SMT检查表
SMT班长日常工作点检表

周别: 完成情况 1 2 3 4 5 6
烧录IC 4 7 8 1 5S 2 3 班后 1 交接 2 3 记录 报表 1 1 烧录IC贴纸是否与实际生产机型、批次、校验码和版 本号一样? 样版票的内容是否与生产机型的要求一致? 即将转产机型的软件资料是否提前准备核对OK? 各工作的摆放及现场的整理? 是否按照规定的班前班后2分钟整理自己的岗位。 需关闭的电源是否关掉(安全工作)? 当天生产过程中的品质异常及注意事项? 生产计划、品质、物料等是否准确交接? 上级领导的要求及公司的文化精神的传达? 是否及时、正确填写设备日常点检记录? 各种报表需准确统计及时上交?
日常 3 4 班前 锡膏红胶印 刷 5 6 7 8 9 各种检点表 1 2 3 贴片 4 7 9 11 1 回流焊 2 3 1 班中 目检 2 4 7 9 2 3 1 静电车、 静电架 2 3 4 1 2 烧录IC 3 检查事项及要求 查看当天的生产计划走向。 开早会,总结头天的工作和当天的工作安排。 锡膏型号是否正确?(ALPHA SAC405 OM338) 红胶型号是否正确?(FUJI NE3000S) 生产前是否及时准备好锡膏与红胶解冻? 操作员在使用开封时有没有写上开封及有效时间? 各区域5S是否规范? 员工对静电防护措施状况跟进。 丝印员是否对丝印品质进行全检?有异常是否及时反 馈? 是否按照规定的时间进行检点并记录。 贴片机程序是否与实际生产机型相符? F5HM操作员是否正确佩戴静电手环? 操作员的对料单是否和机器程序及实际排位一致? 操作员的换料报表记录OK有无涂改、错料的现象? 操作员对机器的错误信息是否能熟练正确的清除? 贴片目检是否及时反馈贴片不良? 更换不良Feeder后是否按照要求进行对整区域进行对 料一次? 回流焊程序参数设置温度和实际温度是否与作业指导 书一致? 回流焊抽风机开了吗?制冷系统是否正常工作? 轨道宽度是否合适(比板宽0.5~1mm)?是否有卡板 、掉板现象? 静电带是否配戴?是否规范? 是否核对烧录程序贴纸? 报表是否如实规范清楚的记录? 目检是否及时反馈贴片不良? 目检员是否按照每4小时对一次首件,确认机型、批 次及贴片元件是否和首件一致? 烙铁温度是否符合工艺要求(380-420度)? 返修后是否按照工艺要求进行清洗并做记号跟踪? 检查宽度是否与板一致(比板宽约0.5~1.0mm)? 检查每一层宽度是否一致? 所有装有板的静电架上是否有LOT管理表并规范填写 检查螺钉是否紧固?有无变形? 静电带是否配戴?是否规范?接触P板、I C是否戴静 电手套? 物料编号是否正确? 烧录OK的IC校验码、版本号是否与软件部门提供的 资料一致? 检查人
SMT常规巡检表
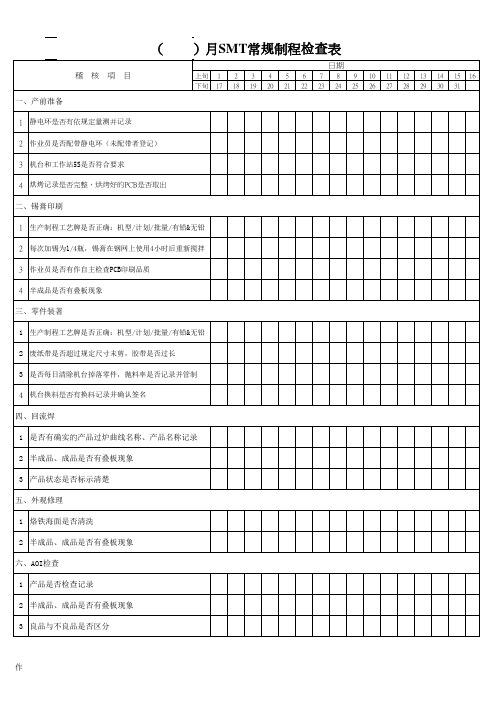
2 废纸带是否超过规定尺寸未剪,胶带是否过长
3 是否每日清除机台掉落零件,抛料率是否记录并管制
4 机台换料是否有换料记录并确认签名
四、回流焊
1 是否有确实的产品过炉曲线名称、产品名称记录
2 半成品、成品是否有叠板现象
3 产品状态是否标示清楚
五、外观修理
1 பைடு நூலகம்铁海面是否清洗
2 半成品、成品是否有叠板现象
(
稽 核 項 目 一、产前准备
)月SMT常规制程检查表
日期
上旬 1 2 3 4 5 6 7 8 9 10 11 12 13 14 15 16 下旬 17 18 19 20 21 22 23 24 25 26 27 28 29 30 31
1 静电环是否有依规定量测并记录
2 作业员是否配带静电环(未配带者登记)
六、AOI检查
1 产品是否检查记录
2 半成品、成品是否有叠板现象
3 良品与不良品是否区分
作
3 机台和工作站5S是否符合要求
4 烘烤记录是否完整,烘烤好的PCB是否取出
二、锡膏印刷
1 生产制程工艺牌是否正确:机型/计划/批量/有铅&无铅
2 每次加锡为1/4瓶,锡膏在钢网上使用4小时后重新搅拌
3 作业员是否有作自主检查PCB印刷品质
4 半成品是否有叠板现象
三、零件装著
1 生产制程工艺牌是否正确:机型/计划/批量/有铅&无铅
1.SMT开班检查记录表
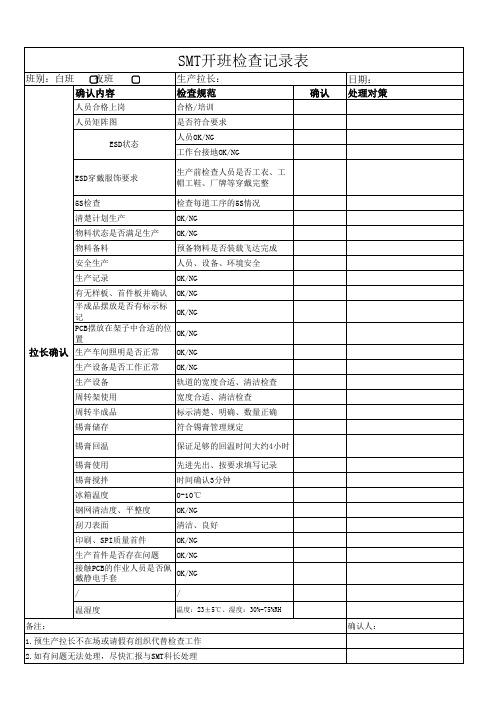
班别:白ห้องสมุดไป่ตู้ 夜班 确认内容
人员合格上岗 人员矩阵图 ESD状态
生产拉长: 检查规范
合格/培训 是否符合要求 人员OK/NG 工作台接地OK/NG 生产前检查人员是否工衣、工 帽工鞋、厂牌等穿戴完整 检查每道工序的5S情况 OK/NG OK/NG 预备物料是否装载飞达完成 人员、设备、环境安全 OK/NG OK/NG
确认
日期: 处理对策
ESD穿戴服饰要求 5S检查 清楚计划生产 物料状态是否满足生产 物料备料 安全生产 生产记录 有无样板、首件板并确认
半成品摆放是否有标示标 OK/NG 记 PCB摆放在架子中合适的位 OK/NG 置
拉长确认 生产车间照明是否正常
生产设备是否工作正常 生产设备 周转架使用 周转半成品 锡膏储存 锡膏回温 锡膏使用 锡膏搅拌 冰箱温度 钢网清洁度、平整度 刮刀表面 印刷、SPI质量首件 生产首件是否存在问题
温度:23±5℃、湿度:30%-75%RH
确认人:
OK/NG OK/NG 轨道的宽度合适、清洁检查 宽度合适、清洁检查 标示清楚、明确、数量正确 符合锡膏管理规定 保证足够的回温时间大约4小时 先进先出、按要求填写记录 时间确认3分钟 0-10℃ OK/NG 清洁、良好 OK/NG OK/NG
接触PCB的作业人员是否佩 OK/NG 戴静电手套 / 温湿度 备注: 1.预生产拉长不在场或请假有组织代替检查工作 2.如有问题无法处理,尽快汇报与SMT科长处理 /
SMT巡回查检表
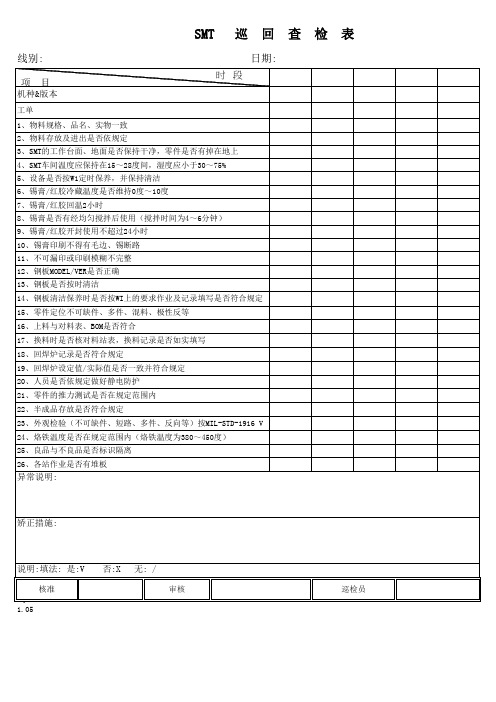
线别:
日期:
项目 机种&版本
时段
工单
1、物料规格、品名、实物一致 2、物料存放及进出是否依规定 3、SMT的工作台面、地面是否保持干净,零件是否有掉在地上 4、SMT车间温度应保持在15~28度间,湿度应小于30~75% 5、设备是否按W1定时保养,并保持清洁 6、锡膏/红胶冷藏温度是否维持0度~10度 7、锡膏/红胶回温2小时 8、锡膏是否有经均匀搅拌后使用(搅拌时间为4~6分钟) 9、锡膏/红胶开封使用不超过24小时 10、锡膏印刷不得有毛边、锡断路 11、不可漏印或印刷模糊不完整 12、钢板MODEL/VER是否正确 13、钢板是否按时清洁 14、钢板清洁保养时是否按WI上的要求作业及记录填写是否符合规定 15、零件定位不可缺件、多件、混料、极性反等 16、上料与对料表、BOM是否符合 17、换料时是否核对料站表,换料记录是否如实填写 18、回焊炉记录是否符合规定 19、回焊炉设定值/实际值是否一致并符合规定 20、人员是否依规定做好静电防护 21、零件的推力测试是否在规定范围内 22、半成品存放是否符合规定 23、外观检验(不可缺件、短路、多件、反向等)按MIL-STD-1916 V 24、烙铁温度是否在规定范围内(烙铁温度为380~450度) 25、良品与不良品是否标识隔离 26、各站作业是否有堆板 异常说明:
矫正措施:
说明:填法: 是:V
核准 BQ-84-038 1.05
否:
SMT巡检表

《AOI日维护检查记录表》是否记录
BI
成品板使用板框放置时必须隔一块放置,避免撞件
不同状态的产品(合格品、不合格品等)是否有分开放置,并有清楚 、 明确的状态标识,预加工、半成品、异常品、缺料待生产等是否有明确标
识或辨别状态的标识 ESD是否按照要求规范穿戴(静电环、静电衣、帽、鞋)
在线维修
PCB是否真空包装
锡膏管控是否符合锡膏管控要求,如锡膏回温、搅拌、放回冰箱、报废等 是否符合要求
锡膏厚度是否按时测量,并记录在《锡厚测量记录表》
上料、换料是否符合要求,如截料是否找PQA确认等
《贴片机日维护记录表》是否记录
F/D list是否受控并会签
F/D list不允许涂改,特殊情况(如移料,换料等)需工程人员签字确认
机台
每2小时是否通查物料并记录
是否和程序核对,并记录(只针对西门子线体)
SMT车间双排孔散料极性是标示湿敏器件的管控是否符合湿敏器件管控要求,如是否有开封管制表做跟踪 和登记相关拆封时间、使用、重新包装等信息
是否按作业指导书规定操作
极性是否确认,并记录
《回流焊温度记录表》是否记录
《回流炉日维护记录表》是否记录
SMT巡检表
PQA:
日期:
类别 岗位 ESD /
印刷
检查项 静电鞋、静电环是否都已测试 ESD是否按照要求规范穿戴(静电环、静电衣、帽、鞋)
温湿度是否点检 各岗位是否有受控作业指导书
各岗位是否有通用文件 是否按作业指导书规定操作,如印刷质量检验等
《上板机日维护记录表》是否记录 《印刷机日维护记录表》是否记录 钢网是否按时清洗,是否找PQA确认,是否记录在《DEK通用记录表》 《印刷工艺参数设定检查表》是否记录,是否在工艺要求范围内 清洗板是否记录,是否找PQA确认 岗位5S,各物品摆放,印刷机机盖是否关闭等
SMT设备班前点检表

4
检查机器前后罩盖是否 盖好
5 检查气压是否在范围内 气压范围:0.4MPa--0.6MPa
6 检查感应器是否遮挡 表面干净,清洁周围无异物
7 检查各轨道是否有杂物 无任何物品,无任何障碍物
8 检查紧急开关是否正常
灵活,可靠
检查气动系统是否漏 9 气,过滤装置有无积
水,是否正常工作。
天
1、正常 √ 记入方法 2、异常 ×
3、无此项 -
稽核人: 备注
1、每日开机前必须实际正确操作点检 2、操作员必须按标准作业指导书作业
设备班前点检表
设备名称
设备型号
使用部门
日期
序号
班前点检项目
衡量标准
日期
1 2 3 4 5 6 7 8 9 10 11 12 13 14 15 16 17 18 19 20 21 22 23 24 25 26 27 28 29 30 31
1 检查总电源是否正常
2 检查各指示灯是否正常
3 检查安全标示是否完整 完好,无破损模糊现象
SMT首件检查表

拒收/REJECT
改善对策
状况
Approved by:
Check ed by:
BY:
1
印 所用的钢板是否与机种相符
刷
机 首片 PCB 的锡膏厚度是否在规格內
首片 PCB 的锡膏外观是否符合 AI
钢板的清洁频率是否与规定相符
2
贴片 所用程是否与生产机种相符
机
首片 PCB 的外观是否规范
所用的料与 BOM 是否相符
零件的极性是否正确
3回
焊 炉
回焊炉的各参数温度是否正常(温度曲线 图) 终检首片 PCB 外观是否符合规范
一:检查内容(Visual Inspection Contents)
序列 项目
检验项目
规格
检查结果
结论
No ITEM
CHECK ITEM
SPEC
CHECK RESULT STATUS
1 PCB
PCB 号,版本号是否与生产机种相符
印
刷
所用的锡膏品牌/型号
机
锡膏的回温时间与开封时间(开封后,必須于
48 小时內用完)
SMT 首件检查表
新机种/NEW PRODUCT
工程变更/EC/CP/FN
正常生产/NOMAL PRODUCT
其它/OTHER
机种/MODEL NAME_______ ___批量/LOTS SIZE___________日期/DATE____________ 线班别/LINE&SHIFT_______
4 其 它 工程变更项目是否完全执行
检 查 人员作业接触 PCBA 时是否作参考
零件受力测试是否在规格
二: 结论与备注(Final Conclusion Or Comments)
SMT产品检验表
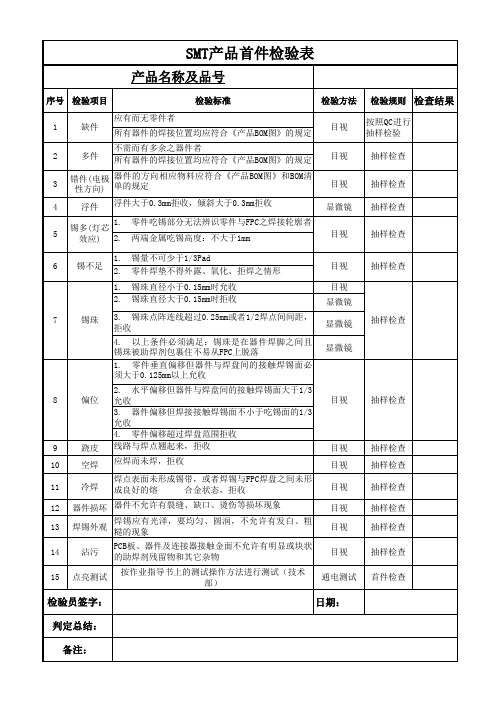
目视
抽样检查
13
焊锡外观
焊锡应有光泽,要均匀、圆润,不允许有发白、粗 糙的现象
目视
抽样检查
14
沾污
PCB板、器件及连接器接触金面不允许有明显或块状 的助焊剂残留物和其它杂物
目视
抽样检查
15
点亮测试
按作业指导书上的测试操作方法进行测试(技术 部)
通电测试 首件检查
检验员签字:
日期:
判定总结:
备注:
SMT产品首件检验表
产品名称及品号
序号 检验项目
检验标准
检验方法 检验规则 检查结果
1
应有而无零件者 缺件 所有器件的焊接位置均应符合《产品BOM图》的规定
目视
按照QC进行 抽样检验
不需而有多余之器件者
2
多件 所有器件的焊接位置均应符合《产品BOM图》的规定 目视
抽样检查
3
错件(电极 器件的方向相应物料应符合《产品BOM图》和BOM清 性方向) 单的规定
目视
4
浮件 浮件大于0.3mm拒收,倾斜大于0.3mm拒收
显微镜
抽样检查 抽样检查
1. 零件吃锡部分无法辨识零件与FPC之焊接轮廓者
5
锡多(灯芯 效应) 2. 两端金属吃锡高度:不大于1mm
目视
抽样检查
1. 锡量不可少于1/3Pad 6 锡不足 2. 零件焊垫不得外露、氧化、拒焊之情形
目视
抽样检查
1. 锡珠直径小于0.15mm时允收 2. 锡珠直径大于0.15mm时拒收
8
偏位 允收
目视
抽样检查
3. 器件偏移但焊接接触焊锡面不小于吃锡面的1/3
允收
4. 零件偏移超过焊盘范围拒收
SMT环境检查表

员工宿舍和饭堂是否按排好?
29
放置的设备和工具是否能保证安全?
30
入机通道是否畅通无阻,门是否够机通过?
31
32
ቤተ መጻሕፍቲ ባይዱ33
34
35
36
37
38
39
40
10
对大地阻抗是否合格?(≦100Ω)
11
有无接入一兆欧电阻?
12
设备的地线是否按装好?
13
对大地的阻抗是否合格?(≦10Ω)
14
消防设施是否已按装好?
15
人行通道是否畅通无阻?
16
电源和气压是否按装到位?
17
有无单相110V电源,能提供多大的功率?
18
有无单相220V电源,能提供多大的功率?
19
有无三相380V电源,能提供多大的功率?
20
电源输出是否非常稳定,有无测定过?
21
是使用市电,还是自已发电?
22
是否每天都要转二次电,每次需要多长时间,什么时候转电?
23
气压是否按装到位?
24
气压的压力是多大(≧5Kgf/CM^2),能提供多大的气体流量?
25
回流炉的抽风管道是否按装好?
26
计算机网络线是否按装好?
27
内线电话是否按装好?
环境状态检查表
No
检查内容
OK
NG
备注
1
厂区环境是否非常干净无灰尘?
2
空气中是否有异味?
3
工作区域是否能听到很大的噪音?
4
灯光是否很明亮?
5
环境温度是否在25℃±5℃以内?
6
环境湿度是否在50%±20%以内?
SMT首件检查表

电测
敲击检查
敲击高度50MM,在静电垫上敲击3次(不可敲击 目视测试有无异常 PCBA正反面)判定基准:无掉件、偏移及功能测
判定
目视测试有无异常
试OK判定合格
推力测试
针对PCBA各电子元件使用推力计进行推料测试, 其推力值必须≥1KG(IC≥2KG)以上无掉件、偏
移及功能测试OK判定合格
C: L:
Kg R: Kg IC:
Kg Kg
C: Kg R: Kg L: Kg IC: Kg
总结 签署 备注
生产:
工
程:
品质:
首件评审:
检查结果:合格项目打“√”,不合格项目打“×”,无此检查项目打“/”;
判定 判定
作成:
审核:
批准: 表单编号: 版本:
首件信息(生产部填写) 料号 型号
首件类型 制作 检查项目:(生产部填写)
检查项目
站位
物料要求
XXX有限公司 SMT首件检查表别 日期 初步判定 检验结果(测试值1由生产填写,测试值2由品质部填写)
(检验结果)
测试值1
判定
测试值2
判定
IC贴片前是否需要烧录: 是□
否□ 是否有测试架: 有□ 无□
工程确认签名:
PCB长:
尺寸(是否与图 PCB宽: 纸一致) PCB厚:
PCBA长:
外观(是否与样 品图纸一致)
各部件结构是否与样品/图纸一致
功能测试(图纸 上备注“测试细
测试工序
测试设备要求
分辨率/EDID
软件版本
节参照TSP文件 ”字样按照TSP 执行,无则按照
图纸执行)
SMT日常生产巡检表

在料盘上做记录;30分钟内QC确认,并在料 换料记录表填写完整、及时、真实
盘上做记录
快要耗尽的材料提前准备完毕
IC材料剩余1-2米时可以接料,CHIP材料接料后以 不超料盘为准
新产品 随时 随时 随时
随时
随时
随时
技术员 技术员 操作员 操作员
操作员
操作员
操作员
材料更换
材料盘与实物不一致时,使用标签覆盖原 有标识标签,标签上记录料号,规格,贴标 签人,时间,确认人(LCR检测)
随时
改任何参数及数字
样板核对 操作员每隔一小时核对一遍样板
1次/时
设备点检 检查设备气压、动作无异常、表面无污染 急停按钮、设备气压无异常
1次/班
程序
程序名称使用正确
与《程序列表》,产品名称、版本号一致
新产品
确认炉温正常达标后才可放板进入回流焊
推板入回流焊
放板进入前确认回流焊链条宽度合适,入 口和出口处宽度一致,设备间轨道水平一 致
使用前确认无凹凸痕,无破损,PIN孔内无 锡膏
有问题及时报告线长或主管
换线时 操作员
定时检查钢网,防止未清洁、堵孔、损坏 等现象
避免在生产时才发现,影响生产效率
2次/班 班组长
MASK清洗后使用气枪吹干净开孔内锡膏
尤其关注IC PIN部位孔内残留锡膏会导致印刷不 良
随时
操作员
刮刀安装在MASK安装之前进行
部分元件规格一样,但是元件尺寸可能不相同, 可能会发生混用,导致抛料
对于SM411正确了解机器的前后TABLE以及
相应的F/R标示
安装FEEDER前用毛刷清洁TABLE上的异物
避免Feeder晃动,造成抛料,用手轻微摇晃 Feeder末端试验
SMT检验记录表(XJ)
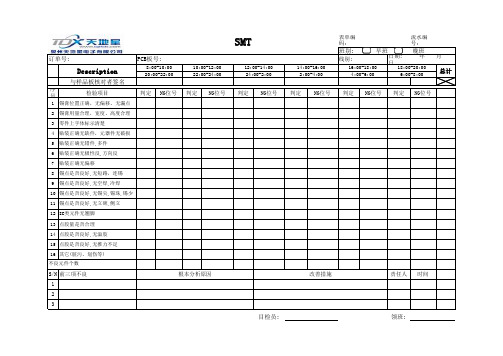
SMT贴片巡检记录表
表单编码:流水编号:
与样品板核对者签名
序号
检验项目
判定NG位号判定NG位号判定NG位号判定NG位号判定NG位号判定NG位号
1锡膏位置正确,无偏移、无漏点2锡膏用量合理,宽度、高度合理3零件上字体标示清楚
4贴装正确无缺件,元器件无破损5贴装正确无错件,多件6贴装正确无极性反,方向反7贴装正确无偏移
8锡点是否良好,无短路,连锡9锡点是否良好,无空焊,冷焊10锡点是否良好,无锡尖,锡珠,锡少11锡点是否良好,无立碑,侧立12IC类元件无翘脚13点胶量是否合理14点胶是否良好,无溢胶15点胶是否良好,无推力不足16其它(脏污、划伤等)S/N 前三项不良责任人时间
123
目检员:领班:
根本分析原因改善措施Description
总计
10:00-12:0022:00-24:0012:00-14:0024:00-2:00订单号:
线别:
日期: 年 月 日
不良元件个数
4:00-6:00
18:00-20:006:00-8:00
8:00-10:0020:00-22:00班别: 早班 晚班
PCB板号:
2:00-4:0014:00-16:0016:00-18:00。
SMT部门安全检查表

项目12345678910111213141516171819202122232425262728293031安全通道及安全出口是否畅通辖区内的门、窗是否破裂、损坏,门上的标示是否清晰消防应急灯和安全出口指示灯有否被移动/挪用;功能是否正常 灭火器材(灭火器,消火栓)是否被移动或被堵塞;是否被使用货物与消防喷淋头间的距离是否符合50CM 以上的要求辖区内是否有未向安全部门申报就开工的明火作业(如各类维修时的电焊、氧焊作业等)地面是否有油污、水渍车间垃圾(特别是擦化学品的废布或废纸)是否每天清理两次电线是否外露(即电线无护管或保护套);是否有电线横穿通道桌下电线是否有序绑扎,排插是否妥善固定,并有明确电压标示;用电插头是否与排插接触良好,并完全插到位(禁止插头金属外露);插头、插座、排插、设备开关等有否破裂、松动或变形开关是否明确标示出控制的部位或设备;是否被堵塞而不便操作电箱是否被堵塞(保持前方至少有80CM 的空隙,并易于接近)操作用电设备、电烙铁、手持电动工具时有电击感是否有私拉乱接电线的现象(除插/拔插头插座外,非电工不得接驳电源)下班前是否与接班者作好交接班工作,或按规定关闭电源;公共设备(如砂轮机、抽风机、照明电源开关等)是否落实了责任人是否有光管闪烁不定(易导致启辉器甚至镇流器发热而失火)员工在上班前是否对安全防护装置(如护罩、双手按钮控制开关、限位装置等)进行检查;功能是否正常为求方便,工作中是否有取下安全防护装置,或使防护装置失去防护作用的现象机械设备、测试设备、各类高温炉/测试炉等设备上面是否摆放物品、工具而容易发生危险,特别摆放重物、易燃物品当天是否有新设备投入使用?如果是,主管和安全员是否对设备作使用前安全检查本辖区内的公共设备(如砂轮机、排气扇、冰箱、空调等)是否有专人负责;是否正常检修中的设备是否挂牌警示使用中的工具类型是否适合;工具的状态是否正常(如扳手因磨损而打滑;刀片变钝;电批松动;夹具固定不紧;旋转部分松动而可能飞出伤人,等)工装夹具是否有摆放不稳固、过高而有倒塌、跌落伤人的危险尖锐/锋利的工具(如刀片、剪钳、螺丝批等)是否处于不安全的状态(如放置不稳而易于坠落;超出工作台边缘或放置方向不当易致人误伤)部 门: SMT 组 别: SMT 时 间: 年 月 第 页,共 页消防及公共设施电气安全设备及工具安全检查日期 检查内容 JLFR--- Rev.A项目12345678910111213141516171819202122232425262728293031部 门: SMT 组 别: SMT 时 间: 年 月 第 页,共 页检查日期 检查内容 JLFR--- Rev.A项目12345678910111213141516171819202122232425262728293031部 门: SMT 组 别: SMT 时 间: 年 月 第 页,共 页检查日期 检查内容 其JLFR--- Rev.A。
SMT车间检查表

序号
检查项
标准值
检查记录
判定
30.
机器贴板最大尺寸
长600mm,宽400mm
31.
元件
核对型号,位置,方向
32.
贴片位置精准度
引脚偏离焊盘≤1/6
33.
贴片压力
根据设备需求设定
34.
吸嘴贴片尺寸补偿
35.
元件上料、换料需登记、确认
元件上料、换料登记,并有人签字确认
回流焊接
序号
检查项
标准值
检查记录
检查记录
判定
52.
LED维修
维修过的LED不可再用
53.
维修位置
元器件维修过的位置及维修方式要记录
54.
维修飞线
不可有飞线
55.
清洁
维修过的位置要清洗
56.
保护层
破坏的保护层要重新保护处理
57.
脱模速度
0.1-0.2mm/sec
25.
钢网擦拭频次
每印刷3~5次
26.
锡膏在钢网上保质时间
≤2小时(湿度45-70%,温度22~28℃)
27.
锡膏在PCB上保质时间
≤2小时(湿度45-70%,温度22~28℃)
28.
印刷锡膏厚度检查
目测印刷锡膏厚度均匀
29.
印刷锡膏完整性检查
目测印刷锡膏没有缺角,漏刷等
判定
36.
炉温曲线设定
根据LED和锡膏特性设定
37.
最高焊接温度
230℃(需根据项目确定)
38.
焊接区时间
60-75sec
39.
冷却速度
4~6℃/ sec
40.
SMT过程审核检查表

100
灯光亮度
灯管不能正常发光 有无昏暗灯管?
对作业员检验技能有无定期有效的考核方式,有
101
检验员技能
检验员有上岗证
无有效证据?
印刷 102 09 效果 103
表面清洁,无任何异物残
清洗频率为多少,如何清洗,清洗效果有无确
96
钢网清洁度
留,包括溶液、
认,有无有效证据?
网孔通畅清洁
97
PCB数量
有详细印刷记录
询问现场管理员如何跟踪,跟踪频率为多少?当 前工单已经完成数量是?
审核记录
过程审核检查表(SMT)
过程 编号
过程
序 号
生产 设备
特性Leabharlann 产品过程特性标准审核问题
站位方向
作业员是否清楚匹配方法?抽查相应站位对应物 与程序设定的方向一致
料式否与站位表一致?
1、作业员是否有这些文件?
核对、与站位表/BOM/ECN一 它们之间如何匹配/核对,以保证其正确性?
致
2、物料规格与文件之间如何匹配/核对,以保证
所用物料规格无误?
核对、与站位表/BOM/ECN一 作业员是否有这些文件?物料数量与文件之间如
最大包装完好
是否每批点检、有无有效证据?
潮敏标签指示值≤20%
损坏包装的IC的指示值是否超过20%? 若超过,是否对其暴露的湿度和时间进行监控? 以保证MSD有效。
核对、与送货单一致 送货单是否正确、有无已经核对的有效证据?
核对、与送货单一致 送货单是否正确、有无已经核对的有效证据?
核对报检单与送货单一致 报检单是否正确、有无已经核对的有效证据?
4.5~6.5kg
点检频率为多少,有无点检、记录?
SMT检查表

问题号提问证据2.3是否通知了影响质量的人员有关不符合质量要求对客户造成的影响的后果?3.1组织是否为所有负责过程操作的人员准备了文件化的作业指导书?3.2这些指导书是否在工作现场易于得到?3.3这些指导书是否来源于质量计划、控制计划和产品实现过程?4.1无论何时作了设定,是否都进行了作业设定验证?4.2作业设定人员是否易于得到作业指导书?4.3适用时,供应商是否使用统计方法进行作业设定验证?5.1组织是否标识关键设备,为机器/设备的维护提供适当的资源,并建立有效的、有计划的全面预防性维护体系?预防性维护体系至少是否包括:4. 作业设定的验证3. 作业指导书5. 预防和预测性维护2. 培训2.1从事特殊工作的人员是否在教育、培训、技能和/或经验等方面具备相应的资格证明?2.2组织是否对对影响质量的新的或变更岗位的人员提供岗位培训,包括合同工或代理人员?SMT检查表1.文件要求书否编制了控制计划/流程图/特殊特性表(关键参数)/PFMEMA/PCBAL零件履历表1.11.2检验指导书是否得到被充分的定义,是否有定期确认其有效性、适用性。
- 计划性维护活动- 设备、工装和量具的包装和防护- 关键生产设备备件的可得性;- 文件化、评估和改进维护的目标5.3组织是否采用预测性维护方法以持续地提高其预防性系统?6.1组织是否提供资源以进行工装和量具设计、制造和验证活动?组织是否建立和实施工装管理的体系,包括:- 维护及修理设施与人员- 贮存与修复- 工装设定- 易损工具的更换计划- 工具设计的修改文件,包括工程等级变更- 工具的修改及相应的文件更改- 用以确定工装状态的标识?6.3如果这些工作中任何一项被外委,组织是否具有对工装管理活动实施跟踪的体系?8.3在有可追溯性要求时,组织是否控制和记录产品的独特标识。
9.1组织是否妥善保管在组织控制下或组织使用的顾客财产?8. 标识和可追溯性8.1组织是否在产品实现的全过程使用适当的方法标识产品?9. 顾客财产9.2组织是否对供其使用或组成产品的顾客财产,进行标识、验证、保护和防护?8.2组织是否就监控和测量要求,标识产品的状态?7. 生产计划7.1组织是否以满足客户要求为目的组织生产?6. 工装管理6.25.211.2过期产品是否用与不合格产品相似的方法加以控制?12.1组织是否确定所需采用的监控和测量,以及所需的监控和测量仪器,以提供产品对规定要求的符合性证据?为了保证有效的结果,测量仪器是否:a) 对照能溯源到国际或国家基准的测量标准,定期或在使用前进行校准和验证。
- 1、下载文档前请自行甄别文档内容的完整性,平台不提供额外的编辑、内容补充、找答案等附加服务。
- 2、"仅部分预览"的文档,不可在线预览部分如存在完整性等问题,可反馈申请退款(可完整预览的文档不适用该条件!)。
- 3、如文档侵犯您的权益,请联系客服反馈,我们会尽快为您处理(人工客服工作时间:9:00-18:30)。
问题号提问
证据2.3是否通知了影响质量的人员有关不符合质量要求对客
户造成的影响的后果?
3.1组织是否为所有负责过程操作的人员准备了文件化的作业指导书?
3.2
这些指导书是否在工作现场易于得到?3.3这些指导书是否来源于质量计划、控制计划和产品实现过程?
4.1
无论何时作了设定,是否都进行了作业设定验证?4.2
作业设定人员是否易于得到作业指导书?4.3适用时,供应商是否使用统计方法进行作业设定验证?
5.1组织是否标识关键设备,为机器/设备的维护提供适当
的资源,并建立有效的、有计划的全面预防性维护体
系?
预防性维护体系至少是否包括:
4. 作业设定的验证
3. 作业指导书
5. 预防和预测性维护
2. 培训2.1从事特殊工作的人员是否在教育、培训、技能和/或经验等方面具备相应的资格证明?
2.2
组织是否对对影响质量的新的或变更岗位的人员提供岗位培训,包括合同工或代理人员?SMT检查表
1.文件要求
书否编制了控制计划/流程图/特殊特性表(关键参
数)/PFMEMA/PCBAL零件履历表
1.11.2检验指导书是否得到被充分的定义,是否有定期确认
其有效性、适用性。
- 计划性维护活动
- 设备、工装和量具的包装和防护- 关键生产设备备件的可得性;- 文件化、评估和改进维护的目标
5.3组织是否采用预测性维护方法以持续地提高其预防性系统?
6.1组织是否提供资源以进行工装和量具设计、制造和验证活动?
组织是否建立和实施工装管理的体系,包括:
- 维护及修理设施与人员
- 贮存与修复
- 工装设定
- 易损工具的更换计划
- 工具设计的修改文件,包括工程等级变更
- 工具的修改及相应的文件更改
- 用以确定工装状态的标识?
6.3如果这些工作中任何一项被外委,组织是否具有对工装管理活动实施跟踪的体系?
8.3在有可追溯性要求时,组织是否控制和记录产品的独特标识。
9.1组织是否妥善保管在组织控制下或组织使用的顾客财产?
8. 标识和可追溯性
8.1组织是否在产品实现的全过程使用适当的方法标识产品?
9. 顾客财产
9.2组织是否对供其使用或组成产品的顾客财产,进行标识、验证、保护和防护?
8.2组织是否就监控和测量要求,标识产品的状态?
7. 生产计划
7.1组织是否以满足客户要求为目的组织生产?
6. 工装管理
6.2
5.2
11.2过期产品是否用与不合格产品相似的方法加以控制?
12.1组织是否确定所需采用的监控和测量,以及所需的监控和测量仪器,以提供产品对规定要求的符合性证据?为了保证有效的结果,测量仪器是否:
a) 对照能溯源到国际或国家基准的测量标准,定期或在使用前进行校准和验证。
b) 必要时的调整和再调整?
c) 加于标识以能确定校准状态?
d) 防止发生可能使校准失效的调整?
e) 在搬运、维护和贮存期间防止损坏或变坏?
12.3当发现仪器不符合要求时,组织是否评估和记录以前测量的有效性?
12.4组织是否对发现不合格的仪器和受影响的产品采取适当措施?
12.5
组织是否维护了校准和验证结果的记录?13. 不合格产品的控制
13.1组织是否确保不符合产品要求的产品得到标识和控制,以防止非预期的使用或交付?12. 监控和测量仪器的控制
12.2
11. 贮存和库存
11.1
组织是否按适宜的时间间隔检查库存品状况,以便发现变质情况?10.3组织对产品的保护是否应用到了外委的零部件?
10.2
对产品的防护是否包括标识、搬运、包装、贮存和保护?10. 产品防护
9.3在顾客财产丢失、损坏或不适用时,组织是否有记录
并向顾客报告的过程?
10.1
组织是否在内部过程和交付到预定地点期间,防护产品的符合性?
13.2
是否以书面程序规定处理不合格品的控制和相关职责和权限?
组织是否用以下一种或多种方式处理不合格产品:a) 采取措施消除发现的不合格?
b) 由授权人员,适当时,顾客以让步方式授权使用
、放行或接受?
c) 采取措施阻止其本来的用途和运用?
13.4不合格的性质和采取后续措施,包括获得让步的记录是否得到了维护?
13.5对不合格品改正后是否作再次验证以证实其对要求的符合性?
13.6当在交付或开始使用后发现产品不合格时,组织是否针对不合格所造成的影响或潜在影响采取适当的措
施?
14.1返工指导书(包括重新检验要求)是否易于得到,并为相关人员所使用?
15.1.1组织是否采取纠正措施消除不合格的原因,以防止再次发生?(8.5.2)
是否建立书面程序规定以下方面的要求:a) 评估不合格(包括顾客投诉)?
b) 评价确保不合格不再发生的措施的需求?c) 确定和实施所需的措施?
d) 记录所采取措施的结果?
e) 评估采取的纠正措施?
15.2.1组织是否有规定的解决问题的过程,引发发现根源确定和根除?
15.3.1组织是否在纠正措施的过程中采用防错方法?15.4 退货产品试验/分析 4.14.2.3
组织是否对从顾客制造厂、工程部门及其代理商退回的产品进行分析?15.3 防错
15.1.215.2 解决问题
15.2.2当客户规定的问题解决格式存在时,组织是否采用规定的格式?
14. 返工产品的控制
15. 改进
15.1 纠正措施
13.3
15.4.2组织是否力求退回产品的测试/分析过程的周期最短?
15.4.3组织是否保存退回产品的测试/分析记录,需要时,可提供此记录?
15.4.4为防止再发生,组织是否进行有效的分析,采取必要的纠正措施?
15.4.1组织是否对从顾客制造厂、工程部门及其代理商退回的产品进行分析?
责任者
记录备注。