低成本通用飞机复合材料设计制造一体化技术_马瑛剑
航空工业复合材料研发与应用方案
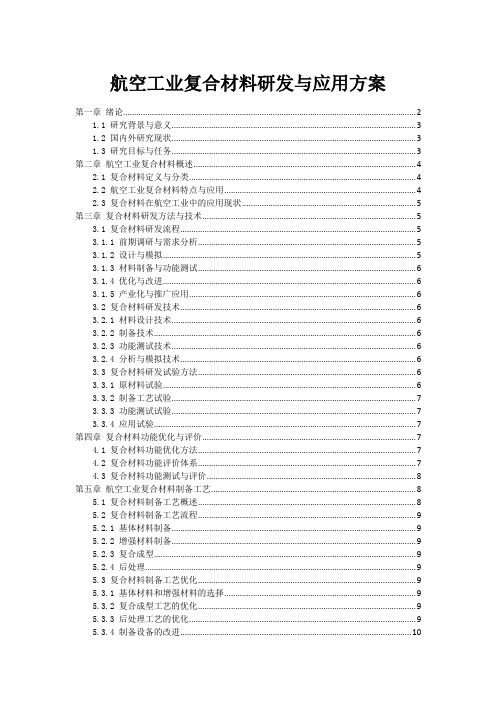
航空工业复合材料研发与应用方案第一章绪论 (2)1.1 研究背景与意义 (3)1.2 国内外研究现状 (3)1.3 研究目标与任务 (3)第二章航空工业复合材料概述 (4)2.1 复合材料定义与分类 (4)2.2 航空工业复合材料特点与应用 (4)2.3 复合材料在航空工业中的应用现状 (5)第三章复合材料研发方法与技术 (5)3.1 复合材料研发流程 (5)3.1.1 前期调研与需求分析 (5)3.1.2 设计与模拟 (5)3.1.3 材料制备与功能测试 (6)3.1.4 优化与改进 (6)3.1.5 产业化与推广应用 (6)3.2 复合材料研发技术 (6)3.2.1 材料设计技术 (6)3.2.2 制备技术 (6)3.2.3 功能测试技术 (6)3.2.4 分析与模拟技术 (6)3.3 复合材料研发试验方法 (6)3.3.1 原材料试验 (6)3.3.2 制备工艺试验 (7)3.3.3 功能测试试验 (7)3.3.4 应用试验 (7)第四章复合材料功能优化与评价 (7)4.1 复合材料功能优化方法 (7)4.2 复合材料功能评价体系 (7)4.3 复合材料功能测试与评价 (8)第五章航空工业复合材料制备工艺 (8)5.1 复合材料制备工艺概述 (8)5.2 复合材料制备工艺流程 (9)5.2.1 基体材料制备 (9)5.2.2 增强材料制备 (9)5.2.3 复合成型 (9)5.2.4 后处理 (9)5.3 复合材料制备工艺优化 (9)5.3.1 基体材料和增强材料的选择 (9)5.3.2 复合成型工艺的优化 (9)5.3.3 后处理工艺的优化 (9)5.3.4 制备设备的改进 (10)5.3.5 质量控制与监测 (10)第六章航空工业复合材料结构设计 (10)6.1 结构设计原则与方法 (10)6.1.1 结构设计原则 (10)6.1.2 结构设计方法 (10)6.2 复合材料结构设计流程 (10)6.3 复合材料结构设计案例分析 (11)第七章复合材料在航空器部件的应用 (12)7.1 复合材料在航空器结构部件的应用 (12)7.1.1 概述 (12)7.1.2 应用实例 (12)7.2 复合材料在航空器功能部件的应用 (12)7.2.1 概述 (12)7.2.2 应用实例 (12)7.3 复合材料在航空器复合材料部件的应用 (12)7.3.1 概述 (12)7.3.2 应用实例 (13)第八章航空工业复合材料制造与质量控制 (13)8.1 复合材料制造流程 (13)8.1.1 原材料准备 (13)8.1.2 预制件制备 (13)8.1.3 预制件铺层 (13)8.1.4 固化成型 (13)8.1.5 后处理 (14)8.1.6 检验 (14)8.2 复合材料制造设备与工艺 (14)8.2.1 制造设备 (14)8.2.2 制造工艺 (14)8.3 复合材料质量控制与检测 (14)8.3.1 质量控制 (14)8.3.2 检测方法 (14)第九章航空工业复合材料维修与养护 (15)9.1 复合材料维修方法 (15)9.2 复合材料养护技术 (15)9.3 复合材料维修与养护案例分析 (16)第十章发展趋势与展望 (16)10.1 航空工业复合材料发展趋势 (16)10.2 面临的挑战与机遇 (17)10.3 未来发展方向与展望 (17)第一章绪论1.1 研究背景与意义我国航空工业的快速发展,复合材料在航空器结构中的应用日益广泛。
复合材料部件设计制造一体化研究_马瑛剑
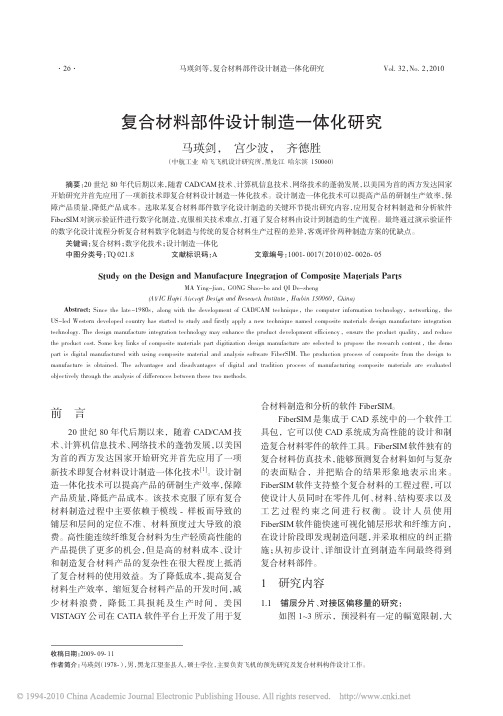
前言20世纪80年代后期以来,随着CAD/CAM技术、计算机信息技术、网络技术的蓬勃发展,以美国为首的西方发达国家开始研究并首先应用了一项新技术即复合材料设计制造一体化技术[1]。
设计制造一体化技术可以提高产品的研制生产效率,保障产品质量,降低产品成本。
该技术克服了原有复合材料制造过程中主要依赖于模线-样板而导致的铺层和层间的定位不准、材料预度过大导致的浪费。
高性能连续纤维复合材料为生产轻质高性能的产品提供了更多的机会,但是高的材料成本、设计和制造复合材料产品的复杂性在很大程度上抵消了复合材料的使用效益。
为了降低成本,提高复合材料生产效率,缩短复合材料产品的开发时间,减少材料浪费,降低工具损耗及生产时间,美国VISTAGY公司在CATIA软件平台上开发了用于复合材料制造和分析的软件FiberSIM。
FiberSIM是集成于CAD系统中的一个软件工具包,它可以使CAD系统成为高性能的设计和制造复合材料零件的软件工具。
FiberSIM软件独有的复合材料仿真技术,能够预测复合材料如何与复杂的表面贴合,并把贴合的结果形象地表示出来。
FiberSIM软件支持整个复合材料的工程过程,可以使设计人员同时在零件几何、材料、结构要求以及工艺过程约束之间进行权衡。
设计人员使用FiberSIM软件能快速可视化铺层形状和纤维方向,在设计阶段即发现制造问题,并采取相应的纠正措施;从初步设计、详细设计直到制造车间最终得到复合材料部件。
1研究内容1.1铺层分片、对接区偏移量的研究:如图1~3所示,预浸料有一定的幅宽限制,大复合材料部件设计制造一体化研究马瑛剑,宫少波,齐德胜(中航工业哈飞飞机设计研究所,黑龙江哈尔滨150060)摘要:20世纪80年代后期以来,随着CAD/CAM技术、计算机信息技术、网络技术的蓬勃发展,以美国为首的西方发达国家开始研究并首先应用了一项新技术即复合材料设计制造一体化技术。
设计制造一体化技术可以提高产品的研制生产效率,保障产品质量,降低产品成本。
复合材料结构与功能及在无人机领域的应用
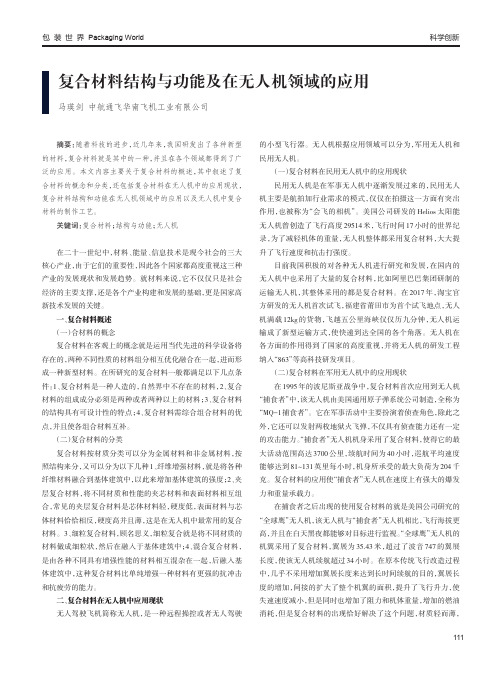
包装世界Packaging World科学创新复合材料结构与功能及在无人机领域的应用马瑛剑中航通飞华南飞机工业有限公司摘要:随着科技的进步,近几年来,我国研发出了各种新型的材料,复合材料就是其中的一种,并且在各个领域都得到了广泛的应用。
本文内容主要关于复合材料的概述,其中叙述了复合材料的概念和分类,还包括复合材料在无人机中的应用现状,复合材料结构和功能在无人机领域中的应用以及无人机中复合材料的制作工艺。
关键词:复合材料;结构与功能;无人机在二十一世纪中,材料、能量、信息技术是现今社会的三大核心产业,由于它们的重要性,因此各个国家都高度重视这三种产业的发展现状和发展趋势。
就材料来说,它不仅仅只是社会经济的主要支撑,还是各个产业构建和发展的基础,更是国家高新技术发展的关键。
一、复合材料概述(一)合材料的概念复合材料在客观上的概念就是运用当代先进的科学设备将存在的,两种不同性质的材料组分相互优化融合在一起,进而形成一种新型材料。
在所研究的复合材料一般都满足以下几点条件:1、复合材料是一种人造的,自然界中不存在的材料,2、复合材料的组成成分必须是两种或者两种以上的材料;3、复合材料的结构具有可设计性的特点;4、复合材料需综合组合材料的优点,并且使各组合材料互补。
(二)复合材料的分类复合材料按材质分类可以分为金属材料和非金属材料,按照结构来分,又可以分为以下几种1、纤维增强材料,就是将各种纤维材料融合到基体建筑中,以此来增加基体建筑的强度;2、夹层复合材料,将不同材质和性能的夹芯材料和表面材料相互组合,常见的夹层复合材料是芯体材料轻,硬度低,表面材料与芯体材料恰恰相反,硬度高并且薄,这是在无人机中最常用的复合材料。
3、细粒复合材料,顾名思义,细粒复合就是将不同材质的材料做成细粒状,然后在融入于基体建筑中;4、混合复合材料,是由各种不同具有增强性能的材料相互混杂在一起,后融入基体建筑中,这种复合材料比单纯增强一种材料有更强的抗冲击和抗疲劳的能力。
通用飞机的低成本研究
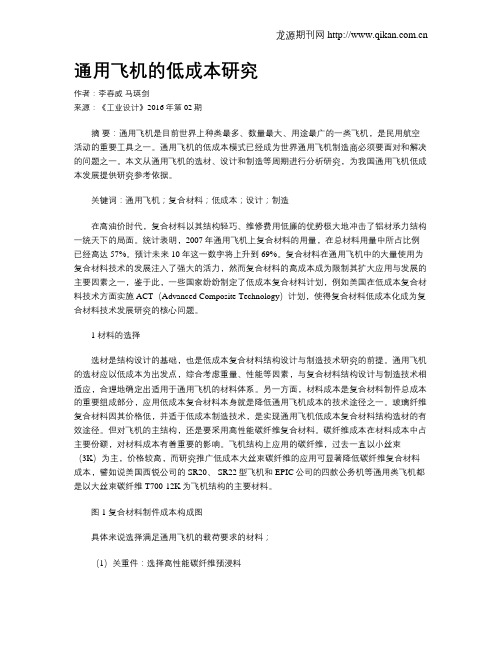
通用飞机的低成本研究作者:李春威马瑛剑来源:《工业设计》2016年第02期摘要:通用飞机是目前世界上种类最多、数量最大、用途最广的一类飞机,是民用航空活动的重要工具之一。
通用飞机的低成本模式已经成为世界通用飞机制造商必须要面对和解决的问题之一。
本文从通用飞机的选材、设计和制造等周期进行分析研究,为我国通用飞机低成本发展提供研究参考依据。
关键词:通用飞机;复合材料;低成本;设计;制造在高油价时代,复合材料以其结构轻巧、维修费用低廉的优势极大地冲击了铝材承力结构一统天下的局面。
统计表明,2007年通用飞机上复合材料的用量,在总材料用量中所占比例已经高达57%。
预计未来10年这一数字将上升到69%。
复合材料在通用飞机中的大量使用为复合材料技术的发展注入了强大的活力,然而复合材料的高成本成为限制其扩大应用与发展的主要因素之一,鉴于此,一些国家纷纷制定了低成本复合材料计划,例如美国在低成本复合材料技术方面实施ACT(Advanced Composite Technology)计划,使得复合材料低成本化成为复合材料技术发展研究的核心问题。
1 材料的选择选材是结构设计的基础,也是低成本复合材料结构设计与制造技术研究的前提。
通用飞机的选材应以低成本为出发点,综合考虑重量、性能等因素,与复合材料结构设计与制造技术相适应,合理地确定出适用于通用飞机的材料体系。
另一方面,材料成本是复合材料制件总成本的重要组成部分,应用低成本复合材料本身就是降低通用飞机成本的技术途径之一。
玻璃纤维复合材料因其价格低,并适于低成本制造技术,是实现通用飞机低成本复合材料结构选材的有效途径。
但对飞机的主结构,还是要采用高性能碳纤维复合材料。
碳纤维成本在材料成本中占主要份额,对材料成本有着重要的影响。
飞机结构上应用的碳纤维,过去一直以小丝束(3K)为主,价格较高,而研究推广低成本大丝束碳纤维的应用可显著降低碳纤维复合材料成本,譬如说美国西锐公司的SR20、 SR22型飞机和EPIC公司的四款公务机等通用类飞机都是以大丝束碳纤维T700-12K为飞机结构的主要材料。
通用飞机复合材料低成本设计及工艺概述

匹配铺贴模具与成型零件的热膨胀系数。零件成型多为中温固 化,因此复合材料工装的树脂体系在低成本制造工程中尤为关 键,一般选择低温固化树脂,脱模后进行后固化使其达到做要 求Tg值,树脂基体的固化工艺要求关系到复合材料工装过渡模 的材料选择。低温固化树脂可降低对过渡模的要求,从而降低 成本,一般较低成本过渡模材料为泡沫、代木等,密度不小于 0.8g/mm³,耐温50℃左右。工装的真空灌注工艺成型相对于预 浸料成型成本较低且技术较为成熟,研制阶段工装可采用真空 灌注工艺可降低设计更改造成的成本风险,但模具刚性相对预 浸料成型工艺较低,批产阶段建议使用预浸料成型工艺制造复 合材料工装。
材料的选择不仅要考虑其本身成本,更要综合考虑后续相 应制造工艺成本、检测工艺成本等。在这方面,航空级玻璃纤 维相对碳纤维的优势尤为突出,尤其是在后续检测成本方面。 在满足载荷要求的情况下,飞机的次承力件和非承力件可采用 玻璃纤维预浸料作为主要材料,主要关重件可选用碳纤维预浸 料作为主要材料。
3 模具 模具成本在飞机研发总费用中占比15%至30%,降低模具
2019/7/16 17:33:43
1 概述 复合材料飞机低成本模式需要从研制阶段开始保证。飞机
的研制过程是一个漫长的过程,每一架优秀飞机型号的诞生都 是在研制阶段反复修改后确定下来的。低成本的研究就要从初 始的材料、模具、设备、工艺等各方面进行长远考虑。
2 材料 材料选择是飞机结构设计的基础,也是飞机制造成本的重
要组成部分。按CCAR-23部适航标准审定的正常类通用飞机一 般重量在5700kg以下,常规航空级复合材料可满足其设计载荷 要求,因此降低复合材料本身成本尤为重要[1]。
通用飞机的低成本研究_李春威
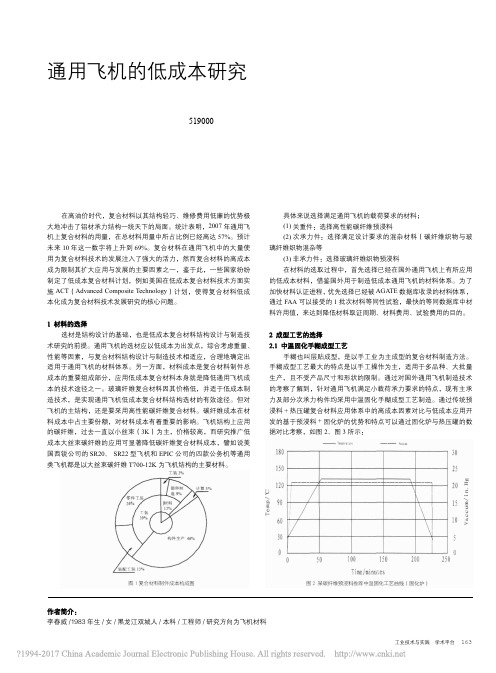
38.4×350=1.35
总计节约( 万元 /架)
5.25
6 制造模具的选择 模具的选择对控制通用飞机的成本也起到至关重要的作用,对于
我们通用飞机而言高产量低成本始终应该放在最重要的位置(以原型 机年产 150 架份考察): 6.1 金属工装
金属工装虽然成本投入较低,但一般均使用在小尺寸、外形简单 的复合材料零件上面,对于大曲面、大尺寸零件来说,热膨胀系数、 搬运操作困难都是难以克服的缺点。 6.2 复材工装
2 成型工艺的选择 2.1 中温固化手糊成型工艺
手糊也叫层贴成型,是以手工业为主成型的复合材料制造方法。 手糊成型工艺最大的特点是以手工操作为主,适用于多品种、大批量 生产,且不受产品尺寸和形状的限制。通过对国外通用飞机制造技术 的考察了解到,针对通用飞机满足小载荷承力要求的特点,现有主承 力及部分次承力构件均采用中温固化手糊成型工艺制造。通过传统预 浸料 + 热压罐复合材料应用体系中的高成本因素对比与低成本应用开 发的基于预浸料 + 固化炉的优势和特点可以通过固化炉与热压罐的数 据对比考察,如图 2、图 3 所示:
2.3 自动铺放技术 自动铺放技术包括自动铺带和自动铺丝两部分。目前,该技术在
速度和准确度上有了很大改进,以自动铺放技术为代表的自动化成型
技术能够降低生产成本,提高复合材料构件质量。但是由于应用规模
的限制,全自动化生产往往会造成有限规模的复合材料成本较高。因
此,一定程度上的自动化生产,仍是复合材料低成本制造比较经济的
备注
热压罐
2
1
固化炉
0.8
0.1
2.2 RTM 工艺
该技术已获得了较为广泛的应用,是先进复合材料低成本制造技
术的主要发展方向之一。该工艺避免了预浸料的生产工序,能够适应
飞机复合材料应用及制造技术探析张诗雨张楠

飞机复合材料应用及制造技术探析张诗雨张楠发布时间:2023-06-03T09:29:59.504Z 来源:《中国科技信息》2023年6期作者:张诗雨张楠[导读] 由于具有高比强度,高比刚度,结构强度,抗疲劳强度和耐腐蚀性等优点,许多零表面和组件的连续复合材料被使用,组件,区域和设备由复合材料制成,重量也增加了。
中航西安飞机工业集团股份有限公司陕西西安 710089摘要:由于具有高比强度,高比刚度,结构强度,抗疲劳强度和耐腐蚀性等优点,许多零表面和组件的连续复合材料被使用,组件,区域和设备由复合材料制成,重量也增加了。
在飞机设计中使用先进的复合材料可以减轻20至30%的重量,这是其他先进技术难以实现的。
复合材料转化为铝,钢和钛。
随着航空四大材料之一的飞速发展,所占的比重不断增加,也广泛应用于飞机,与两家航空巨头波音空客的激烈竞争表明,没有复合材料的飞机在选择飞机材料和技术方面无法竞争和发展。
由于生产和制造技术的限制,复合材料的使用受到限制,飞机制造必须在未来对复合材料进行调整和优化,解决技术问题并促进其应用。
关键词:复合材料;现代大飞机;制造技术随着低成本数字复合材料的开发和应用,自动铺放技术已应用于大型机翼板、梁、机身部件。
自动铺放技术性能好、高效率、稳定可靠质量,能有效提高结构的许用设计值,结构的重量减轻。
一、复合材料在现代大飞机中的应用1.飞机工业中复合材料应用。
可以有效地整合各种资源和材料,减少飞机制造中各种部件的数量,减少组件连接安装过程中因质量问题安全事故引发,金属材料是飞机设计的重要组成部分。
飞机的生产质量是结构强度和稳定性直接影响,在飞机生产中非金属材料发挥着越来越重要的作用,金属和非金属材料是复合材料结合了其优良性能,保证了飞机的质量和生产成本2.适用于飞机的主承力结构,是保证飞机主承力结构质量和基础设施稳定的主要支撑结构。
飞机设计中复合材料应用最初舱门、整流罩等次承力结构上。
随着研发水平的提高,复合材料已应用于各类材料,并逐步优化改进,综合性能得到提高,取得了显着成效。
先进复合材料装配工艺技术的应用探究
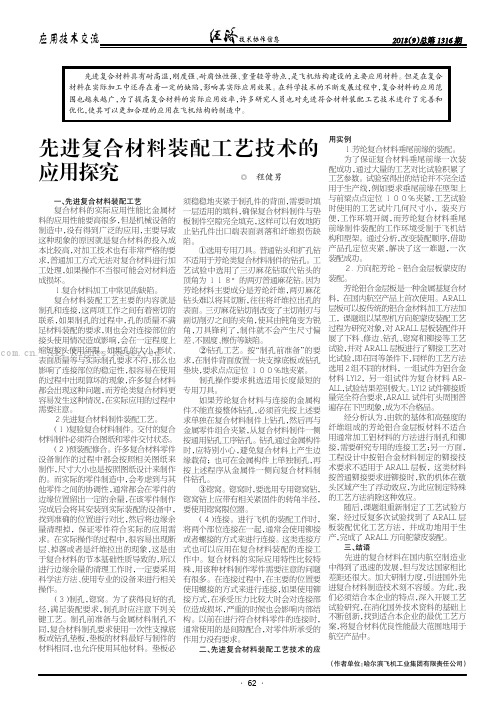
一、先进复合材料装配工艺复合材料的实际应用性能比金属材料的应用性能要高很多,但是机械设备的制造中,没有得到广泛的应用,主要导致这种现象的原因就是复合材料的投入成本比较高,对加工技术也有非常严格的要求,普通加工方式无法对复合材料进行加工处理,如果操作不当很可能会对材料造成损坏。
1.复合材料加工中常见的缺陷。
复合材料装配工艺主要的内容就是制孔和连接,这两项工作之间有着密切的联系,如果制孔的过程中,孔的质量不满足材料装配的要求,则也会对连接部位的接头使用情况造成影响,会在一定程度上缩短接头使用年限。
如果孔的大小,形状、表面质量等与实际制孔要求不符,那么也影响了连接部位的稳定性,很容易在使用的过程中出现算坏的现象,许多复合材料都会出现这种问题,而芳纶类复合材料更容易发生这种情况,在实际应用的过程中需要注意。
2.先进复合材料制件装配工艺。
(1)复验复合材料制件。
交付的复合材料制件必须符合图纸和零件交付状态。
(2)预装配修合。
许多复合材料零件设备制作的过程中都会按照相关图纸来制作,尺寸大小也是按照图纸设计来制作的。
而实际的零件制造中,会考虑到与其他零件之间的协调性,通常都会在零件的边缘位置留出一定的余量,在该零件制作完成后会将其安装到实际装配的设备中,找到准确的位置进行对比,然后将边缘余量清理掉,保证零件符合实际的应用需求。
在实际操作的过程中,很容易出现断层、掉落或者是纤维拉出的现象,这是由于复合材料的节本基础性质导致的,所以进行边缘余量的清理工作时,一定要采用科学法方法、使用专业的设备来进行相关操作。
(3)制孔,锪窝。
为了获得良好的孔径,满足装配要求,制孔时应注意下列关键工艺。
制孔前准备与金属材料制孔不同,复合材料制孔要求使用一次性支撑底板或钻孔垫板,垫板的材料最好与制件的材料相同,也允许使用其他材料。
垫板必须稳稳地夹紧于制孔件的背面,需要时填一层适用的填料,确保复合材料制件与垫板制件空隙完全填充,这样可以有效地防止钻孔件出口端表面剥落和纤维损伤缺陷。
大飞机复合材料应用及制造技术探析
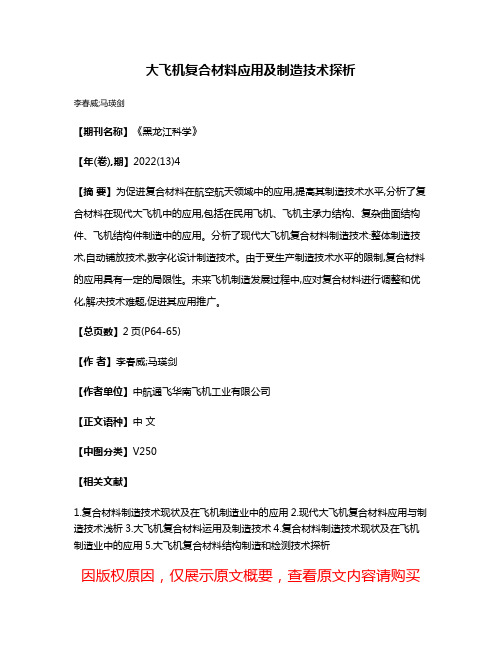
大飞机复合材料应用及制造技术探析
李春威;马瑛剑
【期刊名称】《黑龙江科学》
【年(卷),期】2022(13)4
【摘要】为促进复合材料在航空航天领域中的应用,提高其制造技术水平,分析了复合材料在现代大飞机中的应用,包括在民用飞机、飞机主承力结构、复杂曲面结构件、飞机结构件制造中的应用。
分析了现代大飞机复合材料制造技术:整体制造技术,自动铺放技术,数字化设计制造技术。
由于受生产制造技术水平的限制,复合材料的应用具有一定的局限性。
未来飞机制造发展过程中,应对复合材料进行调整和优化,解决技术难题,促进其应用推广。
【总页数】2页(P64-65)
【作者】李春威;马瑛剑
【作者单位】中航通飞华南飞机工业有限公司
【正文语种】中文
【中图分类】V250
【相关文献】
1.复合材料制造技术现状及在飞机制造业中的应用
2.现代大飞机复合材料应用与制造技术浅析
3.大飞机复合材料运用及制造技术
4.复合材料制造技术现状及在飞机制造业中的应用
5.大飞机复合材料结构制造和检测技术探析
因版权原因,仅展示原文概要,查看原文内容请购买。
复合材料低成本制造工艺与航空应用

10% 修剪
铺贴 52%
件制造工时的一半
17%
封装固化
3%
2020-11-17
12
复合材料成型技术的发展
航空复合材料 结构
主承力 复合材料结构
次承力 复合材料结构
热压罐成型工艺为主,正 在发展非热压罐成型工艺
逐步开始应用 非热压罐成型工艺
VARI液体 真空压力成型工艺
VBO预浸料 真空压力成型工艺
闭模
主要优点:制造高纤维体积含量的大型复杂构型的零件, 保持较高的结构设计效率。
17
OOA技术2-VARI
真空辅助树脂渗透成型(Vacuum Assisted Resin Infusion)技术 将按照结构和性能要求制备好的纤维预成型体放置在模具上,在一个
真空作用下使液态树脂在预成型体内流动并浸润纤维,再经升温固化、 冷却脱模得到能够承载的复合材料构件。
聚酰亚胺
AC729RTM
10
9
8
HT-350RTM
PETI330
7
6
5
4
3
2
1
0
240
260
280
300
320
340
360
Temperature/℃
注射温度~280℃
固化温度120℃
固化温度180℃
固化温度200℃ 固化温度350℃
Tg = 120℃ 服役温度~70℃
Tg = 210℃ 服役温度~130℃
21
国外OOA技术与应用
东丽
• 2007年制造技术创新计划启 动,非热压罐制造是5个核心 领域之一。建立开发OOA体系 目标,提供可达到热压罐固 化质量水平材料
211083992_复合材料尾翼壁板典型特征参数对承载效率的影响研究
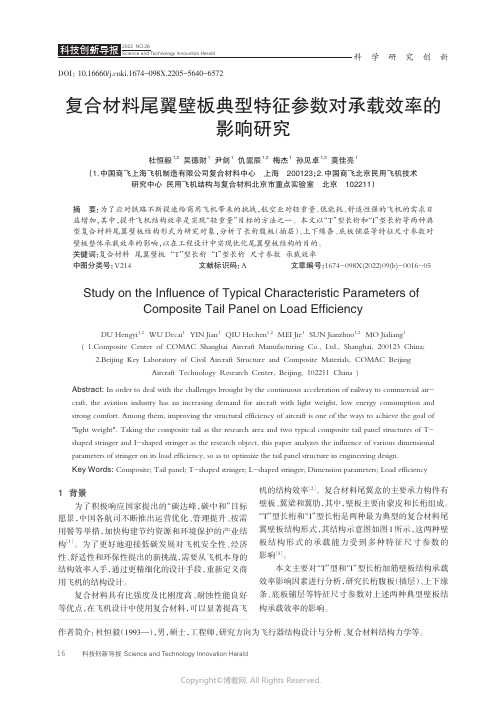
学研究创新复合材料尾翼壁板典型特征参数对承载效率的影响研究杜恒毅1,2吴德财1尹剑1仇翯辰1,2梅杰1孙见卓1,2莫佳亮1(1.中国商飞上海飞机制造有限公司复合材料中心上海200123;2.中国商飞北京民用飞机技术研究中心民用飞机结构与复合材料北京市重点实验室北京102211)摘 要:为了应对铁路不断提速给商用飞机带来的挑战,航空业对轻重量、低能耗、舒适性强的飞机的需求日益增加,其中,提升飞机结构效率是实现“轻重量”目标的方法之一。
本文以“T”型长桁和“I”型长桁等两种典型复合材料尾翼壁板结构形式为研究对象,分析了长桁腹板(插层)、上下缘条、底板铺层等特征尺寸参数对壁板整体承载效率的影响,以在工程设计中实现优化尾翼壁板结构的目的。
关键词:复合材料尾翼壁板“T”型长桁“I”型长桁尺寸参数承载效率中图分类号:V214文献标识码:A文章编号:1674-098X(2022)09(b)-0016-05 Study on the Influence of Typical Characteristic Parameters ofComposite Tail Panel on Load EfficiencyDU Hengyi1,2WU Decai1YIN Jian1QIU Hechen1,2MEI Jie1SUN Jianzhuo1,2MO Jialiang1 ( posite Center of COMAC Shanghai Aircraft Manufacturing Co., Ltd., Shanghai, 200123 China;2.Beijing Key Laboratory of Civil Aircraft Structure and Composite Materials, COMAC BeijingAircraft Technology Research Center, Beijing, 102211 China )Abstract: In order to deal with the challenges brought by the continuous acceleration of railway to commercial air-craft, the aviation industry has an increasing demand for aircraft with light weight, low energy consumption and strong comfort. Among them, improving the structural efficiency of aircraft is one of the ways to achieve the goal of "light weight". Taking the composite tail as the research area and two typical composite tail panel structures of T-shaped stringer and I-shaped stringer as the research object, this paper analyzes the influence of various dimensional parameters of stringer on its load efficiency, so as to optimize the tail panel structure in engineering design.Key Words: Composite; Tail panel; T-shaped stringer; L-shaped stringer; Dimension parameters; Load efficiency1 背景为了积极响应国家提出的“碳达峰,碳中和”目标愿景,中国各航司不断推出运营优化、管理提升、按需用餐等举措,加快构建节约资源和环境保护的产业结构[1]。
铜包铝双金属复合材料构件工装的数字化设计

铜包铝双金属复合材料构件工装的数字化设计马瑛剑(中航通飞华南飞机工业有限公司,广东 珠海 519040)摘 要:常规铜包铝双金属复合材料构件在制造过程,人为因素影响构件加工质量的程度较高,因此提出铜包铝双金属复合材料构件工装的数字化设计。
通过搭建铜包铝双金属复合材料构件分析模型,结合数字化设计技术,完成数字化设计。
关键词:铜包铝;复合材料;构件工装;数字化设计中图分类号:TH122 文献标识码:A 文章编号:1002-5065(2019)04-0318-2Digital Design of Tools for Components of Copper-clad Aluminum Bimetallic CompositesMA Ying-jian(CAAC Flight South China Aircraft Industry Co., Ltd.,Zhuhai 519040,China)Abstract: In the manufacturing process of conventional copper clad aluminium bimetallic composites, human factors have a high degree of influence on the processing quality of components. Therefore, the digital design of tooling for copper clad aluminium bimetallic composites is proposed. By building the analysis model of copper clad aluminium bimetallic composite components and combining with digital design technology, the digital design is completed.Keywords: copper clad aluminium; composite materials; component tooling; digital design传统构件工装是根据设计人员的工作经验进行标准工装选择,但结果往往不太尽人意,常常出现装配工装安装精度低、维护性低等情况,因此提出铜包铝双金属复合材料构件工装的数字化设计。
飞机壁板自动化制孔应用研究

Copyright©博看网. All Rights Reserved.
中国设备工程 2023.06 (下)
99
Research and Exploration 研究与探索·工艺流程与应用
组装偏差修改等这些是基本。在操作中,确保部件组装 质量的先决条件和核心是对壁板的精准定位。操作工人 选择自动钻铆装置,把飞机壁板安装到钻铆机的固定栏 中,并用夹板、定位销等部件将壁板固定住,保持稳定 状态,可以方便接下来的钻铆步骤。钻铆模拟试验是技 术工作人员按照飞机壁板的外形,通过 CAD 等构建模型 的方法来设计壁板的固定位置,实现了其工作过程中程 序的运行和真实性模拟,以达到最优的钻铆检验方法。 组装偏差修改采用基于 NC 编程技术实现对钻铆工艺的 后续改进和优化,能够掌控壁板的整体组装状态,采用 长桁追踪装置对组装部件出现的偏差进行监控。相关技 术工人按照监控的结果对部件的位置进行移动,确保钻 铆工艺较好的可行性和应用,以及对飞机壁板上及周围 零部件组装时的精度。对自动钻铆程序运行引起的零部 件在组装过程中产生的偏差进行分析。 4 自动化制孔应用 4.1 实际应用的自动化制孔系统
长桁孔的钻制。加工下壁板长桁上的孔时,首先按 照已知的基准孔对刀。长桁架可以看作一条轴线 A 与制 孔加工坐标系横轴之间的夹角为 α 的直线,即线 OA。 由于刀具并不完全沿着线 OA 移动,实际上的位移是类 似台阶的折线,因为折线和直线之间的最大误差是在规 定范围内,所以能够将折线看作直线 OA。在对孔径定位 时,首先做出以下规定,如果加工点位于 OA 直线上或 者其上侧,则加工点的偏移值 F 为 0 或正数,如果位于 OA 直线的下侧,则偏差值 F 为负数。通过此种方法,并 依照机床数控设备的相关操作,实现判断误差值并自动 运动。当 F 为 0 或正数,沿横轴的正方向前进一步;当 F 为负数,沿纵轴的正方向前进一步,每行进一次就会 进行自动比较,一边判断一边向前移动,因此刀具的运 动路径表现为折线,且逼近 OA 直线。并且根据上面提 到的方法,采取装置来控制加工头的法线的方向,由 O 点开始逐点穿插进一直加工到 A 点为止,从而完成长桁 上孔的钻制。下部框上孔的钻制。在对壁板下面框架上 的孔进行加工时,应根据存在的基准孔对齐操作。下部 框可以看成是一条圆弧 AB,其半径为 R,而刀具的前进 路径为沿着台阶似的折线。由于折线和圆弧之间最大的 误差为相关要求的容许值,所以能够将折线看作为圆弧 AB。
新材料技术在航空领域的应用

新材料技术在航空领域的应用航空工业是现代工业领域中最为先进的行业之一,是国家科技实力和综合国力的重要标志。
新材料技术是现代工业制造的一个重要组成部分,赋予了制造业以新的理念、新的模式和新的方式。
这种新的技术和新的工艺,在航空领域得到广泛的应用,不仅能够提升航空产品的质量和性能,还能够提高生产效率,降低成本,推动整个航空领域的发展。
本文就新材料技术在航空领域的应用作一介绍。
一、碳纤维复合材料碳纤维复合材料(CFRP)是航空领域中应用最广泛的新材料之一,它具备高强度、高模量、低密度、耐腐蚀、低热膨胀系数等优良特性,是一种性能优异的结构材料。
CFRP的应用范围非常广泛,包括飞机机身、機翼、舵面、推进器、传动轴、热阀门等。
目前,CFRP的应用已经进入到了商用航空领域,如波音787、空客A350等飞机中都广泛使用CFRP材料。
采用CFRP材料可以显著减轻飞机的重量,提高了飞机的航程和运输能力;同时,CFRP材料具备优异的抗疲劳性能和耐腐蚀性能,在飞机使用的过程中,能够保证飞机的安全和长期稳定的性能。
CFRP技术不仅在民用航空领域得到广泛应用,在军用领域也同样得到了应用,如F-22、F-35等战机中采用CFRP材料作为机身外壳,有效提高了战机的使用寿命。
二、3D 打印技术3D 打印技术是一项正在快速发展的新技术,在航空领域也有着广泛的应用。
采用3D 打印技术可以实现复杂形状和密度分布的零件制作,无需模具,可以快速、灵活地完成复杂零部件制造,缩短生产周期,提高生产效率,降低成本。
在航空领域,采用3D 打印技术可以制造出轻量化、高强度的机身、发动机部件、翼面等重要零件,使得飞机的质量更轻、使用寿命更长、性能更好。
同时,采用3D 打印技术还可以更加灵活地进行迭代设计和生产,提高了设计的精度和质量,为航空产品的创新和发展带来了新的机遇。
三、人工智能技术人工智能技术是当下最为热门的一项技术,它在航空领域也得到了广泛应用。
模注复合材料有助于降低无人驾驶飞机成本
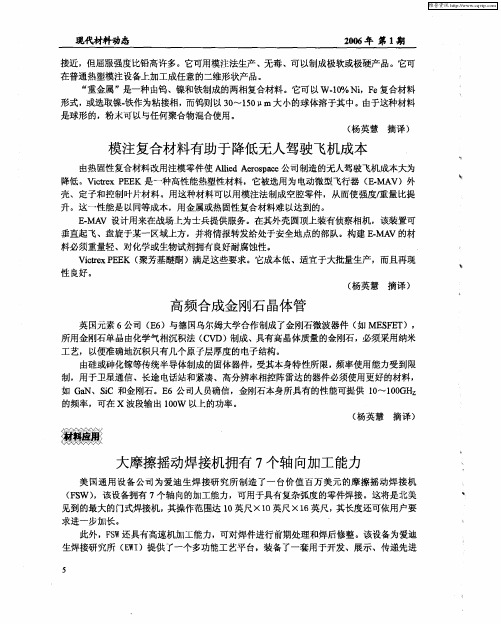
( 杨英慧
摘译 )
高频合成金刚石晶体管
英 国元素 6公司 ( 6 E )与德 国乌尔姆大学合作制成 了金刚石微波器件 ( ME F T 如 S E ), 所用金刚石单 晶由化学气相沉积法 ( V 制成 、 C D) 具有 高晶体质量的金刚石 , 必须采用纳米
工 艺,以便准确地沉积只有几个原子层厚度 的电子结构 。 由硅或砷化镓等传统半导体制成的固体器件, 受其本身特性所 限, 频率使用能力受到限 制 ,用于卫星通信 、长途 电话站和紧凑、高分辨率相控阵雷达 的器件必须使用更好的材料 ,
升。这一性能是以同等成本 ,用金属或热 固性复合材料难 以达到的。 EMA 设计用来在战场上为士兵提供服务。在其外壳圆顶上装有侦察相机 ,该装置可 . V 垂直起飞、盘旋于某一区域上方 ,并将情报转发给处于安全地点的部队。构建 EMA . V的材 料必须重量轻、对化学或生物试剂拥有 良好耐腐蚀性。 Vc e E K ( i r P E 聚芳基醚酮 )满足这些要求 。它成本低、适宜于大批量生产,而且再现 tx
5
如 G N、S 和金刚石 。E a i C 6公司人员确信,金刚石本身所具有的性能可提供 1 ̄10 H 0 0G z 的频率,可在 X波段输出 10 以上的功率 。 0W
( 杨英慧
2- ̄ /- / 3 p  ̄
摘译)
灞隋 Biblioteka ; 大摩擦摇动焊接机拥有 7 个轴 向加工能力
美 国通用设 备公司为爱迪 生焊接研 究所制造 了一 台价值 百万美元的摩擦摇动焊接机 ( S ,该设备拥有 7 F W) 个轴 向的加工能力 ,可用于具有复杂弧度的零件焊接 。这将是北美 见到的最大的门式焊接机 , 其操作范围达 1 英尺 ×1 英尺 X1 英尺, 0 0 6 其长度还可依用户要 求进一步加长。 此外,FW还具有高速机加工能力,可对焊件进行前期处理和焊后修整 。该设备为爱迪 S 生焊接研 究所 (W )提供 了一个多功能工艺平台,装备 了一套用于开发、展示、传递先进 EI
- 1、下载文档前请自行甄别文档内容的完整性,平台不提供额外的编辑、内容补充、找答案等附加服务。
- 2、"仅部分预览"的文档,不可在线预览部分如存在完整性等问题,可反馈申请退款(可完整预览的文档不适用该条件!)。
- 3、如文档侵犯您的权益,请联系客服反馈,我们会尽快为您处理(人工客服工作时间:9:00-18:30)。
料的工程过程,可以使设计人员同时在零件几何、材料、结构要求以及工艺过程约束之间进行权衡。
设计人员使用FiberSIM 软件能快速可视化铺层形状和纤维方向,在设计阶段即发现制造问题,并采取相应的纠正措施;从初步设计、详细设计直到制造车间,最终得到复合材料零件。
研究内容1 铺层分片、对接区偏移量的研究预浸料有一定的幅宽限制,大型复杂复合材料构件通过仿真分析,如果铺层超出了材料的幅宽限制则需要在适当的位置将铺层进行分割,分开的铺层片之间需要进行对接或搭接,偏移量的大小要根据设计要求,通过软件进行设计[3]。
2 复杂曲面下的铺层分析及铺层展开设计研究低成本通用飞机复合材料设计制造一体化技术中航工业通用飞机设计研究院 马瑛剑本文结合演示验证件通过对通用飞机复合材料结构件的数字化设计制造,应用复合材料设计软件FiberSIM 与自动下料系统和激光铺层定位系统等的集成,打通了复合材料构件设计、工艺、制造的数字化生产线。
Composites Design and Manufacturing Integration Technology on Low-CostGeneral Aircraft低成本复合材料设计制造一体化技术已经成为世界通用飞机制造商必须要面对和解决的问题之一。
采用数字化设计制造技术可以提高产品的研制生产效率,保障产品质量,降低产品成本[1]。
该技术克服了原有复合材料制造过程中主要依赖于模线-样板而导致的铺层和层间马瑛剑硕士,现就职于中航工业通用飞机设计研究院通用飞机所结构强度室,复合材料结构主管设计师,主要负责通用飞机复合材料结构设计工作。
的定位不准、材料裕度过大导致的浪费。
高性能连续纤维复合材料为生产轻质高性能的产品提供了巨大的机会,但是高的材料成本、设计和产品制造的复杂性在很大程度上抵消了复合材料的使用效益。
为了降低成本,提高复合材料生产效率,缩短复合材料产品的开发时间,减少材料浪费,降低工具损耗及生产时间,美国VISTAGY 公司在CATIA [2]软件平台上开发了用于复合材料制造和分析的软件FiberSIM。
FiberSIM 是集成于CAD 系统中的一个软件工具包,它可以使CAD 系统成为高性能的设计和制造复合材料零件的软件工具。
FiberSIM 软件独有的复合材料仿真技术,能够预测复合材料如何与复杂的表面贴合,并把贴合的结果形象地表示出来。
FiberSIM 软件支持整个复合材对于复杂曲面上的铺层,进行二维展开时,既要保证铺层能够展开,还要保证展开的铺层铺到与3D模型上边界一致,往往存在较大的困难。
只有当制造可行性分析表明纤维变形在可接受范围之内才可以进行铺层展开。
铺层展开的运算法则有能力绘制从3D铺层模型到铺层展开的曲线,就是可以绘制铺层展开的工装定位孔(工装十字线),也可绘制切割线、参考线和铺层孔。
复合曲线确定极准确的铺层展开是不可能的,可以在制造世界地图的问题上找到解释。
开发绘制地球平面图的过程中产生了一些相当好的方法准确地绘制了曲面的面积和陆地块的形状。
这些条件互相独立,根本不可能既确保形状又保证面积,除非加许多剪口。
如果一个世界地图有足够多的剪口,那么理论上这个地图在形状和面积上相当准确;然而,一般人则难以辨认。
在复合材料铺层展开问题上与绘制地图一样,复合材料铺层展开是将每一自由曲面绘成平面图。
如果在一个铺层上应用太多剪口,则铺层将很难铺放,并影响到零件的整体性。
(1)铺放起始点的优化。
如先前所提到的,制造可行性分析网格表明在铺放起始点周围变形极小。
向前移动起始点变形的面积减小甚至消除变形。
在曲面有较大曲率的情况下,起始点偏移指向铺层的一端代表那里的形状,然后应用其他的技术减小铺层的变形。
(2)铺层拼接。
拼接就是将铺层切开的两条边界对接在一起。
如果两条边界是外部的,则铺层被切成两块。
如果一条边界是外部的,另一条是内部的,铺层保持一片。
在FiberSIM计算中实现上述情况是迫使网格在对接周围计算,因此在特定位置打断了网格的连续约束。
结果在铺层上有很小的纤维变形,但是纤维在拼接边界不再相切。
(3)铺层剪口。
剪口与拼接相似,除了剪开仅包括一条边界外,还在铺放起始点与变形区域之间打断连续纤维。
剪口位置位于铺放起始点和变形区域之间,也可能仅封闭在变形区域。
在拼接处,纤维在剪口不连续。
(4)标记长度分析。
这是一项用于测量铺层展开准确性的技术。
它包括在展开的铺层中需要测量的两个特征间定义标记(曲线),在典型的铺放起始点和工装孔位置。
定义了铺层展开,标记将自动地在展开的铺层上绘制。
在SEL-PLY模块中MLA功能确定标记,测量与3D和2D间长度的差异。
长度上允许的差异与所选材料有关,体现在铺层大小的功能和有多少材料可以伸展方面。
在这种情况下,定义最大允许差值为1.27cm。
(5)分开和连接。
分开和连接技术是最后采用的方法。
事实上铺层展开在接近铺放起始点处最准确。
从本质上看,该技术是在一个展开的铺层上设置多个铺放起始点,即把3D铺层切成几片。
通过分析标记上的长度确定铺层切开的位置,达到预期的切开区域。
切开点位于3D和2D间的距离开始有较明显偏离的地方。
一但定义了切开点,铺层边界即被改变,制造分析网格将在主体部分定义。
网格线之一伸入到切开区域,投影到铺放曲面上,这些曲线在切开区域变成纤维方向曲线,在主体和切开的片之间保持纤维连续。
铺放起始点被设置在靠近切开边界的曲线上。
在切开线两片之间的公共位置生成最佳化的形状。
标记穿过切开线,铺层展开将计算每一区域,不同的铺层展开利用标记在平面中再结合到一起。
3剪口位置确定技术对于较复杂的零件,仿真后多出现许多红色区域,不能满足设计和制造的要求,影响零件的质量。
如果在一个铺层上应用太多剪口,则铺层将很难铺放,并影响到零件的整体性。
剪口与拼接相似,除了剪开仅包括一条边界,在铺放起始点与变形区域之间打断连续纤维。
剪口位置位于铺放起始点和变形区域之间,也可能仅封闭在变形区域。
拼接处,纤维在剪口位置不连续,正确的设计剪口位置可以大大减少或消除红色区域。
演示验证件的设计制造一体化设计1 演示验证件选择及结构选择通用飞机复合材料壁板作为演示验证结构,演示验证结构位置见图1。
演示验证结构尺寸2000mm×1000mm,为蜂窝夹层结构,蜂窝边缘切30°角形式,上蒙皮采用一层碳纤维布,下蒙皮采用两层碳纤维布,边缘用碳纤维预浸布局部加强。
由于蜂窝上下表面的形状不同,为了工艺仿真的精确,分别定义了两个模具面,图2中(a)、(b)分别为蜂窝下表面模具面和蜂窝上表面模具面以及各自的静边界和扩展边界。
2 铺层工艺以下为演示验证件的工艺可行性分析过程,图3为仿真铺层超宽情况,此种情况是不被允许的,可以用图4的方法来解决。
按以上设计方案仿真铺层后分别生成图5中(a)、(b)展开曲线。
图1 复合材料部件3D实体图经过以上设计方案,生成全部铺层仿真前的效果图(见图6),设计后铺层仿真效果图(见图7), 设计仿真展开图(见图8)。
3 数字化制造工艺图7为所有的仿真铺层的展开图,图8是由展开图生成的、格式为DXF 的可供自动下料机使用的文件。
根据每一层边界生成的投影文件和根据每一层展开图生成的下料文件分别输入到投影设备和下料设备中,投影设备在工装表面投影出每一层的轮廓,自动下料机按照下料文件上的信息在预浸料上裁减出每一层的平面展开状态的形状,最后将下料机裁减出的每一层按照工装上所投影出的轮廓铺贴上去,当所有层都铺贴完成后固化成形,经过切割最终成型出产品。
三维模型建好以后,一边用于工装的设计制造,一边输入到复合材料专用设计/制造软件中完成基于三维模型的铺层展开。
进一步提取铺层展开数据,通过数据接口生成下料机专用的排样下料文件、直接支持Virtek 和General Scanning 激光投影系统的激光投影编码以及用于纤维铺放的铺层文件等,通过数据接口将上述文件信息分别输入到排样系统、自动剪裁机、激光铺层定位系统和纤维铺放机等制造设备,自动进行优化排样、下料、各铺层精确定位以及纤维铺放等。
复合材料设计、制造一体化实现了零件三维模型到制造的无缝集成,极大地减少了不准确的铺层尺寸和铺设方向,提高了产品质量,同时自动切割和优化排样减少了材料浪费,激光铺层定位消除了手工切割样板和手工铺层样本。
图9为夹层复合材料结构数字化设计流程[4-5]。
通用飞机的设计制造一体化效益概述本文以某型号通用飞机为例,机图3 设计仿真材料超宽(a)方法一(b)方法二图4 仿真解决超宽视图图6 仿真前效果图图7 设计铺层仿真效果图图8 设计铺层仿真效果展开图(a)曲线a(b)曲线b图5 设计仿真展开曲线图 2 数字化设计表面视图(b)上表面视图(a)下表面视图体主体结构除了机翼主起加强肋和一些连接结构件为金属材料外,其余全为复合材料结构件。
以碳纤维预浸料为例,设计人员将理论尺寸提交给工艺后,工艺人员要依据理论尺寸给出工人操作等余量在150%以上;以日本东丽公司主要预浸料材料报价为依据,主要预浸料材料报价如表1所示;使用FiberSIM 软件设备报价清单如表2所示。
通过表3得出使用FiberSIM 设计制造后单架机一些主要结构节约费用5.25万元,而原表1 主要预浸料材料报价表2 使用设备报价清单表3 使用FiberSIM设计制造后单架机节约费用型机为全复合材料飞机所以整机使用软件后节约成本约在6万元以上,通过表2、表3对比分析得出原型机在销售达到146架机时候,按照年产100架机计算,一年半收回初期软件及设备投入成本;在一年半以后每架机节约费用超过6万元,年节约费用超过600万元。
以上数据为单方面从投入产出比计算效益,而软件及设备投入后在人力成本及产品报废率上都有很可观的收益。
结束语本文结合演示验证件通过对通用飞机复合材料结构件的数字化设计制造,应用复合材料设计软件FiberSIM 与自动下料系统和激光铺层定位系统等的集成,打通了复合材料构件设计、工艺、制造的数字化生产线,与传统设计、制造方法相比有以下优势:(1)从设计到产品的制造整个周期,由原来的设计完成移交工艺进行制造准备,转变成由FiberSIM 软件介入零件设计后的分析优化,进而达到缩短产品设计周期的目的。
(2)通过使用FiberSIM 软件可以对原材料的采购、制造成本进行控制,进而达到节省用材的目的。
(3)通过FiberSIM 软件的前期分析优化、激光投影仪和自动下料机的配合使用,进而达到缩短整个产品的制造周期、提升产品质量、减少产品报废率的目的。
目前,通用飞机中越来越多的采用复合材料替代金属材料,而复合材料设计制造一体化技术的诞生大大提升了设计准确性、制造质量、制造一次性成功的可能性,缩短了制造周期,最大化地降低了产品的制造成本[6]。