品管部管理评审报告
品质控制部管理评审报告

品质控制部管理评审报告1. 引言本报告旨在对品质控制部的管理进行评审,并提出改进建议。
通过这次评审,我们希望能够进一步提高品质控制部的工作效率和质量水平。
2. 评审内容及方法2.1 评审内容我们对品质控制部的组织架构、工作流程、人员配置、流程控制、质量标准以及工作成果等进行了评审。
2.2 评审方法我们采用了综合性评估的方法,包括文件审查、观察实地工作、访谈员工以及与相关部门负责人沟通等。
3. 评审结果根据评审的结果,我们得出以下结论:3.1 组织架构品质控制部的组织架构相对合理,各岗位的职责分工明确,但针对跨部门协作方面可以进一步优化。
3.2 工作流程品质控制部的工作流程比较规范,但在一些重要环节存在一定的滞后和瓶颈,需要进行优化和改进。
3.3 人员配置品质控制部的人员配置相对合理,但在某些职位上可能需要增加专业技术人员,以进一步提升工作质量。
3.4 流程控制品质控制部在流程控制方面存在一定的不足,需要加强对各项关键流程的监控和控制,以降低质量风险。
3.5 质量标准品质控制部的质量标准相对明确,但在与相关部门的对接方面还有一些待改进的空间,以确保整体质量的一致性和稳定性。
3.6 工作成果品质控制部的工作成果整体较好,但仍需加强与其他部门的协作,提高沟通效率,确保工作成果的及时交付和持续改进。
4. 改进建议基于评审结果,我们提出以下改进建议:4.1 优化组织架构改进跨部门协作机制,加强与其他部门的沟通和协调,以提高工作效率和协同能力。
4.2 改进工作流程针对工作流程中的滞后和瓶颈,进行细致分析和优化,以提高工作效率和质量。
4.3 调整人员配置根据工作需求,适当增加专业技术人员,以提升整体的技术水平和工作质量。
4.4 加强流程控制建立监控机制,加强对关键流程的控制和监督,以降低质量风险。
4.5 改进质量标准加强与相关部门的沟通和协调,确保质量标准的一致性和稳定性。
4.6 提升协作能力加强与其他部门的协作,提高沟通效率,确保工作成果的及时交付和持续改进。
品质部管理评审报告

品质部管理评审报告品质部年度工作自查报告汇报人:20XX年品质部目标1.加强与供方的沟通和管理,进货产品合格率达%以上; 2.加强生产过程的控制,成品一次装配合格率达%以上;3.加强生产过程的控制,降低各过程不良率,注塑不良率低于%,喷涂不良率低于%,压铸不良率低于%; 4.确保产品出厂合格,提高客人满意度,客人投诉低于%。
20XX年1月-6月进货检验合格率20XX年1月-6月进货检验合格率2500 99.28% 20XX年1500 1000 500 0 检验批次不合格批次合格率一月968 7 99.28% 二月674 12 98.22% 三月20XX年41 97.97% 四月1677 37 97.79% 五月1713 36 97.90% 六月1484 34 97.71% 98.22% 97.97% 97.79% 97.90% 98.00% 97.71% 97.50% 97.00% 96.50% 99.00% 98.50% 99.50%目标值为%,实际达到%,完成目标值。
20XX年1月-6月来料前十位关健类供应商不合格率20XX 年1月-6月来料前十位关键类供应商不合格率100 80 60 40 20 0 14.58% 2.86% 欣资东燕喷漆喷漆35 1 2.86% 48 7 14.58% 16.67% 13.33% 小苗电源线55 12 21.82% 金丰电源线 4 250.00% 21.82% 15.07% 3.41% 乔良陈奇杰发热管内导线88 3 3.41% 73 11 15.07% 11.54% 12.82% 6.45% 沙连章内导线26 3 11.54% 家泰温控器39 5 12.82% 泉力温控器31 2 6.45% 天威温控器 4 1 25.00% 50.00% 60.00% 50.00% 40.00% 30.00% 25.00% 20.00% 10.00% 0.00%振申双金属片12 2 16.67%粤华泰线路板15 2 13.33%检验批次不合格批次不合格率20XX年1月-6月来料前十位关健类供应商不合格主要原因1.从统计的数据来看,不合格率排在第一位的是电源线,主要原因是摇摆测试通不过,已经上报高层,要求供应商改善,改善正在进行中。
公司管理部管理评审报告范文
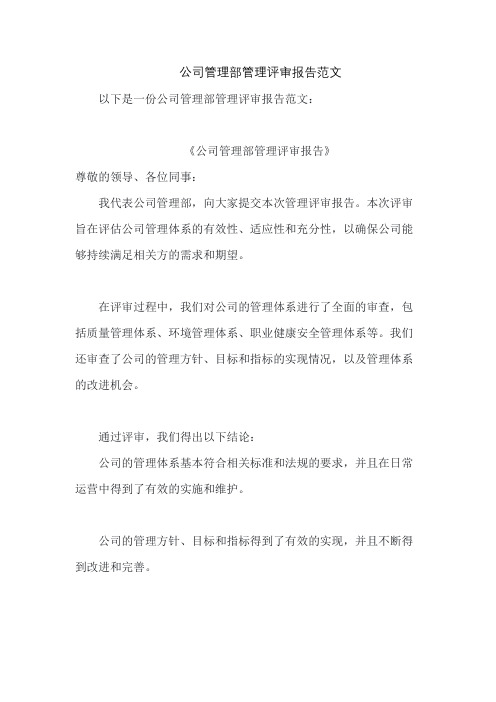
公司管理部管理评审报告范文
以下是一份公司管理部管理评审报告范文:
《公司管理部管理评审报告》
尊敬的领导、各位同事:
我代表公司管理部,向大家提交本次管理评审报告。
本次评审旨在评估公司管理体系的有效性、适应性和充分性,以确保公司能够持续满足相关方的需求和期望。
在评审过程中,我们对公司的管理体系进行了全面的审查,包括质量管理体系、环境管理体系、职业健康安全管理体系等。
我们还审查了公司的管理方针、目标和指标的实现情况,以及管理体系的改进机会。
通过评审,我们得出以下结论:
公司的管理体系基本符合相关标准和法规的要求,并且在日常运营中得到了有效的实施和维护。
公司的管理方针、目标和指标得到了有效的实现,并且不断得到改进和完善。
公司的管理体系存在一些改进的机会,例如进一步提高员工的参与度和意识,加强内部沟通和协调等。
针对以上结论,我们提出以下建议:
加强员工培训和教育,提高员工的参与度和意识。
加强内部沟通和协调,建立更加高效的工作机制。
进一步完善管理体系,持续提高管理水平。
最后,感谢大家对本次管理评审的支持和配合。
我们将继续努力,不断完善公司的管理体系,为公司的可持续发展做出更大的贡献。
谢谢大家!
公司管理部
[报告日期]。
最新管理评审汇报(品管)

品管部管理评审汇报材料1.品管部质量目标达成情况:品管部质量目标:1)准确检验成品,市场出现批次不合格控制在1次/年以下。
2)对每条生产线的全面卫生督察验证频率不少于1 次/2月。
品管部本年度(1月-8月)检验成品456批次,合格批次456批,合格率100%,市场未出现批次不合格产品;本年度每2个月对每条生产线进行全面监督,对相应的质量问题在质量分析会上予以通报,并对出现问题的整改状况进行了验证。
实现了本部门的质量目标。
2.品管部检验标准适宜情况:根据文件要求和实际情况,对检验标准、作业指导书进行了修订:将成品理化指标检验样品数由每批50罐调整为按杀菌釜取样;商业无菌检验指导书规定“王老吉”保温条件为37℃,实际作业中进行了37℃和55℃两种保温试验,在新修改的文件中已经调整;完善了隔离品检验作业指导书,对各种原因引起的质量异常品都规定了具体的检验方案;在微生物检验标准中明确规定了取样位置、取样方法和结果判定;补充了实验室所用仪器的操作规程、维护方法以及相应记录表格。
3.品管部资源配置情况:品管部现有工作人员8人。
主要负责成品的理化检测和微生物检测、车间工艺卫生检验和水质微生物检验、隔离品检验处理、协助集团品管部对外加工厂异常品、顾客投诉产品进行检验分析。
在隔离品处理过程中,由于检验数量大、项目多,还需配置一台计算机、一台投影仪、一台正压型气密性测定仪、一台负压型气密性测定仪、一台真空压力测定仪、一把数显游标卡尺,一台霉菌培养箱、一台生化培养箱。
4.品管部接收质量投诉情况:品管部本年度共接收顾客投诉67例,其中因为运输不当原因造成的产品变质有26例,微生物引起的变质有24例,制程缺陷有4例,原材料原因造成的产品变质有2例,产品有异物(昆虫)有8例,感官差异有3例。
详细投诉情况及相关处理措施如下:。
品质部管理评审报告2
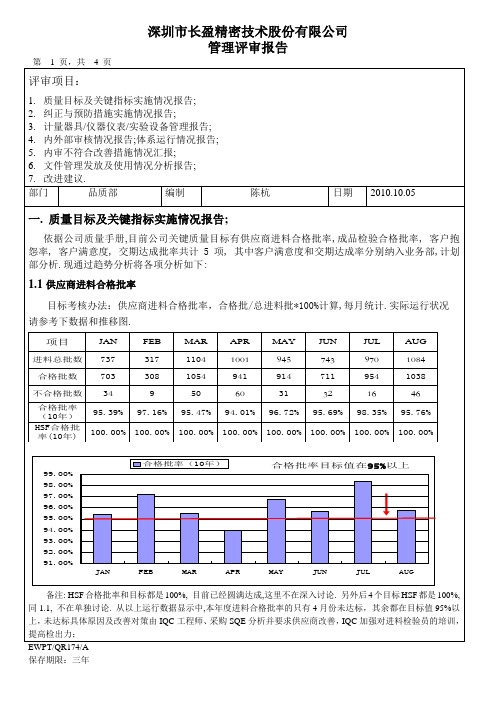
深圳市长盈精密技术股份有限公司管理评审报告EWPT/QR174/A保存期限:三年深圳市长盈精密技术股份有限公司管理评审报告第 2 页,共4 页EWPT/QR174/A保存期限:三年深圳市长盈精密技术股份有限公司管理评审报告EWPT/QR174/A保存期限:三年深圳市长盈精密技术股份有限公司管理评审报告EWPT/QR174/A保存期限:三年深圳市长盈精密技术股份有限公司管理评审报告部门品质部编制陈杭日期2010.10.05五..文件管理发放及使用情况分析报告;文件管理依据文件控制程序作业,公司文件分为;一阶文件、二阶文件、三阶文件与四阶文件。
质量手册为公司纲领性文件描述公司发展方向与宗旨,程序文件以描述各过程如何运作之依据,三阶文件是细化作业人员动作以文字描述讲解,四阶文件是记录之表单以证明记录符合标准要求之证据。
因公司推行OSHAS18001体系需要,按照国家标准及法规要求修改(新增)相关程序及作业指导书,以下为今年各体系文件发行状况(详见下表):项目JAN FEB MAR APR MAY JUN JUL AUG SEP OCT NOV DEC新发行10 2 17 17 11 8 4 5改版发行12 6 12 8 19 13 4 4因文件分发回收有0 0 0 0 0 0 0 0误造成误用发行文件总数量22 8 29 25 30 21 8 9 0 0 0 0六、改进建议通过本次部门内部重要指标评审,目前需要改进的项目主要表现于以下几个方面:1)客户抱怨率超标需要持续跟进,并切实进行有效的辅导,同时加强IQC的检出能力.保存期限:三年。
品质部管理评审报告

品质部管理评审报告一、背景和目的本报告旨在对品质部的管理工作进行评审,进一步提升公司产品和服务的质量,为客户提供更好的体验。
二、评审范围本次管理评审主要围绕以下几个方面展开:1. 品质部的组织架构和人员配置2. 品质部的质量管理制度和流程3. 品质部的工作效率和成果4. 品质部与其他部门的协作情况三、评审方法本次管理评审采用了以下方法:1. 文件审查:审查品质部的管理制度、流程文件,了解其建立、执行和改进情况。
2. 数据分析:分析品质部的关键绩效指标和工作数据,了解其运营情况。
3. 现场观察:到品质部进行实地考察,观察其工作环境和运作情况。
4. 交流访谈:与品质部的相关人员进行访谈,了解他们对品质管理的理解和实施情况。
四、评审结果1. 组织架构和人员配置品质部的组织架构清晰,职责明确,各岗位配备合理,能够有效地开展品质管理工作。
2. 质量管理制度和流程品质部建立了一套完善的质量管理制度和流程,包括质量目标设定、品质检查、问题处理等环节。
制度规范、流程清晰,有利于有效控制和改进产品和服务质量。
3. 工作效率和成果品质部通过引入先进的质量管理工具和技术,提高了工作效率和成果。
各项工作任务按时完成,质量问题得到及时发现和解决,产品合格率得到明显提升。
4. 部门协作情况品质部与其他部门之间的协作紧密,形成了良好的工作合力。
与生产部门的协作更是密切,及时沟通和互动,有效解决生产中的质量问题。
五、改进建议1. 进一步优化组织架构和人员配置,根据工作需要合理调整岗位设置和人员数量,提高工作效率和质量管理能力。
2. 加强培训和技能提升,提高品质部人员的专业水平和综合素质,为更好地开展品质管理工作打下基础。
3. 定期评估和改进质量管理制度和流程,根据实际情况进行调整和优化,以适应市场需求的变化。
4. 持续加强与其他部门的协作,加强沟通和合作,形成良好的工作合力,共同提升产品和服务质量。
六、结论通过本次管理评审,我们对品质部的工作给予了肯定,并提出了相应的改进建议。
品质部年度管理评审报告

一、概述在过去的一年里,品质部全体员工积极努力,充分发挥各自的专业能力,以确保公司产品和服务的质量和可靠性。
本报告将对品质部的管理绩效进行评估和总结,并提出改进和提升的建议。
二、工作目标与完成情况1.提高产品质量:通过优化生产过程、加强质量控制,并引入新的质量管理工具和方法,成功提高了产品的质量。
产品的客诉率和退货率明显下降,得到了客户的一致好评。
2.提升服务质量:加强与客户的沟通和反馈机制,及时解决客户问题,提升了客户满意度。
服务质量指标得到了显著提高,客户投诉率明显下降。
3.实施质量改进活动:根据数据分析和反馈意见,开展了一系列质量改进活动,改善了生产流程、产品设计和服务流程等环节的问题,提升了整体质量水平。
4.培训和人员发展:组织了一系列的质量培训活动,提高了员工的质量意识和技能水平,同时也鼓励员工参与外部培训和学习,努力提升自身的综合素质。
5.质量管理体系的维护和升级:继续维护和改进质量管理体系,确保其符合国家和行业标准要求。
同时,根据公司的发展需求,升级了部分管理体系,进一步提升了管理效能和规范性。
三、存在的问题1.仍有部分产品存在质量问题,需要进一步改进生产工艺和控制措施,以提高产品稳定性和可靠性。
2.还需要加强与供应商的合作和沟通,构建更加紧密的供应链管理体系,以确保原材料和零部件的质量和供应可靠性。
3.服务反馈机制还不够完善,需要加强与客户的沟通和反馈,及时解决客户问题,提升服务质量。
4.需要进一步加强员工的专业能力培养,特别是新员工的培训和技能提升,以满足公司不断提高的质量管理要求。
5.需要继续完善质量管理体系,加强对重要环节和关键岗位的管理和监督。
四、改进与提升措施1.加强产品生产过程的监控和控制,强化质量管理工作的科学性和系统性,进一步提高产品的稳定性和可靠性。
2.建立健全供应商管理体系,加强与供应商的合作,共同提升供应链的质量管理水平。
3.加强与客户的沟通和反馈机制,持续改进服务质量,建立客户满意度调查体系,定期评估和改进服务质量。
品质部年度管理评审报告

尊敬的领导、各位同事:大家好!我是品质部门经理,今天我将向大家汇报品质部的年度管理评审情况。
一、综述过去一年,品质部门积极履行着公司赋予的品质管理职责,团队成员精诚合作,以提升产品品质为核心目标,取得了显著进展。
本报告将从以下四个方面对品质部门的工作进行总结和评析。
二、绩效评估1.重点项目完成情况:我们设定了一系列关键任务和重点项目,并及时分解任务、跟踪执行。
经过全体成员的共同努力,所有重点项目按时完成,并且在品质管理和产品质量方面取得了显著提升。
2.工作流程改善:我们对现有的品质管理流程进行了全面复审,并根据产线特点进行了优化和完善。
通过流程改进,我们提高了问题反馈的速度和准确性,实现了问题快速解决和及时预警。
3.品质培训与知识传承:品质部门注重团队成员的培养和知识传承。
我们在过去一年举办了系统的品质管理培训,不断提高团队成员的专业能力和综合素质。
同时,我们注重团队成员之间的交流和经验分享,提升了整个团队的综合能力。
三、存在问题1.人员不足。
品质部门在过去一年中承担了大量的项目和任务,人员配备不足,严重影响了工作效率和质量水平。
我们需要增加专业人员的配备,提高人员的综合素质和专业能力。
2.沟通协调不畅。
品质部门与其他部门之间沟通协调存在一定的问题,需要加强合作,提升团队之间的沟通能力和协调能力。
四、工作计划1.加强人员招聘和培训。
面对人员不足的问题,我们将加大招聘力度,引入更多优秀的品质管理人才。
同时,加强内部培训和外部培训,使团队成员具备更全面的知识和技能。
2.持续改进流程。
我们将进一步优化品质管理流程,加强与其他部门的协作和信息共享,实现更高效的品质管理。
3.加强团队合作与沟通。
我们将加强团队内外部的合作交流,提高团队成员之间的沟通能力和团队协作能力,实现更好的协同工作。
五、总结过去一年,品质部门全员奋发工作,取得了明显的业绩和品质改进。
然而,我们也要面对存在的问题,并制定相应的解决方案和改进计划。
品质部质量管理评审汇报材料
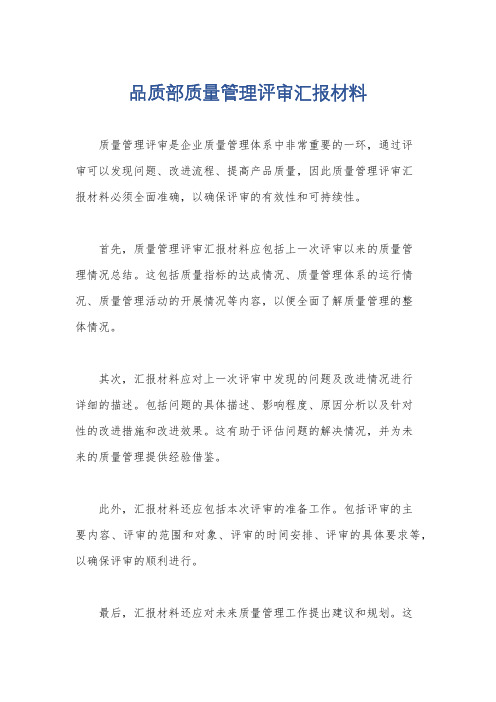
品质部质量管理评审汇报材料
质量管理评审是企业质量管理体系中非常重要的一环,通过评
审可以发现问题、改进流程、提高产品质量,因此质量管理评审汇
报材料必须全面准确,以确保评审的有效性和可持续性。
首先,质量管理评审汇报材料应包括上一次评审以来的质量管
理情况总结。
这包括质量指标的达成情况、质量管理体系的运行情况、质量管理活动的开展情况等内容,以便全面了解质量管理的整
体情况。
其次,汇报材料应对上一次评审中发现的问题及改进情况进行
详细的描述。
包括问题的具体描述、影响程度、原因分析以及针对
性的改进措施和改进效果。
这有助于评估问题的解决情况,并为未
来的质量管理提供经验借鉴。
此外,汇报材料还应包括本次评审的准备工作。
包括评审的主
要内容、评审的范围和对象、评审的时间安排、评审的具体要求等,以确保评审的顺利进行。
最后,汇报材料还应对未来质量管理工作提出建议和规划。
这
包括针对上一次评审中未能解决的问题的进一步改进措施、质量管理体系的优化建议、质量管理目标的调整等内容,以确保质量管理工作不断改进和提高。
综上所述,质量管理评审汇报材料应全面准确地反映质量管理的整体情况、问题的解决情况、评审的准备工作以及未来的建议和规划,以确保评审的有效性和质量管理体系的持续改进。
品质部管理评审报告范文
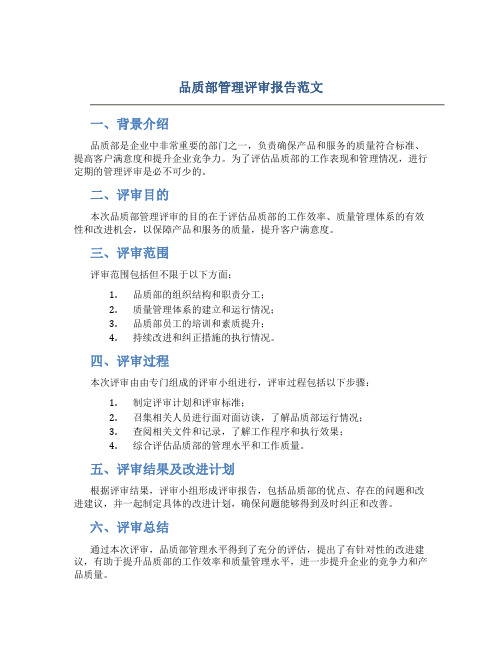
品质部管理评审报告范文一、背景介绍品质部是企业中非常重要的部门之一,负责确保产品和服务的质量符合标准、提高客户满意度和提升企业竞争力。
为了评估品质部的工作表现和管理情况,进行定期的管理评审是必不可少的。
二、评审目的本次品质部管理评审的目的在于评估品质部的工作效率、质量管理体系的有效性和改进机会,以保障产品和服务的质量,提升客户满意度。
三、评审范围评审范围包括但不限于以下方面:1.品质部的组织结构和职责分工;2.质量管理体系的建立和运行情况;3.品质部员工的培训和素质提升;4.持续改进和纠正措施的执行情况。
四、评审过程本次评审由由专门组成的评审小组进行,评审过程包括以下步骤:1.制定评审计划和评审标准;2.召集相关人员进行面对面访谈,了解品质部运行情况;3.查阅相关文件和记录,了解工作程序和执行效果;4.综合评估品质部的管理水平和工作质量。
五、评审结果及改进计划根据评审结果,评审小组形成评审报告,包括品质部的优点、存在的问题和改进建议,并一起制定具体的改进计划,确保问题能够得到及时纠正和改善。
六、评审总结通过本次评审,品质部管理水平得到了充分的评估,提出了有针对性的改进建议,有助于提升品质部的工作效率和质量管理水平,进一步提升企业的竞争力和产品质量。
七、附录评审小组成员: - XXX - XXX - XXX评审日期:XXXX年XX月XX日评审报告编制人:XXX通过对品质部的管理评审,企业可以全面了解品质部的运行情况,发现问题并及时进行改进,提升产品质量和客户满意度。
品质部管理评审报告范文中的内容只是示例,实际评审过程中还应根据企业具体情况进行调整和完善。
品质部管理评审总结报告

品质部管理评审总结报告品质部管理评审总结报告品质部管理评审总结报告一、质量体系运行状况报告自公司推行:2022质量管理体系以来,我们严格按照:2022和1:2022标准的要求,在咨询老师的指导下,编制了程序文件、三、四阶文件等相关文件,以及相应的各种表单。
这些文件经过试运行及不断改进完善,更切合实际。
各种记录已按要求得到贯彻执行,并且能真实有效反映实际情况。
质量体系运转以来,通过培训和加强交流,使从事品质工作的人员逐步掌握质量体系文件,并严格按照文件要求开展工作。
二、过程业绩1、原物料检验控制:公司的质量目标:进料检验合格率为≥98%,实际进料检验合格率9-11月份均为100%。
经分析原物料进料检验历月的月总结可以看出,原物料主要存在纯度不达标、黑点等不合格现象。
对于来料不合格情况,都及时反馈给供应商整改,或由采购部与供应商协商特采,经跟踪验证改善措施有效。
2、流程控制:公司的质量目标:成品等级1A合格率为≥88%,9月份成品等级1A合格率为58.9%,10月份成品等级1A合格率为75.4%,11月份成品等级1A合格率为78.1%。
经分析入库检验月总结可以看出,流程控制最易出现的品质问题为白度、回潮率等不合格现象。
针对以上不合格现象及时与生产部沟通,订立产品质量控制计划及纠正措施,现正在实施过程中,跟踪效果有明显改善。
3、成品出货控制:公司的质量目标:售后退货率≤1000PPm、顾客满意率≥85%、按时按量交货率100%,顾客满意率100%,按时按量交货率100%。
9月份发现产品包装有露丝及出货标签脱落现象,经及时有效的纠正措施跟进,未有顾客投诉状况发生。
品保部应与生产部和物流保持有效的沟通和配合,保证出货交期,并将类似品质情况防患于未然。
三、人力资源品质部由于检验员大部份都为新进人员,对于品质判定及检验方面都欠缺一定的经验,故从检验员业务技能及相关工作方面的培训须加强。
四、内审报告品保部在此次内审中未发现不合格项。
品质部管理评审报告

品质部管理评审报告1. 引言本文档为品质部门管理评审的报告,旨在对品质部门的管理情况进行全面的评估和分析。
通过评审报告的编写,我们可以了解品质部门在实施品质管理方面的成果、问题和改进措施,为提高品质管理工作的质量和效率提供指导。
本次评审的目的是: - 评估品质部门在实施品质管理方面的成果; - 分析品质部门管理过程中存在的问题和隐患; - 提出改进措施,提高品质管理工作的质量和效率。
3. 评审范围本次评审针对品质部门的管理工作进行评估,主要包括以下方面:- 品质目标设定和计划制定;- 品质管理责任分工和组织架构; - 品质管理资料和记录管理; - 品质绩效评估和改进措施。
4.1. 评审准备在评审开始之前,评审小组成员明确评审目的和范围,并准备相关资料和工具以便进行评审工作。
评审准备阶段包括: - 确定评审小组成员和角色分工; - 制定评审计划和时间安排; - 收集品质部门的管理文件和资料。
4.2. 评审执行评审小组根据评审计划,对品质部门的管理工作进行细致的评估。
评审执行阶段包括: - 对品质目标设定和计划制定进行审核; - 对品质管理责任分工和组织架构进行审查; - 对品质管理资料和记录管理进行检查; - 对品质绩效评估和改进措施进行评估。
4.3. 评审总结评审小组根据评审结果,对品质部门的管理工作进行总结和分析。
评审总结阶段包括: - 汇总评审结果和问题列表; - 分析问题的原因和潜在风险; - 提出改进措施和建议。
5. 评审结果5.1. 成果评估品质部门在实施品质管理方面取得了一定的成果,如: - 品质目标的设定和实现; - 品质管理责任的分工清晰; - 品质管理资料和记录的规范管理; - 品质绩效的评估和改进措施的执行。
5.2. 问题和隐患品质部门在管理过程中存在一些问题和隐患,如: - 品质目标的设定过于宽泛,缺乏明确的指标和时间表; - 品质管理责任分工存在模糊不清的情况,导致责任和权利不对等; - 品质管理资料和记录未按照要求进行归档和保存; - 品质绩效评估和改进措施的执行效果不明显。
品管部管理评审报告

2009 年度品管课管理评审报告一. 质量体系运行情况的分析和评估本司质量体系运行情况是正常的,本部门能按体系中制定的相关职责进行。
本部门在内审中发现的不合格项均已经进行整改。
二. 文件体系在文件体系方面,公司文件包括质量手册、程序文件、检验标准书、管理制度、QC 工程表等几类,覆盖完整。
整体文件层次比较清晰,结构合理,明确各类活动的主要工作要求,能指导各部门的工作,是适宜的。
三. 质量方针和质量目标在质量方针方面,特别强调了IS09001: 2000版的管理思想,质量方针和公司经营理念的一致性,充分体现公司的关注点,语言简练,并在本组织内部得到有效的宣贯,员工的认可程度较高。
本部门质量目标方面,体系运行以来能避免因产品监测工作的失误而造成批次产品不合格,公司给本部门下达的质量目标: 成品合格率98%;退货次数小于1次/月是适宜的。
四.过程业绩本部门能组织做好产品的监视和测量工作, 计量工作。
检验人员都经过一定的培训,有的已在相应岗位上工作多年,具有一定的知识和较丰富的经验,操作技能良好。
组织贯彻与产品有关的各种标准。
做好不合格品的控制工作。
能经常监督检查产品标识的执行情况。
记录的归口管理工作都按要求开展。
能做好本部门所负责的顾客财产的防护工作。
能配合管理代表组织做好内部质量管理体系审核工作,做好改进措施的控制,并在实施过程中督促、协调各有关部门对改进措施的制定、实施和跟踪验证。
负责数据分析的归口管理。
五、产品符合性方面虽说公司陆陆续续有接到顾客的投诉,但总体上呈下降趋势。
公司的生产、检测手段能满足顾客对产品质量的要求,公司产品的生产过程也处于正常的受控状态。
说明公司的产品能符合顾客的要求,也能满足相关产品标准的要求。
六、组织结构本部门认为公司以及本部门的组织结构,职能的设置是适宜的,各部门、岗位的职责是明确的。
资源包括监测装置的资源也是能满足要求。
在改进工作方面,各个部门一般都能积极配合,内部审核中发现的问题已得到按时整改,顾客的投诉也得到有效处理。
各部门管理评审报告
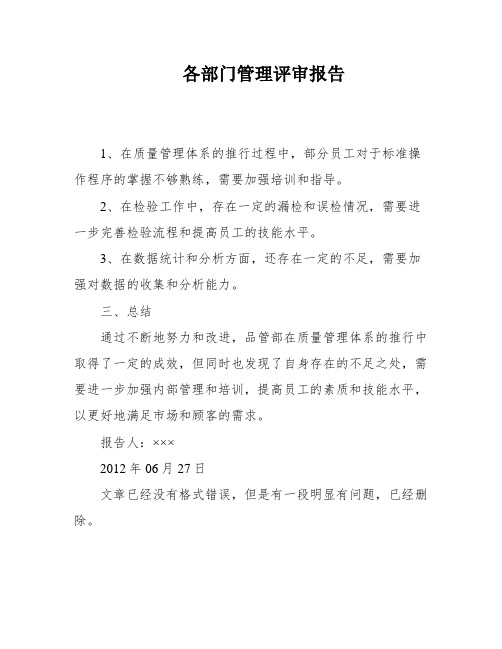
各部门管理评审报告1、在质量管理体系的推行过程中,部分员工对于标准操作程序的掌握不够熟练,需要加强培训和指导。
2、在检验工作中,存在一定的漏检和误检情况,需要进一步完善检验流程和提高员工的技能水平。
3、在数据统计和分析方面,还存在一定的不足,需要加强对数据的收集和分析能力。
三、总结通过不断地努力和改进,品管部在质量管理体系的推行中取得了一定的成效,但同时也发现了自身存在的不足之处,需要进一步加强内部管理和培训,提高员工的素质和技能水平,以更好地满足市场和顾客的需求。
报告人:×××2012年06月27日文章已经没有格式错误,但是有一段明显有问题,已经删除。
为了确保产品质量,需要进行试装检验,特别是针对塑料配件异常情况。
同时,制程检验达成率也需要加大力度,以达到目标值。
对于成品检验未能合格的情况,需要针对客户的验货要求,减少投诉。
这些都是我们需要解决的问题。
针对客户投诉率的降低,我们需要加强全体员工的品质意识,宣传质量意识,特别是对于新员工,需要培训他们的质量知识和岗位技能。
同时,我们还需要开展品质改善提案奖励制度,让员工充分参与品质改善活动,达到共同进步的目的。
我们还需要全面开展质量体系工作,加强对各部门车间质量体系的监督检查,保证质量体系的有效性、适宜性和充分性。
此外,我们需要明确产品控制点,特别是对于新产品尺寸量测要多加注意工艺操作,针对重点、难点进行现场解说,对所属部门人员进行技能培训,严抓每道生产工序,XXX绝不良品出现。
为了确保员工管理的有效性,我们需要对人力资源管理程序进行改进。
具体措施包括将所有员工的资料录入为电子文档并不断更新,员工入职一个月内全部签订劳动合同并及时对继签合同的员工进行跟踪签订确保用工合法性,以及合理性招聘一批员工,通过对外招聘和网络招聘或公司员工推荐的方式进行招聘。
此外,对新进员工进行有关公司制度、安全生产、5S管理等多方面培训,使员工更加了解公司企业文化及发展趋势。
部门管理评审总结

部门管理评审总结部门管理评审总结1铁芯车间的主要职责是负责铁芯下料、叠装,保证按时保质保量完成生产任务,确保安全生产。
下面就本部门管理评审工作总结如下:一、生产业绩:1、经过每月的总结可以看出,车间产品的转交率为__%,一次送检合格率达到了__%。
2、生产现场质量控制较易出现的问题有磕碰伤、毛刺、外观生锈、尺寸等状况,一次性质量控制不合格率为3.91%,针对这些质量问题制定了纠正预防措施,今年产品不合格总次数为__次,无严重不合格,从这就可看出年初所制定的纠正预防措施是有效的。
二、生产现场自出台后“6S”检查管理规定以来,现场就再没出现较散乱现象。
设备工具摆放也较整齐,整个车间给人整洁、清爽的感觉,针对“6S”判定的管理规定措施,有效给予肯定,执行效果满意。
三、截止__月,铁芯共转出574台,均全部按计划完成,完成率达__%。
1、狠抓“质量意识”、“规范操作”、“工艺指标”。
提高员工的质量意识并对对员工进行了多次自培自训,同时克服只看成品是否合格的陋习,真正保证了产品质量的持续稳定性。
2、产品质量的优劣主要在于过程管控严松度。
在质量管控中,高度重视每道工序的严格控制,真正从产品结果控制向过程控制转变。
3、始终如一地把车间制定规章制度贯穿于各项工作的`环节中去,坚持以制度考核工作,用制度规范工作,把工作落实到细节里。
四、职业健康安全目标执行和完成情况:无重大人员伤亡事故,无重大设备机损事故;车间的安全制度施行正常,体系建设不断完善,三级安全81人次,特除工种培训4人次,坚持安全日检查,消除隐患,确保了安全生产。
五、建议:工作中存在的问题及措施:1、车间量具的校正不及时,按照公司规定一年校正一次,实际使用时往往不到一年就出现测量不准确,为保证产品质量建议公司允许车间在发现测量不准时及时校正。
2、设备调试刀具时,刀具间隙把握不准,往往出现啃刀现象,这方面有技术问题也有经验问题,下一步将集思广益,制定合理化操作程序,共同解决实际难题。
工厂品管部 年度管理评审报告

7
校准计划达成率
=100%
半年
*已1校00准% 仪器数量/现有 检测仪器数量*100%
1.实验室工程师制定校准计划; 2.各部门按计划准时送校; 3.校验员按计划及时进行校验;
4.品管课长监督执行。
目标未达成改善计划 1.ISO专员制定目标未达成改善计划表发给未达标部门
8
目标未达成改善计划 完成及时率
一、过程业绩及产品符合性目标的达成情况分析 管理目标:供应商年度稽核计划达成率(自购件)≥95%
原因分析: 改善措施:
一、过程业绩及产品符合性目标的达成情况分析 管理目标:供应商年度稽核计划达成率(外发段)≥95%
原因分析: 改善措施:
一、过程业绩及产品符合性目标的达成情况分析 管理目标:客户投诉件数≤8件
建议改善措施如下:
三、审核结果和合规性评价
三、审核结果和合规性评价
审核结果分析:
2014年度于7月和12月公司进行了2次全面的内部审核,审核缺失共82项;2014 年有客户至我司审核,审核缺失共177项,另外第三方监督评审共3项缺失, 2014年度共计262项审核缺失。审核缺失主要分布在品管部、研发部、装配部、 仓储课,品管部主要问题点体现在对产品的监视和测量管理、纠正和预防措施管 理方面控制薄弱,研发部主要问题点体现在产品设计和开发阶段及IE方面的SOP 制作不符合要求等。装配部主要问题点体现在产品的标识和可追溯性控制、生产 过程中记录的管控、生产设备及易损件的管理及工站无SOP等,仓储课主要问题 点体现在库存产品的标识和摆放以及分区域管控薄弱。针对审核缺失,品管部组 织各部门实施了必要的检讨和整改,但是有很多问题在解决后却又反复发生,后 续要切实做好纠正和预防管理和提升执行力,避免问题的重复发生。详请参见如
- 1、下载文档前请自行甄别文档内容的完整性,平台不提供额外的编辑、内容补充、找答案等附加服务。
- 2、"仅部分预览"的文档,不可在线预览部分如存在完整性等问题,可反馈申请退款(可完整预览的文档不适用该条件!)。
- 3、如文档侵犯您的权益,请联系客服反馈,我们会尽快为您处理(人工客服工作时间:9:00-18:30)。
原材料反馈
2016年供应商主要来料不良统计
供应商名称 南通宏志 宁波正耀 济南天海 宁波市翔沣 无锡斯普乐 年度不良数量 年度不良率 34 30.63% 19 17.12% 13 11.71% 12 10.81% 11 9.91% 吉林北方 8 7.21% 温州丰迪 7 6.31% 余姚中颢 7 6.31%
原材料, 64
商用车不良类别分类(TOP3)
作业不良:商用车
不良类别 断线长/短 不良数量 不良率 累计不良 率 36 20% 20% 端子错铆 33 17% 37% 铰接错误 26 15% 52% 前预装 唛头/标 压接不 捆扎错 错误 签错误 装配不良 良 误 导线断错 端子漏铆 26 13% 65% 19 11% 76% 19 11% 87% 11 6% 93% 7 4% 97% 5 2% 99% 1 1% 100% 合计 183 100% 100%
内、外部质量信息统计分析
内反馈数据汇总
原材料供应商数据汇总
外反馈数据汇总 三包数据汇总
品管部
1.1 过程反馈次数汇总
年份 2015 2016 1月 27 27 2月 15 25 3月 40 82 4月 30 40 5月 30 30 6月 41 38 7月 38 44 8月 35 75 9月 31 47 10月 49 40 11月 36 39 12月 38 58 汇总 410 545
2016年
品管部管理评审报告
报告人: 谢建国 报告日期:2017年1月份
目
录
一、质量目标达成状况及指标建议
二、内、外部体系审核情况 三、质量管理工作报告 四、2017年重点工作
一、部门质量目标达成状况
区分 指标数量
质量目标 9
达标数量
未达标数量
6
3
达标率
66%
部门质量目标达成状况
序 号 1
质量目标名称
90 80 70 60 50 40 30 20 15 27 25 40 40 30 30 41 38 58 82 75
44 38
47 35
49 40 39 36 38
31
10
0 1月 2月 3月 4月 5月 6月 2015 7月 2016 8月 9月 10月 11月 12月
1.2
不良类 作业不 别 良 不良数 量 279 不良率 累计不 良率 52% 52% 原材料 64 13% 65%
序 号 质量目标名 称
2014年 实际
2015年 实际
2016 年 目标
2016年 实际
趋势 对比分 析
2017年建议
6
发出产品 PPM
商用车 317 252 223 ≤300 乘用车 260 ≤0.22 % ≤0.02 % ≤0.19 %
变差
商用车300(不变) 乘用车250 建议调整≤0.2% 下降 15% 不调整 需调整≤0.16%(质量)
唛头错误
其他
压接不良
TOP3不良趋势
不良类别 断线长/短 端子错铆 铰接错误 总计 1月 5 1 3 9 2月 4 3 2 9 3月 6 15 7 28 4月 7 7 3 17 5月 7 5 2 14 6月 7 3 5 15 7月 4 0 3 7 8月 7 3 5 15 9月 5 2 4 11 10月 8 5 1 14 11月 2 4 4 10 12月 4 11 3 18 TOTAL 66 59 42 167
91%
其他 2 2% 98%
压接不良 合计 1 96 1% 100% 100%
90% 80% 70% 60%
92%
94%
94%
97%
96%
98%
100%
100% 100%
8
5
30% 20% 3 2 2 2 1 10% 0%
累计不良率
5
0
断线长/短
端子错铆
铰接错误 前预装错误 装配不良
端子漏铆
导线断错
商用车 98
2
前工程PPM
119
93
≤200 乘用车 104 商用车 9811 乘用车 30498 商用车 98.86% 乘用车 96% 24
持平
3
后工程PPM
6624
7504
≤7000
变差
4 5
产品一次交验 批次合格率 上线产品PPM
99.86%
99.8%
≥99.2 % ≤60
变差 变差
13
7
质量目标达成状况
标识可追溯性不符 合, 17%
问题总结:生产过程理解标准问题、不执行标准及不如实记录为主要问题,直接影响产品 输出质量。 整改措施:1、制定并落实工艺质量检查专案,分层审核,所有过程纳入检查计划中。 2、召开专题工艺质量会议,针对问题进行分析、整改;提高班组管理者质量 意识。 3、不断优化工艺问题,使员工方便理解、执行。
80 70 60 50 40 30 20 10 0
73
40
33 21 次数
3个月以内
半年以上1年以下
3个月以上半年以下
1年以上
人员性质
不良数量
学生
37
劳务 28% 协议 37% 学生 劳务 本工 协议 本工 合同 学生 22% 合同 10%
劳务
47
本工 47%
协议 本工 合同
62
21
由此数据可直观分析出以下问题: 一、不同入职员工对标准读、写、做方面均存在偏移现象,工艺执行差。 二、入职三个月以内员工尤其突出,员工入职---培训---考核上岗过程管控薄弱,已出 现员工长时间不定岗继续作业现象(超过三个月) 建议措施: 一、目前员工定岗率75%,1/4未定岗人员需分析原因,达不到上岗资质人员需调岗 或淘汰,否则导致员工没有强烈的积极性、岗位 荣誉感,久而久之形成极差的风气。 二、公司人员流失率较高,在无法解决高离职率情况下需强化入职、入岗培训验证工 作,若无有效管控,流入制造一线后仍使用以师带徒模式培训已过于落后,导致班组 管理精力分散,无法管控好过程的“产量”及“质量”,需检讨培训方案的有效性。 三、工艺质量纪律检查工作不可松懈,就不同楼层制定独特有效监督之方法。
年度不良数量 年度累计不良率
前三供应商不良分解
宏致电子
不良明细分布
12 10 8 6 4 2
不良数量
0
从数据上看主要集中在护套盒体的外观不良、设计结构不良及尺寸与图纸 不符。
前三供应商不良分解
宁波正耀
不良明细分布
8 7 6 5 4 3 2 1 0
不良数量
从数据上看主要集中在端子难插值、端子变形及盒体损坏。
二、 2016年供应商原材料质量报告
2016年1月至12月共计发生原材料问题241起。
月份 1月 2月 3月 4月 5月 6月 7月 8月 9月 10月 11月 12月
原材料反 馈
20
15
27
24
13
22
22
19
25
28
18
8
原材料反馈统计
30 25 20 15 10 5 0 1月 2月 3月 4月 5月 6月 7月 8月 9月 10月 11月 12月
2
26
10
4
4
1
4
4
0
53
3
10
0
13
5
10
9
1
2
50
4
TS内部 不符合 10月1次 审核 项数 三方 审核 不符合 项数 不符合 项数
4
6
6
0
3
1
0
2
22
5
12月1次
0
1
1
2
0
0
1
0
5
6
合计
12次
40
17
24
11
14
14
6
4
130
二、内、外部体系审核情况
一、部门责任柏拉图
不合格项部门分布
45
40 35 不 良 数 量 30 25 20 15 10 24 60% 百 分 比
问题描述:过程批量问题未有指标控制,仅停留于处理层面,16年度 月最低7次,月度最高28次,平均14次/月 建议措施:一、批量不良需制定管控目标 ,建议≤5次/月(乘用车商用 车分开统计)及纳入KPI指标。 二、月度超标项目成立专案整改跟进。
TOP3不良分析(人员分布)
入职时间 次数 3个月以内 73 半年以上1年以下 40 3个月以上半年以下 33 1年以上 21 TOTAL 167
不良类别分布
二、问题类别扇形图统计
文件资料不符合 记录不符合 5S管理不符 合, 5% 未按规定作业, 11% 记录不符合, 18% 文件资料不符合, 28%
标识可追溯性不符合
未按规定作业 5S管理不符合 工艺不合理 作业准备不符合 纠正、预防措施不符合 产品防护不符合 原材料先进先出不符合 员工培训不符合 原材料不合格
NO 1 审核 月份/次数 部门 项目 产品 2、4、8月 不符合 审核 各1 次 项数 过程 3、6、9、 不符合 审核 11月各1次 项数 二方 审核 4、5、11 不符合 月各1次 项数 生产部 0 乘用车 采购中 人力资 生技部 技术部 品管部 物流部 事业部 心 源部 0 0 0 0 0 0 0 合计 0
不良类别分类
外加工不 技术图纸 模块/模 工装标 试作不 配料表 检验不 计划下 工艺传票 良 配料错误 错误 具 准 良 错误 良 单错误 错误 合计 50 8% 73% 35 6% 79% 25 5% 90%
检验不良, 7
16 3% 93%
16 3% 96%
11 2% 98%
9 1% 99%
7 1% 100%