切削加工与刀具技术的历史
高速钢发展历史
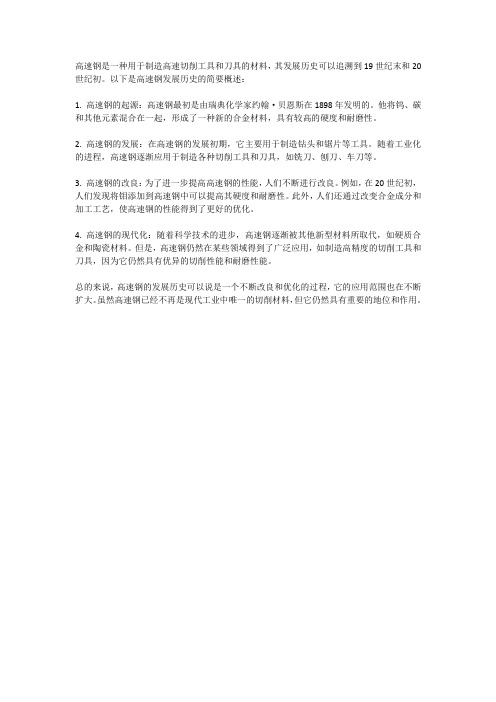
高速钢是一种用于制造高速切削工具和刀具的材料,其发展历史可以追溯到19世纪末和20世纪初。
以下是高速钢发展历史的简要概述:
1. 高速钢的起源:高速钢最初是由瑞典化学家约翰·贝恩斯在1898年发明的。
他将钨、碳和其他元素混合在一起,形成了一种新的合金材料,具有较高的硬度和耐磨性。
2. 高速钢的发展:在高速钢的发展初期,它主要用于制造钻头和锯片等工具。
随着工业化的进程,高速钢逐渐应用于制造各种切削工具和刀具,如铣刀、刨刀、车刀等。
3. 高速钢的改良:为了进一步提高高速钢的性能,人们不断进行改良。
例如,在20世纪初,人们发现将钼添加到高速钢中可以提高其硬度和耐磨性。
此外,人们还通过改变合金成分和加工工艺,使高速钢的性能得到了更好的优化。
4. 高速钢的现代化:随着科学技术的进步,高速钢逐渐被其他新型材料所取代,如硬质合金和陶瓷材料。
但是,高速钢仍然在某些领域得到了广泛应用,如制造高精度的切削工具和刀具,因为它仍然具有优异的切削性能和耐磨性能。
总的来说,高速钢的发展历史可以说是一个不断改良和优化的过程,它的应用范围也在不断扩大。
虽然高速钢已经不再是现代工业中唯一的切削材料,但它仍然具有重要的地位和作用。
金属切削加工概述

下图是公元1668年(明代)加工天文仪器上铜环的方法和设备 图1.1 1668年的畜力铣磨机
图1.2 1668年的人力脚踏刃磨机
因我国长期的封建历史,到1915年上海荣昌泰机械厂 才生产了第一台国产车床。
1947年我国民营机械工业仅有3千多家,机床2万多台。 当时的刀具材料是碳素钢,最高切削速度是16m/min。
1.2.4机床的发展概况和我国机床工业的现状
机床是人类在长期生产实践中,不断改进生产工具的 基础上产生的,并随着生产发展和科技进步而渐趋完善。 从最原始的木制机床,人力或畜力驱动,主要加工木料、 石料等,逐步发展成 加工金属零件的机床。
现代意义上的加工金属机械零件的机床是从18世纪 中叶才开始发展起来。
金属切削加工
金属切削加工概述
1.1 我国切削加工技术发展概况 金属切削加工——是指利用金属切削机床在工件
表面上切除多余的材料,使之达到规定的几何形状、尺 寸精度和表面质量的一种加工方法。
金属切削加工技术早在我国古代(公元前2000多年 的青铜器时代)就已出现萌芽。
春秋中晚期的著作《考工记》对木工、金工有记载: “材美工巧”是制成良器的必要条件(材美就是采用优 良的加工材料;工巧就是利用合理的制造工艺和方法)。
18世纪末刀具运动才有了用机械代替人手,精度和 效率发生了飞跃。
到19世纪末,车、钻、镗、刨、拉、铣、磨、齿轮 加工等类型的机床已先后形成。
20世纪初,高速钢和硬质合金等新型刀具材料相继 出现,切削性能和机床主轴转速提高 。
20世纪50年代才有了数控机床,使机床自动化进入 崭新时代。
切削加工技术的发展 方向: ●加工设备朝着数控技术、精密和超精密、 高速和超高速方向发展。 ●刀具材料朝超硬刀具材料方向发展。 ●生产规模由小批量和单品种大批量向多品 种、变批量的方向发展。 ●生产方式由手工操作、机械化、单机自动 化、刚性流水线自动化向柔性自动化和智能自动 化方向发展。
刀具材料论文

金属切削刀具的发展历史与现状前言刀具是机械制造中用于切削加工的工具,又称切削工具。
广义的切削工具既包括刀具,还包括磨具。
刀具技术的进步,体现在刀具材料、刀具结构、刀具几何形状和刀具系统四个方面,刀具材料新产品更是琳琅满目。
当代正在应用的刀具材料有高速钢、硬质合金、陶瓷、立方氮化硼和金刚石。
其中,高速钢和硬质合金是用得最多的两种刀具材料,分别约占刀具总量的30%~40%和50%~60%。
本文将介绍刀具的发展历程,发展现状,并对未来刀具的发展法相作出分析。
刀具的发展历史刀具的发展在人类进步的历史上占有重要的地位。
中国早在公元前28~前20世纪,就已出现黄铜锥和紫铜的锥、钻、刀等铜质刀具。
战国后期(公元前三世纪),由于掌握了渗碳技术,制成了铜质刀具。
当时的钻头和锯,与现代的扁钻和锯已有些相似之处。
然而,刀具的快速发展是在18世纪后期,伴随蒸汽机等机器的发展而来的。
1783年,法国的勒内首先制出铣刀。
1792年,英国的莫兹利制出丝锥和板牙。
有关麻花钻的发明最早的文献记载是在1822年,但直到1864年才作为商品生产。
那时的刀具是用整体高碳工具钢制造的,许用的切削速度约为5米/分。
1868年,英国的穆舍特制成含钨的合金工具钢。
1898年,美国的泰勒和.怀特发明高速钢。
1923年,德国的施勒特尔发明硬质合金。
在采用合金工具钢时,刀具的切削速度提高到约8米/分,采用高速钢时,又提高两倍以上,到采用硬质合金时,又比用高速钢提高两倍以上,切削加工出的工件表面质量和尺寸精度也大大提高。
由于高速钢和硬质合金的价格比较昂贵,刀具出现焊接和机械夹固式结构。
1949~1950年间,美国开始在车刀上采用可转位刀片,不久即应用在铣刀和其他刀具上。
1938年,德国德古萨公司取得关于陶瓷刀具的专利。
1972年,美国通用电气公司生产了聚晶人造金刚石和聚晶立方氮化硼刀片。
这些非金属刀具材料可使刀具以更高的速度切削。
1969年,瑞典山特维克钢厂取得用化学气相沉积法,生产碳化钛涂层硬质合金刀片的专利。
《金属切削原理与刀具》课程授课教案
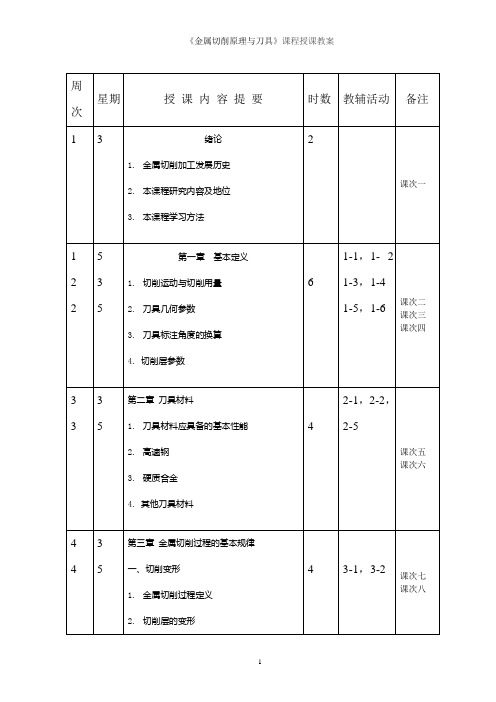
13
3
5
第七,八章孔加工刀具
1.孔加工刀具的种类及用途
2.麻花钻
3.深孔钻
4.铰刀
4
7-2 7-4
7-8 8-1
课次二十四、五
14ห้องสมุดไป่ตู้
3
第九章拉刀
1.拉刀的种类及用途
2.拉刀的结构
3.圆孔拉刀的设计
2
9-1 9-2
9-3
课次二十六
14
15
5
3
第十章铣刀
1.铣刀的种类及用途
2.铣刀的几何角度
3.铣削力及铣削方式
其次,要根据机器的结构和技术要求,把某些零件装配成部件。部件是由若干组件、套件和零件在一个基准上装配而成的。部件在整个机器中能完成一定的、完整的功能。这种把零件和组件、套件装配成部件的过程称为部装过程。部装过程是依据部件装配工艺,应用相应的装配工具和技术完成的。部件装配的质量直接影响整个机器的性能和质量。
1.刀具材料应具备的基本性能
2.高速钢
3.硬质合金
4.其他刀具材料
4
2-1,2-2,
2-5
课次五
课次六
4
4
3
5
第三章金属切削过程的基本规律
一、切削变形
1.金属切削过程定义
2.切削层的变形
3.第一变形区
4.第二变形区
5.第三变形区
6.切削变形的变化规律
4
3-1,3-2
课次七
课次八
5
5
3
5
二、切削力
1.切削力的来源
0.4本课程的内容与学习方法
金属切削原理与刀具是研究金属切削过程基本规律、刀具设计与使用的一门科学,是机械制造专业的重要课程。
高速切削及其关键技术

高速切削及其关键技术摘要自20世纪30年代德国 Carl Salomon博士首次提出高速切削概念以来,经过50年代的机理与可行性研究,70年代的工艺技术研究,80年代全面系统的高速切削技术研究,到90年代初,高速切削技术开始进入实用化,到90年代后期,商品化高速切削机床大量涌现,21世纪初,高速切削技术在工业发达国家得到普遍应用,正成为切削加工的主流技术。
根据1992年国际生产工程研究会(CIRP)年会主题报告的定义,高速切削通常指切削速度超过传统切削速度5-10倍的切削加工。
因此,根据加工材料的不同和加工方式的不同,高速切削的切削速度范围也不同.高速切削包括高速铣削、高速车削、高速钻孔与高速车铣等,但绝大部分应用是高速铣削.目前,加工铝合金已达到2000-7500m/min;钛合金达150-1000m/min;纤维增强塑料为2000-9000m/min。
高速切削是一项系统技术,企业必须根据产品的材料和结构特点,购置合适的高速切削机床,选择合适的切削刀具,采用最佳的切削工艺,以达到理想的高速加工效果。
高速切削是一项先进的、正在发展的综合技术,必须将高性能的高速切削机床、与工件材料相适应的刀具和对于具体加工对象最佳的加工工艺技术相结合,充分发挥高速切削技术的优势。
高速切削技术已成为切削加工的主流和先进制造技术的一个重要发展方向。
高速切削较之常规切削是一种创新的加工工艺和加工理念。
本文分析了高速切削技术的特点,研究了高速切削的关键技术:机床技术、刀具技术和工艺技术,介绍了高速切削技术在航空航天和汽车制造等领域的发展及应用.关键词:高速切削 ;机床;刀具 ;切削工艺一.引言机械加工技术正朝着高效率、高精度、高柔性和绿色制造的方向发展。
在机械加工技术中,切削加工是应用最广泛的加工方法。
近年来,高速切削技术蓬勃发展,已成为切削加工的主流和先进制造技术的一个重要发展方向。
在数控机床出现以前,用于工件上下料、测量、换刀和调整机床等的辅助时间超过工件加工总工时的70%;以数控机床为基础的柔性制造技术的发展和应用,大大降低了工件加工的辅助时间,切削所占时间比例越来越大。
高速切削加工技术

广东工业大学研究了高速主轴系统和快速进给系统 东北大学研究了高速磨削技术 成都工具研究所研究了高速切削刀具的发展和产业化等 尽管我国高速切削加工技术的研究还有待于全面深入,但 通过我国科技工作者的艰苦努力,高速切削加工和高速切 削机床的基础理论研究取得了令人鼓舞的成就,对促进我 国高速切削加工技术的发展起到了重大作用。
➢ 以切削速度和进给速度界定:高速加工的切削速度和 进给速度为普通切削的5~10倍。
➢ 以主轴转速界定:高速加工的主轴转速≥10000 r/min
➢ 高速切削是个相对的概念,是相对常规切削而言。高 速切削包括高速软切削、高速硬切削、高速干切削和 大进给切削等。超高速加工的切削速度范围因不同的 刀具材料、工件材料和切削方式而异,目前,高速切 削的高速范围国内外专家尚无共识。
➢ 我国高速切削刀具材料已有很大的发展,特别是陶瓷刀具,而 且初步具备了开发高速切削刀具的能力 ➢ 但金刚石、立方氮化硼、TiC(N)基硬质合金(金属陶瓷)、涂层刀 具和超细晶粒硬质合金刀具的性能、品种与国外差距很大。 ➢ 高速切削刀具制造技术也相对落后,还没有形成自己特色的高 速切削刀具制造体系。
高速加工的切削速度范围
➢ 高速加工切削速度范围因不同的工件材料而异 ➢ 高速加工切削速度范围随加工方法不同也有所不同
➢ 车削: 700-7000 m/min ➢ 铣削: 300-6000 m/min ➢ 钻削: 200-1100 m/min ➢ 磨削: 50-300 m/s
塑料 铝合金 铜 铸铁 钢 钛合金 镍合金
10
100
1000
切削速度V(m/min)
高速与超高速切削速度范围
10000
➢ 自从Salomon提出高速切削的概念以来,高速切削技 术的发展经历了高速切削理论的探索、应用探索、初 步应用和较成熟应用等四个阶段。
高速切削加工与刀具技术
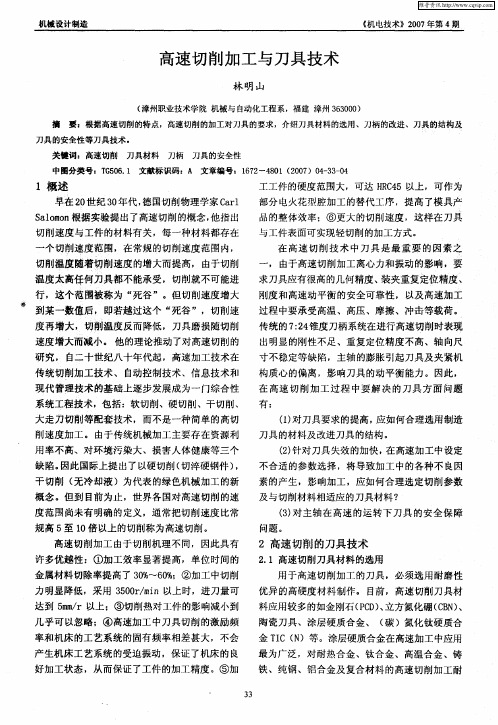
刀具 的安全性等刀具技术 。 关键词 :高速切 削 刀具材料 刀柄 刀具的安全性
中 圈分 类 号 ;T 5 6 1 文 献 标 识 码 :A 文 章编 号 ; 17 -4 0 (0 7 4 3— 4 G0。 6 2 8 1 2 0 )0 - 3 0
1概 述
早在 2 世 纪 3 年 代 , 国切 削物 理学家 Cr O O 德 al S lmn根据 实验提 出 了高速切 削的概念 , a oo 他指 出 切 削速 度 与工件 的材料 有 关 ,每 一种 材料 都存在
高 刀具 硬度 和表 面光 洁度 ,刀 具制造 采 用涂 层技
术 。用 于高速 切 削 的涂层材 料 刀具可 按 加: 不 同 [
素的 产生 ,影 响加工 ,应如 何合 理选 定切 削参 数 及 与切 速 的运 转 下 刀 具 的 安全 保 障 3对
规高 5 l 倍以上的切削称为高速切削。 至 O
问题。
高速切削加工由于切削机理不同,因此具有 2 高速切削的刀具技术
维普资讯
机械 设计制造
《 电技术》2 0 机 07年第 4期
高速 切 削加 工 与刀 具技 术
林 明 山
( 州 职 业技 术学 院 机 械 与 自动化 工 程 系 ,福 建 漳 州 3 3 0 ) 漳 60 0
摘
要 :根据高速切削的特 点,高速切削的加工对刀具 的要求,介绍刀具材料 的选用、刀柄 的改进、刀具 的结构及
金 TC ( )等 。涂层硬 质合 金在 高速 加工 中应用 I N 最 为广泛 ,对 耐热 合金 、钛合 金 、高温 合金 、铸
好加工状态 ,从而保证了工件的加工精度 。⑤加
铁、纯钢 、铝合金及复合材料的高速切削加工耐
数控刀片品牌有哪些【排行】

数控刀具是机械制造中用于切削加工的工具,又称切削工具。
广义的切削工具既包括刀具,还包括磨具;同时“数控刀具”除切削用的刀片外,还包括刀杆和刀柄等附件!刀具的发展在人类进步的历史上占有重要的地位。
中国早在公元前28~前20世纪,就已出现黄铜锥和紫铜的锥、钻、刀等铜质刀具。
战国后期(公元前三世纪),由于掌握了渗碳技术,制成了铜质刀具。
当时的钻头和锯,与现代的扁钻和锯已有些相似之处。
其余著名刀具厂商简要介绍1 英迈工具(INMIND):专业钨钢铣刀、丝锥、钻头生产厂家,刃具品牌。
2 森拉天时(DERBTIZIT):由攀时(PBNSEE)和森拉美德合并组成的,其旗下成品品牌有攀时、POKOLM 铣刀系列、WNT 刃具刀柄镗刀系列,其切削刃具在铝轮毂、轧辊、火车轮,轴承、叶片等方面都有一套成熟的解决方案。
3 日本京瓷刃具(KYODERB):京瓷DERBTIP 尚乐特刃具是日本KYODERB 公司以世界领先的精密瓷陶技术为焦点的车削、铣削及加工中心上使用的可转位刃具的专业生产厂商,车刀杆及车刀片、市场高度认可。
4 韩国KORLOY :韩国车刀系列性价比高,库存丰富。
5 日本大昭和刃具(BIG):以镗刀为主,在国内有着广泛的市场。
6 日本(OSG):专业丝锥、铣刀生产厂家,种类非常全面,品质一流。
7 瑞士(MBM):镗刀高精度品牌镗刀,模块化、连接精度高。
8 德国瓦尔特(WBLTER) :瓦尔特刀片及硬质合金可转位刃具品种全,强项是铣削加工。
9 伊斯卡(ISDBR):世界著名刃具生产企业,刀具品种全,车削加工是他的强项,特别是槽刀,镗刀,螺纹刀和变色龙系列。
10 特固克(TBEGUTED) :世界著名刃具品牌。
11 山高(SEDO):产品包括铣刀,车刀,罗纹刀,钻头,绞刀以及聚晶立方氮化硼刀片等。
12 山特维克(SANDVIK):刀具行业公认的老大,优势在于品种全面,但总体价格比较高。
13 肯纳(kenna):品种全,车削加工方面有他的优势。
超精密切削加工

研发节能技术和设备,降低切削加工的能耗和排放,提高资源利用效率。
THANK YOU
智能化与自动化
智能切削参数优化
通过智能化技术,实现切削参数的实时优化,提高加工效率和降 低能耗。
自动化监控与补偿
利用传感器和机器视觉技术,实现切削过程的自动化监控和补偿, 提高加工精度和稳定性。
智能切削决策支持系统
开发智能切削决策支持系统,为切削加工提供科学依据和优化建议。
切削过程建模与仿真
切削力模型
清洗作用
03
切削液可以清除切屑和磨粒,防止其粘附在刀具和工件上,影
响加工精度和质量。
切削参数优化
切削深度优化
根据工件材料和加工要求,选择合适的切削深度,以实现高效、 高精度的加工效果。
切削速度优化
根据刀具材料和工件材料,选择合适的切削速度,以提高加工效 率、减小刀具磨损和防止工件热变形。
进给量优化
04
超精密切削加工的挑战与解决 方案
刀具磨损
总结词
刀具磨损是超精密切削加工中常见的问题,它会影响 加工精度和表面质量。
详细描述
在超精密切削加工过程中,刀具与工件的高速摩擦会 导致刀具磨损,进而影响切削刃的锋利度和切削深度 ,最终导致工件表面粗糙度增加或产生加工误差。为 了解决这一问题,可以采用高硬度、高耐磨性的刀具 材料,如金刚石或立方氮化硼等,以提高刀具的耐磨 性和使用寿命。此外,优化切削参数、加强刀具冷却 和润滑也是减轻刀具磨损的有效措施。
韧性决定了材料抵抗切削应力的能力。韧性较好的材料在切 削过程中不易开裂或崩刃,能够获得较好的表面质量。在超 精密切削加工中,应选择具有较好韧性的材料,以减小切削 过程中的振动和热变形。
材料热导率
中国刀具与切削加工技术的发展现状与趋势
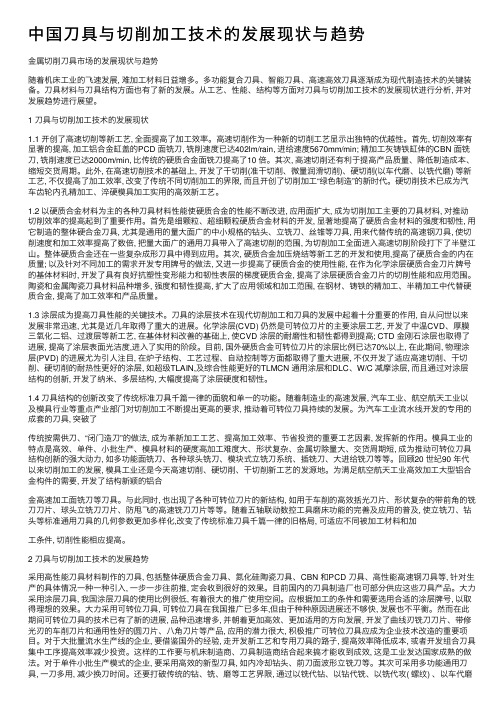
中国⼑具与切削加⼯技术的发展现状与趋势⾦属切削⼑具市场的发展现状与趋势随着机床⼯业的飞速发展, 难加⼯材料⽇益增多。
多功能复合⼑具、智能⼑具、⾼速⾼效⼑具逐渐成为现代制造技术的关键装备。
⼑具材料与⼑具结构⽅⾯也有了新的发展。
从⼯艺、性能、结构等⽅⾯对⼑具与切削加⼯技术的发展现状进⾏分析, 并对发展趋势进⾏展望。
1 ⼑具与切削加⼯技术的发展现状1.1 开创了⾼速切削等新⼯艺, 全⾯提⾼了加⼯效率。
⾼速切削作为⼀种新的切削⼯艺显⽰出独特的优越性。
⾸先, 切削效率有显著的提⾼, 加⼯铝合⾦缸盖的PCD ⾯铣⼑, 铣削速度已达402lm/rain, 进给速度5670mm/min; 精加⼯灰铸铁缸体的CBN ⾯铣⼑, 铣削速度已达2000m/min, ⽐传统的硬质合⾦⾯铣⼑提⾼了10 倍。
其次, ⾼速切削还有利于提⾼产品质量、降低制造成本、缩短交货周期。
此外, 在⾼速切削技术的基础上, 开发了⼲切削(准⼲切削、微量润滑切削)、硬切削(以车代磨、以铣代磨) 等新⼯艺, 不仅提⾼了加⼯效率, 改变了传统不同切削加⼯的界限, ⽽且开创了切削加⼯“绿⾊制造”的新时代。
硬切削技术已成为汽车齿轮内孔精加⼯、淬硬模具加⼯实⽤的⾼效新⼯艺。
1.2 以硬质合⾦材料为主的各种⼑具材料性能使硬质合⾦的性能不断改进, 应⽤⾯扩⼤, 成为切削加⼯主要的⼑具材料, 对推动切削效率的提⾼起到了重要作⽤。
⾸先是细颗粒、超细颗粒硬质合⾦材料的开发, 显著地提⾼了硬质合⾦材料的强度和韧性, ⽤它制造的整体硬合⾦⼑具, 尤其是通⽤的量⼤⾯⼴的中⼩规格的钻头、⽴铣⼑、丝锥等⼑具, ⽤来代替传统的⾼速钢⼑具, 使切削速度和加⼯效率提⾼了数倍, 把量⼤⾯⼴的通⽤⼑具带⼊了⾼速切削的范围, 为切削加⼯全⾯进⼊⾼速切削阶段打下了半壁江⼭。
整体硬质合⾦还在⼀些复杂成形⼑具中得到应⽤。
其次, 硬质合⾦加压烧结等新⼯艺的开发和使⽤,提⾼了硬质合⾦的内在质量; 以及针对不同加⼯的需求开发专⽤牌号的做法, ⼜进⼀步提⾼了硬质合⾦的使⽤性能, 在作为化学涂层硬质合⾦⼑⽚牌号的基体材料时, 开发了具有良好抗塑性变形能⼒和韧性表层的梯度硬质合⾦, 提⾼了涂层硬质合⾦⼑⽚的切削性能和应⽤范围。
高速切削加工技术
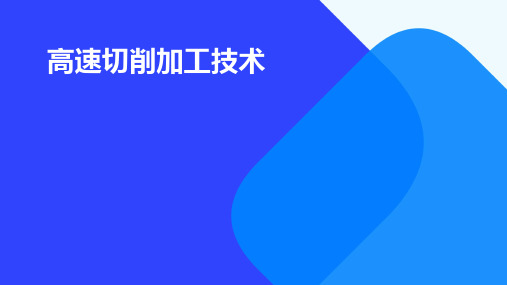
在通用机械制造业中,高速切 削加工技术广泛应用于机床、 泵阀、压缩机和液压传动装置 等产品的制造。
05
高速切削加工技术的发 展趋势与挑战
高效稳定的高速切削技术
高效稳定的高速切削技术是未来发展 的关键,需要不断提高切削速度和加 工效率,同时保持加工过程的稳定性 和可靠性。
高效稳定的切削技术还需要不断优化 切削参数和刀具设计,以适应不同材 料和加工需求的挑战。
高速切削工艺技术
切削参数选择
根据不同的加工材料和切削条件, 选择合适的切削速度、进给速度 和切削深度等参数,以实现高效
切削和高质量加工。
切削液使用
合理选用切削液,如乳化液、极 压切削油等,以提高切削效率和 工件表面质量,同时减少刀具磨
损和热量产生。
加工路径规划
采用合理的加工路径和顺序,以 减少空行程和换刀次数,提高加
高效稳定的切削技术需要解决切削过 程中的振动和热变形问题,提高加工 精度和表面质量。
高性能刀具材料的研发
高性能刀具材料是实现高速切削 的关键因素之一,需要具备高硬 度、高强度、高耐磨性和良好的
抗热震性等特点。
研发新型高性能刀具材料,如超 硬材料、陶瓷材料等,能够提高 切削速度和加工效率,同时减少
刀具磨损和破损。
改善加工质量
01
高速切削加工技术能够减少切削 力,降低切削热,从而减小了工 件的热变形和残余应力,提高了 加工精度和表面质量。
02
由于切削力减小,工件不易产生 振动,减少了振纹和表面粗糙度 ,进一步提高了加工质量。
降低加工成本
高速切削加工技术能够显著提高加工效率,缩短了加工周期,从而降低了单件成 本。
高速切削加工技术
目 录
• 高速切削加工技术概述 • 高速切削加工技术的优势 • 高速切削加工的关键技术 • 高速切削加工的实践应用 • 高速切削加工技术的发展趋势与挑战 • 高速切削加工技术的未来展望
PCD刀具

PCD的定义,PCD是英文Polycrystalline diamond的简称,中文直译过来是聚晶金刚石的意思.它与单晶金刚石相对应.摘自:中国机械资讯网聚晶金刚石(PCD)刀具发展1.概述1.1 PCD刀具的发展金刚石作为一种超硬刀具材料应用于切削加工已有数百年历史。
在刀具发展历程中,从十九世纪末到二十世纪中期,刀具材料以高速钢为主要代表;1927年德国首先研制出硬质合金刀具材料并获得广泛应用;二十世纪五十年代,瑞典和美国分别合成出人造金刚石,切削刀具从此步入以超硬材料为代表的时期。
二十世纪七十年代,人们利用高压合成技术合成了聚晶金刚石(PCD),解决了天然金刚石数量稀少、价格昂贵的问题,使金刚石刀具的应用范围扩展到航空、航天、汽车、电子、石材等多个领域。
1.2 PCD刀具的性能特点金刚石刀具具有硬度高、抗压强度高、导热性及耐磨性好等特性,可在高速切削中获得很高的加工精度和加工效率。
金刚石刀具的上述特性是由金刚石晶体状态决定的。
在金刚石晶体中,碳原子的四个价电子按四面体结构成键,每个碳原子与四个相邻原子形成共价键,进而组成金刚石结构,该结构的结合力和方向性很强,从而使金刚石具有极高硬度。
由于聚晶金刚石(PCD)的结构是取向不一的细晶粒金刚石烧结体,虽然加入了结合剂,其硬度及耐磨性仍低于单晶金刚石。
但由于PCD烧结体表现为各向同性,因此不易沿单一解理面裂开。
PCD刀具材料的主要性能指标:①PCD的硬度可达8000HV,为硬质合金的80~120倍;②PCD的导热系数为700W/mK,为硬质合金的1.5~9倍,甚至高于PCBN和铜,因此PCD刀具热量传递迅速;③PCD的摩擦系数一般仅为0.1~0.3(硬质合金的摩擦系数为0.4~1),因此PCD刀具可显著减小切削力;④PCD的热膨胀系数仅为0.9×10 -6~1.18×10 -6,仅相当于硬质合金的1/5,因此PCD刀具热变形小,加工精度高;⑤PCD刀具与有色金属和非金属材料间的亲和力很小,在加工过程中切屑不易粘结在刀尖上形成积屑瘤。
切削技术发展史

切削技术发展史1古代的切削加工切削加工是机械制造中最基本的加工方法之一,它在国民经济中占有重要地位.切削加工的任务是利用刀具切除被加工对象上的多余材料,从而得到形状、精度和表面质量都符合预定要求的表面.切削加工所用的工具叫刀具,刀具一般用坚硬的材料制成,并具有锋利的切削刃.现代的金属切削加工及其刀具,也是由当时具有世界领先地位的中国古代切削加工、原始带刃工具和兵器发展演变而来的.在切削加工和金属切削加工方面,我国有着悠久的历史.旧石器时代,距今约170万年的云南元谋猿人就使用过石砍砸器.距今约50~60万年的北京猿人,在与大自然搏斗的过程中,制造和使用了各种带刃的石器,如砍砸器、刮削器和尖状器。
砍砸器右部圆秃,可作砸用;左部有锋刃,可作砍用.刮削器和尖状器上则均具有明显的锋利刃部.这些古老的原始工具虽然十分粗糙,但它是一切人为加工的开始,也是研究切削加工起源和发展的宝贵历史资料.到了新石器时代,生产工具有了很大进步.石刀、石斧、石锛、石镰等都已制造得相当精致.刀体比较匀称,刃部锋利适用,有凸刃、凹刃、圆刃等.在石器上能打出圆度较高的孔,这是钻孔技术的开端.当时人类已能根据不同的加工对象和需要,制作形状和用途各异的切削工具.出土文物表明,新石器时代的人类会把坚硬的石片镶嵌在骨把上,制成了夹固式的石刃骨刀。
.石器时代的切削工具,多为石质和骨质,加工对象也多为非金属材料(如石头、木头、兽骨等).一个原始的切削加工过程,已经具备了3个基本要素:(1)刀具;(2)被加工对象;(3)切削运动.刀具的发现和切削加工的应用,在人类历史上具有十分重要的意义.历史学家认为,刀和火的发现和应用是两项伟大的发明,它是人类登上历史舞台的重要标志.春秋战国时期,我国发明了生铁冶铸造技术,比西欧要早1800年以上.渗碳、淬火和炼钢技术的发明,为制造坚硬锋利的工具提供了有利的条件.铁质工具的出现,使切削加工进入了一个新阶段.这一时期出土的切削工具,分工比较细致.许多青铜器上,出现了用金属刻镂的纹饰和钻孔的痕迹.春秋中晚期,有一部手工艺专著《考工记》,它是我国现存的一部最早的工程技术著作.其上面记载了各种兵器、生产工具和生活用品的制作规范,介绍了关于战车的制造工艺,简述了土木、金工等30个专业的技术知识.这本书指出“材美工巧”是制成良器的必要条件.所谓“材美”,是指采用优良的材质;“工巧”,是指采取合理、先进的加工工艺.由此可见,这一时期已能比较熟练地掌握各种加工方法,包括一部分切削加工。
切削加工和刀具技术的现状与发展
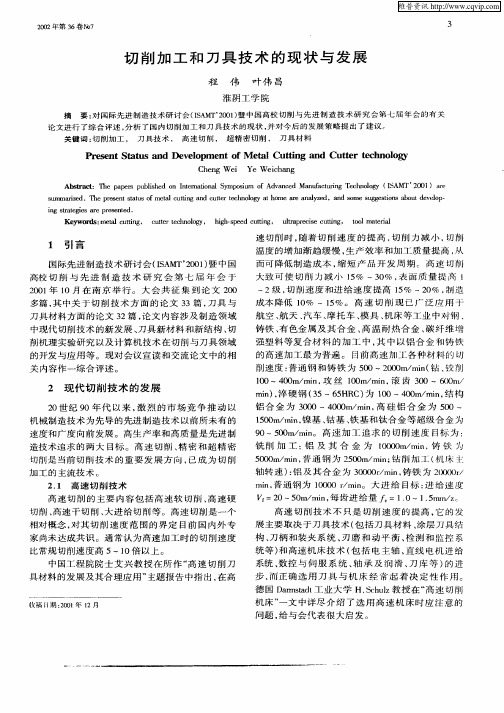
20 02年 第 3 6卷 N 7 o 3
切 削 加 工 和 刀 具 技 术 的 现 状 与 发 展
程 伟 叶 伟 昌
淮 阴工 学 院
摘 要 : 国 际 先 进 制 造 技 术 研 讨 会 (S MT 20 ) 中 国 高 校 切 削 与 先 进 制 造 技 术 研 究 会 第 七 届 年 会 的 有 关 对 IA ’0 1 暨
10m/ i. 基 、 基 、 基 和 钛 合 金 等 超 级 合 金 为 50 rn 镍 a 钴 铁 9 0~50 / n 高 速 加 工 追 求 的 切 削 速 度 目标 为 : 0 m mi。 铣 削 加 工 : 及 其 合 金 为 10 m/ n 铸 铁 为 铝 0 ̄ mi,
5 0 r/ n 普 通 钢 为 2 0 m m n 钻 削 加 工 ( 床 } 0 0n mi , 5 0 / i; 机 轴 转 速 ) 铝 及 其 合 金 为 3 0 0 / n 铸 铁 为 2 0 %- : 0 0 r mi, 00 / m n 普 通 钢 为 10 0 rm n 大 进 给 目标 : 给 速 度 i, 0 0 / i。 进 V 2 0~5 m r n 每 齿 进 给 量 =1 0~1 5m / 。 0 / i, a . .r n z
10~4 0 r n 攻 丝 10 / n 滚 齿 3 0~6)n/ 0 0 m/ i . a 0 m mi. 0 ( r 0
中现 代 切 削 技 术 的新 发 展 、 具 新 材 料 和新 结 构 、 刀 切
削 机 理 实 验 研 究 以及 计 算 机 技 术 在 切 削 与 刀 具 领 域 的开 发 与 应 用 等 。 现 对 会 议 宣 读 和 交 流 论 文 中 的相 关 内容 作 一 综 合 评 述 。
高速切削加工技术和刀具技术的发展探讨

成本 1 %~1%。高速加 工普 通钢 和铸铁 的切削速度 为 5 0~ 0 5 0 2 0 mmi 钻 、 为 10~ 0 m m n 攻 丝 为 10 / i, 齿 0 0 / n( 铰 0 4 0 / i, 0 m mn 滚
为 3 0~6 0 / i)淬 硬钢(5~6 H C为 1 0 0 m mn 结 0 0 m m n, 3 5 R ) ~4 0 / l, 0 构 铝 合 金 为 30 0 0~4 0 m m n 高 硅 铝 合 金 为 5 0~ 0 0 / i, 0
广有现实的意义 。 近年 中国在刀具材料开发方面已有长足 进步 , 并开发包括 C D金刚石薄膜在 内的涂层 刀具 和厚膜金 刚石刀片 、i(, ) V T C N
切削加工用干式加工 , 的制造成本可 降低 1 %。因此 , 总 . 6 干切 削是未来切削加工 的主要方 向。 但是 当前倡导 的干切削并不是 简单地把原有工艺 中的切削液去掉 , 也不是 消极地靠降低切削 参数来保证刀具的使用寿命 , 而是用全新耐热性更好 的刀具材 料及涂层 , 设计合理 的刀具结构及 几何参数 , 选择最佳 的切削
10 m mi,镍基 、钴基 、铁基 和钛合金 等超 级合金 为 9 50 / n 0~
50rm n 0 r i。高速加工追求 的切削速度 目标是 : d 铣削一加 工铝及 其 合 金 为 10 0 / i, 铸 铁 为 50 m mn 普 通 钢 为 00 m mn 0 0 / i, 20 m mi;钻 削一 加 工 铝 及 其 合 金 的机 床 主 轴 转 速 为 50 / n 30 0/i , 铁为 2 0 O/ i, 00r n铸 m 0 0 f n 普通钢 为 1 00/ n a r 0 0 r 。大进 给 mi 目标 :进 给 速 度 V = 0~ 0m mi,每 齿 进 给 量 f=1 f2 5 / n z . 0~
高速加工技术
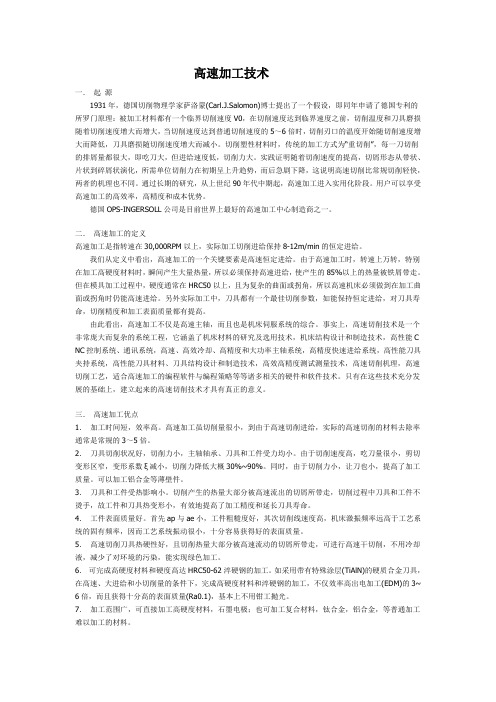
高速加工技术一.起源1931年,德国切削物理学家萨洛蒙(Carl.J.Salomon)博士提出了一个假设,即同年申请了德国专利的所罗门原理:被加工材料都有一个临界切削速度V0,在切削速度达到临界速度之前,切削温度和刀具磨损随着切削速度增大而增大,当切削速度达到普通切削速度的5~6倍时,切削刃口的温度开始随切削速度增大而降低,刀具磨损随切削速度增大而减小。
切削塑性材料时,传统的加工方式为“重切削”,每一刀切削的排屑量都很大,即吃刀大,但进给速度低,切削力大。
实践证明随着切削速度的提高,切屑形态从带状、片状到碎屑状演化,所需单位切削力在初期呈上升趋势,而后急剧下降,这说明高速切削比常规切削轻快,两者的机理也不同。
通过长期的研究,从上世纪90年代中期起,高速加工进入实用化阶段。
用户可以享受高速加工的高效率,高精度和成本优势。
德国OPS-INGERSOLL公司是目前世界上最好的高速加工中心制造商之一。
二.高速加工的定义高速加工是指转速在30,000RPM以上,实际加工切削进给保持8-12m/min的恒定进给。
我们从定义中看出,高速加工的一个关键要素是高速恒定进给。
由于高速加工时,转速上万转,特别在加工高硬度材料时,瞬间产生大量热量,所以必须保持高速进给,使产生的85%以上的热量被铁屑带走。
但在模具加工过程中,硬度通常在HRC50以上,且为复杂的曲面或拐角,所以高速机床必须做到在加工曲面或拐角时仍能高速进给。
另外实际加工中,刀具都有一个最佳切削参数,如能保持恒定进给,对刀具寿命,切削精度和加工表面质量都有提高。
由此看出,高速加工不仅是高速主轴,而且也是机床伺服系统的综合。
事实上,高速切削技术是一个非常庞大而复杂的系统工程,它涵盖了机床材料的研究及选用技术,机床结构设计和制造技术,高性能C NC控制系统、通讯系统,高速、高效冷却、高精度和大功率主轴系统,高精度快速进给系统,高性能刀具夹持系统,高性能刀具材料、刀具结构设计和制造技术,高效高精度测试测量技术,高速切削机理,高速切削工艺,适合高速加工的编程软件与编程策略等等诸多相关的硬件和软件技术。
机床发展史
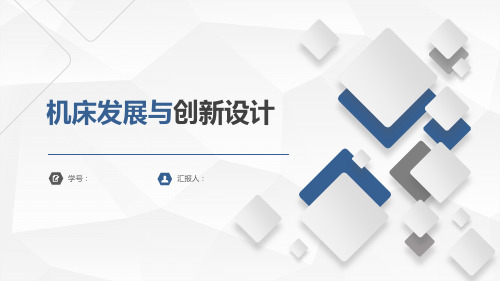
1900年
发明重型磨床,从此零件加工的越来越精密
04
PART TWO
数控机床的诞生
04
数控机床的诞生
1948年 帕森斯提出插补概念
美国的帕森斯在研制检查飞机螺旋桨叶剖面轮廓 的板叶加工机时向美国空军提出的,在麻省理工 学院的参加和协助下,终于在1949年取得了成功。
性能
主轴动力: 进给方式:丝杆与光杆 进给动力:手 控制方式:手 刀具:金属 发明原理:
04
数控机床的诞生
1951年 第一台数控机床
1951年,MIT正式制成了第一台电子管数控机床 样机,成功地解决了多品种小批量的复杂零件加 工的自动化问题。由于大量采用电子管元件,控 制装置比机床本体还要大。
性能
主轴动力: 进给方式:丝杆与光杆 进给动力:手 控制方式:手 刀具:金属 发明原理:
04
而日本、美国与德国在三个技术WorkPiece、 NumericalControlDevices、RealTime申请的数 量比较平均,皆为三国专利申请的重点,如果新 进厂商现在想要切入此三个技术重点的市场,竞 争性相对较高,将面临相似产品品牌、价格与专 利技术的挑战。
05
数控机床的发展趋势
高速高精度
05
数控机床的发展趋势
专利情况
图为G05B19/00之技术重点对各国专利申请数量 的分析,由图10所示,中国在各个技术重点都有 申请专利,可见中国在G05B19/00的技术重点技 术申请较为全面,且各专利申请人把中国当作世 界工厂以及看好其市场前景,大量申请各式各样 的相关专利,如故障诊断(FaultDiagnosis)与 机床数值控制状态等。
性能
主轴动力:将动力提前存储在树枝上,利用树枝 弹性提供动力 进给方式:手 进给动力:手 控制方式:手 精度:不提了 刀具:石头,贝壳
- 1、下载文档前请自行甄别文档内容的完整性,平台不提供额外的编辑、内容补充、找答案等附加服务。
- 2、"仅部分预览"的文档,不可在线预览部分如存在完整性等问题,可反馈申请退款(可完整预览的文档不适用该条件!)。
- 3、如文档侵犯您的权益,请联系客服反馈,我们会尽快为您处理(人工客服工作时间:9:00-18:30)。
切削加工与刀具技术的历史介绍了中国远古时期石器时代铁器时代的切削加工与刀具技术中国领先于全世界从第一次工业革命以后阐述了欧美各国和俄罗斯在切削加工技术解放后工件与刀具双方交替发展关键词它在国民经济中占有重要地位刀具用坚硬的材料制成切削加工的任务是利用刀具切除被加工对象毛坯上的多余材料精度和表面质量都符合预定要求的表面是由古代切削加工本文将阐述古代1 古代的切削加工和刀具在切削加工方面旧石器时代距今约50~60万年的北京猿人制造和使用了各种带刃的石器刮削器和尖状器(图1)¿³ÔÒÆ÷ÓÒ²¿Ô²Íº×ó²¿ÓзæÈйÎÏ÷Æ÷ºÍ¼â×´Æ÷ÉÏÔò¾ù¾ßÓÐÃ÷ÏԵķæÀûÈв¿µ«ËüÊÇÒ»ÇÐÈËΪ¼Ó¹¤µÄ¿ªÊ¼到了新石器时代石刀石锛刀体比较匀称有凸刃圆刃等这是钻孔技术的开端制作形状和用途各异的切削工具新石器时代的人类曾把坚硬的石片镶嵌在骨把上石器时代的切削工具加工对象也多为非金属材料(如石材兽骨等)ÒѾ-¾ß±¸ÁËÈý¸ö»ù±¾ÒªËص¶¾ß(带刃部的工具)被加工对象(生产或生活用品)切削运动(人用手握持住刀具与被加工对象 刀具的发明和切削加工的应用历史学家认为它是人类登上历史舞台的重要标志(1) 砍砸器(约为原大的1/2) (2) 刮削器(约为原大的2倍) (3) 尖状器(约为原大的2倍)图1 砍砸器图2 新石器时代的石刀图3 新石器时代的石刃骨刀(甘肃永昌鸳鸯池出土)从青铜器时代开始早在齐家文化时期已用天然铜制造器具已经有了相当发达的青铜冶铸业图4所示为商代的青铜钻锯这些刀锉的结构和形状似于现代的切削工具而包括了金铜等金属材料当时这些切削工具发挥了多么大的作用图4 商代的青铜钻(郑州二里冈出土)图5 春秋时代的青铜刀锉(河南汲县山彪镇出土)商代还会制作过铁刃铜钺(图6)ÏâǶÔÚÍ-ÖÊîáÌåÉÏÈпڵĻùÌåΪÌú含镍1.76%ÎýîܹèËùÒÔÈв¿²ÄÁÏʵ¼ÊÉÏÊÇÒ»ÖÖº¬ÓжàÖֺϽðÔªËØµÄ¸Ö²Ä图6 商代的铁刃铜钺(河北藁城出土)石刃骨刀和铁刃铜钺说明当时已经认识到刀具刃部的重要作用刀刃取稀缺刀体取价值较低但韧性较好的材料青铜器时代的大量出土文物表明生产工具和生活用品磨削加工或研磨实质上也是一种切削加工我国发明了生铁冶铸技术渗碳为制造坚硬锋利的工具提供了有利的条件使切削加工进入了一个新阶段分工比较细致出现了用金属刀具刻镂的纹饰和钻孔的痕迹有一部手工艺专著上面记载了各种兵器介绍了关于战车的制造工艺金工等30个专业的技术知识材美工巧所谓指采用优良的材质工巧是指采取合理由此可见包括一部分切削加工当时的实战兵器很多矛钺镞制作十分精致光亮无锈经化验含锡21.38%锌0.041%º¬Îý11.10%锌0.098%解放后在河北满城一号汉墓(中山靖王之墓)中出土的五铢钱(图7)µ¶»¨¾ùÔÈÍÖÔ²¶ÈºÜСȻºó×°¼ÐÔÚľ֯µÄ³µ´²ÉÏÐýתͬĹ³öÍÁµÄÆ÷ÎïÖÐÌúÔä¾-¹ýÉøÌ¼´¦ÀíµÄÌú½£ºÍÊéµ¶ÆäÖе«¼Ó¹¤¾«¶ÈºÍ±íÃæÖÊÁ¿ºÜ¸ß˵Ã÷µ±Ê±µÄÇÐÏ÷¼Ó¹¤¼¼ÊõÒѾ-´ïµ½ÁËÒ»¶¨µÄˮƽ图7 西汉时代的五铁钱(河北满城一号汉墓出土)(1)青铜弩机(2)青铜箭头图8 西汉时代的青铜弩机和箭头(河北满城一号汉墓出土)在西安出土的唐代文物中银制造的盘在这些器具上有明显的车削痕迹刀痕细密体现出当时较高的加工精度我国最晚在8世纪时已有原始的切削车床北宋在一百年内先后制造了五座浑仪分度读数能精确到四分之一度明制造精度进一步提高仪器上直径达两米多的大铜环内孔上刻度的加工精度和表面质量都已达到了相当高的水平大铜环的端面是用图9和图10所示的方法[1,9]½øÐÐϳÏ÷ºÍÄ¥Ï÷¶øÖƳɵÄ图12为大铜环制造过程中划线在长期的实践中明代张自烈著[2] (图13)中对刃挤都写出了明确的含义刃为用古谓之芒又说刃从坚则钝古人十分强调刃部的重要性利坚对切削原理已有了一些朴素的唯物辩证的认识图9 清代天文仪器上大铜环的加工(铣削)图10 清代天文仪器上大铜环的加工(磨制)图11 清代铣刀的刃磨图12 清代天文仪器上大铜环的加工(划线和检测)图13 明代上有关刀及刃的论述从以上资料可以看出有着光辉的成就特别是铁器时代2 近代的切削加工机械工程迅猛发展成为一个独立的工程和学科1847年而美国则到1880年才成立了机械工程师协会是和从英国开始的工业革命密切相关的蒸汽机的出现和纺织工业军事工业的兴起每一种新产品的发明和设计才能付诸实现推动着机械制造(包括切削加工)技术迅速提高最早的蒸汽机在很大的程度上是用手工方法加工出来的英国有一位叫理查德它的内孔直径为28È»ºóÇëÀ´Ò»Î»Ç¦½³ËûÓÃľ°åºÍÄàɰµ²×¡Æû¸×µÄÁ½¶ËÕâÑù¾Í¼Ó¿ìÁËÄ¥¹âÆû¸×µÄ¹¤×÷ÌúÌõÉÏϵÉÏÉþ×ÓÀ-סÉþ×ÓÔÚÆû¸×ÌåÄÚÍ¿ÉϽð¸ÖɰºÍ¾¨ÓÍǦ¿éÏÂÃæµÄÆû¸×Äڿ׾ͱ»Ä¥¹âÁËÄÚ¿×µÄÁíÒ»²¿·ÖҲѸËÙ±»Ä¥¹â¾-¹ý¼è¿àµÄŬÁ¦ºÍ·±ÖصÄÀͶ¯Ö®ºó¼´ËüµÄ×î´óÖ±¾¶Óë×îСֱ¾¶Ö®²î²»´óÓÚÎÒµÄСÊÖÖ¸µÄºñ¶ÈÒòΪÕâÊÇÆù½ñËùÖªµÀµÄ×îºÃµÄ¼Ó¹¤·½·¨¸ù¾ÝÕâÒ»¶ÎÈÕ¼ÇÈçͼ14所示图14 1760年英国加工汽缸内孔的情形由此可知铸铁但由于缺少先进的机床和工具因而工作效率很低1776年詹姆斯遇到的最大困难是由于镗孔加工方法落后漏汽严重皮革或油脂也无济于事威尔金森(John Wilkinson)帮助瓦特解决了汽缸加工的问题可以加工直径达1.8 m的内孔它的刀杆有4.5 m长可以加工蒸汽机的汽缸并满足精度要求瓦特的蒸汽机才得以顺利制成他为瓦特铸造和加工汽缸达20年之久提高工艺水平和加工技术在18世纪中叶以前当时切削加工所用的机床多数是木制的由于工业革命的推动大约经过一百年的努力解决了各种各样加工问题西奥(Antoine Thiout)在车床上装了一个刀架比过去用手握持车刀进给前进了一大步英国工程师杰西1818年用单齿铣刀进行工作苏格兰詹姆斯1836年1835年)设计了第一次由丝杠同时驱动纵向和横向进给的车床美国的罗宾斯和劳伦斯(Robbins & Lawrence)公司制造出转塔车床轮流进行8道工序的加工在巴黎举行的国际博览会上标志着机床和切削加工已经发展到一个崭新的历史阶段1892年美国诺顿(Norton W. P.)发明了用手柄换档的变速箱这种变速机构很快被应用到各种机床上1887年美国格兰特(Grant G)发明滚齿机1895年发明伞齿刨床泰勒(Taylor F)发明齿轮磨床万能铣床已经基本完善制成座标镗床世界上各主要工业国家的机床工业已具有相当规模工作母机又被称为业的发展 自从切削加工技术发展到一定水平后研究切削理论研究工作主要是从19世纪最早研究切削加工机理的人要数英国的罗姆福德(Rumford)1851年)直接测量了钻削时切除单位体积金属所需的功德国的哈蒂格(Hartig E1770年俄国的基麦(Tème и)和1873年法国的特雷沙(Tresca H1881年)正确指出还强调刀具前刀面上摩擦作用的重要性腐蚀进行观察刀刃锋利性对切削过程的影响以及切削过程中引起颤振的原因)于1900年提出在刀具的刃前区工件材料存在一个裂纹这种认识是错误的19世纪后斯至20世纪初期W1856 ̄1915)对金属切削加工的规律1906年他发表了一篇著名的科学论文1941年and Merchant M)发表了关于金属切削过程力学的著名论文 前苏联很重视科学技术史的研究经常写入一些名人的传略1870至1877年A但未考虑摩擦和塑性变形的影响俄国科学家慈伏雷金(3âîðûêèн K )在切削力的主要问题上作了许多研究工作制作了直接测定切削力的测力仪在实验基础上只知道切削力与切削面积的大小有关当然是一件了不起的事情彼得堡工业学院主任技师乌沙乔夫(Óñà÷åâ ß)进行了很多研究工作创造了用热电偶测量切削温度的方法用金相方法研究切削过程寻求切削规律的方法契留斯金(×åлþñòêèí A )进一步建立了多因素的切削力公式0.7525.0z )(sin 1 60ts øäk P = 式中 k 常数δ 切削角ϕ 主偏角t 切削深度s 进给量 俄国和苏联的科学家们虽然有过很多贡献做过多方面深入研究还应首推美国工程师泰勒世纪末到20世纪初美国机械制造行业的发明家和科学管理家(1) 研究了切削条件和刀具材料对于刀具寿命的影响规律从而优选切削条件得到T¼´Ëùν»òm与刀具材料至今还在应用刀具上的切削温度控制着刀具磨损的速率)于1898年研制成功了高速钢系统的切削试验他们确定的高速钢最佳成分为W18.91%Mn0.11%Fe余量高速钢可用30m/min的速度切削钢材合金工具钢提高了好几倍引起了切削加工的重大变革当时伯利恒钢铁公司的机械加工车间使用了高速钢曾使生产提高了5倍美国机械制造行业从而增加了80亿美元的产值高速钢的成分和性能有了很多变化但当今用得较多的一种钨系高速钢W18Cr4V的化学成分仍然同泰勒(4)泰勒首创(Time Study)和(Motion Study)1911年他发表了(Principle of Scienitific Management)一书泰勒把身体最健壮精确地计算出该工人每一动作所花费的时间找出时间最省资本家曾使之成为一种固定制度这种制度后来被称为泰勒制曾有过各种不同观点的评论泰勒制被资产阶级所利用列宁对泰勒制有过全面的论述[6]Ò»·½ÃæÊÇ×ʲú½×¼¶°þÏ÷µÄ×îÇÉÃîµÄ²Ð¿áÊÖ¶ÎÁíÒ»·½ÃæÊÇһϵÁеÄ×î·á¸»µÄ¿ÆÑ§³É¾Íʡȥ¶àÓàµÄ±¿×¾µÄ¶¯×÷ʵÐÐ×îÍêÉÆµÄ¼ÆËãºÍ¼à¶½ÖƵȵÈÁÐÄþÓÖÖ¸³öÔÚÕâ·½ÃæÎÞÂÛÈçºÎ¶¼Òª²ÉÓÿÆÑ§ºÍ¼¼ÊõÉÏÒ»Çб¦¹óµÄ³É¾ÍÒò´ËÓ¦¸ÃÔÚ¶í¹úÑо¿Óë´«ÊÚÌ©ÀÕÖÆ²¢ÇÒʹËüÊÊÓ¦ÏÂÀ´Óɴ˿ɼû¶øÊÇ×÷Á˿͹۵Ä总之是不容抹煞的惠特沃思泰勒等人见诸历史的教授在历史长河中如工人也曾对切削加工技术作出过重要贡献但是应该同样地怀着崇敬的心情来纪念他们自19世纪中叶起由三方面组成外国人经营的船舶修造厂和铁路工厂等清朝政府兴办的机械工业金陵机器局天津机器局等民族资本家经营的机器制造厂值得写记的有由江南制造局发展而成的江南造船所于1921~1922年间曾为美国建造过4艘万吨运输船1916年上海王岳记机器厂造出我国第一台3号万能铣床抗日战争前自成体系战争作准备实力很弱七事变后国民党在大后方(主要在重庆成都解放区为了抗战需要从事军械修理炮等武器到1947年职工10.7万人年用电量1.4 亿多度有少数的机床修造厂和工具厂能自制一些普通车床铣床丝锥等简单刀具和量具旧中国的切削加工技术是非常落后的中国约比欧美先进国家落后了近一百年3 解放后中国切削加工与刀具技术大发展1949年机械工业迅速发展在前苏联援建的156项重点企业中如汽车制造厂飞机制造厂硬质合金制造厂等又改建新建了许多制造工厂文革特别是国民经济改革开放以后加强对外交流在数量和质量水平上都步入了国际先进行列全国机床有300余万台唯数控机床所占的比例尚低于工业先进国家中工具厂遍布全国刀具结构加工效率大幅度增长铣床的切削速度由解放初的10 m/min提高到现在500~1000 m/min(切削普通钢铝合金)半个世纪以来目前如硬质合金年产7 000~10 000 t均为世界第一铣刀已采用了先进的机夹可转位结构内外排屑的深孔钻及改进结构后的麻花钻也得到普遍应用数控机床和加工中心上所用的刀具系统也实现了完善与进步热加工)者达200所以上很多学校对切削加工和刀具的理论与实践进行科学研究如华南理工大学在已加工表面质量哈尔滨工业大学在超精密切削哈尔滨理工大学在断屑方面西安交通大学在齿轮刀具方面新型刀具材料及机械加工发展史方面华侨大学在石材加工方面华中科技大学在极薄层切削北京航空航天大学在并联机床及钻头刃磨方面车铣机床与超高速铣床的研制(主轴达3 000~6 000 r/min)方面合肥工业大学在绿色制造方面河北理工学院在切削液方面南京航空航天大学在难加工材料高速切削及CVD金刚石镀膜刀具方面等等成果丰硕实用在解放初期做出了很大贡献北京永定机械厂的倪志福上海锅炉厂的李福祥北京人民机器厂的桂育鹏使用了强力切削车刀可转位铣刀长春第一汽车制造厂的张国良创造了超细长杆的车削工作法哈尔滨的孙茂松创造了高速挑蜗杆先进工作法沈阳全福长对强力车刀等等带动和培养了大量现场工作人员全国劳动模范在20世纪50年代就建立起来的机床研究所兵器55所等均为有关切削加工的专业研究单位做出了很大贡献积累了丰富的经验例如高锰钢的切削方面航天工厂在高温合金电子行业在有色金属的切削方面冶金行业在高硬度钢与铸铁轧辊的切削方面高校与工厂还实践了多种新型切削加工方法等离子体加热)Õæ¿Õ»·¾³ÏÂÇÐÏ÷Ê©¼Ó¸÷ÖÖÇÐÏ÷ÒºµÄÇÐÏ÷Ê©¼ÓÅçÎíÀäÈ´µÄÇÐÏ÷µÈµÈÓеÄÒѸ¶ÖîÓ¦ÓÃĿǰÖйúÒÑÓµÓÐÇ¿´óµÄ»úÐµÖÆÔì¹¤ÒµÒ²ÕÆÎÕÁËÏȽøµÄÇÐÏ÷Óëµ¶¾ß¼¼ÊõÄÜÖÆÔìÎÀÐÇÄܽ¨ÉèÈýÏ¿¹¤³ÌºÍ´óÐ͵çÕ¾ÄÜÖÆÔìËùÓеij£¹æÓëÏȽøµÄ±øÆ÷»¯¹¤ÄÜÖÆÔìËùÓеÄÏȽø»ú´²ºÍµ¶¾ßÖйúÒѳÉΪ»úÐµÖÆÔìµÄ´ó¹úºÍÇ¿¹úÒÙÁ¢ÓÚå¾Çò¼¼ÊõÂäºóµÄ¾ÉÖйúÒѾ-һȥ²»¸´·µÁ˵¶¾ßË«·½½»Ìæ·¢Õ¹µ¶¾ßÓ빤¼þÓÐ×ŶÔÁ¢ºÍͳһµÄ¹ØÏµ¾-³£Íƶ¯ÁíÒ»·½·¢Õ¹Ç°½øÓÉÓÚÉú»î¹¤¼þÒ»·½µÄÇé¿ö¾-³£·¢Éú±ä»¯¹¤¼þ²ÄÁϵĻúеÐÔÄÜ(如强度产品的品种和批量逐渐增多工件的结构等等就不断向刀具提出更新当刀具不能满足这些要求时提高其性能刀具性能提高了接着工件又推动刀具继续前进工件材料多为灰铸铁它们较易加工19世纪中叶以后钢的产量迅速增加熟铁等钢的加工要难一些只能采有5~10 m/min的切削速度于是高碳工具钢已不能适应新的加工要求英国的罗伯特使切削速度提高到8~12 m/minÈÔÊǺÜÓкܵÄÇÐÏ÷ÆÕͨ¸Ö²ÄʱËÙ¶ÈÒ»ÏÂ×ÓÌá¸ßµ½30 m/min³ÉΪÇÐÏ÷¼¼ÊõÀúÊ·ÉϵÄÒ»´ÎÖØ´ó±ä¸ïµ¶¾ß²ÄÁ϶ÔÓÚµ±Ê±¼Ó¹¤µÄÐèÒª´óÌåÉÏÊÇÊÊÓ¦µÄ½øÈë20世纪以来其机械性能日益提高各种高强度钢高硬耐磨铸铁钛合金等难加工材料相继出现或者根本切不动人们又改进高速钢的化学成分与热处理方法出现了很多新型高速钢高钒超硬高速钢等20世纪20年代至30年代初并逐步用于生产可比高速钢提高4~10倍可以切削高速钢所加工不了的材料硬质合金脆性较大因此只能在部分加工范围内代替高速钢使用又出现了陶瓷人造金刚石等更为先进的刀具材料然而加上价昂直到最近它们的使用面均尚受到局限切削加工仍处在大量使用高速钢与硬质合金的时代硬质合金约占50%~60%ÌմɵÈÏȽøµ¶¾ß²ÄÁÏ硬铸铁正因为如此而在19世纪或20世纪初是根本不可想象的维持切削性能的最高温度以及切削速度的大致比值可以预期加工效率要求进一步提高高速切削即所谓超精密切削数控技术主导的和环保要求的所有这些而刀具材料更是关键是既有高的硬度和耐磨性刀具对于被加工工件和工作条件再适应交替发展这就是切削加工与刀具技术发展的历史规律17131665ɽ¶«¿ÆÑ§¼¼Êõ³ö°æÉçÐìºëɽÒë. 北京19805 Taylor F, W. On tne art of cutting metals. Trans. ASME, 1906, 28:13~206 [苏]列宁. 列宁选集. 中文译本第三卷. 北京19727 于启勋. 论现代刀具材料的新进展. 中国高校切削与先进制造技术研究会第六届年会论文集. 北京1999Öйú´ó°Ù¿ÆÈ«Êé³ö°æÉç¸ßµÈ½ÌÓý³ö°æÉç。