HISMELT熔融还原炼铁工艺节能减排分析
hismelt工艺技术

hismelt工艺技术Hismelt工艺技术700字Hismelt工艺技术是一种革命性的铁矿石还原方法,通过该技术,铁矿石可以高效、低成本地还原成金属铁。
Hismelt工艺技术是由澳大利亚的首钢集团与科学家共同研发的一种新型冶金技术,它具有许多优点和创新之处。
首先,Hismelt工艺技术能够高效地还原铁矿石。
该技术使用高温和高速的氧化剂,将铁矿石与煤粉等还原剂快速混合燃烧,产生高温的还原气体,将铁矿石中的氧气去除,从而还原出金属铁。
相比传统的高炉冶炼方法,Hismelt工艺技术具有更高的还原效率,能够将更多的金属铁从铁矿石中提取出来。
其次,Hismelt工艺技术具有较低的成本。
传统的高炉冶炼需要大量的焦炭作为还原剂,而焦炭价格较高,成为高炉冶炼的一大成本。
然而,Hismelt工艺技术可以使用便宜的煤粉作为还原剂,大大降低了生产成本。
此外,Hismelt工艺技术的能源利用率也较高,通过燃烧的方式将废气中的热能回收利用,进一步降低了能源消耗和成本。
再次,Hismelt工艺技术具有较低的环境污染。
传统的高炉冶炼方法排放大量的二氧化碳和有害气体,并产生大量的工业废渣和铁水尾矿,对环境造成了严重的污染。
然而,Hismelt工艺技术采用了封闭式炉膛设计,能够有效控制废气和有害物质的排放。
此外,Hismelt工艺技术还可以利用高温废气来发电,进一步减少了对环境的负面影响。
最后,Hismelt工艺技术具有灵活性和可持续性。
该技术可以适应不同种类和质量的铁矿石,无论是高磷、低硫还是含有其他杂质的铁矿石,都可以通过调整工艺参数进行冶炼。
此外,Hismelt工艺技术还可以与其他冶金工艺相结合,实现资源综合利用,进一步提高资源利用效率和生产效益。
总之,Hismelt工艺技术是一种具有许多优点和创新之处的冶金技术。
它高效、低成本地还原铁矿石,具有较低的环境污染,灵活可持续。
Hismelt工艺技术的应用将为铁矿石冶炼行业带来革命性的变革,提高生产效率、降低成本、减少环境污染,推动铁矿石冶炼行业的可持续发展。
墨龙海斯梅特(HIsmelt)工艺简介

墨龙海斯梅特(HIsmelt)工艺简介HIsmelt工艺作为一种矿粉直接熔融还原的短流程冶金工艺,一直吸引着世界各国冶金企业和科研院所的广泛关注,2012年经山东墨龙升级改造并率先在全球实现连续商业化运行。
该工艺开发的初衷是实现铁矿开采中占比日益增多的粉矿资源和储量丰富的高磷矿资源的综合开发利用,经过三十多年的理论研究和半工业化中试试验,工艺技术逐步成熟,其独特的工艺条件不仅适用于普通铁矿的直接冶炼,对于传统高炉工艺过程难以有效利用的高磷矿、钒钛磁铁矿以及冶金固废综合利用具有优异的工艺条件,是解决现有冶金过程中环境污染大、优质矿石资源和焦煤资源短缺等问题的冶金前沿技术。
一、山东墨龙HIsmelt概述HIsmelt熔融还原炼铁工艺直接使用普通铁矿粉和其他含铁物料,喷吹煤粉作为系统的还原剂及热量来源,与传统高炉工艺相比省去烧结厂、球团和焦化等污染严重的铁前工序,在同等产能条件下节省了大量的投资及运行成本,极大降低了污染物的排放,充分利用生产中的余热和煤气资源,提高能源利用效率。
1.1 生产环保,污染物排放少海斯梅特(HIsmelt)技术彻底摒弃了传统高炉工艺流程中的焦化、烧结和球团工序作为全新的短流程冶金新技术,相比于传统高炉工艺,海斯梅特(HIsmelt)技术工艺流程中颗粒物排放低于超低排放标准70%、SO2排放低于超低排放标准50%、NOx排放低于超低排放标准90%,有效遏制二恶英、焦油和酚等污染物的产生,体现了清洁生产的节能环保理念。
1.2 工艺流程短,占地少、投资低海斯梅特(HIsmelt)技术缩短了钢铁生产流程,山东墨龙海斯梅特(HIsmelt)工厂仅占地260亩;自动化程度高,山东墨龙海斯梅特(HIsmelt)工厂工作人员定编280人;不需要焦化厂、烧结厂或球团厂,降低总投资成本,80万吨HIsmelt项目总投资为8亿元,占可比1080m3高炉总投资73%。
二、山东墨龙HIsmelt技术特征HIsmelt工艺是典型的“一步法”熔融还原工艺,直接利用粉状含铁物料和煤粉进行铁浴熔融还原冶金,具有完全喷吹、炉内涌泉及虹吸出铁三大典型技术特征。
2024年炼铁工业节能减排市场调研报告
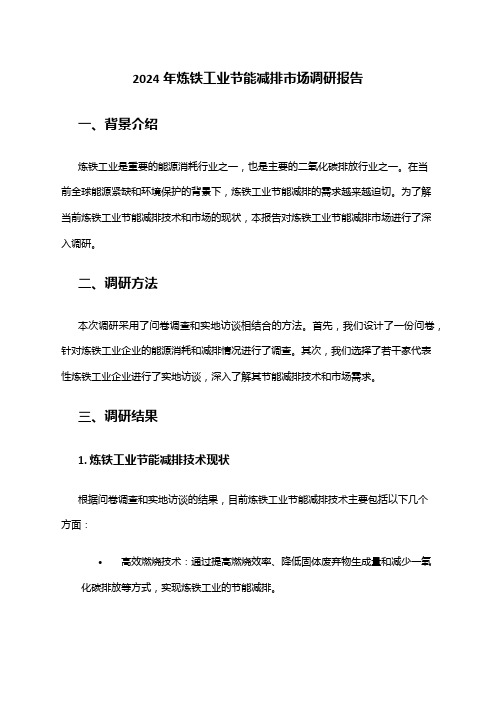
2024年炼铁工业节能减排市场调研报告一、背景介绍炼铁工业是重要的能源消耗行业之一,也是主要的二氧化碳排放行业之一。
在当前全球能源紧缺和环境保护的背景下,炼铁工业节能减排的需求越来越迫切。
为了解当前炼铁工业节能减排技术和市场的现状,本报告对炼铁工业节能减排市场进行了深入调研。
二、调研方法本次调研采用了问卷调查和实地访谈相结合的方法。
首先,我们设计了一份问卷,针对炼铁工业企业的能源消耗和减排情况进行了调查。
其次,我们选择了若干家代表性炼铁工业企业进行了实地访谈,深入了解其节能减排技术和市场需求。
三、调研结果1. 炼铁工业节能减排技术现状根据问卷调查和实地访谈的结果,目前炼铁工业节能减排技术主要包括以下几个方面:•高效燃烧技术:通过提高燃烧效率、降低固体废弃物生成量和减少一氧化碳排放等方式,实现炼铁工业的节能减排。
•废热利用技术:利用高温炉排废气中的废热,进行余热发电或为其他工艺提供热能,显著降低能源消耗。
•原料优化技术:通过优化原料配比和选择高品质原料,降低炼铁过程中的能耗和二氧化碳排放。
•高效烧结技术:采用先进的烧结设备和工艺,提高烧结矿的质量和产量,减少矿石的能源消耗和二氧化碳排放。
2. 炼铁工业节能减排市场现状调研结果显示,当前炼铁工业节能减排市场存在以下几个特点:•市场需求旺盛:受到能源紧缺和环境保护政策的推动,炼铁工业节能减排技术得到了广泛应用和推广,市场需求呈现快速增长的态势。
•技术创新驱动:随着科技的进步和意识的提高,炼铁工业节能减排技术不断创新,出现了一批高效、环保的新技术和设备,受到市场的热捧。
•市场竞争激烈:随着市场需求的增加,炼铁工业节能减排市场竞争日益激烈。
企业需要不断提高技术水平和降低成本,以赢得市场份额。
四、市场前景与建议炼铁工业节能减排市场具有良好的发展前景,但也面临着一些挑战。
为了进一步推动炼铁工业节能减排的发展,我们提出以下建议:•加强技术研发:鼓励企业加大炼铁工业节能减排技术的研发力度,提高技术水平和降低成本,推动技术创新和市场竞争力的提升。
HIsmelt熔融还原技术剖析

be needed.
更大的原料灵活性Great flexibility in raw material:
HIsmelt技术可直接喷吹传统高炉烧结厂不宜使用的低品位铁矿粉。 HIsmelt can use low grade iron ore fines which otherwise can not be used by the blast furnace sinter plant.
国内某公司自2004年以来一直致力于新炼铁工艺、技术、装备的研究,在2012年决定利用部分HIsmelt奎那那工
厂设备,并通过进一步优化工艺流程,建设新的HIsmelt熔融还原炼铁生产厂。 A Chinese company , who has been focusing on the research of innovative iron-making technology, process and equipment, decided to build a elt plant in China. This plant uses some of the Kwinana equipment, but also makes some modification by optimizing the existing process.
3 生产情况介绍 Production Experience
3.1 奎纳纳情况概览 Kwinana summary 从2005年11月开始了为期3年的达产运行:2006年底实现50%,2007 年实现80%,2008年实现85% three year ramp-up period beginning in November 2005: 50% by 2006, 80% by 2007, 85% by 2008 期间主要问题大多由外围设备引起,在这些问题得以解决后生产率逐步 上升。 Major problems caused by ancillary equipment and production rate continued to rise as bottlenecks removed 2008年12月,由于经济危机影响,生铁市场低迷,工厂因此关闭。 Plant put under care and maintenance and then closed due to sluggish market demand caused by global economic crisis from end of 2008
Hismelt法是一种生产高质量生铁的革命性工艺

Hismelt法是一种生产高质量生铁的革命性工艺。
基本上,它是一种避免烧结并产生较低二氧化碳排放的简化工艺。
其他潜在好处包括更低的运营成本、更低的资本成本及原材料及运营方面的更大灵活性。
这是一个以提供可持续性为目标的研究及开发的明显例证。
1982 - 1984∙Hismelt工艺最早可以追溯到最初由德国Klöckner Werke 公司在其Maxhütte工厂开发的底吹氧气转炉工艺(OBM)和随后不断发展的顶低复合吹炼工艺。
∙1981年,CRA公司(现为Rio Tinto力拓集团)认识到利用Klöckner的转炉技术冶炼铁矿石,而不是废钢,这一技术的潜力。
CRA公司与Klöckner Werke公司组成了合资公司,共同开发炼钢和熔融还原技术。
使用60吨的OBM 转炉所进行的测试证明了熔融还原工艺的基本原理1984-1990∙熔融还原工艺概念测试成功后(采用60吨炼钢转炉),在德国南部的Maxhütte钢厂建设了一座小型试验工厂(SSPP)。
该厂设计能力年产10-12,000吨,采用卧式,可旋转的还原炉形式(SRV)。
煤,溶剂和铁矿石通过炉底喷枪喷入炉内。
∙SSPP工厂的试验生产从1984年到1990年,期间证明了技术的可行性。
然而,生产规模能否扩大仍然是个疑问。
∙在此期间,合作方出现了几次变化。
1987年,Klöckner公司撤出了该项目,两年后CRA公司与Midrex 公司按照50:50的比例组成了合资公司,继续共同开发该技术。
∙试验工厂成功后,决定有必要对该公司在更大的生产规模上进行测试。
∙工艺开发的下一步则是位于西澳大利亚奎那那地区HIsmelt研发工厂设施(HRDF)的建设1991∙1991年,年产10万吨的HIsmelt研发工厂设施在奎那那建成。
∙建设HRDF研发工厂设施的目的是进一步证明核心工厂的规模加大后从工艺和设计角度的可行性,同时为最终的商业化提供操作数据。
Hlsmelt熔融还原炼铁工艺

非高炉炼铁工艺—Hlsmelt熔融复原炼铁工艺由澳大利亚的力拓矿业企业开发的 HIsmelt 熔融复原炼铁工艺,采用了铁矿粉及钢厂废料和非炼焦煤直接熔融的复原技术生产高质量的铁产品,可直接用于炼钢或铸成生铁。
还能够够循环使用热能,以到达降低本钱和减少污染的目的。
从不断优化高炉炼铁和开发新式非高炉炼铁工艺考虑,可对炼铁生产实现节能减排和保护环境起到积极的作用。
HIsmelt 熔融复原炼铁工艺作为适应钢铁工业睁开的需要而开发的熔融复原炼铁的生产工艺,可为炼铁生产供给了一种新的选择。
钢铁生产工艺包括传统的高炉—氧气顶吹转炉的长流程和基于电弧炉的短流程。
近来几年来,受环保等方面因素的影响,短流程工艺碰到越来越多的关注。
1996 年以来,世界范围内有大量短流程优异扁平材生产厂投产。
这些短流程钢厂仅担当较低的折旧花销,还能够利用废钢来减少生产本钱。
因此,短流程钢厂的热轧生产本钱要比钢铁结合企业的低。
推动这种趋势睁开的主要原因有以下几个方面:高炉生产对原料的规格要求较严格,原料预加工〔焦化、球团和烧结厂〕使高炉生产成为环境污染的主要排放源,新建或改造高炉的投资额巨大,世界范围内的焦炉宽泛呈老化状态,也需要大量投资。
正常情况下,为了获得规模经济效益,钢铁结合企业的建筑规模都很大,因此,温室气体排放和环境污染的问题比较严重。
电炉炼钢厂的情况那么有所不相同,与钢铁结合企业对照,其竞争力相对较强。
对于电炉炼钢厂来说,优异、坚固的铁供给可明显提高电炉炼钢的生产率,降低生产本钱。
因此,在炉料中搭配铁水就拥有较高的利用价值。
在此条件下,开发拥有能源利用率高、原料及炉料适应性强、投资成本低、操作灵便等特点的炼铁工艺,已成为钢铁结合企业关注的课题之一。
1 Hlsmelt工艺流程简介图 1 为 HIsmelt 熔融复原炼铁的工艺流程图。
图 1HIsmelt熔融复原炼铁的工艺流程图第一, HIsmelt 工艺将金属熔池作为根本的反响媒介,炉料直接注入到金属中,熔炼过程主要经过熔解碳进行。
炼铁生产中的能耗优化与节能减排措施

炼铁生产中的能耗优化与节能减排措施能源是现代社会发展的基石,然而在能源有限的情况下,如何优化炼铁生产中的能耗,实现节能减排已经成为了一个迫切的问题。
本文将探讨炼铁生产中的能耗优化与节能减排措施,并提出具体的解决方案。
一、炼铁生产中的能耗现状炼铁生产是消耗能源的重要行业之一,其能耗情况直接关系到国家能源安全和环境保护。
然而,目前我国炼铁企业的能耗水平普遍较高,存在一系列问题。
首先,传统的高炉炼铁工艺存在能源利用率低的问题。
其次,炼铁生产中的废气、废水和废渣等排放物对环境造成了严重的污染。
因此,亟需采取有效的节能减排措施,优化能源利用,降低能耗水平。
二、能耗优化措施1. 提高高炉燃烧效率高炉是炼铁生产的核心设备,提高高炉燃烧效率是降低能耗的关键一步。
可以通过优化燃烧参数、改善高炉炉况、提高燃烧设备的热效率等方式来提高高炉的燃烧效率。
2. 采用先进的炼铁技术传统的高炉炼铁工艺存在能源损失较大的问题,可以考虑采用先进的炼铁技术来降低能耗。
比如,采用高炉煤气发电技术、煤气制氢技术等可以实现能源的全面利用。
3. 引进节能设备与技术在炼铁生产过程中,引进先进的节能设备与技术是降低能耗的重要手段。
比如,可以引进高效节能的燃烧设备、烟气余热回收技术、废气处理设备等来提高能源利用效率。
三、节能减排措施1. 废气治理高炉炼铁过程中产生大量的废气,其中含有大量的烟尘和有害气体。
应建立完善的废气治理系统,采用高效的除尘设备和废气脱硫、脱硝技术,减少废气的排放,降低对环境的影响。
2. 废水处理炼铁生产中的废水含有较高的悬浮固体和重金属等有害物质,对水环境造成较大污染。
应采用生物法、化学法等多种处理技术对废水进行处理,确保排放水质符合相关标准。
3. 废渣综合利用炼铁过程中产生的废渣具有一定的资源价值,应加强废渣的综合利用。
比如,可以将废渣进行回收再利用,用于生产水泥、建材等,减少对自然资源的占用。
四、结语炼铁生产中的能耗优化与节能减排是实现可持续发展的关键之一。
优化炼铁工艺的节能减排措施

优化炼铁工艺的节能减排措施摘要:现当今,全球变暖、大气污染及土壤污染等环境问题日益突出,而钢铁冶炼行业作为传统的高能耗、重污染型产业也受到越来越多的关注,如何降低炼铁中的能源消耗与碳排放成为当前热门课题。
基于当前高炉炼铁的产业现状,指出面对节能减排目标实现过程中高炉炼铁工艺所存在的困境,提出面向高炉炼铁工艺的节能减排优化策略,并提出未来应从技术与管理等维度进行强化,以实现传统高炉炼铁工艺向绿色、节能、高效的现代化高炉炼铁工艺转型。
关键词:炼铁工艺;节能减排;措施引言工业领域的高速发展,全球污染严重,我国政府认识到环境污染的严重性,着手整治环境污染问题,而在现今能源紧张的局面下,节能减排的一系列政策实行,钢铁行业整治是重点方面之一,为降低能源消耗,减少污染的排放,我国钢铁企业需积极应用、开发节能减排技术。
1我国高炉炼铁产业的发展困境1.1有限的资源与严苛的环境排放标准工业的快速发展推动着社会的发展与生产力的进步,但是现代工业自产生之日开始一直处于一种粗犷式的发展模式之中,既没有制定严格的工业排放标准,也没有充分关注工业生产过程中的能耗控制,进而造成了严重的环境污染问题与资源过度开采与消耗问题。
最近几年,社会各界对环保问题的重视程度逐渐提高,钢铁冶炼产业作为传统的重工业自然受到了更多的关注,近期颁布的环境法也都对钢铁冶炼产业的污染物排放作出了更加严格的限制。
同时,许多化石能源经过长期的开采后,储量紧张且开采成本大幅上涨,如何降低高炉炼铁工艺中产出单位质量生铁所需的焦炭、铁矿石以及熔剂等原材料的使用量成为提高高炉炼铁工艺经济效益的一大壁垒。
1.2产业转型压力巨大钢铁是工业发展与社会基础建设的重要原材料,政府与大型钢铁企业一直将提高高炉炼铁的产能作为一项重要的任务,我国也成为了名副其实的钢铁大国。
但是,长期以来高炉炼铁工艺终端产出的生铁都属于中下品相,不符合制造高强度、高等级钢材的条件,因而高炉炼铁的产业附加值也较低。
HIsmelt炼铁工艺发展状况及前景展望

HIsmelt炼铁工艺发展状况及前景展望发布时间:2021-07-28T10:29:48.980Z 来源:《中国科技信息》2021年9月上作者:曹凯琪陈龙陈子波[导读] 本文从我国日益严格的环保政策以及双碳战略的提出角度出发,介绍了HIsmelt工艺相对于传统高炉炼铁的优势,分析了该工艺的现实性以及经济性。
华北理工大学冶金与能源学院曹凯琪陈龙陈子波唐山 063200摘要:本文从我国日益严格的环保政策以及双碳战略的提出角度出发,介绍了HIsmelt工艺相对于传统高炉炼铁的优势,分析了该工艺的现实性以及经济性。
HIsmelt工艺发展历程以及工艺流程,分析了HIsmelt工艺特点,以及该工艺未来研究方向及发展方向。
关键词:HIsmelt 熔融还原前景展望随着我国钢铁行业的快速发展,2020年我国粗钢产量已超过10亿吨,但是由于铁矿石以及焦炭价格的增长,高炉炼铁成本也越来越高,另外,随着我国双碳战略的提出,炼铁行业面临着资源、能源,尤其是环保方面前所未有的压力。
传统高炉炼铁工艺虽然已经发展成熟,具有高效率、低成本等优势,但是由于其工艺特点,无法摆脱产生大量的环境污染的焦化厂、烧结厂和球团厂的依赖,已不能满足钢铁工业未来的发展要求[1]。
因此,无需建设焦化、烧结、球团、高炉工序,在理论上可以实现无焦炼铁的HIsmelt工艺受到科研工作者的关注[2]。
一方面,HIsmelt熔融还原技术可以使用高磷铁矿石,与传统高炉冶炼技术可以形成互补,降低生产成本。
另外,基于HIsmelt技术自身的优势,能够降低高炉生成过程中产生的环境污染,满足日益严格的环保政策以及我们国家提出的双碳战略,是非常有前景的非高炉炼铁工艺之一。
1. HIsmelt 工艺发展历程HIsmelt熔融还原炼铁工艺最早由德国Klockner公司以及澳大利亚CRA公司在20世纪80年代提出,目的是结合顶底复吹工艺,直接使用铁矿石和煤粉冶炼高质量铁水,在半工业试验中获得验证。
HIsmelt熔融还原高磷铁矿铁水含碳量影响因素研究
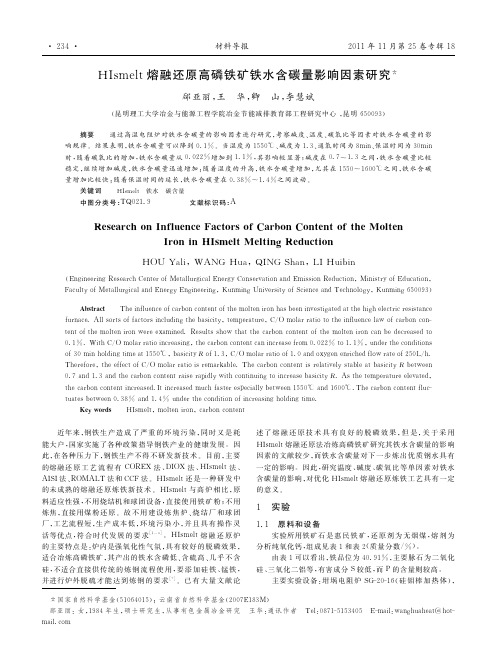
Key words HIsmelt,molten iron,carbon content
近年来,钢铁 生 产 造 成 了 严 重 的 环 境 污 染,同 时 又 是 耗 能大户,国家实施了各种政策指导钢铁产 业 的 健 康 发 展。因 此,在各种压力下,钢铁生产不得不 研 发 新 技 术。目 前,主 要 的熔融还 原 工 艺 流 程 有 COREX 法、DIOX 法、HIsmelt法、 AISI法、ROMALT 法和 CCF 法。HIsmelt还是 一 种 研 发 中 的未成熟的熔融还 原 炼 铁 新 技 术。HIsmelt与 高 炉 相 比,原 料适应性强,不用烧结机和球团设 备,直接 使 用 铁 矿 粉;不 用 炼焦,直接用煤粉 还 原。 故 不 用 建 设 炼 焦 炉、烧 结 厂 和 球 团 厂,工艺流程短,生 产 成 本 低,环 境 污 染 小,并 且 具 有 操 作 灵 活等优点,符 合 时 代 发 展 的 要 求 。 [1-6] HIsmelt熔 融 还 原 炉 的主要特点是:炉内是强氧化性气氛,具有 较 好 的 脱 磷 效 果, 适合冶炼高磷铁矿,其产出的铁水含磷低、含 硫 高、几 乎 不 含 硅,不适合直接供 传 统 的 炼 钢 流 程 使 用,要 添 加 硅 铁、锰 铁, 并进行炉外脱 硫 才 能 达 到 炼 钢 的 要 求 。 [7] 已 有 大 量 文 献 论
熔融还原炼铁技术发展情况和未来的思考

熔融还原炼铁技术发展情况和未来的思考近年来随着全球能源市场的变化和环保意识的增强,⾮⾼炉炼铁技术作为⼀种清洁、节能、降耗的新技术、新⼯艺,越来越受到业界⼈⼠的⾼度关注。
如果在该技术上实现突破,可能会推动钢铁⽣产⼯艺的颠覆性变化。
⽽在这些前沿技术中,熔融还原技术(COREX、FINEX)是⽬前⾮⾼炉炼铁技术中⼯业化应⽤较为成熟的⼯艺。
其中,宝钢集团为了掌握钢铁新⼯艺的前沿技术、加速中国炼铁技术的进步,于2007年和2011年引进两套 COREX 炼铁装置并相继投产,在罗泾中厚板分公司运⾏了4年;同时结合新疆地区资源禀赋,成功搬迁COREX-3000⾄⼋钢并顺利投产,并结合当地资源情况,较好地发展了具有⼋钢特⾊的熔融还原技术。
总体来看,经过宝钢这些年的不断摸索和⽣产实践,基本实现了引进技术、掌握技术、消化技术的⽬的,也为结合不同区域的资源禀赋条件来发展⾮⾼炉炼铁技术做出了积极探索。
本⽂结合国际上和宝钢⾃⾝在熔融还原炉⽅⾯⼀些积极探索和经验总结,提出未来发展熔融还原炼铁技术需要关注和思考的地⽅。
1 全球主要⾮⾼炉炼铁技术使⽤情况和特点1.1 全球主要⾮⾼炉炼铁技术情况为了解决焦煤资源短缺、焦煤价格居⾼不下的影响,并满⾜⽇益提⾼的环境保护要求、降低钢铁⽣产流程中的能耗和污染,全球炼铁⼯作者积极开发了多种⾮⾼炉炼铁技术,这些不同的⼯艺和技术流派近年均取得了较⼤进展,已经成为钢铁⼯业可持续发展、实现节能减排、环境友好发展的前沿技术。
⾮⾼炉炼铁技术从⼤的⼯艺路线来区分,可以分为直接还原技术(⽓基、煤基)、熔融还原技术(COREX、FINEX、Hismelt)两个主要类型。
直接还原炼铁⼯艺主要产品是固态海绵铁,供电炉炼钢⽤。
按还原剂的类型分,有⽓基和煤基直接还原两⼤类;按反应器的类型,分为竖炉法、流化床法、回转窑法、转底炉法以及罐式法等。
直接还原的优点是流程短,没有焦炉,污染较少;缺点是对原料要求严,要⽤⾼品位的铁矿,⽓基必须要有廉价、丰富的天然⽓,回转窑要⽤灰熔点⾼、反应性好的煤。
金属冶炼工艺的节能与减排技术
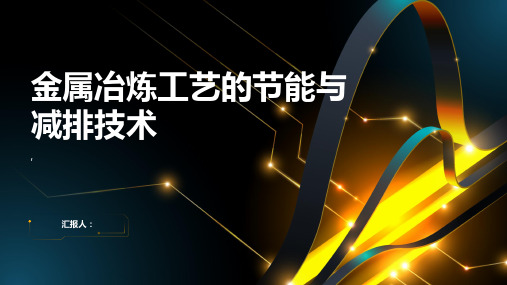
Part Four
金属冶炼工艺的减 排技术
减排技术原理
减排技术分类:根 据金属冶炼工艺的 不同阶段,可分为 燃烧前、燃烧中和 燃烧后减排技术。
燃烧前减排技术原 理:通过优化原料 配比、使用低硫燃 料等手段降低污染 物排放。
燃烧中减排技术原 理:采用低氮燃烧 器、燃烧控制等技 术降低燃烧过程中 的氮氧化物排放。
金属冶炼工艺的节能与 减排技术
,
汇报人:
目录
01 添 加 目 录 项 标 题 03 金 属 冶 炼 工 艺 的 节 能 技 术
02 金 属 冶 炼 工 艺 的 能 耗 与 排 放问题
04 金 属 冶 炼 工 艺 的 减 排 技 术
05 金 属 冶 炼 工 艺 的 节 能 与 减 排技术发展前景
07 金 属 冶 炼 工 艺 的 节 能 与 减 排 技术的政策支持与法规要求
金属冶炼工艺的排放问题
排放物种类:废气、废水、固体废弃物等
排放物危害:空气污染、水污染、土壤污染等 排放量大的原因:冶炼过程中需要大量能源和原材料,且技术水平有待 提高 减排措施:采用节能技术、提高资源利用率、加强废弃物处理和回收等
能耗与排放对环境的影响
金属冶炼工艺 能耗高,排放 大量废气、废 水和固体废弃 物,对环境造 成严重污染。
Part Five
金属冶炼工艺的节 能与减排技术发展
前景
技术发展趋势
高效节能技术:提高能源利用 效率,降低能耗
环保减排技术:减少污染物排 放,实现清洁生产
循环利用技术:实现资源循环 利用,减少废弃物产生
智能化技术:提高生产自动化 水平,优化工艺控制
技术发展面临的挑战
能源消耗大:金属冶炼工艺需要大量的能 源,如何降低能源消耗是技术发展的一大 挑战。
HIsmelt熔融还原工艺中的烟道式余热锅炉设计特点
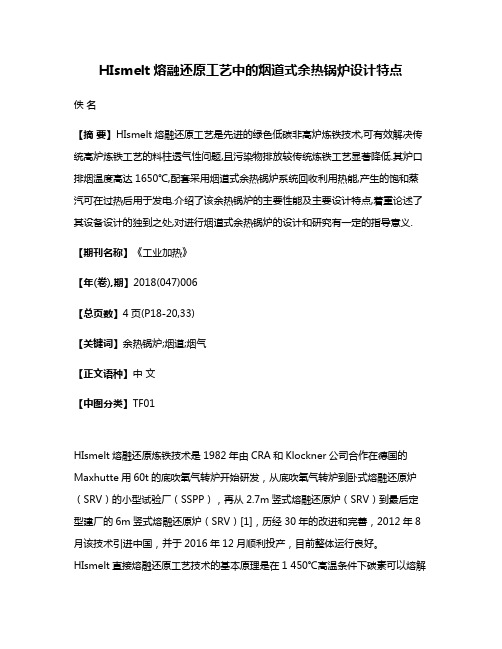
HIsmelt熔融还原工艺中的烟道式余热锅炉设计特点佚名【摘要】HIsmelt熔融还原工艺是先进的绿色低碳非高炉炼铁技术,可有效解决传统高炉炼铁工艺的料柱透气性问题,且污染物排放较传统炼铁工艺显著降低.其炉口排烟温度高达1650℃,配套采用烟道式余热锅炉系统回收利用热能,产生的饱和蒸汽可在过热后用于发电.介绍了该余热锅炉的主要性能及主要设计特点,着重论述了其设备设计的独到之处,对进行烟道式余热锅炉的设计和研究有一定的指导意义.【期刊名称】《工业加热》【年(卷),期】2018(047)006【总页数】4页(P18-20,33)【关键词】余热锅炉;烟道;烟气【正文语种】中文【中图分类】TF01HIsmelt熔融还原炼铁技术是1982年由CRA和Klockner公司合作在德国的Maxhutte用60t的底吹氧气转炉开始研发,从底吹氧气转炉到卧式熔融还原炉(SRV)的小型试验厂(SSPP),再从2.7m竖式熔融还原炉(SRV)到最后定型建厂的6m竖式熔融还原炉(SRV)[1],历经30年的改进和完善,2012年8月该技术引进中国,并于2016年12月顺利投产,目前整体运行良好。
HIsmelt直接熔融还原工艺技术的基本原理是在1 450℃高温条件下碳素可以熔解在铁液中,而熔解在铁液中的碳素又能同炽热铁氧化物中的氧结合,生成铁元素和CO的冶金原理,再经过铸造过程,可获得用于高铁、核电等行业应用的高纯特种生铁。
该工艺摒弃了传统炼铁工艺长流程高污染的冶炼方式,最大限度地减少了污染物的产生。
在冶炼过程中,炉内排出的高温含沉烟气,在锅炉入口处,温度最高可达1 650℃,通过设置烟道式余热锅炉,回收利用其热量,锅炉出口烟气温度降低至约800℃,为后续的排烟除尘和煤气回收创造合适的条件。
余热锅炉生产压力为4.7 MPa的饱和蒸汽,在过热后,可驱动汽轮机组发电,吨铁发电量达到了733 kW·h,实现有效的节能减排。
HISmelt熔融还原优化设计及生产实践
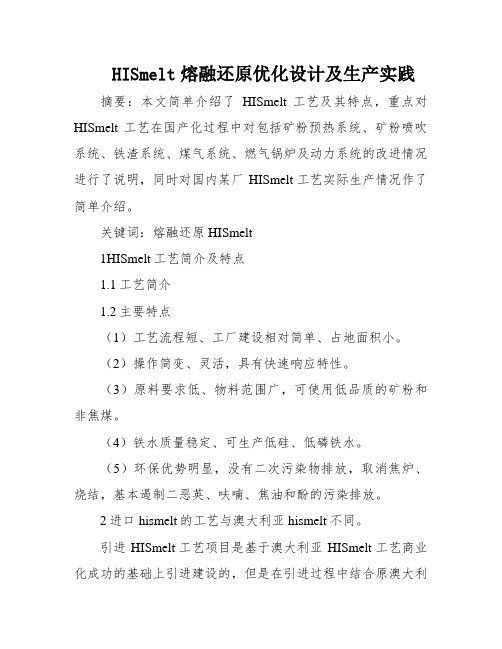
HISmelt熔融还原优化设计及生产实践摘要:本文简单介绍了HISmelt工艺及其特点,重点对HISmelt工艺在国产化过程中对包括矿粉预热系统、矿粉喷吹系统、铁渣系统、煤气系统、燃气锅炉及动力系统的改进情况进行了说明,同时对国内某厂HISmelt工艺实际生产情况作了简单介绍。
关键词:熔融还原HISmelt1HISmelt工艺简介及特点1.1工艺简介1.2主要特点(1)工艺流程短、工厂建设相对简单、占地面积小。
(2)操作简变、灵活,具有快速响应特性。
(3)原料要求低、物料范围广,可使用低品质的矿粉和非焦煤。
(4)铁水质量稳定、可生产低硅、低磷铁水。
(5)环保优势明显,没有二次污染物排放,取消焦炉、烧结,基本遏制二恶英、呋喃、焦油和酚的污染排放。
2进口hismelt的工艺与澳大利亚hismelt不同。
引进HISmelt工艺项目是基于澳大利亚HISmelt工艺商业化成功的基础上引进建设的,但是在引进过程中结合原澳大利亚的生产实践,对工艺路线、部分技术方案进行了优化改进和部分设备的国产化设计,下面针对主要变化内容进行说明。
2.1矿粉预热系统矿粉预热系统的主要功能是完成铁矿粉的预热、预热还原,目的是减少入炉铁矿粉在SRV炉内热量的消耗,提高SRV炉的冶炼强度,进而提高产量。
原澳大利亚该系统采用流化床工艺,具体流程是采用串联的三级旋风装置+流化床工艺,采用SRV高温煤气或者天然气燃烧的高温尾气作为预热预还原的热源,通过高温气体与铁矿粉在流化床和三级旋风装置内实现对流换热,最终达到预热预还原矿粉的目的。
通过在澳大利亚工厂的运行实践证明,该工艺因铁矿粉对多级旋风装置及流化床内衬的磨损,引起耐材的频繁脱落,以及螺旋输送机的故障,导致矿粉预热系统故障频繁,成为影响HISmelt工艺正常生产的主要问题之一。
在引进HISmelt工艺设计中,结合国内实际情况,将原有多级流化床工艺改为两段式回转窑工艺,其具体工艺流程是:通过矿石缓冲仓接收来自原料场的铁矿粉,缓冲后将矿石导入烘干窑,在烘干窑内将铁矿粉脱水干燥,从烘干窑排出的矿粉温度约80~100℃。
- 1、下载文档前请自行甄别文档内容的完整性,平台不提供额外的编辑、内容补充、找答案等附加服务。
- 2、"仅部分预览"的文档,不可在线预览部分如存在完整性等问题,可反馈申请退款(可完整预览的文档不适用该条件!)。
- 3、如文档侵犯您的权益,请联系客服反馈,我们会尽快为您处理(人工客服工作时间:9:00-18:30)。
2 生产工艺装备与技术指标
从熔(表融1)还1传原可统炼见的铁,高工熔炉艺融炼和还铁传原工统炼艺高铁采炉技用生术烧产与结设传矿备统、工高球艺炉团及比矿原有和料如焦要下炭求技,对术对比优原见势料表:使1用。要求比较严格,要求使用含铁高、 杂质低的铁矿粉和稀缺的炼焦煤,尤其是我国炼焦煤资源比较少,焦炭成为发展钢铁工业的制约条件。而熔 融还原炼铁工艺可以直接使用不同挥发分的煤作为能源炼铁,打破了焦炭对钢铁工业的制约,扩展了钢铁工 业的能源范围。
从表 3 可见,HISMELT 熔融还原工艺在能耗上低于传统高炉工艺(包括铁前工序),甚至低于单独的炼 铁工序。 3.3 铁元素利用效率对比
熔融还原工艺铁元素利用率一般在 87%~92%之间,传统高炉系统铁料利用率一般在 93%~95%之间,可 见,熔融还原系统的铁元素利用率要低于传统高炉系统,这主要是熔融还原产生的铁渣中铁分离不彻底,但 考虑到铁前系统的球团和烧结铁元素损失,两者相差不大。
熔融还原铁技术采用矿粉和煤粉直接生产铁水,没有烧结、球团和焦化工序,不同于传统高炉工艺,在 节能减排方面有良好的效果,下面对澳大利亚的 HISMELT 工艺与其他熔融还原工艺及传统高炉工艺在生产 工艺与技术装备、资源与能源利用效率、污染物排放、产品指标、废物利用效率等方面进行分析对比。
HISMELT 熔融还原炼铁工艺节能减排分析
根据目前研究,多数熔融还原工艺还处于开发和试验阶段,只有 COREX 和 HISMELT 工艺有实际应用。 COREX 工艺采用块矿、球团矿和煤块做原料生铁还原铁水,目前在浦项、南非、印度等已经投产,截至 2002 年末累计生产铁水 440 万 t,但不能直接使用矿粉和煤粉进行生产,未能彻底取代铁前工艺。HISMELT 工艺 是直接使用粉矿或其他含铁粉料和非焦煤粉生产铁水的一项新技术,20 世纪 80 年代初由澳大利亚 CRA 公 司研制成功,1989 年在澳大利亚昆纳纳兴建了一座卧式反应炉,后来又研制成功了竖式反应炉,目前澳大 利亚的昆纳纳已经建成一个年产 80 万t铁水的工业厂。
注:全国平均球团新水消耗量按照 0.4m3,折算比例同能耗。 ①来自 2005 年冶金环保统计;②来自中国冶金报社 2006 年我国高炉炼铁技术评述。
全国重点钢铁企业
8.6
从表 4 可见,HISMELT 熔融还原工艺消耗新水小于国内钢铁企业吨钢耗水,与国内重点钢铁企业 2006 年铁前工序吨铁消耗水指标相比,吨铁消耗水小于 1.25m3,但比全国先进企业铁前工序消耗水指标略高。
(2)熔融还原炼铁工艺可直接使用高杂质含量矿粉以及其他含铁工业废料,原料使用范围广,适应性 强,使大量原来炼铁工艺不能使用的高杂质矿等废弃资源得以有效利用。
(3)熔融还原炼铁工艺缩短了钢铁生产流程,可节省建设钢铁厂的投资,具有较好的经济效益。 从表 1 中可见,HISMELT 熔融还原炼铁工艺可以直接使用矿粉、煤粉以及含铁废料生产铁水,而且已 经有实际工程运行,工艺和装备与其他熔融还原炼铁工艺相比较更成熟可行。
预流熔融热化炉还床原、两铁段浴原循风制氧料环炉机破流、碎化熔、床融系、炉统热、
预铁制脱硫还浴氧、原熔机碳竖化、设炉炉连备、、续R化H铁F炉炉+电
设备能力/万 ·t a−1
60
60
15
80
15
15
14
预还原
竖炉 流化床 鼓泡流化床 循环流化床
旋流器
预还原温度/℃
800
850
850
750
预还原率
>90
~20 30
表 3 HISMELT 工艺和我国主要钢铁企业铁前工序能耗对比
企业
烧结工序
标煤 烧结矿 kg
/t
焦化工序
标煤 焦炭 kg
/t
炼铁工序
标煤 铁 kg
/t
折算能耗
标煤 铁 kg
/t
宝钢
56.5
91.17
385.21
500.36
鞍钢
45.14
109.50
①
447
554.02
武钢
50.41
99.33
404.51
2007 中国钢铁年会论文集
HISMELT 熔融还原炼铁工艺节能减排分析 魏有权 戴京宪 (中国京冶工程技术有限公司环保分公司,北京 ) 100088
摘 要 HISMELT 熔融还原炼铁是第三代还原炼铁技术,目前在澳大利亚已经得到实际应用, 本文从生产装备与 操作工艺、资源与能源利用、污染物排放、产品质量、废物回收利用方面分析了 HISMELT 工艺与其他熔融炼铁及 传统高炉炼铁工艺区别,结果证明,HISMELT 技术是资源能源消耗少、污染物排放少、生产操作可行的新型炼铁 技术,符合我国“十一五”期间钢铁工业节能减排的目标和要求,是炼铁技术发展的趋势。 关键词 熔融还原 节能减排 炼铁
3.2 工序能耗对比
由于 HISMELT 工艺无烧结、球团、焦化工序,直接生产铁水,与传统高炉能耗指标无法进行直接对比, 应当将烧结、球团、焦化工序的能耗折算叠加到高炉工序能耗中进行对比。按照每生产 1t 铁水投加 1.2t 烧 结矿和 0.5t 球团矿(球团矿占 30%)、0.3t 焦炭计算,HISMELT 工艺和我国主要钢铁企业铁前工序能耗对比 见表 3(球团工序能耗统一按照 40kg 标煤/t 球团矿来计算)。
3.5 煤气回收利用效率对比
熔融还原炼铁工艺和传统高炉工艺回收煤气利用数据对比见表 。5
HISMELT 熔融还原炼铁工艺节能减排分析
3.4 水资源利用效率对比 熔融还原炼铁工艺和传统高炉工艺水耗数据对比见表 。4
表 4 熔融还原炼铁工艺和传统高炉系统用水情况对比
宝钢 鞍钢 武钢 首钢 攀钢 新余
2005 年吨钢耗水①
7.11
8.14
20.64
4.98
15.86 13.22
HISMELT 工艺吨铁耗水
尾气能量回收 <4.56>
<3.38>
<9.44>
总能量
16.48
21.67
12.7
注:表中数据取自 James M.Mc clell and,Jr.P2004 年的研究报告。 ①包括空气、氧气、水等耗电在内。
COREX 30.77
0.5 0.83
32.10 <13.2> 18.9
REDMELT 14.85
煤
5~40mm 煤粉 煤块 8~22mm −2mm
块或粉 −2mm
还原剂
焦炭 CO
CO
CO、炭 CO、炭
炭 CO、炭
燃 料 焦粉炭、、热煤风 煤、氧(+空气) 煤、氧(空气) 煤、氧气 煤、空气 煤、氧(+空气) 煤、氧气
铁矿球石团、
煤粉 炭 煤、氧(空气)
3 资源与能源利用效率
3.1 能源消耗对比 熔融还原炼铁工艺和传统高炉工艺能源消耗数据对比见表 。2
, , Key words smelting reduction reducing energy consumption iron-making
1 引言
熔融还原法是指一切不用高炉法生产液态铁水的方法,以非焦煤作为主要能源,使用块矿、球团矿或者 直接使用铁矿粉等原料,在高温熔融状态下用碳把铁氧化物还原成金属铁的冶炼方法,工艺简单、资源和能 源利用效率高、对环境污染小。该项技术的发展已经历了三代。第一代技术以竖炉为基础,如 COREX 法、 FINEX 法等。第二代技术是深炉渣法,如日本的 DIOS、美国的 AISI、俄罗斯的 ROMELT、荷兰的 CCF 等。 第三代技术是金属熔池熔融法,如澳大利亚的 HISMELT 法。
Hismelt Smelting Reduction Technology for Reducing Energy Consumption
( ) Wei Youquan Dai Jingxian Environment Dept, China Jingye Engineering Corporation Limited, Beijing,100088
Abstract Hismelt smelting reduction iron-making technology is the third era and has been carried out in Australia. The
article analyzes the differences of production equipment, technics, resources using, contamination letting, the quality and the waste recycling between Hismelt technology and the traditional blast furnace technology. The results shown that Energy consumption and production cost can be reduced, and steel quality and environment can be improved by Hismelt technology, and accords with standard of economizing on energy in “eleventh five-years planning”. It is the trend of iron-making technology.
约 22
0
<30
终还原 高炉 熔融气化炉 熔融气化炉 熔融还原炉 熔融还原炉 熔融还原炉 熔融还原炉 熔融还原炉 炉 RHF
传热效率/%
>80
85
80
二次燃烧
氧气 氧气 氧气 热空气鼓风 氧气和冷空气 氧气
二次燃烧率/%