快速成型技术及应用论文
快速成型毕业论文
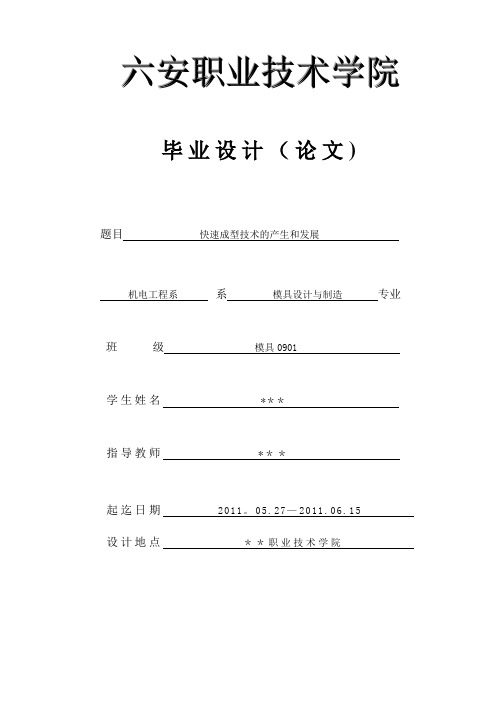
六安职业技术学院毕业设计(论文)题目快速成型技术的产生和发展机电工程系系模具设计与制造专业班级模具0901学生姓名 ***指导教师***起迄日期2011。
05.27—2011.06.15设计地点**职业技术学院**职业技术学院毕业(设计)论文【摘要】近年来,快速成型技术和逆向工程技术发展迅速,尤其是模具制造领域应用非常广泛,将快速成型技术与逆向工程技术相结合,可以在已有样件或原型的基础上进行复制和产品的创新再设计,缩短新产品的设计和研制周期,适应市场的多品种、小批量的快速响应能力。
【关键字】:快速成型技术;特点;分析;前景快速成型的产生与发展目录引言 .................................................................... - 4 - 第一章概述 .......................................................... - 5 - 1。
1 快速成型概述 ..................................................... - 5 - 1。
2 快速成型系统的基本工作原理....................................... - 6 -1.3 快速成型制造的发展................................................. - 6 - 第二章 RPM技术的原理和特点.............................................. - 7 - 2。
1 RPM技术的原理.................................................... - 7 - 2。
2 RPM技术发热内涵.................................................. - 9 -2.2。
快速成型技术论文范文
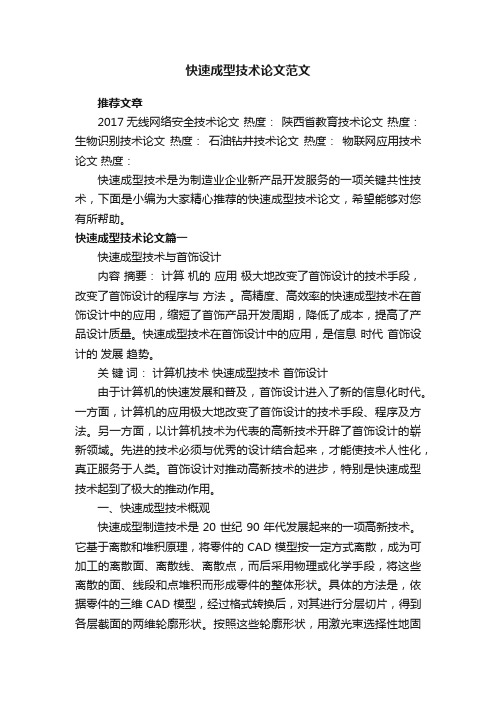
快速成型技术论文范文推荐文章2017无线网络安全技术论文热度:陕西省教育技术论文热度:生物识别技术论文热度:石油钻井技术论文热度:物联网应用技术论文热度:快速成型技术是为制造业企业新产品开发服务的一项关键共性技术,下面是小编为大家精心推荐的快速成型技术论文,希望能够对您有所帮助。
快速成型技术论文篇一快速成型技术与首饰设计内容摘要:计算机的应用极大地改变了首饰设计的技术手段,改变了首饰设计的程序与方法。
高精度、高效率的快速成型技术在首饰设计中的应用,缩短了首饰产品开发周期,降低了成本,提高了产品设计质量。
快速成型技术在首饰设计中的应用,是信息时代首饰设计的发展趋势。
关键词:计算机技术快速成型技术首饰设计由于计算机的快速发展和普及,首饰设计进入了新的信息化时代。
一方面,计算机的应用极大地改变了首饰设计的技术手段、程序及方法。
另一方面,以计算机技术为代表的高新技术开辟了首饰设计的崭新领域。
先进的技术必须与优秀的设计结合起来,才能使技术人性化,真正服务于人类。
首饰设计对推动高新技术的进步,特别是快速成型技术起到了极大的推动作用。
一、快速成型技术概观快速成型制造技术是20世纪90年代发展起来的一项高新技术。
它基于离散和堆积原理,将零件的CAD模型按一定方式离散,成为可加工的离散面、离散线、离散点,而后采用物理或化学手段,将这些离散的面、线段和点堆积而形成零件的整体形状。
具体的方法是,依据零件的三维CAD模型,经过格式转换后,对其进行分层切片,得到各层截面的两维轮廓形状。
按照这些轮廓形状,用激光束选择性地固化一层层的液态光敏树脂,或切割一层层的纸或金属薄片,或烧结一层层的粉末材料,以及用喷射源选择性地喷射黏结剂或热熔性材料,形成各截面的平面轮廓形状,并逐步叠加成三维立体零件。
快速成型技术不同于传统的“去除”加工方法,它是采用新的“增长”加工方法,即先用点和线制作一层“薄片毛干坯”,然后用多层薄片逐步叠加成复杂形状的零件。
快速成型3d打印原理技术论文
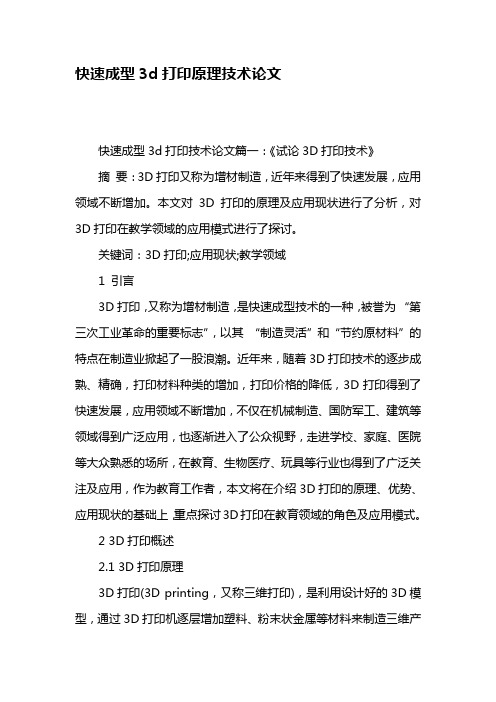
快速成型3d打印原理技术论文快速成型3d打印技术论文篇一:《试论3D打印技术》摘要:3D打印又称为增材制造,近年来得到了快速发展,应用领域不断增加。
本文对3D打印的原理及应用现状进行了分析,对3D打印在教学领域的应用模式进行了探讨。
关键词:3D打印;应用现状;教学领域1 引言3D打印,又称为增材制造,是快速成型技术的一种,被誉为“第三次工业革命的重要标志”,以其“制造灵活”和“节约原材料”的特点在制造业掀起了一股浪潮。
近年来,随着3D打印技术的逐步成熟、精确,打印材料种类的增加,打印价格的降低,3D打印得到了快速发展,应用领域不断增加,不仅在机械制造、国防军工、建筑等领域得到广泛应用,也逐渐进入了公众视野,走进学校、家庭、医院等大众熟悉的场所,在教育、生物医疗、玩具等行业也得到了广泛关注及应用,作为教育工作者,本文将在介绍3D打印的原理、优势、应用现状的基础上,重点探讨3D打印在教育领域的角色及应用模式。
2 3D打印概述2.1 3D打印原理3D打印(3D printing,又称三维打印),是利用设计好的3D模型,通过3D打印机逐层增加塑料、粉末状金属等材料来制造三维产品的技术[1]。
一般来说,通过3D打印获得物品需要经历建模、分割、打印、后期处理等四个环节[2],其中3D虚拟模型,可以是利用扫描设备获取物品的三维数据,并以数字化方式生成三维模型,或者是利用AutoCAD等工程或设计软件创建的3D模型,有些应用程序甚至可以使用普通的数码照片来制作3D模型,比如123D Catch[3]。
2.2 3D打印的优势与传统制造技术相比,3D打印不需事先制模,也不必铸造原型,大大缩短了产品的设计周期,减少了产品从研发到应用的时间,降低了企业因开模不当可能导致的高成本风险,使得特殊和复杂结构的模型的制作也变得相对简单,产品也更能凸显个性化。
另外,3D打印是增材制造,使用金属粉或其他材料,使部件从无到有制造出来,大大减少了原材料和能源的消耗,生产上实行了结构优化。
先进制造技术之快速成型技术论文

先进制造技术课程论文————快速成型技术课程名称:先进制造技术题目名称:快速成型技术班级:20 级专业班姓名:dh学号:000000000授课教师:时间:摘要:简介了快速成型技术的原理与特点,并阐述了快速成型技术的起源发展历程,分析了快速成型技术的研究现状及其推广应用情况,在此基础上根据快速成型技术的发展成果研究现状与市场需求展望了快速成型技术的未来发展趋势发展状况。
关键词:先进制造技术;快速成型技术; 发展历史;应用现状; 发展趋势;引言:本文阐述了快速成型技术的基本概念,包括快速成型技术基本原理,工艺过程,总结了快速成型技术的方法和特点,快速成型技术在产品开发中的应用现状、最后展望了快速成型技术的未来发展趋势。
正文:制造业是现代国民经济和综合国力的重要支柱,其生产总值一般占一个国家国内生产总值的20%~55%。
在一个国家的企业生产力构成中,制造技术的作用一般占60%左右。
而先进制造技术扮演了极其重要的角色,先进机械制造技术不仅是衡量一个国家科技发展水平的重要标志,也是国际间科技竞争的重点。
先进制造技术包罗万象,快速成型技术的出现和应用,代表着先进制造技术发展的高潮!《一》快速成型的基本原理快速成形技术(Rapid Prototyping;RPM)又称快速原型制造(Rapid Prototyping Manufacturing,简称RPM)技术,是基于材料堆积法的一种高新制造技术,被认为是近20年来制造领域的一个重大成果。
它集机械工程、CAD、逆向工程技术、分层制造技术、数控技术、材料科学、激光技术于一身,可以自动、直接、快速、精确地将设计思想转变为具有一定功能的原型或直接制造零件,从而为零件原型制作、新设计思想的校验等方面提供了一种高效低成本的实现手段。
与传统的机械切削加工,如车削、铣削等“材料减削”方法不同的是,“快速成型制造技术”是靠逐层融接增加材料来生成零件的,是一种“材料迭加”的方法,快速成型技术采用离散/堆积成型原理,根据三维CAD模型,对于不同的工艺要求,按一定厚度进行分层,将三维数字模型变成厚度很薄的二维平面模型。
快速成型技术论文
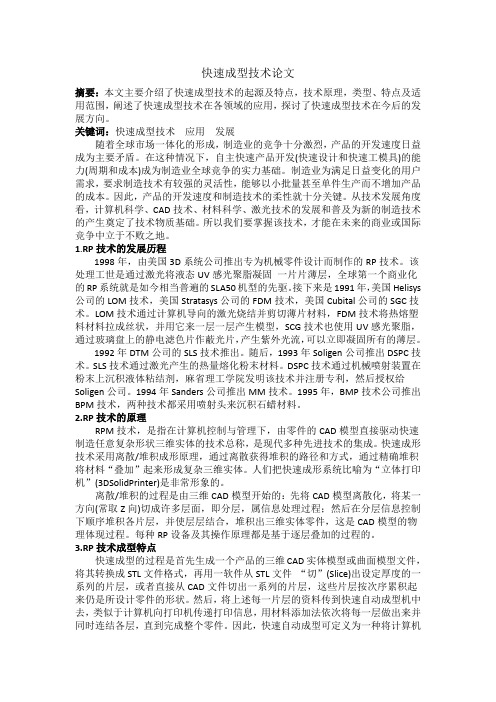
快速成型技术论文摘要:本文主要介绍了快速成型技术的起源及特点,技术原理,类型、特点及适用范围,阐述了快速成型技术在各领域的应用,探讨了快速成型技术在今后的发展方向。
关键词:快速成型技术应用发展随着全球市场一体化的形成,制造业的竞争十分激烈,产品的开发速度日益成为主要矛盾。
在这种情况下,自主快速产品开发(快速设计和快速工模具)的能力(周期和成本)成为制造业全球竞争的实力基础。
制造业为满足日益变化的用户需求,要求制造技术有较强的灵活性,能够以小批量甚至单件生产而不增加产品的成本。
因此,产品的开发速度和制造技术的柔性就十分关键。
从技术发展角度看,计算机科学、CAD技术、材料科学、激光技术的发展和普及为新的制造技术的产生奠定了技术物质基础。
所以我们要掌握该技术,才能在未来的商业或国际竞争中立于不败之地。
1.RP技术的发展历程1998年,由美国3D系统公司推出专为机械零件设计而制作的RP技术。
该处理工世是通过激光将液态UV感光聚脂凝固一片片薄层,全球第一个商业化的RP系统就是如今相当普遍的SLA50机型的先驱。
接下来是1991年,美国Helisys 公司的LOM技术,美国Stratasys公司的FDM技术,美国Cubital公司的SGC技术。
LOM技术通过计算机导向的激光烧结并剪切薄片材料,FDM技术将热熔塑料材料拉成丝状,并用它来一层一层产生模型,SCG技术也使用UV感光聚脂,通过玻璃盘上的静电滤色片作蔽光片,产生紫外光流,可以立即凝固所有的薄层。
1992年DTM公司的SLS技术推出。
随后,1993年Soligen公司推出DSPC技术。
SLS技术通过激光产生的热量熔化粉末材料。
DSPC技术通过机械喷射装置在粉末上沉积液体粘结剂,麻省理工学院发明该技术并注册专利,然后授权给Soligen公司。
1994年Sanders公司推出MM技术。
1995年,BMP技术公司推出BPM技术,两种技术都采用喷射头来沉积石蜡材料。
快速成型技术在工业设计中的应用研究
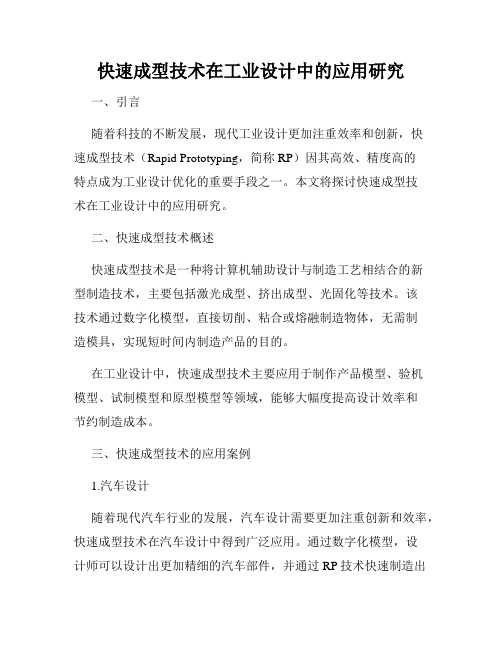
快速成型技术在工业设计中的应用研究一、引言随着科技的不断发展,现代工业设计更加注重效率和创新,快速成型技术(Rapid Prototyping,简称RP)因其高效、精度高的特点成为工业设计优化的重要手段之一。
本文将探讨快速成型技术在工业设计中的应用研究。
二、快速成型技术概述快速成型技术是一种将计算机辅助设计与制造工艺相结合的新型制造技术,主要包括激光成型、挤出成型、光固化等技术。
该技术通过数字化模型,直接切削、粘合或熔融制造物体,无需制造模具,实现短时间内制造产品的目的。
在工业设计中,快速成型技术主要应用于制作产品模型、验机模型、试制模型和原型模型等领域,能够大幅度提高设计效率和节约制造成本。
三、快速成型技术的应用案例1.汽车设计随着现代汽车行业的发展,汽车设计需要更加注重创新和效率,快速成型技术在汽车设计中得到广泛应用。
通过数字化模型,设计师可以设计出更加精细的汽车部件,并通过RP技术快速制造出原型模型进行验证和修改。
相比传统的手工制造方式,RP技术不仅效率更高,而且能够制造更加精准的模型,提供更多的设计空间。
2.工业机器人设计工业机器人是现代工厂自动化生产的重要组成部分,RP技术在机器人设计中得到广泛应用。
通过数字化模型,工程师可以更加快速地进行机器人设计和仿真分析,并通过快速成型技术制造出机器人模型进行试验和评估。
这种方式可以极大地加快机器人设计和仿真分析的效率,减少试制周期和成本。
3.医疗设备设计医疗设备是现代医疗行业的重要组成部分,准确、精细的设计对于患者的治疗效果有着至关重要的作用。
快速成型技术在医疗设备设计中得到了广泛应用,可以通过数字化模型设计出更加准确、高效的医疗设备,并通过RP技术制造体模型进行实验和验证。
四、快速成型技术的优势1.高效性快速成型技术可以大幅度提高设计和制造的效率,加快产品迭代周期。
与传统模具加工相比,RP技术可以在短时间内制造出产品原型模型进行验证和改进。
2.精度高快速成型技术利用数字化模型,精准的控制制造工艺,可以制造出非常高的精度的产品原型模型,同时,可以在改进过程中进行多次尺寸校验。
成型技术论文

成型技术论⽂ 为迎合市场需要将产品快速推向市场并占据先机,快速成型技术将是解决这⼀问题的关键。
这是店铺为⼤家整理的快速成型技术论⽂,仅供参考! 快速成型技术论⽂篇⼀ 快速成型技术的应⽤ 摘要:为迎合市场需要将产品快速推向市场并占据先机,快速成型技术将是解决这⼀问题的关键。
快速成型技术(以下简称RP)是⼀种集计算机辅助设计、精密机械、数控激光技术和材料科学为⼀体的新兴技术,采⽤离散堆积原理,将所设计物体的CAD模型转化为实体样件。
由于此技术采⽤三维形体转化为⼆维平⾯分层制造的原理,对物体构成复杂性不敏感,因此物体越复杂越能体现它的优越性。
关键词:快速成型模具 RP ⼀、快速成型的应⽤ 以 RP 为技术⽀撑的快速模具制造 RT(Rapid Tooling)也正是为了缩短新产品开发周期,早⽇向市场推出适销对路的、按客户意图定制的多品种、⼩批量产品⽽发展起来的新型制造技术。
由于产品开发与制造技术的进步,以及不断追求新颖、奇特、多变的市场消费导向,使得产品(尤其是消费品)的寿命周期越来越短已成为不争的事实。
例如,汽车、家电、计算机等产品,采⽤快速模具制造技术制模,制作周期为传统模具制造的 1/3~1/10,⽣产成本仅为 1/3~1/5。
所以, ⼯业发达国家已将RP/RT 作为缩短产品开发时间及模具制作周期的重要研究课题和制造业核⼼技术之⼀,我国也已开始了快速制造业的研究与开发应⽤⼯作。
⼆、基于 RPM 的快速模具制造⽅法 模具是制造业必不可少的⼿段,其中⽤得最多的有铸模、注塑模、冲压模和锻模等。
传统制作模具的⽅法是:对⽊材或⾦属⽑坯进⾏车、铣、刨、钻、磨、电蚀等加⼯,得到所需模具的形状和尺⼨。
这种⽅法既费时⼜费钱,特别是汽车、摩托车和家电所需的⼀些⼤型模具,往往造价数⼗万元以上,制作周期长达数⽉甚⾄⼀年。
⽽基于RPM 技术的RT 直接或间接制作模具,使模具的制造时间⼤⼤缩短⽽成本却⼤⼤降低。
1、⽤快速成形机直接制作模具 由于⼀些快速成形机制作的⼯件有较好的机械强度和稳定性,因此快速成形件可直接⽤作模具。
零件制造的快速成型技术及其应用
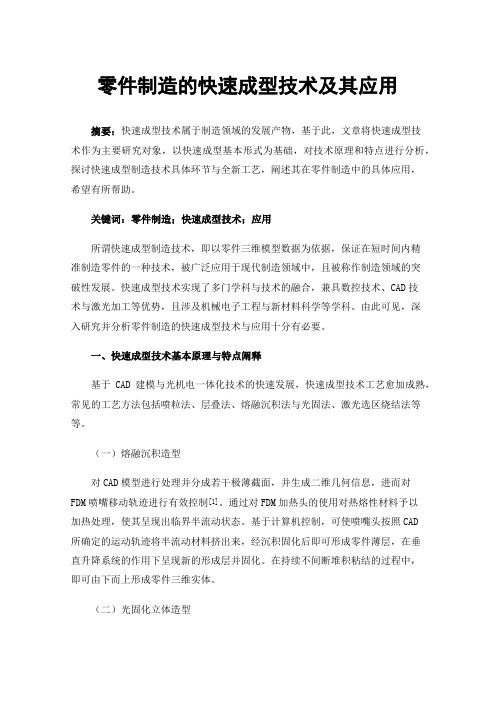
零件制造的快速成型技术及其应用摘要:快速成型技术属于制造领域的发展产物,基于此,文章将快速成型技术作为主要研究对象,以快速成型基本形式为基础,对技术原理和特点进行分析,探讨快速成型制造技术具体环节与全新工艺,阐述其在零件制造中的具体应用,希望有所帮助。
关键词:零件制造;快速成型技术;应用所谓快速成型制造技术,即以零件三维模型数据为依据,保证在短时间内精准制造零件的一种技术,被广泛应用于现代制造领域中,且被称作制造领域的突破性发展。
快速成型技术实现了多门学科与技术的融合,兼具数控技术、CAD技术与激光加工等优势,且涉及机械电子工程与新材料科学等学科。
由此可见,深入研究并分析零件制造的快速成型技术与应用十分有必要。
一、快速成型技术基本原理与特点阐释基于CAD建模与光机电一体化技术的快速发展,快速成型技术工艺愈加成熟,常见的工艺方法包括喷粒法、层叠法、熔融沉积法与光固法、激光选区烧结法等等。
(一)熔融沉积造型对CAD模型进行处理并分成若干极薄截面,并生成二维几何信息,进而对FDM喷嘴移动轨迹进行有效控制[1]。
通过对FDM加热头的使用对热熔性材料予以加热处理,使其呈现出临界半流动状态。
基于计算机控制,可使喷嘴头按照CAD所确定的运动轨迹将半流动材料挤出来,经沉积固化后即可形成零件薄层,在垂直升降系统的作用下呈现新的形成层并固化。
在持续不间断堆积粘结的过程中,即可由下而上形成零件三维实体。
(二)光固化立体造型将业态的光固化树脂放于液槽内,经偏转镜的作用在液面实现激光束扫描,经计算机技术合理控制扫描轨迹与光线,在有光点的部位液体会固化。
自成型初期,工作平台会在液面明确具体深度,在液面光斑聚焦以后即可根据计算机提出的指令逐一进行扫描并固化。
在完成一层扫描后,没有被照射的部位始终是液态树脂。
随后,升降台会使平台降低一层的高度,在已经成型层面再次布满树脂,通过对刮平器的使用可对树脂液面大粘度的部分刮平处理,随后开展下一层扫描操作。
- 1、下载文档前请自行甄别文档内容的完整性,平台不提供额外的编辑、内容补充、找答案等附加服务。
- 2、"仅部分预览"的文档,不可在线预览部分如存在完整性等问题,可反馈申请退款(可完整预览的文档不适用该条件!)。
- 3、如文档侵犯您的权益,请联系客服反馈,我们会尽快为您处理(人工客服工作时间:9:00-18:30)。
基于激光快速成型技术的金属快速成型技术摘要:文章详细介绍了金属粉末快速成型的研究现状 ,分析了金属粉末选择性激光烧结的工艺特点,对这些工艺的影响因素进行了讨论。
关键词:选区激光烧结;金属零件;影响因素。
引言快速制造 (Rapid Manufacturing) 金属零件一直受到国内外的广泛重视 , 是当今快速成型领域的一个重要研究方向。
到目前为止 ,用于直接成型金属材料、制备三维金属零件的技术主要有激光近形制造与金属粉末的选择性激光烧结技术。
激光近形制造(LENS) ,又称激光熔覆制造或熔滴制造 ,它将激光熔覆工艺与激光快速成型技术相结合 , 利用激光熔覆工艺逐层堆积累加材料,形成具有三维形状的三维结构。
在该方面 ,美国的Aeromet、德国的汉诺威激光中心以及清华大学激光加工研究中心等均进行了大量的研究 , 并得到了具有一定形状的三维实体零件。
有异于激光近形制造 ,选择性激光烧结则有选择地逐层烧结固化粉末金属得到三维零件。
在这一领域,美国的DTM丶德国的汉诺威激光中心等进行了多元金属的烧结研究。
就选区激光烧结(SelectiveLaser Sintering , SLS)而言 ,根据成型用金属粉末的不同 , 人们又开发出多种工艺途径来实现金属零件的烧结成型 ,主要有三种途径:一是利用金属粉末与有机粘结剂粉末共混粉体的间接烧结,金属粉末与有机粘结剂粉末均匀共混,烧结中,低熔点的粘结剂粉末熔化并将高熔点的金属粉末粘结,形成原型(“绿件”),经后处理,烧失粘结剂,形成“褐件”,最后通过金属熔渗工艺得到致密的金属件;二是利用金属混合粉末的直接烧结 , 其中一种粉末具有较低的熔点(如铜粉) ,另一种粉末熔点较高 (如铁粉) ,烧结中低熔点的金属粉末铜熔化并将难熔的铁粉粘结在一起 , 这种方法同样需要较大功率激光器;三是利用单一成分金属粉末的直接烧结,这种方法目前主要用于低熔点金属粉末的烧结,对熔点高的金属粉末,需采用大功率激光器。
本文分别对上述的间接和直接烧结成型工艺进行了初步的研究。
1 SLS的烧结原理激光选择性烧结快速成型技术是使用激光束熔化或烧结粉末材料 ,利用分层的思想 ,把计算机中的 CAD 模型直接成型为三维实体零件。
它的创新之处在于将激光、光学、温度控制和材料相联系。
SLS烧结原理如图1所示,烧结过程可分为三部分: (1)首先在粉体床上铺一薄层粉体 , 并压实 , 可以根据需要 ,在激光烧结前进行预热; (2)激光照射粉体层 ,烧结粉体,形成所设计零件一层的形状;(3) 粉体床下降一个薄层厚度的距离;重复上面的过程 ,直到原型零件完成。
SLS对粉末烧结的明显优势在于: (1) 和其它的加工方法比较,能获得优良的材料性能,同时,它的加工材料范围比较宽 (聚合物、金属、陶瓷、铸造砂等);(2) 易于实现液相烧结 , 烧结周期比较短; (3) 比传统的烧结方法更易得到密实的以粉末金属为原料的产品;(4)工艺比较简单 , 烧结路线、烧结温度便于控制。
2 金属零件间接烧结的工艺过程图 2 为基于小功率激光烧结快速成型设备 RAP- II的金属零件快速制造的工艺过程简图。
由图可知 , 主要分三个阶段: 一是利用快速成型技术的 RP原型件 (“绿件”)的制作 ,该部分的关键在于如何选用合理的粉末配比和加工工艺参数实现原型件的制作。
试验表明 ,对 RP原型件成型来说 ,混合粉体中环氧树脂粉末比例高 ,有利于其准确致密成型 ,成型质量高。
但环氧树脂粘结剂含量过高 ,金属粉末含量过低 , 则会出现褐件制作时的烧失“塌陷”现象和金属熔渗时出现局部渗不足现象。
可见 ,粉末材料配比将严重影响原型件及褐件的制作质量,而且两阶段对配比的要求相互矛盾。
原则上必须兼顾绿件成型所需的最少粘结剂成分,同时又不致因过高而导致褐件难以成型。
实际加工中 ,环氧树脂与金属粉末的比例一般控制在 1:5 与 1:3 之间。
同时 ,影响激光烧结快速成型原型件质量的烧结参数很多 , 如粉末材料的物性、扫描间隔、扫描层厚、激光功率以及扫描速度等。
实验表明 ,对于小功率激光器的激光烧结快速成型系统 RAP- II, 激光功率可调范围很小 , 激光功率对烧结性能的影响可以归结到扫描速度上 , 而扫描速度的选择必须兼顾加工效率、烧结过程与烧结质量的要求。
较低的扫描速度 ,可以保证粉末材料的充分熔化 , 获得理想的烧结致密度; 但是 , 扫描速度过低 ,材料熔化区获得的激光能量过多 ,容易引起“爆破飞溅现”象 ,出现烧结表面“疤痕” ,且熔化区内易出现材料“炭化” ,从而降低烧结表面质量。
为保证加工层面之间与扫描线之间的牢固粘结 , 采用的扫描间隔不宜过大。
实际加工中 ,烧结线间、层面间应有少许重叠 ,方可获得较好的烧结质量。
扫描层厚也是激光烧结成型的一个重要参数 ,它的选择 ,也与激光烧结成型的烧结质量密切相关。
扫描层厚度必须小于激光束的烧结深度 , 使正烧结的新层与已烧结层能牢固地粘连在一起 ,形成致密的烧结体 ,但过小的扫描层厚度 , 会增加烧结应力 , 损坏已烧结层面 , 烧结效果反而降低 , 因此,扫描层厚选择必须适当,才能保证获得较好的烧结质量。
总的来说 ,工艺参数的选取不仅要保证层面之间、烧结线之间的牢固粘结 ,还应该保证粉末材料的充分熔化 ,即烧结实体中不应存在“夹生”现象 , 应保证烧结成型各工艺参数的互相匹配。
同时 ,尽量做到粉末材料不炭化 ,烧结过程平稳。
在此基础上尽可能采用较大的工艺参数 , 提高加工效率。
二是“褐件”的制作 ,关键在于探索如何烧失原型件中的有机杂质 , 获得具有相对准确形状和强度的金属结构体。
褐件制作时需经过两次烧结过程 ,烧结温度和时间是主要的影响因素。
应控制合适的烧结温度和时间 ,随着粘结剂烧失的同时 ,使金属粉末颗粒间发生微熔粘结 , 从而保证原型件不致塌陷。
三是金属熔渗阶段 ,关键在于选用合适的熔渗材料及工艺 ,以获得较致密的最终金属零件。
原型件烧结完成后 ,经过二次烧结与三次烧结 ,得到一个具有一定强度与硬度、内部具有疏松性“网状连通”结构的“褐件”。
这些都是金属熔渗工艺的有利条件。
试验表明 ,合适的熔渗材料对形成金属件的致密性有较大影响。
所选渗入金属必须比“褐件”中金属的熔点低 ,以保证在较低温度下渗入。
3 直接烧结成型工艺图4为基于较大功率的激光烧结金属零件快速制造的工艺过程简图。
由图可知 , 成型过程明显缩短 ,无需间接烧结时复杂的后处理阶段。
但必须有较大功率的激光器 , 以保证直接烧结过程中金属粉末的直接熔化。
因而,直接烧结中激光参数的选择 ,被烧结金属粉末材料的熔凝过程及控制是烧结成型中的关键。
激光功率是激光直接烧结工艺中的一个重要影响因素。
功率越高 , 激光作用范围内能量密度越高 , 材料熔化越充分 , 同时烧结过程中参与熔化的材料就越多,形成的熔池尺寸也就越大,粉末烧结固化后易生成凸凹不平的烧结层面,激光功率高到一定程度 ,激光作用区内粉末材料急剧升温 ,能量来不及扩散,易造成部分材料甚至不经过熔化阶段直接汽化 , 产生金属蒸汽。
在激光作用下该部分金属蒸汽与粉末材料中的空气一道在激光作用区内汇聚、膨胀、爆破 ,形成剧烈的烧结飞溅现象 ,带走熔池内及周边大量金属 , 形成不连续表面 , 严重影响烧结工艺的进行 ,甚至导致烧结无法继续进行。
同时这种状况下的飞溅产物也容易造成烧结过程的“夹杂”。
光斑直径是激光烧结工艺的另外一个重要影响因素。
总的来说 , 在满足烧结基本条件的前提下 , 光斑直径越小 , 熔池的尺寸也就可以控制得越小 , 越易在烧结过程中形成致密、精细、均匀一致的微观组织。
同时 ,光斑越细 ,越容易得到精度较好的三维空间结构 ,但是光斑直径的减小 , 预示着激光作用区内能量密度的提高 ,光斑直径过小 ,易引起上述烧结飞溅现象。
扫描间隔是选择性激光烧结工艺的又一个重要影响因素 , 它的合理选择对形成较好的层面质量与层间结合 , 提高烧结效率均有直接影响。
同间接工艺一样 , 合理的扫描间隔应保证烧结线间、层面间有少许重叠 [7 - 8 ]。
在激光连续烧结成形过程中 , 整个金属熔池的凝固结晶是一个动态的过程。
随着激光束向前移动 , 在熔池中金属的熔化和凝固过程是同时进行的。
在熔池的前半部分 , 固态金属不断进入熔池处于熔化状态 ,而在熔池的后半部分 ,液态金属不断脱离熔池而处于凝固状态。
由于熔池内各处的温度、熔体的流速和散热条件是不同的 ,在其冷却凝固过程中 ,各处的凝固特征也存在一定的差别。
对多层多道激光烧结的样品 ,每道熔区分为熔化过渡区和熔化区。
熔化过渡区是指熔池和基体的交界处 , 在这区域内晶粒处于部分熔化状态 , 存在大量的晶粒残骸和微熔晶粒 , 它并不是构成一条线,而是一个区域 , 即半熔化区。
半熔化区的晶粒残骸和微熔晶粒都有可能作为在凝固开始时的新晶粒形核核心。
对 Ni 基金属粉末烧结成形的试样分析表明: 在熔化过渡区其主要机制为微熔晶核作为异质外延 , 形成的枝晶取向沿着固—液界面的法向方向。
熔池中除熔化过渡区外 ,其余部分受到熔体对流的作用较强 , 金属原子迁移距离大 ,称为熔化区。
该区域在对流熔体的作用下 ,将大量的金属粉末粘接到熔池中 , 由于粉末颗粒尺寸的不一致 (粉末的粒径分布为 15~130μm) , 当激光功率不太大时 ,小尺寸粉末颗粒可能完全熔化 ,而大尺寸粉末颗粒只能部分熔化,这样在熔化区中存在部分熔化的颗粒 , 这部分的颗粒有可能作为异质形核核心 ;当激光功率较高时 ,能够完全熔化熔池中的粉末 ,在这种情况下 ,该区域主要为均质形核。
在激光功率较小时,容易形球 , 且形球对烧结成形不利 , 因此对 Ni 基金属粉末烧结成形通常采用较大的功率密度,其熔化区其主要为均质形核 ,形成等轴晶。
4 结论基于小功率激光烧结系统 , 采用间接烧结工艺 , 可以实现金属零件的快速烧结成型。
但成型过程中影响质量的因素较多,必须统筹兼顾合理选取,才能获得高质量的成型零件。
参考文献 :[1] 张可朋,郝昱宇,王鹏.金属烧结过程中温度场分布的有限元分析[J].黑龙江冶金.2015(06)[2] 罗新华 ,花国然.快速原型制造技术的应用及进展[J ].机械制造 ,1998 ,(3) :7 - 9.[3] 尚晓峰,刘伟军,王天然,王志坚.金属粉末激光成形扫描方式[J]. 机械工程学报.2005(07)[4] 凡进军,赵剑峰,肖猛.基于直接激光金属烧结的金属粉末扫描路径实验研究[J]. 热加工工艺. 2010(13)[5] 王家金. 激光加工技术[M]. 北京:中国计量出版社 ,1992 ,63 - 66.[6] 潘海鹏.快速成型制造中分层处理技术的研究[D]. 南昌大学 2007JIANG SU UNIVERSITY《快速成型技术及应用》课程论文班级:机械卓越1301学号:3130301006学生姓名:齐作霖。