冷轧辊的管理与维护(葛)版
轧辊管理制度

轧辊管理制度为了合理的使用轧辊,增加轧辊的寿命,降低轧辊的损耗,减少因轧辊疲劳过度所造成的损失,维护生产的正常运行,特制定本制度。
1.轧辊管理员将工作辊、中间辊、支撑辊记录本备全,并将轧辊编号,确保记录的准确性和完整性。
2.工艺台账应在工作辊、中间辊、支撑辊记录本中如实填写轧制规格卷数、吨位,上下机时间,上下机班组,下机原因,把记录本送至轧辊装配处,专门存放,记录每缺一项,对当班操作工处于20元罚款。
3.轧辊装配人员将待磨辊记录本随待磨辊放置磨床,轧辊必须按下机时间顺序进行磨削,并如实记录磨削量及弧度(含工作辊中间平台数具),以现行最后下发文为准,不允许多磨或少磨,不按规定进行磨削的发现一次,对磨床工罚款100元。
4.磨好的轧辊记录本由磨床工送至轧辊装配处,装配人员根据使用情况进行配对,装配好后,装配人员要仔细检查,防止错装、漏装,仔细检查辊子挡环、轴承座钩子、螺丝必须紧固,否则发现一次对责任人处于10元的罚款,确认无误后,方可放到换辊小车或轧辊架上,轧辊装配人员要在轧辊上机前将轧辊记录本交到工艺台处。
5.在轧辊充足的情况下,装配人员必须保证有备用辊,以提高生产效率,否则发现一次对责任人处以50元罚款。
6.装配好的轧辊在吊装过程中严禁碰伤,碰伤后上机未影响生产的,每次对责任人罚款20元,影响生产的每次对责任人罚款50元,装配人员必须保证装配件的完整性,特别是轴承座油气接头,与生产班组做好交接,上机前归装配,上机后归生产班组,发现一次不完整,对责任人罚款20元。
7.记录本只准由工艺台操作工、轧辊装配工、磨床工进行流转,其他人员严禁乱拿,各工序要保证轧辊记录本的完整性和准确性,严禁乱撕乱画记录本。
流转将由各工序内专人负责保管,并确保流通顺畅,记录本在哪个工序出现问题,每本对当班人员处于20元罚款。
8.轧辊在使用过程中出现报废,轧辊管理员应把报废辊记录本送至办公室存档,并在微机上登记报废原因,报废尺寸,报废时间、轧制产量、使用次数,每月月底有轧辊管理员将当月轧辊使用情况汇表,特别是新辊投入和轧辊报废情况应详细记录备案。
冷轧辊的管理与维护(葛)版

轧辊转速
随着轧辊速度的增加,磨削热在加工面上的移动速 度加快,热作用时间缩短。
砂轮转速
随着砂轮速度增加,单位时间参与切削的磨粒增加, 磨削温度上升较快,使磨削残余拉应力增加。
砂轮粗修后,磨粒高低错落,切削刃锋利,容屑良
砂轮修整 好,冷却好,磨削力较小,磨削温度低。不易控制!
磨削可不仅是技术问题,更重要的是管理上的问题!
机组
轧机
连退 平整机 热度锌 光整机
轧辊类型
工作辊 中间辊 支承辊 工作辊 中间辊 支承辊 工作辊 支承辊
磨削量(mm)
0.15-0.30 0.5-0.6 2.0~3.0
0.10-0.20 0.5-0.6 1.0-2.0 0.1-0.20 1.0-2.0
2) 合理的换辊制度
---典型可逆式六辊UCM轧机换辊规范
4) 合理辊身倒角
CVC或UCM轧机 辊型或弯辊 轧制过程中的磨损 正常磨削后的倒角减小
及时修正
如何修磨? 支撑辊的倒角修
2) 合理的换辊制度
---典型5机架连轧机换辊周期
机架号 支承辊(t) 中间辊(t)
1
80000
7000
2
70000
7000
工作辊(t) 光辊 毛辊
2000
2000
3
70000
7000
2000
4
60000
7000
1200 1500
5
55000
7000
1000 1500
2) 合理的换辊制度
---典型5机架连轧机修磨量
--如家电面板、汽车面板等高表面要求的板材 (采用个性化产品解决,专题讨论)
辊身剥落和辊身边部剥落
轧辊管理制度
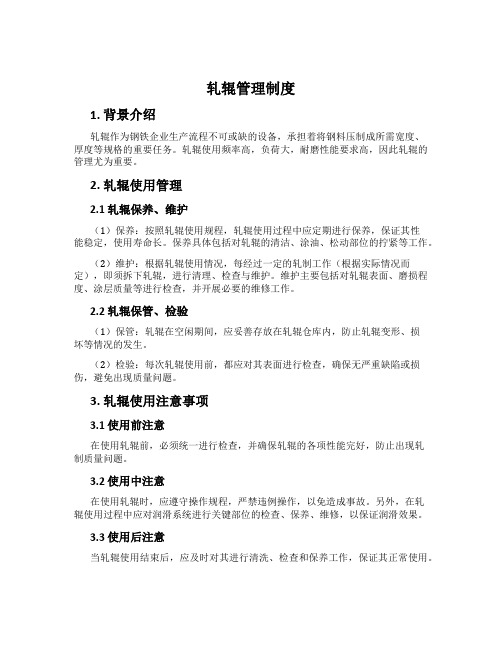
轧辊管理制度1. 背景介绍轧辊作为钢铁企业生产流程不可或缺的设备,承担着将钢料压制成所需宽度、厚度等规格的重要任务。
轧辊使用频率高,负荷大,耐磨性能要求高,因此轧辊的管理尤为重要。
2. 轧辊使用管理2.1 轧辊保养、维护(1)保养:按照轧辊使用规程,轧辊使用过程中应定期进行保养,保证其性能稳定,使用寿命长。
保养具体包括对轧辊的清洁、涂油、松动部位的拧紧等工作。
(2)维护:根据轧辊使用情况,每经过一定的轧制工作(根据实际情况而定),即须拆下轧辊,进行清理、检查与维护。
维护主要包括对轧辊表面、磨损程度、涂层质量等进行检查,并开展必要的维修工作。
2.2 轧辊保管、检验(1)保管:轧辊在空闲期间,应妥善存放在轧辊仓库内,防止轧辊变形、损坏等情况的发生。
(2)检验:每次轧辊使用前,都应对其表面进行检查,确保无严重缺陷或损伤,避免出现质量问题。
3. 轧辊使用注意事项3.1 使用前注意在使用轧辊前,必须统一进行检查,并确保轧辊的各项性能完好,防止出现轧制质量问题。
3.2 使用中注意在使用轧辊时,应遵守操作规程,严禁违例操作,以免造成事故。
另外,在轧辊使用过程中应对润滑系统进行关键部位的检查、保养、维修,以保证润滑效果。
3.3 使用后注意当轧辊使用结束后,应及时对其进行清洗、检查和保养工作,保证其正常使用。
4. 轧辊质量管理轧辊是相关产品的重要配套工具,其质量直接影响到钢铁企业的生产效率和产品质量,因此对其质量的控制非常重要。
钢铁企业应制定完善的质量管理制度,对于生产出来的轧辊进行全方位的检查,确保其出厂前的质量符合国家标准和企业要求。
同时对轧辊的制作过程中每一个环节都进行严格的质量检查,并采取措施纠正问题,以保证轧辊质量。
5. 结束语本文针对轧辊管理制度这一关键问题提出了相关管理方法和注意事项,建议各钢铁企业根据自身情况进行系统建设,加强对轧辊管理的重视,以确保生产过程的规范化和企业经营的成功。
冷轧辊的管理与维护(葛)版共47页文档

41、实际上,我们想要的不是针对犯 罪的法 律,而 是针对 疯狂的 法律。 ——马 克·吐温 42、法律的力量应当跟随着公民,就 像影子 跟随着 身体一 样。— —贝卡 利亚 43、法律和制度必须跟上人类思想进 步。— —杰弗 逊 44、人类受制于法律,法律受制于情 理。— —托·富 勒
45、法律的制定是为了保证每一个人 自由发 挥自己 的才能 ,而不 是为了 束缚他 的才能 。—— 罗伯斯 庇尔
谢谢!
51、 天 下 之 事 常成 于困约 ,而败 于奢靡 。——陆 游 52、 生 命 不 等 于是呼 吸,生 命是活 动。——卢 梭
53、 伟 大 的 事 业,需 要决心 ,能力 ,组织 和责任 感。 ——易 卜 生 54、 唯 书 籍 不 朽。——乔 特
55、 为 中 华 之 崛起而 书。 ——周 恩来
轧辊管理制度[1]
![轧辊管理制度[1]](https://img.taocdn.com/s3/m/f7126c613069a45177232f60ddccda38376be1c9.png)
轧辊管理制度一、背景与目的为了规范轧辊的使用与管理,保障企业生产的安全和效率,订立本《轧辊管理制度》。
二、适用范围本制度适用于公司内全部与轧辊相关的工作人员,包括轧辊的采购、领用、使用、保管等全过程管理。
三、管理标准1.轧辊采购–在采购轧辊前,必需经过采购部门的审批,并依照公司采购流程执行。
–采购轧辊时,必需选择正规的供应商,认真核查其资质和信誉度,确保质量牢靠。
–采购轧辊的数量应依据实际生产需要合理确定,避开过量采购。
–采购轧辊的规格、型号等必需与生产线相匹配,确保使用的兼容性和稳定性。
2.轧辊领用与使用–轧辊的领用必需经过申请流程,并由相关部门审批后方可领用。
–领用轧辊时,工作人员必需认真核对轧辊的规格、型号、数量和质量等信息,确保精准无误。
–轧辊领用后,必需妥当保管,并依照使用要求进行正确安装和调试。
–使用过程中,必需依照操作规程进行操作,严禁超负荷运行或滥用轧辊。
–使用过程中如发觉轧辊存在质量问题或故障,必需适时上报并进行相应的维护和修理或更换。
3.轧辊保管与维护–轧辊的保管必需在专门的库房内,保持干燥、无尘、无腐蚀环境。
–轧辊在保管过程中必需分类、整齐堆放,避开叠压和碰撞,严禁乱丢乱放。
–定期对轧辊进行检查,如发觉有损坏或异常的轧辊,必需适时报告,并进行修复或淘汰处理。
–对存放时间较长的轧辊,必需进行定期检修、清洗和润滑保养,确保其正常运转。
4.轧辊废弃处理–轧辊达到使用寿命后,必需进行废弃处理。
–废弃轧辊必需由专门的人员进行拆解、分类,并依照环保要求进行处理。
–废弃轧辊中的可回收物资,必需进行合理利用或销售,并上报有关部门备案。
–废弃物的处理必需符合国家相关法律法规和企业的环保要求。
四、考核标准1.轧辊采购的标准–是否依照采购流程执行。
–是否选择合格的供应商。
–采购数量是否与生产需要相匹配。
2.轧辊领用与使用的标准–是否依照申请流程和审批程序进行。
–是否精准核对轧辊信息,避开领用错误。
轧辊使用(维护)指导书

锻钢冷轧辊使用(维护)指导书锻钢冷轧辊分为支承辊、中间辊、工作辊三类,采用高碳合金工具钢经复杂的冷、热加工制造而成。
锻钢冷轧辊常用的材料根据其含铬量的不同,分为2Cr系列如9Cr2Mo、85Cr2MoV(86CrMoV7),3Cr系列如85Cr3MoV(MC3)、70Cr3Mo、70Cr3NiMo,4Cr系列如45Cr4NiMoV,5Cr系列如5Cr5NiMoV、85Cr5MoV(MC5)等。
锻钢冷轧辊在轧制中承受巨大的交变应力,常见的失效形式有:清洁度不够造成的辊印压痕;断带等轧制事故造成的粘钢;轧制周期过长、冷却不足造成的表面裂纹或剥落;修磨量不当造成的剥落;轴承烧损抱辊、轧制过载等应力集中造成断辊等。
锻钢冷轧辊的设计、制造、使用(维护)质量直接影响使用寿命,合理的轧辊使用、维护和管理能明显地提高轧辊使用寿命,为此,我们建议轧辊使用单位从下述方面采取措施:(1)储存和运输:应储存在干燥通风的室内(储存期一般在半年以上);运输时避免碰撞;修磨后应及时防锈处理。
(2)轧制控制:检验控制坯料质量;严格按照轧制工艺操作,防止超负荷轧制;轧材要洁净;防止跑偏、叠轧、断带等轧制事故。
(3)定期修磨和检测:根据轧机性能、轧制工艺和产品结构等,统计、分析、确定合理的轧制周期和修磨量。
确定轧制周期的原则是:辊身硬度上升不超过3%。
(针对黑色金属);确定修磨量的原则是:最小的修磨量必须消除轧制疲劳层,特别是辊面微裂纹必须彻底磨去。
对于事故轧辊应反复进行磨削和检测,消除事故影响层,并连续跟踪三次以上。
(4)建立质量档案:轧辊投入使用前应检验并建立轧辊质量卡。
记录轧辊号、规格及相关检测结果;记录每次换辊原因(如正常换辊、变规格换辊、划伤、剥落、粘钢、卡钢、裂纹、换辊等),记录每次修磨量,轧制钢号、规格、轧制量(轧制公里数或吨位)等。
(5)新换轧辊应先预热辊面至70~80℃并保温1~2h;冷轧工作辊应预热至30~50℃,保温后方可正常使用。
轧辊管理制度

轧辊管理制度一、制度目的为规范和保证轧辊的使用、保养和管理,防止轧辊出现故障,保证生产线的正常运转,制定本管理制度。
二、适用范围适用于所有使用轧辊的生产车间,对于负责轧辊管理、维护和保养的工作人员必须严格遵守。
三、轧辊的使用1.轧辊按照规定的工艺和配方进行使用,禁止使用与规定不符的轧辊。
2.轧辊在装卸过程中要避免碰撞和摔落,以免对轧辊造成损坏。
3.严禁不按规定进行定位、支撑、传动等操作,做好支撑和定位工作。
4.轧辊不得长时间在高温、湿度等特殊环境下放置。
四、轧辊的保养和维护1.轧辊使用完毕后,要及时检查,对轧辊进行清洗,去除油污、泥土等杂物,并在生产间隙进行必要的保养维护。
2.如果发现轧辊表面有损伤、开裂、裂纹等情况,需要对轧辊进行更换和修理。
3.对于轧辊的润滑和保养,应当根据生产车间的具体情况,定期对轧辊涂抹润滑油或者润滑脂,保证轧辊的正常运转。
五、轧辊的储存和保管1.将已经使用的轧辊进行分类,区分好不同类型、不同尺寸的轧辊,以便于管理和复用。
2.对于轧辊的储存,要求轧辊不能直接放置于地面上,要使用撑架等工具将轧辊提高高度进行存储,以免轧辊表面受到损害。
3.轧辊的保管,要放置在干燥、防尘、防潮、防腐蚀的环境中,避免轧辊受潮、锈蚀等情况。
六、责任和处罚1.轧辊管理工作由产线班组负责人负责监管和协调,确保轧辊管理工作的落实行动。
2.若对工作人员发现使用、保养、维护和保管不当,轧辊因此损坏,将由负责人员承担相应的责任。
3.对于不按规定管理轧辊的人员,将给予一定的处罚,并进行追究行政责任。
以上是轧辊管理制度的具体内容,希望所有使用轧辊的生产车间工作人员都能认真遵守这些规定,共同维护生产的正常运转,保证生产能够顺利完成。
冷轧企业轧辊管理制度
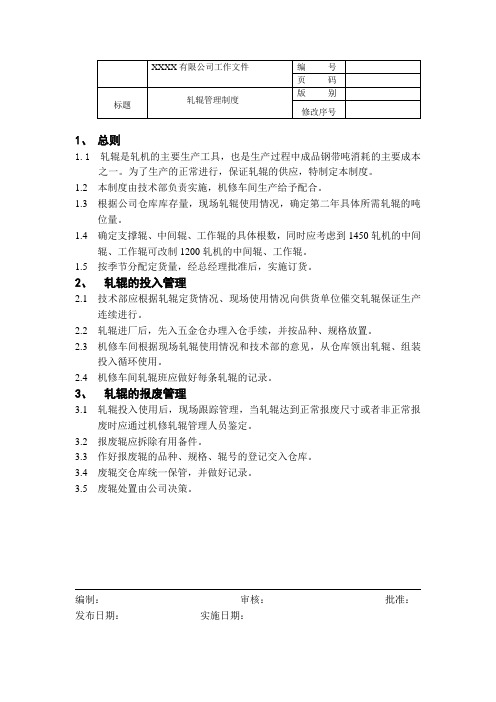
1、总则
1.1 轧辊是轧机的主要生产工具,也是生产过程中成品钢带吨消耗的主要成本
之一。
为了生产的正常进行,保证轧辊的供应,特制定本制度。
1.2 本制度由技术部负责实施,机修车间生产给予配合。
1.3 根据公司仓库库存量,现场轧辊使用情况,确定第二年具体所需轧辊的吨
位量。
1.4 确定支撑辊、中间辊、工作辊的具体根数,同时应考虑到1450轧机的中间
辊、工作辊可改制1200轧机的中间辊、工作辊。
1.5 按季节分配定货量,经总经理批准后,实施订货。
2、轧辊的投入管理
2.1 技术部应根据轧辊定货情况、现场使用情况向供货单位催交轧辊保证生产
连续进行。
2.2 轧辊进厂后,先入五金仓办理入仓手续,并按品种、规格放置。
2.3 机修车间根据现场轧辊使用情况和技术部的意见,从仓库领出轧辊、组装
投入循环使用。
2.4 机修车间轧辊班应做好每条轧辊的记录。
3、轧辊的报废管理
3.1 轧辊投入使用后,现场跟踪管理,当轧辊达到正常报废尺寸或者非正常报
废时应通过机修轧辊管理人员鉴定。
3.2 报废辊应拆除有用备件。
3.3 作好报废辊的品种、规格、辊号的登记交入仓库。
3.4 废辊交仓库统一保管,并做好记录。
3.5 废辊处置由公司决策。
编制:审核:批准:发布日期:实施日期:。
轧辊的使用与维护
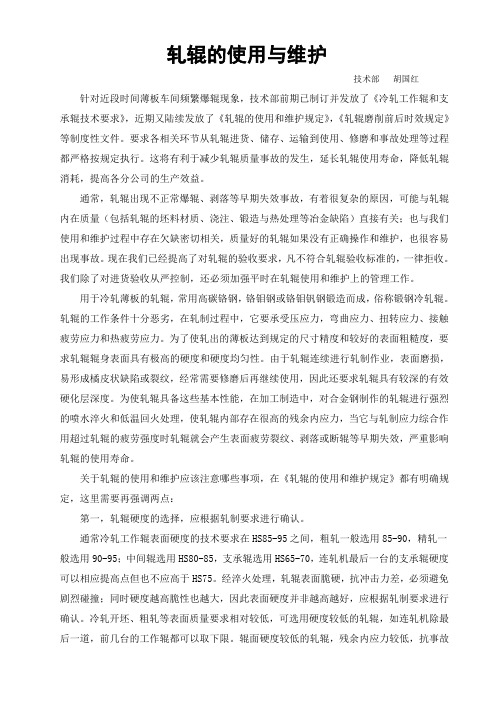
轧辊的使用与维护技术部胡国红针对近段时间薄板车间频繁爆辊现象,技术部前期已制订并发放了《冷轧工作辊和支承辊技术要求》,近期又陆续发放了《轧辊的使用和维护规定》,《轧辊磨削前后时效规定》等制度性文件。
要求各相关环节从轧辊进货、储存、运输到使用、修磨和事故处理等过程都严格按规定执行。
这将有利于减少轧辊质量事故的发生,延长轧辊使用寿命,降低轧辊消耗,提高各分公司的生产效益。
通常,轧辊出现不正常爆辊、剥落等早期失效事故,有着很复杂的原因,可能与轧辊内在质量(包括轧辊的坯料材质、浇注、锻造与热处理等冶金缺陷)直接有关;也与我们使用和维护过程中存在欠缺密切相关,质量好的轧辊如果没有正确操作和维护,也很容易出现事故。
现在我们已经提高了对轧辊的验收要求,凡不符合轧辊验收标准的,一律拒收。
我们除了对进货验收从严控制,还必须加强平时在轧辊使用和维护上的管理工作。
用于冷轧薄板的轧辊,常用高碳铬钢,铬钼钢或铬钼钒钢锻造而成,俗称锻钢冷轧辊。
轧辊的工作条件十分恶劣,在轧制过程中,它要承受压应力,弯曲应力、扭转应力、接触疲劳应力和热疲劳应力。
为了使轧出的薄板达到规定的尺寸精度和较好的表面粗糙度,要求轧辊辊身表面具有极高的硬度和硬度均匀性。
由于轧辊连续进行轧制作业,表面磨损,易形成橘皮状缺陷或裂纹,经常需要修磨后再继续使用,因此还要求轧辊具有较深的有效硬化层深度。
为使轧辊具备这些基本性能,在加工制造中,对合金钢制作的轧辊进行强烈的喷水淬火和低温回火处理,使轧辊内部存在很高的残余内应力,当它与轧制应力综合作用超过轧辊的疲劳强度时轧辊就会产生表面疲劳裂纹、剥落或断辊等早期失效,严重影响轧辊的使用寿命。
关于轧辊的使用和维护应该注意哪些事项,在《轧辊的使用和维护规定》都有明确规定,这里需要再强调两点:第一,轧辊硬度的选择,应根据轧制要求进行确认。
通常冷轧工作辊表面硬度的技术要求在HS85-95之间,粗轧一般选用85-90,精轧一般选用90-95;中间辊选用HS80-85,支承辊选用HS65-70,连轧机最后一台的支承辊硬度可以相应提高点但也不应高于HS75。
冷轧辊的管理与维护(葛)版47页PPT

6、最大的骄傲于最大的自卑都表示心灵的最软弱无力。——斯宾诺莎 7、自知之明是最难得的知识。——西班牙 8、勇气通往天堂,怯懦通往地狱。——塞内加 9、有时候读书是一种巧妙地避开思考的方法。——赫尔普斯 10、阅读一切好书如同和过去最杰出的人谈话。——笛卡儿
冷轧辊的管理与维护(葛)版
31、别人笑我太疯癫,我笑他人看不 穿。(名 言网) 32、我不想听失意者的哭泣,抱怨者 的牢骚 ,这是 羊群中 的瘟疫 ,我不 能被它 传染。 我要尽 量避免 绝望, 辛勤耕 耘,忍 受苦楚 。我一 试再试 ,争取 每天的 成功, 避免以 失败收 常在ቤተ መጻሕፍቲ ባይዱ 人停滞 不前时 ,我继 续拼搏 。
33、如果惧怕前面跌宕的山岩,生命 就永远 只能是 死水一 潭。 34、当你眼泪忍不住要流出来的时候 ,睁大 眼睛, 千万别 眨眼!你会看到 世界由 清晰变 模糊的 全过程 ,心会 在你泪 水落下 的那一 刻变得 清澈明 晰。盐 。注定 要融化 的,也 许是用 眼泪的 方式。
35、不要以为自己成功一次就可以了 ,也不 要以为 过去的 光荣可 以被永 远肯定 。
Thank you
轧辊装配操作与维护规程

支持性文件
轧辊装配操作与维护规程
1目的
规范各轧机(1650热轧机、1550冷轧机、1450箔轧机、1850箔轧机、1550精轧机、1830精轧机、1800铸轧机、1900铸轧机)轧辊装配操作与维护,使其达到工艺要求,满足生产需要。
2适用范围
本规程适用于各轧机轧辊装配操作与维护。
3职责
3.1换辊工每日完成应有的轧辊装配工作,装配过程中认真按照规程严格检查,并做好相关的记录。
3.2换辊工将检查问题点和零部件更换情况如实填写在相关记录里,并反馈给部门主管,部门主管反馈相关归口部门。
3.3换辊工做好轧辊及轴承箱定期维护保养工作,并做好相关的记录。
4作业规程
轴承箱及轴承定期维护检查表。
冷轧机设备保养维护方案

冷轧机设备保养维护方案
冷轧机设备保养维护方案主要包括以下几个方面:
1. 日常保养:每天对设备进行清洁,检查设备的各个部件是否有异常,检查设备的油位、油质、冷却水等是否正常。
2. 定期保养:按照设备的规定,定期对设备进行全面的保养,包括更换机油、清理油路、清理散热器等,以及检查电气系统是否正常。
3. 预防性维修:根据设备的磨损规律和使用情况,提前对设备进行维修,以防止设备出现故障。
4. 应急处理:对于突然出现的故障,应尽快联系专业维修人员进行维修,以免影响生产。
具体的保养维护方案应根据冷轧机的型号、使用环境、工作条件等因素来制定,建议查阅设备的维修保养手册,或咨询厂家及专业维修人员。
冷轧厂设备使用、维护管理制度

宝山钢铁股份有限公司冷轧厂管理文件文件名称: 冷轧厂设备使用、维护管理制度文件编号:GAE00089 第4版签发:姚林龙1.目的和适用范围1.1目的为了正确使用、精心维护、严格管理好设备,使设备保持良好工作环境和工作条件,确保设备保持良好状态,延长设备使用寿命,保证生产正常运行。
1.2适用范围本管理制度适用于冷轧厂参与生产过程的岗位操作人员,设备专职点检员以及与之相关的人员。
2.管理职责2.1冷轧厂各生产分厂及能介、磨辊车间是本区域生产设备的直接使用者,生产操作人员负有用好、维护好、管理好设备的直接责任。
2.2 岗位操作人员要根据维护分工协议承担部分设备的清扫、紧固、调整、给油脂、小修理等日常点检业务。
每当停机检修(特别是定、年修)期间、生产操作人员应主动配合检修人员承担设备清扫、给油脂、小零件的更换、调整等项维护工作,并主动为设备检修创造条件。
2002年4月16日发布2002年4月20日实施发放范围:厂办、轧一、涂镀、精一、轧二、镀锡、精二、镀锌、硅钢、----------------------------精品word文档值得下载值得拥有---------------------------------------------------------------------------------------------------------------------------------------------------------------------------磨辊、2030设备、1420设备、1550设备、能介、设备管理室、质检站2.3 专职点检员要通过点检及倾向管理维护管理好设备,准确分析掌握设备技术状态,跟踪设备的劣化倾向,发现设备有失效倾向或隐患时,必须立即采取有效的预防措施,及时恢复设备正常。
3.设备的使用3.1 生产操作人员必须按岗位的要求,切实做到用好设备、管好设备、修好设备,并且会使用、会维护、会点检、会紧急处理故障。
铝箔、铝板带冷轧辊的生产及维护1

邢台轧辊小冷辊有限责任公司
二、工作辊在制造和使用过程中的修磨
工作辊的磨削是制造单位和使用单位需要掌握的一项 关键技术。磨削质量的高低直接决定了轧辊的形位精度和 表面质量,也关系到轧辊的使用寿命和轧制质量。我们通 过自位托磨和顶磨的方法,采用具有自动调节的软拨装置, 最终工作辊辊身与两端辊颈的同轴度达到了0.0010.002mm,最好可以达到0.0003mm。
纹状”结构。结晶过程中辊面生成树枝晶结构,这种结构 分布于整个轧辊表面。通常出现在轧辊过量磨削之后。
邢台轧辊小冷辊有限责任公司
轧辊印痕(针孔、凹痕、压痕、孔洞) 轧辊印痕的特征是不规则分布的凹痕,一般呈圆形,最大 直凹痕内。
邢台轧辊小冷辊有限责任公司
1、成品铝箔、铝板带工作辊辊身表面必须具有高而均匀的 硬度,以此保证轧材的尺寸精度和良好的表面质量。
邢台轧辊小冷辊有限责任公司
2、辊身淬硬层深度是铝箔、铝板带工作辊所要求的最主要 的性能之一。因为辊身表面淬硬层深度的增加,可增大轧辊 的可用直径,从而有效地提高轧辊使用寿命;与之相应,不 需重新淬火,因此,有利于降低生产成本。
3、具有高弹性极限。防止在高轧制载荷作用下,辊身表面 发生过量的弹性变形。这一特性对于轧制薄带材显得尤为重 要。
4、具有高的耐磨损性能和粗糙度保持能力。
邢台轧辊小冷辊有限责任公司
5、具有高的抗事故能力,特别是应兼有高的抗热冲击和抗 剥落性能。
由于铝箔、铝板带工作辊的抗事故能力对钢的组织和性能 不均匀性特别敏感,因此,要求轧辊本身:一是纯净的冶金 质量;二是高的组织均匀性。工作辊辊身工作层的基体组织 应当是细小的回火马氏体和在马氏体基体中均匀分布有细小 的颗粒状的碳化物,以此赋予轧辊所需要的优异性能。
邢台轧辊小冷辊使用说明
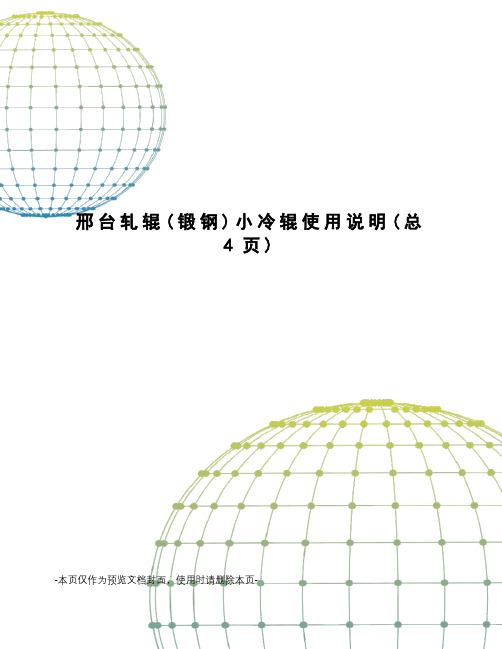
邢台轧辊(锻钢)小冷辊使用说明(总4页)-本页仅作为预览文档封面,使用时请删除本页-邢台轧辊(锻钢)小冷辊使用说明一、搬运与储藏1、轧辊在搬运过程须采用吊装带装卸,防止出现磕碰伤现象。
2、轧辊应贮存在干燥通风的室内,防止受潮,也不要在酸、碱等化学腐蚀环境中存放,储存前轧辊表面应涂防锈油保护。
3、安装拆卸轧辊应十分小心,防止擦伤或碰伤辊面。
4、下机热辊不可堆放湿冷的地面上,并应避免轧辊之间相互碰撞。
5、修磨后的待上机轧辊应注意防锈,严禁就地搁置。
二、轧辊的管理1、投入使用前应建立轧辊使用卡,记录轧辊辊号、规格尺寸、轧辊使用寿命结束后将轧辊使用卡作为原始记录归档。
2、轧辊上下机应在轧辊使用卡上记录上下机时间、本次轧制钢号、规格、轧制量和修磨原因(如正常换辊、变规格换辊、划伤、剥落、粘钢、裂纹等)。
3、轧辊每次修磨后均应记录开始磨削时间、磨削前后直径、重磨量及修磨原因。
4、根据轧制材料制定合理的轧制工艺(使用道次、单道次压下量和轧制速度等),针对不同的轧制工艺建立相应的换辊制度。
5、根据轧辊用途、轧制材料、粗精轧工序,合理选用工作辊辊身硬度及粗糙度相当的轧辊上机使用。
同时保证中间辊、支承辊硬度的合理搭配。
6、使用轧辊的原则是:新(高硬度)辊适用于宽带、薄带的精轧;旧(低硬度)辊适用于窄带、厚带的初轧。
轧辊必须实行分机使用的原则,避免误用混用,勿精作粗用。
7、定期维修、检查和监控轧机运行状况,轧辊装配、传动装置要安装精确、运行自如,避免带“病”设备运行、超期服役。
注意防震,确保轧辊在良好的状态下工作。
三、轧辊的使用1、使用前,应擦去表面油污、灰尘和锈迹,然后进行常规检测。
特别应仔细检查辊身和辊颈表面是否有划痕、压痕、锈斑和裂纹等缺陷,不允许有表面缺陷的轧辊上机使用。
2、轧制前应仔细检查轧制坯料的板面质量、板材成分和硬度等,需要接带时接口要平整,无凸起现象,在轧制中严格按轧制工艺进行操作,防止超负荷轧制,注意观察轧制力的变化和轧材硬化速率,硬度较高时中间要进行退火处理。
轧辊的磨削和使用及维护保养
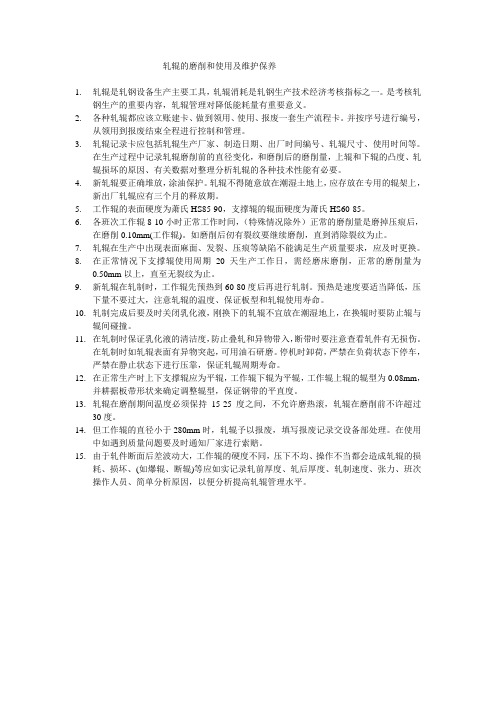
轧辊的磨削和使用及维护保养1.轧辊是轧钢设备生产主要工具,轧辊消耗是轧钢生产技术经济考核指标之一。
是考核轧钢生产的重要内容,轧辊管理对降低能耗量有重要意义。
2.各种轧辊都应该立账建卡、做到领用、使用、报废一套生产流程卡。
并按序号进行编号,从领用到报废结束全程进行控制和管理。
3.轧辊记录卡应包括轧辊生产厂家、制造日期、出厂时间编号、轧辊尺寸、使用时间等。
在生产过程中记录轧辊磨削前的直径变化,和磨削后的磨削量,上辊和下辊的凸度、轧辊损坏的原因、有关数据对整理分析轧辊的各种技术性能有必要。
4.新轧辊要正确堆放,涂油保护。
轧辊不得随意放在潮湿土地上,应存放在专用的辊架上,新出厂轧辊应有三个月的释放期。
5.工作辊的表面硬度为萧氏HS85-90,支撑辊的辊面硬度为萧氏HS60-85。
6.各班次工作辊8-10小时正常工作时间,(特殊情况除外)正常的磨削量是磨掉压痕后,在磨削0.10mm(工作辊)。
如磨削后仞有裂纹要继续磨削,直到消除裂纹为止。
7.轧辊在生产中出现表面麻面、发裂、压痕等缺陷不能满足生产质量要求,应及时更换。
8.在正常情况下支撑辊使用周期20天生产工作日,需经磨床磨削,正常的磨削量为0.50mm以上,直至无裂纹为止。
9.新轧辊在轧制时,工作辊先预热到60-80度后再进行轧制。
预热是速度要适当降低,压下量不要过大,注意轧辊的温度、保证板型和轧辊使用寿命。
10.轧制完成后要及时关闭乳化液,刚换下的轧辊不宜放在潮湿地上,在换辊时要防止辊与辊间碰撞。
11.在轧制时保证乳化液的清洁度,防止叠轧和异物带入,断带时要注意查看轧件有无损伤。
在轧制时如轧辊表面有异物突起,可用油石研磨。
停机时卸荷,严禁在负荷状态下停车,严禁在静止状态下进行压靠,保证轧辊周期寿命。
12.在正常生产时上下支撑辊应为平辊,工作辊下辊为平辊,工作辊上辊的辊型为0.08mm,并耕据板带形状来确定调整辊型,保证钢带的平直度。
13.轧辊在磨削期间温度必须保持15-25度之间,不允许磨热滚,轧辊在磨削前不许超过30度。
轧辊管理制度

轧辊管理制度
是针对轧辊的使用、维护、检修和更新等方面所制定的一套规范和流程。
轧辊是在轧机中起到关键作用的部件,对轧制质量和设备寿命有着重要影响,因此需要进行有效的管理和维护。
轧辊管理制度主要包括以下几个方面:
1. 轧辊的进货验收:对新购轧辊进行质量、规格和数量的验收,确保轧辊符合要求,并记录相关信息。
2. 轧辊的使用与保养:规定轧辊的使用规范,如轧辊的安装、调整和保养等。
包括轧辊使用前的检查和清洁,定期的润滑和维护,以及注意事项和使用禁忌等。
3. 轧辊的检修与维修:对轧辊的定期检修和维修进行计划、组织和实施。
包括对轧辊表面的损伤修复、轧辊孔形和直径的修磨,以及轧辊的超声波检测和磁粉检测等。
4. 轧辊的更新与报废:根据轧辊的使用寿命和磨损情况,及时进行轧辊的更新或报废处理。
对于还可以继续使用的轧辊,可以进行翻修和修复,以延长其使用寿命。
5. 轧辊的记录与统计:建立轧辊的档案记录和统计分析,记录轧辊的进出库情况、使用寿命、维修情况和更新情况等。
通过分析轧辊的使用情况,提出改进措施和优化方案,以提高轧辊的使用效率和延长轧辊寿命。
以上是轧辊管理制度的一些基本内容,不同企业和行业可能会根据实际情况进行具体的调整和完善。
通过有效的轧辊管理制
度,可以提高轧辊的使用寿命和质量,减少因轧辊故障而引起的生产事故和停机时间,提高生产效率和产品质量。
轧辊管理制度(3篇)

轧辊管理制度1.轧辊的购置:1.1按照年、季、月计划,提前联系好生产单位。
1.2在选定供货单位时,了解对方生产能力和基本情况,对产品质量负责。
1.3及时提货,提货时应从外观、产品包装、产品规格等进行验收检查。
1.4提货时,应检查是否有合格证、质保书及其他文件,如没有,应拒绝提货。
2.轧辊的入库:2.1入库的轧辊一定要符合计划、合同,2.2入库的轧辊一定要有合格证、质保书及其他文件,否则不得入库。
2.3轧辊入库后要堆放整齐,不得碰撞。
3.轧辊的保管:3.1轧辊不得丢失、变形、损坏。
3.2定期检查,定期通知加油,严防生锈。
.3.3轧辊出入库要登记清楚,做到三清(规格清、数量清、材质清),三一致(帐、卡、物)。
4.轧辊领用:4.1轧辊凭领用单领用。
4.2对直径365、305以上的大轧辊领用要主管领导批准方可发放。
4.3轧辊开箱时,要先检查合格证、质保书等文件是否相符。
5.轧辊的使用:5.1轧辊安装时,应将辊面,辊颈擦洗干净,不允许有灰尘等杂物粘在辊面、颈上。
5.2轧辊安装时要轻拿轻放,轻装。
5.3轧辊安装好后,应对辊颈部加油、否则不得开机。
5.4使用过程中,轧辊面要经常擦,清楚辊面杂质。
5.5轧机停机后,应将电动压下松开,严防两个辊面直接接触伤害辊面。
5.6轧辊停机后应对辊面擦洗,涂油防锈。
6.轧辊的修磨:6.1轧辊使用过程中发现有麻点、凹点等缺陷不能使用时、应及时修磨。
6.2磨辊时,应视生产情况将轧辊加工成各种辊形。
6.3轧辊修磨好后,如不立即上机安装应将其放到辊架上,防止碰撞到辊面。
6.4做好修磨记录,记录上注明每次修磨的规格、数量和磨削前后的尺寸。
6.5修磨过程中,发现轧辊有质量问题,要及时上报并做好记录。
7.轧辊的报废:7.1轧辊使用到一定尺寸不能使用的应作报废处理。
7.2尺寸过小不能使用需报废的,由主管经历鉴定后决定。
7.3对因质量问题需报废的,要分析原因,做好记录,批准后方可报废。
轧辊管理制度(2)是指针对轧辊的管理工作所制定的一系列规章制度和管理流程。
冷轧辊洛5使用和保养
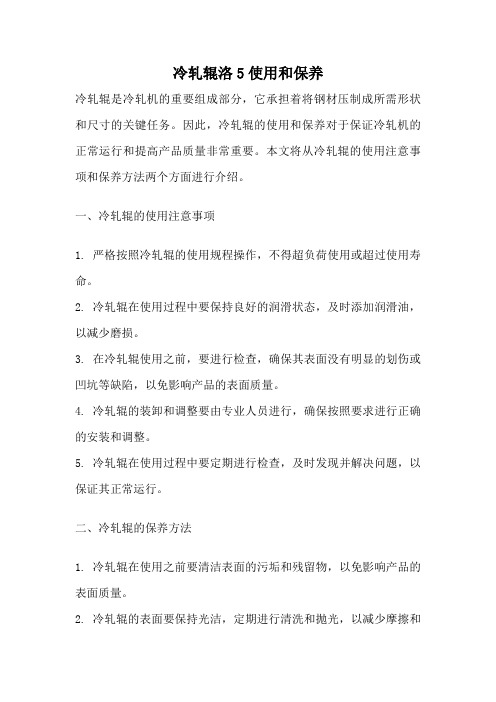
冷轧辊洛5使用和保养
冷轧辊是冷轧机的重要组成部分,它承担着将钢材压制成所需形状和尺寸的关键任务。
因此,冷轧辊的使用和保养对于保证冷轧机的正常运行和提高产品质量非常重要。
本文将从冷轧辊的使用注意事项和保养方法两个方面进行介绍。
一、冷轧辊的使用注意事项
1. 严格按照冷轧辊的使用规程操作,不得超负荷使用或超过使用寿命。
2. 冷轧辊在使用过程中要保持良好的润滑状态,及时添加润滑油,以减少磨损。
3. 在冷轧辊使用之前,要进行检查,确保其表面没有明显的划伤或凹坑等缺陷,以免影响产品的表面质量。
4. 冷轧辊的装卸和调整要由专业人员进行,确保按照要求进行正确的安装和调整。
5. 冷轧辊在使用过程中要定期进行检查,及时发现并解决问题,以保证其正常运行。
二、冷轧辊的保养方法
1. 冷轧辊在使用之前要清洁表面的污垢和残留物,以免影响产品的表面质量。
2. 冷轧辊的表面要保持光洁,定期进行清洗和抛光,以减少摩擦和
磨损。
3. 冷轧辊的润滑油要定期更换,保持良好的润滑状态,以减少磨损和摩擦。
4. 冷轧辊在长时间停机时,要进行防锈处理,涂抹防锈油,以防止生锈和腐蚀。
5. 冷轧辊的存放要注意避免阳光直射和潮湿环境,以免影响其性能和使用寿命。
冷轧辊的使用和保养对于保证冷轧机的正常运行和提高产品质量至关重要。
只有正确使用并定期进行保养,才能保证冷轧辊的性能和使用寿命。
同时,冷轧辊的保养也是为了提高生产效率和降低生产成本的重要手段。
因此,企业在使用和保养冷轧辊时应加强管理,确保冷轧机能够长时间稳定运行,为企业的发展做出贡献。
- 1、下载文档前请自行甄别文档内容的完整性,平台不提供额外的编辑、内容补充、找答案等附加服务。
- 2、"仅部分预览"的文档,不可在线预览部分如存在完整性等问题,可反馈申请退款(可完整预览的文档不适用该条件!)。
- 3、如文档侵犯您的权益,请联系客服反馈,我们会尽快为您处理(人工客服工作时间:9:00-18:30)。
5) 其它事故辊?
打滑的摩擦热
外来碎屑摩擦热 轻微粘钢的热影响区
断带产生的摩擦热
表面用20%的硝酸乙醇腐蚀液剂浸蚀。
5) 修磨记录表(示例)
轧辊修磨记录
__________________轧机,名称:工作辊、中间辊、支承辊 序 号 1 2 3 4 5 6 7 8 9 10 11 12 13 注:操作者应认真如是填写,并妥善保管,本页不够时请续页填写 辊面直径 磨前 磨后 磨削量 下机原因 制造厂编号_____________,使用厂编号____________ 磨削时间 年、月、日、时 表面探伤情况 磨削人 备注
*不重视使用维护技术的企业辊耗较高;
辊耗比例 大于60% 小于40%
原因 异常辊耗 正常磨削损耗
常见非正常失效形式原因
辊身剥落
辊身端部 裂纹剥落
起源于内 部的剥落 热 处 理 应 力
其它 (色差、桔皮、水波纹 … )
断辊
辊印
起源于表 面的剥落
起源于次表 面的剥落 冶 金 缺 陷 接 触 应 力
轧 非轧制事故 制 事 磨 换 修 磨 故 削 辊 周
一重华冶 轧辊 葛浩彬
前 言
轧辊技术是集设计、制造技术,使用、 维护、 检测技术为一体的综合技术。 合理的使用和维护、检测可以进一 步提高轧辊的寿命。 高品质轧辊使用效果是供需双方共同努 力的结果。
轧辊管理维护的现状
企业通过有效的管理,使用效果明显提高; 不同企业的辊耗相差很大:0.2-2.0Kg/t。 *新上项目存在不稳定因素,相对辊耗要高;
残余应力变化,严重时出现裂纹。
3) 磨削烧伤的图片
X100
磨削裂纹一般在浅表层0.10-0.20mm,但有的相当 深,可达到1.0mm以上 由于很多磨削裂纹肉眼不可见,因此其潜在危害很大。
工艺参数
作 用
影响最大,随着进刀量的增大,磨削力和温度均升 磨削深度 高,磨后硬度变化及变质层深度相应增大,对残余 拉应力的影响较显著。不易控制!
---典型可逆式六辊UCM轧机换辊规范
工作辊
修磨 周期 修磨量 修磨 周期 1200Km
中间辊
修磨量
支承辊
修磨 周期
10000-
修磨量
0.15-
1.0- 2.5mm
600-700Km
0.3mm
0.4-0.6mm
12000Km
3) 避免磨削烧伤
高硬度的冷轧工作辊回火温度低,容易产生磨削烧
伤;
磨削控制不当将产生磨削烧伤,造成组织、硬度、
烧 伤 期 长 量 小
冶 金 缺 陷
残 余 应 力
接 触 应 力
冶 金 缺 陷
残 余 应 力
热 加 工 缺 陷
使 用 维 护 不 当
轧 制 条 件
抗 压 性 能
企业中异常辊耗的现状
早期的断辊、表面橘皮想象目前已非常少见
--得益于冶炼、锻造、检测技术的发展
辊印、水波纹等与板材要求有关的逐步上升
1) 避免轧制事故
所有的轧制事故所具有的危害是显而易 见的,而轧制事故又是不可能完全避免的,我 们要做的就是尽力把轧制事故降低到最低。
2) 合理的换辊制度
合理的换辊周期 合理的修磨量 合理的周转辊配备
2) 合理的换辊制度
警示1——不同轧机、不同产品结构、不同的客户 轧制周期和修磨量是不同的。要有自己的定量指标。 警示2——轧制周期和修磨量不是一成不变的。 警示3——轧辊的辊耗绝对不是多磨几道造成的。
人员:不够重视轧辊的管理,缺 乏足够的技术支持 管理:轧辊管理制度没有成熟, 如换辊,探伤,磨辊等,信息流 转不畅通。
6) 轧辊的综合管理体系
仓储 使用
采购
再采购
轧辊管理是一个闭环系统系
维护
统计
分析
新要求
感谢您的关注,欢迎讨论
一重华冶轧辊
表面波
斜探头
直探头
着色/磁粉
0-0.1 0-1.5 OK OK OK OK OK OK OK
0-150 10-心部 表面
OK OK
OK OK
最好的组合:涡流+表面波
最佳:表面波+涡流
40
5) 科学的事故辊处理制度
---需要注意的其他方面
1)轧机处理方式(冷却、安全、冲洗…);
2)事故辊的跟踪检测(3-5周期缩短换辊周期);
--如家电面板、汽车面板等高表面要求的板材 (采用个性化产品解决,专题讨论)
辊身剥落和辊身边部剥落
--依然是当前冷轧企业,尤其是新上项目需要特别 关注的话题
剥落的三种形式
剥落从现象看是突然发生的,但作为一重典型的失效过 程,有裂纹形成、裂纹温度扩展和和快速失稳扩展三阶段。 首先要寻找裂纹的起源。根据微裂纹起源的位置,主要分三
--事故辊处理流程 轧制 常规换辊 磨削 检测 轧制事故 抽出轧辊 检测 掏沟 报废
检测是关键 (消除裂纹和软 点)
检查
5) 科学的事故辊处理制度
---检测配置
有关如何利用检测确定并完全消除裂纹和软点,
是轧辊维护的一个重要环节。
各种表面检测的应用
涡流
有效深度 软点 表面微细裂纹 <0.15 表面裂纹 >0.15 次表层 剩磁 加工硬化
措施及对策
•冶炼技术的进步,尤其ESR技术应用; •检测技术的应用。
?
表面裂纹引发剥落的四个阶段
如何预防这99%? 避免产生裂纹,如果避免不了就在裂 纹扩展之前消除掉!
1) 避免轧制事故 2) 合理的换辊制度
3) 避免磨削烧伤
4) 合理的辊身倒角 5) 科学的事故辊处理制度和检测
易出现 的问题
事故损害的轧 辊,得不到合 理的维护,在 随后的使用中 爆裂 轧辊异常损耗 增加,带来磨辊 间工作负荷过 大,轧机生产工 受到影响.
对策
减少事故数量 提高轧辊的抗事故性能。 磨辊间设备的完善; 改进磨辊间配置; 强化表面检测。 轧辊的售后服务。 人员培训.包括轧机操作、轧辊维护、 修磨、检测等等 建立轧辊管理、评价制度。
4) 合理辊身倒角
CVC或UCM轧机
辊型或弯辊 轧制过程中的磨损 正常磨削后的倒角减小 及时修正
如何修磨? 支撑辊的倒角修
磨尤为重要
5) 科学的事故辊处理制度
5) 科学的事故辊处理制度
粘钢后轧辊表层随温度升高
而回火。
如果温度升高至一定程度, 则在轧制油作用下辊面重新 淬火。 粘钢时局部温度的急剧变化 伴随着组织的变化。 快速的温度及组织的急剧变 化产生的拉应力会造成裂纹 的产生,严重时出现爆辊。
6) 轧辊的综合管理系统
1) 避免轧制事故
--需要考虑的因素
1. 新辊和在役辊的检查验收方案; 2. 制订符合上机条件的轧辊标准; 3 轧辊材料、硬度的适应性的选择; 4. 轧辊传动系统正常化和稳定性研究; 5. 轧辊冷却条件的研究,要有良好冷却和润滑; 6. 综合考虑辊型、轴向移动和弯辊的科学搭 7. 服务于使用的检测技术的开发应用; 8. 优化轧制计划; 9. 优化轧制工艺; 10.优化轧制规程、操作程序等; 11.规范轧机出现轧制事故时的操作程序; 12.操作工的技能培训;
2) 起源于次表层裂纹剥落的宏观特征(端部)
2) 起源于次表层裂纹剥落的宏观特征(辊身)
2) 更多案例(中间辊边部):
2) 更多案例(支承辊被工作辊边部挤压):
3) 起源于内部缺陷剥落的宏观特征
各类剥落发生的比例分析
剥落事故 发生比例 <1-5% >95-99%
原因
材料缺陷 使用维护 不当
轧辊转速 度加快,热作用时间缩短。
随着轧辊速度的增加,磨削热在加工面上的移动速
随着砂轮速度增加,单位时间参与切削的磨粒增加, 砂轮转速 磨削温度上升较快,使磨削残余拉应力增加。 砂轮粗修后,磨粒高低错落,切削刃锋利,容屑良 砂轮修整 好,冷却好,磨削力较小,磨削温度低。不易控制!
磨削可不仅是技术问题,更重要的是管理上的问题!
类:
1) 起源于表面裂纹的剥落;
2) 起源于次表层缺陷的剥落;
3) 起源于内部缺陷的剥落(制造缺陷)
1) 起源于表面裂纹剥落的宏观特征
有明显的光亮带
有明显的扩展痕迹
1) 更多样例:
1) 更多样例:
1) 更多样例:
1) 更多样例:
表面裂纹的来源
轧制事故热冲击裂纹 上次事故形成的热影响区造成的疲劳裂纹 磨削裂纹 表面严重的磕碰伤 各类腐蚀裂纹 疲劳裂纹
3)同时对其它轧辊表面进行检测;中间辊、支撑
辊都要检查。
4)收集剥落块、保护好断口,内部分析,如有异
议 通知供应厂商。
小结:预防剥落要点
1)降低与轧机有关的轧辊损伤。如断带、粘钢、软点、裂纹、 辊印、划痕等应力集中的因素。 2)缩短轧制周期,可以降低表面损伤机会,增加磨削量可避免 疲劳积累,降低出现轧制裂纹的概率。 3)修磨要确保消除最后轧制周期间所引起的任何表面损伤,更
---典型5机架连轧机修磨量 机组 轧机 连退 平整机 热度锌 光整机 轧辊类型 工作辊 中间辊 支承辊 工作辊 中间辊 支承辊 工作辊 支承辊 磨削量(mm) 0.15-0.30 0.5-0.6 2.0~3.0 0.10-0.20 0.5-0.6 1.0-2.0 0.1-0.20 1.0-2.0
2) 合理的换辊制度
5) 科学的事故辊处理制度
---轧辊“下机原因”栏填写 包括:正常、换品种、断带、粘钢、剥裂、 打滑、划伤、辊印、其他
对于磨辊间来说,只有正确了解轧辊下机的原因, 才能指导磨辊间制定合理的修磨工艺,对症下药, 这将会对延长轧辊寿命起到事半功倍的效果;