化学制药合成车间安全事故案例分析
制药车间火灾事故案例分析
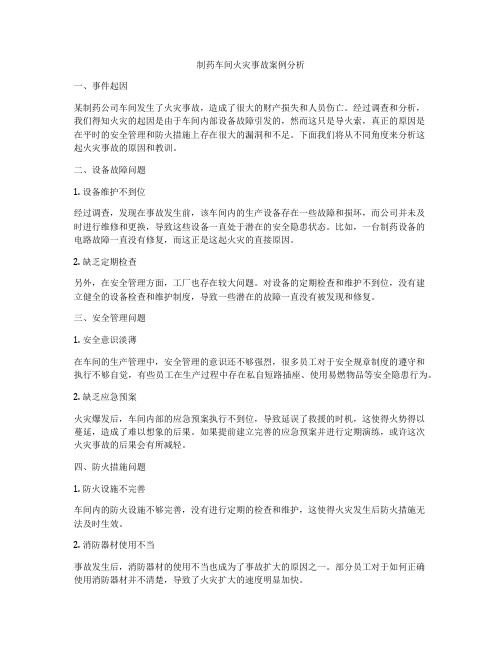
制药车间火灾事故案例分析一、事件起因某制药公司车间发生了火灾事故,造成了很大的财产损失和人员伤亡。
经过调查和分析,我们得知火灾的起因是由于车间内部设备故障引发的,然而这只是导火索,真正的原因是在平时的安全管理和防火措施上存在很大的漏洞和不足。
下面我们将从不同角度来分析这起火灾事故的原因和教训。
二、设备故障问题1. 设备维护不到位经过调查,发现在事故发生前,该车间内的生产设备存在一些故障和损坏,而公司并未及时进行维修和更换,导致这些设备一直处于潜在的安全隐患状态。
比如,一台制药设备的电路故障一直没有修复,而这正是这起火灾的直接原因。
2. 缺乏定期检查另外,在安全管理方面,工厂也存在较大问题。
对设备的定期检查和维护不到位,没有建立健全的设备检查和维护制度,导致一些潜在的故障一直没有被发现和修复。
三、安全管理问题1. 安全意识淡薄在车间的生产管理中,安全管理的意识还不够强烈,很多员工对于安全规章制度的遵守和执行不够自觉,有些员工在生产过程中存在私自短路插座、使用易燃物品等安全隐患行为。
2. 缺乏应急预案火灾爆发后,车间内部的应急预案执行不到位,导致延误了救援的时机,这使得火势得以蔓延,造成了难以想象的后果。
如果提前建立完善的应急预案并进行定期演练,或许这次火灾事故的后果会有所减轻。
四、防火措施问题1. 防火设施不完善车间内的防火设施不够完善,没有进行定期的检查和维护,这使得火灾发生后防火措施无法及时生效。
2. 消防器材使用不当事故发生后,消防器材的使用不当也成为了事故扩大的原因之一。
部分员工对于如何正确使用消防器材并不清楚,导致了火灾扩大的速度明显加快。
五、总结和教训通过对这次火灾事故的原因分析,我们可以得出以下几点教训:1. 安全管理要做到位安全管理需要在企业的日常生产经营中得到充分的认识和重视,需要从领导层到普通员工都要具备安全意识,不容忽视。
2. 定期检查设备和防火设施定期检查和维护设备和防火设施是非常重要的,必须要确保这些设备和设施的正常使用和作用。
制药生产中的安全隐患(二篇)

制药生产中的安全隐患当猪流感在4月下旬肆虐全球,在5月11日确定登陆中国的时候,另外一个令人堪忧的事情却被猪流感的来势汹汹所掩盖,那就是制药厂生产安全。
事件回顾4月11日上午9时40分左右,位于芜湖市九华山北路的博英制药厂生产车间中一烘烤箱突然发生故障爆炸起火,正在作业一名工人受伤。
接警后,芜湖市龙山消防中队迅速赶赴现场将火扑灭,事故原因目前仍在调查中。
4月23日下午5时许,位于镇平工业园内的南阳普康药业有限公司镇平分公司内的一个制药罐发生爆炸,2死1伤。
据一位知情者说,大约下午5时,只听轰的一声巨响,氯洁车间附近的一个20多立方米的大制药罐突然发生爆炸,爆炸的气浪将一个人从工厂的墙内炸飞到了墙外的水沟里。
记者看到,一辆120救护车呼啸而来,将1名伤者和炸飞到墙外的工人的尸体拉走。
事发后,当地相关部门人员立即赶赴现场抢救伤者。
经初步调查,事故原因是一位电焊工作业时点燃了罐内泄漏的二氯乙烷气体从而引发了爆炸。
生产中有哪些隐患制药是化工的一部分,必然存在化学药品的存储问题,如案例二中,就是存储罐中的原来发生了爆炸。
这个爆炸和操作有莫大的关系。
对易燃气体进行操作之前,应该进行检漏,这是从中学化学试验就在强调的安全程序,却在厂区中没能良好执行,从而发生了事故。
此外,在案例一中,是烘烤箱发生了爆炸。
现在还没有确定烘烤箱中烘烤的是什么物质,但可以确定的是,既然发生了爆炸,必然烘烤的是易燃易爆的物质、或者是将数种能反应的物质放到了一起从而产生爆炸。
除了存储和操作外,在制药生产中,人为因素是最重要的安全隐患。
首先在生产流程的设计上要保障安全,其次在设备安装上要合格达标,此外一定要定期维护,消灭隐患。
制药设备质量堪忧是更大的隐患制药设备直接与药品、半成品和原辅料接触,是造成药品生产差错和污染的重要因素。
制药设备是否安全,直接关系到制药企业能否安全生产。
然而在相当长的时间里,它在企业改造中常常处于不被重视的地位。
由于制药设备技术含量较低,行业准入容易,因此我国制药设备行业小、散、乱的现象极其鲜明突出。
药企生产安全事故案例

药企生产安全事故案例近年来,随着全球药品市场的快速发展,药企的生产安全问题备受关注。
药企需要面对的挑战包括不断改变的法规和质量标准、日益严苛的市场监管以及不断增长的市场需求。
然而,一些药企在生产过程中未能严格遵守安全规定,导致了一系列严重的安全事故。
本文将介绍一些药企生产安全事故的案例,以期引起广大药企对生产安全的重视,加强安全管理,保障药品的质量和消费者的安全。
案例一:药企生产车间爆炸事故药企的生产车间在一天晚上突发爆炸事故,造成多名工人丧生和受伤。
调查显示,事故是由于生产车间内严重违反了爆炸物品的储存和管理规定。
有毒、易燃物品未分类存放,容器破损和泄漏,导致了火花引发的爆炸。
该药企在事故发生前并未进行安全演练和员工培训,缺乏对安全事故的应急处理和自救指导。
此外,该企业在事故后也未能及时报告、组织救援和控制事故影响,导致情况进一步恶化。
案例二:药企产品质量事故药企生产的其中一种药品被检测发现严重超标。
经过追查,发现该药企在生产过程中未严格控制原材料的质量,使用了过期或质量不合格的原材料。
同时,该企业的生产车间存在严重的清洁和消毒问题,未经定期清洗和维护设备,导致交叉污染和杂质的产生。
此外,该企业的生产记录不完整,无法追溯产品的生产批次和过程,给事故后的调查和问题解决带来了困难。
这些问题最终导致了该药品质量不合格,给消费者带来了严重的健康风险。
案例三:药企生产环境污染事故药企的生产过程中存在着严重的环境污染问题。
该企业排放的废水和废气中含有高浓度的有毒物质,严重超标。
调查显示,该企业对污染物排放未进行正确处理和监测,生产废液乱倒、未按规定路径运输和处理,导致了地下水、土壤和周边环境的严重污染。
此外,该企业未按照有关规定对废气和废水进行处理,直接排放到空气中和水源中,对周边居民的健康造成了潜在威胁。
从以上案例可以看出,药企在生产过程中如果不严格遵守安全规定,就会导致严重的安全事故。
为了避免类似事故的再次发生,药企应加强对生产过程的管理和控制,并注重以下方面的工作:1.安全规范:药企应制定和实施严格的安全规范,包括原材料采购的质量控制,生产车间的安全管理以及废物的处理和处置等。
药企安全事故案例分析

1 2
药品安全问题频发
需加强行业自律和诚信体系建设,提高企业责任 意识和质量意识。
药品研发创新能力不足
需加大科研投入和人才培养力度,提高药品研发 水平和创新能力。
3
医药市场竞争不规范
需加强市场监管和反垄断执法力度,维护公平竞 争的市场秩序。
05
经验教训总结与防范措施 建议
从本次事故中汲取的经验教训
如药物投料错误、设备操作不当等。
包装和标签错误
如标签混淆、包装破损导致污染等。
质量控制环节失效
如检验方法不准确、检验设备故障等 。
间接原因探讨
安全管理体系不完善
01
如缺乏有效的安全管理制度、安全培训不足等。
生产设备设施维护不当
02
如设备老化、缺乏定期维护等。
供应链管理问题
03
如供应商质量不稳定、原料把关不严等。
药品不良反应监测
建立和完善药品不良反应监测体系,及时发现和处置药品不良反应 事件。
监管漏洞剖析及整改方向
01
02
03
监管制度不完善
如药品审批标准不统一、 审批流程不透明等,需加 强制度建设和执行力度。
监管手段落后
如信息化水平不高、数据 分析能力不强等,需加强 技术投入和创新。
监管资源不足
如人力、物力、财力等方 面的限制,需加强资源配 置和保障。
降低人为操作风险。
建立生产过程的实时监控和预警 系统,及时发现和处理异常情况
。
未来发展规划中安全考虑
在企业未来发展规划中,将安全作为重 要考虑因素之一。
加大在安全领域的投入,包括资金、人 与行业监管机构、专业机构等保持密切
力、技术等。
合作,共同推动行业安全水平的提升。
制药企业制剂车间安全事故案例及分析

制药企业制剂车间安全事故案例及分析例1. 某制药有限公司制剂车间发生爆炸2010年12月30日上午,某制药有限公司发生爆炸并起火,造成5人被烧死亡,6人重伤(烧伤和摔伤),2人轻伤。
2010年12月30日上午,某制药有限公司工厂四楼片剂车间洁净区段当班职工按工艺要求在制粒一房间进行混合、制软剂、制粒、干燥等操作。
9时30分许,检修人员为给空调更换初效过滤器,断电停止了空调工作,净化后的空气无法进入洁净区。
同时,由于操作过程中存在边制粒、边干燥的情况,烘箱内循环热气流使粒料中的水分和乙醇蒸发,排湿口排出水分和乙醇蒸汽的效果明显降低,越来越多的乙醇蒸汽不能从排湿口及时排走,烘箱内蓄积了达到爆炸极限的乙醇气体。
同时,由于当时房间内空调已停止工作,制粒一房间内由于制粒物挥发出的乙醇气体与干燥门开关时溢散出的水分、乙醇气体无法被新风置换,也堆积了大量可以燃烧的乙醇气体。
加之洁净区使用干燥箱的配套电气设备不防爆,操作人员在烘箱烘烤过程中开关烘箱送风机或轴流风机在运转过程中产生的电器火花,引爆了积累在烘箱中达到爆炸极限的乙醇爆炸性混合气体,炸毁烘箱,所产生的冲击波将四楼生产车间的各分区隔墙、吊顶隔板、通风设施、玻璃窗、生产设施等全部毁坏;爆炸过程产生的辐射热瞬间引燃整个洁净区其他可燃物。
形成大面积燃烧,过火面积遍及整个4层。
爆炸和燃烧发生后,由于车间的安全通道只有一条,部分现场人员和受伤人员不能及时逃生,导致5人被烧死亡,6人重伤,两人轻伤。
调查组认为,该事故属于一起责任事故。
该制药有限公司片剂车间爆炸事故汲取教训:1. 空调通风设备的正常运行是车间安全生产的前提。
空调通风设备检修需停车时,所涉岗位一定要停止生产,岗位不能有生产人员,物流停止,趋于静态。
待空调通风设备正常运行后再组织生产。
2. 电气设备的安全性是车间安全生产的一个重要环节。
专业的电气工作人员应对车间所有的用电设备及线路定期进行认真细致的安全巡检,特别是防爆岗位设备的防爆性能有无缺陷要进行检查,发现问题及时处理。
中药提取车间安全事故案例

中药提取车间安全事故案例1992年5月18日,湖北某制药厂皂素车间因药渣治理不善,发生重大燃烧爆炸事故,当场烧死10人,重伤1人,轻伤2人。
(一)事故经过某制药厂皂素车间生产的是避孕药中间体皂素,它以120﹟工业汽油作溶剂,提取黄山药、川地龙两种植物中的皂素并浓缩加工。
为了去掉植物废渣中含有的残留汽油,将药渣放入蒸发罐中进行加压、加温处理,两小时后,将药渣排放到空地上自然挥发6-8小时,使药渣中残留汽油基本除净。
由于药渣是用汽油浸泡过的木质纤维,很轻易燃烧,为此,当地农夫天天将该厂排出的约一吨半的药渣拉回家中做烧柴用。
5月18日7点30分,有14名农夫随着上班的职工一起进入堆放废药渣处装运废渣。
当班工人告诫农夫,药渣刚从罐中排出,自然蒸发残留汽油时间太短,劝阻他们不要装运。
但农夫急于早装运完回家收麦子,就是不听劝阻,强行哄抢。
在挖装药渣过程中,使现场空气中的汽油含量很快达到了爆炸极限。
8点02分,一农夫打火吸烟,当即引起爆炸和燃烧,导致火灾。
经过工厂消防队和全厂职工的全力扑救,大火很快被扑灭,现场留下了死难者横七竖八的尸体,惨不忍睹。
(二)事故分析造成这起爆炸火灾事故的直接原因是,挖装药渣现场空气中的汽油含量达到爆炸极限,同时挖装药渣的农夫打火吸烟,从而导致爆炸和火灾事故的发生。
造成事故的间接原因是,制药厂对药渣处理治理不善,任凭农夫任意挖装药渣,没有采取任何安全防范措施。
(三)事故教训与防范措施事故发生后,省、市政府及制药厂领导组成事故调查组,经调查认定,这起事故属于非生产性爆炸燃烧事故,但制药厂也负有一定责任。
在妥善处理伤亡人员的同时,调查组对厂内存在的不安全因素也进行了检查,并提出建议和制定措施。
(1)改进药渣处理方法。
1988年5月该制药厂曾发生过药渣燃烧爆炸事故,当场炸死农夫1人。
因为事故是由于农夫将药渣拉回家的途中吸烟引起的,当地法院认定制药厂无责任。
但制药厂并未重视事故教训,导致此类事故又一次发生。
生物制药企业车间安全事故案例分析

生物制药企业车间安全事故案例分析----某制药厂克念菌素中毒案例分析某药厂于2005年6月3日发生一起克念菌素中毒事故,现将分析情况报告如下:1、事故经过2005年6月3日上午9点30分,某药厂302车间开始生产克念菌素,在生产过程中产生少量粉尘。
在该室操作的共有4人,上午l1时左右工作结束。
其后1名女操作工于上午l1:30左右感觉不舒服,有发冷、寒战、恶心、头晕、喉部不适等症状。
后感觉呼吸时胸部疼痛,咳嗽加剧,咳后呕吐,共呕吐了7次左右。
下午1:30到医院就诊。
经检查,T 37.5℃,P 80次/min。
R 20次/min,呼吸急促,CT报告两肺纹理增粗、紊乱,经葡萄糖、鱼腥草针、左克针、泰诺林胶囊治疗,症状缓解。
另两名工人下午上班时(b-3o)感觉头昏、头晕、恶心、胸闷、发冷、乏力,于下午3时、4时到医院就诊,另一人未见特殊反应,而未就诊。
医院给予抗菌、抗毒素、激素等治疗后,症状缓解。
目前均已恢复。
2、现场调查某药厂302车间位于外沙东厂区内,该车间主要生产固体制剂,2005年6月3日上午开始生产克念菌素,所用克念菌素原料量75 kg,克念菌素生产工艺流程:用克念菌素原料(颗粒状),加入预胶代淀粉、微晶纤维素、微粒硅胶、硬脂酸镁,经粉碎过筛再混合。
上午粉碎过筛,下午再混合。
粉碎过筛位于302车间四楼417室过筛室内,该室长约4m,宽约2m,高约2.7m.内有一台旋涡振荡筛和一台风冷式粉碎机,天花板上有一个500 mm×6oo mm 的送风口,东北墙角有一个4OO mm ×500 mm 的排风口,地面和粉碎机上散有少量棕黄色和白色粉末。
据介绍6月3日上午生产室内送排风装置已开启,但粉碎机内除尘风机未开启,导致室内有粉尘扬起(经调查,平时工作时全都开启)。
4名操作工进入车间前经二次更衣后穿上连体工作衣帽再戴上普通纱布口罩,但其中一人未戴口罩就进行操作。
3、中毒事故分析通过调查了解及现场勘察。
制药厂火灾事故案例分析

制药厂火灾事故案例分析引言在现代化社会中,制药厂是一个十分重要的行业,它的发展关系到国家的药品供应和人民的生命健康。
然而,由于生产过程中存在的安全隐患,制药厂火灾事故时有发生。
一旦发生火灾,不仅对制药厂的生产造成重大损失,还会对周围环境和居民的生命财产安全造成严重威胁。
本文将通过一个制药厂火灾事故案例分析,探讨制药厂火灾的原因、影响和应对措施,以期为今后制药厂安全管理提供一定的借鉴。
一、制药厂火灾事故案例介绍某市一家制药厂是一家规模较大的制药企业,专业生产化学合成原料和制剂,产品畅销国内外。
该制药厂位于该市郊区,周围居民较少,紧邻高速公路,交通便利。
2017年7月5日清晨,该制药厂发生火灾事故,造成重大损失。
据当事人介绍,火灾是由厂区的一处化学储存仓库内一氧化碳泄漏引发的。
据悉,当时正值夏季高温期,厂区内多处仓库内储存有各种化学原料。
在当天凌晨2时30分左右,工人发现一氧化碳气体泄漏。
为了尽快排除事故隐患,工人立即向仓库投放二氧化碳灭火器,试图控制泄漏。
然而,由于泄漏源头处于仓库深处,气体浓度极高,二氧化碳灭火器并未见效。
工人随后果断撤离现场并向厂方报告。
此时,天色逐渐变亮,气温升高,一氧化碳与空气混合爆炸,引发了火灾。
由于事发时正值夜班工人换班时间,40多名工人被困在现场,其中部分工人被困仓库内。
由于化学原料的特殊性,火势很快蔓延至整个厂区,并向周边蔓延。
事故发生后,消防部门迅速赶到现场,开始全力扑救火灾。
经过11个小时的全力扑救,火势得到控制。
然而,由于当时天气炎热,加上一氧化碳泄漏,火势一度失控,造成了工人伤亡和严重的财产损失。
根据初步统计,火灾事故共造成5人死亡,20多人受伤,厂房、设备和原料损失数千万元。
此外,火灾扩散引发了周边区域的空气污染和环境污染,引起了当地居民的恐慌。
二、制药厂火灾事故原因分析1. 火灾事故的直接原因火灾事故的直接原因是一氧化碳泄漏引起的。
据相关人员介绍,一氧化碳是一种无色无味的有毒气体,易燃易爆,是制药厂生产过程中的常见危险品。
药品企业安全生产事故案例

药品企业安全生产事故案例药品企业是关系到人民健康和生命安全的重要行业之一,安全生产事故的发生不仅会对企业造成巨大的损失,还可能对人民群众的生命财产安全造成严重威胁。
下面介绍一起药品企业安全生产事故案例,以便于引起各方对药品企业安全生产的重视。
该药品企业是一家规模较大的制药公司,主要生产中成药、化学药以及生物制品。
该企业位于一个工业园区内,拥有完善的生产设备和技术力量。
然而,在2018年的某一天,该企业发生了一起严重的安全生产事故。
事故发生在该企业的一条生产线上,据初步调查,原因是生产线上的一个设备出现了设备故障,并未及时得到维修。
当时,该设备负责生产一种化学药品,属于高危品种。
由于设备故障,导致药品生产过程中的温度无法控制,化学反应不受控制,最终产生了大量的有毒气体。
由于生产线上没有及时发现异常情况,没有及时采取应急措施,有毒气体蔓延到了整个车间。
当发生事故时,车间内有近百名工人在进行生产作业。
在有毒气体的侵袭下,工人们瞬间感觉呼吸困难,并出现头晕、恶心等中毒症状。
面对突如其来的危险,工人们纷纷跑向出口,但由于车间的设计存在缺陷,出口并不够多,并且有毒气体的侵袭速度非常快,导致很多工人无法及时逃离现场。
事故发生后,企业立即启动了应急预案,并通知了相关部门提供支持与救援。
当地消防部门、卫生部门等立即赶赴现场,对事故发生地区进行了封锁与疏散,并对受伤的工人进行了救治。
经过一天的紧急搜救和救治工作,最终有40多名工人被救出,其中3人因伤势过重不幸身亡。
随后,有关部门进行了对该企业的调查与责任追究。
调查发现,该企业在安全生产方面存在着严重的问题,主要体现在以下几个方面。
首先,对于设备的维护保养不够重视,导致设备故障没有及时得到维修。
其次,对于化学药品生产过程中可能产生的有毒气体的监测与控制不到位,导致出现了有毒气体泄漏的危险。
再次,车间的疏散通道设计不合理,出口不够多,对工人逃生形成了阻碍。
最后,对于事故发生时的应急处理与救援措施不够及时有效,导致事故造成了更严重的后果。
化学制药合成车间安全事故案例分析

化学制药合成车间安全事故案例分析该案例中,一家化学制药公司的合成车间发生了爆炸事故,造成多人受伤和车间设备的严重损坏。
经过调查,事故的原因归结为以下几个方面。
首先,缺乏正确的安全管理措施是导致事故的主要原因之一、公司在安全管理方面存在严重缺陷,没有建立完善的安全操作规程和标准化作业程序。
车间内的操作人员没有得到充分的安全培训,缺乏对化学品性质和操作规程的了解,导致在操作过程中出现了错误。
其次,车间内存在着不合理的设备配置和布局。
事故发生前,车间内设备摆放杂乱,化学品储存不当。
存在火源和易燃物质相互接触的风险,导致了事故的发生。
此外,车间内的通风系统不完善,无法有效消除有害气体和蒸汽,加剧了事故后果的严重程度。
再次,缺乏有效的应急预案和紧急救援措施也是该事故的原因之一、事故发生后,车间内的应急响应不及时,未能迅速切断有关设备的电源、气源等,造成事故扩大和事故人员无法及时脱离现场。
为了避免类似事故的再次发生,需要采取一些预防措施和改进措施。
首先,公司应加强安全意识教育和培训,确保所有人员都具备必要的安全知识和技能。
其次,应建立完善的安全管理体系,制定详细的安全操作规程和作业程序,并加强对操作人员的监督和管理。
此外,应优化车间布局和设备配置,确保火源和易燃物质的隔离,完善通风系统,确保排放有害气体和蒸汽,减少事故后果。
同时,应建立健全的应急预案和紧急救援机制,提前制定应急处置方案,加强应急演练和培训,提升应急响应能力。
总之,化学制药合成车间安全事故的发生给人员安全和环境带来了巨大威胁。
通过分析该案例,我们可以看到缺乏正确的安全管理措施、不合理的设备配置和布局以及缺乏有效的应急预案和紧急救援措施是造成事故的主要原因。
为了预防类似事故的发生,我们应加强安全意识教育和培训,建立完善的安全管理体系,优化设备配置和布局,并制定健全的应急预案和紧急救援措施。
只有全面提升安全管理水平,才能确保化学制药合成车间的安全运营。
化学制药合成车间安全事故案例分析

化学制药合成车间安全事故案例分析2010年2月27日15时10分许,某药业有限公司发生一起容器爆炸并引发火灾事故,造成2人死亡,2人受伤,直接经济损失约224万元。
药业有限公司,现有职工1000余人,主要生产、销售医药中间体、香料香精、化工产品。
2009年6月,该公司一期工程即1.2万t/a植物酮、5000t/a芳樟醇、3000t/a柠檬醛生产装置建成并进行试生产。
2009年12月22日,取得安全生产许可证。
事故发生车间606车间的主要产品为香料芳樟醇,其最初原料是丙酮,车间有两套醇化系统,分别为丙酮、甲基庚烯酮醇化系统,车间分别称之为第一、第二醇化。
因春节放假,该公司从2010年2月27日开始恢复芳樟醇606车间生产,在恢复生产前,用氨和乙炔混合气(乙炔含量25%)对第二醇化系统试压。
11时左右,发现醇化釜C底阀上端法兰漏气,在对醇化釜C进行泄压后,对底阀上端的法兰垫片进行更换,在卸下连接螺栓之后,两片法兰之间产生了3厘米左右的空隙,整个更换过程用时约50分钟。
13时左右,用乙炔、氨混合气体对醇化釜C继续进行试压,又发现醇化釜C底阀上部短节处漏气,对漏气处法兰的螺栓进行了拧紧加固。
14时20分左右,维修工作完成后又对醇化釜C进行试压,15时许,醇化釜C压力上升到17公斤左右。
15时10分左右,醇化系统缓冲罐发生爆炸并引发火灾,造成2人死亡,2人受伤。
事故发生的直接原因是:违章操作,在对醇化釜C底阀上端法兰更换垫片过程中,空气由醇化釜C进入了缓冲罐,与缓冲罐内的乙炔、氨气体混合,并达到了爆炸极限。
操作工在用乙炔、氨混合气进行试压时,在缓冲罐内造成绝热压缩,产生了引爆已经达到爆炸极限的乙炔、氨、空气混合气体的能量,使其在缓冲罐内发生了化学爆炸。
事故发生的间接原因是:企业对作业现场的安全管理不到位,在系统试压时,没有制订具体的开车方案,未按照操作规程要求对醇化系统进行置换,未及时发现和制止开车过程中的违章行为;职工安全意识不强,未对职工进行有效地安全生产教育培训,导致职工安全意识淡薄,存在侥幸心理,没有估计到违章作业可能造成的危险。
药厂典型事故案例培训课件

药厂典型事故案例培训课件药厂典型事故案例培训课件药厂是生产药品的重要场所,但由于药品的特殊性质,药厂事故可能会对人们的生命安全和健康造成严重威胁。
为了提高药厂员工的安全意识和应急处理能力,本次培训课件将通过典型事故案例的介绍,帮助大家了解药厂事故的原因、影响和防范措施。
一、事故案例一:药品泄漏引发火灾在某药厂的生产车间,由于操作不当,导致一种易燃药品泄漏。
由于车间内通风不良,药品蒸气无法及时扩散,最终引发火灾。
火势迅速蔓延,造成严重的人员伤亡和财产损失。
这起事故的原因主要有两点:一是操作不当,员工在操作过程中没有严格遵守安全规程,没有正确使用防护设备;二是车间通风不良,没有及时检查和维护通风设备,导致药品蒸气无法及时扩散。
为了防范这类事故,药厂应加强员工的安全培训,提高他们的操作技能和安全意识。
同时,药厂管理人员应定期检查和维护通风设备,确保车间内的空气流通畅通。
二、事故案例二:药品交叉污染导致不良反应在某药厂的生产流水线上,由于操作员疏忽,将两种不同药品的原料混在一起。
这种交叉污染导致了不良反应,使得药品的质量受到了严重影响,不仅造成了巨大的经济损失,还可能对患者的健康造成威胁。
这起事故的原因主要是人为疏忽和操作不规范。
为了防止这类事故的发生,药厂应加强员工的操作规范培训,强调操作员的责任和注意事项。
同时,药厂应建立严格的质量控制体系,确保每个环节都有相应的检查和验证机制,防止交叉污染的发生。
三、事故案例三:药品存储不当引发爆炸在某药厂的仓库中,由于存储条件不当,导致一种化学药品发生爆炸。
爆炸造成了巨大的噪音和火焰,对周边环境和人员造成了严重威胁。
这起事故的原因主要是仓库管理不善和存储条件不当。
为了防止这类事故的发生,药厂应加强仓库管理,确保存储条件符合要求,药品得到妥善保管。
同时,药厂应定期检查和维护仓库设施,确保设施的完好性和安全性。
四、事故案例四:药品包装破损导致泄露在某药厂的包装车间,由于包装机械故障,导致药品包装破损,药品泄露。
生物制药企业车间安全事故案例分析

生物制药企业车间安全事故案例分析引言:近年来,随着生物医药技术的不断发展,生物制药企业在全球范围内得到了快速发展。
然而,随之而来的是生物制药企业车间安全事故的增加。
生物制药企业车间安全事故的发生不仅对企业造成一定的经济损失,更重要的是可能对人员健康和生命安全产生严重威胁。
本文将通过分析一个生物制药企业车间安全事故案例,探讨其原因和防范措施。
案例描述:生物制药企业车间发生了一起严重的事故,导致多名工人受伤。
据了解,该企业正在生产一种新型药物,使用了一种高风险的化学原料。
事故发生后,现场调查人员发现,该企业在安全管理方面存在以下问题:车间内未设置明显的安全警示标志,工人在操作过程中缺乏安全教育培训,防护设备的使用不规范等。
案例分析:1.缺乏明显的安全警示标志:车间内未设置明显的安全警示标志是导致事故发生的重要原因之一、在生物制药企业车间,存在着一些潜在的危险因素,如化学物品的泄漏、火灾等,如果车间内没有明显的安全警示标志,工人难以及时察觉到这些潜在危险,从而增加了事故发生的风险。
2.工人缺乏安全教育培训:工人在操作过程中缺乏安全教育培训也是导致事故发生的重要原因之一、在生物制药企业车间,往往涉及到一些高风险工作,如化学物品的混合、反应等。
如果工人没有接受过相关的安全教育培训,不了解操作规程和安全防护措施,就很容易在操作过程中出现错误,从而导致事故的发生。
3.防护设备使用不规范:防护设备的使用不规范也是导致事故发生的重要原因之一、在生物制药企业车间,往往需要工人佩戴防护眼镜、手套、口罩等防护设备。
如果工人不正确地佩戴或使用这些防护设备,就无法起到预防事故的作用。
例如,如果工人没有佩戴防护眼镜,化学物品溅入眼睛,就会对工人的健康和生命安全产生严重威胁。
综合防范措施:针对以上问题,生物制药企业应采取以下综合防范措施:1.设置明显的安全警示标志:在生物制药企业车间设置明显的安全警示标志,能够帮助工人及时察觉危险,并采取相应的安全措施,从而降低事故发生的风险。
2022年3月份安全事故案例分析

2022年3月份安全事故案例分析今年3月,位于宜春市铜鼓县工业园区的江西佰利达制药有限公司发生一起爆炸事故,造成1人死亡、2人受伤。
安全事故发生后,江西省应急管理厅、宜春市委市政府领导高度重视,分别作出指示批示,要求全力救治伤者,做好善后安全稳定,迅速查明事故原因,严格落实“三个一律”[1]措施。
省应急管理厅主要领导视频连线调度现场救援处置情况,指导事故调查和善后处置;省应急管理厅有关负责同志及专家会同宜春市应急管理局有关人员立即赶赴事故现场指导救援,传达了应急管理部、省应急管理厅领导相关指示要求,并通过勘查事故现场、调阅相关图纸资料、与有关人员谈话等方式,对事故情况进行了初步调查了解。
现做以下案例分析。
一、事故发生经过春节过后,佰利达公司向铜鼓县工业园区管委会和县应急管理局报备后复工。
3月10日20时,佰利达公司进行晚班交接班,晚班班长蓝某平,操作工陈某良、陈某富、单某明、何某、钟某才、刘某成等7名工作人员上岗。
3月11日1时30分左右,蓝某平、陈某富、何某、刘某成在101车间一楼。
陈某良、钟某才、单某明在101车间二层操作平台。
1时31分左右,陈某良在查看合成釜设备运行情况时大喊“蓝师傅,合成釜温度高了,升得太快,不对劲”,蓝某平、何某立即上二层操作平台查看;陈某富由于想上厕所,上二楼休息室放安全帽。
1时33分左右,合成釜开始冒出大量白烟,并迅速弥漫,员工见状后当即跑开。
2-3秒钟后,合成釜随即发生爆炸。
爆炸冲击波造成蓝某平死亡;钟某才脾脏破裂,左侧第11肋骨骨折;飞溅物砸中陈某良左小腿,造成左小腿高断,远端缺失而截肢。
二、事故发生原因1、违法储存。
佰利达公司超品种储存二氯乙烷、五氧化二磷、双氧水、尿素、纯碱等许可范围未涉及的多种危险化学品,且数量较大。
2、. 安全管理混乱。
佰利达公司安全生产责任制不落实,安全生产职责不清,规章制度不健全,未制定岗位安全操作规程和管理制度。
未配备化工安全类注册安全工程师,未认真组织开展隐患排查治理、应急救援演练,风险管控措施缺失,应急处置能力严重不足。
违反药品gmp的案例(3篇)
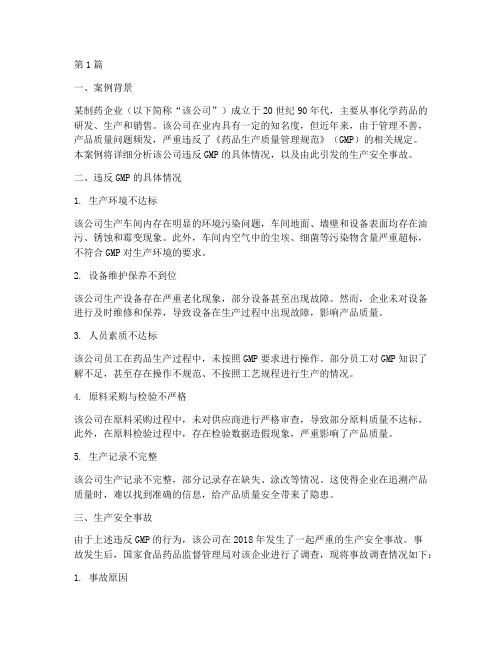
第1篇一、案例背景某制药企业(以下简称“该公司”)成立于20世纪90年代,主要从事化学药品的研发、生产和销售。
该公司在业内具有一定的知名度,但近年来,由于管理不善,产品质量问题频发,严重违反了《药品生产质量管理规范》(GMP)的相关规定。
本案例将详细分析该公司违反GMP的具体情况,以及由此引发的生产安全事故。
二、违反GMP的具体情况1. 生产环境不达标该公司生产车间内存在明显的环境污染问题,车间地面、墙壁和设备表面均存在油污、锈蚀和霉变现象。
此外,车间内空气中的尘埃、细菌等污染物含量严重超标,不符合GMP对生产环境的要求。
2. 设备维护保养不到位该公司生产设备存在严重老化现象,部分设备甚至出现故障。
然而,企业未对设备进行及时维修和保养,导致设备在生产过程中出现故障,影响产品质量。
3. 人员素质不达标该公司员工在药品生产过程中,未按照GMP要求进行操作。
部分员工对GMP知识了解不足,甚至存在操作不规范、不按照工艺规程进行生产的情况。
4. 原料采购与检验不严格该公司在原料采购过程中,未对供应商进行严格审查,导致部分原料质量不达标。
此外,在原料检验过程中,存在检验数据造假现象,严重影响了产品质量。
5. 生产记录不完整该公司生产记录不完整,部分记录存在缺失、涂改等情况。
这使得企业在追溯产品质量时,难以找到准确的信息,给产品质量安全带来了隐患。
三、生产安全事故由于上述违反GMP的行为,该公司在2018年发生了一起严重的生产安全事故。
事故发生后,国家食品药品监督管理局对该企业进行了调查,现将事故调查情况如下:1. 事故原因事故原因主要有以下几点:(1)生产环境不达标,导致生产过程中污染物进入药品,影响产品质量。
(2)设备维护保养不到位,导致设备故障,引发安全事故。
(3)人员素质不达标,操作不规范,导致产品质量不合格。
(4)原料采购与检验不严格,导致原料质量不达标,影响产品质量。
2. 事故影响事故发生后,该公司生产的部分药品被召回,造成了较大的经济损失。
制药企业制剂车间安全事故案例及分析
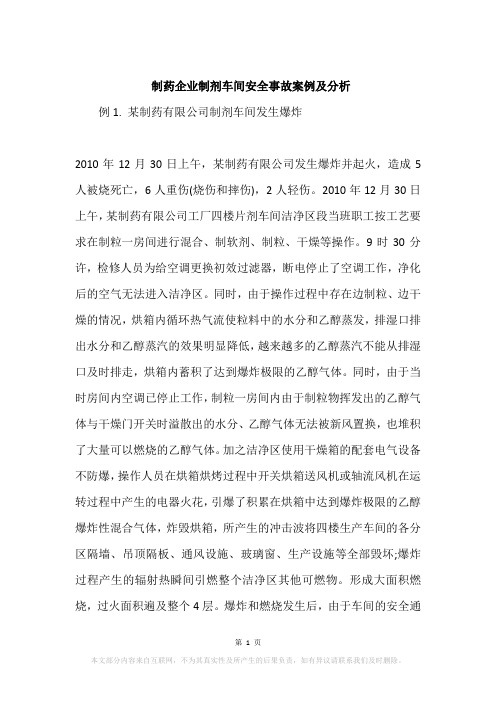
制药企业制剂车间安全事故案例及分析例1. 某制药有限公司制剂车间发生爆炸2010年12月30日上午,某制药有限公司发生爆炸并起火,造成5人被烧死亡,6人重伤(烧伤和摔伤),2人轻伤。
2010年12月30日上午,某制药有限公司工厂四楼片剂车间洁净区段当班职工按工艺要求在制粒一房间进行混合、制软剂、制粒、干燥等操作。
9时30分许,检修人员为给空调更换初效过滤器,断电停止了空调工作,净化后的空气无法进入洁净区。
同时,由于操作过程中存在边制粒、边干燥的情况,烘箱内循环热气流使粒料中的水分和乙醇蒸发,排湿口排出水分和乙醇蒸汽的效果明显降低,越来越多的乙醇蒸汽不能从排湿口及时排走,烘箱内蓄积了达到爆炸极限的乙醇气体。
同时,由于当时房间内空调已停止工作,制粒一房间内由于制粒物挥发出的乙醇气体与干燥门开关时溢散出的水分、乙醇气体无法被新风置换,也堆积了大量可以燃烧的乙醇气体。
加之洁净区使用干燥箱的配套电气设备不防爆,操作人员在烘箱烘烤过程中开关烘箱送风机或轴流风机在运转过程中产生的电器火花,引爆了积累在烘箱中达到爆炸极限的乙醇爆炸性混合气体,炸毁烘箱,所产生的冲击波将四楼生产车间的各分区隔墙、吊顶隔板、通风设施、玻璃窗、生产设施等全部毁坏;爆炸过程产生的辐射热瞬间引燃整个洁净区其他可燃物。
形成大面积燃烧,过火面积遍及整个4层。
爆炸和燃烧发生后,由于车间的安全通道只有一条,部分现场人员和受伤人员不能及时逃生,导致5人被烧死亡,6人重伤,两人轻伤。
调查组认为,该事故属于一起责任事故。
该制药有限公司片剂车间爆炸事故汲取教训:1. 空调通风设备的正常运行是车间安全生产的前提。
空调通风设备检修需停车时,所涉岗位一定要停止生产,岗位不能有生产人员,物流停止,趋于静态。
待空调通风设备正常运行后再组织生产。
2. 电气设备的安全性是车间安全生产的一个重要环节。
专业的电气工作人员应对车间所有的用电设备及线路定期进行认真细致的安全巡检,特别是防爆岗位设备的防爆性能有无缺陷要进行检查,发现问题及时处理。
药企火灾事故分析总结范文
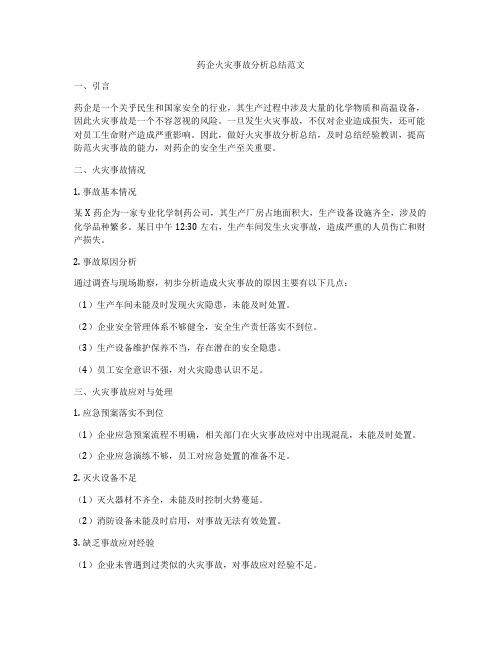
药企火灾事故分析总结范文一、引言药企是一个关乎民生和国家安全的行业,其生产过程中涉及大量的化学物质和高温设备,因此火灾事故是一个不容忽视的风险。
一旦发生火灾事故,不仅对企业造成损失,还可能对员工生命财产造成严重影响。
因此,做好火灾事故分析总结,及时总结经验教训,提高防范火灾事故的能力,对药企的安全生产至关重要。
二、火灾事故情况1. 事故基本情况某X药企为一家专业化学制药公司,其生产厂房占地面积大,生产设备设施齐全,涉及的化学品种繁多。
某日中午12:30左右,生产车间发生火灾事故,造成严重的人员伤亡和财产损失。
2. 事故原因分析通过调查与现场勘察,初步分析造成火灾事故的原因主要有以下几点:(1)生产车间未能及时发现火灾隐患,未能及时处置。
(2)企业安全管理体系不够健全,安全生产责任落实不到位。
(3)生产设备维护保养不当,存在潜在的安全隐患。
(4)员工安全意识不强,对火灾隐患认识不足。
三、火灾事故应对与处理1. 应急预案落实不到位(1)企业应急预案流程不明确,相关部门在火灾事故应对中出现混乱,未能及时处置。
(2)企业应急演练不够,员工对应急处置的准备不足。
2. 灭火设备不足(1)灭火器材不齐全,未能及时控制火势蔓延。
(2)消防设备未能及时启用,对事故无法有效处置。
3. 缺乏事故应对经验(1)企业未曾遇到过类似的火灾事故,对事故应对经验不足。
(2)员工未能迅速逃生,对应急逃生道路不熟悉。
四、火灾事故风险防范1. 加强安全管理(1)建立健全的安全管理体系,明确安全职责,加强安全培训。
(2)加强安全生产监管,引进先进的生产管理模式。
2. 提高员工安全意识(1)加强员工安全教育,提高员工对火灾隐患的识别能力。
(2)加强员工火灾应对演练,提高逃生自救能力。
3. 加强火灾风险识别和评估(1)建立火灾风险识别机制,对生产工艺、设备设施、储存物品进行综合评估。
(2)加强火灾隐患的整改,及时消除安全隐患。
4. 增强灭火设备和消防设备(1)增加灭火器材的存放点,确保在火灾事故发生时能够及时使用。
- 1、下载文档前请自行甄别文档内容的完整性,平台不提供额外的编辑、内容补充、找答案等附加服务。
- 2、"仅部分预览"的文档,不可在线预览部分如存在完整性等问题,可反馈申请退款(可完整预览的文档不适用该条件!)。
- 3、如文档侵犯您的权益,请联系客服反馈,我们会尽快为您处理(人工客服工作时间:9:00-18:30)。
化学制药合成车间安全事故案例分析
2010年2月27日15时10分许,某药业有限公司发生一起容器爆炸并引发火灾事故,造成2人死亡,2人受伤,直接经济损失约224万元。
药业有限公司,现有职工1000余人,主要生产、销售医药中间体、香料香精、化工产品。
2009年6月,该公司一期工程即1.2万t/a植物酮、5000t/a芳樟醇、3000t/a柠檬醛生产装置建成并进行试生产。
2009年12月22日,取得安全生产许可证。
事故发生车间606车间的主要产品为香料芳樟醇,其最初原料是丙酮,车间有两套醇化系统,分别为丙酮、甲基庚烯酮醇化系统,车间分别称之为第一、第二醇化。
因春节放假,该公司从2010年2月27日开始恢复芳樟醇606车间生产,在恢复生产前,用氨和乙炔混合气(乙炔含量25%)对第二醇化系统试压。
11时左右,发现醇化釜C底阀上端法兰漏气,在对醇化釜C进行泄压后,对底阀上端的法兰垫片进行更换,在卸下连接螺栓之后,两片法兰之间产生了3厘米左右的空隙,整个更换过程用时约50分钟。
13时左右,用乙炔、氨混合气体对醇化釜C继续进行试压,又发现醇化釜C底阀上部短节处漏气,对漏气处法兰的螺栓进行了拧紧加固。
14时20分左右,维修工作完成后又对醇化釜C进行试压,15时许,醇化釜C压力上升到17公斤左右。
15时10分左右,醇化系统缓冲罐发生爆炸并引发火灾,造成2人死亡,2人受伤。
事故发生的直接原因是:违章操作,在对醇化釜C底阀上端法兰更换垫片过程中,空气由醇化釜C进入了缓冲罐,与缓冲罐内的乙炔、氨气体混合,并达到了爆炸极限。
操作工在用乙炔、氨混合气进行试压时,在缓冲罐内造成绝热压缩,产生了引爆已经达到爆炸极限的乙炔、氨、空气混合气体的能量,使其在缓冲罐内发生了化学爆炸。
事故发生的间接原因是:企业对作业现场的安全管理不到位,在系统试压时,没有制订具体的开车方案,未按照操作规程要求对醇化系统进行置换,未及时发现和制止开车过程中的违章行为;职工安全意识不强,未对职工进行有效地安全
生产教育培训,导致职工安全意识淡薄,存在侥幸心理,没有估计到违章作业可能造成的危险。