热镀锌盐雾腐蚀的机理..
盐雾试验标准

盐雾试验标准对灯饰产品表面防腐能力的判定分析一、概论灯饰产品有一些材料的耐腐蚀性较差,尤其是室外灯具的工作环境比较差,灯具的装饰性使得其表面要求极其重要。
需要采用一定防腐保护措施才能满足顾客对产品质量的需要。
因此对灯具产品及其材料的耐大气和环境气候的抗腐蚀性试验或模拟试验成了是本行业关心的问题。
我在这方面作了一些工作和研究,在此将盐雾试验的方法或标准对灯装饰产品表面防腐蚀能力的判断分析作个总结,以供设计选材和表面防护处理作参考。
二、腐蚀机理灯饰产品的工作环境为大气和室内环境,条件恶劣的在海洋气候或海底。
大气腐蚀分干大气腐蚀;潮大气腐蚀;湿大气腐蚀三类。
1,大气腐蚀的特点大气腐蚀的特点是金属表面处于薄层电解液下的腐蚀过程,其腐蚀机理符合电化学腐蚀规律:当金属表面形成连续的电解液薄层时,大气腐蚀的阴极过程为:O2+2H2O+4e→4OH-阳极过程为:Me- ne→Me n+ ;当Fe、Zn全部浸入还原性酸液:阴极为氢去极化;在城市污染大气形成的酸性水膜下:阴极为氧去极化腐蚀.在薄层液膜下:氧易达到金属表面生成氧化膜,阳极钝态,阳极极化;液膜增厚(湿大气)氧达到金属表面要有个扩散过程,因此腐蚀受控减缓。
锈蚀机理:大气腐蚀之锈层处于潮湿条件下,锈层起强氧化剂作用,锈层内阳极发生在金属的Fe3O4界面上:Fe-2e→Fe2+;阴极发生在Fe3O4和FeOOH界面上:6FeOOH+2e→2Fe3O4+2H2O+2OH-,锈层参与了阴极过程。
在工业大气下,SO2、NO2、H2S和NH3等都增加大气腐蚀作用。
当湿度大于70%时,水膜形成,发生电化学腐蚀,腐蚀速度急剧增加;当湿度过小于70%湿度时,二氧化硫的电化学腐蚀速度很小。
尤其是铁、锌、镉、镍不耐硫酸的金属,在大气中极容易腐蚀。
一般认为SO2的腐蚀机理是硫酸盐穴自催化过程。
一旦锈层生成硫酸盐,锈层便无保护能力。
所以碳钢在室外大气条件下必须进行保护,方法有防锈漆、镀Zn、AI等或加入耐大气腐蚀之合金元素,如Cu、P等使锈层具有很好的保护作用。
电镀锌、热浸镀锌与热喷锌的原理与应用范围区别
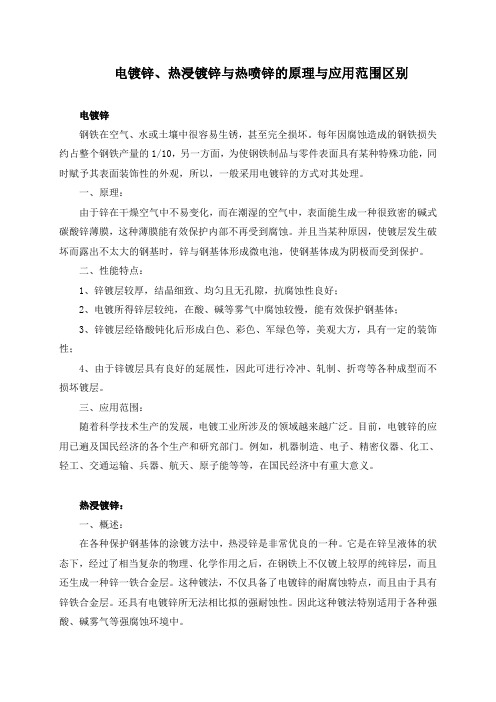
电镀锌、热浸镀锌与热喷锌的原理与应用范围区别电镀锌钢铁在空气、水或土壤中很容易生锈,甚至完全损坏。
每年因腐蚀造成的钢铁损失约占整个钢铁产量的1/10,另一方面,为使钢铁制品与零件表面具有某种特殊功能,同时赋予其表面装饰性的外观,所以,一般采用电镀锌的方式对其处理。
一、原理:由于锌在干燥空气中不易变化,而在潮湿的空气中,表面能生成一种很致密的碱式碳酸锌薄膜,这种薄膜能有效保护内部不再受到腐蚀。
并且当某种原因,使镀层发生破坏而露出不太大的钢基时,锌与钢基体形成微电池,使钢基体成为阴极而受到保护。
二、性能特点:1、锌镀层较厚,结晶细致、均匀且无孔隙,抗腐蚀性良好;2、电镀所得锌层较纯,在酸、碱等雾气中腐蚀较慢,能有效保护钢基体;3、锌镀层经铬酸钝化后形成白色、彩色、军绿色等,美观大方,具有一定的装饰性;4、由于锌镀层具有良好的延展性,因此可进行冷冲、轧制、折弯等各种成型而不损坏镀层。
三、应用范围:随着科学技术生产的发展,电镀工业所涉及的领域越来越广泛。
目前,电镀锌的应用已遍及国民经济的各个生产和研究部门。
例如,机器制造、电子、精密仪器、化工、轻工、交通运输、兵器、航天、原子能等等,在国民经济中有重大意义。
热浸镀锌:一、概述:在各种保护钢基体的涂镀方法中,热浸锌是非常优良的一种。
它是在锌呈液体的状态下,经过了相当复杂的物理、化学作用之后,在钢铁上不仅镀上较厚的纯锌层,而且还生成一种锌一铁合金层。
这种镀法,不仅具备了电镀锌的耐腐蚀特点,而且由于具有锌铁合金层。
还具有电镀锌所无法相比拟的强耐蚀性。
因此这种镀法特别适用于各种强酸、碱雾气等强腐蚀环境中。
二、原理:热镀锌层是锌在高温液态下,分三个步骤形成的:1、铁基表面被锌液溶解形成锌—铁合金相层;2、合金层中的锌离子进一步向基体扩散形成锌铁互溶层;3、合金层表面包络着锌层。
三、性能特点:(1)具有较厚的致密的纯锌层覆盖在钢铁表面上,它可以避免钢铁基体与任何的腐蚀溶液的接触,保护钢基体免受腐蚀。
211175758_汽车整车路试镀锌卡钳生锈及盐雾问题的解决方案

图 3 卡钳电镀酸锌的工艺流程
这种腐蚀长时间作用下,局部电镀锌层腐蚀殆尽,然后就会 腐蚀局部铁基材,形成铁氧化物,腐蚀面积也越来越大。所以最 终卡钳表面会呈现出大面积铁基材生锈的状态。陈敏娟等人在论 文《锌及锌合金镀层盐雾试验腐蚀形态研究》中也阐述了类似的 镀锌层生锈的观点 [3]。 3.2 镀锌层在高湿度以及受到磕碰划伤后的腐蚀机理分析
图 1 路试车辆生锈制动卡钳
图 2 中性盐雾试验后卡钳状态
和环境状态等都有影响。笔者试着运用 5M1E 分析方法,对卡钳 生锈因素进行分析确认。5M1E 是指引起产品质量波动的六大主 要因素人、机、料、法、环、测的简称 [2]。 2.1 操作人员的技术水平
目前外协厂的相关技术人员工作年限基本在 10 年以上,实 际操作水平达到技能的相关要求,工作经验丰富,现场解决问题
032 Copyright©博看网. All Rights Reserved.
AUTO DRIVING & SERVICE 2023 . 03
学术 | 的电镀零件目前未出现卡钳生锈问 题。因此,可以排除技术操作人员技能水平导致的卡钳质量问题。 2.2 电镀线体及周边设备
此批问题所装配车辆已在终端用户中,经过售后调查,未出 现卡钳生锈问题。经分析,终端用户车辆一般为车库或露天状态, 而且很少长时间出现在高盐雾、高低温的沿海环境中行驶,故较 少出现相关问题。所以判定,在高盐雾、高低温的环境长时间测试, 也是导致该车制动卡钳出现腐蚀问题的原因。 4.2 通过特殊包装防护防磕碰及受潮腐蚀
镀锌钢板测试技术:盐雾试验

镀锌钢板测试技术:盐雾试验盐雾试验腐蚀是材料或其性能在环境的作用下引起的破坏或变质。
大多数的腐蚀发生在大气环境中,大气中含有氧气、湿度、温度变化和污染物等腐蚀成分和腐蚀因素。
盐雾腐蚀就是一种常见和最有破坏性的大气腐蚀。
盐雾对金属材料表面的腐蚀是由于含有的氯离子穿透金属表面的氧化层和防护层与内部金属发生电化学反应引起的。
同时,氯离子含有一定的水合能,易被吸附在金属表面的孔隙、裂缝排挤并取代氧化层中的氧,把不溶性的氧化物变成可溶性的氯化物,使钝化态表面变成活泼表面。
盐雾试验是一种主要利用盐雾试验设备所创造的人工模拟盐雾环境条件来考核产品或金属材料耐腐蚀性能的环境试验。
它分为二大类,一类为天然环境暴露试验,另一类为人工加速模拟盐雾环境试验。
人工模拟盐雾环境试验是利用一种具有一定容积空间的试验设备——盐雾试验箱(如图),在其容积空间内用人工的方法,造成盐雾环境来对产品的耐盐雾腐蚀性能质量进行考核。
它与天然环境相比,其盐雾环境的氯化物的盐浓度,可以是一般天然环境盐雾含量的几倍或几十倍,使腐蚀速度大大提高,对产品进行盐雾试验,得出结果的时间也大大缩短。
如在天然暴露环境下对某产品样品进行试验,待其腐蚀可能要1年,而在人工模拟盐雾环境条件下试验,只要24小时,即可得到相似的结果。
实验室模拟盐雾可以分为四类:⑴中性盐雾试验(NSS试验)是出现最早目前应用领域最广的一种加速腐蚀试验方法。
它采用5%的氯化钠盐水溶液,溶液PH值调在中性范围(6.5~7.2)作为喷雾用的溶液。
试验温度均取35℃,要求盐雾的沉降率在1~2ml/80cm/h。
⑵醋酸盐雾试验(ASS试验)是在中性盐雾试验的基础上发展起来的。
它是在5%氯化钠溶液中加入一些冰醋酸,使溶液的PH值降为3左右,溶液变成酸性,最后形成的盐雾也由中性盐雾变成酸性。
它的腐蚀速度要比NSS试验快3倍左右。
⑶铜盐加速醋酸盐雾试验(CASS试验)是国外新近发展起来的一种快速盐雾腐蚀试验,试验温度为50℃,盐溶液中加入少量铜盐-氯化铜,强烈诱发腐蚀。
热镀锌盐雾试验
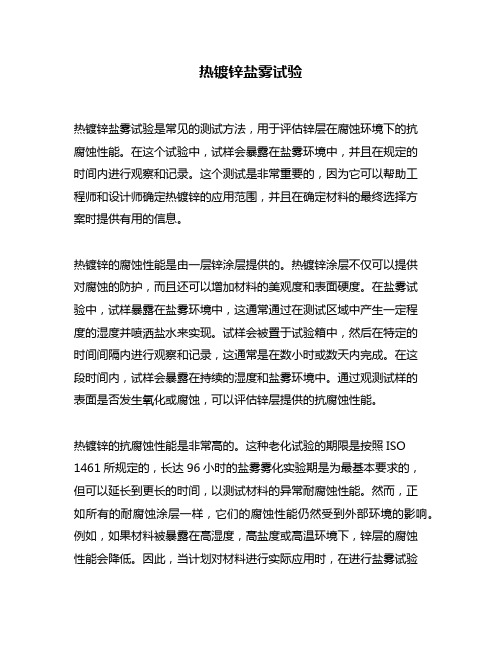
热镀锌盐雾试验热镀锌盐雾试验是常见的测试方法,用于评估锌层在腐蚀环境下的抗腐蚀性能。
在这个试验中,试样会暴露在盐雾环境中,并且在规定的时间内进行观察和记录。
这个测试是非常重要的,因为它可以帮助工程师和设计师确定热镀锌的应用范围,并且在确定材料的最终选择方案时提供有用的信息。
热镀锌的腐蚀性能是由一层锌涂层提供的。
热镀锌涂层不仅可以提供对腐蚀的防护,而且还可以增加材料的美观度和表面硬度。
在盐雾试验中,试样暴露在盐雾环境中,这通常通过在测试区域中产生一定程度的湿度并喷洒盐水来实现。
试样会被置于试验箱中,然后在特定的时间间隔内进行观察和记录,这通常是在数小时或数天内完成。
在这段时间内,试样会暴露在持续的湿度和盐雾环境中。
通过观测试样的表面是否发生氧化或腐蚀,可以评估锌层提供的抗腐蚀性能。
热镀锌的抗腐蚀性能是非常高的。
这种老化试验的期限是按照ISO 1461所规定的,长达96小时的盐雾雾化实验期是为最基本要求的,但可以延长到更长的时间,以测试材料的异常耐腐蚀性能。
然而,正如所有的耐腐蚀涂层一样,它们的腐蚀性能仍然受到外部环境的影响。
例如,如果材料被暴露在高湿度,高盐度或高温环境下,锌层的腐蚀性能会降低。
因此,当计划对材料进行实际应用时,在进行盐雾试验时应该考虑多种因素和环境因素。
总之,热镀锌盐雾试验是一种有效的测试方法,可以帮助工程师和设计师确定材料的最终选择方案。
这个测试不仅可以评估热镀锌涂层的耐腐蚀性能,而且可以提供有用的数据,并为计划进行实际应用的过程提供必要的信息。
但我们需要注意,外部环境的多种因素和条件会影响材料表面的腐蚀性能,因此需要综合多种因素考虑材料的实际应用情况。
热镀锌厚度和盐雾时间对应_概述说明以及解释

热镀锌厚度和盐雾时间对应概述说明以及解释1. 引言1.1 概述热镀锌作为一种常用的防腐蚀技术,在许多工业领域都有广泛应用。
热镀锌处理可以有效地增加金属表面的耐腐蚀性能,并延长其使用寿命。
然而,热镀锌的厚度与材料的耐腐蚀性能之间存在一定的关联,特别是在充满盐分和潮湿环境中。
因此,我们有必要了解热镀锌厚度与盐雾时间之间的对应关系,以更好地评估材料在恶劣环境中的稳定性。
1.2 文章结构本文将按照以下结构组织内容:首先,在第二部分将介绍热镀锌工艺,并探讨热镀锌厚度与耐腐蚀性能之间的关联。
随后,在第三部分将详细介绍我们进行的实验研究,包括实验设计、材料准备以及实验过程。
在第四部分,我们将解释和讨论实验结果,并探讨可能影响热镀锌厚度与盐雾时间对应关系的因素。
最后,在第五部分,我们将总结结果并提出对未来进一步研究方向的建议和展望。
1.3 目的本文旨在通过实验研究,探讨热镀锌厚度与盐雾时间之间的对应关系,并解释其中的机理。
通过了解这一关联性,我们可以更好地评估热镀锌材料在恶劣环境中的耐久性,并为相关工业应用提供指导和建议。
同时,本文还将提供一些可能存在的误差和限制条件分析,以及对未来进一步研究方向的展望。
2. 热镀锌厚度和盐雾时间的相关性:2.1 热镀锌工艺简介:热镀锌是一种常用的金属防腐方法,通过将基材浸入熔融的锌中,形成一层锌铁合金覆盖在基材表面。
这种覆盖层能够有效地保护基材免受腐蚀和氧化。
2.2 热镀锌厚度与耐腐蚀性能的关系:热镀锌厚度是决定其耐腐蚀性能的重要因素之一。
通常情况下,较厚的热镀锌层会提供更好的保护效果,并能延长基材的寿命。
这是因为厚度较大的热镀锌层具有更高的耐侵蚀和阻挡湿气渗透的能力。
2.3 盐雾测试方法简介:盐雾测试是评估金属表面耐腐蚀性能常用的实验方法之一。
该方法通过在特定条件下制造含有各种浓度盐水喷雾环境,模拟真实环境下金属遭受海洋或工业大气环境腐蚀的情况。
在盐雾测试中,将样品暴露在盐雾环境中一定的时间,然后观察和记录其表面的腐蚀情况。
盐雾试验原理及应用_2022年学习资料

阳极反应放出的电子被阴极反应所吸收,因盐水膜中已存有钠离子和氯离-子,阴极产物是氢氧化钠,阳极产物是氯化铜 两者都能大量溶入水中,因此腐-蚀的以不断进行.-铜锈-氯化钠溶液形成水膜-氧化层阴极-铜在盐雾中的腐蚀-1
3.5案例二:-除了氧化物膜与金属接触可产生腐蚀外,还可能以其它方式产生腐-蚀,如不同金属电接触,金属表面 电化学不均匀等等.-不同金属接触,势必会产生一个电位差,当氯化钠微粒与水份所形成-的盐雾做为电解溶液将这两 不同金属接连起来时,即形成了一个腐-蚀电池,-镀锌板的腐蚀过程:-Zn→Zn2++2e阳极反应-Fe2++ e→Fe阴极反应-11
3.6总结:-金属在盐雾中的腐蚀过程,我们不难看到,整个腐蚀过程是在电解溶液中产-生的电化学腐蚀过程,由阴 反应和阳极反应两部分组成!-1.阳极反应中,作为阳极的金属表面的电子离开金属进入溶液,使阳-极的金属受到腐 .M-代表某一金属-MM+ne-2.阴极反应中,是接收来自阳极的电子,有金属还原或氢等元素-的析出,-氢析 :2H++2e-H,↑-氧还原(酸性O,+4H++4e→2HO-氧还原(碱性)02+2H,0+4e→40H 金属离子还原Fe3++e+Fe2+-金属沉淀Cu2++2e→Cu-13
3.3氯化钠盐雾腐蚀机理。-氯化钠是一种强的电介质,极易吸潮,在水中完全电离,-电解后成为氯离子和钠离子, 电解方程为-NaCl Na++Cl-盐雾对金属材料表面的腐蚀,是由于氯离子所造成的,它有强-烈的穿透本领。 容易穿透金属表面的氧化层和防护层与内部-金属发生电化学反应,引起腐蚀。-7
当盐雾沉降到金属表面时,由于其含有水气作用,首先形成一层-盐水膜将整个金属表面罩住,这时,金属面相当于浸在 有氧的氯化-钠溶液中,金属的表面会构成原电池的二个极,产生腐蚀。-铜块-含氧空气-阴极区-液面-阳极区-P
镀锌盐雾试验时间和自然腐蚀时间标准
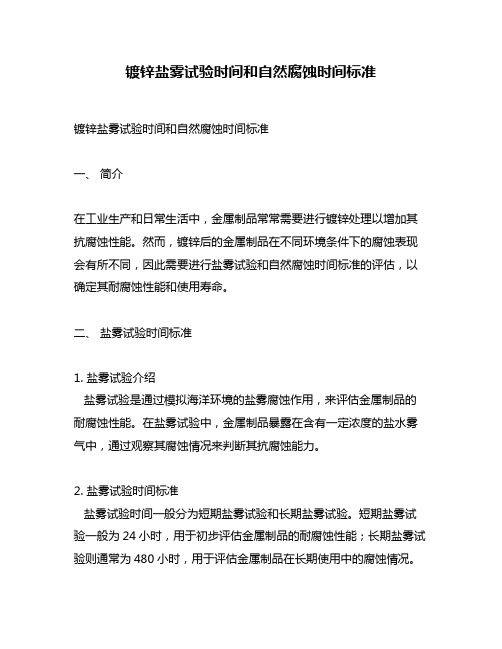
镀锌盐雾试验时间和自然腐蚀时间标准镀锌盐雾试验时间和自然腐蚀时间标准一、简介在工业生产和日常生活中,金属制品常常需要进行镀锌处理以增加其抗腐蚀性能。
然而,镀锌后的金属制品在不同环境条件下的腐蚀表现会有所不同,因此需要进行盐雾试验和自然腐蚀时间标准的评估,以确定其耐腐蚀性能和使用寿命。
二、盐雾试验时间标准1. 盐雾试验介绍盐雾试验是通过模拟海洋环境的盐雾腐蚀作用,来评估金属制品的耐腐蚀性能。
在盐雾试验中,金属制品暴露在含有一定浓度的盐水雾气中,通过观察其腐蚀情况来判断其抗腐蚀能力。
2. 盐雾试验时间标准盐雾试验时间一般分为短期盐雾试验和长期盐雾试验。
短期盐雾试验一般为24小时,用于初步评估金属制品的耐腐蚀性能;长期盐雾试验则通常为480小时,用于评估金属制品在长期使用中的腐蚀情况。
3. 盐雾试验的意义盐雾试验时间标准的确定对于制定金属制品的质量标准和使用要求具有重要意义。
通过对盐雾试验时间的合理设定,可以更准确地评估金属制品的耐腐蚀能力,从而保证其在不同环境条件下的可靠性和持久性。
三、自然腐蚀时间标准1. 自然腐蚀介绍自然腐蚀是金属制品在自然环境中受到大气、水、土壤等介质的腐蚀作用,是其长期使用过程中不可避免的问题。
对金属制品进行自然腐蚀时间的评估,可以有效地预测其使用寿命和性能变化。
2. 自然腐蚀时间标准自然腐蚀时间标准一般以年为单位进行评估,根据金属材料的种类、加工工艺和环境条件的不同,自然腐蚀时间标准也有所差异。
一般而言,常见的自然腐蚀时间标准为5年、10年和20年。
3. 自然腐蚀时间的意义自然腐蚀时间标准的确定对于制定金属制品的设计寿命和维护周期具有重要意义。
通过对自然腐蚀时间的评估,可以更好地了解金属制品在不同环境条件下的腐蚀速度和变化规律,为其设计、生产和使用提供科学依据。
四、个人观点和理解盐雾试验时间和自然腐蚀时间标准的确定对于金属制品的质量和可靠性具有重要意义。
在实际生产和使用过程中,应结合金属材料的特性、工艺条件和使用环境,合理确定盐雾试验时间和自然腐蚀时间标准,以保证金属制品的耐腐蚀性能和使用寿命。
防盐雾
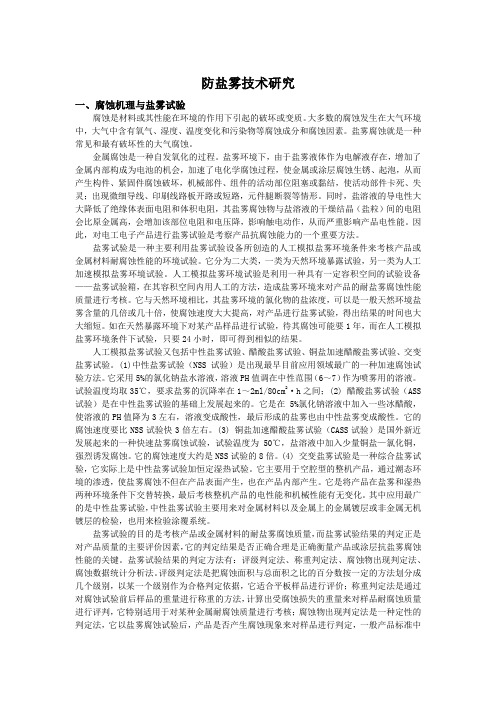
防盐雾技术研究一、腐蚀机理与盐雾试验腐蚀是材料或其性能在环境的作用下引起的破坏或变质。
大多数的腐蚀发生在大气环境中,大气中含有氧气、湿度、温度变化和污染物等腐蚀成分和腐蚀因素。
盐雾腐蚀就是一种常见和最有破坏性的大气腐蚀。
金属腐蚀是一种自发氧化的过程。
盐雾环境下,由于盐雾液体作为电解液存在,增加了金属内部构成为电池的机会,加速了电化学腐蚀过程,使金属或涂层腐蚀生锈、起泡,从而产生构件、紧固件腐蚀破坏,机械部件、组件的活动部位阻塞或黏结,使活动部件卡死、失灵;出现微细导线、印刷线路板开路或短路,元件腿断裂等情形。
同时,盐溶液的导电性大大降低了绝缘体表面电阻和体积电阻,其盐雾腐蚀物与盐溶液的干燥结晶(盐粒)间的电阻会比原金属高,会增加该部位电阻和电压降,影响触电动作,从而严重影响产品电性能。
因此,对电工电子产品进行盐雾试验是考察产品抗腐蚀能力的一个重要方法。
盐雾试验是一种主要利用盐雾试验设备所创造的人工模拟盐雾环境条件来考核产品或金属材料耐腐蚀性能的环境试验。
它分为二大类,一类为天然环境暴露试验,另一类为人工加速模拟盐雾环境试验。
人工模拟盐雾环境试验是利用一种具有一定容积空间的试验设备——盐雾试验箱,在其容积空间内用人工的方法,造成盐雾环境来对产品的耐盐雾腐蚀性能质量进行考核。
它与天然环境相比,其盐雾环境的氯化物的盐浓度,可以是一般天然环境盐雾含量的几倍或几十倍,使腐蚀速度大大提高,对产品进行盐雾试验,得出结果的时间也大大缩短。
如在天然暴露环境下对某产品样品进行试验,待其腐蚀可能要1年,而在人工模拟盐雾环境条件下试验,只要24小时,即可得到相似的结果。
人工模拟盐雾试验又包括中性盐雾试验、醋酸盐雾试验、铜盐加速醋酸盐雾试验、交变盐雾试验。
(1)中性盐雾试验(NSS试验)是出现最早目前应用领域最广的一种加速腐蚀试验方法。
它采用5%的氯化钠盐水溶液,溶液PH值调在中性范围(6~7)作为喷雾用的溶液。
试验温度均取35℃,要求盐雾的沉降率在1~2ml/80cm2·h之间;(2) 醋酸盐雾试验(ASS 试验)是在中性盐雾试验的基础上发展起来的。
热镀锌盐雾腐蚀的机理

随着汽车工业的发展,汽车用热镀锌钢板的国产化程度不断提高,轿车的发展对热镀锌板的质量、品种和规格提出了更高的要求。
热镀锌板由于使用需要,长期以及Cl-等的腐蚀,影响产品质量,暴露于大气中,易于受到大气中潮湿气、SO2、固缩短产品的使用寿命。
在沿海城市及重工业地区,由于同时受到ph值、NO3体颗粒等影响,热镀锌板的腐蚀速率也会加快,对其耐腐蚀性能提出了更高的要求。
热镀锌板在盐雾实验中,表面锌层首先被腐蚀,腐蚀产物比较疏松,呈白色絮状覆盖在钢板表面,称之为“白锈”。
随着盐雾喷淋时间的延长,镀层逐渐被腐蚀殆尽,随后基板开始腐蚀,腐蚀产物为红色,称之为“红锈”。
由此可见,镀层的厚度与组成是决定红锈产生时间,即镀层腐蚀完毕、基板开始腐蚀所需时间的决定因素。
本章通过盐雾腐蚀实验和电化学实验比较稀土含量对镀锌板耐腐蚀性能的影响,并运用XRD分析腐蚀产物,对实际生产提出指导性意见。
1 镀层厚度的测量结果在镀前处理工艺及冷却方式相同的情况下,镀层厚度与热浸镀时间和锌液成分有关。
图4-1所示为采用传统镀锌液成分(Zn-0.177Al)浸镀时间与钢板表面镀层厚度之间的关系。
浸镀时间增加,镀层也逐渐增厚。
当浸镀时间较短(<2min)时,镀层的连续性较差,容易产生漏镀。
浸镀时间超过120s后,镀层已完全覆盖钢板。
把钢板表面划分为9个区域,用测厚仪在每个区域内取10个测量点进行测量,计算平均值作为此区域的平均厚度值,得到镀层厚度曲线(图4-2)。
结合钢板表面宏观形貌来看,传统镀锌液流动性较差,钢板出锌锅后表面锌液向下流动速率较慢,凝固后表面锌层存在波浪状起伏,两侧厚度差较大,厚度明显不均。
由于钢板出锌锅后采用竖直流平冷却的方式,因此靠近钢板底部的7、8、9三个点的平均厚度要高于其他各点。
整体上看,随着浸镀时间的延长,镀层厚度也呈增加的趋势。
图1 镀层平均厚度与浸镀时间的关系(不含稀土)图2 镀层不同区域内厚度曲线图(不含稀土)(a)厚度曲线;(b)测量区域由3.1.2及3.3.1的计算可知,镀锌液中添加稀土元素后,锌液流动性增加,表面张力降低,锌液与基板间的润湿角减小,因而在样板竖直凝固及冷却过程中,锌液不断向下流动,甚至滴落,最终样板表面的粘锌量较少。
热镀锌作用-概述说明以及解释
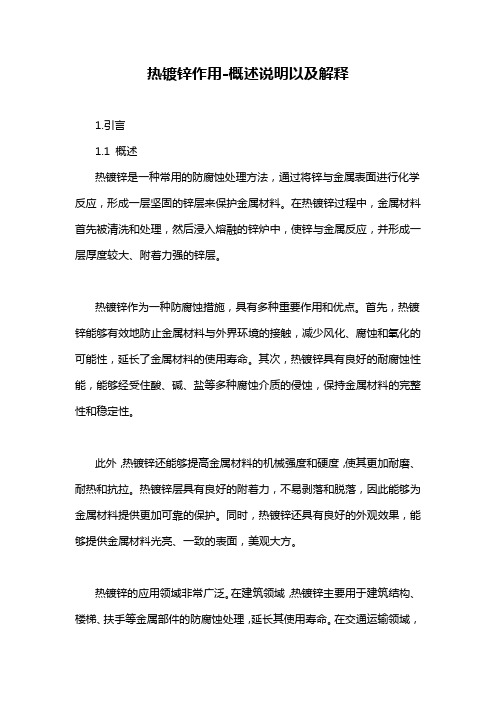
热镀锌作用-概述说明以及解释1.引言1.1 概述热镀锌是一种常用的防腐蚀处理方法,通过将锌与金属表面进行化学反应,形成一层坚固的锌层来保护金属材料。
在热镀锌过程中,金属材料首先被清洗和处理,然后浸入熔融的锌炉中,使锌与金属反应,并形成一层厚度较大、附着力强的锌层。
热镀锌作为一种防腐蚀措施,具有多种重要作用和优点。
首先,热镀锌能够有效地防止金属材料与外界环境的接触,减少风化、腐蚀和氧化的可能性,延长了金属材料的使用寿命。
其次,热镀锌具有良好的耐腐蚀性能,能够经受住酸、碱、盐等多种腐蚀介质的侵蚀,保持金属材料的完整性和稳定性。
此外,热镀锌还能够提高金属材料的机械强度和硬度,使其更加耐磨、耐热和抗拉。
热镀锌层具有良好的附着力,不易剥落和脱落,因此能够为金属材料提供更加可靠的保护。
同时,热镀锌还具有良好的外观效果,能够提供金属材料光亮、一致的表面,美观大方。
热镀锌的应用领域非常广泛。
在建筑领域,热镀锌主要用于建筑结构、楼梯、扶手等金属部件的防腐蚀处理,延长其使用寿命。
在交通运输领域,热镀锌广泛应用于公路护栏、铁路轨道、桥梁等设施的防腐蚀保护,提高其安全性和稳定性。
此外,热镀锌还在电力、化工、冶金等行业广泛应用,为各类金属设备和构件提供可靠的防腐蚀保护。
总之,热镀锌作为一种常用的防腐蚀处理方法,具有重要的作用和优点。
它能够有效保护金属材料不受腐蚀和风化的侵害,延长其使用寿命,并提高其机械性能和外观效果。
未来,随着科技的不断进步,热镀锌技术还将得到进一步发展,提高其防腐蚀效果和处理效率。
因此,进一步研究和应用热镀锌技术具有重要的意义,可以为各个领域的金属材料提供更好的防腐蚀保护。
1.2 文章结构文章结构部分的内容可以如下所示:2. 正文2.1 热镀锌的定义和原理2.2 热镀锌的作用和优点2.3 热镀锌的应用领域在本文中,我们将首先介绍热镀锌的定义和原理。
随后,我们将详细讨论热镀锌的作用和优点,并探讨热镀锌在不同领域的应用。
合金化热镀锌板的腐蚀行为研究
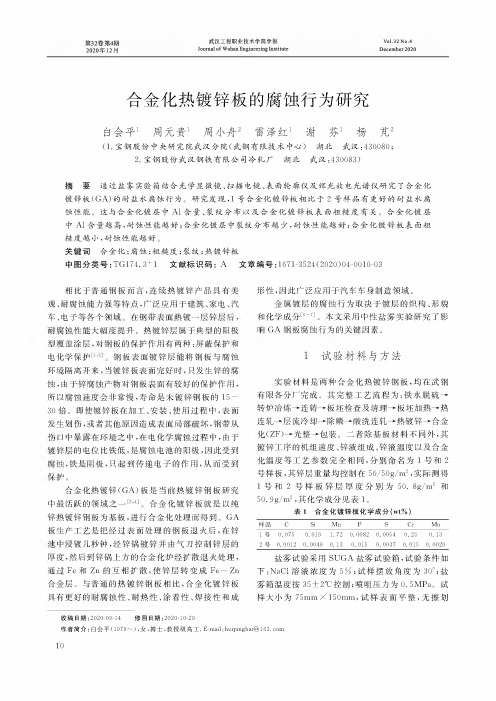
武汉工程职业技术学院学报Journal of Wuhan Engineering InstituteVol.32No.4 December2020第32卷第4期2020年12月合金化热镀锌板的腐蚀行为研究白会平1周元贵1周小舟2雷泽红1谢芬1杨m2(1.宝钢股份中央研究院武汉分院(武钢有限技术中心)湖北武汉"30080;2.宝钢股份武汉钢铁有限公司冷轧厂湖北武汉:430083)摘要通过盐雾实验箱结合光学显微镜、扫描电镜、表面轮廓仪及辉光放电光谱仪研究了合金化镀锌板(GA)的耐盐水腐蚀行为。
研究发现,1号合金化镀锌板相比于2号样品有更好的耐盐水腐蚀性能。
这与合金化镀层中A1含量、裂纹分布以及合金化镀锌板表面粗糙度有关。
合金化镀层中A1含量越高,耐蚀性能越好;合金化镀层中裂纹分布越少,耐蚀性能越好;合金化镀锌板表面粗糙度越小,耐蚀性能越好。
关键词合金化;腐蚀;粗糙度;裂纹;热镀锌板中图分类号:TG174.3+1文献标识码:A文章编号:1671-3524(2020)04-0010-03相比于普通钢板而言,连续热镀锌产品具有美观、耐腐蚀能力强等特点,广泛应用于、家电、汽车、电子等各。
在钢热镀一性能大幅度提升。
热镀锌层属于典型的阳极型覆盖涂层,对钢板的保护作用有两种:屏蔽保护和电化学保护钢板表面镀锌层能将钢板与腐蚀环境隔离开来,当镀锌板表面完好时,只发生锌的腐蚀,由于产物对钢板有较好的保护作用,所以度会非常慢,寿命是钢板的15—30倍。
即使镀锌板在加工、安装、使用过程中,表面发生划伤,或者原因造成,钢带从中暴露之中,在电化学程中,由于的电位比铁低,是腐蚀电池的阳极,因此受到,铁是,只起电子的作用,从而受到保护。
合金化热镀锌(GA)板是当前热镀锌钢板研究中最活跃的领域之一合金化镀锌板就是以纯锌热镀锌钢板为基板,进行合金化处理而得到。
GA 板生产工艺是把经过表面处理的钢板退火后,在锌中浸镀几秒钟,经锌锅气刀控制的厚度,然后到锌锅上方的合金散处理,通过Fe和Zn的互相扩散,使锌层转变成Fe—Zn 合金层。
镀锌钢管腐蚀原因

镀锌钢管腐蚀原因
镀锌钢管腐蚀的主要原因可以归结为以下几个方面:
1.锌层损伤:锌层是镀锌钢管的主要防腐层,如果锌层受损,就会暴露出基材,使得基材容易受到腐蚀。
锌层损伤可能是由于运输、安装过程中的刮擦、磕碰或者机械加工过程中的切削等导致的。
2.锌层不均匀:如果镀锌钢管的锌层厚度不均匀,局部厚度较薄的地方容易发生腐蚀。
这可能是由于镀锌工艺不当、涂锌均匀性差、操作不规范等原因造成的。
3.环境因素:镀锌钢管在潮湿、多雨、多尘、高气湿度等恶劣环境中容易发生腐蚀。
特别是在酸雨、盐雾等腐蚀性气候条件下,镀锌钢管的腐蚀速度会更快。
4.化学因素:例如,如果镀锌钢管暴露在含有酸性或碱性的化学介质中,会导致镀锌层的溶解,从而引发腐蚀。
5.电化学因素:如果镀锌钢管处于电解质溶液中,并且与其他金属接触,可能产生电化学腐蚀。
在这种情况下,锌层将作为阳极受到腐蚀,基材则作为阴极,从而导致锌层腐蚀严重。
6.机械损伤:如果镀锌钢管在使用过程中受到机械冲击或者摩擦,也容易导致锌层的损伤,进而引发腐蚀。
为了减少镀锌钢管的腐蚀,需要采取一系列防护措施,包括选择合适的镀锌工艺、提高锌层的均匀性和厚度、采用合适的防腐涂层、控制环境条件等。
同时,定期检查和维护镀锌钢管的表面状态也是非常重要的。
1 / 1。
热镀锌盐雾试验

热镀锌盐雾试验
热镀锌是一种常见的防腐处理方法,它可以有效地防止金属材料在潮湿环境下的腐蚀。
然而,即使经过热镀锌处理的金属材料也可能会在恶劣的环境下发生腐蚀。
为了测试热镀锌的防腐性能,盐雾试验被广泛应用。
盐雾试验是一种模拟海洋环境的腐蚀试验方法。
在盐雾试验中,将金属样品放置在盐水喷雾室中,通过喷洒盐水来模拟海洋环境中的腐蚀作用。
在试验过程中,可以通过观察样品的腐蚀情况来评估其防腐性能。
对于热镀锌材料来说,盐雾试验是一种非常有效的测试方法。
热镀锌材料在盐雾环境下的腐蚀速度比普通钢材要慢得多,这是因为锌具有良好的防腐性能。
在盐雾试验中,热镀锌材料的腐蚀速度通常比普通钢材要慢得多,这表明热镀锌材料具有更好的防腐性能。
然而,即使经过热镀锌处理的材料也可能会在盐雾环境下发生腐蚀。
这是因为热镀锌层可能会受到损伤,从而暴露出下面的钢材。
如果钢材没有得到适当的防腐处理,它就会在盐雾环境下迅速腐蚀。
因此,在进行盐雾试验时,需要注意以下几点:
1. 样品的表面应该保持干燥和清洁,以避免表面污染对试验结果的影响。
2. 样品的热镀锌层应该均匀且完整,以确保试验结果的准确性。
3. 在试验过程中,应该定期检查样品的腐蚀情况,并记录下来以便后续分析。
盐雾试验是一种非常有效的测试方法,可以用于评估热镀锌材料的防腐性能。
通过合理的试验设计和操作,可以得到准确的试验结果,并为热镀锌材料的应用提供重要的参考依据。
热镀锌工艺流程及原理
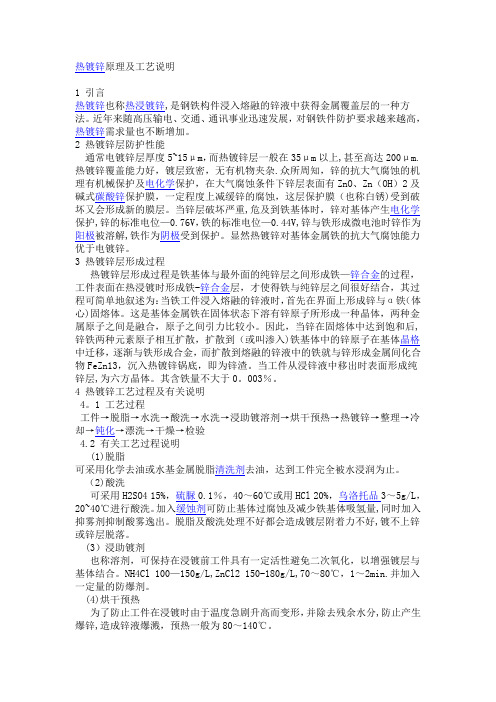
热镀锌原理及工艺说明1 引言热镀锌也称热浸镀锌,是钢铁构件浸入熔融的锌液中获得金属覆盖层的一种方法。
近年来随高压输电、交通、通讯事业迅速发展,对钢铁件防护要求越来越高,热镀锌需求量也不断增加。
2 热镀锌层防护性能通常电镀锌层厚度5~15μm,而热镀锌层一般在35μm以上,甚至高达200μm.热镀锌覆盖能力好,镀层致密,无有机物夹杂.众所周知,锌的抗大气腐蚀的机理有机械保护及电化学保护,在大气腐蚀条件下锌层表面有ZnO、Zn(OH)2及碱式碳酸锌保护膜,一定程度上减缓锌的腐蚀,这层保护膜(也称白锈)受到破坏又会形成新的膜层。
当锌层破坏严重,危及到铁基体时,锌对基体产生电化学保护,锌的标准电位—0.76V,铁的标准电位—0.44V,锌与铁形成微电池时锌作为阳极被溶解,铁作为阴极受到保护。
显然热镀锌对基体金属铁的抗大气腐蚀能力优于电镀锌。
3 热镀锌层形成过程热镀锌层形成过程是铁基体与最外面的纯锌层之间形成铁—锌合金的过程,工件表面在热浸镀时形成铁-锌合金层,才使得铁与纯锌层之间很好结合,其过程可简单地叙述为:当铁工件浸入熔融的锌液时,首先在界面上形成锌与α铁(体心)固熔体。
这是基体金属铁在固体状态下溶有锌原子所形成一种晶体,两种金属原子之间是融合,原子之间引力比较小。
因此,当锌在固熔体中达到饱和后,锌铁两种元素原子相互扩散,扩散到(或叫渗入)铁基体中的锌原子在基体晶格中迁移,逐渐与铁形成合金,而扩散到熔融的锌液中的铁就与锌形成金属间化合物FeZn13,沉入热镀锌锅底,即为锌渣。
当工件从浸锌液中移出时表面形成纯锌层,为六方晶体。
其含铁量不大于0。
003%。
4 热镀锌工艺过程及有关说明4。
1 工艺过程工件→脱脂→水洗→酸洗→水洗→浸助镀溶剂→烘干预热→热镀锌→整理→冷却→钝化→漂洗→干燥→检验4.2 有关工艺过程说明(1)脱脂可采用化学去油或水基金属脱脂清洗剂去油,达到工件完全被水浸润为止。
(2)酸洗可采用H2SO4 15%,硫脲0.1%,40~60℃或用HCl 20%,乌洛托品3~5g/L,20~40℃进行酸洗。
热镀锌板盐雾试验研究

热镀锌板盐雾试验研究董 梅,丰 慧,施国兰(马鞍山钢铁股份公司技术中心,安徽马鞍山243000)摘 要:根据对不同镀层品种、镀层重量和表面处理热镀锌板产品的中性盐雾试验研究,探讨了镀锌板腐蚀的影响因素,并提出提高热镀锌产品耐蚀性能的措施。
关键词:腐蚀;盐雾试验;锌25%铝合金中图分类号:T G 174 文献标识码:A 文章编号:100121447(2008)0320032204R esearch on salt spray test of hot dip galvanized stripDON G Mei ,FEN G Hui ,SHI Guo 2lan(Technology Center of Maanshan Iron &Steel Co.Lt d.,Maanshan 243000,China )Abstract :Based o n neut ral salt spray test s (NSS )of hot dip galvanized st rip wit h differ 2ent layer ,weight ,surface t reat ment ,t his paper analyzes t he factors t hat influence t he corro sion of hot dip galvanized strip.In addition ,measures to improve t he corro sion re 2sistance of hot dip galvanized st rip are also given in t he paper.K ey w ords :corro sio n ;neut ral salt sp ray test ;Zn 25%Al alloy作者简介:董 梅(1973-),男,安徽人,高级工程师,主要从事金属材料、冷轧板材方面的研究. 马钢冷轧厂1号热镀锌生产线2004年初正式投产,由于马钢初次涉足镀锌卷板生产领域,在镀锌板耐蚀性能研究方面还是空白,同时,工厂和运输环境下,不同表面处理的镀锌板出现锈蚀的周期对产品质量控制、生产组织、企业物流也很有意义,因此开展了热镀锌板耐蚀试验研究。
热冲压镀锌板的防腐性能:主要影响因素和机理

热冲压镀锌板的防腐性能:主要影响因素和机理Corrosion Protection of Galvanized Press-Hardening Steel:Main Influencing Factors and MechanismsG Luckeneder(奥地利奥钢联)摘要根据欧洲汽车应用标准循环腐蚀试验(V D A 621 — 415/E N ISO 11997/1和V D A 233 —102),对热冲压镀锌板在涂装和未涂装状态下的防腐性能进行了研究。
结果表明,与传统镀锌板(G I)和合金化镀锌板(G A)相比,热冲压镀锌板(P H S— ZnFe)钢基层的腐蚀和涂层蠕变腐蚀均大为减缓。
本文将对该防腐性能改善现象的机理进行描述和讨论。
关键词热冲压镀锌合金化镀锌腐蚀V D A621 — 415,V D A233 —102,阴极保护1前言当今汽车工业面临诸多挑战。
节省燃料 和环保等生态方面的因素不断地推动车身向 轻量化发展,而另一方面对汽车被动安全性的更高要求又倾向于增加车身重量。
先进高 强度钢(Rm>800M Pa)的应用为确保轻量化 车身构造达到安全性要求带了个好头。
由于 这些钢材缺乏室温下的冷成形性能,所以必 须实施热成形工艺,使几何形状复杂的部件具有1500M P a以上的强度。
可硬化含硼钢(B含量 0. 002%〜0. 005%范围)在>85(TC 温度下奥氏体化,然后在冷具间以大于25K/ s的冷却速率淬火以获得马氏体组织。
将可 硬化钢与热冲压成形相结合的应用方式开始 于上世纪90年代,主要用于制造汽车的被动 安全部件,如侧门防撞杆、B柱、地板通道、踏 板及各种加固件等。
除被动安全和车身减重以外,防腐是汽 车工业使用材料的另一个重要方面。
特别引 人关注的是能够为基体提供牺牲阳极保护的 材料,如镀锌板。
将连续热镀锌板用作热冲压成形的原料可使汽车部件的强度达到很高 水平,具有复杂的几何形状和经典的阴极防腐性能。
热镀锌原理

一、概述锌易溶于酸,也能溶于碱,故称它为两性金属。
锌在干燥的空气中几乎不发生变化。
在潮湿的空气中,锌表面会生成致密的碱式碳酸锌膜。
在含二氧化硫、硫化氢以及海洋性气氛中,锌的耐蚀性较差,尤其在高温高湿含有机酸的气氛里,锌镀层极易被腐蚀。
锌的标准电极电位为-0.76V,对钢铁基体来说,锌镀层属于阳极性镀层,它主要用于防止钢铁的腐蚀,其防护性能的优劣与镀层厚度关系甚大。
锌镀层经钝化处理、染色或涂覆护光剂后,能显著提高其防护性和装饰性。
近年来,随着镀锌工艺的发展,高性能镀锌光亮剂的采用,镀锌已从单纯的防护目的进入防护-装饰性应用。
镀锌溶液有氰化物镀液和无氰镀液两类。
氰化物镀液中分微氰、低氰、中氰、和高氰几类。
无氰镀液有碱性锌酸盐镀液、铵盐镀液、硫酸盐镀液及无氨氯化物镀液等。
氰化镀锌溶液均镀能力好,得到的镀层光滑细致,在生产中被长期采用。
但由于氰化物剧毒,对环境污染严重,近年来已趋向于采用低氰、微氰、无氰镀锌溶液。
镀锌工艺[编辑本段]二、原理在盛有镀锌液的镀槽中,经过清理和特殊预处理的待镀件作为阴极,用镀覆金属制成阳极,两极分别与直流电源的正极和负极联接。
镀锌液由含有镀覆金属的化合物、导电的盐类、缓冲剂、pH调节剂和添加剂等的水溶液组成。
通电后,镀锌液中的金属离子,在电位差的作用下移动到阴极上形成镀层。
阳极的金属形成金属离子进入镀锌液,以保持被镀覆的金属离子的浓度[1]。
在有些情况下,如镀铬,是采用铅、铅锑合金制成的不溶性阳极,它只起传递电子、导通电流的作用。
电解液中的铬离子浓度,需依靠定期地向镀液中加入铬化合物来维持。
镀锌时,阳极材料的质量、镀锌液的成分、温度、电流密度、通电时间、搅拌强度、析出的杂质、电源波形等都会影响镀层的质量,需要适时进行控制。
[编辑本段]三、种类1、碱性氰化物镀锌2、碱性锌酸盐镀锌3、铵盐镀锌4、钾盐镀锌5、铵钾混合浴镀锌6、硫酸盐镀锌三、镀锌层的后处理1、去氢2、钝化3、着色现在钢板的表面镀锌主要采用的方法是热镀锌。
镀锌盐雾试验标准

镀锌盐雾试验标准镀锌盐雾试验是指将镀锌产品放置在盐雾环境中,以模拟产品在潮湿、腐蚀环境中的使用情况,从而评估其耐腐蚀性能的试验方法。
镀锌产品主要是指经过热浸镀锌或电镀锌处理的金属制品,如钢铁制品、铝制品等。
盐雾试验是检验镀锌产品防腐蚀性能的重要手段,也是评价其质量和耐久性的重要依据。
盐雾试验的标准主要包括试验设备、试验条件、试验方法和试验评定等内容。
首先是试验设备,盐雾试验设备通常包括盐雾试验箱、盐水储液箱、压缩空气系统、加热系统等。
盐雾试验箱是模拟盐雾环境的主要设备,其内部采用玻璃纤维增强塑料材料制成,具有耐腐蚀、耐高温、耐压力的特点,能够确保试验条件的稳定和准确。
其次是试验条件,盐雾试验的条件一般按照国际标准或行业标准规定进行,包括试验温度、盐水浓度、喷雾速率等参数。
试验温度一般为35℃±2℃,盐水浓度一般为5%±1%,喷雾速率一般为1~2ml/80cm²/h。
这些条件能够模拟真实环境下的腐蚀情况,确保试验结果的准确性和可靠性。
试验方法是盐雾试验的核心内容,主要包括试样的制备、试验的进行和试验后的评定。
试样的制备是指将待测镀锌产品按照标准规定进行处理,包括清洗、干燥、标记等工序,以确保试验结果的可比性和准确性。
试验的进行是指将制备好的试样放置在盐雾试验箱中进行暴露,根据标准规定的时间进行试验。
试验时间一般为24小时、48小时、72小时、96小时等,根据产品的使用环境和要求进行选择。
试验后的评定是指将试验后的试样进行检验和评定,包括外观检查、腐蚀程度评定等。
根据不同的标准规定,腐蚀程度一般分为轻度、中度、重度等等级,以便对产品的质量和性能进行评价。
盐雾试验的标准对镀锌产品的质量和性能具有重要的指导意义,能够帮助生产厂家和用户评估产品的耐腐蚀性能,选择合适的产品和材料,确保产品的质量和可靠性。
同时,也能够促进产品的技术改进和质量提升,推动行业的健康发展和进步。
总而言之,镀锌盐雾试验标准是评价镀锌产品耐腐蚀性能的重要依据,具有重要的指导意义和推动作用。
热浸镀锌层在中性盐雾试验中的防腐性能研究

热浸镀锌层在中性盐雾试验中的防腐性能研究
胡大伟;李国新;赵高文
【期刊名称】《广东工业大学学报》
【年(卷),期】2016(033)004
【摘要】采用2种定制的热浸镀锌试件,经5000 h中性盐雾试验后发现镀层防腐性能存在显著差异。
采用镀锌层厚度损耗测试法、X射线衍射分析法( XRD)和扫描电镜分析法( SEM)分别测试了镀层的厚度损耗量、盐雾试验前后的晶体物质组成和腐蚀前后的微观形貌。
研究表明:2种热浸镀锌试件在盐雾腐蚀过程中的产物和机理相似,而影响其防腐性能的主要因素为热浸镀锌的生产工艺、腐蚀产物的致密程度。
【总页数】5页(P74-78)
【作者】胡大伟;李国新;赵高文
【作者单位】榆林学院建筑工程系,陕西榆林719000;西安建筑科技大学材料与矿资学院,陕西西安710075;榆林学院建筑工程系,陕西榆林719000
【正文语种】中文
【中图分类】TG178
【相关文献】
1.热浸镀锌层在中性盐雾试验中的寿命预测研究 [J], 胡大伟;李国新;荆红莉;刘光秀;李玉根
2.热浸镀锌镀层在酸性盐雾试验中的防腐性能研究 [J], 胡大伟;荆红莉;刘光秀
3.不同锌浴成分下钢中Mn对热浸镀锌层的影响 [J], 李鹏程;汪雪涛;左汪楠;孙国庆;钱健清
4.锌浴中Ni-Bi协同作用对铁硅合金热浸镀锌层中间相组织的影响 [J], 刘永雄;尹付成;李智;赵满秀
5.助镀剂中氯化镍对热浸镀锌层增重、厚度及形貌结构的影响 [J], 王贺贺;姚敢英;上官帖;李远鹏;江社明;唐囡;俞钢强
因版权原因,仅展示原文概要,查看原文内容请购买。
- 1、下载文档前请自行甄别文档内容的完整性,平台不提供额外的编辑、内容补充、找答案等附加服务。
- 2、"仅部分预览"的文档,不可在线预览部分如存在完整性等问题,可反馈申请退款(可完整预览的文档不适用该条件!)。
- 3、如文档侵犯您的权益,请联系客服反馈,我们会尽快为您处理(人工客服工作时间:9:00-18:30)。
随着汽车工业的发展,汽车用热镀锌钢板的国产化程度不断提高,轿车的发展对热镀锌板的质量、品种和规格提出了更高的要求。
热镀锌板由于使用需要,长期以及Cl-等的腐蚀,影响产品质量,暴露于大气中,易于受到大气中潮湿气、SO2、固缩短产品的使用寿命。
在沿海城市及重工业地区,由于同时受到ph值、NO3体颗粒等影响,热镀锌板的腐蚀速率也会加快,对其耐腐蚀性能提出了更高的要求。
热镀锌板在盐雾实验中,表面锌层首先被腐蚀,腐蚀产物比较疏松,呈白色絮状覆盖在钢板表面,称之为“白锈”。
随着盐雾喷淋时间的延长,镀层逐渐被腐蚀殆尽,随后基板开始腐蚀,腐蚀产物为红色,称之为“红锈”。
由此可见,镀层的厚度与组成是决定红锈产生时间,即镀层腐蚀完毕、基板开始腐蚀所需时间的决定因素。
本章通过盐雾腐蚀实验和电化学实验比较稀土含量对镀锌板耐腐蚀性能的影响,并运用XRD分析腐蚀产物,对实际生产提出指导性意见。
1 镀层厚度的测量结果在镀前处理工艺及冷却方式相同的情况下,镀层厚度与热浸镀时间和锌液成分有关。
图4-1所示为采用传统镀锌液成分(Zn-0.177Al)浸镀时间与钢板表面镀层厚度之间的关系。
浸镀时间增加,镀层也逐渐增厚。
当浸镀时间较短(<2min)时,镀层的连续性较差,容易产生漏镀。
浸镀时间超过120s后,镀层已完全覆盖钢板。
把钢板表面划分为9个区域,用测厚仪在每个区域内取10个测量点进行测量,计算平均值作为此区域的平均厚度值,得到镀层厚度曲线(图4-2)。
结合钢板表面宏观形貌来看,传统镀锌液流动性较差,钢板出锌锅后表面锌液向下流动速率较慢,凝固后表面锌层存在波浪状起伏,两侧厚度差较大,厚度明显不均。
由于钢板出锌锅后采用竖直流平冷却的方式,因此靠近钢板底部的7、8、9三个点的平均厚度要高于其他各点。
整体上看,随着浸镀时间的延长,镀层厚度也呈增加的趋势。
图1 镀层平均厚度与浸镀时间的关系(不含稀土)图2 镀层不同区域内厚度曲线图(不含稀土)(a)厚度曲线;(b)测量区域由3.1.2及3.3.1的计算可知,镀锌液中添加稀土元素后,锌液流动性增加,表面张力降低,锌液与基板间的润湿角减小,因而在样板竖直凝固及冷却过程中,锌液不断向下流动,甚至滴落,最终样板表面的粘锌量较少。
因此,添加稀土元素后,样板表面镀锌层厚度普遍小于未添加稀土的样板,对四种不同成分镀锌液钢板的镀层厚度测量结果如图4-3所示。
比较四种钢板的镀层厚度曲线(图4-3a),可以看出,样板A表面镀层最不均匀,厚度值相差最大;添加稀土后,镀层均匀性较好,镀层厚度曲线比较平缓。
随着镀锌液中稀土含量的增加,在相同浸镀时间(2min)下,镀层的平均厚度逐渐降低,同时镀层也更为平整均匀,钢板各测量区域内厚度相差不大,具有比较好的表面效果。
进一步实验表明,当稀土含量大于0.1%时,钢板表面镀层很薄,易于出现漏镀现象,影响热浸镀效果。
图3 镀层厚度与镀锌液成分的关系(浸镀120s)(a)各测量点厚度;(b)平均厚度2 含稀土热镀锌板的耐腐蚀性能研究2.1 热镀锌板的盐雾腐蚀行为热镀锌板在盐雾腐蚀实验中,镀层和基板先后发生氧化腐蚀,参照美国ASTMB-8腐蚀实验方法,记录初次出现红锈的时间,同时根据热镀锌板红色锈点的面积(锈点周围锈迹的面积不计)来计算样板表面红锈的面积百分比。
一般来说,当镀层成分相同时,镀层全部腐蚀所需的时间与镀层的厚度有关。
镀层越厚,全部腐蚀所需的时间越长,基板越难被腐蚀,出红锈时间也越久。
表4-1所示为未添加稀土的热镀锌板镀层厚度与出红锈时间的关系。
表1 镀层厚度与出红锈时间的关系(不含稀土)四种不同镀层成分钢板的盐雾实验照片如图4所示:图4 红锈(a)11天;(b)30天当盐雾实验进行到第11天时,镀层成分为Zn-0.177Al的钢板表面出现红色锈点,约占样板面积的4%,而C、E、G表面均无红锈产生。
最后一块出现红锈的样板E成分为Zn-0.177Al-0.069Re,时间为30天,红锈百分比约为1%。
根据镀层中稀土含量的不同,适当调整浸镀时间,使得七种样板的镀层厚度相近,尽量消除厚度不同对腐蚀时间的影响,进行盐雾实验,此时,镀层表面的成分、结构以及化学活性是钢板出红锈时间和百分比的决定性因素。
其结果如表2所示。
表2 盐雾腐蚀实验结果从实验结果来看,样板D、E的盐雾腐蚀实验结果最好,初出锈时间普遍长于其他样板,红锈百分比也最低;未添加稀土的样板A初出锈时间最短,且红锈百分比最高,表明稀土对镀层的耐盐雾腐蚀性能有显著的提高作用。
而稀土含量在0.045wt%~0.069wt%区间范围内时,样板耐腐蚀能力优于其他成分区间内的样板。
2.2 盐雾腐蚀产物分析热镀锌板在盐雾实验机内,长期处于高Cl-浓度的湿热环境中,镀层表面纯锌层首先发生腐蚀,产生白色锈迹,称为“白锈”。
镀锌层作为热镀锌板防腐牺牲阳极,在大气环境下容易发生均匀腐蚀,形成致密的碱式碳酸锌(2ZnCO3·3Zn(OH)2),这种碱式碳酸锌比较致密,覆盖在镀层表面起到阻止进一步发生腐蚀的作用。
而在盐雾实验中,在NaCl溶液的浸蚀,局部Cl-逐渐积累并在潮湿气氛共同作用下,难溶、密集的2ZnCO3·3Zn(OH)2被疏松、易于溶解的氯盐化合物所取代,腐蚀产物进一步发生反应,生成ZnCl2·4Zn(OH)2,表面形成的腐蚀产物比较疏松,对镀层的保护作用有限,镀层表面腐蚀和溶解的过程反复交替进行,镀层逐渐被腐蚀。
对A、C、E、G四种样板的腐蚀产物进行XRD分析,结果表明四种样板表面所产生的白锈主要成分均为Zn5(CO3)2(OH)6和ZnCl2·4Zn(OH)2。
当镀层局部腐蚀殆尽后,基板在Cl-和潮湿气氛作用下发生腐蚀,腐蚀产物为红色锈点,周围伴随有黄褐色锈迹。
经实验测定,四种样板红锈的主要成分均为FeCl3、Fe(OH)3等。
2.3 极化曲线的测量与计算分析盐雾实验以红锈的出现时间和百分比为评价标准,只有当部分区域内的镀层腐蚀殆尽时,基板才开始发生腐蚀,产生红锈,是对整个样板表面宏观上耐腐蚀性能的考察,且其腐蚀条件较为苛刻,腐蚀速率比采用NaCl溶液恒温浸泡等实验方法高。
若以出白锈时间和百分比为依据,根据观察,A、C、E、G四种样板表面在1小时内均被白锈全部覆盖。
因此,盐雾实验不能从微观上体现出这四种样板表层耐腐蚀性能的差异。
极化曲线测定的是镀层表面纯锌层在5%NaCl溶液中的极化行为,结合盐雾实验结果,取A、C、E、G四块样板,用电化学方法测定四种样板极化曲线(图5)。
图5 四种样板的极化曲线同样采用5%NaCl溶液作为腐蚀介质,溶液中阳极及阴极反应如下:阳极:Zn-2e→Zn2+阴极:O2+2H2O+4e→4OH-其中O2来自于溶解在NaCl溶液中的氧气,镀层表面Zn层在溶液中的腐蚀为吸氧腐蚀,腐蚀速度受到阴极反应中O2的扩散过程控制,图4-6为这种腐蚀速度受到阴极反应扩散控制的典型极化曲线,可以看出,图4-5中四种样板的极化曲线均属于此种类型。
将阳极和阴极曲线延长,根据其延长线交点计算得出该极化反应的自腐蚀电位Ecorr和腐蚀电流Icorr。
结果表明,样板E的自腐蚀电位Ecorr最高,达到-0.9938V,而未添加稀土的样板A自腐蚀电位最低,仅为-0.9997V,四种样板的自腐蚀电位依次为EE>EC>EG>EA(表4-3)。
表3 四种样板的自腐蚀电位计算值图6 腐蚀速度受阴极反应扩散控制的典型极化曲线[58]与盐雾实验生成白锈的机理相似,在5%NaCl溶液中,镀层表面致密的碱式碳酸锌(2ZnCO3·3Zn(OH)2)保护膜受到破坏,发生腐蚀。
在Zn-0.177Al热浸镀液中,不可避免地存在着细微的锌渣和锌灰颗粒,以及一些锌的氧化物、硫化物等。
钢板出锌锅后至镀层完全凝固时,由于不加稀土的热浸镀液黏度较高,流动性较差,部分杂质颗粒被黏附在镀层中,有些甚至存在于镀层表面。
这些杂质破坏了2ZnCO3·3Zn(OH)2保护膜的完整性和致密性,周围还可能伴随着许多微孔,在Cl-的作用下,容易发生点蚀,在杂质区域内产生蚀坑。
添加稀土元素,利用其强脱氧、脱硫作用下反应生成稀土氧化物、硫化物以及硫氧化物,使热浸镀液中的杂质大大减少。
此外,由于稀土提高了热浸镀液的流动性,钢板出锌锅竖直冷却时,锌液能够流过整个钢板表面,在底部富集滴落的同时带走一部分杂质颗粒,进一步减少了镀层中杂质的含量,由图3-1可知,镀层表面光洁平整,其2ZnCO3·3Zn(OH)2保护膜也较为完整致密,因而在5%NaCl溶液中腐蚀速率较慢。
2.4 Kelvin探针微区电位分析为进一步研究稀土元素对镀层表面耐腐蚀性能的影响,运用Kelvin探针对未添加稀土以及添加稀土的两块样板进行微区电位的测量,结果如图7所示。
图7 微区电位分布图(a)Zn-0.177Al;(b)Zn-0.177Al-0.069ReKelvin探针所反映的是样板表面微小区域(6×4.5mm)内电位的分布情况,具体表现为探针与腐蚀金属电极表面上的薄水膜之间的伏打电位差。
因此,镀层表面的高度差异、晶粒与晶界的区别、杂质微粒的分布等等都会影响Kelvin探针所测得的功函数值。
图7a中,功函数的值较低,且变化幅度较大(-906meV~-998meV)。
在样板表面测量区域内,微区电位存在严重的分布不均匀性。
而在图4-7b中,功函数的值较高,且变化幅度较小(-803meV~-844meV),样板表面的电位分布较为弥散,没有一定的规律可循。
由此可见,稀土元素的添加,可以提高样板表面的平均电位值,使样板表面电位分布更均匀,极差更小。
从理论上来说,电位较高、分布较均匀的样板,其耐腐蚀性能更好。
3 稀土对耐腐蚀性能的影响机理结合第三章中对含稀土热镀锌层的组织结构观察与分析,在热浸镀液中添加稀土元素,能够显著提高热镀锌钢板的耐腐蚀性能,主要有以下一些原因:3.1 添加稀土元素提高了热浸镀液的流动性,使镀层表面更为平整光洁(图3-1),在大气条件下,镀层所形成的2ZnCO3·3Zn(OH)2保护膜更为致密完整,虽然在高Cl-环境中发生反应生成ZnCl2·4Zn(OH)2,但一定程度上仍起到了延缓腐蚀的作用;3.2 稀土元素易于与O、S等结合,生成的稀土氧化物与硫化物在凝固过程中一部分作为晶核继续生长,一部分表层的颗粒则随着锌液的滴落而除去,同时抑制了热浸镀液中锌渣和锌灰的形成。
未添加稀土的热浸镀液中,则存在着大量锌渣、锌灰以及锌或铝的氧化物、硫化物颗粒,根据晶间区杂质或第二相选择性溶解理论[59],镀层中的夹杂物易于在晶界上偏析,形成表面活性区域,造成表面能的不均匀性,在表层形成很多微孔,且腐蚀产物不能在表面形成连续而均匀的覆盖层,反而容易产生蚀坑,加速了腐蚀的进行;3.3 稀土元素抑制了镀层表面胞状组织的生长,镀层平整性、均匀性较好。