金属表面化学热处理
金属材料的热处理和表面处理
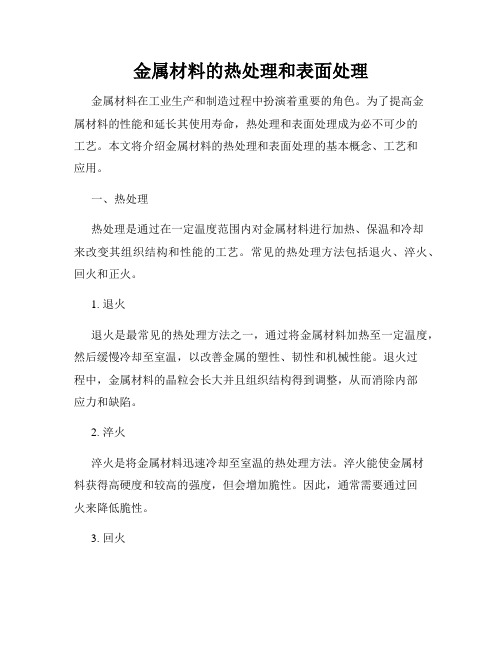
金属材料的热处理和表面处理金属材料在工业生产和制造过程中扮演着重要的角色。
为了提高金属材料的性能和延长其使用寿命,热处理和表面处理成为必不可少的工艺。
本文将介绍金属材料的热处理和表面处理的基本概念、工艺和应用。
一、热处理热处理是通过在一定温度范围内对金属材料进行加热、保温和冷却来改变其组织结构和性能的工艺。
常见的热处理方法包括退火、淬火、回火和正火。
1. 退火退火是最常见的热处理方法之一,通过将金属材料加热至一定温度,然后缓慢冷却至室温,以改善金属的塑性、韧性和机械性能。
退火过程中,金属材料的晶粒会长大并且组织结构得到调整,从而消除内部应力和缺陷。
2. 淬火淬火是将金属材料迅速冷却至室温的热处理方法。
淬火能使金属材料获得高硬度和较高的强度,但会增加脆性。
因此,通常需要通过回火来降低脆性。
3. 回火回火是将淬火后的金属材料加热至一定温度,然后以适当速度冷却的过程。
回火旨在降低金属材料的硬度和脆性,提高其韧性和塑性,以适应不同的使用要求。
4. 正火正火是将金属材料加热至临界点以上,然后冷却至室温的热处理过程。
正火能改善金属材料的硬度、强度和韧性,并且能提高金属材料的耐磨性能。
二、表面处理表面处理是通过对金属材料表面进行物理、化学或电化学处理,以提高金属材料的耐腐蚀性、耐磨性、装饰性和功能性。
常见的表面处理方法包括电镀、喷涂、热喷涂和阳极氧化。
1. 电镀电镀是利用电解质溶液中的金属离子,通过电解沉积在金属材料表面,形成一层金属膜的过程。
电镀可以改善金属材料的外观,提高其耐腐蚀性和耐磨性,同时也可以增加金属材料的导电性和焊接性。
2. 喷涂喷涂是将涂料通过喷枪均匀地喷洒在金属材料表面的过程。
喷涂能够形成一层保护膜,提供金属材料防锈、防腐蚀和装饰的功能。
常见的喷涂涂料有涂胶、烤漆和粉末涂料等。
3. 热喷涂热喷涂是将金属粉末或陶瓷粉末加热至熔点,然后通过喷枪喷射在金属材料表面形成涂层的过程。
热喷涂能够提高金属材料的抗腐蚀性、耐磨性和耐高温性,常用于航空航天和化工等领域。
金属表面处理及热处理加工与表面处理的区别
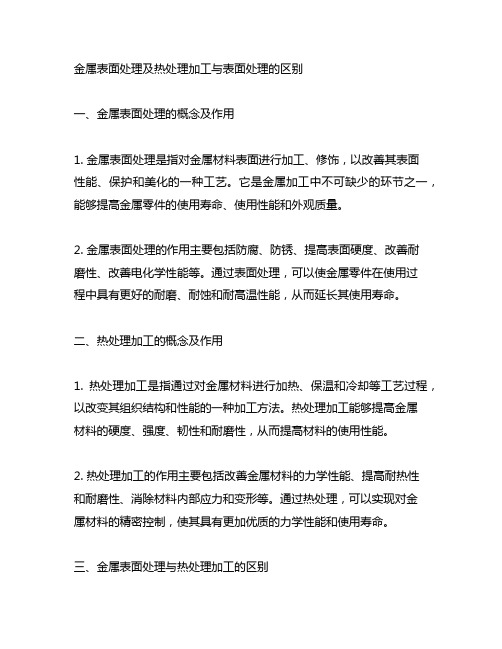
金属表面处理及热处理加工与表面处理的区别一、金属表面处理的概念及作用1. 金属表面处理是指对金属材料表面进行加工、修饰,以改善其表面性能、保护和美化的一种工艺。
它是金属加工中不可缺少的环节之一,能够提高金属零件的使用寿命、使用性能和外观质量。
2. 金属表面处理的作用主要包括防腐、防锈、提高表面硬度、改善耐磨性、改善电化学性能等。
通过表面处理,可以使金属零件在使用过程中具有更好的耐磨、耐蚀和耐高温性能,从而延长其使用寿命。
二、热处理加工的概念及作用1. 热处理加工是指通过对金属材料进行加热、保温和冷却等工艺过程,以改变其组织结构和性能的一种加工方法。
热处理加工能够提高金属材料的硬度、强度、韧性和耐磨性,从而提高材料的使用性能。
2. 热处理加工的作用主要包括改善金属材料的力学性能、提高耐热性和耐磨性、消除材料内部应力和变形等。
通过热处理,可以实现对金属材料的精密控制,使其具有更加优质的力学性能和使用寿命。
三、金属表面处理与热处理加工的区别1. 目的不同:金属表面处理主要是为了改善表面性能,如耐腐蚀、耐磨等;而热处理加工旨在改善整体材料的力学性能,如硬度、强度等。
2. 方法不同:金属表面处理多采用化学处理、机械加工等方式,以在表面形成一层保护膜或改变表面状态;而热处理加工则通过加热、保温和冷却等工艺过程改变材料的组织结构和性能。
3. 范围不同:金属表面处理更偏向于表面的零部件加工和改良;热处理加工则涉及到整体材料的加工和性能提升。
四、个人观点及总结在金属加工领域,金属表面处理和热处理加工都扮演着十分重要的角色。
金属表面处理能够改善金属零件的表面性能,从而提高其使用寿命和稳定性;而热处理加工则能够提升整体材料的力学性能,使其在各种特殊条件下都能够保持优质的性能特性。
两者相辅相成,为金属加工领域的高质量发展提供了重要支撑。
在以后的工程实践中,我会更加注重金属材料的综合加工处理,同时加强对金属表面处理和热处理加工的深入学习和实践应用,以提高自己在金属加工领域的专业技能和水平。
简述金属材料表面主要的处理方法

简述金属材料表面主要的处理方法【摘要】金属材料表面处理方法是为了改善其性能和耐久性,主要包括机械处理、化学处理、电化学处理、热处理和涂层处理。
机械处理方法包括抛光、打磨和喷丸等,可以去除表面缺陷和提高光洁度。
化学处理方法涉及酸洗、镀锌和电镀等,可以防止金属氧化和腐蚀。
电化学处理方法主要是阳极氧化和阳极保护,能够提高金属表面的硬度和耐蚀性。
热处理方法通过调整金属结构和组织,提高其强度和耐磨性。
涂层处理方法包括涂漆、喷涂和镀层等,可以形成保护膜隔绝外界环境。
不同处理方法各有优缺点,未来发展方向是将多种方法相结合,实现表面处理的综合效果。
【关键词】金属材料,表面处理,机械处理,化学处理,电化学处理,热处理,涂层处理,优缺点,发展方向1. 引言1.1 研究背景金属材料在工业生产和日常生活中扮演着重要角色,其表面处理对金属材料的性能和应用有着至关重要的影响。
金属材料表面处理是在金属材料表面施加特定的物理、化学或电化学方法,以改善其表面性能和延长使用寿命的过程。
随着工业技术的不断进步和人们对产品质量要求的提高,金属材料表面处理方法也在不断创新和发展。
传统的金属材料表面处理方法主要包括机械处理方法、化学处理方法、电化学处理方法、热处理方法和涂层处理方法。
每种处理方法都有其独特的优势和适用范围,可以根据具体的应用要求选择合适的方法。
通过对金属材料表面的处理,可以增加其表面硬度、耐磨性、耐腐蚀性等性能,提高其使用寿命和使用性能,满足不同工业领域的需求。
深入研究金属材料表面主要处理方法及其优缺点,对于提高金属材料的品质、推动工业技术进步具有重要意义。
本文将对金属材料表面处理方法进行简要介绍和分析,探讨不同处理方法的特点与应用,为金属材料表面处理技术的发展提供参考和借鉴。
1.2 研究目的金属材料表面处理方法的研究目的主要包括以下几个方面:提高金属材料的耐磨性和耐腐蚀性,增强金属材料的机械性能,改善金属材料的外观和表面质量,延长金属材料的使用寿命,提高金属材料的可持续利用率,满足不同工业领域对金属材料表面性能的需求,以及探索新型表面处理技术,推动金属材料表面处理领域的技术创新与发展。
常用的化学热处理方法及适用范围
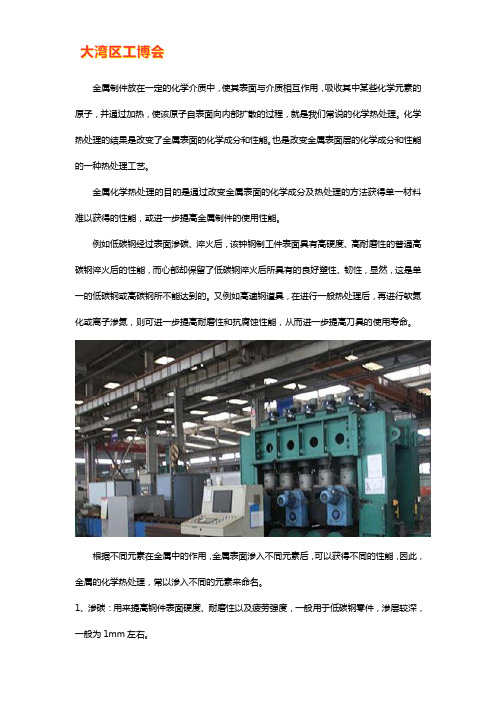
金属制件放在一定的化学介质中,使其表面与介质相互作用,吸收其中某些化学元素的原子,并通过加热,使该原子自表面向内部扩散的过程,就是我们常说的化学热处理。
化学热处理的结果是改变了金属表面的化学成分和性能。
也是改变金属表面层的化学成分和性能的一种热处理工艺。
金属化学热处理的目的是通过改变金属表面的化学成分及热处理的方法获得单一材料难以获得的性能,或进一步提高金属制件的使用性能。
例如低碳钢经过表面渗碳、淬火后,该钟钢制工件表面具有高硬度、高耐磨性的普通高碳钢淬火后的性能,而心部却保留了低碳钢淬火后所具有的良好塑性、韧性,显然,这是单一的低碳钢或高碳钢所不能达到的。
又例如高速钢道具,在进行一般热处理后,再进行软氮化或离子渗氮,则可进一步提高耐磨性和抗腐蚀性能,从而进一步提高刀具的使用寿命。
根据不同元素在金属中的作用,金属表面渗入不同元素后,可以获得不同的性能,因此,金属的化学热处理,常以渗入不同的元素来命名。
1、渗碳:用来提高钢件表面硬度、耐磨性以及疲劳强度,一般用于低碳钢零件,渗层较深,一般为1mm左右。
2、渗氮:用来提高金属的硬度、耐磨性、耐腐蚀性以及疲劳强度,一般常用于中碳钢耐磨结构零件,不锈钢,工、模具钢,铸铁等。
一般渗层深度在0.3mm,渗氮层有较高的热稳定性。
3、碳氮共渗:用来提高工具的硬度、耐磨性、耐腐蚀性以及疲劳强度,高温碳氮共渗一般适用于渗碳钢,并用来代替渗碳,低于渗碳温度,变形小。
低温碳氮共渗适用于中碳结构钢及工模具上。
4、渗硫:减磨,提高抗咬合磨损能力,适用钢种较广,可根据钢种不同,选用不同渗硫方法。
5、渗铝:提高工件抗氧化及抗含硫介质腐蚀的能力。
6、渗铬:提高工件抗氧化、抗腐蚀能力及耐磨性。
7、渗硅:提高工件抗各种酸腐蚀的性能。
8、渗锌:提高铁的抗化学腐蚀及有机介质中的腐蚀能力。
金属表面热处理

浓硫酸 30
重铬酸钠 7.5 水 62.5
在室温下浸渍 1min ,水洗,干燥。
二、镁及镁合金表面处理方法 [方法 1] 脱脂处理。常用溶剂为:三氯乙烯、丙酮、醋酸乙酯和丁酮等。
[方法 2]
脱脂后在下述溶液中于 70-75°C 下浸渍 5min :
氢氧化钠 12
水 100
用冷水冲洗,再于下述溶液中在 20°C 浸渍 5min :
常用的表面处理方法主要有脱脂处理法、机械处理法和化学处理法三大类。选择表面处 理法应考虑多种因素,其中主要包括:
(1)表面污染物的种类。如动物油、植物油、矿物油、润滑油、脏土、流体、无机盐、 水份、指纹等。
(2)污染物的物理特性。如污染物的厚度、紧密或疏松程度等。、 (3)胶接材料的种类。如钢材料可用碱溶液,而处理黄铜、铝材料时应考虑选用腐蚀 性较小的温和溶液。 (4)需要清洁的程度。 (5)清洗液的清洁能力和设备情况。 (6)危险性和价格成本等。 金属表面处理方法 金属表面在各种热处理、机械加工、运输及保管过程中,不可避免地会被氧化,产生 一层厚薄不均的氧化层。同时,也容易受到各种油类污染和吸附一些其他的杂质。 油污及某些吸附物,较薄的氧化层可先后用溶剂清洗、化学处理和机械处理,或直接用化学 处理。对于严重氧化的金属表面,氧化层较厚,就不能直接用溶剂清洗和化学处理,而最好 先进行机械处理。 通常经过处理后的金属表面具有高度活性,更容易再度受到灰尘、湿气等的污染。为此,处 理后的金属表面应尽可能快地进行胶接。 塑料表面处理方法 塑料可分为热塑性塑料和热固性塑料两大类。在通常情况下,热固性塑料要比热塑性 塑料容易胶接。但它们的表面能量均低于玻璃、陶瓷、金属等亲水性材料,而且它们表面常 会粘附脱模剂或逸出增塑剂,因此不易为胶粘剂所浸润,从而影响胶接强度。因此,一般均 需对塑料进行表面处理。由于塑料的品种众多,各种性能差别很大,因此表面处理的方法也 就很不相同。以下介绍几种常见的塑料表面处理方法。 橡胶表面处理方法 一般的橡胶材料表面都比较光滑,需要经机械处理或化学处理增加其粗糙度,才能达
化学镀镍后热处理工艺
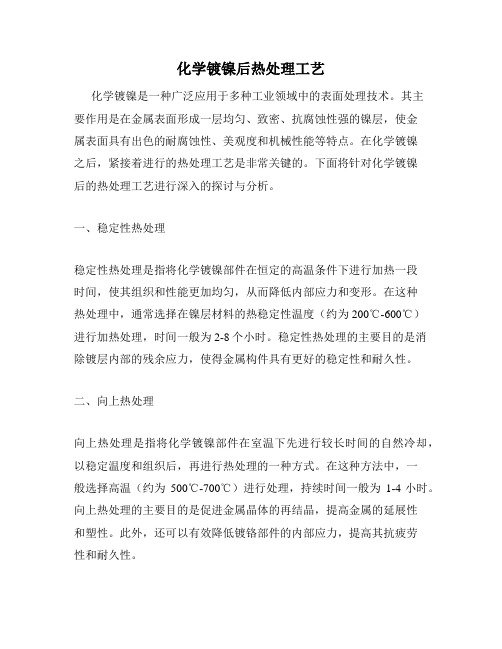
化学镀镍后热处理工艺化学镀镍是一种广泛应用于多种工业领域中的表面处理技术。
其主要作用是在金属表面形成一层均匀、致密、抗腐蚀性强的镍层,使金属表面具有出色的耐腐蚀性、美观度和机械性能等特点。
在化学镀镍之后,紧接着进行的热处理工艺是非常关键的。
下面将针对化学镀镍后的热处理工艺进行深入的探讨与分析。
一、稳定性热处理稳定性热处理是指将化学镀镍部件在恒定的高温条件下进行加热一段时间,使其组织和性能更加均匀,从而降低内部应力和变形。
在这种热处理中,通常选择在镍层材料的热稳定性温度(约为200℃-600℃)进行加热处理,时间一般为2-8个小时。
稳定性热处理的主要目的是消除镀层内部的残余应力,使得金属构件具有更好的稳定性和耐久性。
二、向上热处理向上热处理是指将化学镀镍部件在室温下先进行较长时间的自然冷却,以稳定温度和组织后,再进行热处理的一种方式。
在这种方法中,一般选择高温(约为500℃-700℃)进行处理,持续时间一般为1-4小时。
向上热处理的主要目的是促进金属晶体的再结晶,提高金属的延展性和塑性。
此外,还可以有效降低镀铬部件的内部应力,提高其抗疲劳性和耐久性。
三、退火处理退火处理是针对高强度镍合金部件的一种重要热处理方法。
在化学镀镍之后进行的退火处理,其主要目的是消除金属中的残留应力、改善组织结构、提高金属的延展性和变形能力。
在此种处理中,一般选择高温(约为650℃-800℃)进行加热,时间为1-3小时。
综上所述,无论是稳定性热处理、向上热处理还是退火处理,其目的都是为了提高金属构件的物理和化学性质,提高其的延展性、塑性和耐久性。
化学镀镍与热处理的紧密结合,使得金属的表面处理技术更趋完善。
简述金属材料表面主要的处理方法
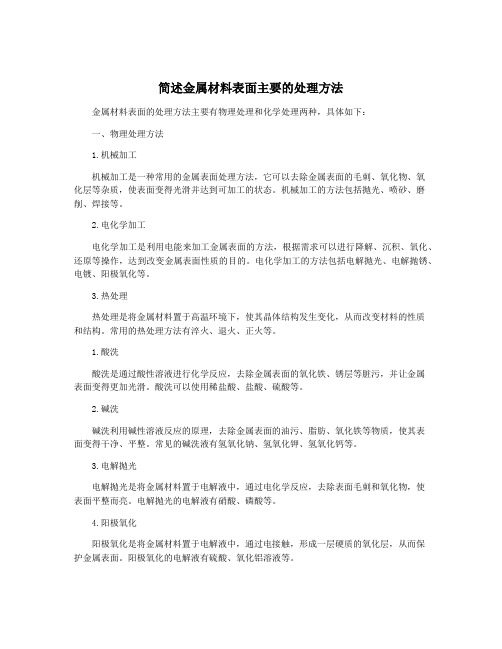
简述金属材料表面主要的处理方法金属材料表面的处理方法主要有物理处理和化学处理两种,具体如下:一、物理处理方法1.机械加工机械加工是一种常用的金属表面处理方法,它可以去除金属表面的毛刺、氧化物、氧化层等杂质,使表面变得光滑并达到可加工的状态。
机械加工的方法包括抛光、喷砂、磨削、焊接等。
2.电化学加工电化学加工是利用电能来加工金属表面的方法,根据需求可以进行降解、沉积、氧化、还原等操作,达到改变金属表面性质的目的。
电化学加工的方法包括电解抛光、电解抛锈、电镀、阳极氧化等。
3.热处理热处理是将金属材料置于高温环境下,使其晶体结构发生变化,从而改变材料的性质和结构。
常用的热处理方法有淬火、退火、正火等。
1.酸洗酸洗是通过酸性溶液进行化学反应,去除金属表面的氧化铁、锈层等脏污,并让金属表面变得更加光滑。
酸洗可以使用稀盐酸、盐酸、硫酸等。
2.碱洗碱洗利用碱性溶液反应的原理,去除金属表面的油污、脂肪、氧化铁等物质,使其表面变得干净、平整。
常见的碱洗液有氢氧化钠、氢氧化钾、氢氧化钙等。
3.电解抛光电解抛光是将金属材料置于电解液中,通过电化学反应,去除表面毛刺和氧化物,使表面平整而亮。
电解抛光的电解液有硝酸、磷酸等。
4.阳极氧化阳极氧化是将金属材料置于电解液中,通过电接触,形成一层硬质的氧化层,从而保护金属表面。
阳极氧化的电解液有硫酸、氧化铝溶液等。
综上所述,金属材料表面的处理方法主要包括机械加工、电化学加工、热处理、酸洗、碱洗、电解抛光和阳极氧化等方面。
这些处理方法既能够使金属表面变得漂亮、光滑,也能够改变其各项物理和化学性质,提高金属的质量和使用寿命。
表面淬火和化学热处理
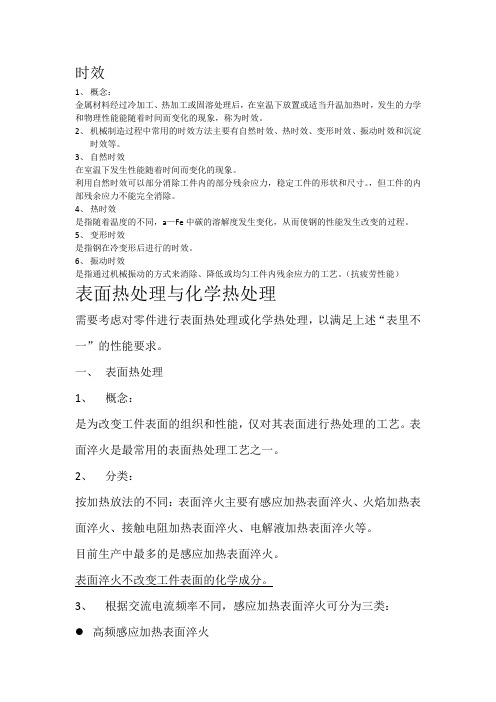
时效1、概念:金属材料经过冷加工、热加工或固溶处理后,在室温下放置或适当升温加热时,发生的力学和物理性能能随着时间而变化的现象,称为时效。
2、机械制造过程中常用的时效方法主要有自然时效、热时效、变形时效、振动时效和沉淀时效等。
3、自然时效在室温下发生性能随着时间而变化的现象。
利用自然时效可以部分消除工件内的部分残余应力,稳定工件的形状和尺寸。
,但工件的内部残余应力不能完全消除。
4、热时效是指随着温度的不同,a—Fe中碳的溶解度发生变化,从而使钢的性能发生改变的过程。
5、变形时效是指钢在冷变形后进行的时效。
6、振动时效是指通过机械振动的方式来消除、降低或均匀工件内残余应力的工艺。
(抗疲劳性能)表面热处理与化学热处理需要考虑对零件进行表面热处理或化学热处理,以满足上述“表里不一”的性能要求。
一、表面热处理1、概念:是为改变工件表面的组织和性能,仅对其表面进行热处理的工艺。
表面淬火是最常用的表面热处理工艺之一。
2、分类:按加热放法的不同:表面淬火主要有感应加热表面淬火、火焰加热表面淬火、接触电阻加热表面淬火、电解液加热表面淬火等。
目前生产中最多的是感应加热表面淬火。
表面淬火不改变工件表面的化学成分。
3、根据交流电流频率不同,感应加热表面淬火可分为三类:高频感应加热表面淬火应用范围:中小型轴、销、套等圆柱形零件,小模数齿轮。
●中频感应加热表面淬火应用范围:尺寸较大的轴类零件,大、中模数齿轮。
●工频感应加热表面淬火应用范围:大型零件表面淬火或棒料穿透加热。
三、化学热处理1、概念:式将工件置于适当的活性介质中加热、保温,使一种或几种元素渗入到它表层,以改变其化学成分、组织和性能的热处理工艺。
2、特点:化学热处理与表面淬火相比,其特点是表层不仅有组织的变化,而且还有化学成分的变化。
3、自身特点:由于渗入元素的不同,工件表面处理后获得的性能也不相同。
渗碳、渗氮、碳氮工渗的主要目的是提高工件表面的硬度和耐磨性;渗金属的主要目的是提高工件表面的耐腐蚀性和抗氧化性等。
金属热处理及表面处理工艺

一、热处理工艺简解1、退火操作方法:将钢件加热到Ac3+30~50°C或Acl+30~50°C或Acl以下的温度(能够查阅有关材料)后,通常随炉温缓慢冷却。
意图:1.下降硬度,进步塑性,改进切削加工与压力加工功能;2.细化晶粒,改进力学功能,为下一步工序做准备:3.消除冷、热加工所发生的内应力。
运用关键:1.适用于合金布局钢、碳素东西钢、合金东西钢、高速钢的锻件、焊接件以及供给状况不合格的原材料;2.通常在毛坯状况进行退火。
2、正火操作方法:将钢件加热到Ac3或Accm以上30~50"C,保温后以稍大于退火的冷却速度冷却。
意图:1.下降硬度,进步塑性,改进切削加工与压力加工功能:2.细化晶粒,改进力学功能,为下步工序做准备:3.消除冷、热加工所发生的内应力。
运用关键:正火通常作为锻件、焊接件以及渗碳零件的预先热处理工序。
关于功能需求不高的低碳的和中碳的碳素布局钢及低合金钢件,也可作为最终热处理。
关于通常中、高合金钢,空冷可致使彻底或部分淬火,因而不能作为最终热处理工序。
3、淬火操作方法:将钢件加热到相变温度Ac3或Acl以上,保温-段吋刻,然后在水、硝盐、油、或空气中疾速冷却。
意图:淬火通常是为了得到高硬度的马氏体安排,有时对某些高合金钢(如不锈钢、耐磨钢)淬火时,则是为了得到单-•均匀的奥氏体安排,以进步耐磨性和耐蚀性。
运用关键:1.通常用于含碳量大于百分Z零点三的碳钢和合金钢;2.淬火能充分发挥钢的强度和耐磨性潜力,但一起会构成很大的内应力,下降钢的塑性和冲击韧度,故要进行回火以得到较好的归纳力学功能。
4、回火操作方法:将淬火后的钢件从头加热到Acl以下某■温度,经保温后,于空气或油、热水、水中冷却。
意图:1.下降或消除淬火后的内应力,削减工件的变形和开裂;2.调整硬度,进步塑性和耐性,取得作业所需求的力学功能;3.安稳工件尺度。
运用关键:1.坚持钢在淬火后的高硬度和耐磨性时用低温回火;在坚持必定韧度的条件下进步钢的弹性和屈从强度时用中温回火:以坚持高的冲击韧度和塑性为主,又有满足的强度时用高温回火:2.通常钢尽量防止在230-280 °C >不锈钢在400~450°C 之间回火,因为这时会发生一次回火脆性。
第6章 金属热处理及表面处理技术
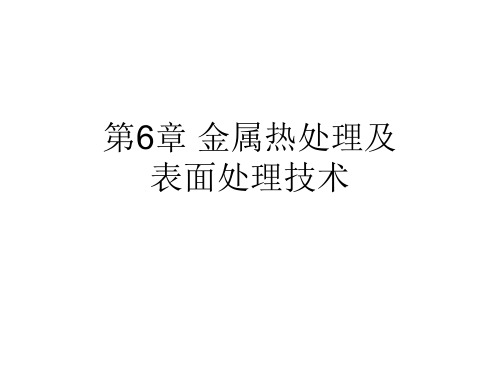
• (1)奥氏体形核 奥氏体晶核首先在铁素体相界面处形成。 • (2)奥氏体长大 形成的奥氏体晶核依靠铁、碳原子的扩散,
同时向铁素体和渗碳体两个方向长大,直至铁素体消失。 • (3)残余渗碳体溶解 在奥氏体形成过程中,铁素体首先消失,
残余的渗碳体随着加热和保温时间的延长,不断溶入奥氏体, 直到全部消失。 • (4)奥氏体成分的均匀化 刚形成的奥氏体,其中的碳浓度是 不均匀的,在原渗碳体处含碳量较高,而原铁素体处含碳量较 低,只有在继续加热保温过程中,通过碳原子的扩散,才能使 奥氏体中的含碳量趋于均匀,形成成分较为均匀的奥氏体。
第6章 金属热处理及 表面处理技术
6.1概述
• 随着科学技术和生产技术的发展,对钢铁材料的性能也提 出了越来越高的要求,改善钢材的性能,有两个主要途径:
一个是加入合金元素,调整钢的化学成分,即合金化的方 法;另一个则通过钢的热处理,调整钢材内部组织的方法。
• 所谓钢的热处理,就是通过加热、保温和冷却,使钢材内 部的组织结构发生变化,从而获得所需性能的一种工艺方 法。
• 从上述分析可以看出,零件加热后进行适当的保温是很有 必要的。其目的是:能使零件在保温过程中彻底完成相变; 为了得到成分较为均匀的奥氏体组织。
• 亚共析钢和共析钢的奥氏体化过程与共析钢相似,不同的 是,在室温下它们的平衡组织中除珠光体外,还有先共析 相存在,当它们被加热到Ac1以上时,首先是其中的珠光 体转变为奥氏体(这一过程与共析钢相同),而此时还有 先共析相(铁素体或渗碳体)存在,要得到单一的奥氏体, 必须提高加热温度,对亚共析钢来说,加热温度超过Ac3 后,先共析铁素体才逐渐转变为奥氏体;对过共析钢来说, 加热温度超过Arcm后,先共析渗碳体才会全部溶解到奥 氏体中去。因此,亚共析钢和过共析钢在上、下临界点之 间加热时,其组织应该是奥氏体和先共析相组成的两相组 织,这种加热方法称为两相区加热或“不完全奥氏体化”, 它常在过共析钢的加热中使用。
金属表面处理工艺及技术
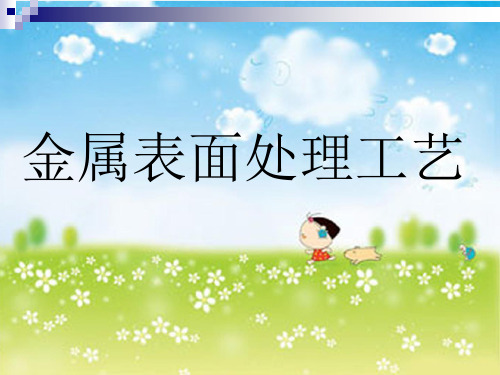
四 喷涂的涂层厚度为几十微米至数毫米.
二.热喷涂的特点
一 工艺灵活,适用范围广.热喷涂施工对象可大可小,小的可 到一0mm内孔[线爆喷涂],大的可到桥梁、铁塔[火焰线材喷 涂或电孤喷涂],可在室内喷涂,也可在野外现场作业;可 整体喷涂,也可以局部喷涂.
低碳钢渗碳缓冷后的组织
五渗碳后的热处理 淬火+低温回火, 回火温度为一六0-一八0℃.淬火方法有: ⑴ 预冷淬火法 渗碳后预冷到略高于Ar一温度直接淬火.
渗碳后的热处理示意图
⑵一次淬火法:即渗碳缓冷后重新加热淬火. ⑶ 二次淬火法: 即渗碳缓冷后第一次加热为心部Ac三+三0-五0℃,细化心部;
金属表面处理工艺
一、表面热处理
一、表面淬火 表面淬火是指在不改变钢的化学成分及心部组织情
况下,利用快速加热将表层奥氏体化后进行淬火以强 化零件表面的热处理方法.
火焰加热 感
应 加 热
表面淬火目的: 一 使表面具有高的硬度、耐磨性和疲劳极限; 二 心部在保持一定的强度、硬度的条件下,具有足够的塑
碳钢. 常用钢号为三八CrMoAl. ⑵氮化温度为五00-五七0℃ 氮化层厚度不超过0.六-0.七
mm.
井式气体氮化炉
⑶常用氮化方法 气体氮化法与离子氮化法. 气体氮化法与气体渗碳法类似,
渗剂为氨. 离子氮化法是在电场作用下,
使电离的氮离子高速冲击作为 阴极的工件.与气体氮化相比, 氮化时间短,氮化层脆性小.
第二次加热为Ac一+三0-五0℃,细化表层.
渗碳后的热处理示意图
常用方法是渗碳缓冷后,重新加热到Ac一+三0-五0℃淬火+低 温回火.此时组织为:
金属热处理的方法

调质热处理指的是金属热处理的方法。
将金属在固态范围内通过一定方式的加热、保温和冷却处理程序,使金属的性能和显微组织获得改善或改变,这种工艺方法称为热处理。
根据热处理的目的不同,有不同的热处理方法,主要可分为下述几种:(1)退火(代号Th):在退火热处理炉内,将金属按一定的升温速度加热到临界温度以上300~500℃左右,其显微组织将发生相变或部分相变,例如钢被加热到此温度时,珠光体将转变为奥氏体。
然后保温一段时间,再缓慢冷却(一般为随炉冷却)至室温出炉,这整个过程称为退火处理。
退火的目的是清除热加工时产生的内应力,使金属的显微组织均匀化(得到近似平衡的组织),改善机械性能(例如降低硬度,提高塑性、韧性和强度等),改善切削加工性能等等。
视退火处理工艺的不同,可分为普通退火、双重退火、扩散退火、等温退火、球化退火、再结晶退火、光亮退火、完全退火、不完全退火等多种退火工艺方式。
(2)正火(代号Z):在热处理炉内,将金属按一定的升温速度加热到临界温度以上200~600℃左右,使显微组织全部变成均匀的奥氏体(例如钢在此温度时,铁素体完全转变为奥氏体,或者二次渗碳体完全溶解于奥氏体),保温一段时间,然后置于空气中自然冷却(包括吹风冷却和堆放自然冷却,或者单件在无风空气中自然冷却等多种方法),这整个过程称为正火处理。
正火是退火的一种特殊形式,由于其冷却速度比退火快,能得到较细的晶粒和均匀的组织,使金属的强度和硬度有所提高,具有较好的综合机械性能。
(3)淬火(代号C):在热处理炉内,将金属按一定的升温速度加热到临界温度以上300~500℃左右,使显微组织全部转变成均匀的奥氏体,保温一段时间,然后快速冷却(冷却介质包括水、油、盐水、碱水等等),获得马氏体组织,可显着提高金属的强度、硬度和耐磨性等等。
淬火时的快速冷却导致的急剧组织转变会产生较大的内应力,并使脆性增大,因此必须随后及时进行回火处理或时效处理,以获得高强度与高韧性相配合的性能,一般较少仅仅采用淬火处理的工艺。
化学镀镍热处理
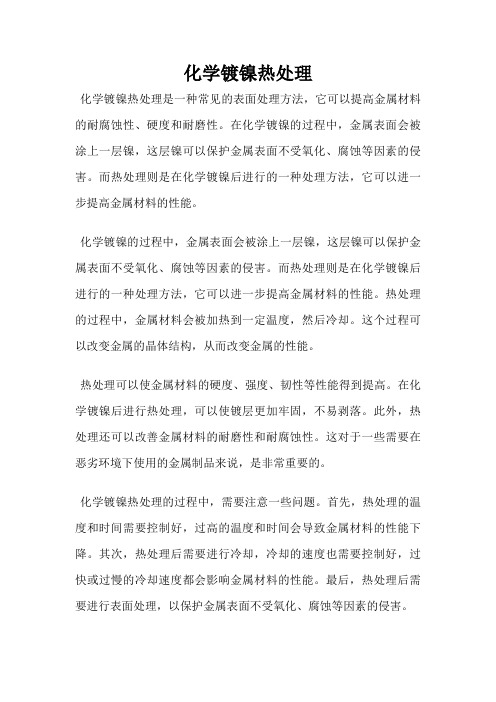
化学镀镍热处理
化学镀镍热处理是一种常见的表面处理方法,它可以提高金属材料的耐腐蚀性、硬度和耐磨性。
在化学镀镍的过程中,金属表面会被涂上一层镍,这层镍可以保护金属表面不受氧化、腐蚀等因素的侵害。
而热处理则是在化学镀镍后进行的一种处理方法,它可以进一步提高金属材料的性能。
化学镀镍的过程中,金属表面会被涂上一层镍,这层镍可以保护金属表面不受氧化、腐蚀等因素的侵害。
而热处理则是在化学镀镍后进行的一种处理方法,它可以进一步提高金属材料的性能。
热处理的过程中,金属材料会被加热到一定温度,然后冷却。
这个过程可以改变金属的晶体结构,从而改变金属的性能。
热处理可以使金属材料的硬度、强度、韧性等性能得到提高。
在化学镀镍后进行热处理,可以使镀层更加牢固,不易剥落。
此外,热处理还可以改善金属材料的耐磨性和耐腐蚀性。
这对于一些需要在恶劣环境下使用的金属制品来说,是非常重要的。
化学镀镍热处理的过程中,需要注意一些问题。
首先,热处理的温度和时间需要控制好,过高的温度和时间会导致金属材料的性能下降。
其次,热处理后需要进行冷却,冷却的速度也需要控制好,过快或过慢的冷却速度都会影响金属材料的性能。
最后,热处理后需要进行表面处理,以保护金属表面不受氧化、腐蚀等因素的侵害。
化学镀镍热处理是一种常见的表面处理方法,它可以提高金属材料的性能。
在进行化学镀镍热处理时,需要注意控制好温度、时间和冷却速度等因素,以保证金属材料的性能得到最大的提升。
金属热处理详解.pptx

材料成形基础-HT
5
第6页/共15页
§3 淬火和正火
一、 淬火 淬火是将钢件加热到 或Ac1以上某一温度,保持一定时间,然后以适当的速度冷却 获得马氏体和(或)贝氏体组织的热处理工艺。 目的:提高钢件的硬度和耐磨性,淬火+不同回火,获得各种需要的性能,是强化 钢的主要方法。
材料成形基础-HT
6
第7页/共15页
淬火介质:淬火冷却时所用的介质。 钢的种类不同,淬火介质不同,常用介质:水、油。 水便宜,冷却能力较强,碳素钢件用的多。 油冷却能力较水低、成本高,但是,可以防止工件产生裂纹等缺陷,主要用于合金 钢淬火的场合。
材料成形基础-HT
7
第8页/共15页
二 、回火
回 火 是 钢 件 淬 硬 后 , 再 加 热 至 Ac1以 下 的 某 一 温 度 , 保 温 一 定 时 间 , 然 后 冷 却 到 室 温的热处理工艺。
材料成形基础-HT
4
第5页/共15页
二、正火
正火是将钢材或钢件加热到或Accm以上30~50℃,保温适当的时间后,在静止空气 中冷却的热处理工艺。
把钢件加热到以上100~150℃的正火则称为高温正火。 与退火类似,冷却速度比退火快。钢件正火后的强度和硬度比退火稍高,但消除残 余应力不彻底。又操作简便、生产率高,所以,正火常优先采用。低碳钢件可代替退火。
刃具、量具、 冷冲模等
58~65
弹簧、钢丝绳 等
35~50
连杆、齿轮及 轴类
20~30
材料成形基础-HT
9
第10页/共15页
§4 表面热处理和化学热处理
一、表面淬火 表面淬火是仅对工件表层进行淬火的工艺。 目的:为了获得高硬度的表面层和有利的残余应力分布,提高工件的硬度和耐磨性。 表面淬火加热的方法很多,如感应加热、火焰加热、电接触加热、激光加热等。
金属表面加工

金属表面加工1. 引言金属表面加工是指对金属材料的表面进行加工处理,以改变其表面性能、外观质量和尺寸精度的一种技术方法。
金属表面加工广泛应用于各个行业,如机械制造、汽车制造、航空航天等。
本文将介绍金属表面加工的常用方法以及其工艺流程。
2. 常用方法金属表面加工的常用方法主要包括机械加工、化学处理、热处理和涂层等几种。
2.1 机械加工机械加工是一种利用机械力对金属材料进行切削、切割、钻孔、铣削等的方法。
常见的机械加工方法包括车削、铣削、钻孔等。
机械加工能够实现高精度的表面加工,但对材料的切削力较大,容易引起变形和损伤。
2.2 化学处理化学处理是一种利用化学反应对金属材料表面进行腐蚀、溶解或沉积等处理的方法。
常见的化学处理方法包括酸洗、电镀、酸洗等。
化学处理可以改变金属材料的表面性能和外观质量,但可能引起环境污染和腐蚀。
2.3 热处理热处理是一种利用热能对金属材料进行加热、冷却等处理的方法。
常见的热处理方法包括淬火、退火、正火等。
热处理可以改变金属材料的晶体结构、硬度、强度等性能,但会使材料的尺寸产生变化。
2.4 涂层涂层是一种在金属表面形成覆盖层的方法,常见的涂层包括喷涂、电镀、热喷涂等。
涂层可以提高金属材料的耐腐蚀性、耐磨性和美观度,但涂层的质量与材料的附着力有很大关系。
3. 加工工艺流程金属表面加工的工艺流程根据加工方法的不同而有所差异,下面以喷涂涂层为例介绍金属表面加工的一般工艺流程。
1.准备工作:清洁金属表面,去除杂质和油脂。
2.喷涂底漆:选择合适的底漆,并使用喷涂设备将底漆均匀地涂在金属表面上。
3.中间处理:根据需要,可以进行中间处理,如研磨、腐蚀等。
4.涂层喷涂:选择合适的涂层材料,并使用喷涂设备将涂层均匀地涂在金属表面上。
5.固化处理:将喷涂后的金属材料置于适当的环境中,使涂层固化。
6.检验和修整:对固化后的金属表面进行检验,如检查涂层的附着力和厚度等,并进行必要的修整和修复。
7.完成:经过以上工艺步骤,金属表面加工完成。
金属表面化学热处理

第三节金属表面化学热处理1、什么叫金属表面化学热处理?表面热处理是指仅对零部件表层加热、冷却,从而改变表层组织和性能而不改变成分的一种工艺,是最基本、应用最广泛的材料表面改性技术之一。
金属表面化学热处理是利用元素扩散性能,使合金元素渗入金属表层的一种热处理工艺。
2、工艺过程首先将工件置于含有渗入元素的活性介质中加热到一定温度,使活性介质通过分解并释放出欲渗入元素的活性原子、活性原子被表面吸附并溶入表面、溶入表面的原子向金属表层扩散渗入形成一定厚度的扩散层,从而改变表层的成分、组织和性能。
3、化学热处理的基本过程化学热处理包括三个基本过程,即①化学渗剂分解为活性原子或离子的分解过程;②活性原子或离子被钢件表面吸收和固溶的吸收过程;③被渗元素原子不断向内部扩散的扩散过程。
4、金属表面化学热处理的特点?和表面淬火不同,化学热处理后的工件表面不仅有组织的变化,而且也有化学成分的变化。
5、金属表面化学热处理的目的?一、提高金属表面的强度、硬度和耐磨性。
如渗氮、渗硼等. 渗氮硬度可达950HV~~1200HV,渗硼硬度可达1400HV~~2000HV.常用的硬度单位有布氏硬度、洛氏硬度和维氏硬度等.什么叫渗氮?渗氮,就是把工件置于含有氮原子的介质中加热到一定温度,保温一段时间后,在工件表面形成一层坚硬的渗氮层。
说白了就是在一定温度下一定介质中使氮原子渗入工件表层。
二、提高材料疲劳强度。
如渗氮、渗硼、渗铬。
三、使金属表面具有良好的抗粘着、抗咬合的能力和降低摩擦系数。
如渗硫等。
四、提高金属表面的耐蚀性。
如渗氮、渗铝等。
5、金属表面化学热处理的性能?化学热处理后的钢件表面可以获得比表面淬火所具有的更高的硬度、耐磨性和疲劳强度;心部在具有塑性和韧性的同时,还可获得较高的强度。
6、化学热处理的种类i.固体法。
(粉末填充法、膏剂涂覆法、电热旋流法、覆盖层扩散法)ii.液体法(包括盐浴法、电解盐浴法、水溶液电解法等)iii.气体法(固体气体法、间接气体法、流动粒子炉法)iv.等离子法。
金属表面氮化处理工艺
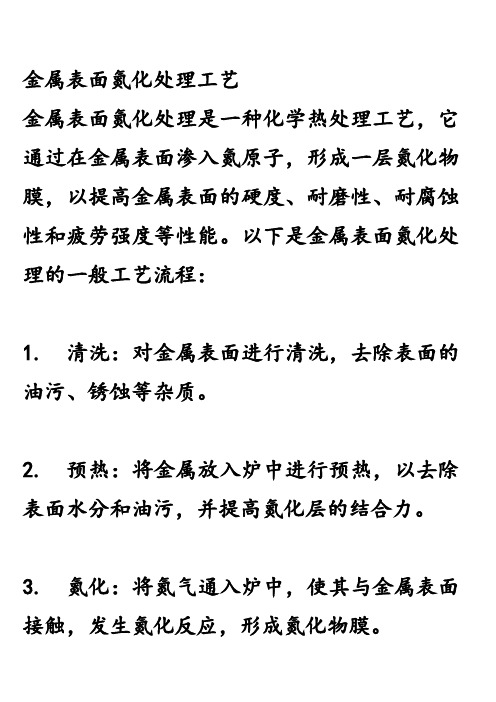
金属表面氮化处理工艺
金属表面氮化处理是一种化学热处理工艺,它通过在金属表面渗入氮原子,形成一层氮化物膜,以提高金属表面的硬度、耐磨性、耐腐蚀性和疲劳强度等性能。
以下是金属表面氮化处理的一般工艺流程:
1. 清洗:对金属表面进行清洗,去除表面的油污、锈蚀等杂质。
2. 预热:将金属放入炉中进行预热,以去除表面水分和油污,并提高氮化层的结合力。
3. 氮化:将氮气通入炉中,使其与金属表面接触,发生氮化反应,形成氮化物膜。
4. 冷却:氮化处理后,将金属从炉中取出,进行自然冷却或淬火冷却。
5. 后处理:对氮化处理后的金属表面进行清洗、抛光等后处理,以获得更好的表面质量。
需要注意的是,不同的金属材料和氮化工艺参数会对氮化层的性能产生影响,因此在实际应用中需要根据具体情况进行选择和调整。
- 1、下载文档前请自行甄别文档内容的完整性,平台不提供额外的编辑、内容补充、找答案等附加服务。
- 2、"仅部分预览"的文档,不可在线预览部分如存在完整性等问题,可反馈申请退款(可完整预览的文档不适用该条件!)。
- 3、如文档侵犯您的权益,请联系客服反馈,我们会尽快为您处理(人工客服工作时间:9:00-18:30)。
2018/11/25
16
4.离子轰击渗镀法
离子轰击渗镀法是利用物质的第四态 —— 等离子体进行渗镀。 等离子体是利用低真空下气体辉光放电 获得的,因为离子活性比原子高,加上 电场的作用,因此渗速较高,质量较好。 但是该法除离子氮化已经成熟,包括渗 碳在内的离子渗金属尚在开发之中。
2018/11/25
2018/11/25 4
(三)化学热处理渗层的基本组织类型
( 1 )形成单相固溶体。如渗碳层中的 α 铁素体相等。
(2)形成化合物。如渗氮层中的ε相 (F2-3N),渗硼层中Fe2B等。 (3)化学热处理后,一般可同时存在固 溶体、化合物的多相渗层。
2018/11/25
5
(四)化学热处理种类
根据渗入元素的介质所处状态不同,化学热处 理可分以下几类: ( 1 )固体法:包括粉末填充法、膏剂涂覆法、电 热旋流法、覆盖层(电镀层、喷镀层等)扩散法等。 ( 2 )液体法:包括盐浴法、电解盐浴法、水溶液 电解法等。 ( 3 )气体法:包括固体气体法、间接气体法、流 动粒子炉法等。 (4)等离子法:
2018/11/25 6
按复合手段划分有 电泳渗、 料浆渗(或膏剂渗)、 喷涂渗、 电镀渗、 化学镀渗等。
2018/11/25
7
热渗镀---化学热处理
2018/11/25
8
1.固渗法
①粉末包渗法
在粉末中加入了防粘结粉末(如 Al2O3 ) 和活化剂(助渗剂)。活化剂一般为卤化 物,如 NH4CI , NH4Br , NH4I 等。包渗 示意图见图4-2。
2018/11/25 1
热渗镀→化学热处理
用加热扩散的方法把一种或几种元素渗入基 体金属的表面,可得到一扩散合金层,但有 时表面上还会残留一薄的覆层。因此被称为 热渗镀。
突出特点:表面强化层的形成主要依靠加热扩散的 作用,因而不存在结合力不足的问题。 热渗镀材料的选择范围很宽,渗入不同元素可得到 不同组织和性能的表面,这些性能包括耐腐蚀性、 耐磨性、耐高温氧化性等。
一、概述
(一)金属表面化学热处理过程 金属表面化学热处理是利用元素扩散性能,使合金 元素渗入金属表层的一种热处理工艺。 其基本工艺过程是: 首先将工件置于含有渗入元素的活性介质中加热到 一定温度, 使活性介质通过分解,并释放出欲渗入元素的活性 原子, 活性原子被表面吸附并溶入表面、 溶入表面的原子向金属表层扩散渗入形成一定厚度 的扩散层,从而改变表层的成分、组织和性能。
2018/11/25 13
③盐浴法
盐浴法是目前世界上采用的较新的热 渗镀技术,其基本原理是在金属盐熔融 液体中加入 V , Nb , Cr , Ti , Ta 等铁合 金粉末,然后把含有较高C,N的钢件浸 入(可预先进行渗碳、氮化或碳、氮共 渗 ) , 在 800—1250℃ 温 度 下 , 经 过 0.5—10h 的时间后,可在表面上形成一 极硬的金属的碳氮化合物薄层,从而赋 予工件表面高的耐磨性。
17
5.复合渗
复合渗实际上是固渗的发展,即采用各种镀 层手段先在工件表面制造一固相涂层,然后 把工件连同涂层一起加热。 加热的方法很多,诸如普通加热炉加热、高 频感应加热、通电加热、辉光放电加热,以 及电子束、离子束加热等。 ①电泳渗 、②料浆渗(或称膏剂渗) 、③ 喷镀渗 、④电镀渗 、⑤化学镀渗 、⑥真空 渗镀
2018/11/25 12
②熔烧法
熔烧法是把渗镀金属或合金粉末加粘结 剂后制成料浆,再将料浆均匀涂敷于工 件表面上,干燥后在惰性气体或真空环 境中以稍高于料浆熔点的温度加热烧 结.通过液固界面扩散而形成合金层。 与热浸法相比,该法能获得成分和厚度 都很均匀的渗层,同时具有热传递性好、 渗速快等特点。
2018/11/25 11
2.液渗法
①热浸法 将工件直接浸入某一液态金属中,经较短 时间即形成合金镀层。 当浸渍时间极短时,所形成的镀层只是附着层 而不是扩散层,因而与基体金属结合不牢固, 因此一般在热浸后还要加热使镀层进行扩散, 以形成合金层。 优点:设备简单,操作容易,因而被广泛采用。 这种方法多用于钢铁制品的镀锌、镀铝、镀锡 等。
2018/11/25 14
3.气渗法
气渗首先把工件加热到渗剂原子在基体中能产 生显著扩散的温度,然后把含有渗镀金属卤化 物(MCl2)的氢气通入,气体和表面接触时, 工件表面的金属A和氢本身与MCl2发生反应。
反应生成的活性原子[M]渗入工件表面。来自2018/11/2515
实现气渗工艺的具体方法很多,大致可分为两大 类: 一类是渗镀金属同工件不在同一空间,用氢气做 载体把欲渗金属的卤化物运载到工件表面; 另一类是渗镀金属同工件在同一空间,使 HCl 气 体先流过被加热了的渗剂金属产生金属氯化物气 体,随后使氯化物气体流经金属表面,置换出活 性原子[M」,进行渗镀。。 优点:渗层厚度均匀,易控制,对异形件和小孔 结构的渗镀效果好,且无粉尘,劳动条件好。
以NH4Cl为例,加热时发生下 列反应:
2018/11/25
9
粉末包渗法的优点: 设备简单,操作容易,适用于形 状复杂的工件的渗镀; 缺点: 效率低,尺寸受限制,温度高, 时间长,基体金属的强度有一定降 低。
2018/11/25
10
②流化床法
与粉末包渗法相似,不同之处是将工 件放于带有固体渗剂的流化床内,然后 加热,同时通入卤气和运载气体(H2 , Ar ),使之与流体粒子反应产生欲渗金 属的活性原子渗入工件。 特点:传热性好,渗速快,渗层质量高 并有利于机械化和自动化; 缺点:流化床设备装置成本极高,运转 费用大,因此这种方法尚未推广使用。
2018/11/25 2
(二)金属表面化学热处理的目的
(1)提高金属表面的强度、硬度和耐磨 性。
如渗氮可使金属表面硬度达到950HV~ 1200HV; 渗硼可使金属表面硬度达到1400HV~ 2000HV等,因而工件表面具有极高的耐 磨性。
2018/11/25 3
(2)提高材料疲劳强度。 如渗碳、渗氮、渗铬等渗层中由于相 变使体积发生变化,导致表层产生很大的残 余压应力,从而提高疲劳强度。 ( 3 )使金属表面具有良好的抗粘着、抗咬 合的能力和降低摩擦系数,如渗硫等。 ( 4 )提高金属表面的耐蚀性,如渗氮、渗 铝等。