第四章精密和超精密加工的机床设备
04第四章:金属切削机床

例:CA6140; X6132; X5132 Y3150E; M7120; Z5140
2.专用机床的型号编制
专用机床型号表示方法
专用机床的型号一 般由设计单位代号和设计顺序号组成,其 表示方法为: (△)-△ 例如,北京第一机床厂设计制造的第100种 专用机床为专用铣床,其型号为B1-100。
联系动力源与执行机构之间的传动链。它使执行件获得动力以及一定的速 度和运动方向,其传动比的变化,只影响生产率或表面粗糙度,不影响加工 表面的形状和精度,如下图4-4所示的主运动传动链。
(2)内联系传动链
联系一个执行机构和另一个执行机构之间运 动的传动链。它决定着加工表面的形状和精度, 对执行机构之间的相对运动有严格要求。因此, 内联系传动链的传动比必须准确,不应有摩擦传 动或瞬时传动比变化的传动副(如皮带传动和链 传动),如下图4-4所示的进给运动传动链。
③组、系代号 为了区分机床的结构、布局和所能加工的 零件特征,每类机床可分为“0~9”十个组别。 为了更细的区分机床的结构特征,机床在组下 面又可细分为“0~9”十个系别。同一组、系 的机床,其主要结构及布局形式基本相同。机 床组、系代号用阿拉伯数字表示。机床的类、 组代号的含义见教材P5表2,组、系代号见表 2.3。
图2.8 车削成需要成形运动。 导线(母线1绕轴线O-O旋转的运动轨迹),由轨迹 法形成,需要1个成形运动B1。 形成成形回转表面的成形运动总数是形成母线和导 线所需成形运动的和,即1个成形运动(B1)。
例2 如图2.9所示,用螺 纹60°成形车刀车削三角 螺纹,试分析其母线、导 线的成形方法及所需要的 成形运动,并说明形成该 表面共需要几个成形运动。
图4-4 CA6140车床的传动系统图
第四章 精密和超精密加工机床 管文 编著

Nanosys-1000机床系统的特点是: (1)床身本体设计成整体类龙门框架结构,具有高刚性、高稳 定性及安装、维修、工件装卸、加工运行易操作性特点。 (2)机身整体坐落在4主动式隔振气垫上,形成动力学 3 支撑, 可随着加工中重心改变自动调水平;隔振气垫下的机床地基设 计成具有横向隔离的重力型减振形式;机床重心及工件刀具加 工点设计在接近支持平面的位置,以最小化床身姿态变化扰动 影响。 (3)机床主轴、导轨均采用液浮静压轴承,并根据工作状态, 主轴采用低阻尼,导轨采用高阻尼油;Z垂直导轨托板设计成无 干涉气浮重力平衡机构。 (4)机床坐标测量采用衍射光栅测量系统;机床采用 PC与多 轴运动控制器构成的开放式数控系统。 (5)机床本体、主轴采用了无脉动重力型水冷恒温;液压源采 用恒温、恒压、脉动滤波技术和装置。
(1)NAM-800型纳米数控车床是1998年北京机床研究所制成, 见图4-9。其主要性能指标见表4-5。
图4-9 NAM-800型CNC超精密金刚石车 床 表4-5 NAM-800型纳米数控车床主要技术性能
(2)航空航天工业303所研制的非球面曲面超精密加工机 床车削加工样件的面形精度 PV= 0.228μm,表面粗糙度 Ra=0.0078μm。303所研制的JCS-031超精密金刚石铣床的 技术指标如表4-6。
表4-2 几种典型的超精密机床技术性能指标
【精品课件】精密和超精密加工的机床设备

美国Pneumo公司的MSG-325超精密车床
采用T形布局,主轴箱下有导轨作z向运动,刀架溜 板作x向运动。机床空气主轴的径向圆跳动和轴向跳动 均≤0.05μm。床身溜板用花岗岩制造,导轨为气浮导 轨;机床用滚珠丝杠和分辨率为0.01μm的双坐标精密 数控系统驱动,用HP5501A双频激光干涉仪精密检测 位移。使用精密的圆弧刃金刚石刀具加工非球曲面的反 射镜,可达到很高的形状精度和很小的表面粗糙度。来自DTM-3大型超精密车床
1983年由美国LLL实验室联合研制。可加 工最大零件φ2100mm重量4500kg的各种金 属反射镜、红外装置零件、大型天体望远镜 等。半径方向形状精度27.9nm,圆度、平面 度12.5nm,Ra≤4.2nm。
采用精密数控伺服方式,控制部分为内装 式CNC装置和激光干涉测长仪,精确测量定 位,在DC伺服机构内装有压电微位移机构, 实现纳米级微位移。
• 空气轴承(又称为气浮轴承)指的是用气体(通常是空气,但也有可能是其 它气体)作为润滑剂的滑动轴承。空气比油粘滞性小,耐高温,无污染,因 而可用于高速机器、仪器及放射性装置中,但其负荷能力比油低。 空气轴承 分为三大类:空气静压轴承、空气动压轴承和挤压膜轴承。在一般工业中, 空气静压轴承用得较广泛。
世界公认技术水平最高、精度最高的大型 金刚石超精密车床之一。
大型光学金刚石车床LODTM
1984年由美国LLL实验室联合研制。可加工 φ1625mm×500mm 、 重 量 1360kg 的 大 型 金 属反射镜。
机床采用立式结构,采用面积较大止推轴承; 7路高分辨力双频激光测量系统;4路激光检测 横梁上溜板的运动;3路激光检测刀架上下运动 位置;使用在线测量和误差补偿;各发热部件 用大量恒温水冷却;用大的地基,地基周围有 防振沟,且整个机床用4个大空气弹簧支承。
超精密加工的机床设备

超精密加工的机床设备摘要:超精密加工技术的发展直接影响整个国家的制造业发展,影响尖端技术和国防工业的发展。
机床是实现超精密加工的重要载体,机床的制造水平和研究水平便显得非常的重要。
本文在论述目前国内外超精密加工机床的现状的同时,介绍了国内外有代表性的几种超精密加工机床,并介绍分析了超精密机床的精密主轴部件、进给驱动系统、误差建模和补偿技术和数控技术。
关键词:超精密加工机床发展关键技术1.引言制造业是一个国家或地区国民经济的重要支柱,其竞争能力最终体现在新生产的工业产品市场占有率上,而制造技术则是发展制造业并提高其产品竞争力的关键。
精密和超精密加工技术是制造业的前沿和发展方向。
精密和超精密加工技术的发展直接影响到一个国家尖端技术和国防工业的发展,世界各国对此都极为重视,投入很大力量进行研究开发,同时实行技术保密,控制关键加工技术及设备出口。
随着航空航天、高精密仪器仪表、惯导平台、光学和激光等技术的迅猛发展和多领域的广泛应用,对各种高精度复杂零件、光学零件、高精度平面、曲面和复杂形状的加工需求日益迫切。
目前,国外已开发了多种精密和超精密车削、磨削、抛光等机床设备,发展了新的精密加工和精密测量技术。
最近几年,我国的机床制造业虽然发展很快,年产量和出口量都明显增加,成为世界机床最大消费国和第一大进口国,在精密机床设备制造方面取得不小进展,但仍和国外有较大差距。
我国还没有根本扭转大量进口昂贵的数控和精密机床、出口廉价中低档次机床的基本状况。
由于国外对我们封锁禁运一些重要的高精度机床设备和仪器,而这些精密设备仪器正是国防和尖端技术发展所迫切需要的,我们必须投入必要的人力物力,自主发展精密和超精密加工机床,使我国的国防和科技发展不会受制于人。
2.超精密机床的发展现状2.1国外超精密机床发展现状目前在国际上处于领先地位的国家有美国、英国和日本, 这3个国家的超精密加工装备不仅总体成套水平高, 而且商品化的程度也非常高。
精密和超精密加工的机床设备技术

精密和超精密加工的机床设备技术引言精密和超精密加工技术在现代制造业中扮演着重要的角色。
为了满足高质量、高精度、高效率的加工需求,机床设备技术不断得到改进和发展。
本文将介绍精密和超精密加工的机床设备技术,并探讨其在制造业中的应用。
1. 精密加工的机床设备技术精密加工是指在工程加工中,对尺寸精度和表面质量要求较高的加工方法。
精密加工的关键在于机床设备的稳定性、刚性和精度。
以下是精密加工机床设备的几个关键技术:1.1 数控技术数控技术是精密加工中最为关键的技术之一。
通过数控技术,可以实现机床的高精度和高效率加工。
数控技术的应用可以大大提高生产效率,并且减少操作人员的工作强度。
1.2 精密传动系统精密传动系统是精密加工机床设备的核心组成部分。
精密传动系统的设计与制造涉及到轴承、传动装置、伺服驱动装置等多个方面。
通过精确的传动系统,可以提高机床的精度和稳定性。
1.3 线性驱动技术线性驱动技术是现代机床设备中的重要发展方向之一。
相比传统的滚动轴承驱动,线性驱动技术能够实现更高的速度和更高的精度。
线性驱动技术可以用于各种类型的机床设备,包括数控机床和超精密加工机床。
2. 超精密加工的机床设备技术超精密加工是指在微米甚至纳米级别下进行加工的技术。
超精密加工在光学、光电子、半导体等领域具有重要的应用。
以下是超精密加工机床设备技术的几个关键技术:2.1 超精密控制系统超精密控制系统是实现超精密加工的关键技术之一。
通过超精密控制系统,可以实现对微小位移和应力的精确控制。
超精密控制系统需要具备高精度、高灵敏度和高稳定性的特点。
2.2 超精密磨削技术超精密磨削技术是超精密加工的核心技术之一。
超精密磨削技术可以实现对工件表面的精确修整和光洁度的提高。
超精密磨削技术需要借助特殊材料和磨削工具,并配合高精度的机床设备。
2.3 超精密检测技术超精密加工过程中,对工件的检测和测量要求非常高。
超精密检测技术可以实现对工件尺寸、形状和表面质量的高精度测量。
精密和超精密加工的机床设备

高精度、高效率、高表面质量、 低误差、低能耗等。
应用领域
01
02
03
04
航空航天
制造飞机发动机叶片、涡轮盘 等关键部件。
汽车制造
加工发动机缸体、曲轴等精密 零部件。
能源领域
制造核聚变反应堆中的超导线 圈、太阳能电池板等。
医疗器械
制造人工关节、牙科种植体等 医疗器件。
发展历程与趋势
发展历程
从20世纪50年代开始,精密和超精密加工技术经历了从简单磨削 到复杂切削,再到超精密切削的发展过程。
航空航天领域的应用案例
案例一
某航空发动机制造企业使用超精密加 工机床,对涡轮叶片进行高精度磨削 和抛光,提高了发动机性能和可靠性 。
案例二
某飞机制造企业采用精密加工机床, 对机身结构件进行高精度切割和加工 ,确保飞机整体装配精度和质量。
汽车工业领域的应用案例
案例一
某汽车零部件制造企业使用精密加工 机床,对发动机缸体进行高精度加工, 提高缸体质量和性能,降低发动机故 障率。
柔性化
为了满足多品种、小批量生产的需求,未来精密和超精密加工机床将采用模块化设计、可 重构制造系统等技术,提高机床的加工范围和适应能力。
新材料、新工艺的应用
新材料
随着新材料技术的发展,未来精密和超精密加工机床将采用新型高强度、高硬 度、轻质材料,提高加工效率和加工质量。
ห้องสมุดไป่ตู้新工艺
为了满足复杂形状和特殊材料的加工需求,未来精密和超精密加工机床将采用 新的切削工艺、光整加工工艺和复合加工工艺等,提高加工精度和表面质量。
伺服驱动技术
采用先进的伺服驱动技术, 实现高精度的位置控制和 速度控制。
插补算法
精密和超精密加工和机床设备共90页PPT

1、最灵繁的人也看不见自己的背脊。——非洲 2、最困难的事情就是认识自己。——希腊 3、有勇气承担命运这才是英雄好汉。——黑塞 4、与肝胆人共事,无字句处读书。——周恩来 5、阅读使人充实,会谈使人敏捷,写作使人精确。——培根
精密和超精密加工和机床设备
6、法律的基础有两个,而且只有两个……公平和实用。——伯克 7、有两种和平的暴力,那就是法律和礼节。——歌德
8、法律就是秩序,有好的法律才有好的秩序。——亚里士多德 9、上帝把法律和公平凑合在一起,可是人类却把它拆开。——查·科尔顿 10、一切法律都是无用的,因为好人用不着它们,而坏人又不会因为它们而变得规矩起来
精密和超精密加工的机床设备
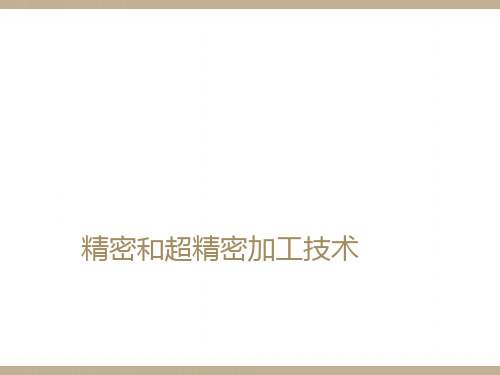
单击此处添加小标题
单击此处添加小标题
缺点:电机发热,容易使主轴产生热变形。
单击此处添加小标题
措施:电动机采用强制通气冷却,或通过恒温油(水)冷却。
单击此处添加小标题
将机床主轴与电机轴合二为一,即将电机的定子、转子直接装入主轴组件的内部,期间不再使用皮带或齿轮传动副,也称电主轴。
单击此处添加大标题内容
轴承内圆柱面上,等间隙地开有几个油腔(通常为4个)。 各油腔之间开有回油槽。 用过的油一部分从这些回油槽流回油箱(径向回油),另一部分则由两端流回油箱(轴向回油)。 油腔四周形成适当宽度的轴向封油面和周向封油面,它们和轴颈之间的间隙一般为0.02~0.04mm。 油泵供油压力为ps,油液经节流器T进入各油腔,将轴颈推向中央,油液最后经封油面流回油箱,压力降低为零。 当主轴不受载荷且忽略自重时,则各油腔的油压相同,保持平衡,轴在轴承正中心,这时轴颈表面与各腔封油面之间的间隙相等,均为h0。 当主轴受径向载荷(包括自重)F作用后,轴颈向下移动产生偏心量e。
立式空气轴承
特点: 下止推面大于上止推面,平衡主轴重量; 圆弧面径向轴承,自动调心、提高精度。
三、超精密机床主轴和轴承的材料
要求:不易磨损,不易生锈腐蚀,热膨胀系数小,且主轴和轴套的热膨胀系数要接近,材料的稳定性好。 主要材料:轴和轴套均采用38CrMoAl氮化钢,经表面氮化和低温稳定处理;不锈钢、多孔石墨和轴承钢;此外还有铟钢、花岗岩、线膨胀系数接近零的微晶玻璃、陶瓷等。
缺点:
圆柱径向轴承和端面止推空气静压轴承
结构与液体静压轴承主轴结构基本相同,只是节流孔和气腔大小形状不同。要求有很高的同轴度和垂直度。 1号车床的径向轴承的轴套制成外面鼓形,能自动调整定心。轴套的外表面做凸形球面,与轴承盖及轴承座上的凹形球面相配合。当轴变形时,轴套可以自动调整位置,从而保证轴颈与轴鼓为面接触。用多孔石墨的轴衬代替小节流孔。
04精密加工和特种加工

抛光特点:
①方法简便、经济,不用特殊设备;
②容易对曲面进行加工;
③只能提高粗糙度,不能改变零件的尺寸精度、形状精度或位置精度;
④劳动条件差。
抛光应用: 抛光主要用于零件表面的装饰加工,或者利用抛光方法去除前道工序的加工
痕迹,提高零件的疲劳强度。
抛光零件表面的形状可以是平面、外圆、孔、以及各种成形表面等。 五、各种精密加工方法的比较:
用装有细磨粒、低硬度的油石磨头,在一定压力下 对工件表面进行光整加工的方法称为超级光磨 。
• 加工时工件旋转,油石以恒力轻压于工件表面, 在作轴向进给的同时作轴向微小振动,从而达到 对工件微观不平的表面进行光磨的效果。
超级光磨的特点 : ①加工余量极少,一般为3 ~ 10μm; ②生产率较高,一般加工时间只需30~60秒; ③表面质量好,Ra<0.012μm; ④设备简单,操作方便。 但是,超级光磨只能提高表面质量,不能提高尺寸精度和形位精度。
第二节 特种加工
特种加工是相对于传统的切削加工而言,传统的切削加工是用刀具靠机械 能去除工件表面的多余材料。当工件材料的强度、硬度、脆性、韧性过高, 或零件的结构过于复杂,或尺寸太小,或零件的刚度较差时,传统的切削加 工方法就难于实现。特种加工就是为解决这些难题而发展起来的一种新的加 工方法.
特种加工是直接利用电能、光能、声能、热能、化学能或多种能量复合形 式进行加工的方法。常用的特种加工有电火花加工、电解加工、超声波加工、 激光加工、电子束加工和离子束加工等。
精度为3~O.3 μm,粗糙度为O.3~O·03μm的叫精密加工;
精度为0.3~0.03 μm,粗糙度为0.03~0.005 μm的叫超精密加工,或亚微米 加工;
精度为0.03 μm(30纳米),粗糙度优于0.005 μm以上的则称为纳米(nm)加工。
先进制造技术第4章超高速加工技术

目前市场上出现的铣削加工机床主轴转速在 20000~60000r/min,最高达到150000 r/min;
20世纪80年代,计算机控制的自动化生产技术的 高速发展成为国际生产工程的突出特点,工业发达国 家机床的数控化率已高达70%~80%。随着数控机 床、加工中心和柔性制造系统在机械制造中的应用, 使机床空行程动作(如自动换刀、上下料等)的速度和 零件生产过程的连续性大大加快,机械加工的辅助工 时大为缩短。在这种情况下,再一味地减少辅助工时, 不但技术上有难度,经济上不合算,而且对提高生产 率的作用也不大。这时辅助工时在总的零件单件工时 中所占的比例已经较小,切削工时占去了总工时的主 要部分,成为主要矛盾。只有大幅度地减少切削工时, 即提高切削速度和进给速度等,才有可能在提高生产 率方面出现一次新的飞跃和突破。这就是超高速加工 技术(Ultra-high speed machining UHSM)得以 迅速发展的历史背景。。
日本约在20世纪60年代开始了对超高速切削机 制的研究,田中义信利用来复枪改制的超高速切削 装置,实现了高达200~700m/s的超高速切削,对主 切削力和加工表面的变形层性能进行研究。指出: 超高速切屑形成完全是剪切作用的结果,随着切削 速度的提高,剪切角急剧增大,工件材料的变质层 厚度与普通速度下相比降低了50%。
W9Mo3Cr4V等。
硬质合金:是由高硬难熔金属碳
化物粉末,以钴或镍为粘接剂,用粉末
冶金的方法制成的。它的硬度可达
74 ~82(90)HRC。目前多用于制 造各种简单刀具,如车刀、铣刀、刨刀 的刀片等。
精密和超精密加工的机床设备技术(PPT 88页)

液体摩擦轴承
液体动压润滑轴承 液体静压润滑轴承
非液体摩擦轴承
• 按滑动轴承承受载荷的方向可分为:
径向滑动轴承(向心) 推力滑动轴承(止推)
2022/3/23
根据润滑膜的形成原理不同分为:
动压润滑轴承
静压润滑轴承
利用相对运动副表面的相对运动 和几何形状,借助流体粘性,把润滑 剂带进摩擦面之间,依靠自然建立的 流体压力膜,将运动副表面分开的润 滑方法为流体动压润滑。
类型:普通(各种精密超精密车、铣等)、专 用(磁盘超精密车床) 按工艺方法:超精密车床、超精密铣床、超精 密磨床、超精密研磨机、超精密抛光机床、超 精密特种加工机床、精密和超精密加工中心等
精度指标:目前,主轴回转精度为0.025um, 导轨直线度为1000000:0.025,定位精度为 0.013um/1000um,进给分辨率为
2022/3/23
在滑动轴承与轴颈表面之间输入 高压润滑剂以承受外载荷,使运动副 表面分离的润滑方法成为流体静压润 滑。
止推轴承(推力轴承)
轴承座
Fa
径向轴瓦 止推轴瓦
径向轴承(向心轴承) Fr
止推轴承受力Fa与 轴的中心线平行
2022/3/23
径向轴承的受力Fr 与轴的中心线垂直
2022/3/23
二、典型机床简介
Pneumo 公司的MSG-325超精密车床 采用T形布局,机床空气主轴的径向圆跳动和轴向
跳动均小于等于0.05μm。床身溜板用花岗岩制造,导 轨为气浮导轨;机床用滚珠丝杠和分辨率为0.01μm的 双坐标精密数控系统驱动,用HP5501A双频激光干涉仪 精密检测位移。
Precision and ultraprecision machining
《精密和超精密加工技术(第3版)》第4章精密和超精密加工的机床设备
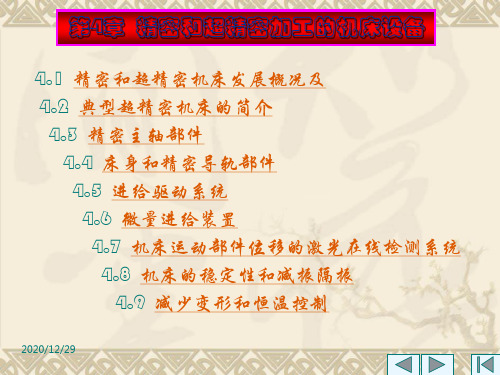
第1节 精密和超精密机床发展概况
二、超精密机床进一步发展的规划
3.中国精密机床和超精密机床的发展情况 1987年北京机床研究所研制成功加工球面的JSC027型超精密车床。后来又研制成功JSC-035型数控 超精密车床。1998年,北京机床研究所制成的加工直 径800mm的NAM-800型CNC超精密金刚石车床(图 4-1)和SQUARE-200型等超精密铣床,哈尔滨工业大 学研制成加工直径300mm的CNC超精密车床, 2006 年,哈尔滨工业大学研制成加工KDP晶体的大平面超 精密飞刀切削机床(图4-2)。
第4章 精密和超精密加工的机床设备
4.1 精密和超精密机床发展概况及 4.2 典型超精密机床的简介 4.3 精密主轴部件
4.4 床身和精密导轨部件 4.5 进给驱动系统 4.6 微量进给装置
4.7 机床运动部件位移的激光在线检测系统 4.8 机床的稳定性和减振隔振
4.9 减少变形和恒温控制
2020/12/29
第1节 精密和超精密机床发展概况
二、超精密机床进一步发展的规划
2.日本提出的“超超精密机床”规划 日本也在原来超精密机床的基础上,再进一步 规划更高精度的机床。按日本的提法,也就是 研制“超超精密机床”。表4-2是日本提出 的该规划的各项指标。 该规划主要围绕提高超精密机床精度性能而 提出的设想,共有13个子课题,并已在20世纪 内完成。该规划是以纳米级精度作为目标的。
2020/12/29
第1节 精密和超精密机床发展概况
二、超精密机床进一步发展的规划
表4-1是POMA规划对精度的具体要求,该规 划已经实现。例如,美国Moore公司现在生产 的Nanotech-500FG五轴数控超精密机床的 主要精度指标都已达到上述要求。
精密和超精密加工的机床设备技术
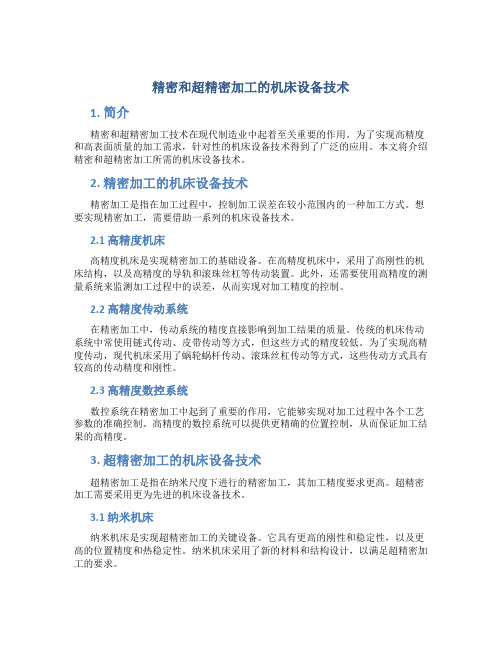
精密和超精密加工的机床设备技术1. 简介精密和超精密加工技术在现代制造业中起着至关重要的作用。
为了实现高精度和高表面质量的加工需求,针对性的机床设备技术得到了广泛的应用。
本文将介绍精密和超精密加工所需的机床设备技术。
2. 精密加工的机床设备技术精密加工是指在加工过程中,控制加工误差在较小范围内的一种加工方式。
想要实现精密加工,需要借助一系列的机床设备技术。
2.1 高精度机床高精度机床是实现精密加工的基础设备。
在高精度机床中,采用了高刚性的机床结构,以及高精度的导轨和滚珠丝杠等传动装置。
此外,还需要使用高精度的测量系统来监测加工过程中的误差,从而实现对加工精度的控制。
2.2 高精度传动系统在精密加工中,传动系统的精度直接影响到加工结果的质量。
传统的机床传动系统中常使用链式传动、皮带传动等方式,但这些方式的精度较低。
为了实现高精度传动,现代机床采用了蜗轮蜗杆传动、滚珠丝杠传动等方式,这些传动方式具有较高的传动精度和刚性。
2.3 高精度数控系统数控系统在精密加工中起到了重要的作用,它能够实现对加工过程中各个工艺参数的准确控制。
高精度的数控系统可以提供更精确的位置控制,从而保证加工结果的高精度。
3. 超精密加工的机床设备技术超精密加工是指在纳米尺度下进行的精密加工,其加工精度要求更高。
超精密加工需要采用更为先进的机床设备技术。
3.1 纳米机床纳米机床是实现超精密加工的关键设备。
它具有更高的刚性和稳定性,以及更高的位置精度和热稳定性。
纳米机床采用了新的材料和结构设计,以满足超精密加工的要求。
3.2 纳米传感器和测量技术在超精密加工中,需要更加精确的测量和控制技术。
纳米传感器和测量技术可以实时测量加工过程中的各种参数,包括加工力、温度、振动等,从而实现对加工过程的准确控制。
3.3 纳米控制系统超精密加工中的控制系统需要具备更高的精度和快速响应能力。
纳米控制系统采用了更高精度的位置控制算法,并配备了更先进的控制器,能够实现对加工过程中微小误差的实时调整。
江苏自考精密加工与特种加工教材大纲---精品模板

江苏:自考精密加工与特种加工教材大纲(发布时间:2006-11—16 9:38 来自:模考网)02213 精密加工与特种加工扬州大学编(高纲号 0627)一、课程性质及其设置目的与要求(一)课程性质和特点《精密加工与特种加工》课程是我省高等教育自学考试机械设计制造及其自动化专业(独立本科段)的一门重要的专业课程.其任务是使应考者获得精密和超精密加工技术的基本理论、基本知识和方法;初步掌握各种精密和超精密加工方法在生产中的应用.获得特种加工工艺的基本原理、常用工艺设备及应用的系统知识,初步具备分析、选择和使用各种常用特种加工工艺的能力.(二)本课程的基本要求通过对本课程的学习,应考者应达到以下具体要求:1、获得精密和超精密加工技术的基本原理和技术,包括超精密切削和金刚石刀具、精密和超精密磨削、研磨与抛光、精密和超精密机床设备、精密加工中的测量技术,在线测量和误差补偿技术、微细加工技术、精密加工的支撑环境等.2、初步具备精密和超精密加工工艺参数的选择及其对加工质量的影响.3、了解精密和超精密加工技术的现状和发展趋势。
4、掌握特种加工的基本理论和一般知识,包括常用加工工艺的加工原理、设备特点和有关应用。
5、在对各种常用特种加工工艺综合理解、比较的基础上,具有选择加工工艺、分析加工工艺过程及解决实际工艺问题的能力.6、了解特种加工技术应用现状和发展趋势.(三)本课程与相关课程的联系本课程的先修课程为电工电子学、大学物理、工程力学、机械设计、机械工程材料、数控技术、机械制造技术;其后续课程有其它专业课程、课程设计、毕业设计.二、课程内容与考核目标精密和超精密加工技术部分第一章精密和超精密加工技术及其发展展望(一)课程内容本章主要介绍了发展精密和超精密加工技术的重要性以及超精密加工的现状。
(二)考核知识点和考核要求1、识记:精密加工和超精密加工概念、领域,金刚石刀具两个重要问题,超精密加工中检测内容。
第二章超精密切削与金刚石刀具(一)课程内容本章主要介绍了超精密切削的切削速度选择;超精密切削时刀具的磨损和耐用度;超精密切削时积屑瘤的生成规律;切削参数变化对加工表面质量的影响;刀刃锋锐度对切削变形和表面质量的影响;超精密切削时最小切削厚度;金刚石刀具晶面选择对切削变形和加工表面质量的影响;超精密切削对刀具的要求及金刚石的性能和晶体结构;金刚石晶体各晶面的耐磨性和好磨难磨方向;单晶金刚石刀具的破损机理;金刚石晶体的定向;金刚石刀具的设计与制造。
精密加工及精密加工机床

Company Logo
2.2
Nanoform250超精密加工系统
既能进行超精密车削,又能进行超精密磨削,还能进行超精密抛光,能 直接磨削出满足光学表面质量和面型精度的硬脆材料的光学零件。最大加工 工件直径Ф250mm,通过一个升高装臵,可使机床的最大加工工件直径达到 Ф450mm,另外通过控制垂直方向的液体静压导轨(Y轴),还能够磨削非轴对称 的零件。ONs实时操作数控系统的直线编程精度为0.01 nm,角度编程精度为 度 10 7 度,直线静压导轨的位臵反馈分辨率0.016nm,进给速率为 4000mm/min,加工工件的面型精度小于0.1μm,表面粗糙度Ra优于lnm。
Company Logo
OAGM 2500大型超 精密机床
2.3
国内超精密机床现状
我国北京机床研究所是国内进行超精密加工技术研究的主要单位之 一。2002年为军工某单位开发研制的“SPHER200C超精密球面加工机 床”,薄壁(1mm)球面零件的批量加工表面粗糙度达Ra10nm,最好件可 达3nm。哈尔滨工业大学成功研制了HCM-l亚微米超精密加工机床。加工 的零件精度0.2 m,表面粗糙度优于Ra0.02m。航空航天工业部303所、 清华大学、华中理工大学、沈阳第一机床厂、成都工具研究所、国防科技 大学等都进行y Logo
2.误差补偿系统的组成
1)误差信号的检测
2)误差信号的处理
3)误差信号的建模
计算机控制系统
4)补偿控制
5)补偿执行机构
1
2
3
4
5
误差补偿系统组成示意图 1-误差信号检测 2-误差信号处理 3-误差信号建模 4-补偿控制 5-补偿执行机构
Company Logo
四、超精密机床的工作环境
精密和超精密加工的机床设备技术
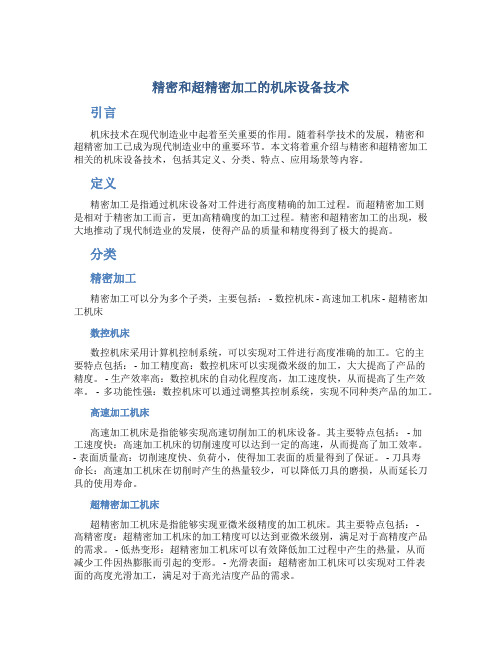
精密和超精密加工的机床设备技术引言机床技术在现代制造业中起着至关重要的作用。
随着科学技术的发展,精密和超精密加工已成为现代制造业中的重要环节。
本文将着重介绍与精密和超精密加工相关的机床设备技术,包括其定义、分类、特点、应用场景等内容。
定义精密加工是指通过机床设备对工件进行高度精确的加工过程。
而超精密加工则是相对于精密加工而言,更加高精确度的加工过程。
精密和超精密加工的出现,极大地推动了现代制造业的发展,使得产品的质量和精度得到了极大的提高。
分类精密加工精密加工可以分为多个子类,主要包括: - 数控机床 - 高速加工机床 - 超精密加工机床数控机床数控机床采用计算机控制系统,可以实现对工件进行高度准确的加工。
它的主要特点包括: - 加工精度高:数控机床可以实现微米级的加工,大大提高了产品的精度。
- 生产效率高:数控机床的自动化程度高,加工速度快,从而提高了生产效率。
- 多功能性强:数控机床可以通过调整其控制系统,实现不同种类产品的加工。
高速加工机床高速加工机床是指能够实现高速切削加工的机床设备。
其主要特点包括: - 加工速度快:高速加工机床的切削速度可以达到一定的高速,从而提高了加工效率。
- 表面质量高:切削速度快、负荷小,使得加工表面的质量得到了保证。
- 刀具寿命长:高速加工机床在切削时产生的热量较少,可以降低刀具的磨损,从而延长刀具的使用寿命。
超精密加工机床超精密加工机床是指能够实现亚微米级精度的加工机床。
其主要特点包括: -高精密度:超精密加工机床的加工精度可以达到亚微米级别,满足对于高精度产品的需求。
- 低热变形:超精密加工机床可以有效降低加工过程中产生的热量,从而减少工件因热膨胀而引起的变形。
- 光滑表面:超精密加工机床可以实现对工件表面的高度光滑加工,满足对于高光洁度产品的需求。
超精密加工•超精密加工器械•超精密切削特点精密和超精密加工的机床设备具有以下特点:1.高精度:机床设备的设计和制造严格遵循高精度要求,以确保加工过程的精确性和稳定性。
精密和超精密加工的机床设备

精密和超精密加工的机床设备简介精密加工和超精密加工是现代制造业中非常重要的工艺,为了实现高精度和高质量的产品制造,需要使用精密和超精密加工的机床设备。
本文将介绍精密和超精密加工的定义、应用领域、常见机床设备及其特点。
精密加工与超精密加工的定义精密加工是指在小尺寸范围内实现高精度、高表面质量的加工过程。
超精密加工则是在精密加工的基础上,进一步提高加工精度和表面质量,通常使用的是非常细小的工具进行加工。
精密加工与超精密加工的应用领域精密加工和超精密加工广泛应用于各个领域,特别是需要高精度和高质量的产品制造领域。
以下是一些典型的应用领域:1.光学器件加工:如镜片、棱镜、透镜等光学组件的加工需要极高的精度和表面质量。
2.高精密模具加工:精密模具通常用于制造电子产品、汽车零部件等需要高精度的零件。
3.精密五金零部件加工:如手表零部件、医疗设备零部件等,需要高精度和高质量的加工。
4.微电子器件加工:微电子器件通常要求极高的精度和表面质量,用于生产集成电路、传感器等。
常见的精密和超精密加工机床设备下面介绍一些常见的精密和超精密加工机床设备及其特点:CNC铣床CNC铣床是一种通过计算机控制的自动化机床,能够在三个轴向上进行加工。
精密加工中常用的是数控铣床,而超精密加工则需要使用高速铣床。
CNC铣床具有高精度、高刚性、高自动化程度等特点。
高精度车床高精度车床是一种用来加工圆柱形工件的机床。
它能够在工件上进行精确的车削、镗削、钻削等操作。
高精度车床具有高工作精度、高生产效率和良好的刚性。
光学加工机光学加工机是用激光或电子束等光学器件进行加工的机床设备。
它能够实现非常高的加工精度和表面质量,常用于光学器件加工和微电子器件加工。
超精密磨床超精密磨床是一种用磨粒对工件进行加工的机床设备。
它能够实现非常高的加工精度和表面质量,常用于精密模具加工和高精度五金零部件加工。
EDM电火花机床EDM电火花机床是一种利用电火花腐蚀的原理进行加工的机床设备,能够实现非常高的加工精度和表面质量。
- 1、下载文档前请自行甄别文档内容的完整性,平台不提供额外的编辑、内容补充、找答案等附加服务。
- 2、"仅部分预览"的文档,不可在线预览部分如存在完整性等问题,可反馈申请退款(可完整预览的文档不适用该条件!)。
- 3、如文档侵犯您的权益,请联系客服反馈,我们会尽快为您处理(人工客服工作时间:9:00-18:30)。
22
液体静压轴承的优缺点
• 特点:回转精度高、转动平稳、承载能力高。主要用于大型超精 密加工机床。
• 缺点:高速下,油温升高造成热变形,影响主轴精度;回油时,
将空气带入油源,降低轴承刚度和动态特性。 解决措施(以DTM-3大型超精密机床为例): • (1)提高静压油的压力到 6~ 8MPa,使油中微小气泡的影响减小, 提高静压轴承的刚度和动特性。
8
美国Pneumo公司的MSG-325超精密车床 采用T形布局,主轴箱下有导轨作z向运动,刀架溜
板作x向运动。机床空气主轴的径向圆跳动和轴向跳动
均≤ 0.05μm。床身溜板用花岗岩制造,导轨为气浮导 轨;机床用滚珠丝杠和分辨率为 0.01μm的双坐标精密 数控系统驱动,用 HP5501A 双频激光干涉仪精密检测位 移。使用精密的圆弧刃金刚石刀具加工非球曲面的反射
• • • •
(11)假如油腔的有效承载面积为A,则轴承的承载能力为:F= A(p3 p1)。 (12)各油腔由同一个液压泵供油,则每个油腔必须串联一个节流器。 (13)没有节流器,各油腔油压相同,互相抵消,就不能平衡外载荷了,
这时主轴产生位移,甚至使轴颈与轴承表面接触。
(14)油腔压力是液压泵供给的,与轴的转速无关。因此,静压轴承可 以在很低的转速下工作。
27
立式空气轴承
特点:
• 下止推面大于上止推面,平衡主轴重量;
• 圆弧面径向轴承,自动调心、提高精度。
28
三、超精密机床主轴和轴承的材料
• 要求:不易磨损,不易生锈腐蚀,热膨胀系数小,且主 轴和轴套的热膨胀系数要接近,材料的稳定性好。
• 主要材料:轴和轴套均采用 38CrMoAl 氮化钢,经表面氮
镜,可达到很高的形状精度和很小的表面粗糙度。
9
DTM-3大型超精密车床
1983年由美国LLL实验室联合研制。可加
工最大零件φ2100mm 重量 4500kg 的各种金属 反射镜、红外装置零件、大型天体望远镜等。
半 径 方 向 形 状 精 度 27.9nm , 圆 度 、 平 面 度
12.5nm,Ra≤4.2nm。 采用精密数控伺服方式,控制部分为内
18
根据承受载荷方向不同分为:
止推轴承(推力轴承) 径向轴承(向心轴承)
轴承座
Fa
径向轴瓦 止推轴瓦
Fr
止推轴承受力Fa与 轴的中心线平行
径向轴承的受力Fr 与轴的中心线垂直
19
液体静压轴承工作原理
静压轴承组成:供油系统、节流器、轴承
20
• • • • •
( 1 )轴承内圆柱面上,等间隙地开有几个油腔(通 常为4个)。 (2)各油腔之间开有回油槽。 ( 3 )用过的油一部分从这些回油槽流回油箱(径向 回油),另一部分则由两端流回油箱(轴向回油)。 ( 4 )油腔四周形成适当宽度的轴向封油面和周向封 油面,它们和轴颈之间的间隙一般为0.02~0.04mm。 (5)油泵供油压力为ps,油液经节流器T进入各油腔,
振垫支承,抗振性好。
生产多台,在世界多个国家广泛使用。
7
Ex-Cell-O公司的2m镜面立式车床
1976年研制。主要用于加工直径达 2m的金属反射镜。 采用双半球结构空气轴承主轴的II-G型卧式车床,和用
端面止推及半球空气轴承主轴结构的 II-B 型立式车床。
轴 承 径 向 跳 动 为 0.10~0.13μm , 端 面 圆 跳 动 为 0.15~0.18μm , 2000r/min 运转 8h 的温升在 5.6 ℃ 以内,径 向刚度为361N/μm。
3
• 空气轴承(又称为气浮轴承)指的是用气体(通常是空气,但也有可能是其
它气体)作为润滑剂的滑动轴承。空气比油粘滞性小,耐高温,无污染,因 而可用于高速机器、仪器及放射性装置中,但其负荷能力比油低。 空气轴承
分为三大类:空气静压轴承、空气动压轴承和挤压膜轴承。在一般工业中,
空气静压轴承用得较广泛。
装式CNC装置和激光干涉测长仪,精确测量定
位,在 DC 伺服机构内装有压电微位移机构, 实现纳米级微位移。
世界公认技术水平最高、精度最高的大 型金刚石超精密车床之一。
10
大型光学金刚石车床LODTM
1984年由美国LLL实验室联合研制。可加工
φ1625mm×500mm、重量1360kg的大型金属反射
• 影响回转精度的因素: (1)轴承精度和间隙的影响。
(2)主轴、支承座等零件中精度的影响。
16
滑动轴承的分类
• 按滑动轴承工作时轴瓦和轴颈表面间呈现的摩擦状态,滑动
轴承可分为:
液体摩擦轴承 液体动压润滑轴承
非液体摩擦轴承
液体静压润滑轴承
• 按滑动轴承承受载荷的方向可分为: 径向滑动轴承(向心)
2
4.1 精密和超精密机床发展概况及典型机床简介
一、发展概况
精密机床是实现精密加工的首要基础条件。 • 美国:50年代首先发展了金刚石刀具的超精密切削技术,并发展了相应的空气轴承主 轴的超精密机床;1983~1984研制成功大型超精密金刚石车床DTM-3型和LODTM大型 超精密车床。 • 英国:1991粘研制成功大型超精密机床OAGM2500。
5.Leabharlann 6.因为不使用油,不存在密封和泄露问题;
可靠性高,维护保养方便。
缺点: • 刚度低,承载能力不如液体静压轴承高,主要用于中、小型超精密加
工机床。
24
圆柱径向轴承和端面止推空气静压轴承
结构与液体静压轴承主轴结构基本相 同,只是节流孔和气腔大小形状不同。要 求有很高的同轴度和垂直度。 1 号车床的径向轴承的轴套制成外面 鼓形,能自动调整定心。轴套的外表面做 凸形球面,与轴承盖及轴承座上的凹形球 面相配合。当轴变形时,轴套可以自动调 整位置,从而保证轴颈与轴鼓为面接触。 用多孔石墨的轴衬代替小节流孔。 Union Carbide 半球车床
三、典型超精密机床简介 Union Carbide 半球车床
1962 年研制。采用空气静压轴承, 立式结构。能加工直径 100mm的半球,达 到 尺 寸 精 度 正 负 0.6μm , 表 面 粗 糙 度 0.025μm。 精密空气轴承主轴采用多孔石墨制 成轴衬,径向空气轴承的外套可以调整 自动定心,可提高前后轴承的同心度, 以提高主轴的回转精度。回转精度达到
•
• •
早期用滚动轴承(1μm,Ra0.04-0.02μm,高精度制造困难)
液体静压轴承(0.1μm,转动平稳无振动) 空气静压轴承
15
一、液体静压轴承主轴 主轴回转精度
回转精度——在主轴空载手动或机动低速旋转情 况下,在主轴前端安装工件或刀具的基面上所测 得的径向跳动、端面跳动和轴向窜动的大小。
12
AHN1O型高效专用车削、磨削超精密机床
由日本TOYOTA公司研制。用于加工塑料高精密透镜的金属模。 有一个x和y向调整的刀架及作B轴转动的高精度转台,借助三轴精密数控, 可加工平面、球面和非球曲面。 采用空气轴承,加工直径φ100mm ,刀架设计滑板结构,直线移动分辨力 0.01μm,激光测量反馈,定位精度全行程0.03μm。
•
日本:在声、光、图像、办公设备中的小型、超小型电子和光学零件超精密加工技术
方面更加先进和具有优势,在中小型超精密机床生产上基本与美国并驾齐驱,甚至超 过了美国。
• •
欧洲其它国家:如德国、瑞士、法国、意大利等的超精密机床水平也很高。 中国:与国外差距很大。70年代末有长足进步,80年代中期出现了具有接近世界水平 的超精密机床及部件,如:JCS-027超精密车床、JCS-031超精密铣床、JCS-035超 精密车床等。
精密和超精密加工技术
华南理工大学 陈松茂 讲师
第四章 精密和超精密加工的机床设备
本章主要提要
1.精密和超精密机床发展概况及典型机床简介 2.精密主轴部件
3.床身和精密导轨部件
4.进给驱动系统 5.微量进给装置 6.机床运动部件位移的激光在线检测系统 7.机床的稳定性和减振隔振 8.减少变形和恒温控制
加工模具形状精度0.05μm,表面粗糙度0.025μm。
13
我国金刚石超精密机床
14
4.2 精密主轴部件
精密主轴部件是超精密机床保证加工精度的核心。 • • • • • 能高速旋转; 高回转精度、高刚度、高稳定性、寿命长; 主轴本身及其驱动系统振动极小; 发热少,且热平衡性能好; 维护保养方便。 主轴关键是轴承。
11
OAGM 2500大型超精密机床
1991 年由英国 CUPE 公司和 SERC 公司联合研制。用于精密磨削和坐
标测量X射线天体望远镜的大型曲面
反 射 镜 , 最 大 加 工 尺 寸 2500mm×2500mm×610mm ,φ2500mm
高精度回转工作台。
机床的 x 和 y 向导轨采用液体静 压,z向的磨轴头和测量头采用空气 轴承。床身采用型钢焊接结构,用 精密数控驱动,双频激光测量系统 检测运动位置。
化和低温稳定处理;不锈钢、多孔石墨和轴承钢;此外
25
双半球空气轴承主轴
前后轴承均采用半球状,既
是径向轴承又是轴向轴承。由 于轴承的气浮面是球面,有自
动调心作用,可提高前后轴承
的同心度,提高主轴的回转精 度。
如: PG150S 型, F 承 载 =180Kg ,
刚度=350N/μm
26
前部用球形后部用圆柱径向空气轴承的主轴
球形一端同时起径向和轴向推力轴承作用,并有自动调心作用,提高前轴 承和后轴承的同轴度,提高主轴回转精度;圆柱一端提高刚度和承载能力。
有轴承内圈和外圈,外圈上有空 气的进出口空,内圈上有喷嘴。
4
二、超精密机床进一步发展的规划
1.
美国POMA计划 0.1μ m形状精度。已经实现。