特种加工第二章电火花加工(1)
特种加工工艺1
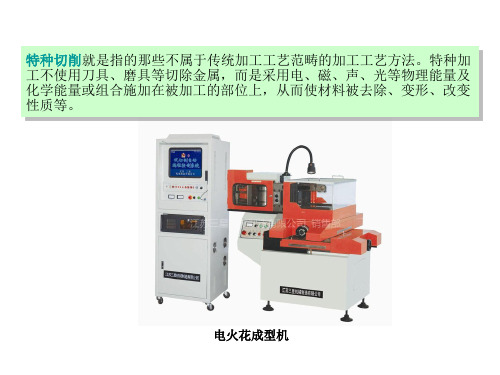
影响激光加工的主要因素如下:
⑴激光加工的机械系统和光学系统的精度; ⑵激光的输出功率与照射时间的乘积等于激光束的能量; ⑶焦距、发散角和焦点位置对打孔的大小、深度和形状的影响 ⑷照射次数多可使孔深大大增加; ⑸光斑内的能量分布对打孔的形状有直接影响; ⑹工件材料不同,影响加工效率。
①不易达到较高的加工精度和加工稳定性; ②电解加工的附属设备比较多; ③电解产物需要进行妥善处理,否则会污染环境。
1——直流电源化气 3——工具 5——电解液泵
2——进给机构 4——工件
6——电解液
二、电解加工的应用
主要用于切削加工困难的领域,广泛应用于以下几个方面:
⒈叶片加工 ⒉型孔和型腔加工 ⒊深孔扩孔加工 ⒋电解抛光
电火花加工工艺特点主要有:
⑴电火花加工是利用火花放电破坏材料的原理,因此这种方法可以加工任何导电 的材料,而不受材料硬度、韧性和脆性等限制。
⑵加工电极与工件不接触,没有切削力的影响。 ⑶电火花加工不需要复杂的切削运动,可以加工形状复杂的零件表面。 ⑷工具只是一个电极,常采用紫铜、黄铜或石墨等材料制成。
四、电子束加工
在真空条件下,利用电子 枪中产生的电子经加速、聚集, 形成高能量大密度的细电子束, 以轰击工件被加工部位,使该 部件的材料熔化和蒸发,从而 进行加工。
⑴电子束能够极其微细地聚集; ⑵加工速度快; ⑶适用范围广; ⑷可通过磁场或电场进行控制。
五、磨料喷射加工
用高速射流来喷射磨粒, 使微小的磨粒在射流的驱动下 达到很高的速度,利用高速磨 粒的功能对工件进行加工。
特种切削就是指的那些不属于传统加工工艺范畴的加工工艺方法。特种加 工不使用刀具、磨具等切除金属,而是采用电、磁、声、光等物理能量及 化学能量或组合施加在被加工的部位上,从而使材料被去除、变形、改变 性质等。
《精密加工与特种加工》电火花加工,电解加工重点简答题.doc

1•什么是电火花加工?试简述其加工过程。
电火花加工又称放电加工(Electrical Discharge Machining, 简称EDM),是通过导电工件(包括半导体)和工具电极(正、负电极)之间脉冲性火花放电时的电腐蚀现象来蚀除多余材料,以达到对工件尺寸、形状及表面质量要求的加工技术。
加工过程大致可分为以下四个连续的阶段:1)极间介质的电离、击穿,形成放电通道;2)介质热分解、电极材料熔化与气化热膨胀;3)电极材料的抛出;4)极间介质的消电离。
2.为什么要及时排除电火花加工过程中产生的电蚀产物?加工过程中产生的电蚀产物(如金属微粒、碳粒子、气泡等)如果来不及排除、扩散出去,就会改变间隙介质的成分和降低绝缘强度,结果导致下一个脉冲放电通道不能顺利地转移到其它部位,而始终集中在某一部位,使该处介质局部过热而破坏消电离过程,脉冲火花放电将恶性循环转变为有害的稳定电弧放电,同时工作液局部高温分解后可能结炭,在该处聚成焦粒而在两极间搭桥,使加工无法进行下去,并烧伤电极对。
3.什么是电化学加工?试简述电化学加工的分类及其加工过程。
电化学加工(Electrochemical Machining,简称ECM)包括从工件上去除金属的电解加工和在工件上沉积金属的电铸加工两大类,属于通过电化学反应去除工件材料或在其上镀覆金属材料的非传统加工方法。
加工过程:用两片金属作为电极,通电并浸入电解溶液中,即可形成通路。
导线和溶液中均有电流通过。
此时在金属片和溶液的界面上产生交换电子的反应,即电化学反应。
若所接的电源是直流电,溶液中的离子便作定向移动,正离子移向阴极并在阴极上得到电子进行还原反应,沉积得到金属物质,称为镀覆沉积,即电铸(电镀、涂镀)加工;负离子将移向阳极并在阳极表面失掉电子,阳极金属原子失去电子而成为正离子进入溶液进行氧化反应为电解蚀除,即电解加工。
4.为什么说电化学加工过程中的阳极溶解是氧化过程,而阴极沉淀是还原过程?金属原子失去电子而成为正离子进入溶液(M—e=M+),化合价升高,为氧化反应;正离子移向阴极并在阴极上得到电子沉积得到金属物质(M++e=M),化合价降低,为还原反应。
特种加工技术第二章电火花加工

(5) 有适当的脉冲间隔时间,使放电介质有足够时间消 除电离并冲去金属颗粒,以免引起电弧而烧伤工件。
第二章 电火花加工的基本原理及设备 二、RC线路脉冲电源
这种电源是利用电容器充电储存电能,然后瞬时放出, 形成火花放电来蚀除金属的。因为电容器时而充电,时而放 电,一弛一张,故又称“弛张式”脉冲电源(如图2-11所示)。 由于这种电源是靠电极和工件间隙中的工作液的击穿作用来 恢复绝缘和切断脉冲电流的,因此间隙大小、电蚀产物的排 出情况等都影响脉冲参数,使脉冲参数不稳定,所以这种电 源又称为非独立式电源。
1.加工速度 体积加工速度υw(mm3/min) 即υw=V/t 质量加工速度υm(g/min)
第二章 电火花加工的基本原理及设备
提高加工速度的途径: 提高脉冲频率f; 增加单个脉冲能量WM ; 设法提高工艺系数K;
电火花加工速度: 粗 加 工 ( 表 面 粗 糙 度 Ra10-20μm ) 时 可 达 200-1000 mm3/min; 半精加工(Ra2.5-10μm)时可达20-100 mm3/min; 精加工(Ra0.32-2.5μm)时一般在10 mm3/min以下;
第二章 电火花加工的基本原理及设备
特种加工技术第二章电火花加工

第二章 电火花加工
定义: 在加工过程中,使工具和工件之间不断产生脉
冲性的火花放电,靠放电时局部、瞬时产生的高 温把金属蚀除下来。这种加工方法就叫电火花加 工。
第二章 电火花加工的基本原理及设备
第一节 电火花加工的基本原理及其分类
一、电火花加工的原理和设备组成 原理:基于工具和工件(正、负电极)之间脉冲性火花 放电时的电腐蚀现象来蚀除多余的金属,以达到对零件 的尺寸、形状及表面质量预定的加工要求。
第二章 电火花加工的基本原理及设备
三、电火花加工的工艺方法分类
按照工具电极和工件相对运动的方式和用途的不同,大 致分为六大类:
电火花穿孔成形加工
电火花线切割
电火花磨削和镗磨
电火花同步共轭回转加工
电火花高速小孔加工
电火花表面强化与刻字
前五种属于电火花成形、尺寸加工,改变零件形状或尺 寸;后一种属于表面加工,改善或改变零件表面性质。
电火花腐蚀的主要原因: 电火花放电时火花通道中瞬时产生大量的热,达到很高
的温度,足以使任何金属材料局部融化、气化而被蚀除 掉,形成放电凹坑。
第二章 电火花加工的基本原理及设备
要达到利用电腐蚀现象对金属材料进行尺寸加工的目的, 必须解决三个问题: 1)必须使工具电极和工件被加工表面之间经常保持一定 的放电间隙,通常为几微米至几百微米。 如果间隙过大,极间电压不能击穿极间介质,因而不会 产生火花放电;如果间隙过小,很容易形成短路接触, 同样不能产生火花放电。 在电火花加工过程中必须具有工具电极的自动进给和调 节装置,使和工件保持某一放电间隙。
其中电火花穿孔成型加工和电火花线切割应用最广泛。
第二章 电火花加工的基本原理及设备
特种加工第2章电火花

极性效应
极性效应是火花放电过程中一种重要现象,产 生这一现象的原因很复杂,通常对这一问题的解 释是:在火花放电过程中,正、负电极表面分别 受到负电子和正离子的轰击和瞬时热源的作用, 在两极表面所分配到的能量不一样,因而熔化、 气化抛出的电蚀量也不一样。
21
这是因为电子的质量和惯性均小,容易获得很高的加速 度和速度,在击穿放电的初始阶段就有大量的电子奔向正 极,把能量传递给阳极表面,使电极材料迅速熔化和气化; 而正离子则由于质量和惯性较大,起动和加速较慢,在击 穿放电的初始阶段,大量的正离子来不及到达负极表面, 到达负极表面并传递能量的只有一小部分离子。
2)可以加工特殊及复杂形状的表面和零件 没有机械加工的切削力,适宜加工低刚度工件及进行微细 加工。
3)易于实现加工过程自动化 直接利用电能加工,而电能、电参数较机械量易于实现数
字控制、适应控制、智能化控制和无人化操作等; 4)通过改进结构设计,改善零件结构的加工工艺性
8
2.局限性: 1)一般只能加工金属等导电材料; 2)加工速度一般较慢; 3)存在电极损耗; 4)最小角部半径有限制; 5)加工表面有变质层甚至微裂纹。
LOGO
第2章 电 火 花 加 工
(Electrical Discharge Machining简称EDM)
南华大学机电学院
1
2.1 电火花加工的概念及分类
2.1.1 电火花加工的基本原理 所谓电火花加工(Electrical Discharge Machine简称EDM)是指在介质中,利用两极(工 具电极与工件电极)之间脉冲性火花放电时的电腐 蚀现象对材料进行加工,使零件的尺寸、形状和 表面质量达到预定要求的加工方法。
22
❖ 在用短脉冲加工时,电子的轰击作用大于离子的轰击作用。 正极的蚀除速度大于负极的蚀除速度,这时工件应接正极。
特种加工习题

本文由liuhuikai1988贡献doc文档可能在WAP端浏览体验不佳。
建议您优先选择TXT,或下载源文件到本机查看。
电火花加工部分习题(1)一、名词解释:名词解释:1. 特种加工 2.极性效应二、判断题:判断题:1.从提高生产率和减小工具损耗角度来看,极性效应越显著越好,所以,电火花加工一般都采用单向脉冲电源。
(√) 2.电火花线切割加工中,电源可以选用直流脉冲电源或交流电源。
(×) 3.电火花加工是非接触性加工(工具和工件不接触),所以加工后的工件表面无残余应力。
(×) 4 特种加工中加工的难易与工件硬度无关。
( √ ) 5 电火花加工在实际中可以加工通孔和盲孔。
( √ ) 6 电火花成型加工时采用的手动侧壁修光方法可以修整圆形轮廓的型腔。
( × ) 7.冲油的排屑效果不如抽油好。
( × )三、填空题1、电火花加工是将电极形状(复制)到工件上的一种工艺方法。
2、冲模的电火花加工方法有(直接加工法)(间接加工法)(混、、合加工法)和(阶梯工具电极加工法)。
3、型腔模的电火花加工方法有(单电极平动法)单电极摇动法)、(、(多电极更换法)和(分解电极加工法)。
4、(放电间隙)是放电时工具电极和工件之间的距离。
5.电火花加工蚀除金属材料的微观物理过程可分为(介质电离击穿)(介质热分解、电极材料熔化、气化)(蚀除物抛出)和(间、、隙介质消电离)四个阶段。
6.电火花加工时用的电加工参数即电主要有(粗规准)(中规准)(精规准)。
7.电火花加工型腔工具电极常用的材料有:(纯铜)、(石墨)、(铜钨合金)等。
8.影响电火花加工精度的主要因素有:(放电间隙的大小)及其一致性、(工具电极的损耗)及其稳定性和(二次放电现象)。
9.电火花加工按工件和工具电极相对运动的关系可分为:电火花(穿孔成形加工)、电火花(线切割加工)、电火花(磨削和镗削加工)、电火花(同步共轭回转加工)、电火花(高速小孔加工)、电火花表面强化和刻字等类型。
特种加工复习纲要

特种加工复习纲要第二章电火花加工本章介绍了电火花加工的基本原理,电火花形成的条件,电火花加工的物理本质,电火花加工的基本规律,电火花加工设备的组成,电火花自动进给系统及其与机械切削,磨削进给系统的区别,电火花成型电极设计。
重点掌握:极性效应等概念,电火花加工的自动进给系统与传统车削,磨削进给系统的区别,电火花加工的四个物理过程,极性效应及其在电火花加工中如何利用极必效应,掌握如何根据工件设计电火花成型电极第三章电火花线切割加工本章介绍了电火花线切割的原理,特点,加工设备,线切割编程,影响线切割工艺的因素及其线切割加工的应用重点掌握:线切割加工类型快走丝慢走丝,线切割加工3B编程,线切割加工的工艺指标第四章电化学加工本章介绍了电化学加工原理及分类,电解加工,电解磨削以及电镀,电铸,电刷镀加工重点掌握:掌握电解磨削的概念,电化学极化,溶差极化的概念,常用的三种电解液,掌握电化学加工时阳极溶解,阴极沉积,掌握电解磨削加工与机械磨削加工及电解加工的区别第五章激光加工本章介绍了激光加工的原理及特点,激光加工设备的组成和激光加工工艺与应用重点掌握:激光产生的原理,粒子束反转的概念,常用的固体激光发生器和气体激光发生器以及这些激光发生器的工作介质必须掌握红宝石激光器的工作介质,第六章电子束和离子束加工本章介绍了电子束,离子束加工的原理,加工设备的组成及其应用(掌握电子束,离子束加工的原理,特点及其两者的区别,常用的离子束发生装置,离子束加工的分类,以及电子束,离子束的应用领域。
)必须掌握离子束发生装置的两种类型第七章超声加工本章主要介绍了超声波加工的原理及特点,超声波加工的设备及其组成部分,超声波加工的工艺参数及其影响因素,超声波加工的应用重点掌握超声波加工的概念、特点,超声加工设备的组成,换能器的种类,变幅杆的作用及类型,超声加工的工艺特点,超声加工的主要应用领域。
必须掌握超声波加工的概念,变幅杆的作用及其它在机床上的装夹位置,超声加工的材料硬度与加工速度的关系。
特种加工技术电火花加工技术
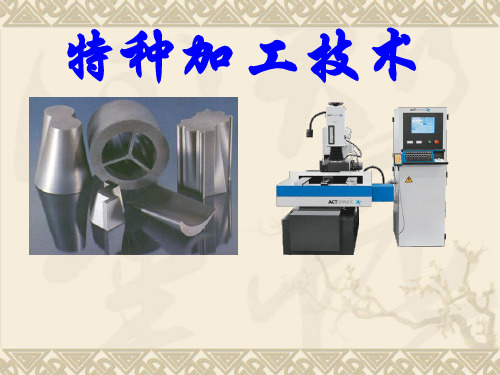
那么,两电极表面的金属材料 是如何被蚀除下来的呢?
电火花加工设备
电火花加工的原理 图2.3 电火花加工原理示意图 -1
3
2
4
5
6 1-工件
2-脉冲电源
7 3-自动进給调节装置
4-工具
1
5-工作液
6—过滤器
7—工作液泵
图2.4 电火花加工原理示意图-2
电火花加工是一个非常复杂的过程,其微观过程 是热力学、流体力学、电场力学、磁力学、电化学等 综合作用的结果。这一过程可分为以下四个阶段,见 图2.5 :
冲 上是被抛出的高温金属的熔滴和碎屑。 (a)
电
源
工件电极
(d)
(4) 极间介质的消电离
及残如余图的A(热e)量所带示走,,加并工迅液速流恢入复放到电绝间缘隙状,态将。电若蚀加产工物 过程中产生的电蚀产物来不及排除和扩散,产生的热 量将不能及时传出,使该处的介质局部过热。 B 局部过热的工作液高温分解、积炭,使加工无法 继续进行,并烧坏电极。因此,为了保证加工过程的 正常进行,在两次放电之间必须有足够的时间间隔让
有杂质及自由电子,它们在强大的电场作用 下,形成了带电粒子,电场强度越大,带电 粒子越多,最终导致液体介质电离、击穿, 形成放电通道。由于通道截面很小,通道内 因高温热膨胀形成的压力高达几万帕,产生 一个强烈的冲击波向四周传播。在放电的同 时还伴随着光效应和声效应,这就形成了我 们看到的电火花。
(2) 电极材料的熔化、气化热膨胀 如图 (b)、(c)所示,液体介质被电离、击穿, 形成放电通道后,通道间带负电的粒子奔向正极, 带正电的粒子奔向负极,粒子间的相互撞击,产生 大量的热能,使通道瞬间达到很高的温度。通道高 温首先使工作液液化,进而气化,然后高温向四周 扩散,使两电极表面的金属材料开始熔化,直至沸 腾气化。
特种加工-第二讲 电火花加工的基本原理及设备(1)
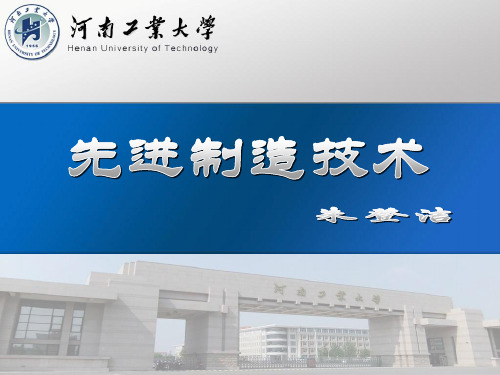
生
。高温高压
每一次火花放电,就会在工件表面蚀出一个带凸边的
。凹
坑
电火花加工中的蚀除产物,一部分以气态形式抛出,其余大部分
以
固体微粒分散悬浮在工作液中。球状
电火花加工和电火花线切割加工的原理是
。相同的
电火花加工 在一定的介质中,通过工具电极和工件电极之间的 脉冲放电的电蚀作用,对工件进行加工的方法。
降低温度;
一次火花放电过程大致分为以下几个阶段: 消除带电离子;
排出电蚀产物;
(4)极间介质的消电离(如图2.2(e)所示)。
防止碳搭桥;
图2.2 电火花一次放电过程
二、电火花(穿孔成形)加工、电火花线切割加工的特点 共同特点
(1)二者的加工原理相同,都是通过电火花放电产生的 热来熔化去除金属的,所以二者加工材料的难易与材料的硬 度无关,加工中不存在显著的机械切削力。
电极相互靠近时,极间形成脉冲性火花放电,在。
放电间隙0.01-0.1mm; 脉冲性放电;
图2.1 电火花加工原理
有绝缘介质;
加工过程 一次火花放电过程大致分为以下几个阶段:
(1)极间介质的电离、击穿,形成放电通道(如图2.2(a) 所示)。
第二讲 电火花加工的基本原理及设备(1)
一、电火花加工的物理本质 二、电火花加工、电火花线切割加工的特点 三、电火花机床型号与分类 四、电火花加工机床结构
N2+2O2===2NO2 化学反应条件:高温、高压
放 电 产 生:高温、高压
一、电火花加工的物理本质
物理本质 电火花加工基于电火花腐蚀原理,是在工具电极与工件
A、32mm
B、320mm
C、3200mm D、32000 mm
特种加工(章 (2)

第2章 电火花加工
图2-1 电火花加工原理示意图
第2章 电火花加工
图2-2 放电间隙状况示意图 (a)放电间隙状况;(b)放电后的表面
第2章 电火花加工
2.2.2 电火花加工的形成条件 利用电火花加工方法对材料进行加工应具备以下条件: (1)作为工具和工件的两极之间要有一定的距离(通常
为数微米到数百微米),并且在加工过程中能维持这一距离。 (2)两极之间应充入介质。对导电材料进行尺寸加工时,
第2章 电火花加工
2.1.2 (1)适合于任何难切削导电材料的加工。由于加工中材料
的去除是靠放电时的电热作用实现的,因此材料的可加工性主 要取决于材料的导电性及其热学特性,如熔点、沸点、比热容、 导热系数、电阻率等,而几乎与其力学性能(硬度、强度等)无 关。这样可以突破传统切削加工对刀具的限制,可以实现用软 的工具加工硬韧的工件,甚至可以加工超硬材料。目前,电极 材料多采用紫铜或石墨,因此工具电极较容易加工。
(5)脉冲放电需要不断地多次进行,并且每次脉冲放电 在时间上和空间上是分散的、不重复的。即每次脉冲放电一般 不在同一点进行,避免发生局部烧伤。
(6)脉冲放电后的电蚀产物能及时排运至放电间隙之外, 使重复性脉冲放电顺利进行。
第2章 电火花加工
2.2.3 电火花加工的机理 火花放电时,电极表面的金属材料究竟是怎样被蚀除下来
第2章 电火花加工
电火花加工在各行业的应用主要表现在: (1)可直接加工各种金属及其合金材料、特殊的热敏感 材料、半导体和非导体材料。 (2)可加工各种形状复杂的型孔和型腔工件,包括圆孔、 方孔、多边形孔、异形孔、曲线孔、螺纹孔、微孔等。 (3)可加工深孔等型孔工件及各种型面的型腔工件。 (4)可进行各种工件与材料的切割,包括材料的切断, 特殊结构工件的切断,切割微细窄缝及微细窄缝组成的工件, 如金属栅网、异型孔喷丝板、激光器件等。
特种加工技术 课件2
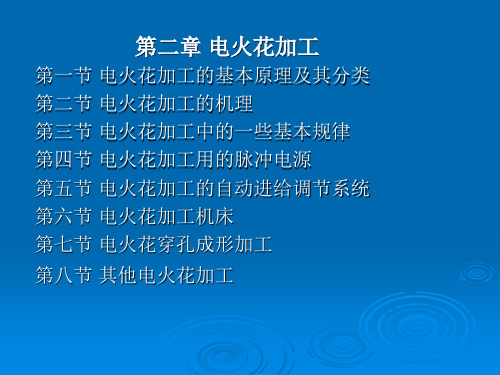
作业
1.电火花加工中的极性效应是什么?加工中 如何利用极性效应来提高加工效率降低工 具损耗? 2.电火花正常系统中为什么必须有自动进给 调节系统?
1.电火花加工过程中,无论是正极还是负极, 都会受到不同程度的电蚀,即使是相同的材 料,两极的电蚀量也不相同。这种单纯由于 正负极性不同而彼此电蚀量不一样的现象叫 极性效应。 一般在短脉冲精加工时采用正极性加工, 而在长脉冲粗加工时采用负极性加工。
2. 加工系统中的自动进给调节系统的作用 是维持一定的“平均”放电间隙,保证电 火花加工正常而稳定的进行,以获得好的 加工效果。
一、电火花加工的原理和设备组成 二、电火花加工的特点及其应用 三、电火花加工工艺方法分类
一、电火花加工的原理和设备组成
电火花加工的原理是基于工具和工件(正、
负电极)之间脉冲性火花放电时的电腐蚀 现象来蚀除多余的金属,以达到对零件的 尺寸、形状及表面质量预定的加工要求。 电火花腐蚀的主要原因是:电火花放电时 火花通道中瞬时产生大量的热,达到很高 的温度,足以使任何金属材料局部熔化、 气化而被蚀除掉,形成放电凹坑。
二、自动进给调节系统的基本组成部分
1.测量环节
2.比较环节 比较环节用以根据进给量或间隙平均电 压的“设定值”(称作伺服参考电压)来 调节进给速度,以适应粗、中、精不同的 加工规准。它实质上是把从测量环节得来 的信号和“给定值”的信号进行比较,再 按此差值来控制加工过程。
3.放大驱动器 为了获得足够的驱动功率,放大器要有一 定的放大倍数。然而,放大倍数过高也不好, 它将会使系统产生过大的超调,即出现自激现 象,使工具电极进进退退,调节不稳定。 常用的放大器主要是各类晶体管放大器。
1.机床总体部分 主机主要包括:主轴头、床身、 立柱、工作台及工作液槽几部分。
《特种加工》第六版课后习题答案
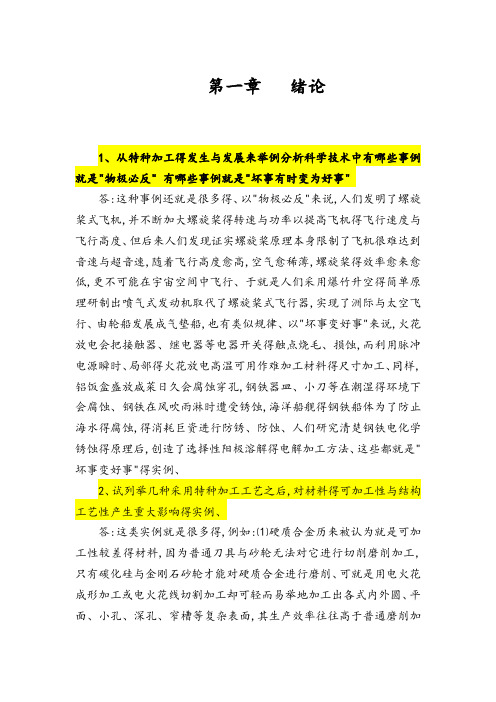
第一章绪论1、从特种加工得发生与发展来举例分析科学技术中有哪些事例就是"物极必反" 有哪些事例就是"坏事有时变为好事"答:这种事例还就是很多得、以"物极必反"来说,人们发明了螺旋桨式飞机,并不断加大螺旋桨得转速与功率以提高飞机得飞行速度与飞行高度、但后来人们发现证实螺旋桨原理本身限制了飞机很难达到音速与超音速,随着飞行高度愈高,空气愈稀薄,螺旋桨得效率愈来愈低,更不可能在宇宙空间中飞行、于就是人们采用爆竹升空得简单原理研制出喷气式发动机取代了螺旋桨式飞行器,实现了洲际与太空飞行、由轮船发展成气垫船,也有类似规律、以"坏事变好事"来说,火花放电会把接触器、继电器等电器开关得触点烧毛、损蚀,而利用脉冲电源瞬时、局部得火花放电高温可用作难加工材料得尺寸加工、同样,铝饭盒盛放咸菜日久会腐蚀穿孔,钢铁器皿、小刀等在潮湿得环境下会腐蚀、钢铁在风吹雨淋时遭受锈蚀,海洋船舰得钢铁船体为了防止海水得腐蚀,得消耗巨资进行防锈、防蚀、人们研究清楚钢铁电化学锈蚀得原理后,创造了选择性阳极溶解得电解加工方法、这些都就是"坏事变好事"得实例、2、试列举几种采用特种加工工艺之后,对材料得可加工性与结构工艺性产生重大影响得实例、答:这类实例就是很多得,例如:⑴硬质合金历来被认为就是可加工性较差得材料,因为普通刀具与砂轮无法对它进行切削磨削加工,只有碳化硅与金刚石砂轮才能对硬质合金进行磨削、可就是用电火花成形加工或电火花线切割加工却可轻而易举地加工出各式内外圆、平面、小孔、深孔、窄槽等复杂表面,其生产效率往往高于普通磨削加工得生产率、更有甚者,金刚石与聚晶金刚石就是世界上最硬得材料,过去把它作为刀具与拉丝模具等材料只有用金刚石砂轮或磨料"自己磨自己",磨削时金刚石工具损耗很大,正就是硬碰硬两败俱伤,确实就是可加工性极差、但特种加工中电火花可成形加工聚晶金刚石刀具,工具,而激光加工则不但"削铁如泥"而且可"削金刚石如泥"、在激光加工面前,金刚石得可加工性与钢铁差不多了、对过去传统概念上得可加工性,得确需要重新评价、(2)对结构工艺性,过去认为方孔,小孔,小深孔,深槽,窄缝以及细长杆,薄壁等低刚度零件得结构工艺性很差,在结构设计时应尽量避免、对E字形得硅钢片硬质合金冲模,由于90*内角很难磨削,因此常采用多块硬质合金拼镶结构得冲模、但采用电火花成形加工或线切割数控加工,则很容易加工成整体硬质合金得E 形硅钢片冲模,特种加工可使某些结构工艺性由"差"变"好"、3、工艺与特种加工工艺之间有何关系(应该说如何正确处理常规工艺与特种加工之间得差别)答:一般而言,常规工艺就是在切削,磨削,研磨等技术进步中形成与发展起来得行之有效得实用工艺,而且今后也始终就是主流工艺、但就是随着难加工得新材料,复杂表面与有特殊要求得零件愈来愈多,常规,传统工艺必然会有所不适应、所以可以认为特种加工工艺就是常规加工工艺得补充与发展、特种加工工艺可以在特定得条件下取代一部分常规加工工艺,但不可能取代与排斥主流得常规加工工艺、第二章电火花加工1、两金属在(1)在真空中火花放电;(2)在空气中;(3)在纯水(蒸馏水或去离子水)中;(4)在线切割乳化液中;(5)在煤油中火花放电时,在宏观与微观过程以及电蚀产物方面有何相同与相异之处答:(1)两金属在真空中火花放电时,当电压(电位差)超过一定时即产生"击穿",电子由"-"极逸出飞向"+"极,由于真空中没有物质阻挡电子得运动,所以没有正离子形成,没有发热得放电"通道"得概念,示波器,显象管中电子流得运动与此类似、基本上没有"电蚀产物"生成、(2)两金属在空气中放电得例子就是电火花表面强化,涂覆、电焊,等离子切割,等离子焊等,也就是在空气中放电,利用电子流在空气中撞击气体原子形成放电通道,在通道中与工件表面产生大量得热能用于强化,涂覆,切割与焊接、(3)在纯水,蒸馏水或去离子水中,两金属间电火花放电与在煤油中类似,只就是水分子,原子受电子,正离子撞击发热气化,最后分解为氧原子与氢原子(分子),而不像煤油中会分解出碳原子(碳黑微粒)与氢气等、(4),(5)在乳化液中与煤油中放电过程,详见教材中有关章节,不再另行论述、2、有没有可能或在什么情况下可以用工频交流电源作为电火花加工得脉冲直流电源在什么情况下可用直流电源作为电火花加工用得脉冲直流电源 (提示:轧辊电火花对磨,齿轮电火花跑合时,不考虑电极相对磨损得情况下,可用工频交流电源;在电火花磨削,切割下料等工具,工件间有高速相对运动时,可用直流电源代替脉冲电源,但为什么 )答:如提示所述,在不需要"极性效应",不需要考虑电极损耗率等得情况下,可以直接用220V得50HZ交流电作为脉冲电源进行轧辊电火花对磨与齿轮电火花跑合等、不过回路中应串接限流电阻,限制放电电流不要过大、如需精规准对磨或跑合,则可在交流工频电源上并联RC电路(R=500-1000,C=0、1-0、01),再接到两个工件上、在用高速转动得金属轮或圆片作电火花磨削,电火花切割,下料时,如果可以不计电极损耗率,则就可以用全波整流或整流后并联电解电容滤波得直流电源进行电火花磨削、由于工具电极高速转动,所以一般不会产生稳定电弧烧伤工件、最好就是经调压变压器降压到5-100V再整流供磨削之用,一则可以调节电压或电流,二则与220V交流电源隔离,以保障人身避免触电得危险、3、电火花加工时得自动进给系统与车,钻,磨削时得自动进给系统,在原理上,本质上有何不同为什么会引起这种不同答:电火花加工时工具电极与工件间并不接触,火花放电时需通过自动调节系统保持一定得放电间隙,而车,钻,磨削时就是接触加工,靠切削力把多余得金属除去,因此进给系统就是刚性得,等速得,一般不需要自动调节、4、电火花共轭同步回转加工与电火花磨削在原理上有何不同工具电极与工件上得瞬间放电之间有无相对移动加工内螺纹时为什么不会"乱扣" 用铜螺杆做工具电极,在内孔中用平动法加工内螺纹,在原理上与共轭同步回转法有何异同答:不同之处在于电火花共轭同步回转加工时:(1)工具电极与工件得转动方向相同;(2)转速严格相等(或成倍角,比例关系);(3)工具与工件上瞬时放电点之间有很慢得相对移动、而电火花磨削时工具与工件可以同向或反向转动;工具与工件得转速并不相同,磨削点之间有很大得相对移动、加工内螺纹时,其所以不会"乱扣",就是因为加工中工具电极与工件得转向与转速相等,工具与工件圆周表面上有着"各点对应"得关系,所以能把工具表面得螺纹形状复制到工件表面上去而不会"乱扣"、在内孔中用平动法加工内螺纹,本质上与共轭同步回转法相同,不同之处在于平动法加工时工件不转动而代之以工具电极在平动头中作"公转"行星式运动,其内外圆上"各点对应"得规则仍然存在、5,电火花加工时,什么叫做间隙蚀除特性曲线粗,中,精加工时,间隙蚀除特性曲线有何不同脉冲电源得空载电压不一样时(例如80V,100V,300V三种不同得空载电压),间隙曲线有何不同试定性,半定量地作图分析之、答:间隙蚀除特性曲线就是电火花放电间隙蚀除速度与放电间隙大小(间隙平均电压得大小)之间得关系,此关系可以定量地用作图法画成间隙蚀除特性曲线、粗,中,精加工时,由于脉宽,峰值电流等电规准不同,同样大小间隙得蚀除速度也就不一样,总得来说,粗加工时蚀除速度较大,上凹得间隙蚀除特性曲线就高于中,精加工得曲线、当脉冲电源得空载电压不一样时,例如电压较高为300V时,其击穿间隙,平均放电间隙都大于100V或80V得放电间隙,因此横坐标上得A点(电火花击穿间隙)将大于100V或80V时得间隙、间隙特征曲线原点不动,整个曲线稍向右移、同理,80V空载电压得间隙特征曲线得A点将偏向左边、S/ m/V6,在电火花加工机床上用Ф10mm得纯铜杆加工Ф10mm得铁杆,加工时两杆得中心矩偏距5mm,选用=200 s, i=5、4A,各用正极性与负极性加工10min, 试画出加工后两杆得形状,尺寸,电极侧面间隙大小与表面粗糙度值(提示:利用电火花加工工艺参数曲线图表来测算)、答:加工示意图见图2-1a、设先用正极性加工,加工后得图形见图b,负极损耗较大;负极性加工后得图形见图c,正极工具损耗较小、具体数据请自行在图中标明,并与书中工艺曲线图表进行对照比较)、图2-17,电火花加工一个纪年章浅型腔花模具,设花纹模电极得面积为10mm×20mm=200,花纹得深度为0、8㎜,要求加工出模具得深度为1㎜,表面粗糙度为=0、63 m,分粗,中,精三次加工,试选择每次得加工极性,电规准脉宽,峰值电流,加工余量及加工时间,并列成一表(提示:用电火花加工工艺参数曲线图表来计算)、答:可按书中电火花加工工艺曲线图表选择粗,中,精加工得规准、例如:极性脉宽脉间峰值电流加工余量加工后表面粗糙度时间粗加工(可不加抬刀)负600 s100 s10A0、9㎜3 m约30min中加工(加抬刀)负100 s50 s4A0、08㎜1、25 m30min精加工(加正20 s50 s2A0、02㎜30min答:不同之处在于电火花共轭同步回转加工时:(1)工具电极与工件得转动方向相同;(2)转速严格相等(或成倍角,比例关系);(3)工具与工件上瞬时放电点之间有很慢得相对移动、而电火花磨削时工具与工件可以同向或反向转动;工具与工件得转速并不相同,磨削点之间有很大得相对移动、加工内螺纹时,其所以不会"乱扣",就是因为加工中工具电极与工件得转向与转速相等,工具与工件圆周表面上有着"各点对应"得关系,所以能把工具表面得螺纹形状复制到工件表面上去而不会"乱扣"、在内孔中用平动法加工内螺纹,本质上与共轭同步回转法相同,不同之处在于平动法加工时工件不转动而代之以工具电极在平动头中作"公转"行星式运动,其内外圆上"各点对应"得规则仍然存在、第三章电火花线切割加工1、电火花线切割时,粗,种,精加工时生产率得大小与脉冲电源得功率,输出电流得大小有关、用什么方法衡量,判断脉冲电源加工性能得好坏(绝对性能与相对性能)答:可用单位电流(每安培电流)得生产率来衡量,即可客观地判断脉冲电源加工性能得好坏、例如某脉冲电源峰值电流25A时得切割速度为100mm2/min,另一电源峰值电流27A时切割速度为106mm2/min,则前者得相对生产率为100/25=4mm2/min,优于后者106/27=3、9mm2/min 、又如某线切割脉冲电源3A s时切割速度为100mm2/min,另一电源3,5A时为124mm2/min,则前者相对切割速度为33、3mm2/min,后者35、5mm2/min、2、电火花加工与线切割加工时,如何计算脉冲电源得电能得利用率试估计一般线切割方波脉冲电源得电能利用率答:设脉冲电源得空载电压为100V ,加工时火花放电间隙得维持电压为25V则消耗在晶体管限流电阻上得电压为 100-25=75V,由此可以算出电能利用率:有用能量:输入能量=25:100=1:4=25%能量得消耗率为:损耗能量:输入能量=75:100=3:4=75%可见75%得能量损耗在限流电阻得发热上、3、设计一个测量,绘制数控线切割加工得间隙蚀除特性曲线得方法(提示:使线切割等速进给,由欠跟踪到过跟踪)、答:这一习题有一定得难度,需对间隙蚀除特性曲线与线切割加工伺服进给系统有一定深度得理解才行、间隙蚀除特性曲线就是蚀除速度与放电间隙(间隙平均电压)得关系曲线(参见第二章电火花加工得伺服进给)、线切割加工时,调节伺服进给量得大小,可以在一定程度上改变平均放电间隙、例如把进给速度人为放慢,处于"欠进给"状态,则平均放电间隙偏大,反之,进给速度过高,"过进给"时,则放电间隙偏小、测绘间隙蚀除特性曲线时,利用"改变预置进给速度"来改变放电间隙得大小、实际上放电间隙得大小(绝对值)很难测量,但可以用加工时得平均间隙电压大小来相对测量间隙值得大小、为此,要在工件与钼丝(导电块)或直接在电源输出端并一个满刻度100V(用于测空载,偏空载时得开路间隙电压),20V(用于测偏短路时得间隙电压)得直流电压表、实际测绘时,先不用线切割机床得"自动档"(伺服)进给,而采用"人工档"(等速进给)进给功能、最初用较慢得等速进给速度进行切割,此时处于"欠跟踪"得进给状态,待切割稳定后就记下进给速度与此时得间隙平均电压,在坐标上作出曲线上得某一点、以后稍微调快进给速度(仍为等速进给),同样测得第二,三```点得数据、当调节到进给速度约等于蚀除速度时,此时即为最佳状态 B 点放电间隙为最佳放电间隙SB 此时得切割速度为最大、当以更大得进给速度(等速)切割时,由于没有伺服功能,进给速度大于可能得蚀除速度,放电间隙逐步减小,最后即将形成短路,放电间隙为零、此时应尽快停止进给,并事先作好记录、在曲线最高点B只右,用上述方法比较容易做出间隙蚀除特性曲线得右半部分、但B点左边得曲线,因放电间隙逐步减小并趋于短路,易把钼丝顶弯,因此应多加小心、4、一般线切割加工机床得进给调解特性曲线与电火花加工机床得进给特性曲线有何不同与有短路回退功能得线切割加工机床得进给调解特性曲线又有什么不同答:一般线切割机床得进给得进给系统,往往没有短路回退功能,或短路后经一定时间例如30s后仍不能自动消除短路状态,则回退256步(相当于0、256 mm),如仍不能消除短路,则自动停止进给或同时报警,这与电火花成型加工机床遇短路即退回不一样、上述无短路回退功能得线切割机床得进给特性曲线就不会有横坐标左下部分得曲线,亦即工具电极(钼丝)得进给速度 vd没有负值、即使有短路回退功能得线切割机床,短路后得回退速度就是固定得(不象电火花成型加工机床那样短路后将以较高得速度vd0回退),所以进给调节特性曲线得左下部为窄小矩形,即放电间隙较小时,进给速度vd《0,一旦完全短路后,钼丝才低速(恒速)回退、5、设计一个测量,绘制数控线切割加工机床得进给调解特性曲线得方法(提示:在线切割机床上做空载模拟实验、用可调得得直流电源模拟火花间隙得平均电压)、答:这一习题也有一定难度,需对线切割机床得变频进给系统有一定得了解、线切割机床得进给速度vd就是由火花放电间隙得平均电压ue来决定得、ue越大,vd亦大,ue小vd也小,ue=0,vd=0或等速回退、为此可以用"模拟法"来测绘线切割加工机床得进给调解特性曲线、具体得得方法就是:使线切割机床处于加工状态,可不开丝筒,不开高频电源,但应使工作台处于"人工"等速进给状态、此时工作台进给得"取样电压",并不就是来自火花放电间隙得平均电压ue(ue再经电阻分压成10~12v得电压,经"变频调节"电位器送至"压—频"(u-f)转换器,将此低电压u转换成进给脉冲,频率为f,另工作台进给),而就是由+12V得外加电压,经"变频调节"电位器调压输入至 "压—频"(u-f)转换器、低电压0V相当于间隙短路,最高10~12V相当于间隙开路状态、可以将此电压由低向高调节,例如0V,2V,4V,6V,8V,10V……直至12V,模拟不同得ue、记录下每种不同电压时得工作台进给速度(可以从控制器面板数显表上测得),然后即可绘制出进给调节特性曲线、6、今拟用数控线切割加工有8个齿得爪牙离合器,试画出其工艺示意图并编制出相应得线切割3B相应程序、答:由于爪牙离合器工件就是圆筒形得,端面上需切割出8个爪牙方齿,故切割时必须有一个数控回转工作台附件、办法为先在圆套筒上钻一个∮1~2mm得穿丝孔,装夹好工件后,调整到穿丝孔为最高点时穿丝,回转台转动切除爪牙得端面,见示意图、(俯视图)切割得程序(一次切出凹,凸两个爪牙离合器)为:BBBJ=穿丝孔距离GXL3(x向移动)BBBJ=1/2齿宽GYL4(y向转动)BBBJ=齿深GXL3(x向移动)BBBJ=齿宽GYL4(y向转动)BBBJ=齿深GXL1(x向移动) BBBJ=齿宽GYL4(y向转动)第四章电化学加工1.从原理与机理上来分析,电化学加工有无可能发展成为"纳米级加工"或"原子级加工"技术?原则上要采用哪些措施才能实现?答:由于电化学加工从机理上瞧,就是通过电极表面逐层地原子或分子得电子交换,使之在电解液中"阳极溶解"而被去除来实现加工得,可以控制微量、极薄层"切削"去除。
特种加工_第二章_电火花加工(2-1)
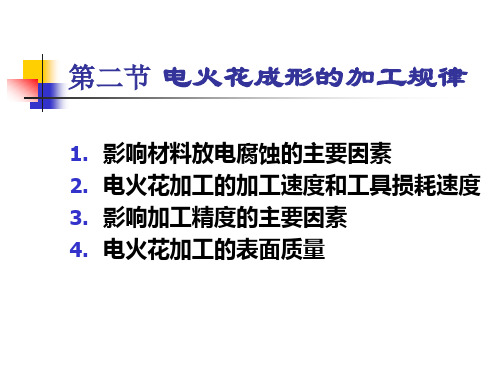
3 影响加工精度的主要因素
除通常的加工误差(机床本身的各种误差/工 件和电极的定位和安装误差)外,还有与电火 花加工的工艺有关的误差。 放电间隙的大小及其稳定性 0 ˆ S Kuui KRWM.4 Sm
工具电极的损耗及其稳定性
4 电火花加工的表面质量
表面质量主要包括:
0.3 0.4 R e e
电火花加工的表面质量与加工速度之间存在很 大的矛盾,如从Ra2.5μm提高到Ra1.25μm,加 工速度要下降十多倍。 加工面积对对表面粗糙度也有影响
工件材料对表面粗糙度也有影响
精加工时,工具电极的表面粗糙度也影响加工 粗糙度。
表面变质层—电火花加工的表面质量
结束
表面粗糙度 表面变质层 表面力学性能
表面粗糙度—电火花加工的表面质量
电火花加工表面是由无数的小坑和硬凸所组成 的,有利于保存润滑油。
与传统加工方法一样,表面粗糙度用
微观平面度的平均算术偏差Ra表示
平面度最大高度值Rmax表示
对表面粗糙度影响最大的是单个脉冲的能量, 实验公式:
ˆ Rmax K t i
极性效应
电火花加工过程中正负极都会受到电腐蚀,即使材 料相同,其电腐蚀程度也不同。这种由于正负极不 同而引起电腐蚀量不一样的现象,称为极性效应。
极性定义
电火花加工分“正极性加工” 和“负极性加 工” 。 通常定义以电极为准:
“正极性加工”——工件接正极
“负极性加工”——工件接负极,也称反极 性
工作液的好坏对电蚀量有较大的影响 一般选用粘度小、流动性好、渗透性好的 煤油为工作液。
2.1电火花加工的原理和基本条件
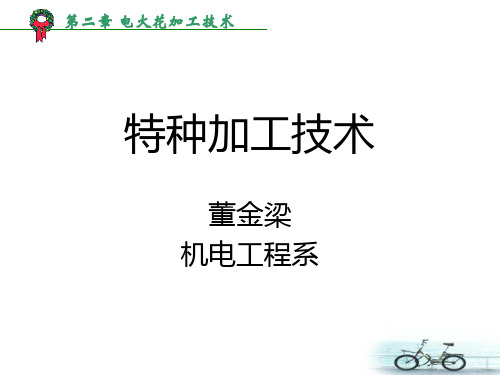
第二章 电火花加工技术
2.1 电火花加工的原理和基本条件
1.电火花加工的原理
电火花加工是在液体介质中利用两电极 (工具和工件电极或正负电极)之间脉冲性 火花放电时的电腐蚀来蚀除多余的金属,使 工件达到预定的尺寸、形状和表面质量的加 工。
第二章 电火花加工技术
电火花加工的实质是电腐蚀,简称电蚀。 所谓电腐蚀:是指两电极之间的绝缘介质被 瞬时击穿,形成火花放电,产生大量热,造 成局部高温,使工件的放电部分熔化、甚至 气化,使工件电极放电局部被蚀除带走的过 程。
➢ 自动进给装置:工具电极由自动进给调节装置控制, 以保证工具与工件在正常加工时维持很小的放电间隙 (0.01-0.05mm)。在保持工具电极与工件之间恒定放电 间隙的条件下,一边蚀除工件金属,一边使工具电极 不断地向工件进给,最后便加工出与工具电极形状相 对应的形状来。
➢ 脉冲电源放电:提供每秒成千上万次的脉冲放电。 ➢ 工作液循环:通过过滤装置和工作液循环装置来清除
工作液中的杂质。
第二章 电火花加工技术
2.电火花加工的基本条件
(1)火花放电必须在具有一定绝缘强度的液体 介质中进行。
(2)必须采用脉冲电源,以形成瞬时脉冲放电。 (3)必须采用自动进给调节装置,以保持工具
电极与工件间微小的放电间隙。
第二章 电火花加工技术
看视频,想一想如何回答问题:
1.电火花加工在哪个领域具有绝对优势?(相对于 传统机械难加工而言的) 2.为什么电火花加工会如此优秀呢? 3.电火花放电的瞬时高温可达多少度? 4.一秒钟可以放电多少次? 5.电火花加工需要在什么环境(介质)? 6.电火花需要哪几种电极?
因此,电火花加工也被称作放电加工或电 蚀加工。
第二章 电火花加工技术
《特种加工技术》 习题答案

《特种加工技术》2017版习题参考答案【说明】:每章的第一大题是简答题,其答案基本在书中有描述,此处不再给出;部分章节的拓展题主要目的是启迪、开拓思路或展开应用,故没有统一或固定的答案。
第1章电火花成形加工(EDM SINKING)二、选择题1.电火花深小孔加工应当选择以下 C 作为工作液;A.自来水;B.煤油;C.去离子水(工业纯水) ;D.乳化液2.电火花共轭回转加工的最早发明人是:AA.中国人;B.美国人C.俄国人D.德国人3. 欲将小型交叉孔口毛刺去除彻底干净,最好采用D加工方法来完成。
A.锉刀;B.砂带磨削C.砂轮磨削D.电火花工艺4.欲保证最高的加工精度,电火花加工中工作液供给方式最好采用C。
A.静态淹没工件;B.侧面冲液C.工具电极内部抽吸D.工具电极内部射出5.对于象筛网零件有成千上万个小孔需要加工,为保证生产率,电火花加工宜采用以下D工具电极.A.单个实心电极逐个加工;B.单个空心电极逐个加工C. 实心群电极D.空心管群电极三、判断题1.电火花加工中的吸附效应都发生在正极上。
(F )2.电火花成型加工时,电极在长度方向上损耗后无法得到补偿,需要更换电极。
(T )3.电火花成型加工中的自动进给调节系统应保证工具电极的进给速度等于工件的蚀除速度;(T)4.电火花成型加工和穿孔加工相比,前者要求电规准的调节范围相对较小。
(F )5.电火花成型加工电极损耗较难进行补偿。
(T )6.在型号为DK7740的数控电火花线切割机床中,D表示电加工机床。
(T)7.弛张式脉冲电源电能利用率相当高,所以在电火花加工中应用较多。
(F)8.电火花成型加工属于盲孔加工,工作液循环困难,电蚀产物排除条件差。
(T)9.电火花加工的粗规准一般选取的是窄脉冲、高峰值电流。
(F)10.电火花加工的粗规准一般选取的是宽脉冲、高峰值电流。
(T)11.电火花加工的效率较低。
(T)12.煤油作为电火花液,冷却效果最好(F)13.紫铜又叫纯铜;(T)14.电火花机床没有主运动,只有进给运动。
特种加工第二章电火花加工电火花加工的自动进给调节系统讲义资料
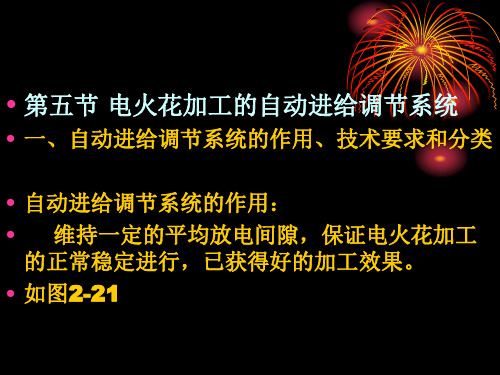
• 冲模加工中,常选用粗、中、精三种规 准,每种规准有可分几档。(详细介绍)
改变输入动圈 中的电流,可 使挡板随着运 动
电机械 转换器
节流孔
溢
流 阀
主轴的移动是由电机械 转换器中控制线圈电流 大小来实现的
动圈 静圈 挡板
控制线 圈电流 大小由 加工间 隙电信 号控制
四、电—机械式自动进给调节系统 (示例)
将电压信号放大并转变为0~1000HZ不同频率的脉冲串
发出恒频率的回退触发脉冲
同类型的伺服电动机,它能根据控制信
号的大小及时地调节工具电极的进给速
度,以保持合适的放电间隙。
• 要求执行环节能快速反映间隙状态 变化;机械传动间隙和摩擦力应当尽量 小,以减少系统的不灵敏区;具有较宽 的调速范围。
三、电液自动进给调节系统(示例)
这种系统在20世纪80年代应用很广泛,但 目前已逐渐被电—机械式的各种交直流伺服电 极所替代,但分析了解其调节过程,仍具有典 型的理论意义。
4、放大驱动器:
• 由测量环节获得的信号,一般都很
小,难于驱动执行元件,必须要有一个 放大环节,通常称它为放大器。
•
为了获得足够的驱动功率,放大器
要有一定的放大倍数,但放大倍数也不
能过高,过高会使工具电极时进时退,
调节不稳定。
• 常用的放大器主要是各类晶体管放大器
5、执行环节:
•
执行环节也称执行机构,常采用不
• 工具电极的尺寸精度和表面粗糙度比凹模高 一级,一般精度不低于IT7,表面粗糙度小于 Ra1.25,且直线度、平面度和平行度在 100mm的长度上不大于0.01mm。
• 工具电极应有足够的长度。
• (3)电极的制造:线切割的方法
- 1、下载文档前请自行甄别文档内容的完整性,平台不提供额外的编辑、内容补充、找答案等附加服务。
- 2、"仅部分预览"的文档,不可在线预览部分如存在完整性等问题,可反馈申请退款(可完整预览的文档不适用该条件!)。
- 3、如文档侵犯您的权益,请联系客服反馈,我们会尽快为您处理(人工客服工作时间:9:00-18:30)。
3)工件材料对加工表面粗糙度的影响
熔点高的材料容易得到好的表面粗糙度
(加工速度应适当下降)
可编辑ppt
18
4)精加工时,工具电极的表面粗糙度也会 影响加工表面粗糙度。
精加工时不要采用石墨电极。
可编辑ppt
19
放电间隙不一致的影响:
若放电间隙大小能保持一致,则可以通过 修正工作电极对放电间隙进行补偿,以 获得较高的加工精度。但放电间隙的大 小实际上是变化的,影响着加工精度。
可编辑ppt
4
放电间隙的大小对加工精度的影响:
放电间隙越大,对精度的影响越严重 (仿形精度和尺寸精度) 如图2-10(A)(B) (放电具有等距性)
可编辑ppt
9
电火花加工中影响表面粗糙度的因素:
1)单个脉冲能量
实验得: Rmax=KR*te0.3*ie0.4 Rmax 实测的表面粗糙度
KR 常数 te 脉冲放电时间 ie 峰值电流
可编辑ppt
10
注意:
在电极面积较大时,即使单个脉冲能量很 小Rmax很难小于2μm(约Ra0.32μm),而 且加工面积越大,可达到的最佳表面粗 糙度愈差。
(煤油工作液中的工具和工件具有潜布电 容,相当于在放电间隙上并联了一个电 容)
可编辑ppt
11
研究成果:采用“混粉加工”新工艺,
可较大面积地加工出质量很高
的光亮面。
具体方法:在煤油工作液中加入硅或铝
等导电微粉。
原因:这样可使工作液的电阻率降低、放
电间隙成倍增大,潜布寄生电容成倍减
小,放电通道被分割成多个小的火花放
工件上。 ❖ 对策:采用高频窄脉宽精加工,减小放电间隙,圆
弧半径可明显减小从而提高加工精度
可编辑ppt
8
四、电火花加工的表面质量
电火花加工的表面质量包括:表面粗糙度、 表面变质层、表面力学性能。
1、表面粗糙度 表示方法:
电火花加工表面粗糙度通常用微观平面度 的平均算术偏差Ra表示,
也有用平面度的最大高度值Rmax表示的
三、影响加工精度的主要因素
和通常的机械加工一样,机床本身的各种 误差,以及工件和工具的定位、安装误 差都回影响到加工精度。
这里主要讨论与电火花加工工艺有关的因 素
可编辑ppt
1
影响加工精度的主要因素有: 放电间隙的大小及其一致性 工具电极损耗及其稳定性
可编辑ppt
2
1、放电间隙的计算(经验公式):
放电间隙越大电场强度分布更加不均匀,棱角处 损耗严重,放电间隙变化量增大
相应措施:缩小放电间隙
(由公式知:采用较小的加工
归准)
精加工的放电间隙(单面)一般只有
0.01mm,而粗加工时则可可编辑达ppt 0.5mm以上。
5
工具电极的损耗对尺寸精度及形状精 度都有影响:
对策: 穿孔加工时:让电极贯穿型孔来补偿电 极的损耗。 型腔加工时:采用更换电极的方法
2、表面变质层
电火花加工中,在火花放电的瞬时高温和 工作液的快速冷却下,材料的表面层发 生了很大变化,大致可分为:
熔化凝固层
热影响层
可编辑ppt
20
可编辑ppt
21
1)熔化凝固层
位于工件表面最上层,它被放电时瞬时高 温熔化而又滞留下来,受工作液快速冷 却而凝固。对于碳钢来说,熔化层在金 相照片上呈白色,谷又称之为白层。它 与基体完全不同,是一种树枝状的淬火 铸造组织,与内层的结合也不牢固。
24
不同金属材料的热影响层金相组织结构是 不同的,耐热合金的热影响层与基体差 异不大。
可编辑ppt
25
3)显微裂纹
电火花加工表面由于受到瞬时高温并迅速 冷却而产生拉应力,往往出现显微裂纹
实验表明:一般裂纹仅在熔化层出现,只 有在脉冲能量很大的情况下才有可能扩 展到热影响层。
可编辑ppt
26
影响显微裂纹的因素:
熔化层的厚度随脉冲能量的增大而增厚, 一般不超过0.1mm
可编辑ppt
22
2)热影响层
它位于熔化层和基体之间.热影响层的金属 材料并没有变化,只是受到高温的影响,使 材料的金相组织发生了变化,它与基体材 料之间没有明显的界限。
对淬火钢:热影响层包括再淬火区、高
温回火区和低温回火区。
对未淬火钢:热影响层主要为淬火区
S=Ku*ui+KR*WM+Sm s 放电间隙(指单面放电间隙)
ui 开路电压 Ku 与工作液介电强度有关的常数,含有
点蚀产物后该系数会增大。
KR 与加工材料有关的常数。一般易熔金 属的值较大
WM 单个脉冲能量 约为3μm
可编辑ppt
3
注意:随着加工时间的延长,放电间隙逐渐 增大.即在加工过程中放电间隙是一个变 化量
因此,淬火钢的热影响层厚度比未淬火钢
大。
可编辑ppt
23
热影响层分布:
靠近熔化凝固层部分由于受到高温作用并 迅速冷却,形成为淬火区,其厚度与条 件有关,一般为最大微观平面度的2-3倍。
与淬火层相邻的部分受到温度的影响而形 成高温、低温回火区,回火区的厚度约 为最大微观平面度的3-4倍。
可编辑ppt
可编辑ppt
6
电火花加工中 “二次放电” 对形状精度有影响:
集中反映在在 加工深度方向 产生斜度, 加工棱角棱边 变钝方面。
可编辑ppt
7
结论:
❖ 电参数对放电间隙影响明显 ❖ 工作液的状况会影响放电间隙 ❖ 减小放电间隙可提高加工精度 ❖ 减少电极损耗可提高加工精度 ❖ 电火花加工时工具的尖角和凹角很难精确地复制到
1、脉冲能量:能量越大,显微裂纹越宽越 深,脉冲能量很小,一般不出现微裂纹。
2、工件材料:脆硬材料容易产生微裂纹
3、工件预先的热处理情况:淬火材料比未 淬火材料容易产生微裂纹(因为淬火材 料脆硬,原始内应力较大)
可编辑ppt
27
3、表面力学性能
(1)显微硬度及耐磨性
一般来说,电火花加工表面最外层的硬度 比较高,耐磨性好。但对于滚动摩擦, 由于是交变载荷,尤其是干摩擦,则因 其熔化凝固层和基体结合不牢,容易剥 落而磨损。因此,有些要求高的模具需 把电火花加工后的表面变质层事先磨掉。
电通道,到达工件表面的脉冲能量被分
散,相应的电痕就较小,表面较光整。
可编辑ppt
12
可编辑ppt
13
可编辑ppt
14
可编辑ppt
15
可编辑ppt
16
可编辑ppt
17
2)加工速度对表面粗糙度的影响
加工速度愈大,表面粗糙度愈差。(数据书)
对策:采用平动或摇动(工作台按一定轨迹做 微量移动)加工工艺可大为 改善。(慢)