锂电池极片辊压工艺基础解析
锂电池辊压工艺中存在的问题及解决措施
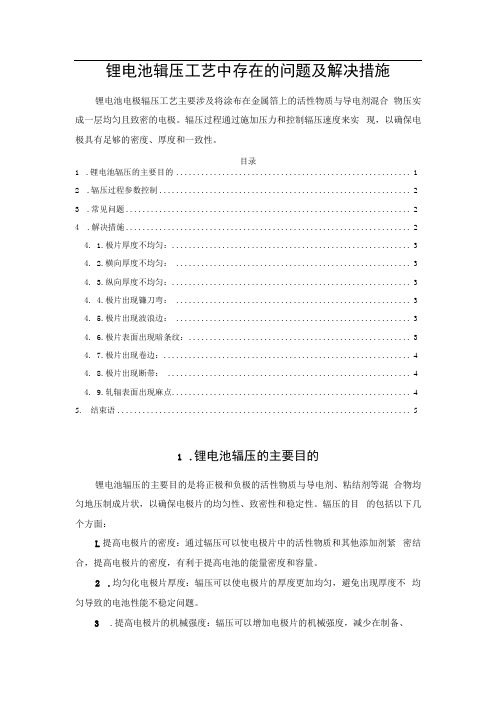
锂电池辑压工艺中存在的问题及解决措施锂电池电极辐压工艺主要涉及将涂布在金属箔上的活性物质与导电剂混合物压实成一层均匀且致密的电极。
辐压过程通过施加压力和控制辐压速度来实现,以确保电极具有足够的密度、厚度和一致性。
目录1.锂电池辐压的主要目的 (1)2.辐压过程参数控制 (2)3.常见问题 (2)4.解决措施 (2)4. 1.极片厚度不均匀: (3)4. 2.横向厚度不均匀: (3)4. 3.纵向厚度不均匀: (3)4. 4.极片出现镰刀弯: (3)4. 5.极片出现波浪边: (3)4. 6.极片表面出现暗条纹: (3)4. 7.极片出现卷边: (4)4. 8.极片出现断带: (4)4. 9.轧辐表面出现麻点 (4)5. 结束语 (5)1.锂电池辐压的主要目的锂电池辐压的主要目的是将正极和负极的活性物质与导电剂、粘结剂等混合物均匀地压制成片状,以确保电极片的均匀性、致密性和稳定性。
辐压的目的包括以下几个方面:L提高电极片的密度:通过辐压可以使电极片中的活性物质和其他添加剂紧密结合,提高电极片的密度,有利于提高电池的能量密度和容量。
2.均匀化电极片厚度:辐压可以使电极片的厚度更加均匀,避免出现厚度不均匀导致的电池性能不稳定问题。
3.提高电极片的机械强度:辐压可以增加电极片的机械强度,减少在制备、组装和使用过程中的断裂和变形。
4.改善电极片的电导率:通过辐压可以使电极片中的导电剂均匀分布,提高电极片的电导率,有利于提高电池的充放电性能。
2.辐压过程参数控制在锂电池制作中,辐压是电池正极和负极片时应控制好以下几个方面:1、辐压温度:控制辐压温度能够影响电池片与电解质层、隔膜的结合程度, 一般需要在一定的温度范围内进行辐压。
2、辐压压力:合适的辐压压力能够确保电池片与电解质层、隔膜的紧密结合,但过大的压力可能会导致电池片变形或损坏。
3、辐压速度:辐压速度的控制也是辐压过程中需要考虑的因素,适当的辐压速度可以确保复合过程的均匀性。
磷酸铁锂极片压实与辊压的关系_解释说明以及概述

磷酸铁锂极片压实与辊压的关系解释说明以及概述1. 引言磷酸铁锂(LiFePO4)作为一种新型的锂离子电池正极材料,由于其具有优异的安全性、稳定性和环保性能而受到广泛关注。
在制备磷酸铁锂极片的过程中,压实和辊压等工艺步骤发挥着重要作用。
本文旨在探讨磷酸铁锂极片压实与辊压之间的关系,并解释说明其原理与机制。
1.1 概述首先,我们将概述磷酸铁锂极片的压实过程以及辊压对其性能的影响。
通过深入了解这些工艺步骤的基本原理,可以更好地理解磷酸铁锂电池性能优化的途径,并且为进一步提高其电化学性能提供指导。
1.2 文章结构接下来,我们将介绍本文的结构安排。
文章包括五个主要部分:引言、磷酸铁锂极片压实与辊压的关系、解释说明磷酸铁锂极片压实与辊压的关系、实验与案例分析以及结论与展望。
每个部分都有其独特的内容和重点。
1.3 目的最后,我们将说明本文的主要目的。
通过深入探讨磷酸铁锂极片压实与辊压之间的关系,我们旨在揭示其影响机制,并为优化磷酸铁锂电池性能提供新思路和方法。
同时,通过实验和案例分析,我们将验证和加强理论推断,并展望未来可能的研究方向。
随着全球对高性能锂离子电池需求的不断增长,了解和优化磷酸铁锂电池性能的方法变得尤为重要。
因此,在本文中详细探讨磷酸铁锂极片压实与辊压的关系是极为必要且具有意义的。
2. 磷酸铁锂极片压实与辊压的关系2.1 磷酸铁锂极片的压实过程磷酸铁锂(LiFePO4)作为一种新兴的正极材料,具有高安全性、良好的电化学性能和长寿命等优点,在锂离子电池中得到广泛应用。
在制备过程中,磷酸铁锂极片需要经过压实过程,将粉末材料紧密堆积形成均匀且致密的极片。
2.2 辊压对磷酸铁锂极片性能的影响辊压是一种常用的压实工艺,通过辊轧机将磷酸铁锂粉末材料进行挤压和变形,从而提高其密度和力学性能。
辊压可以改善磷酸铁锂极片的结构致密度,并提高其电导率、容量和循环寿命等性能指标。
此外,辊压还可以调控磷酸铁锂极片中晶体结构、颗粒大小及分布等微观结构参数。
锂离子电池辊压工艺

锂离子电池辊压工艺锂离子电池辊压工艺是一种有利于流体化生产的锂离子电池生产工艺,它是将涂布好的正负极片通过辊压设备将正负极片压紧,从而形成电池正负极接触面,并通过其他工序完善电池的组装工艺,从而达到电池的组装和完善的目的。
2. 工艺特点(1)辊压工艺的技术要求比较严格,辊压设备要求具备较强的压力精度,能够精确的控制压力,并且正负极片的厚度也必须保持一定的精度要求,同时特殊的表面处理要求也得到了有效的满足。
(2)辊压工艺的特点是快速、不变形、省时、省力,对正负极片的厚度要求也相对较低,从而能够降低过厚的正负极片产生的表面损耗,提高电池产品的成型效果。
(3)辊压工艺还具有良好的灵活性和可靠性,它可以根据电池的型号和规格随意更改,实现快速的电池更换,提高了工作效率。
3. 设备要求辊压工艺所需要的设备主要包括:(1)辊压机:需要能够满足规定的压力要求,正负极片的厚度必须保持一定的精度要求,能够有效的将正负极片压紧,从而将正负极片的接触面紧密接合。
(2)辊压轴:辊压工艺的核心设备,需要具有良好的抗磨损、耐腐蚀性能,同时能够有效的控制正负极片的厚度,保持一定的表面处理精度。
(3)辊压组件:辊压组件的设计要求要符合正负极片的设计规范,誊损要合理,正负极片要保持足够的表面粘结力,以及一定的弹性。
4. 操作要求(1)在进行辊压工艺前,需要首先将正负极片涂布好,确保正负极片接触面涂料均匀,接触面涂布厚度一致。
并且在辊压前,需要辊压机进行调试,确保辊压机的压力是否能够达到规定要求。
(2)正负极片在辊压工艺过程中,需要注意正负极片的厚度调节,确保正负极片的厚度调节在一个可接受的范围内,以保证电池的质量。
(3)在辊压工艺过程中,需要定期对辊压机进行维护,以确保辊压机的正常运行,并保持辊压机的压力精度。
5. 安全注意事项(1)辊压过程中必须注意控制压力,确保压力控制在规定的范围内,以免对正负极片造成损坏。
(2)辊压过程中,应注意人身安全,不要接触辊压机的高速运转部分,防止发生受伤。
锂电池极片辊压工艺基础解析

锂电池极片辊压工艺基础解析锂电池极片辊压工艺基础解析锂离子电池极片制造一般工艺流程为:活性物质,粘结剂和导电剂等混合制备成浆料,然后涂敷在铜或铝集流体两面,经干燥后去除溶剂形成极片,极片颗粒涂层经过压实致密化,再裁切或分条。
辊压是锂电池极片最常用的压实工艺,相对于其他工艺过程,辊压对极片孔洞结构的改变巨大,而且也会影响导电剂的分布状态,从而影响电池的电化学性能。
为了获得最优化的孔洞结构,充分认识和理解辊压压实工艺过程是十分重要的。
辊压工艺基本过程工业生产上,锂电池极片一般采用对辊机连续辊压压实,如图1所示,在此过程中,两面涂敷颗粒涂层的极片被送入两辊的间隙中,在轧辊线载荷作用下涂层被压实,从辊缝出来后,极片会发生弹性回弹导致厚度增加。
因此,辊缝大小和轧制载荷是两个重要的参数,一般地,辊缝要小于要求的极片最终厚度,或载荷作用能使涂层被压实。
另外,辊压速度的大小直接决定载荷作用在极片上的保持时间,也会影响极片的回弹,最终影响极片的涂层密度和孔隙率。
图1 极片辊压过程示意图在轧制速度V cal下,极片通过辊缝时,线载荷可由式(1)计算:q L = F N / W C其中,q L为作用在极片上的线载荷,F N为作用在极片上的轧制力,Wc为极片涂层的宽度。
辊压过程极片微观结构的演变通过辊缝,极片被压实,涂层密度由初始值ρc变为ρc。
压实密度ρc可由,0式(2)计算:其中,m E为单位面积内的电极片重量,m C为单位面积内的集流体重量,h E为电极片厚度,h C为集流体厚度。
而压实密度与极片孔隙率相关,物理上的涂层孔隙率εc,ph可由式(3)计算,其含义为颗粒内部的孔隙和颗粒之间的孔隙在涂层的体积分数:其中,ρph为涂层各组成材料平均物理真密度。
在实际的辊压工艺中,随着轧制压力变化,极片涂层压实密度具有一定规律,图2为极片涂层密度与轧制压力的关系。
图2 极片涂层密度与轧制压力的关系曲线 I 区域,为第一阶段。
锂电池极片辊压工艺变形分析
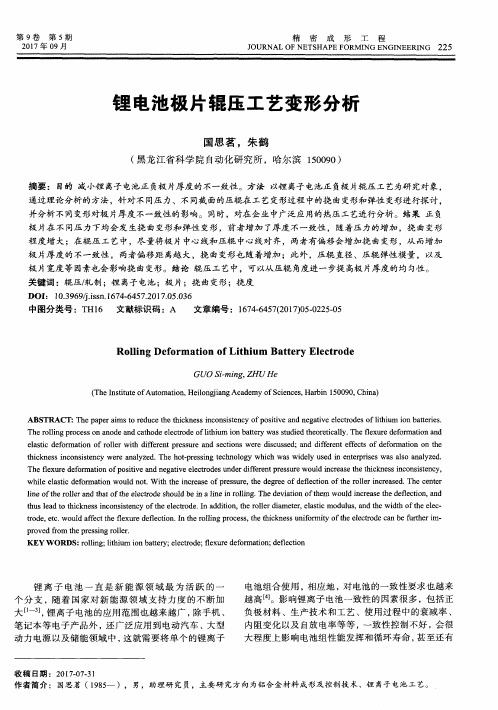
极 片厚 度的 不一致 性 ,两者偏移距 离越 大,挠 曲变形也随 着增加 ;此外 ,压辊 直径 、压辊弹性模量 ,以及
极 片宽度 等 因素也会影响挠 曲变形 。结论 辊压 工艺 中,可以从 压辊 角度进 一步提 高极片厚度的均 匀性 。
关键词 :辊 压/ 轧制 ;锂 离子电池 ;极 片;挠 曲变形 ;挠度 DOI :1 0 . S 9 6 9  ̄ . i s s0 1 7 . 0 5 . 0 3 6
中图分类号 :T H1 6 文献标识码 :A
文章编号 :1 6 7 4 — 6 4 5 7 ( 2 0 1 7 ) 0 5 — 0 2 2 5 . 0 5
Ro l l i ng De f o r ma t i o n of Li t hi um Ba t t e r y El e c t r od e
摘要 :目的 减小锂 离子 电池正 负极 片厚度 的不一致性 。方 法 以锂 离子 电池正 负极 片辊 压工艺为研 究对象 , 通过理论 分析的方法 ,针对不 同压 力、不 同截 面的压辊在 工艺变形过程 中的挠曲变形和弹性 变形进行探讨 , 并分析 不同 变形对极 片厚度不一致性的影响 。同时 ,对在 企业 中广泛应用的热压工艺进行 分析 。结果 正 负 极 片在 不 同压 力下均会发 生挠 曲变形和 弹性变形 ,前者增加 了厚 度不一致性 ,随着压力的增加 ,挠 曲变形 程度 增大 ;在辊 压工 艺中,尽 量将 极 片中心线和压辊 中心 线对齐 ,两者有偏移会 增加 挠 曲变形 ,从 而增加
T h e r o l l i n g p r o c e s s o n a n o d e a n d c  ̄h o d e e l e c t r o d e o f l i t h i u m i o n b a t t e r y wa s s ud t i e d t h e o r e t i c a l l y . T h e le f x u r e d e : f o r m ̄i o n a n d e l a s t i c d e f o r ma t i o n o f r o l l e r wi t h d i f f e r e n t p r e s s re u a n d s e c t i o n s we r e d i s c u s s e d ;a n d d i fe r e n t e f f e c t s o f d e f o r ma t i o n o n he t
锂电池辊边工艺
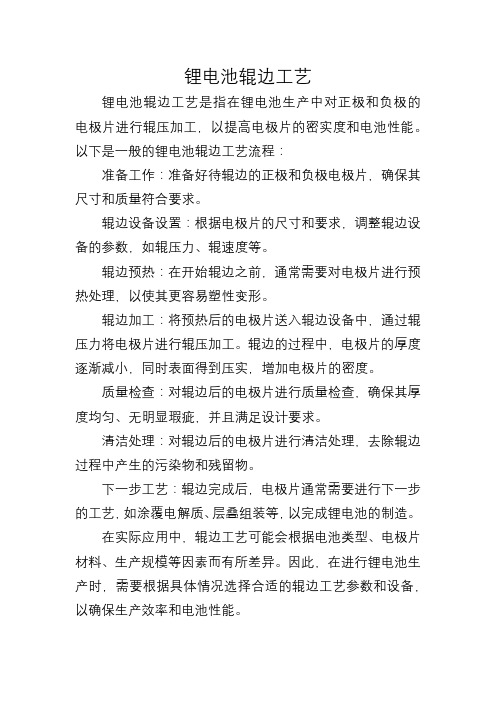
锂电池辊边工艺
锂电池辊边工艺是指在锂电池生产中对正极和负极的电极片进行辊压加工,以提高电极片的密实度和电池性能。
以下是一般的锂电池辊边工艺流程:
准备工作:准备好待辊边的正极和负极电极片,确保其尺寸和质量符合要求。
辊边设备设置:根据电极片的尺寸和要求,调整辊边设备的参数,如辊压力、辊速度等。
辊边预热:在开始辊边之前,通常需要对电极片进行预热处理,以使其更容易塑性变形。
辊边加工:将预热后的电极片送入辊边设备中,通过辊压力将电极片进行辊压加工。
辊边的过程中,电极片的厚度逐渐减小,同时表面得到压实,增加电极片的密度。
质量检查:对辊边后的电极片进行质量检查,确保其厚度均匀、无明显瑕疵,并且满足设计要求。
清洁处理:对辊边后的电极片进行清洁处理,去除辊边过程中产生的污染物和残留物。
下一步工艺:辊边完成后,电极片通常需要进行下一步的工艺,如涂覆电解质、层叠组装等,以完成锂电池的制造。
在实际应用中,辊边工艺可能会根据电池类型、电极片材料、生产规模等因素而有所差异。
因此,在进行锂电池生产时,需要根据具体情况选择合适的辊边工艺参数和设备,以确保生产效率和电池性能。
锂电池极片压实工艺模型 考察活性物质和面密度对孔隙率的影响
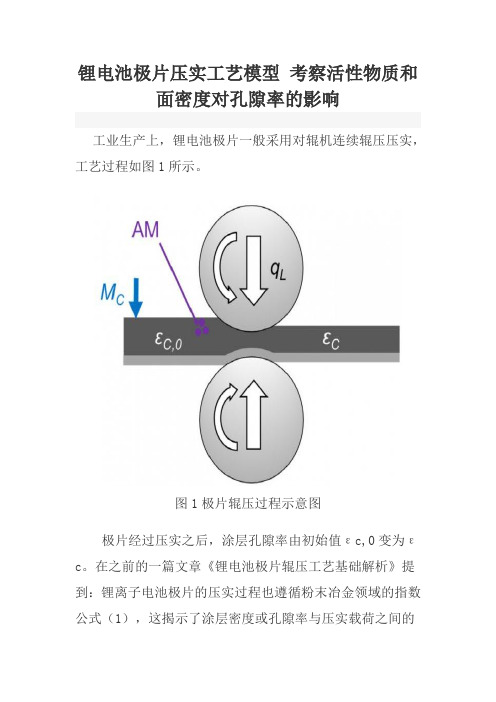
锂电池极片压实工艺模型考察活性物质和面密度对孔隙率的影响工业生产上,锂电池极片一般采用对辊机连续辊压压实,工艺过程如图1所示。
图1极片辊压过程示意图极片经过压实之后,涂层孔隙率由初始值εc,0变为εc。
在之前的一篇文章《锂电池极片辊压工艺基础解析》提到:锂离子电池极片的压实过程也遵循粉末冶金领域的指数公式(1),这揭示了涂层密度或孔隙率与压实载荷之间的关系。
(1)其中,ρc,0是涂层密度初始值,ρc是压实后涂层的密度。
qL为作用在极片上的线载荷,可由式(2)计算:qL=FN/WC(2)FN为作用在极片上的轧制力,WC为极片涂层的宽度。
ρc,max和γC可以通过实验数据拟合得到,分别表示某工艺条件下涂层能够达到的最大压实密度以及涂层压实阻抗。
将压实密度转化成孔隙率,指数公式(1)转变为公式(3):(3)参考文献[1]依据以上压实工艺模型,考察了不同活性物质,不同面密度对极片的压实孔隙率的影响。
原材料的粒径分布和形貌等参数如表1所示,所制备的极片组成和面密度等参数如表2所示。
No.1是两种不同粒径的NCA1和NCA2的混合,No.2-5分别是NCA1、NCM811、NCM622、NCM111,这五种活性物质不同,浆料组成和面密度相同,单面涂布223g/m2。
No.6-12分别是一锅浆料,涂布不同的面密度。
No.13-15是其他的文献报道。
初始孔隙率及最小孔隙率预测理想球形不可压缩的硬质颗粒简单立方堆垛的理论孔隙率为47.64%,实际的锂离子电池极片No.1–5和7–12初始孔隙率基本都在42-48%,与理论值略有偏差,这主要是一方面颗粒不是理想的球形,另一方面涂层中还有粘结剂和导电剂的影响。
而No.6和13–15的初始孔隙率比较高,No.6是因为面密度比较低导致初始孔隙率高,而且从No.6-12极片看,随着极片面密度增加,初始孔隙率逐渐降低,但是减小幅度越来越小。
厚涂层在干燥过程中,上层会对下层施加重力作用,使涂层密度更高些。
细致分析锂离子电池中的极片辊压工艺【钜大锂电】

细致分析锂离子电池中的极片辊压工艺【钜大锂电】先来张图,如上图,这是一款时髦流行的辊压分切一体机图片,通过把涂布后的极卷,运送到辊压机,经过双辊的压力,把极片压薄,控制在我们想要的厚度,达到增强剥离强度、减少离子传输距离的效果。
基本原理则:因此得到:注:R为辊的半径,=H-h简单的公式计算,只是让你明白他们之间的关系。
涂布后极片厚度不变的情况下,辊的直径越大,极片越薄。
极片所需要的厚度,通过张力控制双辊来实现。
辊压后的结构更加稳定,颗粒之间空隙间距更小。
辊压影响克容量、首次库伦效率、倍率性能,循环性能等。
辊压关键点1、厚度影响极片厚度一致性的主要原因有轧辊直线度,辊跳度,辊弯曲等。
轧辊直线度影响因素多是由于长期使用,辊有磨损。
辊跳值则是由辊的刚性有关,刚性越好,辊跳值越小。
辊弯曲则是需要张力和轧件的变形抗力共同决定,轧件变形张力越大,辊弯曲越大,简单来说就是轧纸片和铁片,两者造成的辊弯曲度不一样。
2、打皱影响极片打皱的原因主要有导辊水平度和平行度,张力不均,收卷张力等。
辊压过辊打皱示意图3、PINCH工艺主要是为了消除打皱而提出的一种工艺,通过差速拉伸,使得涂覆区和极耳区长度一致,消除打皱。
在辊压的过程中,极耳区比较薄,双面涂布下是无法接触到轧辊,涂覆区受到辊的压力,两边张力不一致,一般来讲,辊径越小,极片延展越严重,褶皱越厉害。
4、极片反弹上一张老图,如上图:1塌陷期-2初步作用期-3剧烈作用期-4受控反弹期-5自由反弹期。
反弹是一定的,但是反弹率我们希望在可接受的范围,并且稳定下来,使用辊压后烘烤(baking)可以加速极片的反弹并让其尽快稳定下来。
辊压后测试辊压阶段常测量极片厚度、剥离强度、弧高和延伸率。
一般来说,压力越大,膜片区延伸就越大。
一般控制孤高为±3mm之内,延伸率<0.8%。
厚度可实时监测,剥离强度需根据样本检测,如果配备分切设备,还需要测量毛刺,允许毛刺长度<隔膜厚度/2。
锂电池辊压机的辊缝和压力 -回复
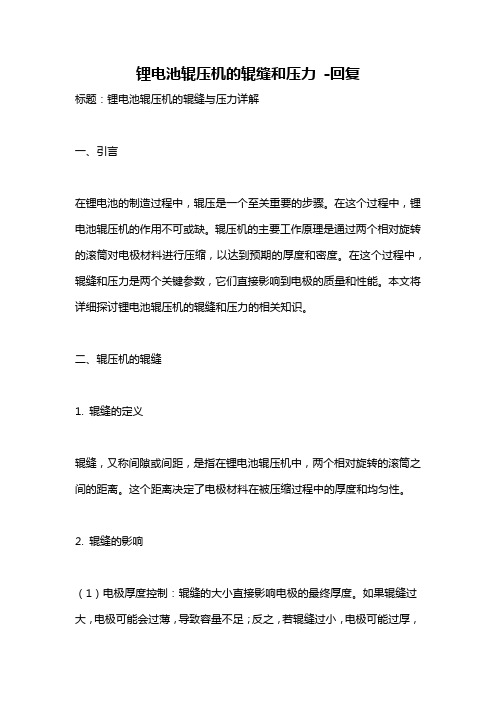
锂电池辊压机的辊缝和压力-回复标题:锂电池辊压机的辊缝与压力详解一、引言在锂电池的制造过程中,辊压是一个至关重要的步骤。
在这个过程中,锂电池辊压机的作用不可或缺。
辊压机的主要工作原理是通过两个相对旋转的滚筒对电极材料进行压缩,以达到预期的厚度和密度。
在这个过程中,辊缝和压力是两个关键参数,它们直接影响到电极的质量和性能。
本文将详细探讨锂电池辊压机的辊缝和压力的相关知识。
二、辊压机的辊缝1. 辊缝的定义辊缝,又称间隙或间距,是指在锂电池辊压机中,两个相对旋转的滚筒之间的距离。
这个距离决定了电极材料在被压缩过程中的厚度和均匀性。
2. 辊缝的影响(1)电极厚度控制:辊缝的大小直接影响电极的最终厚度。
如果辊缝过大,电极可能会过薄,导致容量不足;反之,若辊缝过小,电极可能过厚,影响电池的能量密度和循环性能。
(2)电极均匀性:适当的辊缝可以确保电极材料在压缩过程中的均匀分布,避免局部过厚或过薄,从而提高电极的性能和一致性。
3. 辊缝的调整根据电极材料的特性和电池设计的要求,需要精确调整辊缝的大小。
通常,这可以通过机械或电子方式进行。
机械方式主要是通过调整滚筒的位置来改变辊缝,而电子方式则是通过传感器和控制系统自动调整。
三、辊压机的压力1. 压力的定义在锂电池辊压机中,压力是指两个滚筒在压缩电极材料时施加的力。
这个力的大小直接影响电极的密度和结构。
2. 压力的影响(1)电极密度:压力越大,电极的密度通常越高。
高密度的电极可以提高电池的能量密度和功率密度,但也可能导致电极的导电性下降。
(2)电极结构:适当的压力可以优化电极的微观结构,如颗粒间的接触和粘结,从而提高电极的电化学性能和稳定性。
3. 压力的调整压力的调整应根据电极材料的特性和电池设计的要求进行。
一般来说,对于脆性大的材料,应采用较低的压力,以防止材料破裂;而对于塑性好的材料,可以适当提高压力,以获得更高的密度。
此外,还需要考虑电极的厚度和宽度,以及滚筒的转速等因素。
一文看懂锂电池极片辊压工序

一文看懂锂电池极片辊压工序导读:极片在涂布、干燥完成后,活物质与集流体箔片的剥离强度很低,需要对其进行辊压,以增强活物质与箔片的粘接强度,以防在电解液浸泡、电池使用过程中剥落。
同时,极片辊压可以压缩电芯体积,提高电芯能量密度,降低极片内部活物质、导电剂、粘结剂之间的孔隙率,降低电池的电阻提高电池性能。
一、辊压机介绍为了提高电池极片表面材料的密度及厚度的一致性,正负极片在涂布工序之后须进行滚压,此工序称为电池极片的辊压。
目前国内外锂离子电池厂家均使用二辊辊压机辊压极片,双辊压机是由两个铸钢压实辊以及电机和传动轴组成。
主流机型辊径为500 mm,辊身长度为500 mm~700 mm,辊压出的极片沿宽度方向的厚度一致性较差。
为保证厚度一致性的精度要求,轧辊长度与直径比值往往较小,最终导致极片辊压宽度较窄。
图1 极片轧制生产线示意图而在铜箔、铝箔等箔材制造领域,箔材绝大多数由四辊辊压机辊压制造,表面精度能达到几微米的同时,辊压宽度能达到1 m 以上。
但是当前还没有四辊辊压机在极片辊压中应用的先例?(如果有,欢迎给我们留言补充)图2 左:二辊辊压机辊系布置示意图右:四辊辊压机辊系布置示意图完整的辊压过程是将涂布完成的极片,固定于放卷机构后,将极片正确穿过双辊间隙,并连接收卷系统。
开启辊压模式后,电机带动上下辊同时转动,收卷机构拉动极片将稳步穿过辊压间隙,最终被压到所需压实密度。
辊压机在非工作状态时需要涂一层薄油层,以防其生锈,在使用前用无水乙醇将油层擦干净,并清理收放卷机构、自动纠偏机构。
因此,一个优秀的辊压机必须包含以下八大功能模块:图3:气液增压泵加压式极片轧机轧辊压力调整及快速反应功能:滚压机两只轧辊之间的压力调整是提高电池极片活性物质压实密度的必要条件,由于涂布间歇、单双面交错等因素影响,两辊之间的压力调整必须快速反应。
轧辊间隙调整及准确复位功能:滚压机两只轧辊之间的间隙调整是获得电池极片厚度的必要条件。
锂电池极片压实工艺模型 考察活性物质和面密度对孔隙率的影响
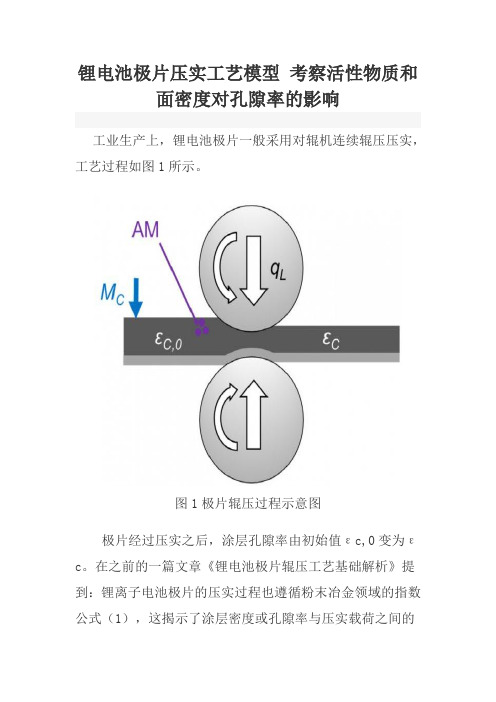
锂电池极片压实工艺模型考察活性物质和面密度对孔隙率的影响工业生产上,锂电池极片一般采用对辊机连续辊压压实,工艺过程如图1所示。
图1极片辊压过程示意图极片经过压实之后,涂层孔隙率由初始值εc,0变为εc。
在之前的一篇文章《锂电池极片辊压工艺基础解析》提到:锂离子电池极片的压实过程也遵循粉末冶金领域的指数公式(1),这揭示了涂层密度或孔隙率与压实载荷之间的关系。
(1)其中,ρc,0是涂层密度初始值,ρc是压实后涂层的密度。
qL为作用在极片上的线载荷,可由式(2)计算:qL=FN/WC(2)FN为作用在极片上的轧制力,WC为极片涂层的宽度。
ρc,max和γC可以通过实验数据拟合得到,分别表示某工艺条件下涂层能够达到的最大压实密度以及涂层压实阻抗。
将压实密度转化成孔隙率,指数公式(1)转变为公式(3):(3)参考文献[1]依据以上压实工艺模型,考察了不同活性物质,不同面密度对极片的压实孔隙率的影响。
原材料的粒径分布和形貌等参数如表1所示,所制备的极片组成和面密度等参数如表2所示。
No.1是两种不同粒径的NCA1和NCA2的混合,No.2-5分别是NCA1、NCM811、NCM622、NCM111,这五种活性物质不同,浆料组成和面密度相同,单面涂布223g/m2。
No.6-12分别是一锅浆料,涂布不同的面密度。
No.13-15是其他的文献报道。
初始孔隙率及最小孔隙率预测理想球形不可压缩的硬质颗粒简单立方堆垛的理论孔隙率为47.64%,实际的锂离子电池极片No.1–5和7–12初始孔隙率基本都在42-48%,与理论值略有偏差,这主要是一方面颗粒不是理想的球形,另一方面涂层中还有粘结剂和导电剂的影响。
而No.6和13–15的初始孔隙率比较高,No.6是因为面密度比较低导致初始孔隙率高,而且从No.6-12极片看,随着极片面密度增加,初始孔隙率逐渐降低,但是减小幅度越来越小。
厚涂层在干燥过程中,上层会对下层施加重力作用,使涂层密度更高些。
锂电池极片辊压工艺基础解析

锂电池极片辊压工艺基础解析锂离子电池极片制造一般工艺流程为:活性物质,粘结剂和导电剂等混合制备成浆料,然后涂敷在铜或铝集流体两面,经干燥后去除溶剂形成极片,极片颗粒涂层经过压实致密化,再裁切或分条。
辊压是锂电池极片最常用的压实工艺,相对于其他工艺过程,辊压对极片孔洞结构的改变巨大,而且也会影响导电剂的分布状态,从而影响电池的电化学性能。
为了获得最优化的孔洞结构,充分认识和理解辊压压实工艺过程是十分重要的。
辊压工艺基本过程工业生产上,锂电池极片一般采用对辊机连续辊压压实,如图1所示,在此过程中,两面涂敷颗粒涂层的极片被送入两辊的间隙中,在轧辊线载荷作用下涂层被压实,从辊缝出来后,极片会发生弹性回弹导致厚度增加。
因此,辊缝大小和轧制载荷是两个重要的参数,一般地,辊缝要小于要求的极片最终厚度,或载荷作用能使涂层被压实。
另外,辊压速度的大小直接决定载荷作用在极片上的保持时间,也会影响极片的回弹,最终影响极片的涂层密度和孔隙率。
图1 极片辊压过程示意图在轧制速度V cal下,极片通过辊缝时,线载荷可由式(1)计算:q L = F N / W C其中,q L为作用在极片上的线载荷,F N为作用在极片上的轧制力,Wc为极片涂层的宽度。
辊压过程极片微观结构的演变通过辊缝,极片被压实,涂层密度由初始值ρc变为ρc。
压实密度ρc可,0由式(2)计算:其中,m E为单位面积内的电极片重量,m C为单位面积内的集流体重量,h E为电极片厚度,h C为集流体厚度。
而压实密度与极片孔隙率相关,物理上的涂层孔隙率εc,ph可由式(3)计算,其含义为颗粒内部的孔隙和颗粒之间的孔隙在涂层的体积分数:其中,ρph为涂层各组成材料平均物理真密度。
在实际的辊压工艺中,随着轧制压力变化,极片涂层压实密度具有一定规律,图2为极片涂层密度与轧制压力的关系。
图2 极片涂层密度与轧制压力的关系曲线 I 区域,为第一阶段。
此阶段压力相对较小,涂层内颗粒产生位移,孔隙被填充,压力稍有增加时,极片的密度快速增加,极片的相对密度变化有规律。
锂离子电池制片中辊压工序的问题分析
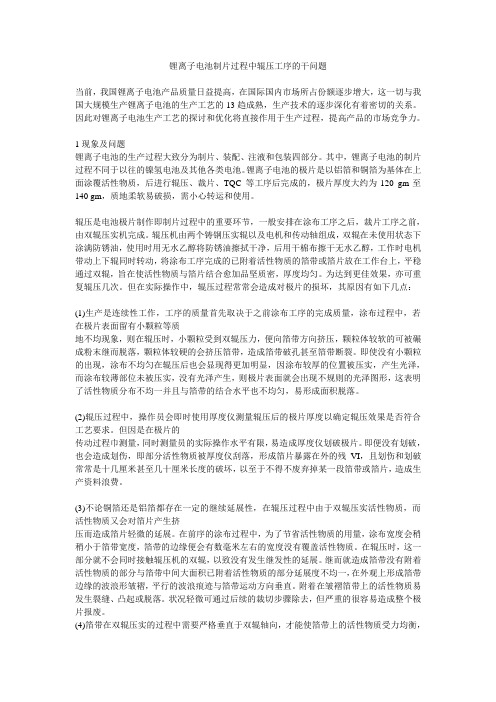
锂离子电池制片过程中辊压工序的干问题当前,我国锂离子电池产品质量日益提高,在国际国内市场所占份额逐步增大,这一切与我国大规模生产锂离子电池的生产工艺的13趋成熟,生产技术的逐步深化有着密切的关系。
因此对锂离子电池生产工艺的探讨和优化将直接作用于生产过程,提高产品的市场竞争力。
1现象及问题锂离子电池的生产过程大致分为制片、装配、注液和包装四部分。
其中,锂离子电池的制片过程不同于以往的镍氢电池及其他各类电池。
锂离子电池的极片是以铝箔和铜箔为基体在上面涂覆活性物质,后进行辊压、裁片、TQC 等工序后完成的,极片厚度大约为120 gm至140 gm,质地柔软易破损,需小心转运和使用。
辊压是电池极片制作即制片过程中的重要环节,一般安排在涂布工序之后,裁片工序之前,由双辊压实机完成。
辊压机由两个铸钢压实辊以及电机和传动轴组成,双辊在未使用状态下涂满防锈油,使用时用无水乙醇将防锈油擦拭干净,后用干棉布擦干无水乙醇,工作时电机带动上下辊同时转动,将涂布工序完成的已附着活性物质的箔带或箔片放在工作台上,平稳通过双辊,旨在使活性物质与箔片结合愈加品坚质密,厚度均匀。
为达到更佳效果,亦可重复辊压几次。
但在实际操作中,辊压过程常常会造成对极片的损坏,其原因有如下几点:(1)生产是连续性工作,工序的质量首先取决于之前涂布工序的完成质量,涂布过程中,若在极片表面留有小颗粒等质地不均现象,则在辊压时,小颗粒受到双辊压力,便向箔带方向挤压,颗粒体较软的可被碾成粉末继而脱落,颗粒体较硬的会挤压箔带,造成箔带破孔甚至箔带断裂。
即使没有小颗粒的出现,涂布不均匀在辊压后也会显现得更加明显,因涂布较厚的位置被压实,产生光泽,而涂布较薄部位未被压实,没有光泽产生,则极片表面就会出现不规则的光泽图形,这表明了活性物质分布不均一并且与箔带的结合水平也不均匀,易形成面积脱落。
(2)辊压过程中,操作员会即时使用厚度仪测量辊压后的极片厚度以确定辊压效果是否符合工艺要求。
锂离子电池极片辊压工序简介
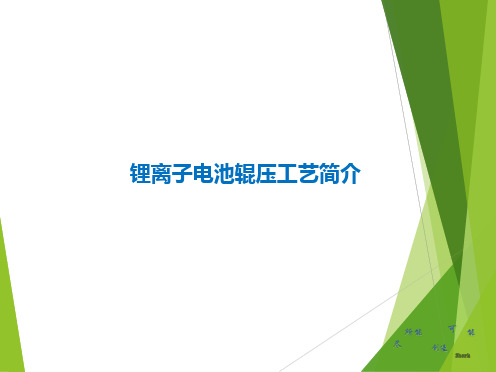
弹导致厚度增加。因此辊缝大小和扎制载
荷是两个重要的参数,所以辊缝要小于要
求的极片最终厚度。辊压速度的大小直接
决定载荷作用在极片上的保持时间,也会
影响极片的回弹,最终影响极片的涂层密
极片你辊压示意图
度和孔隙率。
在辊压速度Vcal下,极片通过辊缝,线载荷可由以下公式计算:
qL=Fn/Wc 其中qL为作用在极片上的线载荷,Fn为作用在极片上的轧制力,Wc为 极片涂层的宽度。
所能 尽
可能
创造
Sherk
三 辊压影响
2.辊压情况对电芯性能的影响
辊压过程会出现的几个典型问题是:
①极片厚度不一致。厚度不一致,意味着活物质密度不一 致,锂离子和电子在极片中传输、传导速率则会有所不同 。当电流密度不同时,极易引起枝晶锂的析出,对电芯性 能不利。此外,极片厚度不同时,活性物质与集流体之间 的接触电阻也是不同的,极片越厚内阻越大,电池极化也 就越严重,影响电芯容量。 ②极片部分位置出现过压。原因可能是涂布时部分位置厚 度过厚,过压后影响电解液的浸润效果,对电芯的性能也 有很大的影响。易出现析锂现象
所能 尽
可能
创造
Sherk
三 辊压影响
1.辊压情况对极片加工状态的影响
辊压后极片的理想状态是极片表面平整、在光下光泽度 一致、留白部分无明显波浪、极片无大程度翘曲。但是 ,在实际生产中操作熟练度、设备运行情况等都会引起 部分问题的产生。
最直接的影响是影响极片分切,分切极片宽度不一致, 极片出现毛刺;辊压结果影响极片的卷绕,严重的翘曲 会造成极片卷绕过程中极片、隔膜间产生较大的空隙, 在热压后会形成某些部分多层隔膜叠加,成为应力集中 点,影响电芯性能。
160 161.1 159
锂离子电池极片辊压工艺模拟

锂离子电池极片辊压工艺模拟来源:mikoWoo LIBLife工业生产上,锂电池极片一般采用对辊机连续辊压压实,如图1所示,在此过程中,两面涂敷颗粒涂层的极片被送入两辊的间隙中,在轧辊线载荷作用下涂层被压实,从辊缝出来后,极片会发生弹性回弹导致厚度增加。
图1 锂电池极片辊压示意图电池极片的轧制不同于金属板材的轧制,比如轧钢的过程是一个板材沿纵向延伸和横向宽展的过程,其密度在轧制过程中不发生变化;而电池极片的轧制是一个正负极板上电极粉体材料压实的过程,其目的在于增加正极或负极材料的压实密度。
压实对极片微结构的控制起决定性作用,影响电池的电化学性能。
辊压是锂电池极片最常用的压实工艺,相对于其他工艺过程,辊压对极片孔洞结构的改变巨大,而且也会影响导电剂的分布状态,从而影响电池的电化学性能。
为了获得最优化的孔洞结构,充分认识和理解辊压压实工艺过程是十分重要的。
文献[1]采用离散元法模拟了锂离子电池极片辊压过程中,微结构的演变过程。
离散元是一种与连续介质力学中的finite element method相区别的数值计算方法,主要用来计算大量颗粒在给定条件下如何运动。
单颗粒力学行为首先,作者采用纳米压痕设备测试了单个颗粒的压缩载荷应力-应变曲线,并采用两种材料本构模型拟合数据:弹塑性模型和Hertz模型,结果如图2所示。
从应力-应变曲线确定材料屈服点,屈服点以下材料主要是弹性行为,颗粒形貌基本无变化(图2c),符合Hertz理论;屈服点以上,材料是塑性行为,颗粒发生断裂(图2b),符合弹塑性理论。
通过大量实验,拟合了屈服应变与颗粒尺寸的关系(图2d)。
Hertz接触理论是研究两物体因受压相触后产生的局部应力和应变分布规律的学科。
1881 年 H.R.赫兹最早研究了玻璃透镜在使它们相互接触的力作用下发生的弹性变形。
他假设:① 接触区发生小变形。
②接触面呈椭圆形。
③相接触的物体可被看作是弹性半空间,接触面上只作用有分布的垂直压力。
锂离子电池极片辊压工序简介.ppt
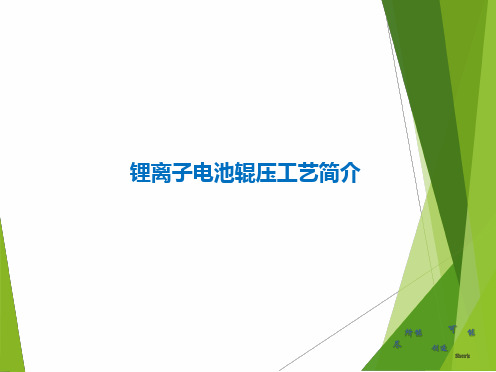
,真空等是否正常。
料:检查来料是否合格(包装有无破损,外观是否正常,生产
日期及批号是否匹配),流程单上是否盖有pass章。
法:严格按照标准作业指导书上的操作步骤进行作业。
环:巡检时严格注意检查车间的温湿度,洁净度是否符合作业
标准。
六 注意事项
1、辊压作业过程中,如非意外,严禁修改压力,走 速等参数; 2、物料搬运过程中,安全操作,勿使卷料磕碰; 3、辊压过程发现问题及时停机检查,联系技术人员 进行调试; 4、正负极毛刷,擦辊装置不允许互换使用; 5、辊压过程出现粘辊现象应立刻停机,清理干净后 方可生产; 6测厚度时保证极片平整,无打皱,刻度对其后再读 书; 7、尾检测试合格后,方可进行下一步工序。
弹导致厚度增加。因此辊缝大小和扎制载
荷是两个重要的参数,所以辊缝要小于要
求的极片最终厚度。辊压速度的大小直接
决定载荷作用在极片上的保持时间,也会
影响极片的回弹,最终影响极片的涂层密 度和孔隙率。
极片你辊压示意图
在辊压速度Vcal下,极片通过辊缝,线载荷可由以下公式计算: qL=Fn/Wc
其中qL为作用在极片上的线载荷,Fn为作用在极片上的轧制力,Wc为 极片涂层的宽度。
极片反弹一是极片内部水分较多,而是辊压时速度太快。极片 反弹问题可以通过使用热辊工艺和控制辊压速度解决。
所能 尽
可能
创造
Sherk
极片厚度反弹
正极辊压时间-厚度变化表格
时间/h 样本点1 样本点2 样本点3 样本点4 样本点5 样本点6 样本点7 样本点8 样本点9
0.08 157.6 160.1 157.5 158.5 157.2 159.1 158.3 159.8 157.4
锂电池极片辊压工艺基础解析
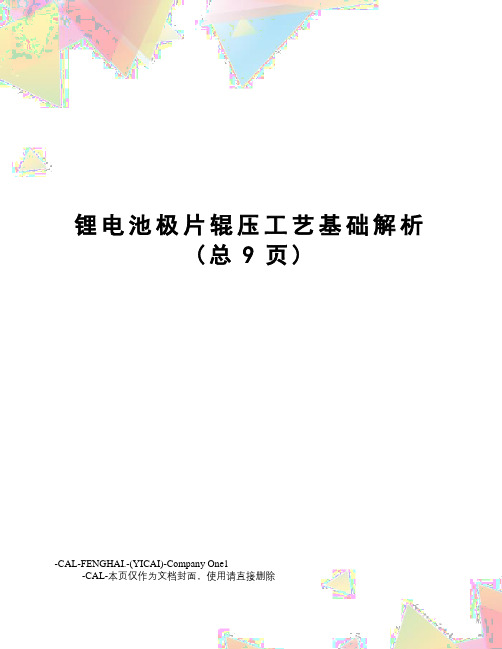
锂电池极片辊压工艺基础解析(总9页)-CAL-FENGHAI.-(YICAI)-Company One1-CAL-本页仅作为文档封面,使用请直接删除锂离子电池极片制造一般工艺流程为:活性物质,粘结剂和导电剂等混合制备成浆料,然后涂敷在铜或铝集流体两面,经干燥后去除溶剂形成极片,极片颗粒涂层经过压实致密化,再裁切或分条。
辊压是锂电池极片最常用的压实工艺,相对于其他工艺过程,辊压对极片孔洞结构的改变巨大,而且也会影响导电剂的分布状态,从而影响电池的电化学性能。
为了获得最优化的孔洞结构,充分认识和理解辊压压实工艺过程是十分重要的。
??辊压工艺基本过程?工业生产上,锂电池极片一般采用对辊机连续辊压压实,如图1所示,在此过程中,两面涂敷颗粒涂层的极片被送入两辊的间隙中,在轧辊线载荷作用下涂层被压实,从辊缝出来后,极片会发生弹性回弹导致厚度增加。
因此,辊缝大小和轧制载荷是两个重要的参数,一般地,辊缝要小于要求的极片最终厚度,或载荷作用能使涂层被压实。
另外,辊压速度的大小直接决定载荷作用在极片上的保持时间,也会影响极片的回弹,最终影响极片的涂层密度和孔隙率。
图1?极片辊压过程示意图?在轧制速度V cal下,极片通过辊缝时,线载荷可由式(1)计算:?q L?= F N?/ W C?其中,q L为作用在极片上的线载荷,F N为作用在极片上的轧制力,Wc为极片涂层的宽度。
??辊压过程极片微观结构的演变?变为ρc。
压实密度ρc可由通过辊缝,极片被压实,涂层密度由初始值ρc,0式(2)计算:其中,m E为单位面积内的电极片重量,m C为单位面积内的集流体重量,h E 为电极片厚度,h C为集流体厚度。
而压实密度与极片孔隙率相关,物理上的涂层孔隙率εc,ph可由式(3)计算,其含义为颗粒内部的孔隙和颗粒之间的孔隙在涂层的体积分数:其中,ρph为涂层各组成材料平均物理真密度。
?在实际的辊压工艺中,随着轧制压力变化,极片涂层压实密度具有一定规律,图2为极片涂层密度与轧制压力的关系。
锂离子电池正极辊压加热退火消褶技术
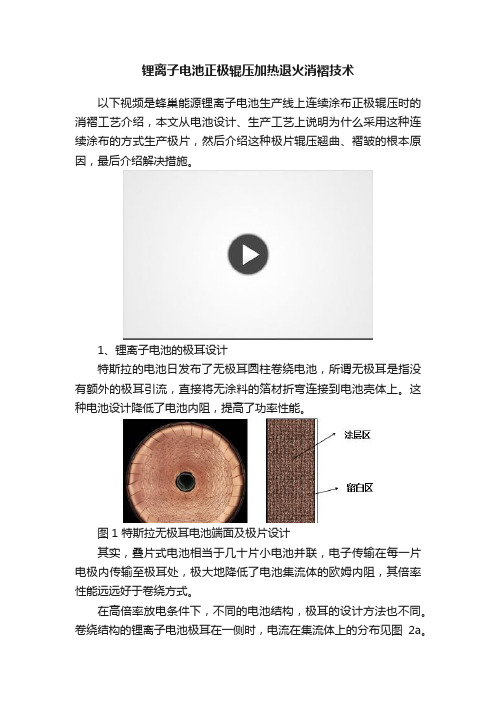
锂离子电池正极辊压加热退火消褶技术以下视频是蜂巢能源锂离子电池生产线上连续涂布正极辊压时的消褶工艺介绍,本文从电池设计、生产工艺上说明为什么采用这种连续涂布的方式生产极片,然后介绍这种极片辊压翘曲、褶皱的根本原因,最后介绍解决措施。
1、锂离子电池的极耳设计特斯拉的电池日发布了无极耳圆柱卷绕电池,所谓无极耳是指没有额外的极耳引流,直接将无涂料的箔材折弯连接到电池壳体上。
这种电池设计降低了电池内阻,提高了功率性能。
图1 特斯拉无极耳电池端面及极片设计其实,叠片式电池相当于几十片小电池并联,电子传输在每一片电极内传输至极耳处,极大地降低了电池集流体的欧姆内阻,其倍率性能远远好于卷绕方式。
在高倍率放电条件下,不同的电池结构,极耳的设计方法也不同。
卷绕结构的锂离子电池极耳在一侧时,电流在集流体上的分布见图2a。
离极耳最远端的xn处流出的电流,需要经过前面的x1 - xn段,x3段流出的电量需要经过x1 - x2 - x3段……,外部放电电流为I,每一段的反应电流为Ia,则流经x1段集流体的电流为n·Ia,流经x2段集流体的电流为( n - 1)·Ia,流经x3段集流体的电流为( n - 2)·Ia,流经xn段的集流体的电流为Ia。
图2 极耳位置对电流分布的影响对集流体的每一段,计算电流经过集流体的欧姆热量式中:ρ为集流体的电阻率,dx 为每一段的长度,A 为集流体的横截面积。
可由下式计算在集流体上的总热量Q,计算在集流体上的热等效内阻R极耳在极片中间时,电流在集流体上的分布见图2b。
同样,利用热量积分计算集流体等效热内阻。
对比极耳两种位置可知,极耳位于中间时,集流体的内阻仅为在一侧时的1 /4,在电极宽度一定时,集流体内阻与长度成正比。
卷绕结构的锂离子电池可在电极极片上多焊接几个极耳,这样在高倍率放电初期,电池内部就会有多个区域内阻较小,电流密度较大,反应速度较快,从而缓解单极耳情况下的剧烈反应。
- 1、下载文档前请自行甄别文档内容的完整性,平台不提供额外的编辑、内容补充、找答案等附加服务。
- 2、"仅部分预览"的文档,不可在线预览部分如存在完整性等问题,可反馈申请退款(可完整预览的文档不适用该条件!)。
- 3、如文档侵犯您的权益,请联系客服反馈,我们会尽快为您处理(人工客服工作时间:9:00-18:30)。
锂电池极片辊压工艺基础解析
————————————————————————————————作者:————————————————————————————————日期:
锂电池极片辊压工艺基础解析
锂离子电池极片制造一般工艺流程为:活性物质,粘结剂和导电剂等混合制备成浆料,然后涂敷在铜或铝集流体两面,经干燥后去除溶剂形成极片,极片颗粒涂层经过压实致密化,再裁切或分条。
辊压是锂电池极片最常用的压实工艺,相对于其他工艺过程,辊压对极片孔洞结构的改变巨大,而且也会影响导电剂的分布状态,从而影响电池的电化学性能。
为了获得最优化的孔洞结构,充分认识和理解辊压压实工艺过程是十分重要的。
辊压工艺基本过程
工业生产上,锂电池极片一般采用对辊机连续辊压压实,如图1所示,在此过程中,两面涂敷颗粒涂层的极片被送入两辊的间隙中,在轧辊线载荷作用下涂层被压实,从辊缝出来后,极片会发生弹性回弹导致厚度增加。
因此,辊缝大小和轧制载荷是两个重要的参数,一般地,辊缝要小于要求的极片最终厚度,或载荷作用能使涂层被压实。
另外,辊压速度的大小直接决定载荷作用在极片上的保持时间,也会影响极片的回弹,最终影响极片的涂层密度和孔隙率。
图1 极片辊压过程示意图
在轧制速度V cal下,极片通过辊缝时,线载荷可由式(1)计算:
q L = F N / W C
其中,q L为作用在极片上的线载荷,F N为作用在极片上的轧制力,Wc为极片涂层的宽度。
辊压过程极片微观结构的演变
通过辊缝,极片被压实,涂层密度由初始值ρc
变为ρc。
压实密度ρc可由
,0
式(2)计算:
其中,m E为单位面积内的电极片重量,m C为单位面积内的集流体重量,h E 为电极片厚度,h C为集流体厚度。
而压实密度与极片孔隙率相关,物理上的涂层孔隙率εc,ph可由式(3)计算,其含义为颗粒内部的孔隙和颗粒之间的孔隙在涂层的体积分数:
其中,ρph为涂层各组成材料平均物理真密度。
在实际的辊压工艺中,随着轧制压力变化,极片涂层压实密度具有一定规律,图2为极片涂层密度与轧制压力的关系。
图2 极片涂层密度与轧制压力的关系
曲线 I 区域,为第一阶段。
此阶段压力相对较小,涂层内颗粒产生位移,孔隙被填充,压力稍有增加时,极片的密度快速增加,极片的相对密度变化有规律。
曲线 II 区域,为第二阶段。
此阶段压力继续增加,极片经压缩后,密度已增高。
孔隙已被填充,浆料颗粒产生了更大的压实阻力。
压力再继续提高,但极片密度增加较少。
因此时浆料颗粒间的位移已经减少,颗粒大量的变形还没开始。
曲线 III 区域,为第三阶段。
当压力超过一定值后,压力增加极片密度也会继续增加,随后又逐渐平缓下来。
这是因为当压力超过浆料颗粒的临界压力时,颗粒开始变形、破碎,颗粒内部的孔隙也被填充,使极片密度继续增大。
但当压力继续增加,极片密度的变化逐渐平缓。
实际极片轧制过程的情况十分复杂。
在第一阶段,粉末体的致密化虽然以浆料颗粒的位移为主,但同时也有少量的变形。
在第三阶段,致密化以浆料颗粒的变形为主,同时也会存在少量位移。
另外,由于正负极材料本身性质差异,正负极极片辊压过程微观结构变化也不相同。
正极颗粒材料硬度大,不容易产生变形,而石墨负极硬度小,压实过程会发生塑性变形,如图3所示。
中等程度的压实会减轻石墨的塑性变形量,锂离子嵌入和脱出阻力更小,电池循环稳定性更好。
而载荷过大可能导致颗粒破碎。
正极极片中由于活性物质导电性很差,与负极相比,辊压过程引起导电剂分布变化对电子传导影响更明显。
图3 正负极极片辊压颗粒位移和变形示意图
压实密度对电化学性能的影响
在电池极片中,电子传导主要通过多孔结构中的活性物质和导电剂进行,而锂离子传导主要通过多孔结构中的电解液相进行,电解液填充在多孔电极的孔隙中,锂离子在孔隙内通过电解液传导,锂离子的传导特性与孔隙率密切相关。
孔隙率越大,相当于电解液相体积分数越高,锂离子有效电导率越大。
而电子通过活物质或碳胶相等固相传导,固相的体积分数,迂曲度又直接决定电子有效电导率。
孔隙率和固相的体积分数是相互矛盾的,孔隙率大必然导致固相体积分数降低,因此,锂离子和电子的有效传导特性也是相互矛盾的。
一方面,压实极片改善电极中颗粒在之间的接触,以及电极涂层和集流体之间的接触面积,降低不可逆容量损失接触内阻和交流阻抗。
另一方面,压实太高,孔隙率损失,孔隙的迂曲度增加,颗粒发生取向,或活物质颗粒表面粘合剂被挤压,限制锂盐的扩散和离嵌入/脱嵌,锂离子扩散阻力增加,电池倍率性能下降。
辊压工艺参数的影响规律
前面提到辊压工艺直接决定极片的多孔结构,而线载荷、速度等辊压工艺参数对极片微观结构到底有什么样的影响呢?德国布伦瑞克工业大学研究人员Chris Meyer等做了相关的研究。
他们研究发现,锂离子电池极片的压实过程也遵循粉末冶金领域的指数公式(4),这揭示了涂层密度或孔隙率与压实载荷之间的关系。
其中,
和
可以通过实验数据拟合得到,分别表示某工艺条件下涂层能够达到的最大压实密度以及涂层压实阻抗。
表1 实验用正负极极片参数
研究者对表1中所示NCM三元正极极片和石墨负极极片进行辊压实验,研究辊压工艺参数对极片涂层密度和孔隙率的影响规律。
根据材料物理真密度计算,当孔隙率为0%时,正极涂层密度应该为4.3 g/cc,负极涂层密度应该为2.2 g/cc。
而实际上根据实验数据拟合得到了参数(见表2)表明正极涂层达到的最大密度约3.2 g/cc,负极约为1.7 g/cc。
图4是辊压线载荷和正负极极片涂层密度的关系,不同的载荷和辊压线速度条件下采集实验数据点,然后采用指数方程(4)对数据进行拟合,得到相应的方程拟合参数,列入表2中。
表示为涂层的压实阻抗,较低值表明随着线载荷增加,涂层密度能够较快达到最大值,而较高的阻抗值表明涂层密度较慢达到最大值。
从图4和表2中可见,辊压速度对涂层密度影响较小,较小的速度导致涂层密度略微增加。
另外,正负极极片的压实过程差异大,正极极片压实阻抗大约为负极的一倍多,这是由于正负极材料特性差异引起的,正极颗粒硬度大,压实阻抗大,而负极颗粒硬度小,压实阻抗小,更容易辊压压实。
图4 线载荷与正负极极片涂层压实密度的关系
表2 不同辊压工艺条件下拟合得到的参数值
此外,从孔隙结构角度分析辊压工艺的影响。
电池极片涂层的孔隙主要包含两类:颗粒材料内部的孔隙,尺寸为纳米-亚微米级;颗粒之间的孔隙,尺寸为微米级。
图5是不同辊压条件下正负极极片中孔径分布情况,首先很明显可以看到极片压实可以减小孔径尺寸并降低孔隙含量。
随着压实密度增加,与正极相比,负极孔径尺寸更明显降低,这是由于负极涂层压实阻抗低更容易被辊压压实。
同时数据表明辊压速度对孔隙结构的较小。
图5 不同辊压条件下孔径分布
从涂层的孔隙率角度考虑,辊压线载荷与涂层孔隙率之间也可以通过指数方
程拟合得到规律,图
6是线载荷与正负极极片涂层孔隙率的关系,不同的线载荷
作用下对正负极极片进行辊压,通过物理真密度计算孔隙率、同时也通过实验测量涂层的孔隙率,得到的数据点作图并进行线性拟合,结果如图6所示。
图6 线载荷与正负极极片涂层孔隙率的关系
辊压工艺对锂电池极片微观结构影响巨大,特别是对多孔结构,因此,辊压工艺强烈影响电池性能。
总之,在锂电池技术研究与开发中,我们同样需要特别关注制造工艺。
11。