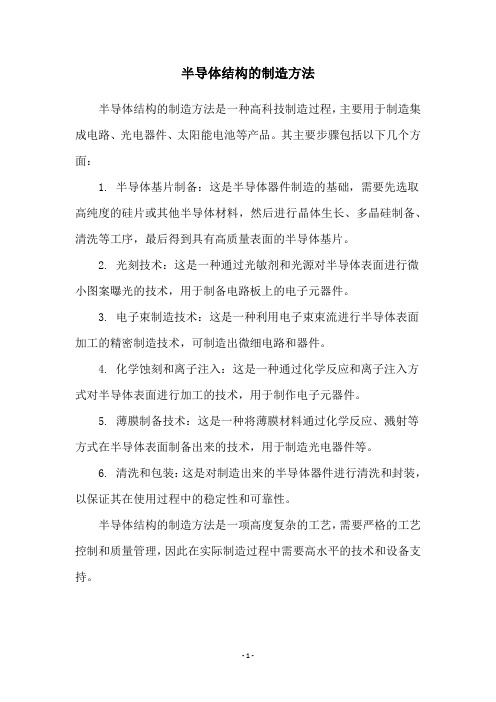
半导体结构的制造方法
半导体结构的制造方法是一种高科技制造过程,主要用于制造集成电路、光电器件、太阳能电池等产品。
其主要步骤包括以下几个方面:
1. 半导体基片制备:这是半导体器件制造的基础,需要先选取高纯度的硅片或其他半导体材料,然后进行晶体生长、多晶硅制备、清洗等工序,最后得到具有高质量表面的半导体基片。
2. 光刻技术:这是一种通过光敏剂和光源对半导体表面进行微小图案曝光的技术,用于制备电路板上的电子元器件。
3. 电子束制造技术:这是一种利用电子束束流进行半导体表面加工的精密制造技术,可制造出微细电路和器件。
4. 化学蚀刻和离子注入:这是一种通过化学反应和离子注入方式对半导体表面进行加工的技术,用于制作电子元器件。
5. 薄膜制备技术:这是一种将薄膜材料通过化学反应、溅射等方式在半导体表面制备出来的技术,用于制造光电器件等。
6. 清洗和包装:这是对制造出来的半导体器件进行清洗和封装,以保证其在使用过程中的稳定性和可靠性。
半导体结构的制造方法是一项高度复杂的工艺,需要严格的工艺控制和质量管理,因此在实际制造过程中需要高水平的技术和设备支持。
- 1 -。
- 1、下载文档前请自行甄别文档内容的完整性,平台不提供额外的编辑、内容补充、找答案等附加服务。
- 2、"仅部分预览"的文档,不可在线预览部分如存在完整性等问题,可反馈申请退款(可完整预览的文档不适用该条件!)。
- 3、如文档侵犯您的权益,请联系客服反馈,我们会尽快为您处理(人工客服工作时间:9:00-18:30)。
• 積體年代
– 從 SSI 晶片到 ULSI 晶片 – 1960 - 2000
8
第一個積體電路
(由TI之Jack所製造)
9
晶圓晶片的俯視圖
一個單一的積體 電路,如晶粒、 晶片和微晶片
圖 1.3
10
半導體積體電路
積體電路
沒有整合 (離散組成)
小尺寸整合 (SSI)
半導體工業的時間週期
1960年前
年
1970
1980
1990
2000
Redrawn from C. Chang & S. Sze, McGraw-Hill, ULSI Technology, (New York: McGraw-Hill, 1996), xxiii. 28 圖 1.15
電子發展的階段
1950年代: 1960年代: 1970年代: 1980年代: 1990年代: 電晶體技術 製造技術 競爭 自動化 大量生產
半导体制造技术简介
課程大綱
1. 敘述目前半導體工業的經濟規模與工業基 礎。 2. 說明IC結構,並且列出5個積體年代。 3. 討論晶圓及製造晶圓的5個主要階段。 4. 敘述與討論晶圓製造的改進技術之3項重要 趨勢。 5. 說 明 臨 界 尺 寸 ( CD) 的 定 義 , 同 時 討 論 Moore’s定律與未來晶圓發展的關係。 6. 從發明電晶體開始到現今晶圓製造,討論 電子工業的發展歷程。 7. 討論半導體工業中生涯發展的不同路線。
1960年早期
每個晶片組成數
1
25
中尺寸整合 (MSI)
大尺寸整合 (LSI) 非常大尺寸整合 (VLSI) 超大尺寸整合 (ULSI)
1960年到1970年早期
1970年早期到1970年晚期 1970年晚期到1980年晚期 1990年至今
50 5,000
5,000 100,000 100,000 1,000,000 >1,000,000
1997 0.25
1999 0.18
2001 0.15
2002 0.13
2005 0.10
表 1.2
22
晶片上電晶體數目之增加趨勢
1600
每 一 微 處 理 器 上 之 電 晶 體 數 目 ( 百 萬
1400
1200
1000 800 600 400 200
)
1997 1999 2001 2.11
24
早期與現在半導體尺寸的對照
1990年的微晶片 (5 25百萬個電晶體)
1960年的電晶體
US硬幣 (10分)
圖 1.12
25
10
每年呈現下滑現象的 IC功率消耗
8
平 均 功 率 w (106W)
6
4
2
0 1997 1999 2001 2003 2006 2009 2012
圖 1.16
30
半導體工業的生涯發展路線
工廠領導者 維修領導者 維修管理者 設備工程師 設備技術人員 維修技術人員 製造技術人員 生產領導者 生產管理者 工程師領導者 製程工程師 整合工程師 良率&錯誤分析技術人員 製程技術人員 研究技術人員 MS BS BEST* AS+ AS
晶製程造技術人員 生產者
產品應用
消費者: 電腦 汽車 航空和宇宙航行空間 醫學的 其他工業 顧客服務 原始的設備製程 印刷電路板工業
晶片製造者
圖 1.1
5
第一個電晶體
(由Bell Labs研究製造)
圖 1.3
6
第一平面式電晶體
圖 1.2
7
積體電路
• 積體電路 (IC)
– 微晶片, 晶片 – 發明者 – 積體電路的好處
1976
1980
1984
1988
1992
1996
2000
年
圖 1.14
27
半導體晶片價錢每年降低
104
真空管
標準管 縮小管 BIT
半導體元件
元件尺寸 = 價錢 =
102
1
積體電路
MSI LSI VLSI
比 較 值
10-2 10-4 10-6
ULSI
10-8
10-10 1930
1940
1950
1960
沿切刻線切 割 晶 圓 , 以 單一晶粒 分隔每個晶 粒。
切刻線
2. 晶圓製造
包括清洗、 加層、圖案 化、蝕刻、
摻雜。
晶粒黏著於 封裝體內, 並進行金屬 打線。 缺陷晶粒
裝配
封裝
3. 測試/分類
包括探針、 測試、分類 晶圓上的每 個晶粒。
5. 最後測試
確定IC通過 電子和環境 測試。
16
矽晶片的製備
13
晶片尺寸的發展
2000
1992 1987
1981
1975
1965
50 mm
100 mm
125 mm
150 mm
200 mm
300 mm
圖 1.4
14
矽晶片的元件和膜層
圖 1.5
15
IC 製造的主要階段
1. 晶圓準備
包括結晶、 長晶、圓柱 化、切片和 研磨。 單晶矽 矽棒切片
4. 裝配和封裝
2012
年
Redrawn from Semiconductor Industry Association, The National Technology Roadmap for Semiconductors, 1997.
圖 1.10
23
微處理器之發展與Moore’s定 律之關係
100M
500
Pentium Pentium Pro
多晶矽
晶種結晶
1.長晶
坩鍋 加熱
6. 邊角磨光
7. 研磨 2.單晶錠
8. 晶圓蝕刻 3.端點移除和 直徑研磨 9. 拋光
4.主平面形成
研磨台 研漿 研磨頭
5.晶圓切片
圖 1.7
10. 晶圓檢視
(注意:圖1.7的名詞於第4章解釋。)
17
晶圓廠
Photo courtesy of Advanced Micro Devices-Dresden, © S. Doering
29
晶片費用每年持續增加
$100,000,000,000
實際費用 預測費用
$10,000,000,000
成 本
$1,000,000,000
$100,000,000
$10,000,000
1970
1980
1990
2000
2010
2020
年
Used with permission from Proceedings of IEEE, January, 1998 © 1998 IEEE
年
Redrawn from Semiconductor Industry Association, National Technology Roadmap, 1997
圖 1.13
26
晶片可靠度的增進
700
長 期 每 百 萬 部 分 故 障 率 目 標 (PPM)
600
500
400
300
200 100 0 1972
18
微晶片封裝
圖 1.8
19
半導體趨勢
• 增加晶片特性
– – – – 臨界尺寸 (CD) 每一晶片上的組件數目 Moore’s 定律 功率消耗
• 增加晶片的可靠度 • 降低晶片價錢
20
臨界尺寸
圖 1.9
21
對於臨尺寸過去和未來技術點 的比較
1988 CD ( m) 1.0
1992 0.5
1995 0.35
2
微處理晶片
微處理機晶片 (Photo courtesy of Advanced Micro Devices)
微處理機晶片 (Photo courtesy of Intel Corporation)
3
真空管
4
半導體工業
基本設施
工業協會 (SIA, SEMI, NIST, etc.) 生產工具 實用品 材料 & 化學 度量衡學工具 分析研究所 技術能力 學院 & 大學
晶片移動
晶片出廠
1 2 3 4 5 6 7 8 9 10 11 12 13 14 15 16 17 18 19 20 21 22 23 24 25 26 27 28 29
製程 設備 蝕刻
檢查
製程 設備 薄膜
檢查
製程 設備
檢查 金屬化
30 31
工作時間=開始工作之時間-工作結束之時間 晶圓產量=啟始晶圓數量-出廠晶圓數量 操作員工作效率=理想的工作時間/實際工作時間
10M
電 1M 晶 體
100K
8086 80286
80486
25
80386
10K
8080 4004
每 秒 百 1.0 萬 條 指 令
.1
1975
1980
1985
1990
1995
.01 2000
年
Used with permission from Proceedings of the IEEE, January, 1998, © 1998 IEEE
*Bachelor of Science在電 子的技術
HS+
HS 教育
圖 1.17
31
晶圓廠的產量測量
微處理 光罩
12
離子植入 廢棄 檢查
時間到
擴散 製程 設備
重作
3
9
6
製程設備