汽车零部件强度试验和评价
汽车配件检测报告

汽车配件检测报告引言汽车配件作为构成汽车的重要组成部分,其质量的好坏直接影响到汽车的安全性和性能。
为了保证车辆的正常运行和乘客的安全,对汽车配件进行检测是必不可少的。
本文将介绍汽车配件检测的步骤和重要性。
步骤一:外观检查首先进行的是外观检查,目的是检查配件的表面是否有明显的损伤、划痕或者其他质量问题。
外观检查可以通过肉眼观察或者辅助工具,如放大镜或显微镜进行。
如果发现了任何问题,应及时记录并标记。
步骤二:尺寸测量尺寸测量是汽车配件检测中的重要步骤之一。
通过测量配件的尺寸,可以判断其是否符合设计要求。
尺寸测量可以使用测量工具,如卡尺、游标卡尺或激光测距仪等。
通过与设计图纸进行对比,可以确定是否存在尺寸偏差。
步骤三:材料检测材料检测是为了确认配件所使用的材料是否符合标准和要求。
常用的材料检测方法包括化学分析、金相分析和力学性能测试等。
化学分析可以确定材料的成分和含量,金相分析可以观察材料的组织结构,力学性能测试可以测试材料的硬度、强度和韧性等。
步骤四:功能测试功能测试是为了验证配件的功能是否正常。
根据不同的配件类型,功能测试可以采用不同的方法。
例如,对于刹车片,可以通过制动测试来验证其制动效果;对于灯具,可以通过电气测试来验证其照明效果。
功能测试的目的是确保配件在使用过程中能够正常工作。
步骤五:耐久性测试耐久性测试是为了评估配件在长时间使用后的性能稳定性和寿命。
通过模拟实际使用条件,如振动、温度变化和湿度等,可以测试配件的耐久性。
耐久性测试可以通过使用专门的测试设备进行,或者使用特定的测试方法来模拟实际使用条件。
结论汽车配件的检测是确保汽车质量和安全性的重要环节。
通过外观检查、尺寸测量、材料检测、功能测试和耐久性测试等步骤,可以全面评估配件的质量和性能。
只有经过严格的检测和验证,才能保证配件的安全可靠性,为车辆的正常运行提供保障。
参考文献[1] 张三, 李四. 汽车配件检测技术综述. 机械工程学报, 2020, 52(6): 100-110.[2] 王五, 赵六. 汽车配件耐久性测试方法研究. 汽车工程学报, 2019, 48(3): 200-210.。
汽车零部件可靠性常用测试标准

温度循环/冲击试验是评估产品在高底温和温度交变的效应。效应:膨胀、减弱结构强度、 化学腐蚀电解所用、增加绝缘体导电作用、可动零件变形、表面涂料鬼裂等。
参考的测试标准: BMW GS95003-4,GMW3172 5.5.5, GMW3431 4.4.2, GM9123P 10.2.1, VW801015.2.2, Etl_82517 8.2.8 , FORD Ds00005 10.9.4 , FORD_WDS00.00EA_D114.5.6/4.5.7 , MGRES6221001 9.3.6, SES E 001-04 6.7, PSAB21 7090 6.6.3, IEC60068-2-14(air to air), MIL-STD-883E 1011.9,MIL-STD-202G/107G,MIL-STD-810F 503.4,GB2324.22,GJB150.5 0)
4. 温湿度试验目的:
温湿度测试方法是用来评估产品有可能储存或者使用在高温潮湿环境中的功能。
参考的测试标准: BMW GS95003-4,GMW3172 5.5.1/5.5.2/5.6,GMW3431 4.4.1/4.4.5/4.4.6,GM9123P 9.6/9.11/9.12,GME60202_0181,VM801015.1.2/5.1.3/5.3/5.5.2, FORD DS0000510.9.1/10.9.2/10.9.3/10.9.8/10.9.9/10.9.10,
更多信息敬请垂询:
联系人:Rocket Chen (陈先生) 电话: 0592-5773013 (电话打不通可写邮件) 邮箱: Rocket.Chen @
外壳防护等级(IP 代码) Road vehicles: Degrees of protection (IP code)- Protection against foreign objects, water and access Electircal Equipment Degrees of protection provided by enclosures (IP code) Road vehicles: Degrees of protection (IP code)- Protection against foreign objects, water and access Electircal Equipment
汽车零部件制造工艺规范书

汽车零部件制造工艺规范书第一章概述 (4)1.1 编写目的 (4)1.2 适用范围 (4)1.3 相关标准 (4)1.3.1 国家标准 (4)1.3.2 行业标准 (4)1.3.3 企业标准 (4)第二章零部件设计要求 (5)2.1 设计原则 (5)2.2 设计流程 (5)2.3 设计评审 (6)第三章材料选择与功能 (6)3.1 材料分类 (6)3.1.1 按材质分类 (6)3.1.2 按用途分类 (6)3.2 材料功能要求 (7)3.2.1 结构功能要求 (7)3.2.2 功能功能要求 (7)3.2.3 舒适性功能要求 (7)3.3 材料检验 (7)3.3.1 入厂检验 (7)3.3.2 过程检验 (7)3.3.3 出厂检验 (7)3.3.4 检验方法 (7)第四章零部件加工工艺 (8)4.1 加工方法 (8)4.2 加工设备 (8)4.3 加工参数 (8)第五章零部件装配工艺 (9)5.1 装配流程 (9)5.1.1 准备工作 (9)5.1.2 零部件定位 (9)5.1.3 零部件组装 (9)5.1.4 连接件连接 (9)5.1.5 检查与调试 (9)5.2 装配方法 (9)5.2.1 手动装配 (9)5.2.2 半自动化装配 (10)5.2.3 自动化装配 (10)5.3 装配检验 (10)5.3.1 外观检验 (10)5.3.2 尺寸检验 (10)5.3.3 功能检验 (10)5.3.4 质量检验 (10)5.3.5 出厂检验 (10)第六章零部件试验与验证 (10)6.1 试验方法 (10)6.1.1 概述 (10)6.1.2 功能试验 (10)6.1.3 耐久性试验 (11)6.1.4 安全试验 (11)6.1.5 环境适应性试验 (11)6.2 验证标准 (11)6.2.1 概述 (11)6.2.2 国家标准 (11)6.2.3 行业标准 (11)6.2.4 企业标准 (11)6.3 试验结果分析 (11)6.3.1 概述 (11)6.3.2 数据整理 (12)6.3.3 数据分析 (12)6.3.4 评价与建议 (12)第七章零部件质量检验 (12)7.1 检验标准 (12)7.1.1 零部件检验标准应依据国家相关法律法规、行业标准及企业内部质量控制要求制定。
汽配产品性能检测报告模板

汽配产品性能检测报告模板1. 背景介绍本报告是对某款汽配产品的性能进行检测和评估的结果总结。
该产品是广泛应用于汽车行业的重要零部件,其性能的稳定性和可靠性直接关系到汽车的安全和性能。
通过对该产品的性能检测,可以了解其质量和可靠性,为用户提供可靠的参考。
2. 检测项目和方法2.1 检测项目本次检测主要涵盖以下几个方面的项目:1. 强度和耐久性检测2. 尺寸精度检测3. 摩擦和磨损检测4. 温度和湿度适应性检测5. 材料成分和加工工艺分析2.2 检测方法1. 强度和耐久性检测:通过负载实验和循环使用实验测试产品的承重能力和使用寿命。
2. 尺寸精度检测:采用三坐标测量和数字显微镜等方法,对产品的尺寸和形状进行精确测量。
3. 摩擦和磨损检测:利用模拟测试设备,在不同工况下测试产品的摩擦系数和磨损情况。
4. 温度和湿度适应性检测:将产品置于不同温度和湿度环境下,测试其在复杂气候条件下的性能。
5. 材料成分和加工工艺分析:采用光谱分析和显微结构观察等方法,对产品的材料成分和工艺进行分析。
3. 检测结果和分析经过以上检测项目的严格评估和分析,得出以下结论:1. 强度和耐久性:产品在负载实验中承重能力良好,且经过循环使用实验后仍保持较高的使用寿命,表现出良好的强度和耐久性。
2. 尺寸精度:产品的尺寸精度在允许范围内,与设计要求相符。
3. 摩擦和磨损:产品具有较低的摩擦系数,能够有效减小摩擦损失,并具有良好的磨损抗性。
4. 温度和湿度适应性:产品在不同温度和湿度环境下表现稳定,具有良好的适应性。
5. 材料成分和加工工艺:产品的材料成分符合标准要求,加工工艺精细,表面光滑,无明显缺陷。
4. 结论和建议根据上述检测结果,可以得出以下结论和建议:1. 该产品在强度、耐久性和尺寸精度等方面表现出良好的性能,可以满足汽车行业的使用需求。
2. 产品具有较低的摩擦系数和良好的磨损抗性,可有效降低能源损失和改善车辆性能。
3. 产品在复杂气候条件下表现稳定,适应性良好。
汽车零部件检测要求
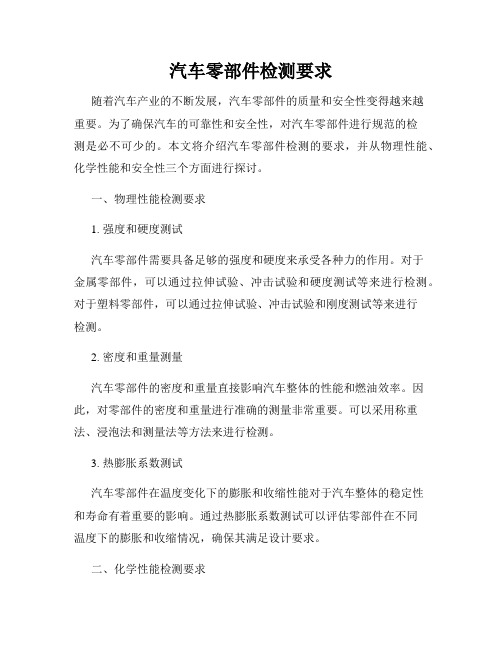
汽车零部件检测要求随着汽车产业的不断发展,汽车零部件的质量和安全性变得越来越重要。
为了确保汽车的可靠性和安全性,对汽车零部件进行规范的检测是必不可少的。
本文将介绍汽车零部件检测的要求,并从物理性能、化学性能和安全性三个方面进行探讨。
一、物理性能检测要求1. 强度和硬度测试汽车零部件需要具备足够的强度和硬度来承受各种力的作用。
对于金属零部件,可以通过拉伸试验、冲击试验和硬度测试等来进行检测。
对于塑料零部件,可以通过拉伸试验、冲击试验和刚度测试等来进行检测。
2. 密度和重量测量汽车零部件的密度和重量直接影响汽车整体的性能和燃油效率。
因此,对零部件的密度和重量进行准确的测量非常重要。
可以采用称重法、浸泡法和测量法等方法来进行检测。
3. 热膨胀系数测试汽车零部件在温度变化下的膨胀和收缩性能对于汽车整体的稳定性和寿命有着重要的影响。
通过热膨胀系数测试可以评估零部件在不同温度下的膨胀和收缩情况,确保其满足设计要求。
二、化学性能检测要求1. 化学成分分析汽车零部件在使用过程中会暴露在各种工作环境和化学物质中,因此对零部件的化学成分进行分析是十分必要的。
通过化学成分分析可以确定零部件的成分组成,确保其符合相关标准和法规要求。
2. 耐腐蚀性测试汽车零部件需要具备良好的耐腐蚀性能,以应对复杂的工作环境。
可以通过盐雾试验、湿热试验和化学试剂浸泡试验等方法来评估零部件的耐腐蚀性能,并确保其在恶劣环境下的使用寿命。
3. 表面处理性能检测汽车零部件的表面处理对于外观和使用寿命有着直接的影响。
可以通过表面质量检查、耐磨性测试和附着力测试等方法来评估零部件的表面处理质量,并确保其满足相关要求。
三、安全性检测要求1. 摩擦性能测试摩擦性能直接影响零部件与其他部件之间的紧密程度和操作的顺畅性。
可以通过滑动摩擦试验、磨损试验和耐磨试验等方法来评估零部件的摩擦性能,并确保其能够正常工作。
2. 安全阻燃性能测试汽车零部件需要具备良好的阻燃性能,以确保在发生事故时能够有效地防止火灾蔓延。
汽车零部件检测报告
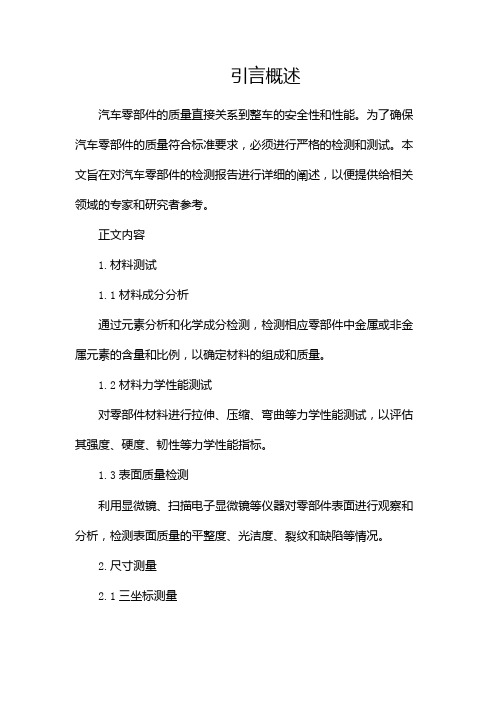
引言概述汽车零部件的质量直接关系到整车的安全性和性能。
为了确保汽车零部件的质量符合标准要求,必须进行严格的检测和测试。
本文旨在对汽车零部件的检测报告进行详细的阐述,以便提供给相关领域的专家和研究者参考。
正文内容1.材料测试1.1材料成分分析通过元素分析和化学成分检测,检测相应零部件中金属或非金属元素的含量和比例,以确定材料的组成和质量。
1.2材料力学性能测试对零部件材料进行拉伸、压缩、弯曲等力学性能测试,以评估其强度、硬度、韧性等力学性能指标。
1.3表面质量检测利用显微镜、扫描电子显微镜等仪器对零部件表面进行观察和分析,检测表面质量的平整度、光洁度、裂纹和缺陷等情况。
2.尺寸测量2.1三坐标测量采用三坐标测量仪对零部件的尺寸进行精确测量,以确定其几何形状和尺寸是否符合设计要求。
2.2光学测量利用光学仪器如投影仪、激光扫描仪等对零部件进行形状和尺寸的测量,以验证其外形和尺寸的精确性。
2.3表面粗糙度测量通过表面粗糙度测量仪对零部件的表面粗糙度进行评估,以判断其表面质量和加工工艺的优劣。
3.性能测试3.1疲劳寿命测试对零部件进行循环加载、振动等测试,以评估其在使用寿命内的耐久性和疲劳性能。
3.2环境适应性测试模拟不同环境条件下的气候、温湿度等,对零部件进行测试,以评估其在不同环境下的性能和适应性。
3.3渗透性测试通过渗透测试,检测零部件内部是否存在气体、液体或杂质,以确定其无泄露问题。
4.安全性测试4.1碰撞测试模拟车辆发生碰撞的情况,对零部件进行强度和安全性测试,以评估其在碰撞时的承载能力和保护能力。
4.2燃烧性能测试对零部件进行燃烧测试,以评估其在火灾等极端情况下的燃烧性能和阻燃性能。
4.3声响测试通过声学测试对零部件进行评估,以判断其在使用过程中是否会产生噪音和共振问题。
5.可靠性测试5.1可靠性试验对零部件进行长时间的使用试验,以评估其在实际使用条件下的可靠性和稳定性。
5.2寿命试验通过模拟零部件的使用寿命,对其进行加速老化和寿命试验,以评估其在实际使用寿命内的可靠性。
汽车结构实验报告小结

汽车结构实验报告小结引言本次实验旨在研究汽车的结构特点以及对汽车结构进行有限元分析,为汽车设计和优化提供数据支持。
通过实验,了解了汽车结构的材料、组成部分、受力情况等方面的基本知识。
实验结果表明,有限元分析是汽车结构研究中一种重要的分析方法,可以有效地评估车身刚度、安全性和舒适性等指标。
实验方法1. 汽车结构材料的研究我们首先对汽车的结构材料进行了研究。
通过观察和测量,我们了解到汽车主要使用钢材和铝材作为结构材料。
钢材具有良好的强度和刚度,适用于车身和底盘等主要部分的制造。
铝材则具有较低的密度和良好的耐腐蚀性,适用于发动机罩、车门等较轻的部件。
2. 汽车结构的组成部分我们对汽车的结构组成部分进行了详细的研究。
通过拆解汽车并观察其各部件,我们发现汽车主要由车身、底盘、发动机、悬挂、车轮等部分组成。
其中,车身和底盘是汽车的主要承载部分,发动机提供动力,悬挂和车轮则为汽车提供悬挂和行驶支持。
3. 汽车结构的有限元分析我们对汽车的结构进行了有限元分析。
首先,我们建立了汽车的有限元模型,并设置了边界条件和加载情况。
然后,通过有限元分析软件对模型进行分析,得到了应力、位移、变形等相关结果。
最后,我们对结果进行了分析和讨论,评估了汽车结构的刚度、安全性和舒适性等指标。
实验结果通过实验,我们得到了如下结论:1. 汽车的结构材料主要包括钢材和铝材,钢材具有较好的强度和刚度,适用于承载部分的制造;铝材具有较低的密度和良好的耐腐蚀性,适用于轻质部件的制造。
2. 汽车的组成部分主要包括车身、底盘、发动机、悬挂和车轮等。
其中,车身和底盘是汽车的主要承载部分,发动机提供动力,悬挂和车轮为汽车提供悬挂和行驶支持。
3. 通过有限元分析,我们可以有效地评估汽车的结构刚度、安全性和舒适性等指标。
有限元分析软件能够计算汽车结构的应力、位移、变形等相关结果,为汽车设计和优化提供数据支持。
结论本次实验使我们对汽车的结构特点有了更深入的理解,并学会了应用有限元分析方法对汽车结构进行评估。
汽车配件检测项目及标准-日产汽车零部件专项检测

汽车配件检测标准,日产汽车零部件专项检测如果准备向客户证明您产品的安全性、高质量和耐用性,同时降低产品返回或召回的风险,那么很有必要全面了解您产品的物理、化学和环境特性。
在面向消费品、零售、汽车等各种行业,针对产品的安全性、稳定性和可靠性开展物理和机械测试方面,GRGTEST是行业先行者。
在全国实验室和办事处组成的全球网络以及技术精湛的业内专家的支持之下,我们的物理、化学和环境测试服务既具有国际触角又贴近当地监管要求,因此您可相信,我们一方面在制定满足您具体期望的测试方案,另一方面也在关注您客户和监管机构的期望。
作为整车生产的基础,汽车材料及零部件的质量是整车生产成功与否的先决条件。
随着各种新车型日益完善的功能和人们对乘车感受及安全的不断追求,要求汽车生产企业必须在源头上对材料质量和安全性作出监控。
汽车供应链对质量越来越关注,伴随着众多零部件和原材料在很多不同的地区和供应商采购,期望着每一个质量环节都能达到高的质量标准,同时也期望在开始就知道这些质量信息,并期望着众多的供应商能在现在和未来都能持续满足他们的需要,这是一个挑战,同时也是一个机遇以证明产品质量并且与汽车供应链建立持续的互动联系。
广电计量检测股份有限公司向各大汽车零部件供应商提供贯穿整个汽车及其零部件从生产到价值链的服务,帮客户降低风险,抵抗质量危机。
汽车零部件检测项目包括:1)汽车用材料测试:高分子材料测试(机械力学性能、热学性能、绝缘电性能、耐化学药品测试、人工加速老化、燃烧测试等)反光测试测试(尺寸、颜色、反光性能、耐着力、冲击性能、冲击强度、抗磨性能、色牢度、盐雾试验、压缩性能、绕曲强度、裂纹等)泡沫泡棉材料测试(表观密度、压缩形变、硬度、拉伸性能、吸水率、导热系数、反抗弹力、燃烧性能等)橡胶材料测试(密度、硬度、拉伸性能、冲击性能、挠曲性能、门尼粘度、热学性能、燃烧试验、人工加速老化试验、耐化学试剂、耐油试验等)2)汽车外饰件测试3)适用产品:汽车前后塑料(金属)保险杠、金属&非金属翼子板、后视镜壳、发动机罩、外装饰件、防撞条等测试项目:机械力学性能、刚强度、变形量测试、表层厚度测试、附着力测试、抗腐蚀测试、抗磨耗测试、高低温环境测试/紫外线老化测试、紫外/氙弧光老化、高低温环境力学试验、环境机械性能测试、沙尘/淋雨/飞石测试、金相测试、无损探伤、综合性能测试/疲劳耐久测试等。
材料的力学性能测试与评价
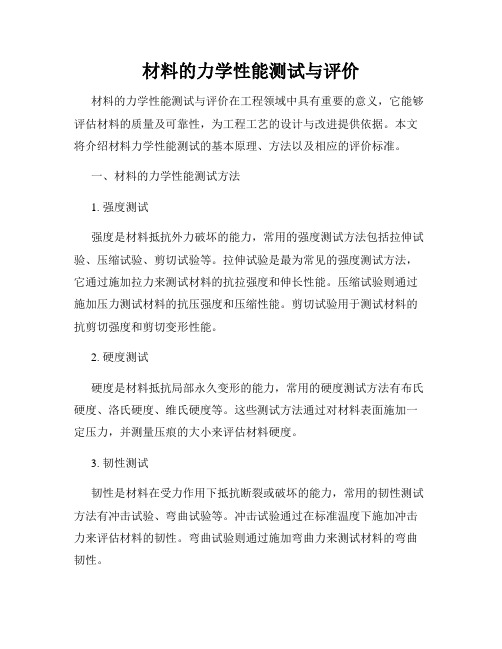
材料的力学性能测试与评价材料的力学性能测试与评价在工程领域中具有重要的意义,它能够评估材料的质量及可靠性,为工程工艺的设计与改进提供依据。
本文将介绍材料力学性能测试的基本原理、方法以及相应的评价标准。
一、材料的力学性能测试方法1. 强度测试强度是材料抵抗外力破坏的能力,常用的强度测试方法包括拉伸试验、压缩试验、剪切试验等。
拉伸试验是最为常见的强度测试方法,它通过施加拉力来测试材料的抗拉强度和伸长性能。
压缩试验则通过施加压力测试材料的抗压强度和压缩性能。
剪切试验用于测试材料的抗剪切强度和剪切变形性能。
2. 硬度测试硬度是材料抵抗局部永久变形的能力,常用的硬度测试方法有布氏硬度、洛氏硬度、维氏硬度等。
这些测试方法通过对材料表面施加一定压力,并测量压痕的大小来评估材料硬度。
3. 韧性测试韧性是材料在受力作用下抵抗断裂或破坏的能力,常用的韧性测试方法有冲击试验、弯曲试验等。
冲击试验通过在标准温度下施加冲击力来评估材料的韧性。
弯曲试验则通过施加弯曲力来测试材料的弯曲韧性。
二、材料力学性能评价标准1. 国际标准化组织(ISO)标准ISO为广泛应用于全球的工程和科学领域的组织,它制定了许多与材料力学性能测试与评价相关的标准。
例如ISO 6892-1标准规定了金属材料的拉伸试验方法,ISO 6506-1标准则规定了金属材料的布氏硬度测试方法。
2. 行业标准不同行业根据自身需求和特点制定了相应的材料力学性能评价标准。
例如汽车行业的ISO 16750标准规定了汽车电子元器件的耐久性和环境要求,电力行业的IEC标准则规定了电力设备的强度和耐久性要求。
3. 国家标准各个国家根据自身国情和工程需求制定了相应的材料力学性能评价标准。
例如中国国家标准GB/T 228.1规定了金属材料拉伸试验的一般要求,GB/T 231.1则规定了金属材料硬度试验的一般要求。
三、材料力学性能测试的意义与应用1. 材料选择与设计通过力学性能测试与评价,工程师可以了解不同材料的强度、硬度、韧性等性能指标,从而选取最合适的材料用于特定工程设计。
cjt5162017标准

cjt5162017标准随着科技的不断发展,汽车工业也得到了飞速的发展。
为了更好地规范汽车零部件的生产和检测,制定了一系列的标准,其中包括《cjt5162017标准》。
该标准是针对汽车零部件的检测而制定的,旨在确保汽车零部件的质量和安全性能。
一、标准简介《cjt5162017标准》是针对汽车零部件的检测而制定的,包括发动机、底盘、车身等零部件的质量和性能要求。
该标准规定了零部件的尺寸、材质、强度、耐久性等方面的要求,并规定了相应的检测方法和检测设备。
该标准的制定,旨在确保汽车零部件的质量和安全性能,提高汽车的安全性和可靠性。
二、检测方法《cjt5162017标准》规定了各种零部件的检测方法和检测设备,以确保零部件的质量和性能符合要求。
具体来说,该标准规定了以下几种检测方法:1.尺寸检测:采用测量仪器对零部件的尺寸进行测量,确保其符合规定的尺寸范围。
2.材质检测:采用化学分析、光谱分析等方法对零部件的材质进行检测,确保其符合规定的材质要求。
3.强度检测:采用力学试验等方法对零部件的强度进行检测,确保其能承受规定的载荷和压力。
4.耐久性检测:采用模拟行驶、疲劳试验等方法对零部件的耐久性进行检测,确保其能够长时间使用而不出现故障。
三、标准应用《cjt5162017标准》的应用范围非常广泛,涉及到汽车零部件的生产、销售、维修等多个领域。
具体来说,该标准的应用包括以下几个方面:1.生产厂家:生产厂家需要按照《cjt5162017标准》的要求生产汽车零部件,确保其质量和性能符合要求。
2.销售商:销售商需要按照《cjt5162017标准》的要求对汽车零部件进行检测和验收,确保其质量和性能符合要求。
3.维修企业:维修企业需要按照《cjt5162017标准》的要求对汽车零部件进行维修和更换,确保其安全性和可靠性。
四、总结《cjt5162017标准》是针对汽车零部件的检测而制定的,规定了各种零部件的检测方法和检测设备,以确保零部件的质量和性能符合要求。
汽车零部件验收及全套检验标准
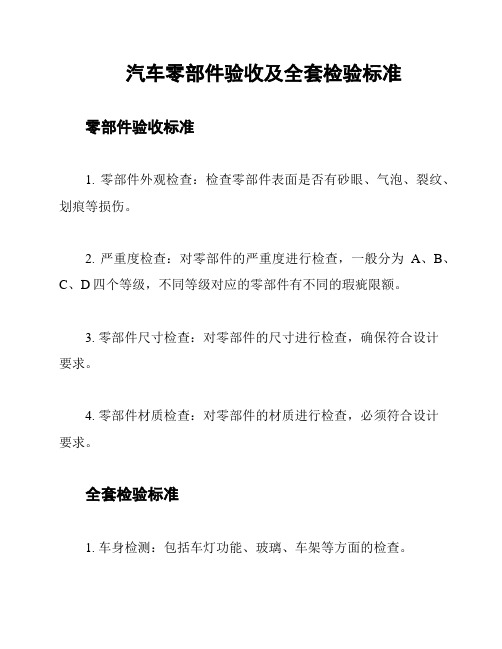
汽车零部件验收及全套检验标准零部件验收标准
1. 零部件外观检查:检查零部件表面是否有砂眼、气泡、裂纹、划痕等损伤。
2. 严重度检查:对零部件的严重度进行检查,一般分为A、B、
C、D四个等级,不同等级对应的零部件有不同的瑕疵限额。
3. 零部件尺寸检查:对零部件的尺寸进行检查,确保符合设计
要求。
4. 零部件材质检查:对零部件的材质进行检查,必须符合设计
要求。
全套检验标准
1. 车身检测:包括车灯功能、玻璃、车架等方面的检查。
2. 发动机检测:对发动机的性能进行测试,包括启动、怠速、
加速等方面。
3. 制动系统检测:对制动系统性能进行测试,确保制动力稳定。
4. 悬挂系统检测:对悬挂系统进行检查,确保能够正常工作。
5. 转向系统检测:对转向系统进行检查,确保能够正常工作。
6. 轮胎检测:对轮胎进行检查,检查轮胎的花纹深度、磨损情况、气压等。
以上为汽车零部件验收及全套检验标准,供参考。
为确保行车
安全和质量,建议对汽车定期进行检查、保养和维修。
汽车零部件试验汇总
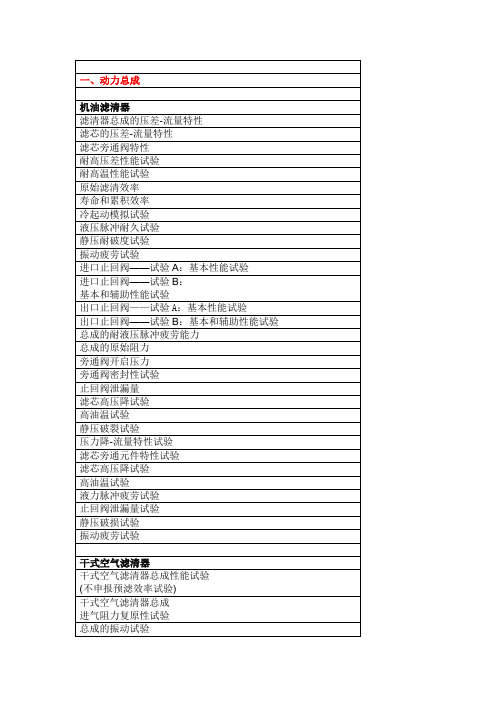
温升试验
低温工作和高温工作试验
温度变化试验
湿热试验
振动试验
耐久性试验
带点火开关的转向锁
外观检查
结构检查
档位转换试验
钥匙转动力矩试验
钥匙强度试验
转向锁强度试验
点火开关接线柱强度试验
绝缘电阻检查
触点压降试验
触点温升试验
耐温性试验
耐盐雾试验
耐振动试验
耐久性试验
翘板式开关
外形及安装尺寸检查
外壳防护等级试验
接头的耐腐蚀性试验
尼龙软管耐氯化锌试验
真空度试验
弯曲试验
耐汽油性试验
变形试验
结构
液压试验
缩颈试验
膨胀试验
吸水性试验
低温弯曲试验
动态条件下耐臭氧性
高温脉冲强度试验
盐雾试验
车轮
乘用车动态弯曲疲劳试验
乘用车动态径向疲劳试验
商用车辆辐板式车轮的
动态弯曲疲劳试验
商用车辆辐板式车轮和可拆卸式
轮辋的车轮动态径向疲劳试验
跑合试验Ⅱ
流量特性试验
效率试验
气密性试验
噪声试验
定转速冲击试验
变转速冲击试验
高温试验
真空助力器
密封性试验
空行程试验
反应时间试验
释放时间试验
输入一输出性能试验
振动耐久性试验
静强度试验
工作耐久性试验
耐腐蚀性试验
制动钳
扭转疲劳强度试验
清洁度
低压密封性试验
高压密封性试验
真空密封性试验
所需液量试验
拖滞扭矩试验
燃油箱盖的密封性
燃油箱内清洁度
燃油箱进气阀的通气试验
顶锻试验方法

顶锻试验方法
顶锻试验方法是一种测试汽车零部件强度和结构的试验方法。
顶锻试验通常由汽车制造商或汽车零部件供应商进行,用于验证汽车零部件的强度和稳定性。
顶锻试验方法包括顶压试验和顶冲试验两种类型。
顶压试验是通过施加一定的压力来测试汽车零部件的抗压强度。
顶冲试验则是通过施加一定的冲击力来测试汽车零部件的抗拉强度。
在顶压试验中,试验者使用一个压力机或冲击试验机,向汽车零部件施加压力。
根据汽车零部件的类型和设计,压力可以是逐渐增加的,也可以是逐渐下降的。
在顶压试验中,汽车零部件可能会受到多次试验,以获得更准确的结果。
在顶冲试验中,试验者使用一个冲击器或冲击钻,向汽车零部件施加冲击力。
根据汽车零部件的类型和设计,冲击力可以是逐渐增加的,也可以是逐渐下降的。
在顶冲试验中,汽车零部件可能会受到多次试验,以获得更准确的结果。
除了测试汽车零部件的抗压强度或抗拉强度外,顶锻试验方法还可以测试其他强度指标,如屈服强度、延伸率、弹性模量等。
通过测试这些指标,可以评估汽车零部件的强度和稳定性,确保它们能够满足汽车制造商和汽车零部件供应商的要求。
顶锻试验方法是一种重要的测试方法,可以评估汽车零部件的强度和稳定性,确保它们能够满足汽车制造商和汽车零部件供应商的要求。
汽车零部件强度分析

汽车零部件强度试验和评价关键词:汽车零部件汽车零部件的强度试验和评价是一项比较复杂的工作,必须考虑各方面的影响因素,载荷的复杂性、零件强度的离散性、以及影响这些参数外部和内部因素。
本文从所涉及的力学和统计学的概念和理论入手,介绍了在强度分析中所用到的基础知识。
随后对载荷分析和测量、零部件强度试验、强度评价等一些在实际工作中采用的方法进行了阐述,最后通过一个应用实例进一步希望能起到抛砖引玉的作用。
1.概述汽车的结构设计是一项综合性的工程,从时间上讲,它几乎贯穿整个产品开发阶段;从开发的对象来分,可以大致分成发动机、底盘、车身和电器部件;而从所涉及的专业上讲,又包括造型、振动和噪声、结构强度、整车性能等方面。
在这些专业领域中,强度是一个比较重要的问题。
一方面,为了满足在整个使用寿命内可靠性和耐久性要求,所有零部件、乃至整车需要有足够的强度;而另一方面,由于产品成本的要求,又要将零部件的材料用得最省。
强度设计的目标就是要在这两个相矛盾的要求间找到一个平衡点,使得零部件达到轻量化的同时,满足可靠性的要求。
与此同时,为了缩短整个产品开发过程的周期和降低开发费用,往往在样车还没有制成的开发初期阶段就需要强度设计的介入。
因此,强度设计要回答的问题就是:设计的零部件是否能够在使用寿命内不发生破坏?进行汽车零部件强度设计主要的手段包括:载荷测量,零部件试验和模拟计算。
本文结合作者的工作实际,重点从试验的角度出发,对汽车零部件的强度设计和评价进行阐述。
2.概念和理论载荷和强度金属的疲劳理论经过近百年的发展历史,已自成体系,对实际工作具体较好的指导意义。
我们在进行强度设计时,实际上只需要关注两个参数:一是所研究的零部件在整个使用过程中将会受到的各种各样的载荷,其表现形式是多种多样的,可以是零部件上所受的力,也可以是某处的应变,也可以是某个物体的振动加速度,等等;二是零部件本身能够承受这些载荷的能力有多强,也即俗称的“强度”,它是由零部件的结构、材料、加工工艺等因素决定的,是零部件本身的特性。
汽车行业汽车零部件质量标准
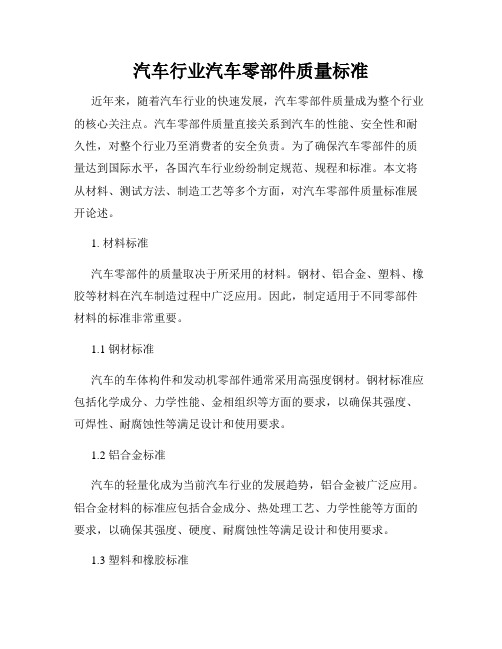
汽车行业汽车零部件质量标准近年来,随着汽车行业的快速发展,汽车零部件质量成为整个行业的核心关注点。
汽车零部件质量直接关系到汽车的性能、安全性和耐久性,对整个行业乃至消费者的安全负责。
为了确保汽车零部件的质量达到国际水平,各国汽车行业纷纷制定规范、规程和标准。
本文将从材料、测试方法、制造工艺等多个方面,对汽车零部件质量标准展开论述。
1. 材料标准汽车零部件的质量取决于所采用的材料。
钢材、铝合金、塑料、橡胶等材料在汽车制造过程中广泛应用。
因此,制定适用于不同零部件材料的标准非常重要。
1.1 钢材标准汽车的车体构件和发动机零部件通常采用高强度钢材。
钢材标准应包括化学成分、力学性能、金相组织等方面的要求,以确保其强度、可焊性、耐腐蚀性等满足设计和使用要求。
1.2 铝合金标准汽车的轻量化成为当前汽车行业的发展趋势,铝合金被广泛应用。
铝合金材料的标准应包括合金成分、热处理工艺、力学性能等方面的要求,以确保其强度、硬度、耐腐蚀性等满足设计和使用要求。
1.3 塑料和橡胶标准塑料和橡胶材料在汽车零部件中主要用于密封件、避震器、导流板等。
塑料和橡胶材料的标准应包括物理性能、化学性能、耐老化性能等方面的要求,以确保其满足汽车零部件的密封、减震、防水等功能。
2. 测试方法标准为了确保汽车零部件的质量,必须进行严格的测试。
测试方法标准的制定对于准确评估汽车零部件的性能、安全性和可靠性至关重要。
2.1 强度和刚度测试方法标准汽车零部件在使用过程中需要承受各种复杂的载荷。
为了确保其强度和刚度满足设计要求,需要制定相应的测试方法标准。
例如,对汽车底盘横梁进行弯曲试验、对车门进行开合循环试验等。
2.2 耐久性测试方法标准汽车零部件需要具备较长的使用寿命,因此耐久性测试非常重要。
制定耐久性测试方法标准,以模拟实际使用条件下的振动、温度、湿度等环境,对汽车零部件进行持久性能测试。
2.3 安全性测试方法标准汽车零部件的安全性对驾驶员和乘客的生命财产安全至关重要。
- 1、下载文档前请自行甄别文档内容的完整性,平台不提供额外的编辑、内容补充、找答案等附加服务。
- 2、"仅部分预览"的文档,不可在线预览部分如存在完整性等问题,可反馈申请退款(可完整预览的文档不适用该条件!)。
- 3、如文档侵犯您的权益,请联系客服反馈,我们会尽快为您处理(人工客服工作时间:9:00-18:30)。
汽车零部件强度试验和评价 周 炜 上海大众汽车有限公司 【摘要】 汽车零部件的强度试验和评价是一项比较复杂的工作,必须考虑各方面的影响因素,载荷的复杂性、零件强度的离散性、以及影响这些参数的外部和内部因素。
本文从所涉及的力学和统计学的概念和理论入手,介绍了在强度分析中所用到的基础知识。
随后对载荷分析和测量、零部件强度试验、强度评价等一些在实际工作中采用的方法进行了阐述,最后通过一个应用实例进一步希望能起到抛砖引玉的作用。
关键词:强度 汽车零部件 疲劳耐久性试验1. 概述汽车的结构设计是一项综合性的工程,从时间上讲,它几乎贯穿整个产品开发阶段;从开发的对象来分,可以大致分成发动机、底盘、车身和电器部件;而从所涉及的专业上讲,又包括造型、振动和噪声、结构强度、整车性能等方面。
在这些专业领域中,强度是一个比较重要的问题。
一方面,为了满足在整个使用寿命内可靠性和耐久性要求,所有零部件、乃至整车需要有足够的强度;而另一方面,由于产品成本的要求,又要将零部件的材料用得最省。
强度设计的目标就是要在这两个相矛盾的要求间找到一个平衡点,使得零部件达到轻量化的同时,满足可靠性的要求。
与此同时,为了缩短整个产品开发过程的周期和降低开发费用,往往在样车还没有制成的开发初期阶段就需要强度设计的介入。
因此,强度设计要回答的问题就是:设计的零部件是否能够在使用寿命内不发生破坏?进行汽车零部件强度设计主要的手段包括:载荷测量,零部件试验和模拟计算。
本文结合作者的工作实际,重点从试验的角度出发,对汽车零部件的强度设计和评价进行阐述。
2. 概念和理论载荷和强度金属的疲劳理论经过近百年的发展历史,已自成体系,对实际工作具体较好的指导意义。
我们在进行强度设计时,实际上只需要关注两个参数:一是所研究的零部件在整个使用过程中将会受到的各种各样的载荷,其表现形式是多种多样的,可以是零部件上所受的力,也可以是某处的应变,也可以是某个物体的振动加速度,等等;二是零部件本身能够承受这些载荷的能力有多强,也即俗称的“强度”,它是由零部件的结构、材料、加工工艺等因素决定的,是零部件本身的特性。
对一个零部件来说,载荷和强度两者都是随机变量,它们符合一定log p图1 载荷和强度的概率密度分布的统计规律。
在理想的情况下,我们借助概率密度分布,可以对两者以及它们之间的关系进行数学描述(图1)。
假设两者都符合对数正态分布,其均值和方差分别为m L ,m S 和s S ,s L 。
两个均值之间的差称安全系数j SF :()220log S L L S SF s s m m j +⋅−=−=µ,其中µ0是正态分布的标准偏量。
当载荷大于强度时,即两条概率密度分布相交的区域,失效就会发生。
广义损伤值载荷是一种物理量,而疲劳强度则是指使用寿命,具有时间的量纲。
为了使这两者具有可比性,引入了广义损伤值的概念。
狭义的损伤原来是用于表征金属构件在一定的外载荷作用下在一定时间内发生疲劳的量度。
记录金属构件某个危险部位在一段时间内的局部应变,采用一定的计数方法,如雨流法,得到应变载荷谱,然后根据材料或构件的应变-寿命曲线,利用线型损伤累积的理论,当损伤值累计到1则构件将发生破坏。
而这里引申了损伤表征载荷累积程度的意义,将它应用于其它物理量,如加速度,力,位移等,上。
同样记录这些载荷的时间历程,通过计数方法得到载荷谱,然后根据一条标准的S-N 曲线(图2),利用线性累积损伤理论计算广义的损伤值。
这样,就可以通过一个统一的量度来对载荷和强度进行比较。
强度准则和检验手段 对于强度设计来说,首先必须确定相应的强度准则,也即我设计的产品最终在强度方面要满足什么样的量化指标?一般来说,每个整车厂都对强度准则有自己的定义,例如,欧洲的汽车生产厂家对涉及安全性的零部件的要求是在用户道路行驶200,000至300,000公里不发生破坏。
需要注意的是,由于以上提到的载荷和强度的随机特性,因此在制定强度准则时,也必须考虑概率的因素。
不同的厂家,根据多年研发的经验,有各自的强度和耐久性试验方法。
有的采用用户道路试验方法,即根据载荷分析和经验积累,选择一条或多条用户道路的组合,作为整车耐久性试验道路,如果设计的产品在试验道路上行驶一定的里程后没有发生破坏,那么则认为其强度是足够的。
采用用户道路作为试验道路,其真实性勿庸置疑,但缺点是试验周期太长,花费也较大。
大多数的厂家选择试车场的强化耐久道路作为试验道路,这样在载荷强度较高的强化路面进行耐久试验可以加快试验周期。
在我国,有国家行业认可的试车场,也有企业自己建设的试车场,无论是在什么样的试车场里做试验,关键的问题在于如何找到强化道路和所确定的强度准则之间的当量关系。
在有些零部件的开发阶段,样车还没有制成,或者单个零部件的结构改型,如果要用一辆整车来进行耐久试验的话,比较浪费,这时利用台架试验来验证强度准则就显得十分方便和必要了。
由于实验室内的环境相对比较固定,载荷的离散度非常小,通过一定的载荷处理技术又可以将试验时间缩短。
一般采用单一频率等幅加载N S图2 标准S-N 曲线 106和道路模拟随机加载两种方式:等幅疲劳试验又称为Wöhler 试验,这是获取零部件S-N 曲线的较简单的方法;道路模拟试验是利用远程参数控制技术,在试验台上再现实际道路载荷的一种试验方法,相对来说比较复杂。
近年来,从计算机CAE 基础上又发展了所谓的虚拟试验技术,有了零部件的有限元模型和虚拟路面谱以及虚拟试验台模型,可以在软件上模拟真实的试验状况。
从而在较早的开发阶段就可以对零部件的强度进行评价,大大缩短了开发周期。
以上提到的这些试验方法并不是孤立的,往往在开发过程中相结合使用。
3. 载荷分析和测量如上所述,载荷和强度都是符合一定统计规律的随机变量,相比较而言,载荷的离散度比零件本身强度的离散度要大得多。
因为对于汽车上某个零部件来说,在整个使用寿命内所受到的载荷其影响因素实在是太多了:路面状况、气候条件、交通情况、法律法规、驾驶方式……这些不确定因素导致要想准确得到载荷的真实分布是不可能的,通过测量等手段获得的载荷只是其中的某些样本。
资料表明,如果要相对准确得到一辆汽车在整个寿命期间受到的载荷的话,样本容量要满足这些条件:第一,测量通道数大致在50个左右,包括车轮上的力、悬挂和车身的加速度、车身局部应变等;第二,测量车的样本数量大概在2,000辆左右;第三,每辆车记录的行驶里程必须大于10,000公里。
在现有技术条件下,这样庞大的测量任务几乎是不可能完成的。
欧洲的各大汽车生产厂家联合了一些技术服务公司,多年前开展了一项名为“Kuko (用户道路谱)”的测量项目。
他们在一些用户的车辆上安装很小规模的测量系统,测量通道数8个以下,大多数的信息从车载CAN 总线中测量,然后在用户行驶3,000公里后下载测量数据。
由这些少数的测量通道,通过事先计算的“传递函数”转换,推广到其它更多的物理量上。
同时,在较大规模的用户中进行有关驾驶习惯和道路状况的问卷调查,将测量结果与调查结果相结合,推导出载荷的概率分布。
用户使用状况的调查和道路载荷测量是一个长期的项目,更多的情况下,在开发阶段没有时间做这项工作。
这时,我们把试车场的强化耐久试验道路作为载荷测量的依据。
测量轮技术的出现为道路载荷测量提供了极大的方便(图3)。
通过安装在一个特制的轮毂上的力传感器单元,可以方便的测量地面作用在车轮中心的六个分力(三个方向的力和三个方向的力矩)。
而以往,分解纵向力、侧向力和垂直力的工作非常复杂。
首先要在底盘部件上分别找到对单向载荷敏感的关键点,然后在相应位置粘贴应变片,最后在台架上进行单向载荷标定,才能测量车轮载荷。
这样的做法有很大的局限性,实际上各方向载荷在这些关键点藕合作用不能完全消除,整个过程步骤烦杂,误差积累明显。
因而,准确性和适用性很低,影响了载荷分析和将来台架试验的迭代。
除测量轮之外,根据研究对象的不同,底盘加速度、车身加速度、重心加速度、减震器位移、车身危险截面应变等其它物理量也是测量的目标。
图3 用于道路载荷测量的测量轮4. 零部件的强度零部件的疲劳强度,是指零部件能够承受随时间变化的外载荷而不发生破坏的能力。
在强度评价中,根据疲劳寿命估算方法的不同,用零部件的应力-寿命曲线或应变-寿命曲线来表示。
一定材料的疲劳强度可以从资料中查到,而一定尺寸和形状的零部件的疲劳强度虽然也勉强可以通过乘以一系列的经验系数得到,但在实际工作中绝大多数还是通过试验的方法获取的。
因为通过试验得到的疲劳强度跟实际情况非常接近,并且最主要的还是,通过试验方法可以得到零部件强度的离散度。
由于,如上所述,零部件的强度也是符合统计规律的随机变量,因此获取一批零部件的强度离散度也是非常重要的。
考虑试验成本和试验时间的约束,零部件疲劳试验一般采用等幅加载的方式进行。
在该零部件疲劳强度区合理选取二到三个级别的载荷进行试验,每个载荷级别至少做五个样本。
对得到的试验数据经过一定的分析处理,可以得到该零部件的均值S-N 曲线以及相应的强度离散度,两者一起作为强度评价的依据。
除了等幅单级加载试验外,有些时候还采用更接近实际工况的道路模拟试验。
道路模拟试验可以是对单个零部件,也可以是对总成甚至是整车的。
整个试验过程大致分为以下几个步骤:首先对所关心的零部件在典型道路上的载荷进行测量,一般也是在试车场的强化道路上进行;其次对采集所得到的载荷进行浓缩和编辑处理,得到目标载荷谱;然后利用远程参数控制技术,在专门的道路模拟试验台上对目标载荷谱进行迭代,得到试验载荷谱;反复播放得到的载荷谱,经过一定的循环次数后,对零部件强度进行评价。
随着试验台技术的日臻完善,基于液压伺服系统的整车道路模拟试验台,从原来简单的四通道轮胎耦合方式发展到更接近实际行驶状况的多通道轴耦合形式(图4),其系统的复杂程度也日益提高。
在对载荷和强度这两个随机变量有一定的了解之后,我们就可以依据某种疲劳损伤理论,对所关心的零部件的强度进行评价。
比较成熟的疲劳寿命预测方法有名义应力法和局部应力应变法(图5)。
图4 MTS 21通道整车轴耦合试验台图5 两种疲劳寿命估算理论5. 应用实例为了降低材料成本,对某车型的排气管支架进行了改进设计,我们的任务是通过试验的手段来检验新结构是否能够满足强度的要求。
由于结构改动只涉及很小的零件范围,如果改装一批整车来做道路耐久试验的话,花费太大,而且试验周期较长,因此决定只进行零部件级别的台架试验。
首先进行道路载荷测量,金属支架的两边通过焊接的方式固定在排气管上,中间通过螺栓连接在车身某处。
根据简单的受力分析和以往的经验,确定螺栓孔周边为载荷相对较大的危险点。
在螺栓孔周边贴上应变片,安装在一辆整车上,在试车场的强化耐久道路上进行载荷测量(图6)。