浅谈小直径筒体焊接
浅谈小管径常见缺陷分析与识别
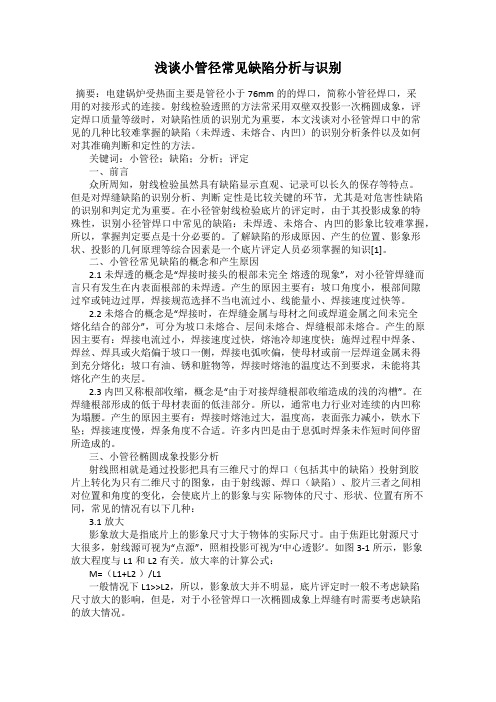
浅谈小管径常见缺陷分析与识别摘要:电建锅炉受热面主要是管径小于76mm的的焊口,简称小管径焊口,采用的对接形式的连接。
射线检验透照的方法常采用双壁双投影一次椭圆成象,评定焊口质量等级时,对缺陷性质的识别尤为重要,本文浅谈对小径管焊口中的常见的几种比较难掌握的缺陷(未焊透、未熔合、内凹)的识别分析条件以及如何对其准确判断和定性的方法。
关键词:小管径;缺陷;分析;评定一、前言众所周知,射线检验虽然具有缺陷显示直观、记录可以长久的保存等特点。
但是对焊缝缺陷的识别分析、判断定性是比较关键的环节,尤其是对危害性缺陷的识别和判定尤为重要。
在小径管射线检验底片的评定时,由于其投影成象的特殊性,识别小径管焊口中常见的缺陷:未焊透、未熔合、内凹的影象比较难掌握,所以,掌握判定要点是十分必要的。
了解缺陷的形成原因、产生的位置、影象形状、投影的几何原理等综合因素是一个底片评定人员必须掌握的知识[1]。
二、小管径常见缺陷的概念和产生原因2.1 未焊透的概念是“焊接时接头的根部未完全熔透的现象”,对小径管焊缝而言只有发生在内表面根部的未焊透。
产生的原因主要有:坡口角度小,根部间隙过窄或钝边过厚,焊接规范选择不当电流过小、线能量小、焊接速度过快等。
2.2 未熔合的概念是“焊接时,在焊缝金属与母材之间或焊道金属之间未完全熔化结合的部分”,可分为坡口未熔合、层间未熔合、焊缝根部未熔合。
产生的原因主要有:焊接电流过小,焊接速度过快,熔池冷却速度快;施焊过程中焊条、焊丝、焊具或火焰偏于坡口一侧,焊接电弧吹偏,使母材或前一层焊道金属未得到充分熔化;坡口有油、锈和脏物等,焊接时熔池的温度达不到要求,未能将其熔化产生的夹层。
2.3 内凹又称根部收缩,概念是“由于对接焊缝根部收缩造成的浅的沟槽”。
在焊缝根部形成的低于母材表面的低洼部分。
所以,通常电力行业对连续的内凹称为塌腰。
产生的原因主要有:焊接时熔池过大,温度高,表面张力减小,铁水下坠;焊接速度慢,焊条角度不合适。
小口径管道焊接
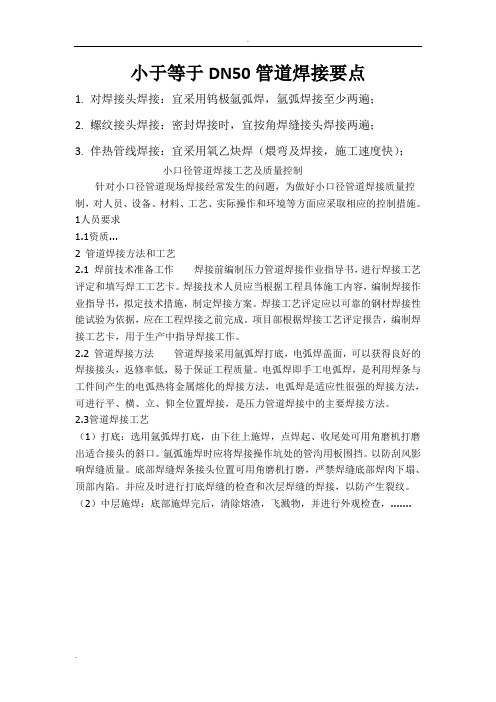
小于等于DN50管道焊接要点1.对焊接头焊接:宜采用钨极氩弧焊,氩弧焊接至少两遍;2.螺纹接头焊接:密封焊接时,宜按角焊缝接头焊接两遍;3.伴热管线焊接:宜采用氧乙炔焊(煨弯及焊接,施工速度快);小口径管道焊接工艺及质量控制针对小口径管道现场焊接经常发生的问题,为做好小口径管道焊接质量控制,对人员、设备、材料、工艺、实际操作和环境等方面应采取相应的控制措施。
1人员要求1.1资质...2 管道焊接方法和工艺2.1 焊前技术准备工作焊接前编制压力管道焊接作业指导书,进行焊接工艺评定和填写焊工工艺卡。
焊接技术人员应当根据工程具体施工内容,编制焊接作业指导书,拟定技术措施,制定焊接方案。
焊接工艺评定应以可靠的钢材焊接性能试验为依据,应在工程焊接之前完成。
项目部根据焊接工艺评定报告,编制焊接工艺卡,用于生产中指导焊接工作。
2.2 管道焊接方法管道焊接采用氩弧焊打底,电弧焊盖面,可以获得良好的焊接接头,返修率低,易于保证工程质量。
电弧焊即手工电弧焊,是利用焊条与工件间产生的电弧热将金属熔化的焊接方法,电弧焊是适应性很强的焊接方法,可进行平、横、立、仰全位置焊接,是压力管道焊接中的主要焊接方法。
2.3管道焊接工艺(1)打底:选用氩弧焊打底,由下往上施焊,点焊起、收尾处可用角磨机打磨出适合接头的斜口。
氩弧施焊时应将焊接操作坑处的管沟用板围挡。
以防刮风影响焊缝质量。
底部焊缝焊条接头位置可用角磨机打磨,严禁焊缝底部焊肉下塌、顶部内陷。
并应及时进行打底焊缝的检查和次层焊缝的焊接,以防产生裂纹。
(2)中层施焊:底部施焊完后,清除熔渣,飞溅物,并进行外观检查,.......小口径管道焊接工艺及质量控制针对小口径管道现场焊接完成后,在试压及使用过程中经常发生“跑、冒、滴、漏”等现象,为做好小口径管道焊接质量控制,预防此类现象发生。
现对焊接施工过程中人员、设备、材料、工艺、实际操作和环境等方面制定相应的控制措施,以便为公司范围内工程施工和检修施工等所有小口径管道焊接作业提供技术支持。
筒体焊接工艺分析
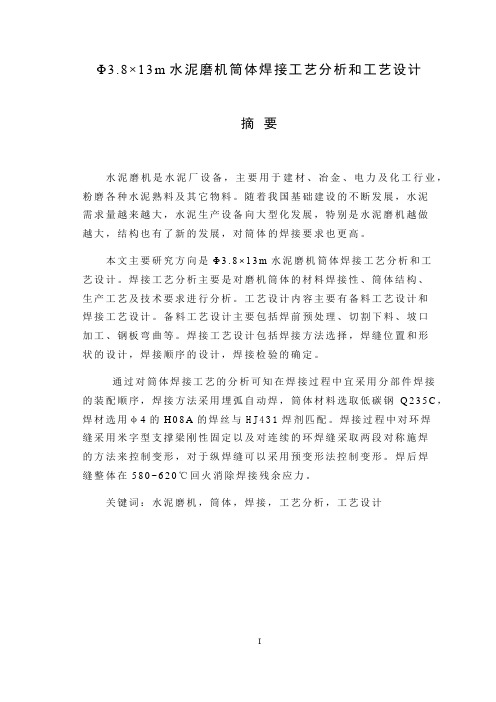
Φ3.8×13m水泥磨机筒体焊接工艺分析和工艺设计摘要水泥磨机是水泥厂设备,主要用于建材、冶金、电力及化工行业,粉磨各种水泥熟料及其它物料。
随着我国基础建设的不断发展,水泥需求量越来越大,水泥生产设备向大型化发展,特别是水泥磨机越做越大,结构也有了新的发展,对筒体的焊接要求也更高。
本文主要研究方向是Φ3.8×13m水泥磨机筒体焊接工艺分析和工艺设计。
焊接工艺分析主要是对磨机筒体的材料焊接性、筒体结构、生产工艺及技术要求进行分析。
工艺设计内容主要有备料工艺设计和焊接工艺设计。
备料工艺设计主要包括焊前预处理、切割下料、坡口加工、钢板弯曲等。
焊接工艺设计包括焊接方法选择,焊缝位置和形状的设计,焊接顺序的设计,焊接检验的确定。
通过对筒体焊接工艺的分析可知在焊接过程中宜采用分部件焊接的装配顺序,焊接方法采用埋弧自动焊,筒体材料选取低碳钢Q235C,焊材选用φ4的H08A的焊丝与H J431焊剂匹配。
焊接过程中对环焊缝采用米字型支撑梁刚性固定以及对连续的环焊缝采取两段对称施焊的方法来控制变形,对于纵焊缝可以采用预变形法控制变形。
焊后焊缝整体在580~620℃回火消除焊接残余应力。
关键词:水泥磨机,筒体,焊接,工艺分析,工艺设计Welding P ro cedu re An alysis an d Pro cedu re Des ign fo r th e b arrel of Φ3.8×13m C e men t millABS TR AC TC e m e n t g r i n d i n g m a c h i n e i s c e m e n t p l a n t e q u i p m e n t, m a i n l y u s e d i n b u i l d i n g m a t e r i a l,m e t a l l u r g y,e l e c t r i c p o w e r a n d c h e m i c a l i n d u s t r y,g r i n d i n g v a r i o u s c e m e n t c l i n k e r a n d o t h e r m a t e r i a l s.Wi t h C h i n a's i n f r a s t r u c t u r e d e v e l o p m e n t,t h e d e m a n d t o c e m e n t i s m o r e a n d m o r e s t r i c t a n d t h e c e m e n t p r o d u c t i o n e q u i p m e n t i s d e v e l o p i n g t o t h e l a r g e-s c a l e.E s p e c i a l l y c e m e n t g r i n d i n g m a c h i n e i s b i g g e r a n d b i g g e r. S t r u c t u r e s h a v e t h e n e w d e v e l o p m e n t o f t h e c y l i n d e r b o d y w e l d i n g r e q u i r e m e n t s a r e a l s o h i g h e r.To g e t t h e r e l i a b l e q u a l i t y a n d t h e g o o d p e r f o r m a n c e o f c e m e n t g r i n d i n g m a c h i n e, w e s h o u l d a n a l y s i s w e l d i n g p r o c e s s a n d t o w o r k o u t t h e r e a s o n a b l e w e l d i n g p r o c e s s.W h a t t h i s a r t i c l e s t u d i e s a r e w e l d i n g p r o c e s s a n a l y s i s a n d t h e w e l d i n g p r o c e s s d e s i g n f o r t h e b a r r e l o fΦ3.8×13m c e m e n t m i l l.A n a l y s i s o f w e l d i n g t e c h n o l o g y a r e m a i n l y t h e a n a l y s i s o f t h e m a t e r a l’s w e l d a b i l i t y,t h e a n a l y s i s o f b a r r e l s t r u c t u r e p r o c e s s a n d t h e a n a l y s i s o f t h e t e c h n i c a l c o n d i t i o n a n d p r o d u c t i o n p r o c e s s e s.T h e p r o c e s s d e s i g n c o n t a i n s t h e d e s i g n o f p r e p a r a t i o n p r o c e s s a n d w e l d i n g p r o c e s s.T h e d e s i g n o f w e l d i n g p r o c e s s c o n t a i n s t h e s e l e c t i o n o f w e l d i n g m e t h o d,t h e d e s i g n o f g r o o v e,t h e d e s i g n o f w e l d p o s i t i o n a n d s h a p e,t h e d e s i g n o f w e l d i n g s e q u e n c e a n d t h e c h e c k o f w e l d.T h r o u g h t o t h e a n a l y s i s o f t h e c y l i n d e r b o d y w e l d i n g p r o c e s s t h a t t h e w e l d i n g p r o c e s s o f a p p r o p r i a t e t h e w h o l e a s s e m b l y-w e l d i n g a s s e m b l y s e q u e n c e,w e l d i n g m e t h o d a d o p t s a u t o m a t i c s u b m e r g e d a r c w e l d i n g,w e l d i n g m a t e r i a l s e l e c t i o n o fφ4H08A w e l d i n g w i r e a n d H J431f l u x.We l d i n g p r o c e s s t o r i n g t h e s u p p o r t b e a m w e l d i n g r i g i d l y c o n t r o l d e f o r m a t i o n,t o v e r t i c a l w e l d s c a n u s e t h e m e t h o d o f d e f o r m a t i o n c o n t r o ld e f o r m a t i o n.A f t e r w e l d i n g w e s h o u l d o v e r a l l a n n e a l i n ge l i m i n a t e w e l d i n g r e s i d u a l s t r e s s.K E Y W R O D S:C e m e n t g r i n d i n g m a c h i n e,c y l i n d e r,w e l d i n g, p r o c e s s a n a l y s i s a n d p r o c e s s d e s i g n目录第一章绪论 (1)§1.1水泥磨机的发展现状 (1)§1.2水泥磨机的简介 (1)§1.3本文研究内容 (2)第二章Φ3.8×13m水泥磨机筒体生产工艺分析 (4)§2.1筒体材料的焊接性分析 (4)§2.2筒体焊接的结构工艺性分析 (8)§2.2.1结构工艺性分析 (8)§2.2.2焊接变形的分析、控制及矫正 (9)§2.3备料工艺分析 (12)§2.3.1钢材的预处理 (13)§2.3.2放样、划线与号料 (15)§2.3.3切割下料 (15)§2.4技术要求分析 (18)§2.4.1筒体部技术要求 (18)§2.5焊接工艺分析 (20)§2.5.1焊接生产装配工艺分析 (20)§2.5.2焊接方法分析 (22)§2.5.3焊接材料分析 (24)§2.5.4焊接工艺参数分析 (26)§2.5.5焊前预热及焊后热处理 (27)§2.6焊接检验 (28)第三章Φ3.8×13m水泥磨机筒体焊接工艺设计 (29)§3.1备料工艺设计 (29)§3.2焊接工艺设计 (30)§3.2.1焊接方法确定 (30)§3.2.2焊接材料的选择 (30)§3.2.3焊接工艺参数的选择 (30)§3.2.4焊接坡口形式的设计 (31)§3.2.5焊缝位置和尺寸的确定 (32)§3.2.6焊接顺序和焊接层数的选择 (32)§3.3热处理工艺和检验方法的设计 (32)结论 (33)参考文献 (34)致谢 (35)第一章绪论§1.1水泥磨机的发展现状水泥磨机作为传统的水泥厂设备,已有了100多年的历史。
X射线照相法检测小直径筒体环焊缝横向裂纹特点分析

X射线照相法检测小直径筒体环焊缝横向裂纹特点分析【摘要】文章分析了X射线照相法检测小直径筒体环焊缝横向裂纹特点,在结合了试验与理论的基础上,对确保检出横向裂纹的小直径的筒体环焊缝,论述了X射线照相法中,必须按照标准严格执行透照厚度比K值的规定,为确保检出横向裂纹,采用了减少曝光次数以及表面探伤的方法。
【关键词】横向裂纹小直径X射线通过加压或加热,亦或者两者并用,且不采用填充材料,促使工件的材质达到原子间结合,最终形成永久性连接的工艺过程为焊接。
按照相关规定与标准,针对小直径的钢管或筒体环焊缝,应以达到焊缝透照厚度比K值为基准,来设计每次曝光所检验的焊缝长度。
在透照环焊缝时,如果采用外透法,为了确保对横向裂纹的检出率,应达到透照厚度比K值所需要的最少曝光次数,在透照时,对于环焊缝增加了相应的拍片数量,最终从很大程度上增加了费用以及检测所需的工作量。
对于直径较小的钢管或筒体环焊缝而言,有效评片范围应以黑度、灵敏度等符合标准规定的因素为准,采用不受标准中K值限定的值,在此基础上辅以渗透检测或表面检测,可以检出对横向裂纹。
但这一会对产品的质量造成影响,增加横向裂纹漏检率。
1 裂纹类型焊缝裂纹类型多种多样,具体有:焊缝根部裂纹、热影响区焊缝贯穿裂纹、焊趾裂纹、焊缝内部晶间裂纹、焊道下裂纹、火口裂纹、热影响区横向裂纹、热影响区纵向裂纹、焊缝上横向裂纹、焊缝中纵向裂纹。
2 分析理论检测的承压小直径壳体的上下各有两件与筒体对接焊接的变形法兰,从而形成了2跳环焊缝,其壁厚为5.5毫米,内径为110毫米,对于内径尺寸较小的工件而言,以减轻人工劳动强度、将检测周期缩短的方式来进行透照。
透照时采用五段外照法,检测工艺的规定为1000毫米。
根据标准规定,在选择AB级时,按照射线照相直来那个要求,经过计算能够得出,透照厚度比K为1.1,如果要想达到该透照度,应最少进行九次透照。
裂纹自身特性参数决定了裂纹的检出率。
裂纹自身的参数例如裂纹宽度或开口尺寸,裂纹的自身高度为,裂纹的埋藏深度为,裂纹平面对射线束的倾角为,走向为,长度为。
小直径管件水平固定氩电联焊

小直径管件水平固定氩电联焊手工钨极氩弧焊在操作过程中,熔孔的大小和熔池的形状容易控制,根部焊缝成形美观,易于获得良好的探伤成绩。
小直径管件对接水平固定氩电联焊是技术等级考试及技能比赛中的一个重要的考核项目,能熟练掌握这项技术,对每名焊工来说是提高技能水平、走向成熟的硬件标准。
在这里将小直径管件水平固定氩电联焊的认识与心得整理出来,和大家共同交流。
当前白酒国际化热潮持续升温的形势下,要想突破中国白酒仍旧面临的阻碍,不管是名优酒企还是中小酒企,切不可各自为阵、单打独斗。
在国际酒业市场上,中国白酒企业应该抱团发展,依托中国白酒品牌伞,打好白酒的“文化牌”和“标准牌”,开启中国白酒国际化的新征程。
1.焊前准备管件材质为20钢,规格为φ60mm×5mm×100mm,坡口角度30°±2.5°(见图1)。
将管件坡口20mm范围的内外表面清理干净,坡口钝边留0.5~1mm。
氩气纯度>99.7%,喷嘴孔径8~10mm,采用φ2.5mm的铈钨极,端头磨成锥形,钨极伸出长度5mm左右。
焊丝采用H08Mn2SiA,焊条采用E5015,直径均为2.5mm,焊条按规定时间和温度烘干后,放入保温筒中备用。
图1 管件加工示意2.组对及定位焊管件组对间隙:仰焊部位2.5mm,平焊部位3mm左右。
在管件钟表的2点和10点位置进行定位焊接,定位焊缝的长度为5mm左右。
定位焊后,将定位焊缝两端加工成斜坡形,以便于接头操作。
焊接参数如附表所示。
欧美国家的法律法规都是比较健全,十分完善的。
如果游客遇到问题,首先要进行及时的有效沟通。
大哭大闹不但不能解决问题,反而会引发不必要的麻烦。
比如美国等一些国家,是不禁止使用枪支的,可能会造成人身伤害。
3.打底层的操作(1)操作技巧及焊接角度焊接操作时,为增强操作稳定性,可将焊枪喷嘴的外边缘顶在管件坡口内侧作为支点,左右摆动焊枪,沿着管件坡口向前匀速移动焊接。
小口径钢管的焊接工艺及操作技术

小口径钢管的焊接工艺及操作技术改进型的9Cr-1Mo钢即SA213T91(以下简称T91)钢,现在国外各种300MWA1000MW 亚临界及超临界电力机组中正得到越来越多的应用. T91钢是一种改进型马氏体耐热钢,该材料具有良好的高温热强性和抗氧化性能,与其他合金耐热钢(如 2.25Cr-1Mo、钢102等)相比,在同样的温度、压力条件下,钢管壁厚可大大降低,材料可大大节省. T91小口径钢管主要应用于各种大型电站锅炉及燃气轮机锅炉的再热器、过热器等承受高温高压(蒸汽温度580〜650?E,蒸汽压力10MPa以上)的电力机组部件,由于T91合金元素含量很高,导致该材料可焊性很差,为满足我国不断增加的对提高电站效率和环境保护的需求,为适应我国电力工业向大电站、大机组发展的趋势,我们对T91小口径钢管的焊接进行了先期的探索和试验,并形成了一套完整的焊接工艺及操作技术规范.1焊接性分析1.1T91钢的特点T91钢属于9Cr-1Mo-V-Cb钢种•是在9Cr-1Mo的基础上添加V、Cb等碳化物元素,并采用真空脱氧,炉外精炼,在1040〜1060?C正火空冷+760〜780?E回火后得到单相马氏体组织•该钢材具有良好的高温热强性和抗氧化性能,其化学成份见表1.T91谢的血械性腿如下:g鼻MP A.7衣1.2T91钢的焊接特点分析T91钢合金元素含量很高,折算成碳的相当含量高,其金相组织为典型的马氏体组织, 可焊性差,具体表现为:(1 )T91含有Cr、Mo V、Cb等强碳化物元素,焊接时焊缝从高温冷却时易产生淬硬性的马氏体组疑,普斃左艰丈冷、窪裂便皐;(2 )T91含有很多的合金元素,其熔融金属的流动性差,焊接时还产生较多的熔渣;(3)由于马氏体钢导热性差,焊接应力不能得到充分释放,焊后焊缝的残余应力很大.因此,T91钢焊接时,如焊接工艺选择不当,焊工操作不当,很容易产生焊接冷、热裂纹、夹渣等缺陷•为了得到优质的焊接接头,有必要从焊接工艺及参数、焊工操作技术等方面进行严格控制.1.3T91小口径钢焊接的特点T91小口径钢管(即管子外径w 76mm焊接时,由于其外径很小,曲率很大,须采用单面焊双面成形技术(焊工在正面焊接时,焊成的焊缝需同时在正、反两面形成良好的形状)•同时,由于一般小口径钢管焊接时,其焊接位置为全位置,即在一个圆周范围内涵盖仰、立、平焊三个位置,对焊工的操作技术要求很高.由于T91熔融金属的流动性差,给T91小「住铜淨疙孩帯耒进丈的程装+2试脸用母筱及焊对2.1母材根据国外合作商的最新投标电力机组的情报,我们对下述多种管子规格T91钢管进行试验,见表2.3焊接工艺3.1焊接方法该批小口径钢管由于管子口径小、壁厚薄,对接采用手工氩弧焊工艺(以下简称:TIG),焊2层,打底层采用单面焊双面成形技术.3.2焊接坡口焊接坡口采用V型坡口,尺寸见图1|円I 口图焊前坡口及周围20mn范围内清除水、油、锈等污物,并露出金属光泽,以严格控制扩散氢的含量.3.3焊机的选择为了保证焊缝的质量,我们选择了焊枪上带有手控开关的、可控制焊接电流大小的手工钨极氩弧焊焊机,以便焊工焊接时,可根据焊接熔池的情况随时调节焊接电流大小.3.4充氫保护为防止T91焊接时焊缝根部的氧化,TIG打底及盖面焊时管子内部都采用充氩保护. 氩气纯度为99.99%,充氩保护流量控制在7〜12L/min范訓I—3.5预热温度弼层间温度的控制T91钢材的淬硬性大大高于常用的铬钼钢,因此,该钢材焊接时,一方面必须严格控制扩散氢的含量,另一方面,需减缓焊接时焊缝的冷却速度,而焊前预热是控制扩散氢含量及减缓焊接时焊缝的冷却速度的最有效的措施,对T91小口径钢管焊接,焊前预热控制在150C以上.为了充分保证下一道焊接前,上一道焊缝已转变为马氏体组织,以利下一道焊接时,能对上一道焊缝进行部分回火,达到改善马氏体组织的焊缝的性能,因此,我们严格限制层间温度在260 C以下.茨/们采用接詁式测温计热温度和底i可温度,次达到严珞控制温度的目的.3.6焊接工艺顺序及參数(1) 装配点焊,位置在时钟12点,长度约10〜15mm(2) 焊接时焊机采用直流正接及小的焊接线能量(单位长度上输入的焊接热量),焊接电流为100〜115A 电压为10〜12V,焊接速度为8〜12cm/min;(3) 焊接位置为全位置,从时钟6点仰位位置起弧,并从两侧向上爬坡施焊,焊工操作顺序见图2|⑷焊接接头作100%X寸幾探俗;(5)焊后焊缝按右侧曲线进行热处理,见图3.3.7操作技术T91小口径钢管焊接时,由于其外径很小,曲率大,焊缝须单面焊双面成形,同时,由于T91熔融金属的流动性差,而焊接位置为全位置,导致成形更难•因此,焊工操作时,需严格挖制各种S 素,并特另〔注意运用好卑面焊双面成形操作技天.(1) 焊工施焊前,必须严格按上述3.2节的要求控制焊接坡口间隙.过大或过小间隙对焊缝成疗都不利+(2) 由于T91含有很多的合金元素,焊接时产生较多的熔渣,每次熄弧后,必须打磨熄船处,以减夕杂质.聚宾*(3) 由于T91熔融金属的流动性差,且焊接位置为全位置(位置图见图2),因此,焊工需严格按下述要求操作,通过调整焊接参数,运用好单面焊双面成形操作技术,使焊缝得到良好成形:①在时钟6点位置,焊缝处于仰位,熔滴下挂,操作不当时,内侧焊缝极易产生内凹•因此焊工操作时,应采用电流上限,利用电弧的吹力托住熔滴进行焊缝成形,避免焊缝产生内凹;②从时钟6点向时钟9点过渡区位置,处于仰位向立位过渡区,熔滴下挂,操作不当时,内侧焊缝易产生内凹•因此焊工操作时,应采用电流上限,施焊中充分利用维弧电流调节焊接熔池形状,利用电弧的吹力托住熔滴进行焊缝成形,避免焊缝产生内凹;③ 在时钟12点及附近位置,焊缝处于平位,熔滴下挂,内侧焊缝极易下挂并产生焊瘤;因此焊工操作时,应采用电流下限,施焊中充分利用维弧电流调节焊接熔池形状,利用熔滴重力进行焊缝成形,避免焊缝内侧产生焊瘤.4试验结果所有焊缝成形良好,焊缝呈亮黄色;所有焊缝经100%X寸线探伤,按美国ASMES准全部合格;焊接接头机械性能,如表3;焊缝组织为回火马氏体,未发现微裂纹及过烧.5结论(1 )焊接T91小口径钢管,选用ER90S-B9旱丝是匹配的.(2 )采用合适的焊接工艺(包括充氩保护、预热温度、层间温度的控制、焊接工艺参数的选择等)是T91 小口径钢管获得优质焊接接头的关键.(3) 严格控制焊前预热在150C以上,层间温度在260C以下是避免焊缝从高温冷却时产生淬硬性的马氏体组织和防止焊接裂纹的重要一环.(4) 掌握T91 小口径钢管操作技术(如控制坡口间隙、焊接电流合理调节等)是焊工焊制优质焊接接头的重要前提.。
薄壁筒形容器的气焊
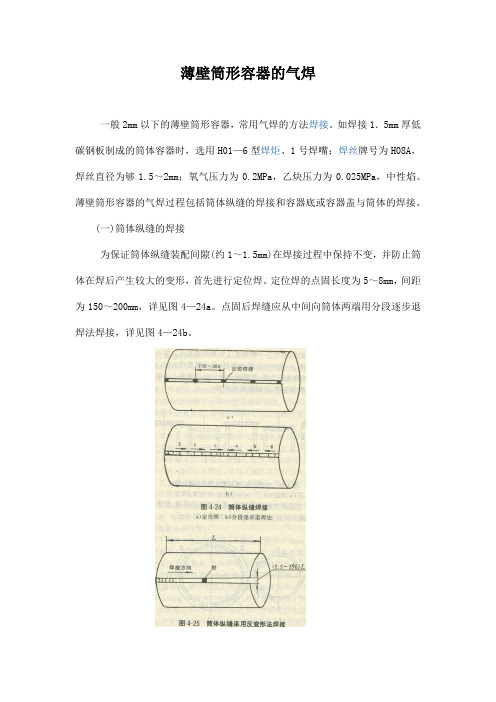
薄壁筒形容器的气焊一般2mm以下的薄壁筒形容器,常用气焊的方法焊接。
如焊接1.5mm厚低碳钢板制成的筒体容器时,选用H01—6型焊炬、1号焊嘴;焊丝牌号为H08A,焊丝直径为够1.5~2mm;氧气压力为0.2MPa,乙炔压力为0.025MPa,中性焰。
薄壁筒形容器的气焊过程包括筒体纵缝的焊接和容器底或容器盖与筒体的焊接。
(一)筒体纵缝的焊接为保证筒体纵缝装配间隙(约1~1.5mm)在焊接过程中保持不变,并防止筒体在焊后产生较大的变形,首先进行定位焊。
定位焊的点固长度为5~8mm,间距为150~200mm,详见图4—24a。
点固后焊缝应从中间向筒体两端用分段逐步退焊法焊接,详见图4—24b。
为防止烧穿,焊嘴应作适当的上下摆动,焊丝要均匀地加入熔池。
采取左焊法,焊嘴与纵缝轴线夹角(焊嘴倾角)约20°~30°,焊丝与焊嘴夹角约90°~110°。
当筒体纵缝长度在1m以下时,在焊接前也可不进行定位焊,而采用在纵缝末端加大间隙(间隙约为焊缝长度的 2.5%~3%)的方法进行焊接,如图4—25所示。
这种方法因在焊接过程中纵缝的收缩,使间隙逐渐减小,从而保证了正常的焊接。
为了更好地控制纵缝间隙的大小,在焊接时可在熔池前面的缝隙中插入一个铁楔或扁铁,并根据间隙的收缩情况,灵活地向后移动,直至焊接结束为止。
这种方法如果使用得当,不仅可以减少定位焊工序,提高生产率,而且可以防止和减少焊接变形,使焊后获得平整的焊件。
但只有操作非常熟练时,采用这种方法才能取得满意的效果。
(二)容器的底、盖与筒体的焊接容器底与容器盖根据其要求不同,可做成凸面形、凹面形或平面形,与筒体连接的接头型式详见图4—26。
图4—26a为凸面形,多用于受压容器的封头,因此要求焊透,并防止烧穿。
图4—26b为凹面形,图4一26c为平面形,多用于一般非受压容器的底和善。
图4—26b、e为卷边接头,一般可不必添加焊丝,但当厚度较大时,应填充焊丝,使焊缝成形良好;焊嘴熔化卷边时应稍作上下跳动,同时为防止简体变形,火焰要偏向外侧。
当前小口径钢管电焊焊接技术中存在问题和解决策略研究
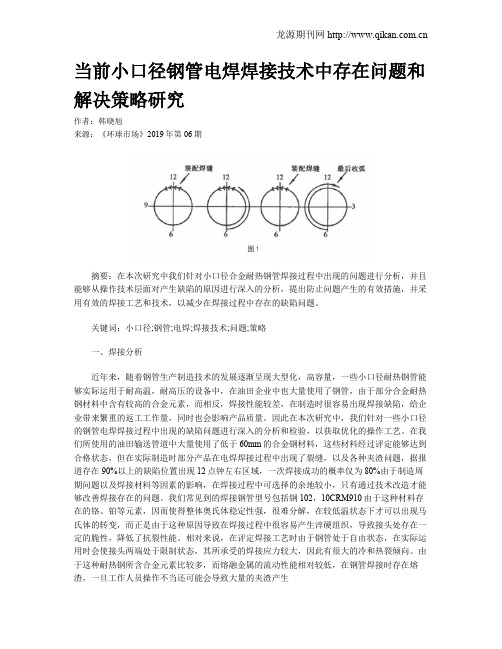
当前小口径钢管电焊焊接技术中存在问题和解决策略研究作者:韩晓旭来源:《环球市场》2019年第06期摘要:在本次研究中我们针对小口径合金耐热钢管焊接过程中出现的问题进行分析,并且能够从操作技术层面对产生缺陷的原因进行深入的分析,提出防止问题产生的有效措施,并采用有效的焊接工艺和技术,以减少在焊接过程中存在的缺陷问题。
关键词:小口径;钢管;电焊;焊接技术;问题;策略一、焊接分析近年来,随着钢管生产制造技术的发展逐渐呈现大型化,高容量,一些小口径耐热钢管能够实际运用于耐高温,耐高压的设备中,在油田企业中也大量使用了钢管,由于部分合金耐热钢材料中含有较高的合金元素,而相反,焊接性能较差,在制造时很容易出现焊接缺陷,给企业带来繁重的返工工作量,同时也会影响产品质量。
因此在本次研究中,我们针对一些小口径的钢管电焊焊接过程中出现的缺陷问题进行深入的分析和检验,以获取优化的操作工艺。
在我们所使用的油田输送管道中大量使用了低于60mm的合金钢材料,这些材料经过评定能够达到合格状态,但在实际制造时部分产品在电焊焊接过程中出现了裂缝,以及各种夹渣问题,据报道存在90%以上的缺陷位置出现12点钟左右区域,一次焊接成功的概率仅为80%由于制造周期问题以及焊接材料等因素的影响,在焊接过程中可选择的余地较小,只有通过技术改造才能够改善焊接存在的问题。
我们常见到的焊接钢管型号包括钢102,10CRM910由于这种材料存在的铬、铂等元素,因而使得整体奥氏体稳定性强,很难分解,在较低温状态下才可以出现马氏体的转变,而正是由于这种原因导致在焊接过程中很容易产生淬硬组织,导致接头处存在一定的脆性,降低了抗裂性能。
相对来说,在评定焊接工艺时由于钢管处于自由状态,在实际运用时会使接头两端处于限制状态,其所承受的焊接应力较大,因此有很大的冷和热裂倾向。
由于这种耐热钢所含合金元素比较多,而熔融金属的流动性能相对较低,在钢管焊接时存在熔渣,一旦工作人员操作不当还可能会导致大量的夹渣产生二、焊接过程中存在的问题及解决措施在焊接过程中存在下列问题:对于焊接过程中可能会导致出现裂纹,通过晶相分析我们认为是一种沿晶裂纹,而且成为热裂纹的可能性比较大,而针对焊接过程中产生的夹渣问题,这主要是与工作人员对于焊件熟悉度以及操作技术有一定的联系,因此需要高度重视。
浅谈小口径管道焊接工艺及质量控制
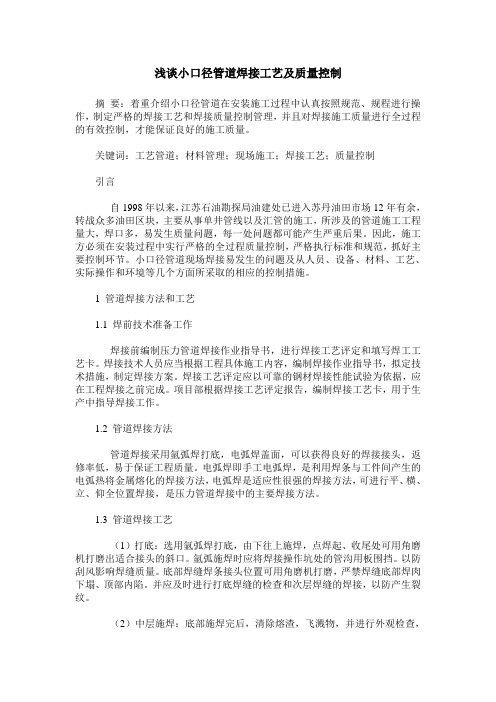
浅谈小口径管道焊接工艺及质量控制摘要:着重介绍小口径管道在安装施工过程中认真按照规范、规程进行操作,制定严格的焊接工艺和焊接质量控制管理,并且对焊接施工质量进行全过程的有效控制,才能保证良好的施工质量。
关键词:工艺管道;材料管理;现场施工;焊接工艺;质量控制引言自1998年以来,江苏石油勘探局油建处已进入苏丹油田市场12年有余,转战众多油田区块,主要从事单井管线以及汇管的施工,所涉及的管道施工工程量大,焊口多,易发生质量问题,每一处问题都可能产生严重后果。
因此,施工方必须在安装过程中实行严格的全过程质量控制,严格执行标准和规范,抓好主要控制环节。
小口径管道现场焊接易发生的问题及从人员、设备、材料、工艺、实际操作和环境等几个方面所采取的相应的控制措施。
1 管道焊接方法和工艺1.1 焊前技术准备工作焊接前编制压力管道焊接作业指导书,进行焊接工艺评定和填写焊工工艺卡。
焊接技术人员应当根据工程具体施工内容,编制焊接作业指导书,拟定技术措施,制定焊接方案。
焊接工艺评定应以可靠的钢材焊接性能试验为依据,应在工程焊接之前完成。
项目部根据焊接工艺评定报告,编制焊接工艺卡,用于生产中指导焊接工作。
1.2 管道焊接方法管道焊接采用氩弧焊打底,电弧焊盖面,可以获得良好的焊接接头,返修率低,易于保证工程质量。
电弧焊即手工电弧焊,是利用焊条与工件间产生的电弧热将金属熔化的焊接方法,电弧焊是适应性很强的焊接方法,可进行平、横、立、仰全位置焊接,是压力管道焊接中的主要焊接方法。
1.3 管道焊接工艺(1)打底:选用氩弧焊打底,由下往上施焊,点焊起、收尾处可用角磨机打磨出适合接头的斜口。
氩弧施焊时应将焊接操作坑处的管沟用板围挡。
以防刮风影响焊缝质量。
底部焊缝焊条接头位置可用角磨机打磨,严禁焊缝底部焊肉下塌、顶部内陷。
并应及时进行打底焊缝的检查和次层焊缝的焊接,以防产生裂纹。
(2)中层施焊:底部施焊完后,清除熔渣,飞溅物,并进行外观检查,发现隐患必须磨透清除后重焊,焊缝与母材交接处一定清理干净。
小型直径钢筒体焊接问题
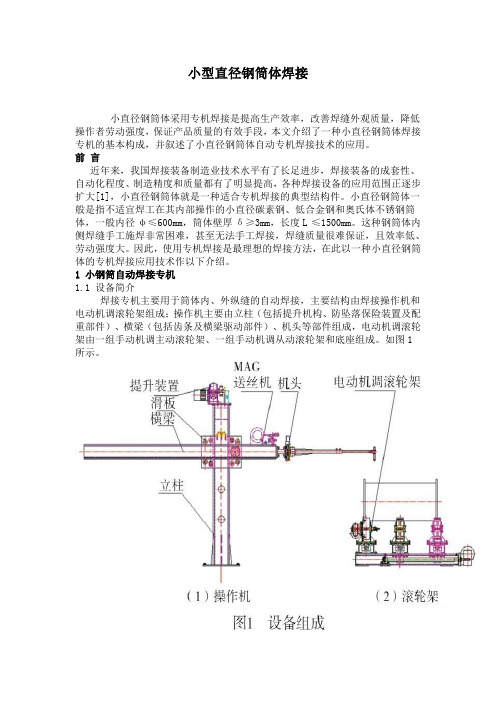
小型直径钢筒体焊接小直径钢筒体采用专机焊接是提高生产效率,改善焊缝外观质量,降低操作者劳动强度,保证产品质量的有效手段,本文介绍了一种小直径钢筒体焊接专机的基本构成,并叙述了小直径钢筒体自动专机焊接技术的应用。
前言近年来,我国焊接装备制造业技术水平有了长足进步,焊接装备的成套性、自动化程度、制造精度和质量都有了明显提高,各种焊接设备的应用范围正逐步扩大[1],小直径钢筒体就是一种适合专机焊接的典型结构件。
小直径钢筒体一般是指不适宜焊工在其内部操作的小直径碳素钢、低合金钢和奥氏体不锈钢筒体,一般内径φ≤600mm,筒体壁厚δ≥3mm,长度L ≤1500mm。
这种钢筒体内侧焊缝手工施焊非常困难,甚至无法手工焊接,焊缝质量很难保证,且效率低、劳动强度大。
因此,使用专机焊接是最理想的焊接方法,在此以一种小直径钢筒体的专机焊接应用技术作以下介绍。
1 小钢筒自动焊接专机1.1 设备简介焊接专机主要用于筒体内、外纵缝的自动焊接,主要结构由焊接操作机和电动机调滚轮架组成;操作机主要由立柱(包括提升机构、防坠落保险装置及配重部件)、横梁(包括齿条及横梁驱动部件)、机头等部件组成,电动机调滚轮架由一组手动机调主动滚轮架、一组手动机调从动滚轮架和底座组成。
如图1所示。
本焊接专机的电气控制采用PLC集成控制,均具有自动控制和手动控制方式,控制精度高、体积小、功能强大,可实现焊接速度、焊枪提升机构、焊枪位置及焊接参数、焊接电流、电弧电压等工艺参数的调节。
主动滚轮架旋转采用变频器控制、无级调速,满足环缝焊接要求。
启动、停止、正、反转、调速、横梁升降伸缩,均在遥控盒上操作,滚轮架与操作机系统相连,可实现联动操作。
1.2 设备特点本焊接专机具有以下几个特点:①适用于筒体直径范围:φ260~1000mm,筒体长度范围:L≤1500mm;②操作机横梁可上下升降;③横臂可自由伸缩,且伸缩采用变频器调速驱动,速度无级可调, 数字显示,变频调速设有过流、过压和过力矩保护等自我保护功能;④焊接机头上配有提升电动拖板、横向摆动器、加长杆、焊枪夹持机构;⑤焊枪通过电动拖板可上下升降和左右移动,焊枪偏移角、焊接倾角均可调节,使用方便;⑥设备的启动、停止、正、反转、调速、横梁升降伸缩,均可在遥控盒上操作,滚轮架与操作机系统相连,可实现联动操作;也可分开进行控制, 可单独使用;⑦利用手控盒可实现异位操作;⑧成组的两个滚轮可同时横向调整,应对工件误差,使纵焊缝焊接时焊枪轨迹与坡口保持一致;⑨滚轮中心距可调,以适应不同直径的工件,且能调整工件的高度及水平度,使纵缝焊接时喷嘴至工件的距离保持一致;⑩横梁前端连接焊枪的加长细杆,长度可非常方便地进行调整,以适应不同长度工件内侧施焊。
接管与筒体的焊接方法

接管与筒体的焊接方法焊接是金属加工中常用的连接方法之一,它通过加热和熔化金属工件,使其相互粘接,达到连接的目的。
在工业制造中,焊接技术广泛应用于许多领域,其中包括接管与筒体的焊接。
本文将详细介绍接管与筒体的焊接方法,包括焊接工艺、焊接设备以及注意事项等方面。
一、接管与筒体的焊接工艺1.准备工作:从焊接前的准备工作来看,接管与筒体的焊接过程需要先进行以下准备:1) 清洁工作:确保接管与筒体表面干净无油污、锈蚀等杂质,以免影响焊接质量。
2) 除毛刺:使用去毛刺工具将接管和筒体口部的毛刺去除,保证焊缝的质量。
3) 对齐工作:确保接管与筒体在焊接过程中保持正确的位置对齐。
2.选择合适的焊接方法:接管与筒体的焊接可采用多种焊接方法,常用的包括:1) 电弧焊接:通过燃烧电弧,熔化工件并使其粘接在一起。
2) 氩弧焊接:利用惰性气体(如氩气)作为保护剂,使电弧焊接过程中的焊缝处于惰性气体保护的环境中,以防止氧化。
3) 滚焊接:将两个工件进行卷合,同时通过加热和压力,使其焊接在一起。
3.焊接设备及工艺参数选择:在进行接管与筒体的焊接时,合适的焊接设备及工艺参数的选择是至关重要的,包括:1) 焊接机:根据焊接方法的选择,选择相应种类的焊接机,如电弧焊机、氩弧焊机等。
2) 电流及电压设置:根据焊接材料和工件的厚度,合理设置电流和电压,以确保焊接质量。
3) 焊接电极选择:选择适合接管与筒体焊接的电极,以保证焊接强度和质量。
4) 焊接速度控制:根据焊接工艺要求,控制焊接速度,保证焊缝的均匀性和稳定性。
二、接管与筒体的焊接注意事项1.焊接位置选择:在焊接时,应选择合适的焊接位置,确保焊接能够顺利进行。
如果接管或筒体的形状复杂,需要保证焊接位置清晰可见,以便焊工操作。
2.防止过热:在焊接过程中,应注意控制焊接时间和焊接机的功率,避免过度加热引起的变形和焊接质量下降。
3.焊接接头设计:接管与筒体的焊接接头设计要合理,以确保焊接接头的稳定性和强度。
接管与筒体的焊接方法

接管与筒体的焊接方法焊接是一种常用的金属连接方法,广泛应用于各个行业中。
在工业生产中,接管与筒体的焊接是一项重要的工艺,其质量直接影响到产品的使用寿命和安全性。
本文将从焊接方法的选择、焊接工艺参数的确定以及焊接质量的控制等方面,对接管与筒体的焊接方法进行探讨。
选择合适的焊接方法是确保焊接质量的重要因素之一。
对于接管与筒体的焊接,常见的焊接方法包括手工电弧焊、气体保护焊和激光焊等。
手工电弧焊是一种常用的焊接方法,适用于焊接较小的接管和筒体,其优点是操作简单、成本低廉,但焊接效率较低;气体保护焊是一种常见的自动化焊接方法,适用于焊接较大的接管和筒体,其优点是焊缝质量好、焊接速度快,但设备投资较高;激光焊是一种高能量密度焊接方法,适用于焊接精密接管和筒体,其优点是焊缝热影响区小、焊接速度快,但设备和维护成本较高。
根据具体的焊接要求和工艺条件,选择合适的焊接方法是确保焊接质量的关键。
确定合理的焊接工艺参数是保证焊接质量的关键环节。
焊接工艺参数包括焊接电流、焊接电压、焊接速度、焊接时间等。
焊接电流和焊接电压是影响焊接熔深和焊缝形状的重要参数,应根据接管和筒体的材质和厚度合理选择;焊接速度是影响焊接质量和生产效率的关键参数,应根据焊接方法和焊接要求进行调整;焊接时间是控制焊接热输入和焊缝质量的重要参数,应根据焊接要求和实际情况进行确定。
合理选择和调整焊接工艺参数,能够有效地控制焊接过程中的热输入和熔深,提高焊接质量和生产效率。
焊接质量的控制是确保焊接质量的重要保障。
焊接质量的控制主要包括焊接前的准备工作、焊接过程的监控和焊接后的检验与评定。
在焊接前的准备工作中,应对接管和筒体进行清洁和除锈处理,以保证焊接区域的表面质量;在焊接过程的监控中,应对焊接工艺参数进行实时监测和调整,以确保焊接过程的稳定和一致性;在焊接后的检验与评定中,应对焊缝进行外观检查和无损检测,以评估焊接质量的合格性。
通过严格的焊接质量控制,能够有效地提高焊接质量和产品的使用寿命。
小直径钢管体全熔透焊缝焊接方法的比较研究
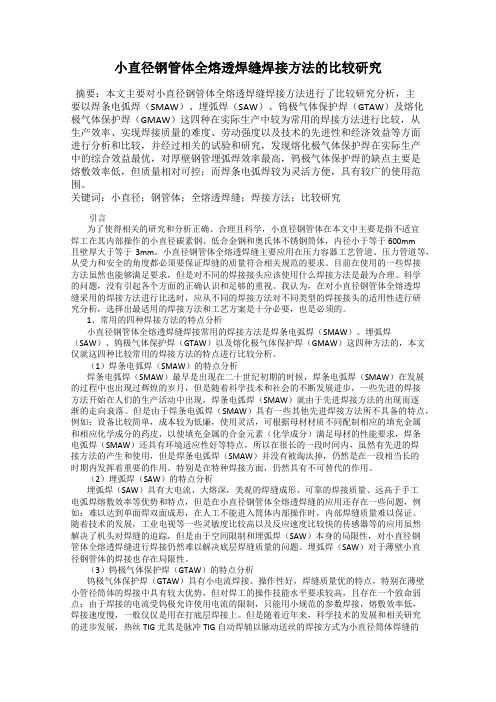
小直径钢管体全熔透焊缝焊接方法的比较研究摘要:本文主要对小直径钢管体全熔透焊缝焊接方法进行了比较研究分析,主要以焊条电弧焊(SMAW)、埋弧焊(SAW)、钨极气体保护焊(GTAW)及熔化极气体保护焊(GMAW)这四种在实际生产中较为常用的焊接方法进行比较,从生产效率、实现焊接质量的难度、劳动强度以及技术的先进性和经济效益等方面进行分析和比较,并经过相关的试验和研究,发现熔化极气体保护焊在实际生产中的综合效益最优,对厚壁钢管埋弧焊效率最高,钨极气体保护焊的缺点主要是熔敷效率低,但质量相对可控;而焊条电弧焊较为灵活方便,具有较广的使用范围。
关键词:小直径;钢管体;全熔透焊缝;焊接方法;比较研究引言为了使得相关的研究和分析正确、合理且科学,小直径钢管体在本文中主要是指不适宜焊工在其内部操作的小直径碳素钢、低合金钢和奥氏体不锈钢筒体,内径小于等于 600mm且壁厚大于等于3mm。
小直径钢管体全熔透焊缝主要应用在压力容器工艺管道、压力管道等,从受力和安全的角度都必须要保证焊缝的质量符合相关规范的要求。
目前在使用的一些焊接方法虽然也能够满足要求,但是对不同的焊接接头应该使用什么焊接方法是最为合理、科学的问题,没有引起各个方面的正确认识和足够的重视。
我认为,在对小直径钢管体全熔透焊缝采用的焊接方法进行比选时,应从不同的焊接方法对不同类型的焊接接头的适用性进行研究分析,选择出最适用的焊接方法和工艺方案是十分必要,也是必须的。
1、常用的四种焊接方法的特点分析小直径钢管体全熔透焊缝焊接常用的焊接方法是焊条电弧焊(SMAW)、埋弧焊(SAW)、钨极气体保护焊(GTAW)以及熔化极气体保护焊(GMAW)这四种方法的,本文仅就这四种比较常用的焊接方法的特点进行比较分析。
(1)焊条电弧焊(SMAW)的特点分析焊条电弧焊(SMAW)最早是出现在二十世纪初期的时候,焊条电弧焊(SMAW)在发展的过程中也出现过辉煌的岁月,但是随着科学技术和社会的不断发展进步,一些先进的焊接方法开始在人们的生产活动中出现,焊条电弧焊(SMAW)就由于先进焊接方法的出现而逐渐的走向衰落。
筒体焊接知识
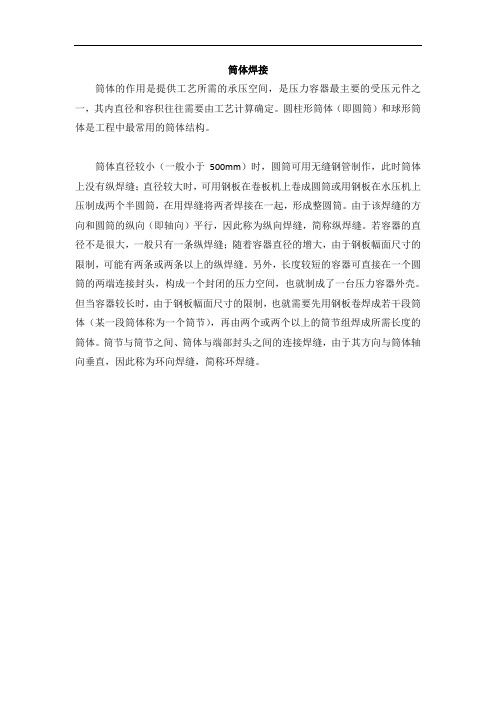
筒体焊接
筒体的作用是提供工艺所需的承压空间,是压力容器最主要的受压元件之一,其内直径和容积往往需要由工艺计算确定。
圆柱形筒体(即圆筒)和球形筒体是工程中最常用的筒体结构。
筒体直径较小(一般小于500mm)时,圆筒可用无缝钢管制作,此时筒体上没有纵焊缝;直径较大时,可用钢板在卷板机上卷成圆筒或用钢板在水压机上压制成两个半圆筒,在用焊缝将两者焊接在一起,形成整圆筒。
由于该焊缝的方向和圆筒的纵向(即轴向)平行,因此称为纵向焊缝,简称纵焊缝。
若容器的直径不是很大,一般只有一条纵焊缝;随着容器直径的增大,由于钢板幅面尺寸的限制,可能有两条或两条以上的纵焊缝。
另外,长度较短的容器可直接在一个圆筒的两端连接封头,构成一个封闭的压力空间,也就制成了一台压力容器外壳。
但当容器较长时,由于钢板幅面尺寸的限制,也就需要先用钢板卷焊成若干段筒体(某一段筒体称为一个筒节),再由两个或两个以上的筒节组焊成所需长度的筒体。
筒节与筒节之间、筒体与端部封头之间的连接焊缝,由于其方向与筒体轴向垂直,因此称为环向焊缝,简称环焊缝。
小直径筒体全熔透焊缝焊接方法比较

小直径筒体全熔透焊缝焊接方法比较
刘速志;许志强;罗全奎
【期刊名称】《机械工程与自动化》
【年(卷),期】2005(000)003
【摘要】以焊条电弧焊(SMAW)、埋弧焊(SAW)、钨极气体保护焊(GTAW)和熔化极气体保护焊(GMAW)四种通用焊接方法为例,从生产率、实现焊接质量的难度、劳动强度、技术先进性和经济效益等方面对小直径钢筒体的全熔透焊缝进行了比较.结果表明GMAW具有最强的竞争力,SAW对厚壁筒最合适,GTAW的缺点是熔敷效率太低,而传统的SMAW在较长期内仍不会被完全淘汰.
【总页数】3页(P112-114)
【作者】刘速志;许志强;罗全奎
【作者单位】太原锅炉集团有限公司,山西,太原,030021;太原锅炉集团有限公司,山西,太原,030021;太原锅炉集团有限公司,山西,太原,030021
【正文语种】中文
【中图分类】TG441.3
【相关文献】
1.小直径钢管体全熔透焊缝焊接方法的比较 [J], 杜国华
2.板单元U形肋角焊缝全熔透焊接技术研究 [J], 刘志新; 常国光; 刘斌; 乔春江
3.两种焊接衬垫在铝合金T形接头全熔透焊缝中的应用研究 [J], 杨丽; 曾庆略
4.铁路货车“十字交叉”全熔透焊缝盲点焊接方法 [J], 易冉;陈娜娜;李春明;陈建
5.钢桥面板U肋角焊缝全熔透焊接工艺研究 [J], 裴雪峰;车平;冯辉
因版权原因,仅展示原文概要,查看原文内容请购买。
小直径管对接垂直固定焊技术
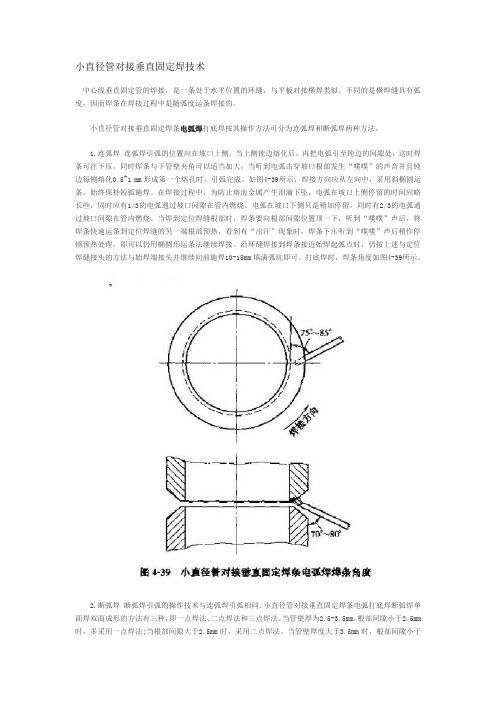
小直径管对接垂直固定焊技术中心线垂直固定管的焊接,是一条处于水平位置的环缝,与平板对接横焊类似。
不同的是横焊缝具有弧度,因而焊条在焊接过程中是随弧度运条焊接的。
小直径管对接垂直固定焊条电弧焊打底焊按其操作方法可分为连弧焊和断弧焊两种方法。
1.连弧焊连弧焊引弧的位置应在坡口上侧,当上侧钝边熔化后。
再把电弧引至钝边的间隙处,这时焊条可往下压,同时焊条与下管壁夹角可以适当加大,当听到电弧击穿坡口根部发生“噗噗”的声音并且钝边每侧熔化0.5~1 mm形成第一个熔孔时,引弧完成。
如图4-39所示,焊接方向应从左向中,采用斜椭圆运条,始终保持短弧施焊。
在焊接过程中,为防止熔池金属产生泪滴下坠,电弧在坡口上侧停留的时间应略长些,同时应有1/3的电弧通过坡口间隙在管内燃烧。
电弧在坡口下侧只是稍加停留,同时有2/3的电弧通过坡口间隙在管内燃烧。
当焊到定位焊缝根部时,焊条要向根部间隙位置顶一下,听到“噗噗”声后,将焊条快速运条到定位焊缝的另一端根部预热,看到有“出汗”现象时,焊条下压听到“噗噗”声后稍作停顿预热处理,即可以仍用椭圆形运条法继续焊接。
沿环缝焊接到焊条接近始焊起弧点时,仍按上述与定位焊缝接头的方法与始焊端接头并继续向前施焊10-15mm填满弧坑即可。
打底焊时,焊条角度如图4-39所示。
2.断弧焊断弧焊引弧的操作技术与连弧焊引弧相同。
小直径管对接垂直固定焊条电弧打底焊断弧焊单面焊双面成形的方法有三种,即一点焊法、二点焊法和三点焊法。
当管壁厚为2.5-3.5mm,根部间隙小于2.5mm 时,多采用一点焊法;当根部间隙大于2.5mm时,采用二点焊法。
当管壁厚度大于3.5mm时,根部间隙小于2.5mm采用一点焊法;根部间隙大于2.5mm时,采用二点焊法;若根部何隙大于4mm时,采用三点焊法。
断弧焊的焊接方向应从左向右焊,逐点将熔化金属送到坡口根部,然后迅速向右侧后方灭弧。
灭弧动作要干净利落,不拉长弧,防止产生咬边缺陷。
- 1、下载文档前请自行甄别文档内容的完整性,平台不提供额外的编辑、内容补充、找答案等附加服务。
- 2、"仅部分预览"的文档,不可在线预览部分如存在完整性等问题,可反馈申请退款(可完整预览的文档不适用该条件!)。
- 3、如文档侵犯您的权益,请联系客服反馈,我们会尽快为您处理(人工客服工作时间:9:00-18:30)。
浅谈小直径筒体焊接
摘要:小直径筒体焊接的一个重要特点就是,不能双面焊接,这就要求在施焊时制定一个完善的焊接工艺流程,才能保证施焊的质量,本文从焊接的两个方法,即手工焊接和自动焊接,分别阐述小直径筒体的焊接工艺。
归根结底的要点,就是要保证焊接的质量!
关键词:小直径筒体焊接工艺
正文:所谓非机加工小直径筒体,在国家标准规范里,并没有明确其直径范围是多少,一般以卷板机能卷制最小直径。
有的筒体直径不大于500mm,坡口采用半自动火焰或是手工火焰切割;然后打磨至露出金属光泽,手工电弧焊焊接;也有的小直径碳素钢、低合金钢和奥氏体不锈钢筒体,一般指内径φ≤600mm,筒体壁厚δ≥3mm,长度L ≤1500mm。
坡口以机械加工坡口为主,一般都是小型的压力容器。
如气瓶、立式反应罐等。
压力容器对焊接要求严格得多,小直径筒体焊接还包括了一些人能进去但不能施焊的压力容器,比如:600--700mm锅炉汽包,人仅能进去检验、但不能处理焊道、不能焊接。
像这样的小直径筒体,可以参照GB150《固容规》去焊接。
小直径筒体焊接有如下几个特点:
仅能单面焊接;
焊缝必须为全熔透焊缝!在电焊工考试中有一个比较严格的项目,就是关于管道焊接或者针对于小直径筒体焊接的,叫做“背透”。
所谓的“背透”,就是单面焊接,双面成形。
施焊不能过流、焊接工艺要求极为苛刻。
对坡口要求高、返修难度大,严格的焊道甚至不允许返修。
小直径筒体焊接方法有两种:一是手工焊接、一是自动焊接,下面我们就逐一介绍这两种方法的焊接工艺。
我们将从人、机、料、法、环等五个方面阐述:
一、焊接工艺方法:
1焊接坡口加工:在实际生产中坡口机加工小直径筒体与封头环焊缝焊接较容易;为保证焊接的质量,坡口尽量采用机械加工坡口,这样可以减少坡口处的氧化层,得于焊接和清理,如果采用碳弧气刨加工坡口,必须清除渗碳层,而且需要用角磨砂轮机进行打磨。
坡口有设计要求的,一定遵照设计要求施工,没有设计要求的,要参照相关规范与标准施工。
2.常用的焊接工艺方法:手工钨极氩弧焊(GTAW)打底,焊条电弧焊(SMAW)填充、盖面。
即氩—电联焊。
对于非机加工坡口来说由于坡口角度偏差大,表面
可能有凹凸不平,致使筒体与封头、筒体与筒体间装配后间隙大小不一致,经常造成手工钨极氩弧焊未焊透或是带垫板的焊缝熔敷金属流入垫板与筒体内壁之间,致使焊缝的射线探伤不合格。
所以在筒体在氩—电联焊时,要采用机械加工坡口。
3.焊道布置方法:A:环缝带垫板焊接;封焊垫板两侧;B:环焊缝背透。
二、施焊有关人员:
1.焊接工程师应根据NB/T47014(JB/T4708)《承压设备焊接工艺评定》的要求编制《焊接工艺指导书》,指导施焊人员的操作,建立特种作业人员管理体系、《焊接操作规程》等。
2.由于小直径筒体焊接的要求很高,对施工焊的有关人员要求也特别的高,其一就是铆工下料、坡口对接、筒体校直、封头检查等,都需要一个有要验、有水平的铆工;其二就是对施焊人员要求也高,施焊人员在操作前,要做以下工作:
A:图纸及工艺交底;
B:焊工考试:尤其是考施焊范围内的平口、纵缝、横缝等;
C:焊接试件的检查:也是对施焊焊工的检查,包括力学性能检验,UT、RT 检验等。
三、机具:机具的准备分两个方面,一个是坡口加工,需要小型车床,一个是焊接机具,即电焊机,电焊机的选用只要能满足氩弧焊接所需要的电流、电压及稳定性就可以了。
UT、RT所用的仪器等
四、材料:焊接材料宜根据筒体材料确定,如筒体材料为20钢、Q235B钢,则在氩—电联焊时,选用焊丝为H08Mn2Si,电焊条选用E4315型(J427);如果筒体材料为Q345R,选用焊丝为H08Mn2SiA,焊条选用E5015(J507)型低氢碱性焊条。
五、关于环境,由于小直径筒体设备,占地小。
自重轻,所以宜在车间内施焊,这样可以保证焊接质量,如果在室外时,需要采取一定的防护措施,包括防风、防雨、焊口防锈等。
下面举例说明小直径筒体焊接的过程。
一、焊前准备;选择直径为450mm壁厚为8mm的Q345R筒体进行2个不同的焊接工艺实验对比,(有垫板和无垫板)
1:坡口形式及加工对于8mm厚的钢卷制的筒体与封头焊接时;常用的坡口形式有两种I形和Y形;I型坡口仅适用不非熔透焊接常压容器或盛瓶,机械
坡口加工[如下图所示]
2:组装定位定位焊缝长度25~30mm 间距不大于150mm
3:焊前清理坡口清理打磨焊丝用无水乙醇或丙酮去油垢
4:采用氩—电联焊。
二、焊接材料;根据接头与母材等强度原则GTAW用焊丝H08Mn2SiA和纯度为99.99%以上的氩气;SMAW用低氢型碱性焊条E5015[J507]使用前进行350~400度烘陪,保温时间不少于1h。
焊条要存放在保温筒内,要随用随取!
1.垫板;材质为Q345R 厚度6mm 宽度30mm
2.焊接设备:用符合要求的电焊机。
一般宜用BX型电焊机。
3.焊接参数及焊接顺序:(见下表)
方案一:焊缝背面带垫板,采用钨极氩弧焊封焊板两侧焊条电弧焊填充(SMAW)及盖面的焊接工艺
注:氩弧焊氩气流量:8~10L|Min 型式如下:
焊后进行100%RT探伤,Ⅱ级以上为合格,一次探伤合格率达100%;未发现未焊透,表面气孔等缺陷;探伤结果满足相关要求。
方案二:焊缝背面不带垫板,采用手工钨极氩弧焊打底,焊条电弧焊填充,最后用细丝埋弧焊的焊接工艺。
焊后进行100%RT探伤,Ⅱ级以上为合格,一次探伤合格率达100%;未发现未焊透,表面气孔等缺陷;探伤结果满足相关要求。
结果分析
1:在上述工艺实验分析中;均采用的是氩—电联焊,当进行很好的层间处理后。
未出现未焊透的现象。
2:对于带垫板的焊缝,必须用手工钨极氩弧焊对垫板两侧进行封焊然后用焊条电弧焊进行填充,否者熔敷金属流入垫板与内壁之间,造成探伤结果不合格。
因为焊缝带垫板,垫板在于筒体内壁装配时有的部位间隙较大,焊接时熔敷金属很容易流入垫板与内壁之间。
3:对于不带垫板的焊缝,采用传统的焊接工艺,GTAW打底SMAW填充盖面,这样能保证焊接质量的,但需要注意的是,在用SMAW填充过程中,一定要进行层间处理!否则,一旦在填充层出现焊接缺陷,则处理起来很麻烦和费力。
氩—电联焊的关键就在于填充层。
要做好层间打磨、层间焊道的清理工作。
小直径筒体焊接---机械自动焊:
机械自动焊接:是机械化大生产的需要,也是生产力发展的趋势。
近十几年来,我国在焊接装备制造业技术水平有了长足进步,焊接装备的成套性、自动化程度、制造精度和质量都有了明显提高,各种焊接设备的应用范围正逐步扩大,小直径钢筒体就是一种适合专机焊接的典型结构件。
这种钢筒体内侧焊缝手工施焊非常困难,甚至无法手工焊接,焊缝质量很难保证,且效率低、劳动强度大。
因此,使用专机焊接是最理想的焊接方法,在此以一种小直径钢筒体的专机焊接应用技术作以下介绍。
1 小直径筒体自动焊接机
1.1 设备简介
焊接专机主要用于筒体内、外纵缝的自动焊接,主要结构由焊接操作机和电动机调滚轮架组成;操作机主要由立柱(包括提升机构、防坠落保险装置及配重部件)、横梁(包括齿条及横梁驱动部件)、机头等部件组成,电动机调滚轮架由一组手动机调主动滚轮架、一组手动机调从动滚轮架和底座组成。