对混凝土早期强度高,后期强度增长缓慢的几点看法
水泥细度对混凝土强度的影响
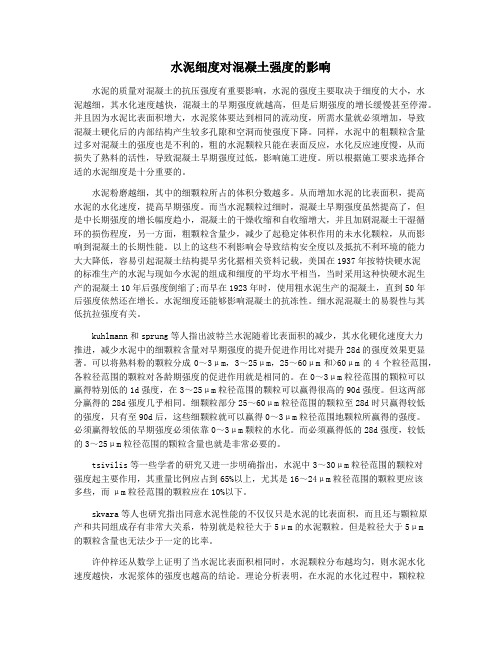
水泥细度对混凝土强度的影响水泥的质量对混凝土的抗压强度有重要影响,水泥的强度主要取决于细度的大小,水泥越细,其水化速度越快,混凝土的早期强度就越高,但是后期强度的增长缓慢甚至停滞。
并且因为水泥比表面积增大,水泥浆体要达到相同的流动度,所需水量就必须增加,导致混凝土硬化后的内部结构产生较多孔隙和空洞而使强度下降。
同样,水泥中的粗颗粒含量过多对混凝土的强度也是不利的,粗的水泥颗粒只能在表面反应,水化反应速度慢,从而损失了熟料的活性,导致混凝土早期强度过低,影响施工进度。
所以根据施工要求选择合适的水泥细度是十分重要的。
水泥粉磨越细,其中的细颗粒所占的体积分数越多。
从而增加水泥的比表面积,提高水泥的水化速度,提高早期强度。
而当水泥颗粒过细时,混凝土早期强度虽然提高了,但是中长期强度的增长幅度趋小,混凝土的干燥收缩和自收缩增大,并且加剧混凝土干湿循环的损伤程度,另一方面,粗颗粒含量少,减少了起稳定体积作用的未水化颗粒,从而影响到混凝土的长期性能。
以上的这些不利影响会导致结构安全度以及抵抗不利环境的能力大大降低,容易引起混凝土结构提早劣化据相关资料记载,美国在1937年按特快硬水泥的标准生产的水泥与现如今水泥的组成和细度的平均水平相当,当时采用这种快硬水泥生产的混凝土10年后强度倒缩了;而早在1923年时,使用粗水泥生产的混凝土,直到50年后强度依然还在增长。
水泥细度还能够影响混凝土的抗冻性。
细水泥混凝土的易裂性与其低抗拉强度有关。
kuhlmann和sprung等人指出波特兰水泥随着比表面积的减少,其水化硬化速度大力推进,减少水泥中的细颗粒含量对早期强度的提升促进作用比对提升28d的强度效果更显著。
可以将熟料粉的颗粒分成0~3μm,3~25μm,25~60μm和>60μm的4个粒径范围,各粒径范围的颗粒对各龄期强度的促进作用就是相同的。
在0~3μm粒径范围的颗粒可以赢得特别低的1d强度,在3~25μm粒径范围的颗粒可以赢得很高的90d强度。
混凝土的龄期及强度发展规律
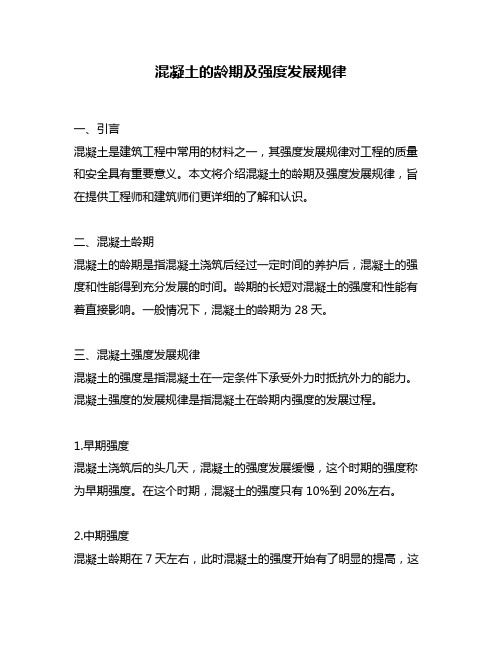
混凝土的龄期及强度发展规律一、引言混凝土是建筑工程中常用的材料之一,其强度发展规律对工程的质量和安全具有重要意义。
本文将介绍混凝土的龄期及强度发展规律,旨在提供工程师和建筑师们更详细的了解和认识。
二、混凝土龄期混凝土的龄期是指混凝土浇筑后经过一定时间的养护后,混凝土的强度和性能得到充分发展的时间。
龄期的长短对混凝土的强度和性能有着直接影响。
一般情况下,混凝土的龄期为28天。
三、混凝土强度发展规律混凝土的强度是指混凝土在一定条件下承受外力时抵抗外力的能力。
混凝土强度的发展规律是指混凝土在龄期内强度的发展过程。
1.早期强度混凝土浇筑后的头几天,混凝土的强度发展缓慢,这个时期的强度称为早期强度。
在这个时期,混凝土的强度只有10%到20%左右。
2.中期强度混凝土龄期在7天左右,此时混凝土的强度开始有了明显的提高,这个时期的强度称为中期强度。
在这个时期,混凝土的强度可以达到28天强度的50%左右。
3.后期强度混凝土的龄期在28天左右,此时混凝土的强度可以达到设计强度的70%左右,这个时期的强度称为后期强度。
在龄期到达28天后,混凝土强度的发展速度逐渐变缓,但是强度仍然会有所提高。
4.极限强度混凝土的极限强度是指混凝土能够承受的最大力量,在龄期达到28天后,混凝土的强度会逐渐趋于稳定,并且达到极限强度。
四、影响混凝土强度发展的因素混凝土强度的发展受到许多因素的影响,包括水胶比、水泥品种、养护条件、温度和湿度等。
1.水胶比水胶比是指混凝土中水的重量与水泥和其他固体材料重量的比值。
水胶比越小,混凝土的强度越高。
2.水泥品种不同的水泥品种对混凝土的强度发展具有不同的影响。
高强度的水泥可以提高混凝土的强度。
3.养护条件混凝土在养护过程中需要保持一定的湿度和温度,以促进混凝土强度的发展。
养护不当会导致混凝土强度的下降。
4.温度和湿度温度和湿度也会影响混凝土的强度发展。
过高或过低的温度会影响混凝土的强度,过高的湿度会导致混凝土的强度下降。
混凝土强度与龄期关系分析

混凝土强度与龄期关系分析一、前言混凝土是一种常用的建筑材料,其强度是评价混凝土质量的重要指标之一。
混凝土强度与龄期之间存在一定的关系,通过分析这种关系可以预测混凝土在不同龄期下的强度表现,为混凝土的工程应用提供依据。
本文将从混凝土强度的影响因素、混凝土龄期的定义及测试方法、混凝土强度与龄期关系等方面进行详细的分析和探讨。
二、混凝土强度的影响因素混凝土强度受多个因素的影响,主要包括以下几个方面:1.水灰比:水灰比是混凝土中水和水泥重量之比,它直接影响混凝土的强度,一般来说,水灰比越小,混凝土的强度越高。
2.骨料:混凝土中的骨料种类、粒径、形状等都会影响混凝土的强度,一般来说,较光滑的骨料强度较低,粗糙的骨料强度较高。
3.水泥品种:不同种类、品牌的水泥其强度差异较大,一般来说,硅酸盐水泥的强度比普通硬化水泥高。
4.混凝土配合比:混凝土中各组分的配比也会影响混凝土的强度。
5.施工工艺:混凝土的施工工艺对混凝土的强度也有直接影响。
三、混凝土龄期的定义及测试方法混凝土的龄期是指混凝土从浇筑开始到测试时的时间,龄期越长,混凝土的强度越高。
混凝土的龄期测试一般采用标准养护条件下的试块试验方法,具体步骤如下:1.混凝土试块制备:按照标准配合比制备混凝土试块,试块尺寸为150mm×150mm×150mm。
2.混凝土试块养护:混凝土试块在模具中振实后,应及时加盖模具盖,然后放入标准养护室养护,养护条件为温度(20±2)℃、湿度不小于90%。
3.混凝土试块测试:试块的测试应在规定的龄期内进行,常见的龄期包括3d、7d、28d等。
试块测试时应保持试块表面平整,不得有明显的裂缝和缺陷,测试时应采用压力机进行负荷测试。
四、混凝土强度与龄期关系混凝土强度与龄期之间的关系是一种非线性的曲线关系,一般来说,混凝土强度会随着龄期的增加而增加。
根据实验数据统计,混凝土强度与龄期之间的关系可以用以下公式进行表示:f(t)=k×t^n其中,f(t)表示龄期为t时的混凝土强度,k和n为常数,可以通过实验数据拟合得到。
混凝土的强度发展规律及影响因素

混凝土的强度发展规律及影响因素一、混凝土的强度发展规律混凝土的强度发展规律指的是混凝土在不同时间内的强度变化规律。
混凝土的强度是指在规定的条件下,混凝土所能承受的最大压力。
混凝土的强度发展规律与混凝土的材料特性、混凝土的配合比、混凝土的施工工艺以及混凝土的养护方式等因素有关。
1. 初期强度混凝土在浇筑后的最初几小时内会发生明显的水化反应,这个阶段的强度被称为初期强度。
这个阶段的强度增长非常快,一般在浇筑后的24小时内,混凝土的强度可以达到其28天强度的30%至40%左右。
2. 中期强度混凝土的中期强度是指混凝土的强度在浇筑后的3天至28天内逐渐增长的阶段。
在这个阶段内,混凝土的强度增长速度逐渐减缓,但是增长的幅度仍然很大。
一般来说,混凝土的中期强度可以达到其28天强度的70%至80%左右。
3. 后期强度混凝土的后期强度是指混凝土的强度在浇筑后的28天以后逐渐增长的阶段。
在这个阶段内,混凝土的强度增长速度非常缓慢,但是增长的幅度仍然存在。
一般来说,混凝土的后期强度可以达到其28天强度的100%至120%左右。
二、影响混凝土强度的因素1. 混凝土材料特性混凝土的材料特性是影响混凝土强度的最重要的因素之一。
混凝土的强度受到水泥的品种、砂子的粒径、骨料的种类和粒径、掺合料等因素的影响。
其中,水泥是混凝土强度的重要组成部分,其品种的不同会导致混凝土强度产生较大的差异。
2. 混凝土的配合比混凝土的配合比是指混凝土中水泥、砂子、骨料、水和掺合料的比例。
混凝土的配合比对混凝土的强度有很大的影响。
如果混凝土的水泥用量过少,混凝土的强度会相应地降低。
如果混凝土的水泥用量过多,混凝土的强度也不会提高,反而会导致混凝土的裂缝增多。
3. 混凝土的施工工艺混凝土的施工工艺也会对混凝土的强度产生一定的影响。
例如,混凝土的振捣程度、浇注速度、浇注高度、浇注温度等因素都会对混凝土的强度产生影响。
在施工过程中,如果振捣不当,会导致混凝土中的气泡无法排出,从而影响混凝土的强度。
混凝土强度随时间增长规律

混凝土强度随时间增长规律混凝土是一种常见的建筑材料,其强度随着时间的增长而不断提高。
这是因为混凝土在硬化过程中会发生化学反应,形成更加紧密的结构,从而提高其强度。
下面将详细介绍混凝土强度随时间增长的规律。
一、混凝土强度的定义混凝土强度是指混凝土在承受外力作用下的抗压能力。
通常用抗压强度来表示混凝土的强度,单位为兆帕(MPa)。
二、混凝土强度随时间增长的规律1. 初期强度增长快混凝土在浇筑后,最初的几天内强度增长非常快。
这是因为混凝土在这个时期内会发生水化反应,形成水化产物,从而使混凝土的结构更加紧密,强度也随之提高。
通常情况下,混凝土的初期强度在浇筑后的3天内达到了其28天强度的40%左右。
2. 中期强度增长缓慢混凝土的中期强度增长相对较缓慢,通常在浇筑后的7天到28天之间。
这是因为混凝土的水化反应已经基本完成,水化产物的形成速度减缓,从而导致强度增长速度变慢。
通常情况下,混凝土的中期强度在浇筑后的28天内达到了其设计强度的70%左右。
3. 后期强度增长较慢混凝土的后期强度增长非常缓慢,通常在浇筑后的28天到1年之间。
这是因为混凝土的水化反应已经基本结束,水化产物的形成速度非常缓慢,从而导致强度增长速度非常慢。
通常情况下,混凝土的后期强度在浇筑后的1年内达到了其设计强度的90%左右。
4. 长期强度增长仍然存在混凝土的长期强度增长仍然存在,通常在浇筑后的1年以上。
这是因为混凝土的水化反应虽然已经基本结束,但是混凝土中的水化产物仍然会不断地与周围环境发生反应,从而形成新的水化产物,使混凝土的结构更加紧密,强度也随之提高。
通常情况下,混凝土的长期强度在浇筑后的10年内会有所提高。
三、混凝土强度随时间增长的影响因素混凝土强度随时间增长的规律受到多种因素的影响,主要包括以下几个方面:1. 水胶比:水胶比越小,混凝土的强度越高。
2. 水泥种类:不同种类的水泥对混凝土的强度影响不同。
3. 骨料种类:不同种类的骨料对混凝土的强度影响不同。
混凝土的龄期及其对强度的影响原理

混凝土的龄期及其对强度的影响原理一、引言混凝土是一种广泛应用的建筑材料,在建筑和土木工程中具有重要的地位。
混凝土的龄期是指混凝土浇筑后所经历的时间,其对混凝土的强度和性能有着重要的影响。
本文将详细介绍混凝土的龄期及其对强度的影响原理。
二、混凝土的龄期混凝土的龄期是指混凝土浇筑后所经历的时间。
混凝土的龄期可以分为初期、中期和后期三个阶段。
初期是指混凝土刚浇筑后的时间,大约持续1-3天。
中期是指混凝土经历了初期后到达21天左右的时间。
后期是指混凝土经历了中期后的时间,大约持续28天以上。
三、混凝土的强度混凝土的强度是指混凝土能够承受的压力或拉力。
混凝土的强度是由其组成成分及其配合比、制备工艺、养护条件等因素决定的。
混凝土的强度可以分为抗压强度和抗拉强度两种。
四、混凝土龄期对强度的影响1.初期初期是混凝土的塑性变形期,混凝土在这个阶段内的强度增长较慢。
这是由于混凝土在这个阶段内的水化反应速度较慢,且水泥浆体中的大部分水分都被吸附在孔隙中,从而减缓了水化反应的速度。
此外,混凝土在初期的龄期内还存在着收缩和裂缝等问题,这些问题也会对混凝土的强度产生一定的影响。
2.中期中期是混凝土强度增长的主要阶段。
在这个阶段内,混凝土的水化反应速度逐渐加快,水泥胶体的硬化速度也逐渐增大。
混凝土中的钙矾土和硅酸盐等矿物质也会逐渐形成,这些矿物质的形成可以填充混凝土中的孔隙,从而提高混凝土的密实度和强度。
此外,中期还是混凝土收缩的重要阶段,混凝土在这个阶段内的收缩量较大,这也会对混凝土的强度产生一定的影响。
3.后期后期是混凝土强度增长的缓慢阶段。
在这个阶段内,混凝土的水化反应速度逐渐减缓,混凝土的强度增长速度也逐渐变缓。
此外,后期还是混凝土收缩的最后阶段,混凝土在这个阶段内的收缩量较小,但仍会对混凝土的强度产生一定的影响。
五、影响混凝土龄期及其强度的因素1.配合比混凝土的配合比是影响混凝土强度的重要因素之一。
合理的配合比可以保证混凝土的强度和性能。
混凝土龄期强度的影响因素
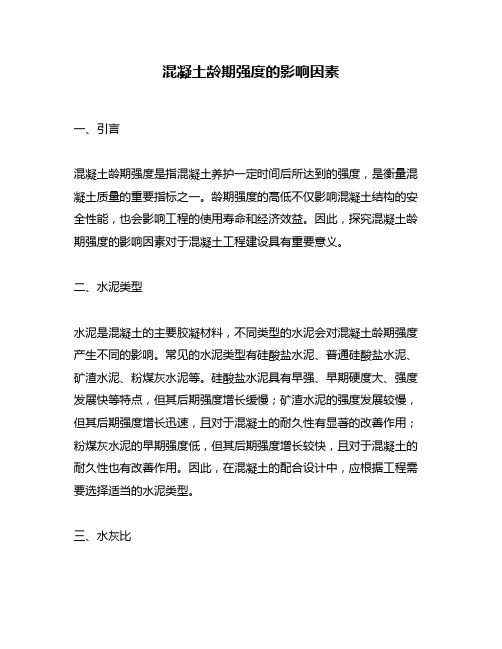
混凝土龄期强度的影响因素一、引言混凝土龄期强度是指混凝土养护一定时间后所达到的强度,是衡量混凝土质量的重要指标之一。
龄期强度的高低不仅影响混凝土结构的安全性能,也会影响工程的使用寿命和经济效益。
因此,探究混凝土龄期强度的影响因素对于混凝土工程建设具有重要意义。
二、水泥类型水泥是混凝土的主要胶凝材料,不同类型的水泥会对混凝土龄期强度产生不同的影响。
常见的水泥类型有硅酸盐水泥、普通硅酸盐水泥、矿渣水泥、粉煤灰水泥等。
硅酸盐水泥具有早强、早期硬度大、强度发展快等特点,但其后期强度增长缓慢;矿渣水泥的强度发展较慢,但其后期强度增长迅速,且对于混凝土的耐久性有显著的改善作用;粉煤灰水泥的早期强度低,但其后期强度增长较快,且对于混凝土的耐久性也有改善作用。
因此,在混凝土的配合设计中,应根据工程需要选择适当的水泥类型。
三、水灰比混凝土的水灰比是指混凝土中水和水泥质量的比值,水灰比的大小对混凝土龄期强度有着重要的影响。
水灰比过大会导致混凝土早期开裂、后期强度不足等问题,而水灰比过小则会导致混凝土难以拌和、施工困难等问题。
一般来说,水灰比越小,混凝土的龄期强度越高。
但是,如果过小的水灰比会导致混凝土的耐久性下降,甚至引起混凝土的龟裂。
四、养护条件混凝土的养护条件对混凝土龄期强度同样有着重要的影响。
养护的目的是为了保证混凝土在早期获得足够的强度,以满足后续施工的要求,提高混凝土的龄期强度。
混凝土的养护时间、养护温度、养护湿度等因素都会影响混凝土的龄期强度。
一般来说,养护时间越长、养护温度越高、养护湿度越大,混凝土的龄期强度就越高。
五、骨料骨料是混凝土的重要组成部分,骨料的性质也会对混凝土的龄期强度产生影响。
一般来说,骨料的强度越高、抗压强度越大,混凝土的龄期强度就越高。
此外,骨料的形状、粒度分布、含水率等因素也会影响混凝土的龄期强度。
例如,粗骨料的含水率过高会导致混凝土强度下降,而过细的骨料会导致混凝土的坍落度降低、施工难度加大。
混凝土的龄期与强度发展关系
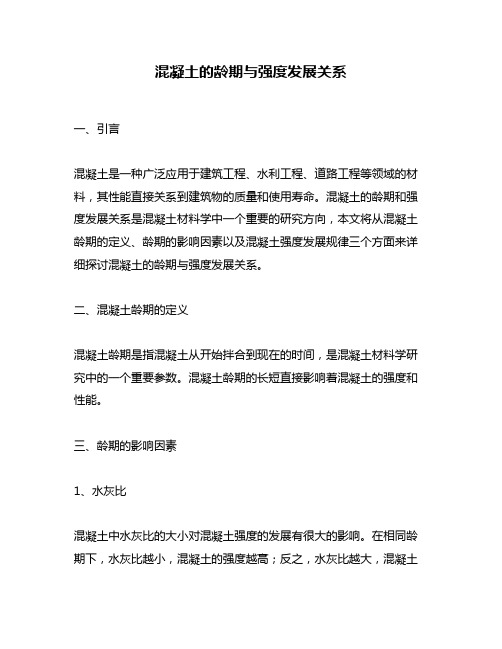
混凝土的龄期与强度发展关系一、引言混凝土是一种广泛应用于建筑工程、水利工程、道路工程等领域的材料,其性能直接关系到建筑物的质量和使用寿命。
混凝土的龄期和强度发展关系是混凝土材料学中一个重要的研究方向,本文将从混凝土龄期的定义、龄期的影响因素以及混凝土强度发展规律三个方面来详细探讨混凝土的龄期与强度发展关系。
二、混凝土龄期的定义混凝土龄期是指混凝土从开始拌合到现在的时间,是混凝土材料学研究中的一个重要参数。
混凝土龄期的长短直接影响着混凝土的强度和性能。
三、龄期的影响因素1、水灰比混凝土中水灰比的大小对混凝土强度的发展有很大的影响。
在相同龄期下,水灰比越小,混凝土的强度越高;反之,水灰比越大,混凝土的强度越低。
这是因为水灰比的变化会影响混凝土的孔隙度和结晶水的含量,从而影响混凝土的硬化过程。
2、拌合时间混凝土的拌合时间对混凝土龄期和强度发展都有影响。
在相同水灰比和混凝土配合比的情况下,拌合时间越长,混凝土强度越高,但同时也会导致混凝土的龄期延长。
3、温度温度是影响混凝土强度发展的重要因素之一。
在适宜的温度下,混凝土的硬化速度会加快,强度也会提高;但是在过高或过低的温度下,混凝土的强度会受到影响。
此外,温度变化还会导致混凝土龄期的变化。
4、混凝土配合比混凝土配合比的大小也直接影响着混凝土的强度发展。
在相同水灰比和拌合时间的情况下,配合比越小,混凝土强度越高;反之,配合比越大,混凝土强度越低。
四、混凝土强度发展规律1、初始阶段混凝土在初始阶段,由于水泥胶体和骨料之间的化学反应还未形成足够的胶凝物,强度增长速度较慢。
这个阶段的时间一般为几小时到几天。
2、加速阶段混凝土在加速阶段,胶凝物开始形成,强度增长速度加快。
这个阶段的时间一般为几天到几周。
3、减速阶段混凝土在减速阶段,强度增长速度逐渐减慢,这个阶段的时间一般为几周到几个月。
4、稳定阶段混凝土在稳定阶段,强度增长速度趋于平缓,但在一定程度上仍会有一定的强度增长。
混凝土的强度发展规律及影响因素
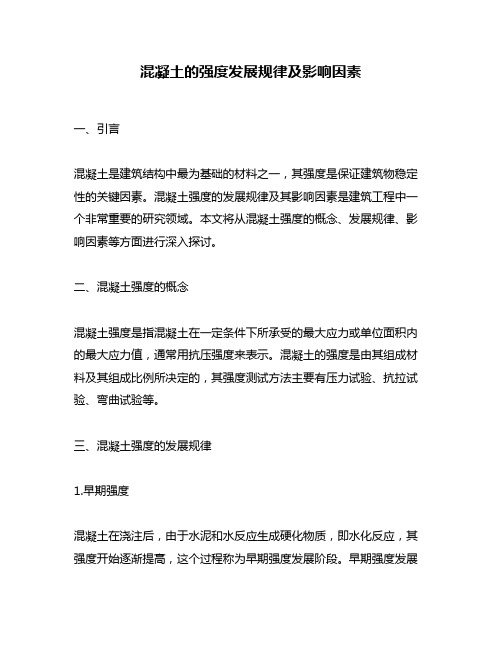
混凝土的强度发展规律及影响因素一、引言混凝土是建筑结构中最为基础的材料之一,其强度是保证建筑物稳定性的关键因素。
混凝土强度的发展规律及其影响因素是建筑工程中一个非常重要的研究领域。
本文将从混凝土强度的概念、发展规律、影响因素等方面进行深入探讨。
二、混凝土强度的概念混凝土强度是指混凝土在一定条件下所承受的最大应力或单位面积内的最大应力值,通常用抗压强度来表示。
混凝土的强度是由其组成材料及其组成比例所决定的,其强度测试方法主要有压力试验、抗拉试验、弯曲试验等。
三、混凝土强度的发展规律1.早期强度混凝土在浇注后,由于水泥和水反应生成硬化物质,即水化反应,其强度开始逐渐提高,这个过程称为早期强度发展阶段。
早期强度发展阶段的时间一般为3-7天。
2.中期强度当混凝土的早期强度发展到一定程度后,其强度的增长速度开始逐渐变缓,但是强度还在不断提高,这个过程称为中期强度发展阶段。
中期强度发展阶段的时间一般为7-28天。
3.后期强度当混凝土的中期强度发展到一定程度后,其强度的增长速度再次开始变缓,但是强度仍在不断提高,这个过程称为后期强度发展阶段。
后期强度发展阶段的时间一般为28天以上。
四、混凝土强度的影响因素1.材料因素混凝土中主要材料是水泥、骨料和水,它们的种类和质量对混凝土的强度有着重要的影响。
其中,水泥的种类、品牌和用量是影响混凝土强度的重要因素。
2.配合比因素混凝土配合比是指水泥、骨料、水的配合比例。
合理的配合比可以保证混凝土的强度和耐久性,而不合理的配合比则会导致混凝土的强度降低、开裂等问题。
3.养护因素混凝土在浇注后需要进行充分的养护,以保证其强度的发展。
养护条件包括温度、湿度、养护时间等,不同养护条件对混凝土强度的影响不同。
4.施工工艺因素混凝土的施工工艺包括浇注、振捣、加料等环节,这些环节的操作是否得当也会影响混凝土的强度。
例如,振捣不充分会导致混凝土内部空隙较大,从而影响其强度。
五、结论混凝土强度是建筑结构中最为基础的材料之一,其强度的发展规律及影响因素对建筑工程的稳定性和耐久性有着非常重要的影响。
混凝土强度发展过程及影响因素原理
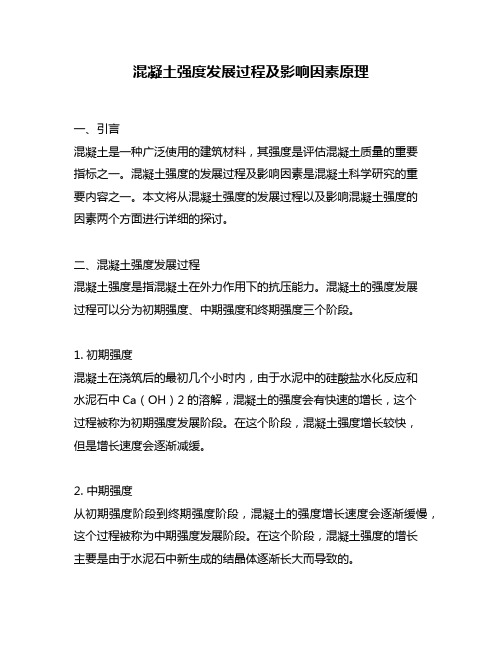
混凝土强度发展过程及影响因素原理一、引言混凝土是一种广泛使用的建筑材料,其强度是评估混凝土质量的重要指标之一。
混凝土强度的发展过程及影响因素是混凝土科学研究的重要内容之一。
本文将从混凝土强度的发展过程以及影响混凝土强度的因素两个方面进行详细的探讨。
二、混凝土强度发展过程混凝土强度是指混凝土在外力作用下的抗压能力。
混凝土的强度发展过程可以分为初期强度、中期强度和终期强度三个阶段。
1. 初期强度混凝土在浇筑后的最初几个小时内,由于水泥中的硅酸盐水化反应和水泥石中Ca(OH)2的溶解,混凝土的强度会有快速的增长,这个过程被称为初期强度发展阶段。
在这个阶段,混凝土强度增长较快,但是增长速度会逐渐减缓。
2. 中期强度从初期强度阶段到终期强度阶段,混凝土的强度增长速度会逐渐缓慢,这个过程被称为中期强度发展阶段。
在这个阶段,混凝土强度的增长主要是由于水泥石中新生成的结晶体逐渐长大而导致的。
3. 终期强度终期强度是指混凝土在长时间内(一般是28天)内的最终强度。
在这个阶段,混凝土强度的增长速度会逐渐趋于稳定,但是由于水泥石中结晶体的继续生长和水泥石微观结构的变化,混凝土的强度仍然会有一定的增长。
三、影响混凝土强度的因素混凝土强度的大小受到多种因素的影响。
下面将从材料、配合比、养护等方面进行详细的介绍。
1. 材料因素(1)水泥的品种和用量:水泥是混凝土中最主要的胶凝材料,不同品种和用量的水泥对混凝土强度的影响不同。
一般来说,硅酸盐水泥的强度高于普通硅酸盐水泥,而用量适当的水泥能够提高混凝土的强度。
(2)骨料的品种和粒径:骨料是混凝土中的主要骨架材料,不同品种和粒径的骨料对混凝土强度的影响也不同。
一般来说,粗骨料的强度高于细骨料,而用量适当的骨料能够提高混凝土的强度。
2. 配合比因素混凝土中水泥、骨料、水和掺合料的比例被称为配合比。
不同的配合比对混凝土强度的影响很大。
一般来说,水泥用量过少会导致混凝土强度不足,而水泥用量过多会导致混凝土收缩过大和开裂。
混凝土的龄期与强度发展关系
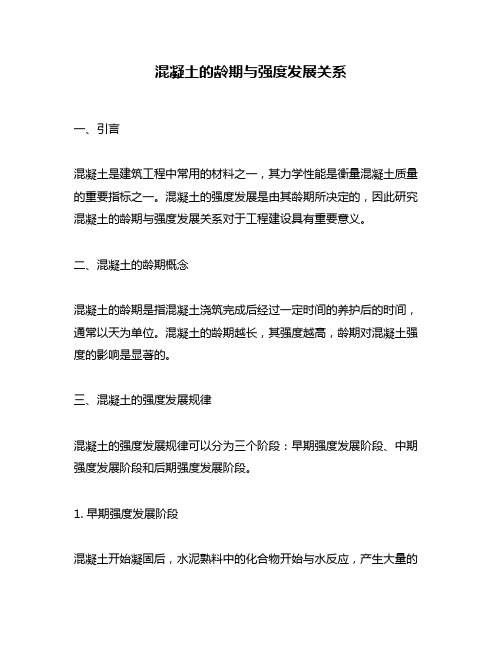
混凝土的龄期与强度发展关系一、引言混凝土是建筑工程中常用的材料之一,其力学性能是衡量混凝土质量的重要指标之一。
混凝土的强度发展是由其龄期所决定的,因此研究混凝土的龄期与强度发展关系对于工程建设具有重要意义。
二、混凝土的龄期概念混凝土的龄期是指混凝土浇筑完成后经过一定时间的养护后的时间,通常以天为单位。
混凝土的龄期越长,其强度越高,龄期对混凝土强度的影响是显著的。
三、混凝土的强度发展规律混凝土的强度发展规律可以分为三个阶段:早期强度发展阶段、中期强度发展阶段和后期强度发展阶段。
1. 早期强度发展阶段混凝土开始凝固后,水泥熟料中的化合物开始与水反应,产生大量的热量,使混凝土内部温度升高,从而促进了水泥熟料中的化合物的反应速率,因此混凝土的强度在早期发展较快。
一般认为,混凝土浇筑后1~3天为早期强度发展阶段。
2. 中期强度发展阶段随着时间的推移,混凝土内部水分逐渐减少,水泥熟料中的化合物的反应速率逐渐降低,混凝土的强度增长速度逐渐减缓。
一般认为,混凝土浇筑后3~28天为中期强度发展阶段。
3. 后期强度发展阶段混凝土在中期强度发展阶段后进入后期强度发展阶段,此时混凝土强度增长速度缓慢,但强度增长的持续时间较长,一般认为,混凝土浇筑后28天后为后期强度发展阶段。
四、龄期对混凝土强度的影响混凝土的龄期对混凝土强度的影响是显著的,不同龄期的混凝土强度差异较大。
1. 早期强度混凝土的早期强度受到龄期的影响较大,随着龄期的增长,早期强度逐渐增加,但增长速度逐渐减缓。
一般认为,混凝土浇筑后1天到7天为早期强度,此时混凝土强度增长速度较快,约占混凝土强度的60%。
2. 中期强度混凝土的中期强度受到龄期的影响较小,龄期对混凝土中期强度的影响主要是在早期强度发展阶段对中期强度的影响。
一般认为,混凝土浇筑后7天到28天为中期强度,此时混凝土强度增长速度逐渐减缓,约占混凝土强度的30%。
3. 后期强度混凝土的后期强度受到龄期的影响较小,龄期对混凝土后期强度的影响主要是在早期强度和中期强度发展阶段对后期强度的影响。
影响混凝土强度的主要因素

影响混凝土强度的主要因素混凝土是现代建筑中广泛使用的重要材料之一,其强度直接关系到建筑物的质量和安全性。
了解影响混凝土强度的主要因素对于确保建筑工程的质量至关重要。
以下我们将详细探讨这些因素。
首先,水泥的强度和品种是影响混凝土强度的关键因素之一。
水泥作为混凝土中的胶凝材料,其强度等级越高,制成的混凝土强度往往也越高。
不同品种的水泥,其化学成分和矿物组成有所差异,这会导致其与水反应的速度和产物不同,从而影响混凝土的强度发展。
例如,硅酸盐水泥的早期强度相对较高,而矿渣水泥的后期强度增长潜力较大。
水灰比也是一个极其重要的因素。
水灰比是指混凝土中水的用量与水泥用量的比值。
水灰比越大,意味着混凝土中的水分越多,在混凝土硬化过程中,多余的水分蒸发后会留下较多的孔隙,从而降低混凝土的密实度和强度。
相反,较小的水灰比能使混凝土更加密实,强度也就更高。
但水灰比过小,会导致混凝土的和易性变差,施工难度增大。
骨料的性质对混凝土强度有着不可忽视的影响。
骨料的强度、级配、表面特征和最大粒径等都会作用于混凝土的强度。
高强度、良好级配且表面粗糙的骨料能够与水泥浆更好地结合,提高混凝土的强度。
同时,骨料的最大粒径也需要合理控制,过大或过小的粒径都可能对混凝土强度产生不利影响。
养护条件对于混凝土强度的形成和发展至关重要。
混凝土在浇筑后需要在适宜的温度和湿度环境下进行养护。
适宜的温度可以促进水泥的水化反应,加快强度的增长。
而足够的湿度能够防止混凝土表面过快干燥,避免出现收缩裂缝,保证混凝土内部的水化反应充分进行。
如果养护不当,例如养护温度过低、湿度不足或者养护时间过短,都会导致混凝土强度达不到设计要求。
施工质量同样会影响混凝土的强度。
在搅拌、浇筑和振捣过程中,如果操作不规范,可能导致混凝土不均匀、存在气泡或离析等问题,从而影响混凝土的强度。
例如,搅拌不均匀会使水泥不能充分与骨料结合;浇筑时如果分层过厚或振捣不密实,都会使混凝土内部存在缺陷,降低强度。
混凝土后期强度倒缩问题

混凝土后期强度倒缩问题尽管引起混凝土强度倒缩的原因可能很多,也不排除广泛使用矿物掺合料和外加剂(包括减水剂)等原因,但作为现代混凝土最主要的胶凝材料——水泥的确出了问题。
其一,早期强度越来越高,但28天强度的富余系数却越来越小,后期强度增长缓慢,60天至90天时水泥胶砂强度基本上没有增长甚至有所下降,用这样的水泥拌制的混凝土,仅7天的抗压强度就能达到28天强度的90%以上,但28天以后,强度增长很小,60天以后,除了处于水中或地下等湿润环境中的混凝土构件外,抗压强度基本没有继续增长。
其二,水泥粉磨颗粒越来越细,水化速度越来越快,水化热放热集中,混凝土浇筑后,内外温差加大,温度应力导致混凝土结构内部细微裂缝增加,加之工期进度要求紧,混凝土浇筑后难以按规范进行保湿保温养护,故很难保证混凝土结构的长期性和耐久性。
其三,水泥生产厂家为了获取经济利益,乱掺加混合材,其品种和掺量对外保密,若商品混凝土企业一定要求厂家提供,其所供资料也不一定可信。
除了混合材,助磨剂也同样影响到水泥与减水剂的适应性,对混凝土的后期强度都会带来不同程度的影响。
水泥为何能够高早强?除了高细度、水化快,就是水泥本身的矿物成分改变了,水泥中C3S和C3A矿物成分提高了,而C2S降低了,所以早期强度高,后期强度上不来,有冲劲无后劲,导致混凝土丧失了自愈合能力。
前几年,施工方把混凝土裂缝的责任归罪于“商品混凝土”,后来发现自拌的混凝土不养护也照样裂缝,其实裂缝的根源也是水泥和早些年使用的不一样了,还按照老经验施工不灵了,当今的水泥普遍患有“三高”症,即“高早强、高细度、高碱含量”。
形成水泥产品现状的责任究竟在谁?好像还不应全归罪于水泥生产厂,因为当今的水泥强度和细度,并没有违反国家现行的GB175—2007/XG2—2015《通用硅酸盐水泥》标准。
该标准于2007年发布后,又在2009年和2015年先后进行过两次修改,但对于水泥的强度和细度的规定,都是一如既往并没有改变。
混凝土的龄期与强度发展原理

混凝土的龄期与强度发展原理混凝土是一种广泛应用于建筑、道路、桥梁等各个领域的重要建筑材料,其强度发展与龄期密切相关。
本文将从混凝土的龄期、强度发展等方面,全面介绍混凝土的龄期与强度发展原理。
一、混凝土的龄期1.1 定义混凝土的龄期是指混凝土从拌和开始到某一时刻所经历的时间,通常以拌合浆的时间为起点。
混凝土的龄期可以分为初期、中期和后期三个阶段。
1.2 初期初期龄期通常是指混凝土从拌合到28天内的时间段,此时混凝土强度的发展速度较快,强度增长大约占混凝土总体强度增长的70%左右。
初期龄期的主要特点是混凝土的水泥胶体逐渐形成,水泥胶体的硬化过程主要是由于水泥中的C3S和C2S与水反应生成C-S-H胶体和Ca(OH)2。
在这个过程中,Ca(OH)2逐渐溶于水中,同时与空气中的CO2反应生成CaCO3,从而使得混凝土表面出现白色的氢氧化钙层。
1.3 中期中期龄期通常是指混凝土从28天到90天之间的时间段,此时混凝土的强度增长速度开始变缓,强度增长大约占混凝土总体强度增长的25%左右。
中期龄期的主要特点是水泥胶体中的C-S-H胶体逐渐形成,C-S-H胶体的形成是由于水泥胶体中的C3S和C2S与水反应生成的,在这个过程中,C3S和C2S中的氢氧化物逐渐与水中的离子交换,从而形成C-S-H胶体。
1.4 后期后期龄期通常是指混凝土从90天到1年之间的时间段,此时混凝土的强度增长速度变得非常缓慢,强度增长大约占混凝土总体强度增长的5%左右。
后期龄期的主要特点是水泥胶体中的C-S-H胶体逐渐变得致密,同时混凝土中一些不稳定的化合物逐渐分解为稳定的化合物,从而使得混凝土强度趋于稳定。
二、混凝土强度的发展2.1 定义混凝土强度是指混凝土在受外力作用下所能承受的最大应力。
混凝土强度的发展过程是指混凝土在不同阶段内所表现出来的强度特性。
2.2 影响混凝土强度的因素影响混凝土强度的因素有很多,主要包括下面几个方面:(1)水胶比:水胶比是指混凝土中水的用量与水泥用量的比值,水胶比过高会导致混凝土中的水泥胶体形成不充分,从而影响混凝土的强度。
当前混凝土存在的问题

当前混凝土存在的问题在飞速发展的今天,中国快速成为全球最大的基建市场,而所有的建设材料中,用量最大,使用最广泛的应首推混凝土。
现在,混凝土更加越来越多地应用研于现代工程建设之中,各项大小工程项目的建设都离不开混凝土材料。
同时,混凝土也同其他很多项目的发展一样,面临着可持续发展的问题,如生态问题、环保问题、节能问题等等。
混凝土作为基建工程中不可缺少的材料,既要保持科学发展的态势,又要适应人类的环保、生态、绿色发展需要。
一、混凝土原材料问题现状1、水泥性能发生了巨大的变化经过近三十年的快速发展,水泥性能发生了巨大的变化。
(1)水泥的早期强度越来越高,后期强度增长缓慢,60d 至 90d 时水泥胶砂强度基本上没有增长甚至有所下降。
(2)水泥越来越细,水化速度越来越快,水化放热集中,使混凝土内外温差加大,导致混凝土结构内部细微裂缝增加,增加了混凝土开裂的机会。
(3)混合材掺量过高,使水泥的性能与传统的硅酸盐系列水泥性能大相径庭。
(4)助磨剂的大量使用使水泥与外加剂的适应性变差。
因此研究水泥性能,合理利用水泥特性,配制满足工程设计要求的混凝土非常必要。
2、粉煤灰真假难辨粉煤灰作为混凝土中不可缺少的重要材料之一,同时也严重影响混凝土的性能,市场上不同品质的粉煤灰,真假难辨,个别严重的按现行标准,难以判断粉煤灰的纯度,甚至无法区分真假粉煤灰,常见的包括“脱硫灰”、“脱硝灰”、“浮黑灰”等粉煤灰以次充好,通过正常检测无法区别真假,在实际使用过程中严重影响混凝土的质量。
而使用这些粉煤灰会严重影响混凝土的性能,造成混凝土需水量高,和易性差,坍落度损失快,混凝土开裂等一系列问题。
3、砂子的质量需要同步控制当前影响混凝土质量的一个因素是砂子质量的波动,主要表现在紧密堆积密度的变化、含石率的变化、吸水率的变化以及级配的变化。
砂子紧密堆积密度变化的主要原因是矿山资源的多元化,母岩密度的变化以及机制砂中石粉含量的波动。
砂子含石率的变化主要原因是由于砂子生产、运输及堆垛过程中砂子离析引起的。
混凝土的龄期和强度发展规律
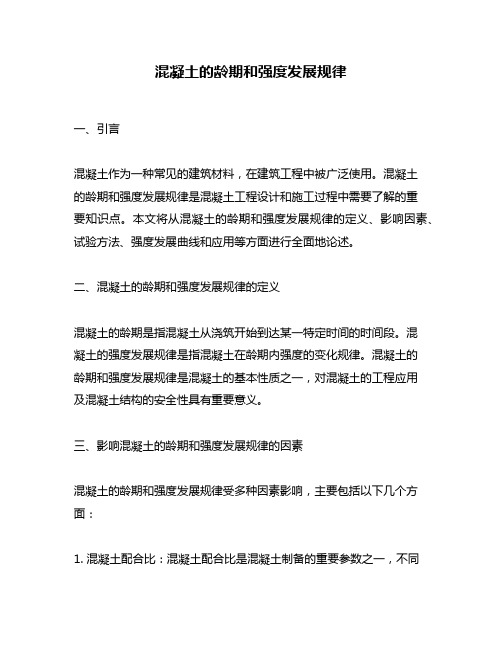
混凝土的龄期和强度发展规律一、引言混凝土作为一种常见的建筑材料,在建筑工程中被广泛使用。
混凝土的龄期和强度发展规律是混凝土工程设计和施工过程中需要了解的重要知识点。
本文将从混凝土的龄期和强度发展规律的定义、影响因素、试验方法、强度发展曲线和应用等方面进行全面地论述。
二、混凝土的龄期和强度发展规律的定义混凝土的龄期是指混凝土从浇筑开始到达某一特定时间的时间段。
混凝土的强度发展规律是指混凝土在龄期内强度的变化规律。
混凝土的龄期和强度发展规律是混凝土的基本性质之一,对混凝土的工程应用及混凝土结构的安全性具有重要意义。
三、影响混凝土的龄期和强度发展规律的因素混凝土的龄期和强度发展规律受多种因素影响,主要包括以下几个方面:1. 混凝土配合比:混凝土配合比是混凝土制备的重要参数之一,不同的配合比会对混凝土的龄期和强度发展产生不同的影响。
2. 水胶比:水胶比是混凝土的重要参数之一,它直接影响混凝土的强度和耐久性。
水胶比越小,混凝土的强度越高,龄期越长。
3. 混凝土的成分:混凝土的成分主要包括水泥、砂、骨料等,不同的成分会对混凝土的龄期和强度发展产生不同的影响。
4. 外部环境条件:外部环境条件包括温度、湿度、气压等因素,对混凝土的龄期和强度发展也有一定的影响。
四、混凝土龄期和强度发展规律的试验方法混凝土龄期和强度发展规律的试验方法主要包括以下几种:1. 压缩强度试验:压缩强度试验是测定混凝土强度的常用方法,试验中采用标准试块进行压缩试验,通过试验数据绘制强度发展曲线。
2. 抗拉强度试验:抗拉强度试验是测定混凝土强度的另一种方法,试验中采用标准试件进行拉伸试验,通过试验数据绘制强度发展曲线。
3. 超声波检测法:超声波检测法是一种非破坏性试验方法,可以测定混凝土的龄期和强度发展规律。
通过测量混凝土中超声波的传播速度和衰减程度,推算出混凝土的龄期和强度发展规律。
五、混凝土强度发展曲线混凝土强度发展曲线是衡量混凝土龄期和强度发展规律的重要指标,通常将其分为三个阶段:1. 初期强度发展阶段:从混凝土浇筑开始到28天为止,混凝土的强度发展较快,但增长幅度较小。
混凝土的龄期和强度发展规律原理

混凝土的龄期和强度发展规律原理一、引言混凝土是一种常见的建筑材料,其性能的优劣直接关系到建筑物的质量和安全。
混凝土的强度是一个重要的性能指标,它的发展规律与龄期密切相关。
本文将从混凝土的龄期和强度发展规律两个方面进行详细的阐述。
二、混凝土的龄期1.龄期的概念混凝土的龄期是指混凝土从浇筑开始到某个时刻的时间长度。
一般来说,混凝土的龄期可以分为初期、中期和后期三个阶段,分别对应着混凝土的塑性、凝结和硬化阶段。
2.初期龄期初期龄期是指混凝土从开始浇筑到初凝阶段的时间,一般为1~2小时。
在这个阶段,混凝土处于塑性状态,具有较好的可塑性和流动性,可以通过振动来完全填充模板中的空隙。
3.中期龄期中期龄期是指混凝土从初凝到硬化阶段的时间,一般为1~3天。
在这个阶段,混凝土开始逐渐失去可塑性,但仍然具有一定的流动性,可以通过振动来排除气泡和提高密实性。
4.后期龄期后期龄期是指混凝土从硬化到强度达到设计强度的时间,一般为28天。
在这个阶段,混凝土已经完全失去了可塑性,具有较高的强度和稳定性,可以承受一定的荷载。
三、混凝土的强度发展规律1.强度的概念混凝土的强度是指混凝土抗压承载能力的大小。
混凝土的强度与其成分、配合比、龄期等因素有关。
2.强度的发展规律混凝土的强度发展规律可以分为三个阶段:初期强度发展快、中期强度发展缓慢、后期强度发展逐渐趋于平缓。
初期强度发展快是由于混凝土处于塑性状态,内部孔隙水分含量较高,水泥石的水化反应较为活跃,导致混凝土的强度迅速提高。
中期强度发展缓慢是由于混凝土已经逐渐失去塑性,但水泥石的水化反应仍在继续,此时混凝土的强度增长速度变缓。
后期强度发展逐渐趋于平缓是由于水泥石的水化反应已经基本结束,混凝土的强度增长速度变得极其缓慢,但仍然会有一定的增长。
3.影响强度的因素混凝土的强度受多种因素的影响,主要包括以下几个方面:(1) 水泥品种和用量:不同品种和用量的水泥对混凝土的强度有显著影响。
混凝土早期强度发展规律及原理

混凝土早期强度发展规律及原理一、引言混凝土是一种常用的建筑材料,其强度发展规律对于建筑结构的安全和使用寿命有着至关重要的影响。
本文将探讨混凝土早期强度发展规律及其原理。
二、混凝土早期强度发展规律混凝土早期强度发展规律是指混凝土在浇筑后的一段时间内,随着时间的推移,其强度的增长情况。
通常认为,混凝土的早期强度发展可以分为三个阶段:初期、中期、后期。
1. 初期初期是混凝土浇筑后1~3天内的时间段,也称为凝胶期。
在这个阶段,混凝土的强度增长缓慢,但随着时间的推移,强度的增长速度将逐渐加快。
初期强度的增长主要是由于硬化反应的进行,其主要包括水泥水化反应和水化热反应。
水泥水化反应是指水泥与水反应生成硬化产物的过程,这个过程是一个放热反应,同时产生的水化产物也会填充混凝土中的微观孔隙,从而提高混凝土的密实度和强度。
水泥的水化反应主要是由于水泥中的硅酸盐和铝酸盐矿物质与水反应生成硬化产物所引起的。
水化热反应是指由于水泥水化反应的进行而产生的热量,这个热量会使混凝土中的水分蒸发,从而加速混凝土的硬化。
2. 中期中期是混凝土浇筑后3~7天内的时间段,也称为胶凝期。
在这个阶段,混凝土的强度增长速度逐渐加快,这是由于硬化反应的加速和水分的逐渐蒸发所引起的。
同时,混凝土中的孔隙逐渐减少,密实度逐渐提高,这也是强度增长的原因之一。
在中期,混凝土的强度增长主要是由于凝胶硬化产物的形成和孔隙结构的变化所引起的。
3. 后期后期是混凝土浇筑后7天以上的时间段,也称为硬化期。
在这个阶段,混凝土的强度增长速度逐渐变慢,但仍然会持续增长。
强度增长的原因主要是由于凝胶硬化产物的形成和孔隙结构的变化所引起的。
三、混凝土早期强度发展原理混凝土早期强度发展的原理主要涉及到几个方面,包括水泥水化反应、水化热反应、孔隙结构的变化等。
1. 水泥水化反应水泥水化反应是混凝土早期强度发展的主要原因之一。
水泥中的硅酸盐和铝酸盐矿物质与水反应生成硬化产物,这个过程是一个放热反应。
混凝土的龄期与强度发展的关系原理

混凝土的龄期与强度发展的关系原理一、引言混凝土是一种广泛使用的建筑材料,其性能的关键之一是强度。
混凝土的龄期和强度发展是混凝土强度评估的重要因素。
本文将介绍混凝土的龄期和强度发展的关系、混凝土强度的发展过程、影响混凝土强度的因素以及如何利用混凝土的龄期和强度发展来评估混凝土的强度。
二、混凝土的龄期和强度发展的关系混凝土的龄期是指混凝土浇筑后经过一定时间的养护和硬化后的时间。
龄期对混凝土的强度发展有重要影响。
混凝土的强度发展过程可以分为三个阶段:早期强度、中期强度和后期强度。
混凝土的龄期和强度发展的关系如下:1. 早期强度早期强度是指混凝土浇筑后的前三天内所达到的强度。
早期强度的发展与混凝土在浇筑后的养护和硬化过程密切相关。
在早期,混凝土的强度主要受到水泥胶凝体的早期强度发展影响。
在这个阶段,水泥胶凝体的体积稳定性和矿物反应会导致混凝土的早期强度发展。
此外,混凝土的环境条件也会影响早期强度的发展,如温度和湿度等。
2. 中期强度中期强度是指混凝土浇筑后3天到28天之间所达到的强度。
在这个阶段,混凝土的强度主要受到水泥胶凝体和石英砂的强度发展影响。
水泥胶凝体的早期强度发展和石英砂的颗粒间的相互作用会导致混凝土的中期强度发展。
此外,混凝土的环境条件也会影响中期强度的发展,如温度和湿度等。
3. 后期强度后期强度是指混凝土浇筑后28天以上所达到的强度。
在这个阶段,混凝土的强度主要受到水泥胶凝体和石英砂的强度发展影响。
水泥胶凝体和石英砂的颗粒间的相互作用以及水泥石和石英砂的反应会导致混凝土的后期强度发展。
此外,混凝土的环境条件也会影响后期强度的发展,如温度和湿度等。
三、混凝土强度的发展过程混凝土的强度发展过程是一个复杂的过程,涉及到多种因素的相互作用。
混凝土的强度发展过程可以分为以下几个阶段:1. 水泥胶凝体的形成阶段水泥胶凝体的形成是混凝土强度发展的第一个阶段。
在这个阶段,水泥和水反应生成水泥胶凝体。
水泥胶凝体的形成是混凝土早期强度发展的主要因素。
混凝土龄期对强度的影响原理
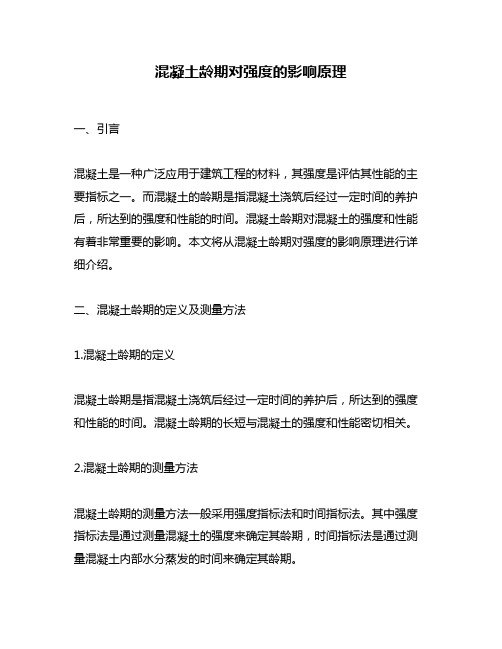
混凝土龄期对强度的影响原理一、引言混凝土是一种广泛应用于建筑工程的材料,其强度是评估其性能的主要指标之一。
而混凝土的龄期是指混凝土浇筑后经过一定时间的养护后,所达到的强度和性能的时间。
混凝土龄期对混凝土的强度和性能有着非常重要的影响。
本文将从混凝土龄期对强度的影响原理进行详细介绍。
二、混凝土龄期的定义及测量方法1.混凝土龄期的定义混凝土龄期是指混凝土浇筑后经过一定时间的养护后,所达到的强度和性能的时间。
混凝土龄期的长短与混凝土的强度和性能密切相关。
2.混凝土龄期的测量方法混凝土龄期的测量方法一般采用强度指标法和时间指标法。
其中强度指标法是通过测量混凝土的强度来确定其龄期,时间指标法是通过测量混凝土内部水分蒸发的时间来确定其龄期。
三、混凝土强度的形成机理混凝土强度的形成机理是混凝土中的水泥水化反应,水泥水化反应是指水泥与水反应,生成硬化后的水泥石。
水泥水化反应是一个复杂的过程,水泥石的强度取决于水泥石中的化合物种类、比例、孔隙度、结晶状态等多种因素。
四、混凝土龄期对强度的影响原理1.混凝土龄期的早期强度混凝土浇筑后,经过初凝和终凝两个阶段,混凝土处于早期强度阶段。
初凝是指混凝土刚刚凝固时的状态,此时混凝土的强度极低,无法承受荷载。
而终凝是指混凝土中的水泥水化反应已经完成,混凝土达到了最终强度。
在早期强度阶段,混凝土的强度随着龄期的增加而逐渐提高,但提高幅度较小。
2.混凝土龄期的中期强度混凝土龄期达到28天后,混凝土处于中期强度阶段。
此时混凝土的强度已经提高到了一定的水平,但仍然存在一些孔隙和缺陷,混凝土的强度仍然存在一定的不稳定性。
龄期超过28天后,混凝土的强度提高幅度明显减缓,但仍然会随着龄期的增加而提高。
3.混凝土龄期的后期强度混凝土龄期达到90天后,混凝土处于后期强度阶段。
此时混凝土的强度已经达到稳定状态,混凝土中的孔隙和缺陷已经得到充分填补,混凝土的强度已经达到最终强度。
此时混凝土的强度不再随着龄期的增加而提高,反而会因为多年的风雨侵蚀和荷载作用而逐渐降低。
- 1、下载文档前请自行甄别文档内容的完整性,平台不提供额外的编辑、内容补充、找答案等附加服务。
- 2、"仅部分预览"的文档,不可在线预览部分如存在完整性等问题,可反馈申请退款(可完整预览的文档不适用该条件!)。
- 3、如文档侵犯您的权益,请联系客服反馈,我们会尽快为您处理(人工客服工作时间:9:00-18:30)。
对混凝土早期强度高,后期强度增长缓慢的几点看法混凝土强度是工程质量控制和工程验收的一项重要内容,也必然成为混凝土企业技术人员、施工单位等关注的重点。
在混凝土生产和工程实践中经常会遇到混凝土早期强度(7d强度)偏高,28d以后强度增长缓慢,即“前期畸形,后期不良”。
混凝土早期强度过快的增长,一方面影响后期强度的增长,另一方面早期强度过快增长往往伴随着较高的水化速率,水化热高,给混凝土裂缝控制带来困难,不利于混凝土的耐久性能。
1.造成混凝土早强的因素
造成混凝土早期强度偏高,是多种因素造成的:
(1)近年来,施工速度的加快,施工单位希望混凝土具有较高的早期强度,混凝土早期强度的快速增长可以满足快速施工的需要。
此外,混凝土早期强度快速增长,可以满足施工单位早期尽快拆模的需要,这样可以加快模板的周转,提高模板应用效率。
因此,施工单位希望混凝土早期强度高。
(2)混凝土强度是工程验收的重要指标,强度的检测相对其他技术指标要简单、快捷。
混凝土企业技术人员往往从心理上比较重视混凝土强度,有时会担心混凝土强度不足,不能满足工程验收要求。
混凝土技术人员对混凝土强度的过分重视,往往形成混凝土强度第一,强度唯一的思想。
在混凝土强度唯一的思想支配下,设计配合比时担心混凝土强度不够,使得混凝土早期强度偏高,7d达到设计的
90%,甚至超过100%,否则心里不踏实。
(3)水泥技术的发展为混凝土早期强度偏高起到了推波助澜的作用。
首先,水泥中的C3A、C3S含量增加,提高了早期水泥强度,后期强度增长缓慢。
其次,水泥粉磨工艺的发展,使得水泥熟料越磨越细,水泥中粒径在1μm以下的细颗粒加速了水泥的水化速率,提高早期强度,几乎对后期强度没有任何贡献,倒是对早期的水化热、混凝土的自收缩和干燥收缩有贡献。
再次,水泥生产企业在环保压力下,废气禁止外排造成窑内高温区气相的碱无法在窑外冷凝到粉尘表面排除到窑外,所有原燃材料带入窑内的碱几乎全部留在熟料中,水泥碱含量提高。
最后,水泥粉磨过程中,添加的某些助磨剂具有早强作用,加速水泥水化,提高早期强度,不利于后期强度的发展,如醇氨胺类助磨剂。
2.影响混凝土后期强度增长的因素
混凝土后期强度的持续增长受多种因素制约,其中既有原材料质量、配合比设计的因素,也包含后期施工养护的因素。
(1)水泥强度的增长趋势对混凝土强度增长具有直接影响,一般来说,水泥早期强度高后期发展缓慢,混凝土强度也会表现出类似的强度发展趋势。
(2)粉煤灰品种和掺量对混凝土后期强度的增长具有重要影响,一般来说粉煤灰品种和质量对混凝土强度增长的影响大于掺量的影响。
目前,市场上粉煤灰供不应求,问题粉煤灰层次不穷,如氨味粉
煤灰、脱硫灰、喷油灰、非玻璃体灰以及添加石灰石粉等物质的假粉煤灰,这些粉煤灰往往常规指标检测合格,但会对混凝土强度尤其是长期性能产生不利影响。
(3)骨料含泥量。
骨料含泥量直接影响混凝土中水泥浆体与骨料的粘接力,含泥量越高,混凝土强度降低越明显。
砂的含泥量在3%以内,对混凝土强度影响不明显;含泥量3%~5%时,通过合理的养护依然可以满足设计要求,但砂含泥量超过5%以后,混凝土各龄期强度均出现不同程度的降低,而且还造成混凝土后期强度增长缓慢。
即使在使用含泥量偏大的砂石骨料时适当增加水泥用量以获得满意的早期强度,但后期混凝土强度增长缓慢的缺点依然难以克服。
(4)混凝土后期养护是保障后期强度持续增长的重要因素。
混凝土的28d抗压强度与保湿养护时间有着密切的关系,混凝土早期保湿养护不足造成过早失水,造成部分水泥颗粒失去水化,不利于后期强度的持续增长。
实践发现,浇筑1d脱模的混凝土不再保湿养护,其28d回弹强度仅为标准养护试件抗压强度的80%,保湿养护仅2d 或3d的混凝土,其28d回弹强度仅为标准养护试件28d抗压强度的85%或90%,由此可见,保湿养护对后期强度的增长很重要。
3.针对混凝土早期强度高后期强度增长缓慢的一些建议
混凝土早期强度高后期强度增长缓慢不利于混凝土耐久性能的发挥,如裂缝控制难度增加。
在混凝土工程实践中要避免这种现象的出现,使混凝土强度良性发展,要加强原材料进场质量控制、配合比设计以及后期的施工养护等环节。
具体做法有一下几点:
(1)注意水泥选用。
选择水泥时,应尽量选择早期强度适中(如3d强度26MPa~28MPa),28d强度高的水泥,选择3d到28d强度增长较大的水泥。
(2)加强粉煤灰等矿物掺合料的质量控制。
加强矿物掺合料活性指数检测,选择活性发展良好的矿物掺合料,避免使用早期活性合格,后期活性偏低的掺合料,保障混凝土强度良性发展。
(3)控制骨料含泥量。
依据本公司生产、试验实践数据设立砂石骨料含泥量极限值,超过极限值应拒绝使用。
(4)混凝土配合比设计时,充分调整水泥与矿物掺合料添加比例,使设计的配合比早期强度满足施工要求,后期利于矿物掺合料二次水化作用持续增长。
不同品种、不同质量的矿物掺合料与水泥搭配的最佳比例不同,甚至不同水胶比下,矿物掺合料最佳比例也不相同。
因此,应以试验结果为依据,切忌盲目使用矿物掺合料。
(5)督促施工单位加强保温、保湿养护,严格执行养护制度,保障混凝土强度持续增长。