快速换模改善报告
案例干货冲压行业案例分享——快速换模

案例干货冲压行业案例分享——快速换模全文总计2763字,需阅读7分钟,以下为正文:01今天给大家分享的是冲压企业案例分享之——快速换模。
快速换模一是能够直接降低换模时间,提高设备利用率;二是可以通过缩短换模时间增加换模次数而改变大批量生产模式,减少库存。
对于快速换模的详细知识以后择机再给大家分享,这里不做赘述。
下面我将从四个方面给大家分享:一、企业基本信息及行业特点;二、项目指标达成状况;三、项目推进步骤及要点;四、客户评价。
首先我们来了解一下企业的基本信息。
该企业属于冲压设备为主的、汽车配件制造企业,生产的产品底盘功能件、焊接件为主,主要客户有沃尔沃、吉利、长城、福特、广汽、日产、东风小康、比亚迪等车企。
生产主要有裁切、冲压成型、焊接装配及检查包装工序流程。
02该企业主要特点是什么呢?除了前面产线规划、自工序完结两个案例所介绍的具备几大问题外,还存在以下几个问题:1、客户多、产品型号丰富,换模时间长,不能快速切换。
为了适应客户交货需求,只能大批量生产库存来确保;2、设备、模具型号规格多样,无法快速匹配计划生产,造成设备、模具浪费。
本次给大家主要介绍一下冲压模具快速换模改善案例。
本次改善项目指标达成状况如下:换模时间从改善前的50分钟缩短至改善后的18分钟,低减62%,超过了目标低减30%一倍。
这里面特别说明一下换模时间的定义,它是上一个机型最后一个合格品下线作业停止后开始计时,直至下一个机型产品第一个合格品制造出来为止的时间周期,这里应该包括模具切换时间及调整时间,很多企业说自己的换模时间很快,了解后才知道说的更多的只是上下模具时间,而没有把调整时间算进去的,这样是不对的,因为调整时间同样是影响了产出。
接下来重点给大家介绍一下项目推进的步骤及各个步骤中的一些要点。
03首先介绍一下总体流程方法:稍微总结了一下,SMED项目推进同样遵照PDCA循环原则来推进整个项目,总共11个小步骤,同样也是由丰田经典的问题解决法八步骤演变而来的。
注塑换模改善措施
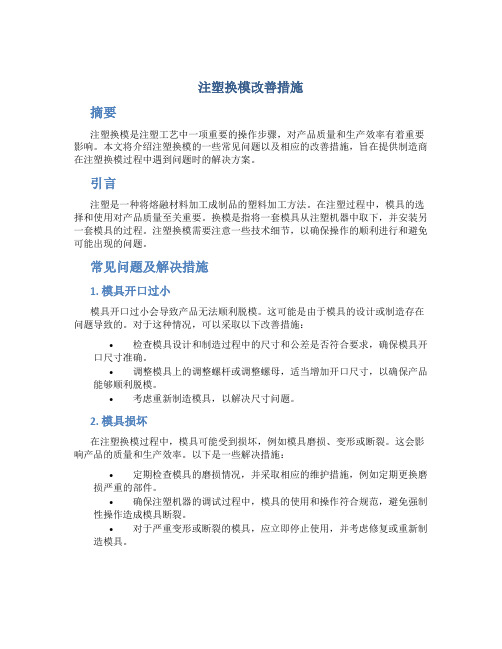
注塑换模改善措施摘要注塑换模是注塑工艺中一项重要的操作步骤,对产品质量和生产效率有着重要影响。
本文将介绍注塑换模的一些常见问题以及相应的改善措施,旨在提供制造商在注塑换模过程中遇到问题时的解决方案。
引言注塑是一种将熔融材料加工成制品的塑料加工方法。
在注塑过程中,模具的选择和使用对产品质量至关重要。
换模是指将一套模具从注塑机器中取下,并安装另一套模具的过程。
注塑换模需要注意一些技术细节,以确保操作的顺利进行和避免可能出现的问题。
常见问题及解决措施1. 模具开口过小模具开口过小会导致产品无法顺利脱模。
这可能是由于模具的设计或制造存在问题导致的。
对于这种情况,可以采取以下改善措施:•检查模具设计和制造过程中的尺寸和公差是否符合要求,确保模具开口尺寸准确。
•调整模具上的调整螺杆或调整螺母,适当增加开口尺寸,以确保产品能够顺利脱模。
•考虑重新制造模具,以解决尺寸问题。
2. 模具损坏在注塑换模过程中,模具可能受到损坏,例如模具磨损、变形或断裂。
这会影响产品的质量和生产效率。
以下是一些解决措施:•定期检查模具的磨损情况,并采取相应的维护措施,例如定期更换磨损严重的部件。
•确保注塑机器的调试过程中,模具的使用和操作符合规范,避免强制性操作造成模具断裂。
•对于严重变形或断裂的模具,应立即停止使用,并考虑修复或重新制造模具。
3. 模具温度不均匀模具温度不均匀可能导致产品的尺寸和形状偏差,从而影响产品的质量。
以下是一些改善措施:•调整注塑机器的模具温度控制系统,确保温度均匀分布。
•在模具上使用加热或冷却设备,以进一步控制温度分布。
•在注塑过程中使用合适的注塑工艺参数,例如注射速度、压力等,以控制温度均匀性。
4. 模具拆装困难模具拆装困难可能会延长换模时间,增加生产成本。
以下是一些建议:•在模具设计中考虑易于拆装的因素,例如采用快速拆装结构、使用调整螺杆等。
•确保模具表面清洁,涂上适当的润滑剂,以减少摩擦。
•培训操作人员正确使用工具和设备,避免人为损坏模具。
FMS改进案例
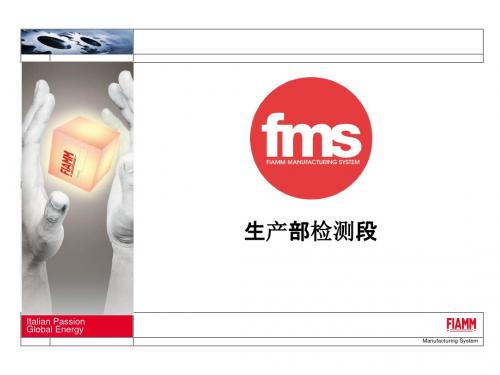
Italian Passion Global Energy
Manufacturing System
Pag 1
Group
2016年生产部检测段kainzen(FMS)项目----检测机快速换模
项目组成员: 组长:魏
组员:胡矛、朱翀鸷、李永祥、代少利
检测机快速换模改进的目的: 将检测机换模简单化、标准化,缩短换模时间、提高效率。
Pag 21
Group
2016年生产部检测段kainzen(FMS)项目----多能工培训
多能工培训计划的制定:(5、6、7月份)
班组 序号 受训人 毛翠平 培训负责人 曾德纯 培训岗位 放电测试 培训时间 5月16日~5月31日 7月1日~7月31日
1 加酸、充电
2
毛翠平
曾德纯
压盖
3
Pag 22
2016年生产部检测段kainzen(FMS)项目----多能工培训
项目组成员: 组长:魏其国
组员:毛翠平、肖义虎、刘艳磊、曾德纯、胡矛、朱翀鸷、田飞、李永祥、代少利
充电检测推行多能工的目的: 在加酸、充电、检测实施多能工培训来实现加酸、充电、检测跨班组的灵活 化生产、柔性化生产。一方面保障员工安全、健康与收入稳定;另一方面降低生 产成本、提高生产效率。
(不含改进后气缸损坏减少、电池报废减少收益)
Pag 13
Group
包装的快速改进----------------裁剪填充纸板的改进
改进前
改进后
改进前:购买回填充纸板,自行安排人员裁剪,生产时裁剪至少需要1人
改进后:直接买回需要的尺寸减少裁剪的过程,节约员工1名(推广到相同包装的FG21703电池上)
Pag 14
模具改善报告怎么写

模具改善报告怎么写模具改善报告怎么写一、引言模具改善是企业生产过程中的重要环节,它能够提高产品质量、降低成本、提高效率等多方面的效益。
因此,对于企业来说,编写一份全面详细的模具改善报告非常必要。
二、改善目标在编写模具改善报告之前,需要明确改善目标。
通常来说,企业进行模具改善的目标有以下几个方面:1. 提高产品质量:通过对模具进行改进,使得生产出来的产品更加符合规格和标准。
2. 降低成本:通过对模具进行优化或者简化设计等手段,降低生产成本。
3. 提高效率:通过优化生产流程或者采用先进的工艺技术等手段,提高生产效率和产能。
三、现状分析在明确了改善目标之后,需要对现状进行分析。
主要内容包括以下几个方面:1. 模具使用情况:需要了解当前使用的模具种类、数量、使用年限等情况。
2. 生产情况:需要了解当前生产情况包括产品类型、规格和数量等情况。
3. 故障情况:需要了解当前模具存在的故障情况包括频率、影响程度等情况。
4. 维修情况:需要了解当前模具的维修情况包括维修次数、维修费用等情况。
四、改善方案在分析了现状之后,需要提出具体的改善方案。
根据不同的改善目标,可以采取不同的改善方案。
以下是一些常见的改善方案:1. 提高产品质量:可以通过优化模具设计、提高生产工艺技术等手段来达到提高产品质量的目标。
2. 降低成本:可以通过简化模具设计、采用更加经济实惠的材料等手段来达到降低成本的目标。
3. 提高效率:可以通过优化生产流程、提高设备自动化程度等手段来达到提高效率和产能的目标。
五、实施计划在确定了改善方案之后,需要制定实施计划。
主要内容包括以下几个方面:1. 实施时间表:需要确定改善计划实施时间表,明确每个阶段所需完成的任务和时间节点。
2. 责任人员:需要明确每个阶段所需负责人员及其职责和任务。
3. 预算和资源:需要预估改善计划所需的预算和资源,并制定相应的采购计划。
六、实施效果在实施改善计划之后,需要对实施效果进行评估。
快速换产换模心得报告
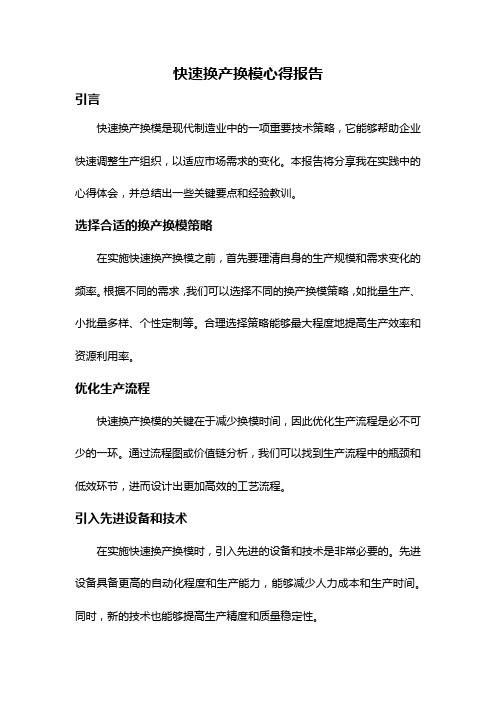
快速换产换模心得报告引言快速换产换模是现代制造业中的一项重要技术策略,它能够帮助企业快速调整生产组织,以适应市场需求的变化。
本报告将分享我在实践中的心得体会,并总结出一些关键要点和经验教训。
选择合适的换产换模策略在实施快速换产换模之前,首先要理清自身的生产规模和需求变化的频率。
根据不同的需求,我们可以选择不同的换产换模策略,如批量生产、小批量多样、个性定制等。
合理选择策略能够最大程度地提高生产效率和资源利用率。
优化生产流程快速换产换模的关键在于减少换模时间,因此优化生产流程是必不可少的一环。
通过流程图或价值链分析,我们可以找到生产流程中的瓶颈和低效环节,进而设计出更加高效的工艺流程。
引入先进设备和技术在实施快速换产换模时,引入先进的设备和技术是非常必要的。
先进设备具备更高的自动化程度和生产能力,能够减少人力成本和生产时间。
同时,新的技术也能够提高生产精度和质量稳定性。
建立高效的生产团队一个高效的生产团队是实施快速换产换模的重要保障。
团队成员需要有良好的沟通和协作能力,并且熟悉各种设备和工艺。
团队还需要定期进行培训,掌握最新的生产技术和操作方法。
实施合理的物料管理物料管理是实施快速换产换模的关键环节之一。
通过合理规划和控制库存,能够减少备料时间和废品率。
同时,建立快速供应链也能够及时满足生产需求,避免因物料不足而延误交货。
推行持续改进快速换产换模是一个持续改进的过程。
我们需要定期评估和优化整个生产过程,找出可能存在的问题和改进的空间。
通过持续改进,我们能够不断提高生产效率和质量水平。
项目案例为了充分展示快速换产换模的效果,我们在某生产企业进行了一次实施。
通过引入新设备和技术,优化生产流程,培训团队成员,并进行物料管理的优化,我们成功地将模具换模时间从原先的十几个小时缩短到仅需一个小时。
这大大提高了生产效率,节约了人力成本,提高了产品质量。
结论快速换产换模技术是现代制造业中的一项重要策略,能够帮助企业灵活应对市场需求的变化。
模具改进验证报告范文
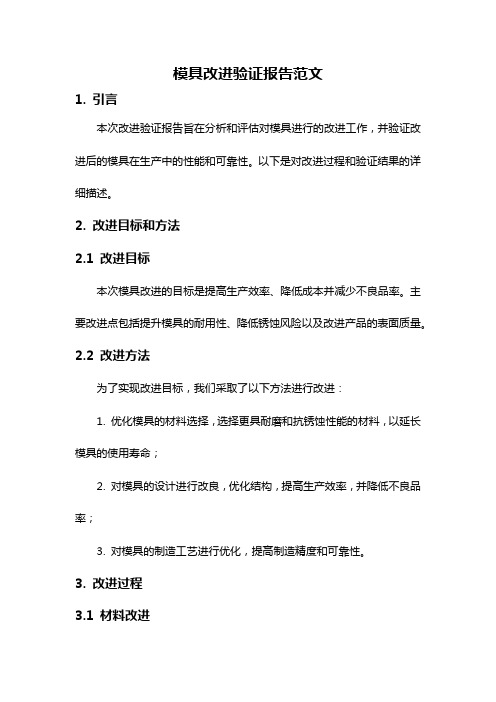
模具改进验证报告范文1. 引言本次改进验证报告旨在分析和评估对模具进行的改进工作,并验证改进后的模具在生产中的性能和可靠性。
以下是对改进过程和验证结果的详细描述。
2. 改进目标和方法2.1 改进目标本次模具改进的目标是提高生产效率、降低成本并减少不良品率。
主要改进点包括提升模具的耐用性、降低锈蚀风险以及改进产品的表面质量。
2.2 改进方法为了实现改进目标,我们采取了以下方法进行改进:1. 优化模具的材料选择,选择更具耐磨和抗锈蚀性能的材料,以延长模具的使用寿命;2. 对模具的设计进行改良,优化结构,提高生产效率,并降低不良品率;3. 对模具的制造工艺进行优化,提高制造精度和可靠性。
3. 改进过程3.1 材料改进我们采用高耐磨和抗锈蚀性能的材料作为模具的制造材料。
这种材料能够有效延长模具的使用寿命,并降低锈蚀风险。
通过对比测试,我们确认选用的材料能够满足改进目标,并提供更好的性能。
3.2 结构优化通过对模具的结构进行优化,我们设计了更合理的构造,以提高生产效率和降低不良品率。
改进后的模具具有更好的流线型设计,减少了产品的缺陷和扭曲。
此外,我们还增加了冷却系统,以降低模具温度和提高制造精度。
3.3 制造工艺优化为了提高模具的制造精度和可靠性,我们对制造工艺进行了优化。
我们使用了先进的数控机床和加工工艺,确保模具的精度和可靠性。
此外,我们还采用了全程质量控制措施,保证每个工序的质量符合标准。
4. 实验验证4.1 生产效率通过对改进后的模具进行生产实验,我们发现生产效率得到了显著提高。
优化的模具结构和制造工艺使得产品的加工速度提高了20%,生产效率提高了15%。
这对于提高生产线的产能和降低生产成本有着积极的影响。
4.2 表面质量改进后的模具能够生产出更加平整和光滑的产品表面。
与之前的模具相比,改进后的模具产品表面质量提高了30%。
该改进对于提高产品的质量和外观有着重要意义。
4.3 耐用性通过长期使用改进后的模具,我们发现其耐用性得到了有效提升。
快速换模改善建议讲解
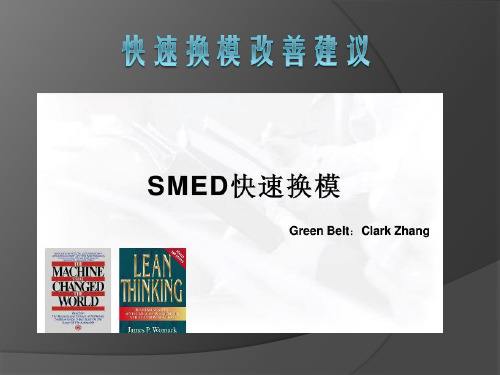
模具摆放样式及区分
左图的意思: 1.模具喷黄漆(代表的含义是不常用模具) 2.摆放样式:由模具尺寸小到大进行摆放) 3.摆放数量:每层摆放4套模具,一个模具 架摆放16套模具.每层制作一个标识。
镶 件摆放样式及区分
左图的意思: 镶件运用以前遗留的模架进行改装增加层数 1.顶部两层作为不常用镶件放置 2.底部作为常用镶件放置 3.每款镶件运用胶盒进行放置.
4.注塑部对技术员实行激励奖制. (未按周排程生产的严惩,对按周排成生产的激励)
5.制定技术员工作职责明确化. (目前很多技术员及领班都没明确自己的工作职责 还停留在以前有文员什么事都做好给到他们的想法 如:当班订单扣数·交接·员工培训等.)
四. 资 源 调 配
一·销售部
1.需要提供端盖/胶圈目前销量各排名前100的模具编号
结合目前本司换模频率的统计约平均每天换8-10套模, 但是据2013年统计换模时间平均 端盖类换模时间最短约平均在1H左右. 胶圈平均在0.5H左右(生产报表统计) 从生产现场观察到目前换模时间都是在1H上(端盖) 现场目前换模的路线是:
订单完成, 是由操作员停机 去找技术员换模
技术员处理方式
五. 改 善 前 后 对 比
模具摆放样式
VS
优势一眼可看出: 车间5S·模具清晰度·技术员找模·模具管理上 后者优势远远大于现状.
五. 改 善 前 后 对 比
镶件摆放样式
VS
优势: 车间5S·镶件清晰度·技术员找镶件上·镶件管 理·不容易出错上后者优势远远大于现状.
五. 改 善 前 后 对 比
1. 继续生产(库存)
2.停机找模 3.停机去找工具
(同时还在寻找镶 件/更换)
目前模具摆放·工具样式以及技术员思路中并未有快速换模的含义 针对以上的现状,我个人有一些建议和想法。 以下 为公司现状的一些图片.
超实用精益改善案例(某集团改善报告)

xxx精密机械有限公司
改善前生产现场
改善后生产现场
工具摆放不整齐,没有标示,经常用 工具时需要到处寻找工具浪费时间
工具摆放整齐、标示清楚明了, 员工不需要再寻找工具。
xxx精密机械有限公司
改善后标准工作表及负荷表
标准工作表
质量检验
起亚机
安全预防
+
哈斯 机
+
哈斯 机
+ +
品 检
+
半品
半品数量
3
北
接拍时间/U秒
1 下料
卧铣
15
5
1 下料
卧铣
10
3
2 飞底面
立铣
35
15
2 飞底面
立铣
30
15
3 铣长度
哈斯机
15
60
3 铣长度
哈斯机
10
64
4 铣内腔
起亚机
15
270
4 铣内腔
起亚机
10
110
5 铣外宽
哈斯机
15
80
5 铣外宽及沉孔 哈斯机
15
80
6 反面沉孔
佳铁
15
18
7 自检
60
6 自检
60
8 研磨去毛刺 振动研磨
120
周期时间/u秒
289
46302011生产线员工技能表
一级:(能培训员工,并且使他们能达到二级水平)
二级:(单独熟练操作)
三级:(能操作但不熟练)
产品
工序 下料
姓名
夏世强
飞面
46302011AG
铣长度 与粗加 工内腔
内腔精 加工
模具维修质量提升改善方案(共5篇)
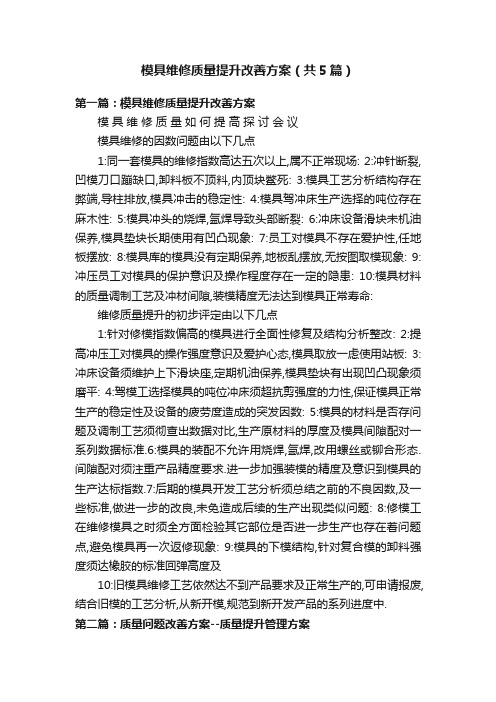
模具维修质量提升改善方案(共5篇)第一篇:模具维修质量提升改善方案模具维修质量如何提高探讨会议模具维修的因数问题由以下几点1:同一套模具的维修指数高达五次以上,属不正常现场: 2:冲针断裂,凹模刀口蹦缺口,卸料板不顶料,内顶块鳖死: 3:模具工艺分析结构存在弊端,导柱排放,模具冲击的稳定性: 4:模具驾冲床生产选择的吨位存在麻木性: 5:模具冲头的烧焊,氩焊导致头部断裂: 6:冲床设备滑块未机油保养,模具垫块长期使用有凹凸现象: 7:员工对模具不存在爱护性,任地板摆放: 8:模具库的模具没有定期保养,地板乱摆放,无按图取模现象: 9:冲压员工对模具的保护意识及操作程度存在一定的隐患: 10:模具材料的质量调制工艺及冲材间隙,装模精度无法达到模具正常寿命: 维修质量提升的初步评定由以下几点1:针对修模指数偏高的模具进行全面性修复及结构分析整改: 2:提高冲压工对模具的操作强度意识及爱护心态,模具取放一虑使用站板: 3:冲床设备须维护上下滑块座,定期机油保养,模具垫块有出现凹凸现象须磨平: 4:驾模工选择模具的吨位冲床须超抗剪强度的力性,保证模具正常生产的稳定性及设备的疲劳度造成的突发因数: 5:模具的材料是否存问题及调制工艺须彻查出数据对比,生产原材料的厚度及模具间隙配对一系列数据标准.6:模具的装配不允许用烧焊,氩焊,改用螺丝或铆合形态.间隙配对须注重产品精度要求.进一步加强装模的精度及意识到模具的生产达标指数.7:后期的模具开发工艺分析须总结之前的不良因数,及一些标准,做进一步的改良,未免造成后续的生产出现类似问题: 8:修模工在维修模具之时须全方面检验其它部位是否进一步生产也存在着问题点,避免模具再一次返修现象: 9:模具的下模结构,针对复合模的卸料强度须达橡胶的标准回弹高度及10:旧模具维修工艺依然达不到产品要求及正常生产的,可申请报废,结合旧模的工艺分析,从新开模,规范到新开发产品的系列进度中.第二篇:质量问题改善方案--质量提升管理方案××公司正式投产后产品质量提升策划文案一、背景分析××公司在7月6日至22日进行了投料试生产,在这半个多月的试生产期间,公司依靠一流的生产设备、高素质的管理人员、操作人员和××集团派出的专家团队,圆满完成了公司制定的试生产计划,并达到了预计的效果。
模具改善报告

模具改善报告报告目的:本报告旨在分析公司所使用的模具制造过程中存在的问题,并提出改善建议,以期提高模具的制造效率和品质。
报告内容:1. 模具制造过程存在的问题:1.1 生产效率低下:目前公司所使用的模具加工设备老化,无法满足高效率的加工需求,导致生产效率不高;1.2 质量控制不严:在模具制造过程中往往会出现一些质量问题,例如模具表面出现气泡、翘曲等问题;1.3 人力资源不足:公司缺乏一支熟练的模具制造团队,这将影响整个模具制造过程的效率和产能。
2. 解决方案:2.1 更新设备:公司应该优先考虑更新现有的模具加工设备,投资一些国内外先进的设备,例如:数控加工中心等,以提高生产效率;2.2 加强质量控制:公司应该建立一套完善的质量控制管理体系,及时发现并改进存在的问题,以确保模具制造的品质;2.3 培养员工:公司应该加强对相关人员的培训,特别是针对年轻员工进行岗前培训和一线操作技能培训。
经过一段时期的培训,他们将能熟练掌握模具制造技能,从而为公司创造出更高的产值。
3. 经济效益:本次模具制造改善方案需要协调多方面的工作,但是如果顺利实施,将会给公司带来可观的经济效益。
首先,提高生产效率将会增加产品数量;其次,改善模具的制造质量,将会降低后期的质量问题及维护成本;再者,增强员工技能,将会提高团队的协同作用和创造性。
综上所述,本报告所提出的模具改善方案符合公司发展和产业升级要求。
报告结论:模具是一个关键的生产因素,影响到公司的产品品质和生产效率。
当前,公司所使用的模具加工设备旧,技术落后,制造工艺流程不完善,影响模具的制造效率和制造质量。
综合分析,本报告建议公司优先更新模具加工设备,建立完善的质量控制体系,并加强员工的培训和技能提高。
以上为模具改善报告,报告内容涉及“问题分析、解决方案及经济效益等”,属于正式报告的格式。
本报告旨在客观、详实地对模具生产过程中所出现的问题进行分析,并提供可行的解决方案,以帮助企业提高生产效率和产品品质,从而达到降低成本、增加收益、促进企业可持续发展的目的。
改善实战经典(快速换模改善)
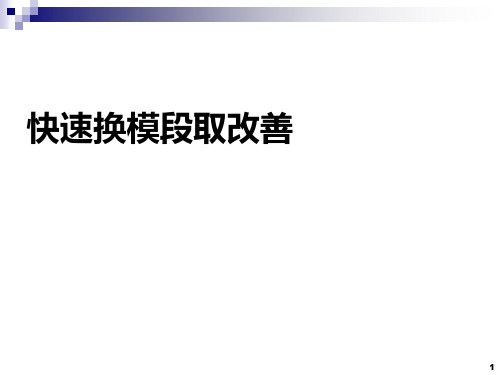
三、段取改善步骤&案例
段取改善的步骤
STEP
改善着眼点
内段取、调整、外段取 作业明确区分
内段取作业向外段取作 业移行 内段取时间短缩
內段取 內段取 內段取
总段替时间
调整 调整 调整 外段取 外段取 外段取
1
2 3
4
5
调整时间缩短
外段取时间短缩
內段取
调整
外段取
內段取
调整
外段取
一.內段取的外段取化
1.定义、目的
为了缩短內段取的时间,将內段取的作业变 为外段取作业。
2.改善事例
(1)模具预热的外段取化
将附有自动温度调节控制回路的预热控制盘,设置于单能机的后部, Heater线及温度调节用补偿导线延长至模具台车。下次生产使用模具乘放 于模具台车上,将温度上升至预备设定温度。
模具
进口 出口
换模时油路状态
2.预期目标
1)内段取时间:28Min↘5Min
2)SPH:169次/H↗450次/H 内段取时间 实 际 82%
目 标 5Min
SPH 目 标 166% 实 际 169次/H 450次/H
28Min
3.对象工程LAYOUT(现况)
OUT IN
机台07
机台08
机台09
机台10
全检 除毛边
暂置 台
擦油 检查
改善前 改善后
Block座
U型锁扣及Block
各別组付取 付
U型锁扣及Block一体化 改为滑动方式
三、调整时间的短缩、排除
1.定义、目的: 为缩短因调整作业造成生产线停止的时间,实施缩短 及排除调整时间。
2.改善事例
(1)工作台上的Center Key
冲压车间快速换模改善案例

10
Presentation's Title
Confidential
步骤三:将内部工作转换成外部工作
3)将检具调整为零 After Kaizen改善后
改善前:
测量上盖尺寸的检具未清零
改善后:操作工需在模修人员换 完磨具前将检具调整为零
11
Presentation's Title
Confidential
改善后:在料道上画线,操作工再调 整时只需将卷料的一边与线对齐,再 将两边限位拧紧即可
15
Presentation's Title
Confidential
Result 结果:60分钟降至45分钟
下图是换型过程5个阶段改善前后的时间对比 分钟
0 10 20 30 40 50 60
改善前 改善后
换卷料 时间
Value %
Results of GK改善收益
Value %
生产能力 Production Capacity (百万 台/年 Mi unidades / year)
多生产 83142台/年 60 66.48 45 67.42 25%
换型时间 Change over Time (m) OEE (%)
改善后:制作工具盒,存放换型用 的工具,字头,冲头,调整垫。换 型时只需将工具盒放到冲床上即可
13
Confidential
Presentation's Title
步骤四:减少内部工作
Before Kaizen改善前 After Kaizen改善后
换型工具
调整工具
改善前:所有换型用的工具,模具都 放在车上面,比较凌乱也不容易找。 调整所需工具有时带不齐全,需回维 修站取
模具更换总结报告范文(3篇)

第1篇一、前言模具作为现代制造业中不可或缺的重要工具,其性能直接影响着产品的质量和生产效率。
随着生产需求的不断变化和产品更新换代,模具的更换工作变得尤为重要。
本报告旨在总结我司模具更换过程中的经验与教训,为今后模具更换工作提供参考。
二、模具更换背景我司主要从事精密模具的研发、生产和销售,产品广泛应用于电子、汽车、家电等行业。
近年来,随着市场竞争的加剧,客户对产品性能和外观的要求越来越高,原有模具已无法满足生产需求。
为提升产品竞争力,公司决定对部分模具进行更换。
三、模具更换过程1. 需求分析在模具更换前,我们对现有模具进行了全面分析,包括模具结构、性能、寿命等方面。
同时,与客户沟通,了解其对产品性能和外观的具体要求,为模具更换提供依据。
2. 模具选型根据需求分析结果,我们选择了具有先进技术和较高性能的模具。
在选型过程中,充分考虑了以下因素:- 模具结构:确保模具结构合理,满足产品生产需求。
- 模具材料:选择耐磨、耐腐蚀、易于加工的材料。
- 模具性能:确保模具具有良好的精度、刚度和稳定性。
- 模具寿命:提高模具使用寿命,降低生产成本。
3. 模具加工模具加工是模具更换过程中的关键环节。
我们严格按照模具设计图纸和技术要求进行加工,确保模具质量。
- 加工设备:采用先进的加工设备,如CNC加工中心、线切割机等。
- 加工工艺:根据模具材料、结构特点等因素,选择合适的加工工艺。
- 质量控制:严格控制加工过程中的各项指标,确保模具精度。
4. 模具装配模具装配是模具更换的最后一道工序。
我们严格按照装配工艺进行装配,确保模具各部件的配合精度。
- 装配工具:使用专用工具进行装配,避免损坏模具部件。
- 装配顺序:按照装配工艺要求进行装配,确保装配质量。
- 装配质量:对装配后的模具进行检测,确保装配精度。
5. 试模与调试模具更换完成后,进行试模和调试,验证模具性能是否符合要求。
- 试模:在模拟实际生产条件下进行试模,检验模具的加工精度、稳定性等性能。
基于快速换模的文字印刷机设备效率改善
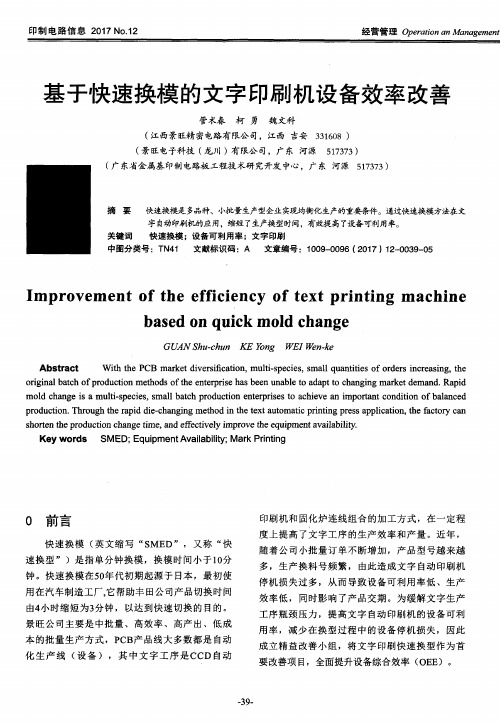
形 ,并分析存在的问题 。现场观察法来源于 “ 大野
耐…” ( 丰 田生产方 式 的创始 人 )的 “ 站 在 圆 圈 里 ”练 习 , 这 是 “ 现地 现 物 ”理 念 的 一 部 分 , 是 强 调 现 场 观 察 与 了解 ,站 在 圆 圈中 好 几 小 时或 更 长时
问有助于识别生产 中的浪 费问题 。 从表1 、表2 的时 间观 察表 中识别 出的生产 浪 费包括 : ( 1 )在3 h 内待料时间达 ̄ 1 4 4 mi n ,待料
备 好 ;在换 型前 可 以提 前准 备调 试板 ,如 调试板 提前 贴好膜 。
表4 改善后换型过 程分 析表
2 3
网版 质 量检 查 、工具 准备 调试 板 贴好膜
置商 疆 I 蹄 Z箭氍 雪I 麓 量词 稿譬 嚣 | .
3Hale Waihona Puke 0 9 0 内部时 间转 换 为外 部时 间 ,减 少设 备停
2 快 速换 模 在 文 字 自动 印刷 机 的 应 用
推 行快速换模 ( 快 速 换 型 )的 目的 就 是 将 浪 费 降低 到最 少 ,减少换 型过 程 中的设 备停机 时
表1 1 0 月2 6 日时 间 观 察 表 ( 观 察设 备 )
l 号 自动 印刷 机 时 间 设 备状况 操作员工作情况
工厂改善报告汇总
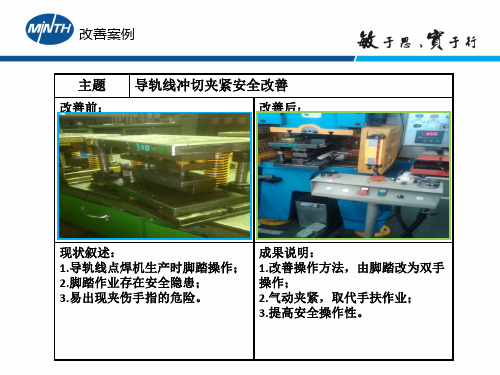
我们的期望(需求)
工装方面:
1.弯曲模锯切类在后期开发时考虑安全及防尘,目前所有车顶类弯曲锯切 铁屑四处飞扬,给环境及设备造成很大的污染,5S清理困难; 2.水切类产品受断面变化的影响入模困难,适应变化范围较小,效率低下; 3.水切类产品缺口、LIP边、骨架导向精度不足、冲切尺寸不稳定,调整困 难; 4.亮面产品定位点分布不合理,经常出现顶伤、凹凸等品质不良;亮面水 切冲切时产品入模导向为切刀,在切断时产品会有上下活动导致端部顶 伤、凹凸。 5.水切类冲切模具,冲切工序间无防呆、防错、防漏工序等互检功能,经 常性出现漏工序等不良流出; 6.弯曲模具类游离胶生产中单个安装,作业安全性不足、效率低下、定位 不准,希望消除此类操作,能够做到产品直接放上去就可以启动,无需 手扶; 7.导轨类点焊治具,配件定位不准,需要手扶,存在严重的安全隐患。
现状叙述: 1.原生产线没有过滤装置; 2.冷却水质量较差,影响产 品品质; 3.管路易堵塞,故障较多。
成果说明: 1.改善后水质清澈见底; 2.有效地保证了产品冷却效果; 3.并增加了漏水报警提示,有效控制漏水现象。 4.可横向推广至其他线别
改善案例
主题
改善前:
560行李架长度防呆检测改善
改善后:
改善案例-(能源室储气罐、冷冻式干燥机排水自动化)
改善前 无 改善后
Diagram
改善前问题点
由于空气湿度较大,空气机系统设备运 时形成水份过多,在过滤器中及储气罐 内积储,平均两至三小时放水一次也难 保证空气水分滤净,从而保证不了涂装 喷漆用气。
改善后优点
改善后: 从节省人员及劳动强度方面考虑,保证了涂装喷漆用气质量, Add Your Text 棉的造成喷漆质量缺陷。
改善后优点