冶金概论1
冶金概论[1]
![冶金概论[1]](https://img.taocdn.com/s3/m/1ba1e6b4b14e852458fb57d1.png)
结构钢 工具钢
特殊性能钢
PPT文档演模板
冶金概论[1]
(3)铁合金:
铁与一种或几种元素组成的中间合金,用于炼钢脱氧及合金化
PPT文档演模板
冶金概论[1]
2)钢铁副产品
(1)炉渣 炉料冶炼过程中不能进到金属中的S-化物,O-化物
等形成的熔融体,主要成分: CaO,MgO,SiO2, Al2O3,MnO,FeO, P2O5, CaS 等。
PPT文档演模板
冶金概论[1]
3)我国能源使用情况
据资料统计,我国的能源开采回收率 只有32%, 能源加工、转换和储存的 效率为70.3%, 终端能源利用率平均为 42%, 这表示所生产能源中得到利用 的只占29%。
PPT文档演模板
冶金概论[1]
4)我国单位产值能耗
据资料统计,我国每百万美元的单位 产 值 能 耗 为 1172 吨 油 当 量 , 远 高 于 日 本(162)、德国(229)、英国(292) 和美国(384)等发达国家的数值,也 远高于世界平均水平(397)。
PPT文档演模板
冶金概论[1]
中国冶金的辉煌历史
PPT文档演模板
冶金概论[1]
1.4 现代冶金过程—冶炼过程
PPT文档演模板
冶金概论[1]
现代冶金过程—轧钢过程
PPT文档演模板
冶金概论[1]
1.5 钢铁产品及副产品
1)钢铁冶炼产品
(1)生铁:
炼钢生铁[Si]≤1.25%
铁与C、Si、Mn、P、S组成的合金,主要由高炉生产
• 矿产资源人均占有量只有世界平均水平的 58%,排世界第53位;
PPT文档演模板
冶金概论[1]
在13种主要金属原料的地区分布前五位排名上,我 国除锡(占14.8%)和钼(占6.0%)外,其余都榜上 无名。
冶金概论1
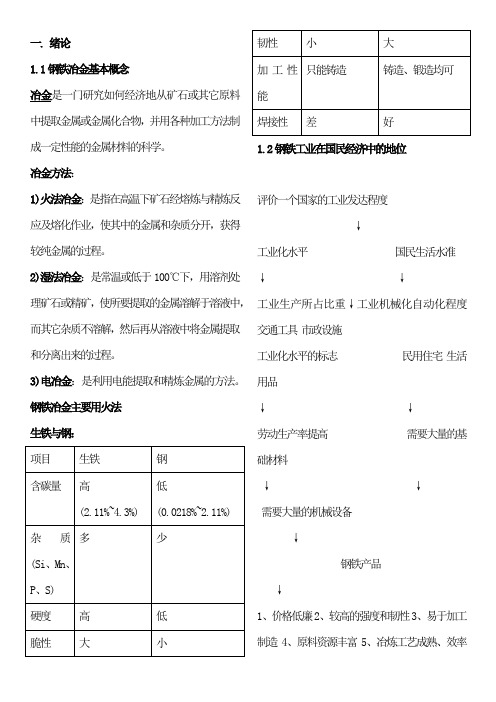
一. 绪论1.1钢铁冶金基本概念冶金是一门研究如何经济地从矿石或其它原料中提取金属或金属化合物,并用各种加工方法制成一定性能的金属材料的科学。
冶金方法:1)火法冶金:是指在高温下矿石经熔炼与精炼反应及熔化作业,使其中的金属和杂质分开,获得较纯金属的过程。
2)湿法冶金:是常温或低于100℃下,用溶剂处理矿石或精矿,使所要提取的金属溶解于溶液中,而其它杂质不溶解,然后再从溶液中将金属提取和分离出来的过程。
3)电冶金:是利用电能提取和精炼金属的方法。
钢铁冶金主要用火法生铁与钢:1.2钢铁工业在国民经济中的地位评价一个国家的工业发达程度↓工业化水平国民生活水准↓↓工业生产所占比重↓工业机械化自动化程度交通工具市政设施工业化水平的标志民用住宅生活用品↓↓劳动生产率提高需要大量的基础材料↓↓需要大量的机械设备↓钢铁产品↓1、价格低廉2、较高的强度和韧性3、易于加工制造4、原料资源丰富5、冶炼工艺成熟、效率高1.3钢铁工业的发展炼钢技术的发展方面:⑴氧气底吹空气转炉法和顶底复合吹炼法⑵引进真空技术,采用各种真空冶炼和炉外精炼技术,改善钢的品质,扩大产品品种⑶连铸技术,使炼钢工艺连续化⑷大容量、超高功率的炼钢炉子,提高生产率,降低成本。
发展趋势:扩大高炉容积,原料预处理,发展精料技术,采用富氧鼓风、脱湿鼓风和喷吹燃料等技术,提高产量,降低焦比;利用皮带运料,炉前除尘等先进设备和仪器,改善了人工劳动条件。
钢铁生产用能源:主要:煤炭,燃料油,天然气,电力等节能途径:改进生产设备及生产工艺、降低能源损失,减少生产工序、回收利用散失热量、加强企业能源管理,推进技术研究与创新。
1.4钢铁生产基本流程矿山→烧铁厂球团厂→烧结厂球团厂煤矿→焦化厂→→焦炭﹜→高炉→铁水→1、铁水→铁水预处理→转炉炼钢→钢水精炼→连铸→轧钢2、废钢→电弧炉→钢水精炼→连铸→轧钢二. 高炉炼铁用原料2.1概述地壳中的Fe元素居第四位,占4.2%,由于以富集状态存在,故有开采价值。
冶金概论第一章

第一章、概述1.1. 金属及其分类1.1.1.金属:通常把元素周期表中具有光亮的金属光泽,很高的导热、导电性及良好的延展加工性的化学元素称为金属有色轻金属黑色金属稀有轻金属1.1.2.分类有色重金属稀有高熔点金属有色金属稀有金属稀有分散性金属贵金属稀土金属稀有放射性金属1.2. 冶金和冶金方法1.2.1. 冶金1、定义:冶金是一门研究如何经济地从矿石或精矿或其他原料中提取金属或金属化合物,并用各种加工方法制备成具有一定性能的金属材料科学2、广义的冶金:包括矿石的开采、选矿、冶炼、金属加工3、狭义的冶金:指矿石或精矿的冶炼,即提取冶金4、冶金:提取冶金、物理冶金5、提取冶金:从矿石或精矿提取金属(包括金属化合物)的生产过程称为提取冶金,也称为化学冶金;6、物理冶金:加工制备具有一定性能的金属或合金材料7、5、冶金学(过程冶金学):它研究火法冶炼、湿法提取或电化学沉积等过程的原理、流程、工艺及设备1.2.2. 二、冶金方法1、火法冶金2、(1)定义:它是指在高温下矿石或精矿经熔炼与精炼反应及熔化作业,使其中金属与脉石和杂质分开,获得较纯金属的过程。
3、(2)过程:原料准备、熔炼、精炼4、湿法冶金5、定义:它是在常温(或低于100℃)常压或高温(100℃~300℃)高压下,用溶剂处理矿石或精矿,使所要提取的金属溶解于溶液中,而其它杂质不溶解,然后再从溶液中将金属提取和分离出来的过程。
也称为水法冶金。
6、过程:浸出、分离、富集、提取等7、电冶金8、定义:它是利用电能提取和精炼金属的方法9、分类:10、①电热冶金:利用电能转化为热能,在高温下提炼金属,本质与火法冶金相同11、②电化学冶金:用电化学反应使金属从含金属的盐类的水溶液或熔体中析出12、(3)过程:水溶液电解、熔盐电解等1.3. 冶金工艺流程和冶金过程1.3.1. 工艺流程图1、设备连接图:表示冶炼厂主要设备之间的联系2、原则流程图:表示各个阶段作业间联系3、数质量流程图:表示各阶段作业获得产物的数量和质量情况1.3.2. 冶金过程1、焙烧:是指将矿石或精矿置于适当气氛下,加热至低于它们的熔点温度,发生氧化、还原或其他化学变化的过程。
冶金概论1
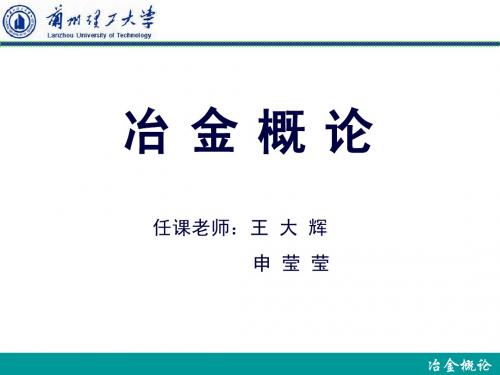
总学时:32
冶金概论
主要内容
1
2 绪论
采矿与选矿
钢铁冶金
3
4 5
有色冶金
冶金过程环境保护 冶金概论
欢迎大家走进冶金行列!
首问:为什么选择冶金专业?
答曰:冶金是国计民生中最基础的行业之一 或答:属于重要原材料工业,是经济发展物质基础 再答:………
再再答:72行,行行都重要
不管做什么,都能在所从事的那一行做得好-北京大学
叠铸技术 在战国和秦汉时期逐渐形成了一次铸造数十件器物 的层叠铸造技术,大大提高了铸造效率,减少了金属的 消耗。 胆铜法 始于汉代,在宋代大规模使用的湿法冶铜技术,是世 界上最早的湿法冶金技术。
白铜
中国是白铜的故乡,《汉书》中已有“白铜”的记载。
冶金概论
采矿和深井技术 大冶铜绿山古矿冶遗址的发掘,展示了商周以来规模 宏大的地下采矿场面。
100℃;在高压下,也不超过300℃。
冶金过程:浸出、净化、金属还原
浸出:用适当的溶剂处理矿石,使要提取的金属成为离子进入
溶液中,而主要的杂质矿物不溶解,通过过滤,分理出固相杂 质。
净化:除去与要提取金属一起进入溶液中的金属或非金属杂质
的过程为净化。
金属还原:用置换或电沉积的方法将要提取金属还原。
冶金概论
冶金概论
冶金概论
冶金概论
冶金概论
冶金概论
冶金概论
冶金技术革新
改革的动因:源于对现状不满钢铁工业的一些现象 ● 忽大忽小 矿石磨细再烧结成“块” 钢锭钢坯做大再压小
● 反应过量 还原过头(BF)-氧化过头(BOF)-精炼调整(LF\RH\CAS-OB) ● 忽冷忽热 焦炭和烧结先冷却再加热 连铸坯的保温
冶金工程概论
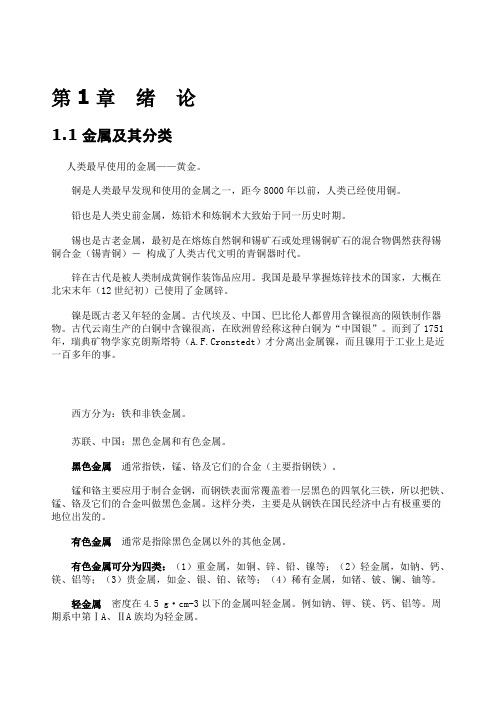
第1章绪论1.1金属及其分类人类最早使用的金属——黄金。
铜是人类最早发现和使用的金属之一,距今8000年以前,人类已经使用铜。
铅也是人类史前金属,炼铅术和炼铜术大致始于同一历史时期。
锡也是古老金属,最初是在熔炼自然铜和锡矿石或处理锡铜矿石的混合物偶然获得锡铜合金(锡青铜)-构成了人类古代文明的青铜器时代。
锌在古代是被人类制成黄铜作装饰品应用。
我国是最早掌握炼锌技术的国家,大概在北宋末年(12世纪初)已使用了金属锌。
镍是既古老又年轻的金属。
古代埃及、中国、巴比伦人都曾用含镍很高的陨铁制作器物。
古代云南生产的白铜中含镍很高,在欧洲曾经称这种白铜为“中国银”。
而到了1751年,瑞典矿物学家克朗斯塔特(A.F.Cronstedt)才分离出金属镍,而且镍用于工业上是近一百多年的事。
西方分为:铁和非铁金属。
苏联、中国:黑色金属和有色金属。
黑色金属通常指铁,锰、铬及它们的合金(主要指钢铁)。
锰和铬主要应用于制合金钢,而钢铁表面常覆盖着一层黑色的四氧化三铁,所以把铁、锰、铬及它们的合金叫做黑色金属。
这样分类,主要是从钢铁在国民经济中占有极重要的地位出发的。
有色金属通常是指除黑色金属以外的其他金属。
有色金属可分为四类:(1)重金属,如铜、锌、铅、镍等;(2)轻金属,如钠、钙、镁、铝等;(3)贵金属,如金、银、铂、铱等;(4)稀有金属,如锗、铍、镧、铀等。
轻金属密度在4.5 g·cm-3以下的金属叫轻金属。
例如钠、钾、镁、钙、铝等。
周期系中第ⅠA、ⅡA族均为轻金属。
重金属一般是指密度在4.5 g·cm-3以上的金属叫重金属。
例如铜、锌、钻、镍、钨、钼、锑、铋、铅、锡、镉、汞等,过渡元素大都属于重金属。
贵金属贵金属通常是指金、银和铂族元素。
这些金属在地壳中含量较少,不易开采,价格较贵,所以叫贵金属。
这些金属对氧和其他试剂较稳定,金、银常用来制造装饰品和硬币。
稀有金属稀有金属通常指在自然界中含量较少或分布稀散的金属。
冶金概论(1)
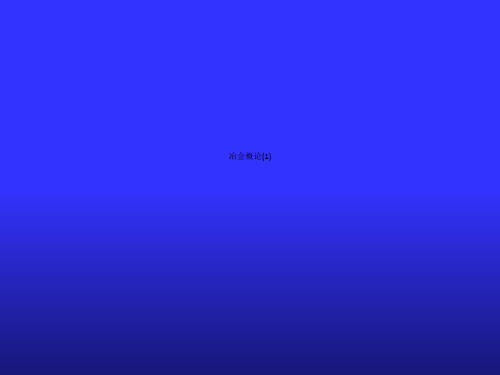
16
1.6 钢铁资源与能耗
1)我国主要自然资源现状
• 我国的四类基本资源中,耕地、淡水人均 占有量只分别相当于世界平均水平的1/3 和1/4,森林和草地只分别相当于世界平 均水平的1/7和1/3;
• 能源资源中,煤炭、石油和天然气的人均 探明储量分别只有世界平均水平的1/2、 1/10和1/20。
24
7)钢铁工业在降低能耗方面的成绩
近20年来钢铁工业在降低资源消耗 和环境负荷方面已作出很大努力并取 得显著的成绩,大幅降低了吨钢综合 能耗和大中型企业吨钢可比能耗。
25
例如吨钢综合能耗从1980年的2040公斤标煤降 低到1999年的1083公斤标煤,大中型企业吨钢可 比能耗从1980年的1285公斤标煤降低到1999年的 833.0公斤标煤。
41
3)中国钢铁工业实施循环经济的战略构想
金属材料的发现开创了人类物质文明的新 纪元,几千年来大规模的应用又加速了人类 社会发展的历史进程,金属材料和其它材料 一起构成了人类社会的四大支柱之一。但是 随着地球表壳资源的日益贫化,金属矿产资 源已迅速枯竭。据专家估计,地球上金属矿 产的开采只能维持100至300年,其中,铁 只能开采100——160年,而钛、铜、银的 开采将不足50年。
19
3)我国能源使用情况
据资料统计,我国的能源开采回收率 只有32%, 能源加工、转换和储存的 效率为70.3%, 终端能源利用率平均为 42%, 这表示所生产能源中得到利用 的只占29%。
20
4)我国单位产值能耗
据资料统计,我国每百万美元的单位 产 值 能 耗 为 1172 吨 油 当 量 , 远 高 于 日 本(162)、德国(229)、英国(292) 和美国(384)等发达国家的数值,也 远高于世界平均水平(397)。
冶金概论考试复习(睿子)
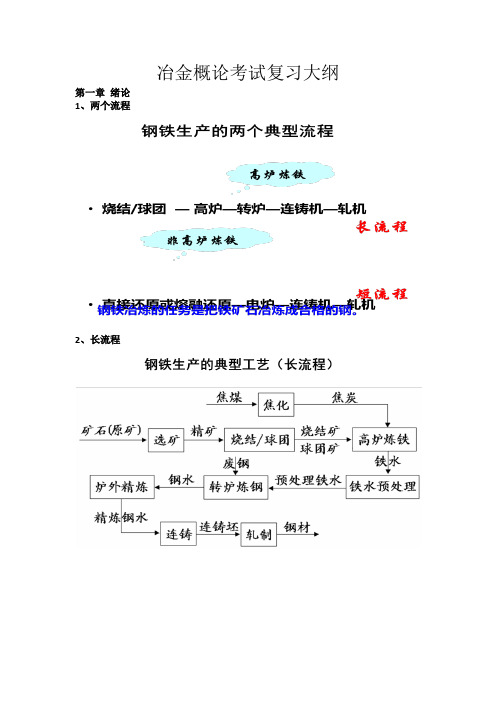
冶金概论考试复习大纲第一章绪论1、两个流程2、长流程第二章高炉炼铁1、铁矿石有哪几种2、有害元素有什么危害有益元素:Mn,Cr,Ni,V,Ti,Nb及稀有元素等改善钢铁质量。
有害元素:S,P,As,Cu等易还原进入生铁,对钢形成危害。
K,Na,Zn,Pb,F等虽不进入生铁,但①易破坏炉衬等;②炉内易挥发,循环积累造成结瘤事故;③污染环境。
3、粒度要求书P10一般入炉矿石的粒度为8~35mm。
小于5mm称为粉末,不能直接入炉。
4、燃料成分以及作用(焦炭及溶剂)焦炭成分作用:起发热剂、还原剂及料柱骨架作用。
溶剂成分:1、碱性—石灰石,白云石等2、酸性—硅石等作用:为去除矿石中的脉石与焦炭中的灰分(它们的主要成分为酸性氧化物,且熔点较高,在高炉冶炼条件下很难熔化)加入一定数量的助熔剂(简称熔剂)。
5、高炉结构(填)6、高炉炉内炉料状况及反应(记住)7、填空用CO和H2还原铁氧化物,生成CO2和H2O还原反应叫间接还原。
用CO作还原剂的还原反应主要在高炉内小于800℃的区域进行。
用H2作还原剂的还原反应主要在高炉内800~1100℃的区域进行。
8、炉渣作用(1)分离渣铁,具有良好的流动性,能顺利排出炉外。
(2)具有足够的脱硫能力,尽可能降低生铁含硫量,保证冶炼出合格的生铁。
(3)具有调整生铁成分,保证生铁质量的作用。
(4)保护炉衬,具有较高熔点的炉渣,易附着于炉衬上,形成“渣皮”,保护炉衬,维持生产。
9、熔料运动怎样下降(空间因素力学因素)炉料在炉内下降的基本条件:高炉内不断形成促使炉料下降的自由空间。
形成炉料下降的自由空间的因素焦炭在风口前燃烧生成煤气。
炉料中的碳素参加直接还原。
炉料在下降过程中重新排列、压紧并熔化成液相,体积缩小。
定时放出渣铁。
空间因素(原因)燃料燃烧和消耗、炉料的熔化和渣、铁的周期性排出是炉料下降的主要因素。
除此以外,直接还原和渗碳引起的碳素溶解损失、炉料下降过程中小块充填于大块之间引起的体积收缩。
有色冶金概论-第1章 绪论
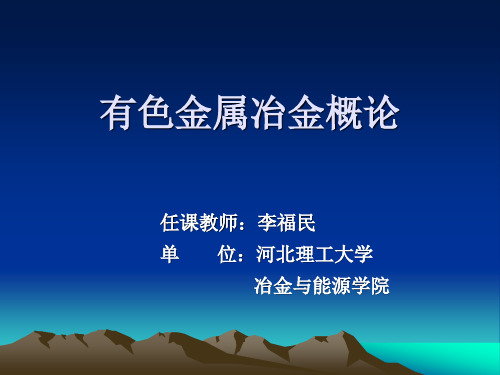
第五部分:金银冶金(10学时 学时) 第五部分:金银冶金(10学时)
• 学习目的和要求: 学习目的和要求: 通过对本部分的学习,应了解混汞法提取金银的工艺、基 本原理;熟悉金银电解精炼的方法;掌握氰化法提取金银 的工艺、基本原理。 • 教学内容: 教学内容: 从金银的性质、用途、及提取金银的原料入手,介绍混汞 法、氰化法提取金银的工艺、基本原理;介绍金银电解精 炼的工艺、基本原理、主要设备及主要技术经济指标的影 响因素。 • 重点和难点: 重点和难点: 氰化法提取金银工艺、基本原理;金银电解精炼的方法。
1.1.2 金属的分类
• 西方:铁(Ferrous Metal); 西方: ); • 非铁金属( 非铁金属(Non-Ferrous Metal)。 )。 • 苏联、中国:黑色金属和有色金属。 苏联、中国:黑色金属和有色金属。 • 黑色金属:通常指铁、锰、铬及它们的合金(主要指 黑色金属:通常指铁、 铬及它们的合金( 钢铁)。锰和铬主要应用于制合金钢, )。锰和铬主要应用于制合金钢 钢铁)。锰和铬主要应用于制合金钢,而钢铁表面常 覆盖着一层黑色的Fe3O4,所以把铁、锰、铬及它们 覆盖着一层黑色的 所以把铁、 的合金叫做黑色金属。这样分类, 的合金叫做黑色金属。这样分类,主要是从钢铁在国 民经济中占有极重要的地位出发的。 民经济中占有极重要的地位出发的。 • 有色金属:通常是指除黑色金属以外的其他金属。 有色金属:通常是指除黑色金属以外的其他金属。
1.1.1 人类使用金属的历史
• 锌在古代是被人类制成黄铜作装饰品应用。我国是 最早掌握炼锌技术的国家,大概在北宋末年(12世 纪初)已使用了金属锌。 • 镍是既古老又年轻的金属。古代埃及、中国、巴比 伦人都曾用含镍很高的陨铁制作器物。古代云南生 产的白铜中含镍很高,在欧洲曾经称这种白铜为 “中国银”。而到了1751年,瑞典矿物学家克朗斯 塔特(A.F. Cronstedt)才分离出金属镍,而且镍用 于工业上是近一百多年的事。
有色冶金概论
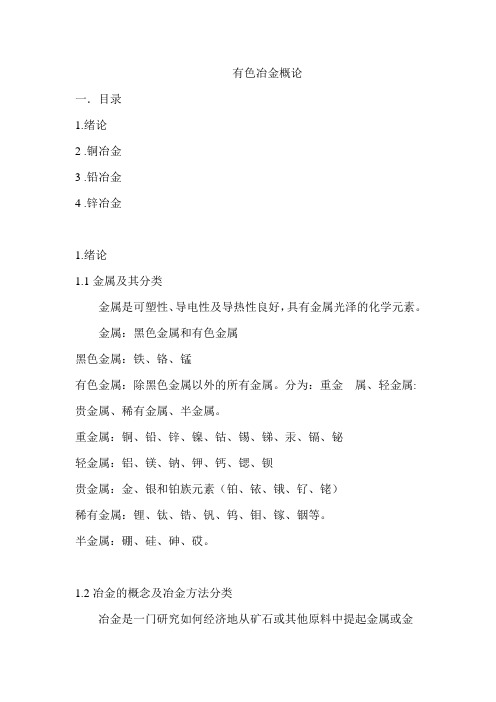
有色冶金概论一.目录1.绪论2 .铜冶金3 .铅冶金4 .锌冶金1.绪论1.1金属及其分类金属是可塑性、导电性及导热性良好,具有金属光泽的化学元素。
金属:黑色金属和有色金属黑色金属:铁、铬、锰有色金属:除黑色金属以外的所有金属。
分为:重金属、轻金属:贵金属、稀有金属、半金属。
重金属:铜、铅、锌、镍、钴、锡、锑、汞、镉、铋轻金属:铝、镁、钠、钾、钙、锶、钡贵金属:金、银和铂族元素(铂、铱、锇、钌、铑)稀有金属:锂、钛、锆、钒、钨、钼、镓、铟等。
半金属:硼、硅、砷、砹。
1.2冶金的概念及冶金方法分类冶金是一门研究如何经济地从矿石或其他原料中提起金属或金属化合物,并用各种加工方法制成具有一定性能的科学。
1.3冶金方法:火法冶金、湿法冶金、电冶金。
1.4主要冶金过程:干燥、焙烧、煅烧、烧结和球团、熔炼、精炼、吹炼、蒸馏、浸出、净化、水溶液电解、熔盐电解。
干燥:除去原料中的水分。
焙烧:将矿石原料或精矿置于适当的气氛下,加热至低于他们的熔点温度,发生氧化、还原或其他化学变化的冶金过程。
煅烧:将碳酸盐或氢氧化合物的矿物原料在空气中加热分解,除去二氧化碳或水分的过程。
烧结和球团:将不同粉矿均匀或造球后加热焙烧,固结成多孔块状或球状的物料。
熔炼:将处理好的矿石或其他原料,在高温下通过氧化还原反应,使矿石中的金属和杂质分离为两个液相层即金属液和熔渣过程。
精炼:进一步处理熔炼所得含有少量的粗金属,以提高其纯度。
吹炼:实质是氧化熔炼。
蒸馏:将冶炼的物料在加热的条件下,利用物料的挥发度不同,使物料中某些组分分离。
浸出:将固体物料加到液体溶剂中,使固体物料中的一种或几种有价金属溶解于溶液中。
净化:净化是用于处理浸出溶液或其他含有杂质超标的溶液,以除去溶液中杂质至达标的过程。
水溶液电解:在水溶液电解质中,插入两极,通入直流电,使水溶液电解质发生氧化-还原反应。
电解精炼和电解沉积。
熔盐电解:用熔融盐做为电解质的电解过程。
2.铜冶金铜的冶炼方法:火法炼铜和湿法炼铜火法炼铜是生产铜的主要方法。
冶金概论考试重点总结

冶金概论考试重点总结第一章:绪论1、冶金学的分类?按研究的领域分:提取冶金学(从矿石中提取金属及金属化合物的过程,因其中进行很多化学反应,又称化学冶金)和物理冶金学(材料的加工成型,通过控制其组成、结构使已提取的金属具有某种性能)。
按所冶炼金属类型分:有色冶金和钢铁冶金(黑色冶金)。
按冶金工艺过程不同分:火法冶金、湿法冶金、电冶金。
2、钢与生铁的区别?3、钢铁生产的典型工艺(长流程)?4、什么是耐火材料?钢铁生产对耐火材料的要求是什么?凡是耐火度高于1580℃,能在一定程度上抵抗温度骤变、炉渣侵蚀和承受高温荷重作用的无机非金属材料,称为耐火材料。
其要求是:耐火度高;能抵抗温度骤变;抗熔渣、金属液等侵蚀能力强;高温性能和化学稳定性好。
5、什么是炉渣?炉渣的分类以及碱度?炉渣是炉料在冶炼过程中不能进到生铁和钢中的氧化物、硫化物等形成的熔融体。
其主要成分是CaO、MgO、SiO2、Al2O3、MnO、FeO、P2O5、CaS等。
根据冶炼方法的不同,钢铁生产产生的炉渣分为高炉渣和炼钢渣,按炉渣中含有不同的化学成分又可分为碱性渣和酸性渣。
第二章:高炉炼铁1、高炉冶炼用原料?高炉冶炼用的原料主要有铁矿石(天然富矿和人造富矿)、燃料(焦炭和喷吹燃料)、熔剂(石灰石与白云石等)。
高炉冶炼是连续生产过程,必须尽可能为其提供数量充足、品味高、强度好、粒度均匀粉末少、有害杂质少及性能稳定的原料。
2、高炉结构及附属设备?高炉本体主要由钢结构(炉体支承框架、炉壳)、炉衬(耐火材料)、冷却设备(冷却壁、冷却板等)、送风装置(热风围管、支管、直吹管、风口)和检测仪器设备等组成。
附属设备:原料供应系统、送风系统、煤气净化系统、渣铁处理系统。
3、高炉生产主要技术经济指标?有效容积利用系数(ŋV):高炉每立方米有效容积每天生产的合格铁水量(t/m3·d)入炉焦比(K):冶炼一吨生铁消耗的焦炭量(kg/t)煤比(或油比):冶炼一吨生铁消耗的煤粉量或重油(kg/t)燃料比=焦比+煤比(或油比)冶炼强度:高炉每立方米有效容积每天消耗的(干)焦炭量(焦比一定的情况下)生铁合格率:生铁化学成分符合国家标准的总量占生铁总量的指标。
第一篇 冶金工程概论部分 第1章,第2章 4h

8
1.2 金属的分类
2.有色金属
3)贵金属 : Au Ag 铂及铂族元素
4)稀有金属 稀有轻金属:Li Be Rb Cs 稀有难熔金属:W Mo Nb Ta Zr Hf V 稀散金属: In Ge Ga Tl Se Te Re 稀土金属: Sc Y 及 La系元素 稀有放射金属:Th Pa U Ra 锕及锕系元素
28
2、提取冶金方法的分类 注 意
任何一种金属的提取都不是一步完成的,需要分为若干个 阶段进行; 一种金属的提取往往是多步冶金过程联合作用的结果; 金属的提取方法取决于金属的性质、原料的情况、最终产 品的要求等。 钢铁冶金主要采用火法,有色金属的提取往往是多种冶金 方法联合而制备的。
29
第1章 绪论
3、工艺流程图
金属的冶金过程是由若干个阶段或步骤完成的,各个阶段 的冶炼方法和使用的设备不尽相同。 各阶段过程间的联系及其所获得的产物间流动线路图称为 工艺流程图。可分为设备连接图,原则流程图和数质量流 程图。 设备连接图是表示冶炼厂主要设备之间联系的图; 原则流程图是表示各阶段作业间联系为主的图;
如石灰石煅烧为石灰;氢氧化铝煅烧成氧化铝,作 电解铝原料。
16
第1章 绪论
2、提取冶金方法的分类 主要火法冶金单元过程:
烧结和球团:将粉矿或精矿经加热焙烧,固结成多孔状 或球状的物料,以适应下一工序熔炼的要求。 如鼓风炉熔炼,高炉炼铁,氧气底吹炼铅的物料准备。 熔炼:是指将处理好的矿石、精矿或其他原料,在高温 下通过氧化还原反应,使矿物原料中有色金属组分与脉 石和杂质分离为两个液相层即金属(或金属锍)液和熔 渣的过程,也叫冶炼。 分为:还原熔炼、造锍熔炼、氧化吹炼
Ti
1668 4.51VΒιβλιοθήκη 1900 6.1Cr
冶金概论
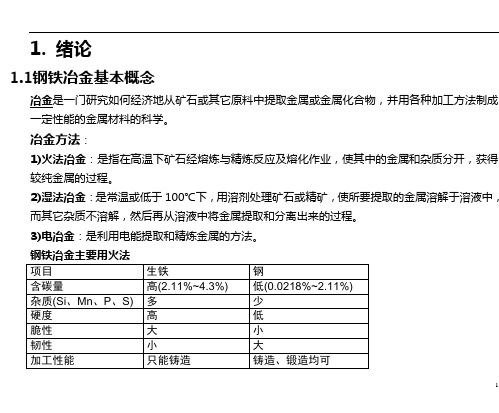
1. 绪论1.1钢铁冶金基本概念冶金是一门研究如何经济地从矿石或其它原料中提取金属或金属化合物,并用各种加工方法制成一定性能的金属材料的科学。
冶金方法:1)火法冶金:是指在高温下矿石经熔炼与精炼反应及熔化作业,使其中的金属和杂质分开,获得较纯金属的过程。
2)湿法冶金:是常温或低于100℃下,用溶剂处理矿石或精矿,使所要提取的金属溶解于溶液中,而其它杂质不溶解,然后再从溶液中将金属提取和分离出来的过程。
3)电冶金:是利用电能提取和精炼金属的方法。
1.2钢铁工业在国民经济中的地位评价一个国家的工业发达程度↓工业化水平国民生活水准↓↓工业生产所占比重↓工业机械化自动化程度交通工具市政设施工业化水平的标志民用住宅生活用品↓↓劳动生产率提高需要大量的基础材料↓↓需要大量的机械设备↓钢铁产品↓1) 价格低廉2) 有较高的强度和韧性3) 易于加工制造4) 所需原料资源丰富5) 冶炼工艺成熟、效率高1.3钢铁工业的发展1856年英国人H.Bessemer发明底吹酸性空气转炉炼钢法。
1864年法国人Martin发明酸性平炉法炼钢。
1878年英国人S.G.Thomas发明碱性底吹空气转炉炼钢法1899年法国人Heroult发明三相交流电弧炉。
1948年德国人Robert成功进行氧气顶吹转炉炼钢试验。
2007年11月24日世界最大的Corex熔融还原炉在我国宝钢投产。
国内最大转炉⑴底吹空气转炉的发明⑵平炉时代⑶电弧炉的发明⑷氧气转炉时代⑸直接还原和熔融还原二次世界大战后的四十多年中,钢铁工业获得重大发展新中国成立以后,特别是改革开放以来,我国钢铁工业有了重大发展中国既是钢铁大国,也是钢铁穷国1、从1996年中国大陆钢产量首次超过一亿吨大关,并跃居世界第一位以后,中国钢产量连年快速增长,并一直保持钢产量世界排名第一的位臵,中国钢产量已经连续13年居世界第一位。
2008年中国钢铁产量5.02亿吨,相当于日美俄印韩德乌巴等8国的总和。
冶金概论

感应炉冶炼一、冶金历史简介:冶金概念:就是从矿石中提取金属或金属化合物,用各种加工方法制成具有一定性能的金属材料的过程和工艺。
冶金作为一门古老的技术,在国内外都已有几千年的历史。
人类由使用石器、陶器进入到使用金属,这是人类文明的一次飞跃。
根据冶金史的研究,大约在公元前30世纪,人类开始大量使用青铜,此时代被称为“青铜器时代”;到公元前13世纪,铁器的应用在埃及已占一定比例,通常认为这是人类进入“铁器时代”的开端。
人类同金属材料及其制品的关系日益密切,在人们的日常生活、生产和其他活动中所使用的工具及设施都离不开金属材料及其制品,也就是说没有金属材料就没有人类的物质文明。
中国古代冶金技术的发展要比欧洲国家早,尤其是在掌握铸铁及热处理技术方面。
就金属种类而言,中国在春秋战国之际(公元前7世纪),已经能够提取铜、铁、锡、铅、汞、金和银等7种常用金属。
但由于冶金技术长期停留在凭经验操作或师徒传授的传统方式,在中世纪近一千多年内,全世界的冶金技术发展均十分缓慢。
现代冶金可以认为是开始于19世纪前后,冶金学受到其他学科的影响而获得迅速发展。
特别是化学、物理学、热能及工程学等方面的成就,促使冶金的生产技术不断改进。
例如,冶金方法已不仅局限于传统的碳还原法和氧化法,而开始使用电能和制造出能够产生高温和能控制气氛的电炉,并出现了熔盐电解铝和水溶液电解有色金属的新方法、在冶金过程中应用氧气、使用大型自动化炼铁高炉、氧气顶吹转炉炼钢、真空冶金和闪速熔炼等新技术,从此冶金技术进入到新的发展阶段。
冶金工业是指对金属矿物的勘探、开采、精选、冶炼、以及轧制成材的工业部门,包括黑色冶金工业和有色冶金工业两大类,前者包括生铁、钢和铁合金(如铬铁、锰铁等)的生产;后者包括其余所有各种金属的生产。
是重要的原材料工业部门,为国民经济各部门提供金属材料,也是经济发展的物质基础。
冶金工程领域是研究从矿石等资源中提取金属或化合物,并制成具有良好的使用性能和经济价值的材料的工程技术领域。
冶金工程概论全册配套最完整精品课件
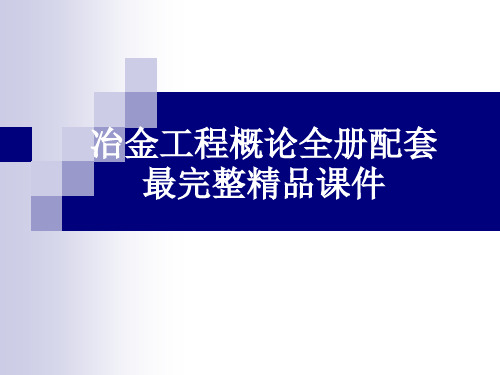
28
开采方法:
为了经济而有效地开发地下资源,需根据矿床所处的 地理位置、埋藏条件以及国民经济发展的需要,进行 可行性的技术经济分析,选择合理的开采方法。
露天开采:如果矿床埋藏得比较浅时可采用露天开采, 以台阶的方式一层一层地向下开采,剥离岩石到达矿 体,然后再以台阶方式开采矿石。露天采矿的步骤主 要包括矿区的地面准备、矿山基本建设、剥离岩石和 每种类型的金属的性质、及其冶炼方法都有其特殊性。 黑色金属:冶炼方法均为火法。 重金属:可分为火法和湿法冶炼。
轻金属:密度小、活性大,多采用熔盐电解法和金属热还原 法生产。
贵金属:一部分可由矿石提取,大部分都是从铜、镍、铅、 锌冶炼厂的副产品(阳极泥)中回收的。
稀有金属:分散、没有富集的矿床,难于开采和冶炼。 有的熔点高,硬度大,耐腐蚀;有的没有形成单独
一、火法冶金
定义: 在高温条件下,使矿石或精矿中的有用矿物部分或全部 在高温条件下进行一系列的物理化学反应,达到提取、 提纯金属与脉石和其它杂质分离的目的。 高温的获得: 燃料、自身反应,电能 地位:火法冶金在金属冶炼中占主导地位。
二、湿法冶金
在低温下(一般低于100℃,现代湿法冶金的高温高 压过程,200℃~300℃)用溶剂来处理矿石和精 矿,并在低温溶液中进行一系列的物理化学反应, 达到提取、提纯金属与脉石和其它杂质分离的目 的。
的矿床,只能从化工厂和冶金厂的废料中提取;有的提取 异常困难;有的含有放射性。所以稀有金属的冶炼方法多 种多样。
定义
冶金:是一门研究如何经济地从矿石或精矿和其它材料中 提取金属,并使之经过加工处理,适用于人类的科学。 广义的冶金包括矿石的开采、选矿、冶炼和金属加工。由 于科学技术的进步和工业的发展,采矿、选矿和金属加工 已形成一门独立的学科。因而目前的冶金是指矿石或精矿 的冶炼。 又称: 化学冶金:主要采用的是化学的方法。 提取冶金:从矿石或精矿中提取金属。 冶金方法是多种多样的,根据冶炼方法的不同,大致可分为 三类:火法冶金、湿法冶金、电冶金。
冶金概论
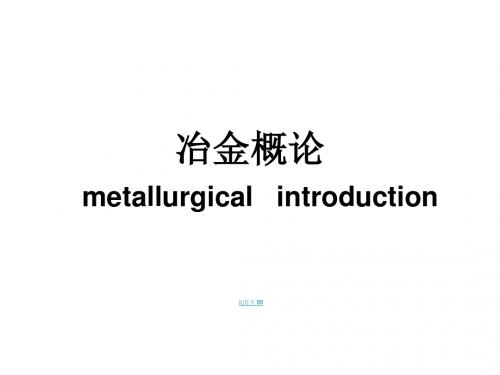
8.熔盐电解:以熔盐作电解质的电解过程。
水溶液电解一般都在低于100℃的温度下进行, 而进行熔盐电解时,必须使电解质成为熔融体,因此, 过程是在高温下进行的。如电解生产铅的过程,就是 在约1000 ℃ 的温度下,电解冰晶石和氧化铝熔融体 的过程。 熔盐电解其主要用于制取轻金属如铅、镁、钙、 钠等。原因很简单,因它们化学活性很大,其对氧、 卤素和碳的化合物都很稳定。水溶液电解得不到金属。 有些稀有金属如铍、锂、钍、锆、钽也用熔盐电解制 取。
5.火法精炼:
就是用各种方法除去熔融粗金属中的杂质的精炼过程。根 据金属和杂质的不同特性,常用下列一些方法:加剂法、熔析 法、精馏法等。 加剂精炼就是向熔融的粗金属中加入一种或几种附加物质, 使杂质与附加物质生成不溶于金属的稳定化合物,并上浮成渣 而除去杂质的过程。如氧化熔炼、氯化熔炼、硫化熔炼等。 熔析精炼是将粗金属加热熔化后,在冷却的过程中,控制 温度,由于杂质与金属相互溶解及比重的不同,发生分层而达 到分离杂质的目的。例如粗铅熔析除铜。
7.水溶液电解:
水溶液电解就是在水溶液的电解质中,插入两个电极, 让电流通过电解质使其发生化学反应的过程。重有色金属 的电解过程大多采用水溶液电解法。 根据使用的阳极不同分为: 可溶阳极电解称为电解精炼; 不溶性阳极电解称为电积。 如铜的电解精炼,粗铜为阳极,纯铜为阴极。在硫酸 铜溶液中进行电解。在通电电解时,阳极粗铜逐渐溶解, 纯铜则阴极上沉积出来,达到了精练的目的,称电解精练。 又如锌的电积就是用铅板作成不溶阳极,对浸出过程中所 得到的硫酸锌溶液来进行电积,以便使溶液中的锌在阴极 上沉淀出来。
炼铜的步骤: (1)炉料制备 (炉料) (2)熔炼 (3)吹炼 (粗铜) (4)火法精炼 (阳极) (5)电解精炼
冶金概论
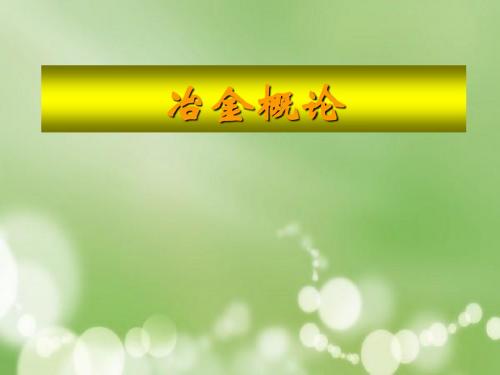
2、炼 铁
铁氧化物的离解
T>570℃ T<570℃ Fe2O3→Fe3O4→FeO→Fe Fe2O3→Fe3O4→Fe
铁氧化物的还原
T>570℃ Fe2O3→Fe3O4→FeO→Fe T<570℃ Fe2O3→Fe3O4→Fe 间接还原:用CO还原 直接还原:用C还原
2、炼 铁
高炉内非铁氧化物的行为
第一章 绪论
第一章 绪论
Ⅰ A Ⅱ A Ⅲ B Ⅳ B Ⅴ B Ⅵ B Ⅶ B Ⅷ B Ⅰ B Ⅱ B Ⅲ A Ⅳ A Ⅴ A Ⅵ A Ⅶ A Ⅷ A
2
1 2 3 4 5 6 7
1
H
3 4 5 6 7 8 9
He
10
Li
11 19
Be
12 20 38 56 88 21 39 22 23 24 42 74 25 43 75 26 44 76 27 45 77 28 46 78 29 47 79 30 48 80
B
13
C
14
N
15
O
6
F
17
Ne
18
Na Mg K
37 55 87
Al
31 49 81
Si
32 50 82
P
33 51 83
S
34 52 84
Cl
35
Ar
36
Ca Sc Y
57 89
Ti
40 72
V
41 73
Cr Mn Fe
Co Ni
Cu Zn Ga Ge As Se Sn Sb Te Pb Bi
Br
第二章 炼铁
高炉炼铁技术的发展
(1)高炉大型化 (2)精料
- 1、下载文档前请自行甄别文档内容的完整性,平台不提供额外的编辑、内容补充、找答案等附加服务。
- 2、"仅部分预览"的文档,不可在线预览部分如存在完整性等问题,可反馈申请退款(可完整预览的文档不适用该条件!)。
- 3、如文档侵犯您的权益,请联系客服反馈,我们会尽快为您处理(人工客服工作时间:9:00-18:30)。
冶金概论1第一篇:冶金概论1第一章绪论1.1.1 冶金学冶金学是一门研究如何经济地从矿石或其它原料中提取金属或金属化合物,并用一定加工方法制成具有一定性能的金属材料的科学。
由于矿石性能不同,提取金属的原理、工艺过程和设备不同,从而形成专门的冶金学科—冶金学。
冶金学研究所涉及的内容:金属的制取,金属的加工,金属性能的改进→对金属成分、组织结构、性能和相关理论的研究。
冶金学按研究的领域分:提取冶金学(化学冶金学)和物理冶金学(材料的加工成型,通过控制其组成、结构使已提取的金属具有某种性能)。
提取冶金(extractive metallurgy):从矿石中提取金属及金属化合物的过程,因其中进行很多化学反应,又称化学冶金(chemical metallurgy)。
提取冶金的分类按所冶炼金属类型分:有色冶金钢铁冶金(黑色冶金)按冶金工艺过程不同分:火法冶金湿法冶金电冶金1.1.2 火法冶金主要过程简介干燥:去水,温度为400~600℃。
焙烧:以改变原料组成为目的的、在低于矿石熔点温度下、在特定气氛中进行的冶金过程。
煅烧:在空气中以去CO2和水为目的的冶金过程。
烧结与球团:以获得特定矿物组成、结构及性能的造块。
熔炼:还原氧化物,提取粗金属。
精炼:氧化杂质,获得纯金属。
铸造:液态金属凝固成固态。
1.2.1 钢铁材料钢铁是使用最多的金属材料原因:储量大;冶炼加工容易;综合性能好;易改质处理预计未来几年钢铁产品在各行业中占的比例1.2.3 钢铁冶炼技术发展简史远古至13世纪末:半熔融状态的铁块—海绵铁;13世纪末至19世纪中叶:熔融状态的生铁→粗钢,形成两步法炼钢;19世纪中期至今:1856年英国人发明了空气底吹酸性转炉炼钢法;1864年法国人发明了平炉炼钢法;1874年发明了空气底吹碱性转炉炼钢法;20世纪初发明了电弧炉炼钢;20世纪中叶氧气顶吹转炉(LD法)。
1.2.3 我国钢铁工业的发展1996年,突破1亿吨;1999年,产量世界第一;2003年,突破2亿吨,世界惟一年产钢超过2亿吨的国家;2004年,产量2.8亿吨;2005年,产量3.5亿吨;2006年,产量4.2亿吨;2008年,产量5.0亿吨;2009年,产量5.6亿吨。
中国钢铁工业发展目标“加强自主创新,建设创新型国家”目标下,通过结构调整和产业升级,努力使我国从钢铁大国转变为钢铁强国。
钢铁冶炼的任务是把铁矿石冶炼成合格的钢。
1.4 钢铁产品及副产品产品:生铁、钢副产品:炉渣、煤气生铁:它是铁和碳及少量硅。
锰、硫、磷等元素组成的合金,主要由高炉生产,按其用途可分为炼钢生铁和铸造生铁。
炉渣:炉渣是炉料在冶炼过程中不能进到生铁和钢中的氧化物、硫化物等形成的熔融体。
其主要成分是CaO、MgO、SiO2、Al2O3、MnO、FeO、P2O5、CaS等。
根据冶炼方法的不同,钢铁生产产生的炉渣分为高炉渣和炼钢渣,按炉渣中含有不同的化学成分又可分为碱性渣和酸性渣。
煤气:钢铁生产中还能获得大量的可燃气体,高炉炼铁可产生高炉煤气,转炉炼钢可获得转炉煤气,炼焦时可得焦炉煤气等。
煤气主要成分:CO、H2、CO2、N2、CH41.5.1 钢铁生产用能源钢铁工业是能源消耗的大户,约占全国总能源消耗量的10~11%。
钢铁生产所用能源主要有煤炭、燃料油(重油)、天然气、电力等。
煤占钢铁生产中燃料消耗的70%,钢铁工业用煤量已超过煤炭总产量的15%。
煤在钢铁企业主要用来炼焦和自备电厂发电、蒸汽机车烧煤、烧工业锅炉及部分窑炉,少部分制成粉煤用于高炉喷吹及烧结生产。
1.5.2 钢铁工业能耗我国钢铁工业的能源消耗中,钢铁冶炼是耗能最高的工序,占钢铁工业能耗的60~70%。
其主要耗于炼铁系统,焦化、烧结、球团、炼铁等工序,占钢铁生产能耗的一半以上。
1.5.3 节能途径改进生产工艺及操作,更新和改造耗能高的设备。
降低能源损失(“废料”、煤气、热能、压力能),减少生产工序。
回收利用散失热量。
加强企业能源管理,加强能源利用技术的研究工作,提高操作技术水平,充分发挥现有设备能力,以节能为目标合理组织生产。
1.6 耐火材料凡是耐火度高于1580℃,能在一定程度上抵抗温度骤变、炉渣侵蚀和承受高温荷重作用韵无饥非金属材料,称为耐火材料。
耐火材料由耐火砂岩进入到现代科技产品,已成为独立的生产行业,其产品的60~80%消耗于冶金工业。
钢铁生产对耐火材料的要求是:耐火度高;能抵抗温度骤变;抗熔渣、金属液等侵蚀能力强;高温性能和化学稳定性好。
1.7 环境保护钢铁厂产生的各种污染物有:大气污染物质污水固体废弃物大气污染物质SOX:是通过原料、燃料中硫磺成分的燃烧而产生的。
烧结工厂等为其主要发生源。
NOX:通过燃烧后发生。
烧结工厂等为其主要发生源。
煤尘:通过燃烧后发生。
烧结炉、各加热炉为其发生源。
粉尘:从燃料原料的输送、处理过程,及储藏场中产生。
炼铁、炼钢工程为其主要发生源。
污水:钢铁工业用水主要是冷却水,其次是煤气洗涤水,以及冲洗设备、地面及除尘用水等。
污水中含有下列污染物:固体悬浮物(SS):从排气集尘、高温物质的直接冷却等过程中产生。
油:由各种机械等所使用的油所发生的漏泄及冷轧工程使用轧制机的机油等原因而产生。
化学需氧量(COD):从煤炭干馏时的氨水,及冷轧、电镀废水中产生。
酸、碱:从冷轧工程的酸洗工程、电镀工程等的脱脂工程中产生。
固体废弃物炉渣:从高炉、铁水预处理、转炉、电炉、二次精炼设备等的冶炼工程中产生。
污泥:在各种水处理过程中产生。
灰尘:从各种干式集尘机中产生。
第一章小结重点掌握内容:火法冶金及其主要工序;钢铁冶炼的任务;钢铁生产长流程生产工艺;钢铁工业能源及能耗特点;耐火材料及其要求。
第二篇:冶金概论论文选课课号:(2011-2012-2)-BG11191-320001-1课程类别:公选课《冶金工程概论》课程考核题目:(课程论文)钢铁冶金联合企业生产环及过程及特点—冶金与计算机科学的联系作者:学号:授课教师:杜长坤班级:计算机科学与技术1102级重庆科技学院冶金与材料工程学院2012年5月 8日中国重庆钢铁冶金联合企业生产环及过程及特点—冶金与计算机科学的联系作者:***重庆科技学院电气信息工程学院计算机科学与技术班摘要:钢铁工业是国家的基础工业之一,钢铁产量往往是衡量一个国家工业水平和生产能力的主要标志,首先要提高钢铁生产就必须明确知道起生产环节及特点等,这样才可以知道该怎么改进设备以提高钢铁生产,节约成本。
而随着计算机科学的不断提高,计算机专业在钢铁生产中占着不可或缺的重要地位!关键词:冶金环节钢铁生产计算机科学1.冶金炼铁的生产过程现代化的钢铁联合生产企业,其生产环节是一个复杂而庞大的生产体系,每个生产环节都有其主要生产过程、主要设备、生产方法以及特点。
主要包括原料处理、炼铁、炼钢、轧钢、能源供应、交通运输等。
1.1选原材料炼铁原料: 1,铁矿石:一种或几种含铁矿物和脉石组成2,燃料:焦炭,并作为还原剂3,熔剂:有酸、碱之分,多选用碱性石灰石,选矿经历了从处理粗粒物料到细粒物料、从处理简单矿石到复杂矿石、从单纯使用物理方法向使用物理化学方法和化学方法的发展过程。
包括精矿、中间产品、尾矿的脱水,尾矿堆置和废水处理。
选矿主要在水中进行,选后产品需要脱水干燥。
方法有重力泄水、浓缩、过滤和干燥。
尾矿水可回收再用。
不合排放标准的废水须经净化处理。
旧尾矿场地要进行植被、复田。
1.2炼铁炼铁是把铁矿石还原成生铁的连续生产过程,其中,高炉冶炼在钢铁工业中占有重要地位。
具体的炼铁过程为:(1)炉顶装入铁矿石、焦炭、造渣用熔剂(石灰石)燃料的燃烧:焦碳自炉顶下落至风口时与空气相遇,燃烧,进行放热反应。
C+O2→CO2+1600~1750℃CO2上升,遇赤热焦碳,被还原成COCO2+C→2CO-ΔCO热气继续上升,遇热矿石,发生还原反应,将Fe还原出来(2)从位于炉子下部沿炉周的风口吹入经预热的空气(3)在高温下焦炭(也喷吹煤粉、重油、天然气等辅助燃料)中的碳同鼓入空气中的氧燃烧生成的一氧化碳和氢气,在炉内上升过程中除去铁矿石中的氧,从而还原得到铁。
铁的还原:直接或间接还原两种.1)直接还原:950℃以上,固体碳呈烟状进入矿石孔隙内完成反应。
FeO+C→Fe+CO2CO→CO2+C2)间接还原:开始于炉口(250℃-350℃)终止于950℃。
顺序地利用CO,将高价的铁氧化物还原成低价的铁氧化物。
3Fe2O3+CO→2Fe3O4+CO22Fe3O4+2CO→6FeO+2CO26FeO+6CO→6Fe+6CO2(4)炼出的铁水从铁口放出(5)铁矿石中不还原的杂质和石灰石等熔剂结合生成炉渣,从渣口排出。
炉渣具有重要作用:1)熔化其余各种氧化物,控制生铁合格成分。
2)浮在熔融液表面,能保护金属,防止其过分氧化、热量散失或不致过热。
因添加剂不同,有酸性、碱性、中性渣。
造渣是矿石中废料,燃料中灰分与熔剂熔合过程的产物。
与熔融金属液不互熔,又比其轻,能浮在熔体表面,便于排出。
主要成分;SiO2、Al2O3、CaO,及少量MnO、FeO、CaS等。
产生的煤气从炉顶导出,经除尘后,作为热风炉、加热炉、焦炉、锅炉等的燃料。
特点:高炉炼铁的缺点:投资大、流程长,能耗高,污染大。
改进:不用焦碳,不用高炉,用烟煤或天然气作还原剂,采用直接还原或熔融还原生产铁,以供电炉炼钢二次精炼,连铸连轧。
直接还原:用煤或天然气等还原剂直接将固态铁矿石还原成固态海绵铁。
可用煤基回转窑、气基竖炉等设备直接还原。
煤基回转窑中:Fe2O3+3CO→2Fe+3CO2气基竖炉中:CH4+H2O→CO+3H2+天然气裂化反应Fe2O3+3H2→2Fe+3H2OFe2O3+3CO→2Fe+3CO21.3炼钢炼钢,就是通过冶炼来降低生铁中的碳和去除有害杂质,再根据对钢性能的要求加入适量的合金元素,使其成为具有高的强度、韧性或其它特殊性能的钢。
主要方法有三种:(1)氧气转炉炼氧气顶吹转炉炼钢设备工艺,如图4所示。
按照配料要求,先把废钢等装入炉内,然后倒入铁水,并加入适量的造渣材料(如生石灰等)。
加料后,把氧气喷枪从炉顶插入炉内,吹入氧气(纯度大于99%的高压氧气流),使它直接跟高温的铁水发生氧化反应,除去杂质。
用纯氧代替空气可以克服由于空气里的氮气的影响而使钢质变脆,以及氮气排出时带走热量的缺点。
在除去大部分硫、磷后,当钢水的成分和温度都达到要求时,即停止吹炼,提升喷枪,准备出钢。
出钢时使炉体倾斜,钢水从出钢口注入钢水包里,同时加入脱氧剂进行脱氧和调节成分。
钢水合格后,可以浇成钢的铸件或钢锭,钢锭可以再轧制成各种钢材。
氧气顶吹转炉在炼钢过程中会产生大量棕色烟气,它的主要成分是氧化铁尘粒和高浓度的一氧化碳气体等。