连硫硫化时间和生产速度
橡胶硫化过程的四阶段:起硫、欠硫、正硫和过硫
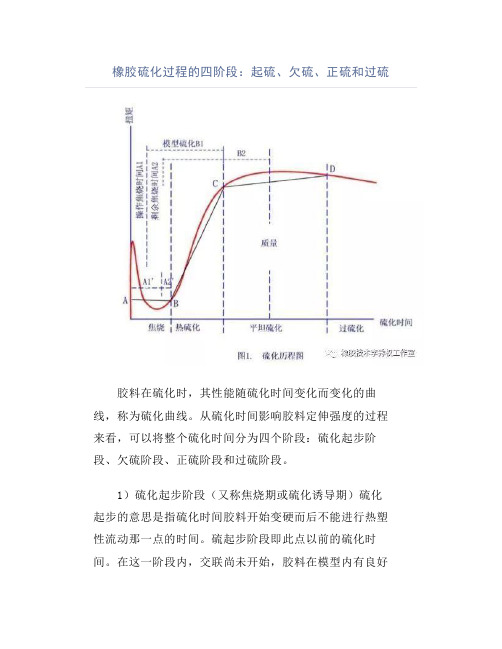
橡胶硫化过程的四阶段:起硫、欠硫、正硫和过硫胶料在硫化时,其性能随硫化时间变化而变化的曲线,称为硫化曲线。
从硫化时间影响胶料定伸强度的过程来看,可以将整个硫化时间分为四个阶段:硫化起步阶段、欠硫阶段、正硫阶段和过硫阶段。
1)硫化起步阶段(又称焦烧期或硫化诱导期)硫化起步的意思是指硫化时间胶料开始变硬而后不能进行热塑性流动那一点的时间。
硫起步阶段即此点以前的硫化时间。
在这一阶段内,交联尚未开始,胶料在模型内有良好的流动性。
胶料硫化起步的快慢,直接影响胶料的焦烧和操作安全性。
这一阶段的长短取决于所用配合剂,特别是促进剂的种类。
用有超速促进剂的胶料,其焦烧比较短,此时胶料较易发生焦烧,操作安全性差。
在使用迟效性促进剂(如亚磺酰胺)或与少许秋兰姆促进剂并用时,均可取得较长的焦烧期和良好的操作安全性。
但是,不同的硫化方法和制品,对焦烧时间的长短亦有不同要求。
在硫化模压制品时,总是希望有较长的焦烧期,使胶料有充分时间在模型内进行流动,而不致使制品出现花纹不清晰或缺胶等到缺陷。
在非模型硫化中,则应要求硫化起步应尽可能早一些,因为胶料起步快而迅速变硬,有利于防止制品因受热变软而发生变形。
不过在大多数情况下仍希望有较长的焦烧时间以保证操作的。
2)欠硫阶段(又称预硫阶段)硫化起步与正硫化之间的阶段称为欠硫阶段。
在此阶段,由于交联度低,橡胶制品应具备的性能大多还不明显。
尤其是此阶段初期,胶料的交联度很低,其性能变化甚微,制品没有实用意义。
但是到了此阶段的后期,制品轻微欠硫时,尽管制品的抗张强度、弹性、伸长率等尚未达到预想的水平,但其抗撕裂性耐磨性和抗动态裂口性等则优于正硫化胶料。
因此,如果着重要求后几种性能时,制品可以轻微欠硫。
3)正硫阶段大多数情况下,制品在硫化时都必须使之达到适当的交联度,达到适当的我联度的阶段叫做正硫化阶段,即正硫阶段。
在此阶段,硫化胶的各项物理机械性能并非在同一时都达到最高值,而是分别达到或接近最佳值,其综合性能最好。
电线电缆快速硫化生产的硫化工艺参数
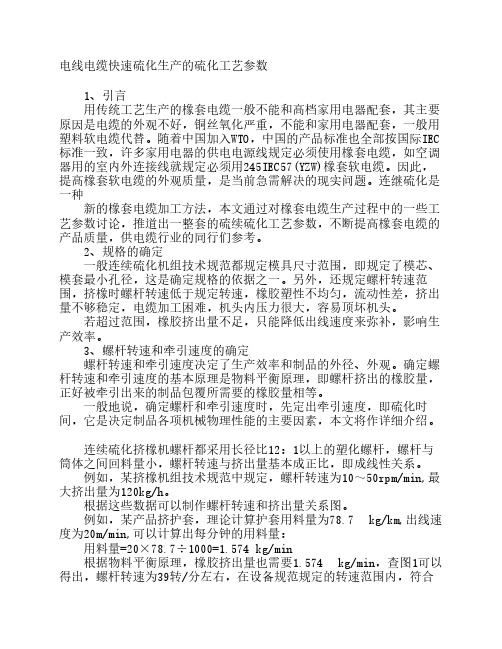
电线电缆快速硫化生产的硫化工艺参数 1、引言 用传统工艺生产的橡套电缆一般不能和高档家用电器配套,其主要原因是电缆的外观不好,铜丝氧化严重,不能和家用电器配套,一般用塑料软电缆代替。
随着中国加入WTO,中国的产品标准也全部按国际IEC 标准一致,许多家用电器的供电电源线规定必须使用橡套电缆,如空调器用的室内外连接线就规定必须用245IEC57(YZW)橡套软电缆。
因此,提高橡套软电缆的外观质量,是当前急需解决的现实问题。
连继硫化是一种 新的橡套电缆加工方法,本文通过对橡套电缆生产过程中的一些工艺参数讨论,推道出一整套的硫续硫化工艺参数,不断提高橡套电缆的产品质量,供电缆行业的同行们参考。
2、规格的确定 一般连续硫化机组技术规范都规定模具尺寸范围,即规定了模芯、模套最小孔径,这是确定规格的依据之一。
另外,还规定螺杆转速范围,挤橡时螺杆转速低于规定转速,橡胶塑性不均匀,流动性差,挤出量不够稳定,电缆加工困难,机头内压力很大,容易顶坏机头。
若超过范围,橡胶挤出量不足,只能降低出线速度来弥补,影响生产效率。
3、螺杆转速和牵引速度的确定 螺杆转速和牵引速度决定了生产效率和制品的外径、外观。
确定螺杆转速和牵引速度的基本原理是物料平衡原理,即螺杆挤出的橡胶量,正好被牵引出来的制品包覆所需要的橡胶量相等。
一般地说,确定螺杆和牵引速度时,先定出牵引速度,即硫化时间,它是决定制品各项机械物理性能的主要因素,本文将作详细介绍。
连续硫化挤橡机螺杆都采用长径比12:1以上的塑化螺杆,螺杆与筒体之间回料量小,螺杆转速与挤出量基本成正比,即成线性关系。
例如,某挤橡机组技术规范中规定,螺杆转速为10~50rpm/min,最大挤出量为120kg/h。
根据这些数据可以制作螺杆转速和挤出量关系图。
例如,某产品挤护套,理论计算护套用料量为78.7 kg/km,出线速度为20m/min,可以计算出每分钟的用料量: 用料量=20×78.7÷1000=1.574 kg/min 根据物料平衡原理,橡胶挤出量也需要1.574 kg/min,查图1可以得出,螺杆转速为39转/分左右,在设备规范规定的转速范围内,符合设备技术规范。
促进剂的硫化曲线

促进剂的硫化曲线
硫化曲线指的是在橡胶硫化过程中,不同时间和温度下橡胶中硫化程度的变化曲线。
硫化是橡胶加工工艺中非常重要的步骤,通过硫化可以使橡胶获得优良的弹性、耐热、耐腐蚀等性能。
在硫化曲线中,通常可以分为几个阶段:
1. 延迟期(t0到t1):橡胶在橡胶-硫混合物中,尚未出现硫
化反应,此时橡胶材料保持弹性。
2. 加速期(t1到t2):在此阶段,橡胶中的硫化反应开始加速,硫化速度逐渐增加,橡胶材料的硫化程度也逐渐增加。
橡胶开始变得发硬。
3. 高速期(t2到t3):硫化反应在此阶段达到最高速度,橡
胶材料的硫化程度迅速增加。
此时橡胶开始形成网络结构,整体硬化。
4. 减速期(t3到t4):硫化反应速度开始减慢,硫化程度的
增加趋于平缓。
橡胶变得更加耐磨和耐热。
5. 稳定期(t4到t5):硫化反应基本结束,硫化程度变化很小。
橡胶材料的硫化程度达到最高水平。
不同类型的橡胶和硫化体系会有不同的硫化曲线特征,这取决于使用的促进剂、硫化温度和时间等因素。
硫化曲线的了解有助于合理选择硫化条件,以获得符合要求的橡胶制品。
橡胶硫化三要素(时间、温度、压力)

橡胶硫化三要素(时间、温度、压力)橡胶件硫化的三大工艺参数是:温度、时间和压力。
其中硫化温度是对制品性能影响最大的参数,硫化温度对橡胶制品的影响的研究也比比皆是。
但对硫化压力比较少进行试验。
橡胶硫化三要素之时间橡胶制品硫化时间:在一定的温度、模压下,为了使胶料从塑性变成弹性,且达到交联密度最大化,物理机械性能最佳化所用的时间叫橡胶制品硫化时间。
通常不含操作过程的辅助时间。
硫化时间是和硫化温度密切相关的,在硫化过程中,硫化胶的各项物理、力学性能达到或接近最佳点时,此种硫化程度称为正硫化或最宜硫化。
在一定温度下达到正硫化所需的硫化时间称为正硫化时间,一定的硫化温度对应有一定的正硫化时间。
当胶料配方和硫化温度一定时,硫化时间决定硫化程度,不同大小和壁厚的橡胶制品通过控制硫化时间来控制硫化程度,通常制品的尺寸越大或越厚,所需硫化的时间越长。
硫化时间的设定方法:1. 1.正硫化时间的测试,胶料正硫化时间的测试方法有:1.1物理-化学法(包括游离硫测定法和溶胀法);1.2 物理-力学性能测定法(包括定伸应力法、拉伸强度法、定伸强度法、抗张积法、压缩永久变形法、综合取值法等);1.3专用仪器法(包括门尼粘度法、硫化仪法)等。
目前最常用的是硫化仪法。
通过硫化仪测试,可以得到胶料的正硫化时间。
2.制品硫化时间的确定2.1若制品厚度为6mm或小于6mm,并且胶料的成形工艺条件可以认为是均匀受热状态,那么,制品的硫化时间与硫化曲线中所测得的正硫化时间相同(温度一致的情况下,即加硫温度使用硫化仪测试的温度);2.2若制品壁厚大于6mm,每增加1mm的厚度,则测试的正硫化时间增加1min,这是一个经验数据。
例如,一橡胶制品,其厚度为22mm,试片测试的正硫化时间为6min(温度设定150℃),那么,在150℃硫化时,该制品的硫化时间为6+(22-6)×1=22min。
这时间不包括操作过程的辅助时间。
二段加硫时间设定:1.定义为了达到合理的制造工艺和合理成本,把橡胶硫化分为一段、二段两个过程来完成的工艺方法,其第二段的工艺就是所谓的二段加硫。
橡胶硫化过程的四阶段:起硫、欠硫、正硫和过硫

橡胶硫化过程的四阶段:起硫、欠硫、正硫和过硫胶料在硫化时,其性能随硫化时间变化而变化的曲线,称为硫化曲线。
从硫化时间影响胶料定伸强度的过程来看,可以将整个硫化时间分为四个阶段:硫化起步阶段、欠硫阶段、正硫阶段和过硫阶段。
1)硫化起步阶段(又称焦烧期或硫化诱导期)硫化起步的意思是指硫化时间胶料开始变硬而后不能进行热塑性流动那一点的时间。
硫起步阶段即此点以前的硫化时间。
在这一阶段内,交联尚未开始,胶料在模型内有良好的流动性。
胶料硫化起步的快慢,直接影响胶料的焦烧和操作安全性。
这一阶段的长短取决于所用配合剂,特别是促进剂的种类。
用有超速促进剂的胶料,其焦烧比较短,此时胶料较易发生焦烧,操作安全性差。
在使用迟效性促进剂(如亚磺酰胺)或与少许秋兰姆促进剂并用时,均可取得较长的焦烧期和良好的操作安全性。
但是,不同的硫化方法和制品,对焦烧时间的长短亦有不同要求。
在硫化模压制品时,总是希望有较长的焦烧期,使胶料有充分时间在模型内进行流动,而不致使制品出现花纹不清晰或缺胶等到缺陷。
在非模型硫化中,则应要求硫化起步应尽可能早一些,因为胶料起步快而迅速变硬,有利于防止制品因受热变软而发生变形。
不过在大多数情况下仍希望有较长的焦烧时间以保证操作的。
2)欠硫阶段(又称预硫阶段)硫化起步与正硫化之间的阶段称为欠硫阶段。
在此阶段,由于交联度低,橡胶制品应具备的性能大多还不明显。
尤其是此阶段初期,胶料的交联度很低,其性能变化甚微,制品没有实用意义。
但是到了此阶段的后期,制品轻微欠硫时,尽管制品的抗张强度、弹性、伸长率等尚未达到预想的水平,但其抗撕裂性耐磨性和抗动态裂口性等则优于正硫化胶料。
因此,如果着重要求后几种性能时,制品可以轻微欠硫。
3)正硫阶段大多数情况下,制品在硫化时都必须使之达到适当的交联度,达到适当的我联度的阶段叫做正硫化阶段,即正硫阶段。
在此阶段,硫化胶的各项物理机械性能并非在同一时都达到最高值,而是分别达到或接近最佳值,其综合性能最好。
皮带硫化要求

⽪带硫化要求关于规范胶带硫化的要求为统⼀公司胶带硫化⼯艺,进⼀步规范胶带硫化过程,装备部根据各胶带⽣产⼚家硫化要求和省内基地⼦公司硫化操作实际情况,对胶带硫化要求如下,请各⼦公司参照执⾏。
⼀、胶带硫化主要⼯艺参数1、胶接长度和胶接型式(1)、帆布芯、尼龙芯胶带胶带硫化接头长度决定着接头的粘合⾯积,粘合⾯积的⼤⼩⼜决定着接头的强度。
各⼦公司在硫化尼龙、帆布芯胶带时,要求根据使⽤的硫化机长度确定接头长度,尽可能取最⼤值,接头部位左右两侧应⽐硫化机加热板对应的侧边短100mm左右,然后根据⽪带层数确定每个阶梯长度。
接头⽅法采⽤对接⽅法。
(2)、钢丝绳芯胶带钢丝绳芯胶带的接头是依靠钢丝绳对橡胶的粘着⼒来实现,接头中的钢丝绳,应有⼀定的搭接长度,使接头处的钢丝与橡胶的粘合强度⼤于钢丝绳的破断拉⼒。
接头的搭接长度和连接的⼏何结构需要根据钢丝绳的直径、间距、钢丝绳的破断⼒和钢丝绳与橡胶粘合(强度)⽽定。
各⼦公司在硫化钢丝绳胶带时,采取的接头型式及接头长度不⼤⼀样,即使同⼀⼦公司内部由于⽪带机胶带承受负荷、长度等不同,采取的接头型式、接头长度也不⼀样。
接头型式主要有三级搭接或三级交错搭接法,其它的型式有⼆级交错搭接法、⼀级搭接法。
为保证胶带接头有⾜够的粘合强度,统⼀胶接型式,要求钢丝绳胶带胶接采取⼀对⼀搭接法,胶接长度为1600mm(具体尺⼨详见附录⼆)。
如硫化机宽度允许,接头长度做成1630mm。
2、硫化温度及时间:胶带硫化胶接时的硫化温度,是⽣胶料在⼀定要求条件下,硫化反应的最佳温度,是橡胶硫化⼯艺中最主要的控制条件之⼀。
规定⽪带接头硫化时硫化温度都控制在145±5℃,保温时间为35-40min。
3、硫化压⼒:硫化⼒⼤⼩,要根据胶料的性能(主要是可塑性),产品结构、⼯艺条件⽽定。
胶料流动⼩,硫化压⼒应⼤些;反之,压⼒要⼩些。
胶带较厚,胶布层多(芯层),结构复杂,钢丝绳为芯层的,则应需要较⼤的硫化压⼒。
硫黄硫化体系之组成及特点

促进剂,PHR
促进剂/硫黄 多硫和双硫交联% 单硫交联% 环状硫% 低温性能
0.4~1.2
0.1~0.6 95 5 高 高
1.2~2.5
0.7~2.5 50 50 中 中
2.0~5.0
2.5~12 20 80 低 低
耐热性
硫化还原 压缩永久变形% 70℃×22hrs
低
低 30
中
中 20
高
高 10
84 68 64
九、架桥种类对架桥变动性的关系: 1. C-C架桥会限制旋转。 2. C-S-C键会增加旋转。 3. C-S-S-C键一方面会增加旋转,另一方面会限制线性运动。 4. C-SX-C键可自由的旋转和线性运动。
十、硫化体系的配方与硫化胶性能:
CV 硫黄,PHR 2.3~3.5 Semi-EV 1.0~1.7 EV 0.4~0.8
老 化 后 拉 伸 强 度 保 持 率
90
200
60
疲 劳 寿 命 60 ( 千 周 )
1.5 30 3.0
疲 劳 寿 命 ( 千 周 )
CV
S-EV
EV
100
0
1.5
S-EV
1.0
EV
起始疲劳寿命 于90℃老化2days后的疲劳寿命
NR硫化体系对老化与疲劳寿命的影响
NR硫化体系对老化前后疲劳寿命的影响
三种硫化体系由于交联结构的不同,表现出不同的动态或静态物理力学 性能。 CV体系适用于常温下各种动、静态条件的橡胶; EV适用于耐热和常温 静态条件的胶料;S-EV适用于中等温度的动静态条件的胶料。
PS:在等摩尔比条件下,硫黄用量在1.0~1.5范围内,各种促进剂在NR中的 抗氧化返原能力的顺序为:
连续硫化生产线
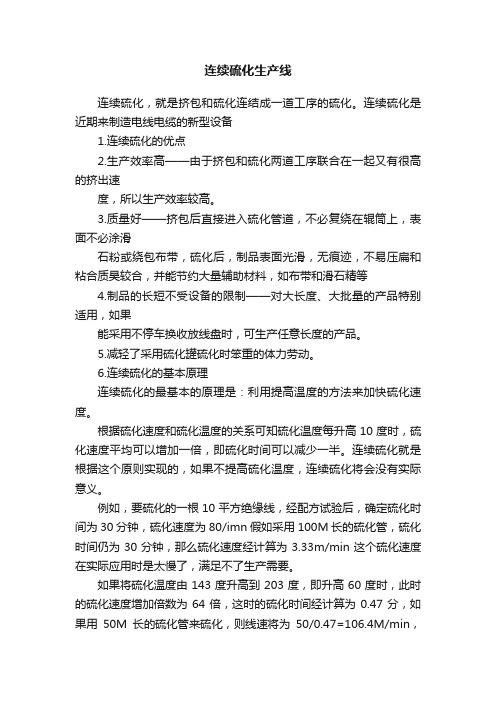
连续硫化生产线连续硫化,就是挤包和硫化连结成一道工序的硫化。
连续硫化是近期来制造电线电缆的新型设备1.连续硫化的优点2.生产效率高——由于挤包和硫化两道工序联合在一起又有很高的挤出速度,所以生产效率较高。
3.质量好——挤包后直接进入硫化管道,不必复绕在辊筒上,表面不必涂滑石粉或绕包布带,硫化后,制品表面光滑,无痕迹,不易压扁和粘合质昊较合,并能节约大量辅助材料,如布带和滑石精等4.制品的长短不受设备的限制——对大长度、大批量的产品特别适用,如果能采用不停车换收放线盘时,可生产任意长度的产品。
5.减轻了采用硫化罐硫化时笨重的体力劳动。
6.连续硫化的基本原理连续硫化的最基本的原理是:利用提高温度的方法来加快硫化速度。
根据硫化速度和硫化温度的关系可知硫化温度每升高10度时,硫化速度平均可以增加一倍,即硫化时间可以减少一半。
连续硫化就是根据这个原则实现的,如果不提高硫化温度,连续硫化将会没有实际意义。
例如,要硫化的一根10平方绝缘线,经配方试验后,确定硫化时间为30分钟,硫化速度为80/imn假如采用100M长的硫化管,硫化时间仍为30分钟,那么硫化速度经计算为3.33m/min这个硫化速度在实际应用时是太慢了,满足不了生产需要。
如果将硫化温度由143度升高到203度,即升高60度时,此时的硫化速度增加倍数为64倍,这时的硫化时间经计算为0.47分,如果用50M长的硫化管来硫化,则线速将为50/0.47=106.4M/min,这个硫化速度是可以满足生产需要的。
这就证明了连续硫化只有提高温度才能有实用价值,所以,连续硫化也是采用高压锅供气。
上述的计算结果只是考虑本身的时间而没有考虑外界的影响因素。
当考虑到硫化前的加热时间、橡皮的厚度及制品的规格等因素时,正确的硫化时间是很难计算出来的,实践证明,理论计算硫化时间是实际硫化时间的60~70%,因此在确定硫化的线速度时,应当记住,实际线速度要比理论计算的线速度低1/3左右。
橡胶硫化压力、温度、(厚制品)时间计算(公式全,收藏)
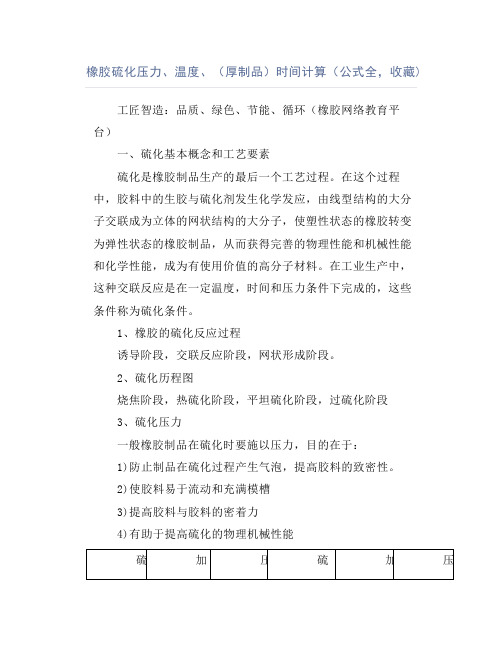
橡胶硫化压力、温度、(厚制品)时间计算(公式全,收藏)工匠智造:品质、绿色、节能、循环(橡胶网络教育平台)一、硫化基本概念和工艺要素硫化是橡胶制品生产的最后一个工艺过程。
在这个过程中,胶料中的生胶与硫化剂发生化学发应,由线型结构的大分子交联成为立体的网状结构的大分子,使塑性状态的橡胶转变为弹性状态的橡胶制品,从而获得完善的物理性能和机械性能和化学性能,成为有使用价值的高分子材料。
在工业生产中,这种交联反应是在一定温度,时间和压力条件下完成的,这些条件称为硫化条件。
1、橡胶的硫化反应过程诱导阶段,交联反应阶段,网状形成阶段。
2、硫化历程图烧焦阶段,热硫化阶段,平坦硫化阶段,过硫化阶段3、硫化压力一般橡胶制品在硫化时要施以压力,目的在于:1)防止制品在硫化过程产生气泡,提高胶料的致密性。
2)使胶料易于流动和充满模槽3)提高胶料与胶料的密着力4)有助于提高硫化的物理机械性能硫化机把压力传递给模型,再由模型传递给胶料;二是硫化介质直接加压(如蒸汽加压);三是以压缩空气加压;四是由注压机注压等。
4、硫化温度和硫化时间硫化温度是橡胶发生硫化反应的基本条件,它直接影响硫化速度和产品质量。
硫化温度高,硫化速度快,生产效率高。
反之,硫化速度慢,生产效率低。
硫化温度高低应取决于胶料配方,其中最重要的是取决于橡胶种类和硫化体系。
但应注意的是,高温橡胶分子链裂解,至发生硫化返原现象,结果导致强伸性能下降,困此硫化温度不宜太高。
温度是硫化三大要素之一,与所有化学反应一样,硫化反应随温度升高而加快,并且大体适用范特霍夫定律,即温度每上升8~10。
C(约相当于一个表压的蒸汽压力),其反应速度约增加一倍;或者说,反应时间约减少一半。
随着室温硫化胶料的增加和高温硫化出现,硫化温度趋向两个极端。
从提高硫化效率来说,应当认为硫化温度越高越好,但实际上不能无限提高硫化温度。
首先受到橡胶导热性极小阻碍,对于厚制品来说,采用高温硫化很难使内外层胶料同时达到平坦范围;其次,各种橡胶的耐高温性能不一,有的橡胶经受不了高温的作用,如高温硫化天然橡胶时,溶于橡胶中的氧随温度提高而活性加大,引起强烈的氧化作用,破坏了橡胶的组织,降低了硫化胶的物理机械性能,第三,高温对橡胶制品中的纺织物有害为棉纤维布料超过期作废140℃时,强力下降,在240℃下加热四小时则完全破坏。
橡胶三层共挤连硫操作流程
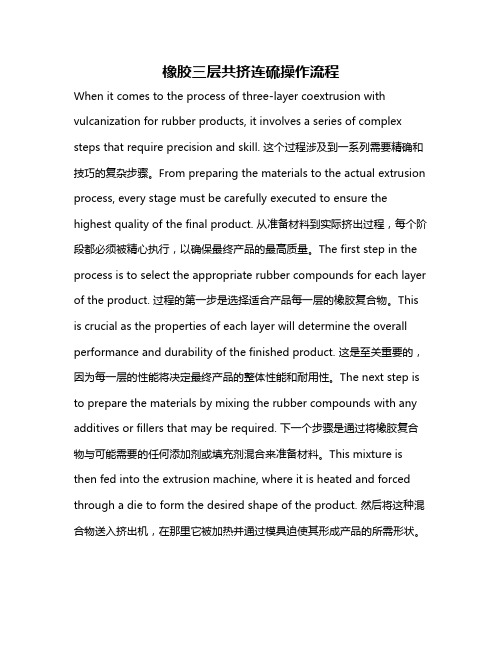
橡胶三层共挤连硫操作流程When it comes to the process of three-layer coextrusion with vulcanization for rubber products, it involves a series of complex steps that require precision and skill. 这个过程涉及到一系列需要精确和技巧的复杂步骤。
From preparing the materials to the actual extrusion process, every stage must be carefully executed to ensure the highest quality of the final product. 从准备材料到实际挤出过程,每个阶段都必须被精心执行,以确保最终产品的最高质量。
The first step in the process is to select the appropriate rubber compounds for each layer of the product. 过程的第一步是选择适合产品每一层的橡胶复合物。
This is crucial as the properties of each layer will determine the overall performance and durability of the finished product. 这是至关重要的,因为每一层的性能将决定最终产品的整体性能和耐用性。
The next step is to prepare the materials by mixing the rubber compounds with any additives or fillers that may be required. 下一个步骤是通过将橡胶复合物与可能需要的任何添加剂或填充剂混合来准备材料。
橡胶制品连续硫化方法简介

橡胶制品连续硫化方法简介连续硫化法是一种动态硫化方法。
其优点是产品不受长度限制,无重复硫化,能实现连续化、自动化、提高生产效率。
常见的连续硫化工艺如下:(1)热空气连续硫化室硫化法这是一种常压硫化方法,主要应用于硫化胶布、海绵胶条和胶乳制品。
制品连续通过硫化室进行加热硫化。
硫化室可分为三段,第一段为预热、升温,将制品加热到硫化温度;第二段为恒温硫化,制品于该段内的停留时间可以通过调节制品运动速度的方法加以调节;第三段为降温冷却,以便于制品的收卷。
硫化室可采用间接蒸汽、电、红外线等方式加热。
(2)蒸汽管道连续硫化法此工艺的特点是使制品连续地通过密封的硫化管道进行硫化。
硫化管道与压出机相连,制品经压出后直接进入硫化管道,管道中通入1~2.5MPa的高压蒸汽,管道尾部有高压冷却水进行冷却。
硫化管道的两端都安装防止高压蒸汽泄露的密封装置,一般采用迷宫式垫圈或水封法密封。
这种硫化方法主要用于硫化胶管、电缆、电线等两端易于密封的制品。
(3)液体介质连续硫化法(盐浴连续硫化法)硫化介质为熔融合金(锡42%、铋58%),熔点150℃;或者熔盐(硝酸钾53%、亚硝酸钠40%、硝酸钠7%),其熔点142℃,沸点500℃。
硫化时先将硫化介质以电加热至180~250℃,然后将半成品通过(通过时间依胶料的硫化条件而定),便可进行连续硫化。
由于熔融合金或熔融盐密度很大(1926kg/m3),因而必须用钢带将半成品型材压住使其浸入熔融液中。
由于熔融液传热很快,能使半成品迅速受热硫化,在180~250℃下以10~15m/min的速度硫化制品,但存在易使薄制品和空心制品变形的缺陷。
此法常用于胶管、胶条、电缆以及其他型材的硫化。
(4)沸腾床连续硫化法沸腾床是指在热空气流中悬浮直径为0.15~0.25mm的玻璃珠或粒径为0.2~0.3mm的石英砂为硫化介质的装置。
在受热空气流的吹动下,固体粒子悬浮于气体翻动,形成沸腾状态的加热床。
沸腾床可用电热或者过热蒸汽等加热,使之达到200~250℃的温度。
6590150连硫机组操作规程

8.4生产过程中参数需严格参考连续硫化设备挤出参数工艺过程卡,保证绝缘层或护套层充分硫化,挤出线芯外观、表面质量、断面质量及线芯识别用目力、手感进行检验。
6生产线的停车
6.1将生产线线速度预置值置于0m/min。
6.2在硫化管里的绝缘层达到硫化程度之前,所有设备仍然处于工作状态。
6.3停止蒸汽发生器。
6.4当硫化管里无压力时,才能打开伸缩管。
6.5剪断电缆,启动挤出机,直到无胶料排出为止。
6.6打开出口密封,排净冷却水。
6.7卸下机头,清洗零件。
6.8关闭全部设备。
编号:
Q/KH04-01.4-2014
2014年2月
共5页第4页
4.8.3经常注意收放线张力及排线情况,防止导线拉细。
4.8.4每盘线下车后,必须挂上产品跟踪卡,并在卡上注明产品型号、电压等级、规格、长度、生产号、生产班组、质量状况、制造日期等项目。
5设备运行中紧急停车
5.1在下列情况下需要停车:
5.1.1对操作人员及其它人员的身体有危险时。
2.14.2密封垫外径:Φ150mm(橡胶制品)。
2.15下牵引线速度:最大120m/min。
3生产前的准备
3.1穿戴好劳保用品,搞好设备以及设备周围的环境卫生。
3.2查看生产日报表,按生产产品规格穿引线芯,领取生产辅助材料。
3.3检查设备:
3.3.1检查生产线机电设备,水汽阀门,电器开关等是否完好正常,并对机械传动部位加注润滑油。
3.8使用尺寸不同的线盘时,可按收线机电位器的要求,进行调正。
考研化学第十章硫化

思考题:
1.生胶和硫化胶在分子结构及性能上有何不同?
2.橡胶的硫化历程分为几个阶段?各阶段的实质 和意义是什么?(作业题)
3.何谓硫化三要素?对硫化且要素控制不当会造 成什么后果?
4.试选择硫化轮胎外胎、布面胶鞋、纯胶管的最 佳硫化介质、硫化设备和硫化工艺方法。(任 选其一制品为作业题)
优点:传热均匀,密度较高,使制品变形 倾向较小。
缺点:热含量不高,导热效率低。 仅限于硫化含有活性温度低于100 ℃超速 促进剂的薄壁浸渍制品。
二、硫化方法
1.室温硫化法
在常温常压下进行,不需硫化设备。如汽 车、建筑用的胶粘剂;运输带的冷接和橡胶制 品修补用的自硫胶浆。
2.冷硫化法
多用于薄膜浸渍制品的硫化。将制品浸入 含2~5%的一氯化硫的溶液中经过数分钟或数 秒钟的浸渍即可完成硫化。
生成含有硫黄和促进剂的活性侧基,是橡胶 分子链形成交联的前驱体。
3.活性侧基之间或与橡胶间的化学反应
形成交联键。活性剂使交联键的数量增加, 交联键中硫原子数减少,硫化胶的性能提高。
4.交联键的继续反应
初始形成的交联网络中,交联键大多是多硫 交联键,继续反应,变成较短的二硫和一硫交联 键。在多硫交联键短化的同时,又增加新的硫黄 交联键,并伴有主链改性、环化等过程。
★混气硫化:在硫化的第一阶段以热空气为介 质.在第二阶段再通入蒸汽作介质。胶鞋硫化 采用该方法。
(3)过热水
优点:既能保持较高的温度,又能赋予较 大的压力,因此常用于高压硫化场合。
缺点:热含量小,导热效率低,且温度不 易掌握均匀。
典型的用途是轮胎硫化时,将过热水充注 于水胎中,以保持内温。
(4)热水
(2)注压机硫化法
是模压硫化的一种进展, 它是通过注射筒将胶料自动注 入模型中。具有成型快速、自 动化程度高,产品致密性高, 硫化周期短等优点,在胶鞋工 业、橡胶零件、密封件生产中 得到了广泛应用。
连硫硫化时间和生产速度
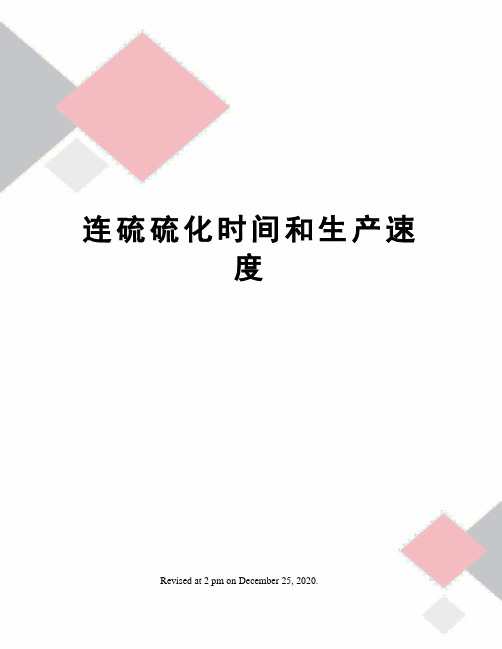
连硫硫化时间和生产速
度
Revised at 2 pm on December 25, 2020.
文件编号:G L/W J J X Z03-2010
广东电缆企业集团有限公司
Φ70+Φ90连续硫化机组硫化管
温度、压力、硫化时间、生产速度关系对照表
1. 蒸汽压力和生产线速度要严格按照工艺卡、工艺技术指导书的要求执行。
2. 不同的胶种、不同的蒸汽压力对应着不同的生产速度,当蒸汽压力低
于规定值时,应将线速度按比例降低,具体参照本表数据。
3. 本表只适用于Φ70+Φ90连续硫化机组日常生产橡套线缆,使用的胶
种为
连硫绝缘胶:XJ-L01 连硫护套胶:XH-L01 连硫焊缆
胶:XH-L02
4. 硫化管内的最高气压不得超过 MPa 。
编制:孔令南审核:批准: 2010年6月10日。
连续硫化生产线
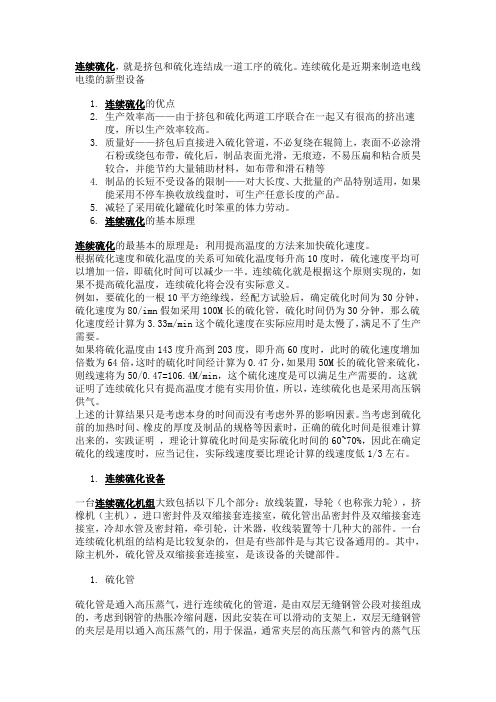
连续硫化,就是挤包和硫化连结成一道工序的硫化。
连续硫化是近期来制造电线电缆的新型设备1.连续硫化的优点2.生产效率高——由于挤包和硫化两道工序联合在一起又有很高的挤出速度,所以生产效率较高。
3.质量好——挤包后直接进入硫化管道,不必复绕在辊筒上,表面不必涂滑石粉或绕包布带,硫化后,制品表面光滑,无痕迹,不易压扁和粘合质昊较合,并能节约大量辅助材料,如布带和滑石精等4.制品的长短不受设备的限制——对大长度、大批量的产品特别适用,如果能采用不停车换收放线盘时,可生产任意长度的产品。
5.减轻了采用硫化罐硫化时笨重的体力劳动。
6.连续硫化的基本原理连续硫化的最基本的原理是:利用提高温度的方法来加快硫化速度。
根据硫化速度和硫化温度的关系可知硫化温度每升高10度时,硫化速度平均可以增加一倍,即硫化时间可以减少一半。
连续硫化就是根据这个原则实现的,如果不提高硫化温度,连续硫化将会没有实际意义。
例如,要硫化的一根10平方绝缘线,经配方试验后,确定硫化时间为30分钟,硫化速度为80/imn假如采用100M长的硫化管,硫化时间仍为30分钟,那么硫化速度经计算为3.33m/min这个硫化速度在实际应用时是太慢了,满足不了生产需要。
如果将硫化温度由143度升高到203度,即升高60度时,此时的硫化速度增加倍数为64倍,这时的硫化时间经计算为0.47分,如果用50M长的硫化管来硫化,则线速将为50/0.47=106.4M/min,这个硫化速度是可以满足生产需要的。
这就证明了连续硫化只有提高温度才能有实用价值,所以,连续硫化也是采用高压锅供气。
上述的计算结果只是考虑本身的时间而没有考虑外界的影响因素。
当考虑到硫化前的加热时间、橡皮的厚度及制品的规格等因素时,正确的硫化时间是很难计算出来的,实践证明,理论计算硫化时间是实际硫化时间的60~70%,因此在确定硫化的线速度时,应当记住,实际线速度要比理论计算的线速度低1/3左右。
电线电缆快速硫化生产的硫化工艺参数

电线电缆快速硫化生产的硫化工艺参数1、引言用传统工艺生产的橡套电缆一般不能和高档家用电器配套,其主要原因是电缆的外观不好,铜丝氧化严重,不能和家用电器配套,一般用塑料软电缆代替。
随着中国加入WTO,中国的产品标准也全部按国际IEC标准一致,许多家用电器的供电电源线规定必须使用橡套电缆,如空调器用的室内外连接线就规定必须用245IEC57(YZW)橡套软电缆。
因此,提高橡套软电缆的外观质量,是当前急需解决的现实问题。
连继硫化是一种新的橡套电缆加工方法,本文通过对橡套电缆生产过程中的一些工艺参数讨论,推道出一整套的硫续硫化工艺参数,不断提高橡套电缆的产品质量,供电缆行业的同行们参考。
2、规格的确定一般连续硫化机组技术规范都规定模具尺寸范围,即规定了模芯、模套最小孔径,这是确定规格的依据之一。
另外,还规定螺杆转速范围,挤橡时螺杆转速低于规定转速,橡胶塑性不均匀,流动性差,挤出量不够稳定,电缆加工困难,机头内压力很大,容易顶坏机头。
若超过范围,橡胶挤出量不足,只能降低出线速度来弥补,影响生产效率。
3、螺杆转速和牵引速度的确定螺杆转速和牵引速度决定了生产效率和制品的外径、外观。
确定螺杆转速和牵引速度的基本原理是物料平衡原理,即螺杆挤出的橡胶量,正好被牵引出来的制品包覆所需要的橡胶量相等。
一般地说,确定螺杆和牵引速度时,先定出牵引速度,即硫化时间,它是决定制品各项机械物理性能的主要因素,本文将作详细介绍。
连续硫化挤橡机螺杆都采用长径比12:1以上的塑化螺杆,螺杆与筒体之间回料量小,螺杆转速与挤出量基本成正比,即成线性关系。
例如,某挤橡机组技术规范中规定,螺杆转速为10~50rpm/min,最大挤出量为120kg/h。
根据这些数据可以制作螺杆转速和挤出量关系图。
例如,某产品挤护套,理论计算护套用料量为78.7 kg/km,出线速度为20m/min,可以计算出每分钟的用料量:用料量=20×78.7÷1000=1.574 kg/min根据物料平衡原理,橡胶挤出量也需要1.574 kg/min,查图1可以得出,螺杆转速为39转/分左右,在设备规范规定的转速范围内,符合设备技术规范。
1硫化体系配合剂

硫化体系配合剂硫化指的是线形大分子链交联成三维网状结构。
橡胶硫化概念的两次扩大。
硫化剂:能引起橡胶交联的化学药品。
凡在胶料中起到硫化作用的化学药品,都称为硫化体系的配合剂。
硫化体系配合剂包括:硫化剂、促进剂、活性剂、防焦剂。
第一节硫磺硫化的硫化剂------硫磺硫化剂种类:硫(硒,碲)、有机多硫化物、有机过氧化物、金属氧化物、醌类、树脂、胺类、特种硫化剂。
一、硫黄(S)简介1、硫磺的品种和性质粉末硫磺(硫磺粉)、沉降硫磺、胶体硫磺、表面处理硫磺、不溶性硫磺等硫磺分子是由八个硫原子构成的八元环(S8),有结晶和无定形两种形态。
在自由状态下,硫磺以结晶形态存在,把硫磺加热至熔点(119℃)以上时,则变成液体硫磺。
所以橡胶在硫化时,因为温度高,硫磺处于无定形状态。
1)硫磺粉:是将硫磺块粉碎筛选而得。
其粒子平均直径15 ~ 20μm,熔点114 ~ 118℃,相对密度1.96 ~2.07,是橡胶工业中使用最为广泛的一种硫磺。
2)不溶性硫磺:不溶性硫磺是一种无毒、可燃的黄色粉末,因其不溶于二硫化碳而得名。
它经普通硫磺热聚合制得,分子链上的硫原子数高达108以上,也有有类似高聚物的粘弹性和分子量分布,也称弹性硫或聚合硫。
因大部分(65% ~ 95%)不溶于二硫化碳(因聚合),故称不溶性硫磺。
由于它具有不溶于橡胶的特点(因聚合),因此在胶料中不易产生早期硫化和喷硫现象,无损于胶料的黏性,从而可剔除涂浆工艺,节省汽油、清洁环境。
在硫化温度,不溶性硫磺转变为通常的硫磺以发挥它对橡胶的硫化作用。
一般用于特别重要的制品,如钢丝轮胎等。
不溶性硫磺是将硫磺粉加热至沸腾(444.6℃),倾于冷水中急冷而得的透明、无定形链状结构的弹性硫磺。
亦可将过热硫磺蒸气用惰性气体稀释,喷在冷水雾中冷却至90℃以下制得,或将硫磺块溶于氨中立即喷雾干燥获得。
优点:分散均匀、不容易聚集、不容易迁移、不易产生早期硫化和喷硫,无损于胶料的黏性。
在硫化温度,不溶性硫磺转变为通常的硫磺(解聚)以发挥它对橡胶的硫化作用。
橡胶制品的硫化时间及正硫化时间
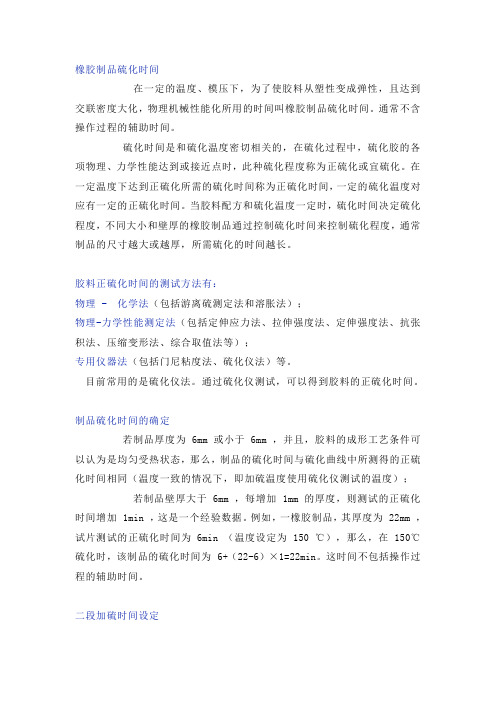
橡胶制品硫化时间在一定的温度、模压下,为了使胶料从塑性变成弹性,且达到交联密度大化,物理机械性能化所用的时间叫橡胶制品硫化时间。
通常不含操作过程的辅助时间。
硫化时间是和硫化温度密切相关的,在硫化过程中,硫化胶的各项物理、力学性能达到或接近点时,此种硫化程度称为正硫化或宜硫化。
在一定温度下达到正硫化所需的硫化时间称为正硫化时间,一定的硫化温度对应有一定的正硫化时间。
当胶料配方和硫化温度一定时,硫化时间决定硫化程度,不同大小和壁厚的橡胶制品通过控制硫化时间来控制硫化程度,通常制品的尺寸越大或越厚,所需硫化的时间越长。
胶料正硫化时间的测试方法有:物理 - 化学法(包括游离硫测定法和溶胀法);物理-力学性能测定法(包括定伸应力法、拉伸强度法、定伸强度法、抗张积法、压缩变形法、综合取值法等);专用仪器法(包括门尼粘度法、硫化仪法)等。
目前常用的是硫化仪法。
通过硫化仪测试,可以得到胶料的正硫化时间。
制品硫化时间的确定若制品厚度为 6mm 或小于 6mm ,并且,胶料的成形工艺条件可以认为是均匀受热状态,那么,制品的硫化时间与硫化曲线中所测得的正硫化时间相同(温度一致的情况下,即加硫温度使用硫化仪测试的温度);若制品壁厚大于 6mm ,每增加 1mm 的厚度,则测试的正硫化时间增加 1min ,这是一个经验数据。
例如,一橡胶制品,其厚度为 22mm ,试片测试的正硫化时间为6min (温度设定为 150 ℃),那么,在 150℃硫化时,该制品的硫化时间为 6+(22-6)×1=22min。
这时间不包括操作过程的辅助时间。
二段加硫时间设定为了达到合理的制造工艺和合理成本,把橡胶硫化分为一段、二段两个过程来完成的工艺方法,其第二段的工艺就是所谓的二段加硫。
一段硫化主要是使制品得到定形,然后将未100% 正硫化状态而得到定形的制品集中起来进行二段硫化。
这样,提升了一段硫化的效率,二段硫化的集中处理,也提升了效率,节省了能源。
- 1、下载文档前请自行甄别文档内容的完整性,平台不提供额外的编辑、内容补充、找答案等附加服务。
- 2、"仅部分预览"的文档,不可在线预览部分如存在完整性等问题,可反馈申请退款(可完整预览的文档不适用该条件!)。
- 3、如文档侵犯您的权益,请联系客服反馈,我们会尽快为您处理(人工客服工作时间:9:00-18:30)。
连硫硫化时间和生产速
度
TPMK standardization office【 TPMK5AB- TPMK08- TPMK2C- TPMK18】
文件编号:GL/WJ JXZ03-2010广东电缆企业集团有限公司
Φ70+Φ90连续硫化机组硫化管
温度、压力、硫化时间、生产速度关系对照表
1. 蒸汽压力和生产线速度要严格按照工艺卡、工艺技术指导书的要求执行。
2. 不同的胶种、不同的蒸汽压力对应着不同的生产速度,当蒸汽压力低于规
定值时,应将线速度按比例降低,具体参照本表数据。
3. 本表只适用于Φ70+Φ90连续硫化机组日常生产橡套线缆,使用的胶种为
连硫绝缘胶:XJ-L01 连硫护套胶:XH-L01 连硫焊缆胶:XH-L02
4. 硫化管内的最高气压不得超过1.9 MPa 。
编制:孔令南审核:批准: 2010年6月10日。