粘土湿型砂的控制要点之欧阳光明创编
湿型砂的检测要求与质量控制
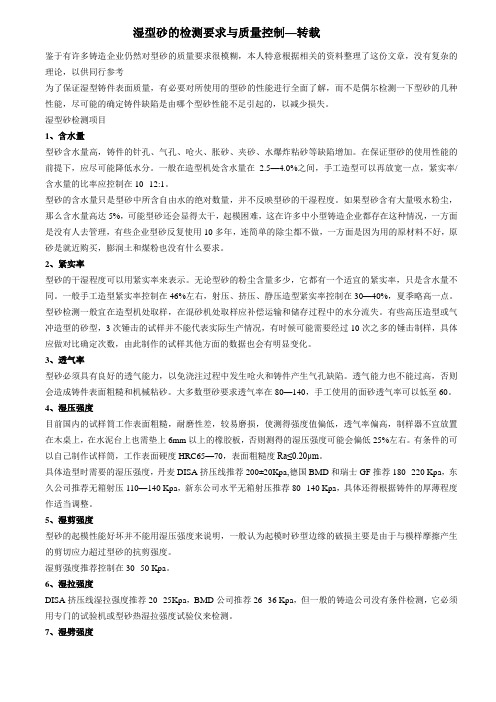
湿型砂的检测要求与质量控制—转载鉴于有许多铸造企业仍然对型砂的质量要求很模糊,本人特意根据相关的资料整理了这份文章,没有复杂的理论,以供同行参考为了保证湿型铸件表面质量,有必要对所使用的型砂的性能进行全面了解,而不是偶尔检测一下型砂的几种性能,尽可能的确定铸件缺陷是由哪个型砂性能不足引起的,以减少损失。
湿型砂检测项目1、含水量型砂含水量高,铸件的针孔、气孔、呛火、胀砂、夹砂、水爆炸粘砂等缺陷增加。
在保证型砂的使用性能的前提下,应尽可能降低水分。
一般在造型机处含水量在 2.5—4.0%之间,手工造型可以再放宽一点,紧实率/含水量的比率应控制在10--12:1。
型砂的含水量只是型砂中所含自由水的绝对数量,并不反映型砂的干湿程度。
如果型砂含有大量吸水粉尘,那么含水量高达5%,可能型砂还会显得太干,起模困难,这在许多中小型铸造企业都存在这种情况,一方面是没有人去管理,有些企业型砂反复使用10多年,连简单的除尘都不做,一方面是因为用的原材料不好,原砂是就近购买,膨润土和煤粉也没有什么要求。
2、紧实率型砂的干湿程度可以用紧实率来表示。
无论型砂的粉尘含量多少,它都有一个适宜的紧实率,只是含水量不同。
一般手工造型紧实率控制在46%左右,射压、挤压、静压造型紧实率控制在30—40%,夏季略高一点。
型砂检测一般宜在造型机处取样,在混砂机处取样应补偿运输和储存过程中的水分流失。
有些高压造型或气冲造型的砂型,3次锤击的试样并不能代表实际生产情况,有时候可能需要经过10次之多的锤击制样,具体应做对比确定次数,由此制作的试样其他方面的数据也会有明显变化。
3、透气率型砂必须具有良好的透气能力,以免浇注过程中发生呛火和铸件产生气孔缺陷。
透气能力也不能过高,否则会造成铸件表面粗糙和机械粘砂。
大多数型砂要求透气率在80—140,手工使用的面砂透气率可以低至60。
4、湿压强度目前国内的试样筒工作表面粗糙,耐磨性差,较易磨损,使测得强度值偏低,透气率偏高,制样器不宜放置在木桌上,在水泥台上也需垫上6mm以上的橡胶板,否则测得的湿压强度可能会偏低25%左右。
黏土砂型铸造规模生产中的质量控制方法

黏土砂型铸造规模生产中的质量控制方法稳定地保证黏土型砂质量是大批量黏土砂铸造生产中的关键问题之一。
目前,汽车铸铁件采用黏土砂湿型铸造占有主导地位,大批量流水线式生产是其主要生产方式。
因此,黏土型砂的质量稳定直接影响铸件生产质量,控制好型砂质量对于黏土砂湿型铸造有着重要的意义。
在实际生产中,应严格控制好型砂性能。
从目前国内部分大型铸造厂的生产情况来看,在型砂质量控制方面还存一些问题,如残留芯砂含量偏高、循环使用的旧砂温度过高、生产配方单一、缺少有效的实时监测设备等。
针对这些问题,可以从以下几个方面入手来提高型砂质量,减少铸件缺陷率。
1、合理选用原材料湿砂型铸造所用型砂由旧砂、原砂、黏土、煤粉及水等原材料混制而成,这些材料的性能和质量将直接关系到型砂的性能和质量。
若想制备出高质量的型砂,则必须选用优质的原材料,并处理好回用的旧砂。
(1)造型用原砂选用优良的原砂,可以减少黏结剂的用量,减少铸件废品率,提高铸件表面质量,减少清理费用,其经济效益大大超过采购好砂的超出费用。
(2)膨润土(黏土)膨润土在型砂中起黏结剂的作用,同时在高温时可以抵消硅砂的体积膨胀。
型砂中加入量多时呈干燥状态,流动性降低,容易产生掉砂冲砂缺陷;加入量少时则型砂强度受到影响,砂型的回弹性也变大。
为追求铸件尺寸准确,要把铸型的膨胀、收缩、回弹等减少到最小程度,故对膨润土提出以下要求:①湿强度、干强度、热态强度综合性能好。
②水分变化时对湿强度影响小。
③浇注后溃散性好。
④受热后能恢复原有湿态性能。
2、合理控制型砂组分湿型砂经反复使用,硅砂有受热开裂,粒度变小,以及砂粒受黏土包围结壳,粒度变大的倾向,膨润土及煤粉受热而部分失效。
因此,回用时如不及时调整型砂成分,会出现起模性能下降、铸件表面粘砂、气孔、砂眼、夹砂等现象。
合理控制型砂成分并维持连续地动态平衡,是型砂管理中的关键。
(1)限制细粉量型砂中的细粉量随循环次数的增多也逐渐增加。
其细粉越多,需水量也越多,在保证型砂强度、韧性、紧实率等要求前提下,含水量应为2.5%~3%(质量分数)。
粘土湿型砂应用实例分析及对策
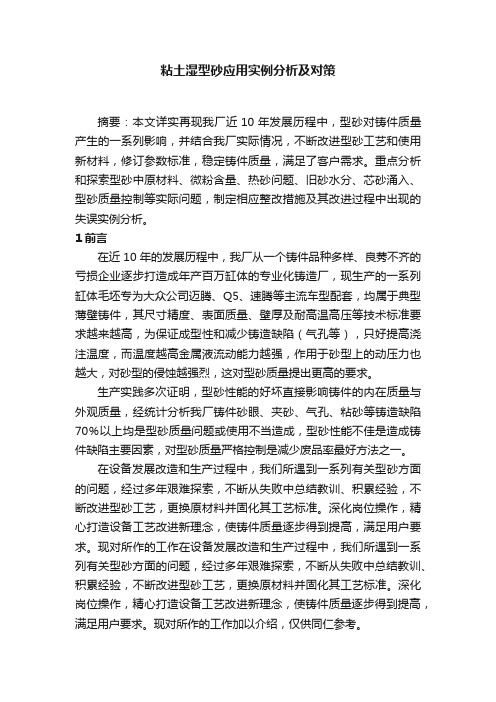
粘土湿型砂应用实例分析及对策摘要:本文详实再现我厂近 10 年发展历程中,型砂对铸件质量产生的一系列影响,并结合我厂实际情况,不断改进型砂工艺和使用新材料,修订参数标准,稳定铸件质量,满足了客户需求。
重点分析和探索型砂中原材料、微粉含量、热砂问题、旧砂水分、芯砂涌入、型砂质量控制等实际问题,制定相应整改措施及其改进过程中出现的失误实例分析。
1前言在近 10年的发展历程中,我厂从一个铸件品种多样、良莠不齐的亏损企业逐步打造成年产百万缸体的专业化铸造厂,现生产的一系列缸体毛坯专为大众公司迈腾、Q5、速腾等主流车型配套,均属于典型薄壁铸件,其尺寸精度、表面质量、壁厚及耐高温高压等技术标准要求越来越高,为保证成型性和减少铸造缺陷(气孔等),只好提高浇注温度,而温度越高金属液流动能力越强,作用于砂型上的动压力也越大,对砂型的侵蚀越强烈,这对型砂质量提出更高的要求。
生产实践多次证明,型砂性能的好坏直接影响铸件的内在质量与外观质量,经统计分析我厂铸件砂眼、夹砂、气孔、粘砂等铸造缺陷70%以上均是型砂质量问题或使用不当造成,型砂性能不佳是造成铸件缺陷主要因素,对型砂质量严格控制是减少废品率最好方法之一。
在设备发展改造和生产过程中,我们所遇到一系列有关型砂方面的问题,经过多年艰难探索,不断从失败中总结教训、积累经验,不断改进型砂工艺,更换原材料并固化其工艺标准。
深化岗位操作,精心打造设备工艺改进新理念,使铸件质量逐步得到提高,满足用户要求。
现对所作的工作在设备发展改造和生产过程中,我们所遇到一系列有关型砂方面的问题,经过多年艰难探索,不断从失败中总结教训、积累经验,不断改进型砂工艺,更换原材料并固化其工艺标准。
深化岗位操作,精心打造设备工艺改进新理念,使铸件质量逐步得到提高,满足用户要求。
现对所作的工作加以介绍,仅供同仁参考。
2型砂材料对铸件质量的影响及其控制标准2.1 选用内蒙优质原砂满足铸件基本质量要求原砂是型砂中主要材料,其性能与参数的变化对铸件质量及生产有直接影响,我们对 SiO2含量、粒度、含泥量、角型系数等参数均有严格要求。
湿型砂造型中型砂质量的控制

_
j 誊 毒 誊。 。 。 ; 。l。。 。 - l 。 l 一 。
湿 型 砂 造型 中型砂 质 量 的控 制
赵 洪仁 , 顺 龙 马
( 汽 铸 造有 限公 司 一 技术 中心 , 林 吉 长春 10 6 ) 30 2
摘要 : 介绍 了湿 型 砂各 组 分 的作 用 , 述 了 型砂 性 能 与 其 组 分 的关 系 , 为 控制 好 有 效 膨 润 土 量 和 有 效 添 加 剂量 是 控 制 型 砂 质 论 认 量 的关 键 , 结合 生 产 实 例 说 明 了 型砂 质 量 的 控 制 要 点 ; 出提 高 型 砂 质 量控 制 水 平 、 产 优 质铸 件 和实 现 铸 造 生 产循 环 用 砂 是 指 生
铸 造 生 产节 能 减 排 的根 本 方 法之 一 。
关 键 词 : 型砂 ; 湿 型砂 质 量 ; 效 膨 润土 量 ; 有 有效 添 加 剂量 中 图分 类号 :G 4 T 22 文 献标 识 码 : A 文章 编 号 :0 3 84 (0 lZ — 0 2 0 10 — 3 52 1 】10 8— 8
a o n s t e k y me s r t o tol he qu lt f modi s n m u t i h e a u e o c n r t a i o l ng a d.By ho n r ci a x mpl,t e ke p i s o l ng s n y s wi g p a tc le a e h y ont f modi a d q a i o to r e p an d.I s ontd o h tee a ig t e uaiy o to lv lo l n a d t p o uc hg q a i u lt c n r lwe e x l ie y twa p i e utt a lv tn h q l c nr l e e f modig s n o r d e ih u lt t y c si sa cuaie s n y l s g n fun y r d t n i n ft e r dia eho st o du t ne g a i n m iso at ng nd a t lz a d c ci u a e i o dr p o uci s o e o h a c lm t d o c n c e ry s vng a d e s in ng o rdu i n f u dr o ucin. e cng i o n y pr d to
如何控制黏土湿型砂旧砂性能
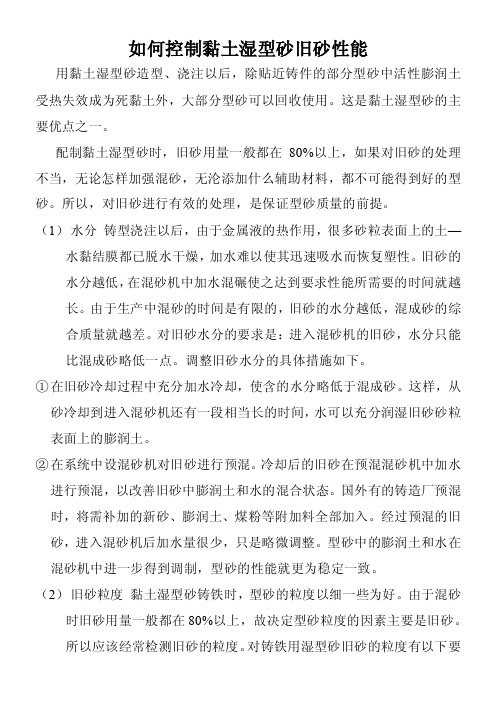
如何控制黏土湿型砂旧砂性能用黏土湿型砂造型、浇注以后,除贴近铸件的部分型砂中活性膨润土受热失效成为死黏土外,大部分型砂可以回收使用。
这是黏土湿型砂的主要优点之一。
配制黏土湿型砂时,旧砂用量一般都在80%以上,如果对旧砂的处理不当,无论怎样加强混砂,无沦添加什么辅助材料,都不可能得到好的型砂。
所以,对旧砂进行有效的处理,是保证型砂质量的前提。
(1)水分铸型浇注以后,由于金属液的热作用,很多砂粒表面上的土—水黏结膜都已脱水干燥,加水难以使其迅速吸水而恢复塑性。
旧砂的水分越低,在混砂机中加水混碾使之达到要求性能所需要的时间就越长。
由于生产中混砂的时间是有限的,旧砂的水分越低,混成砂的综合质量就越差。
对旧砂水分的要求是:进入混砂机的旧砂,水分只能比混成砂略低一点。
调整旧砂水分的具体措施如下。
①在旧砂冷却过程中充分加水冷却,使含的水分略低于混成砂。
这样,从砂冷却到进入混砂机还有一段相当长的时间,水可以充分润湿旧砂砂粒表面上的膨润土。
②在系统中设混砂机对旧砂进行预混。
冷却后的旧砂在预混混砂机中加水进行预混,以改善旧砂中膨润土和水的混合状态。
国外有的铸造厂预混时,将需补加的新砂、膨润土、煤粉等附加料全部加入。
经过预混的旧砂,进入混砂机后加水量很少,只是略微调整。
型砂中的膨润土和水在混砂机中进一步得到调制,型砂的性能就更为稳定一致。
(2)旧砂粒度黏土湿型砂铸铁时,型砂的粒度以细一些为好。
由于混砂时旧砂用量一般都在80%以上,故决定型砂粒度的因素主要是旧砂。
所以应该经常检测旧砂的粒度。
对铸铁用湿型砂旧砂的粒度有以下要求。
①140目筛上的砂粒应在10%~15%之间。
保持较多的细砂,可以减轻铸件表面粘砂,而且会增加砂粒之间黏结桥的数量,从而降低型砂的脆性,避免冲砂缺陷。
此外,这对提高型砂的高温强度和水分凝聚区强度都有好处。
②200目筛、270目筛和底盘上细砂的总和应量少。
这类细砂对改善铸件表面质量的作用不大,却会使混成砂的水分较高,而且会使型砂的透气性降低。
粘土型(芯)砂
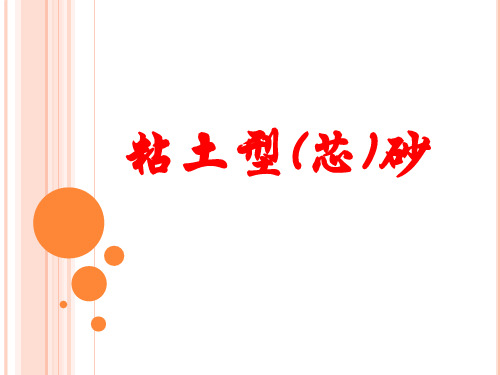
对湿型砂而言,混砂时严格控制加水量是 必要的。工厂中常用的加水量控制办法有 以下几种: ①人工加水。 ②定量水箱、定量水表、时间继电器控制 电磁水阀。边测量、边控制。
28
三、型砂的质量检验和控制
通过型砂的质量检验和宏观控制,不但可了解型砂 是否达到要求的性能,而且还可掌握型砂在使用中 的变化,这样就能及早采取措施,保证型砂符合要 求和保持稳定,保证铸件质量,预防缺陷产生。 试验结果的综合分析 每次取样测出的型砂性能,常在一定范围内波动, 故一次试验结果还不能说明问题,应取每天试验结果 的平均值,才能较好地代表整个型砂系统的状况。
20
铸钢型砂的特点:
为了防止铸件增碳,型砂中不含煤粉和煤粉烧损的残 留物,因而铸钢型砂的含泥量较铸铁型砂低,需水量少 。在同样紧实率下.铸钢型砂的水分低,有利于防止产 生针孔或皮下气孔。水分最好控制在4%-5%(质量分数) 或更低些。 由于型砂中不含煤粉和含泥量低,单一砂和面砂的透 气性容易偏高。单一砂的透气性最好不超过120,面砂 的透气性还应更低才能生产出表面光洁无机械粘砂的铸 件。为此,可选用粒度15Q(或2lQ)的硅砂,不宜使用粒 度为30Q的粗硅砂。
4.高密度造型型砂
(1)高密度造型特点 高密度造型是指提高造型紧实力制得较高紧实程度或较高 密度砂型的造型方法而言。过去高密度造型只指各种高压造 型。近十多年来,高速的冲击造型包括动力(机械)冲击和气 流冲击造型得到了越来越广泛的开发相应用,也属高密度造 型。 一般认为,压实比压高到0.7MPa以上称为高压造型,用 此法生产出来的铸件不仅尺寸精度高,表面粗糙度大大改善 ,而且能使铸件更加致密,力学性能更高,加工余量减少, 铸件质量减轻,劳动条件改善,生产率大大提高等。 高压造型中,由于其不良的砂型强度分布;另外,随着压 实比压的提高,还可能引起“水爆炸”,从而会出现型壁移 动,并使铸件产生气孔、局部表面粗糙和机械粘砂、甚至整 24 个铸件表面粘砂等缺陷 。
膨润土在粘土湿型砂中应用的几个应注意的控制要点

膨润土在粘土湿型砂中应用的几个应注意的控制要点膨润土在铸造中主要用于粘土粘结砂中,因为膨润土具有粘结力强、可塑性高、脱膜好、透气性优、高温湿态条件下物理化学性能稳定等特点。
粘土粘结砂作造型材料生产铸件,本是历史悠久的工艺方法,在各种化学粘结砂蓬勃发展的今天,粘土湿型砂仍是最重要的造型材料,其适用范围之广,耗用量之大,是任何其他造型材料都不能与之比拟的。
近代的高压造型、射压造型、气冲造型、静压造型及无震击真空加压造型等新工艺,也都是以使用粘土湿型砂为前提的,粘土湿型砂适应造型条件的能力极强。
现今,随着科学技术快速发展,各产业部门对铸件的需求不断增长,同时,对铸件品质的要求也越来越高。
也使粘土湿型砂面临许多新的问题,促使我们对粘土湿型砂的研究不断加强、认识不断深化。
前不久,笔者走访了国内一些铸造单位,发现铸件的废品较多,特别是一些小规模铸造单位,问题主要是有气孔等缺陷。
产生问题主要在生产新铸件、换其他厂家膨润土和长期使用旧砂期间。
有必要对膨润土和旧砂的控制要点进行一下强调。
1.膨润土和膨润土粘土粘结砂中的,作用及变化,铸造用膨润土主要有钠基膨润土和钙钠膨润土两类,钠基膨润土是由天然钠基膨润土或人工钠化膨润土加工而成,以其复用性好和湿压强度高而受铸造行业欢迎。
因具有良好的可塑性,可遏止铸件夹砂、结疤、掉块、砂型塌方等现象,加之成型性强、型腔强度高,便于金属行业浇铸湿态或干态型模,是精密铸件首选的型砂粘结剂。
钙钠膨润土由天然基钙钠膨润土加工它以实用和铸件清砂便捷是轻型铸件普遍采用的型砂粘结剂。
而成,而受用户欢迎。
和其他黏结剂相比,膨润土有一个重要的特点,就是它具有一定的耐热能力。
只要加热温度不太高,脱除了自由水的膨润土只要加水,仍能恢复粘能力。
膨润土的粘结能力只有在加水以后才能表现出来。
膨润土失去粘结能力,也与它的脱水有关。
到目前为止,认为膨润土中的水分有3种形态:一种水是自由水,即膨润土颗粒吸附的水,加热到100℃以上,就可脱除自由水,脱除了自由水的膨润土,粘结能力不受影响;二种水是牢固结合水,110℃下长时间加热,膨润土可完全脱除自由水,但不会脱除牢固结合水。
粘土湿型砂所有优缺点及几种常用的附加材料

粘土湿型砂所有优缺点及几种常用的附加材料黏土湿型砂是铸造行业中人人都很熟悉的事物,正是因为我们对它太“熟悉”了,铸造行业不少同仁反而是‘与之久处而不知其香’,对它的一些特性只知其梗概,而未深究其精微,因而,虽然天天离不了它,却不能运用自如,充分发挥它的作用。
一、黏土湿型砂优点1、使用历史最悠久的造型材料从开创人类文明的‘青铜时代’起,我们就离不了黏土湿型砂,由于没有记载可考,不能确切地说出其应用的最早年代,认为其有5000年左右的历史,可能不会是夸大其词。
当然,早期的黏土湿型砂与目前所用的差别很大,而且所用主要是天然的黏土黏结砂,采掘以后,加水混拌后就可以使用。
这种黏土砂中的黏土主要是高岭土质的耐火黏土,一个典型的例子就是我国南京附近出产的六合红砂,以前一度真可谓是闻名遐迩,直到20世纪50年代初期,我国第一个五年计划期间,不少手工作业的铸造厂仍然使用。
18世纪后期,简单的造型机问世以后,逐渐强化了对型砂性能的要求。
随着造型机不断地改进、优化,19世纪初期又催生了混砂机,加速了由天然黏土黏结砂到用混砂机配制的合成砂的转变。
用混砂机配制的合成砂推广应用以后,为了适应不断提高造型机的生产效率、提高铸件质量的要求,莫来石质膨润土的应用,在改善黏土湿型砂的质量方面的作用,应该说是至关重要的、具有划时代的意义。
目前,世界各国所用的黏土湿型砂全都都是加膨润土配制的膨润土的应用至少有一百多年了,但是,我们对膨润土的认知还很不够,今后必须不断深化对它的了解。
2、黏土湿型砂性能控制的空间宽阔,对各种造型方式的适应性很好粘土湿型砂,有较高的湿强度,在舂实过程中,其流动性较差,使砂型紧实所需的能量较多,但是,其适应各种造型方式的能力很好。
从最原始的手工造型,到各种现代化的自动造型生产线,用黏土湿型砂作为造型材料,都有令人满意的效果。
黏土湿型砂对各种舂实方式,如手工紧实、舂实、震实、压实、抛砂、射砂、气冲、静压、等造型工艺,都能适应。
砂子试验标准操作方法之欧阳法创编

2021.03.09 欧阳法创编2021.03.09一.目的检测砂子颗粒级配、含泥量、泥块含量,确定砂子的规格和类别。
指导检测人员按标准正确操作,确保检测结果科学、准确。
二.检测参数及执行标准颗粒级配、含泥量、泥块含量、表观密度、堆积密度、紧密密度。
执行标准:GB50204-2002《混凝土结构工程质量验收规范》中7.2.5条。
GB/T14684-2011《建设用砂》JGJ52-2006《普通混凝土用砂石质量及检验方法标准》三.适用范围适用于建设工程中混凝土及其制品和建筑砂浆用砂。
四.职责检测员必须执行国家标准,按照标准操作,2021.03.09 欧阳法创编2021.03.09随时作好试验记录,填写检测报告,并对数据负责。
五.样本大小及抽样方法同一规格产地,每验收批取样部位应均匀分布,将表面层铲去,然后由8个部位取大致等量的砂,组成一组样品,人工四分法缩分至所需试样。
用大型运输工具的,以400m3或600t为一验收批,用小型工具运输时,以200m3或300t为一验收批。
不足上述数量以一批论。
最少取样数量不少于30kg。
六.仪器设备1.鼓风烘箱:能使温度控制在(105±5)℃;2.案称:称量10kg,感量5g;3.电子天平1000g:精度1g。
4.摇筛机5.方孔筛:孔径为75μm -9.50mm的筛共八只,并附有筛底和筛盖;6.容器:要求淘洗试样时,保持试样不溅出(深度大于250 mm);7.量具:500 mL容量瓶;2021.03.09 欧阳法创编2021.03.098.容量筒:圆柱形金属筒,内径108 mm,净高109mm,壁厚2mm,筒底厚约5mm,容积为1L;;9.密度计;10.放大境:3倍—5倍放大率;钢针;11.搪瓷盘,毛刷、垫棒(直径10 mm,长500 mm的圆钢)、直尺、漏斗或料勺、亚甲蓝溶液等;七.环境条件操作室:20 ±5℃。
八.检测步骤及数据处理1.颗粒级配准备好试验用的工具,检查仪器设备的状态是否正常。
铸造粘土湿型砂的特性及其控制要点
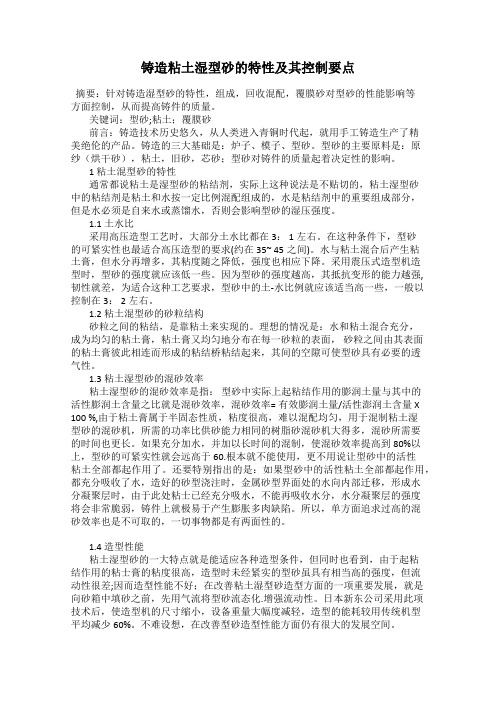
铸造粘土湿型砂的特性及其控制要点摘要:针对铸造湿型砂的特性,组成,回收混配,覆膜砂对型砂的性能影响等方面控制,从而提高铸件的质量。
关键词:型砂;粘土;覆膜砂前言:铸造技术历史悠久,从人类进入青铜时代起,就用手工铸造生产了精美绝伦的产品。
铸造的三大基础是:炉子、模子、型砂。
型砂的主要原料是:原纱(烘干砂),粘土,旧砂,芯砂;型砂对铸件的质量起着决定性的影响。
1 粘土混型砂的特性通常都说粘土是湿型砂的粘结剂,实际上这种说法是不贴切的,粘土湿型砂中的粘结剂是粘土和水按一定比例混配组成的,水是粘结剂中的重要组成部分,但是水必须是自来水或蒸馏水,否则会影响型砂的湿压强度。
1.1 土水比采用高压造型工艺时,大部分土水比都在3: 1左右。
在这种条件下,型砂的可紧实性也最适合高压造型的要求(约在35~ 45之间)。
水与粘土混合后产生粘土膏,但水分再增多,其粘度随之降低,强度也相应下降。
采用震压式造型机造型时,型砂的强度就应该低一些。
因为型砂的强度越高,其抵抗变形的能力越强, 韧性就差,为适合这种工艺要求,型砂中的土-水比例就应该适当高一些,一般以控制在3: 2左右。
1.2 粘土混型砂的砂粒结构砂粒之间的粘结,是靠粘土来实现的。
理想的情况是:水和粘土混合充分,成为均匀的粘土膏,粘土膏又均匀地分布在每一砂粒的表面,砂粒之间由其表面的粘土膏彼此相连而形成的粘结桥粘结起来,其间的空隙可使型砂具有必要的透气性。
1.3 粘土湿型砂的混砂效率粘土湿型砂的混砂效率是指:型砂中实际上起粘结作用的膨润土量与其中的活性膨润土含量之比就是混砂效率,混砂效率= 有效膨润土量/活性澎润土含量 X 100 %,由于粘土膏属于半固态性质,粘度很高,难以混配均匀,用于混制粘土湿型砂的混砂机,所需的功率比供砂能力相同的树脂砂混砂机大得多,混砂所需要的时间也更长。
如果充分加水,并加以长时间的混制,使混砂效率提高到80%以上,型砂的可紧实性就会远高于60.根本就不能使用,更不用说让型砂中的活性粘土全部都起作用了。
粘土湿型砂的控制要点

粘土湿型砂的控制要点粘土湿型砂在铸造工艺中起着重要的作用,控制好粘土湿型砂的质量是确保铸件质量和生产效率的关键。
以下是控制粘土湿型砂质量的要点:1. 选择合适的粘土湿型砂配方:根据铸件的要求和工艺要求,选择合适的粘土种类和比例。
不同的粘土具有不同的粘结性和流动性,要根据具体情况进行选择,保证铸件的表面光滑度和精度。
2. 严格控制水分含量:粘土湿型砂中的水分含量对于浇铸过程和铸件的表面质量有着重要影响。
过少的水分会导致砂型难以成型和裂纹的产生,过多的水分则会造成砂型的变形和铸件的表面缺陷。
因此,要通过严格控制水分含量来确保砂型的强度和铸件的质量。
3. 控制粘度和流动性:粘度和流动性是粘土湿型砂的两个重要指标,直接影响到砂型的成型性能和浇注的顺利进行。
通过控制粘土的粒度分布、粘接剂的种类和比例等因素,调整粘土的粘度和流动性,确保砂型的成型质量和铸件的形状精度。
4. 保证砂型的干燥性能:粘土湿型砂在使用前需要进行干燥处理,以去除多余的水分。
因为湿度高的砂型易造成铸件内部气孔,降低铸件的强度和表面质量。
因此,在干燥处理过程中,要严格控制砂型的干燥温度和时间,确保砂型的干燥性能。
5. 严格控制砂型质量:粘土湿型砂的质量对于铸件的成型质量和表面质量至关重要。
因此,要定期进行砂型的质量检测,包括外观检查、尺寸测量、强度测试等。
对于不合格的砂型,要及时进行处理或更换,以保证生产的正常进行。
6. 做好砂型的储存和保管:在使用粘土湿型砂的过程中,要做好砂型的储存和保管工作。
砂型应放置在干燥、通风的环境中,避免接触水分和其他污染物。
同时,要定期检查砂型的保存状态,及时处理发现的问题,以保证下次使用时的质量。
通过以上的控制要点,可以有效地提高粘土湿型砂的质量,确保铸件的表面质量和生产效率的提升。
粘土湿型砂在铸造工艺中扮演着重要的角色,其质量的控制直接影响到铸件的成型质量和表面质量。
为了保证粘土湿型砂具备良好的流动性和粘结性,需要在配方设计、水分控制、粘土颗粒分布、干燥处理、质量检测以及储存保管等方面进行精细的控制。
浅谈粘土湿型砂性能指标及科学管理
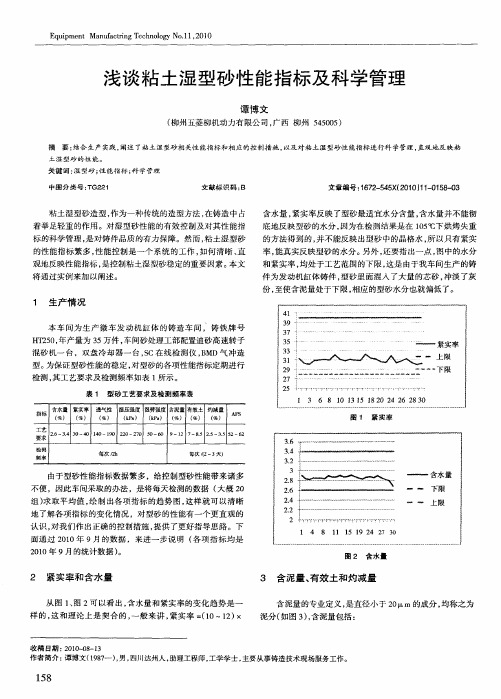
土 湿 型砂 的性 能 。
关键 词 : 型砂 ; 能 指 标 ; 学 管 理 湿 性 科 中 国分 类 号 :G2 1 T 2 文 献标 识 码 : B
交 童 编 号 :6 2 5 5 ( 0 0J1 O 5 — 3 17— 4 X 2 1 一 18 0 1
粘土湿型砂造 型 , 作为一种传 统的造型方法 , 在铸造 中 占 着举足轻重 的作用 。对湿 型砂性能的有效控制及对其性能指 标的科学 管理 , 是对 铸件品质 的有力保障。然而 , 粘土湿型砂
对 型砂 性 能 和 铸 件 品 质 将 起 到 很好 的 帮 助 ,所 以选 用 优 质 的
灼 减 量 来 测 量 有 效 煤 粉 含 量 的 ,也 有 厂 家 通 过 测 定 发 气 量 来 反映 ) ; ( ) 效 组 分— — 经 浇 注 烧 损 的死 膨 润 土 和 死 煤 粉 , 润 2 无 膨 土 、 粉 、 砂 里 的灰 分 , 及 细 小 的 砂粒 。 煤 新 以
面通 过 2 1 0 0年 9 的 数 据 ,来 进 一 步 说 明 ( 项 指 标 均 是 月 各
21 00年 9月的统计数据 ) 。
图 2 含 水 量
2 紧实 率和含水 量
从 图 1图 2可 以看 出 , 、 含水量和紧实率的变化趋势是 一 样的 , 这和理论 上是契合 的 , 一般来讲 , 紧实率 = 1 ( 0~1 ) 2X
18 5
《 装备制造技术) 00 ) 1 年第 1 期 2 1
( ) 效 组 分— — 有 效 膨 润 土 、 效 煤 粉 ( 车 问 是 通 过 1有 有 本
为 微 车 发 动 机 铸 件 , 质 量 相 对 较 小 , 且 砂 箱 较 大 , 铁 比 净 并 砂 为 7 1 经 测 量 , 润土 烧 损 为 05 煤 粉 烧损 为 01 % , 加 :, 膨 .%, . 3 补 量 相 当之 少 , 与我 们 的 砂 铁 比大 、 用 优 质 的膨 润 土 和 煤 粉 这 选 有 很 大 的关 系 。 烧 损 少 , 意 味 着 型 砂 里 面 的无 效 灰 分 少 , 就 这
黏土湿型砂的性能要求

黏土湿型砂的性能要求为了制造出合格的砂型和砂芯,黏土湿型砂应具有良好的常温工艺性能,如湿度、流动性、强度、可塑性与韧性、不粘模性等。
液态合金浇入铸型后,与型腔表面砂层之间发生着机械作用、热作用和化学作用。
机械作用是指液态合金充填过程中对腔壁的动压力和静压力,合金液凝固收缩时对铸型产生的压应力。
热作用是由于合金液与铸型腔存在着很大的温差,型腔壁被强烈加热,靠近合金液的型腔表面加热特别严重,局部甚至开裂或烧结。
化学作用是液态合金及其氧化物与型腔表面的砂层发生化学反应。
因此黏土湿型砂应具有良好的高温性能,如耐火度、发气性、热膨率、溃散性、退让性等。
下面分别简述这些主要性能。
1)湿度(水分)为了得到所需的可塑性、韧性和湿态强度,黏土湿型砂必须含有适量水分。
生产现场判断型砂湿度有以下几种方法:有丰富经验的混砂和造型工人常根据手捏型砂是否容易捏成闭和是否粘手来判断型砂的干湿程度;还可根据捏紧的动作中型砂是否柔软和变形情况来判断型砂的可塑性;根据手指掐碎砂团时用力大小判断型砂的湿强度是否合适。
如果用手捏砂时,只有潮的感觉,不觉得沾手,且柔和,印在砂团上手指痕迹清晰,那这样的型砂干湿度就比较合适。
2)流动性型(芯)砂在外力或自重作用下,沿模样(或芯盒表面)和砂粒间相对移动的能力称为流动性。
流动性好的型砂可形成紧实度均匀、无局部疏松、轮廓清晰、表面光洁的型腔,这有助于防止机械粘砂,获得光洁铸件。
此外,还能减轻型砂紧实时的劳动强度,提高生产率和便于实现造型、制芯过程的机械化。
3)强度型砂必须具备一定的强度以承受各种外力的作用,如果强度不足,在起模、搬运砂型、下芯、合型等过程中,铸型有可能破损塌落;浇注时可能承受不住金属液的冲刷和冲击,冲坏砂型而造成砂眼缺陷,或者造成胀砂(铸件肿胀)或跑火(漏铁液)等现象。
但是强度也不宜过高,因为高强度的型砂需要加入更多的黏土,不但增加了水分需求量,降低了砂型透气性,还会使铸件的生产成本增加,而且给混砂、紧实砂型和落砂等工序带来困难。
砂型铸造-湿型铸造之欧阳法创编

砂型铸造-湿型铸造1 概述粘土砂型可分为湿型、干砂型和表面烘干砂型。
三者之间的主要差别在于:湿型是造好的砂型不经烘干,直接浇入高温金属液体;干砂型是在合箱和浇注前将整个砂型送入窑中烘干;表面烘干砂型只在浇注前对型腔表层用适当方法烘干一定深度(一般5~10mm,大件20mm以上)。
目前,湿型砂是使用最广泛的、最方便的造型方法,大约占所有砂型使用量的60~70%,但是这种方法还不适合很大或很厚实的铸件。
表面烘干型与干型比,可节省烘炉,节约燃料和电力,缩短生产周期,所以曾在中型和较大型铸铁件的生产中推广过。
通常采用较粗砂粒(使有高的透气性),加入较多粘土和水分,有时还在型砂中加1~2%的木屑(提高抗夹砂结疤能力),其型腔表面必须涂敷涂料。
干型主要用于重型铸铁件和某些铸钢件,为了防止烘干时铸型开裂,一般在加入膨润土的同时还加入普通粘土。
干型主要靠涂料保证铸件表面质量。
其型砂和砂型的质量比较容易控制,但是砂型生产周期长,需要专门的烘干设备,铸件尺寸精度较差,因此,近些年的干型,包括表面烘干的粘土政型已大部分被化学粘结的自硬砂型所取代。
2 湿型铸造2.1湿型铸造特点湿型铸造法的基本特点是砂型(芯)无需烘干,不存在硬化过程。
其主要优点是生产灵活性大,生产率高,生产周期短,便于组织流水生产,易于实现生产过程的机械化和自动化;材料成本低;节省了烘干设备、燃料、电力及车间生产面积;延长了砂箱使用寿命等。
但是,采用湿型铸造,也容易使铸件产生一些铸造缺陷,如:夹砂、结疤、鼠尾、粘沙、气孔、砂眼、胀砂等。
随着铸造科学技术的发展,对金属与铸型相互作用原理的理解更加深刻;对型砂质量的控制更为有效;加上现代化砂处理设备使型砂质量得到了一定保证;先进的造型机械使型砂紧实均匀,起模平稳,铸型的质量较高,促进了湿型铸造方法应用范围的扩大。
例如汽车、拖拉机、柴油机等工业中,质量在300~500kg以下的薄壁铸铁件,现都已成功地采用湿型铸造。
粘土湿型砂及其质量控制

粘土湿型砂及其质量控制一粘土湿型砂的特点湿型砂主要由原砂、膨润土、附加物(煤粉、淀粉等)和水组成。
造型过程中,型砂捣实并达到一定紧实度后,形成砂型。
粘土湿型砂的结构示意图通常使用的硅砂,来源广,便宜,耐火度高。
另一方面,原砂砂粒能为砂型(芯)提供众多孔隙,保证型、芯具有一定的透气性,在浇注时,使型内产生的大量气体顺利逸出。
湿型砂按在造型时的情况,可分为面砂、背砂和单一砂。
二粘土湿型砂用的原材料1 硅砂1)硅砂种类及其SiO2含量天然硅砂河砂、湖砂、、海砂(牟平)、风积砂(大林、围场)。
人工硅砂由硅石岩、硅砂岩采矿、清洗、破碎、筛选加工而成。
硅砂的SiO2含量及不同用途铸铁用砂SiO2≥85%;铸钢用砂SiO2≥95%。
2)石英的结构转变特性石英为硅氧四面体,相变温度:573℃时产生体积膨胀,易夹砂。
870℃时也产生相变,故烧过此温度后,用于复膜砂。
3)硅砂的杂质长石、云母、氧化铁、碳酸盐及粘土,均降低(1)耐火度。
4)硅砂的含泥量原砂含有的直径小于0.02mm的颗粒,其质量分数称为原砂的含泥量。
5)硅砂的粒度和表示方法例如:三筛>75%,40/70;四筛>85%,50/1406)硅砂的颗粒形状和角形因数颗粒较圆(角形因数小)的砂粒,型砂的流动性好,紧实密度较高,透气性好。
2膨润土粘土的主要成分是水化硅酸铝(mAl2O3.SiO2.xH2O)。
晶体结构有两层型(高岭土,即普通粘土),三层型(蒙脱石,即膨润土)。
和普通粘土相比,膨润土有较大的吸水膨胀性、胶体分散性、、吸附性、离子交换性和湿态粘结性能。
故多用于湿型砂。
膨润土在500-700℃时失去结构水,加热到800℃以上时,晶格破坏,失去粘结作用。
膨润土分钙基膨润土和钠基膨润土,钠基膨润土在水分较高时仍有较好的强度,即具有较高的热湿拉强度和抗夹砂能力。
铸造用膨润土按工艺试样湿压强度值分为4级,,热湿拉强度值也分为4级。
(2)各种牌号的铸造用膨润土,其吸附亚甲基蓝量每100克至少应在20克以上;水分不大于12%,膨润土的95%应通过200号铸造用试验筛。
粘土湿型砂的控制要点之欧阳音创编

粘土湿型砂的控制要点用粘土粘结砂作造型材料生产铸件,是历史悠久的工艺方法,也是应用范围最广的工艺方法。
说起历史悠久,可追溯到几千年以前;论其应用范围,则可说世界各地无一处不用。
值得注意的是,在各种化学粘结砂蓬勃发展的今天,粘土湿型砂仍是最重要的造型材料,其适用范围之广,耗用量之大,是任何其他造型材料都不能与之比拟的。
据报道,美国钢铁铸件中,用粘土湿型砂制造的占80%以上;日本钢铁铸件中,用粘土湿型砂制造的占73%以上。
适应造型条件的能力极强,也是粘土湿型砂的一大特点。
1890年震压式造型机问世,长期用于手工造型条件的粘土湿型砂,用于机器造型极为成功,并为此后造型作业的机械化、自动化奠定了基础。
近代的高压造型、射压造型、气冲造型、静压造型及无震击真空加压造型等新工艺,也都是以使用粘土湿型砂为前提的。
各种新工艺的实施,使粘土湿型砂在铸造生产中的地位更加重要,也使粘土湿型砂面临许多新的问题,促使我们对粘土湿型砂的研究不断加强、认识不断深化。
现今,随着科学技术的速发展,各产业部门对铸件的需求不断增长,同时,对铸件品质的要求也越来越高。
现代的铸造厂,造型设备的生产率已提高到前所未有的水平,如果不能使型砂的性能充分适应具体生产条件,或不能有效的控制其稳定、一致,则不用多久就可能将铸造厂埋葬于废品之中。
随着科学技术的发展,目前采用粘土湿型砂的铸造厂,一般都适合其具体条件的砂处理系统,其中包括:旧砂的处理、新砂及辅助材料的加入、型砂的混制和型砂性能的监控。
粘土湿砂系统中,有许多不断改变的因素。
如某一种或几种关键性能不能保持在控制范围之内,生产中就可能出现问题。
一个有效的砂处理系统,应能监控型砂的性能,如有问题,应能及时加以改正。
由于各铸造厂砂处理系统安排不同,选用的设备也不一样,要想拟定一套通用的控制办法是做不到的。
这里,打算提出一些目前已被广泛认同的控制要点。
各铸造厂认真地理解了这些要点之后,可根据自己的具体条件确定可行的控制办法。
泥工施工技术交底之欧阳治创编

8mm
标
高
层高
±10mm
全高
±30mm
截面尺寸
8mm -5mm
表面平整度
5mm
3.2、垫层施工质量保证措施:垫层面标高允许偏差为±20mm。垫层表面应平整,无低洼。
3.3、认真做好现场施工记录和交接班工作,严格防止低强度等级砼流入高强度等级砼区域,可允许部分高强度等级砼流入低强度等级砼区域。
2.4.1、振捣时,遵循“快插慢拔”的原则,按顺序振动,振动捧插入砼的间距300,振点呈梅花形布置,砼振捣采用高频率插入式振动机,振捣时间以不再有气泡冒出及混凝土不再沉陷为准。每个出料口配备四只插入式振动器及专职机修工。
2.4.2、加强对钢筋集中部位的混凝土振捣,确保密实。振动机插入时,不宜碰撞钢筋、埋件、模板。
2.5、混凝土泵送
2.5.1、砼泵送过程要保持连续泵送,避免中断,而造成砼离析,堵塞泵管;砼不能及时供应时,要降低泵送速度,作间隔推动,间隔时间控制在15分钟左右,确保泵管不被堵塞。泵送过程中严禁向混凝土中加水。当混凝土坍落度低于控制下限制而不易施工时,在搅拌筒快转2分钟后方可卸料。
2.5.2、夏季泵送砼,泵的受料斗及泵管要用麻袋包裹,并浇水湿润,必要时,在泵车受料斗上方搭设遮阳棚。气温在35℃以上不得浇砼
1.6、垫层完成后,即进行测量定位弹线,弹出各条轴线,并测出工程桩的位置偏差,及时申请质检站对桩基进行验收。
1.7、必须和防水施工单位配合好,不得延误项目部工期。
二、主体砼浇注
2.1、砼浇捣泵车及泵管布置由生产经理及总施工根据现场定,泥工班组配合做好浇注准备。
2.2、底顶板砼一次浇捣,施工时不得出现冷缝,振动机插点成梅花形,间距≤0.5m。顶板面标高严格按留在插筋上的标高点的标记,拉麻线,长尺刮平。在砼浇捣后2-3小时(砼初凝前),待砼表面稍收水后用木蟹进行打磨,起到压实和表面提浆作用。做到槎纹顺直、均匀,不留铁板印,用塑料扫把拉毛,为达到美观要求拉毛方向必须一致,特别是柱墙板插筋处须特别注意平整且标高准确,以免支模时下部缝隙不均匀或模板放不进。砼达到1.2Mpa强度后才能上人施工。
湿型砂质量控制

湿型砂质量控制
刘承尧
【期刊名称】《现代铸铁》
【年(卷),期】1989(000)003
【摘要】对粘土的选用、型砂调匀水、混砂机和混砂工艺的选择和确定、粘土和新砂的补充量以及型砂温度等方面作了分析和阐述.
【总页数】5页(P56-59,61)
【作者】刘承尧
【作者单位】东南大学
【正文语种】中文
【中图分类】TG25
【相关文献】
1.粘土湿型砂处理系统的在线检测及质量控制 [J], 吴毅
2.静压造型生产线湿型砂质量控制探索 [J], 张娜;吴来发;孙洪超
3.粘土湿型砂技术讲座第四讲粘土湿型砂的强度 [J], 李传栻
4.粘土湿型砂技术讲座第五讲粘土湿型砂的调制 [J], 李传栻
5.《粘土湿型砂及其质量控制》 [J],
因版权原因,仅展示原文概要,查看原文内容请购买。
- 1、下载文档前请自行甄别文档内容的完整性,平台不提供额外的编辑、内容补充、找答案等附加服务。
- 2、"仅部分预览"的文档,不可在线预览部分如存在完整性等问题,可反馈申请退款(可完整预览的文档不适用该条件!)。
- 3、如文档侵犯您的权益,请联系客服反馈,我们会尽快为您处理(人工客服工作时间:9:00-18:30)。
粘土湿型砂的控制要点欧阳光明(2021.03.07)用粘土粘结砂作造型材料生产铸件,是历史悠久的工艺方法,也是应用范围最广的工艺方法。
说起历史悠久,可追溯到几千年以前;论其应用范围,则可说世界各地无一处不用。
值得注意的是,在各种化学粘结砂蓬勃发展的今天,粘土湿型砂仍是最重要的造型材料,其适用范围之广,耗用量之大,是任何其他造型材料都不能与之比拟的。
据报道,美国钢铁铸件中,用粘土湿型砂制造的占80%以上;日本钢铁铸件中,用粘土湿型砂制造的占73%以上。
适应造型条件的能力极强,也是粘土湿型砂的一大特点。
1890年震压式造型机问世,长期用于手工造型条件的粘土湿型砂,用于机器造型极为成功,并为此后造型作业的机械化、自动化奠定了基础。
近代的高压造型、射压造型、气冲造型、静压造型及无震击真空加压造型等新工艺,也都是以使用粘土湿型砂为前提的。
各种新工艺的实施,使粘土湿型砂在铸造生产中的地位更加重要,也使粘土湿型砂面临许多新的问题,促使我们对粘土湿型砂的研究不断加强、认识不断深化。
现今,随着科学技术的速发展,各产业部门对铸件的需求不断增长,同时,对铸件品质的要求也越来越高。
现代的铸造厂,造型设备的生产率已提高到前所未有的水平,如果不能使型砂的性能充分适应具体生产条件,或不能有效的控制其稳定、一致,则不用多久就可能将铸造厂埋葬于废品之中。
随着科学技术的发展,目前采用粘土湿型砂的铸造厂,一般都适合其具体条件的砂处理系统,其中包括:旧砂的处理、新砂及辅助材料的加入、型砂的混制和型砂性能的监控。
粘土湿砂系统中,有许多不断改变的因素。
如某一种或几种关键性能不能保持在控制范围之内,生产中就可能出现问题。
一个有效的砂处理系统,应能监控型砂的性能,如有问题,应能及时加以改正。
由于各铸造厂砂处理系统安排不同,选用的设备也不一样,要想拟定一套通用的控制办法是做不到的。
这里,打算提出一些目前已被广泛认同的控制要点。
各铸造厂认真地理解了这些要点之后,可根据自己的具体条件确定可行的控制办法。
而且,还要随着技术的进步和工厂的实际能力(包括人员和资金)不断改进对型砂系统的控制。
一.旧砂的处理用粘土湿型砂造型,浇注以后,除贴近铸件的部分型砂中活性膨润土受热失效成为死粘土外,大部分型砂可以回收使用。
这是粘土湿型砂的主要优点之一。
配制粘土湿型砂时,旧砂用量一般都在90%以上,如果对旧砂的处理不当,无论怎样加强混砂,无论添加什麽辅助材料,都不可得到好的型砂。
所以,对旧砂进行有效的处理,是保证型砂质量的前提。
1.旧砂温度的控制热砂问题,已被公认为粘土湿型砂铸造必须面对的最大问题。
型砂温度太高,铸件容易产生夹砂、表面粗糙、冲砂、气孔等缺陷。
热砂对铸件质量的负面影响,主要由于以下几个方面:・由于热砂使水分蒸发,混砂时无论怎样注意,也难以控制型砂的性能;・将热型砂送往造型机的过程中,由于水份损失,型砂性能改变,造型时实际上用的型砂,其性能与混砂时控制的性能差别很大;・造型时,热型砂的水分容易在模样表面上凝结,型砂粘模;・合型后,热砂的水分蒸发,凝结在冷的芯子上,会使芯子的强度降低,铸件也易于产生气孔;・如果旧砂要贮存在砂斗中备用,则热砂容易粘附在砂斗壁上。
严重时,砂斗四周堵满了型砂,只剩中间一个孔洞,使系统中的型砂只有一部分周期使用,这部分型砂周转快、温度又会进一步提高,使热砂问题更加严重。
多高温度的砂算是热砂?判断热砂的温度界限,是看其是否使混砂、造型及铸件质量方面出现问题。
对此,许多研究者从个方面进行了研究;有人研究了型砂温度对其性能稳定性的影响;有人研究了温度对膨润土-水系统流变性的影响;有人研究了型砂温度与铸件质量的关系。
各方面的研究,得到了一致的结论,即:为保证型砂的性能稳定,温度应保持在50℃以下。
使型砂冷却,最有效的办法是加水,但是,简单的加水,效果是很差的。
一定要吹入大量空气使水分蒸发,才能有效地冷却。
以下,给出一个简略的计算比较:型砂的比热大致是:9.22×102J/kg・℃,水的比热是:4.19×103J/kg・℃,水的蒸发热是:2.26×106J/kg,1吨砂中加20℃的水10kg(加水1%),使其温度升到50℃,所能带走的热量为4.19×103×10×30,即12.57×105J。
1吨砂温度降低1℃,需散热9.22×102×1000 J,即9.22×105 J。
所以,在旧砂中加水1%,只能使温度降低24.5℃。
使1吨砂中的水分蒸发1%(10kg),能带走的热量为2.26×107J,却可使砂温降低24.5℃。
以上的分析表明:简单地向皮带机上加水或向砂堆洒水,冷却效果是很差的。
即使加水后向砂表面吹风,也不能有多大的改善。
加水后,要使水在型砂中分散均匀,然后向松散的砂吹风,使水分迅速蒸发,同时将蒸汽排除。
目前,型砂冷却装置的品种、规格很多,主要有冷却滚筒、双盘冷却器和冷却沸腾床等,都是利用水分蒸发冷却型沙。
其中,冷却沸腾床效果较好。
2.旧砂的水分控制几乎所有的铸造厂都检查和控制混成砂的水分,但是,对于严格控制旧砂水分的重要性,很多铸造厂的领导和技术人员还缺乏足够的认识。
进入混砂的旧砂水分太低,对混砂质量的影响可能并不亚于砂温过高。
试验研究和经验都已证明,加水润湿干膨润土比润滑湿膨润土难得多。
型砂中的膨润土和水,并非简单的混在一起就行,要对其加搓揉,使之成为可塑状态。
这就像用陶土和水制陶器一样,将水和土和一和,是松散的,没有粘接能力;经过搓揉和摔打,使每粒土都充分吸收了水分,就成为塑性状态,才可以成形,制成陶器毛坯。
铸型浇注以后,由于热金属的影响,很多砂粒表面上的土-水粘结膜都脱水干燥了,加水使其吸水恢复塑性是很不容易的。
旧砂的水分较低,在混砂机中加水混碾使之达到要求性能所需要的时间就越长。
由于生产中混砂的时间是有限的,旧砂的水分越低,混成砂的综合质量就越差。
目前,各国铸造工作者已有了这样一种共识:进入混砂机的旧砂,水分只能比混成砂略低一点。
较好的做法是:在旧砂冷却过程中充分加水冷却后所含的水分略低于混成砂。
这样,从砂冷却到进入混砂机还有一段相当长的时间,水可以充分润湿旧砂砂粒表面上的膨润土。
更好的做法是:在系统中设混砂机对旧砂进行预混,冷却后的旧砂在预混混砂机中加水进行预混,以改善旧砂中膨润土和水的混合状态。
国外,有的铸造厂预混时,将需补加的新砂、膨润土、煤粉等附加料全部加入。
天津的新伟祥铸造公司,用德国制造的EiRich混砂机预混。
经过预混的旧砂,进入混砂机后加水量很少,只是略微调整。
型砂中的膨润土和水在混砂机进一步得到调制,型砂的性能就更为稳定一致。
3.旧砂的粒度对于用粘土湿型砂制造的铸铁件,型砂的粒度以细一些为好。
由于混砂时旧砂用量一般都在90%以上,决定型砂粒度的因素主要是旧砂。
新砂加入量很少,不可能靠加入新砂来改变型砂的粒度。
所以,应该经常检测旧砂的粒度。
检测粒度时,取样后先清洗除去泥分(可用测定含泥量时剩下的砂样),烘干后筛分。
对粒度有以下两点要求。
(1)140目筛上的砂粒应在10-15%之间。
保持较多的细砂,可以减轻铸件表面粘砂。
而且,会增加砂粒之间粘结桥的数量,从而降低型砂的脆性,避免冲砂缺陷。
此外,这对提高型砂的温强度、干强度和水分迁移后增湿层强度都有好处。
(2)200目筛、270目筛和底盘上细砂的总和应尽量地少。
这样的细砂对改善铸件表面质量的作用不大,却会使混成砂的水分较高,而且会使型砂的透气性降低。
细砂的总和一般应少于4%。
4.吸水细粉的含量吸水细粉中主要是死粘土,还包括焦化了的煤粉细粒和其他细粉。
吸水细粉的含量并非越低越好,最好将其控制在2-5%之间。
吸水细粉,混砂时会和膨润土争夺水分,使混成砂达到可紧实性目标值所需的水分增高。
但是,据目前大家的认识,吸水细粉的吸水能力比膨润土强,而保持水分的能力却低于膨润土。
因此,在型砂中加水量略有不当时,吸水细粉对型砂性能有一定的"微调和稳定"作用。
水分高时,细粉首先吸水,膨润土所吸收水可较稳定一致;混成砂在输送过程中水分蒸发时,吸水细粉所吸的水先蒸发,粘结砂粒的粘土膏中的水分较为稳定,型砂的性能也就较小波动。
吸水细粉含量太高也不好,会使型砂的水分较高,易于导致铸件上产生针孔、表面粗糙和砂孔的缺陷。
吸水细粉含量太低,则型砂的性能(尤其是可紧实性)不易稳定。
二.补加新砂及辅助材料粘土湿型砂在系统中反复使用,由于铸件粘附的砂粒被带走,部分膨润土受热成为死粘土,煤粉受热失效以及抽尘系统吸走粉状材料等因素,补加新材料以保持系统砂的总量稳定、性能一致是绝对必要的。
这里,只简单谈谈各种材料补加量的确定,不想罗列各种材料的规格。
1、新砂用新砂配成的型砂,是简单的混合物。
在生产条件下,混砂时间不可能很长,膨润土和水形成的粘土膏不可能均匀涂布在砂粒表面上,砂粒的结构见图1(a)。
反复使用的旧砂,砂粒结构见图1(b),砂粒表面上积了多层变质烧结层,粘土膏的涂布则相当均匀。
图1 粘土湿型砂的砂粒结构因此,混砂时补加的新砂不宜太多,以保持系统砂总量稳定为原则。
新砂加入量太多,会对型砂质量有负面的影响。
国外一些运转良好的型砂系统,新砂补加量一般是每浇注1吨铁水120~150kg。
如考虑砂-铁比平均为5,则混砂时新砂补加量为2.6~3%。
当然,新砂补加量还要考虑很多因素,如设备条件,芯砂进入量。
很多铸造厂要根据自己的条件确定,外厂的经验只能参考。
我国铸造厂一般散落砂都较多,很多厂新砂补加量为5-8%,这也是合适的。
也有少数铸造厂以为多家新砂可以提高型砂质量,这种想法可能来自旧砂完全没有处理、生产量又小的条件。
2、膨润土和其他黏结剂相比,膨润土有一个重要的特点,就是它具有一定的耐热能力。
只要加热温度不太高,脱除了自由水的膨润土只要加水,仍能恢复粘能力。
不同的膨润土,丧失粘结能力的温度不同。
通过一系列加热试验和差热分析实验,得知天然钠膨润土的失效温度为638℃,钙膨润土为316℃。
人工活化的钠膨润土,由于活化条件各异,准确的失效温度不详。
据日本报道的实验结果,人工活化的钠膨润土,在最初使用时,失效温度略低于天然钠膨润土;几次反复加热后,就与钙膨润土相近,其"耐用性"不佳。
(1)膨润土中水的形态活性膨润土的粘结能力,只有在加水以后才能表现出来。
膨润土失去粘结能力,也与它的脱水有关。
到目前为止,认为膨润土中的水分有三种形态。
一种是自由水,即膨润土颗粒吸附的水。
加热到100℃以上,就可脱除自由水。
脱除了自由水的膨润土,粘结能力不受影响。
第二种是牢固结合水。
将膨润土置110℃下长时间加热,可完全脱除自由水,但但不会脱除牢固结合水。