φ12mm带肋钢筋四切分轧制技术的开发与实践
四切分轧制Ф12mm螺纹钢筋的线差分析及改进措施
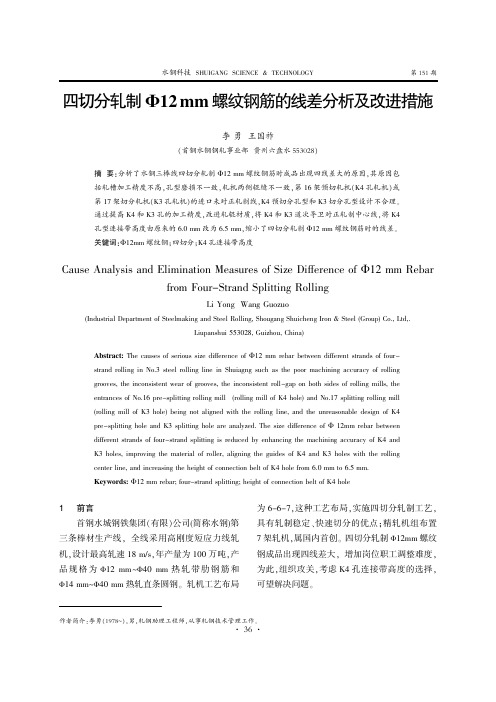
水钢科技SHUIGANG SCIENCE &TECHNOLOGY第151期1前言首钢水城钢铁集团(有限)公司(简称水钢)第三条棒材生产线,全线采用高刚度短应力线轧机,设计最高轧速18m/s,年产量为100万吨,产品规格为Φ12mm ~Φ40mm 热轧带肋钢筋和Φ14mm~Φ40mm 热轧直条圆钢。
轧机工艺布局为6-6-7,这种工艺布局,实施四切分轧制工艺,具有轧制稳定、快速切分的优点;精轧机组布置7架轧机,属国内首创。
四切分轧制Φ12mm 螺纹钢成品出现四线差大,增加岗位职工调整难度,为此,组织攻关,考虑K4孔连接带高度的选择,可望解决问题。
Abstract:The causes of serious size difference of Φ12mm rebar between different strands of four-strand rolling in No.3steel rolling line in Shuiagng such as the poor machining accuracy of rolling grooves,the inconsistent wear of grooves,the inconsistent roll-gap on both sides of rolling mills,the entrances of No.16pre-splitting rolling mill (rolling mill of K4hole)and No.17splitting rolling mill (rolling mill of K3hole)being not aligned with the rolling line,and the unreasonable design of K4pre-splitting hole and K3splitting hole are analyzed.The size difference of Φ12mm rebar between different strands of four-strand splitting is reduced by enhancing the machining accuracy of K4and K3holes,improving the material of roller,aligning the guides of K4and K3holes with the rolling center line,and increasing the height of connection belt of K4hole from 6.0mm to 6.5mm.Keywords:Φ12mm rebar;four-strand splitting;height of connection belt of K4hole作者简介:李勇(1978~),男,轧钢助理工程师,从事轧钢技术管理工作。
Φ12 mm螺纹钢精轧机组工艺优化
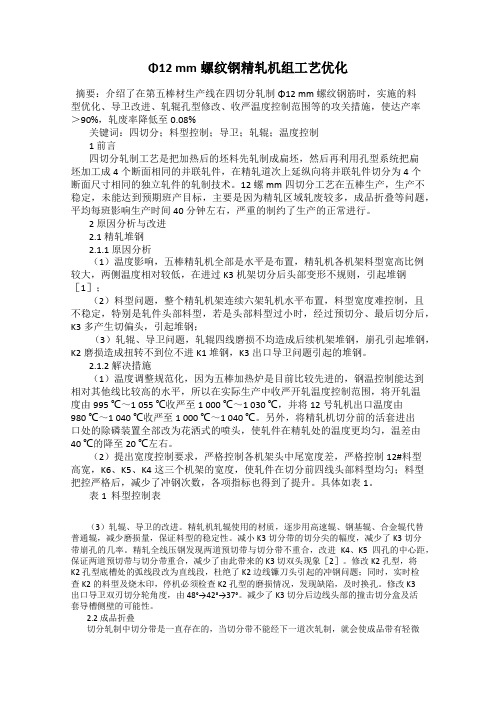
Φ12 mm螺纹钢精轧机组工艺优化摘要:介绍了在第五棒材生产线在四切分轧制Φ12 mm螺纹钢筋时,实施的料型优化、导卫改进、轧辊孔型修改、收严温度控制范围等的攻关措施,使达产率>90%,轧废率降低至0.08%关键词:四切分;料型控制;导卫;轧辊;温度控制1 前言四切分轧制工艺是把加热后的坯料先轧制成扁坯,然后再利用孔型系统把扁坯加工成4个断面相同的并联轧件,在精轧道次上延纵向将并联轧件切分为4个断面尺寸相同的独立轧件的轧制技术。
12螺mm四切分工艺在五棒生产,生产不稳定,未能达到预期班产目标,主要是因为精轧区域轧废较多,成品折叠等问题,平均每班影响生产时间40分钟左右,严重的制约了生产的正常进行。
2 原因分析与改进2.1 精轧堆钢2.1.1 原因分析(1)温度影响,五棒精轧机全部是水平是布置,精轧机各机架料型宽高比例较大,两侧温度相对较低,在进过K3机架切分后头部变形不规则,引起堆钢[1];(2)料型问题,整个精轧机架连续六架轧机水平布置,料型宽度难控制,且不稳定,特别是轧件头部料型,若是头部料型过小时,经过预切分、最后切分后,K3多产生切偏头,引起堆钢;(3)轧辊、导卫问题,轧辊四线磨损不均造成后续机架堆钢,崩孔引起堆钢,K2磨损造成扭转不到位不进K1堆钢,K3出口导卫问题引起的堆钢。
2.1.2 解决措施(1)温度调整规范化,因为五棒加热炉是目前比较先进的,钢温控制能达到相对其他线比较高的水平,所以在实际生产中收严开轧温度控制范围,将开轧温度由995 ℃~1 055 ℃收严至1 000 ℃~1 030 ℃,并将12号轧机出口温度由980 ℃~1 040 ℃收严至1 000 ℃~1 040 ℃。
另外,将精轧机切分前的活套进出口处的除磷装置全部改为花洒式的喷头,使轧件在精轧处的温度更均匀,温差由40 ℃的降至20 ℃左右。
(2)提出宽度控制要求,严格控制各机架头中尾宽度差,严格控制12#料型高宽,K6、K5、K4这三个机架的宽度,使轧件在切分前四线头部料型均匀;料型把控严格后,减少了冲钢次数,各项指标也得到了提升。
Ф12mm热轧带肋钢筋四切分轧制开发实践
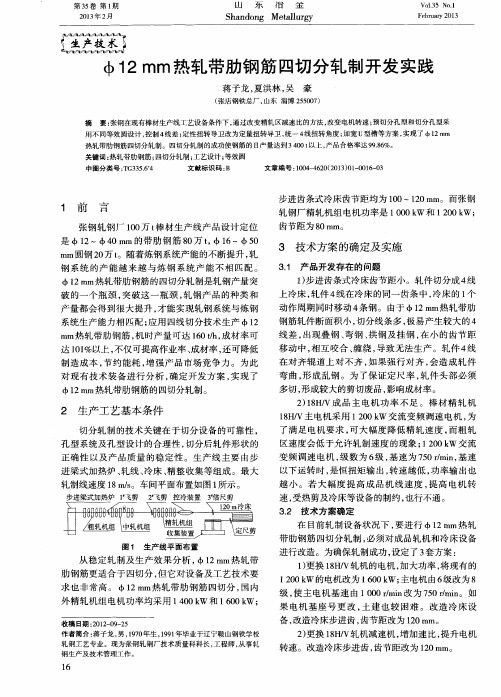
2 生产 工艺基本 条件
切 分 轧制 的技 术关 键在 于切 分设 备 的可 靠性 ,
孔 型系 统及 孔型 设计 的合 理性 , 切 分后 轧件形 状 的 正 确性 以及 产 品质 量 的稳 定性 。生 产线 主要 由步 进 梁式 加热 炉 、 轧线 、 冷床 、 精 整收 集等 组成 。最 大
肋 钢筋 更适 合 于 四切 分 , 但 它对设 备及 工艺 技 术要 求 也非 常 高 。 1 2 m m热 轧带 肋 钢筋 四切 分 , 国 内 外 精轧 机组 电机 功率 均采 用 1 4 0 0 k W和1 6 0 0 k W;
制造 成 本 , 节约能耗 , 增 强 产 品市 场 竞争 力 。为此
钢 筋轧件 断 面积小 , 切分 线条 多 , 极 易产 生较 大 的 4
线差 , 出现 叠钢 、 弯钢 、 拱钢及挂钢 , 在 小 的齿 节距
移动中, 相 互 咬合 、 缠绕 , 导 致无 法 生产 。轧 件 4 线
在 对 齐辊 道 上 对不 齐 , 如 果 强 行对 齐 , 会 造 成 轧件
了满 足 电机 要 求 , 可 大 幅度 降低精 轧 速 度 , 而 粗 轧 区速度 会低 于允 许 轧制 速度 的现 象 ; 1 2 0 0 k W交 流
变 频 调速 电机 , 级数为6 级, 基速为 7 5 0 r / mi n , 基 速
以下运 转 时 , 是 恒扭 矩输 出 , 转 速 越低 , 功 率输 出也 越 小 。若 大 幅度 提 高 成 品 机 线 速 度 , 提 高 电机 转 速, 受热剪 及冷床 等设备 的制约 , 也 行不通 。
φ12四切分轧制汇总
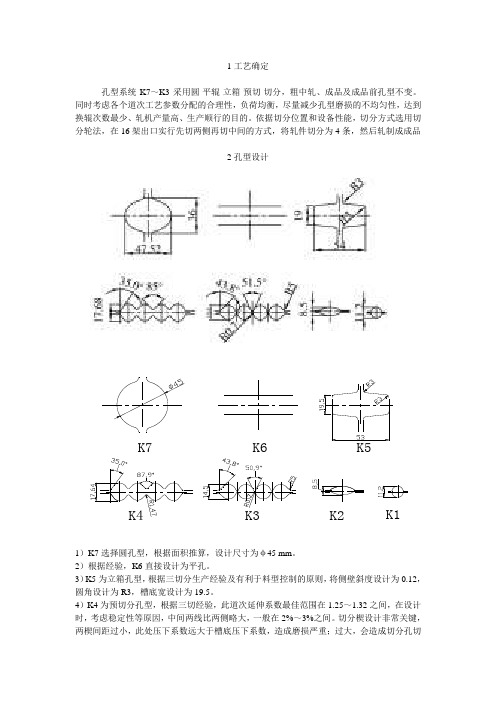
1工艺确定孔型系统K7~K3采用圆-平辊-立箱-预切-切分,粗中轧、成品及成品前孔型不变。
同时考虑各个道次工艺参数分配的合理性,负荷均衡,尽量减少孔型磨损的不均匀性,达到换辊次数最少、轧机产量高、生产顺行的目的。
依据切分位置和设备性能,切分方式选用切分轮法,在16架出口实行先切两侧再切中间的方式,将轧件切分为4条,然后轧制成成品2孔型设计K6K7K3K2K1K5K41)K7选择圆孔型,根据面积推算,设计尺寸为φ45 mm 。
2)根据经验,K6直接设计为平孔。
3)K5为立箱孔型,根据三切分生产经验及有利于料型控制的原则,将侧壁斜度设计为0.12,圆角设计为R3,槽底宽设计为19.5。
4)K4为预切分孔型,根据三切经验,此道次延伸系数最佳范围在1.25~1.32之间,在设计时,考虑稳定性等原因,中间两线比两侧略大,一般在2%~3%之间。
切分楔设计非常关键,两楔间距过小,此处压下系数远大于槽底压下系数,造成磨损严重;过大,会造成切分孔切分楔磨损过快,甚至崩槽,在成品表面形成折叠,根据经验,一般设计为6~8mm。
预切分楔角度设计时应考虑与K3孔切分楔角度的配合及耐磨性,一般设计为78°~88°,切分楔圆角半径一般选为1.4~1.8,过小不耐磨。
5)K3为切分孔型,其作用是对轧件4线料型进行规整、加工切分带,为切分做好料型准备。
根据三切经验,此道次延伸系数最佳范围为1.10~1.25,设计要点是切分楔角度、切分带厚度、基圆尺寸。
切分带厚度必须控制在0.8~1.0 mm之间,过厚过宽,在K2道次压不合,造成成品孔型较早出现轧痕,同时切分轮受力过大,出现导卫烧轴承事故;过薄,切分带直接被碾到K2料表面,在成品道次出现折叠现象。
切分楔角度一般选为45°~55°,切分楔圆角半径设计为r0.7~r1.0,过小强度不够。
3关键道次导卫设计1)K4道次:进口设计为双排4轮滚动导卫,同时导轮设计为“V”形,这样有利于夹持轧件,确保轧件运行中的稳定性、对中性。
四切分轧制Ф12mm螺成品勾头冲出口故障的处理
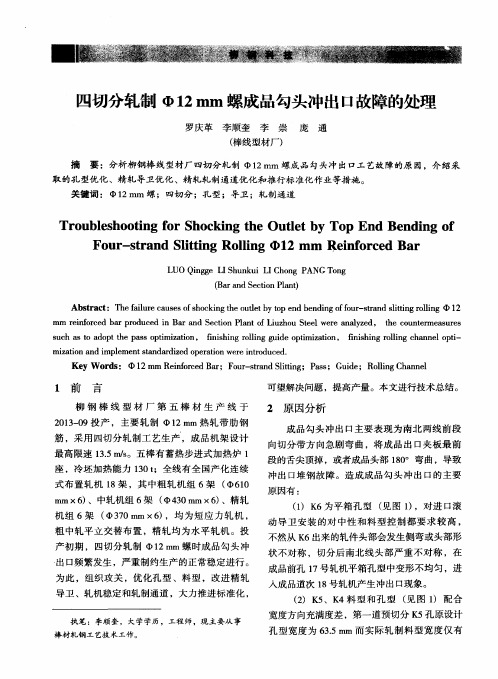
2 原 因分析
成 品勾头冲 出口主要表现为南北两线前段
向切 分 带 方 向急 剧 弯 曲 ,将 成 品 出 口夹 板 最 前
段 的舌 尖顶 掉 ,或者 成 品头部 1 8 0 。 弯 曲 ,导致
座 ,冷 坯 加 热 能 力 1 3 0 t ;全 线 有 全 国产 化 连 续 式布置轧机 1 8架 ,其 性 和 料 型 控 制 都 要 求 较 高 , 不然 从 K 6出来 的轧 件 头部 会发 生侧 弯 或 头部 形 状 不 对 称 ,切 分 后 南 北 线 头 部 严 重 不 对 称 ,在
出 口频繁发生 ,严重制约生产的正常稳定进行。
为 此 ,组织 攻 关 ,优 化 孔 型 、料 型 ,改 进 精 轧 导卫 、轧机 稳定 和轧制 通 道 ,大 力推 进 标 准化 ,
Fo u r - s t r a n d S l i t t i n g Ro l l i n g 01 2 m m Re i n f o r c e d Ba r
L U O Q i n g g e L I S h u n k u i L I C h o n g P A NG T o n g ( B a r a n d S e c t i o n P l nt a )
1 前
言
可 望解决 问题 ,提 高产 量 。本 文进行 技 术总 结 。
柳 钢 棒 线 型 材 厂 第 五 棒 材 生 产 线 于 2 0 1 3 — 0 9投 产 ,主要 轧 制 ①1 2 m m 热 轧 带 肋 钢 筋 ,采 用 四切 分 轧 制 工 艺 生产 ,成 品 机架 设 计
Ke y W o r d s :
带肋钢筋四切分轧制常见故障及处理措施(酒钢科技)
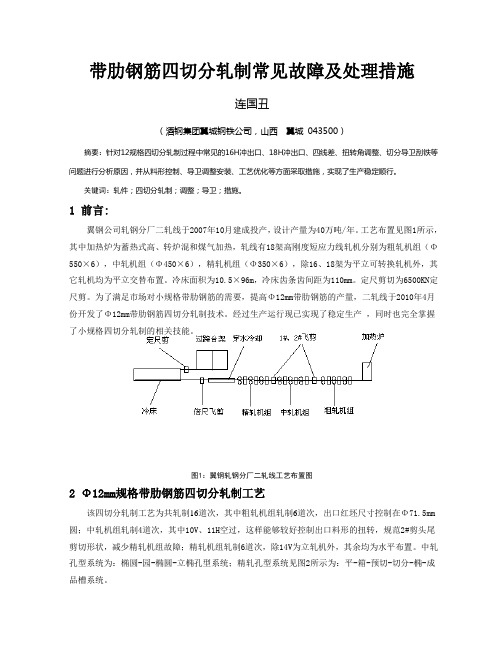
带肋钢筋四切分轧制常见故障及处理措施连国丑(酒钢集团翼城钢铁公司,山西翼城043500)摘要:针对12规格四切分轧制过程中常见的16H冲出口、18H冲出口、四线差、扭转角调整、切分导卫刮铁等问题进行分析原因,并从料形控制、导卫调整安装、工艺优化等方面采取措施,实现了生产稳定顺行。
关键词:轧件;四切分轧制;调整;导卫;措施。
1 前言:翼钢公司轧钢分厂二轧线于2007年10月建成投产,设计产量为40万吨/年。
工艺布置见图1所示,其中加热炉为蓄热式高、转炉混和煤气加热,轧线有18架高刚度短应力线轧机分别为粗轧机组(Φ550×6),中轧机组(Φ450×6),精轧机组(Φ350×6),除16、18架为平立可转换轧机外,其它轧机均为平立交替布置。
冷床面积为10.5×96m,冷床齿条齿间距为110mm。
定尺剪切为6500KN定尺剪。
为了满足市场对小规格带肋钢筋的需要,提高Φ12mm带肋钢筋的产量,二轧线于2010年4月份开发了Φ12mm带肋钢筋四切分轧制技术。
经过生产运行现已实现了稳定生产,同时也完全掌握了小规格四切分轧制的相关技能。
图1:翼钢轧钢分厂二轧线工艺布置图2 Φ12mm规格带肋钢筋四切分轧制工艺该四切分轧制工艺为共轧制16道次,其中粗轧机组轧制6道次,出口红坯尺寸控制在Φ71.5mm 圆;中轧机组轧制4道次,其中10V、11H空过,这样能够较好控制出口料形的扭转,规范2#剪头尾剪切形状,减少精轧机组故障;精轧机组轧制6道次,除14V为立轧机外,其余均为水平布置。
中轧孔型系统为:椭圆-园-椭圆-立椭孔型系统;精轧孔型系统见图2所示为:平-箱-预切-切分-椭-成品槽系统。
图2:精轧机组孔型系统3 常见故障分析:四切分轧制固然能大幅度提升小规格带肋钢筋的产量,但因其工艺的复杂对设备性能,生产准备,导卫安装调整,料形的精准控制,张力调整和钢温等过程控制的要求非常高。
φ12 mm带肋钢筋四线切分轧制生产工艺开发
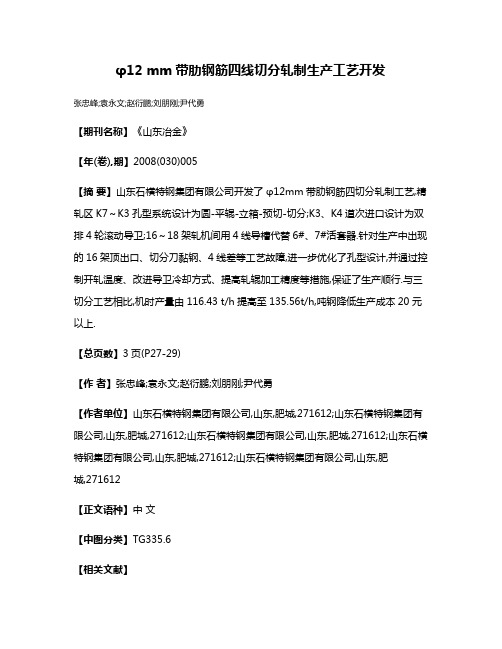
φ12 mm带肋钢筋四线切分轧制生产工艺开发
张忠峰;袁永文;赵衍鹏;刘朋刚;尹代勇
【期刊名称】《山东冶金》
【年(卷),期】2008(030)005
【摘要】山东石横特钢集团有限公司开发了φ12mm带肋钢筋四切分轧制工艺,精轧区K7~K3孔型系统设计为圆-平辊-立箱-预切-切分;K3、K4道次进口设计为双排4轮滚动导卫;16~18架轧机间用4线导槽代替6#、7#活套器.针对生产中出现的16架顶出口、切分刀黏钢、4线差等工艺故障,进一步优化了孔型设计,并通过控制开轧温度、改进导卫冷却方式、提高轧辊加工精度等措施,保证了生产顺行.与三切分工艺相比,机时产量由116.43 t/h提高至135.56t/h,吨钢降低生产成本20元以上.
【总页数】3页(P27-29)
【作者】张忠峰;袁永文;赵衍鹏;刘朋刚;尹代勇
【作者单位】山东石横特钢集团有限公司,山东,肥城,271612;山东石横特钢集团有限公司,山东,肥城,271612;山东石横特钢集团有限公司,山东,肥城,271612;山东石横特钢集团有限公司,山东,肥城,271612;山东石横特钢集团有限公司,山东,肥
城,271612
【正文语种】中文
【中图分类】TG335.6
【相关文献】
1.Φ12mm热轧带肋钢筋四线切分轧制工艺存在问题及解决措施 [J], 祖超;史盼盼
2.φ12 mm热轧带肋钢筋四切分轧制开发实践 [J], 蒋子龙;夏洪林;吴豪
3.φ12mm热轧带肋钢筋五线切分轧制技术开发 [J], 吴经理
4.莱钢12mm热轧带肋钢筋四切分轧制技术的开发 [J], 黄海玉;刘艳林;孙道清;李健
5.Φ12mm热轧带肋钢筋五切分轧制工艺开发 [J], 宋将
因版权原因,仅展示原文概要,查看原文内容请购买。
Φ12mm螺纹钢四切分轧制工艺优化

钢等 ,平均每班故 障时间 4 0 m i n 左右 ,严重地
制 约 了生产 的正 常进行 。为此 ,展开 攻关 ,实 施
Te mp e r a t u r e
1 2 mm Re i n f o r c e d B a r ; Ro l l i n g ; F o u r - s t r a n d S p l i t t i n g ; P r o i f l e ; P a s s ; G u i d e ;
陆文韬等 : l 2 m I I l 螺纹钢 四切分轧制工艺优化
停 机 必 须 检查 K 2孔 型 的磨 损 情 况 ,发 现 缺 陷 , 及 时 换 孔 ;修 改 K 3出 口导 卫 双 刃 切 分 轮 角度 ,
( 3 )轧辊 、导卫方面。轧辊 4线磨损不均 造成后续机架堆钢 ,崩孔引起堆钢 ,K 2 磨损造
LU we n t a o ZHANG Bi n b i n
( B a r a n d S e c t i o n P l a n t )
Ab s t r ac t : The b r a i n s t o r m c o u n t e r me a s u r e s i mpl e me n t e d f o r t he f o u r - s t r a n d s pl i t t i n g r o l l i ng p r o c e s s f o r
中1 2 mm r e i n f o r c e d b a r p r o d u c t i o n w e r e i n t r o d u c e d i n r e s p e c t s o f p r o i f l e o p t i mi z a t i o n , g u i d e i mp r o v e me n t , r o l l e r p a s s r e f o r ma t i o n a n d t e mp e r a t u r e c e n c e t h e r e a c h a b i l i t y o f d e s i g n c a p a c i t y w a s >9 0 %, t h e r o l l i n g s c r a p r a t e w a s r e d u c e d t o 0 . 0 8 % a n d t h e r o l l i n g y i e l d wa s 1 0 3 . 1 %. Ke y W o r d s :
小型棒材切分轧制生产实践
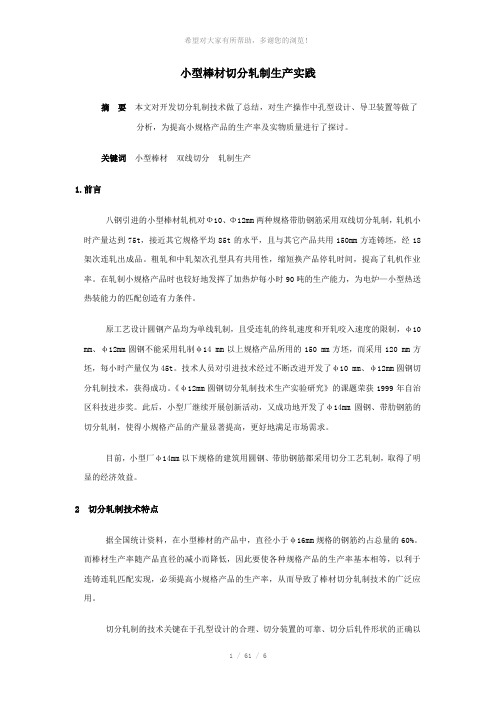
小型棒材切分轧制生产实践摘要本文对开发切分轧制技术做了总结,对生产操作中孔型设计、导卫装置等做了分析,为提高小规格产品的生产率及实物质量进行了探讨。
关键词小型棒材双线切分轧制生产1.前言八钢引进的小型棒材轧机对Ф10、Φ12mm两种规格带肋钢筋采用双线切分轧制,轧机小时产量达到75t,接近其它规格平均85t的水平,且与其它产品共用150mm方连铸坯,经18架次连轧出成品。
粗轧和中轧架次孔型具有共用性,缩短换产品停轧时间,提高了轧机作业率。
在轧制小规格产品时也较好地发挥了加热炉每小时90吨的生产能力,为电炉—小型热送热装能力的匹配创造有力条件。
原工艺设计圆钢产品均为单线轧制,且受连轧的终轧速度和开轧咬入速度的限制,φ10 mm、φ12mm圆钢不能采用轧制φ14 mm以上规格产品所用的150 mm方坯,而采用120 mm方坯,每小时产量仅为45t。
技术人员对引进技术经过不断改进开发了φ10 mm、φ12mm圆钢切分轧制技术,获得成功。
《φ12mm圆钢切分轧制技术生产实验研究》的课题荣获1999年自治区科技进步奖。
此后,小型厂继续开展创新活动,又成功地开发了φ14mm圆钢、带肋钢筋的切分轧制,使得小规格产品的产量显著提高,更好地满足市场需求。
目前,小型厂φ14mm以下规格的建筑用圆钢、带肋钢筋都采用切分工艺轧制,取得了明显的经济效益。
2 切分轧制技术特点据全国统计资料,在小型棒材的产品中,直径小于φ16mm规格的钢筋约占总量的60%。
而棒材生产率随产品直径的减小而降低,因此要使各种规格产品的生产率基本相等,以利于连铸连轧匹配实现,必须提高小规格产品的生产率,从而导致了棒材切分轧制技术的广泛应用。
切分轧制的技术关键在于孔型设计的合理、切分装置的可靠、切分后轧件形状的正确以及产品实物质量的稳定性。
切分轧制具有以下明显的技术特点:2.1 不同规格产品的生产能力基本均衡。
因为炼钢连铸能力相对稳定,而轧钢能力波动大,采用切分工艺可以使多种规格棒材的轧制能力基本相等,同时,对于轧钢工序来说,可使加热炉、轧机、冷床及其它辅助设备的生产能力充分发挥。
Φ12mm热轧带肋钢筋四线切分轧制工艺存在问题及解决措施

度 是 固定 的 , 而起 套辊起 套后 轧件 高度是 变 化 的 , 导
致 活套起 套后 轧件 经压 辊导 向与 下一架次 进 口导 板 发 生摩 擦 。 () 2 导板 无 冷 却水 , 件 与 导 板 摩 擦 后 导 板 温 轧
度过高 。
( ) D E双 排 导 卫 导 板 上 下 配 合 后 插 入 导 34 4
s i us w o e i r v s ero r n g oo e .
Ke o ds: ot—r ln yW r h olig;fn s i g r li i ih n olng; p o e sp o lm ;m e s r s r c s r b e aue
1
前 言
总第 11 9 期 21 0 1年 第 1 1期
河 北冶金
H EBE M E AL U R GY I T L
Toa l l tl 9
2 01 , u b r 1 1 N m e 1
1 mm 热 轧 带肋 钢 筋 2 四线切 分 轧 制 工 艺存 在 问题 及 解 决 措 施
轴窜 。
造成 切分架 次 出 口堆钢 的 主要 原 因有 切偏 头 、 切分 刀粘 钢等 。
9 . % 。针对 生产 初 期存 在 的粘 钢 、 钢等 问题 进 71 堆 行 了改 进 , 得 了 比较好 的效 果 。 取
2 四 线 切 分 轧 制 原 理
架 , 中 1 、8 2 其 6 1 、0架 为平 立 可转换 轧 机 , 、 粗 中轧 机
组 出 口设 有 1 、 # # 2 飞剪 , 于 轧制 过 程 中切 头 尾 和 用
收 稿 E 期 :0 1 7— O t 2 1 —0 2
的两切 分 , 过 这 两 个 步骤 实 现 四线 切 分 。与 传 统 通 的单 线 轧制工 艺 和二 、 线切 分轧 制工艺 相 比较 , 三 四
Ф12mm螺四切分轧制成品勾头冲出口故障处理分析
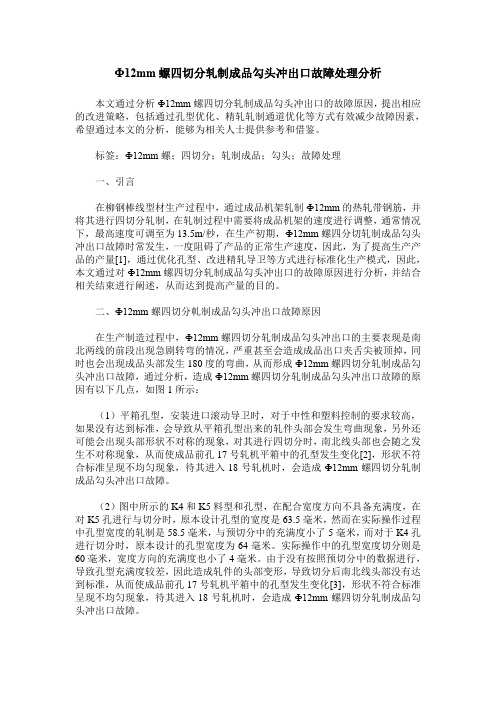
Ф12mm螺四切分轧制成品勾头冲出口故障处理分析本文通过分析Ф12mm螺四切分轧制成品勾头冲出口的故障原因,提出相应的改进策略,包括通过孔型优化、精轧轧制通道优化等方式有效减少故障因素,希望通过本文的分析,能够为相关人士提供参考和借鉴。
标签:Ф12mm螺;四切分;轧制成品;勾头;故障处理一、引言在柳钢棒线型材生产过程中,通过成品机架轧制Ф12mm的热轧带钢筋,并将其进行四切分轧制,在轧制过程中需要将成品机架的速度进行调整,通常情况下,最高速度可调至为13.5m/秒,在生产初期,Ф12mm螺四分切轧制成品勾头冲出口故障时常发生,一度阻碍了产品的正常生产速度,因此,为了提高生产产品的产量[1],通过优化孔型、改进精轧导卫等方式进行标准化生产模式,因此,本文通过对Ф12mm螺四切分轧制成品勾头冲出口的故障原因进行分析,并结合相关结束进行阐述,从而达到提高产量的目的。
二、Ф12mm螺四切分軋制成品勾头冲出口故障原因在生产制造过程中,Ф12mm螺四切分轧制成品勾头冲出口的主要表现是南北两线的前段出现急剧转弯的情况,严重甚至会造成成品出口夹舌尖被顶掉,同时也会出现成品头部发生180度的弯曲,从而形成Ф12mm螺四切分轧制成品勾头冲出口故障,通过分析,造成Ф12mm螺四切分轧制成品勾头冲出口故障的原因有以下几点,如图1所示:(1)平箱孔型,安装进口滚动导卫时,对于中性和塑料控制的要求较高,如果没有达到标准,会导致从平箱孔型出来的轧件头部会发生弯曲现象,另外还可能会出现头部形状不对称的现象,对其进行四切分时,南北线头部也会随之发生不对称现象,从而使成品前孔17号轧机平箱中的孔型发生变化[2],形状不符合标准呈现不均匀现象,待其进入18号轧机时,会造成Ф12mm螺四切分轧制成品勾头冲出口故障。
(2)图中所示的K4和K5料型和孔型,在配合宽度方向不具备充满度,在对K5孔进行与切分时,原本设计孔型的宽度是63.5毫米,然而在实际操作过程中孔型宽度的轧制是58.5毫米,与预切分中的充满度小了5毫米,而对于K4孔进行切分时,原本设计的孔型宽度为64毫米。
提高四切分轧制负公差Ф12mm螺纹钢合格率的生产实践
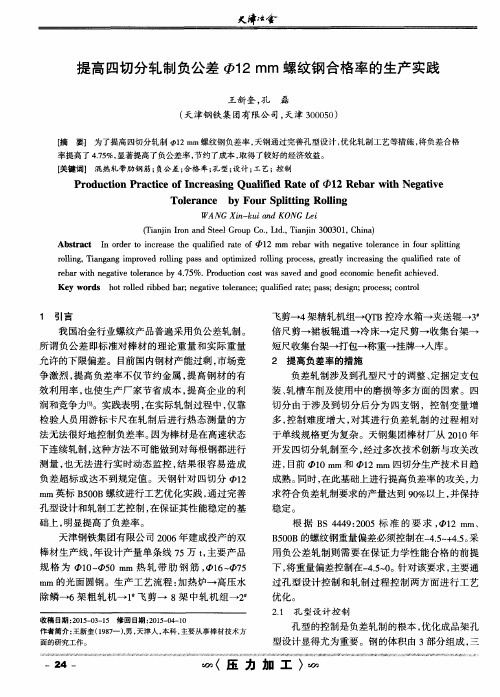
提高四切分轧制负公差 1 2 mm 螺纹钢合格率的生产 实践
王新奎 , 孔 磊
( 天 津钢铁 集 团有限公 司, 天津 3 0 0 0 5 0 )
【 摘 要】 为了提 高四切分轧制 1 2 m m螺纹钢负差率 , 天钢通过完善孔型设计 , 优化轧制工艺 等措施 , 将负差合格
Ke y wo r d s h o t r o l l e d ib f b e d b a r ;n e g a t i v e t o l e r a n c e ; q u a l i i f e d r a t e ; p a s s ; d e s i g n ;p r o c e s s ;c o n t r o l
棒材生产线 , 年设计产量单条线 7 5 万t , 主要产 品
To l e r a n c e b y Fo ur Sp l i t t i ng Ro l l i ng
WANG Xi n - k u i a n d K ONG L e i
( T i a n j i n I r o n a n d S t e e l G r o u p C o . , L t d . , T i a n j i n 3 0 0 3 0 1 , C h i n a )
础上 , 明显提高了负差率。
天津 钢铁 集 团有 限公 司 2 B S 4 4 4 9 : 2 0 0 5标 准 的 要 求 , 1 2 mm、 B 5 O O B的螺纹 钢重 量偏差 必须 控制 在一 4 . 5 ~ + 4 . 5 。 采
率提高了 4 . 7 5 %, 显著提高了负公差率 , 节约了成本 , 取得了较好 的经济效益。 【 关键词】 混热轧带肋钢 筋; 负公 差; 合格 率; 孔型 ; 设计 ; 工 艺; 控制
带肋钢筋切分轧制技术的开发与应用
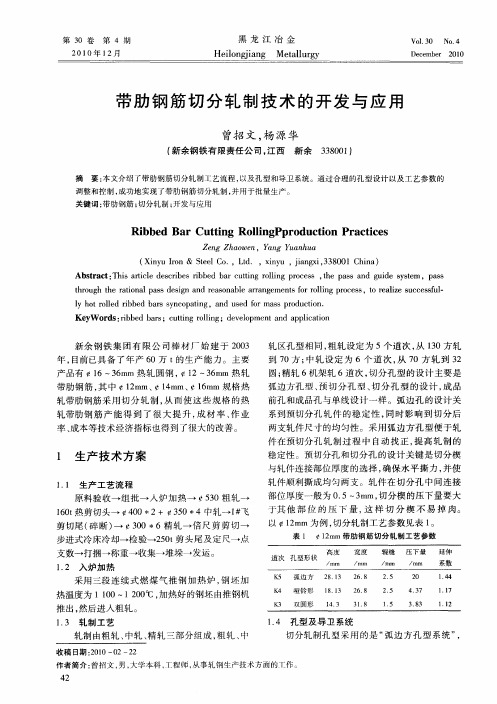
轧制 由粗 轧 、 中轧 、 轧 三部分 组成 , 轧 、 精 粗 中
收 稿 日期 :00— 2—2 21 0 2
作者简介 : 曾招文 , , 男 大学本科 , 丁程师 , 从事轧钢生产技术方 面的T作 。
曾招 文 , 源华 杨
( 新余钢 铁有 限责任公 司 , 江西 新余 3 80 ) 3 0 1
摘
要 : 文介 绍 了带 肋 钢 筋 切 分 轧 制 工 艺 流 程 , 本 以及 孔 型 和 导卫 系统 。通 过 合 理 的孔 型 设 计 以 及 工 艺 参 数 的
调 整和 控 制 , 成功 地 实 现 了带 肋 钢 筋 切 分 轧 制 , 用 于 批 量 生产 。 并 关键 词 : 带肋 钢筋 ; 分 轧 制 ; 发 与 应 用 切 开
Ri e r Cu tng R0 l g bb d Ba ti l n Ppr du t0 a tc s i 0 c i n Pr c ie
ze g Zh o n.Ynn u n a n a we g Y a hu
( iy o X nuI n& Sel o ,Ld xnu , i gi3 8 0 hn ) r te C . t., iy j nx ,3 0 1C ia a
轧 件顺 利撕成 均匀 两 支 。轧 件 在切 分 孔 中 间连接 部 位厚 度一般 为 0 5~ m 切 分楔 的压 下量 要大 . 3 m, 于其 他 部 位 的 压 下 量 , 样 切 分 楔 不 易 掉 肉。 这
以 1 mm为例 , 2 切分 轧制工 艺参数 见表 1 。
表l 1 m 带 肋 钢 筋切 分 轧 制 工 艺参 数 2m
到7 0方 ; 轧设 定 为 6个 道 次 , 7 中 从 0方 轧 到 3 2
Ф12mm螺纹钢四切分轧制技术的开发实践
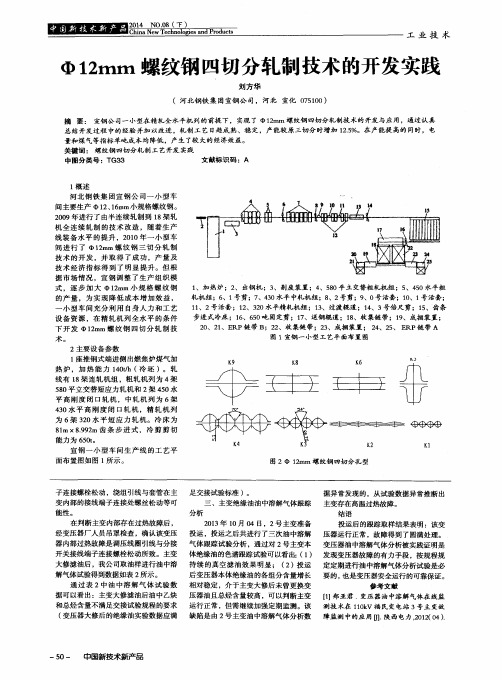
小型车 间充 分利用 自身人力和 工艺 设 备资源 ,在精 轧机列全 水平 的条 件 下 开发 中1 2 m m 螺 纹 钢 四 切 分 轧 制 技
一
1 、加 热 炉 ;2 、 出钢机 ;3 、剔废 装置 ;4 、5 8 0 平 立 交替粗 轧机 组 ;5 、4 5 0水平 粗 轧机 组 ;6 、1 号剪 ;7 、4 3 0水平 中轧机 组 ;8 、2 号剪; 9 、0 号 活套 ;1 0 、1 号 活套 ; 1 1 、2 号 活套 ;1 2 、3 2 0水平精 轧机 组 ;1 3 、过渡 辊道 ;1 4 、3 号倍 尺 剪 ;1 5 、齿 条 步进式冷床 ;1 6 、6 5 0 吨 固定剪;1 7 、送钢辊道;1 8 、收集链带 ;1 9 、成捆装置 ; 2 o 、2 1 、E R . P链带 B ;2 2 、收集链带 ;2 3 、成捆装置 ;2 4 、2 5 、E KP链带 A
目匪盈圈圆
工业技术
1 2 mm 螺 纹钢 四切 分轧制 技术 的开发实践
刘 方 华
(河北钢铁 集 团宣钢公 司,河北 宣化 0 7 5 1 0 0 )
摘 要 : 宣钢公 司一 小型在 精 轧全 水平机 列的前 提 下 ,实现 了 中1 2 m m 螺 纹钢 四切 分轧制 技 术的 开发 与应 用 ,通过 认 真
一
5 0一 中国新技术新产品
K 9
K8
K 6
宣
串
图2 1 2 mm 螺 纹钢 四切 分孔 型
书 1 2 一 n
子 连接 螺栓 松 动 ,绕组 引 线与 套管 在 主 足交接 试验 标 准 )。 据 异 常发 现 的 ,从 试验 数 据 异常 推断 出 变 内部 的接 线端 子 连接 处 螺丝 松动 等 可 三 、主变绝 缘 油油 中溶解 气体 跟踪 主变 存 在高 温过热 故 障 。 能性 。 分析 结语 在判断主变内部存在过热故障后 , 2 0 1 3 年 l 0月 0 4 日,2 号 主 变 准备 投运 后 的跟 踪取 样结 果 表 明 :该 变 经变压器厂人员 吊罩检查,确认该变压 投 运 ,投 运之 后 共进 行 了三 次 油 中溶解 压器 运 行正 常 ,故 障得 到 了 圆满 处理 。 器 内部过热故障是调压线圈引线与分接 气体跟踪试验分析,通过对 2 号主变本 变压器油中溶解气体分析被实践证 明是 开关 接线 端 子连 接 螺栓 松 动所 致 。主变 体 绝缘 油 的色谱 跟踪 试验 可 以看 出: ( 1 ) 发现 变 压器 故 障 的有力 手段 ,按规 程 规 大修 滤 油后 ,我 公 司取 油样 进 行油 中溶 持 续 的真 空滤 油效 果 明 显 ; ( 2 )投 运 定定期进行油中溶解气体分析试验是必 解气体试验得到数据如表 2 所示。 后变压器本体绝缘油 的各组分含量增长 要 的 , 也是 变压 器安 全运 行 的可靠 保证 。 通 过 表 2中 油 中 溶 解 气 体 试 验 数 相对稳定 ,介于主变大修后未曾更换变 参 考文献
Φ12螺纹钢四切分轧制技术在棒材厂的应用与改进

Φ12螺纹钢四切分轧制技术在棒材厂的应用与改进摘要:本文叙述了棒材厂φ12螺纹钢生产的工艺选择、试轧时出现的问题和工艺改进以及对切分技术的成果分析和切分技术的展望。
关键词:螺纹钢四切分轧制孔型系统导卫1 前言切分轧制是在轧机上利用特殊的轧辊孔型和导卫或者其他切分装置,将原来的一根坯料纵向切成两根以上的轧件,进而轧制多根成品或中间坯的轧制工艺。
采用切分轧制技术可缩短轧制节奏,提高机时产量,显著提高生产效率,降低能耗和成本。
目前棒材φ12mm螺采用三切分轧制工艺,终轧速度为15米/秒,其最高小时产量为57.4支/小时,平均小时产量为50支/小时,平均日产为2380吨/天,与其他规格的平均日产2903—3189吨/天存在较大的差异。
为了更好的发挥切分轧制的经济效益,结合市场对小规格螺纹钢需求量较大的实际,棒材厂决定开展φ12螺纹钢四切分生产工艺改造。
这将大幅度提高小规格产能和生产效率,降低生产成本,提高经济效益。
2 主要设备概况2.1 加热炉加热炉为步进式加热炉,最大加热能力为11Ot/h。
采用钢坯尺寸为150mm ×150mm ×12000mm,重约2075kg。
2.2 轧机一棒轧线上共有20架轧机,粗轧6架550轧机(1-6架)、中轧6架420轧机(7-12架),精轧8架350轧机(7-20架,其中17、18架轧机为平立转换轧机);二棒轧线上共有18架轧机,粗轧6架550轧机(1-6架)、中轧6架420轧机(7-12架),精轧6架350轧机(7-18架),一棒采用平立交替布置,粗、中轧为无扭微张力轧制,精轧采用活套无张力轧制,粗中轧、中精轧之间各有一台飞剪,精轧后设有一台倍尺飞剪。
2.3 冷床冷床为126米齿条步进式冷床,可收集和冷却剪成倍尺的棒材。
2.4 冷剪冷剪剪切能力为850T,可将成排棒材按定尺剪切,剪切范围6~12米。
3 四切分技术的应用与改进四切分轧制,即在轧制过程中通过孔型,将1根轧件轧成具有4个相同形状的并联轧件,再通过切分导卫及孔型将并联轧件沿纵向切分成4个单根轧件。
小规格带肋钢筋四切分轧制工艺开发和优化实践

Ke y W o r ds: Ri b b e d S t e e l Ba r ; Ro l l i ng; F o u r —s t r a n d S p l i t t i n g Ro l l i n g Pr o c e s s ; Pa s s; Gu i d e s a n d
mm r i b b e d s t e e l i s 3 0 % h i g h e r t h a n t h a t o f t h r e e - s t r a n d s p l i t t i n g r o l l i n g p r o c e s s .
| 蠹
毫 _ — 瞬l 蔫 l _
I 芬 爱 钧 6 苹 每 s 觏
小规格带肋钢筋四切分轧制工艺开发和优化实践
罗庆革 ( 棒 线型 材厂)
摘
要 :介 绍 了柳 钢棒 线 型材 厂 小规格 带肋钢 筋 四切 分 工 艺的孔 型 、导 卫 装置 和 和轧 制 通道 的
轧 件 ,并 在 精轧 道 次 上 延 纵 向将 并 联 轧 件 切 分
为 四个 尺 寸 面 积 相 同 的 独 立 轧 件 的 轧 制 技 术 。 四线 切 分 C L N技 术 的核 心 是先 完 成 并 联 轧 件 的
三 切 分 ,再 完成 并 联 轧 件 的两 切 分 ,通 过 这 两
莱钢12mm热轧带肋钢筋四切分轧制技术的开发
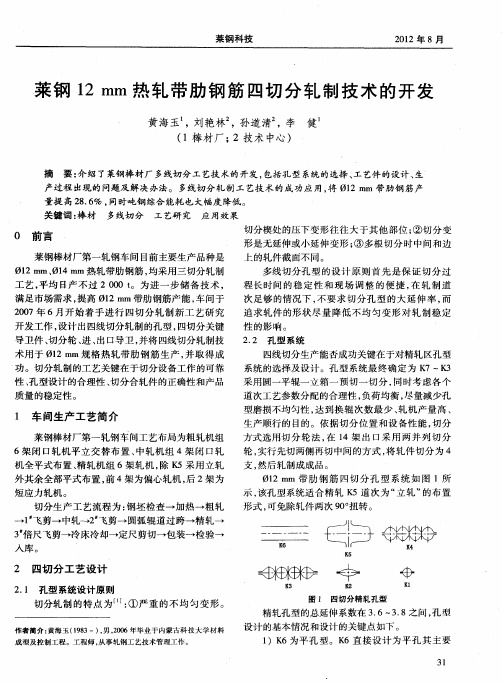
第 4期 ( 总第 10期 ) 6
作用 为将 来料压 宽 。K 6机架 采用 平辊 , 分利 用平 充
辊轧 制 的特点 : 宽 度 限制 、 无 调整 量 大 , 辊 利 用率 轧 高 的 < 5轧件 的
上下 对应 的 , 分楔 两侧 的压下 量是 基本 相 同 的 , 切 即
莱钢 科技
21 0 2年 8月
莱 钢 1 m 热 轧 带 肋 钢 筋 四切 分 轧 制技 术 的开 发 m 2
黄海 玉 ,刘艳林 ,孙道清 ,李 健
( 1棒材厂 ; 2技术 中心)
摘
要 : 绍 了莱钢棒 材 厂 多线切 分 工 艺技 术的 开发 , 介 包括孔 型 系统 的选择 、 工艺件 的设计 、 生
采用 立 轧
外其余全部平式布置 , 4架为偏心轧机 , 2 前 后 架为
切分 生 产 工艺 流 程 为 : 坯 检 查一 加 热 一 粗 轧 钢 一 1飞剪一 中轧
入库 。
飞 剪一 圆弧辊 道 过 跨一 精 轧 一
3倍 尺 飞 剪一 冷床 冷却一 定 尺剪 切 一包 装 一 检验 一
是遵 循尽 量减 小不均 匀 变形 的设 计 原则 。从 图 中可 以直观地 看 出 , 中间孔 的压缩 面积 比两侧 孔 大 , 且 并
中间孔 没有金 属横 向流 动 的空 间 , 这种情 况 , 必然 导 致K 3中间 孔 两 侧 的切 分 楔 壁 磨 损 速 度 较 两 侧 孔
快, 中间孔 的面积 和宽度 在 轧制过 程 中越来 越大 , 虽
性 、 型设 计 的合 理性 、 分合 轧件 的 正确性 和 产 品 孔 切
质量 的稳 定性 。
1 车 间生产 工艺简介
莱钢 棒材 厂第 一 轧钢 车 问工艺 布局 为粗 轧 机组 6架 闭 口轧 机 平 立 交 替 布 置 、 中轧 机 组 4架 闭 口轧
唐山钢铁公司轧钢厂12四切分工艺学习总结
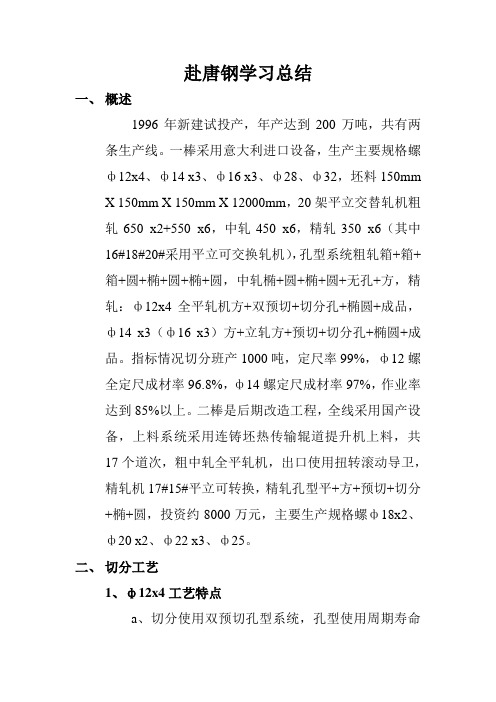
赴唐钢学习总结一、概述1996年新建试投产,年产达到200万吨,共有两条生产线。
一棒采用意大利进口设备,生产主要规格螺ф12x4、ф14 x3、ф16 x3、ф28、ф32,坯料150mm X 150mm X 150mm X 12000mm,20架平立交替轧机粗轧650 x2+550 x6,中轧450 x6,精轧350 x6(其中16#18#20#采用平立可交换轧机),孔型系统粗轧箱+箱+箱+圆+椭+圆+椭+圆,中轧椭+圆+椭+圆+无孔+方,精轧:ф12x4全平轧机方+双预切+切分孔+椭圆+成品,ф14 x3(ф16 x3)方+立轧方+预切+切分孔+椭圆+成品。
指标情况切分班产1000吨,定尺率99%,ф12螺全定尺成材率96.8%,ф14螺定尺成材率97%,作业率达到85%以上。
二棒是后期改造工程,全线采用国产设备,上料系统采用连铸坯热传输辊道提升机上料,共17个道次,粗中轧全平轧机,出口使用扭转滚动导卫,精轧机17#15#平立可转换,精轧孔型平+方+预切+切分+椭+圆,投资约8000万元,主要生产规格螺ф18x2、ф20 x2、ф22 x3、ф25。
二、切分工艺1、ф12x4工艺特点a、切分使用双预切孔型系统,孔型使用周期寿命长,辊耗低。
b、孔型与导卫配置合理,工艺稳定。
c、合金导轮及轴承采用内置水冷油气润滑系统,导轮二次加工可再利用。
2、导卫配置:a、粗中轧机进口导卫1#2#3#5#7#9#11#13#滑动导板,4#6#8#10#12#14#滚动导轮。
b、粗中轧机出口导卫全部为滑动导板。
C、精轧机ф12x4导卫K5K6进口双排轮(前大后小均为平轮),K4进口双排圆弧轮(前大后小),K3进口双排菱形轮(前大后小),K1K2采用分段式圆形喇叭+导轮(平)总成,K4K5K6出口上下导板斜铁固定结构,K3出口切分双排轮(切分刀上下结构,先切两侧后切中),K2出口扭转轮总成(平轮x4)。
ф14x3规格K2进口采用滑动导板,K5进口单排平轮总成,其它导卫相同。
Ф12mm螺纹钢四切分轧制技术的开发实践
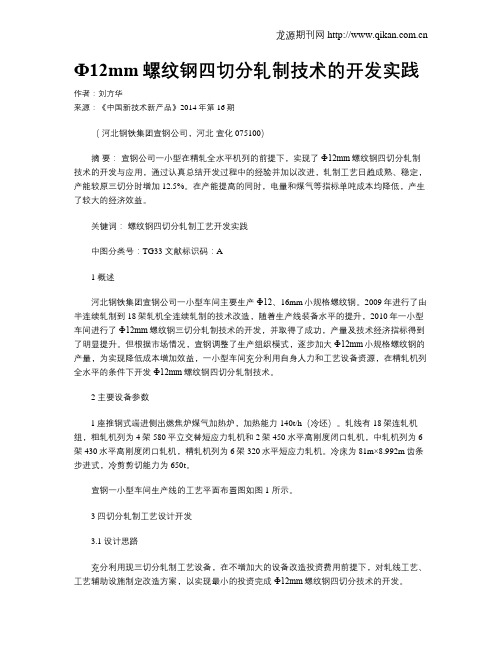
Ф12mm螺纹钢四切分轧制技术的开发实践作者:刘方华来源:《中国新技术新产品》2014年第16期(河北钢铁集团宣钢公司,河北宣化 075100)摘要:宣钢公司一小型在精轧全水平机列的前提下,实现了Ф12mm螺纹钢四切分轧制技术的开发与应用,通过认真总结开发过程中的经验并加以改进,轧制工艺日趋成熟、稳定,产能较原三切分时增加12.5%。
在产能提高的同时,电量和煤气等指标单吨成本均降低,产生了较大的经济效益。
关键词:螺纹钢四切分轧制工艺开发实践中图分类号:TG33 文献标识码:A1 概述河北钢铁集团宣钢公司一小型车间主要生产Ф12、16mm小规格螺纹钢。
2009年进行了由半连续轧制到18架轧机全连续轧制的技术改造,随着生产线装备水平的提升,2010年一小型车间进行了Ф12mm螺纹钢三切分轧制技术的开发,并取得了成功,产量及技术经济指标得到了明显提升。
但根据市场情况,宣钢调整了生产组织模式,逐步加大Ф12mm小规格螺纹钢的产量,为实现降低成本增加效益,一小型车间充分利用自身人力和工艺设备资源,在精轧机列全水平的条件下开发Ф12mm螺纹钢四切分轧制技术。
2 主要设备参数1座推钢式端进侧出燃焦炉煤气加热炉,加热能力140t/h(冷坯)。
轧线有18架连轧机组,粗轧机列为4架580平立交替短应力轧机和2架450水平高刚度闭口轧机,中轧机列为6架430水平高刚度闭口轧机,精轧机列为6架320水平短应力轧机。
冷床为81m×8.992m齿条步进式,冷剪剪切能力为650t。
宣钢一小型车间生产线的工艺平面布置图如图1 所示。
3 四切分轧制工艺设计开发3.1 设计思路充分利用现三切分轧制工艺设备,在不增加大的设备改造投资费用前提下,对轧线工艺、工艺辅助设施制定改造方案,以实现最小的投资完成Ф12mm螺纹钢四切分技术的开发。
3.2设计孔型系统考虑轧线粗中轧Ф12、16mm规格孔型的共用和Ф12规格切分后精轧孔型不变,此次Ф12规格螺纹钢四切分孔型主要设计11-16架,甩掉12架次,11架与13架采用平辊,孔型形式14架次为立箱孔,15架次为哑铃形,16架次为切分孔,15、16架孔型的设计主要是通过确定合理的孔型宽高比以实现四线孔型的面积精确控制,四线金属流量分配均匀,保证料型稳定。
Ф12mm螺四切分轧制工艺的优化
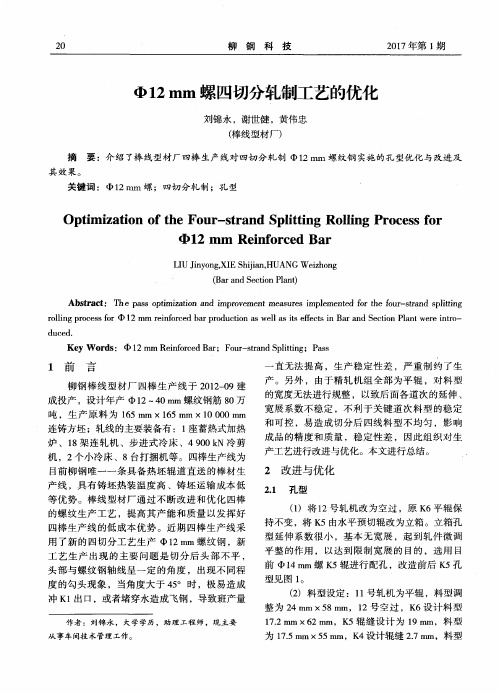
其 效果 。 关键 词 :
Op t i mi z a t i o n o f t h e Fo u r - s t r a n d S p l i t t i n g Ro l l i n g Pr o c e s s f o r
1 2 mm Re i n or f c e d Ba r
2 0 1 7年第 1 期
刘锦永等:中 1 2 m m螺四切分轧制工 艺的 优化
2 1
度 均 匀 性 ,轧 制 温 度 控制 以 2号 飞 剪 处 温 度 为
准 ,控制在 1 0 4 0℃ ±1 0℃;上冷床温度 :6 9 0 ℃~ 7 0 0℃。三是开展轧制线对 中,重点对活套 架 进 出 口导槽 ,喇 叭 口 ,导 卫 进 出 口安 装 ,K1
1 前
言
直 无 法 提 高 ,生 产 稳 定 性 差 ,严 重 制 约 了生
柳 钢 棒 线 型材 厂 四棒 生 产 线 于 2 0 1 2 — 0 9建 成 投产 ,设计 年 产 1 2~ 4 0 m m 螺纹 钢筋 8 0万
吨 ,生 产 原 料 为 1 6 5 mm ×1 6 5 mm ×1 0 0 0 0 m m
( 2 ) 料型设 定 :1 1 号 轧机 为 平辊 ,料 型调
整为 2 4 mm×5 8 m m,1 2号 空 过 ,K 6设 计 料 型 1 7 . 2 m m×6 2 m m,K 5辊缝 设 计 为 1 9 mm,料 型 为1 7 . 5 mm×5 5 m m,K 4设计 辊缝 2 . 7 mm,料 型
出 口至 穿 水 管 进 口 ( 空 过竹 节 管 导 槽 ) 水 平 校
对 ,避 免 与 K l出 口不水平 造 成钢 头 碰对 盖板 或
- 1、下载文档前请自行甄别文档内容的完整性,平台不提供额外的编辑、内容补充、找答案等附加服务。
- 2、"仅部分预览"的文档,不可在线预览部分如存在完整性等问题,可反馈申请退款(可完整预览的文档不适用该条件!)。
- 3、如文档侵犯您的权益,请联系客服反馈,我们会尽快为您处理(人工客服工作时间:9:00-18:30)。
辊一立箱一预切一切分,孔型系统图见图3。
IOH
11H
12H
盟
塑
坦
世
◇二空过二晋紫黪
图3:宣钢一小型12四切孔翌图
3.2孔型设计
①K1、K2孔:与三切共用。 ②K3切分孔:结合三切的孔型设计经验及生产调整控制,该孔型仍按三切的料型进行 设计。连接带厚度设计选择0.8mm,宽度0.7mm,中间楔角61。,重新配比边孔与中间孔型
图1:一小型车间工艺平面布置简图
l一加热炉;2一Q
580x4+qu
550×2粗轧机列;3一l群剪;4一Q 430×6机列;5—2撑剪;6—伽套;
7—Q 320×6机列;8—2群活套;9一输送辊道;lO一3撑倍尺剪;1l一冷床:12一收集区
3四切分工艺开发技术方案
3.1总体思路
研究分析四切分工艺特点,结合现有《;P 12mm带肋钢筋三切分孔型设计及生产实践,最大
加了换槽换辊次数降低了作业率,提高了生产成本。 分析原因,除了与冷却水有关外,最主要的是轧辊存在内裂纹。经与合金轧辊生产厂
家沟通,改进了轧机冷却水,但崩槽问题未明显减轻。进一步分析,发现造成轧辊辊环处内
裂纹主要由轧件头部进入孔型不正确,碰撞辊环后再咬入孔槽,辊环处形成裂纹,在第1、2
次使用后,轧辊修复裂纹层被部分或全部修复掉,随着后续使用,裂纹层加深最后导致崩槽。
出口导卫,导卫的设计要综合考虑4线配辊、操作调整灵活方便来选型,确定外形尺寸。K1 进口采用JXMA35P带有鼻锥的滚动导卫,其他采用现有的三切型式。
②K3出口切分导卫:采用切分轮法通过“一分三,三变四”完成四切分轧制技术,除
孔型设计外最重要的是切分导卫的设计,随着切分支数的增加,对导卫的设计、制作及安装
4.25L制过程难稳定顺行
主要表现在生产过程中轧槽磨损一旦需要换孔型,换孔型架次数超过两架轧机以上,换
孔型调整时间长,生产难稳定。经分析主要原因是铸铁材质轧辊不利于四切生产料型的控制,
因其耐磨性低,料型变化快,新Ilt孑L型配合给料型控制、速度调整均增加了难度。 解决方案:首先,提升精轧机轧辊材质,除K5立箱孔外,其余轧机全部采用合金轧辊, 确保料型能在较长时间内保持在标准要求之内,摸索各架次轧辊磨损程度制定合理的轧制吨
平辊轧机,为确保轧件正确进入K7轧机,设计该出口导卫为扭转导卫,与K6出口扭转导卫 共用。 具体导卫选型情况如下:
四切形式
进口
K7 11H
目前三切形式 滑动
滑动
不变,与三切同 与K4出口相同,设计时 内腔加耐磨衬板 不变,与三切同, 只修改内腔尺寸
RTO一2B
滑动 扭转 滑动 扭转,RTO一1B 滚动 扭转,RTO一1B
导致在生产过程中轧件中心与切分轮不在同一中心线上发生切偏。
解决措旋:在鼻锥中间加一个导向楔,并在鼻锥导向楔外部标刻线,确保装配时导向楔 与孔型中心、单刃切分轮严格对中。 ②切分轮切分力大
对现场堆钢进行分析,发现轧件经单刃切分轮撕开后角度过大造成中间一线顶长刀钻入
两侧通道,轧件经单刃切分轮撕开后角度过大说明切分轮切分力大,影响切分轮的切分力因 素有切分轮的切分角度和切分刃的宽度两方面。 解决措施:结合孔型切分角度设计,修改单刃切分轮切分角,在原有的基础上减小3。,
调整精度要求增倍,四切切分生产最关键、难度最大的导卫是K3出口切分导卫。
在导卫选型上,通过与导卫生产厂家的技术交流,结合现场情况选用了4CF型,导卫结 构(如图1)主要有鼻锥、切分轮、导卫体、分料器组成。鼻锥的作用主要是引导切分轧件 正确进入第一组双刃切分轮,将轧件从两侧一分为三。第二组切分轮为单刃切分轮,使通过
对于中轧孔型系统,主要是考虑与9 12三切分最大化共用及四切精轧一架轧机的力能 参数。通过对轧机力能、咬入的校核,中轧孔型系统与币12三切分共用到9H,lOt{设计为 立椭孔满足轧件宽展的需要,11H为平辊,甩掉12H轧机。
这样,qo 12四切分为17道次轧制,K9—K3孔型系统方案确定为立椭一平辊一空过—平
4四切分轧制生产中存在的问题及解决方案
4.1切分架次出口堆钢
通过分析,切分导卫堆钢的主要原因是切偏头、切分轮切分力大造成中间一线顶长刀钻 入两侧通道、左右长刀装反轧件运行不畅项刀、导卫安装不正等,针对不同原因进行分别解 决。
①切偏头
造成切偏头的主要原因是切分鼻锥无导向楔不能正确引导轧件造成切偏。切分鼻锥是由 上下两部分对称组成,前部的舌形部分直接贴入轧辊。根据两线、三线切分的经验,切分鼻 锥设计有导向锲时轧制过程中易发生粘皮而堆钢,因此在四切的鼻锥设计时也未加导向锲,
位。其次,制定换孔型方案,将换孔型时间尽可能安排在白班更换,提高换孔型操作精度, 同时K3切分与K4预切分孔型采用同时更换方式,便于料型控制。
4.3合金轧辊成品辊崩槽严重
主要表现在成品辊应用合金轧辊后,在返修两次及以上后出现崩槽严重,四切生产成 品槽一组四个,一组中崩其中任何一个槽该组都要废掉,这不仅降低了轧辊利用率,同时增
关键词:四切分;
带肋钢筋;孔型;导卫
1
前言
在棒材生产中,因切分轧制能有效提高产量、降低生产成本,使得该技术得到广泛应
用,并很快由两线发展到三线、四线甚至五线的多线切分轧制。目前,两线、三线切分技术 己趋于成熟,四线及以上的多线切分轧制技术还存在相当的难度。 宣钢小型轧钢厂一小型车间主要承担宣钢公司小规格带肋钢筋的生产任务。f12004年
化的共用孔型和现有设施,切分位置仍为K3孑L,切分方式仍采用切分轮切分,在K3出口先切 两边“一分三”,再切中间“三变四”,将一根轧件分为四根,在经过K2、K1轧制成成品。
3.2孔型系统方案
四切分精轧孔型系统设计思路与三切分相同,但在具体设计上目前存在两种方式: 一种是双预切孔型系统(如图2),即在预切分孔型前再增加一个预切分孔,孔型系统
切分
K2
17H
进口
出口
不变,与三切同 不变,与三切同
JXMA35P
滑动 滚动 滚动,35SP 滑动
扭转
,聋、
K1
18H
进口
出口
滚动 滑动
。≮乡
不变,与三切同
3.4其它技术方案
①设计制作四线专用2抖活套。 因精轧机的机架间间距较小,给活套的设计带来困难。又因2抖活套布置于K2与K3间, 活套的设计需综合考虑K3出口切分导卫的外形尺寸、四个通道间距,以及K1、K2配辊的设 计,而配辊的设计需考虑进出口导卫的外形尺寸。综合考虑以上因素,在最大化利用轧辊的
出口
K6
13H
进口
出口
滑动 扭转
滚动
K5
14H
进口
出口
RE75SP,与中轧12H现用 进口形式相同
RTO一2B
扭转
进口
K4
15H
娘啪
赶迁迂妊
ቤተ መጻሕፍቲ ባይዱ滚动
滑动 滚动 切分 滑动
RE55WBS,三排轮 不变,与三切同, 只修改尺寸 RE55WBS,三排轮
4CF
滚动,RE55WBF
滑动
出口
K3
16H
进口
出口
滚动,RE55WBF
为平辊一箱一预切一预切一切分,采用该种方式的主要优点是降低K4预切孔型负荷,使K4 孔不易磨损确保K3孔型的正常使用。缺点是多一道平轧孔型,对料型的控制精度要求更高, 如果K6料型不精确或K5导卫不对中会造成料型不规范、项切分导卫等事故,且无法通过调
整来弥补。
另一种是与三切分孔型系统完全相同,即平辊一箱一预切一切分系统。
2主要工艺及设备概况
宣钢小型轧钢厂-4,型车间经过不断的技术改造,目前已形成一条全连续轧制生产线, 主要生产9 12ram、叩16mm两个规格带肋钢筋,均采用切分轧制,叩12mm规格三线切分、9
16mm
规格双线切分,设计最大成品速度16m/s,年产量80万吨。
原料采用150方连铸坯,单重1.57t。 主要设备有:一座端进侧出推钢式加热炉,最大冷坯加热能力为140t/h。 18架轧机,粗轧机组为9 580X4(短应力线轧机、平立交替布置)+cp 550X2(闭口式
切分刃的宽度由原设计的2mm降低为lmm。
③左右长刀装反
四线切分导卫分料器中设有三个刀,主要用于切分后轧件通道分割,原设计的长刀尺寸
外形完全一样,但分左右向,装配时需仔细否则易装反,刀装反后易发生堆钢事故。
解决措施:设计长刀不分左右向,这样不仅解决了因操作失误造成的堆钢事故还降低了 配件量。
④导卫安装不正 针对由于导卫上线安装对不正孔型造成堆钢问题,制定措施:所有精轧机进出口导卫全 部线下安装,确保导卫与孔型严格对中。
轧机、水平布置),中轧机组为Q 430X6(闭口式轧机、水平布置),精轧机组为9 (短应力线轧机、水平布置),全连续布置。 一座步进齿条式冷床,冷床面积81mX8.992m:2台热剪,1台650t冷剪。
全线共设2个活套,分别布置在终轧末架与精轧一架、精轧第四与第五架间。
320X6
图1为车间平面布置布置简图。
解决方案:修改成品前平椭孔型,增加平椭孔型的平直段长度,利于导卫对轧件的夹 持,使轧件头部直立性的进入成品孔型。修改成品进口导卫,根据成品前料型缩小进口导板
的孔型尺寸,使导板尽可能把正确持住轧件。修改成品进口导卫轮形,由两用的“V”形轮 改为平轮,增加导轮对轧件的夹持与导送。提高导卫的上线安装精度,确保导卫对中孔型。
基础上尽可能缩小四线间距,结合三切分的经验,优化压套辊与起套辊的间距设计2#活套。
②设计制作成品末架与3#倍尺剪间的辊道及过渡导槽。 当前成品末架与3#倍尺剪间采用的是导槽的形式,轧件在运行过程中易出现顶撞,针 对此,废弃导槽,全部改为辊道输送形式与倍尺剪后输送辊道相同,实现配件的共用,仅在
辊道的两端设计过渡导槽。 ③设计制作2#剪过渡导槽。 因中轧甩掉末架12H轧机,11H出来的料型为平辊料,在11H与2#剪间设计制作矩形导 槽,同时将2#剪前摆动导槽由圆形改为矩形。