焊接缺陷的问题
焊接的六大缺陷及其产生原因、危害、预防措施

焊接的六大缺陷及其产生原因、危害、预防措施一、外观缺陷外观缺陷(表面缺陷)是指不用借助于仪器,从工件表面可以发现的缺陷。
常见的外观缺陷有咬边、焊瘤、凹陷及焊接变形等,有时还有表面气孔和表面裂纹。
单面焊的根部未焊透等。
A、咬边是指沿着焊趾,在母材部份形成的凹陷或者沟槽,它是由于电弧将焊缝边缘的母材熔化后没有得到熔敷金属的充分补充所留下的缺口。
产生咬边的主要原因:是电弧热量太高,即电流太大,运条速度太小所造成的。
焊条与工件间角度不正确,摆动不合理,电弧过长,焊接次序不合理等都会造成咬边。
直流焊时电弧的磁偏吹也是产生咬边的一个原因。
某些焊接位置( 立、横、仰 )会加剧咬边。
咬边减小了母材的有效截面积,降低构造的承载能力,同时还会造成应力集中,发展为裂纹源。
咬边的预防:矫正操作姿式,选用合理的规范,采用良好的运条方式都会有利于消除咬边。
焊角焊缝时,用交流焊代替直流焊也能有效地防止咬边。
B、焊瘤焊缝中的液态金属流到加热缺陷未熔化的母材上或者从焊缝根部溢出,冷却后形成的未与母材熔合的金属瘤即为焊瘤。
焊接规范过强、焊条熔化过快、焊条质量欠佳(如偏芯),焊接电源特性不稳定及操作姿式不当等都容易带来焊瘤。
在横、立、仰位置更易形成焊瘤。
焊瘤常伴有未熔合、夹渣缺陷,易导致裂纹。
同时,焊瘤改变了焊缝的实际尺寸,会带来应力集中。
管子内部的焊瘤减小了它的内径,可能造成流动物阻塞。
防止焊瘤的措施:使焊缝处于平焊位置,正确选用规范,选用无偏芯焊条,合理操作。
C、凹坑凹坑指焊缝表面或者反面局部的低于母材的部份。
凹坑多是由于收弧时焊条(焊丝)未作短期停留造成的(此时的凹坑称为弧坑),仰立、横焊时,常在焊缝反面根部产生内凹。
凹坑减小了焊缝的有效截面积,弧坑常带有弧坑裂纹和弧坑缩孔。
防止凹坑的措施:选用有电流衰减系统的焊机,尽量选用平焊位置,选用合适的焊接规范,收弧时让焊条在熔池内短期停留或者环形摆动,填满弧坑。
D、未焊满未焊满是指焊缝表面上连续的或者断续的沟槽。
常见焊接缺陷产生原因及防止措施
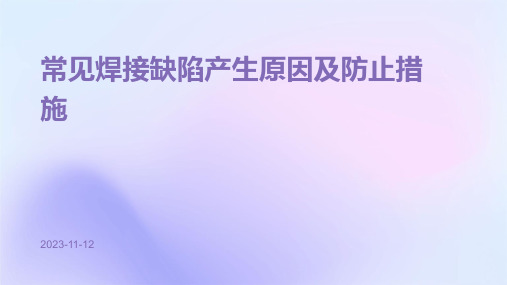
实例三:夹渣问题分析
01
夹渣总结:夹渣是由于焊接过程中熔渣清理不干净所导致的一种缺陷。
02
夹渣夹渣是指在焊缝中存在的非金属夹杂物,如氧化物、硫化物等。这些夹杂 物主要是由于焊接过程中熔渣清理不干净所导致。
03
防止措施:为了防止夹渣的产生,可以采取提高焊接速度、选择合适的焊接电 流和电压、使用合适的焊条和保护气体等措施。此外,还可以通过改善焊接工 艺、增加焊缝的过渡圆角等手段来减少夹渣的产生。
实例五:未熔合问题分析
未熔合总结:未熔合是由于焊接过程 中电流不足、速度过快等原因导致的 一种缺陷。
未熔合未熔合是指在焊接过程中,焊 缝没有完全熔合或者没有完全融合。 这可能会导致焊缝强度不足,容易引 发泄漏等问题。
防止措施:为了防止未熔合的产生, 可以采取增加电流、减慢焊接速度、 更换合适的焊条和保护气体等措施。 此外,还可以通过改善焊接工艺、增 加焊缝的过渡圆角等手段来减少未熔 合的产生。
坡口尺寸不合适容易导致未焊透。
减小间隙
间隙过大容易导致未焊透,应尽量减小间隙。
3
提高焊接速度
焊接速度过慢容易导致未焊透,应尽量提高焊接 速度。
未熔合防止措施
提高焊接温度
01
焊接温度过低容易导致未熔合,应尽量提高焊接温度。
选用合适的焊接电流和速度
02
焊接电流和速度不合适容易导致未熔合。
减小间隙
03
间隙过大容易导致未熔合,应尽量减小间隙。
04
焊接缺陷实例分析
实例一:气孔问题分析
气孔总结:气孔是焊接过程中常见的缺陷之一,主要由于焊接保护不足、操作不当 等原因导致。
气孔气孔是指在焊接过程中,熔融的金属中产生的空穴或气泡。当熔池中的气体在 金属冷却并凝固前未能完全逸出时,就会形成气孔。
常见的焊接缺陷及其处理方法
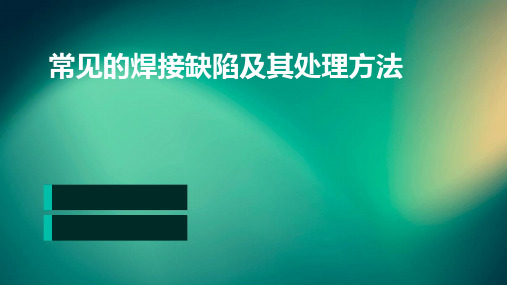
焊接缺陷的影响
强度下降
焊接缺陷会导致焊接接头强度下降,影响设备的 安全性能和使用寿命。
泄漏
对于要求气密或液密的设备,焊接缺陷可能导致 泄漏,影响设备的正常运行。
应力集中
焊接缺陷的存在可能引起应力集中,增加设备在 运行过程中发生疲劳断裂的风险。
02 常见的焊接缺陷
焊缝尺寸不符合要求
总结词
焊缝尺寸不符合要求是指焊接完成后,焊缝的宽度、高度或长度等参数不满足 设计要求。
提高焊接操作技能
总结词
提高焊接操作技能是预防焊接缺陷的重要措施之一。
详细描述
焊接操作人员的技能水平直接影响焊接质量。因此,应定期对操作人员进行技能培训和考核,提高其焊接操作技 能。此外,操作人员应严格遵守焊接工艺规程,按照规定的参数进行焊接,避免因操作不当导致的焊接缺陷。
加强焊接过程的监控与检验
05
04
详细描述
使用清洗剂清理焊缝表面,去除杂质 和氧化物,以提高表面光滑度。
06
详细描述
根据焊缝表面不光滑的情况,调整焊接电流、 电压、焊接速度等参数,以获得更光滑的焊缝 表面。
焊缝内部存在气孔的处理方法
总结词
选用合适的焊接材料
详细描述
选用低氢型焊条、烘干焊条等合适的 焊接材料,减少气孔的产生。
03 焊接缺陷的处理方法
焊缝尺寸不符合要求的处理方法
在此添加您的文本17字
总结词:调整焊接参数
在此添加您的文本16字
详细描述:对焊缝进行修整,包括打磨、补焊等,以使焊 缝尺寸符合要求。
在此添加您的文本16字
详细描述:根据焊缝尺寸不符合要求的情况,调整焊接电 流、电压、焊接速度等参数,以获得符合要求的焊缝尺寸 。
焊接常见缺陷产生的原因及其预防措施
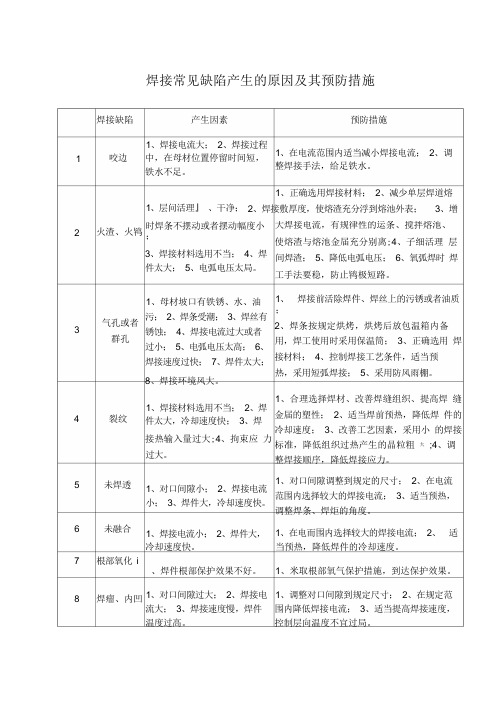
焊接常见缺陷产生的原因及其预防措施1 2 3 45 6 7 8 焊接缺陷咬边火渣、火鸨气孔或者群孔裂纹未焊透未融合根部氧化i焊瘤、内凹产生因素1、焊接电流大;2、焊接过程中,在母材位置停留时间短,铁水不足。
预防措施1、在电流范围内适当减小焊接电流;2、调整焊接手法,给足铁水。
1、正确选用焊接材料;2、减少单层焊道熔1、层问活理』、干净;2、焊接敷厚度,使熔渣充分浮到熔池外表;3、增时焊条不摆动或者摆动幅度小;3、焊接材料选用不当;4、焊件太大;5、电弧电压太局。
1、母材坡口有铁锈、水、油污;2、焊条受潮;3、焊丝有锈蚀;4、焊接电流过大或者过小;5、电弧电压太高;6、焊接速度过快;7、焊件太大;8、焊接环境风大。
1、焊接材料选用不当;2、焊件太大,冷却速度快;3、焊接热输入量过大;4、拘束应力过大。
1、对口间隙小;2、焊接电流小;3、焊件大,冷却速度快。
1、焊接电流小;2、焊件大,冷却速度快。
、焊件根部保护效果不好。
1、对口间隙过大;2、焊接电流大;3、焊接速度慢,焊件温度过高。
大焊接电流,有规律性的运条、搅拌熔池、使熔渣与熔池金届充分别离;4、子细活理层间焊渣;5、降低电弧电压;6、氧弧焊时焊工手法要稳,防止鸨极短路。
1、焊接前活除焊件、焊丝上的污锈或者油质;2、焊条按规定烘烤,烘烤后放包温箱内备用,焊工使用时采用保温筒;3、正确选用焊接材料;4、控制焊接工艺条件,适当预热,采用短弧焊接;5、采用防风雨棚。
1、合理选择焊材、改善焊缝组织、提高焊缝金届的塑性;2、适当焊前预热,降低焊件的冷却速度;3、改善工艺因素,采用小的焊接标准,降低组织过热产生的晶粒粗大;4、调整焊接顺序,降低焊接应力。
1、对口间隙调整到规定的尺寸;2、在电流范围内选择较大的焊接电流;3、适当预热,调整焊条、焊炬的角度。
1、在电而围内选择较大的焊接电流;2、适当预热,降低焊件的冷却速度。
1、米取根部氧气保护措施,到达保护效果。
常见焊接缺陷产生原因及防止措施
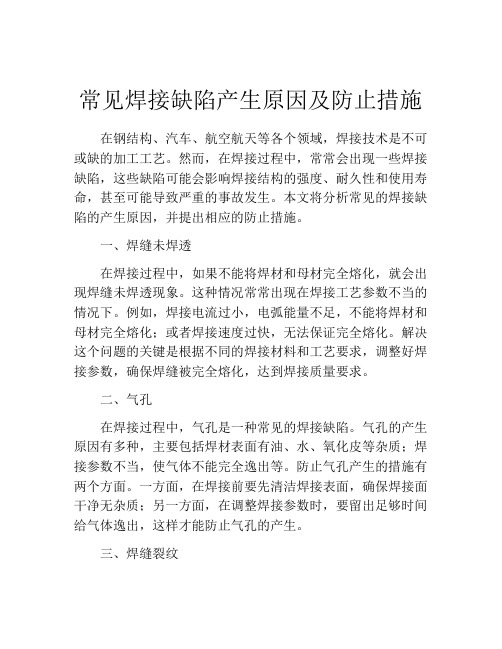
常见焊接缺陷产生原因及防止措施在钢结构、汽车、航空航天等各个领域,焊接技术是不可或缺的加工工艺。
然而,在焊接过程中,常常会出现一些焊接缺陷,这些缺陷可能会影响焊接结构的强度、耐久性和使用寿命,甚至可能导致严重的事故发生。
本文将分析常见的焊接缺陷的产生原因,并提出相应的防止措施。
一、焊缝未焊透在焊接过程中,如果不能将焊材和母材完全熔化,就会出现焊缝未焊透现象。
这种情况常常出现在焊接工艺参数不当的情况下。
例如,焊接电流过小,电弧能量不足,不能将焊材和母材完全熔化;或者焊接速度过快,无法保证完全熔化。
解决这个问题的关键是根据不同的焊接材料和工艺要求,调整好焊接参数,确保焊缝被完全熔化,达到焊接质量要求。
二、气孔在焊接过程中,气孔是一种常见的焊接缺陷。
气孔的产生原因有多种,主要包括焊材表面有油、水、氧化皮等杂质;焊接参数不当,使气体不能完全逸出等。
防止气孔产生的措施有两个方面。
一方面,在焊接前要先清洁焊接表面,确保焊接面干净无杂质;另一方面,在调整焊接参数时,要留出足够时间给气体逸出,这样才能防止气孔的产生。
三、焊缝裂纹焊缝裂纹是一种比较危险的焊接缺陷。
它常常由以下原因引起:焊接材料的拉伸强度不均,焊接接头部位过于脆弱,或者是焊接温度过高、冷却过快等。
为了防止焊缝裂纹的产生,可以采取以下措施。
一是控制焊接参数,避免过高的焊接温度和过快的冷却速度。
二是在焊接过程中,注意焊接的连续性,确保焊接成形完整。
三是在焊接过程中,采用预热的方法,改善焊接材料的拉伸强度,避免裂纹的出现。
四、过度熔深焊接过度熔深是由于焊接材料熔化过度,穿过母材嵌入焊接面内,使得焊缝结构松散,焊接强度降低。
过度熔深的原因有多种,如焊接电流过大,焊接速度过慢等。
预防过度熔深可以通过调整焊接参数、控制熔化深度和焊接速度等措施实现。
总之,焊接缺陷的产生原因可能有很多,需要针对具体情况采取相应的防止措施。
这需要焊接工艺人员有丰富的焊接经验和专业知识,对焊接材料和工艺有深入的了解,才能确保焊接质量达到要求。
焊接质量缺陷原因分析及预防、治理措施
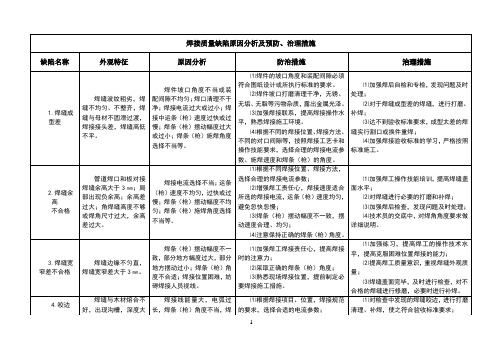
⑷根据自己的操作技能,选择合适的线能量、焊接速度和操作手法。
厚度符合标准要求;
⑵加强打底练习,熟练掌握操作手法以及对应的焊接线能量及焊接速度等。
18.管道焊口根部焊瘤、凸出、凹陷
⑷注意周围焊接施工环境,搭设防风设施,管子焊接无穿堂风;
⑸氩弧焊时,氩气纯度不低于%,氩气流量合适;
⑹尽量采用短弧焊接,减少气体进入熔池的机会;
⑺焊工操作手法合理,焊条、焊枪角度合适;
⑻焊接线能量合适,焊接速度不能过快;
⑼按照工艺要求进行焊件预热。
⑴严格按照预防措施执行;
⑵加强焊工练习,提高操作水平和责任心;
⑴严格按照规程和作业指导书的要求准备各种焊接条件;
⑵提高焊接操作技能,熟练掌握使用的焊接方法;
⑶采取合理的焊接顺序等措施,减少焊接应力等。
⑴针对每种产生裂纹的具体原因采取相应的对策;
⑵对已经产生裂纹的焊接接头,采取挖补措施处理。
11.焊缝表面不清理或清理不干净,电弧擦伤焊件
焊缝焊接完毕,焊接接头表面药皮、飞溅物不清理或清理不干净,留有药皮或飞溅物;焊接施工过程中不注意,电弧擦伤管壁等焊件造成弧疤。
⑶发现问题及时采取必要措施。
14.气孔
在焊缝中出现的单个、条状或群体气孔,是焊缝内部最常见的缺陷。
根本原因是焊接过程中,焊接本身产生的气体或外部气体进入熔池,在熔池凝固前没有来得及溢出熔池而残留在焊缝中。
⑴焊条要求进行烘培,装在保温筒内,随用随取;
⑵焊丝清理干净,无油污等杂质;
⑶焊件周围10~15㎜范围内清理干净,直至发出金属光泽;
⑴焊件的坡口角度和装配间隙必须符合图纸设计或所执行标准的要求。
焊接缺陷问题分析
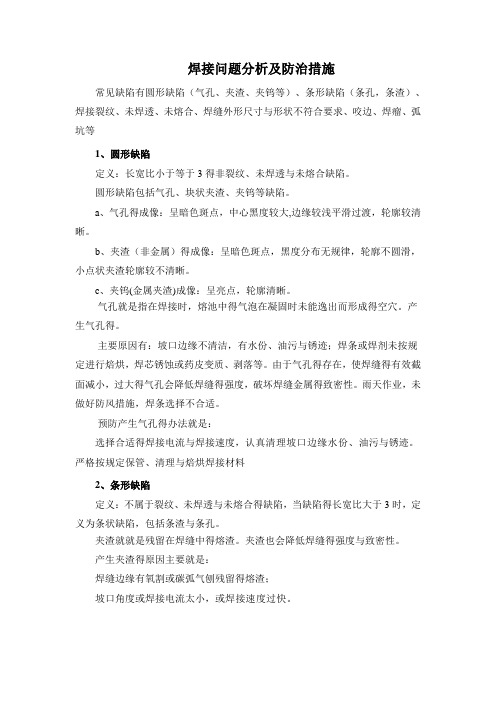
焊接问题分析及防治措施常见缺陷有圆形缺陷(气孔、夹渣、夹钨等)、条形缺陷(条孔,条渣)、焊接裂纹、未焊透、未熔合、焊缝外形尺寸与形状不符合要求、咬边、焊瘤、弧坑等1、圆形缺陷定义:长宽比小于等于3得非裂纹、未焊透与未熔合缺陷。
圆形缺陷包括气孔、块状夹渣、夹钨等缺陷。
a、气孔得成像:呈暗色斑点,中心黑度较大,边缘较浅平滑过渡,轮廓较清晰。
b、夹渣(非金属)得成像:呈暗色斑点,黑度分布无规律,轮廓不圆滑,小点状夹渣轮廓较不清晰。
c、夹钨(金属夹渣)成像:呈亮点,轮廓清晰。
气孔就是指在焊接时,熔池中得气泡在凝固时未能逸出而形成得空穴。
产生气孔得。
主要原因有:坡口边缘不清洁,有水份、油污与锈迹;焊条或焊剂未按规定进行焙烘,焊芯锈蚀或药皮变质、剥落等。
由于气孔得存在,使焊缝得有效截面减小,过大得气孔会降低焊缝得强度,破坏焊缝金属得致密性。
雨天作业,未做好防风措施,焊条选择不合适。
预防产生气孔得办法就是:选择合适得焊接电流与焊接速度,认真清理坡口边缘水份、油污与锈迹。
严格按规定保管、清理与焙烘焊接材料2、条形缺陷定义:不属于裂纹、未焊透与未熔合得缺陷,当缺陷得长宽比大于3时,定义为条状缺陷,包括条渣与条孔。
夹渣就就是残留在焊缝中得熔渣。
夹渣也会降低焊缝得强度与致密性。
产生夹渣得原因主要就是:焊缝边缘有氧割或碳弧气刨残留得熔渣;坡口角度或焊接电流太小,或焊接速度过快。
在使用酸性焊条时,由于电流太小或运条不当形成“糊渣”;使用碱性焊条时,由于电弧过长或极性不正确也会造成夹渣。
防止产生夹渣得措施就是:选择合适种类得焊条、焊剂;多层焊时,认真清理前层得熔渣;正确选取坡口尺寸,认真清理坡口边缘,选用合适得焊接电流与焊接速度,运条摆动要适当。
3、未焊透定义:未焊透就是指母材金属之间没有熔化,焊缝金属没有进入接头得部位根部造成得缺陷。
影像特征:未焊透得典型影像就是细直黑线,两侧轮廓都很整齐,为坡口钝边痕迹,宽度恰好就是钝边得间隙宽度。
简述常见的焊接缺陷
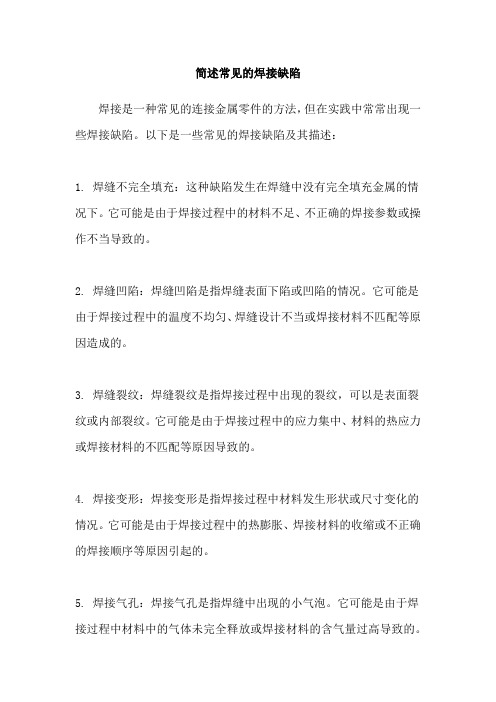
简述常见的焊接缺陷
焊接是一种常见的连接金属零件的方法,但在实践中常常出现一些焊接缺陷。
以下是一些常见的焊接缺陷及其描述:
1. 焊缝不完全填充:这种缺陷发生在焊缝中没有完全填充金属的情况下。
它可能是由于焊接过程中的材料不足、不正确的焊接参数或操作不当导致的。
2. 焊缝凹陷:焊缝凹陷是指焊缝表面下陷或凹陷的情况。
它可能是由于焊接过程中的温度不均匀、焊缝设计不当或焊接材料不匹配等原因造成的。
3. 焊缝裂纹:焊缝裂纹是指焊接过程中出现的裂纹,可以是表面裂纹或内部裂纹。
它可能是由于焊接过程中的应力集中、材料的热应力或焊接材料的不匹配等原因导致的。
4. 焊接变形:焊接变形是指焊接过程中材料发生形状或尺寸变化的情况。
它可能是由于焊接过程中的热膨胀、焊接材料的收缩或不正确的焊接顺序等原因引起的。
5. 焊接气孔:焊接气孔是指焊缝中出现的小气泡。
它可能是由于焊接过程中材料中的气体未完全释放或焊接材料的含气量过高导致的。
6. 焊缝咬边:焊缝咬边是指焊接过程中焊缝两侧的金属出现过度熔化或溶解的现象。
它可能是由于焊接过程中焊接电流过大、焊接速度过快或焊接材料的选择不当导致的。
除了上述常见的焊接缺陷,还有一些其他可能出现的问题,如焊接渣、焊结不牢固、焊接变色等。
为了避免焊接缺陷,焊接操作人员应该控制好焊接参数,选择合适的焊接材料,同时要进行焊前、焊中和焊后的质量检查,以确保焊接接头的质量和可靠性。
史上最全的焊接缺陷产生原因及处理办法

史上最全的焊接缺陷产生原因及处理办法焊接缺陷是指焊接过程中出现的质量问题,包括焊接接头的裂纹、孔隙、夹杂物等缺陷。
这些缺陷会影响焊接接头的强度、密封性和耐腐蚀性,因此及时发现并处理焊接缺陷至关重要。
本文将介绍一些常见的焊接缺陷产生原因及相应的处理办法。
1.焊接接头裂纹:原因:(1)热裂纹:焊接过程中,金属在快速冷却过程中产生应力,导致裂纹产生。
(2)冷裂纹:焊接接头长时间在低温环境下使用,受到外部冻结和膨胀引起。
处理办法:(1)控制焊接温度和预热焊件,以减少热应力。
(2)使用低氢焊条或预热焊件,以减少氢原子的进入。
(3)进行适当的回火处理,以减少残余应力。
2.焊接接头孔隙:原因:(1)焊接材料含有气体,如铁锈或涂层。
(2)焊接过程中保护性气体不足。
(3)焊接参数设置不正确,如焊接电流过低或焊接速度过快。
(4)焊接材料含有水分。
处理办法:(1)使用清洁的焊接材料,并确保焊接表面干净。
(2)提供足够的保护气体,以减少氧气和水蒸气的进入。
(3)调整焊接参数,使其适合焊接材料。
(4)在焊接前进行预热,以减少水分含量。
3.焊接接头夹杂物:原因:(1)焊接材料中包含的杂质。
(2)焊接材料与辅助材料的不匹配。
(3)焊接材料的氧化物。
处理办法:(1)使用高纯度的焊接材料,以减少杂质含量。
(2)选用合适的焊接材料和辅助材料,确保它们的化学成分相似。
(3)确保焊接材料没有明显的氧化。
4.焊接接头下沉:原因:(1)焊接时材料太薄,导致热传导速度过快。
(2)焊接过程中温度不均匀分布。
(3)焊接电流过高,引起材料融化。
处理办法:(1)加大焊接电流,以增加热量传输。
(2)调整焊接速度和焊接参数,使其适合焊接材料。
(3)使用合适的焊接材料和辅助材料,以增加熔池的稳定性。
5.焊接接头变形:原因:(1)焊接过程中产生的应力导致材料变形。
(2)焊接过程中热膨胀引起的变形。
处理办法:(1)使用适当的夹具和支撑装置,以减少焊接过程中的应力。
焊接中常见的缺陷及防治措施
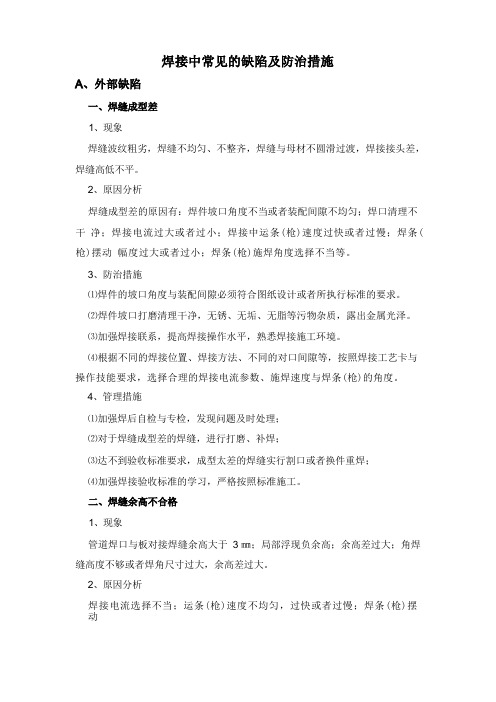
1、现象焊缝波纹粗劣,焊缝不均匀、不整齐,焊缝与母材不圆滑过渡,焊接接头差,焊缝高低不平。
2、原因分析焊缝成型差的原因有:焊件坡口角度不当或者装配间隙不均匀;焊口清理不干净;焊接电流过大或者过小;焊接中运条(枪)速度过快或者过慢;焊条(枪)摆动幅度过大或者过小;焊条(枪)施焊角度选择不当等。
3、防治措施⑴焊件的坡口角度与装配间隙必须符合图纸设计或者所执行标准的要求。
⑵焊件坡口打磨清理干净,无锈、无垢、无脂等污物杂质,露出金属光泽。
⑶加强焊接联系,提高焊接操作水平,熟悉焊接施工环境。
⑷根据不同的焊接位置、焊接方法、不同的对口间隙等,按照焊接工艺卡与操作技能要求,选择合理的焊接电流参数、施焊速度与焊条(枪)的角度。
4、管理措施⑴加强焊后自检与专检,发现问题及时处理;⑵对于焊缝成型差的焊缝,进行打磨、补焊;⑶达不到验收标准要求,成型太差的焊缝实行割口或者换件重焊;⑷加强焊接验收标准的学习,严格按照标准施工。
1、现象管道焊口与板对接焊缝余高大于 3 ㎜;局部浮现负余高;余高差过大;角焊缝高度不够或者焊角尺寸过大,余高差过大。
2、原因分析焊接电流选择不当;运条(枪)速度不均匀,过快或者过慢;焊条(枪)摆动幅度不均匀;焊条(枪)施焊角度选择不当等。
3、防治措施⑴根据不同焊接位置、焊接方法,选择合理的焊接电流参数;⑵增强焊工责任心,焊接速度适合所选的焊接电流,运条(枪)速度均匀,避免忽快忽慢;⑶焊条(枪)摆动幅度不一致,摆动速度合理、均匀;⑷注意保持正确的焊条(枪)角度。
4、管理措施⑴加强焊工操作技能培训,提高焊缝盖面水平;⑵对焊缝进行必要的打磨与补焊;⑶加强焊后检查,发现问题及时处理;⑷技术员的交底中,对焊角角度要求做详细说明。
三、焊缝宽窄差不合格1、现象焊缝边缘不匀直,焊缝宽窄差大于3 ㎜。
2、原因分析焊条(枪)摆动幅度不一致,部份地方幅度过大,部份地方摆动过小;焊条(枪)角度不合适;焊接位置艰难,妨碍焊接人员视线。
焊接中常见的缺点及解决方式

焊接中常见的缺点及解决方式在焊接过程中,常见的缺点包括焊接缺陷、焊接变形、焊接应力等,下面将对这些缺点进行详细阐述,并提供相应的解决方式。
一、焊接缺陷:1.气孔:气孔是焊接过程中最常见的缺陷,主要由于焊接材料中含有的气体未能完全排除或者焊接过程中引入了大量气体所致。
解决气孔问题的方法包括:-提高焊接设备的气体保护性能,确保焊接区域的环境干燥。
-使用质量好的焊接材料,确保焊接材料的纯净度。
-控制焊接参数,如电流、电压、焊接速度等,以确保焊接过程中可以形成稳定的焊接池。
2.缺口:焊接缺口是指焊缝中断裂的现象,通常由于焊接过程中的拉伸或剪切力过大所致。
解决缺口问题的方法包括:-优化焊接顺序,避免对焊缝施加过大的力。
-选用合适的焊接材料,具有良好的韧性和抗断裂性能。
-控制焊接过程中的热输入,避免产生过大的热应力。
3.结构性缺陷:结构性缺陷是焊缝内部存在的结构性问题,如未融合、不均匀融合、夹渣等。
解决结构性缺陷的方法包括:-严格按照焊接工艺要求进行焊接,确保焊接过程中的热量均匀分布。
-控制焊接速度,避免焊接过程中出现局部过热或不足的情况。
-使用合适的电极或焊丝,能够提高焊接池的稳定性,减少结构性缺陷的发生。
二、焊接变形:焊接变形是指焊接过程中由于热膨胀和冷却引起的构件形状的变化。
焊接变形常见的解决方式包括:1.控制焊接过程中的热输入,避免产生过大的热应力。
2.采用适当的焊接顺序,避免不同区域的温度差异过大。
3.使用焊接变形补偿技术,如预应力焊接、补偿焊接等。
三、焊接应力:焊接应力是指由于焊接过程中产生的热应力所引起的构件内部应力。
焊接应力常见的解决方式包括:1.适当控制焊接参数,避免产生过大的焊接热。
这样可以减小构件的焊接应力。
2.选用合适的焊接方法和焊接顺序,尽量减小焊接区域的变形,从而减小应力集中。
3.对于大型和重要的焊接构件,可以采用热处理等后续加工工艺,以减小焊接应力。
综上所述,焊接中常见的缺点包括焊接缺陷、焊接变形和焊接应力,针对这些缺点,可以通过优化焊接工艺参数、选用合适的焊接材料、控制焊接顺序和使用后续加工工艺等方法来解决。
焊接培训资料--焊接缺陷

焊接培训资料--焊接缺陷焊接是一种常见的连接金属材料的方法,应用广泛,但在焊接过程中可能会出现一些焊接缺陷。
本文将主要讨论焊接缺陷的分类、原因以及如何避免和修复这些缺陷。
第一篇:一、焊接缺陷的分类焊接缺陷可以分为表面缺陷和内部缺陷两大类。
表面缺陷主要包括焊缝不充分、气孔、裂纹、夹渣等。
内部缺陷则包括焊缝夹杂物、未熔合、未熔透等。
1. 焊缝不充分:焊缝不充分是指焊接时金属材料没有完全融合,导致焊缝的强度降低。
主要原因是焊接接头准备不充分、焊接电流过小或焊接速度过快等。
2. 气孔:气孔是焊接过程中产生的气体聚集在焊缝中形成的孔洞。
气孔的出现主要是由于焊接材料表面涂有油脂、水分等杂质、焊接电流过大或焊接区域未完全覆盖保护气体等原因造成的。
二、焊接缺陷的原因1. 材料本身质量差:焊接缺陷的一个重要原因是焊接材料本身的质量差。
如果材料含有太多的夹杂物、杂质或其他有害成分,焊接过程中就容易产生缺陷。
2. 焊接参数不合理:焊接参数不合理也是焊接缺陷的一个重要原因。
焊接电流、电压、焊接速度、保护气体流量等参数的选择与设置非常关键,如果这些参数选择不当,就容易导致焊接缺陷的产生。
第二篇:三、如何避免焊接缺陷1. 牢记焊接原理:焊接操作人员应该熟记焊接原理,了解焊接过程中各种参数的作用和要求,确保操作正确。
2. 保证焊接材料质量:选择优质的焊接材料,避免使用含有太多夹杂物、杂质的材料,同时要保证焊接材料的储存条件良好。
3. 合理设置焊接参数:根据焊接材料和焊接要求,合理设置焊接电流、电压、焊接速度等参数。
通过实验和经验总结,找到最佳的焊接参数组合。
4. 做好前期准备工作:焊接前应将焊接接头进行清洁处理,确保表面没有油脂、水分等杂质。
同时,还应对焊接机器进行检查和维护,确保其正常运行。
四、焊接缺陷的修复方法1. 对于焊缝不充分的缺陷,可以采取焊后补焊或采用其他焊接方法进行修复。
2. 对于气孔缺陷,可以采用填焊、补焊等方法进行修复。
焊接中常见的缺陷及预防措施
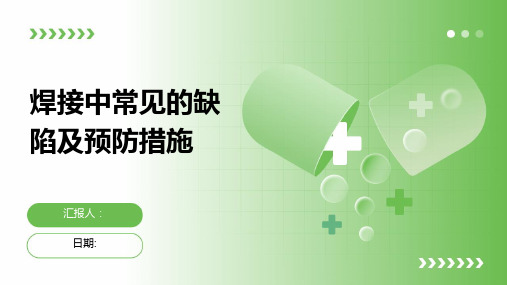
合理选择焊接顺序
避免在结构中产生过大的 拘束度。
夹渣的预防措施
1 2
选用合适的焊接电流和焊接速度
确保熔池充分熔化,避免熔渣残留。
清除杂质
焊接前彻底清除坡口边缘和焊丝上的杂质。
3
多层焊接
每层焊接完成后,彻底清除熔渣再进行下一层焊 接。
未焊透与未熔合的预防措施
选用合适的坡口和焊接参数
根据母材厚度和焊接位置选择合适的坡口形状和焊接参数 。
裂纹
总结词
裂纹是焊接中危险的缺陷,表现为焊缝中的开裂部分。
详细描述
裂纹的产生主要是由于焊接过程中热应力、材料质量、结构设计等因素的影响, 焊缝中的应力超过材料的强度极限,导致焊缝开裂。裂纹的存在会严重影响焊接 的强度和稳定性。
夹渣
总结词
夹渣是焊接中常见的缺陷,表现为焊缝中存在的杂质和夹杂 物。
详细描述
电弧太长使得热量分散过大,不利于 熔池的保持和气体的排除,容易形成 气孔。
裂纹的产生原因
碳当量过高
预热温度不足
对于一些高碳钢或合金钢,其碳当量过高 ,焊接时易产生裂纹。
对于一些大厚度的焊件,预热温度不足导 致焊缝冷却速度过快,产生裂纹。
应力集中
焊缝处理不当
由于结构或工件形状的原因,焊缝处存在 较大的应力集中,易产生裂纹。
焊接中常见的缺 陷及预防措施
汇报人: 日期:
目录
• 引言 • 焊接缺陷的分类与识别 • 焊接缺陷的产生原因 • 焊接缺陷的预防措施 • 焊接缺陷的修复方法 • 结论
01
引言
焊接的定义与重要性
• 焊接是一种通过加热或加压金属接头,使其原子间相互结合, 达到连接金属的方法。焊接在工业制造中扮演着至关重要的角 色,包括桥梁、建筑、汽车、船舶、飞机等。
焊接常见缺陷有哪些原因
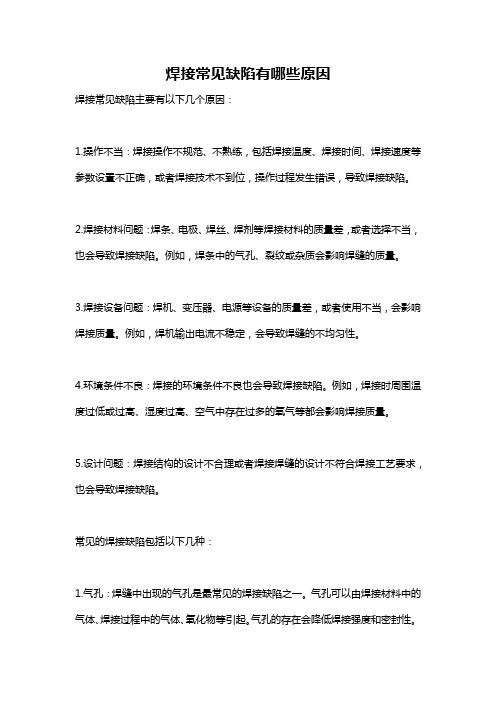
焊接常见缺陷有哪些原因焊接常见缺陷主要有以下几个原因:1.操作不当:焊接操作不规范、不熟练,包括焊接温度、焊接时间、焊接速度等参数设置不正确,或者焊接技术不到位,操作过程发生错误,导致焊接缺陷。
2.焊接材料问题:焊条、电极、焊丝、焊剂等焊接材料的质量差,或者选择不当,也会导致焊接缺陷。
例如,焊条中的气孔、裂纹或杂质会影响焊缝的质量。
3.焊接设备问题:焊机、变压器、电源等设备的质量差,或者使用不当,会影响焊接质量。
例如,焊机输出电流不稳定,会导致焊缝的不均匀性。
4.环境条件不良:焊接的环境条件不良也会导致焊接缺陷。
例如,焊接时周围温度过低或过高、湿度过高、空气中存在过多的氧气等都会影响焊接质量。
5.设计问题:焊接结构的设计不合理或者焊接焊缝的设计不符合焊接工艺要求,也会导致焊接缺陷。
常见的焊接缺陷包括以下几种:1.气孔:焊缝中出现的气孔是最常见的焊接缺陷之一。
气孔可以由焊接材料中的气体、焊接过程中的气体、氧化物等引起。
气孔的存在会降低焊接强度和密封性。
2.夹渣:焊缝中出现的夹渣是焊接中常见的缺陷之一。
夹渣会使焊缝中夹杂物增多,降低焊接强度。
夹渣通常由焊条、焊丝、焊剂等材料中的杂质引起。
3.裂纹:焊接过程中材料的收缩或冷却不均匀可能导致焊接缺陷,如焊缝中出现裂纹。
裂纹会降低焊接强度和密封性。
4.未熔透:未熔透是焊接缺陷的一种,指焊缝中未完全熔化的部分。
未熔透会使焊接强度降低,影响焊接质量。
5.焊缝形状不符合要求:焊缝的几何形状与设计要求不符,如焊缝宽度、高度等超过规定范围,都属于焊接缺陷。
这种缺陷可能影响焊接件的负载能力和外观要求。
6.焊渣:焊缝中残留的焊渣也是一种常见的焊接缺陷。
焊渣会降低焊接强度和密封性,还会影响焊接表面的平整度。
综上所述,焊接常见缺陷的产生主要与操作不当、焊接材料问题、焊接设备问题、环境条件不良、设计问题等有关。
为了确保焊接质量,必须严格按照焊接工艺要求进行操作,并选择合适的焊接材料和设备,同时注意环境条件的影响。
焊接常见的缺陷及产生原因
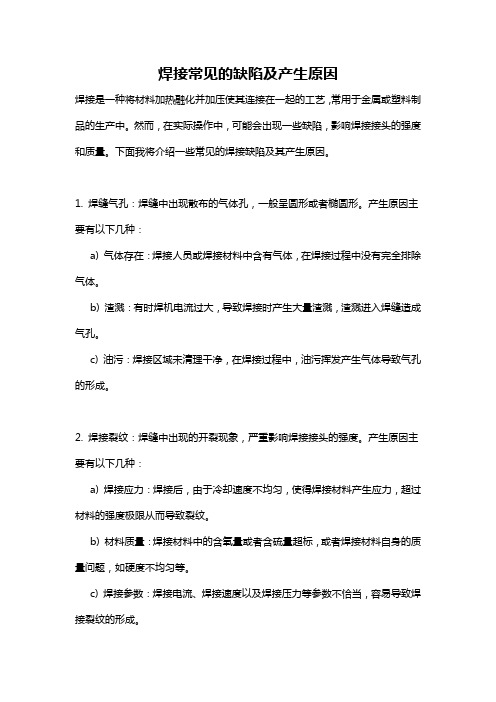
焊接常见的缺陷及产生原因焊接是一种将材料加热融化并加压使其连接在一起的工艺,常用于金属或塑料制品的生产中。
然而,在实际操作中,可能会出现一些缺陷,影响焊接接头的强度和质量。
下面我将介绍一些常见的焊接缺陷及其产生原因。
1. 焊缝气孔:焊缝中出现散布的气体孔,一般呈圆形或者椭圆形。
产生原因主要有以下几种:a) 气体存在:焊接人员或焊接材料中含有气体,在焊接过程中没有完全排除气体。
b) 渣溅:有时焊机电流过大,导致焊接时产生大量渣溅,渣溅进入焊缝造成气孔。
c) 油污:焊接区域未清理干净,在焊接过程中,油污挥发产生气体导致气孔的形成。
2. 焊接裂纹:焊缝中出现的开裂现象,严重影响焊接接头的强度。
产生原因主要有以下几种:a) 焊接应力:焊接后,由于冷却速度不均匀,使得焊接材料产生应力,超过材料的强度极限从而导致裂纹。
b) 材料质量:焊接材料中的含氧量或者含硫量超标,或者焊接材料自身的质量问题,如硬度不均匀等。
c) 焊接参数:焊接电流、焊接速度以及焊接压力等参数不恰当,容易导致焊接裂纹的形成。
3. 焊接结构不均匀:焊接接头的强度和质量不均匀,一部分焊缝更容易破裂。
产生原因主要有以下几种:a) 预热温度不够:焊接材料在焊接前没有经过预热处理,容易导致结构不均匀。
b) 焊接参数不一致:不同焊缝采用了不同的焊接参数,导致焊接接头的质量不均匀。
c) 焊接过程控制不当:焊接时控制不良,如焊接速度不稳定、电流波动大等,容易导致结构不均匀。
4. 焊缝错边:焊接接头两边焊缝位置不对称或偏移,容易导致接头强度下降。
产生原因主要有以下几种:a) 材料不准确对位:焊接前没有正确的对位,或者对位不准确导致焊缝偏移。
b) 焊接操作不当:焊接人员的焊接技术不熟练或者操作不当,容易导致焊缝错边。
c) 焊接设备问题:焊机设备本身有问题,如电流不稳定等,导致焊接接头错边。
针对这些常见的焊接缺陷,可以采取一些措施来避免或解决:1. 焊缝气孔:焊接前进行充分的气体排除,确保焊缝周围环境清洁,使用合适的焊接工艺参数。
焊接过程中的八大缺陷

一、焊缝尺寸不符规范要求现象:焊缝在检查中焊缝的高度过大或过小;或焊缝的宽度太宽或太窄,以及焊缝和母材之间的过渡部位不平滑、表面粗糙、焊缝纵、横向不整齐,还有在角焊缝部位焊缝的下凹量过大。
原因:焊缝坡口加工的平直度较差,坡口的角度不当或装配间隙大小不均等而引起的。
焊接中电流过大,使焊条熔化过快,控制焊缝成形困难,电流过小,在焊接引弧时会使焊条产生“粘合现象”,造成焊不透或焊瘤。
焊工操作熟练程不够,运条方法不当,如过快或过慢,以及焊条角度不正确。
埋弧自动焊过程,焊接工艺参数选择不当。
防治措施:按设计要求和焊接规范的规定加工焊缝坡口,尽量选用机械加工以使坡口角度和坡口边缘的直线度和坡口边缘的直线度达到要求,避免用人工气割、手工铲削加工坡口。
在组对时,保证焊缝间隙的均匀一致,为保证焊接质量打下基础。
通过焊接工艺评定,选择合适的焊接工艺参数。
焊工要持证上岗,经过培训的焊工有一定的理论基础和操作技能。
多层焊缝在焊接表面最后一层焊缝是,在保证和底层熔合的条件下,应采用比各层间焊接电流较小,并用小直径(φ2.0mm~3.0mm)的焊条覆面焊。
运条速度要求均匀,有节奏地向纵向推进,并作一定宽度的横向摆动,可使焊缝表面整齐美观。
二、咬边(咬肉)现象:焊接时的电弧将焊缝边缘熔出的凹陷或沟槽没有得到熔化金属的补充而留下缺口。
过深的咬边会使焊接接头的强度减弱,造成局部应力集中,承载后会在咬边处产生裂纹。
原因:主要是焊接电流过大,电弧过长,焊条角度掌握不合适和运条的速度不当以及焊接终了焊条留置长度太短等而形成咬边。
一般在立焊、横焊、仰焊时是一种常见缺陷。
防治措施:焊接时电流不宜过大,电弧不要拉得过长或过短,尽量采用短弧焊。
掌握合适的焊条角度和熟练的运条手法,焊条摆动到边缘时应稍慢,使熔化的焊条金属填满边缘,而在中间则要稍快些。
焊缝咬边的深度应小于0.5mm,长度小于焊缝全长的10%,且连续长度小于10mm。
一旦出现深度或产度超过上述允差,应将缺陷处清理干净,采用直径较小、牌号相同的焊条,焊接电流比正常的稍偏大,进行补焊填满。
焊接中常见的缺陷及防治措施
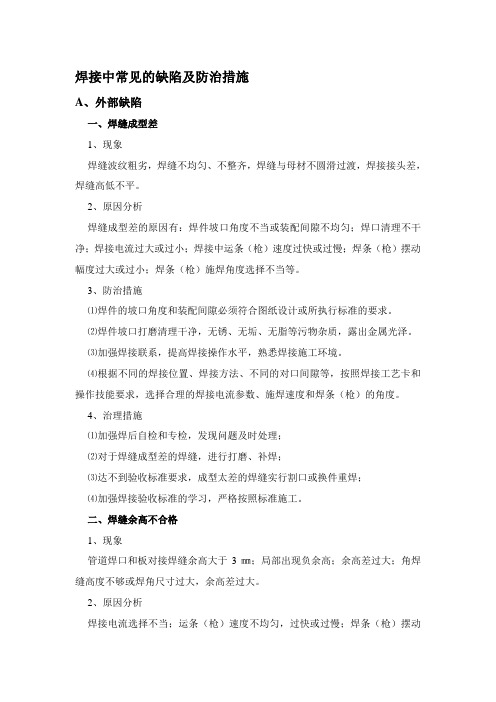
焊接中常见的缺陷及防治措施A、外部缺陷一、焊缝成型差1、现象焊缝波纹粗劣,焊缝不均匀、不整齐,焊缝与母材不圆滑过渡,焊接接头差,焊缝高低不平。
2、原因分析焊缝成型差的原因有:焊件坡口角度不当或装配间隙不均匀;焊口清理不干净;焊接电流过大或过小;焊接中运条(枪)速度过快或过慢;焊条(枪)摆动幅度过大或过小;焊条(枪)施焊角度选择不当等。
3、防治措施⑴焊件的坡口角度和装配间隙必须符合图纸设计或所执行标准的要求。
⑵焊件坡口打磨清理干净,无锈、无垢、无脂等污物杂质,露出金属光泽。
⑶加强焊接联系,提高焊接操作水平,熟悉焊接施工环境。
⑷根据不同的焊接位置、焊接方法、不同的对口间隙等,按照焊接工艺卡和操作技能要求,选择合理的焊接电流参数、施焊速度和焊条(枪)的角度。
4、治理措施⑴加强焊后自检和专检,发现问题及时处理;⑵对于焊缝成型差的焊缝,进行打磨、补焊;⑶达不到验收标准要求,成型太差的焊缝实行割口或换件重焊;⑷加强焊接验收标准的学习,严格按照标准施工。
二、焊缝余高不合格1、现象管道焊口和板对接焊缝余高大于3㎜;局部出现负余高;余高差过大;角焊缝高度不够或焊角尺寸过大,余高差过大。
2、原因分析焊接电流选择不当;运条(枪)速度不均匀,过快或过慢;焊条(枪)摆动幅度不均匀;焊条(枪)施焊角度选择不当等。
3、防治措施⑴根据不同焊接位置、焊接方法,选择合理的焊接电流参数;⑵增强焊工责任心,焊接速度适合所选的焊接电流,运条(枪)速度均匀,避免忽快忽慢;⑶焊条(枪)摆动幅度不一致,摆动速度合理、均匀;⑷注意保持正确的焊条(枪)角度。
4、治理措施⑴加强焊工操作技能培训,提高焊缝盖面水平;⑵对焊缝进行必要的打磨和补焊;⑶加强焊后检查,发现问题及时处理;⑷技术员的交底中,对焊角角度要求做详细说明。
三、焊缝宽窄差不合格1、现象焊缝边缘不匀直,焊缝宽窄差大于3㎜。
2、原因分析焊条(枪)摆动幅度不一致,部分地方幅度过大,部分地方摆动过小;焊条(枪)角度不合适;焊接位置困难,妨碍焊接人员视线。
- 1、下载文档前请自行甄别文档内容的完整性,平台不提供额外的编辑、内容补充、找答案等附加服务。
- 2、"仅部分预览"的文档,不可在线预览部分如存在完整性等问题,可反馈申请退款(可完整预览的文档不适用该条件!)。
- 3、如文档侵犯您的权益,请联系客服反馈,我们会尽快为您处理(人工客服工作时间:9:00-18:30)。
镀覆孔的质量控制和检测方法
正确认识SPC
PCB板返修时的两个关键工艺
GERBER RS274X - CAD/CAM文件格式
2000版ISO9000族标准翻译中几对术语辨析
利用PPM质量制建立电子质量文档
b)在进行汽相焊接时印制电路组件预热不充分。汽相焊是利用惰性液体蒸汽冷凝在元件引脚和PCB焊盘上时,释放出热量而熔化焊膏。汽相焊分平衡区和饱和蒸汽区,在饱和蒸汽区焊接温度高达217°C,在生产过程中我们发现,如果被焊组件预热不充分,经受一百多度的温差变化,汽相焊的汽化力容易将小于1206封装尺寸的片式元件浮起,从而产生立片现象。我们通过将被焊组件在高低箱内以145°C-150°C的温度预热1-2分钟,然后在汽相焊的平衡区内再预热1分钟左右,最后缓慢进入饱和蒸汽区焊接消除了立片现象。
[相关专题]
元件竖立的问题
使用聚焦白光的选择性焊接
芯片的偏斜
国庆购买品牌机,选哪台最超值?
印制板外形加工技术
制造执行系统:改进周期时间和品质
无铅焊锡与导电性胶
焊锡膏使用常见问题分析
自动装配设备中的静电防护问题
二、 桥联
桥联的发生原因,大多是焊料过量或焊料印刷后严重塌边,或是基板焊区尺寸超差,SMD贴装偏移等引起的,在SOP、QFP电路趋向微细化阶段,桥联会造成电气短路,影响产品使用。
作为改正措施 基板焊区的尺寸设定要符合设计要求。
3、 SMD的贴装位置要在规定的范围内。
a)丝印细间距引线,通常选用厚度较薄的模板,为避免漏印的焊膏量偏少,所需的焊膏黏度应较低,这样焊膏流动性好,易漏印,而且模板与PCB脱模时不易带走焊膏,保证焊膏涂覆量。但同时为了保持焊膏印刷图形的理想形态,又需要较高的焊膏黏度。我们解决这一矛盾的方法是选用45-75um的更小粒度和球形颗粒焊膏,如爱法公司的RMA390DH3型焊膏。另外,在丝印时保持适宜的环境温度,焊膏黏度与环境温度的关系式表示如下 :
2.1.2 回流焊中的锡球
2.1.2.1 回流焊中锡球形成的机理
回流焊接中出的锡球,常常藏于矩形片式元件两端之间的侧面或细距引脚之间。在元件贴装过程中,焊膏被置于片式元件的引脚与焊盘之间,随着印制板穿过回流焊炉,焊膏熔化变成液体,如果与焊盘和器件引脚等润湿不良,液态焊锡会因收缩而使焊缝填充不充分,所有焊料颗粒不能聚合成一个焊点。部分液态焊锡会从焊缝流出,形成锡球。因此,焊锡与焊盘和器件引脚润湿性差是导致锡球形成的根本原因。
2. 基板焊区长度的尺寸要适当制定。
3. 减少焊料熔融时对SMD端部产生的表面张力。
4. 焊料的印刷厚度尺寸要设定正确。
5. 采取合理的预热方式,实现焊接时的均匀加热。
--------------------------------------------------------------------------------
b)如果总在同一位置上出现焊球,就有必要检查金属板设计结构。模板开口尺寸腐蚀精度达不到要求,对于焊盘大小偏大,以及表面材质较软(如铜模板),造成漏印焊膏的外形轮廓不清晰,互相桥连,这种情况多出现在对细间距器件的焊盘漏印时,回流焊后必然造成引脚间大量锡珠的产生。因此,应针对焊盘图形的不同形状和中心距,选择适宜的模板材料及模板制作工艺来保证焊膏印刷质量。
一、 润湿不良
润湿不良是指焊接过程中焊料和基板焊区,经浸润后不生成金属间的反应,而造成漏焊或少焊故障。其原因大多是焊区表面受到污染,或沾上阻焊剂,或是被接合物表面生成金属化合物层而引起的,例如银的表面有硫化物,锡的表面有氧化物等都会产生润湿不良。另外,焊料中残留的铝、锌、镉等超过0.005%时,由焊剂吸湿作用使活性程度降低,也可发生润湿不良。波峰焊接中,如有气体存在于基板表面,也易发生这一故障。因此除了要执行合适的焊接工艺外,对基板表面和元件表面要做好防污措施,选择合适的焊料,并设定合理的焊接温度与时间。
2 几种典型焊接缺陷及解决措施
2.1 波峰焊和回流焊中的锡球
锡球的存在表明工艺不完全正确,而且电子产品存在短路的危险,因此需要排除。国际上对锡球存在认可标准是:印制电路组件在600范围内不能出现超过5个锡球。产生锡球的原因有多种,需要找到问题根源。
2.1.1 波峰焊中的锡球
波峰焊中常常出现锡球,主要原因有两方面:第一,由于焊接印制板时,印制板上的通孔附近的水分受热而变成蒸汽。如果孔壁金属镀层较薄或有空隙,水汽就会通过孔壁排除,如果孔内有焊料,当焊料凝固时水汽就会在焊料内产生空隙(针眼),或挤出焊料在印制板正面产生锡球。第二,在印制板反面(即接触波峰的一面)产生的锡球是由于波峰焊接中一些工艺参数设置不当而造成的。如果助焊剂涂覆量增加或预热温度设置过低,就可能影响焊剂内组成成分的蒸发,在印制板进入波峰时,多余的焊剂受高温蒸发,将焊料从锡槽中溅出来,在印制板面上产生不规则的焊料球。
2.2 立片问题(曼哈顿现象)
矩形片式元件的一端焊接在焊盘上,而另一端则翘立,这种现象就称为曼哈顿现象。引起该种现象主要原因是元件两端受热不均匀,焊膏熔化有先后所致。在以下情况会造成元件两端热不均匀:
a)有缺陷的元件排列方向设计。我们设想在再流焊炉中有一条横跨炉子宽度的再流焊限线,一旦焊膏通过它就会立即熔化,如图1所示。片式矩形元件的一个端头先通过再流焊限线,焊膏先熔化,完全浸润元件的金属表面,具有液态表面张力;而另一端未达到183°C液相温度,焊膏未熔化,只有焊剂的粘接力,该力远小于再流焊焊膏的表面张力,因而,使未熔化端的元件端头向上直立。因此,保持元件两端同时进入再流焊限线,使两端焊盘上的焊膏同时熔化,形成均衡的液态表面张力,保持元件位置不变。
c)焊盘设计质量的影响。若片式元件的一对焊盘大小不同或不对称,也会引起漏印的焊膏量不一致,小焊盘对温度响应快,其上的焊膏易熔化,大焊盘则相反,所以,当小焊盘上的焊膏熔化后,在焊膏表面张力作用下,将元件拉直竖起。焊盘的宽度或间隙过大,也都可能出现立片现象。严格按标准规范进行焊盘设计是解决该缺陷的先决条件。
2.3 细间距引脚桥接问题
导致细间距元器件引脚桥接缺陷的主要因素有:a)漏印的焊膏成型不佳;b)印制板上有缺陷的细间距引线制作;c)不恰当的回流焊温度曲线设置等。因而,应从模板的制作、丝印工艺、回流焊工艺等关键工序的质量控制入手,尽可能避免桥接隐患。
2.3.1模板材料的选择
SMT工艺质量问题70%出至于印刷这到工序,而模板是必不可少的关键工装,直接影响印刷质量。通常我们使用的模板材料是铜板和不锈钢板,不锈钢板与铜板相比有较小的摩擦系数和较高的弹性,因此在其它条件一定的情况下,更有利于焊膏脱模和焊膏成型效果好。通过0.5mm引脚中心距QFP208器件组装试验统计,因铜模板漏印不合格而造成的疵点数占器件总焊点数(208个)的20%左右;在其它条件一定的情况下,利用不锈钢模板漏印,造成的疵点率平均为3%。因此,对引脚中心距为0.635mm以下的细间距元器件的印刷,提出必须采用不锈钢板的要求,厚度优选0.15mm~0.2mm.。
4、 基板布线间隙,阻焊剂的涂敷精度,都必须符合规定要求。
5、 制订合适的焊接工艺参数,防止焊机传送带的机械性振动。
三、裂纹
焊接PCB在刚脱离焊区时,由于焊料和被接合件的热膨胀差异,在急冷或急热作用下,因凝固应力或收缩应力的影响,会使SMD基本产生微裂,焊接后的PCB,在冲切、运输过程中,也必须减少对SMD的冲击应力。弯曲应力。
logu=A/T+B ---------------(1)
式中:u —粘度系数;
A,B—常数
T—绝对温度。
通过上式可看出,温度越高,粘度越小。因此,为获得较高的粘度,我们将环境温度控制20+3°C。
b)刮刀的速度和压力也影响焊膏的流变特性。因为他们决定了焊膏所受的剪切速率和剪切力大小。焊膏黏度与剪切速率的关系如图2所示。在焊膏类型和环境温度较合适的情况下,在刮刀压力一定的情况下,将印刷速度调慢,可以保持焊膏黏度基本不变,这样供给焊膏的时间加长,焊膏量就增多,而且有好的成型。另外,控制脱模速率的减慢和模板与PCB的最小间隙,也会在减少细间距引脚桥接方面起到良好的效果。根据我们使用的SP200型丝印机,我们认为印刷细间距线较理想的工艺参数是:印刷速度保持在10mm/s-25mm/s;脱模速率控制在2s左右;模板与PCB的最小间隙小于等于0.2mm。
2.3.2丝印过程工艺控制
焊膏在进行回流焊之前,若出现坍塌,成型的焊膏图形边不清晰,在贴放元器件或进入回流焊预热区时,由于焊膏中的助焊剂软化,则会造成引脚桥接。焊膏的坍塌是由于使用了不合适的焊膏材料和不宜的环境条件,如较高的室温会造成焊膏坍塌。在丝印工序中,我们通过以下工艺的调整,小心地控制焊膏的流变特性,减少了坍塌。
3.焊膏的使用要符合要求,无吸湿不良。
4.按照焊接类型实施相应的预热工艺。
五、吊桥(曼哈顿)
吊桥不良是指元器件的一端离开焊区而向上方斜立或直立,产生的原因是加热速度过快,加热方向不均衡,焊膏的选择问题,焊接前的预热,以及焊区尺寸,SMD本身形状,润湿性有关。
防止对策:
1. SMD的保管要符合要求
表面贴装产品在设计时,就应考虑到缩小热膨胀的差距,正确设定加热等条件和冷却条件。选用延展性良好的焊料。
四、焊料球
焊料球的产生多发生在焊接过程中的加热急速而使焊料飞散所致,另外与焊料的印刷错位,塌边。污染等也有关系。
防止对策:
1.避免焊接加热中的过急不良,按设定的升温工艺进行焊接。
2.对焊料的印刷塌边,错位等不良品要删除。
制造执行系统:改进周期时间和品质
统计工具促进底线改良
多少静电保护才足够?
寂寞到底 2003-01-17 02:45
1 引言
表面组装技术在减小电子产品体积重量和提高可靠性方面的突出优点,迎合了未来战略武器洲际射程、机动发射、安全可靠、技术先进的特点对制造技术的要求。但是,要制定和选择适合于具体产品的表面组装工艺不是简单的事情,因为SMT技术是涉及了多项技术的复杂的系统工程,其中任何一项因素的改变均会影响电子产品的焊接质量。