废橡胶的循环利用技术
再生橡胶工艺流程

再生橡胶工艺流程
《再生橡胶工艺流程》
再生橡胶是指将废弃的橡胶制品,如废旧轮胎、废橡胶管等,通过再生工艺处理,使之重新变为可用的橡胶原料。
再生橡胶工艺流程包括了废弃橡胶制品的回收、破碎、粉碎、颗粒化、分选、去异物等多个环节,整个过程既环保又资源化利用,也是目前橡胶行业发展的重要方向之一。
首先,在再生橡胶工艺流程中,需要对废弃的橡胶制品进行回收和分类。
废旧的橡胶制品通常会经过收集、运输、清洗等步骤,然后按照不同的类型进行分类,如轮胎、橡胶管、橡胶垫等。
接下来是破碎和粉碎的环节,这一步是为了将废弃的橡胶制品进行粉碎,使之变为粉末状。
通常会使用破碎机和粉碎机进行处理,将废弃的橡胶制品破碎成颗粒状或粉末状。
然后是颗粒化和分选的过程,这一步是为了将粉碎后的橡胶进行颗粒化处理,并进行分选,去除其中的异物和杂质。
这个环节通常会用到振动筛、气流分选机等设备进行处理。
最后是去异物环节,即对颗粒化后的橡胶进行清洗、除尘、磁选等处理,去除其中的异物和杂质,以保证再生橡胶的质量。
整个再生橡胶工艺流程,将废弃的橡胶制品重新变为可用的橡胶原料,实现了资源的再利用,同时也有利于保护环境。
再生
橡胶在橡胶制品制造领域有着广泛的应用,可以用于生产橡胶地板、橡胶管、橡胶密封件等产品,为橡胶行业的可持续发展做出了积极的贡献。
废橡胶脱硫再生工艺的最新进展

胶 ,替代 新 胶 ,可用 于各种 橡胶制 品,1 0 0 多年 来
被世 界各 国所 采用 ,被认 为是 处理废 旧橡 胶再 生 循环 利用 最为 科学 、最 为合理 、应 用最 广 的一 条 重要 途径 。特 别是 改革 开放 以来 ,新工 艺与技 术
力 下进 行 7 - 8小 时的脱硫 ,随后 进行 捏炼 、制 成再 生胶 。水 油法 利用
了胶粉 在 高温 高压 条件 下 可迅 速溶 胀 的特 点进 行 脱硫 。2 0世纪 8 0年 代末 9 0年 代初 ,国 内研 发成 功 高温 高压 动态 脱 硫法 ,它集 中了水 油法 和 油法 的优 点 ,该 脱硫 方 法是 在 高温 高压 和 脱硫 活化 剂
近 年 来 开 发成 功 的 脱硫 再 生 法 有 : 密 闭 式 捏
I I I 、双 螺杆 剪 切 脱硫 再生 法 【 1 】 :此 法 由南 京
科 普公 司近 几年研 制 成功 , 主 要用 于特 种橡胶 ( 丁
基 橡胶 , 乙丙橡胶 ,丁 腈橡 胶 )再 生 ,现 已可 用
炼 机 脱硫 再 生法 ,单 螺杆 或双 螺 杆连 续 脱硫 再 生
作者简介: 董诚春 ( 1 9 3 6 . ) ,男 ,北 京 橡 胶 研 究设 计 院退
生技 术有 了极大 的发 展 ,现将 废 旧橡胶 再生方 法
休高级工程师 ,主要从 事轮胎及橡胶制品 的配方、工 艺以及 简述如 下 。 再生胶 的脱硫配方 、工艺的研究及应用 。合编橡胶专业书籍
六本 ,独 自编著 《 废橡胶 资源综合利用》 ,《 废轮胎 回收加工
生 产 效率 低 , 能耗 大 。2 ) 除 切 断硫 键 交联 网 点 以
橡胶高分子材料直接循环利用的工艺流程
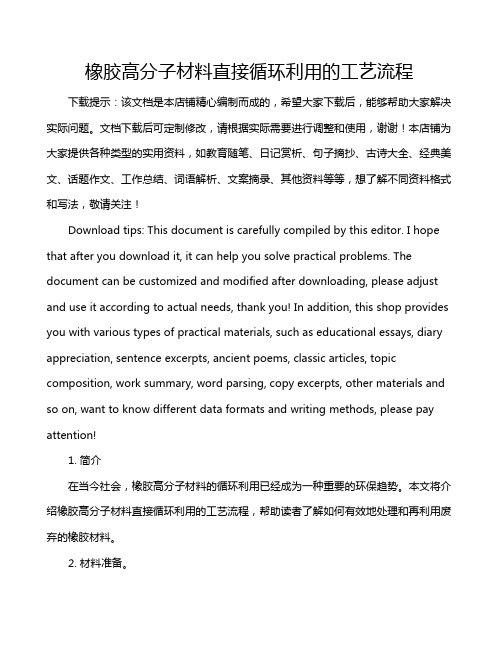
橡胶高分子材料直接循环利用的工艺流程下载提示:该文档是本店铺精心编制而成的,希望大家下载后,能够帮助大家解决实际问题。
文档下载后可定制修改,请根据实际需要进行调整和使用,谢谢!本店铺为大家提供各种类型的实用资料,如教育随笔、日记赏析、句子摘抄、古诗大全、经典美文、话题作文、工作总结、词语解析、文案摘录、其他资料等等,想了解不同资料格式和写法,敬请关注!Download tips: This document is carefully compiled by this editor. I hope that after you download it, it can help you solve practical problems. The document can be customized and modified after downloading, please adjust and use it according to actual needs, thank you! In addition, this shop provides you with various types of practical materials, such as educational essays, diary appreciation, sentence excerpts, ancient poems, classic articles, topic composition, work summary, word parsing, copy excerpts, other materials and so on, want to know different data formats and writing methods, please pay attention!1. 简介在当今社会,橡胶高分子材料的循环利用已经成为一种重要的环保趋势。
废旧橡胶的回收和循环利用

废旧橡胶的回收和循环利用随着工业和现代文明的发展,各种工业和生活废弃物的处理已经成为人们面临的一大难题,特别是对于经过化学交联的橡胶,由于它内部具有交联的网络结构,因此既不溶也不熔。
目前橡胶制品已经广泛应用于生活中的每一个领域,而这些橡胶制品使用后如果处理不当,可能会给环境带来严重的污染,同时造成资源的浪费。
如何经济\有效\环保地回收具有交联结构的橡胶,始终是全社会关注的焦点问题。
自150多年前Goodyear发明了弹性体的硫化工艺以来,人们为了解决硫化橡胶回收利用问题想出了各种各样的解决方法,甚至于Goodyear本人都在1853年发明了一项专利,其工艺就是将各种废旧的硫化橡胶磨成胶粉然后回收利用,这种方法目前仍在广泛利用。
现在人们已经发明了各种各样的方法用以解决废旧弹性体的回收利用问题,例如轮胎翻新、焚化燃烧以作为燃料、掩埋、磨成胶粉用作填充剂以及脱硫制备再生胶等等。
本文将介绍废旧橡胶的回收和循环利用的主要途径。
一、废旧橡胶的直接利用直接利用是将废旧橡胶制品以原有形状或近似原形加以利用,以废旧轮胎为例,轮胎翻修便是其直接利用中最有效、最直接而且经济的利用方式。
在使用保养良好的情况下,一条轮胎可多次翻修,这样总的翻胎寿命往往可达新胎的1-2倍,而所耗原材料仅为新胎的15%-30%,所以世界各过都普遍重视轮胎翻修工作。
目前世界上最先进的翻胎技术为预硫化翻胎法,又称冷翻法,即把已经硫化成型的胎面胶粘合到经过打磨处理的胎体上,装上充气内胎和包封套,送入大型硫化罐,在较低温度和压力下硫化,一次可生产多条翻新轮胎。
除翻修外,废旧轮胎还可作为人工鱼礁、码头护弦以及赛道车辆等的缓冲材料;在美国还有将其做成高速公路的隔音墙使用。
另外,废旧橡胶还用于防止重金属污染,据分析这是因为水银等重金属会和橡胶制品中的硫磺及其他化合屋发生化学反映的缘故。
二、粉碎为胶粉后利用将废旧橡胶通过常温粉碎或者低温粉碎等方法制备胶粉后加以利用,这是很早以来就采用的方式,也是目前废旧橡胶回收的一种非常重要的途径,目前生产精细胶粉已成为废旧橡胶再利用的主导方向。
橡胶材料的回收利用
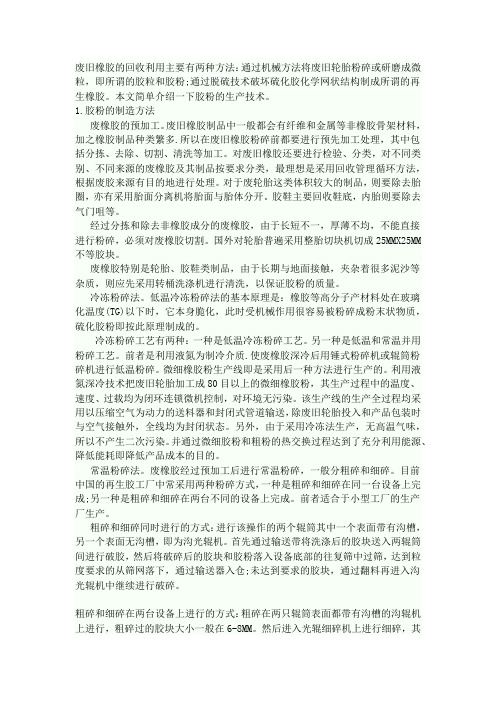
废旧橡胶的回收利用主要有两种方法:通过机械方法将废旧轮胎粉碎或研磨成微粒,即所谓的胶粒和胶粉;通过脱硫技术破坏硫化胶化学网状结构制成所谓的再生橡胶。
本文简单介绍一下胶粉的生产技术。
1.胶粉的制造方法废橡胶的预加工。
废旧橡胶制品中一般都会有纤维和金属等非橡胶骨架材料,加之橡胶制品种类繁多.所以在废旧橡胶粉碎前都要进行预先加工处理,其中包括分拣、去除、切割、清洗等加工。
对废旧橡胶还要进行检验、分类,对不同类别、不同来源的废橡胶及其制品按要求分类,最理想是采用回收管理循环方法,根据废胶来源有目的地进行处理。
对于废轮胎这类体积较大的制品,则要除去胎圈,亦有采用胎面分离机将胎面与胎体分开。
胶鞋主要回收鞋底,内胎则要除去气门咀等。
经过分拣和除去非橡胶成分的废橡胶,由于长短不一,厚薄不均,不能直接进行粉碎,必须对废橡胶切割。
国外对轮胎普遍采用整胎切块机切成25MMX25MM 不等胶块。
废橡胶特别是轮胎、胶鞋类制品,由于长期与地面接触,夹杂着很多泥沙等杂质,则应先采用转桶洗涤机进行清洗,以保证胶粉的质量。
冷冻粉碎法。
低温冷冻粉碎法的基本原理是:橡胶等高分子产材料处在玻璃化温度(TG)以下时,它本身脆化,此时受机械作用很容易被粉碎成粉末状物质,硫化胶粉即按此原理制成的。
冷冻粉碎工艺有两种:一种是低温冷冻粉碎工艺。
另一种是低温和常温并用粉碎工艺。
前者是利用液氮为制冷介质.使废橡胶深冷后用锤式粉碎机或辊筒粉碎机进行低温粉碎。
微细橡胶粉生产线即是采用后一种方法进行生产的。
利用液氮深冷技术把废旧轮胎加工成80目以上的微细橡胶粉,其生产过程中的温度、速度、过载均为闭环连锁微机控制,对环境无污染。
该生产线的生产全过程均采用以压缩空气为动力的送料器和封闭式管道输送,除废旧轮胎投入和产品包装时与空气接触外,全线均为封闭状态。
另外,由于采用冷冻法生产,无高温气味,所以不产生二次污染。
并通过微细胶粉和粗粉的热交换过程达到了充分利用能源、降低能耗即降低产品成本的目的。
废旧橡胶的回收利用

废旧橡胶的回收利用——胶粉的物理化学法制备摘要胶粉是废旧橡胶经过机械粉碎制得的颗粒状粉体,具有致密的交联网络结构,但被人们长期使用的废旧橡胶表面已失去活性,因此,胶粉在应用到其他材料时,与基质材料的相容性很差,导致复合材料的性能不理想。
然而,对胶粉进行表面改性,是解决这一瓶颈的关键所在。
本文针对胶粉的再利用难题,开展了一系列的胶粉表面改性的研究工作:采用微波脱硫改性方法和机械力化学改性方法对胶粉改性,进而将改性胶粉应用到橡胶材料中制备了胶粉/天然橡胶硫化胶,并探讨了两种方法的改性效果。
最后,为进一步扩大胶粉的应用领域,结合机械力化学改性方法制备了改性胶粉/丁腈橡胶发泡材料,并研究了其相关性能。
本文主要采用纯度为90%以上的胶粉为原料,研究了该胶粉与橡胶基质中的应用情况。
关键词:精细胶粉; 粒度; 物理化学法; 延伸率; 抗拉强度;江阴职业技术学院毕业论文(设计)Recycling of Waste Rubber——Ultrasonic Desulphurization and Re-vulcanizedAbstractWaste rubber powder (WRP) is granular powder which is made from waste rubber grinded by machines.Waste rubber powder (WRP) with dense cross-linked network structure has lost its surface activity, because waste vulcanized rubber is used by people for a long time. Therefore, when waste rubber powder (WRP) is applied for other materials, the compatibility beween WRP and the matrix material is very poor, so that the properties of composites is not ideal. However, surface modification of WRP is the key to solve ....Keywords:fine-grade rubber power;grade;physicochemistry method;elongation coefficient;tensile strength;Abstract目录摘要 (1)ABSTRACT (2)前言 (4)第一章概述 (5)1.1废旧橡胶回收利用的历史回顾 (5)1.2我国废旧轮胎回收利用现状 (5)第二章废旧橡胶再生方法 (9)2.1传统的再生方法 (9)2.2现代的再生方法 (9)第三章废旧橡胶的物理化学法制备胶粉 (13)3.1废旧橡胶的传统制备胶粉法 (13)3.1.1 常温粉碎法 (13)3.1.2 低温粉碎法 (15)3.1.3 湿法或溶液粉碎法 (17)3.2 物理化学法制备精细胶粉 (18)3.2.1 物理化学法处理工艺 (18)3.3试验结果分析 (19)3.3.1 物理化学法与普通粉碎法的比较 (19)3.3.2 胶粉∕介质体积比对胶粉粒度的影响 (20)3.3.3 胶粉力学性能的比较 (20)第四章结论 (24)4.1 物理化学法的优点 (24)4.2 废旧橡胶的未来发展趋势 (24)参考文献 (26)致谢 (27)江阴职业技术学院毕业论文(设计)前言随着废旧轮胎累积堆存,而新废弃轮胎不断增加的现状,科学的废旧轮胎回收利用已成为当前急待解决的一个化学技术难题。
废旧橡胶再生回收处理技术

废旧橡胶再生回收处理技术废旧橡胶再生回收处理技术橡胶是一种重要的工业原料,广泛应用于汽车、轮胎、建筑、医疗等领域。
然而,橡胶废料的处理一直是一个全球性的问题,废旧橡胶的大量堆积不仅浪费资源,还对环境造成了严重的污染。
因此,废旧橡胶再生回收处理技术显得尤为重要。
在废旧橡胶再生回收处理技术方面,主要有以下几种方法:1.橡胶粉碎再生技术:这种技术是目前较为成熟的废旧橡胶处理方法之一。
首先将废旧橡胶进行机械粉碎,然后通过物理或化学方法处理,使粉碎的橡胶再生为橡胶颗粒。
这种方法具有操作简单、成本低廉等优点,但是处理后的橡胶颗粒质量不稳定,对环境有一定的污染。
2.溶剂回收技术:此技术主要利用溶剂将废旧橡胶中的有机杂质分离出来,以实现橡胶的再生。
该方法对橡胶的再生效果较好,产品质量稳定,且无污染,但溶剂回收过程中产生的废水、废气处理比较复杂,增加了处理成本。
3.热塑化再生技术:这种技术是一种将废旧橡胶加热融化,然后形成新橡胶制品的方法。
具体操作过程是将废旧橡胶加热到一定温度,使其熔化,然后添加一定量的再生橡胶添加剂,最终形成新的橡胶产品。
该技术具有工艺简单、能耗低等优点,但热塑化过程中产生的废气会对环境造成一定的污染。
综上所述,废旧橡胶再生回收处理技术是解决橡胶废料处理问题的重要手段。
每种技术方法都有其优缺点,所以在实际应用中,需要根据条件和需要选择合适的技术。
未来,废旧橡胶再生回收处理技术将不断得到改进和创新,以提高再生橡胶的质量和利用率,降低处理成本和环境污染。
同时,政府和企业应加大对废旧橡胶再生回收处理技术的研究投入,推动技术的产业化和市场化。
总的来说,废旧橡胶再生回收处理技术的发展与应用能有效解决橡胶废料的问题。
通过科学合理地利用废旧橡胶资源,不仅可以减少资源浪费,还可以保护环境,实现可持续发展。
废旧橡胶再生回收处理技术的发展与应用对于推动循环经济、实现可持续发展具有重要意义。
随着全球对环境污染和资源浪费问题的日益关注,废旧橡胶再生回收处理技术已成为各国政府和企业研究和推动的重点。
废橡胶循环利用方案(二)
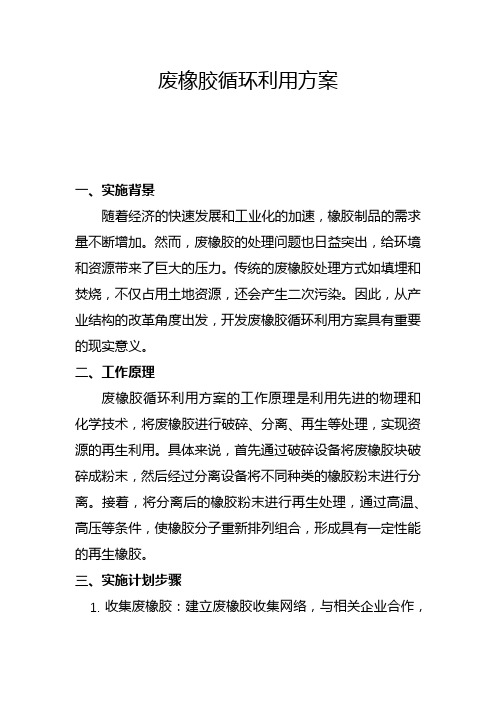
废橡胶循环利用方案一、实施背景随着经济的快速发展和工业化的加速,橡胶制品的需求量不断增加。
然而,废橡胶的处理问题也日益突出,给环境和资源带来了巨大的压力。
传统的废橡胶处理方式如填埋和焚烧,不仅占用土地资源,还会产生二次污染。
因此,从产业结构的改革角度出发,开发废橡胶循环利用方案具有重要的现实意义。
二、工作原理废橡胶循环利用方案的工作原理是利用先进的物理和化学技术,将废橡胶进行破碎、分离、再生等处理,实现资源的再生利用。
具体来说,首先通过破碎设备将废橡胶块破碎成粉末,然后经过分离设备将不同种类的橡胶粉末进行分离。
接着,将分离后的橡胶粉末进行再生处理,通过高温、高压等条件,使橡胶分子重新排列组合,形成具有一定性能的再生橡胶。
三、实施计划步骤1.收集废橡胶:建立废橡胶收集网络,与相关企业合作,确保废橡胶的稳定供应。
2.破碎与分离:购买或租赁破碎设备和分离设备,建立废橡胶处理生产线。
3.再生处理:将破碎后的废橡胶进行再生处理,形成再生橡胶。
4.再生橡胶应用:将再生橡胶应用于制造新的橡胶制品,如轮胎、管材、鞋类等。
5.持续改进:根据市场反馈和生产数据,不断优化工艺流程,提高产品质量和降低成本。
四、适用范围该方案适用于所有产生废橡胶的企业和机构,如轮胎制造厂、橡胶管生产厂家、鞋类制造商等。
通过实施这一方案,这些企业可以减少废物的产生,降低处理成本,同时为环保事业做出贡献。
五、创新要点1.技术创新:采用先进的破碎和分离技术,确保废橡胶的高效处理和再生利用。
2.模式创新:建立废橡胶收集、处理、再生的完整产业链,实现废物的资源化利用。
3.合作创新:与相关企业建立合作关系,共同推动废橡胶的循环利用。
4.环保创新:注重环保要求,采取严格的环境保护措施,减少对环境的影响。
六、预期效果1.环境保护:减少废橡胶对环境的污染,降低填埋和焚烧产生的温室气体排放。
2.经济效益:通过废橡胶的循环利用,为企业节约原材料采购成本,提高产品竞争力。
废旧橡胶制品及其资源化利用
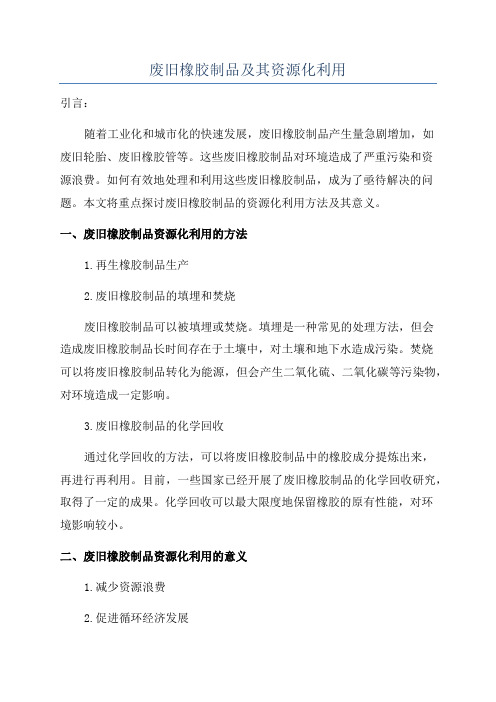
废旧橡胶制品及其资源化利用引言:随着工业化和城市化的快速发展,废旧橡胶制品产生量急剧增加,如废旧轮胎、废旧橡胶管等。
这些废旧橡胶制品对环境造成了严重污染和资源浪费。
如何有效地处理和利用这些废旧橡胶制品,成为了亟待解决的问题。
本文将重点探讨废旧橡胶制品的资源化利用方法及其意义。
一、废旧橡胶制品资源化利用的方法1.再生橡胶制品生产2.废旧橡胶制品的填埋和焚烧废旧橡胶制品可以被填埋或焚烧。
填埋是一种常见的处理方法,但会造成废旧橡胶制品长时间存在于土壤中,对土壤和地下水造成污染。
焚烧可以将废旧橡胶制品转化为能源,但会产生二氧化硫、二氧化碳等污染物,对环境造成一定影响。
3.废旧橡胶制品的化学回收通过化学回收的方法,可以将废旧橡胶制品中的橡胶成分提炼出来,再进行再利用。
目前,一些国家已经开展了废旧橡胶制品的化学回收研究,取得了一定的成果。
化学回收可以最大限度地保留橡胶的原有性能,对环境影响较小。
二、废旧橡胶制品资源化利用的意义1.减少资源浪费2.促进循环经济发展3.减少对环境的污染4.节约能源焚烧废旧橡胶制品可以产生大量的热能,可以作为能源进行利用。
这样既可以减少对传统能源的依赖,降低能源消耗,也可以减少对环境的污染。
结论:废旧橡胶制品的资源化利用具有重要的意义。
通过再生橡胶制品的生产、化学回收等方法,可以减少资源浪费、促进循环经济发展、减少对环境的污染、节约能源。
因此,应该加大对废旧橡胶制品资源化利用技术的研究和推广,推动废旧橡胶制品的可持续利用,实现资源循环利用的目标。
废橡胶的再生利用课件
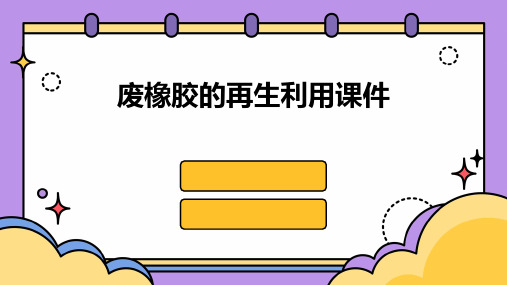
铺路材料
废橡胶可以加工成铺路材料,如橡胶沥青和橡胶砖。
这些铺路材料具有较好的抗滑性能和降噪性能,可以提高道路的安全性和舒适性 。同时,废橡胶的利用还可以减少对传统石料和沥青的依赖,降低道路建设和维 护成本。
04
废橡胶再生利用的挑战与 前景
技术挑战
分离与提纯技术
生产效率提升
废橡胶中的杂质和不同成分的分离、 提纯是再生利用的关键技术之一,需 要高效、环保的分离和提纯技术。
通过政策扶持和资金支持,培育一批废橡胶再生利用的龙头企业, 发挥示范带动作用。
加强产业链整合
鼓励企业向上下游延伸,形成完整的产业链条,提高资源利用效率 和产业竞争力。
推动绿色生产
引导企业采用环保、低碳的生产方式,减少废橡胶再生利用过程中的 环境污染,实现可持续发展。
THANKS
感谢观看
工业生产
在工业生产过程中,如输送带、密封件等橡胶制 品损坏或达到使用寿命后被废弃。
废橡废橡胶不易降解,长期存 在于环境中会对土壤、水 源造成污染。
安全隐患
废橡胶可能被误食或阻塞 排水系统,造成安全问题 。
资源浪费
废橡胶原本可以经过再生 利用,转化为有价值的产 品。
废橡胶的处理现状
轮胎翻新
01
轮胎翻新是将废旧轮胎进行修复 和再利用的过程,通过更换胎面 和加强材料,使轮胎能够再次使 用。
02
轮胎翻新能够延长轮胎使用寿命 ,减少新轮胎的需求,从而降低 资源消耗和环境污染。
橡胶制品的生产
废橡胶可以用于生产各种橡胶制品, 如橡胶管、橡胶垫、橡胶带等。
这些橡胶制品广泛应用于汽车、建筑 、机械、化工等领域,具有优良的耐 腐蚀、耐老化、耐高温等性能。
VS
废弃资源综合利用的橡胶废料处理与再利用

废弃资源综合利用的橡胶废料处理与再利用1.橡胶废料是工业生产中产生的一种重要废弃物。
据统计,每年全球产生的橡胶废料数量高达数百万吨。
这些橡胶废料如果得不到有效的处理和再利用,将对环境造成严重的影响。
因此,如何对橡胶废料进行处理和再利用,已经成为当前亟待解决的问题。
2. 橡胶废料的来源和分类橡胶废料主要来源于轮胎生产、橡胶制品加工和橡胶原料生产等环节。
根据橡胶废料的形态和性质,可以将其分为以下几类:1.轮胎橡胶废料:包括废旧轮胎和磨削下来的轮胎橡胶屑。
2.橡胶制品废料:包括橡胶板、橡胶管、橡胶条等制品的边角料和废品。
3.橡胶原料废料:包括废旧橡胶原料和生产过程中产生的废料。
3. 橡胶废料的处理方法橡胶废料的处理方法主要包括物理法、化学法和热解法等。
1.物理法:主要包括粉碎、筛选和磁分离等。
通过物理方法将橡胶废料进行处理,使其达到再利用的要求。
2.化学法:主要包括酸碱处理、氧化还原处理和络合处理等。
通过化学反应,改变橡胶废料的化学性质,使其更适合再利用。
3.热解法:通过高温热解,将橡胶废料分解为小分子化合物,从而实现资源的回收和利用。
4. 橡胶废料的再利用途径橡胶废料的再利用途径非常广泛,主要包括以下几个方面:1.再生橡胶:将橡胶废料经过处理后,重新用于橡胶制品的生产,可以大大节约原材料,降低生产成本。
2.橡胶填充料:将橡胶废料作为填充料,用于橡胶制品的生产,可以提高产品的密度和强度。
3.橡胶沥青:将橡胶废料用于生产橡胶沥青,可以用于道路铺设和防水材料等。
4.生物质能源:将橡胶废料进行热解,产生的可燃气体可以用于发电和供暖等。
5. 结论橡胶废料的处理和再利用是一个复杂的过程,需要综合考虑废料的来源、性质和处理方法等因素。
通过科学的处理和再利用,橡胶废料不仅可以减少环境污染,还可以实现资源的回收和利用,具有重要的经济和环境效益。
6. 橡胶废料处理与再利用的技术挑战橡胶废料的处理与再利用虽然具有明显的经济效益和环境效益,但在实际操作过程中,仍然面临着一系列的技术挑战。
我国的废橡胶资源循环利用现状和胶粉应用

专家论坛我国的废橡胶资源循环利用现状和胶粉应用纪奎江(青岛科技大学,山东青岛 266042) 我国是世界上最大的橡胶消费国,又是橡胶资源匮乏的国家,2005年的耗胶量达517万t ,占世界耗胶量的20%以上,其中一半靠进口。
与此同时我国又是世界上废橡胶产生量最大国家。
我国废橡胶利用除翻新轮胎外,再生胶达130万t ,占世界第一,硫化胶粉产能约十几万t 。
废橡胶回收利用率为65%左右。
废橡胶是六大再生资源之一,但近年兴起的土法炼油,既浪费资源,又污染环境,应该严令禁止。
1废橡胶的循环利用方法废旧橡胶主要来源于废弃橡胶制品,其次来自橡胶工厂生产过程中产生的边角余料和废品。
它属于工业固体废物中的一大类,作为高分子材料的循环利用资源,已引起世界各国的关注。
多年实践表明,其处理原则是:(1)减少废料来源;(2)再使用;(3)循环利用;(4)回收。
图 废旧橡胶材料循环利用图2我国胶粉工业的发展简况硫化胶粉是以废橡胶为原料,通过机械加工粉碎或研磨制成不同粒度的粉末状物质,简称胶粉。
它依据废橡胶来源不同而加工成粉末的粒度不同,分成很多品种和牌号,是宝贵的聚合物回收利用材料。
胶粉工业是废橡胶综合利用产业的一个分支,在我国始于上世纪80年代后期。
在中国建设与发展的第8个五年计划中,当时由于开始引进子午线轮胎的制造技术,在配方软件中含有胶粉的组分,加之1989年我国首次组团赴德国考察废橡胶利用情况,才引起国人的注意,但并非是再生胶生产过程中粉碎工序所得的粗胶粉。
“八五”规划中由青岛化工学院与山东高密再生胶厂、航空航天部第609研究所合作,承担原化工部下达的“低温冷冻法生产微细胶粉及其应用研究”攻关项目,并于1993年通过鉴定。
当时,粗碎是利用再生胶生产的粉碎设备,细碎则由四川亚西机械厂首次设计制造的齿盘粉碎机,但由于金属材料等原因,并没有彻底解决设备问题,引进国外设备又太贵。
然后,天津橡胶工业研究所和一些再生胶生产厂利用粉碎后的粗胶粉,经筛分获得的40目左右的胶粉,经活化处理,生产数量不多的活化胶粉,并在轮胎厂中得到一定的推广应用(主要用于胎侧胶),后因效果并不理想而被中止。
废橡胶循环利用方案(一)
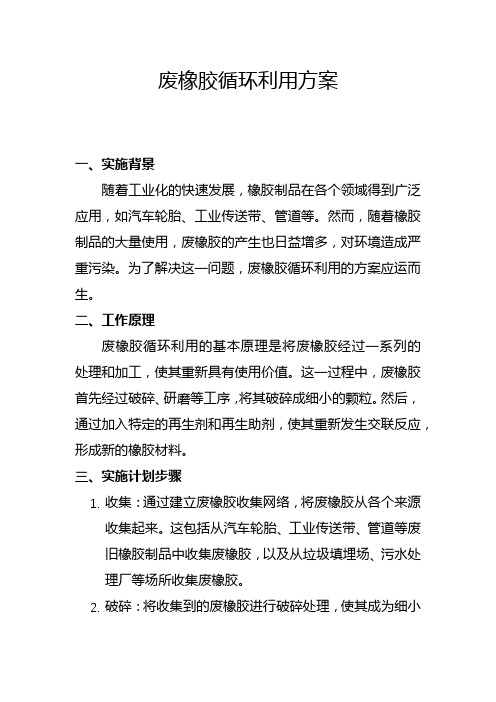
废橡胶循环利用方案一、实施背景随着工业化的快速发展,橡胶制品在各个领域得到广泛应用,如汽车轮胎、工业传送带、管道等。
然而,随着橡胶制品的大量使用,废橡胶的产生也日益增多,对环境造成严重污染。
为了解决这一问题,废橡胶循环利用的方案应运而生。
二、工作原理废橡胶循环利用的基本原理是将废橡胶经过一系列的处理和加工,使其重新具有使用价值。
这一过程中,废橡胶首先经过破碎、研磨等工序,将其破碎成细小的颗粒。
然后,通过加入特定的再生剂和再生助剂,使其重新发生交联反应,形成新的橡胶材料。
三、实施计划步骤1.收集:通过建立废橡胶收集网络,将废橡胶从各个来源收集起来。
这包括从汽车轮胎、工业传送带、管道等废旧橡胶制品中收集废橡胶,以及从垃圾填埋场、污水处理厂等场所收集废橡胶。
2.破碎:将收集到的废橡胶进行破碎处理,使其成为细小的颗粒。
这一步骤可以通过专业的破碎设备完成,也可以使用化学方法进行破碎。
3.再生:将破碎后的废橡胶颗粒与特定的再生剂和再生助剂混合,进行再生反应。
这一步骤可以通过专业的再生设备完成,也可以使用化学方法进行再生。
4.加工:将再生后的橡胶材料进行加工,使其满足各种产品的需求。
这包括将其加工成各种形状和尺寸的橡胶制品,如轮胎、管道、密封件等。
5.销售:将再生橡胶产品销售给各个行业,用于制造新的橡胶制品。
这包括将其销售给汽车制造、橡胶制品制造、轮胎制造等行业。
四、适用范围该方案适用于所有产生废橡胶的行业,如汽车制造、橡胶制品制造、轮胎制造等。
同时,也适用于那些需要使用橡胶制品的各个领域,如建筑、交通、农业等。
此外,该方案还可以适用于垃圾填埋场、污水处理厂等场所的废橡胶处理。
五、创新要点1.废橡胶的破碎技术:采用先进的破碎设备和技术,使废橡胶破碎得更加均匀和细小。
这有助于提高再生剂和再生助剂的渗透性和交联反应的效率。
2.再生剂和再生助剂的开发:通过不断研发新的再生剂和再生助剂,提高再生橡胶的性能和质量。
这有助于提高再生橡胶的耐磨性、耐油性、耐老化性等性能指标。
橡胶的循环再生

1.1 三种循环利用方法
目前国内对于废旧橡胶的循环利用主三 种方法: 1. 2. 3. 生产硫化橡胶粉法 再生橡胶法 热裂解回收法
三种方法优缺点比较
生产硫化橡胶粉法
硫化橡胶粉是以废橡胶为原料,通过机 械加工粉碎或研磨制成不同粒度的粉状物 质,简称胶粉。
目前工业化胶粉生产工艺路线主要有两 种常温法和冷冻法。
硫化橡胶粉法循环橡胶的应用
胶粉的应用概括起来可分为两大领域: 制造各种橡胶制品,可以直接用胶粉采 用不同工艺方法和配方制造橡胶制品,亦 可与其他原料橡胶并用共混制造各类橡胶 制品; 非橡胶工业的广阔领域中应用,比如用 公路工程、铁道系统、建筑工业、公用工 程、农业以及其他聚合物材料共混改性等
再生橡胶法循环橡胶的应用
ห้องสมุดไป่ตู้
热裂解回收法
将废轮胎转化为再生资源的另一种途径 是废旧轮胎热裂解回收利用,裂解后的产 品主要为油品、碳黑、可燃气体,可燃气 体可回收作为热裂解炉的加热能源,碳黑 又可以作化工生产原料。
再生胶生产是目前我国废旧轮胎再利用的主要方 法。再生胶技术早期是建立在逆向天然橡胶脱硫工 艺技术基础上,生产中的再生(脱硫)化学反应过 程会产生较严重的废气,这些酸性废气造成的环境 污染治理成本高,技术复杂。 发达国家早在上世纪 70~80 年代已停止生产再生 胶。 但我国由于历史性原因和橡胶资源长期匮乏加之 再生胶行业起步较早发展成熟,因此国内一直稳定 持续发展,目前已形成近百万吨的生产能力。
橡胶循环再生
目录 橡胶应用现状 橡胶的三种循环利用方法 回收橡胶的应用
废旧橡胶应用现状
我国废旧橡胶的利用方式主要为再生胶、 胶粉和轮胎翻新三种。目前、在我国废旧橡胶 综合利用的各种形式中,再生胶占 71.3 %, 胶粉占7.5%,轮胎翻新占 11.8%,其他形式 占 9.38%。 目前,再生胶已在胶板、垫带、内胎等制品 中获得大量应用,在农用胎等低速轮胎中再生 胶也可以与天然胶或合成胶按一定比例掺用。 胶粉改性沥青在高速公路中的应用仍处试用阶 段,热裂解技术在我国尚未成熟。
废旧橡胶循环利用与技术进展

对 物 理性 质起 到 很 强 的正面 效应 。业 已发 现 ,采 用 活 性和 非 活性 配合 剂可 改进 物 理性 质和 性 能特 征 。这将 对 发展 塑料 工业 有利 。另外 ,这 些很 小
1 回收利用现 状
产生 的废轮 胎 已有 8 .% ( 95 按质量 计 ,下 同)得 到重新 利用 。 2 0 年 的废轮胎 利用 率约为 8 %, 而 05 2
国外 废 旧橡胶 的利用 除 了轮胎翻 修外 ,主要 是制 造胶粉应 用于建筑 材料和 燃烧热 利用 。
废 旧轮 胎 的产 生 率正在 增加 ,特别 是 随着汽 车和 卡车生 产 的持续增 加 。2 0 年 ,美 国废 旧轮 09 胎 数量 约4 0 7 万吨 ,欧洲 为近3 0 吨, 日本超 过 5万
《 塑 资源 利 用 》 橡
21. 4 00 NO.
废 旧橡胶 循环 利用 与技 术进 展
C -章 ,朱 建芳 kf  ̄ ( 上海擎 督信息科 技公 司金秋 能源石化工 作室 ,上海 202 ) 0 17
摘 要 : 本 文评 述 了 国外 废 旧橡 胶 循 环 利 用 、 回 收 利 用现 状 和 回收 利 用 新技 术进 展 ,并 阐述 了 我 国废 旧橡 胶 综合 利 用现 状及 提 出 了发展 建议 。 关键 词 : 废 旧橡 胶 ;循 环 利 用 ;轮 胎翻 新 ;综合 利 用 ;世 界 ; 中国
据 美 国 《 胶 世界 》 报道 ,废 轮 胎胶 粉 用 来 橡
‘
表 12 0 0 9年 世 界 各 国 家 及 地 区 再 生胶 产 量
Hale Waihona Puke 2 回收利 用新技 术进 展 美 国 L hg e ih技 术 公司 回收 的 P lDy e轮胎 oy n 橡 胶 粉末 可用 于 制造 新 型热 塑性 塑 料和 热 固性 塑
废橡胶处理危害及处理办法

废橡胶的危害以及有效的再生方法废橡胶的处理是当今人们面临的严重问题之一。
为了满足不断提高的材料性能要求,橡胶朝着高强度、耐磨、稳定和耐老化的方向发展,但是同时造成了废弃后的橡胶长时期不能自然降解的问题,大量的废旧橡胶造成了比塑料污染(白色污染)更难处理的黑色污染。
另一方面浪费了宝贵的橡胶资源。
全世界每年有数百万吨废橡胶产生,数量如此巨大,如何对其进行有效处理已成为全社会普遍关注的问题。
为此,除将堆积如山的废弃橡胶制品当燃料焚烧外,自1910年开始,各国科学家纷纷研究更为有效的废橡胶再生处理技术。
再生胶是指废旧硫化橡胶经过粉碎、加热、机械处理等物理化学过程,使其从弹性状态变成具有塑性和粘性的、能够再硫化的橡胶。
再生过程的实质是在热、氧、机械作用和再生剂的化学与物理作用等的综合作用下,使硫化胶网络破坏降解,断裂位置既有交联键,也有交联键之间的大分子键。
橡胶再生方法大体上可以分为两类:物理再生和化学再生物理再生物理再生是利用外加能量,如力、热-力、冷-力、微波、超声等,使交联橡胶的三维网络被破碎为低分子的碎片。
除微波和超声能造成真正的橡胶再生外,其余的物理方法只能是一种粉碎技术,即制作胶粉。
当这些胶粉被用回橡胶行业时,只能作为非补强性填料来应用。
利用微波、超声等物理能量能够达到满意的橡胶再生效果,但设备要求高,能量消耗大。
常温粉碎法常温粉碎法一般是指加工温度在50士5℃或略高温度下通过机械作用粉碎橡胶制成胶粉的一种粉碎法。
低温粉碎法低温粉碎法是通过制冷介质,主要采用液氮使橡胶冷冻到玻璃化温度以下,在低温下进行粉碎的一种有效方法。
湿法或溶液粉碎法湿法或溶液粉碎法是一种在溶剂或溶液等介质中进行粉碎生产胶粉的方法。
微波再生法微波再生法是一种非化学、非机械的一步脱硫再生法。
超声波再生法阿克隆大学于l993年发明超声波再生法,此法是利用高密度能量场来破坏交联键而保留分子主链,从而达到再生的目的,超声波场可在多种介质中产生高频伸缩应力,高振幅振荡波能引起固体碎裂和液体空穴化。
废橡胶回收、再生及应用技术

废橡胶回收、再生及应用技术-标准化文件发布号:(9456-EUATWK-MWUB-WUNN-INNUL-DDQTY-KII最新废橡胶材料回收、再生及应用技术综述一、废橡胶回收与再利用的目的和意义可持续发展的必然要求:自自1992年联合国制定《21世纪议程》以来,世界各国都在采取行动促进可持续发展战略的实施,可持续发展已成为世界各国共同追求的目标。
2003年中共十六届三中全会提出了“以人为本,全面、协调,可持续发展”的科学发展观,这标志着我国的发展战略有了重大调整,步入了一个全新的发展阶段。
近五十多年来,石油化工异军突起,合成树脂、合成纤维、合成橡胶等三大合成材料迅猛发展。
同时,也带来了污染问题。
大量废弃的高分子材料制品散落在社会上,形成“白色污染”、“黑色污染”,极大地污染环境,侵占有用土地,损害人体健康。
废橡胶的堆积占用土地,污染环境。
废轮胎堆积在一起还会滋生蚊虫、细菌,不但损害居民健康,而且易引起火灾,燃烧导致的污染使周围寸草不生,生态环境造成极大的危害。
要实现我国在本世纪中叶人均国民生产总值达到中等发达国家水平的第三步战略目标,其关键之一是保证“生态环境的良性循环”。
从石化资源的供给角度,世界石油资源日益枯竭。
我国是石油消耗大国,“九五”期间已成为石油净进口国。
以石油为主要原料的合成橡胶以及主要补强材料——炭黑的发展必然随着石油的枯竭而受到极大影响。
在能源相当紧缺的今天,回收利用废橡胶具有重大的意义。
为了可持续发展、充分利用资源和保护环境,发达国家对回收利用废胶十分重视,较早走上了法制轨道,并建立了一整套符合市场经济规律的回收利用管理办法。
欧盟的芬兰回收利用率达100%;美国1996年的废胶回收利用率为75.9%,废轮胎的利用率超过90%;目前日本废胶回收利用率接近90%。
中国:一个橡胶应用大国,2004年共消耗生胶450万吨,居世界第一位,轮胎产量超过2.3亿条。
报废的轮胎4000~600万条,加上胶管、胶带、胶鞋到及其他橡胶制品,废橡胶年产生量近300万吨/年。
废橡胶再生利用技术

废橡胶再生利用技术一、概述橡胶属于热固性的聚合物材料,在自然条件下很难发生降解,弃于地表或被埋十几年都不腐烂。
我国是一个橡胶消费大国,2006年共消耗生胶超过5300kt,超过美国,居世界第一位。
每年产生的废橡胶800~1000kt。
如此大量的废橡胶,若不及早处理,除了污染环境外还是资源的极大浪费。
同时我国又是一个生胶资源短缺的国家,几乎每年生胶消耗量的45%左右需要进口,而且这种情况短时期内不会有根本的转变,所以如何解决橡胶原料来源及代用材料是十分迫切的任务。
人类社会进入21世纪,面临的主要问题之一就是废橡胶的处理及其再生利用。
目前,废橡胶制品是除废旧塑料外居第二位的废旧聚合物材料,它主要来源于废轮胎、胶管、胶带、胶鞋、密封件、垫板等工业制品,其中以废旧轮胎的数量最多,此外还有橡胶生产过程中产生的边角料。
进入20世纪70年代以后,随着科技的发展,人们发现回收利用废橡胶可以节约生产合成橡胶所消耗的大量原油,开始把废橡胶称为“新型黑色黄金”(new black gold),千方百计设法回收利用,或者作为橡胶、塑料的填充材料,或者单用胶粉生产橡胶制品,从而开辟了废橡胶利用的新时代。
从各个方面来讲,在能源相对紧缺的今天,回收利用废橡胶都具有十分重大的意义。
二、废橡胶的回收利用技术废旧橡胶制品以废旧轮胎为最多,其次为管、带、内胎、密封件、垫板、鞋底等。
以废轮胎为主的废旧橡胶处理方法主要有轮胎翻新、生产胶粉、再生胶、热分解和热能利用等。
(一)轮胎翻新轮胎翻新具有较好的经济效益,旧轮胎翻新后其使用寿命一般为新轮胎使用寿命的60%~90%,平均行驶里程为5万~8万km。
当前世界名牌载重轮胎一般都可以翻新二三次,并且翻新轮胎的使用寿命接近于新轮胎,而翻新轮胎所用的原材料一般为新轮胎的15%~30%,可节约大量橡胶、帘布和炭黑等材料,其价格仅为新轮胎的25%~50%,因此,翻新轮胎是废轮胎利用的最有效方式。
目前轮胎翻新已经实现工业化,主要集中在载重轮胎和轿车轮胎,轮胎翻新量大约是轮胎报废量的22%。
昆山废橡胶垃圾处置方案

昆山废橡胶垃圾处置方案
背景和现状
随着工业化的发展,废橡胶垃圾的问题越来越突出。
据昆山市环境保护局统计,全市每年产生的废橡胶垃圾约为2000吨,其中大部分是来自制造和加工行业。
废橡胶垃圾的处理不仅涉及到环境保护,还涉及到资源的利用。
目前,昆山市
政府正在积极推进废物资源化利用的工作,寻找可行的废橡胶垃圾处置方案,推动市级的废物资源化利用。
方案
经过多年的研究和试验,我们提出了以下几个方案:
1.橡胶粉碎再生方案
该方案采用机械粉碎的方法,将废橡胶垃圾切割成小块或细粉,然后通过加工、制造等方式再生为橡胶制品。
这种方法不仅能够有效地减少废橡胶垃圾的堆积量,而且还能够节约资源和降低制造成本。
2.橡胶热解方案
这种方案采用高温热解技术,将废橡胶垃圾转化为可再利用的物质,如热解油、炭黑等。
这种方法可以有效地实现废物资源的再利用,同时降低对环境的污染,具有非常高的使用价值。
3.橡胶焚烧方案
这种方案是将废橡胶垃圾进行焚烧处理,将其转化为热能进行利用。
虽然能够
有效减少废物量,但是会对环境造成一定的污染,因此需要在技术上加以改进。
结论
经过对以上三种方案的比较和分析,我们发现复合利用方案是最佳选择。
通过
机械粉碎的方式将废橡胶垃圾初步处理成小块或细粉,然后运用高温热解技术,把废橡胶垃圾热解成油、炭黑和其他可再利用的材料。
而这些物质可以作为再生原料制造新的橡胶制品,既保护环境,也实现了资源的循环利用。
- 1、下载文档前请自行甄别文档内容的完整性,平台不提供额外的编辑、内容补充、找答案等附加服务。
- 2、"仅部分预览"的文档,不可在线预览部分如存在完整性等问题,可反馈申请退款(可完整预览的文档不适用该条件!)。
- 3、如文档侵犯您的权益,请联系客服反馈,我们会尽快为您处理(人工客服工作时间:9:00-18:30)。
4.总结
目前对于废橡胶的循环利用的三种方法各有优缺点,并且在各个国家和地区的使用情况也不尽相同。⒀
废橡胶资源循环利用是典型的发展循环经济的范例,中国作为世界橡胶大国,应该在遵循低碳经济的发展道路上做出应有的贡献。目前轮胎资源循环利用已经被列为《国家鼓励发展的资源节约综合利用和环境保护技术目录》之中,可以相信,我国的轮胎资源循环利用必将出现一个新的快速发展的局面。⒁
目前国内对于废旧橡胶的循环利用主要有三种方法:
生产硫化橡胶粉、再生橡胶和热裂解回收利用。
1.硫化橡胶粉法
硫化橡胶粉是以废橡胶为原料,通过机械加工粉碎或研磨制成不同粒度的粉状物质,简称胶粉。它依据废橡胶来源不同和加工成粉末的粒度不同,分很多品种和牌号,是重要的橡胶回收利用材料。
胶粉工业是废橡胶综合利用产业的一个重要分枝,在我国始于上世纪八十年代后期。目前工业化胶粉生产工艺路线主要有两种:
目前,我国废斜交轮胎大部分还是用于生产再生胶。虽然再生胶为缓解橡胶资源缺乏和供需矛盾紧张做出过巨大贡献,但全国500多家再生胶企业中万吨以上生产能力的只有大约40家,90%以上的企业属于小型加工企业,技术水平落后、设备陈旧,环境污染严重。随着环境保护要求的提高和管理力度的加强,国家会进一步淘汰二次污染严重、能源消耗高的小再生胶生产。目前我国产量在万吨以上的再生胶厂经过近几年的技术改造,采用动态脱硫法进行生产,环境污染问题有所缓解。例如国内江苏强维橡塑、福建环科橡胶、四川万成橡胶、河北兴宇橡胶等再生胶企业积极组织再生胶新技术、新工艺、新设备和新材料的开发与应用,对解决生产过程中的环境污染起到了积极的作用。这些企业的产品各项性能指标比传统加工工艺有很大提高,可部分直接代替天然橡胶或合成橡胶,并获得了良好的经济效益和社会效益。其中加压捏炼法丁基胶脱硫再生新工艺、高品质再生胶及其制备技术、高品质精细轮胎再生胶等技术分别通过了省部级科技成果鉴定,代表着再生胶的发展方向。⑼
对于子午线轮胎,青岛黄海集团研究了将80目常温全胎胶粉用于半钢子午胎胎侧胶中,掺用5~8PHR,结果表明,硫化胶拉伸性能略有降低,但耐屈挠性和耐热空气老化性能提高,综合性能与未加胶粉的硫化胶相近,且可降低成本。但我国目前尚未进行深入研究,胶粉还未普遍应用。值得指出的是,米其林公司已将10%的胶粉用于轮胎生产中,并已成功安装于Ford汽车上,表明轮胎能够满足当前的行驶安全和性能要求。⑺
2.再生橡胶法
再生胶生产是目前我国废轮胎再利用的主要方法。再生胶技术早期是建立在天然橡胶逆向化学脱硫工艺技术基础上,生产中的再生(脱硫)化学反应过程会产生较严重的废气,这些酸性废气造成的环境污染治理成本高,技术复杂。发达国家早在上世纪70~80年代已停止生产再生胶,很多国家将再生胶列为有二次污染和能耗高的淘汰产品,加以限制。但我国由于历史性原因和橡胶资源长期匮乏,加之再生胶行业起步较早发展成熟,因此国内一直稳定持续发展,目前已形成近百万吨的生产能力。⑻
可将废旧橡塑进行粉碎或熔融回收,再进行加工二次使用;或将废旧橡塑材料进行化学改性,应用于建筑材料和道路保温材料中。废旧橡塑改性材料因价格低廉、性能优良而具有广泛的应用前景。随着塑料制品消费量不断增大,废弃塑料也不断增多。目前我国废弃塑料主要为塑料薄膜、塑料丝及编织品、泡沫塑料、塑料包装箱及容器、日用塑料制品、塑料袋和农用地膜等。塑料包装消费量2004年为
常温粉碎——废钢丝胎处理实现工业化
近年来,国内多家企业在废旧橡胶粉碎尤其在废钢丝胎常温粉碎方面有了突破性进展,大大推动了再生胶及胶粉工业的发展。其中,浙江绿环橡胶粉工程公司自主开发的年处理
1.5万吨全钢废子午胎粉碎生产线,采用3项自有专利技术,工艺稳定,噪音低,无污染。常州三橡机械有限公司开发的低功率节能粉碎机系列产品,为废旧橡胶综合利用提供了节能创效的新设备。江阴台联超细胶粉厂是国内第一家从事常温精细胶粉设备研制的企业,1996年即通过了江苏省鉴定,其xz-300型常温超细橡胶粉碎机填补了国内空白。⒇
胶粉的应用概括起来可分为两大领域:
一是回归到橡胶工业作为原料用于制造各种橡胶制品,可以直接用胶粉采用不同工艺方法和配方制造橡胶制品,亦可与其他原料橡胶并用共混制造各类橡胶制品;二是在非橡胶工业的广阔领域中应用,比如用公路工程、铁道系统、建筑工业、公用工程、农业以及其他聚合物材料共混改性等。⑸
胶粉可以添加在原料橡胶中用于制造各种橡胶制品,达到节约原料橡胶、减少进口、降低橡胶制品成本和改善性能的多重效果。一般来说,当未经处理的粗胶粉加入到橡胶制品中,会提高体系的粘度,降低拉伸强度,这些因素致使橡胶制品只能用于非技术场合,如地板材料、胶垫和鞋类。因此,对性能要求较高的制品,胶粉必须要有较小的粒度并经过活化处理。⑹废Biblioteka 胶的循环利用技术应化113xx
摘要:
废旧橡胶主要来源于废弃橡胶制品,其次来自橡胶工厂生产过程中产生的边余料和废品。废橡胶是六大固态再生资源之一,其无害化资源化再利用一直是世界各国积极研究的一个重要课题。
关键词无害化资源化再利用
科学技术的发展使得橡胶和塑料在工农业生产中得到越来越广泛的应用。但是橡塑材料的应用伴随着大量废旧橡胶塑料的堆积,如处理不得当就会给环境带来严重污染,同时也造成了资源的浪费。废旧橡塑材料可进行再生循环利用:
随着我国能源紧张状况的进一步加剧和能源价格的不断上涨,近年来利用废旧轮胎土法炼油在全国蔓延,一部分企业和个人采用简单的砖砌式热解炉将废轮胎烧熔,用钢管引流出液体沉淀后作为锅炉燃油,甚至掺入加油站的成品油中坑害消费者。土法炼油不完全燃烧产生的有毒有害气体和沉淀的油渣造成严重的环境污染,炼油场地周边土壤、地表和地下水遭到严重破坏。一个土法炼油加工点每年烧掉2万t左右的废旧轮胎,是一种极大的浪费,因此必须加以遏制。采用先进的废轮胎高温热裂解工艺技术及成套设备才是替代土法炼油、保护环境、提高轮胎橡胶资源利用率的有效手段。⑾
3.废轮胎热裂解回收利用法
将废轮胎转化为再生资源的另一种途径是废轮胎热裂解回收利用,裂解后的产品主要为油品、碳黑、可燃气体,可燃气体可回收作为热裂解炉的加热能源,碳黑又可以作化工生产原料。目前,上海绿人生态经济科技有限公司和济南友邦恒誉科技开发有限公司自主开发的废轮胎热裂解生产装臵已经成功出口到台湾地区,并在当地形成生产能力。如果能够达到油品无残留硫、尾气排放达到环保要求、产品的市场经济性可行,将为我国废轮胎橡胶(包括危险橡胶废弃物)的最终处臵开拓一种很好的资源化处理方法。⑽
我国在"八五"期间,由于当时的液氮价格昂贵,因此把航空系统的涡轮膨胀空气制冷技术移植到胶粉工业上来,冷冻温度可达到-130℃,但终因成本偏高等原因而未能推广。1999年青岛绿叶橡胶有限公司与珠海业精机电研究所、青岛化工学院联合研发出我国第一条利用液氮冷冻法生产微细胶粉生产线,但由于设备尚需完善等原因未能进一步深入研究,目前中海油则开展了此项目建设。
动态脱硫法再生胶生产技术和废旧轮胎的常温粉碎技术。目前,这两项技术均居世界领先水平。技术创新,自主开发已经成为行业发展的主流。⒃
动态脱硫——废旧橡胶生产工艺的革命
1990年以前,国内再生胶生产基本停留在油法、水油法等技术水平上,生产工艺、装备几十年不变。其中,油法因产品质量低,生产不稳定而逐渐被淘汰;而水油法工艺虽优于油法,但生产中产生大量工业废水严重污染环境。随着社会对环保要求的提高以及废橡胶中合成胶比例的增加,水油法生产再生胶污染严重、能源消耗高、生产效率低等弊端,已经成为阻碍废旧橡胶综合利用行业发展的瓶颈,国家明令规定禁止再建新厂。⒄
在再生胶行业发展面临何去何从的关键时刻,1990年,原化工部橡胶司和中国橡胶工业协会根据对国外再生胶工艺的考察,并结合国内生产现状,果断决定在行业内开展废旧橡胶动态脱硫新工艺技术的攻关试验,并由当时的合肥环球橡胶总厂、沈阳再生胶总厂和天津再生胶厂共同承担。1991年,该项目被列入化工部科技攻关项目;1992年,该项目又被列入国家科委星火计划项目。经过3年多的攻关,废旧橡胶动态脱硫新工艺技术开发成功,并于1994年通过了原化工部科技鉴定。废旧橡胶动态脱硫新工艺技术彻底改变了我国落后的、污染严重的再生胶生产工艺,推动了废旧橡胶综合利用行业的再次发展,同时,这项技术还走出了国门。⒅
三明环科化工橡胶有限公司研制的塔式回流工艺尾气净化系统,使含矿物焦油的再生胶实现无味生产。
(22)
目前,行业内年产5000吨以上的废旧橡胶企业对脱硫尾气基本上采用物理法、生物法及自行改造的办法,二次污染基本得到了有效治理。
(23)废橡胶综合利用,是橡胶工业充分利用和节约资源的有效途径,也是实施科学发展和循环经济的重要内容之一,同时对解决我国橡胶资源短缺也具有重要意义。
据检测,废旧橡胶动态脱硫新工艺技术生产的再生胶,产品性能稳定,质量可靠,各项物化指标均达到国家标准。与水油法相比,简化了工艺,减少了投资。
当时测算,全国再生胶总产量为30万吨左右,如采用该技术,每年可节电9516万千瓦时,节水552万吨,节煤
8.18万吨,直接节约成本
4793.4万元。
目前,我国再生胶生产已基本采用动态脱硫工艺。⒆
作为对有限的橡胶资源的补充和对废旧橡胶的利用,废橡胶综合利用行业的历史源远流长。尤其是新中国建立以后,在资源紧缺的计划经济时代,我国曾经有过用20吨大米换取1吨进口天然胶的历史,那时再生胶也被作为三类战略物资受到高度重视。⒂
我国废旧橡胶的综合利用主要是生产再生胶和胶粉。支撑这一产业发展的是我国具有独立知识产权的自主创新技术:
四川双流天利民橡胶有限公司的一次性常温精细粉碎机,单机台时80目胶粉产量达到300千克以上,耗电仅为400千瓦时,是废斜交胎、废丁基胶囊、废三元乙丙胶等精细粉碎的节能机型。
(21)
环保治理——提高行业整体形象
在废旧橡胶再生产中,由于其脱硫过程中硫化氢恶臭和生产中尾气排放不达标,造成二次污染,严重影响了其作为环保产业的形象。由江西国燕橡胶有限公司2002年研制成功的物理法再生胶工艺尾气治理装臵,彻底改变了困扰行业多年的恶臭和脱硫尾气治理问题。经治理后的恶臭等级低于国家标准1万倍,且无苯系物气体排放,回收利用尾气作为燃料,再次节省了能源,降低了生产成本。