五金件常用缺陷说明
五金常见不良分析

7尺寸偏差: 原因:模具定位有间隙; 改善措施:调整模具定位。
2020/5/17
一.冲压加工不良异常处理说明
8凸台拉破: 原因:a.模具存在问题; b.材质过硬; c.冲床速度过大; d.未加拉伸油;
改善措施:a.修改模具; b.更换材质; c.调整冲床速度; d.按时加拉伸油。
外形的厚度以完成各种形状复杂的成品,如端压,挤制,压印,压花等工作. 2.4.1端压:将材料的全体或一部份沿其长度方向压缩,以减少长度
而增大断面积. 2.4.2冲程能同时作数种单工程的工作,由于设计方式的不同又可区 2.4.3压花:将上下模作成凹凸花样,在几乎不改变材料厚度的情况
下, 使材料成凹凸断面. 2.4.4压印:压印与压花相似,但材料在加工后其厚度被改娈,
扭曲等工作 2.1.1一般弯曲:将平的毛胚冲制成弯曲件,如V形弯曲,U形弯曲. 2.1.2卷边:将平板料的边缘用一定半经弯曲在平顺的圆形.
2020/5/17
冲压加工工艺<五>
2.1.3扭曲:将平毛胚的一部份与另一部份相对的扭转一个角度,使 变成
曲线形的制件. 2.2抽制加工
将平板的材料变成任意有底无缝的容器,或将直径较大的有 底有缝
NO .2-56UNC -64UNC
NO .3-48UNC -56UNC
NO .4-40UNC -48UNC
NO .5-40UNC -44UNC
NO .6-32UNC -40UNC
NO .8-32UNC 2020/5/17 -36UNC
RH4 3
RH4 4
RH5 4
RH5 4
RH5 5
精密五金冲压件不良品常见问题及解决办法
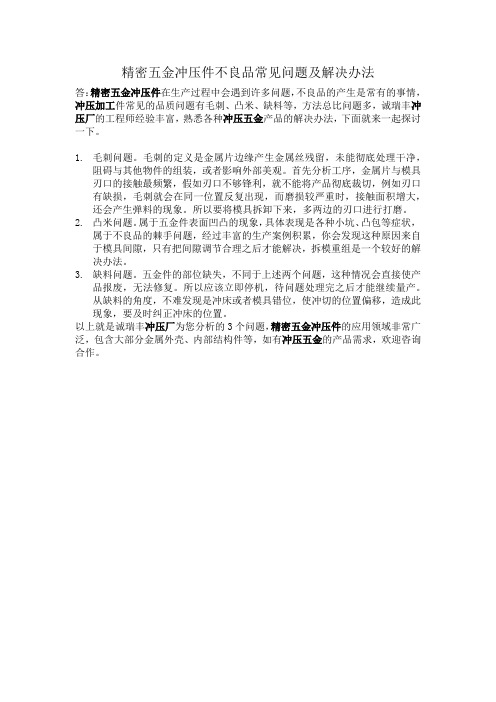
精密五金冲压件不良品常见问题及解决办法
答:精密五金冲压件在生产过程中会遇到许多问题,不良品的产生是常有的事情,冲压加工件常见的品质问题有毛刺、凸米、缺料等,方法总比问题多,诚瑞丰冲压厂的工程师经验丰富,熟悉各种冲压五金产品的解决办法,下面就来一起探讨一下。
1.毛刺问题。
毛刺的定义是金属片边缘产生金属丝残留,未能彻底处理干净,
阻碍与其他物件的组装,或者影响外部美观。
首先分析工序,金属片与模具刃口的接触最频繁,假如刃口不够锋利,就不能将产品彻底裁切,例如刃口有缺损,毛刺就会在同一位置反复出现,而磨损较严重时,接触面积增大,还会产生弹料的现象。
所以要将模具拆卸下来,多两边的刃口进行打磨。
2.凸米问题。
属于五金件表面凹凸的现象,具体表现是各种小坑、凸包等症状,
属于不良品的棘手问题,经过丰富的生产案例积累,你会发现这种原因来自于模具间隙,只有把间隙调节合理之后才能解决,拆模重组是一个较好的解决办法。
3.缺料问题。
五金件的部位缺失,不同于上述两个问题,这种情况会直接使产
品报废,无法修复。
所以应该立即停机,待问题处理完之后才能继续量产。
从缺料的角度,不难发现是冲床或者模具错位,使冲切的位置偏移,造成此现象,要及时纠正冲床的位置。
以上就是诚瑞丰冲压厂为您分析的3个问题,精密五金冲压件的应用领域非常广泛,包含大部分金属外壳、内部结构件等,如有冲压五金的产品需求,欢迎咨询合作。
五金常见不良汇总1

冲压每个工序间的操作、摆放 因操作不当而发生。
常见五金不良
(四)变
定 义: 产品在冲压或摆放流向过程中,因受模具的变异或碰撞造成 外观整体或局部发生不规则的形态变化. 图 片:
部品受外力碰撞 引起变形
形
OK样品形 状
常见五金不良
(四)变 形
一般产生原因: 1.作业员在产品摆放及装箱时,杂乱堆压。 2.作业员放入模具管位不到位。 3.模具在生产过程中,结构发生变异。送料不到位。 不良影响: 1.严重影响客户组装功能。 2.影响外观。 预防措施: 1、作业员现场操作时产品摆放及装箱,不要用力碰撞部品 或滑拉. 2.放入模具要放到位。 3.遵守自检指引,发现异常即时停止作业向上反馈。 易发生变形的工序: 扎边各个工序。
具内的料屑)在重压下产生的痕迹. 一般压印在非正 表面,且无明显凹凸可以接收
图 片:
模具内有铁屑 未清除致压印 OK品
常见五金不良
(一)压 印
一般产生原因:
1、来料在未加工前就因来料表面不良。 2、原材料待加工部品表面附有脏物,在冲压时产生。
3、模具内的顶针有磁性或顶针弹簧不够,易带铁屑在模具
表面受压下一个部品时产生. 4、模具间隙过小,长时间的生产产生料屑堆积模具内产生 不良. 5、加工周围环境空气含有尘粒,流入模具产生不良。
3.作业员按标准作业方式操作,避免只求数量,一味蛮干;部
品一定要放入到管位。
易发生尺寸超差的工序:扎形工序、冲孔工序
常见五金不良
(七)生 锈
定 义: 又称氧化,是指物体在高温高湿环境下,或受盐、碱等腐蚀
物质的影响,腐蚀物体外表面保护层,表层被 破坏,生成点状、
块状、变色等不良现象.
图 片:
五金件及烤漆常见不良现象及原因分析

不良現象
雜質 磨印 油點
烤漆常見不良缺陷原因分析
不良現象分析
1. 涂料﹑溶濟中含有雜質 2. 噴涂車間室內空氣中含塵量過大﹐及用于擦試清潔之布帶有毛線﹐這些灰塵及毛線 隨空氣流動及受噴涂時靜電的吸附于產品表面﹐導致產品表有細小之顆粒狀及線狀之 雜質 3. 通風系統過濾不徹底
因沖壓時產品有凹凸痕﹐表面進行維修打磨時﹐打磨粗糙﹐正常噴涂后不能完全 遮蓋打磨部分﹐導致烤漆后出現印痕 1. 空壓機壓縮空氣時﹐產生水份及機械油污干燥機過濾不徹底隨氣壓混入油漆中﹐ 噴涂于產品上形成﹐
4. 噴房室內溫度過高﹐油漆噴涂與產品上后﹐溶劑揮發太快﹐導至表面桔皮
1. 速度過快﹐治具晃動﹐導致噴槍噴不到位及不均勻
2. 生產時間過長﹐槍內管道堵塞﹐噴涂不均勻
1. Disc噴涂升降機上下點位置太底或高 2. DISC噴涂房內軌道上轉向器安裝位置不當﹐導致噴涂時面與面噴涂不均勻﹐少漆 。 3. 涂料濃度進高﹑噴涂靜電偏小﹐導致邊角部分少漆
1. 產品重工次數過多﹐膜厚過厚(120um以上)
2. 涂料中樹脂聚合不當﹐溶劑與油漆不相溶
3. 油漆太濃﹑噴涂壓力過大﹑距離近
不良現象 壓傷
刮傷
變形 尺寸不良
氧化 模痕 毛刺
五金常見不良缺陷原殘留于模具內﹐再次沖壓時壓于產品表面﹐導致產 品表面損傷﹐出現凹或凸出之痕跡。 2. 原材料本身凹凸痕 1. 作業員作時﹐作業動作不規范,傳送過程中碰刮模具及工作台邊角尖銳部分﹐導致 產品表面損傷。 2. 工作台面粗糙不清潔 3. 送料機送料時因調整不當引起產材料表面磨傷﹑擦傷 4. 制程中產品裸疊及包裝時產品之間相互碰刮引起表面刮傷。 1. 產品沖壓時﹐模具折邊擠壓或避位不夠導致變形 2. 操作員作業不小心,產品碰﹑摔造成 3. 產品包裝方式不正確擠壓所至 1. 產品沖壓時﹐模具定位不准及模高不正確 2. 模具設計尺寸達不到 1. 受高溫﹑高濕天氣的影響﹐車間空氣濕度過高﹐產品與空氣中的氧分子發生化學 反映。 2. 作業員作業時未確實戴好手套﹐手汗中的鹽﹑與水與產品發生氧化發映。 3. 生產排程變異,庫存時間太長 1. 模具擠壓造成 2. 材質因素 1. 模具刀口鈍化 2. 模具閉模間隙過大
五金件缺陷定义
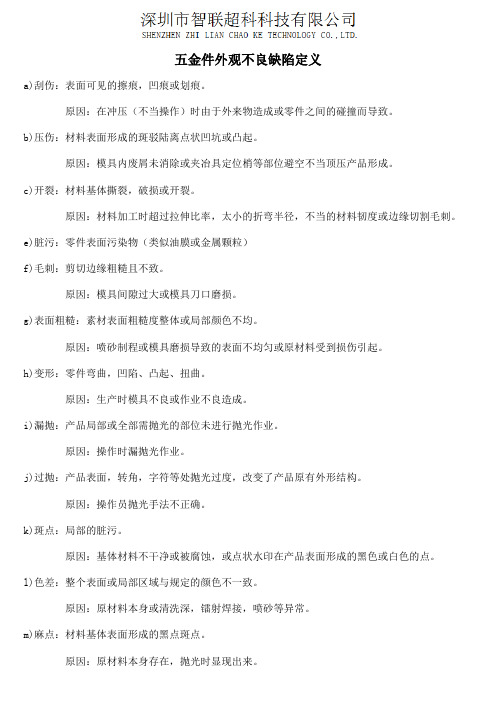
五金件外观不良缺陷定义
a)刮伤:表面可见的擦痕,凹痕或划痕。
原因:在冲压(不当操作)时由于外来物造成或零件之间的碰撞而导致。
b)压伤:材料表面形成的斑驳陆离点状凹坑或凸起。
原因:模具内废屑未消除或夹冶具定位梢等部位避空不当顶压产品形成。
c)开裂:材料基体撕裂,破损或开裂。
原因:材料加工时超过拉伸比率,太小的折弯半径,不当的材料韧度或边缘切割毛刺。
e)脏污:零件表面污染物(类似油膜或金属颗粒)
f)毛刺:剪切边缘粗糙且不致。
原因:模具间隙过大或模具刀口磨损。
g)表面粗糙:素材表面粗糙度整体或局部颜色不均。
原因:喷砂制程或模具磨损导致的表面不均匀或原材料受到损伤引起。
h)变形:零件弯曲,凹陷、凸起、扭曲。
原因:生产时模具不良或作业不良造成。
i)漏抛:产品局部或全部需抛光的部位未进行抛光作业。
原因:操作时漏抛光作业。
j)过抛:产品表面,转角,字符等处抛光过度,改变了产品原有外形结构。
原因:操作员抛光手法不正确。
k)斑点:局部的脏污。
原因:基体材料不干净或被腐蚀,或点状水印在产品表面形成的黑色或白色的点。
l)色差:整个表面或局部区域与规定的颜色不一致。
原因:原材料本身或清洗深,镭射焊接,喷砂等异常。
m)麻点:材料基体表面形成的黑点斑点。
原因:原材料本身存在,抛光时显现出来。
二十种五金件喷漆作业中常见的缺陷及处理方法,收藏备查!
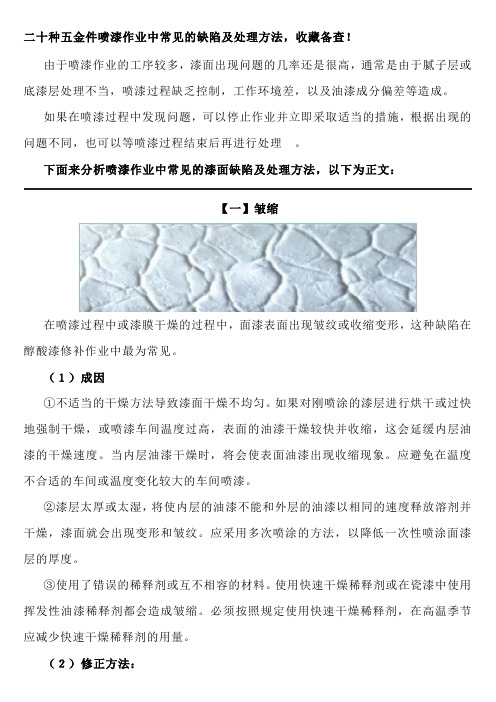
二十种五金件喷漆作业中常见的缺陷及处理方法,收藏备查!由于喷漆作业的工序较多,漆面出现问题的几率还是很高,通常是由于腻子层或底漆层处理不当,喷漆过程缺乏控制,工作环境差,以及油漆成分偏差等造成。
如果在喷漆过程中发现问题,可以停止作业并立即采取适当的措施,根据出现的问题不同,也可以等喷漆过程结束后再进行处理。
下面来分析喷漆作业中常见的漆面缺陷及处理方法,以下为正文:【一】皱缩在喷漆过程中或漆膜干燥的过程中,面漆表面出现皱纹或收缩变形,这种缺陷在醇酸漆修补作业中最为常见。
(1)成因①不适当的干燥方法导致漆面干燥不均匀。
如果对刚喷涂的漆层进行烘干或过快地强制干燥,或喷漆车间温度过高,表面的油漆干燥较快并收缩,这会延缓内层油漆的干燥速度。
当内层油漆干燥时,将会使表面油漆出现收缩现象。
应避免在温度不合适的车间或温度变化较大的车间喷漆。
②漆层太厚或太湿,将使内层的油漆不能和外层的油漆以相同的速度释放溶剂并干燥,漆面就会出现变形和皱纹。
应采用多次喷涂的方法,以降低一次性喷涂面漆层的厚度。
③使用了错误的稀释剂或互不相容的材料。
使用快速干燥稀释剂或在瓷漆中使用挥发性油漆稀释剂都会造成皱缩。
必须按照规定使用快速干燥稀释剂,在高温季节应减少快速干燥稀释剂的用量。
(2)修正方法:在油漆充分干燥后,清除皱缩漆面,重新进行喷漆。
【二】隆起也称为浮皱。
在喷漆过程中或漆膜干燥的过程中,由于漆面膨胀而在部分区域形成的隆起,可能呈现出不同的形状。
(1)成因①使用了错误的稀释剂。
在瓷漆中使用挥发性油漆稀释剂会促进内部油漆层的隆起,最终导致面漆层的隆起。
②使用了互不相容的原料。
新喷涂的漆层与原有漆层发生了化学反应,或原有漆层的缺陷没有被妥善处理,漆层之间脱离从而造成面漆层的隆起。
③底层没有进行彻底地清洁,例如底层表面的油脂或蜡质物没有彻底清除,由于夹层效应的影响,导致再喷涂的油漆无法附着。
④二次喷涂的间隔时间太短,没有给予底层油漆充分的干燥时间,导致湿漆面中的溶剂侵蚀中涂底漆或面漆使之变软。
家具五金的质量标准和缺陷术语
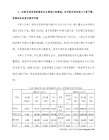
(12)扭拧:指型、管棱角线、型材和棒材绕其纵轴发生扭转,严重时形成麻花状或螺旋状。
(13)切斜 :指管、棒、材等锯切后,端面与纵面轴线不垂直。
(14)端面不齐:指箔卷两端面层与层之间发生串动,使箔卷端面不平齐。
(15)不成形:指模锻件的凸出部分、圆角、筋顶等处没有完全充满,造成尺寸不足。
(14)油迹:指加工材表面有油或油类物质干燥后所形成的点状、条状和片状的连续或不连续的油膜痕迹。油迹使材料表面失去本来的颜色,其色泽因金属不同而异。
(15)水迹:指产品表面的残水蒸发干燥后留下的痕迹。以点状、条状或片状的连续或不连续地存在于制品的表面,使表面失去本来的颜色。
(16)酸迹:指板、带、棒材等表面存在着不规则的残酸腐蚀斑迹。使表面失去原本的金属光泽。
家具五金的质量标准和缺陷术语
1.外形尺寸缺陷:
(1)尺寸超差:指有色金属加工产品的实际外形尺寸超出标准规定的允许偏差范围。
(2)厚度不均:指板、带、箔材的横断面及纵断面的厚度不均匀。
(3)壁厚不均:指管材在同一横截面上各方面的管壁厚度不一致。
(4)椭圆圆度:椭圆是指产品(圆管、圆棒、盘条、线材等)同一横截面上各方面直径不等。圆度是用同一横截面上最大与最小的直径之差来表示。
(17)矫直痕迹:指管、棒经辊式矫直(或压力矫直)时,表面呈现螺旋状痕迹或比较大的圆滑凹下缺陷。辊矫产品螺旋状痕迹轻重不同,轻至感觉不到,重至直径超差。
(18)拉痕:指线材表面沿纵向呈现沟痕。
(19)箔材表面印痕:箔材表面常出现各种印痕,如麻点、辊印、凹坑、凸点等。有的一面凸起而相对一面凹下,个别的出现断续或周期的印痕。
(5)起皮:指加工表面有明显的金属结构分离的薄层,呈现出条状、舌状、鱼 鳞片状或指甲状的翘起薄片。有的与金属本体相连的,压合到表面不易脱落。起皮的断面上呈黑线或黑带状,严重时,其分离处一般有用肉眼可见的夹杂物。
五金冲压缺陷分析
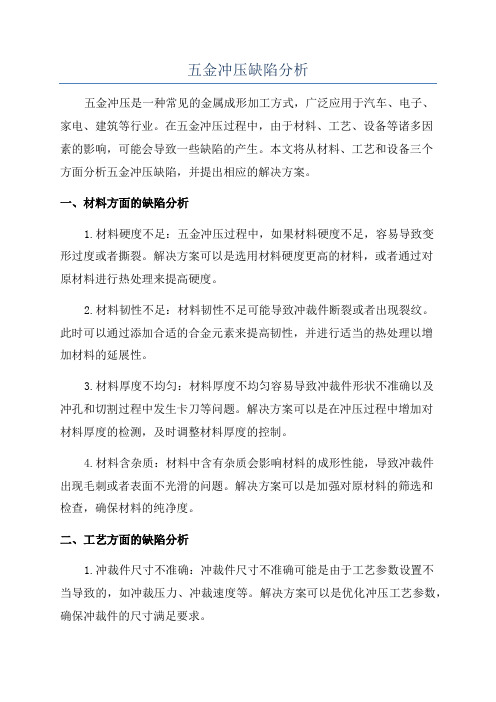
五金冲压缺陷分析五金冲压是一种常见的金属成形加工方式,广泛应用于汽车、电子、家电、建筑等行业。
在五金冲压过程中,由于材料、工艺、设备等诸多因素的影响,可能会导致一些缺陷的产生。
本文将从材料、工艺和设备三个方面分析五金冲压缺陷,并提出相应的解决方案。
一、材料方面的缺陷分析1.材料硬度不足:五金冲压过程中,如果材料硬度不足,容易导致变形过度或者撕裂。
解决方案可以是选用材料硬度更高的材料,或者通过对原材料进行热处理来提高硬度。
2.材料韧性不足:材料韧性不足可能导致冲裁件断裂或者出现裂纹。
此时可以通过添加合适的合金元素来提高韧性,并进行适当的热处理以增加材料的延展性。
3.材料厚度不均匀:材料厚度不均匀容易导致冲裁件形状不准确以及冲孔和切割过程中发生卡刀等问题。
解决方案可以是在冲压过程中增加对材料厚度的检测,及时调整材料厚度的控制。
4.材料含杂质:材料中含有杂质会影响材料的成形性能,导致冲裁件出现毛刺或者表面不光滑的问题。
解决方案可以是加强对原材料的筛选和检查,确保材料的纯净度。
二、工艺方面的缺陷分析1.冲裁件尺寸不准确:冲裁件尺寸不准确可能是由于工艺参数设置不当导致的,如冲裁压力、冲裁速度等。
解决方案可以是优化冲压工艺参数,确保冲裁件的尺寸满足要求。
2.裂纹、断裂:由于冲裁压力过大或者冲裁件的形状设计不合理,可能会导致冲裁件出现裂纹或者断裂。
解决方案可以是调整合适的冲裁压力和速度,并优化冲裁件的形状设计。
3.表面不光滑:冲裁过程中可能会出现毛刺和划痕等表面缺陷。
解决方案可以是优化冲裁模具的设计,避免刺激到材料的表面,同时可以在冲压过程中添加润滑剂,减少摩擦。
三、设备方面的缺陷分析1.模具磨损:由于长时间使用或者工作条件不合理,冲压模具可能会出现磨损问题。
解决方案可以是定期对冲压模具进行维护和检查,及时更换磨损严重的模具。
2.设备不稳定:设备本身的不稳定性可能导致冲裁过程中发生偏移、错位等问题。
解决方案可以是定期对设备进行维护和调整,保证设备的稳定性。
金属常见加工工艺缺陷的特征、原因、影响及措施

度下,金属再结晶退火加热温度过高或时间过长所致。晶粒粗大或粗细不均会导致在变形量较 大的部位产生裂纹,且裂纹多沿粗细混晶交界区择优分布。
三.由于材料成分、性能不合格
1.成分不合格 冷冲用钢板的化学成份应严格控,特别是碳、硫、磷元素极为重要。碳元素在钢中形成渗
2.带状组织 钢中带状组织是由铁素体和珠光体相间分布组成。它是由于碳、磷、硫晶间偏析,在热压
力加工中使之沿着金属变形方向被拉长,呈带状分布的夹杂物。 由于带状组织的取向平行于钢材轧制方向,而铁素体和珠光体的强度及塑性差异悬殊,因
此,冷冲时当钢件的变形方向与钢板带状组织相垂直,容易产生拉裂和撕裂。由于钢板带状组 织引起的冲裂,裂纹平行于钢板轧制方向,裂纹粗大,显微观察时裂纹多沿珠光体边缘分布、 取向平行于带状组织。
3.鳞片状毛刺
以较低或中等切削速度切削塑性金属时,加工表面往往会出现鳞片状毛刺,尤其对圆孔采 用拉削方法更易出现,若拉削出口毛刺没有去除,则将成为使用中应力集中的根源。
4.“R”加工过小
零件拐角半径小,尤其是横截面形状发生急骤的变化,会在局部发生应力集中而产生微裂 纹并扩展成疲劳裂纹,导致疲劳断裂。
3.涡流
金属在锻造过程中由于剧烈的热变形使金属组织发生晶粒结晶重新定向排列,形成结晶织 构和金属中的非金属夹杂物、树枝晶偏析、第二相质点等沿热加工方向形变延伸呈带状分布, 形成了锻件的纤维状组织即锻造流线。
产生的原因主要是表面氮浓度富集,化合物虽连续粗大网络状分布。在磨削时倾向于脱落 的氮化层的显微结构特点是沿奥氏体晶界存在稠密的网状氮化物,它的存在使晶格畸变加剧, 在位错与晶界处三向应力增大,在磨削力、热应力及组织应力的作用下,粗大的氮化物网络边 界区切口效应敏感性增大,造成综合应力叠加,当这种应力超过渗层的强度极限时,即产生脆 性破裂与剥落。当晶界强度大于晶内强度时,则裂纹沿晶扩展产生脆裂及剥落;当晶界强度等 于晶内强度时,则裂纹的扩展呈穿晶脆裂及剥落。
五金部品缺陷定义和判定基准(20080707)
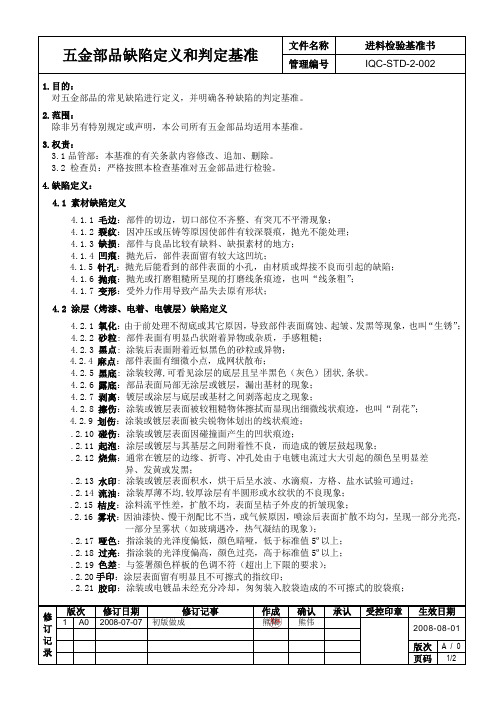
.2.15桔皮:涂料Байду номын сангаас平性差,扩散不均,表面呈桔子外皮的折皱现象;
.2.16雾状:因油漆快、慢干剂配比不当,或气候原因,喷涂后表面扩散不均匀,呈现一部分光亮,一部分呈雾状(如玻璃遇冷,热气凝结的现象);
.2.17哑色:指涂装的光泽度偏低,颜色暗哑,低于标准值5º以上;
4.2.5黑底:涂装较薄,可看见涂层的底层且呈半黑色(灰色)团状,条状。
4.2.6露底:部品表面局部无涂层或镀层,漏出基材的现象;
4.2.7剥离:镀层或涂层与底层或基材之间剥落起皮之现象;
4.2.8擦伤:涂装或镀层表面被较粗糙物体擦拭而显现出细微线状痕迹,也叫“刮花”;
4.2.9划伤:涂装或镀层表面被尖锐物体划出的线状痕迹;
.2.18过亮:指涂装的光泽度偏高,颜色过亮,高于标准值5º以上;
.2.19色差:与签署颜色样板的色调不符(超出上下限的要求);
.2.20手印:涂层表面留有明显且不可擦式的指纹印;
.2.21胶印:涂装或电镀品未经充分冷却,匆匆装入胶袋造成的不可擦式的胶袋痕;
5.判定基准:
.2.10碰伤:涂装或镀层表面因碰撞面产生的凹状痕迹;
.2.11起泡:涂层或镀层与其基层之间附着性不良,而造成的镀层鼓起现象;
.2.12烧焦:通常在镀层的边缘、折弯、冲孔处由于电镀电流过大大引起的颜色呈明显差
异、发黄或发黑;
.2.13水印:涂装或镀层表面积水,烘干后呈水波、水滴痕,方格、盐水试验可通过;
4.1.2裂纹:因冲压或压铸等原因使部件有较深裂痕,抛光不能处理;
4.1.3缺损:部件与良品比较有缺料、缺损素材的地方;
4.1.4凹痕:抛光后,部件表面留有较大这凹坑;
五金模具表面处理常见缺陷分析和消除措施
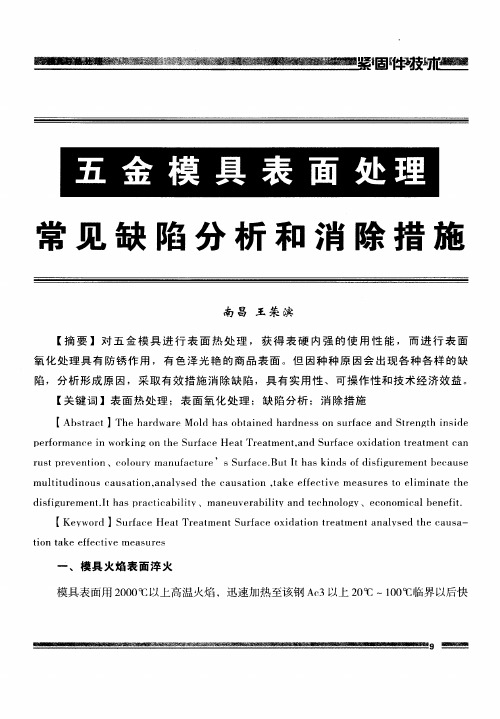
淬火模具不受体积大小 限制 ,可局部
淬硬 ; 淬火畸变小 , 淬火表面清洁无氧化 、 脱
碳;
成本低 、易上 马 、生产效率高 。
经验和最佳工艺参数后投产 ;
仔细观察火色 ,控制淬火加热温度 。 火焰表 面淬火后应及时在 2 0C± 1 0 ̄ 0 ℃ X1 h —2 低温 回火 , 消除淬火 内应力 , 避 免淬裂。
陷 , 分 析 形 成 原 因 , 采 取 有 效 措 施 消 除 缺 陷 ,具 有 实 用 ・ 可 操 作 性 和 技 术 经 济 效 益 。 性、 【 键 词 】表 面 热 处 理 ;表 面 氧 化 处 理 ;缺 陷 分 析 ; 消 除 措 施 关
【 bt c 】 h ad aeM l h s ban dh rn s o ufc n t n t is e A s a t T eh rw r od a o tie ad es nsr ea dSr gh n i r a e d
移 动速 度
1 65
/ m . i m m n
l5 4
1 25
11 0
10 O
9 0
8 0
到该钢 临界温度 A 3 t 以上 1 0 10 0℃ 5 ℃高
温奥 氏体 状 态 ,然 后 急速 冷却 淬火 ,实
模具感应 加热表面淬火 常见 缺陷及防
治措 施 :
2淬硬层 深度不易控制 、受热不均 . 匀、 硬度不均匀 , 主要靠实践经验控制淬 火质量。
防治措施 : 选用精炼钢 、电渣重熔钢或真空熔炼
钢。 它们具有纯度高 、 杂质少 、 晶粒细 、 碳
五金不良培训

(八)起 皱
定 义:
指产品的边缘表面有皱纹现象 。
图 片:
起皱
起皱 图 7
一般产生原因: 1. 压边力太小、压边力不均匀; 2. 凸凹模间隙过大; 3. 凹模圆角半径太大; 4. 材料表面有颗粒状杂物等都将导致工件起皱。
起皱不良影响: 严重影响产品的外观或增加抛光成本,严重时产品报废。
(九)R位偏大或偏小或不均匀
严重影响产品的外观或增加抛光成本,严重时产品报废。
(十)牙位偏深或偏浅
定 义:
指产品的牙位的凹凸痕迹过浅、过深。
牙位偏浅 图 片:
一般产生原因:
1、弹力胶胆力造成材料受力不均牙位深浅不均;
2.冲压机台调试参数大小冲压行程过浅(材料受力不均)造成。
3. 上下模不同心造成模具间隙不均导致材料受力不均造成。 4. 一次拉伸弧度不够或深度程度不够,造成二次成型时有裂痕。
3.在生产过程中,模具/夹具弹簧弹力不均匀。脱料弹力小。
(六)裂 痕/拉伤
定 义:
指产品的表面有破裂的痕迹或迹象 。
图 片: 裂痕 裂痕
一般产生原因:
1、上模R位处R角小(凸凹模圆角半径太小)的模具的崩裂造成的 2.模具/夹具模具间隙偏小(间隙太小,摩擦阻力太大)造成;
3. 上下模不同心、不平行。
一般产生原因:
1. 模具/夹具设计不完善、模具/夹具磨损/老化, 2. 产品在模具/夹具可能发生管位/定位松、断公或爆模的不良, 3. 作业员未按作业指导书的正确方法操作,会发生不良 4. 在前工序的来料(半成品)尺寸即以起差,受其影响,致本工 序尺寸不良. 5. 铝/冲压、加工---减料过程 ---抛光/研磨---减料过程 ---氧化的影响
(五)变 形
五金件及烤漆常见不良现象及原因分析

不良現象 壓傷
刮傷
變形 尺寸不良
氧化 模痕 毛刺
五金常見不良缺陷原因分析
不良現象分析 1. 沖壓時﹐模具切除之廢料反彈殘留于模具內﹐再次沖壓時壓于產品表面﹐導致產 品表面損傷﹐出現凹或凸出之痕跡。 2. 原材料本身凹凸痕 1. 作業員作時﹐作業動作不規范,傳送過程中碰刮模具及工作台邊角尖銳部分﹐導致 產品表面損傷。 2. 工作台面粗糙不清潔 3. 送料機送料時因調整不當引起產材料表面磨傷﹑擦傷 4. 制程中產品裸疊及包裝時產品之間相互碰刮引起表面刮傷。 1. 產品沖壓時﹐模具折邊擠壓或避位不夠導致變形 2. 操作員作業不小心,產品碰﹑摔造成 3. 產品包裝方式不正確擠壓所至 1. 產品沖壓時﹐模具定位不准及模高不正確 2. 模具設計尺寸達不到 1. 受高溫﹑高濕天氣的影響﹐車間空氣濕度過高﹐產品與空氣中的氧分子發生化學 反映。 2. 作業員作業時未確實戴好手套﹐手汗中的鹽﹑與水與產品發生氧化發映。 3. 生產排程變異,庫存時間太長 1. 模具擠壓造成 2. 材質因素 1. 模具刀口鈍化 2. 模具閉模間隙過大
油點 噴漆不均
異色 溢漆 少漆 桔皮 咬花不良
2. 噴漆池循環水濺于產品一
3. 素材表面油污未清洗干淨
1. 烤漆線上懸挂產品之吊盤轉動不靈活
2. DISC自動噴涂上下定位不佳
3. 噴漆技朮員作修補噴涂時﹐手補動作不均勻﹐導致表面噴漆不均 1. 涂料中顏料密度不同﹐密度大的下沉﹐輕的上浮于表面﹐噴涂后產品表面形成異 色。 2. 換機種生產是﹐噴涂設備清洗不干淨﹐不同顏色的油漆混合在一起噴涂于產品表 面上形成 1. 作業員將產品挂于治具上時﹐產品未有與治具完全密合 2. 治具因搬運﹑積漆過厚除漆時不正當的作業使治具變形﹐當產品挂在治具上時﹐ 導致產品與治具無法密合 3. 產品噴涂時﹐靜電過大﹐導致不需要噴涂的區域因受靜電的吸附溢漆
五金冲压缺陷分析

五金冲压缺陷分析
金属冲压是金属制品加工工艺中非常常见的一种加工,其加工的效率极高,精度也比较高,但是由于运动精度的限制和材料的本身特性,冲压过程中往往会出现不同的缺陷,严重影响了冲压件的性能和特性,因此有必要进行缺陷的准确分析,以提高冲压件的质量。
一、冲裁缺陷
1.错配缺陷:指的是由于模具的尺寸偏差造成的冲压件的尺寸偏差,从而影响其它部件的安装。
2.冲裂缺陷:指的是材料在冲压过程中没有得到充分的成形,或者模具的尺寸设计不当、材料的屈服点过高等原因,导致金属板料在冲裁过程中裂开。
3.冲凹缺陷:指的是在冲压过程中,模具与工件之间的贴合不够,从而造成冲压件本身的凹陷。
4.冲松缺陷:指的是冲压件材料的屈服应力不足,或者模具与工件之间的尺寸偏差太大,从而使冲压件本身的紧固强度不足。
二、压花缺陷
1.波纹缺陷:指的是材料在压花过程中,因模具的不平整或材料本身的特性,而出现不完全的压出,形成了波纹缺陷。
2.破裂缺陷:指的是在压花过程中,由于模具的尺寸偏差、材料的屈服强度过高、制造工艺错误等原因,导致材料在压花过程中破裂。
常见五金产品加工工艺及缺陷分析-精
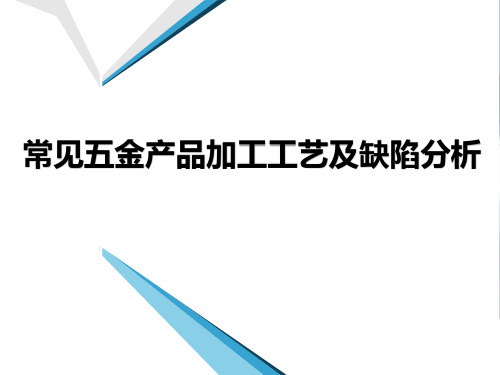
常见五金产品加工工艺及缺陷分析 add your subheading
五金产品常见工艺
1
冲压(3-19页)
2
机加(20-36页)
3
螺丝(37-48页)
2
冲压工艺及常见缺陷分析
冲压 :
金属塑性加工方法之一,又称板料冲压。在压 力作用下利用模具使金属板料分离或产生塑性变 形,以获得所需工件的工艺方法。
高的孔时,通常用镗床进行
镗削加工。在镗床上除进行
镗孔外,还可完成铣端面、
钻孔、攻丝、车外圆和端面
等多种工作。
1-后支承 2-后立柱 3-工作台 6-径向导轨 7-前立柱 8-主轴箱 11-下滑座 12-上滑座
4-镗轴 9-尾筒
5-平旋盘 10-床身
25
机械加工工艺及常见缺陷分析
镗削加工方式:
26
机械加工工艺及常见缺陷分析
b.涂油润滑过多。 c.送料外滑块调整不当造成倾斜,致 使各处压料面受力不均,送的区域易 起皱。 d. 压料面接触不还,严重时造成里松 内紧。
19
机械加工工艺及常见缺陷分析
切削加工:
又称为冷加工。利用切削刀具在切削机床上(或用手工)将金属 工件的多余加工量切去,以达到规定的形状、尺寸和表面质量的工 艺过程。
冲压常见缺陷:
18
冲压工艺及常见缺陷分析
冲压常见缺陷:
影响:失去产品某种特定功能 原因:a.局部毛坯受到的拉应离力超过了强
度极限。 b.材料偏厚或毛坯表面锈蚀、划伤 过多。 c.材料放偏导致压料不均匀。 d.未合理的涂润滑剂导致进料困难。
影响:失去产品某种特定功能或干涉其他部件 原因:a.压料面阻力小,进料过多。
五金件外观检验标准

不可有
不可有
√
拉模
HT007
参照A(刮伤)
√
变形
HT008
不可有
不可有
不可有
√
材质不符
HT009
不可有
不可有
不可有
√
集油
HT010
参照限度样品
参照限度样品
参照限度样品
√
少油
HT011
参照限度样品
参照限度样品
参照限度样品
√
色差
HT012
参照限度样品
参照限度样品
参照限度样品
√
颗粒
(无明显手感)
HT013
B面在直径50mm内容许有面积≤1.2mm旳污痕1处;面积≤1mm旳污痕3处,两处中心点间距大于30mm,同一表面上总数不得大于3处;
C面在直径50mm内容许有面积≤1.2mm旳污痕1处;面积≤1mm旳污痕4处,两处中心点间距大于30mm,同一表面上总数不得大于4处;ABC三面不超过7处。
√
麻点
HT018
在直径50mm内容许有面积≤0.8mm颗粒1个;面积≤0.5mm2个,两点间距大于30mm,同一表面上总数不得大于2个。
在直径50mm内容许有面积≤0.8mm颗粒1个;面积≤0.5mm3个,两点间距大于30mm,同一表面上总数不得大于3个。
在直径50mm内容许有面积≤0.8mm颗粒1个;面积≤0.5mm4个,两点间距大于30mm,同一表面上总数不得大于4个。ABC三面不超过7处。
1、目旳:
2、本检查规范为了进一步提高五金制品旳质量,在产品成产及出厂时能严格把关,制定出适应我司旳五金件检查原则,为外观检查提供科学、客观旳措施。对某些无法用定量表白旳缺陷,用供需双方制定旳检查原则和封样旳措施加以解决。
常见缺陷的分类描述

常见缺陷的分类描述
3)未熔合
常见缺陷的分类描述
4) 夹渣
夹渣是在熔焊时所产生的金属氧化物或非金属夹杂物, 因来不及浮出表面,停留在焊缝内部而形成的缺陷,主要分 布在焊缝或焊缝熔合区。
常见缺陷的分类描述
夹钨:由于钨密度大于钢或铝,对射线吸收强,因此夹钨底
常见缺陷的分类描述
常见缺陷的分类描述
常见缺陷的分类描述
第一节 金属材料与构件中的
6.使用与维修中的常见缺陷现象
1)裂纹: 疲劳裂纹:工件在使用过程中承受交变应力作用产生 的裂纹。一般出现在工件的应力集中部位。 应力腐蚀: 2)摩擦腐蚀: 3)汽蚀:
常见缺陷的分类描述
常见缺陷的分类描述
4) 裂纹 金属液在铸型内冷却凝固收缩时,表面和内部冷 却速度不同产生很大的热应力而导致铸件破裂。多发 生在截面突变处。
图6-53 铸件裂纹照片
常见缺陷的分类描述
5) 冷隔
冷隔由浇铸温度偏低造成,金属熔液在铸模中不 能充分流动而造成的一类缺陷。一般分布在较大平面 的薄壁上或厚壁过渡区,铸件清理后有时肉眼可见。
常见缺陷的分类描述
2)缩孔和疏松 浇铸时局部温差过大,在
金属收缩过程中,邻近金属补 缩不良,产生缩孔或疏松。多 产生在铸件的冒口根部、厚大 部位、厚薄交界处和具有大面 积的薄壁处。
常见缺陷的分类描述
3) 夹砂与夹渣
夹砂是浇铸时由于型砂受 铸液的冲击掺入铸件内部而 形成的缺陷,它多半发生在 大型铸件和用刮板造型的铸 件上。夹渣则是浇铸时由于 浇铸液中的溶渣没有与浇铸 液分离开而进入铸件形成。
第一节 金属材料与构件中的
3. 焊缝中的常见缺陷现象
经典五金常见不良分析汇总

常见不良分析汇总
(2017年8月修编)
品管部培训教材
1
深圳西卡姆同位素有限公司
一个理念
产品的质量是设计、开发和生产 出来的,质量是在检验之前已经存在 。
同时在工序能力不稳定的情况下 ,产品质量又是检验控制出来的。
深圳西卡姆同位素有限公司
品质控制的首要任务
1、风险意识—风险就是不知道; 2、品质意识—第一次就做好; 3、执行力—责任。
其不良影响:
毛刺对后工序加工影响、装配组立与安全的影响。
品管部培训教材
26
深圳西卡姆同位素有限公司
预防措施:
1、保证模具设计,治具上对其间隙作出科学合理的计算及装配. 2、购买合适的原材料. 3、作业员工在开料时,可对每张料涂上合适的冲压油,在冲孔、
落料工序,对对模具内加一定的冲压油. 4、模具/夹具使用硬度强的模材。增加模具使用寿命。 5、生产技工牢固锁模块、调整机台行程参数并牢固螺母。
B 观察角度:被检测面与视线在45度范围内旋转左右转动15 度范围。
C 观察距离:人眼和被测物体表面距离为300-350㎜。 D 观察时间:≤10S E 视力:祼视或矫正视力在1.0以上且无色盲。
在此条件下,目测可见的不良现象认为是缺陷。
品管部培训教材
5
深圳西卡姆同位素有限公司
缺陷分级定义
A 严重缺陷/CRITICAL:有可能对使用者造成伤害或 有安全隐患的缺陷,造成产品不能使用缺陷或不符合产 品出厂配置要求的缺陷或严重影响主要性能指标,功能 不能实现的缺陷(漏工序、少装配件等)
易发生鼓包的工序:
冲压工序, 合金工序、 抛光工序、
品管部培训教材
24
深圳西卡姆同位素有限公司
五金件常用缺陷说明
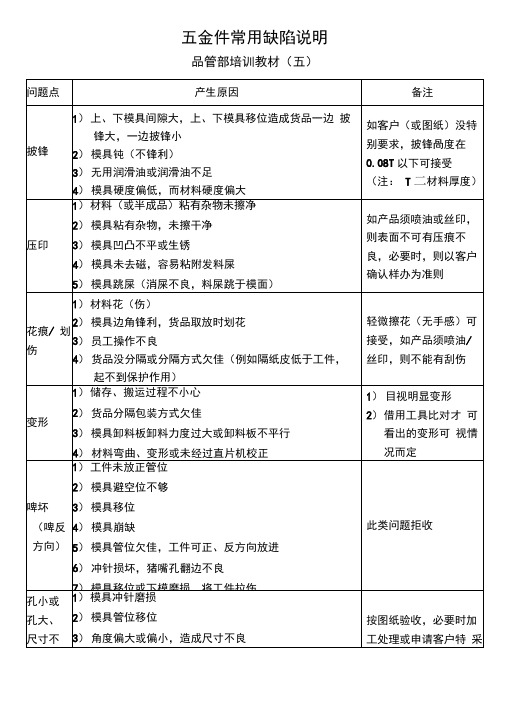
变形
1)储存、搬运过程不小心
2)货品分隔包装方式欠佳
3)模具卸料板卸料力度过大或卸料板不平行
4)材料弯曲、变形或未经过直片机校正
1)目视明显变形
2)借用工具比对才 可看出的变形可 视情况而定
啤坏
(啤反 方向)
1)工件未放正管位
2)模具避空位不够
2)拉伸不到底时,会影响下工序质量(如 冲孔容易变形或扭曲)
攻螺纹
1)漏攻牙
2)滑牙或牙紧
3)螺纹倾斜
4)螺纹孔有缺丝
5)攻牙未到底(上部有螺纹, 下部没螺纹)
1)注意货品之明示分隔是否清晰
2)员工操作方式正确或错漏
3)嗒牙管位是否良好(有否起到固定作 业)
4)使用牙规时,力度要适当,不能用狠劲
拨斜孔
1)检查根部尺寸与顶部尺寸时,分开检 测,不能单检测根部尺寸
2)如有字唛则须留意字体有否漏缺、清 晰,有否一边深一边浅
3)注意工件之摆放会否引致货品变形刮 花
4)留意工件是否正、反面方向都能放进模 具,有此情况须及时向上汇报
压延(深 拉伸)
1)拉伤(刮手)
2)R角位(或波位)爆裂
1)如须喷油货品,还须注意货品之分隔, 会否碰伤工作
2)模具粘有杂物,未擦干净
3)模具凹凸不平或生锈
4)模具未去磁,容易粘附发料屎
5)模具跳屎(消屎不良,料屎跳于模面)
如产品须喷油或丝印, 则表面不可有压痕不 良,必要时,则以客户 确认样办为准则
花痕/划伤
1)材料花(伤)
2)模具边角锋利,货品取放时划花
Байду номын сангаас3)员工操作不良
- 1、下载文档前请自行甄别文档内容的完整性,平台不提供额外的编辑、内容补充、找答案等附加服务。
- 2、"仅部分预览"的文档,不可在线预览部分如存在完整性等问题,可反馈申请退款(可完整预览的文档不适用该条件!)。
- 3、如文档侵犯您的权益,请联系客服反馈,我们会尽快为您处理(人工客服工作时间:9:00-18:30)。
1)储存、搬运过程不小心
2)货品分隔包装方式欠佳
3)模具卸料板卸料力度过大或卸料板不平行
4)材料弯曲、变形或未经过直片机校正
1)目视明显变形
2)借用工具比对才可看出的变形可视情况而定
啤坏(啤反方向)
1)工件未放正管位
2)模具避空位不够
3)模具移位
4)模具崩缺
5)模具管位欠佳,工件可正、反方向放进
2)就模具冲压常出现之问题及检查注意事项见下表(注:每工序之检查项目都必须包括外观检查):
工序名称
常见不良现象
检查注意事项
剪口(剪口或开料)
1)披锋
2)片纹方向
3)材料正、反面方向错
4)料弯曲(或扭曲)
5)材料错误(包括厚度、硬度等)
材料厚度、硬度、片纹方向、料弯曲将直接影响下工序成形效果,须重拮留意,如图纸标示不明确须即时反映(如不锈钢材料没注明其硬度要求或型号是SUS301 1/2H 3/4H或SUS304 1/2H
1)注意有否管位,工件是否能反方向放进
2)可使用投影机,相配之螺丝或夹具检测
铆接
碰焊
1)焊点披锋或焊点过深
2)虚焊(假焊)
3)锅钉松脱
4)锅钉歪斜
5)漏焊、漏铆钉(锅钉)
6)焊接移位或焊接反方向
7)锅钉螺纹被压坏或孔径变小
1)焊点深度控制在0.2mm以下
2)所有碰焊工件都必须做破坏性测试
3)用胶棒轻拿货品,可检测虚焊现象
5)模具跳屎(消屎不良,料屎跳于模面)
如产品须喷油或丝印,则表面不可有压痕不良,必要时,则以客户确认样办为准则
花痕/划伤
1)材料花(伤)
2)模具边角锋利,货品取放时划花
3)员工操作不良
4)货品没分隔或分隔方式欠佳(例如隔纸皮低于工件,起不到保护作用)
轻微擦花(无手感)可接受,如产品须喷油/丝印,则不能有刮伤
屈曲扎形(成形)
1)屈曲位置裂纹折断
2)啤反方向
3)屈曲位拉伤表层
4)模崩缺引致屈曲位置不良(凹或凸)且角度不良
5)模具未冲到位引致底部呈弧状,R角偏大及角度不符
6)模具避空不够,靠近屈曲边缘之脚仔或猪嘴孔被压扁
7)扎形时材料拉伸变形,孔径尺寸不符
1)检查根部尺寸与顶部尺寸时,分开检测,不能单检测根部尺寸
8)孔内披锋(孔边披锋过大,下工序被压平堵于孔内)
9)冲孔后,下工序模具避空不够或模具下压过深,材料受挤压而令孔变小
按图纸验收,必要时加工处理或申请客户特采
氧化生锈
1)材料氧化
2)制程工序间没防锈油或防锈油不足
3)下班时材料或产品未遮盖(如光泊、红铜材料)
4)操作时没戴手套,直接用手接触产品,工件粘有汗渍而生锈
6)冲针损坏,猪嘴孔翻边不良
7)模具移位或下模磨损,将工件拉伤
此类问题拒收
孔小或孔大、尺寸不良、角度不良
1)模具冲针磨损
2)模具管位移位
3)角度偏大或偏小,造成尺寸不良
4)模具冲针错误(孔大或孔小)
5)设计欠佳,先冲孔后拉伸,则孔变大
6)模具冲压不到底或冲压过深
7)模具冲压不稳定,时深时浅(啤机性能)
按情况轻重,而限度接受
螺纹不良
1)丝攻粘有杂物,将螺孔打坏
2)工件放歪,造成螺纹孔倾斜
3)未落嗒牙油或丝攻磨损
4)螺纹机性能不稳定或丝攻左右晃动
5)螺孔内粘有杂物或孔内油渍干涸后堵塞,令孔小牙规不过
不接受
一、制程冲压及检查注意事项:
1)目前,本厂所用之模具多为单工序模具,覆合模、步进模压延(深拉伸)模较少
2)如有字唛则须留意字体有否漏缺、清晰,有否一边深一边浅
3)注意工件之摆放会否引致货品变形刮花
4)留意工件是否正、反面方向都能放进模具,有此情况须及时向上汇报
压延(深拉伸)
1)拉伤(刮手)
2)R角位(或波位)爆裂
1)如须喷油货品,还须注意货品之分隔,会否碰伤工作
2)拉伸不到底时,会影响下工序质量(如冲孔容易变形或扭曲)
攻螺纹
1)漏攻牙
2)滑牙或牙紧
3)螺纹倾斜
4)螺纹孔有缺丝
5)攻牙未到底(上部有螺纹,下部没螺纹)
1)注意货品之明示分隔是否清晰
2)员工操作方式正确或错漏
3)嗒牙管位是否良好(有否起到固定作业)
4)使用牙规时,力度要适当,漏拨孔
3)拨孔不够深
4)拨孔边出现披锋
5)拨孔过深
4)若有力度要求,则须测试拉力或扭力
冲孔(包括翻边孔)
1)披锋
2)啤反方向
3)多孔或缺孔
4)孔径尺寸或形状不符
5)塞孔或孔屎未脱或孔边披锋丝
6)模具冲针磨损引致孔翻边不良(或一边高低)
1)注意孔披锋大,下工序冲压后引致孔径偏小
2)检查只须清楚了解该工序冲压位置,检查时应逐个核对孔数是否多出或漏缺,若孔数太多,应用针板辅助检查。
3)孔屎未脱或孔边披锋丝有可能影响客户之整机功能(如短路)必须控制
五金件常用缺陷说明
品管部培训教材
问题点
产生原因
备注
披锋
1)上、下模具间隙大,上、下模具移位造成货品一边披锋大,一边披锋小
2)模具钝(不锋利)
3)无用润滑油或润滑油不足
4)模具硬度偏低,而材料硬度偏大
压印
1)材料(或半成品)粘有杂物未擦净
2)模具粘有杂物,未擦干净
3)模具凹凸不平或生锈
4)模具未去磁,容易粘附发料屎