普通冲裁的基本原理.
冲裁工艺及冲裁模具

冲裁工艺及冲裁模具1. 引言冲裁工艺是一种常用的金属加工方法,用于通过冲压、剪切等手段将材料切割成所需形状或尺寸的工艺过程。
冲裁模具是冲裁工艺的关键设备,它提供了对材料的切割、定位和加工力的控制。
本文将介绍冲裁工艺及冲裁模具的根本原理、常见类型、应用等相关内容。
2. 冲裁工艺的根本原理冲裁工艺是利用冲压机将冲裁模具对材料施加高压力,使其实现切割或形状变化的工艺过程。
主要包括以下几个根本原理:冲裁工艺中,材料会经历弹性变形和塑性变形两个阶段。
在冲压过程中,冲裁模具施加的压力会使材料发生塑性变形,从而实现切割或形状变化的目的。
2.2 切割原理切割是冲裁工艺的主要目标之一。
利用冲压机和冲裁模具,对材料进行高速冲击,使其发生应力集中破断,实现切割作业。
2.3 定位原理冲裁工艺中,精确的定位是保证加工精度的关键。
冲裁模具通过合理的定位装置,确保材料在冲压过程中的位置准确、稳定,以实现高精度的切割和加工。
冲裁工艺中,冲压机和冲裁模具施加的压力是完成切割和加工的关键。
合理设计冲裁模具可以实现适当的加工力,并确保加工过程中不会对材料造成过度损坏。
3. 冲裁模具的常见类型根据不同的加工需求和材料特性,冲裁模具可以分为多种类型。
常见的冲裁模具类型包括切割模具、弯曲模具、拉伸模具等。
3.1 切割模具切割模具是冲裁工艺中最常见的类型。
它通常由上下两块模板和切割刀具组成。
切割模具可以将材料快速切割成需要的形状或尺寸,广泛应用于金属加工、汽车制造等领域。
3.2 弯曲模具弯曲模具可将材料通过施加力矩实现曲面或弯曲变形。
不同形状、尺寸和角度的弯曲模具适用于不同的加工需求,常见于金属制品的生产和加工中。
3.3 拉伸模具拉伸模具用于将材料拉伸至需要的形状或尺寸。
它通常由多个模块组成,可实现复杂形状的拉伸加工,广泛应用于汽车制造、航空航天等领域。
4. 冲裁工艺及冲裁模具的应用冲裁工艺及冲裁模具在各行各业都有广泛的应用。
以下是几个常见的应用领域:4.1 汽车制造汽车制造是冲裁工艺及冲裁模具的主要应用领域之一。
02冲裁模具的基本结构及工作原理

冲裁模具的基本结构及工作原理一、冲裁模具按工序组合程度可分为:简单冲裁模、连续冲裁模、复合冲裁模。
(一)简单冲裁模即敞开模1、定义:它是指在一次冲裁中只完成冲孔或落料的一个工序。
2、简单冲裁模按其导向方式可分为:(1)无导向单工序模它的特点是结构简单,重量轻、尺寸较小、模具制造容易、成本低廉。
但冲模使用安装时麻烦,模具寿命低,冲栽件精度差,操作也不安全。
无导向简单冲模适用于精度要求不高、形状简单、批景小或试制的冲裁件。
无导向单工序模冲模的上模部分由模柄、凸模组成,通过模柄安装在冲床滑块上。
下模部分由卸料板、导尺、.凹模、下模座、定位板组成,通过下模座安装在冲床工作台上。
上模与下模没有直接导向关系,靠冲床导轨导向。
(2)导板式简单冲裁模模精度高、寿命长、使用安装帧、操作安全,.但制造比较复杂。
一般适用于形状较简单、尺寸不大的工件。
导板式简单冲裁模上模部分主要由模柄、上模板、垫板、凸模固定板、凸模组成。
下模部分主要由下模板凹模、导尺、导板、回带式挡料销、托料板组成。
这种模具的特点是上模通过.凸模利用导板上的孔迸行导向,导板兼作卸料板。
工作时凸模始终不脱离导板.以保证模具导向精度。
因而,要求使用的压力机行程不大于导板厚度。
这种冲模的工作过程是:条料沿托料板、导尺从右向左送科,首次冲裁时使用临时挡料销定位,首次冲裁以后再往前送料,搭边越过活动挡料销后. 再反向拉拽条料,使挡料销后端面抵住条料搭边进行定位,凸模下行实现冲裁。
(3)导柱式简单冲裁模由于这模具准确可靠,能保证冲裁间隙的均匀,冲裁的工件精度较高、模具使用寿命长 而且在冲床上安装使用方便,因此导柱式冲裁模是应用最广泛的一种冲模,适合大批量生产。
导柱式简单冲裁模该冲模利用丁对导柱和导套实现、下模精确导向。
冲模主作时条料靠导尺和固定挡料销(亦称定位销)实现正确定位,以保证冲裁时搭边值的均匀一致。
此冲模采用刚性卸料板卸掉箍在凸模上的废料,冲出的工件在凹模洞口中经凸模的顶压作用,逐个实行自然漏料。
冲裁模具的基本结构与工作原理
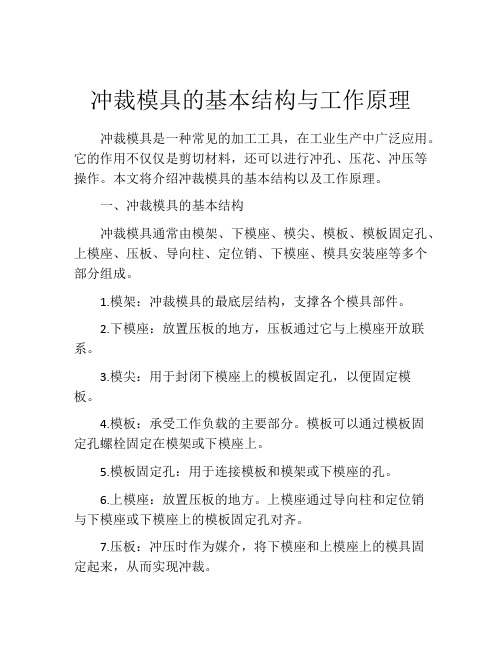
冲裁模具的基本结构与工作原理冲裁模具是一种常见的加工工具,在工业生产中广泛应用。
它的作用不仅仅是剪切材料,还可以进行冲孔、压花、冲压等操作。
本文将介绍冲裁模具的基本结构以及工作原理。
一、冲裁模具的基本结构冲裁模具通常由模架、下模座、模尖、模板、模板固定孔、上模座、压板、导向柱、定位销、下模座、模具安装座等多个部分组成。
1.模架:冲裁模具的最底层结构,支撑各个模具部件。
2.下模座:放置压板的地方,压板通过它与上模座开放联系。
3.模尖:用于封闭下模座上的模板固定孔,以便固定模板。
4.模板:承受工作负载的主要部分。
模板可以通过模板固定孔螺栓固定在模架或下模座上。
5.模板固定孔:用于连接模板和模架或下模座的孔。
6.上模座:放置压板的地方。
上模座通过导向柱和定位销与下模座或下模座上的模板固定孔对齐。
7.压板:冲压时作为媒介,将下模座和上模座上的模具固定起来,从而实现冲裁。
8.导向柱:用于连接上模座和下模座,确保冲裁过程中的精准度。
9.定位销:也用于对齐上模座和下模座的位置。
10.下模座:承受模具的卡紧力,防止模具在模具固定孔处滑动。
11.模具安装座:将冲裁模具固定在机械或压力机上的底座。
二、工作原理冲裁模具的工作原理是利用压力让模板和压板卡死工件,对工件进行切割或冲孔。
具体来说,它包括材料、凸台(刀模)、凹模、冲孔机床和机械手等多个部分。
在工作之前,必须先进行模压,并设置工作参数。
然后将工件放置在压板上,逐步移动到凹模下部。
随着压力的逐渐增加,材料被弯曲、伸长或压缩,最终断裂。
刀模和凹模都是刻有图案的特殊工具,它们能够对工件进行不同的操作。
除了切割和冲孔,冲裁模具还可以进行拉伸和弯曲等操作。
不同的操作需要使用不同的模具。
总的来说,冲裁模具的工作原理是依靠刃口的形状和力学原理,将压力转化为工件的变形。
冲裁模具的安装和调整需要经验和技能。
准确设置参数有助于防止模具的脱离、折断或损坏,从而确保生产效率和质量。
结论冲裁模具是工业生产中不可或缺的工具之一。
01冲裁原理
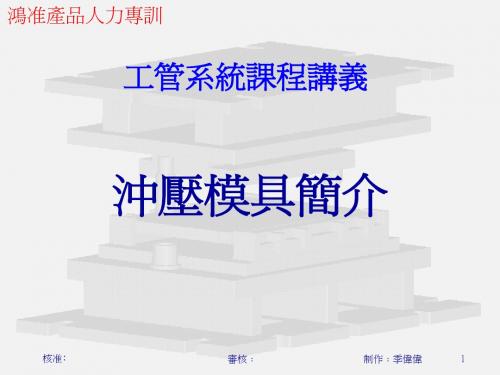
鴻准產品人力專訓
一.沖孔模原理---沖裁斷面
Z/2
M—毛面 R—塌角
核准﹕
G—光面
沖裁所得的表面﹐如 右圖所示﹐在沖出孔 的上部﹐有些微圓角 稱塌角﹐接著是由剪 切形成的光亮光面﹐ 最后是撕裂形成的毛 面。而在廢料上﹐也 有類似的三部分﹐只 是分布位置的上下次 序相反。
鴻准產品人力專訓
沖裁概述
定義:
基于金屬塑性變形,利用沖模對板料金屬進行加工
以得到所需要的零件形狀和尺寸
分類:
沖裁 :是材料分離工序
彎曲 拉深 從廣義上講,沖裁可分為沖孔,落料,切口,剖切等; 從變形機理上講,沖裁可分普通沖裁和精密沖裁
核准﹕ 審核﹕ 制作﹕季偉偉 24
鴻准產品人力專訓
沖裁分離過程
上模端部下邊 的材料開始
彎曲
彈 性 形 變 階 段間隙愈大,Fra bibliotek曲和上翹愈嚴重
核准﹕ 審核﹕
下模刀口上邊 的材料開始
上翹
制作﹕季偉偉 25
鴻准產品人力專訓
沖裁分離過程
塑 性 變 形 階 段
1.上模繼續下行
材料內部應力增大到屈服極限
進入塑性變形階段
2. 拉應力和彎矩增大
變形區材料開始硬化
刃口 附近材料出現裂紋 3.裂紋的出現標示塑性變形階段結束 4.間隙的大 小直接影響切斷面的質量(詳見下一張).
剖切
核准﹕ 審核﹕
模具結構
制作﹕季偉偉 21
鴻准產品人力專訓
2.1.7沖裁工序(修邊1)
將 實將 心平 件的 多、 余空 外心 邊的 切或 掉立 體
模具結構
核准﹕ 審核﹕ 制作﹕季偉偉 22
鴻准產品人力專訓
常用冲压工艺基本原理

常用冲压工艺基本原理冲压工艺是一种通过冲压设备将金属或非金属材料加工成所需形状的加工方法。
它广泛应用于制造行业中,如汽车制造、航空航天、电子等领域。
常用冲压工艺的基本原理如下:1.冲裁:冲裁是冲压工艺的基础,通过在金属材料中施加剪切力,将材料分离成所需的形状。
冲裁要求冲压设备具有足够的压力和刚度,以确保能够将材料切割成准确的形状,并保持相对平整的边缘。
2.弯曲:弯曲是将金属材料弯曲成所需的形状。
通过将材料置于折弯模具中,并施加压力使其弯曲。
弯曲要求冲压设备具有足够的刚度,以确保能够在材料上施加足够的压力,并保持所需的形状。
3.拉伸:拉伸是将金属材料拉伸成所需的形状。
通过将材料固定在一端,然后通过施加拉力来延长材料并形成所需的形状。
拉伸要求冲压设备具有足够的拉力和刚度,以确保能够在材料上施加足够的拉力,并保持所需的形状。
4.成形:成形是将金属材料压制成所需的形状。
通过在材料表面施加压力,使其逐渐变形成所需的形状。
成形要求冲压设备具有足够的压力和灵活性,以确保能够在材料上施加足够的压力,并保持所需的形状。
5.切削:切削是将金属材料切割成所需形状的方法。
通常采用冲床、剪切机等设备,在材料上施加切割力,将材料切断成准确的形状。
切削要求冲压设备具有足够的切削力和刚度,以确保能够将材料切割成准确的形状,并保持相对平整的边缘。
6.模具设计:模具是冲压工艺中不可缺少的工具,它影响着冲压加工的质量和效率。
模具设计要求考虑材料的物理特性、形状复杂程度以及生产要求等因素,以确保能够精确加工出所需的形状,并保持高效的生产速度。
综上所述,常用冲压工艺的基本原理包括冲裁、弯曲、拉伸、成形、切削和模具设计等。
这些原理在冲压加工中起着重要的作用,决定了加工质量和效率。
因此,工程师在进行冲压加工时需要充分理解和应用这些基本原理,以确保能够获得满足生产要求的加工零件。
冲裁的基本原理与冲压模具的结构

1,按加工的形式或內容分為: ①,沖裁模--------將一部分材料與另一部分材料分離的模 具。(切邊﹑下料模) ②,彎曲模--------將坯料彎曲成一定形狀的模具。(折彎模) ③,拉延模--------將坯料拉延成開口空心的零件或進一步改變空心工件形狀或尺
innovative Display Solution Provider
2,塑性變形階段
塑性变形、外力作用超出材料的强度极限,产生断 裂纹。当凸模继续压入,压力增加,材料内部的应力 也随之加大,在材料内的应力达到屈服极限时便开 始进入塑性变形阶段。在这一阶段中随着凸模挤入 材料的深度逐渐增加,材料的塑性变形程度也逐渐 增大。由于刃日处间隙的存在,材料内部的拉应力 及弯矩也都增大,使变形区材料硬化加剧,直到刃口 附近的材料由于拉应力及应力集中的作用开始出现 微裂纹,此时,冲裁变形力也达到最大值。微裂纹的 出现说明材料开始破坏,塑性变形阶段也告结束。
材料 SKD11 SKD11
SKD11
Solution Provider
熱處理 HRC58-62 HRC58-62
HRC58-62
性能
冲模零部件
工艺构 件
部件
定义
所含零件
凸模
工作零件
它是指直接进行冲裁分离工件的零件。 凹模
凸凹模
定位板定位销
定位零件
它是指能保证条料在送进和冲裁时在 挡料销
模具上有正确位置的零件。
innovative Display Solution Provider
二、 普通冲裁件的断面特征:
<1>塌角带 由主单性变形阶段产生初始塌角,带动边塑性变形阶段。 <2>光亮带 产生于塑性变形阶段,断面较光洁平整,是质量最佳的一段。 <3>断裂带 撕裂造成的,表面粗糙而无光泽,并带有锥度。 <4>毛刺区 产生微裂时便产生毛刺。
冲裁工艺及冲裁模具设计

冲裁工艺及冲裁模具设计冲裁工艺是一种常用的金属加工方法,通过冲切将金属材料切割成所需形状和尺寸,通常用于制作金属零部件和工件。
冲裁工艺的成功与否,不仅与冲裁机床的性能和工艺操作的技能有关,也与冲裁模具的设计质量密切相关。
本文将重点介绍冲裁工艺及冲裁模具设计的相关内容。
冲裁工艺的基本原理是,通过在金属材料上施加一定的冲击力,使模具上的刀具快速切入材料中,沿着预定轨迹切割出所需形状的零件。
冲裁工艺具有以下几个特点:一是加工速度快,冲裁速度通常为每分钟几十次到几百次,可以高效地完成大批量生产;二是加工精度高,冲裁工艺可以实现较高的尺寸精度和形状精度;三是适用范围广,冲裁工艺适用于各种金属材料,如钢材、铝材、铜材等。
冲裁模具是实现冲裁工艺的关键工具,其质量和设计能力直接影响着冲裁工艺的效果和生产成本。
冲裁模具的设计要考虑以下几个方面的因素:首先,要根据零件的形状和尺寸确定冲裁模具的结构和形式。
常见的冲裁模具包括简单冲模、复杂冲模、连续冲模等多种形式。
对于形状复杂、尺寸较大的零件,通常需要采用复杂冲模,以满足工艺要求。
其次,要合理选择冲裁模具的材料。
冲裁模具的材料应具有较高的硬度和耐磨性,以保证长时间的使用寿命。
常见的冲裁模具材料有合金工具钢、硬质合金等。
同时,还应根据不同材料的特性,选择合适的冲裁模具涂层,以减小摩擦阻力,延长模具的使用寿命。
再次,要根据冲裁工艺要求确定冲裁模具的加工精度和工艺要求。
冲裁模具的加工精度直接影响着冲裁零件的尺寸精度和形状精度。
因此,在设计冲裁模具时,要考虑到刀具的选择、工艺参数的确定等因素,以保证冲裁零件的质量和成品率。
最后,要根据冲裁生产的需求,合理设计冲裁模具的结构和布局。
冲裁模具的结构应简洁、紧凑,以降低制造成本和提高生产效率。
同时,还要合理设计模具的装卸和调整方式,以便于模具的更换和维护。
综上所述,冲裁工艺及冲裁模具设计是金属加工中非常重要的环节。
通过合理的冲裁工艺和冲裁模具设计,可以提高生产效率,降低生产成本,提高冲裁零件的质量和生产效率。
第二章 冲裁工艺及冲裁模设计

普通冲裁件的断面情况:
普通冲裁变形所得到的冲裁件端面常带有一定的锥度,并且 都有明显的区域特征,不同的是各区域的大小占整个断面的比例 不一样。 光亮带 产生于塑性变 圆角带
发生在弹性变形后 期和塑性变形初期, 由金属的弯曲和拉伸 而形成。其大小与材 质有关。
形阶段,断面主 要受剪应力和压 应力作用。断面 平整、光滑。通 常占整个区域的 1/2~1/3,与材质 有关。
第二章 冲裁工艺及冲裁模设计
普通冲裁原理
冲裁间隙 冲裁模刃口尺寸的计算(重点) 冲裁件的排样(重点) 冲压工艺力(重点) 压力中心的计算(重点) 冲裁件的工艺性 冲裁模的基本形式及特点 冲裁模主要零、部件结构和设计(重点) 冷冲模的设计程序(重点)
2.1 普通冲裁的基本原理
冲模刃口尺寸、制造公差的大小主要取决于 冲裁件的形状和精度。
刃口尺寸的计算方法
冲模刃口 尺寸公差带 分析图
1. 凸、凹模分开加工时的刃口计算
δd+δp≤Zmax-Zmin 运用该方法必须使模具的制造公差与间隙满足 或 δp= 0.4(Zmax-Zmin) δd= 0.6(Zmax-Zmin)
根据刃口尺寸的计算原则,分开加工时凸、凹模刃口尺寸 的计算公式如下:
推件力Pd: Pd = KdP
冲压工艺力的计算:
(它是选取压力机吨位的主要依据,具体计算要考虑模具的结构型式) 采用刚性卸料自然漏料方式:Pz≥P+Pt = P +nKtP 采用刚性打料、弹性卸料的倒装结构方式:Pz≥P + Px = P + KxP 采用弹性卸料和弹性顶料方式:Pz≥P + Px + Pd = P + KxP + KdP 采用弹性卸料自然漏料方式:Pz≥P + Px + Pd = P + KxP + nKdP (选择压力机时,压力机的公称压力N必须大于或等于Px)
常用冲压工艺基本原理

常用冲压工艺基本原理冲压工艺是现代工业生产中常见的金属成形方法之一,其基本原理是通过将金属板材置于压力机上,依靠冲压模具对金属板材进行冲压、拉伸、弯曲、剪切等操作,从而使其形成所需的零件或产品。
以下是常用冲压工艺的基本原理。
1.冲裁:冲裁是冲压过程中最常见的一种工艺,它通过模具上的切割刀具将金属板材切割成所需形状的零件。
冲裁工艺能够快速高效地生产出一大批形状相同的零件,适用于大批量生产。
2.拉伸:拉伸是指将金属板材置于模具中,在压力机的作用下,使金属板材产生拉伸变形,从而使其成为带有凹陷或凸起的零件。
拉伸工艺常用于制造深凹型零件,如汽车车身、洗衣机筒等。
3.弯曲:弯曲是将金属板材置于模具中,在压力机的作用下,使其产生塑性变形,从而使其成为带有曲线形状的零件。
弯曲工艺常用于制造弧形或曲线形状的零件,如门把手、管道弯头等。
4.折弯:折弯是将金属板材置于模具中,在压力机的作用下,将金属板材弯曲成所需的角度,从而使其成为带有角度的零件。
折弯工艺常用于制造角度零件,如梁、角铁等。
5.压铸:压铸是将熔化的金属注入到模具中,经过一段时间冷却后取出。
压铸工艺能够制造出复杂形状的零件,并具有高精度和高表面质量,适用于生产要求较高的零件。
6.制模:制模是冲压工艺中不可或缺的一个环节,其主要目的是根据产品的要求制造出适用的模具。
制模包括模具的设计、制造和调试过程,通过模具的精确度和准确性来保证冲压过程中零件的质量和精度。
7.板料分配:板料分配是冲压工艺中非常重要的一环,它决定了金属板材的利用率和材料的利用率。
合理的板料分配能够最大限度地减少金属板材的浪费,提高产品的生产效率和经济效益。
总之,冲压工艺基本原理是通过模具对金属板材进行冲压、拉伸、弯曲、剪切等操作,从而使其成为所需的零件或产品。
通过合理的制模和板料分配,冲压工艺能够快速高效地生产出形状复杂、精度高的零件,广泛应用于汽车、家电、机械设备等领域。
冲裁工艺ppt课件

2、刃口计算方法
(1)凸、凹模分开加工 即:在设计图上分别标注凸、凹模尺寸及公差
刃 口 计 算
必须同时满足下列两个条件 (1)形状简单 (2)符合δ凸+δ凹≤Zmax-Zmin 计算方法: ①落料 工件标注尺寸为(D-Δ) 先计算凹模尺寸: D凹=(D-xΔ)+δ凹 减去间隙为凸模尺寸:D凸=(D-xΔ- Zmin)-δ凸
n为凹模刃口卡住工件或废料个数
顶件力 反冲压方向从凹模中顶出工件 F顶=k顶F
(各系数K可查P57表3-8)
降低冲裁力的措施: ①.选用阶梯凸模
落料、冲孔,多孔冲制时,凸模刃口阶梯差 (0.5~1)t。
b
第 二 章 冲 裁
②.选用斜刃口模具
模具刃口做成斜面。落料时凹模为斜刃口; 冲孔时凸模为斜刃口。
③加热冲裁
冲 裁 力
2、卸料、推件力 卸料力 从凸模上卸去条料: F卸 = k 卸 F 推件力 顺冲压方向从凹模中推出工件: F推 = n k 推 F
故:先确定凹模尺寸→减去间隙为凸模尺寸。
冲孔:工件尺寸取决于凸模尺寸。
故:先确定凸模尺寸→加上间隙为凹模尺寸。
刃 口 计 算
(2)按刃口磨损规律 凹模:磨损后刃口尺寸变大。故:落料 刃口尺寸应等于或接近于工件落料最小极限 尺寸 D 。 凸模:磨损后刃口尺寸变小。故:冲孔 凸模刃口尺寸应等于或接近于工件冲孔最大 极限尺寸 d 。 无论落料或冲孔,凸、凹模磨损都使间 隙加大,故Z应取最小值Z min 。 (3)模具刃口制造公差δ 高于工件精度(Δ)2~4级; 工件一般为IT8~14,模具IT6~9; 或:取工件公差Δ的1/3~1/4 或:查表3-6,P49
(2)凸、凹模配合加工
①条件:形状复杂; 或δ凸+δ凹﹥Zmax-Zmin
冲裁的原理
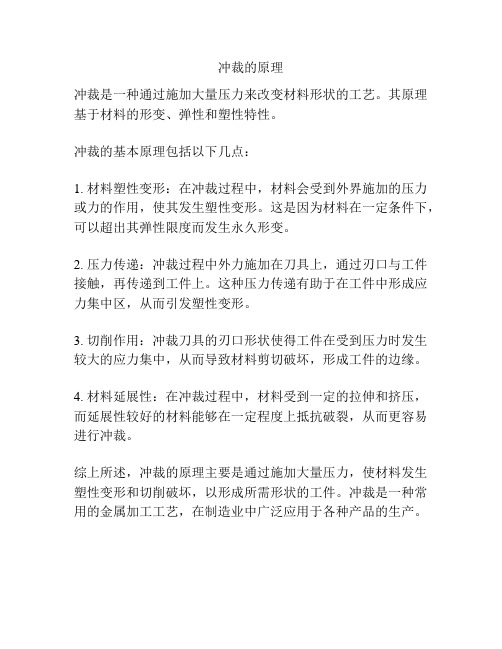
冲裁的原理
冲裁是一种通过施加大量压力来改变材料形状的工艺。
其原理基于材料的形变、弹性和塑性特性。
冲裁的基本原理包括以下几点:
1. 材料塑性变形:在冲裁过程中,材料会受到外界施加的压力或力的作用,使其发生塑性变形。
这是因为材料在一定条件下,可以超出其弹性限度而发生永久形变。
2. 压力传递:冲裁过程中外力施加在刀具上,通过刃口与工件接触,再传递到工件上。
这种压力传递有助于在工件中形成应力集中区,从而引发塑性变形。
3. 切削作用:冲裁刀具的刃口形状使得工件在受到压力时发生较大的应力集中,从而导致材料剪切破坏,形成工件的边缘。
4. 材料延展性:在冲裁过程中,材料受到一定的拉伸和挤压,而延展性较好的材料能够在一定程度上抵抗破裂,从而更容易进行冲裁。
综上所述,冲裁的原理主要是通过施加大量压力,使材料发生塑性变形和切削破坏,以形成所需形状的工件。
冲裁是一种常用的金属加工工艺,在制造业中广泛应用于各种产品的生产。
冲裁模具的基本结构及工作原理
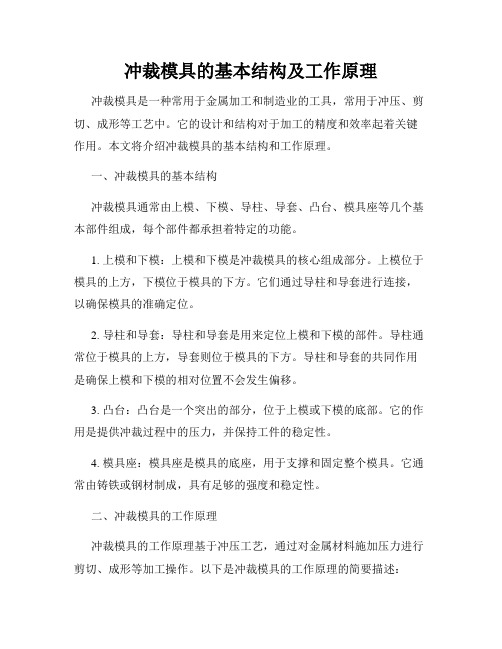
冲裁模具的基本结构及工作原理冲裁模具是一种常用于金属加工和制造业的工具,常用于冲压、剪切、成形等工艺中。
它的设计和结构对于加工的精度和效率起着关键作用。
本文将介绍冲裁模具的基本结构和工作原理。
一、冲裁模具的基本结构冲裁模具通常由上模、下模、导柱、导套、凸台、模具座等几个基本部件组成,每个部件都承担着特定的功能。
1. 上模和下模:上模和下模是冲裁模具的核心组成部分。
上模位于模具的上方,下模位于模具的下方。
它们通过导柱和导套进行连接,以确保模具的准确定位。
2. 导柱和导套:导柱和导套是用来定位上模和下模的部件。
导柱通常位于模具的上方,导套则位于模具的下方。
导柱和导套的共同作用是确保上模和下模的相对位置不会发生偏移。
3. 凸台:凸台是一个突出的部分,位于上模或下模的底部。
它的作用是提供冲裁过程中的压力,并保持工件的稳定性。
4. 模具座:模具座是模具的底座,用于支撑和固定整个模具。
它通常由铸铁或钢材制成,具有足够的强度和稳定性。
二、冲裁模具的工作原理冲裁模具的工作原理基于冲压工艺,通过对金属材料施加压力进行剪切、成形等加工操作。
以下是冲裁模具的工作原理的简要描述:1. 上模下压:在冲裁过程中,上模通过导柱和导套与下模相连,并施加下压力。
这种压力将工件夹紧在两个模具之间,以确保加工的准确性和稳定性。
2. 冲裁操作:一旦上模和下模夹住工件,冲裁操作就开始了。
在冲裁过程中,凸台会施加额外的压力,使工件发生形变、剪切或成形。
3. 释放和回弹:当冲裁操作完成后,上模和下模会释放对工件的压力,并迅速回到起始位置。
这是为了方便取出已加工的工件,并为下一次冲裁操作做好准备。
三、冲裁模具的优势和应用领域冲裁模具具有以下优势,使其在许多行业中得到广泛应用:1. 高精度:冲裁模具的结构设计精细,能够实现高精度加工,保证了成品的质量和尺寸精度。
2. 高效率:冲裁模具的自动化程度高,能够实现批量生产和连续加工,提高了生产效率。
3. 多功能性:冲裁模具可以适应各种形状和尺寸的工件加工,具有良好的适应性和灵活性。
冲裁的工作原理范文

冲裁的工作原理范文冲裁(Stamping)是一种常见的金属加工方法,其工作原理简单描述为在上、下冲裁模具的作用下,将金属板材通过机械或液压力量施加在金属板表面上,使其表面产生塑性变形,从而完成所需的形状。
下面将详细介绍冲裁的工作原理。
冲裁过程主要包括四个阶段:进料、定位、加工和退料。
先将金属板材定位到冲裁模具的定位孔中,然后通过外界力的作用使金属板材与冲裁模具之间产生大的变形,完成冲裁过程。
具体的工作原理如下:1.进料:首先将待冲裁的金属板材放入冲床的进料区。
进料是保证冲裁工艺能够连续进行的关键步骤。
在进料过程中,金属板材会被夹紧并沿着预定的路径进入冲裁模具的工作区域。
2.定位:一旦金属板材进入工作区域,它需要被准确而稳定地定位到冲裁模具的工作位置。
这是为了确保冲裁的准确性和一致性。
通常,冲裁模具上会设置一系列的定位针或定位孔,用于将金属板材正确安排在所需位置上。
3.加工:加工阶段是整个冲裁过程最重要的一步。
金属板材将被夹紧并通过冲床的压力施加在冲裁模具上,产生塑性变形。
冲裁模具上通常包含两部分:上模和下模。
当冲床施加力量时,上模会向下推动,将金属板材压到下模上。
下模上通常设置了一定形状的凹槽或凸台,用于使金属板材产生所需的形状。
4.退料:加工完成后,需要将冲裁好的金属零件从模具中取出。
这个过程通常通过顶出装置完成,顶出装置会通过一定的力量将金属零件从模具上顶出,并将其传送到下一个工作站点或接收区域。
退料过程要确保金属零件完整无损。
总的来说,冲裁工作原理主要是通过施加力量使金属板材产生塑性变形,以完成所需的形状。
冲裁过程需要准确的定位、合适的冲裁模具和适量的力量控制,以确保冲裁过程的稳定性和零件质量的一致性。
冲裁是一种高效、精准的金属加工方法,在汽车制造、家电制造等行业得到广泛应用。
冲裁原理

角度來分析受力過程
刃口磨損大,壽命變短.
B 間隙大
沖裁件與刃口摩擦力小
刃口磨損小,壽命延長.
(如圖所示)
Confidential
Hon Hai Precision Industry Co., Ltd.
三.沖裁間隙選擇
===========
DS 零件處模修員培訓專案
沖裁間隙
一般指凸凹模之單面間隙,表示方法為: Clears=%t 設計時按4~6%t 選取。
2.產生微裂紋時即產生了初始毛刺.
3.材料分離時,毛刺將進一步拉長, 初始毛刺變為永久性毛刺.
Confidential
Hon Hai Precision Industry Co., Ltd.
二.沖裁過程詳述
4.影響斷面四區域形狀的因素
===========
DS 零件處模修員培訓專案
1.毛刺材料的種類 : 塑性好則光亮帶 大,斷裂帶小;塌角大,毛刺高.
DS 零件處模修員培訓專案
光 光亮帶產生于塑性變形階段,當凸模擠 亮 入板料,壓應力占主導地位,壓應力起 帶 到了陰止減小金屬晶間變形的作用,增
強了金屬的塑性,能使材料在塑剪情況 下進行分離,所以在斷面上形成較光潔 平整的光亮帶,這個區域表面光潔,並 且與板料平面垂直,是斷面質量最佳的 一段.
Confidential
從變形機理上講,沖裁可分普通沖裁 和精密沖裁
Confidential
Hon Hai Precision Industry Co., Ltd.
二.沖裁過程詳述
1.沖裁過程:
沖裁時的分離動作 是在瞬間完成,一般 經過以下三個階段。
A: 第一階段:彈性
變形階段
因產生彎曲,材料
普通冲裁的基本原理

3.断裂带
4.毛刺区
断裂带产生于冲裁变 毛刺是因为凸、凹模 形第3阶段,由于拉应 刃口之间存在间隙和 力的作用促使裂纹不 刃口不锋利产生的。
断扩展,金属纤维拉 材料在产生微裂纹时
断,生成表面粗糙无 就产生了初始毛刺,
光泽且有斜度的断裂 当材料分离时毛刺被
微裂纹的出现标志着材料开始破坏,塑性变
形阶段结束。
3.断裂分离阶段
凸模继续下降,已经产生的上、下裂纹不断扩 大并向板料内部延伸,当上、下裂纹互相重合 时,端面产生粗糙的断裂带,板料被分离,完 成整个冲裁过程。
1.2 普通冲裁件的断面情况
一般把断面分为四个特征区:即塌角带(圆角
带)、光亮带、断裂带和毛刺区.
冷冲模具设计
普通冲裁的基本原理
1.1 板料的分离过程
冲裁时材料的分离过程
由于有间隙存在,材料受垂直方向压力、剪切 力、横向挤压力、弯矩和拉力的共同作用,除主 要的剪切变形外,还要产生弯曲、过深、挤压等 附加变形。
分离过程大致可分为3个阶段。
图2.1为无弹压板的金属板料分离过程
第1阶段
第3阶段 第2阶段
1.塌角带
塌角带发生是由于金 属材料的弯曲与拉伸 变形而形成的。
弹性初始塌角随着凸 模的下降而进入塑性 变形阶段,从而成为 永久性的塌角留在断 面上,塑性好的材料 圆角大
1 2 3
4
图2.2 冲裁件断面特征 1. 毛刺区 2. 断裂带 3. 光亮带
4. 塌角带
2.光亮带
光亮带产生于塑性变形阶段,由于压应力阻 止和减小了金属晶间变形,使金属产生塑剪 变形. 所以端面光滑、平整、且与板料平面垂直, 是断面质量最好的一段。
一、冲裁加工原理

一、沖裁加工原理沖裁是利用沖模在壓力機上使板料分離的一種沖壓工藝。
它包括切斷、落料、沖孔、修邊、切口等多種工序,但一般說來主要是落料和沖孔工序。
沖裁變形可分為三個階段:第一階段:彈性變形階段(圖2-1a)凸模與材料接觸後,先將材料壓平,繼而凸模及凹模刃口壓入材料中,由於彎矩M的作用,材料不僅產生彈性壓縮且略有彎曲。
隨著凸模繼續壓入,材料在刃口部分所受的應力也逐漸增大,直到h1深度時,材料內應力達到彈性極限,此為材料的彈性變形階段。
第二階段:塑性變形階段(圖2-1b)凸模繼續壓入,壓力增加,材料內的應力達到屈服極限,產生塑性變形。
隨著塑性變形程度的增大,材料內部的拉應力和彎矩隨之增大,變形區材料硬化加劇,當壓入深度達到h2時,刃口附近材料的應力值達到最大值,此為塑性變形階段。
第三階段:段裂階段(圖2-1c)凸模壓入深度達到h3時,先後在凹、凸模刃口側面產生裂紋,裂紋產生後沿最大剪應力方向向材料內層發展,當凹、凸模刃口處的裂紋相遇重合時,材料便被剪斷分離。
沖裁變形的三個階段,可以在剪切曲線圖中得到驗証,如下圖所示。
二、沖裁的工藝性沖裁件的工藝性,是指沖裁件對沖壓工藝的適應性。
主要包括有以下幾個方面。
(一)沖壓件的形狀和尺寸1.沖裁件的形狀盡可能設計間單、對稱,使排樣時廢料最少。
如圖2-4所示。
2.沖裁件的外形或內孔應避免尖稅的清角,在各直線或曲線的連接處,除屬於無廢料沖裁或採用鑲拼模結構外,宜有適當的圓角,其半徑R的最小值見表2-1。
圖2-4少廢料沖裁的排樣表2-1沖裁件圓角半徑R的最小值(二)沖裁件的精度和表面粗糙度1.沖裁件內外形的經濟精度不高於GB1800-79IT11級。
一般要求落料件精度最好低於IT10級,沖孔件最好低於IT9級。
2.非金屬沖裁件內外形的經濟精度為GB1800—79 IT14~~IT15級。
對於紙膠板、布膠板、硬紙等材料。
3.沖裁件的彎曲,是落料時,沖件的周圍與凹模孔壁之間發生摩擦,因而受到力偶的作用致使沖件彎曲變形。
冲裁原理

3.進入塑性變形階段,初始塌角變成永久性塌角,
光亮帶產生于塑性變形階段,當凸模擠入
光 亮 帶
板料,壓應力占主導地位,壓應力起到了陰 止減小金屬晶間變形的作用,增強了金屬的 塑性,能使材料在塑剪情況下進行分離,所以 在斷面上形成較光潔平整的光亮帶,這個區 域表面光潔,並且與板料平面垂直,是斷面質 量最佳的一段.
影響斷面四區域形狀的因素
1.毛刺材料的種類 : 塑性好則光亮帶大,斷裂帶小;塌角大,毛刺高.
2. 沖裁條件 : 刃口間隙----間隙小,光亮帶大高; 刃口形狀 刃口鋒利程度
注 :獲得較寬光亮帶的辦法 消除或抑制拉應力的影響,使變形區處于三向壓 應力狀態,具有較強的靜水壓效應
(精密沖裁的理論依據)
1.斷裂帶產生于沖裁變形后期的剪裂階段.
斷 裂 段
2.拉應力增大
金屬晶界破坏,原子層分離 金屬縴維被拉斷
產生微觀裂紋
粗糙斷面形成
3.斷裂區粗糙,並帶有錐度,質量較差
1. 從沖壓變形原理上講,毛刺的產生是不可避免的;
毛 刺 區
間隙合適時,毛刺的高度很小.
2.產生微裂紋時即產生了初始毛刺.
3.材料分離時,毛刺將進一步拉長,初始毛刺變為永 久性毛刺.
模具設計沖壓概述基于金屬塑性變形利用沖模對板料金屬進行加工以得到所需要的零件形狀和尺寸下模刀口上邊的材料開始變形區材料開始硬化刃口附近材料出現裂紋光亮帶產生于塑性變形階段當凸模擠入板料壓應力占主導地位壓應力起到了陰塑性能使材料在塑剪情況下進行分離所以在斷面上形成較光潔平整的光亮帶這個區域表面光潔並且與板料平面垂直是斷面質量最佳的一段
沖子
刀口ห้องสมุดไป่ตู้
間隙過小 合適 間隙過大
斷裂帶
- 1、下载文档前请自行甄别文档内容的完整性,平台不提供额外的编辑、内容补充、找答案等附加服务。
- 2、"仅部分预览"的文档,不可在线预览部分如存在完整性等问题,可反馈申请退款(可完整预览的文档不适用该条件!)。
- 3、如文档侵犯您的权益,请联系客服反馈,我们会尽快为您处理(人工客服工作时间:9:00-18:30)。
3.断裂带
断裂带产生于冲裁变形第3阶段,由于拉应力的作用促使裂纹不
断扩展,金属纤维拉断,生成表面粗糙无光泽且有斜度的断裂带。
4.毛刺区
毛刺,是由于刃口正面材料被压缩,刃尖部分是高静水压应力状态, 微裂纹的起点在模具侧面距刃尖不远的地方发生而产生 。
• 由上可知 : 冲裁 是通过凸、凹模的刃口像剪子一
一 冲裁间隙是决定弹性恢复量大小的重要因素。
当间隙较大时,材料的拉变形大,冲裁后,弹性恢复使落料件
外径收缩,使冲孔孔径扩张,结果是落料件尺寸小于凹模尺寸, 冲出的孔径大于凸模尺寸 • 当间隙较小时,材料的侧向挤压变形大,冲裁后弹性恢 复使落料件外径扩张,使冲出的孔径收缩,结果是落料 件尺寸大于凹模尺寸,冲孔孔径小于凸模直径。
拉应力成分增大,材料容易产生裂纹、使塑性变形较早 结束。 所以光亮带变窄,断裂带、圆角带增大,毛刺相对较大, 锥度也较大。
间隙过小
间隙合适
间隙过大
间隙大小对断面质量的影响
(2)间隙对冲裁件尺寸精度的影响
冲裁件的尺寸精度是指冲裁件的实际尺寸与 基本尺寸的差值。 这个差值包含两个方面的偏差: 一是冲裁件相对凸模或凹模刃口尺寸的偏差 二是模具本身的制造偏差。
光亮带
图8.2冲裁区应力、变形和冲裁件正常的断面状况
a)冲孔件 b)落料件
1.塌角带
• 塌角带发生是由于金属材料的弯曲与拉伸变形而形成的。弹性初 始塌角随着凸模的下降而进入塑性变形阶段,从而成为永久性的 塌角留在断面上,塑性好的材料塌角大。
2.光亮带
光亮带产生于塑性变形阶段,金属产生塑剪变形时,由于,材料 在与模具侧面接触中被模具侧面挤光而形成的光亮垂直的断面。 所以断面光滑、平整、且与板料平面垂直,是断面质量最好的一 段。通常,光亮带占断面的1/2~1/3,塑性好的材料,光亮带所 占的比例更大。
• 凸、凹模每侧间隙称 为单边间隙 • 两侧间隙之和称为双
边间隙
• Z=Dd-Dp
式中 Z——冲裁间隙(mm); Dp——凸模刃口尺寸(mm); Dd——凹模刃口尺寸(mm)。
图8.3 冲裁间隙
8.2.1 冲裁间隙对冲裁工序的影响
1.冲裁间隙对冲裁件质量的影响
冲裁件质量包括冲裁断面质量、尺寸精度 和弯曲度三个方面。
二 冲裁件的尺寸精度主要取决于模具本身的制造精度
表8.2 冲裁件的尺寸精度与冲模的制造精度
(3)间隙对弯曲度的影响
间隙对弯曲度的影响是:
间隙愈大,弯曲愈严重。为了减小弯曲度, 可在模具上加压料板或另外加校平工序。
2.间隙对冲裁力的影响
间隙愈小
冲裁变形区的压应力成分越大,拉应力成分越小, 材料变形抗力大,冲裁力越大
(1)间隙对冲裁件断面质量的影响
• 间隙过小时,上、下裂纹不能相遇重合,板料将被第 二次剪切,断面会产生两个光亮带,并造成夹层,毛 刺被拉长。 间隙合理时,上、下表面产生的初始裂纹能相遇重 合,光亮带较大,塌角带、断裂带、毛刺区都较小, 锥度也比较小。
间隙过大时,上、下裂纹仍然不重合,因应力状态中的
样将板料剪断分离,这就决定了其断面 粗糙且有斜度 等弊端。 理凸、凹模间隙、等措施,可以改善断面质量。
另外,也可通过增加整形工序来提高冲裁件断面
• 所以,通过提高模具和冲床的精度、刚度,以及采用合
质量。表8.1为冲裁件断面的近似粗糙度值。
表8.1 一般冲裁件断面的近似表面粗糙度
8.2 冲 裁 间 隙
塑性变形阶段
断裂分离阶段
图8.1 冲裁变形过程
1.弹性变形阶段
• 凸模对板料施压,使材料产生弹性变形。板料稍微挤入凹模口。板料与凸、 凹模接触处形成很小的塌角。由于凸、凹模之间存在间隙,板料同时受到弯 曲和拉伸的作用,凸模下的板料产生弯曲,凹模上的板料开始上翘。
2.塑性变形阶段
凸模继续压到一定深度时,材料内部应力达到屈服点,板料开始 在与凸模、 凹模的刃口接触处产生塑性剪切变形。凸模切入板料并将下部板料挤入凹模孔内。 在板料剪切面处形成塌角,同时在切断面上形成一小段光亮且与板料垂直的表面。 随着冲压过程的继续,应力不断增加,材料的变形程度便不断增加,变形区向板 材的深度方向发展、扩大,同时硬化加剧,变形抗力也不断上升,应力也随之增 加,直至凸、凹模刃口处达到极限应力和应变值,这就意味着塑性变形结束,材 料即产生微小裂纹。
3.间隙对模具寿命的影响
模具寿命分为刃磨寿命和模具总寿命。 模具失效的原因一般有:磨损、变形、崩刃、折断 和胀裂。 小间隙将使磨损增加,甚至使模具与材料之间产生粘结 现象,并引起崩刃、凹模胀裂、小凸模折断、凸凹模相 互啃刃等异常损坏。
• 间隙越小,摩擦越严重,模具寿命越短。 • 较大的间隙,不仅可以减小磨损,也可以缓解间 隙不均匀的影响,从而提高模具的寿命
8.1 普通冲裁的基本原理
8.1.1 板料的分离过程
冲裁时材料的分离过程 由于有间隙存在,材 料受垂直方向压力、剪切 力、横向挤压力、弯矩和 拉力的共同作用,除主要 的剪切变形外,还要产生 弯曲、过深、挤压等附加 变形。
• 分离过程大致可分为3个阶段。
图8.1为无弹压板的金属板料分离过程
弹性变形阶段
3.断裂分离阶段
裂纹产生后,随凸模继续压入,凸、凹模刃口附近产生的微裂纹沿最大剪应变 速度方向不断向板材内部扩展。若间隙合适,上、下裂纹则相遇重合,板料上 下部分分离。
8.1.2 普通冲裁件的断面情况
一般把断面分为四个特征区:即塌角带(圆角带)、光亮带、
断裂带和毛刺区.
塌角带
光亮带
断裂带
毛刺
塌角带