换线时间
工厂生产排线换线技巧.

如何实现生产线快速切换
切换作业的项目所占时间的比例 序号
1
准备材料、工装夹具
项目
工装夹具、模具及刀具的安装、拆卸 2
3
决定尺寸
4
试作、调整
时间比例 2Hale Waihona Puke % 20% 10% 50%10
如何实现生产线快速切换
切换作业记录表 设备号
T105
品名
前
后
X
Y
Y
Z
Z
A
A
Y
日月
切换时间
3/30 15’15” 3/30 20’20” 3/30 14’15” 3/30 24’50”
工厂生产排线换线技巧.
换型时间对照表
类型 五金类 注塑类
国内企业
吨位
300吨 以下
1000吨
时间/分钟
30分钟 40-50分钟
300吨 以下
500-800吨
110-150分钟 150-200分钟
流水线
10-30分钟
说明:以上所指换型时间含换模和调试时间。
500强企业
吨位
300吨 以下
1000吨
时间/分钟
20
节拍.6.8 ′
流水线节拍:6.8′
单PCS标准工时:20人×6.8 ′=136 ′/PCS
生产总时间(秒) 10.5 × 3600
每日10.5H、20人标准产能=
=
节拍
6.8
=5559
使用设备/治工具 熔焊机(两台) 卡尺 电栓柜(一台) 手工 内阻仪(一台) 目检 电脑、扫描仪
6
如何实现生产线快速切换
时间,可大幅度减少切换时间。
8
如何实现生产线快速切换
SMT 快速换线推进报告 .pptx11
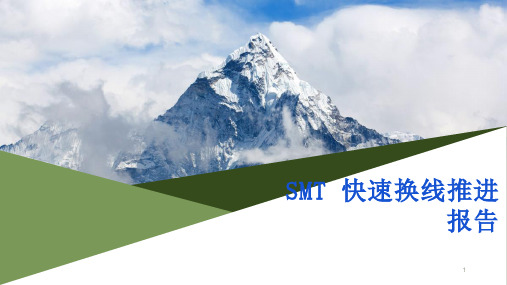
快速换线效益评估
1,SMT 快速换线节约成本: =SMT 全年工单数量* 1.5 *(改善前换线工时- 改善后的换线工时)*SMT 小时成本 = 7,488 *1.5*(1-0.5)*400元/小时 = 2,246,400 元/年
2, 增加人力成本: =人力* 月工资 *13 = 3人/班* 2 班 *7000 元/月* 13月= 546,000 元/年
机台
镭雕 (激光打标)
印刷
动作
时间 (min)
动作
时间 (min)
调程式, 调轨道
回收上个工单 2 钢网(清洗、 2
测张力)
SPI
动作
时间 (min)
贴片
动作
时间 (min)
下料,将料与 料枪放于料车
4
动作
回流焊
时间 (min)
动作
调炉温设 定,调轨
道
时间 (min)
3
AOI
时间
动作
时间 (min) (min)
贴片机
回流焊
AOI
打标机、印刷机、SPI换线 ◄换线小组
第二张工 单换线
换线时 间 第二张工 单/面 第一片
贴片机换线 回流焊换线
AOI换线
◄生技
◄换线小组+随线操机 ◄生技/品质
◄随线AOI
→ ▲→▲→ ▲→ ▲→ ▲
打标 印刷 SPI 贴片 回流焊 AOI
合计
换线时间间隔:30分钟
换线流程改善
AOI(随线)
1人
1,换线小组成员包括生产、生技、品质; 2,换线小组长负责确认计划、料况,联系生技、品质巡检人员; 3, 生技、品质针对换线指定人员,且指定替补人员(当指定人员正在处理其它事情,有替补人员不影响换 线);
换线作业流程
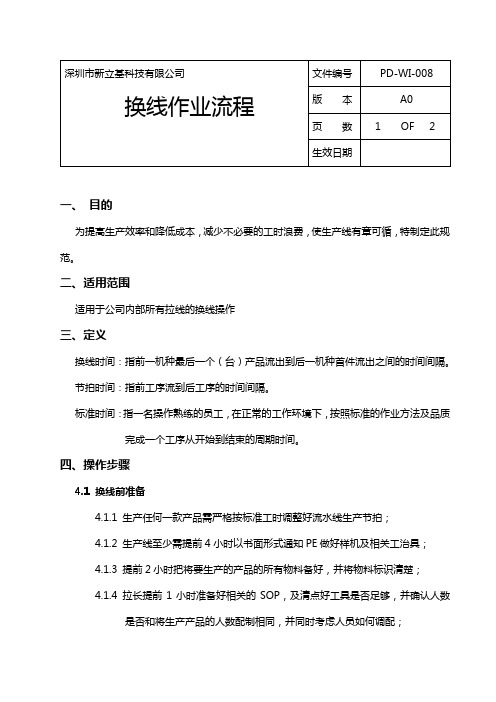
一、目的为提高生产效率和降低成本,减少不必要的工时浪费,使生产线有章可循,特制定此规范。
二、适用范围适用于公司内部所有拉线的换线操作三、定义换线时间:指前一机种最后一个(台)产品流出到后一机种首件流出之间的时间间隔。
节拍时间:指前工序流到后工序的时间间隔。
标准时间:指一名操作熟练的员工,在正常的工作环境下,按照标准的作业方法及品质完成一个工序从开始到结束的周期时间。
四、操作步骤4.1 换线前准备4.1.1 生产任何一款产品需严格按标准工时调整好流水线生产节拍;4.1.2 生产线至少需提前4小时以书面形式通知PE做好样机及相关工治具;4.1.3 提前2小时把将要生产的产品的所有物料备好,并将物料标识清楚;4.1.4 拉长提前1小时准备好相关的SOP,及清点好工具是否足够,并确认人数是否和将生产产品的人数配制相同,并同时考虑人员如何调配;4.1.5 拉长提前30分钟从拉头走到拉尾,通知员工将要转产的型号,并观察生产线上是否有堆积及不良品,如有须尽快处理并要求前后工序人员有效地配合以尽快完成上一款装配;4.1.6 上料员提前5-10分钟准备好将转产型号的物料放于相关岗位附近处。
4.2 换线中4.2.1 当拉头投完最后一台机时,中间间隔3-5分钟投入转产的产品,在此期间,要求员工迅速整理自己区域内的5S;4.2.2 助拉同时将上一产品的SOP收好,并放上新的SOP,让员工能在此间隔内了解自己本工位的作业内容;4.2.3 拉长按照产品流程图负责排拉,由上料员负责摆放好各工位的物料;4.2.4 助拉负责上一款产品的清尾工作,同时统计好未清尾数量并做好相关记录。
4.3 换线后4.3.1 换线完后由助拉负责上一款产品的不良品跟踪,统计好缺料数量,并尽快申请补料;4.3.2 拉长将拉速调整与所生产产品相对应的节拍,再重新确认所排工位是否合理,并作相应调整。
五、注意事项。
如何缩短转线时间,提高生产效率

缩短换线时间就是要提前做相应准备,需要各环节相互配合才行,我们公司叫精益生产。
以下为我公司(例配置Mouentum+CM602+YG100RB+YG100RB(Auto Tray)+HELLER1912)精益生产的方法:
1.物料中心(仓库)收到换线产品型号,就应该针对相应的型号提前备料,一般来说我们是在上个Model 时提前2H将材料准备好,并发给飞达装料组,装好后确认无问题再给生产线待生产。
2.生产线换线前需要提前做到以下:
a:生产线提前10Min将换线产品通知程序组备程序;
b:准备好换线所需的钢网Stencil、刮刀Squeegee;
c:当印锡机印完最后一块就对下一Model进行换线,第一台贴片机完后立即送程序、拆料下线准备换线,最后一台贴完后依次换线;
d:通知测温员试测下一产品炉温;
3.为了不影响下一产品生产,上一产品尾数板移置空闲区域收尾;。
对标准工时认识

标准工时的基本认识被尊称为科学管理之父的泰勒,以作业合理化的手法,从事在当时没有人做过的时间研究( Time Study );换言之,这意味着:「标准工时」是 IE 的原点。
即即是经过一世纪以后的今日,这项 IE 的基本手法之一,仍合适全球的工厂使用,以提高家产的生产性。
标准工时的定义现代对标准工时最一般的定义是:「标准工时乃指对于必需之能力受过充分训练的作业人员,在合适的速度和作业环境下,执行作业所需的时间。
」在这个定义中,所谓「合适的速度」,指的是「在合适的督查之下,工作均衡性的作业人员执行作业的速度;并且依据这类速度,即使作业人员每天连续执行作业,也不会引起身体及精神上的过分疲惫,所以为了保持这类速度,作业人员一定相当努力。
」而所谓「工作均衡性的工作人员」,是指「能够拥有执行某一项作业所需要的知识、体力、完好的训练,以及达成令人满意的质量水平之充分经验等等技术与作业步伐节奏,并足堪成为作业集体之代表者。
」但是,即使经过以上详细的说明,仍没法就此求出标准工时的绝对数值,因此只好依据各家企业使用标准工时的目的及其企业实力,来设定标准工时。
标准工时的角色标准工时的角色,是运用在工厂管理、价格管理的基准,或是对外估价的基准;其范围之广,以以下图所示。
正因这样,在设定标准工时制度与基准值以前,一定经过充分的考量,并且从设定标准工时开始,到全部情况都十分稳固为止,需要投入相当的人力,以及好多的时间与花费。
同一家产内的各家企业,其标准工时并不是完好一致,所以,每家企业应该各自设定其标准工时。
其他,决定后的标准工时,也不是绝对不变的;设备更新、作业改进,或是效率提高等,都会使标准工时不停的更改,并且,重要的标准工时更要合时加以更正。
一般来说,标准工时应在 2 至 3 年内加以更正。
标准工时的构成标准工时的构成,是以在本体作业时间中加入换模时间的型态来表示。
本体作业时间又分为机械作业时间和手工作业时间;其他,换模时间、机械作业时间,以及手工作业时间中,都包含了宽放时间。
SMED快速换线(二)资料重点

11 mins (note: NOT SMED) 59 mins 29 secs 23 mins 33 secs 23 mins 12 secs
96%
57% * 28% * 59% *
➢ 经过一次SMED改善后
The End (or really only the beginning…)
为何需要 SMED?
❖ 降低库存 ❖ 改善产能 ❖ 更好的品质水准 ❖ 更高的安全性 ❖ 弹性灵活运用 ❖ 总产能工时之降低 ❖ 作业员能力之改善 ❖ 更低廉的制造成本
SMED 方法论
❖ 辩认出内在和外在活动步骤 ❖ 将内在活动步骤转换成外在活动步骤 ❖ 改善所有工装设置作业方面的问题 ❖ 废除旧有之设置活动
传统式方法
▪ 工装设置是既有且固定的 ▪ 因此,
➢雇用技巧纯熟工装设置之人员 ➢减少新产品的多样性 ➢合并货堆 ➢大量制造
ቤተ መጻሕፍቲ ባይዱ
新方法
❖ 工装设置方法是可以被改善的! ❖ 小批量生产仅须要很快之工装设置 ❖ 一般而言,工装设置时间至少减少90%是很正常的
装设置时间降低之好处
➢最好之产品品质 ➢最低廉之成本
SMED系统-结果
公司
机器
改善前
改善后
Red’n
T Manufacturing1 80吨单次冲压
4 hours 0 mins 4 mins 18 sec 98%
S Metals1
100吨单次冲压
40 mins
2 mins 26 sec 94%
H Press1
30吨单次冲压
50 mins
48 sec
快速换线及Cell线介绍描述讲课讲稿

快速换线的定义和基本原理—为福什田么电换工线时间长福满中国
观念:传统的切换观念 –要求很高的知识和技巧 –只有通过经验的积累才能提高 –为了减少切换时间太长造成的影响,尽量
将生产批量扩大
这些都是基于切换时间不能大量减少的结论!
快速换线的定义和基本原理—为福什田么电换工线时间长福满中国
•混淆了内部和外部的切换操作
•作业员更换测试治具
快速换线的定义和基本原理—介福绍田电工
福满中国
•什么是SMED ? –Single Minute Exchange of Dies (快速换线/快速换模) •SMED系统是一种能有效缩短产品切换 时间的理论和方法
快速换线的定义和基本原理—历福史田电工
福满中国
• SMED在50年代初期起源于日本 • 在丰田企业发展起来 • Single的意思是小于10分钟(Minutes) • 最初使用在汽车制作厂,以达到快速的模
•法则六:基准不要变动。调整基准浪费时间。
•法则七:做好事前准备
•法则八:能简则简
SMED的五个步骤—五个步骤概述福田电工
福满中国
SMED的五个步骤—1 作业分析2 福区田分电内工外
福满中国
步骤一:对切换作业进行分析。 步骤二:区分内部与外部作业。 方法: •所有新的部件和工具必须在停机前运到现场 •所有换下的部件和工具应在切换结束后才进行清理和 转存 •提前准备好物料 •提前进行功能检查 •准备和使用检查表(防止遗漏琐碎的项目)
换线时间
上一料号生产直到停机
产线停机直到开机
下一工单正式生产
快速换线的定义和基本原理—换福线田定电义工案例 福满中国
案例:某拉线由A产品到B产品转换,换线具体时间如下表, 请问该拉线的换线时间是多少?
二号线首末班车换乘时间表
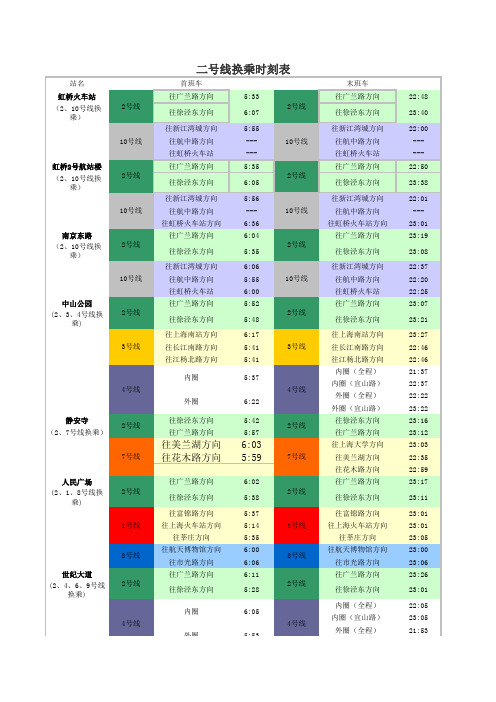
23:27 22:46 22:46 21:37 22:37 22:22 23:22 23:16 23:12 23:03 22:35 22:59 23:17
23:11
23:01 23:01 23:05 23:00 23:06 23:26
23:01
22:05 23:05 21:53
龙阳路 (2、7号线换乘)
8号线 2号线
4号线
二号线换乘时刻表
首班车
往广兰路方向 往徐泾东方向
5:33 6:07
2号线
往新江湾城方向 往航中路方向 往虹桥火车站 往广兰路方向
往徐泾东方向
5:55 ----5:35
6:05
10号线 2号线
往新江湾城方向 往航中路方向
往虹桥火车站方向 往广兰路方向
往徐泾东方向
5:56 --6:36 6:04
往徐泾东方向
往富锦路方向 往上海火车站方向
往莘庄方向 往航天博物馆方向
往市光路方向 往广兰路方向
往徐泾东方向
内圈(全程) 内圈(宜山路) 外圈(全程)
22:48
23:40
22:00 -----
22:50
23:38
22:01 ---
23:01 23:19
23:08
22:37 22:20 22:25 23:07
4号线
6号线 9号线 2号线 7号线
外圈
往东方体育中心方向 往港城路方向
往松江新城方向 往杨高中路方向
往广兰路方向 往徐泾东方向
往美兰湖方向 往花木路方向
江苏路 (2、11号线换乘)
2号线
往广兰路方向 往徐泾东方向
11号线
往安亭方向 往嘉定北方向
流水线快速换线方法

流水線快速換線方法降低能率损耗,提升效率的利器在我们的生产中常会有以下的问题:员工每天都忙碌不停,但生产任务为什么老是完不成,生产效率不能达标;按照产能计算,完成现有产量是绰绰有余!实际生产中却就不行;生产线刚刚理顺,但是要不就是这个岗位的员工离岗要不就是那条岗位的机器故障,生产线又不平衡不流畅了,经常看到员工等待、设备等待等现象;物料、配件供应不及时等等。
这些时间上的浪费,也就是说能率的损耗,影响了生产效率、延长了生产周期、降低了员工士气。
今天我们就生产线换线(品种/规格)频繁、换线时间长、能率损耗大这一不合理现象来对换线进行讨论,研讨快速换线的方法,以减少能率损耗,减少浪费来提升生产效率。
从公司的生产排程和生产计划中可以了解到,一般来说,装配课每条流水线每天至少要有4~5次以上的换线,且有的规格的雨刷数量只有几百。
而频繁的换线对生产效率有什么影响呢?其导致的人员调动、配件材料的更换及清退、机器的调试、工装治具的更换及调试、工作台面的整理、铆钉的清理更换、文件的更换及首件的制作等都将带来的时间的浪费(属于能率损耗的一部分),而时间的浪费又是影响生产效率的一个重要方面。
当然换线频繁还会导致混料等情况,会导致某些品质问题的发生。
观察我们目前换线,换线时间过长有以下几个方面的原因:1、作业员、供料员及组长对换线速度对生产效率的影响认识度不够;2、工装治具准备不足、机器故障率高,换线时调试治具、机器;3、材料准备不到位,有断线的情况;4、相关的部门、课对生产的配合度不够;5、对换线产品的人数配置、作业方法、管控要点不太清楚;6、换线前没有预料异常的发生,换线中异常处理时效太慢;7、生产线不平衡、单件产品生产时间过长;8、作业程序及规章制度没有有效地执行。
说到换线,我们先要明白什么叫换线,换线的定义就是:前一机种和后一机种的转换。
而换线时间就是指前一机种最后一个(台)产品流出到后一机种首件流出之间的时间间隔。
生产线平衡与快速换线

生产线平衡与快速换线
3、增加各作业员,只要平衡率提高了,人均产量就等 于提高了,单位产品成本也随之下降;
4、合并相关工序,重新排布生产工序,相对来讲在 作业内容较多的情况下容易拉动平衡;
5、分解作业时间较短的工序,把该工序安排到其它 工序当中去。
生产线平衡与快速换线
(件/小时) 35.0
7.0 45%
生产线平衡与快速换线
120.0 100.0
80.0 60.0 40.0 20.0
0.0 1
改善前
2
3
4
5
生产线平衡与快速换线
改善后
定员
工序
1 灌装/贴贴
2 3 4 合计
拧盖
装箱
叠纸箱/封箱/贴纸 箱贴
生产效率
人均效率
平衡率
(秒/瓶) 5.06 4.70
时间 (秒/件) 60.72 56.43 46.86
6、转换中要坚持的原则
一旦设备停止运转,作业人员绝对不要离开设备 参与外部作业转换的操作。
在外部作业转换中,模具、工具以及材料必须事 前整整齐齐地准备到设备旁边,而且模具必须事 前修理好。
在内部作业转换中,必须只拆卸和安装模具。
生产线平衡与快速换线
7、快速换线八步法
STEP 1 STEP 2 STEP 3 STEP 4 STEP 5 STEP 6 STEP 7 STEP 8
外部作业转换 : 可以在设备运转当中进行转换。
生产线平衡与快速换线
3、转换作业改善要点
✓明确区分内部作业转换和外部作业转换 ✓将内部作业转换B转化为外部作业转换 ✓缩短内部作业转换C ✓缩短调整作业D ✓缩短外部作业转换A
生产线作业评价基准(修订)
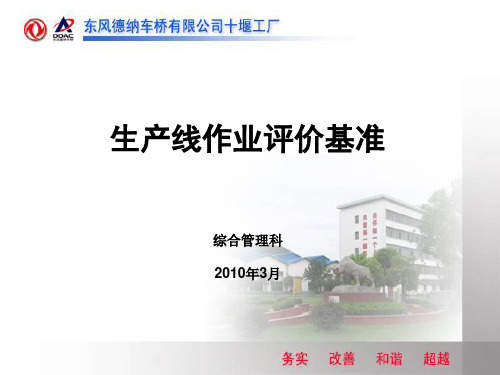
NPW人机工程-姿势负荷评价标准
动作 图型 姿势等级 对应工序等级 4-5级 3h>T≥0.5h/班为4级;T≥3h/班为5级 3-4级 T<3h/班为3级,T≥3h/班为4级 1-3级 步行时间<3h/班为2 级,≥3h/班为3级 弯腰大 下蹲 扭大 后仰 手在头上 后退 低头 弯腰中 屈腿坐 扭中 手在头前 升降 歩行 好姿势
改善思路:工位器具改善,零件在工位器具中定置定放
12、质量保证:
评价内容:除始业检查外,中间检查次数单班超4次的工序数/工序总数
改善思路:改善作业方法,贯彻执行标准作业
13、防错设置:
评价内容:设置防错装置的工序数/工序总数
改善思路:对易发不良工序进行防呆设置
14、工序间在制品:
评价内容:工序中平均在制品数量(A类产品)
10、工位器具放置:
评价内容:工位器具1PITCH化率=100%工位数/总工位数 1 PITCH化率=1工位内存放零件种数/1工位内需装配〔使用〕的所有零件种数
改善思路:工位器具定置定放
11、零件放置:
评价内容:露脸率=100%的工位数/总工位数
1露脸率:生产线上1个工位(1PITCH)从零件取出口可直接取到的零件与使用的 所有零件的比率。(零件线边直取零件数/使用零件总数)
推进思路:减少换刀频次,降低每次换刀时间。
9、工位器具:
定义:广义上指工具、检具、吊具、辅具、零件料架、滑道等的统称 评价内容:无安全隐患、防磕碰、填充率70%以上、SNP消耗时间2小时内、取放便利 SNP:一件工位器具中可放的零件件数
改善思路:消除安全隐患,设置防磕碰装置,零件料架小型化、符合人机 工程学原理。
(2)作业负荷评价:搬运重量和操作力、以及每班的搬运总量和总的操作力来评价
SOP的执行与生产排线换线技巧
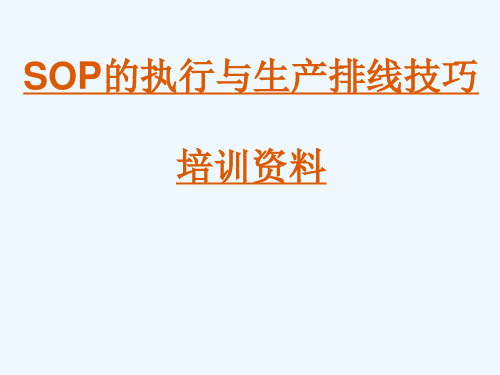
也可以分为:主料(电池、胶壳)、辅助材料(海棉胶、青 稞纸)、包装材料;
放在车间的物料,规划好放置区域;原材料区、半成品区、 成品区;待检验区、已检验合格区、不合格待返工区;定期 查看,防止遗失;或明明在车间,却找不到;(或者是按订 单分区)
物料状态标识清楚(名称、规格型号、数量、被加工状态、 是否为合格品)、订单号;
培训场合:现场岗位、开早会、专门会议; 培训考核方式:口头、书面、实际操作;
如何培训新员工
由助拉/拉长培训新员工;先教她看作业指导书;并 手把手教她操作;
把她放在一名有责任心、比较熟练、平时表现良好 的老(优秀)员工旁边上班,以“老”带“新”; 好师傅才会带出好徒弟; 安排新员工先做简单的工作;不要期望马上就能达 到熟练员工水平; 新员工犯了错、速度跟不上时,不要严厉指责。多 鼓励、多教导;
工序管理
助拉/拉长每道工序都要会操作,才能教新员工;必 须熟悉每道工序用什么设备、夹具/治具、原材料 (如胶件)、辅助材料(如海棉胶、标贴类)、包 材。 须熟悉每道工序的标准每小时产量/每天产量;
知道哪道工序是瓶颈工序(工时最长的工序) 以上信息在作业指导书里可以体现;
如何消除生产线堆“机”
早会管理
开早会时间:上班铃声响准时开会;
员工的站立姿势:列好队伍后,双手背在后
面; 拉长先点名;登记缺席人数; 若需讲产品问题,拉长提前准备好产品样品; 拿着产品给员工讲,印象才深刻、直观;
早会管理
通常,开会内容如下: 总结昨天的产量、质量达标情况及改善对策;简单 宣讲今日的工作安排;
拉长按排各工序的人员坐到指定的工序,投放工具及物料, 各工序熟悉完SOP后,拉长排线指导作业; 并随即跟踪制作3个首件(首件完成的时间为10到15分钟, 随即排线完成),送首件给IPQC检验; 首检合格后,才开始大量生产;
SMT换线时间改善

2 設備調試時間過長
協調由生技進行技朮和作 業協助
准備不足﹐工治具到 換線前確認工治具和各換
3 位不及時
線責任人員
部分線內作業時間太 合理調配人力協助(目檢員 4 長(擦鋼板﹑上/對料) ﹑IPQC)
5 作業流程隨意不規范 制定作業標准規范和流程
6 人員意思和方法不佳 進行集中宣導和訓練說明
4.1 作业进程指导
印刷參數必須與SOP規定的參數一致
和軌道寬度 OK后填寫V
OK后填寫V
OK后填寫V
1.確認印刷無偏移﹑短路﹑少錫等不良 2.連續確認三片以上
OK后填寫V
要求
記錄方式
結果
程式名稱必須與SOP規定的程式名稱一致
填寫程式名
1.寬度比PCB寬0.5~1mm
填寫PCB寬度
2.需保証進出板順暢 1.PCB支撐須良好﹑穩定﹑基板不會被頂起或懸空
SMT Line
A
印刷机
H1
H2
G1
OQ
完成高速机扫描上料﹑对料
P 印刷机作业员 A 操作 O 换料员 V 炉前检验员
L 线长 Q IPQC M 生技 R 测炉温人员
V 回流焊
换线进程示意图(2)
洗换钢板
P
Q
A
印刷机
H1
O
P 印刷机作业员 A 操作 O 换料员 V 炉前检验员
H2
G1
L 线长 Q IPQC M 生技 R 测炉温人员
4 吸嘴確認
5 MARK 辨識位置確認
6 元件位置/極性確認
Reflow 換線人員簽名:
序號
檢查項目
1 Reflow 溫度設定
2 profile 規格確認
换线时间kpi

换线时间kpi摘要:一、引言二、换线时间的定义和计算方法三、换线时间KPI 的重要性四、如何提高换线时间KPI五、总结正文:换线时间KPI 是制造业生产管理中的一个关键性能指标,衡量了生产过程中换线操作的效率。
换线时间是指在生产过程中,从一个产品切换到另一个产品所需的时间。
准确计算和控制换线时间对于提高生产效率、降低生产成本具有重要意义。
一、引言在现代制造业中,为了满足市场对多样化产品的需求,生产线上经常需要更换产品型号。
换线操作是生产过程中的一个重要环节,直接影响到生产效率、生产成本和产品质量。
因此,对换线时间进行科学管理和优化具有十分重要的意义。
二、换线时间的定义和计算方法换线时间通常包括准备时间、操作时间和清理时间三部分。
1.准备时间:为换线操作所做的准备工作所花费的时间,如检查设备、调整参数等。
2.操作时间:实际进行换线操作所花费的时间,如拆卸旧产品、安装新产品等。
3.清理时间:换线操作完成后,对现场进行清理所花费的时间,如清理废料、整理工具等。
换线时间的计算公式为:换线时间= 准备时间+ 操作时间+ 清理时间三、换线时间KPI 的重要性换线时间KPI 是衡量生产过程中换线操作效率的重要指标,对于企业提高生产效率、降低生产成本具有重要意义。
1.提高生产效率:缩短换线时间可以增加生产线的有效运行时间,从而提高生产效率。
2.降低生产成本:换线时间短,可以减少因换线操作造成的生产损失,降低生产成本。
3.提高产品质量:缩短换线时间有助于减少生产过程中的停顿,保证产品质量的稳定。
四、如何提高换线时间KPI1.优化换线流程:对换线操作流程进行优化,减少不必要的步骤,提高操作效率。
2.提高员工技能:培训员工熟练掌握换线操作技能,提高操作速度和质量。
3.引入自动化设备:采用自动化设备进行换线操作,降低人工操作的复杂度和时间。
4.合理安排生产计划:合理安排生产计划,减少频繁换线,降低换线时间KPI。
五、总结换线时间KPI 是制造业生产管理中的一个关键性能指标,对于提高生产效率、降低生产成本具有重要意义。
- 1、下载文档前请自行甄别文档内容的完整性,平台不提供额外的编辑、内容补充、找答案等附加服务。
- 2、"仅部分预览"的文档,不可在线预览部分如存在完整性等问题,可反馈申请退款(可完整预览的文档不适用该条件!)。
- 3、如文档侵犯您的权益,请联系客服反馈,我们会尽快为您处理(人工客服工作时间:9:00-18:30)。
SMT换线时间分析及改善报告一、目的:为了查明SMT换线时间超标(30分钟/次)的根本原因,并为时间改善找到更明确的方向和需要改善的节点,从而减少SMT损耗时间,提高生产效率。
二、目前SMT换线时间和次数现状调查:(2015年20周至22周)2.1、SMT总体平均换线时间=40分钟2.2、SMT换线时间和换线次数:(时间:分钟)2.3、通过三周的数据分析结果,我司SMT目前换线现状如下:1)平均每一次换线时间40分钟左右。
(公司暂定平均换线标准时间:45分钟/次)2)平均每周换线总次数32次。
3)平均每周换线损失总时间:1280分钟 = 21.3H。
4)平均每天换线损失总时间:21.3H/6天= 3.6H。
5)平均每天每条线损失时间: 3.6H/3条 = 1.2H。
按每天生产11H,占了总生产时间:1.2/11=11%.6)平均每天每条线转线次数:32次/6天/3条=2次。
2.4、目标换线时间因是:30分钟/次,所以我们参考以下“第三点”内容共同学习SMED技术,从“第四点”开始结果公司实际情况,进行“SMT换线时间研究和改善”。
三、学习SMED 技术---为了更快让大家撑握快速换线知识,更能了解第四部份内容流水线生产快速换线SMED技术(以下摘自网络,与大家分享,共学之!)在我们的生产中常会有以下的问题:员工每天都忙碌不停,但生产任务为什么老是完不成,生产效率不能达标;按照产能计算,完成现有产量是绰绰有余!实际生产中却就不行;生产线刚刚理顺,但是要不就是这个岗位的员工离岗要不就是那条岗位的机器故障,生产线又不平衡不流畅了,经常看到员工等待、设备等待等现象;物料、配件供应不及时等等。
这些时间上的浪费,也就是说能率的损耗,影响了生产效率、延长了生产周期、降低了员工士气。
今天我们就生产线换线(品种/规格)频繁、换线时间长、能率损耗大这一不合理现象来对换线进行讨论,研讨快速换线的方法,以减少能率损耗,减少浪费来提升生产效率。
从公司的生产排程和生产计划中可以了解到,一般来说,装配课每条流水线每天至少要有4~5次以上的换线,且有的规格的雨刷数量只有几百。
而频繁的换线对生产效率有什么影响呢?其导致的人员调动、配件材料的更换及清退、机器的调试、工装治具的更换及调试、工作台面的整理、铆钉的清理更换、文件的更换及首件的制作等都将带来的时间的浪费(属于能率损耗的一部分),而时间的浪费又是影响生产效率的一个重要方面。
当然换线频繁还会导致混料等情况,会导致某些品质问题的发生。
观察我们目前换线,换线时间过长有以下几个方面的原因:1、作业员、供料员及组长对换线速度对生产效率的影响认识度不够;2、工装治具准备不足、机器故障率高,换线时调试治具、机器;3、材料准备不到位,有断线的情况;4、相关的部门、课对生产的配合度不够;5、对换线产品的人数配置、作业方法、管控要点不太清楚;6、换线前没有预料异常的发生,时效太慢换线中异常处理;7、生产线不平衡、单件产品生产时间过长;8、作业程序及规章制度没有有效地执行。
说到换线,我们先要明白什么叫换线,换线的定义就是:前一机种和后一机种的转换。
而换线时间就是指前一机种最后一个(台)产品流出到后一机种首件流出之间的时间间隔。
而换线时间包括两部分时间即外部时间和内部时间。
内部时间是指停机过程中作业仍应该继续(如取放工具),而外部时间是指机器仍在运转过程中或是刚刚重启动之后可以进行的作业(如第一次检测)。
从上述可知,换线慢的根本原因在于:1、换线的外部时间与内部时间划分不清;2、内部换线时间过长。
而解决换线慢、换线时间过长的方法就是:1)划分清楚内外部时间并减少内部时间;2)将内部作业转移到外部并尽可能地缩短外部时间。
这就要求我们在换线前要做好换线前的准备工作。
如何才能解决换线慢,提升换线速度呢?而今在工业工程界最流行的换线方法就是“SMED”法,即“六十秒即时换线法”( Single Minute Exchange of Dies)。
以缩短换线时间、提升生产力为目的而推行快速换线。
会有什么样的好处呢?快速换线的好处有:1、缩小批量大小;2、减少加工中的存货;3、缩短备货时间;4、提高生产灵活性;5、提高品质;6、减少浪费提高产能;7、提高机器设备的稼动率。
这些都是显而易见的,也是我们所在寻求的目标。
应该如何导入SMED法?我们可以分5个步骤导入SMED,运用系统的方法缩短换线时间。
第一步:观察当前的流程,第二步:区分内部和外部的要素,第三步:将内部作业转移到外部,第四步: 减少内部工作,第五步: 减少外部作业。
导入过程中要做哪些工作,要注意哪些呢?第一步:成立快速换线推行小组,制定推行计划和日程。
小组成员由生技课长、装配课长、装配组长,装配技术员、物料员、修理、IE、PE、IPQC等组成,小组组长可由IE担当。
换线小组每天举行换线会议,检讨换线状况,会议由小组组长主导,小组成员共同讨论换线中发生的问题并提出改善对策;第二步:选择线别,量测并记录换线时间。
记录下所有的动作,以发现任何问题或是任何机会,必要的地方通过录像记录活动;第三步:资料分析,改善对策拟订。
分析第二步收集到的当前数据,确定在停机前后有哪些事情可以做,将内外部时间分开来,对内部的活动进行严格的检查分析、考察第二步发现的机会、集思广益地讨论新的办法和创意、工具标准化、确保人与物在正确的时间配置到正确的位置,并制作“工具更换流程记录”“供料流程记录”等以供小组成员使用;第四步:对策执行,量测并记录对策执行后的换线时间。
制定换线流程及推行细则等相关的文件资料,将改善对策试运行到换线中,对比第二步并记录对策执行后的换线时间及相关的问题点等事项;第五步:效果追踪、验证,对策检讨,标准化制定。
对改善后的换线方法进行数据化的分析、检讨,验证、确认改善效果,直到达到标准换线的时间;第六步:标准化实施,所有生产线水平化展开。
围绕新的方法提供培训,将最后的标准化换线实施于观测线,并以点带面地展开于其它线,同时完善相关资料;第七步:标准化维持,持续改善。
对流程实行监控,不间断地汇报换线部分的业绩表现。
在推行过程中要订定标准换线时间,换线前后两款产品的节拍时间或者说标准工时不同、平衡率不同都会影响换线时间。
一般来说,同一系列,前一规格产品的节拍时间比后一款产品的节拍时间短,那么换线时间要稍长(比如4个点换成8个点同8个点换成4个点相比);不同系列的产品比同一系列的产品换线时间要长(比如408换成428同408的8个点换成6个点),平衡率高的换成平衡率低的比平衡率低换成平衡率高的切换要快。
在这以我们现有的雨刷组装为例,大致说说流水线的切换技法及注意点,从文件资料及人、机、料、法、环管控方面入手,首先,组长要清楚知道本组明天(或当天)装配哪几款产品?每一款产品相应的文件资料是否齐备?每一款组装需要多少人作业,人员如何调配?相应岗位作业员对作业方法是否清楚、熟练?机器设备是否够用且全部可动?模具是否齐备且可用?使用到的工装治具有哪些,是否已调试好且可用?物料是否已全部配齐,数量是否准确?放置的位置是否清楚?每一款产品的生产数量是多少,需装配多长时间?何时开始供料最适合,供料的先后岗位是否清楚?如何制作首件及填写《首检验报告》?换线过程,前后工序人员如何更有效地配合以尽快完成上一款装配?余料如何管控并清退出现场?周转箱、半成品的处理?如何及时地发现、反馈、处理异常等;然后,做好相关的准备工作,必要时需寻求上司支援;最后,在生产、换线过程中,统筹调配相关资源,达到快速切换流水线。
当然,快速换线需依赖于相关的基础工作:良好的6S维护、生产线的平衡、员工熟练的作业技能、供料员对产品和工艺的熟悉及积极的工作心态、现场管理者的调控统筹能力、机器设备的日常保养和点检、工装设备的日常管理、相关部门的配合、相关管理规定的执行力度等。
改善是点滴的积累,持续不断的改善才能不断地优化生产系统,以达到提高生产效率和降低成本的目的。
四、SMT换线时间研究分析:4.1、换线时间定义:从上一个产品生产结束切换到下一个合格产品生产出来所需要的时间。
SMT换线时间定义:从上一个工单最后一件产品SMT贴装结束﹐到下一个工单第一件产品炉前检验OK并开始正式生产到炉前所花费的工时。
即SMT产线因换线而没有产品产出的时间。
必须停机才能进行的切换以及为保证质量进行的调整、检查等占用的切换时间。
如:SMT机上飞达、IPQC对料、工程调机、首件确认等。
4.3 SMT换线时间现状分析:1)现状:平均每次换线时间:45分钟。
2)目标:平均每次换线时间:30分钟。
3)提升值:15分钟/次。
平均一周换线32次,则节省机器换线时间:32*15=480分钟=8H。
4)节省人工工时:8H*15人=120H/周=120*20=2400元。
5)提高机器产值:8H*8000*0.02=1200元/周。
(SMT机器平均每小8000点)。
6)一年节省资金:打一年上43周(300天),则(2400+1200)*43 = 154800元/年。
五、快速换线改善的方向:主要就是将内部转化为外部,如增加ON LINE 离线作业(事前准备)。
通过优化内外部作业时间,进行时间压缩,如单人操作转化为多人作业。
初期 1 2 3 内部与外部未区分开区分外部与内部内部转化为外部内部与外部优化操作交替作业六、SMT换线改善的具体方法:6.1、明确内部、外部作业时间:建立标准作业规范,分清内外部作业时间,严格执行内外部作业时间,绝不允许内部作业时间用来做外部作业。
6.2、将内部转化为外部:ON LINE作业,并增加OFF LINE作业:一般的换线动作是一人操作,逐机更换.如此一步等一步,时间非常漫长,若可,非机器上作业事项提前准备OK则无形中亦提前许多再变更多人同时进行换线,亦可达到同时到达之效果.--- 平行作业:指两人以上共同切换作业。
6.3、作好事前准备:如提前备料等。
6.4、手动、脚勿动:主要靠手,减少脚的走动、移动。
6.5、使用专用的设备:如飞达车、SMT料车。
七、结论:SMT换线时间损失的原因:1、混淆了内部和外部的切换时间:外部时间占用了内部时间。
如:等SMT停机后才来找钢网,搅拌锡膏。
将外部时间转成内部时间。
2、太长的调试时间:飞达未校验,过多的重新调坐标时间。
---建议购买飞达校正仪。
(见图)3、未进行优化操作,有时找料要在一大胶盆中翻找,浪费时间:如利用飞达表进行备料、增加上料架,按料站顺序排好并编好号。
---建议购买料架。
(见后图)4、未平行作业:如目前SMT操作员一个人上二台机器,上完一台,再上另一台。
如果SMT拉长或作业员同时与操作员上料,则可同时上两台。
技术员与工程师同时调机,则两台机一起调,节省时间。