喷涂工艺规程
涂装工艺规程
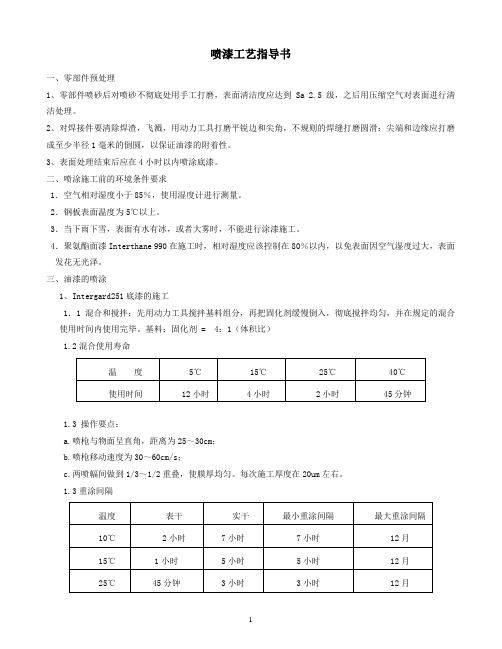
喷漆工艺指导书一、零部件预处理1、零部件喷砂后对喷砂不彻底处用手工打磨,表面清洁度应达到Sa 2.5级,之后用压缩空气对表面进行清洁处理。
2、对焊接件要清除焊渣,飞溅,用动力工具打磨平锐边和尖角,不规则的焊缝打磨圆滑:尖端和边缘应打磨成至少半径1毫米的倒圆,以保证油漆的附着性。
3、表面处理结束后应在4小时以内喷涂底漆。
二、喷涂施工前的环境条件要求1.空气相对湿度小于85%,使用湿度计进行测量。
2.钢板表面温度为5℃以上。
3.当下雨下雪,表面有水有冰,或者大雾时,不能进行涂漆施工。
4.聚氨酯面漆Interthane 990在施工时,相对湿度应该控制在80%以内,以免表面因空气湿度过大,表面发花无光泽。
三、油漆的喷涂1、Intergard251底漆的施工1.1混合和搅拌:先用动力工具搅拌基料组分,再把固化剂缓慢倒入,彻底搅拌均匀,并在规定的混合使用时间内使用完毕。
基料:固化剂 = 4:1(体积比)1.2混合使用寿命1.3 操作要点:a.喷枪与物面呈直角,距离为25~30cm;b.喷枪移动速度为30~60cm/s;c.两喷幅间做到1/3~1/2重叠,使膜厚均匀。
每次施工厚度在20um左右。
1.3重涂间隔2、 Intergard400施工说明2.1.混合和搅拌:具体操作与底漆相同基料:固化剂=5.67:1(体积比)2.2混合使用寿命3.3 重涂间隔3、Interthane 990施工说明3.1混合和搅拌:具体操作同底漆基料:固化剂=6:1(体积比)3.2混合使用寿命3.3.重涂间隔4、弛张筛结构件外表面用油漆系统三、注意事项1 在涂装中层漆和面漆之前应先检查前一道涂层表面是否有损坏、漏涂、流挂等现象,并进行处理,以达到规定的质量要求2 除了不易喷涂到的地方作刷涂之外,所有表面都要喷涂或滚涂施工。
四、完工检查1、漆膜:色泽均匀,无流挂、无漆雾、无污染。
2、缺陷:无针孔、无气泡、无漏喷等。
3、湿膜厚度与干膜厚度:根据规定的最低/最高厚度。
喷涂喷漆工艺规程

7.3 预处理中除锈(酸洗)或抛丸处理
7.3.1 化学除锈
处理槽名称
主要成分
处理温度
液面控制风速
硫酸酸蚀处理槽
硫酸 15-25%
0.35m/s
若丁 15-25%
盐酸酸蚀处理槽
盐酸 10-2允许放于有色金属零件和含有有色金属零件的钢铁零件;
1)加工精度在 以上的零件不准酸洗;
喷涂喷漆工艺规程
———————————————————————————————— 作者:
———————————————————————————————— 日期:
ﻩ
喷涂喷漆工艺规程
1.本规程的全部内容为强制性
2.编制本规程的依据是:
GB 7692—1999 《涂装作业安全规程,涂装前处理工艺安全及其通风净化》
9.4 所使用的面漆必须要充分搅拌均匀,并用120目以上的铜(不锈钢)筛网过滤,工作完毕后用稀释剂清洗干净喷枪;
9.5 底漆的喷涂要特别注意边缘棱角,底漆一般喷两道,在前一道底漆未干燥之前,不能喷下一次漆,干燥要适度,干燥小容易被面漆咬起,干燥过大,与面漆结合不好,容易形成缩孔和发酵,喷完底漆的工件,小心再次被污染;
6. 操作现场场地要求
6.1 操作场地应通风良好,首先启动通风设备。通风设备未启动之前,喷涂喷漆设备不应工作,涂喷漆工作结束后,通风设备应继续运行5-10分钟;
6.2 操作场地外露电气应接地保护,防止静电及漏电,接地电阻值应小于100Ω;
6.3 被喷涂喷漆的零件,或喷涂材料,与电极,电器或带电导体之间应保持一定的安全距离,至少为该电极及带电导体电压下火花放电距离的两倍,并应有明显的警告标志。
GB 12367—2006 《涂装作业安全规程,静电喷漆工艺安全》
喷漆工工艺守则

喷漆工艺守则一、喷漆前的表面处理:(1)铸件:对表面凸起不平处,应用工具进行磨凿平整,清除其表面污物。
(2)钢板件:一般应采取酸洗磷化处理,必须彻底清除残余酸液,以防漆层起泡。
(3)经机加工后的零部件,须用金属净洗剂或工业汽油等进行淋洗或刷洗,彻底清除表面的油污及其他赃物。
二、喷涂防锈底漆:底漆施工可用喷、刷、浸方法,漆膜要均匀,附着力要好。
三、填腻对于产品表面往往带有凹凸锈痕铸件砂孔等缺陷,必须采用填腻填平,每次填刮厚度应在0.5㎜以内,总厚度一般不超过1.5㎜为宜。
四砂磨:应用1#—2#金刚砂布或磨石在干燥的腻子表面进行砂磨,以达到表面平整去除粒屑,砂磨后需抹去表面的灰尘。
五水磨:将磨石或水砂纸全部浸湿,然后用少量水一起砂磨已干燥的涂层或腻子,以湿布擦净粉浆,最后的砂纹应不影响涂膜外观的性能。
六、喷涂面漆:应根据设计要求规定的漆类,调配置适当的粘度喷涂。
七、干燥:应放在通风、早晚干燥的地方,根据工艺规程严格控制,八、注意事项:1、涂装环境应清洁,无灰尘,施工时温度不得低于12℃,相对湿度不得低于80%。
2、喷漆时采用的压缩空气不允许含有油和水,并应经常检查油水分离器的可靠性。
3、钢板焊接件采用酸洗时,应特别注意把焊缝等地方的酸液及时清洗干净。
4、经清理或磷化处理过的表面不允许受到雨水、潮气、污物及腐蚀气体等的作用,并应在10小时内涂上底漆。
5、调配漆液时,应充分搅拌均匀,对底漆采用120目,而漆采用200目的钢丝网过滤。
6、漆种的稀释应使用规定的稀释剂,禁止不同漆种及稀释剂相互掺用,防止变质。
7、按工艺规程使喷枪和压缩机,每班后清洗喷枪,关闭电源。
8、在涂装施工过程中,操作人员必须穿戴防护用品,并要防止漆与皮肤直接接触。
威海市海翔试验机制造有限公司工艺科2003年12月。
喷涂工程施工规范

喷涂工程施工规范一、总则1.1 喷涂工程是指使用喷枪将各种涂料均匀地喷涂在物体表面的施工过程。
喷涂工程广泛应用于建筑、装饰、防腐、保温等领域。
为确保喷涂工程的质量和安全,特制定本规范。
1.2 本规范适用于新建、改建、扩建的喷涂工程施工。
1.3 喷涂工程施工应遵循国家有关法律法规、标准和规定。
二、施工准备2.1 材料准备2.1.1 喷涂材料应符合设计要求和国家相关标准,应有出厂合格证和质量检验报告。
2.1.2 喷涂材料应妥善存放,防止日晒、雨淋、污染和损坏。
2.2 设备准备2.2.1 喷涂设备应具备良好的性能,包括喷枪、空气压缩机、输料系统等。
2.2.2 设备应进行试运行,确保正常运行后方可使用。
2.3 施工场地准备2.3.1 施工场地应清理干净,无杂物、油污、水分等。
2.3.2 施工场地应设置安全警示标志,非施工人员不得进入。
2.3.3 施工场地应配备必要的消防设施。
三、施工工艺3.1 基层处理3.1.1 基层应平整、干净、牢固,无松动、脱落、裂缝等现象。
3.1.2 基层处理应符合设计要求和相关标准。
3.2 底涂施工3.2.1 底涂应均匀涂抹在基层表面,厚度应符合设计要求。
3.2.2 底涂施工后应进行验收,确保无遗漏、无缺陷。
3.3 面涂施工3.3.1 面涂应均匀喷涂在底涂层上,厚度应符合设计要求。
3.3.2 面涂施工应均匀,避免出现流淌、滴落、气泡等现象。
3.3.3 面涂施工后应进行验收,确保无遗漏、无缺陷。
四、施工质量控制4.1 喷涂工程的厚度、均匀度、附着力等应符合设计要求和相关标准。
4.2 施工过程中,应定期对材料、设备、施工质量进行检测和检查,确保符合要求。
4.3 施工完成后,应进行验收,验收不合格的工程不得投入使用。
五、施工安全与环保5.1 施工人员应遵守安全操作规程,佩戴必要的防护用品。
5.2 施工过程中应防止火灾、爆炸等事故的发生。
5.3 施工过程中应防止污染环境,妥善处理废弃物。
喷涂喷漆工艺规程
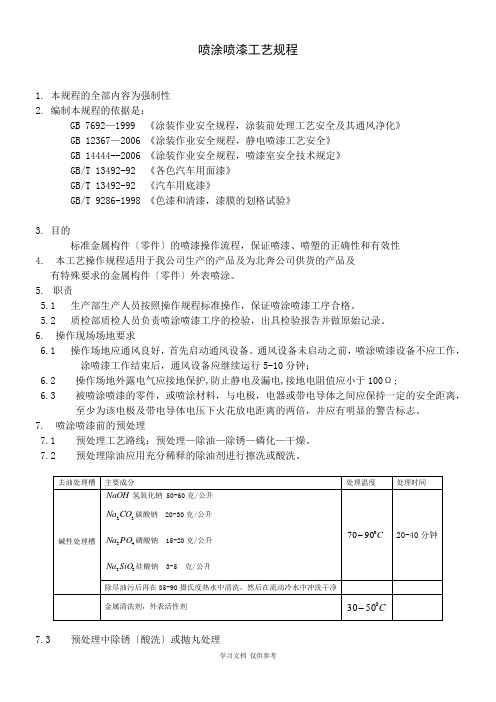
喷涂喷漆工艺规程1.本规程的全部内容为强制性2.编制本规程的依据是:GB 7692—1999 《涂装作业安全规程,涂装前处理工艺安全及其通风净化》GB 12367—2006 《涂装作业安全规程,静电喷漆工艺安全》GB 14444--2006 《涂装作业安全规程,喷漆室安全技术规定》GB/T 13492-92 《各色汽车用面漆》GB/T 13492-92 《汽车用底漆》GB/T 9286-1998 《色漆和清漆,漆膜的划格试验》3.目的标准金属构件〔零件〕的喷漆操作流程,保证喷漆、喷塑的正确性和有效性4.本工艺操作规程适用于我公司生产的产品及为北奔公司供货的产品及有特殊要求的金属构件〔零件〕外表喷涂。
5.职责5.1 生产部生产人员按照操作规程标准操作,保证喷涂喷漆工序合格。
5.2 质检部质检人员负责喷涂喷漆工序的检验,出具检验报告并做原始记录。
6. 操作现场场地要求6.1 操作场地应通风良好,首先启动通风设备。
通风设备未启动之前,喷涂喷漆设备不应工作,涂喷漆工作结束后,通风设备应继续运行5-10分钟;6.2 操作场地外露电气应接地保护,防止静电及漏电,接地电阻值应小于100Ω;6.3 被喷涂喷漆的零件,或喷涂材料,与电极,电器或带电导体之间应保持一定的安全距离,至少为该电极及带电导体电压下火花放电距离的两倍,并应有明显的警告标志。
7. 喷涂喷漆前的预处理7.1 预处理工艺路线:预处理—除油—除锈—磷化—干燥。
7.2 预处理除油应用充分稀释的除油剂进行擦洗或酸洗。
7.3 预处理中除锈〔酸洗〕或抛丸处理7.3.1 化学除锈操作要求酸洗槽内不允许放于有色金属零件和含有有色金属零件的钢铁零件;1)2)小型零件不能直接放入槽中,应放在框内或悬挂后放置槽内;3)酸洗后零件外表的黑膜冲洗不掉时,可以用毛刷刷掉之;4)每隔10-15分钟检查一次酸洗情况,一直到到达要求为止;5)防止温度过高和酸洗时间过长,造成零件过蚀;6)槽液铁盐含量到达200克/公升以上,或酸液浓度稀至5%以下时,更换新液;7)酸洗后再在流动冷水槽中仔细清洗零件;8)清洗后用压缩空气吹干,或自然干燥12-24h。
铝材喷涂工艺操作规程

1、目的通过对生产过程中的每一工艺过程作定性和定量的规定,规范和指导每一工艺过程中的操作者操作要求,从而确保型材的质量。
2、适用范围适用于喷涂车间对铝合金型材进行彩色静电粉末喷涂处理。
3、职责3.1 车间主任负责指导和监督车间员工按本操作规程的规定操作。
3.2 各岗位员工严格按本规程的规定进行作业。
4、操作规程4.1 喷涂车间生产工艺流程图4.2生产前的准备工作4.2.1提前15分钟上班,做好交接班手续,并配戴好生产安全防护用品。
4.2.2型材上架前,按《喷涂车间设备操作规程》的相关规定,将设备启动空载运行并巡回检查,确认设备运转是否正常。
4.2.3坯料准备:(责任人:前处理工)a)前处理工按生产部下达的生产指令领用和吊运坯料;b)上架工检查并确认坯料质量符合公司的规定要求。
4.2.4专用工具准备。
相关岗位人员检查以下工具是否齐备和符合使用要求:a)挂钩:已清洗干净,表面无积粉、无变形;b)小车:能正常推动。
4.2.5原材料准备。
相关岗位人员检查以下生产用原材料是否足够:前处理药水、粉末、溶剂、砂纸等。
4.2.6前处理操作要求(1)脱脂:温度为常温,AC剂浓度2-3%脱脂时间8-12分钟(视铝件表面污染程序而定),材料吊起过槽时,要尽量倾斜,倾斜度一般为5-10度角,并吊起控水1分钟;(2)水洗:两次用自来水洗,时间为1-3分钟,要求水洗槽有溢流;(3)无铬钝化:无铬钝化温度为常温,无铬酸浓度0.8-1.2%,PH值为3.0~4.0,无铬钝化时间为1-2分钟。
材料过槽时,要尽量倾斜,倾斜度一般为5-10度角(注:耗量指数根据铝件厚薄不同,药水消耗有所增减。
如铝材厚度平均在1mm,每吨铝材的药水耗量为1~2kg)。
(4)水洗:两次用自来水,时间各1-3分钟,吊起倾斜嘴为10度角,并吊起控水1分钟;(5)烘干:烘干时,烘干炉温度必须达到65-95℃,但不得超过100℃;烘干时间为30-40分钟;A、烘干的材料应为金黄色或略带彩红色,材料必须干燥、干净、无油污;B、烘干后,材料应小心放在料车上,运至喷涂车间做后工序处理,应做到当天铬化当天喷涂,最长放置时间不许超过48小时,且一定要用防尘布将其盖好。
喷涂的工艺流程(3篇)

一、前言喷涂是一种将涂料均匀涂覆在物体表面的工艺,广泛应用于汽车、建筑、家具、金属制品等行业。
喷涂工艺具有施工简便、涂层均匀、附着力强等优点,能够提高产品的外观质量和使用寿命。
本文将详细介绍喷涂工艺的流程,以供相关从业人员参考。
二、喷涂工艺流程1. 准备工作(1)材料准备:根据产品要求,选择合适的涂料、固化剂、稀释剂等材料。
涂料应符合国家相关标准,确保产品质量。
(2)设备准备:检查喷涂设备是否正常,包括喷枪、喷壶、搅拌器、空气压缩机等。
(3)场地准备:确保喷涂场地通风良好,无灰尘、油污等杂质,地面平整。
2. 喷涂前的表面处理(1)清洗:使用溶剂或水将物体表面的油污、灰尘、锈蚀等杂质清洗干净。
(2)打磨:对物体表面的凹凸不平、焊缝、焊点等部位进行打磨,提高涂层的附着力。
(3)磷化:对金属表面进行磷化处理,提高涂层的耐腐蚀性。
3. 喷涂作业(1)涂装前的准备工作:将涂料、固化剂、稀释剂按比例搅拌均匀,确保涂料均匀。
(2)喷涂方法:根据产品形状、尺寸和涂料特性选择合适的喷涂方法,如空气喷涂、高压无气喷涂等。
(3)喷涂参数:根据涂料特性、物体表面及环境温度等因素调整喷涂压力、喷枪距离、喷涂速度等参数。
(4)喷涂操作:手持喷枪,均匀地喷涂涂料,避免漏喷、流淌、堆积等现象。
(1)自然固化:将喷涂后的物体放置在通风、干燥的环境中,待涂料自然固化。
(2)加热固化:对需要快速固化的物体进行加热处理,提高固化速度。
5. 检查与修整(1)外观检查:检查涂层颜色、光泽、厚度、平整度等是否符合要求。
(2)附着力检查:使用专用仪器检测涂层与物体表面的附着力。
(3)修整:对不符合要求的涂层进行修整,如打磨、补涂等。
6. 包装与储存(1)包装:将完成喷涂的物体进行包装,防止涂层受到污染。
(2)储存:将包装好的物体存放在干燥、通风、避光的场所,避免阳光直射和潮湿。
三、喷涂工艺注意事项1. 涂料选择:根据产品要求、施工环境等因素选择合适的涂料。
喷涂生产工艺操作规程
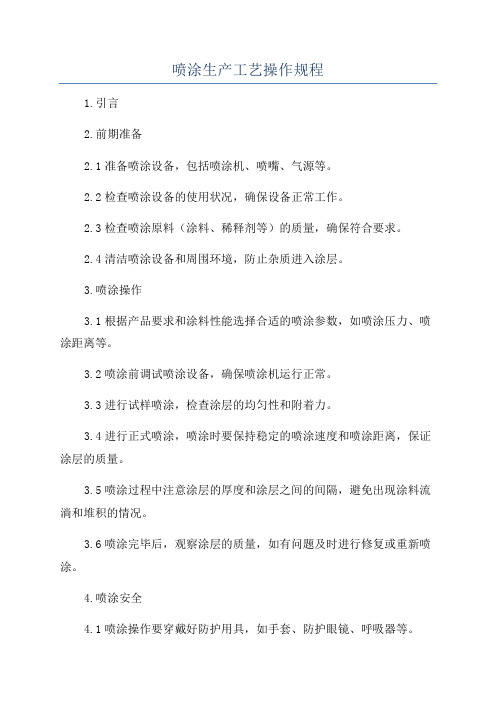
喷涂生产工艺操作规程1.引言2.前期准备2.1准备喷涂设备,包括喷涂机、喷嘴、气源等。
2.2检查喷涂设备的使用状况,确保设备正常工作。
2.3检查喷涂原料(涂料、稀释剂等)的质量,确保符合要求。
2.4清洁喷涂设备和周围环境,防止杂质进入涂层。
3.喷涂操作3.1根据产品要求和涂料性能选择合适的喷涂参数,如喷涂压力、喷涂距离等。
3.2喷涂前调试喷涂设备,确保喷涂机运行正常。
3.3进行试样喷涂,检查涂层的均匀性和附着力。
3.4进行正式喷涂,喷涂时要保持稳定的喷涂速度和喷涂距离,保证涂层的质量。
3.5喷涂过程中注意涂层的厚度和涂层之间的间隔,避免出现涂料流淌和堆积的情况。
3.6喷涂完毕后,观察涂层的质量,如有问题及时进行修复或重新喷涂。
4.喷涂安全4.1喷涂操作要穿戴好防护用具,如手套、防护眼镜、呼吸器等。
4.2喷涂设备要放置在通风良好的区域,避免喷涂过程中产生有害气体。
4.3喷涂过程中要注意防火防爆,禁止在喷涂区域内吸烟或使用明火。
4.4喷涂人员要经过专业培训,熟悉喷涂设备的操作和安全规范。
5.喷涂质量控制5.1进行涂层的质量检查,包括涂层的厚度、附着力、颜色等。
5.2进行涂层的耐腐蚀性测试,确保涂层能够满足产品的使用要求。
5.3进行涂层的外观检查,包括涂层的光泽度、平整度等。
5.4对不合格的涂层进行处理,如重喷、研磨、修补等。
6.喷涂设备维护6.1定期检查喷涂设备的工作状况,如气源是否正常、喷嘴是否堵塞等。
6.2定期清洗和保养喷涂设备,包括清洗喷嘴、更换密封件等。
6.3定期对喷涂设备进行维修和保养,确保设备的正常运行和寿命。
7.总结喷涂生产工艺是一项重要的表面处理方法,正确的操作能够保证涂层的质量和产品的性能。
本操作规程规定了喷涂生产工艺的操作步骤、安全要求和质量控制方法,对于提高生产效率和产品质量具有重要意义。
喷涂操作人员要严格按照本规程的要求进行操作,并不断总结和改进,以适应不同产品的需求。
喷漆工艺规程完整

喷漆工艺规程一、目的规范金属结构件的喷漆操作流程,保证油漆喷涂的正确性与有效性。
二、适用范围本工艺操作规范适用于我司生产产品用金属结构件喷涂以及有特殊要求金属结构件的表面喷涂。
三、职责3.1 生产部生产人员按照规范操作,保证喷漆工序合格。
3.2 品质部检验人员负责喷漆工序的检验,出具检验报告并保持纪录。
四、喷涂前准备4.1 外观检查检查待喷漆金属结构件表面有无披锋、多肉、粘砂、散热片缺损、油污、锈迹等缺陷,若存在上述缺陷则必须打磨或修补处理,合格后方可进行下道工序。
4.2 喷漆前处理a.用干毛刷清除金属结构件表面污物,然后用压缩空气将浮灰等吹干净。
b.用三合一除锈剂手工清洗金属结构件表面油污。
根据油污的程度调整稀释比例,搅拌均匀后使用。
c.用 120#砂纸打磨金属结构件表面,清除毛刺后吹干净,保证表面光洁,必要时再次清洗。
干燥后不可用手触摸待喷漆表面。
d.根据要求经过喷丸或喷砂处理的工件,要再进行清理工序、表面应洁净、干燥、无杂质、油污、尘埃,8小时内涂上配套底漆;e.喷漆件的内壁和地面贴(铺)防护材料应保持清洁,防止喷砂或漆雾凝结颗粒落于涂漆的部件上。
真对不同产品表面做喷砂使之达到一定粗糙度以增加油漆附着力。
喷砂后彻底进行清理,必须将产品中的缝隙、死角处的沙尘清理干净。
f.使用美纹纸与报纸粘贴、密封(钢板温度≥16℃),交界(两种漆颜色交界处)及不需要喷漆处(如玻璃、不锈钢件等)必须密封严,防止受到漆层污染;g.施工表面必须干燥清洁,温度高于露点,以免冷凝。
4.3原子灰处理:a.原子灰的两个基本处理时间段,第一是在底漆涂覆前进行填平、修补处理;第二是在底漆或中间漆涂覆并干燥后进行的二次填补处理,具体刮涂次数视产品的表面不平度而定。
b.腻子干燥后用电动工具或手工进行打磨,底漆前的原子灰打磨用150-320#砂纸打磨,至表面光滑平整为止,中间漆前的原子灰打、磨使用46-60#砂布进行打磨,打磨后必须用空压机清理磨屑。
喷涂生产工艺操作规程
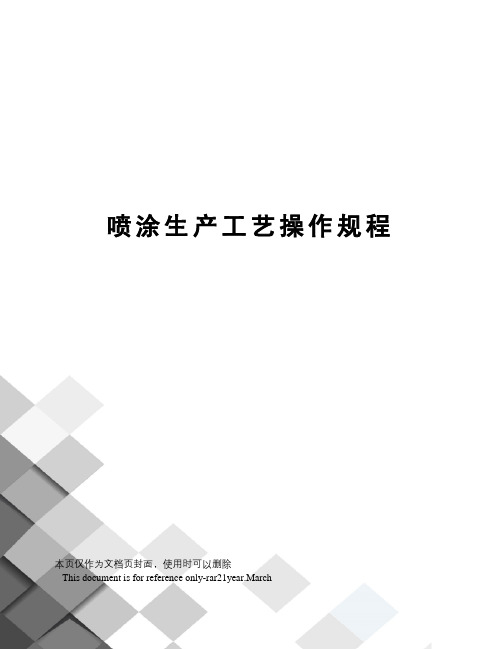
喷涂生产工艺操作规程本页仅作为文档页封面,使用时可以删除This document is for reference only-rar21year.March喷涂生产工艺操作规程发布日期:2010-5-4 [ 收藏评论没有找到想要的知识 ]粉末喷涂涂装生产工艺操作规范粉末涂装设备的启动 ,确保所有开关处于关闭状态,所有气压调节阀都已关闭.将粉末倒入流化桶,注意不要装得太多,因为充分流化后粉末的容积最多可能增加一倍.将空气总开关打开,以供气给流化供粉桶.打开流化空气压力调节器,慢慢增加空气量,当粉末表面产生气泡时,将气压调节器调小,直至粉末表面能产生持续均匀的小气泡为止.打开控制单元上的主电源开关.按住板机,慢慢打开供粉气调节阀,直至达到所需的出粉量.将喷枪指向粉室,按住板机,并慢慢增大辅助空气,指示球必须于表上绿色范围内浮动.注:当供粉气压力设于以上时,便不须打开辅助空气.可调节吹净空气来保证高压针和喷射面的清洁.进一步调节能改变粉末喷出图案的大小和形状以及粉末离开喷嘴的速率.供粉气(FEED AIR)一般为,辅助空气(DOSAGE AIR)一般为,吹净空气(ATOMIZING AIR).喷涂的一般的原则喷涂时应保证所有基板和夹具的清洁,并且工件一定要接地良好,以保证上粉率.喷涂时喷枪的移动不能过快,这一点正好与喷漆相反.(对返工件和砂纹粉的施工尤为重要)供粉量大并不意味着较快的喷涂速度.因为它无法保证上粉率以及边角凹角处较好的渗入性.在实际应用中通常会产生相反的作用,使得涂层质量低劣.同样,较高的放电电流或电压也不意味着有效的喷涂,出不能保证边角和凹处的较好的渗入性.1.注意:喷涂时应戴防尘面具.关机和清洗程序下班清洗将主电源开关关闭.将总供气阀关闭.将粉管和文丘里粉泵拆下,将其一头置于喷粉室中,另一头塞入海绵,用压缩空气反复吹2~3次.取下喷枪粉管,用压缩空气清洁喷枪和枪头的内外部.重新装上枪头和粉管,将枪放于安全位置.清理粉室.换色清洗参照下班清洗的步骤(1)~(5),但最后不要将粉管装上文丘里泵.从供粉桶取下文丘里粉泵,并拆下上面的气管.先用清洁干燥的压缩空气吹洗气管接口.从粉桶中提专职吸粉管,用压缩空气吹干净.倒出粉桶中剩余的粉末,并卸下无色的流化气管.彻底清洗流化床部件.重新安装各部件.1.注:粉室在喷枪工作和清理时必须终处于工作状态,即风机和回收系统处于工作状态,所有工作完成5分钟后才可关闭风机.粉末喷涂车间须注意的安全的事项由于在静电涂装装置上使用高电压,须定期检查喷枪的绝缘性能.在喷涂中,喷枪不能过分接近,更不能接触接地的导体.喷涂室、风道、回收装置、挂具,被涂物等都必须接地良好。
喷涂作业安全操作规程
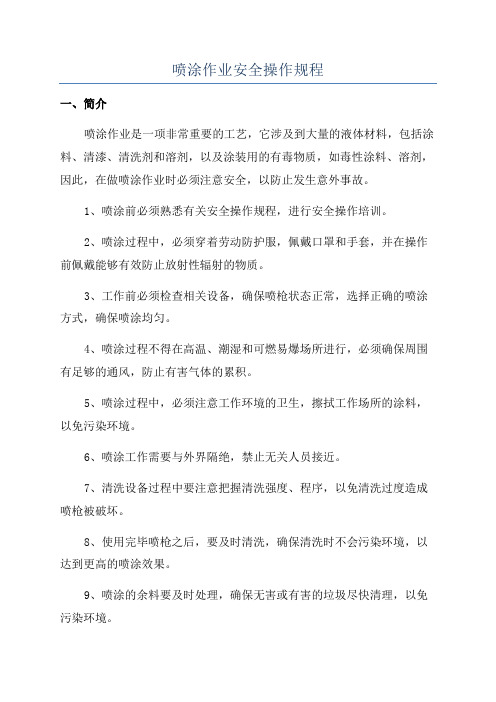
喷涂作业安全操作规程
一、简介
喷涂作业是一项非常重要的工艺,它涉及到大量的液体材料,包括涂料、清漆、清洗剂和溶剂,以及涂装用的有毒物质,如毒性涂料、溶剂,因此,在做喷涂作业时必须注意安全,以防止发生意外事故。
1、喷涂前必须熟悉有关安全操作规程,进行安全操作培训。
2、喷涂过程中,必须穿着劳动防护服,佩戴口罩和手套,并在操作前佩戴能够有效防止放射性辐射的物质。
3、工作前必须检查相关设备,确保喷枪状态正常,选择正确的喷涂方式,确保喷涂均匀。
4、喷涂过程不得在高温、潮湿和可燃易爆场所进行,必须确保周围有足够的通风,防止有害气体的累积。
5、喷涂过程中,必须注意工作环境的卫生,擦拭工作场所的涂料,以免污染环境。
6、喷涂工作需要与外界隔绝,禁止无关人员接近。
7、清洗设备过程中要注意把握清洗强度、程序,以免清洗过度造成喷枪被破坏。
8、使用完毕喷枪之后,要及时清洗,确保清洗时不会污染环境,以达到更高的喷涂效果。
9、喷涂的余料要及时处理,确保无害或有害的垃圾尽快清理,以免污染环境。
2铝合金型材立式喷涂工艺操作规程

2铝合金型材立式喷涂工艺操作规程一、工艺简介立式喷涂是一种常见的铝合金型材表面涂装方法。
该工艺适用于对铝合金型材进行喷涂处理,能够提高型材的表面质量和防腐蚀性能。
二、工艺流程1.准备工作(1)确认所需喷涂的型材种类、规格和数量;(2)清理喷涂设备和喷枪,并确保其正常工作;(3)准备好所需颜料、稀释剂和涂装辅助材料。
2.表面处理(1)将待喷涂的铝合金型材进行去油、除锈等表面处理,确保表面干净平整;(2)进行阳极氧化处理,增加型材表面的耐腐蚀性能。
3.涂装准备(1)根据需要选择适当的颜料和稀释剂,并按照比例混合均匀;(2)根据喷涂需求和型材规格,调整喷枪的喷嘴尺寸和压力。
4.喷涂操作(1)将准备好的颜料倒入喷涂设备,并调整喷涂机的压力和流量;(2)将型材放置在喷涂设备位置,确保喷涂面朝上;(3)根据喷涂需要,进行单层或多层涂装,确保涂层均匀;(4)进行涂层固化,可采用自然干燥或辅助加热方式。
5.检测和质量控制(1)对喷涂的型材进行目测检查,确保涂层无明显缺陷;(2)进行涂层的硬度测试、粘度测试等必要的检测,确保涂层质量符合要求。
6.清洗和维护(1)对喷涂设备进行清洗,清除残留的颜料和稀释剂;(2)定期对喷涂设备进行维护保养,保持其正常工作状态。
三、安全注意事项1.操作人员必须佩戴防护服、手套、眼镜和口罩等个人防护装备;2.喷涂区域必须通风良好,避免喷涂过程中产生有害气体的积聚;3.喷涂设备必须密封良好,避免颜料和稀释剂溅出或泄漏;4.喷涂工作必须远离火源,并遵守防火措施;5.喷涂设备必须定期检查和保养,确保其正常工作。
四、工艺优点1.能够提高铝合金型材的表面质量,增加其观感和美观度;2.喷涂涂层能够提供一定的防腐蚀性能,延长型材的使用寿命;3.工艺操作简单,喷涂效率高,适用于大批量生产。
五、工艺不足1.费用较高,包括喷涂设备和喷涂材料的投入;2.涂层厚度较薄,抗磨损性能相对较差。
总结:通过对铝合金型材立式喷涂工艺操作规程的描述,可以看出该工艺对于提高铝合金型材的表面质量和防腐蚀性能具有一定的优势。
氟碳喷涂工艺规程1

氟碳喷涂工艺规程前处理流程:铝材的去油去污→水洗→碱洗(脱脂)→水洗→酸洗→水洗→铬化→水洗→纯水洗氟碳喷涂流程:喷底漆→面漆→罩光漆→烘烤(180-250℃)→质检多层氟碳喷涂工艺以三次喷涂(简称三喷),喷底面漆、面漆及罩光漆和二次喷涂(底漆、面漆)。
1.前处理的目的:在铝合金型材、板材进行氟碳喷涂前,工件表面要经过去油去污及化学处理,以产生铬化膜,增加涂层和金属表面结合力和防氧化能力,有利于延长漆膜的使用年限。
2.底漆涂层:作为封闭底材的底漆涂层,其作用在于提高涂层抗渗透能力,增强对底材的保护,稳定金属表面层,加强面漆与金属表面的附着力,可以保证面漆涂层的颜色均匀性,漆层厚度一般为5-10微米。
3.面漆涂层:面漆涂层是氟碳喷涂层关键的一层,在于提供铝材所需要的装饰颜色,使铝材外观达到设计要求,并且保护金属表面不受外界环境大气,酸雨,污染的侵蚀,防止紫外线穿透。
大大增强抗老化能力,面漆涂层是氟碳喷涂中最厚的一层漆层,漆层厚度一般为23-30微米。
4.罩光漆涂层:罩光漆涂层也称清漆涂层,主要目的是更有效地增强漆层抗外界侵蚀能力,保护面漆涂层,增加面漆色彩的金属光泽,外观更加颜色鲜明,光彩夺目,涂层厚度一般为5-10微米。
三氟碳喷涂层总厚度一般为40-60微米,特殊需要的可以加厚。
5.固化处理:三氟碳喷涂层一般需要二次固化,铝材进入固化炉处理,固化温度一般在180℃-250℃之间,固化时间为15-25分钟,不同氟碳涂料生产厂家,都会根据自己的涂料,提供最佳的温度和时间。
根据自己经验把三喷时的两次固化也可以改为一次固化。
6.质量检验:质量检验应按AAMA-605.02.90标准。
严格的质量检查才能保证高质量喷涂产品。
粉末静电喷涂工艺规程粉末静电喷涂是将喷涂介质,即粉末固化物,进行充电,并使其附着在已经接地的工件上的一种涂装工艺。
粉末附着在工件上主要是依靠静电吸附的作用,附着了粉末的工件还要经过加热固化流平过程,才能最终形成完整的涂膜,其厚度大约在60---120微米之间。
喷塑操作规程

喷塑操作规程引言概述:喷塑是一种常见的表面涂装技术,广泛应用于各行各业。
为确保喷塑操作的质量和效果,制定一套完善的喷塑操作规程是非常重要的。
本文将详细介绍喷塑操作规程的五个部分,包括准备工作、喷涂准备、喷涂操作、喷涂后处理和安全注意事项。
一、准备工作:1.1 清洁工作区域:在进行喷塑操作之前,必须确保工作区域的干净整洁。
清除工作区域内的灰尘、杂物和其他污染物,以确保喷涂表面的质量。
1.2 准备喷涂设备:检查喷涂设备的工作状态,确保设备正常运行。
清洗和维护喷涂枪、喷嘴和喷涂系统,以保证喷涂操作的顺利进行。
1.3 准备喷涂材料:根据喷涂工艺要求,准备好所需的喷涂材料。
检查材料的质量和数量,确保喷涂过程中不会出现材料不足或质量问题。
二、喷涂准备:2.1 表面处理:在进行喷涂之前,必须对待喷涂表面进行适当的处理。
根据需要,可以采用除锈、打磨、清洗等方法,确保喷涂表面的平整度和附着力。
2.2 喷涂底漆:在进行喷涂之前,可以先涂刷一层底漆。
底漆可以提高喷涂表面的附着力和耐久性,同时还可以提供更好的颜色效果。
2.3 遮盖保护:在进行喷涂操作之前,应该遮盖和保护不需要喷涂的部分。
使用遮盖胶带、塑料薄膜等材料,确保喷涂只作用于需要喷涂的区域。
三、喷涂操作:3.1 喷涂技术:选择适当的喷涂技术,根据喷涂材料的特性和要求,控制喷涂枪的喷涂角度、距离和速度。
保持喷涂均匀和连续,避免喷涂过厚或过薄。
3.2 喷涂顺序:根据喷涂的工艺要求,确定喷涂的顺序。
通常情况下,先喷涂边角和细节部分,然后再进行整体喷涂。
确保喷涂过程中不会漏喷或重喷。
3.3 喷涂厚度控制:根据喷涂工艺要求,控制喷涂的厚度。
可以使用喷涂厚度测量仪器进行实时监测,确保喷涂厚度符合要求。
四、喷涂后处理:4.1 干燥时间:在喷涂完成后,必须给予足够的干燥时间。
根据喷涂材料的要求,确定干燥时间,并避免在干燥过程中暴露于湿度较高或温度较低的环境中。
4.2 修整和修复:检查喷涂表面的质量,如有需要,可以进行修整和修复。
喷涂安全生产操作规程

喷涂安全生产操作规程喷涂工作是现代工业生产中常见的工艺之一,广泛应用于汽车制造、家具生产、航空航天、建筑装饰等领域。
然而,喷涂工作涉及到涂料的储存、搬运、混合、喷涂等环节,操作不当可能会引发火灾、爆炸、中毒等安全事故。
因此,制定喷涂安全生产操作规程,加强员工的安全意识和操作规范,对于预防事故的发生具有重要意义。
一、喷涂安全生产的基本要求1.1严格遵守国家有关安全生产法律法规,特别是《中华人民共和国安全生产法》、《危险化学品安全管理条例》等法规规定。
1.2喷涂作业前应进行作业风险评估,采取相应的安全防护措施。
1.3遵守喷涂设备的使用和维护规定,确保设备正常运行。
1.4参加过岗前培训及使用个人防护装备的培训,经过合格的考核方可上岗操作。
二、喷涂涂料的储存和搬运2.1储存涂料应在专用的储存区域进行,远离火源和明火。
2.2涂料容器应密封完好,防止涂料的挥发和泄漏。
2.3涂料储存区域应保持干燥、通风良好,并设有防火设施。
2.4涂料搬运时应注意轻放,避免撞击和摩擦,防止涂料容器破损。
三、涂料的混合和准备3.1涂料混合时应穿戴好防护眼镜、口罩、手套等个人防护装备。
3.2喷涂涂料的混合要按照配方和工艺进行,严禁随意调整配比。
3.3使用配比清楚的容器进行涂料的混合和储存。
四、喷涂作业现场的安全措施4.1应在专门的喷涂车间进行喷涂作业,确保通风良好。
4.2喷涂作业区域应设立明显的警示标志,禁止非操作人员进入。
4.3喷涂作业人员应佩戴防尘口罩、防毒面具、防静电服等个人防护装备。
4.4喷枪、喷嘴等喷涂设备要定期检查、维护,确保正常使用。
五、喷涂作业中的安全操作5.1喷涂前应将喷涂区域清理干净,移除易燃物品。
5.2操作人员应熟悉喷涂设备的使用方法,严禁调试和使用不熟悉的设备。
5.3涂料喷枪要妥善清洗,避免堵塞和喷洒不均。
5.4喷涂过程中不得吸烟、使用明火,禁止拆卸设备和更换部件。
5.5喷涂结束后要及时清理喷涂设备,保持清洁。
喷涂规程_流程图

卧式生产喷涂工艺操作规程工艺流程上架→喷涂→固化→卸料→包装→入库1.上架1.1 上架前要佩带干净的棉纱手套,严禁徒手操作,长时间使用或受污染的手套应及时更换。
1.2 上架是半成品的最后自检工作,必须认真严格,对于存在质量问题的型材应挑出,尽量避免不合格的型材上架生产,对于铬化后起粉的型材绝对不允许上架。
1.3 挂具上架前要大磨处理,每挂一种型号,要选用合适的挂具,挂同一长度的型号要成一直线,并要检查所挂工件是否符合工艺要求,特别是工件装饰面是否正确。
2. 喷粉目的是提高铝材的耐腐蚀性,以达到用户要求和装饰效果。
2.1 粉末准备2.1.1 检查喷涂设备是否正常运转,接地是否良好,如出现设备问题应及时通知维修人员维修,流气桶,粉管,喷枪,喷房回收系统是否干净后才可投入新粉,不干净的要彻底清理,以保证设备的干净而不出现混色。
2.1.2按生产指定的色号领取粉末,根据粉末固化要求,工件厚簿等情况来调节固化温度及链条速度。
2.1.3同一订单欠数,应尽可能使用同一批号的粉末,用完后方可使用另一批号的粉末。
2.1.4为了减少粉末库存时间,必须先进先用(如;粉仓同一种粉末共近三次,那么领用的顺序为第一批,第二批,第三批)。
2.1.5加粉时一定要检查粉末是否有混色,受潮,结块等情况,经核实后方可加入粉箱。
2.1.6要严格控制回收粉的添加比例,针对生产细料多添加,大料少添加的方法,当全是回收粉时,特别要注意涂层出现色差现象,保证生产的产品符合标准。
2.2 喷涂2.2.1 严格按《喷涂设备操作规程》进行操作,根据不同的工件调节粉量及喷枪与工件的距离,保证喷涂质量,避免吐粉,出粉不均匀等情况出现。
2.2.2在喷粉出口如有吐粉,色差,混色,粉不全等现象,应及时减法不合格的工件拿下,以免进入固化炉固化。
2.2.3要严格控制涂层厚度,避免膜厚不够造成返工或膜厚超标报废。
2.2.4要监控固化炉及压缩机空气压力的正常运转(检查压缩空气是否有油,干燥,冷却)。
喷漆安全技术操作规程(3篇)

喷漆安全技术操作规程喷漆是一种常见的涂装工艺,广泛应用于建筑、汽车、家具等行业。
虽然喷漆可以美化和保护物体表面,但是其过程中也存在一定的安全风险。
为了确保员工的安全,建立和遵守喷漆安全技术操作规程是非常重要的。
下面是一份大约____字的喷漆安全技术操作规程,供参考:一、喷漆原则1.1 安全第一在任何情况下,安全都应该是第一位的原则。
在进行喷漆作业之前,必须确保工作场所的安全,并采取适当的措施来防止事故的发生。
1.2 环保守则在喷漆过程中,必须遵守相关的环保法规和标准,使用符合环保要求的涂料和溶剂,并正确处理和处置废液、废弃物。
二、工作准备2.1 工作场所准备2.1.1 选择通风良好的工作场所进行喷漆作业,确保室内空气流通。
2.1.2 清理工作场所,将易燃和易爆物品移除,确保作业空间无火源和明火。
2.1.3 检查喷漆设备和防护设施,确保其正常工作并完好无损。
2.1.4 设置警示标示,明确标明禁止吸烟、明火和其他危险行为。
2.2 个人准备2.2.1 确保个人身体健康,无酒精、药物或其他身体不适情况。
2.2.2 穿戴适当的工作服,包括长袖衬衫、长裤、安全鞋和防护手套。
2.2.3 配戴个人防护设施,如防护眼镜、面具和呼吸器等。
2.2.4 进行喷漆作业前,检查和清洁喷枪、喷嘴等喷漆设备,确保其正常工作。
三、安全操作步骤3.1 确定喷漆方法3.1.1 根据物体的材质、形状和大小等要素,选择合适的喷漆方法,如手持喷枪、气动喷枪或喷漆柱等。
3.1.2 根据涂料的特性和要求,确定适当的喷漆技术,如喷涂、滚涂或喷涂加滚涂等。
3.2 喷漆涂料准备3.2.1 根据涂料的使用说明,将涂料稀释至适宜的浓度。
3.2.2 在进行稀释时,必须使用合适的溶剂,并遵守溶剂的安全使用规定。
3.2.3 将涂料过滤,去除其中的杂质和颗粒,以保证喷涂质量。
3.3 喷漆前准备3.3.1 将欲喷漆物体清洗干净,去除油污、灰尘和其他杂质,以保证涂层附着力和质量。
- 1、下载文档前请自行甄别文档内容的完整性,平台不提供额外的编辑、内容补充、找答案等附加服务。
- 2、"仅部分预览"的文档,不可在线预览部分如存在完整性等问题,可反馈申请退款(可完整预览的文档不适用该条件!)。
- 3、如文档侵犯您的权益,请联系客服反馈,我们会尽快为您处理(人工客服工作时间:9:00-18:30)。
喷涂工艺操作规程粉末静电喷涂工艺流程为:工件前处理→喷粉→固化→检查→成品一、前处理本工序为关键质量控制点,控制好槽液的浓度,确保在工艺范围内。
工件经过前处理除掉表面的油污和灰尘后才能喷涂粉末,同时在工件表面形成一层铬化膜以增强喷粉后的附着力。
前处理后的工件必须完全烘干水分并且充分冷却到35℃以下才能保证喷粉后工件的理化性能和外观质量。
第一步水洗1、材料:水洗2、时间:2-3分钟3、温度:常温备注:该水洗工序是将型材表面的灰尘、铝屑及表面的轻微的赃物清洗掉,减少灰尘、铝屑及轻微油污对脱脂槽的污染,降低脱脂剂的消耗。
第二步脱脂1、材料:AluetchAluetch是为清洗合金而特别配制的一种液体化学品,通常用艺。
它在清洗表面油脂的同时还可清除表面较轻的氧化皮。
Aluetch的研制是为了迎合不需对合金进行深度腐蚀的工艺。
特别适用于对合金进行铬化处理以及喷涂处理之前。
Aluetch含有表面活性剂,因此没有必要进行通常的除油处理。
经Aluetch 处理过的表面可保持铝的原有光泽。
2、开槽:往槽内注入3/4满水,开泵循环,将计量的Aluetch加入脱脂槽,搅拌至完全溶解(约半小时),加水至操作线,槽液即可使用。
3、配槽浓度 3.5%(重量比)4、时间 6分钟——10分钟5、槽液温度:常温6、测试:见使用说Aluetch明书。
7、控制范围:浓度:3~7%。
8、槽液维持:①、按分析结果添加;②、目前按以下经验数据添加:0.7~0.9mm壁厚型材按4.0~4.5kg/吨1.0~1.2mm壁厚型材按3.5~4.0kg/吨1.2~1.4mm壁厚型材按3.0~3.5kg/吨以上为行业经验平均数据,在实际生产过程需要进行经验数据校正(根据槽液分析数据进行校正)当脱脂液内的污物累积至影响脱脂效果时,即使添加脱脂Aluetch效果也不会明显改善,槽液就应排放。
排放周期取决于产量及工件的油污量。
9、安全须知:槽液添加过程需要按照相关操作规程及汉高产品说明书进行操作。
如果出现药品飞溅到身体时需要及时冲洗或医治。
第三步水洗1、材料:来水2、处理时间: 1—2分钟3、温度:常温4、测试:取100毫升溢流漂洗水样,加8滴溴甲酚绿指示剂,用0.1N氢氧化钠滴定至绿色,氢氧化钠耗用的毫升数为酸污染度。
5、控制范围:酸污染度:最好<3ml,不能>5ml。
如污染度超出上述范围,应加大溢流。
如果尽管有足够的溢流,污染度仍超出要求范围,就应检查原因,及时纠正。
6、排放周期:视碱污染而定,要不断溢流。
备注:关于脱脂后水流的溢流量一般为0.5—0.8m³/h,更具体的要根据生产实际和产品带回溶液量的大小来确定(有一个理论公式:水溢流量=工件等带过量X4.7)。
第四步水洗1、材料:水洗2、时间:2~3分钟3、温度:常温第五步无铬转化1、材料:开槽剂Alodine4830/4831 去离子水本产品能够提供一种优良的钝化膜。
此外,钝化处理还提供了:(1)一个干净、无油脂的表面;(2)耐蚀底层;(3)化学惰性表面。
2、开槽:往槽内注3/4满纯水,开泵循环,加入计量的Alodine4830/4831,混合均匀。
3、配槽浓度:1-1.5%4、时间:50—90秒(新配槽期间处理时间不能超出90秒)5、槽液温度:15~25℃6、测试;见说明书7、控制范围:滴定点数:7—11ml pH:2.2—3.28、槽液维持:①、按分析结果添加:对于1m³槽液,每加入1公斤无铬钝化辅剂Alodine4831 和0.5kg的无铬钝化辅剂Alodine4830的混合液可使点数升高0.0011~0.0013左右(此数据作为参考,浓度需要按分析的点数控制);②、目前按以下经验数据添加:0.7~0.9mm壁厚型材按1.8~2.0kg/吨1.0~1.2mm壁厚型材按1.5~1.6kg/吨1.2~1.4mm壁厚型材按1.2~1.4kg/吨以上为行业经验平均数据,在实际生产过程需要进行经验数据校正(根据槽液分析数据进行校正)③、正常情况下无铬钝化剂的添加按Alodine4830: Alodine4831=1:2的比例进行添加;④、当槽液的点数控制在上限时,pH值也在上限时,需要采用5%的稀HNO3溶液调整其槽液PH值;⑤、当槽液的点数控制在下限时,pH值也在上限时,需要采用添加Alodine4830/4831调整槽液;9、安全须知:槽液添加过程需要按照相关安全操作规程及汉高产品说明书进行操作。
如果出现药品飞溅到身体时需要及时冲洗或医治。
第六步水洗1、材料:水洗2、时间:2~3分钟3、温度:常温第七步水洗1、材料:去离子水,使用去离子水对无铬钝化膜的耐腐蚀和提高油漆附着力有很大帮助。
2、时间2~3分钟3、温度:常温4、排放周期;视污染度而定,要不断溢流5、PH:>5.56、电导率﹤30μS/cm第八步烘干1、型材经过无铬钝化处理后,将型材表面的水滴干,然后再基材不超过100℃的烘炉中进行烘干10分钟,使其表面的干燥。
2、配槽程序1)原铬化槽及后面水洗槽的清洗转化槽和其后的水洗槽要用15%的NaOH循环清洗12个小时,有加热条件的槽体最好加热至50℃。
加入0.1—1.0%的30%的双氧水能加速清洗。
然后排放清洗液,用自来水进行清洗,清除槽子里的残留淤渣。
加入自来水,用硫酸调pH为4并继续循环清洗,循环清洗中继续用硫酸保持pH为4,6小时后再排掉清洗液。
清除淤渣。
检查喷淋管路和槽体,如角落处有任何的残留黏附淤渣,也要用机械方法将其除掉。
进一步的程序要根据客户方面的条件来决定:a)用纯水充满槽体并循环,然后排放掉并再用纯水充满,循环清洗并检测其电导率,如果电导率小于30μS/cm,即可用Alodine4830/4831进行配槽。
若电导率大于30μS/cm,则必须继续清洗。
b)将离子交换器与转化槽连通是可行的,槽里的自来水循环流经离子交换器,直到电导率小于30μS/CM即可开槽。
2)新槽及水洗槽清洗,使用自来水清洗槽体清洗,再使用纯水清洗槽体3、槽液污染管理Fe:即使是在低浓度下,铁离子也会与聚合物絮凝,该凝聚物会沉降到工件上。
因此,生产线上应排除一切铁的来源。
铁的最大浓度为10mg/l。
PO4:磷酸盐会抑制转化膜生成,当使用酸性清洗剂时,推荐使用不含磷酸根的清洗剂。
磷酸根的最大浓度为100mg/l。
Cr:铬会抑制转化膜的生成。
铬的最大浓度为1mg/l。
4、废水处理1)沉淀/絮凝:水洗水:用石灰浆将水洗水中和至PH值为8.5或9.5,可达到如下结果:PH COD[mg/l] TOC[mg/l] Ti[mg/l] Al[mg/l] Mg[mg/l] F[mg/l]8.5 <7 <3 <0.1 <1 <6 <359.5 <6 <4 <0.1 <5 <5 <202)Alodine4830/4831槽液:用石灰浆将Alodine4830/4831槽液中和至pH值为8.5或9.5,再加入P3-ferrocryl8721或8701絮凝剂,可达到如下结果:PH COD[mg/l] TOC[mg/l] Ti[mg/l] Al[mg/l] Mg[mg/l] F[mg/l]8.5 <50 n.b. 0.1 <1 <15 <309.5 <50 n.b. 0.1 <3 <10 <15检测沉淀物,以尽可能找出适当的排放方法。
按DIN 38414第4段制备的洗出液。
氟的浓度可以完全满足Ⅱ类垃圾要求。
因为燃烧可减少干燥的固体物,所以沉淀淤渣必须采用焚烧的排放方法(德国法规)。
3)蒸发用NaOH中和至pH为7,TOC将会降至<10mg/l,重金属的量也相应减少。
蒸馏物可再生作为水洗水或开槽用水。
残留物约为5%,可溶于水。
备注:1、喷涂型材前处理工艺的除油工序是前处理的重中之重,要求型材表面达到完全除油的效果,经水洗后型材表面的水膜完全不破裂(由于新配槽槽液中槽液活性较大,其工艺参数可以控制下限,但随着生产量的增加其工艺参数逐步提升);2、除油后需要充分清洗,以保证以清洁的型材进入无铬钝化槽中处理(最好使用一道纯水清洗);3、无铬钝化工艺参数常规控制PH、点数即可,但必须严格控制其工艺参数(无铬钝化槽属于新配槽,其槽液活性较大前期的参数需要控制在下限,随着生产增加工艺参数需要逐步提升到控制范围)4、型材经无铬钝化处理后,斜看铝材表面有一层五彩色的膜层,正看型材表面有一层薄薄的透明树脂层的感觉(经过除油的型材经无铬钝化处理后表面呈白色,经过除油的型材没有进行无铬钝化处理的表面为青色)二、喷粉本工序为特殊工序,根据不同截面型材,随时调整枪距、进粉量、上粉的均匀性。
1、粉末静电喷涂的基本原理工件通过输送链进入喷粉房的喷枪位臵准备喷涂作业。
静电发生器通过喷枪枪口的电极针向工件方向的空间释放高压静电(负极),该高压静电使从喷枪口喷出的粉末和压缩空气的混合物以及电极周围空气电离(带负电荷)。
工件经过挂具通过输送链接地(接地极),这样就在喷枪和工件之间形成一个电场,当粉末在电场力和压缩空气压力的双重推动下到达工件表面,依靠静电吸引在工件表面形成一层均匀的涂层。
2、粉末静电喷涂的基本原料粉末涂料。
它的主要成分是环氧树脂、聚酯树脂、固化剂、颜料、填料、各种助剂(例如流平剂、防潮剂、边角改性剂等).粉末加热固化后在工件表面形成所需涂层。
辅助材料是压缩空气,要求清洁干燥、无油无水[含水量小于1.3g/m3、含油量小于1.0×10-5%(质量分数)]3、粉末静电喷涂的加工工艺1)静电高压60-90kV。
电压过高容易造成粉末反弹和边缘麻点;电压过低上粉率低。
2)静电电流10~20μA。
电流过高容易产生放电击穿粉末涂层;电流过低上粉率低3)流速压力0.30-0.55MPa。
流速压力越高则粉末的沉积速度越快,有利于快速获得预定厚度的涂层,但过高就会增加粉末用量和喷枪的磨损速度。
4)雾化压力0.30~0.45MPa。
适当增大雾化压力能够保持粉末涂层的厚度均匀,但过高会使送粉部件快速磨损。
适当降低雾化压力能够提高粉末的覆盖能力,但过低容易使送粉部件堵塞。
5)清枪压力0.5MPa。
清枪压力过高会加速枪头磨损,过低容易造成枪头堵塞。
6)供粉桶流化压力0.04~0.10MPa。
供粉桶流化压力过高会降低粉末密度使生产效率下降,过低容易出现供粉不足或者粉末结团。
7)喷枪口至工件的距离150~300mm。
喷枪口至工件的距离过近容易产生放电击穿粉末涂层,过远会增加粉末用量和降低生产效率。
8)输送链速度4.5~5.5m/min。
输送链速度过快会引起粉末涂层厚度不够、沟槽根处易漏底,过慢则降低生产效率。